По отношению к рабочей поверхности шабер устанавливают под углом – , , . . . .
alexxlab | 10.02.2017 | 0 | Вопросы и ответы
Приемы шабрения
ДОМАШНИЙ СЛЕСАРЬ
Подготовленную к шабрению деталь в большинстве случаев закрепляют в тисках; детали среднего веса часто шабрят непосредственно на верстаках без дополнительного крепления или устанавливают в приспособлениях, поверхности тяжелых и громоздких деталей шабрят на месте.
Как правило, шабрение производится в три этапа.
Первый этап — черновое шабрение — начинается с удаления следов инструмента после механической обработки на выступающих частях поверхности, обнаруженных при контроле. Работа производится шабером с широким режущим лезвием (ширина шабера не должна превышать 20—25 мм, так как в противном случае слесарь быстро утомляется и его производительность падает. Длина рабочего хода шабера 15—20 мм: толщина стружки, снимаемой за один проход, 0,01—0,03 мм. Черновое шабрение считается законченным, когда вся пришабриваемая поверхность при нанесении на нее краски покроется крупными пятнами.
На втором этапе — получистовом — производится более точное шабрение. Поверхность обрабатывают шабером шириной не более 12—15 мм при длине рабочего хода 7—12 мм. Толщина снимаемой стружки не превышает 0,005—0,01 мм. После этого перехода число пятен на пришабриваемой поверхности должно быть от 8 до 16 на площади 25 х 25 мм2.
Третий этап — чистовой. На нем осуществляется окончательная отделка поверхностей. Ширина шабера от 5 до 12 мм; шабрение ведется мелким штрихом (длина рабочего хода шабера 3—5 мм). После третьего перехода пришабриваемая поверхность должна иметь на квадрате 25 х 25 мм2 от 20 до 25 пятен. Для получения большей чистоты поверхности следует при обратном ходе несколько приподнимать шабер.
Во время шабрения (каждый раз после удаления шабером покрытых краской мест) поверхность детали очищают щеткой и тщательно вытирают сухой тряпкой. Деталь пришабриваемой прверхностью снова накладывают на окрашенную поверочную плиту, снимают и вновь шабрят образовавшиеся пятна. Так продолжают до тех пор, пока количество пятен на пришабриваемой поверхности не достигнет установленной нормы.
Шабрение плоскостей. При шабрении плоскости шабер, удерживаемый правой рукой за рукоятку, устанавливают под углом 20—30° к пришабриваемой поверхности; левой рукой нажимают на конец шабера вблизи режущей кромки и двигают его вперед (рабочий ход) и назад (холостой ход).
Вначале процесса шабрения приступают к так называемой разбивке больших пятен. Прием осуществляется сильными движениями шабера, соскабливающего стружку с окрашенных мест. Поверхность очищается от стружки и снова проверяется на краску, после чего процесс шабрения повторяется. Когда пятна расположатся на поверхности равномерно, разбивку заканчивают и приступают к увеличению количества пятен, соскабливая все появляющиеся после проверки по плите или линейке окрашенные места. Очевидно, что каждое последующее снятие стружки будет уменьшать высоту неровностей, которые будут делиться на несколько менее высоких выступов; общее число их будет увеличиваться. При этом направление рабочего хода шабера каждый раз изменяется, так что следы шабера от предыдущего прохода пересекаются со следами последующего шабрения под углом примерно 45—90°, а площадки, образуемые штрихами, имеют вид ромбиков или квадратиков.
Для придания пришабриваемой поверхности декоративного вида иногда на ней наносится так называемый «мороз» различной формы — симметрично расположенные клеточки или полоски.
Весьма рациональным следует считать применяемый многими слесарями метод ручного шабрения «на себя». При обычном способе ручное шабрение ведется передвижением шабера обеими руками «от себя». При способе «на себя» шабер берут за среднюю часть (стержень) обеими руками в обхват и устанавливают лезвием к обрабатываемой поверхности под углом 65—75°, а не 20—30°, как при шабрении «от себя»; верхняя же часть шабера, оканчивающаяся деревянной рукояткой, упирается в плечо работающего. Шабер при этом является как бы рычагом с центром вращения в точке соприкосновения шабера с плечом работающего. При таком методе шабрения значительно улучшается качество обработанной поверхности, так как совершенно исключается возможность «дробления» часто наблюдающегося при шабрении «от себя». Это объясняется тем, что вследствие увеличенной длины (до 450—550 мм) шабер при шабрении «на себя» пружинит, благодаря чему лезвие его плавно врезается и металл и также плавно выходит из зоны резания. При шабрении же «от себя» шабер при рабочем ходе обычно сильно врезается в металл, и в конце каждого штриха остаются заусенцы, которые затем приходится удалять дополнительным пришабриванием.
Шабрение плоскостей, расположенных под острыми углами. Примером такой обработки может служить шабрение направляющих типа «ласточкин хвост». В этом случае применяют шаберы, режущая часть которых имеет некоторую кривизну и специальную заточку.
Для правильной обработки направляющих нужно иметь трехгранные линейки, а также «каретку» (ползун) с хорошо пришабренным нижним основанием. С помощью каретки производят шабрение крайних горизонтальных направляющих плоскостей, их окрашивают по нижнему основанию «каретки», на которое нанесена краска. Затем шабрят наклонные направляющие под трехгранную поверочную линейку.
Шабрение плоскостей, сопряженных под острыми или тупыми углами, можно производить, пользуясь поверочными призмами. В данном случае проверка пришабриваемой поверхности на краску производится по скосу призмы, установленной на плите.
Шабрение криволинейных поверхностей. К группе деталей с криволинейными поверхностями, которые слесарю приходится часто шабрить, относятся вкладыши подшипников, втулки, гильзы и т. п. Их шабрят трехгранным шабером и проверяют по валу. Вначале поверочный вал покрывают тонким и равномерным слоем краски и укладывают на нижний вкладыш подшипника. Затем на этот вал накладывают верхний вкладыш и равномерно с угла на угол с помощью гаек затягивают крышку подшипника так, чтобы вал с некоторым усилием можно было повернуть в подшипнике вправо и влево на 2—3 оборота. После этого подшипник разбирают и шабрят окрашенные места вначале нижнего, а затем верхнего вкладыша, перемещая шабер по окружности вкладыша.
В процессе шабрения трехгранный шабер следует наклонять к поверхности под таким углом, чтобы стружку снимала средняя часть его режущей кромки. Образующиеся при этом штрихи от шабера на поверхности детали должны иметь форму четырехугольника или ромба. В зависимости от конфигурации и положения вкладыша рабочее движение шабера может быть направлено в правую и левую сторону. Угол резания р при грубом шабрении трехгранным шабером обычно составляет 70—75°, а при чистовом — около 120° Увеличение угла резания при отделке позволяет снимать очень тонкую стружку.
При обработке вкладышей подшипников шабрение с периодическим окрашиванием поверхности вкладыша по поверочному валу ведут до тех пор, пока пришабриваемая поверхность не будет равномерно покрываться пятнами краски на площади не менее 3/4 поверхности вкладыша.
Итак, вы приобрели массивную доску для покрытия пола, теперь следует ознакомиться с способами ее укладки на пол. Ведь правильно уложенная массивная доска обеспечит вам красивый и надежный пол на долгое …
Какой должна быть ванная комната для ребенка? В первую очередь, безопасной, интересной и оригинальной. На это следует ориентироваться, выбирая не только мебель и аксессуары, но и сантехнику для детского санузла. …
На что обратить внимание при оформлении кухни? Привычная обстановка кухни может надоедать. Тогда появляется желание изменить ее. Для этого приобретаются кухни Киев, но мебели недостаточно. Необходимо правильно оформить окно, подобрать …
msd.com.ua
Шабрение металла: технология, виды, инструменты
Шабрение, которое также называется шабрование или шабровка, — это технологическая операция, позволяющая выполнять обработку поверхностей металлических деталей с высокой степенью точности и качества. Совершенно не случайно специалисты считают такую операцию одной из самых сложных и трудоемких, так как она практически не поддается механизации, а ее выполнение требует от исполнителя соответствующих навыков и достаточного опыта работы.
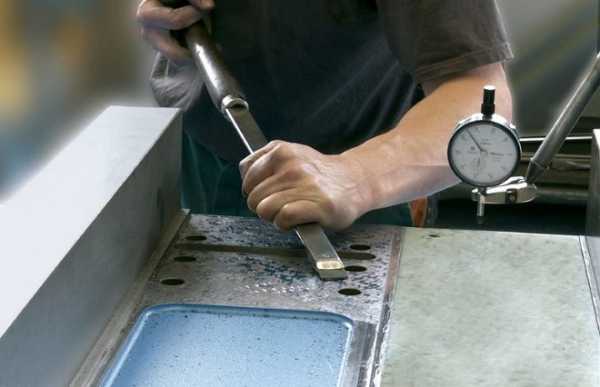
Шабрение стальной пластины
Особенности операции и инструменты
Шабрение поверхностей — это финишная слесарная операция, смысл которой состоит в том, чтобы используя специальный инструмент, называемый шабер, соскоблить с детали тонкий слой материала. Толщина материала варьируется в интервале 0,005–0,07 мм. При помощи такой операции преимущественно обрабатываются изделия из металла, достаточно редко — детали из пластика и древесины.
Так как шабрение является финишной операцией, ее используют для выполнения обработки деталей, поверхность которых уже имеет невысокую степень шероховатости.
Такой технологический процесс просто идеально подходит для обработки частей, которые в дальнейшем будут сопрягаться и перемещаться относительно друг друга. В подобных подвижных соединениях, сформированных из деталей с идеально обработанными плоскостями, надежно удерживается смазочный материал, и обеспечено плотное прилегание элементов, что является необходимым условием точного функционирования узла. Используя операцию шабрения, выполняют обработку:
- деталей приборов различного назначения;
- элементов подшипников скольжения;
- наружной части измерительных инструментов и контрольных приспособлений: поверочных плит, линеек, угольников и др.;
- направляющих элементов различных станков: токарного, сверлильного и др.;
- плоских и криволинейных поверхностей любого другого назначения, к которым предъявляются повышенные требования по степени их шероховатости и точности взаимного расположения.
