Погрешность микрометра – Погрешность микрометра — ГОСТы
alexxlab | 01.10.2020 | 0 | Вопросы и ответы
Погрешность микрометра — ГОСТы
Это измерительное устройство предназначено для точного измерения, поэтому надо знать погрешность микрометра. Он придуман ученым Лораном Палмером в XIX веке, именовался сначала круговым штангенциркулем с нониусом. Им заинтересовались американцы, увидев на Парижской выставке, после этого начались его производство и продвижение.Теперь это обычный, практичный и популярный инструмент для замеров диаметра снаружи детали, ее толщины, ширины. Конструкция проста. Прибор быстро измеряет с весьма высокой точностью.
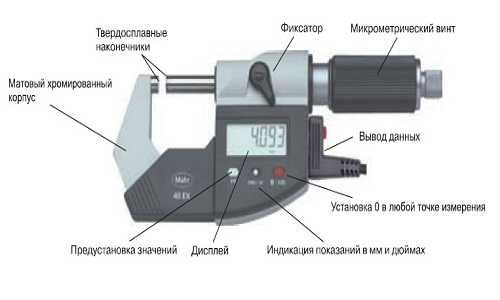
Устройство мкрометра с цифровой индикацией.
Незаменим для производственного цеха, в линейных замерах. Известен каждому станочнику, слесарю, конструктору. Разнообразен по своей конструкции. Универсальный диапазон поверхностей, измеряемых им, очень широк.
На выпуске МК специализируются известные компании: швейцарская Tesa, японская Mitutoyo, германская CarlMahr, отечественные ЧИЗ и КРИН. К китайским относятся осторожно.
Качество их высокое, они имеют шлифовальный вид, отсутствие зазоров прилегания рабочих частей, исполняются из особо прочных, твердых металлов. Это обеспечивает продвижение болта, не деформируя торцевую плоскость. Он абсолютно антикоррозийный, износоустойчивый. Инструмент соблюдает правило Аббе, повышающее точность.
Есть два типы МК:
- механические, имеют штриховую плоскость, нониус;
- цифровые или электронные.
Они с аналоговыми или цифровыми индикациями.
Устройства со штриховой плоскостью
Допустимые значения микрометра.
Главные части — винтовые, микрометрические детали. Перемещаемая поверхность для измерения (торец винта) соединена с барабаном для отсчета. Его оборот равняется шагу резьбы болта. Стандартным считается шаг в 0,5 мм, барабанный элемент имеет 50, 100 штрихов. Цена отсчетного штриха — 0,01 мм, 0,05 мм. Чем точнее резьбовой элемент (изготавливают с максимальной точностью), тем лучше работает прибор. Микрометрический элемент является отдельной измерительной деталью — головкой.
Она есть в МК разных устройств и типов: нутромерных, глубиномерных, стационарных конструкций. Это главный измерительный узел. В нем болт двигается с барабанным элементом относительно твердо фиксируемой планки с закруткой. Узел чаще оборудован двумя шкалами: круговая (под дробные) и линейная вида (для счета полных вращений болта).
Линейная плоскость со штрихами есть снаружи на стебле. Цена шкаловой черты равняется шагу болта, если он 0.5 мм, то наносят два шкаловых участка со штрихом в 1 мм, они подвинуты вместе на 0,5 мм.
Диапазон винта определяет длину шкалы (обычно это 25 мм). Круговая шкала имеется на скосе барабанного элемента, его торец — указатель для линейной плоскости. Для круговой плоскости указатель — продольная черта на линейной.
Устройство микрометра.
Барабан имеет диаметр под деление в 1 мм. Под дробные размерная сетка по кругу иногда использует нониус такой же, как и в штангенциркуле с отсчетом без параллакса.
Нониус имеет размер черты 0,001 мм, его применение целесообразно для считываемых долей сетки, когда она ниже погрешности хода.
Стабилизирует усилия при измерении специальная конструкция микрометра (барабанная трещотка, фрикцион). Конструкция имеет устройство, стопорящее болт. Плоскости для замеров — параллельные торцевые плоскости на микрометрическом болте с пяткой (она напротив головки), стандартная их ширина — 8 мм. Есть приборы с 100 мм размером, а диаметр рабочих плоскостей делают меньшим (6,5 мм). Приборы с границей снизу от 25 мм имеют установочную меру.
В большинстве цена штриха — 0,01, 0,05 мм, нониус — 0,001 мм. Под диаметры больше 500 мм есть тип микрометра со скобами из трубчатых деталей, изготовленных способом сваривания. Их снабжают теплоизоляцией. Скобы есть с границей замеров в 100 мм, они снабжены сменными концами. Длина может приращиваться на 25 мм, границы их замеров — до 1500 мм. Погрешность для них вычисляют формулой: U = ±(6 + L/75) мкм, где L-максимальная граница замеров в миллиметрах.
Вернуться к оглавлению
Цифровые изделия: нюансы
Микрометр (а) и примеры расчета по его шкале (б, в, г).
Счет по штриховочным шкалам микрометра порой неудобен. Если зрение нехорошее или освещение несильное, эту проблему решают электронные МК. Они мало разнятся от механических, плоскости со штрихами заменены инкрементными емкостями, индуктивными элементами преобразования, электронным блоком с цифровым табло. Преобразователь — это две дисковые пластины с проводами. Один диск двигается с болтом, другой — закреплен жестко, держится шпонкой. Они двигаются с болтом на весь его размер.
Скоба микрометров имеет процессорный узел, табло с показателями 0,01 или 0,001 мм, функцией установки нуля, есть также и возможности подключения к внешним вычислительным приборам. Прибор имеет питание от батареи со сроком службы в полтора года. Электромикрометры имеют границу замеров до 300 мм. Делают много разных модификаций, в них параметры могут различаться. Так, есть со сферическими плоскостями под замеры трубчатых элементов, с дисками — для замеров мягких предметов.
Вернуться к оглавлению
Микрометричный глубиномер
Этот прибор состоит из базовой основы, в ней зафиксирован микроболт с измерительными границами в 25 мм, также есть заменяемые измерительные вставки различной длины. Предельный показатель замеров — 300 мм.
Такие приборы так же, как МК, являются механическими, цифровыми устройствами.
Неточность замеров с минимальной вставкой — 5 мм.
Погрешность включает в себя:
- Неточность измерительного узла.
- Неточности плоскостности, параллельности винта с пяткой. Они возникают при поворотных углах, стопорении. Такой вид неточности бывает разным в разнообразных формах (круглых, плоских). Также есть неточности объектов при усилии во время замера.
- Изменение скобы вследствие усилия.
- Неправильность мер установки.
- Неточность вследствие действия температуры, она характерна для больших приборов.
- В электронных приборах может возникнуть неисправность электродеталей.
Погрешность допускается для головки, в случае если она выступает отдельным устройством, в пределах установленных ГОСТом 6507-90. Есть специальные системы с границами погрешностей для приборов, Они имеют показатели, зависящие от границ замеров. Сетка неточностей указывает на допускаемую ошибку G прибора в пункте границ замеров.
Эти граничные показатели состоят из неточности микрометрического узла, неточности от деформации скоб прибора, от бугристости, непараллельности замеряемых плоскостей.
Калибрование, настройку (поверку) микрометра выполняют, используя показатели концевых мер в нескольких пунктах границ замеров, соответственно, ISO 3611:2010, DIN 863, ГОСТ 6207-90. Они берутся, чтобы узнать значение G, то есть предельную неточность устройства во всех пунктах диапазона замеров. Вот стандартные, желательные параметры под концевые меры замеров, под настройку устройства: 3,1; 6,5; 9,7; 12,5; 15,8; 19,0; 21,9; 25 мм.
