Минимальный диаметр фрезы по металлу – Размеры фрез для обработки металла
alexxlab | 04.02.2020 | 0 | Вопросы и ответы
таблица подбора скорости подачи фрезы и рекомендации по фрезеровке и эксплуатации оборудования.
В последние годы большое количество людей сконструировали или приобрели ЧПУ станок и «ударились» в искусство. Как правило, 99% из них непрофессиналы-любители в фрезеровальной индустрии, и не знают таких понятий как «величина подачи на зуб» и «стойкость инструмента», а “скорость резания” и “скорость подачи” для них это одно и тоже. Кроме того, многие фрезеровщики не знают, что под каждый материал, имеющий разную плотность и твёрдость, каждый диаметр фрезы и различное количество ножей у фрезы, выставляются разные режимы фрезеровки. В этом случае любители выставляют режимы из трёх доступных версий:
- “от балды”,
- “от фонаря”,
- “от Кулибина из интернета»
Если хорошо прошерстить Интернет, то необходимые формулы и неупорядоченную, разбросанную как попало, информацию можно насобирать. Но часто полученные данные из заумных формул будут неудобны для применения к реальному станку, например из-за полученных оборотов шпинделя выше, чем имеющийся в наличии, или нестандартных неокруглённых значений оборотов шпинделя, которые непонятно каким образом можно установить на разных станках.
Универсальная таблица подбора скорости подачи фрезы
В таблице ниже, предпринята попытка облегчить жизнь фрезеровщикам – любителям древесины, и приведены расчётные значения для древесины при стандартных удобных значениях оборотов шпинделя.
Упрощённый вариант таблицы для экспресс расчёта доступен по ссылке: скачать
Как пользоваться таблицей?
Предположим у Вас имеется торцевая двухперьевая фреза диаметром 3мм. Находим её в левой колонке таблицы. Если Вы работаете “на дядю”, то можете выбрать самые максимальные обороты шпинделя, если не жалко шпиндель, как правило – это 24000 об/мин. Если это личный Ваш станок, или нет желания гонять чужой шпиндель на максимальных предельных оборотах, то выбираем 21000 об/мин. В четвёртой колонке таблицы находим подачу 2388мм/мин. Если будет использоваться сферическая 3D фреза для шлифовки поверхности после предварительной черновой обработки
, то допустимо увеличивать подачу вплоть до двухкратного значения =4776мм/мин – это продлит срок службы фрезы. Если хотите быстрее работу закончить, например в два раза быстрее, то лучше применить четырёхпёрую фрезу (6-я колонка), тогда подачу можно установить 4245мм/мин, но для четырёхпёрой 3D фрезы не увеличивают подачу в два раза, аналогично двухпёрой, так как в работе на кончике 3D фрезы участвуют только 2 ножа, а вторые 2 ножа работают частично. Но не всегда ускорение обработки будет возможно на хобби-станке.Как правило, из-за недостатка средств, и полной экономии, хобби-станок собран из подручных средств и всякого хлама, и не позволяет работать на скоростях выше 2000мм/мин. В этом случае выбирайте меньшие обороты шпинделя и строку с подачей, на которой ваш станок не будет глючить из-за превышения скорости подачи.
В станках, на основе ШВП и шагового двигателя, возможно добиться максимальной скорости подачи 11000 мм/мин при условии отсутствия экономии на требуемых деталях при сборке станка. Но для надёжности, и предотвращения проскакивания шагов при нагрузке на фрезу, не следует пользоваться станком на ШВП при подачах выше 4500мм/мин для фрез с большими диаметрами, и не более 5000мм/мин для фрез с малыми диаметрами. В станках на основе реечной передачи и шагового двигателя, возможно добиться скорости подачи 24000мм/мин (32000 в лучших моделях), но для надёжности, и предотвращения проскакивания шагов при нагрузке на фрезу, не следует пользоваться станком на реечной передаче с шаговым двигателем при подачах выше 13 000мм/мин. При выборе станка следует помнить: станки с ШВП более точные, но и более медленные. Станки для обработки древесины на реечной передаче с шестернями более скоростные, но точность их низкая, даже, если управляются серводвигателями, соответственно очень мелкие и точные изделия изготавливать на них нежелательно и противопоказано.
Профессионалы обычно имеют 2 станка: маленький точный на ШВП для мелочёвки со шпинделем 1.5-2квт, и большой скоростной на реечной передаче для крупных изделий со шпинделем не менее 3квт. Любительский подход к теме типа «хачу один станок, могущий всё» является в корне неправильным для бизнеса. Выбор между шаговым двигателем и сервоприводом – это личное дело каждого, и зависит только от толщины имеющегося кошелька.
Таблица режимов для торцевых фрез при фрезеровке/резке древесины: Ясень, Орех, Граб, Акация, Самшит, Клён
Для Дуба, Бука. Вишни, Берёзы, модельный пластик и т.д., можно умножить горизонтальную подачу на коэффициент 1.13
Для мягких пород типа Сосны, и т.д., можно умножить горизонтальную подачу на коэффициент 1.3
Данные таблицы действительны для прямых фрез со стандартизованой длиной заточки = диаметр фрезы умножить на 4. Все заточки, которые более этого значения – это фрезы с удлиннёной заточкой. Следует уменьшать глубину прохода в слой, подачу и обороты шпинделя для нестандартных заточек до уменьшения визга и прекращения обламывания фрезы.
Диаметр фрезы из твёрдого сплава |
Обороты шпинделя |
Горизонтальная подача при определённом количестве ножей у торцевой прямой фрезы |
||||||
1 нож: |
2 ножа: |
3 ножа: |
4 ножа: |
|||||
0.1мм |
24000 об/мин |
44 мм/мин |
83 мм/мин |
– |
– |
|||
21000 об/мин |
38 мм/мин |
72 мм/мин |
– |
– |
||||
0.2мм |
24000 об/мин |
67 мм/мин |
127 мм/мин |
– |
– |
|||
21000 об/мин |
59 мм/мин |
111 мм/мин |
– |
– |
||||
0.3мм |
24000 об/мин |
121 мм/мин |
230 мм/мин |
– |
– |
|||
21000 об/мин |
106 мм/мин |
201 мм/мин |
– |
– |
||||
0.35мм |
24000 об/мин |
141 мм/мин |
268 мм/мин |
– |
– |
|||
21000 об/мин |
124 мм/мин |
235 мм/мин |
– |
– |
||||
0.4мм |
24000 об/мин |
162 мм/мин |
306 мм/мин |
434 мм/мин |
544 мм/мин |
|||
21000 об/мин |
142 мм/мин |
268 мм/мин |
380 мм/мин |
477 мм/мин |
||||
18000 об/мин |
121 мм/мин |
230 мм/мин |
325 мм/мин |
408 мм/мин |
||||
0.5мм |
24000 об/мин |
202 мм/мин |
383 мм/мин |
542 мм/мин |
595 мм/мин |
|||
21000 об/мин |
177 мм/мин |
335 мм/мин |
475 мм/мин |
681 мм/мин |
||||
18000 об/мин |
152 мм/мин |
287 мм/мин |
407 мм/мин |
510 мм/мин |
||||
0.6мм |
24000 об/мин |
243 мм/мин |
460 мм/мин |
651 мм/мин |
817 мм/мин |
|||
21000 об/мин |
212 мм/мин |
402 мм/мин |
570 мм/мин |
715 мм/мин |
||||
18000 об/мин |
182 мм/мин |
344 мм/мин |
488 мм/мин |
612 мм/мин |
||||
0.79мм и 0.8мм |
24000 об/мин |
320 мм/мин |
605 мм/мин |
857 мм/мин |
1075 мм/мин |
|||
21000 об/мин |
280 мм/мин |
530 мм/мин |
750 мм/мин |
940 мм/мин |
||||
18000 об/мин |
242 мм/мин |
459 мм/мин |
650 мм/мин |
816 мм/мин |
||||
1.0мм |
24000 об/мин |
404 мм/мин |
766 мм/мин |
1085 мм/мин |
1361 мм/мин |
|||
21000 об/мин |
354 мм/мин |
670 мм/мин |
949 мм/мин |
1191 мм/мин |
||||
18000 об/мин |
303 мм/мин |
575 мм/мин |
814 мм/мин |