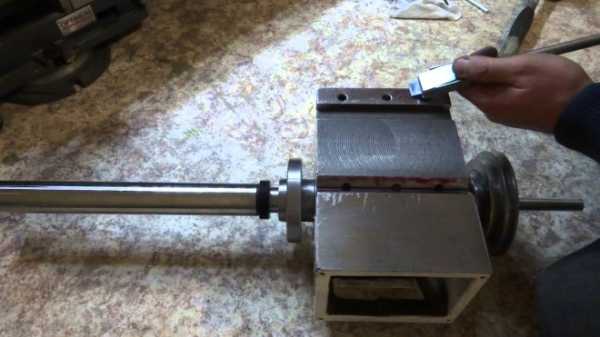
Шабровка деталей токарного станка
Процесс шабрения, как уже говорилось выше, практически не поддается механизации. Выполняют такую технологическую операцию при помощи ручного инструмента, который называется шабером. На сегодняшний день используются следующие виды инструментов для выполнения шабрения:
- классифицирующиеся по конфигурации своей режущей части на плоские, фасонные и трехгранные;
- подразделяющиеся по своей конструкции на цельные и составные;
- одно- и двухсторонние инструменты, отличающиеся количеством режущих частей.
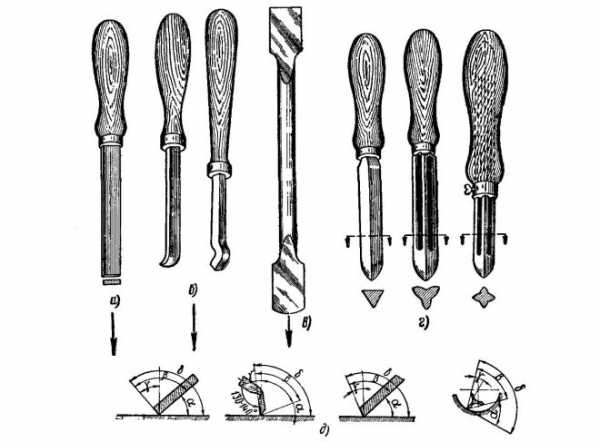
Конструкции шаберов: а — односторонний плоский, б — с загнутым концом, в — двусторонний плоский; г — многогранные; д — углы заточки
При производстве инструментов, предназначенных для выполнения шабрения, в качестве основного материала используется инструментальная сталь. В тех случаях, когда инструмент имеет составную конструкцию, его рабочая часть может быть оснащена твердосплавными пластинами или режущими элементами, изготовленными из быстрорежущей стали.
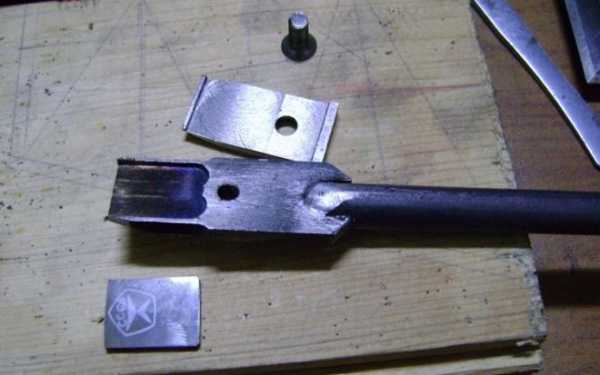
Державка шаберной пластины
На геометрические параметры инструментов, при помощи которых выполняется шабровка, оказывает влияние ряд параметров:
- материал изготовления детали, которую предстоит обрабатывать;
- угол, под которым инструмент располагается по отношению к поверхности детали;
- характеристики поверхности, необходимые для получения в процессе выполнения обработки.
Шабрение плоских поверхностей преимущественно выполняется при помощи одно- и двухстороннего инструмента, режущая часть которого может иметь прямолинейную или криволинейную конфигурацию. В зависимости от типа обработки, торцевой участок инструмента затачивается под различным углом по отношению к его оси:
- при выполнении черновой обработки — 75–90°;
- для выполнения обработки отделочного типа — 90–100°;
- шаберы для выполнения финишной чистовой обработки — 90°.
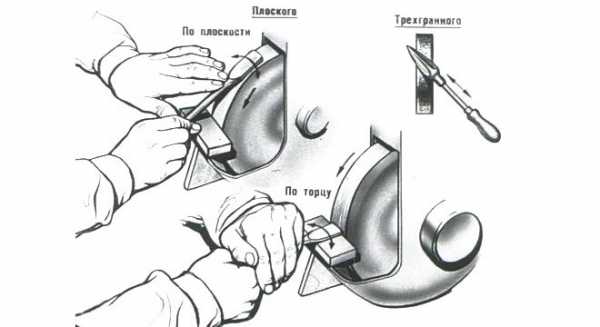
Заточка шабера
На параметры данного угла оказывает влияние и твердость металла, поверхность которого необходимо подвергнуть обработке. Так, шабрение деталей, изготовленных из мягких материалов, производится инструментом, торцевая часть которого заточена под углом 35–40 градусов по отношению к оси инструмента, изделий из стали — 75–90 градусов, из бронзы и чугуна — 90–10°градусов.
Важными параметрами инструмента, при помощи которого выполняется шабровка, являются длина режущей кромки инструмента и радиус ее закругления.
На величину таких параметров основное влияние также оказывает твердость обрабатываемого металла и тип обработки. Те, кто профессионально занимается слесарным делом, наверняка знают, что более твердые металлы обрабатываются инструментом с узкой рабочей частью и минимальным радиусом закругления режущей кромки. В зависимости от типа обработки и требований, предъявляемых к степени шероховатости обрабатываемой детали, ширина режущей кромки шабера выбирается в следующих пределах:
- черновая обработка — 20–30 мм;
- чистовое шабрение — 15–20 мм;
- отделочная обработка — 5–12 мм.
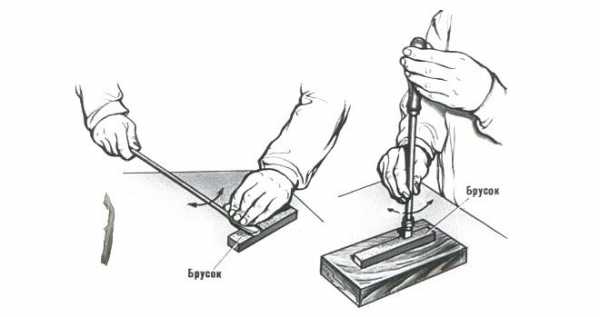
Ручная доводка шабера
Шабрение плоских поверхностей — наиболее простая технологическая операция. Для выполнения обработки элементов криволинейной конфигурации используется инструмент с более сложной формой его режущей части. Так, части подшипников скольжения обрабатываются при помощи шаберов, имеющих кольцевую конструкцию, а поверхности вогнутой формы — инструментом, который обладает одновременно тремя режущими гранями. Такие инструменты, которые совсем несложно заправить и заточить своими руками, имеют на своей режущей части продольные желобки, а угол заострения их режущей части составляет 60°.
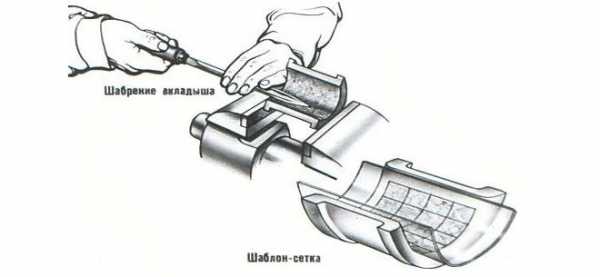
Шабрение криволинейных поверхностей
Шабрение плоских деталей
Операция шабрения поверхностей деталей, имеющих плоскую форму — наиболее распространенная технологическая операция, алгоритм выполнения которой уже хорошо отработан на протяжении нескольких десятилетий. Таким способом, в частности, выполняют обработку элементов станины, направляющих токарного и станков любого другого типа.
Инструмент, при помощи которого выполняется операция шабрения, может перемещаться вручную «на себя» или «от себя». Практически все специалисты слесарного дела подтверждают, что более производительным шабрение получается в том случае, если инструмент двигается «на себя». Очень важным моментом для выполнения качественной обработки является правильная подготовка поверхности, которая ей будет подвергаться.
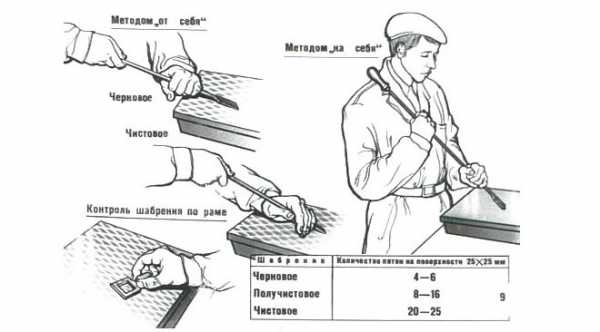
Приемы шабрения
Неотъемлемым элементом данного технологического процесса является краска, необходимая для более качественного выполнения шабрения. Такая краска, представляющая собой смесь машинного масла с суриком, лазурью или синькой, изначально наносится на поверочную плиту, с которой затем посредством круговых движений переносится на поверхность обрабатываемой детали. При помощи нанесенной таким образом краски специалист выявляет на поверхности детали наиболее выступающие участки, подлежащие шабрению в первую очередь.
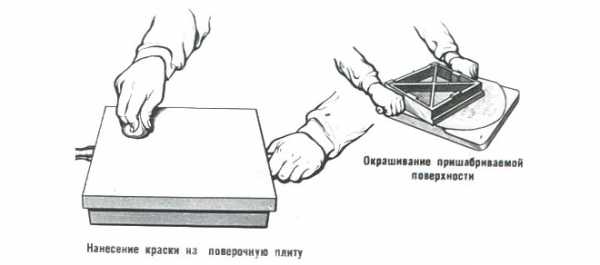
Подготовка к шабрению
Алгоритм, по которому выполняется шабрение с движением шабера «на себя», выглядит следующим образом:
- деталь, которую предстоит обрабатывать, фиксируют в тисках;
- шабер берут обеими руками в средней его части и подводят его режущую часть к поверхности детали, следя за тем, чтобы угол наклона по отношению к поверхности изделия составлял порядка 80°;
- режущая кромка инструмента, при помощи которой будет выполняться операция шабрения, подводится к границе окрашенного пятна, затем оно соскабливается;
- выполняется непосредственно шабрение, сначала черновое или предварительное, а затем — чистовое.