Вернуться к оглавлению
Подведение итогов
Проверяются неточности плоскостности-параллельности торца болта с пяткой при помощи трех, четырех плоскопараллельных оптических пластинок из стекла, вертикально градуированных в 1/4 или 1/3 хода микроболта (0,5 мм). Так, проверятся 3 или 4 места с полным его поворотом.
Чтобы осуществить поверку микрометра, плоскость фиксируют между пяткой и винтовым торцом. Сдвигая ее между измеряемыми плоскостями, определяют минимальное количество интерференционных колец на одной такой плоскости.
К числовому результату добавляют количество колец второй измерительной плоскости. Если световая волна имеет 640 Нм, то ширина одной полоски будет около 0, 32 мкм. Рекомендуется использовать под поверку калибрование сертифицированные меры.
Надо учесть, что МК имеют хорошую прослеживаемость при поверке погрешности или калибровке по сертифицированным мерам.
МК — это достаточно универсальный прибор. Его выпускают с усовершенствованными видами конструкций рабочих элементов, благодаря которым можно замерять детали различных нестандартных размеров, например, зубчатые поверхности.
moiinstrumenty.ru
1.1. Погрешности приборов
В лабораторных работах метод измерений обычно задан, поэтому из систематических погрешностей учитываются только приборные.
Все приборы и инструменты, используемые для измерений физических величин: амперметр, вольтметр и т.д., характеризуются классом точности и (или) ценой деления. Класс точности L – это обобщенная характеристика прибора, показывающая относительную погрешность прибора выраженную в процентах. Класс точности обозначается числом на шкале прибора: 0,1; 0,2; 0,5; 1,0; 1,5; 2,5; 4. Приборы класса точности 0,1; 0,2; 0,5; применяются для точных измерений и называются прецизионными. В технике применяют приборы классов 1,0; 1,5; 2,5; 4, которые называются техническими. Если на шкале прибора класс точности не указан, то данный прибор внеклассный, то есть имеет большую погрешность измерений.
Абсолютная
систематическая погрешность прибора
где Д – наибольшее значение физической величины, которое может быть измерено по шкале прибора.
Если класс точности
прибора не известен, то его абсолютная
систематическая погрешность принимается равной половине цены
наименьшего деления шкалы:
(2)
При измерении линейкой, наименьшее деление которой 1мм допускается погрешность 0,5мм.
Для приборов, оснащенных нониусом, за приборную принимают погрешность, определяемую нониусом. Для штангенциркуля (рис. 1) – 0,1мм или 0,05мм; для микрометра (рис. 2) – 0,01мм.
Штангенциркуль – прибор для наружных и внутренних измерений. Он построен по принципу штанги 1 с основной шкалой, представляющей собой миллиметровую линейку, и подвижной рамки
На рис. 1 представлен штангенциркуль с нониусом 0,05мм. Шкала этого нониуса получена при делении 39 мм на 20 частей. Следовательно, каждое деление нониуса равно 1,95 мм, то есть на 0,05 мм меньше делений основной шкалы. Если расположить нониус ровно так, что первый штрих нониуса совпадет с первым штрихом основной шкалы, то основное деление нониуса отойдет от основного деления шкалы на 0,05 мм. Для получения нониуса с ценой деления 0,1 мм делят 19 мм на 10 частей (19 мм : 10 = 1,9 мм), тогда каждое деление нониуса будет на 0,1 мм меньше, чем 1 мм.
Рис. 1
Измеряемый предмет располагают между ножками 5, 6 штангенциркуля и закрепляют винтом 4. Целые значения в миллиметрах отсчитывают по основной шкале от «0» основной шкалы до «0» нониуса. Затем смотрят, какое деление нониуса совпало с делением основной шкалы. Если номер совпавшего деления нониуса умножить на цену деления прибора, то получаются сотые доли миллиметра. Если с делением основной шкалы совпадает нулевое или последнее деления нониуса, то сотых долей не будет.
На рис. 2 представлены измерения штангенциркуля с нониусом 0,05 мм.
Рис. 2
Микрометр – это инструмент, применяемый для точных измерений. Принцип действия микрометра основан на работе винтовой пары, то есть преобразования вращательного движения в поступательное.
В скобе 1 микрометра при вращении барабана 2 перемещается микрометрический винт 3, между торцом которого и пяткой 4 помещают измеряемую деталь (рис. 3). Шаг микрометрического винта равен 0,5 мм, а конусная поверхность барабана разделена на 50 равных частей. Следовательно, поворот барабана на одно деление соответствует перемещению винта на 0,01мм. Вращения барабана нужно производить с помощью трещотки 5, обеспечивающей постоянное усилие на измеряемую деталь. Зажим детали производят, вращая трещотку до появления первого треска во избежание порчи инструмента.
Рис. 3
На стебле 6 микрометра расположены две шкалы. Деления нижний шкалы нанесены через 1 мм, деления верхней расположены посередине между штрихами нижней шкалы. По нижней шкале отсчитывают целые миллиметры, а по верхней ‑ половину миллиметра. При измерении встречаются два характерных случая. В первом случае (рис. 4) деления нижний шкалы расположены ближе к барабану, нежели деления верхней шкалы. При этом целые значения миллиметров отсчитываются по нижней шкале, а сотые доли ‑ по барабану. Например, показания инструмента соответствуют размеру 18,04 мм. Во втором случае деление верхней шкалы расположены ближе к барабану, чем деление нижней шкалы. При этом учитываются целые, половинка и сотые доли миллиметра. Например, показания инструмента соответствует размеру 18 целых + половинка 0,50 + 9 сотых, то есть 18,59 мм.
Рис. 4
studfiles.net
ДОПУСТИМЫЕ ПОГРЕШНОСТИ МИКРОМЕТРА | moiinstrumenty.com
Это измерительное устройство предназначено для точного измерения, поэтому надо знать погрешность микрометра. Он придуман ученым Лораном Палмером в XIX веке, именовался сначала круговым штангенциркулем с нониусом. Им заинтересовались американцы, увидев на Парижской выставке, после этого начались его производство и продвижение.Теперь это обычный, практичный и популярный инструмент для замеров диаметра снаружи детали, ее толщины, ширины. Конструкция проста. Прибор быстро измеряет с весьма высокой точностью.
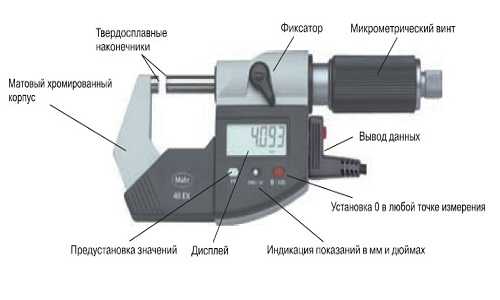
Устройство мкрометра с цифровой индикацией.
Незаменим для производственного цеха, в линейных замерах. Известен каждому станочнику, слесарю, конструктору. Разнообразен по своей конструкции. Универсальный диапазон поверхностей, измеряемых им, очень широк.
На выпуске МК специализируются известные компании: швейцарская Tesa, японская Mitutoyo, германская CarlMahr, отечественные ЧИЗ и КРИН. К китайским относятся осторожно.
Качество их высокое, они имеют шлифовальный вид, отсутствие зазоров прилегания рабочих частей, исполняются из особо прочных, твердых металлов. Это обеспечивает продвижение болта, не деформируя торцевую плоскость. Он абсолютно антикоррозийный, износоустойчивый. Инструмент соблюдает правило Аббе, повышающее точность.
Есть два типы МК:
- механические, имеют штриховую плоскость, нониус;
- цифровые или электронные.