1021 мм/мин |
||||
15000 об/мин |
252 мм/мин |
478 мм/мин |
677 мм/мин |
850 мм/мин |
||||
1.19мм и 1.2мм |
24000 об/мин |
481 мм/мин |
911 мм/мин |
1291 мм/мин |
1620 мм/мин |
|||
21000 об/мин |
421 мм/мин |
797 мм/мин |
1130 мм/мин |
1417 мм/мин |
||||
18000 об/мин |
361 мм/мин |
683 мм/мин |
968 мм/мин |
1215 мм/мин |
||||
15000 об/мин |
303 мм/мин |
574 мм/мин |
813 мм/мин |
1020 мм/мин |
||||
1.5мм |
24000 об/мин |
606 мм/мин |
1148 мм/мин |
1627 мм/мин |
2041 мм/мин |
|||
21000 об/мин |
530 мм/мин |
1005 мм/мин |
1424 мм/мин |
1786 мм/мин |
||||
18000 об/мин |
455 мм/мин |
861 мм/мин |
1220 мм/мин |
1531 мм/мин |
||||
15000 об/мин |
379 мм/мин |
717 мм/мин |
1017 мм/мин |
1276 мм/мин |
||||
1.59мм |
24000 об/мин |
643 мм/мин |
1218 мм/мин |
1726 мм/мин |
2165 мм/мин |
|||
21000 об/мин |
563 мм/мин |
1066 мм/мин |
1510 мм/мин |
1895 мм/мин |
||||
18000 об/мин |
482 мм/мин |
914 мм/мин |
1294 мм/мин |
1624 мм/мин |
||||
15000 об/мин |
402 мм/мин |
761 мм/мин |
1078 мм/мин |
1353 мм/мин |
||||
2.0мм |
24000 об/мин |
875 мм/мин |
1658 мм/мин |
2348 мм/мин |
2946 мм/мин |
|||
21000 об/мин |
765 мм/мин |
1450 мм/мин |
2054 мм/мин |
2578 мм/мин |
||||
18000 об/мин |
656 мм/мин |
1243 мм/мин |
1761 мм/мин |
2210 мм/мин |
||||
15000 об/мин |
547 мм/мин |
1036 мм/мин |
1467 мм/мин |
1841 мм/мин |
||||
2.35мм и 2.38мм |
24000 об/мин |
1073 мм/мин |
2033 мм/мин |
2879 мм/мин |
3613 мм/мин |
|||
21000 об/мин |
939 мм/мин |
1778 мм/мин |
2520 мм/мин |
3161 мм/мин |
||||
18000 об/мин |
805 мм/мин |
1525 мм/мин |
2160 мм/мин |
2710 мм/мин |
||||
15000 об/мин |
674 мм/мин |
1277 мм/мин |
1809 мм/мин |
2270 мм/мин |
||||
3.0мм |
24000 об/мин |
1440 мм/мин |
2729 мм/мин |
3866 мм/мин |
4852 мм/мин |
|||
21000 об/мин |
1260 мм/мин |
2388 мм/мин |
3383 мм/мин |
4245 мм/мин |
||||
18000 об/мин |
1080 мм/мин |
2047 мм/мин |
2900 мм/мин |
3639 мм/мин |
||||
15000 об/мин |
900 мм/мин |
1706 мм/мин |
2416 мм/мин |
3032 мм/мин |
||||
12000 об/мин |
720 мм/мин |
1364 мм/мин |
1933 мм/мин |
2426 мм/мин |
||||
9000 об/мин |
540 мм/мин |
1023 мм/мин |
1450 мм/мин |
1819 мм/мин |
||||
6000 об/мин |
360 мм/мин |
682 мм/мин |
966 мм/мин |
1212 мм/мин |
||||
3000 об/мин |
180 мм/мин |
341 мм/мин |
483 мм/мин |
606 мм/мин |
||||
3.175мм |
24000 об/мин |
1540 мм/мин |
2916 мм/мин |
4132 мм/мин |
5185 мм/мин |
|||
21000 об/мин |
1347 мм/мин |
2551 мм/мин |
3615 мм/мин |
4537 мм/мин |
||||
18000 об/мин |
1155 мм/мин |
2188 мм/мин |
3099 мм/мин |
3888 мм/мин |
||||
15000 об/мин |
962 мм/мин |
1823 мм/мин |
2582 мм/мин |
3240 мм/мин |
||||
12000 об/мин |
770 мм/мин |
1458 мм/мин |
2066 мм/мин |
2592 мм/мин |
||||
9000 об/мин |
577 мм/мин |
1094 мм/мин |
1549 мм/мин |
1944 мм/мин |
||||
6000 об/мин |
385 мм/мин |
729 мм/мин |
1033 мм/мин |
1296 мм/мин |
||||
3000 об/мин |
192 мм/мин |
365 мм/мин |
516 мм/мин |
648 мм/мин |
||||
4.0мм |
24000 об/мин |
2081 мм/мин |
3944 мм/мин |
5587 мм/мин |
7010 мм/мин |
|||
21000 об/мин |
1821 мм/мин |
3450 мм/мин |
4888 мм/мин |
6134 мм/мин |
||||
18000 об/мин |
1561 мм/мин |
2958 мм/мин |
4190 мм/мин |
5258 мм/мин |
||||
15000 об/мин |
1300 мм/мин |
2465 мм/мин |
3492 мм/мин |
4382 мм/мин |
||||
12000 об/мин |
1040 мм/мин |
1972 мм/мин |
2793 мм/мин |
3505 мм/мин |
||||
9000 об/мин |
780 мм/мин |
1479 мм/мин |
2095 мм/мин |
2629 мм/мин |
||||
6000 об/мин |
520 мм/мин |
986 мм/мин |
1397 мм/мин |
1753 мм/мин |
||||
3000 об/мин |
260 мм/мин |
493 мм/мин |
698 мм/мин |
876 мм/мин |
||||
4.76мм |
24000 об/мин |
2666 мм/мин |
5050 мм/мин |
7156 мм/мин |
8980 мм/мин |
|||
21000 об/мин |
2333 мм/мин |
4420 мм/мин |
6262 мм/мин |
7857 мм/мин |
||||
18000 об/мин |
1999 мм/мин |
3789 мм/мин |
5367 мм/мин |
6735 мм/мин |
||||
15000 об/мин |
1666 мм/мин |
3157 мм/мин |
4473 мм/мин |
5613 мм/мин |
||||
12000 об/мин |
1333 мм/мин |
2526 мм/мин |
3578 мм/мин |
4490 мм/мин |
||||
9000 об/мин |
999 мм/мин |
1894 мм/мин |
2684 мм/мин |
3368 мм/мин |
||||
6000 об/мин |
666 мм/мин |
1263 мм/мин |
1789 мм/мин |
2245 мм/мин |
||||
3000 об/мин |
333 мм/мин |
631 мм/мин |
895 мм/мин |
1122 мм/мин |
||||
5.0мм |
24000 об/мин |
3108 мм/мин |
5890 мм/мин |
8344 мм/мин |
10470 мм/мин |
|||
21000 об/мин |
2720 мм/мин |
5153 мм/мин |
7300 мм/мин |
9162 мм/мин |
||||
18000 об/мин |
2331 мм/мин |
4417 мм/мин |
6258 мм/мин |
7853 мм/мин |
||||
15000 об/мин |
1943 мм/мин |
3681 мм/мин |
5215 мм/мин |
6544 мм/мин |
||||
12000 об/мин |
1555 мм/мин |
2945 мм/мин |
4172 мм/мин |
5235 мм/мин |
||||
9000 об/мин |
1166 мм/мин |
2209 мм/мин |
3129 мм/мин |
3926 мм/мин |
||||
6000 об/мин |
777 мм/мин |
1472 мм/мин |
2086 мм/мин |
2618 мм/мин |
||||
3000 об/мин |
388 мм/мин |
736 мм/мин |
1043 мм/мин |
1308 мм/мин |
||||
6.0мм |
24000 об/мин |
4338 мм/мин |
8212 мм/мин |
11645 мм/мин |
14612 мм/мин |
|||
21000 об/мин |
3796 мм/мин |
7192 мм/мин |
10189 мм/мин |
12786 мм/мин |
||||
18000 об/мин |
3254 мм/мин |
6165 мм/мин |
8734 мм/мин |
10960 мм/мин |
||||
15000 об/мин |
2712 мм/мин |
5138 мм/мин |
7278 мм/мин |
9133 мм/мин |
||||
12000 об/мин |
2169 мм/мин |
4110 мм/мин |
5822 мм/мин |
7307 мм/мин |
||||
9000 об/мин |
1626 мм/мин |
3082 мм/мин |
4367 мм/мин |
5480 мм/мин |
||||
6000 об/мин |
1085 мм/мин |
2055 мм/мин |
2911 мм/мин |
3653 мм/мин |
||||
3000 об/мин |
542 мм/мин |
1028 мм/мин |
1455 мм/мин |
1827 мм/мин |
||||
6.35мм |
24000 об/мин |
4515 мм/мин |
8555 мм/мин |
12119 мм/мин |
15208 мм/мин |
|||
21000 об/мин |
3951 мм/мин |
7485 мм/мин |
10604 мм/мин |
13307 мм/мин |
||||
18000 об/мин |
3386 мм/мин |
6416 мм/мин |
9089 мм/мин |
11406 мм/мин |
||||
15000 об/мин |
2822 мм/мин |
5347 мм/мин |
7575 мм/мин |
9505 мм/мин |
||||
12000 об/мин |
2258 мм/мин |
4277 мм/мин |
6060 мм/мин |
7604 мм/мин |
||||
9000 об/мин |
1693 мм/мин |
freza93.ru
Режимы резания при фрезеровании фрезами
На предприятиях, в составе которых есть подразделения, занимающиеся поверхностной обработкой заготовок, на основе нормативных документов составляются специальные карты, которыми руководствуется оператор при изготовлении той или иной детали. Хотя в некоторых случаях (к примеру, новое оборудование, инструмент) нюансы технологических операций фрезеровщику приходится определять самостоятельно. Если маломощный станок эксплуатируется в домашних условиях, тем более, никаких официальных подсказок под рукой, как правило, нет.
Эта статья поможет не только понять, на основе чего производится расчет режима резания при фрезеровании и выбор соответствующего инструмента, но и дает практические рекомендации, которые достаточны для обработки деталей на бытовом уровне.
Тем, кто по большей степени связан с металлами, для более детального ознакомления с нюансами фрезерования стоит обратиться к учебнику «Металлорежущие станки» – 2003 года, Черпаков Б.И., Альперович Т.А. Порядок расчета режимов резания также хорошо изложен в различных пособиях. Например, в методических рекомендациях от 2000 года (МГАУ – Колокатов А.М., Баграмов Л.Г.).