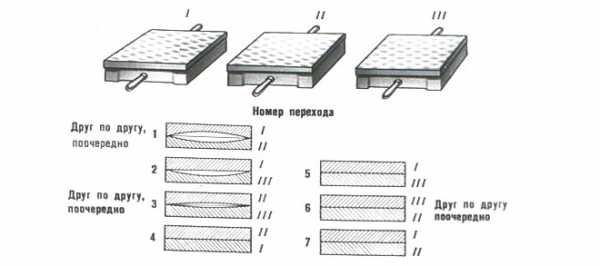
Последовательность шабрения методом «трех плит»
Естественно, габаритные элементы токарного или любого другого станка, которые не представляется возможным снять и зафиксировать в тисках, обрабатываются по месту. При выполнении шабрения, как и любых других слесарных работ, следует строго придерживаться требований техники безопасности.
Контроль качества выполненного шабрения осуществляется при помощи специальной рамки с прозрачным окошком, размеры которого составляют 25 на 25 мм. В таком окошке, если операция шабрения выполнена качественно, должно явно просчитываться 12–16 пятен краски, распределенных равномерно по всей его площади. Техника выполнения такого контроля выглядит следующим образом:
- рамку с окошком помещают на поверхность обработанной детали;
- считают количество пятен краски на площади поверхности, ограниченной окошком рамки;
- данную процедуру повторяют в нескольких местах поверхности детали;
- высчитывают среднее арифметическое количества пятен краски в окошке и сравнивают его с нормативным показателем — 12–16 пятен.
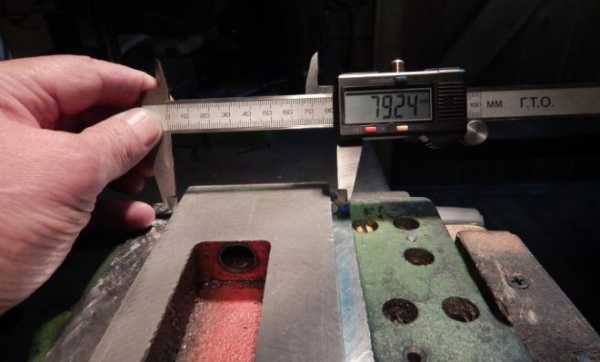
Поверка плоскостей с помощью цифрового штангенциркуля
Такое приспособление, как рамка с окошком, не подходит для проверки качества обработки криволинейных поверхностей. Поэтому для таких целей используют гибкую полимерную пленку, на которую нанесена сетка с размерами 25 на 25 мм. Удобство использования такой пленки состоит в том, что ей можно с легкостью придать ту конфигурацию, которую имеет поверхность обработанной детали. Удовлетворительно проведенной обработка считается в том случае, если на 75-ти участках поверхности детали количество пятен краски в окошке соответствует нормативному значению.
После операции шабрения, как правило, проводится процедура притирки, которая позволяет выровнять обрабатываемую поверхность с точностью до 0,0001 мм. Выполняется этот процесс не только при помощи инструмента различного вида, но и с применением абразивных материалов: порошков и паст.
Технологические операции по финишной обработке поверхности деталей после шабрения, о которых говорилось выше, несмотря на свою сложность и массу нюансов по их выполнению, могут быть достаточно успешно и быстро освоены по обучающим видео роликам, размещающимся на просторах сети интернет.
Оценка статьи:
Загрузка…Поделиться с друзьями:
met-all.org
Подготовка к шабрению – Шабрение, притирка и др.
Подготовка к шабрению
Категория:
Шабрение, притирка и др.
Подготовка к шабрению
Перед шабрением поверхность очищают от грязи, промывают керосином и протирают. Затем с помощью поверочной линейки и щупа определяют величину износа поверхности.
При значительном износе (выработке) поверхности (от 0,5 мм и выше на длине 1 м) обработку под шабрение производят строганием или фрезерованием на станках. В ряде случаев предварительная обработка поверхности выполняется опиливанием. Поверхность считается подготовленной к шабрению, если при наложении на нее лекальной линейки образуется ровный просвет не более 0,05—0,06 мм.
Окрашивание поверочного инструмента. Выше было сказано, что шабрение выполняется по краске, наносимой на поверочную плиту или линейку. Лучшими красками следует считать берлинскую лазурь, железный сурик и голландскую сажу. Перед употреблением краску растирают в мельчайший порошок и разводят на машинном масле. Рабочие поверхности плиты или линейки тщательно протирают масляной тряпкой и насухо вытирают, после чего покрывают тонким и равномерным слоем краски. Рабочую поверхность поверочной плиты, покрытую краской, накладывают на пришабриваемую поверхность детали и с легким нажимом перемещают плиту в разных направлениях 2—3 раза. При шабрении небольших деталей, напротив, деталь пришабриваемой поверхности кладут на поверочную плиту и перемещают по ней таким же образом. На хорошо подготовленной поверхности окрашенные выступы располагаются но всей площади, на плохо подготовленной — густо окрашиваются отдельные большие участки и наряду с этим кое-где образуются слабо окрашенные пятна; наконец, на очень плохо подготовленной поверхности окрашиваются всего лишь две-три точки. После проверки поверхности детали на краску можно приступить к шабрению. Процесс шабрения заключается в постепенном снятии металла с окрашенных мест.
Заточка и заправка (доводка) шаберов. Углы заточки режущих граней шаберов выбирают в зависимости от характера работы и материала пришабриваемой детали.
Наиболее распространенным углом заострения является р=90° (рис. 1). При установке такого шабера под углом а = 15-^25°^ легко соскабливается металлическая стружка, шабер излишне не врезается в металл и не проскальзывает.
Большое значение имеет правильный выбор формы режущего лезвия шабера. Наиболее рациональной является выпуклая форма, которую рекомендуется очерчивать дугой радиуса 30—40 мм для получистового шабрения и дугой радиуса 40—55 мм — для чистового шабрения. При отсутствии такого закругления шабер соскабливает металл всем лезвием, что требует приложения больших усилий. Кроме того, острые углы шабера при малейшем отклонении его в сторону врезаются в металл и затрудняют работу.
Заточка режущих граней шаберов производится на заточных станках. У плоских шаберов сначала затачивают боковые грани, а затем торцовую. Заточку нужно вести с охлаждением. После заточки на лезвии шабера образуются заусенцы и шероховатости, поэтому шабер нужно заправлять (доводить) вручную на мелкозернистых абразивных кругах или брусках зернистостью 90 и выше, на чугунных плитах, покрытых мелкозернистым абразивным порошком, или на корундовых оселках. Круги и чугунные плиты при доводке покрывают легким слоем машинного масла. На кругах и плитах заправляют и торцовую грань шабера. На оселке заправляют сначала торцовую, а затем боковые грани шабера.
Заправку шаберов обычно производят через каждые 1,5—2 часа работы. Затачивают шаберы после четырех-пяти правок.
—
Окрашивание проверочного инструмента. При шабрении работа ведется по краске, наносимой на проверочную плиту. Лучшими красками являются железный сурик, берлинская лазурь, индиго и голландская сажа. Перед употреблением краску растирают в мельчайший порошок и разводят на машинном масле. Краска не должна быть чересчур жидкой, и в ней нельзя оставлять сухих крупинок. Наносят краску тампоном (тряпка, сложенная вдвое, свернутая в трубку и перевязанная бечевкой), равномерно покрывая ею поверхность тонким слоем.
Заточка и заправка шаберов (рис. 2). Предварительная заточка шаберов производится на заточных станках; после этого шаберы заправляют на абразивных брусках или оселках зернистостью 90 и выше. Поверхность бруска смазывают тонким слоем машинного масла. Установив шабер на брусок торцовой частью, сообщают ему движение вдоль торца, слегка покачивая брусок с целью получения криволинейной режущей кромки. После заправки торца правят широкие плоскости шабера, двигая его вдоль режущей кромки.
Рис. 2. Заточка и заправка шаберов
Для особо точных работ шабер сначала заправляют на карборундовых брусках с мелким зерном, а затем на чугунных плитках с применением очень мелкого наждачного порошка и масла. При такой заправке шаберы дают хорошую гладкую поверхность. Заправлять шабер надо не менее четырех-пяти раз за 8 час. работы.
Подготовка поверхности к шабрению. В зависимости от состояния поверхности, подлежащей шабрению (степень ее изношенности, наличие или отсутствие царапин или забоин), выбирают тот или иной способ предварительной обработки под шабрение.
Если износ (выработка) поверхности достигает 0,5—1 мм на длине 1000 мм, то предварительную обработку производят на строгальных, фрезерных или шлифовальных станках. Иногда, при небольших поверхностях, предварительная обработка выполняется опиливанием напильниками (драчевыми и личными) «под краску», т. е. с проверкой обрабатываемой поверхности окрашенным проверочным инструментом.
При опиливании «под краску» громоздких деталей проверочную линейку или плиту после нанесения на них равномерного слоя краски накладывают на обрабатываемую поверхность, по которой их передвигают без нажима; при обработке легких деталей их накладывают на плиту и передвигают по ней. Накладывать и снимать линейку (плиту) надо в строго отвесном направлении.
Поверхность считается подготовленной к шабрению, если при наложении на нее лекальной линейки образуется ровный просвет не более 0,05 мм.
После опиливания снимают личным напильником небольшие фаски на острых ребрах детали и приступают к шабрению. Легкие детали для шабрения зажимают в тисках или ставят на верстак; более тяжелые устанавливают на козлах; очень тяжелые детали (например станины) шабрят на месте.
Реклама:
Читать далее:
Точность шабрения и контроль качества
Статьи по теме:
Главная → Справочник → Статьи → Блог → Форум
pereosnastka.ru
Шабрение прямолинейных и криволинейных поверхностей
Шабрение прямолинейных и криволинейных поверхностей
Категория:
Шабрение, притирка и др.
Шабрение прямолинейных и криволинейных поверхностей
Шабрение прямолинейных (плоских) поверхностей
Для получения поверхности высокого качества последовательно выполняют черновое, получистовое и чистовое шабрение.
Черновое шабрение (предварительное) заключается в грубой обработке поверхности: широкими шаберами удаляют следы и риски предыдущей обработки. Вначале из-за недостаточно тщательной подготовки поверхности отдельные, наиболее выступающие места будут окрашиваться густо и на них образуются крупные пятна. В этом случае делают «разбивку» больших пятен: снимают металл с силь-ноокрашенных мест. После каждого окрашивания направление движения шабера изменяют. Шабером захватывают все пятно, иначе на поверхности образуются заусенцы. Когда пятна расположатся равномерно, разбивку заканчивают и приступают к увеличению числа пятен, ведя шабрение всех окрашенных мест, включая и слабоокрашенные. Получив четыре-шесть пятен в квадрате 25х 25 мм, предварительное шабрение заканчивают.