Они с аналоговыми или цифровыми индикациями.
Устройства со штриховой плоскостью
Допустимые значения микрометра.
Главные части — винтовые, микрометрические детали. Перемещаемая поверхность для измерения (торец винта) соединена с барабаном для отсчета. Его оборот равняется шагу резьбы болта. Стандартным считается шаг в 0,5 мм, барабанный элемент имеет 50, 100 штрихов. Цена отсчетного штриха — 0,01 мм, 0,05 мм. Чем точнее резьбовой элемент (изготавливают с максимальной точностью), тем лучше работает прибор. Микрометрический элемент является отдельной измерительной деталью — головкой.
Она есть в МК разных устройств и типов: нутромерных, глубиномерных, стационарных конструкций. Это главный измерительный узел. В нем болт двигается с барабанным элементом относительно твердо фиксируемой планки с закруткой. Узел чаще оборудован двумя шкалами: круговая (под дробные) и линейная вида (для счета полных вращений болта).
Линейная плоскость со штрихами есть снаружи на стебле. Цена шкаловой черты равняется шагу болта, если он 0.5 мм, то наносят два шкаловых участка со штрихом в 1 мм, они подвинуты вместе на 0,5 мм.
Диапазон винта определяет длину шкалы (обычно это 25 мм). Круговая шкала имеется на скосе барабанного элемента, его торец — указатель для линейной плоскости. Для круговой плоскости указатель — продольная черта на линейной.
Устройство микрометра.
Барабан имеет диаметр под деление в 1 мм. Под дробные размерная сетка по кругу иногда использует нониус такой же, как и в штангенциркуле с отсчетом без параллакса.
Нониус имеет размер черты 0,001 мм, его применение целесообразно для считываемых долей сетки, когда она ниже погрешности хода.
Стабилизирует усилия при измерении специальная конструкция микрометра (барабанная трещотка, фрикцион). Конструкция имеет устройство, стопорящее болт. Плоскости для замеров — параллельные торцевые плоскости на микрометрическом болте с пяткой (она напротив головки), стандартная их ширина — 8 мм. Есть приборы с 100 мм размером, а диаметр рабочих плоскостей делают меньшим (6,5 мм). Приборы с границей снизу от 25 мм имеют установочную меру.
В большинстве цена штриха — 0,01, 0,05 мм, нониус — 0,001 мм. Под диаметры больше 500 мм есть тип микрометра со скобами из трубчатых деталей, изготовленных способом сваривания. Их снабжают теплоизоляцией. Скобы есть с границей замеров в 100 мм, они снабжены сменными концами. Длина может приращиваться на 25 мм, границы их замеров — до 1500 мм. Погрешность для них вычисляют формулой: U = ±(6 + L/75) мкм, где L-максимальная граница замеров в миллиметрах.
Цифровые изделия: нюансы
Микрометр (а) и примеры расчета по его шкале (б, в, г).
Счет по штриховочным шкалам микрометра порой неудобен. Если зрение нехорошее или освещение несильное, эту проблему решают электронные МК. Они мало разнятся от механических, плоскости со штрихами заменены инкрементными емкостями, индуктивными элементами преобразования, электронным блоком с цифровым табло. Преобразователь — это две дисковые пластины с проводами. Один диск двигается с болтом, другой — закреплен жестко, держится шпонкой. Они двигаются с болтом на весь его размер.
Скоба микрометров имеет процессорный узел, табло с показателями 0,01 или 0,001 мм, функцией установки нуля, есть также и возможности подключения к внешним вычислительным приборам. Прибор имеет питание от батареи со сроком службы в полтора года. Электромикрометры имеют границу замеров до 300 мм. Делают много разных модификаций, в них параметры могут различаться. Так, есть со сферическими плоскостями под замеры трубчатых элементов, с дисками — для замеров мягких предметов.
Микрометричный глубиномер
Этот прибор состоит из базовой основы, в ней зафиксирован микроболт с измерительными границами в 25 мм, также есть заменяемые измерительные вставки различной длины. Предельный показатель замеров — 300 мм.
Такие приборы так же, как МК, являются механическими, цифровыми устройствами.
Неточность замеров с минимальной вставкой — 5 мм.
Погрешность включает в себя:
- Неточность измерительного узла.
- Неточности плоскостности, параллельности винта с пяткой. Они возникают при поворотных углах, стопорении. Такой вид неточности бывает разным в разнообразных формах (круглых, плоских). Также есть неточности объектов при усилии во время замера.
- Изменение скобы вследствие усилия.
- Неправильность мер установки.
- Неточность вследствие действия температуры, она характерна для больших приборов.
- В электронных приборах может возникнуть неисправность электродеталей.
Погрешность допускается для головки, в случае если она выступает отдельным устройством, в пределах установленных ГОСТом 6507-90. Есть специальные системы с границами погрешностей для приборов, Они имеют показатели, зависящие от границ замеров. Сетка неточностей указывает на допускаемую ошибку G прибора в пункте границ замеров.
Эти граничные показатели состоят из неточности микрометрического узла, неточности от деформации скоб прибора, от бугристости, непараллельности замеряемых плоскостей.
Калибрование, настройку (поверку) микрометра выполняют, используя показатели концевых мер в нескольких пунктах границ замеров, соответственно, ISO 3611:2010, DIN 863, ГОСТ 6207-90. Они берутся, чтобы узнать значение G, то есть предельную неточность устройства во всех пунктах диапазона замеров. Вот стандартные, желательные параметры под концевые меры замеров, под настройку устройства: 3,1; 6,5; 9,7; 12,5; 15,8; 19,0; 21,9; 25 мм.
Подведение итогов
Проверяются неточности плоскостности-параллельности торца болта с пяткой при помощи трех, четырех плоскопараллельных оптических пластинок из стекла, вертикально градуированных в 1/4 или 1/3 хода микроболта (0,5 мм). Так, проверятся 3 или 4 места с полным его поворотом.
Чтобы осуществить поверку микрометра, плоскость фиксируют между пяткой и винтовым торцом. Сдвигая ее между измеряемыми плоскостями, определяют минимальное количество интерференционных колец на одной такой плоскости.
К числовому результату добавляют количество колец второй измерительной плоскости. Если световая волна имеет 640 Нм, то ширина одной полоски будет около 0, 32 мкм. Рекомендуется использовать под поверку калибрование сертифицированные меры.
Надо учесть, что МК имеют хорошую прослеживаемость при поверке погрешности или калибровке по сертифицированным мерам.
МК — это достаточно универсальный прибор. Его выпускают с усовершенствованными видами конструкций рабочих элементов, благодаря которым можно замерять детали различных нестандартных размеров, например, зубчатые поверхности.
moiinstrumenty.com
Погрешность микрометра – госты — Немного о ремонте и строительстве
Оглавление: Устройства со штриховой плоскостью Цифровые изделия: нюансы Микрометричный глубиномер Подведение итогов Это измерительное устройство предназначено для правильного измерения, исходя из этого нужно знать погрешность микрометра. Он придуман ученым Лораном Палмером в десятнадцатом веке, именовался сперва круговым штангенциркулем с нониусом.
Им заинтересовались американцы, заметив на Парижской выставке, затем начались его продвижение и производство.Сейчас это простой, практичный и популярный инструмент для замеров диаметра снаружи подробности, ее толщины, ширины. Конструкция несложна.
Прибор скоро измеряет с высокой точностью.
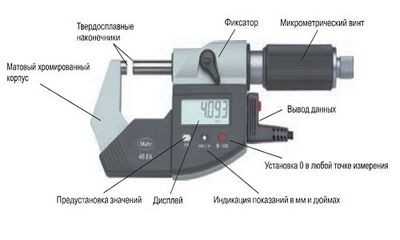
Устройство мкрометра с цифровой индикацией. Незаменим для производственного цеха, в линейных замерах.