Особенность фрезерования в том, что режущие кромки вступают в прямой контакт с материалом лишь периодически. Как следствие – вибрации, ударные нагрузки и повышенный износ фрез. Наиболее эффективным режимом считается такой, при котором оптимально сочетаются следующие параметры – глубина, подача и скорость резания без ухудшения точности и качества обработки. Именно это позволяет существенно снизить стоимость технологической операции и повысить производительность.
Предусмотреть буквально все нюансы фрезерования невозможно. Заготовки, подлежащие обработке, отличаются структурой, габаритами и формой; режущие инструменты – своей геометрией, конструктивным исполнением, наличием/отсутствием защитного слоя и тому подобное. Все, что изложено по режимам резания далее, следует рассматривать всего лишь как некий ориентир. Для уточнения конкретных параметров фрезерования следует пользоваться специальными таблицами и справочными данными.
Выбор инструмента
Главным образом это относится к его диаметру. В чем особенность подбора фрезы (все виды описаны здесь) по этому параметру?
- Повышение диаметра автоматически приводит к увеличению стоимости инструмента.
- Взаимозависимость двух показателей – если подача возрастает, то скорость резания падает, так как она ограничивается структурой обрабатываемой детали (см. ниже).
Рекомендация
Оптимальным считается такой диаметр фрезы, при котором его величина соответствует (или немного больше) требуемой глубине резания. В некоторых случаях за 1 проход можно выбрать стружку и более толстую, но это относится лишь к материалам, характеризующимся невысокой плотностью. Например, пенопласт или некоторые породы древесины.
Скорость резания
В зависимости от материала образца можно ориентироваться на следующие показатели (м/мин):
- древесина, термопласты – 300 – 500;
- ПВХ – 100 – 250;
- нержавейка – 45 – 95;
- бронза – 90 – 150;
- латунь – 130 – 320;
- бакелит – 40 – 110;
- алюминий и его сплавы – 200 – 420.
Рекомендуется ориентироваться на среднее значение величины. Например, если материал – алюминий, за исходную взять скорость = 300. В процессе фрезерования заготовки станет ясно, уменьшить ее или увеличить.
Частота вращения фрезы
Простейшая формула выглядит так:
n (число оборотов) = 1000 Vc (желаемая скорость реза) / π D (диаметр фрезы).
Рекомендация
Гонять шпиндель на максимальных оборотах с точки зрения безопасности не следует. Значит, только за счет этого скорость резания уменьшится примерно на 10 – 15%. Частично компенсировать эту «потерю» можно установкой фрезы большего диаметра. Этим скорость несколько повышается. Если подходящей под рукой нет, придется решать – тратить деньги на новый инструмент или довольствоваться теми возможностями, которые имеются у фрезерного станка. Опять-таки, все это проверяется лишь практикой работы на конкретном оборудовании, но общий смысл рекомендации понятен.
Подача
На этот параметре фрезерования следует обратить пристальное внимание!
Долговечность фрезы и качество обработки заготовки зависят от того, какой толщины слой снимается за одну проходку, то есть при каждом обороте шпинделя. В этом случае говорят о подаче на 1 (2,3) зуба, в зависимости от разновидности инструмента (фреза одно- , двух- или трехзаходная).
Рекомендуемые значения подачи «на зуб» указываются производителем инструмента. Фрезеровщик по этому пункту режима резания сталкивается с трудностями, если работает с фрезами «made in China» или какого-то сомнительного (неизвестного) происхождения. В большинстве случаев можно ориентироваться на диапазон подачи (мм) 0,1 – 0,25. Такой режим подходит практически для всех распространенных материалов, подвергающихся обработке фрезерованием. В процессе реза станет понятно, достаточно или несколько «прибавить» (но не раньше, чем после 1-го захода). А вот менее 0,1 пробовать не стоит, разве только при выполнении ювелирной работы с помощью микрофрез.
Рекомендация
Начинать фрезерование следует с минимальной подачи – 0,1. В процессе станет понятно, насколько податлив обрабатываемый материал перед конкретной фрезой. Это исключит вероятность слома режущей кромки (зуба) и позволит поставить возможностям станка и инструмента точный «диагноз», особенно если это «чужое» оборудование.
Полезные советы
- Превышение значения оптимальной подачи чревато повышением температуры в рабочей области, образованием толстой стружки и быстрой поломкой фрезы. Для инструмента диаметром свыше 3 мм начинать следует с 0,15, не более
- Если скорость фрезерования детали повысить за счет оптимального использования возможностей оборудования не получается, можно попробовать установить фрезу двухзаходную.
- При выборе инструмента нужно учитывать, что увеличение длины режущей части приводит к снижению подачи и увеличению вибраций.
- Не следует стремиться повысить скорость обработки за счет замены фрезы на аналогичную, но с большим количеством зубьев. Стружка от такого инструмента отводится хуже, поэтому часто приводит к тому, что качество фрезерования резко снижается. В некоторых случаях, при полной забивке канавок, фреза начинает работать «вхолостую». Толку от такой замены никакого.
Вывод
Качественного фрезерования можно добиться только опытным путем. Конкретные станок + инструмент + практический опыт, навыки. Поэтому не стоит слепо доверять даже табличным данным. Например, в них не учитывается степень износа фрезы, с которой предстоит работать. Не нужно бояться экспериментировать, но начинать всегда следует с минимального значения параметров. Когда мастер «почувствует» и станок, и фрезу, и обрабатываемый материал, он сам определит, в каком режиме стоит работать.
ismith.ru
Фреза дисковая по металлу: ГОСТ, типы, выбор, назначение
Непривычной формы режущий инструмент – фреза дисковая широко используется в металлообработке. Отрезные пилы малого диаметра ставят на болгарки и используют для раскроя металлического проката, труб, пластика. На производстве дисковыми фрезами раскраивают прокат на заготовки, прорезают пазы и шлицы. Огромные пилы диаметром более 1200 мм устанавливают в конце прокатных станов. Вращаясь с огромной скоростью, они отрезают в нужный размер трубы, слябы, профильный прокат, без остановки валков.
Особенности конструкции
На фрезерном станке для работы пользуются в основном отрезными и прорезными фрезами дисковыми по металлу ГОСТ 2679-93. Они представляют собой тонкий диск с зубьями по кромке – наружному диаметру. Изготавливаются их высоколегированных сталей инструментальной группы. Основные элементы фрезы:
- ступица с посадочным отверстием;
- диск;
- зубья.
По толщине ступица одинаковая с диском или больше него в пределах 0,2 мм. Она имеет посадочное отверстие со шлицем или без него. Устанавливается инструмент на оправку, закрепленную на шпинделе станка. Фиксируется шайбой и гайкой. Для дисковых пил диаметром более 200 мм стандартом предусмотрены поводковые отверстия. Они сверлятся на втулке в количестве 4 штук.
По назначению дисковые фрезы делятся на 2 класса:
- отрезные – для выполнения отрезных и прорезных работ;
- прорезные – нарезка шлицев на валах, прорезка пазов.
Одной их основных характеристик, влияющих на чистоту резания и производительность, является тип инструмента – размер зуба: мелкий, средний и крупный.
Сами зубья могут быть цельными, нарезанными по краю диска, и вставными. Заточка производится:
- прямая, по режущей кромке;
- по 3 рабочим сторонам – торцевой и боковым;
- с затыловкой – режущая кромка и тыльная сторона зуба.
Способ заточки и форма зуба определяются назначением инструмента, твердостью и вязкостью металла, который обрабатывается, производительностью.
Отрезные
У круглой пилы по металлу – фрезы дисковой отрезной, зуб вырезается с тела инструмента. Размер наружного диаметра по ГОСТ 2679-93 от 20 мм до 315 мм. Отверстие может иметь шпоночный паз. Ступица в большинстве случаев отсутствует. Перепада по толщине отрезная фреза не имеет.
Скачать ГОСТ 2679-93
Профиль стружечных канавок зависит от типа дисковой фрезы и количества зубьев. Угол выдерживается 60 градусов, изменяется глубина канавки и угол заточки. На среднем и мелком зубе делается затыловка под углом до 20 градусов относительно касательной линии наружного диаметра диска. Чем мельче зуб, тем меньше подача инструмента, поскольку стружка должна истекать из паза и не забивать канавки.
На фрезах 3-го типа – с крупным зубом производится заточка боковых поверхностей режущей кромки. В сочетании с глубоким профилем канавок, это позволяет резать быстро, с большой подачей.
При работе дисковой пилы в зону реза подается охлаждающая жидкость. Она способствует истеканию стружки и не допускает перегрева, возникающего при срезании металла фрезой и трении металлических поверхностей.
Прорезные
Шпоночные пазы и канавки имеют определенную конфигурацию и требуют высокой точности и чистоты обработки. У фрезы дисковой прорезной эти параметры обеспечиваются формой зуба и заточкой по трем поверхностям. Режущая кромка по бокам образует прямой угол.
Прорезные дисковые фрезы имеют хорошо выраженную ступицу, выступающую над телом фрезы на 0,2–0,6 мм.
Установочное отверстие со шпоночным пазом, что позволяет резать с большим усилием, избегая проворачивания инструмента на оправке.
Зубья наборные – пластины вставляются в пазы в теле фрезы и припаиваются. На инструменте большого диаметра возможно крепление клиньями. Сборка производится на специальной инструментальной плите, обеспечивающей большую точность по плоскости наружных режущих кромок. После набора пластин и их крепления, дисковая фреза проверяется на торцевое и радиальное биение. Для этого она надевается на оправку и вращается. К торцу и радиусу поочередно подводится индикаторная головка.