Работу выполняют шабером шириной 20 — 30 мм при длине рабочего хода 10 —15 мм. Направление шабера непрерывно меняют так, чтобы последующий штрих шел под углом 90° к предыдущему.
За один ход шабера снимают слой толщиной 0,02 — 0,05 мм. Шабрят до тех пор, пока не исчезнут видимые риски. Качество шабрения проверяют на краску, которую наносят на поверочную плиту. После наложения и движения (плиты или детали) обнаруженные выступающие места снова шабрят.
Получистовое шабрение (точечное) заключается в снятии только серых, т. е. наиболее выступающих мест, выявленных проверкой на краску. Работу выполняют плоским узким (12 — 15 мм) шабером при длине рабочего хода от 5 до 10 мм; за один ход шабера снимают слой толщиной 0,01 —0,02 мм.
Чистовое шабрение (отделрчное) применяют для получения очень высокой точности поверхности. При легком нажиме на шабер снимают тонкий (8 — 10 мкм) слой. Применяют шаберы шириной от 5 до 10 мм при длине рабочего хода 4 — 5 мм (мелкие штрихи).
Прием шабрения «от себя» имеет следующие недостатки:
– недостаточно устойчив при рабочем ходе шабер, вследствие чего стружка неодинакова по сечению, поверхность получается неровной и рваной;
– в конце каждого движения шабер оставляет заусенцы, которые приходится снимать дополнительно.
Рис. 1. Шабрение плоских деталей при отделочных операциях
Рис. 2. Нанесение краски перед шабрением направляющих типа «ласточкин хвост»
Рис. 3. Шабрение по методу трех плит (для наглядности слой металла увеличен)
Прием шабрения «на себя» разработан слесарем-новатором Ленинградского завода станков-автоматов А. А. Барышниковым. Шабер берут за среднюю часть (стержень) обеими руками в обхват и устанавливают лезвие к обрабатываемой поверхности под углом 60 —75° , а не 25 — 30° , как при шабрении «от себя». Верхняя часть шабера, оканчивающаяся деревянной ручкой, упирается в плечо работающего. Рабочее движение шабера осуществляется «на себя». При таком методе шабрения значительно улучшается качество обрабатываемой поверхности, так как совершенно исключаются «дробления», часто наблюдающиеся при шабрении «от себя». Это объясняется тем, что вследствие увеличенной длины (до 450 — 500 мм) шабер при шабрении «на себя» пружинит, благодаря чему лезвие его плавно врезается в металл и плавно выходит из зоны резания.
Преимущества этого приема шабрения:
– увеличенная длина шабера позволяет использовать кроме рук также и плечо работающего, шабер оказывается более устойчивым. Кроме того, длинный шабер пружинит, поэтому режущая часть его врезается в металл и выходит из металла плавно: поверхность при этом получается более ровная, без рванин, а в конце штриха не остается заусенцев;
– прием шабрения «на себя» в 1,5 — 2 раза производительнее шабрения «от себя».
Чистовое (отделочное) шабрение применяют только для поверочных линеек, поверочных плит и очень точных сопряжений. Выполняют узкими шаберами и очень короткими штрихами. Во время холостого хода инструмент должен отделяться от плиты. Последние притирки производят без краски, выступающие части определяют по блеску. Точность этого вида шабрения 20 — 25 пятен на квадрате 25 х 25 мм.
Декоративное шабрение (наведение «мороза»), на обработанную поверхность шабером наносят штрихи, образующие на поверхности тот или иной рисунок. Наиболее часто применяется шахматный рисунок, когда на поверхности образуются ромбики с разным направлением штрихов. Выполняют его в два приема: сначала наносят в шахматном порядке штрихи в одном направлении, затем в промежутках — штрихи в противоположном направлении. «Мороз» наводят на рабочих и нерабочих поверхностях. Создавая на поверхности штрихи в определенном направлении, декоративное шабрение вместе с тем улучшает условия смазки ее, так как в полученных штрихах за счет поверхностного натяжения лучше удерживается смазка. По исчезновении штрихов судят об износе (при износе более 3 мк|\л рисунок исчезает).
Шабрение по методу совмещения граней дает более точные поверхности и гарантирует их перпендикулярность боковым сторонам детали. Этот метод применяется при шабрении рабочих граней деталей прямоугольно-призма-тической формы. Пришабривание начинается с взаимной пригонки двух рабочих граней. После этого обработанные грани совмещают друг с другом. Это совмещение дает возможность одновременно проверить обе шаброванные поверхности одной и той же контрольной плитой. После окончания этого цикла переходов процесс повторяют. По этому методу пришабривают грани детали параллельно одной из ее сторон, но при совмещении пользуются не боковыми, а параллельными поверхностями, установив деталь на второй контрольной плите, и процесс обработки таким образом ведут между двумя контрольными плитами.
Точность шабрения и контроль качества. Шабрением можно получить высокие точность (0,003 — 0,01 мм) и качество обработки. Качество шабрения определяют по числу пятен (точек), приходящихся на единицу обработанной поверхности. Чем больше это число, тем выше точность обработанной поверхности. Для определения степени точности служит квадратная рамка 25х 25 мм (рис. 4, а), которую накладывают на пришабренную поверхность и считают число пятен (рис. 4, б). Для удобства рамку делают с ручкой.
Рис. 4. Рамка (а) и контроль ею качества шабрения (б)
Рис. 5. Шабрение криволинейных поверхностей: а — перенос краски с вала на подшипник, 6 — вкладыш со следами краски, в — прием шабрения, г — шаблон-сетка -для проверки количества пятен после шабрения
Шабрение заканчивают при следующих числах пятен на поверхности, ограниченной рамкой 25 х 25 мм: черновое — 8 — 10, получистовое — 12, чистовое — 15, точное — 20, тонкое — 25.
Рис. 6. Шабрение по методу совмещенных граней: а — пригонка двух граней, б — совмещенная пригонка, в — повторение перехода
Шабрение криволинейных поверхностей
Шабрение кливолинейных поверхностей, например, подшипников, выполняют следующим образом. На вал или шейку вала, с который должен сопрягаться подшипник, равномерно наносят тонкий слой краски, вал вкладывают во вкладыш подшипника или вкладыш подшипника на шейку вала и легким усилием поворачивают его, после чего снимают вал и шабрят трехгранным шабером выступающие места.
Шабер наклоняют так, чтобы металл снимала средняя часть режущей кромки. Шабер удерживают за ручку правой рукой, слегка вращая, а левой прижимают его к обрабатываемой поверхности. Шабрение продолжают до тех пор, пока не получат необходимое количество пятен, которое определяют шаблоном-сеткой.
Реклама:
Читать далее:
Заточка и заправка трехгранных шаберов
Статьи по теме:
pereosnastka.ru
Шабрение и притирка при слесарных работах в автомобилестроении
Строительные машины и оборудование, справочник
Шабрение и притирка при слесарных работах в автомобилестроении
Категория:
Автомобилестроение
Шабрение и притирка при слесарных работах в автомобилестроении
Шабрением называется процесс обработки поверхности изделий, при котором с отдельных участков шабером соскабливают тонкие слои металла.
Шаберы делаются из инструментальных сталей У12, У12А. Режущий конец шабера закаливается без отпуска до твердости HRC 60—65.
Шабер затачивают на наждачном круге так, чтобы штрихи от заточки располагались поперек лезвия, при заточке шабер периодически охлаждают в воде. После заточки лезвие шабера доводят на точильных брусках-оселках или на абразивных кругах, поверхность которых покрывается машинным маслом.
Шаберы бывают с одним или двумя режущими концами, первые называются односторонними, вторые — двусторонними. По форме режущего конца шаберы разделяют на плоские, трехгранные и фасонные.
Плоские односторонние шаберы с прямым или отогнутым вниз концом применяют для шабрения плоских поверхностей, пазов, канавок. Для шабрения кривых поверхностей (при обработке втулок, подшипников и т. п.) применяют трехгранные шаберы.
Фасонные шаберы предназначены для шабрения фасонных поверхностей, сложных по профилю канавок, желобков, пазов и т. п. Фасонный шабер представляет собой набор стальных пластинок, форма которого соответствует форме обрабатываемой поверхности.
Пластинки насаживают на металлическую державку шабера и закрепляют гайкой.
В зависимости от длины и ширины обрабатываемой плоской поверхности величина припуска на шабрение должна быть от 0,1 до 0,4 мм.
Ручное шабрение. Поверхность детали или заготовки перед шабрением обрабатывают на металлорежущих станках или опиливанием. Затем начинают шабрение. Для проверки качества шабрения поверхность поверочной плиты покрывают тонким слоем краски (сурик, синька или сажа, разведенные в масле). Обрабатываемую поверхность тщательно протирают тряпкой, аккуратно накладывают на поверочную плиту и медленно перемещают по ней круговыми движениями, после чего осторожно снимают.
В результате такой операции все выступающие на поверхности участки окрашиваются и отчетливо выделяются пятнами. Окрашенные участки (пятна) вместе с металлом удаляют шабером. Затем обрабатываемую поверхность и поверочную плиту очищают и плиту вновь покрывают слоем краски, деталь снова накладывают на нее и процесс повторяют.
Пятна при повторных операциях будут делаться меньшего размера, а количество их будет увеличиваться. Шабрят до тех пор, пока пятна не будут равномерно расположены по всей обрабатываемой поверхности, а количество их будет соответствовать техническим условиям.
При шабрении кривых поверхностей (например, вкладыша подшипника) вместо поверочной плиты пользуются шейкой вала, которая Должна находиться в сопряжении с обрабатываемой поверхностью вкладыша. В этом случае вкладыш подшипника накладывают на шейку вала, покрытую тонким слоем краски, осторожно поворачивают его вокруг нее, затем снимают, зажимают в тиски и шабрят по пятнам.