Известен каждому станочнику, слесарю, конструктору. Разнообразен по собственной конструкции. Универсальный диапазон поверхностей, измеряемых им, весьма широк.
На выпуске МК специализируются узнаваемые компании: швейцарская Tesa, японская Mitutoyo, германская CarlMahr, отечественные ЧИЗ и КРИН. К китайским относятся с опаской.
Уровень качества их высокое, они имеют шлифовальный вид, отсутствие зазоров прилегания рабочих частей, исполняются из очень прочных, жёстких металлов. Это снабжает продвижение болта, не деформируя торцевую плоскость. Он полностью антикоррозийный, износоустойчивый.
Инструмент выполняет правило Аббе, повышающее точность. Имеется два типы МК: механические, имеют штриховую плоскость, нониус; цифровые либо электронные. Они с аналоговыми либо цифровыми индикациями. Устройства со штриховой плоскостью Допустимые значения микрометра.
Главные части — винтовые, микрометрические подробности. Перемещаемая поверхность для измерения (торец винта) соединена с барабаном для отсчета. Его оборот равняется шагу резьбы болта. Стандартным считается ход в 0,5 мм, барабанный элемент имеет 50, 100 штрихов.
Цена отсчетного штриха — 0,01 мм, 0,05 мм. Чем правильнее резьбовой элемент (изготавливают с большой точностью), тем лучше трудится прибор.
Микрометрический элемент есть отдельной измерительной подробностью — головкой. Она имеется в МК различных типов и устройств: нутромерных, глубиномерных, стационарных конструкций. Это основной измерительный узел.
В нем болт двигается с барабанным элементом довольно твердо фиксируемой планки с закруткой. Узел чаще оборудован двумя шкалами: круговая (под дробные) и линейная вида (для счета полных вращений болта).
Линейная плоскость со штрихами имеется снаружи на стебле. Цена шкаловой черты равняется шагу болта, если он 0.5 мм, то наносят два шкаловых участка со штрихом в 1 мм, они подвинуты совместно на 0,5 мм.
Диапазон винта определяет длину шкалы (в большинстве случаев это 25 мм). Круговая шкала имеется на скосе барабанного элемента, его торец — указатель для линейной плоскости.
Для круговой плоскости указатель — продольная черта на линейной. Устройство микрометра. Барабан имеет диаметр под деление в 1 мм. Под дробные размерная сетка по кругу время от времени применяет нониус такой же, как и в штангенциркуле с отсчетом без параллакса.
Нониус имеет размер черты 0,001 мм, его использование целесообразно для считываемых долей сетки, в то время, когда она ниже погрешности хода. Стабилизирует упрочнения при измерении особая конструкция микрометра (барабанная трещотка, фрикцион).
Конструкция имеет устройство, стопорящее болт. Плоскости для замеров — параллельные торцевые плоскости на микрометрическом болте с пяткой (она наоборот головки), стандартная их ширина — 8 мм.
Имеется устройства с 100 мм размером, а диаметр рабочих плоскостей делают меньшим (6,5 мм). Устройства с границей снизу от 25 мм имеют установочную меру. В большинстве цена штриха — 0,01, 0,05 мм, нониус — 0,001 мм.
Под диаметры больше 500 мм имеется тип микрометра со скобами из трубчатых подробностей, изготовленных методом сваривания. Их снабжают теплоизоляцией. Скобы имеется с границей замеров в 100 мм, они снабжены сменными финишами.
Протяженность может приращиваться на 25 мм, границы их замеров — до 1500 мм. Погрешность для них вычисляют формулой: U = ±(6 + L/75) мкм, где L-большая граница замеров в миллиметрах.
Возвратиться к оглавлению Цифровые изделия: нюансы Микрометр (а) и примеры расчета по его шкале (б, в, г). Счет по штриховочным шкалам микрометра иногда неудобен.
В случае если зрение плохое либо освещение несильное, эту проблему решают электронные МК. Они мало разнятся от механических, плоскости со штрихами заменены инкрементными емкостями, индуктивными элементами преобразования, электронным блоком с цифровым табло.
Преобразователь — это две дисковые пластины с проводами. Один диск двигается с болтом, второй — закреплен жестко, держится шпонкой. Они двигаются с болтом на целый его размер.
Скоба микрометров имеет процессорный узел, табло с показателями 0,01 либо 0,001 мм, функцией установки нуля, имеется кроме этого и возможности подключения к внешним счётным устройствам. Прибор имеет питание от батареи со сроком работы в полтора года.
Электромикрометры имеют границу замеров до 300 мм. Делают большое количество различных модификаций, в них параметры смогут различаться. Так, имеется со сферическими плоскостями под замеры трубчатых элементов, с дисками — для замеров мягких предметов.
Возвратиться к оглавлению Микрометричный глубиномер Данный прибор складывается из базисной базы, в ней зафиксирован микроболт с измерительными границами в 25 мм, кроме этого имеется заменяемые измерительные вставки разной длины. Предельный показатель замеров — 300 мм.
Такие устройства так же, как МК, являются механическими, цифровыми устройствами. Неточность замеров с минимальной вставкой — 5 мм.
Погрешность включает в себя: Неточность измерительного узла. Неточности плоскостности, параллельности винта с пяткой. Они появляются при поворотных углах, стопорении. Таковой вид неточности бывает разнообразным в разнообразных формах (круглых, плоских).
Кроме этого имеется неточности объектов при упрочнении на протяжении замера. Изменение скобы благодаря упрочнения. Неправильность мер установки. Неточность благодаря действия температуры, она характерна для громадных устройств.
В электронных устройствах может появиться неисправность электродеталей. Погрешность допускается для головки, в случае если она выступает отдельным устройством, в пределах установленных ГОСТом 6507-90.
Имеется особые совокупности с границами погрешностей для устройств, Они имеют показатели, зависящие от границ замеров. Сетка неточностей показывает на допускаемую неточность G прибора в пункте границ замеров.
Эти граничные показатели складываются из неточности микрометрического узла, неточности от деформации скоб прибора, от бугристости, непараллельности замеряемых плоскостей. http://youtu.be/p8lpJDR0g-8 Калибрование, настройку (поверку) микрометра делают, применяя показатели концевых мер в нескольких пунктах границ замеров, соответственно, ISO 3611:2010, DIN 863, ГОСТ 6207-90. Они берутся, дабы определить значение G, другими словами предельную неточность устройства во всех пунктах диапазона замеров.
Вот стандартные, желательные параметры под концевые меры замеров, под настройку устройства: 3,1; 6,5; 9,7; 12,5; 15,8; 19,0; 21,9; 25 мм. Возвратиться к оглавлению Подведение итогов Проверяются неточности плоскостности-параллельности торца болта с пяткой при помощи трех, четырех плоскопараллельных оптических пластинок из стекла, вертикально калиброванных в 1/4 либо 1/3 хода микроболта (0,5 мм).
Так, проверятся 3 либо 4 места с полным его поворотом. Дабы осуществить поверку микрометра, плоскость фиксируют между винтовым торцом и пяткой.
Сдвигая ее между измеряемыми плоскостями, определяют предельное число интерференционных колец на одной таковой плоскости. К числовому результату додают количество колец второй измерительной плоскости.
В случае если световая волна имеет 640 Нм, то ширина одной полосы будет около 0, 32 мкм. Рекомендуется применять под поверку калибрование сертифицированные меры.