Назначение инструмента
Фрезы отрезные прорезные, выпускаемые по ГОСТ 2679-93 предназначены для обработки чугунных и стальных заготовок и деталей. Они выполняют отрезку, подрезку, фрезерование канавок и шлицевых пазов на наружных поверхностях. Дисковую фрезу по металлу используют при различных операциях:
- отрезка мерных заготовок из проката;
- обрезка литейных припусков и прибылей на малых деталях;
- прорезка канавок для фиксации деталей;
- фрезеровка шпоночных и шлицевых пазов.
Круглые гладкие оси в цепи конвейера не выпадают из своих втулок только благодаря тому, что в узкую прорезь, сделанную дисковой пилой, вставлена пластина.
Пазы по торцу корончатой гайки имеют переменное сечение. Их стороны образованы лучами от центра радиуса. Поэтому они вырезаются за 2 прохода, сначала по касательной одной стороны, затем дорезается в размер второй торец выборки короны.
Прорезка шлицов осуществляется прямоугольными зубьями с высокой точностью размера по H6 и H7. Ширина и глубина шлица нормализована, и инструмент изготавливается соответствующего размера и конфигурации.
Нюансы подбора оборудования
Чугун обрабатывается на малых оборотах режущего инструмента с небольшой подачей. Стружка образуется мелкая, как пыль. Для работы с таким материалом подойдут фрезы дисковые отрезные по металлу ГОСТ 2678-93. При прорезке пазов по классу точности от 4 и выше, используют прорезной инструмент.
Выборка пазов в деталях типа вал из углеродистых и высоколегированных сталей осуществляется на фрезерных и зуборезных станках фрезами дисковыми с напайными пластинами соответствующей конфигурации.
Инструмент может применяться на двухстоечных горизонтально-фрезерных станках, если надо сделать канавки на боку большой детали. Область использования дисков с зубьями широкая.
Если вы нашли ошибку, пожалуйста, выделите фрагмент текста и нажмите Ctrl+Enter.
stankiexpert.ru
Режимы резания при фрезеровании – подбор элементов + Видео
От правильности выбора режимов резания при обработке металлических изделий на фрезерных станках зависит качество производимых работ. По этой причине аналитический расчет таких режимов должен осуществляться максимально грамотно и качественно.
1 Оптимальный режим резания – что под ним понимают?
При фрезеровании обработка деталей по своей сути намного сложнее, чем при точении. Связано это с тем, что любой зуб фрезерного инструмента при каждом обороте фрезы сначала входит, а затем выходит из контакта с обрабатываемым изделием. Причем процесс его входа в контакт сопровождается ударом достаточно ощутимой силы. Кроме того, с детали при фрезеровании снимается прерывистая стружка, толщина которой не является постоянной (при точении сечение стружки всегда имеет один и тот же показатель).
По указанным причинам оператору необходимо очень ответственно выполнять расчет режимов резания, чтобы добиться максимальной производительности фрезерного агрегата на самых выгодных условиях его функционирования с учетом мощности оборудования.
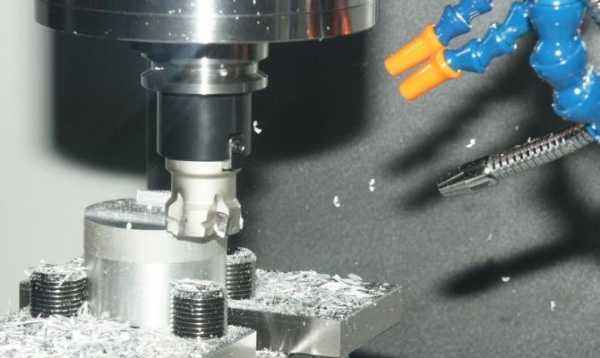
Фрезерная обработка детали
Рекомендуем ознакомиться
Под такими условиями понимают режимы резания, обеспечивающие оптимальное сочетание подачи при фрезеровании, скорости и силы процесса, глубины срезаемого металлического слоя с целью получения заданной чистоты и точности обработки при минимальных затратах на нее.
На любом металлообрабатывающем предприятии имеются стандартные нормативы, в которых даются четкие рекомендации, облегчающие выбор варианта резки различных заготовок. С их помощью можно разрабатывать операционные карты и непосредственно технологический процесс, в который включаются все элементы фрезерования. Но многие параметры, указанные в таких нормативах, не подходят для случаев, когда используется новое оборудование и современный режущий инструмент. В подобных ситуациях оператору приходится самостоятельно производить расчет режимов обработки. Далее мы опишем их основные элементы.
2 Материал и геометрия рабочего инструмента
Материал, из которого сделана фреза, напрямую влияет на возможности и качество режущих операций. Наиболее эффективным инструментом признаются фрезы из быстрорежущей стали и резцы с пластинками из твердых сплавов. Их используют в настоящее время для большинства фрезерных операций, но при условии, что технический потенциал станков (показатель мощности их двигателя, скорость вращения шпинделя и так далее) позволяет работать с такими приспособлениями.
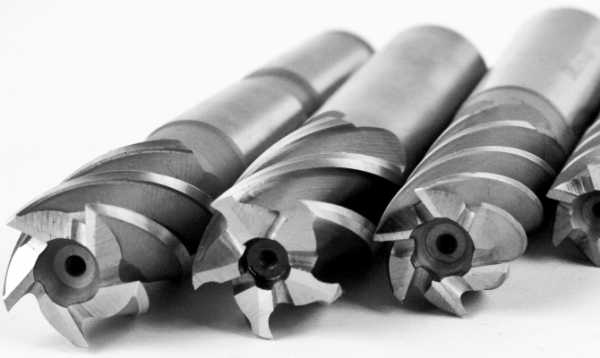
Фрезы из быстрорежущей стали
Некоторые агрегаты старых моделей просто-напросто не могут применять твердосплавный и быстрорежущий инструмент. Тогда на них работают обычными концевыми и иными фрезами. Если же изделие после фрезерования должно иметь высокую точность и чистоту поверхности, и при этом скорость выполнения процедуры не имеет большого значения, лучше использовать приспособления из обычных легированных и углеродистых сталей.
Геометрия режущей части инструмента также влияет на выбор конкретного режима обработки детали. Форму и размеры, которые имеет зуб фрезы, задние и передние ее углы, параметры переходной кромки и углов подбирают из специальных таблиц. В них даются сведения о том, какие размеры обязан иметь зуб и все указанные углы при работе с заготовками, сделанными из различных материалов (легированные, жаропрочные, углеродистые стали, сплавы на основе меди, чугун). При использовании быстрорежущего инструмента все нужные параметры берутся из другой таблицы.
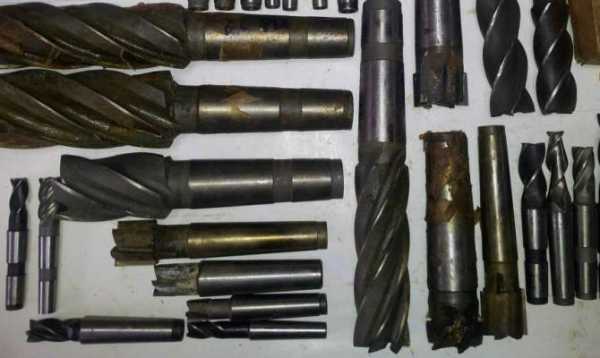
Разные виды инструмента
Современные комбинаты по производству фрез в большинстве случаев поставляют их с четко обозначенными геометрическими размерами, которые оговорены в соответствующих Госстандартах. Каким-либо образом изменить геометрию такого инструмента фрезеровщик не может, поэтому ему требуется правильно сделать выбор нужного ему приспособления (например, торцевой фрезы) из набора имеющихся рабочих приспособлений. Особых проблем при этом у опытного специалиста не возникает, так как он может воспользоваться таблицами с рекомендованными геометрическими величинами фрезерного инструмента.
3 Глубина и ширина фрезерной обработки
Для рационального фрезерования любых изделий указанные параметры имеют огромное значение. Глубина (иными словами – толщина срезаемого слоя) представляет собой дистанцию между обработанной и обрабатываемой поверхностями. Величина срезаемого слоя обычно подбирается максимально большой, всегда стараются делать всего один проход инструмента с целью получения заданного результата фрезерования.
Если же поверхность готовой детали должна иметь повышенную чистоту и точность, следует осуществлять операцию в два прохода – черновой, а затем чистовой. Иногда величина срезаемого слоя высока и даже два прохода не позволяют качественно выполнить операцию. В данном случае требуемая глубина достигается посредством выполнения двух черновых проходов.
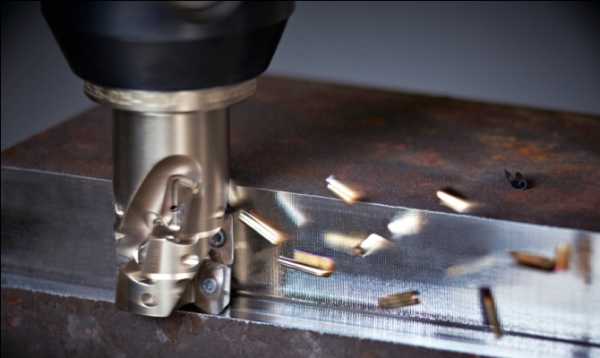
Осуществление чернового прохода
Кроме того, нужной толщины срезаемого слоя не всегда удается добиться за один проход на старых фрезерных агрегатах. Их силы (мощности электрооборудования) просто-напросто не хватает. В подобных ситуациях также рекомендуется делать две черновые процедуры. Под шириной фрезерования понимают ширину обрабатываемого изделия. Если на станке фрезеруется сразу несколько деталей, которые крепятся в зажимном механизме параллельно друг другу, учитывается их общая ширина.