Рис. 1. Шаберы ручные: а — прямой плоский односторонний и плоский односторонний с отогнутым концом, б — трехгранные, в — механизированный; 1 — электродвигатель, 2 — редуктор, 3 — гибкий вал, 4 — шабер
При шабрении шабер устанавливают по отношению к обрабатываемой поверхности под углом 25—30° и держат его правой рукой за рукоятку, прижав локоть к туловищу, а левой рукой нажимают на шабер. Шабрение производится короткими движениями шабера, причем если шабер плоский прямой, то движение его должно быть направлено вперед (от себя), плоским шабером с отогнутым вниз концом движение производят назад (к себе), а трехгранным шабером — вбок.
В конце каждого хода (движения) шабера его отрывают от обрабатываемой поверхности, чтобы не получились заусенцы и уступы. Для получения ровной и точной обрабатываемой поверхности направление шабрения каждый раз после проверки по краске меняют так, чтобы штрихи пересекались.
Точность шабрения определяют по количеству равномерно расположенных пятен на площади размером 25 х 25 мм2 обработанной поверхности путем наложения на нее контрольной рамки. Среднее количество пятен определяется проверкой нескольких участков обрабатываемой поверхности.
Механизация шабрения. Ручное шабрение заменяется по возможности шлифованием, точением или его осуществляют механизированными шаберами.
Механизированный шабер приводится в действие электродвигателем через гибкий вал, присоединенный одним концом к редуктору, а другим к кривошипу. При включении электродвигателя кривошип начинает вращаться, сообщая шатуну и прикрепленному к нему шаберу возвратно-поступательное движение. Кроме электрического шабера, применяют пневматические шаберы.
Притиркой называется процесс обработки поверхностей деталей при помощи шлифующих порошков и паст с целью снятия тончайших слоев металла. Притирка применяется в тех случаях, когда требуется получить высокую точность сопряженных поверхностен двух илй нескольких деталей.
Притиркой можно достичь точности обработки в 0,001—0,002 мм. Притиркой получают также поверхности с высоким классом шероховатости и соединения, обеспечивающие герметичность. При притирке снимается тончайший слой металла (за один ход притира 0,002 мм), поэтому перед притиркой поверхности деталей должны быть отшлифованы и припуск на притирку должен оставляться не более 0,01— 0,02 мм.
Притирочные материалы. При притирке применяют абразивные твердые и мягкие материалы. Из твердых абразивных материалов для обработки стали применяют порошки корунда, электрокорунда, для чугуна и хрупких материалов — карбид кремния, для твердых сплавов — карбид бора, синтетические алмазы. К мягким абразивным материалам относятся порошки окислов хрома, железа, алюминия, которые применяются для обработки отожженной стали, чугуна, сплавов меди, алюминия.
Широкое распространение при притирке находят пасты: абразивные на основе электрокорунда или окиси хрома (пасты ГОИ) и алмазные (АПЮО, АП40, АП14, АП1 и др.) на основе синтетического алмаза. Абразивные пасты выпускаются трех типов: грубая для грубой доводки, средняя для предварительной доводки и тонкая для окончательной доводки.
При притирке используют смазочные и охлаждающие жидкости: керосин, легкие минеральные масла, бензин, содовую воду и др. Добавка олеиновой кислоты и канифоли в керосин резко повышает производительность притирки.
Инструментами для притирки служат притиры. Они изготавливаются с высокой точностью по форме обрабатываемой поверхности, имеют правильную геометрическую форму (допускаемое отклонение — несколько микрон). Материал притиров должен иметь однородный состав и твердость и быть мягче материала притираемой детали. Чаще всего притиры изготовляют из мелкозернистого перлитного чугуна твердостью НВ 150—200, а также из стали, меди, латуни, свинца, стекла.
Процесс притирки. При притирке твердыми абразивными материалами обработка ведется за счет механического воздействия зерен этих материалов на частички металла.
При работе мягкими абразивными материалами и пастами под воздействием поверхностно-активных веществ (олеиновой кислоты, стеарина, канифоли) на обрабатываемой поверхности образуется мягкая окисная пленка толщиной порядка сотых долей микрона, которая затем снимается механическим путем (химико-механическая обработка).
Притирка с помощью притиров подразделяется на доводку шаржированными притирами и доводку с намазкой абразивной смесью (доводку свободным абразивным зерном).
В первом случае притир шаржируют, т. е. в его поверхность до начала обработки вдавливают абразивные зерна. Во втором случае абразивная смесь (паста) разводится до полужидкой массы, которой покрывается поверхность притира.
Реклама:
Читать далее: Сверление, зенкование, зенкерование и развертывание при слесарных работах в автомобилестроении
Категория: – Автомобилестроение
Главная → Справочник → Статьи → Форум
stroy-technics.ru
Шабрение. Шаберы. Слесарное дело |
Шабрение
Шабрение — это окончательная слесарная операция, заключающаяся в соскабливании очень тонких слоев материала с поверхности заготовки с помощью режущего инструмента — шабера. Шабрение применяется в тех случаях, когда необходимо обработать поверхности с очень малой шероховатостью. Как правило, шабрению подвергаются сопрягаемые поверхности, перемещающиеся друг относительно друга (трущиеся поверхности). С его помощью достигается плотное прилегание сопрягаемых поверхностей, надежное удерживание смазки между трущимися поверхностями и точные размеры деталей.
Шабрением обрабатываются как плоские, так и криволинейные поверхности (например, направляющие станков), поверхности подшипников скольжения, детали приборов, а также поверхности различных инструментов и приспособлений (например, поверочные плиты, угольники, линейки). За один проход шабер может удалить с поверхности заготовки очень тонкий слой металла толщиной не более 0,7 мм. При средних усилиях, прикладываемых к инструменту, толщина снимаемой стружки составляет 0,01 …0,03 мм.
Шабрение является весьма трудоемкой операцией и требует чрезвычайно высокой квалификации слесари. В практике слесарных работ шабрение занимает около 20%, поэтому большое значение имеют механизации труда и замена ручного шабрения станочными методами обработки.
Инструменты и приспособления для шабрения. Шаберы
Режущим инструментом при шабрении является шабер. Шаберы различаются по конструкции — цельные и составные, по форме режущей кромке — плоские, трехгранные и фасонные, а также по числу режущих граней — односторонние и двухсторонние.
Шаберы изготовляются из углеродистых инструментальных сталей марок У10…У13. Составные шаберы могут оснащаться пластинами из быстрорежущей стали или твердого сплава.
Для шабрения плоских поверхностей используются одно- или двухсторонние шаберы с прямолинейной или криволинейной режущей кромкой (рис. 4.3, а, б, в). Геометрические параметры шаберов зависят от вида обработки, материала заготовки и угла установки инструмента по отношению к обрабатываемой поверхности. Торцевая поверхность шабера затачивается под углом заострения 90… 100° по отношению к оси инструмента. При черновой обработке угол заострения равен 75…90°, при чистовой — 90°, а при отделочной — 90… 100°. Угол заострения для чугуна и бронзы выбирается равным 90… 100°, для стали — 75…90°, а для мягких металлов — 35…40°.
Выбор длины режущей кромки и радиуса ее закругления зависит от твердости обрабатываемого материала и заданной шероховатости обработанной поверхности. Чем тверже обрабатываемый материал и выше требования к чистоте обработанной поверхности, тем более узкой должна быть режущая кромка шабера и меньшим радиус закругления.
Для чернового шабрения применяются шаберы с шириной режущей кромки 20… 30 мм, для чистового — 15… 20 мм и для отделочного — 5… 12 мм.
Для шабрения вогнутых поверхностей, например вкладышей подшипников скольжения, предназначены трехгранные шаберы (рис. 4.3, г), которые имеют три режущие кромки и могут быть прямыми и изогнутыми; их угол заострения составляет 60°. У этих шаберов на гранях находятся продольные канавки (желобки), что делает более удобной заточку и заправку инструмента.
Помимо цельных, используются составные шаберы (рис. 4.3, д), позволяющие быстро заменять режущие пластины, а потому удобные для выполнения различных шабровочных работ. Такой шабер состоит из корпуса держателя 2, рукоятки 4 и зажимного винта 3. Сменную режущую пластину 1 из углеродистой, быстрорежущей стали или твердого сплава закрепляют в держателе 2, вращая винт 3 при помощи рукоятки 5.
В более простой конструкции шабера (рис. 4.3, е) режущие пластины 6 закрепляются в рукоятке 7 при помощи гайки.
При шабрении вкладышей подшипников скольжения для уменьшения числа переточек в процессе работы применяются шаберы- кольца (рис. 4.4), которые могут быть изготовлены из кольца изношенного конического роликового подшипника.
Поскольку шабрение является заключительной операцией слесарной обработки, то качество ее выполнения необходимо контролировать в течение всего процесса. Для этих целей предназначены проверочные инструменты.
К проверочным инструментам (рис. 4.5) относятся: проверочные плиты для контроля широких плоских поверхностей; плоские проверочные линейки (рис. 4.5, а, б), применяемые при контроле шабрения длинных и сравнительно узких плоских поверхностей; трехгранные угловые линейки (рис. 4.5, в), использующиеся при контроле шабрения поверхностей, расположенных под внутренним углом, угловые плиты — для контроля качества шабрения поверхностей под прямым углом; а также проверочные валики — для контроля шабрения цилиндрических поверхностей и выемок. Контроль качества шабрения всеми этими инструментами основан на выявлении неровностей на обработанной шабрением поверхности. Неровности на обрабатываемой поверхности становятся видимыми после наложения ее на окрашенный проверочный инструмент или наоборот, после наложения окрашенного инструмента на обработанную поверхность и взаимного их перемещения друг относительно друга.
Весьма важным является хранение проверочных инструментов в надлежащем состоянии, поэтому после работы проверочный инструмент следует очищать, смазывать и только потом укладывать в футляр или накрывать крышкой.
dlja-mashinostroitelja.info
Шабер и шабрение — всё о них.
Шабер и осуществляемая с помощью него операция, называемая шабрением, применяется с целью обеспечения плотного прилегания поверхностей сопрягаемых деталей. Это довольно трудоёмкая и специфичная слесарная операция, позволяющая довести (или восстановить) сопрягаемые плоскости различных деталей до идеала и тем самым достичь точности различных станков и оборудования, а также нормального сопряжения трущихся между собой деталей.
В этой статье, рассчитанной больше на новичков, я очень подробно опишу такой инструмент как шабер, все его типы, его правильная заточка и доводка, а также будет описано, как грамотно произвести шабрение, припуски на шабрение, точность шабрения, контроль качества, шабрение направляющих станин станков и многие другие нюансы.
Для начала давайте рассмотрим какие бывают шаберы и для чего они применяются.