Нужно учесть, что МК имеют хорошую прослеживаемость при поверке погрешности либо калибровке по сертифицированным мерам. http://youtu.be/y6DxYP6RG2E МК — это достаточно универсальный прибор. Его производят с усовершенствованными видами конструкций рабочих элементов, благодаря которым возможно замерять подробности разных нестандартных размеров, к примеру, зубчатые поверхности.
3-2 Измерения микрометром (Measurements with a micrometer)
Вы прочитали статью, но не прочитали журнал…
stonemoscow.ru
Погрешности микрометров – Энциклопедия по машиностроению XXL
Погрешность отсчетного устройства 0,5 погрешность микрометра, включая отсчетное устройство, 0,002 мм [c.78]Погрешности микрометров со вставками для метрических и дюймовых резьб при проверке их по аттестованным резьбовым калибрам не должны превышать величин, указанных в табл. 26. [c.655]
В этих случаях лучше пользоваться термином действительное значение измеряемой величины , т. е. значение, определенное с погрешностью, которой можно пренебречь в условиях поставленной задачи (например, исследование погрешности микрометра с по-мош,ью плитки высокого класса точности). По М. Ф. Маликову [104] под истинным значением измеряемой величины понимается ее значение, свободное от погрешностей измерений. [c.69]
Концевые меры 4-го, 5-го и 6-го разрядов, по которым определяется суммарная погрешность микрометров, подбираются так, чтобы проверка была произведена [c.98]
Погрешность микрометра Концевые меры длины 5-го разряда или 2-го класса точности. При проверке микрометра пользуются плоскими вставками или плоской и шаровой вставками Погрешность микрометра должна находиться в пределах [c.267]
Суммарная погрешность микрометра с резьбовыми вставками [c.268]
Примечания 1. Допустимые погрешности микрометров для наружных измерений — см. табл. 14, микрометрических нутромеров — см. табл. 15. [c.428]
Допустимые погрешности микрометров [c.428]
Допустимые погрешности микрометров со вставками приведены в табл. 36. [c.438]
Суммарную погрешность микрометров проверяют по концевым мерам, причем для микрометров нулевого класса берут концевые меры первого класса, для микрометров первого класса — концевые меры второго класса и для микрометров второго класса — концевые меры третьего класса. [c.35]
Допускаемая погрешность микрометров класса точности 1 составляет 4 мкм для диапазона измерений О…100 мм 5 мкм для диапазона 100…200 мм 6 мкм для диапазона 200…300 мм 8 мкм для диапазона [c.41]
Погрешность микрометров и микрометрических глубиномеров определяют по концевым мерам длины класса точности 2-го или 5-го разряда. Показания микрометрических головок проверяют в точках шкалы, равных 5,12 10,24 15,36 и 25 мм. Микрометры при поверке укрепляют в стойке, а глубиномеры устанавливают на двух концевых мерах, притертых к стеклянной пластине или плите. Погрешности микрометрических головок нутромеров и суммарные погрешности микрометрической головок нутромеров и суммарные погрешности микрометрической головки с присоединенными удлинителями определяют на горизонтальном оптиметре или измерительной машине. Точки поверки показаний такие же, как у микрометров. [c.47]
В гл. I был рассмотрен винтовой окулярный микрометр. Преимуществом спирального микрометра является то, что зубчатая пара поворота сетки не несет измерительные функции. Погрешности микрометра обусловливаются местными ошибками нанесения шкал и спирали, эксцентрицитетом оси вращения подвижной сетки относительно центра спирали и возможным наклоном подвижной сетки. [c.100]
Верхние пределы измерения в мм Суммарная погрешность микрометров в микронах ( ) Допустимая непараллельность в микронах измерительных поверхностей микрометра Изгиб скобы в микронах при усилии в 1 кг [c.638]
Погрешности микрометров со вставками для метрической и дюймовой резьбы при поверке их по аттестованным резьбовым кали- [c.638]
При проверке суммарной погрешности микрометра сопоставляются его показания с размерами блоков мер. [c.95]
Определим погрешность микрометра, если 5 = 0,5 мм, 0 = 20 мм, А/=0,1 мм. Погрешность от ввода угла поворота винта определится по формуле (7.7) [c.77]
Таким образом, погрешность микрометра примерно в 100 раз меньше погрешности входной величины А1. [c.78]
Допуск на длину установочной меры равен половине допускае .юй погрешности микрометра. [c.421]
Допустимые погрешности микрометров (1-го класса точности) в мк [c.723]
Допустимые погрешности микрометров даны в табл. 6. [c.32]
Предельная погрешность микрометров зависит от верхних пределов измерения и может составлять от 3 мкм для микрометров с пределом измерения О—25 мм до 49 мкм для микрометров с пределом измерения 400—500 мм. [c.102]
Допустимые погрешности микрометров (по гост 6507-60) [c.347]
В ЭТИ погрешности входят как инструментальные погрешности микрометра — систематические и случайные, так и неизбежные погрешности установки и неточности отсчета. Однако сюда не должны входить погрешности формы измеряемой поверхности, а также температурные погрешности при отклонениях температуры от нормальной (20° С). [c.279]
Зазор шпинделя в застопоренном состоянии превышает суммарную погрешность микрометра. [c.263]
Каждый ИЗ перечисленных факторов по разному влияет на результат измерения. Одни факторы при повторных измерениях одного и того же объекта сказываются на систематической составляющей, другие – на случайной составляющей погрешности. В связи с этим общую погрешность микрометра можно представить в следующем виде [c.102]
Описать методику исследований погрешности микрометра и методику обработки результатов измерений с использованием гармонического анализа. [c.106]
Выбираем измерительные средства уточненным методом. По табл. П28 в интервале размеров 80. .. 120 мм для седьмого квалитета находим погрешность измерения Д , = 10 мкм. Затем по табл. 5.2 по найденному значению Дм и заданному диаметру определяем, что для контроля вала может быть применен микрометр. [c.68]
Для контроля резьб с D > 100 мм применяют одну проволочку. В цеховых условиях и прн ремонте используют микрометры с резьбовыми вставками (рис. 12.14, Э). Погрешность этого метода 0,025— 0,2 мм. [c.299]
Очень удобны для измерения больших величин износа микрометрические инструменты, которые могут быть встроены в различного вида скобы, приспособления, измерительные приборь/. Допустимые погрешности микрометров колеблются в пределах 4—10 мкм в зависимости от верхних пределов измерений. Суш,сствуют следуюш,ие типы микрометров рычажный, рычажно-винтовой, рычажно-пружинный, рычажно-зубчатый, зубчатый. [c.200]
Следовательно, отсчетная и оптическая системы должны быть таковъ , чтобы соотношение между увеличением и погрешностью микрометра было не менее [c.307]
Пределы допускаемой погрешности микрометра 0,0 04 мкм Погреш10сть микрометра не более 0,10 мм. . . [c.332]
Для микрометрических штихмассов установлены только 1-й и 2-й классы точности. Допустимые суммарные погрешности штихмасса равны допустимым суммарным погрешностям микрометров соответствующих классов. Для размера 1500 мм [c.99]
Вернемся к оценке погрешностей измерений и сравним ее с оценкой погрешностей средств измерений. Если измерения уже произведены, случайные погрешности реализовались. Поэтому их можно складывать с систематическими погрешностями статистически. В примере из предыдущей беседы случайная погрешность измерения суммировалась с потенциальной погрешностью микрометра (последняя могла быть и систематической) не арифметически, а геометрически, так как гипотенуза всегда короче суммы катетов. [c.120]
При исследовании погрешностей микрометра с использованием гармонического анализа по 24 ординатам необходимое число измерений п,п – 24. Тогда шаг дискретизации Дх = 25/24 = 1 мм иМо= ПтПа = 24-4 = 96. [c.104]