Величину заготовок оператор узнает из рабочего чертежа, прилагаемого к каждому изделию, которое ему нужно обработать. Ширина и глубина, как элементы фрезерования, определяются достаточно легко даже неопытными рабочими. Но здесь стоит помнить, что показатель срезаемого слоя при работе с отливками и поковками из стали и чугуна, на поверхности которых имеются загрязнения, литейная корка или окалина, берется больше величины загрязненного слоя.
Если не прислушиваться к этому совету, зуб инструмента будет скользить по загрязненной поверхности и оставлять на ней дефекты в виде черновин. Необходимый показатель срезаемого слоя будет достигнут и в этом случае, но режущая кромка фрезы быстро придет в негодность. Да и затраты силы (мощности) оборудования потребуются значительные.
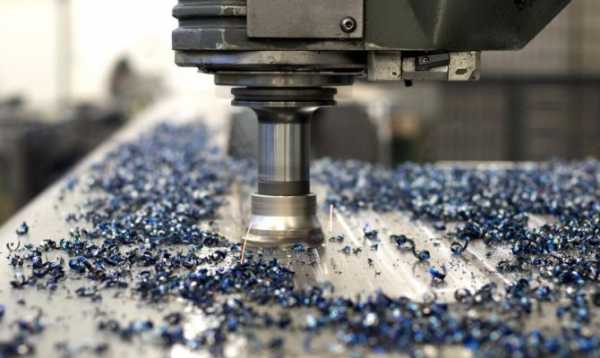
Срезание загрязненного слоя
Стандартные рекомендации по величине срезаемого слоя:
- 0,5–1 мм – чистовая обработка;
- 5–7 мм – черновая обработка по чугунному и стальному литью;
- 3–5 мм – черновое фрезерование деталей из сталей разных марок.
Соблюдение данных показателей срезаемого слоя обычно гарантирует высокое качество обработки заготовок на станках любой мощности.
4 Выбор диаметра инструмента
Показатель срезаемого слоя, а также ширина обработки обуславливают выбор диаметра рабочего приспособления. Подбор сечения фрезы для резания производится по трем таблицам для разных видов инструмента:
- дискового;
- торцового;
- цилиндрического.
Производительность фрезерной обработки зависит от грамотного подбора сечения фрезы, так как диаметр инструмента влияет на величину среза. Она будет при идентичной глубине фрезерования и подаче приспособления тем меньше, чем большее сечение имеет фреза. Производя расчет режимов обработки, это всегда нужно принимать во внимание.
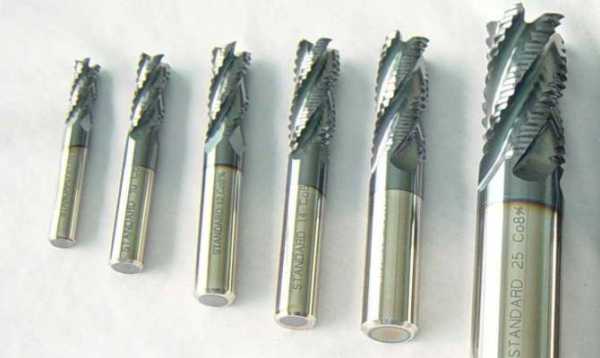
Подбор диаметра фрезы
Отметим, что оператору станка проще работать со срезами большой толщины (чем меньше глубина резания, тем выше удельное давление, а значит, необходимо затрачивать больше силы для обработки). По этой причине при любой возможности он должен подбирать фрезу с минимальным диаметром. Сечение рабочего инструмента также влияет на расстояние, которое преодолевает фреза при одном проходе. Данный показатель называют величиной пути. Формула для его расчета учитывает величины перебега и врезания инструмента, а также непосредственно длину обрабатываемой детали.
Показатель перебега чаще всего равняется 2–5 миллиметрам. С целью снижения холостого хода фрезерного агрегата (по сути – для уменьшения величины перебега) нужно брать фрезы малого сечения. Расчет показателя врезания осуществляется по формуле, учитывающей глубину обработки детали на конкретном станке определенной мощности. Для большинства фрез любых типов готовые значения пути врезания даются в таблицах. Найти в них эти элементы несложно.
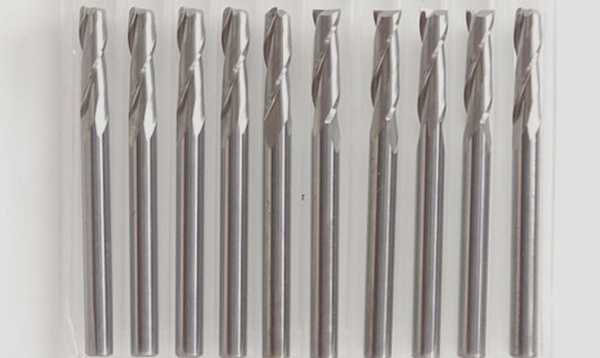
Инструмент малого сечения
Еще одной величиной, на которую влияет сечение инструмента, является крутящий момент определенной силы. Шпинделю агрегата следует сообщать меньший момент при малом диаметре фрезы, увеличивая его при повышении сечения приспособления для резания.
Учитывая все сказанное, может показаться, что целесообразнее всего производить выбор фрезы с малым сечением. Но это не так. Проблема заключается в следующем: со снижением диаметра инструмента для него необходимо подбирать оправку с малой жесткостью (так как фреза будет тонкой). А это ведет к потребности снижать величину срезаемой стружки с детали, то есть к необходимости уменьшать силы давления на оправку. Эффективность режима фрезерования при этом, как вы сами понимаете, снижается.
5 Расчет подачи фрезы и его особенности
При чистовом фрезеровании подача зависит от того, какой чистотой должна будет характеризоваться обработанная поверхность изделия, при черновом – от следующих факторов:
- показатель жесткости схемы “деталь/фреза/станок”;
- материал, из которого изготовлена деталь;
- углы заточки рабочего инструмента;
- величина мощности (силы) привода фрезерного агрегата;
- материал инструмента для резания.
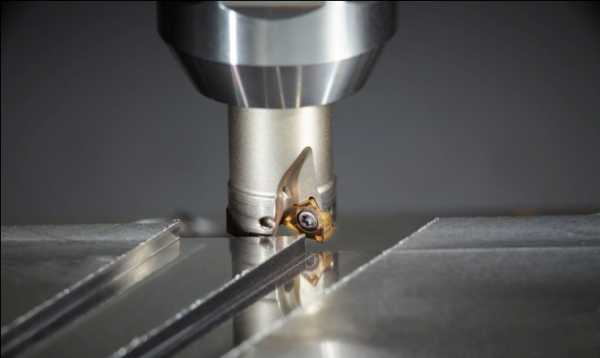
Выбор подачи для обработки поверхности
Главным первоначальным показателем, по которому выполняется выбор подачи для черновой обработки, считается величина S(зуб). Она зависит от варианта монтажа (по отношению к детали, подвергаемой обработке) режущего инструмента, который определяет:
- толщину стружки;
- параметр угла, под которым зуб начинает взаимодействовать с заготовкой;
- величину угла, при которой зуб фрезы выходит из детали после ее обработки.
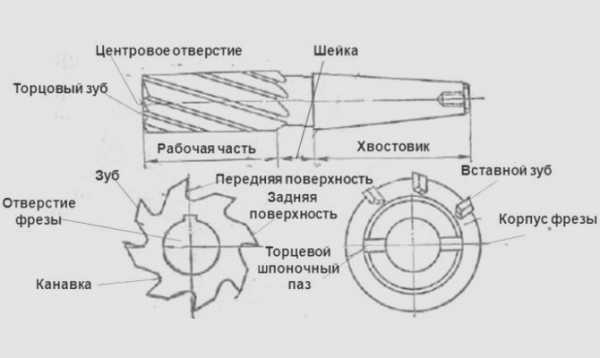
Элементы фрезы
Показатель S(зуб), как и иные элементы фрезерной обработки металлических заготовок, важен для правильного расчета режимов резания. Вручную его никто не высчитывает. Обычно пользуются стандартными таблицами, составленными для разных видов рабочего инструмента.
Выбор подачи при чистовой обработке также производится по табличным данным. Здесь есть один нюанс. На каждый зуб инструмента при чистовой обработке приходится очень малая величина подачи. Поэтому в таблицах даются значения на полный оборот инструмента, а не на один его зуб.
6 Как выполнить расчет скорости резания?
Скорость фрезерования определяется по специальным нормативам, включающим в себя множество карт для разных типов фрез и обрабатываемых материалов (для стали, алюминия и пр.). В таких картах учитываются мощности станков и другие их технические показатели. Выбрать нужную скорость обработки за счет этого достаточно просто.
Обратите внимание – стандартные таблицы для установления скорости содержат информацию для условий фрезерования одним инструментом при определенном уровне стойкости фрезы. Если стойкость инструмента отличается от табличного стандартного показателя, расчет скорости осуществляют с учетом поправочных коэффициентов. Последние созданы на основании следующих данных:
- для торцового инструмента – ширина обработки;
- свойства (механические) фрезеруемой заготовки;
- величина основного угла фрезы в плане;
- отсутствие либо наличие на детали окалины.