Шабер — для чего он, какие они бывают и другие нюансы.
С помощью этого инструмента производится такая операция как шабрение, которая, как я уже говорил, применяется для обеспечения плотного прилегания трущихся деталей различных механизмов и станков. Шабрение, при умелых действиях, позволяет получить точность поверхности от 0,003 до 0,01 мм (подробнее о процессе шабрения я напишу ниже).
За один проход с помощью шабера можно снять слой металла толщиной примерно 0,005 — 0,07 мм. А при среднем давлении на инструмент, толщина снимаемого металла (стружки) как правило не превышает 0,01-0,03 мм. При чистовом шабрении и малом давлении на инструмент, как правило снимается очень тонкая стружка, толщиной всего 0,002 — 0,005 мм
По форме режущей части шаберы делятся на плоские, фасонные и трёхгранные. А по числу режущих кромок (граней) шаберы бывают односторонние и двухсторонние. Ниже мы рассмотрим эти нюансы более подробно, но прежде следует сказать, что заводские шаберы изготавливают из углеродистой инструментальной стали марки У10А или У12А. После изготовления, их подвергают закалке до твёрдости HRC56-64.
Плоские шаберы. Наиболее распространены и их применяют для шабрения плоских поверхностей (станин металорежущих станков и т.п.), открытых плоскостей, а так же различных пазов, канавок и других полостей, которые не имеют криволинейных поверхностей.
Шаберы: а — плоский односторонний, б — с изогнутым концом, в — двухсторонний (с плоским и закруглённым концом), г — трёхгранный, д, е — фасонные (трёх и четырёхгранные).
В зависимости от числа режущих концов плоские шаберы бывают двухсторонними и односторонними — с рукоятками на втором конце (см. рисунок 1) и двухсторонними.
Важные рекомендации. Следует помнить, что важное значение имеет форма режущей кромки (лезвия) у шабера. Наиболее распространённой и рациональной является немного выпуклая (полукруглая) форма лезвия (см. рисунок 1 в, и фото выше).
При изготовлении инструмента и заточке полукруглой режущей кромки, саму кромку (лезвие) советую очерчивать и изготавливать с дугой радиуса примерно 30-40 мм — это если вы будете производить получистовое шабрение. Для чистового шабрения рекомендую изготавливать (затачивать) полукруг лезвия с чуть бóльшим радиусом — примерно 40 — 55 мм.
Основное преимущество шаберов с полукруглой режущей кромкой, перед плоской режущей кромкой в том, что при отсутствии закругления у кромки лезвия, шабер в работе снимает металл всей плоскостью режущей кромки (всем лезвием) и от этого придётся применять большее усилие, но не это главное.
А то, что при недостатке опыта и при малейшем отклонении (вправо-влево) плоской режущей кромки инструмента, острые углы плоского лезвия врезаются в металл и вызывают появление глубоких царапин на обрабатываемой поверхности деталей.
На полукруглой форме лезвия ещё и углы закруглены (это хорошо видно на самом первом фото выше, где показаны закруглённые сменные пластинки) и таким инструментом невозможно сделать глубокие царапины даже при недостаточном опыте, поэтому я рекомендую новичкам работать только с полукруглой формой режущих пластинок.
Плоскую форму лезвия шабера рекомендуется использовать только при грубом шабрении, и при этом советую изготавливать режущее лезвие более широким, для повышения производительности труда и уменьшения возможности отклонить инструмент вправо-влево (конечно же если поверхность имеет большую площадь и позволяет подлезть более широкому инструменту).
А при получистовом шабрении ширину лезвия уменьшают, а если недостаточно опыта (или при чистовом шабрении), лучше всего использовать шаберы с полукруглой заточкой, или с односторонней радиусной заточкой (см. рисунок 1).
Трёхгранные и фасонные шаберы. Этот инструмент (см. рисунок 1 г,д,е, а так же рисунок 2 в, г) изготавливают прямыми и изогнутыми и применяются они как правило для шабрения криволинейных поверхностей, ну например отверстий в подшипниках скольжения (вкладышей — об этом ниже) и других деталей, которые не имеют плоских поверхностей.
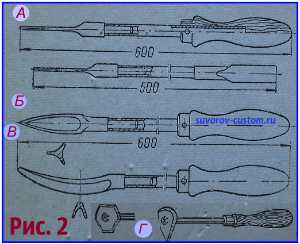
фасонные и составные шаберы : А — составной плоский, Б — трёхгранный прямой, В — трёхгранный изогнутый, Г — фасонный.
Отличия каждого инструмента хорошо видны, если посмотреть с его торца и с боку (см. рисунок 1 и 2).
Фасонные шаберы ещё бывают в виде стальных закалённых пластинок (и сменных тоже), которые закреплены с помощью гайки на конце стержня с рукояткой (рисунок 2 г).
А форма и размеры режущей пластинки такого инструмента (см. рисунок 2 г) конечно же зависит от размеров и формы фасонных поверхностей, которые подлежат шабрению.
Составные шаберы. Они как правило отличаются меньшим весом, по сравнению с другими типами шаберов. Например плоский шабер длиной 40 см имеет вес чуть больше 450 грамм, а составной шабер при длине в 60 см весит примерно 350 — 370 грамм.
Форма режущей части у составных шаберов бывает плоской (см. рисунок 2) трёхгранной прямой и трёхгранной изогнутой (и двухгранной тоже). Следует отметить, что составные шаберы отличаются большой чувствительностью, хорошо пружинят (имеют хорошую упругость) и поэтому ими удобно работать и регулировать толщину снимаемого слоя металла.
Шаберы- кольца (кольцевые). Эти инструменты изготавливают из обойм изношенных конических роликовых подшипников, при помощи заточки их на шлифовальных кругах (позиция А на рисунке 3) и далее доводят их торец на мелкозернистом или алмазном круге (позиция Б на рисунке 3).
шаберы-кольца: А — заточка на точильном станке, Б- доводка, Г — шабрение вкладыша кольцевым шабером.
Применяют их как правило для шабрения вкладышей — позиция В на рисунке 3 (о шабрении вкладышей ниже) и для других криволинейных поверхностей.
Шаберы со сменными режущими пластинками. Это сейчас наиболее распространённые инструменты из-за их удобства и преимуществ перед другими типами и такой тип показан на самом верхнем фото и на рисунке 4 ниже. Основное преимущество — это конечно же возможность быстрой смены режущих пластинок, которые изготавливают из различных твёрдых сплавов.
Составные шаберы (со сменной пластинкой) l — основные части шабера, ll и lll — способы крепления пластинок.
А возможность быстрой смены пластинок позволяет подобрать инструмент (в зависимости от формы пластинки) практически для всех целей и задач и для разных обрабатываемых поверхностей. К тому же при затуплении пластинки её всегда можно заменить, если пока нет заточного станка.
Ну и ещё один немаловажный аргумент состоит в том, что пластинку нужной формы несложно изготовить самостоятельно, например из какой то старой дисковой фрезы, ножовочного полотна и других подобных (плоских) инструментов, изготовленных из быстрорежущей стали или твёрдых сплавов.
Но сейчас уже можно купить и качественные заводские пластинки от зарубежных фирм (см. самое первое фото вверху) или найти советские пластинки, отличного качества.
Инструмент для шабрения со сменными режущими пластинками и способы закрепления этих пластинок показаны на рисунке 4 (и самом верхнем фото).
Шабер с радиусной заточкой. Такой инструмент показан на рисунке 5 а, и основное отличие его от других типов в том, что режущая часть 1 затачивается по некоторому радиусу, что существенно облегчает шабрение, так как такой инструмент требует приложения гораздо меньших усилий (чем при шабрении плоским шабером).
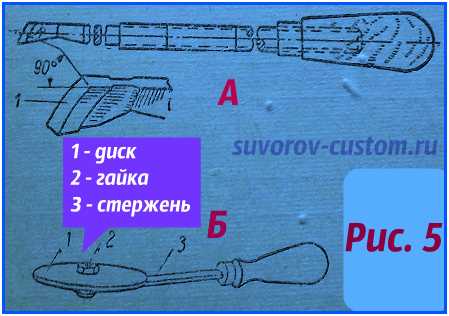
Шабер с радиусной заточкой и дисковый шабер
Радиус закругления делаем примерно 30 — 40 мм для предварительного шабрения, и 40 — 55 мм для окончательного.
Дисковый шабер показан на рисунке 5б и как видно там, режущая часть у такого инструмента выполнена в виде стального диска из закалённой (или быстрорежущей) стали. Такой инструмент применяется для шабрения широких плоскостей и его можно изготовить самостоятельно из маленькой дисковой фрезы, если сточить её зубья и затем довести кромку диска на заточном станке.
Диск имеет наружный диаметр примерно 50-60 мм, при толщине 3-4 мм и как правило крепится с помощью гайки 2 к концу стержня 3 инструмента. А в случае затупления режущей кромки инструмента, следует всего лишь немного провернуть диск, ослабив гайку 2, затем зажать её и можно продолжать работу не затупившимся участком. Разумеется, когда затупится вся режущая кромка диска, то его снимают и производят заточку на круглошлифовальном станке.
Заточка и доводка шаберов.
Заточку этого инструмента производят на заточных станках (о станках подробно вот здесь) и кто знаком с заточкой и доводкой токарных резцов (о заточке резцов подробно вот тут) то без проблем сможет заточить практически любой шабер. В этом деле важно правильно выбрать угол заточки и заточить под нужным углом режущие грани инструмента.
А углы заточки режущих граней (кромок) следует выбирать в зависимости от материала обрабатываемых деталей, а также от характера работ. Режущими кромками плоских шаберов являются их торцовые рёбра. На рисунке 6 показаны углы заточки плоского шабера в зависимости от обрабатываемого материала, а также там указаны углы (углы установки), под которыми следует держать инструмент при работе.
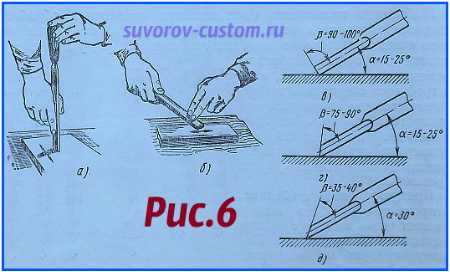
Углы установки шабера и его доводка:
а — доводка торца шабера, б — доводка боковой поверхности шабера;
Углы заточки шабера для шабрения: в — чугуна и бронзы, г — стали, д — мягких сплавов.