Резьбовые микрометры со вставками позволяют измерять средний диаметр резьбы непосредственно в процессе ее изготовления. Резьбовой микрометр отличается от обычного тем, что в пятке и в стержне микрометрического впита имеются отверстия, в которые устанавливают призматическую / и коническую 2 вставки с углами, равными уьлу профиля резьбы. Для того чтобы вставки не выпадали, их хвостовики имеют прорези (рис. 14.12). К каждому микрометру прилагают комплект вставок для измерения резьб в определенном интервале шагов. Призматические вставки вставляют в отверстие пятки, а конические — в отверстие микрометрического винта. Одну из вставок (призматическую) устанавливают на выступ профиля резьбы, другую — в канавку резьбы, и поэтому микрометр располагается перпендикулярно оси резьбы. Погрешность контроля резьбовым микрометром может доа 11-гать 0,2 мм. [c.178]
Измерение длины общей нормали. Измерением длины общей нормали по колесу Х 1 (см. рис. 16.2, г) можно выявить погрешность обката, зависящую от неточности делительной червячной пары зубо-обрабатывающих станков. Среднее значение длины общей нормали характеризует смещение исходного контура Анг- Длину общей нормали можно проверять (для повышения точности измерений) штангенциркулем, микрометром с тарельчатыми наконечниками (рис. 17.5, а) или нормалемерами (рис. 17.5, б). Нормалемер состоит из полой штанги /, на которую насажена разрезная втулка 2, имеющая ) естко закрепленную измерительную губку 3. В корпусе б установлена подвижная губка 4, которая может совершать небольшие по- [c.213]
Измерение зубчатых колес при помощи двух роликов В две диаметрально расположенные впадины проверяемого колеса помещают ролики расстояние Л/т между крайними точками их цилиндрических поверхностей измеряют микрометрами. По размеру Мт вычисляют толш ину зуба. Этот метод не требует специальных измерительных средств на точность измерения не влияют погрешности окружности вершин зубьев. [c.187]
Величину /р называют диаметральной компенсацией погрешностей шага резьбы и определяют по формулам (ДР п fp в микрометрах) для метрической резьбы (а = 60″) fp = 1,732ДР для трубной резьбы (а = 55″) fp = 1,921 ДР для трапецеидальной резьбы (а = 30″) /р= 3,732AP для упорной резьбы ( = 30° у = 3″) /р – 3,175ДР . [c.279]
Для измерения размера М используют длиномеры, оптиметрьч микрометры и т. п. При измерении на горизонтальном оптиметре (см. рис. 12.14, е) обеспечивается погрешность измерения 1,5— [c.299]
mash-xxl.info
Микрометры гладкие – основные характеристики, диапазон измерений
Микрометр – это профессиональный ручной измерительный инструмент с точностью до 0,01 мм. Микрометр используется для определения длин и наружных диаметров изделий малого размера (до 1000 мм). Наиболее широко используемыми являются микрометры гладкие (МК) состоящие из скобы с пяткой, винта с мелкой резьбой, втулки-стебля и трещотки. На втулке-стебле расположены две шкалы с точностью делений в 1 и 0,5 мм. Шкала с точностью до сотых долей миллиметра расположена на конической части барабана.
Методика измерений микрометром гладким
Для получения точного размера измеряемое изделие необходимо разместить и неподвижно зафиксировать с помощью трещотки между пяткой и винтом. При этом нельзя измерять грубо обработанные поверхности покрытые слоем ржавчины, металлической пыли или окалины. Не следует работать и с нагретыми деталями, из-за температурного расширения вы не получите точный результат. Трещотку барабана необходимо вращать медленно и аккуратно.
Показание с микрометра снимаются в следующем порядке:
- шкала стебля с точностью 1 мм,
- шкала с точностью 0,5 мм;
- шкала барабана.
Три полученных результата складываются и получается точное значение.
Диапазон измерений микрометром гладким
Из-за ограничений хода винта с точной резьбой микрометры гладкие выпускаются в определенных диапазонах измерений – от 0 до 25 мм и до 900-1000 мм. Верхняя граница измерений указана в обозначении прибора: МК-25 – от 0 до 25 мм, МК-50 – от 25 до 50 мм и т. д. вплоть до МК-1000 – от 900 до 1000 мм. Все инструменты от МК-50 и более имеют в комплекте установочную концевую меру для установки «на ноль». Есть и приборы с цифровой индикацией существенно облегчающей проведение измерений.
Помимо диапазона измерений, важной характеристикой гладкого микрометра является его класс точности – 1-й или 2-й. От него зависит предел допустимой погрешности прибора. В зависимости от диапазона измерений приборы с 1 классом точности имеют погрешность от 2 до 6 мкм, со 2 классом точности – от 4 до 10 мкм.
Точность измерения является залогом правильного изготовления деталей. Поэтому мы, Интернет-магазин «Мекка Инструмента» предлагаем только точные и проверенные измерительные инструменты от известных российских и зарубежных производителей. Вас ожидает широкий ассортимент предложений, профессиональные консультации, приятные цены и быстрая доставка в любой регион России.
mekkain.ru
Выбор измерительных средств. Приемы и точность измерений: штангенглубиномер, микрометрический нутромер, резьбовой микрометр, резьбомеры
Большое разнообразие объектов измерений приводит к большому разнообразию контрольно-измерительных инструментов и приборов, а также методов и приемов измерений. Вместе с тем в зависимости от назначения отдельных деталей машин, измерения необходимо производить с различной точностью. В одном случае достаточно воспользоваться обычной масштабной линейкой, а в другом — применить точный прибор, дающий возможность произвести измерение с точностью до величины ±0,01 мм.
Допустим, требуется замерить диаметр поршня. Его можно замерить кронциркулем и масштабной линейкой, штангенциркулем и микрометром. В первом случае точность измерений соответствует величине —0,5 мм, во втором — от 0,1 до 0,05 мм, а в третьем — 0,01 мм.
Нормальные условия выполнения линейных и угловых измерений установлены ГОСТ 8.050-73. Погрешности, допускаемые при измерении линейных размеров от 1 до 500 мм, в зависимости от допусков и номинальных размеров изделий регламентированы в ГОСТ 8.051-73. Предел допускаемой погрешности измерения учитывает влияние погрешности измерительных средств, установочных мер, температурных деформаций, метода измерения и т. д. Результат измерений с погрешностью, не превышающей допускаемую, принимают за действительное значение.
Основные факторы, влияющие на выбор средства измерения, — это размер и квалитет (класс точности) измеряемого изделия, допускаемая погрешность средства измерения, условия и метод использования средства измерения.
Раздвижной измерительный инструмент с линейным нониусом. Штангенциркуль — многомерный раздвижной инструмент с нониусом* для измерения наружных и внутренних размеров, диаметров, глубин и высот деталей. Конструкции выпускаемых штангенциркулей позволяют производить отсчет размеров с точностью до 0,1 и 0,05 мм. Такая высокая точность достигается применением специального устройства для отсчета — линейного нониуса.
На рис. 129 изображен штангенциркуль (универсальный) с точностью измерений до 0,1 мм ГОСТ 116-89. Он состоит из штанги 1, на которой нанесена шкала линейки, губок 2 и 9 и перемещающейся по штанге рамки 7 с губками рамки 3 и 8.
Рис. 129
Измеряемый предмет слегка зажимают между губками, фиксируют рамку зажимным винтом 4 и затем по шкалам штанги и нониуса производят отсчет размера. В пазу обратной стороны штанги свободно скользит линейка 5 глубиномера, представляющая собой плоский стержень. Один конец ее жестко соединен с рамкой. В сомкнутом положении свободный торец линеики глубиномера точно совпадает с торцом штанги. При измерении глубины штанга торцом устанавливается на плоскость детали у измеряемого отверстия. Нажимом на рамку стержень глубиномера перемещают до упора в дно отверстия и затем фиксируют положение рамки зажимным винтом.