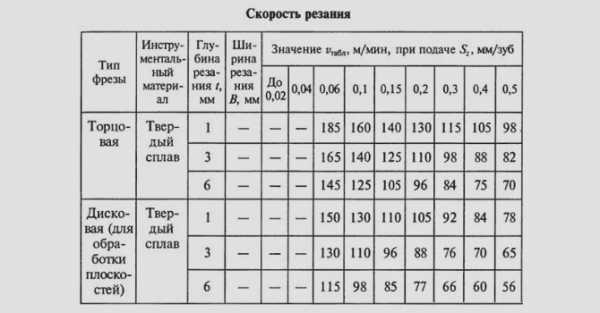
Таблица для расчета скорости резания
В описываемых нормативах для определения скорости указываются такие элементы – минутная подача и количество оборотов. Кинематика, показатели силы и технических возможностей шпинделя конкретного оборудования для фрезерования нередко отличаются от табличных данных. В подобных ситуациях рабочий на свое усмотрение подбирает рациональную скорость функционирования станка. При этом он обязан сделать выбор таким образом, чтобы фреза не затуплялась преждевременно.
Отдельно отметим, что при фрезеровании заготовок из алюминия рекомендуется назначать высокоскоростные режимы их обработки. Они обеспечивают при малых затратах силы электрооборудования большую глубину резания. Если же работать с деталями из алюминия на медленных скоростях, увеличивается риск выхода фрез из строя, ввиду того, что получающаяся мягкая стружка полностью забивает канавки инструмента.
tutmet.ru
Фреза отрезная по металлу – типы, назначение, ГОСТ
Фреза отрезная по металлу – это режущий инструмент фрезерных станков различного типа используемые для работы с деталями, изготовленными из марок сталей со средними показателями твердости и чугуна. Данная оснастка может быть использована на универсальных станках и оборудовании с ЧПУ, являются разновидностью дисковых фрез.
Конструкция и применение отрезных фрез
В современной металлообработке фреза отрезная, назначение которой в полной мере отражено в её названии, применяется в основном для резки частей заготовок, деления их на части перед последующей обработкой. Также данный инструмент может быть использован для нарезания канавок на деталях.
Отрезная фреза представляет собой инструмент в форме диска с режущими зубьями. Все рабочие кромки зубьев расположены по периферии и, в отличие от других конструкций, они полностью отсутствуют на торцах диска. Диаметр находится в пределах от 50 до 315 мм, толщина диска составляет от 1 до 6 мм.
В зависимости от твердости обрабатываемого материала и требований к чистоте среза подбирается количество зубьев фрезы отрезной, типы инструмента с малым и средним размерами применяются для работы со стальными и чугунными металлами. Для резки заготовок из мягких металлов используются фрезы с большим зубом. Большинство инструмента соответствует классу точности «В». Материалом для изготовления фрез, согласно ГОСТ 2679-93 является сталь инструментальной быстрорежущая марки Р18 или Р6М5. При выборе инструмента необходимо обратить внимание на диаметр посадочного места и наличие шпоночного паза.
Особенности выбора и работы отрезной фрезой
Приведем основные рекомендации по подбору и применению фрез отрезных по металлу:
- Чистота полученного среза и скорость зависят от количества зубцов на фрезе. Чем больше зубьев, тем чище срез.
- Фрезы с большим количеством зубьев (от 80 и более) рекомендуются для чистовой обработки. При использовании данного инструмента затруднен отвод стружки и увеличивается нагрузка на оборудование. Поэтому для первичной черновой нарезки рекомендуются фрезы с малым количеством зуба (10-40 шт.) после которых необходима дополнительная зачистка торца.
- Инструмент со средним количеством зубьев (40-80 шт.) является наиболее универсальным и подходит для многих операций.
- Для работы с заготовками из металла прочностью от 500 до 800 рекомендуются фрезы из стали Р6М5 благодаря наличию в составе молибдена. Для заготовок большей твердости желательно использовать фрезы с содержанием кобальта.
- Для работы с нержавеющими марками стали применяются фрезы с напайками из карбида вольфрама, которые нельзя перетачивать.
- При работе скорость реза необходимо устанавливать в соответствии со справочной литературой. Для быстрорежущих сталей она составляет порядка 40-60 м/мин.
- Для получения максимально чистого торца рекомендуется работать с малыми подачами.
Действующие стандарты
Основной действующий стандарт на фрезу отрезную ГОСТ 2679-93 (ИСО 2296-72). В нем определены размеры и другие технические условия инструмента.
mekkain.ru
Режимы резания при фрезеровании: таблица, элементы, выбор режимов
Поверхностная обработка заготовок методом фрезерования может проводиться исключительно после разработки технологической карты, в которой указываются основные режимы обработки. Подобной работой, как правило, занимается специалист, прошедший специальную подготовку. Режимы резания при фрезеровании могут зависеть от самых различных показателей, к примеру, типа материала и используемого инструмента. Основные показатели на фрезерном станке могут устанавливаться вручную, также проводится указание показателей на блоке числового программного управления. Особое внимание заслуживает резьбофрезерование, так как получаемые изделия характеризуются довольно большим количеством различных параметров. Рассмотрим особенности выбора режимов резания при фрезеровании подробно.
Скорость резания
Наиболее важным режимом при фрезеровании можно назвать скорость резания. Он определяет то, за какой период времени будет снят определенный слой материала с поверхности. На большинстве станков устанавливается постоянная скорость резания. При выборе подходящего показателя учитывается тип материала заготовки:
- При работе с нержавейкой скорость резания 45-95 м/мин. За счет добавления в состав различных химических элементов твердость и другие показатели меняются, снижается степень обрабатываемости.
- Бронза считается более мягким составом, поэтому подобный режим при фрезеровании может выбираться в диапазоне от 90-150 м/мин. Она применяется при изготовлении самых различных изделий.
- Довольно большое распространение получила латунь. Она применяется при изготовлении запорных элементов и различных клапанов. Мягкость сплава позволяет повысить скорость резания до 130-320 м/мин. Латуни склонны к повышению пластичности при сильном нагреве.
- Алюминиевые сплавы сегодня весьма распространены. При этом встречается несколько вариантов исполнения, которые обладают различными эксплуатационными характеристиками. Именно поэтому режим фрезерования варьирует в пределе от 200 до 420 м/мин. Стоит учитывать, что алюминий относится к сплавам с низкой температурой плавления. Именно поэтому при высокой скорости обработки есть вероятность существенного повышения показателя пластичности.
Встречается довольно большое количество таблиц, которые применяются для определения основных режимов работы. Формула для определения оборотов скорости резания выглядит следующим образом: n=1000 V/D, где учитывается рекомендуемая скорость резания и диаметр применяемой фрезы. Подобная формула позволяет определить количество оборотов для всех видов обрабатываемых материалов.
Рассматриваемый режим фрезерования измеряется в метрах в минуту режущие части. Стоит учитывать, что специалисты не рекомендуют гонять шпиндель на максимальных оборотах, так как существенно повышается износ и есть вероятность повреждения инструмента. Поэтому полученный результат уменьшается примерно на 10-15%. С учетом этого параметра проводится выбор наиболее подходящего инструмента.
Скорость вращения инструмента определяет следующее:
- Качество получаемой поверхности. Для финишной технологической операции выбирается наибольший параметр. За счет осевого вращения с большим количеством оборотов стружка получается слишком мелкой. Для черновой технологической операции, наоборот, выбираются низкие значения, фреза вращается с меньшей скоростью, и размер стружки увеличивается. За счет быстрого вращения достигается низкий показатель шероховатости поверхности. Современные установки и оснастка позволяют получить поверхность зеркального типа.
- Производительность труда. При наладке производства уделяется внимание и тому, какова производительность применяемого оборудования. Примером можно назвать цех машиностроительного завода, где налаживается массовое производство. Существенное снижение показателя режимов обработки становится причиной уменьшения производительности. Наиболее оптимальный показатель существенно повышает эффективность труда.
- Степень износа устанавливаемого инструмента. Не стоит забывать о том, что при трении режущей кромки об обрабатываемую поверхность происходит ее сильный износ. При сильном изнашивании происходит изменение показателей точности изделия, снижается эффективность труда. Как правило, износ связан с сильным нагревом поверхности. Именно поэтому на производственной линии с высокой производительностью применяется оборудование, способное подавать СОЖ в зону снятия материала.
При этом данный параметр выбирается с учетом других показателей, к примеру, глубины подачи. Поэтому технологическая карта составляется с одновременным выбором всех параметров.
Глубина резания
Другим наиболее важным параметром является глубина фрезерования. Она характеризуется следующими особенностями:
- Глубина врезания выбирается в зависимости от материала заготовки.
- При выборе уделяется внимание тому, проводится черновая или чистовая обработка. При черновой выбирается большая глубина врезания, так как устанавливается меньшая скорость. При чистовой снимается небольшой слой металла за счет установки большой скорости вращения инструмента.
- Ограничивается показатель также конструктивными особенностями инструмента. Это связано с тем, что режущая часть может иметь различные размеры.
Глубина резания во многом определяет производительность оборудования. Кроме этого, подобный показатель в некоторых случаях выбирается в зависимости от того, какую нужно получить поверхность.
Мощность силы резания при фрезеровании зависит от типа применяемой фрезы и вида оборудования. Кроме этого, черновое фрезерование плоской поверхности проводится в несколько проходов в случае, когда нужно снять большой слой материала.
Особым технологическим процессом можно назвать работу по получению пазов. Это связано с тем, что их глубина может быть довольно большой, а образование подобных технологических выемок проводится исключительно после чистовой обработки поверхности. Фрезерование т-образных пазов проводится при применении специального инструмента.