Так для шабрения деталей из чугуна и бронзы угол заточки равен 90-100°, для шабрения стали как правило делают угол заточки равным 75 — 90° (чем мягче сталь, тем угол меньше), ну а для шабрения деталей из мягких металлов угол заточки составляет всего 35-40°.
Кроме рисунка 6, рекомендуемые углы заточки, в зависимости от обрабатываемого материала, показаны в таблице. Кроме того, там указаны углы заточки трёхгранных шаберов, а также указаны углы установки инструмента при работе и углы резания.
Наиболее распространена заточка инструмента под углом заострения в 90°, так как в основном шабрение используют для восстановления направляющих металлорежущих станков, у которых направляющие изготовлены из чугуна. При угле заточки в 90° и установки инструмента под углом 15-25º, угол резания будет составлять примерно 105-125º.
При таком угле резания инструмент довольно легко снимает металл и при этом не слишком врезается в него, ну и не проскальзывает. Ну и как я уже говорил, наиболее распространённой и рациональной формой заточки лезвия является радиусная форма.
ТАБЛИЦА рекомендуемых углов режущей части плоских и трёхгранных шаберов.
Угол установки инструмента может быть и значительно больше(75-80°) при работе методом на себя, но об этом подробнее ниже, в разделе «практика шабрения».
Практика заточки и доводки шаберов.
Как было сказано выше, заточку режущих поверхностей инструмента производят на заточных станках, шлифовальным кругом (о заточных станках и о различных шлифовальных кругах ссылка выше). У плоских шаберов следует сначала затачивать боковые грани, и только после этого затачивают торцовую поверхность инструмента. Ну и после этого выполняется доводка, которая осуществляется вручную на чугунной плите, покрытой мелким абразивным порошком или пастой.
При доводочных операциях инструмент ставят в строго вертикальное положение (см. рисунок 6а выше) и сначала доводят (заправляют) торцовую режущую грань (двигая грань инструмента по плите вперёд-назад, с небольшим нажимом), при этом важно держать инструмент строго вертикально. Ну а после уже доводят боковые грани (см. рисунок 6б) двигая инструмент по чугунной плите вправо-влево (указано стрелкой на рисунке).
Если производить доводку инструмента в последовательности, описанной мной выше, то это позволит получить наиболее острые грани режущей кромки, при этом на инструменте не будет завалов от доводки торцовой грани. При интенсивной работе заправку (правку, доводку) шаберов как правило необходимо заново производить через пару часов интенсивной работы.
А после четырёх или пяти заправок инструмент необходимо заново заточить и довести. Хотя это конечно же примерные данные и всё зависит от качества и твёрдости материала режущей пластинки инструмента, ну и от твёрдости обрабатываемой детали.
Процесс шабрения, точность и контроль качества.
Шабрение — это окончательная отделочная обработка поверхностей деталей, с помощью соскабливания (снятия) с нужных участков очень тонкого слоя материала, с помощью шабера, подробно описанного выше. Шабрение применяется в тех случаях, когда нужно обеспечить очень точное соприкосновение поверхностей трущихся деталей и получить плотное прилегание поверхностей сопрягаемых деталей, ну и придать деталям точные формы и размеры.
Эта операция часто используется для восстановления плотного прилегания трущихся поверхностей деталей металлорежущих станков (например направляющих станины и суппорта) и восстановления точности под изношенных станков.
Припуски на шабрение должны быть небольшими, так как было сказано выше, в процессе шабрения инструментом снимается очень тонкая стружка, толщиной всего 0,002 — 0,005 мм. Ну и конечно же припуски зависят от длины и ширины обрабатываемой поверхности (или от диаметра и длины обрабатываемого отверстия).
Ниже приведены величины припусков на шабрение в миллиметрах, в зависимости от длины и ширины плоскостей и отверстий:
- Ширина обрабатываемой поверхности — до 100 мм, а длина — от 100 до 500 мм ——припуск составляет 0,10 мм.
- Ширина обрабатываемой поверхности- до 100 мм, а длина — от 500 до 1000 мм —— припуск составляет 0,15 мм.
- Ширина обрабатываемой поверхности- до 100 мм, а длина — от 1000 до 2000 мм —— припуск составляет 0,15 мм.
- Ширина обрабатываемой поверхности- до 100 мм, а длина — от 2000 до 4000 мм —— припуск составляет 0,15 мм.
- Ширина обрабатываемой поверхности- до 100 мм, а длина — от 4000 до 6000 мм —— припуск составляет 0,15 мм.
- Ширина обрабатываемой поверхности- 100 -500 мм, а длина — от 100 до 500 мм —— припуск составляет 0,15 мм.
- Ширина обрабатываемой поверхности- 100 -500 мм, а длина — от 500 до 1000 мм —— припуск составляет 0,20 мм.
- Ширина обрабатываемой поверхности- 100 -500 мм, а длина — от 1000 до 2000 мм —— припуск составляет 0,25 мм.
- Ширина обрабатываемой поверхности- 100 -500 мм, а длина — от 2000 до 4000 мм —— припуск составляет 0,30 мм.
- Ширина обрабатываемой поверхности- 100 -500 мм, а длина — от 4000 до 6000 мм —— припуск составляет 0,40 мм.
- Ширина обрабатываемой поверхности- 500 -1000 мм, а длина — от 100 до 500 мм —— припуск составляет 0,18 мм.
- Ширина обрабатываемой поверхности- 500 -1000 мм, а длина — от 500 до 1000 мм —— припуск составляет 0,25 мм.
- Ширина обрабатываемой поверхности- 500 -1000 мм, а длина — от 1000 до 2000 мм —— припуск составляет 0,30 мм.
- Ширина обрабатываемой поверхности- 500 -1000 мм, а длина — от 2000 до 4000 мм —— припуск составляет 0,45 мм.
- Ширина обрабатываемой поверхности- 500 -1000 мм, а длина — от 4000 до 6000 мм —— припуск составляет 0,50 мм.
Поверхности деталей, предназначенных для шабрения заранее подготавливают на строгальных, фрезерных или шлифовальных станках, ну а поверхности малых деталей опиливают вручную сначала крупным (драчёвым), а затем мелким (личным) напильником.
Разумеется это не относится к поверхностям станков (направляющих станин и суппортов) которые изнашиваются и их необходимо восстановить с помощью шабрения (на тему восстановления направляющих станины и суппорта станков я как нибудь напишу отдельную статью — статья уже написана и находится вот тут и желающие могут кликнуть на ссылку и почитать). Хотя некоторые станки (их направляющие) восстанавливают сначала шлифованием, но конечно же всё зависит от степени выработки поверхностей и от возможностей ремонтной мастерской.
Перед шабрением поверхности ещё нужно обработать (снять) острые кромки, по всему периметру обрабатываемой поверхности детали. Далее потребуется поверочная плита, которая тщательно протирается чистой ветошью и затем на неё наносится равномерный тонкий слой краски, которая представляет из себя смесь моторного масла и порошка сажи или лазури (берлинская лазурь), которые следует измельчить настолько, что бы между пальцами вообще не ощущалось даже мелких зёрен (в качестве измельчителя можно использовать кофемолку).
Для получения ровного и равномерного слоя, подготовленную краску наносим с помощью холщовой тряпки, причём краску наносим с внутренней стороны тряпки. И выступая через поры тряпки, краска при движении по поверхности плиты тряпки, покрывает плиту тонким и равномерным слоем.
Теперь следует тщательно очистить поверхность детали чистой ветошью и наложить деталь на смазанную краской плиту. Ну и далее остаётся с лёгким нажимом на деталь, сделать два-три круговых движения по плите, после чего осторожно отделить деталь от поверочной плиты и рассмотреть поверхность детали. Окрашенные пятна на поверхности детали означают выступающие участки, которые нужно снять с помощью шабрения.
Точно так же проверяются и сопрягаемые детали станков, например салазки суппортов и направляющие станин, только вместо плиты краской намазываем специальную линейку, например ШД — 630 (ГОСТ 8026) и прикладываем её на направляющие станины, по которым движется суппорт станка (или намазываем краской одну из сопрягаемых плоскостей продольных и поперечных салазок суппорта). Как я уже говорил — эта темя для отдельной статьи и я её обязательно напишу (уже написал и ссылка на статью чуть выше), так как она довольно актуальна.
Практика шабрения.
Сам процесс шабрения заключается в постепенном снятии металла с окрашенных мест (окрашенные места означают выпуклости, а не окрашенные — впадины). Для начала приступаем к так называемой «разбивке» больших пятен, при которой сильными движениями шабера снимаем (соскабливаем) стружку с выпуклых (окрашенных) мест.
Далее поверхность детали очищаем от стружки и вновь производим проверку на краску, описанную мной выше, и после этого заново повторяем процесс шабрения, соскабливая металл с выпуклых мест. А когда пятна на поверхности будут располагаться равномерно, заканчиваем «разбивку» и приступаем к увеличению количества пятен , соскабливая вновь появляющиеся (после проверки на краску) окрашенные места.
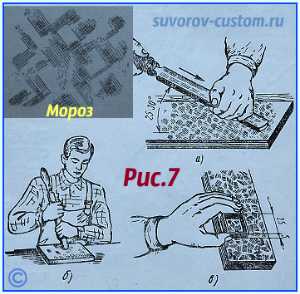
Практика шабрения — а — установка шабера, б — шабрение на себя, в — проверка точности шабрения.
Разумеется, что каждое последующее снятие металла (стружки) будет способствовать уменьшению высоты неровностей, которые будут делиться на несколько менее высоких выпуклостей, а общее их количество будет с каждым разом увеличиваться, при этом направление рабочего хода инструмента каждый раз следует изменять, но об этом чуть позже.
В процессе шабрения шабер удерживаем правой рукой за ручку (если Вы правша), и устанавливаем его под нужным углом по отношению к обрабатываемой поверхности детали (об углах, в зависимости от твёрдости материала, я написал выше и показал на рисунке 6). Ну а левой рукой нажимаем на инструмент (см. рисунок 7а) примерно чуть ниже его середины.
Следует примерно учесть, что давление рукоой на инструмент должно быть в пределах 2-5 кг, не более. Ну а при обратном (холостом) ходе назад, на инструмент не давим вообще. Ещё новичкам следует учесть, что шабрение выполняют за несколько переходов, а инструмент следует двигать в разных направлениях так, чтобы последующий ход (штрих) происходил с перекрытием предыдущего.