Отсчет размеров производят по штанге и нониусу. Нониус длиной 19 мм разделен на 10 частей. Одно его деление, таким образом, составляет 19/10 = 1,9 мм, что на 0,1 мм меньше целого миллиметра (рис. 130,I). При нулевом показании штрих нониуса находится от ближайшего справа штриха штанги на расстоянии, равном величине отсчета 0,1 мм, умноженной на порядковый номер штриха нониуса, не считая нулевого (рис. 130, II). Целое число миллиметров отсчитывается по шкале штанги слева направо нулевым штрихом нониуса. Дробная величина (количество десятых долей миллиметра) определяется умножением величины отсчета ОД мм на порядковый номер штриха нониуса (не считая нулевого), совпадающего со штрихом штанги.
На рис. 130, III показано два примера отсчета. В первом по шкале штанги читаем целое число 39 мм, затем по шкале нониуса определяем дробную величину 0,1 мм х 7 = 0,7 мм (седьмой штрих обозначен крестиком). Значит, замеряемый размер 39 мм + 0,7 мм = 39,7 мм. Во втором примере аналогично первому определяем 61 мм + 0,1 мм х 4 = 61,4 мм.
Рис. 130
Точность отсчета в 0,1 мм иногда бывает недостаточной. В этом случае пользуются штангенциркулем, позволяющим производить измерение с точностью до 0,05 мм.
Штангенглубиномер (ГОСТ 162-90) (рис. 131) предназначен для измерения глубины глухих отверстий, пазов, канавок, уступов и высот с величиной отсчета по нониусу 0,1 и 0,05 мм. Он отличается от штангенциркуля только конструкцией: штанга заканчивается срезанным торцом, являющимся измерительной поверхностью, рамка имеет вместо губок широкую опорную поверхность — основание 1.
Рис. 131
При измерениях штангенглу- биномер основанием устанавливают над отверстием, а штангу выдвигают до упора в его дно. Далее все действия аналогичны операции по замеру детали штангенциркулем.
Микрометрический измерительный инструмент. Микрометр (ГОСТ 6507-90) — более сложный по устройству инструмент, чем рассмотренные раньше (рис. 132). Он позволяет производить измерения с большей точностью.
Рис. 132
Микрометр для наружных измерений состоит из подковообразной скобы 1, пятки 2, стебля 5, зажимного устройства — стопора 4, барабана 6 с микрометрическим винтом 3, колпачка 7 с насечкой, навинченного на правую часть барабана, и трещотки, присоединенной при помощи винта к торцу шейки колпачка. Отсчеты измерений производятся по шкале на стебле 5 и шкале на коническом нониусе барабана 6.
Шкала на стебле имеет 25 делений, нанесенных вдоль оси стебля сверху и снизу и перпендикулярных к ней с расстоянием между ними в 1 мм. Штрихи, расположенные над риской, смещены вправо относительно нижних штрихов на 0,5 мм. По ,нижним штрихам отсчитывают целое число миллиметров, а по верхним — 0,5 мм. Сотые доли миллиметра определяются при помощи делений на нониусе, поверхность которого разделена штрихами в виде образующих нониуса на 50 равных частей.
При повороте на одно деление микрометрический винт 3, соединенный с барабаном 6, перемещается вдоль оси на 1/50 шага, т. е. на расстояние, равное 0,5 мм : 50 = 0,01 мм.
Для определения какого-либо размера детали микрометром ее помещают между пяткой 2 и торцом микрометрического винта 3. Затем поворачивают барабан до тех пор, пока торец микрометрического винта не приблизится к поверхности детали. Дальнейшее продвижение винта 3 производят при помощи колпачка 7 с трещоткой. Услышав характерный треск, подобный треску пружины часов при заводе, поворот колпачка прекращают. После этого стопором 4 стопорят микрометрический винт, отделяют микрометр от детали и считывают показания.
Отсчет показаний производят следующим образом (рис. 133): если кромка барабана остановится ближе к нижнему штриху стебля (рис. 133, I), то число целых миллиметров полученного размера определяют по нижнему делению шкалы, а Число сотых долей миллиметра — по показаниям барабана. Так, приведенное на рисунке положение шкал соответствует размеру 8 + 0,24 = 8,24 мм;
Рис. 133
если кромка барабана остановится ближе к верхнему штриху стебля, то полученный размер представит сумму трех величин: числа целых миллиметров до ближайшего нижнего к кромке барабана деления на стебле плюс 0,5 мм от него до верхнего деления и плюс показания сотых долей миллиметра по барабану. В приведенном случае (рис. 133, II) положение шкал соответствует размеру 8 + 0,5 + 0,24 = 8,74 мм. На рис. 134 показаны приемы измерения деталей микрометром.
Рис. 134
Микрометрический нутромер (штихмас) (ГОСТ 10-88) служит для измерения внутренних размеров деталей, а также размеров диаметров отверстий. Точность измерений нутромером такая же, как и микрометром — 0,01 мм. Состоит он (рис. 135) из головки и сменных калиберных стержней (удлинителей). Микрометрическая головка состоит из микрометрического винта 6, расположенного внутри барабана 4, колпачка 5, стебля 3, стопорного устройства 2 и сменного наконечника 1. С помощью сменных наконечников (удлинителей) увеличивают предел измерений.
Рис. 135
Считывают размеры при пользовании зтим инструментом так же, как и при замерах микрометром.
Инструмент для измерения углов и конусов. Размеры углов, как и все другие, могут иметь допуски. Верхнее и нижнее отклонения угловых размеров располагают на чертежах так же. как и линейных размеров. Например, означает угол с номинальным размером 90°, верхнее допустимое отклонение которого равно 10°, а нижнее — 8°. Когда размеры углов на чертежах не имеют допусков, их устанавливают в соответствии с отраслевыми стандартами.
Для измерения углов и конусов применяют различные инструменты. Рассмотрим некоторые из них.
Универсальный угломер (ГОСТ 5378-88) (рис. 136) применяют для измерения наружных и внутренних углов различных деталей.
Рис. 10
Угломер состоит из основания 1, на котором нанесена основная шкала на дуге 130°, и жестко скрепленной с ним линейки 4. По дуге основания перемещается сектор 3, несущий нониус 2. К сектору 3 посредством державки 7 может быть прикреплен угольник 6, в котором в свою очередь с помощью державки 8 закреплена съемная линейка 5. Угольник 6 и съемная линейка 5 имеют возможность перемещаться по краю сектора 3.
Хотя основная шкала угломера нанесена лишь на дуге 130°, но, меняя установку измерительных деталей, можно измерять углы от 0 до 320°. Точность отсчета по нониусу равна 2′. Отсчет, полученный при измерении угловых величин или при установке заданного угла, производится так же, как и на линейных шкалах штангенинструмента, т. е. по шкале и нониусу. Число градусов отсчитывают по шкале основания, а минут — по шкале иониуса.
Например, на рис. 137 нулевой штрих нониуса пришелся на деление между 76 и 77° основной шкалы, а со штрихом (отмечен крестиком) шкалы основания совпадает 9-й штрих нониуса. Следовательно, по основной шкале отсчитывают 76°, а по шкале нониуса 9 х 2′ = 18′. Значит, угол в данном случае равен 76°18′.
Рис. 137
Калибры и шаблоны. Предельные калибры —скобы ГОСТ 16775-71…16777-71 применяют для контроля наружных диаметров валов по предельным размерам.