Подача
Понятие подачи напоминает глубину врезания. Подача при фрезеровании, как и при проведении любой другой операции по механической обработке металлических заготовок, считается наиболее важным параметром. Долговечность применяемого инструмента во многом зависит от подачи. К особенностям этой характеристики можно отнести нижеприведенные моменты:
- Какой толщины материал снимается за один проход.
- Производительность применяемого оборудования.
- Возможность проведения черновой или чистовой обработки.
Довольно распространенным понятием можно назвать подачу на зуб. Этот показатель указывается производителем инструмента, зависит от глубины резания и конструктивных особенностей изделия.
Как ранее было отмечено, многие показатели режимом резания связаны между собой. Примером можно назвать скорость резания и подачу:
- При увеличении значения подачи скорость резания снижается. Это связано с тем, что при снятии большого количества металла за один проход существенно повышается осевая нагрузка. Если выбрать высокую скорость и подачу, то инструмент будет быстро изнашиваться или попросту поломается.
- За счет снижения показателя подачи повышается и допустимая скорость обработки. При быстром вращении фрезы возможно существенно повысить качество поверхности. На момент чистового фрезерования выбирается минимальное значение подачи и максимальная скорость, при применении определенного оборудования можно получить практически зеркальную поверхность.
Довольно распространенным значением подачи можно назвать 0,1-0,25. Его вполне достаточно для обработки самых распространенных материалов в различных отраслях промышленности.
Ширина фрезерования
Еще одним параметром, который учитывается при механической обработки заготовок считается ширина фрезерования. Она может варьировать в достаточно большом диапазоне. Ширина выбирается при фрезеровке на станке Have или другом оборудовании. Среди особенностей отметим следующие моменты:
- Ширина фрезерования зависит от диаметра фрезы. Подобные параметры, которые зависят от геометрических особенностей режущей части, не могут регулироваться, учитываются при непосредственном выборе инструмента.
- Ширина фрезерования также оказывает влияние на выбор других параметров. Это связано с тем, что при увеличении значения также увеличивается количество материала, который снимается за один проход.
В некоторых случаях ширина фрезерования позволяет получить требуемую поверхность за один проход. Примером можно назвать случай получения неглубоких канавок. Если проводится резание плоской поверхности большой ширины, то число проходов может несколько отличаться, рассчитывается в зависимости от ширины фрезерования.
Как выбрать режим на практике?
Как ранее было отмечено, в большинстве случаев технологические карты разработаны специалистом и мастеру остается лишь выбрать подходящий инструмент и задать указанные параметры. Кроме этого, мастер должен учитывать то, в каком состоянии находится оборудование, так как предельные значения могут привести к возникновению поломок. При отсутствии технологической карты приходится проводить выбор режимов фрезерования самостоятельно. Расчет режимов резания при фрезеровании проводится с учетом следующих моментов:
- Типа применяемого оборудования. Примером можно назвать случай резания при фрезеровании на станках ЧПУ, когда могут выбираться более высокие параметры обработки по причине высоких технологических возможностей устройства. На старых станках, которые были введены в эксплуатацию несколько десятков лет назад, выбираются более низкие параметры. На момент определения подходящих параметров уделяется внимание и техническому состоянию оборудования.
- Следующий критерий выбора заключается в типе применяемого инструмента. При изготовлении фрезы могут применяться различные материалы. К примеру, вариант исполнения из быстрорежущей качественной стали подходит для обработки металла с высокой скоростью резания, фреза с тугоплавкими напайками предпочтительно выбирается в случае, когда нужно проводить фрезерование твердого сплава с высоким показателем подачи при фрезеровании. Имеет значение и угол заточки режущей кромки, а также диаметральные размер. К примеру, с увеличением диаметра режущего инструмента снижается подача и скорость резания.
- Тип обрабатываемого материала можно назвать одним из наиболее важных критериев, по которым проводится выбор режима резания. Все сплавы характеризуются определенной твердостью и степенью обрабатываемости. К примеру, при работе с мягкими цветными сплавами могут выбираться более высокие показатели скорости и подачи, в случае с каленной сталью или титаном все параметры снижаются. Немаловажным моментом назовем то, что фреза подбирается не только с учетом режимов резания, но и типа материала, из которого изготовлена заготовка.
- Режим резания выбирается в зависимости от поставленной задачи. Примером можно назвать черновое и чистовое резание. Для черного свойственна большая подача и небольшой показатель скорости обработки, для чистовой все наоборот. Для получения канавок и других технологических отверстий и вовсе показатели подбираются индивидуально.
Как показывает практика, глубина резания в большинстве случаев делится на несколько проходов при черновой обработке, при чистовой он только один. Для различных изделий может применяться таблица режимов, которая существенно упрощает поставленную задачу. Встречаются и специальные калькуляторы, проводящие вычисление требуемых значений в автоматическом режиме по введенным данным.
Выбор режима в зависимости от типа фрезы
Для получения одного и того же изделия могут применяться самые различные виды фрез. Выбор основных режимов фрезерования проводится в зависимости от конструктивных и других особенностей изделия. Режимы резания при фрезеровании дисковыми фрезами или другими вариантами исполнения выбираются в зависимости от нижеприведенных моментов:
- Жесткости применяемой системы. Примером можно назвать особенности станка и различной оснастки. Новое оборудование характеризуется повышенной жесткостью, за счет чего появляется возможность применения более высоких параметров обработки. На старых станках жесткость применяемой системы снижается.
- Уделяется внимание и процессу охлаждения. Довольно большое количество оборудования предусматривает подачу СОЖ в зону обработки. За счет подобного вещества существенно снижается температура режущей кромки. СОЖ должна подаваться в зону снятия материала постоянно. При этом также удаляется и образующаяся стружка, что существенно повышает качество резания.
- Стратегия обработки также имеет значение. Примером можно назвать то, что получение одной и той же поверхности может проводится при чередовании различных технологических операций.
- Высота слоя, который может сниматься за один проход инструмента. Ограничение может зависеть от размера инструмента и многих других геометрических особенностей.
- Размер обрабатываемых заготовок. Для больших заготовок требуется инструмент с износостойкими свойствами, который при определенных режимах резания сможет не нагреваться.
Учет всех этих параметров позволяет подобрать наиболее подходящие параметры фрезерования. При этом учитывается распределение припуска при фрезеровании сферическими фрезами, а также особенности обработки концевой фрезой.
Классификация рассматриваемого инструмента проводится по достаточно большому количеству признаков. Основным можно назвать тип применяемого материала при изготовлении режущей кромки. К примеру, фреза ВК8 предназначена для работы с заготовками из твердых сплавов и закаленной стали. Рекомендуется применять подобный вариант исполнения при невысокой скорости резания и достаточной подаче. В тоже время скоростные фрезы могут применяться для обработки с высоким показателем резания.
Как правило, выбор проводится с учетом распространенных таблиц. Основными свойствами можно назвать:
- Скорость резания.
- Тип обрабатываемого материала.
- Тип фрезы.
- Частота оборотов.
- Подача.
- Тип проведенной работы.
- Рекомендуемая подача на зуб в зависимости от диаметра фрезы.
Использование нормативной документации позволяет подобрать наиболее подходящие режимы. Как ранее было отмечено, разрабатывать технологический процесс должен исключительно специалист. Допущенные ошибки могут привести к поломке инструмента, снижению качества поверхности заготовки и допущению погрешностей в инструментах, в некоторых случаях, поломке оборудования. Именно поэтому нужно уделять много внимания выбору наиболее подходящего режима резания.
Выбор режима в зависимости от материала
Все материалы характеризуются определенными эксплуатационными характеристиками, которые также должны учитываться. Примером можно назвать фрезерование бронзы, которое проводится при скорости резания от 90 до 150 м/мин. В зависимости от этого значения выбирается величина подачи. Сталь ПШ15 и изделия из нержавейки обрабатываются при применении других показателей.
При рассмотрении типа обрабатываемого материала уделяется внимание также нижеприведенным моментам:
- Твердости. Наиболее важной характеристикой материалов можно назвать именно твердость. Она может варьировать в большом диапазоне. Слишком большая твердость делает деталь прочной и износостойкой, но при этом усложняется процесс обработки.
- Степени обрабатываемости. Все материалы характеризуются определенной степенью обрабатываемостью, зависящая также от пластичности и других показателей.
- Применение технологии улучшения свойств.
Довольно распространенным примером можно назвать проведение закалки. Подобная технология предусматривает нагрев материала с последующим охлаждением, после чего показатель твердости существенно повышается. Также часто проводится ковка, отпуск и другие процедуры изменения химического состава поверхностного слоя.
В заключение отметим, что сегодня можно встретить просто огромное количество различных технологических карт, которые достаточно скачать и использовать для получения требуемых деталей. При их рассмотрении уделяется внимание типу материала заготовки, виду инструмента, рекомендуемому оборудованию. Самостоятельно разработать режимы резания достаточно сложно, при этом нужно делать предварительную проверку выбранных параметров. В противном случае может пострадать как инструмент, так и применяемое оборудование.
Если вы нашли ошибку, пожалуйста, выделите фрагмент текста и нажмите Ctrl+Enter.
stankiexpert.ru
Концевые фрезы – конструкция и технические особенности
Это статья-справочник. Здесь перечислены основные понятия и определения конструкции концевых фрез, а также технические особенности.
Конструкция концевых фрез
Режущая кромка прямого типа (прямолинейная режущая кромка) –режущая кромка, представляющая собой прямую линию, проходящую под углом к оси фрезы. В отличие от режущей кромки спирального или винтового типа, обработанная поверхность, образуемая прямолинейной режущей кромкой, не является плоской.