Точнее, чтобы последующий штрих проходил под углом в 45 — 90 градусов к предыдущему штриху. Так и появляется так называемый «мороз» различной формы, то есть симметрично расположенные риски (полоски) или клеточки, ну или ромбики (см. рисунок 7). Они так же способствуют удерживанию смазки на сопрягаемых друг с другом трущихся деталях, что важно (так же важно как и риски от хона, удерживающие моторное масло на поверхности цилиндров двигателей). Надеюсь с этим понятно новичкам, идём дальше.
При получистовом и чистовом шабрении лучше всего применять метод на себя, при котором шабер, имеющий длину примерно 45 — 55 см (иногда и более — зависит от роста работника) обхватываем за среднюю часть обеими руками, а верхняя часть своей рукояткой упирается в плечо работника. При этом стараемся расположить инструмент под углом в 75-80° по отношению к обрабатываемой поверхности.
При таком способе рабочим ходом инструмента является движение лезвия на себя и при таком способе работать гораздо удобнее, положение инструмента оказывается более устойчивым, соответственно улучшается качество обработки и к тому же достигается более высокая производительность (примерно в 1,5 — 2 раза) по сравнению с обычным способом шабрения.
Ну и ещё немаловажный момент — при этом способе длинный шабер лучше пружинит, что обеспечивает плавное врезание лезвия и гораздо бóльшую точность обработки.
Проверка качества шабрения.
Качество проверяют сначала внешним осмотром, и пришабренная поверхность не должна иметь глубоких следов шабера и царапин. Ну а точность шабрения проверяется количеством пятен, расположенных на площади квадрата, каждая из сторон которого равна 25 мм. В качестве квадрата применяют специальные рамочки (см. рисунок 7в) со сторонами равными 25 мм, которые несложно вырезать самому.
Приложив рамочку к пришабренной поверхности, далее следует посчитать количество пятен, находящихся внутри неё (внутри квадрата со сторонами 25 мм). Причём количество пятен на всей пришабренной поверхности определяют как среднее арифметическое значение, вычисленное из нескольких проверок на разных участках всей поверхности детали.
На площади, ограниченной рамкой 25х25 мм, для очень грубого шабрения достаточно добиться всего четырёх пятен; для грубого шабрения достаточно девяти пятен; для точного шабрения достаточно 16 пятен; ну и для очень точного шабрения необходимо добиться 20 — 25 пятен.
Точное шабрение. При точном шабрении не используется проверка на краску, а используют как правило грубую или среднюю полировальную пасту ГОИ (государственный оптический институт). После одного или двух проходов шабером по поверхности детали, разводят с помощью керосина полировальную пасту и наносят её на поверочную плиту. Затем на поверхность плиты уладывают деталь притираемой поверхностью и ведут притирку шабруемой поверхности до того момента, когда паста из зелёной превратится в чёрную и такой процесс повторяют три или четыре раза.
После этого тщательно очистив поверхность детали, осматривают поверхность, на которой появились блестящие пятна (которые означают выпуклости) и остались более тёмные пятна, означающие впадины. Теперь нужно снять с помощью шабера блестящие пятна, и вновь притереть поверхность пастой и повторить шабрение, пока не будет получена поверхность требуемого качества, которая определяется опять же с помощью рамочки, размером 25х25 мм.
При вышеописанном способе (с использованием пасты) следует учесть важное обстоятельство: полировальная паста способна срабатывать не только поверхность детали, но и поверхность поверочной плиты. Поэтому обязательно необходимо, до и после работы, тщательно контролировать состояние поверхности поверочной плиты, например с помощью лекальной линейки (на просвет — о величине отклонения от прямолинейности судят по размерам световой щели).
Несмотря на выше описные хлопоты с проверкой состояния плиты, использование пасты ГОИ позволяет повысить производительность точного шабрения в полтора-два раза.
Шабрение криволинейных поверхностей (вкладышей подшипников).
Шабрение криволинейных поверхностей, например вкладышей подшипников скольжения, имеет некоторые особенности. Во первых здесь применяют трёхгранные прямые или изогнутые шаберы (о них написано выше), ну и во вторых имеются отличия в работе.
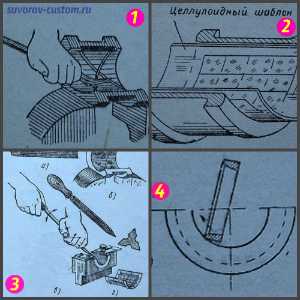
шабрение вкладышей: 1 — шабрение вкладыша полукруглым шабером, 2 — прозрачный целлулоидный шаблон сетка для проверки качества, 3 — шабрение фасонным трёхгранным шабером, 4 — шабрение кольцевым шабером.
Сначала наносят тонкий и равномерный слой краски на участок вала, который будет соприкасаться с вкладышем. Затем окрашенный вал укладывают на нижний вкладыш (вкладыши) и далее равномерно (крест на крест) и с небольшим усилием затягивают крышку подшипника. Затягиваем гайки крышки до такой степени, что бы вал можно было провернуть с некоторым усилием вправо-влево, на пару-тройку оборотов.
Можно на начальном этапе и не зажимать крышки подшипников, а просто укладывать вал в нижние вкладыши и немного прижав его, провернуть вправо влево на 2-3 оборота.
После этого откручиваем гайки и снимаем крышку подшипника и вал, и далее пришабриваем окрашенные места вкладыша (означающие выпуклости) перемещая инструмент по форме окружности вкладыша. Шабер наклоняем к поверхности вкладыша так, чтобы снимала металл средняя часть режущей кромки инструмента.
Инструменту придают небольшое вращательное движение и при этом одновременно прижимают к поверхности обрабатываемой детали. Далее повторяем проверку на краску и шабрение, пока не менее 3/4 площади поверхности вкладыша не будет равномерно покрыто пятнами краски.
Но более точно качество шабрения можно проверить если вырезать из картона шаблон, в котором имеется всё то же окошко 25х25 мм и приложить его (изогнув шаблон) к поверхности вкладыша. Если вкладыш имеет большой размер, то можно изготовить шаблон из прозрачного пластика (целлулоида — показан на рисунке чуть выше), на котором расчертить сетку, с ячейками опять же размером 25х25 мм.
Механизация шабрения. Шабрение является довольно трудоёмкой слесарно-подгоночной (доводочной) операцией. К примеру для шабрения чугунной поверхности площадью 2 квадратных метра, необходимо затратить более 100 часов труда квалифицированного работника. Поэтому механизация таких работ на производстве имеет большое значение.
Для механизированного шабрения применяют различные специальные приспособления, ускоряющие и облегчающие процесс шабрения. Это и пневматические шаберы, работающие по принципу отбойного молотка от действия сжатого воздуха, и электро-механические инструменты, работающие от электросети. У всех из них практически один и тот же принцип работы — это преобразование электроэнергии (или энергии давления воздуха) в возвратно поступательное движение режущей пластинки шабера.
Но всё же механическое шабрение подходит больше для больших площадей и объёмов работы на производстве. Поэтому подробно я не буду описывать его. Ну а ручной способ считается более точным и аккуратным, ну и подходит он лучше всего для гаражных мастеров и их мастерских.
Брак при шабрении и меры его предупреждения.
- Вид брака: полное перекрытие краской пришабриваемойповерхности металла. Причина брака: нанесение на поверочную плиту (или линейку) слишкомтолстого слоя краски. Мера предупреждения: осторожно наносим краску (берлинскую лазурь) тонким слоем.
- Вид брака: окрашивание края или середины пришабриваемой поверхности. Причина брака: неправильная предварительная обработка поверхности металла. Мера предупреждения: проверять правильность предварительной обработки поверхности.
- Вид брака: наличие блестящих полос на пришабриваемой поверхности металла. Причина брака: шабрение только в одном направлении. Мера предупреждения: производим шабрение в разных направлениях, что бы штрихи располагались под углами 45 — 60º.
- Вид брака: неравномерное расположение пятен на пришабриваемой поверхности. Причина брака: слишком сильный нажим на шабер, или шабрение слишком длинными штрихами. Мера предупреждения: при шабрении соблюдаем осторожность и не делаем сильный нажим на инструмент, а так же не делаем слишком длинные рабочие ходы инструмента. При черновом шабрении ход инструмента должен быть не более 10 — 15 мм, а при чистовом шабрении ход должен быть не более 5 — 10 мм.
- Вид брака: образование рисок на пришабриваемой поверхности металла. Причина брака: не качественная заправка (доводка) инструмента, или наличие заусенцев на его кромках, ну или попадание твёрдых примесей в краску. Мера предупреждения: проверяем качество заправки и состояние режущей кромки лезвия шабера. Далее проверяем его работу на ненужной детали. Проверяем качество и состав краски, кстати, если её наносить через тампон из мелко-пористой ткани, то вероятность попадания твёрдых частиц сводится к нулю.
- Вид брака: глубокие впадины на пришабриваемой поверхности. Причина брака: слишком сильный нажим на шабер. Мера предупреждения: заранее подготавливаем деталь к шабрению с помощью предварительного опиливания и чернового шабрения с малыми просветами. При шабрении не сильно давим на инструмент и снимаем стружку небольшой толщины.
- Вид брака: наличие заусенцев и шероховатостей на пришабриваемой поверхности. Причина брака: неправильная заточка и доводка шабера, а так же его неправильное движение при шабрении. Мера предупреждения: правильно затачиваем и доводим инструмент, чтобы исключить работу тупым лезвием, а так же читаем выше о правильном пользовании и правильных движениях инструмента.
- Вид брака: неточность пришабренной поверхности. Причина брака: применение неточного поверочного инструмента, или неправильное пользование им, или неправильное перемещение шабруемой детали по поверочному инструменту (или наоборот инструмента по детали) при проверке на краску. Мера предупреждения: своевременно проверяем точность (или прямолинейность) поверочного инструмента, а так же содержим в чистоте рабочие поверхности поверочного инструмента и поверхности деталей. Ну и не нажимаем сильно на поверочный инструмент при проверке на краску (правильно пользуемся инструментом).
Вот вроде бы и всё, если ещё что то вспомню, то обязательно допишу. Надеюсь, что описанный здесь инструмент — шабер, да и сам процесс шабрения, я описал достаточно подробно и этот материал будет полезен начинающим мастерам, успехов всем.
suvorov-castom.ru