Осевое биение – разница между минимальным и максимальным показаниями индикатора (микрометра), установленного по наружному диаметру фрезы на её режущей части, при её вращении.
A — диаметр фрезы
B — диаметр хвостовика
C — Длина режущей части
D — Общая длина
Подточка углов — короткий скошенный участок, расположенный в месте схождения торцевой и цилиндрической поверхностей фрезы. Выполняется для усиления фрезы и во избежание излома выступающих острых углов режущих кромок.
Стружколомы – выступы и впадины особой формы на передней поверхности, заставляющие стружку свиваться и обламываться.
Расщепители стружки – выемки в виде желобков и зазубрин, расположенные по периферии концевой фрезы кукурузного типа, выполненные с целью получения более узкой стружки. Применимы для черновой обработки.
Диаметр сердцевины – диаметр цилиндра (или конуса, для конусных фрез), образуемого касательными в точках наибольшей глубины стружкоотводящих канавок.
Подрезка – место входа канавочной фрезы или шлифовальной головки при проточке канавок концевой фрезы во время её изготовления.
Режущая кромка – непосредственно режущая часть зуба. Представляет собой пересечение двух хорошо обработанных поверхностей под заданным углом, обычно, не превышающим 90 градусов.
Угол наклона режущей кромки – угол между осью фрезы и режущей кромкой.
Фреза с переменным окружным шагом зуба – фреза, сконструированная особым образом с целью уменьшения вибрации и дребезга в процессе резания. Эффект основан на том, что при таком расположении зубьев не происходит наложения гармоник колебаний зубьев друг на друга.
Угол в плане (иногда угол входа, угол атаки) – чем ближе этот угол к 90 градусам, тем выше ударная нагрузка на инструмент.
Радиус закругления в основании стружечной канавки — радиус там же, где измеряется диаметр сердцевины.
Стружечная канавка – канал-впадина в теле фрезы в промежутке между зубьями, обеспечивающий вывод стружки наружу и используемый для заточки инструмента. Число стружечных канавок напрямую соответствует числу зубьев, что, в свою очередь, определяет скорость подачи.
Длина стружечной канавки – длина канавки или проточки. Часто неверно используется в значении «длина режущей части».
Хвостовик – часть фрезы, служащая для зажима в патроне станка и передающая режущей части фрезы вращательное движение от шпинделя.
Прямой хвостовик – цилиндрический хвостовик с канавками или проточками или без них. Очень распространенное решение у твердосплавных концевых фрез.
Хвостовик Велдона (Weldon) – промышленное название особого типа хвостовика с плоской лыской, которая служит для предотвращения проскальзывания хвостовика инструмента в зажимном патроне.
Зуб – выпуклость на теле концевой фрезы с режущей кромкой на ней.
Передняя поверхность – поверхность зуба фрезы, непосредственно находящаяся в контакте с заготовкой.
Отступление (прим. перев.)
Существует передняя поверхность зуба (которой фреза врезается в заготовку) и задняя поверхность (противоположная ей). В месте соединения передней и задней поверхности выполняется площадка, параллельная обработанной поверхности (поверхность после прохода фрезы). После площадки для уменьшения трения заднюю поверхность «поднимают» от заготовки, чтобы они не тёрлись друг об друга, вызывая нагрев. Задних поверхностей может быть до 3 шт (в российской практике – обычно 1 или 2). Каждая из них немного скошена одна относительно другой. При заточке фрезы, если задняя поверхность плоская – фрезу точат по задней поверхности, если же затылованная (не одна-две-три плоскости под углом одна к другой, как у острозаточенной, а плавное скругление – спираль Архимеда) – тогда её точат со стороны передней поверхности.
Своеобразная «Площадка» с аналогичными функциями есть и на боковой поверхности фрез и сверл (они схожи конструктивно) – но она у нас называется «Ленточка».
Заточка инструмента (видео)
На видео производится заточка инструмента. Первой обрабатывается торцевая поверхность, в конце – боковая. Сначала выполняется площадка на всех четырех зубцах, далее делается первичная задняя поверхность (срезается задняя часть зуба вместе с площадкой), далее делаются подточки, после чего на боковой поверхности делаются ленточки.
http://www.s-t-group.com/catalog/yg_1_teh_ii.pdf — здесь также очень хорошо расписана подобная техническая информация.
Технические особенности концевых фрез
Обратный конус – режущая часть фрезы выполнена в виде обратного конуса, когда диаметр рабочей части у хвостовика меньше её диаметра у кончика фрезы.
Обнижение, падение профиля – пустое пространство между фрезой и заготовкой, находящееся со стороны спинки зуба.
Угол обнижения/задний угол – угол между задней поверхностью и линией, являющейся продолжением режущей кромки.
- Первичный задний угол – (обычно 5-9 градусов) – угол между первичной задней поверхностью и режущей кромкой.
- Вторичный задний угол – (обычно 14-17 градусов) – по отношению к продолжению режущей кромки.
- Третичный задний угол (опционально) – угол наклона третичной задней поверхности (на этот раз – по отношению ко вторичной поверхности, а не к режущей кромке)
Поднутрение – впадина в торцевой поверхности фрезы, образованная благодаря скосу его поверхностей внутрь. Степень вогнутости зависит от угла поднутрения торцовой режущей кромки.
КОНВЕКС — проекция наружного радиуса зубьев фрезы с радиусной заточкой
Угол поднутрения торцовой режущей кромки – угол, образованный режущей кромкой и плоскостью, перпендикулярной оси фрезы. Целью поднутрения является гарантированное получение плоской поверхности в результате обработки фрезой.
Подточка (перемычки) – вспомогательные прорези в теле фрезы, облегчающие выход стружки. То же, что и «канавки» но не сбоку фрезы, а в торце.
Винтовая заточка фрезы – режущая кромка или канавка равномерно вьющаяся вокруг цилиндрической поверхности фрезы в осевом направлении. Нормальное направление вращения спирали – правое.
Угол наклона винтовой канавки – угол, образованный линией, касательной к спирали, и осевой плоскостью.
Радиус стружечной канавки – термин, используемый чтобы подчеркнуть вогнутость и кривизну передней поверхности зуба.
Площадка (ленточка) – узкая плоскость непосредственно за режущей кромкой. На торцевой части – площадка, на цилиндрической — ленточка.
Цилиндрическая (А) – узкий кусочек ленточки на цилиндрической части фрезы, непосредственно примыкающий к режущей кромке, не имеющей радиального скоса.
Скошенная (B) – узкий кусочек ленточки на цилиндрической части фрезы, непосредственно примыкающий к режущей кромке с радиальным скосом.
Глубина резания – длина цилиндрической режущей части, предназначенной для резания (имеющей все необходимые элементы – стружечную канавку, режущую кромку, площадку, переднюю и заднюю поверхности).
Радиальный передний угол – угол, образуемый радиусом, проведенным по нормали к оси фрезы и радиальной передней поверхностью зуба.
Угол – угловое соотношение между передней поверхностью зуба или линией, касательной к передней поверхности зуба, проведенной через заданную точку и контрольной плоскостью.
Угол наклона канавки – угол, образованный плоскостью, проходящей через ось фрезы и линией, совпадающей или касающейся передней поверхности зуба.
Эффективный угол – угол, наиболее сильно влияющий на образование стружки; представляющий собой перпендикуляр к режущей кромке.
Винтовой угол – в большинстве случаев означает то же самое, что и термин «угол наклона винтовой канавки». Означает отклонение передней поверхности зуба по отношению к плоскости, проходящей через ось фрезы.
Отрицательный передний угол – у инструмента с таким углом первоначальный контакт заготовки и зуба инструмента происходит в точке, не находящейся на режущей кромке.
Положительный передний угол – у инструмента с таким углом первоначальный контакт заготовки и инструмента происходит по линии режущей кромки.
Главный задний угол (осевой) – угол между линией, проходящей касательно или совпадающей с задней поверхностью зуба и плоскостью, перпендикулярной оси фрезы.
Осевая задняя поверхность – выборка (подточка) на тыловой части зуба, размер которой измеряется в осевом направлении, между плоскостью, перпендикулярной оси инструмента, проходящей через режущую кромку и задней поверхностью (подточенной). Предотвращает трение задней поверхности о заготовку и тепловыделение.
Вогнутая задняя поверхность – поверхность, непосредственно за режущей кромкой имеет вогнутую форму. Изготавливается с помощью шлифовального круга, расположенного под углом 90 градусов к оси инструмента.
Выпуклая задняя поверхность – задняя поверхность имеет выпуклую форму (см.ссылку выше). Образуется путем применения I-образного шлифовального круга под углом к оси инструмента.
Подточка углов – необходима только для погружных фрез, а также при переточке инструмента при повреждении или износе углов режущей кромки.
Плоская задняя поверхность – задняя поверхность имеет плоскую форму, на производстве выполняется торцевой частью U-образного шлифовального круга.
Радиальная задняя поверхность – задняя поверхность зуба в радиальном направлении. Может быть измерена индикатором или микрометром в плоскости вращения инструмента по показаниям микрометра на различных углах поворота фрезы.
Тангенциальный главный передний угол – угол, образованный касательной к зубу с вогнутой передней поверхностью зуба, проходящей через режущую кромку, и радиусом, проведенным через ту же точку по плоскости, перпендикулярной оси инструмента.
Источник
Также советуем прочитать:
Нет связанных записей.
Понравилась статья? Поделитесь:
tverdysplav.ru