Предельная скоба имеет две стороны с размерами: наибольший допустимый ПР — проходная сторона и наименьший допустимый НЕ — непроходная сторона.
На рис. 138 показана схема и прием контроля измеряемого диаметра вала 1 проходной скобой; 2 — непроходная скоба; 3 — проходная скоба. Разница между этими размерами составляет допуск на размер диаметра контролируемого вала. Сторона скобы НЕ делается по наименьшему допустимому размеру диаметра таким образом, чтобы вал не проходил через нее. Действительный размер диаметра вала при этом виде контроля установить нельзя. Нельзя также установить действительный размер отклонений от геометрических форм вала, т. е. овальность, конусность и т. д. Для определения действительного размера диаметра вала и действительных отклонений, выраженных в числовых значениях, следует применять универсальные измерительные средства.
Рис. 138
Предельные калибры — пробки (рис. 139) применяют для контроля цилиндрических отверстий ГОСТ 24962- 81, для определения соответствия размера диаметра отверстия заданным на чертеже пределом (допуском). Принцип контроля этим калибром аналогичен предыдущему.
Рис. 139
Для проверки цилиндрической крепежной резьбы II применяют рабочие, приемные и контрольные калибры ГОСТ 24963-81. Рабочие калибры используют для проверки правильности размеров резьбы изделий в процессе их изготовления. Приемные калибры — для проверки правильности размеров резьбы контролерами и заказчиками. Контрольные калибры (контркалибры) — для контроля и регулировки (установки) размеров рабочих калибров.
Шаблоны широко распространены в машиностроении для проверки деталей сложного профиля. Профиль шаблона (отсюда название профильный калибр — шаблон) по идее представляет собой ту идеальную форму, которую следует придать детали. Проверка шаблоном заключается в прикладывании его к изделию и оценке величины световой щели между проверяемым профилем и измерительной кромкой шаблона. Шаблонами контролируют профиль зубьев зубчатых колес I и зубьев ходовых резьб II, профиль кулачков и шпоночных пазов, радиусы скруглении, углы заточки режущего инструмента и др. (рис. 140).
Рис. 140
Шаблоны профильные служат для определения отклонений действительного профиля зуба от теоретического. Проверка заключается в накладывании шаблона на зуб колеса и определении отклонения по величине световой щели на просвет. Такая проверка не дает числового выражения отклонения, но во многих случаях бывает достаточной.
Кроме специальных шаблонов индивидуального назначения, в производстве используют еще и нормализованные шаблоны. Один из них ГОСТ 4126-82 показан на рис. 141. Он представляет собой набор стальных пластинок с закругленными по определенному радиусу (отмеченному на пластинках) концами. Данный радиусомер имеет комплект пластин для замера радиусов от 1 до 6,5 мм. Промышленность располагает радиусомерами и большего размера.
Рис. 141
Измерение цилиндрических резьб. Наиболее ходовыми средствами измерения и контроля резьбы являются резьбовой микрометр и резьбомеры.
Резьбовой микрометр ГОСТ 4380-86 предназначен для измерения среднего диаметра наружной резьбы на стержне (рис. 142,I). Внешне он отличается от обычного только наличием измерительных вставок: конусного наконечника, вставляемого в отверстие микровинта и призматического наконечника, помещаемого в отверстие пятки. Вставки к микрометру изготовляются парами, каждая из которых предназначена для измерения крепежной резьбы с углом профиля 55 или 60° с определенным шагом. Например, одна пара вставок применяется в тех случаях, когда надо измерить резьбу с шагом 1… 1,75 мм, другая — 1,75 … 2,5 мм и т. д.
Рис. 142
После установки микрометра на нуль вставками как, бы обнимается один виток проверяемой резьбы (рис. 142, II). После того как вставки вошли в соприкосновение с поверхностью резьбы, стопорят микрометрический винт и отсчитывают результат по шкалам микрометрической головки (рис. 142, III).
Резьбомеры ГОСТ 519-77 (рис.143) применяют для измерения шага резьбы. Это наборы шаблонов (тонких стальных пластинок), измерительная часть которых представляет собой профиль стандартной резьбы определенного шага или числа ниток на дюйм для подсчета шага. Резьбомеры изготавливают двух типов: на одном из них № 1 выбито клеймо «М60°», на другом № 2 — «Д55°».
Рис. 143
Для измерения шага резьбы подбирают шаблон-пластинку (гребенку), зубцы которой совпадают с впадинами измеряемой резьбы. Затем читают указанный на пластинке шаг или число ниток на дюйм. Для определения шага по резьбомеру № 2 требуется дюйм — 25,4 мм разделить на число ниток, указанное на шаблоне.
Наружный диаметр резьбы <2 на стержне или внутренний диаметр резьбы D1 в отверстии измеряют штангенциркулем. Зная два этих исходных параметра, подбирают точное значение резьбы по сравнительным таблицам стандартных резьб.
Измерение элементов зубчатых колес. На чертеже зубчатых колес всегда задают размер толщины зуба (длину хорды) как расчетную величину.
Штангензубомер — инструмент для замера толщины зуба у зубчатых колес (рис. 144). Он состоит из двух взаимно перпендикулярных линеек 1 и 5 со шкалами. Линейка 1 служит для установки заданной высоты, а линейка 5 для измерения толщины зуба — длины хорды по этой высоте. Заметим, что толщина зуба, замеряемая по хорде делительной окружности, всегда находится на определенном расстоянии от окружности вершин зубьев, что на чертеже специально оговаривается.
Рис. 144
В начале измерения упор 3 устанавливают при помощи нониуса 2 на размер заданной высоты и фиксируют его стопорным винтом. Штангензубомер упором 3 ставят на окружность вершины зуба, который собираются замерить. Затем сдвигают губки горизонтальной линейки до соприкосновения с профилем зуба, после чего по шкале нониуса 4 отсчитывают размер толщины зуба, так же как и при измерении штангенциркулем.
Обычно, когда говорят о точности обмера, подразумевают под этим то максимальное отклонение от истинного размера, которое может получиться при измерении. Например, точность измерения ± 0,02 показывает, что истинное значение может отличаться от прочитанного на шкале инструмента максимум на 0,02 мм. Эта величина характеризует измерительный инструмент, но для практики она неудобна, так как не дает прямого указания, когда в сложившихся обстоятельствах и каким инструментом следует производить измерение. В этом случае удобнее связать тип инструмента с размером допуска. Допуск всегда указан на чертеже. При отсутствии чертежа величину допуска выбирают в зависимости от характера сопряжения данной детали с другими.
Таблица 15
Измерительный инструмент для внешнего промера
Рис. 144 А
Таблица 16
Измерительный инструмент для внутреннего промера
Рис. 144 Б
Таблица 17
Измерительный инструмент для промера глубины
Рис. 144 В
В табл. 15, 16 и 17 (рис. 144 А, В и В) приведены рекомендации по применению измерительного инструмента со шкалами в зависимости от установленных допусков и размеров детали. В ней даны верхние пределы применения инструмента, т. е. наименьшие допуски, которые могут быть промерены данным инструментом. Каждый из приведенных в таблице типов инструмента может быть применен и для более грубых промеров.
Совершенствование методов и средств технического контроля осуществляется путем механизации и автоматизации контрольных операций и применением так называемого активного контроля, позволяющего проверять размеры деталей во время их обработки. Прогрессивные средства контроля выбирают исходя из экономической эффективности их применения. Для механизации контрольных операций применяют многомерные контрольные приспособления и различные механические устройства.
В таких многомерных приборах и приспособлениях используются различные жесткие калибры, индикаторы и устройства, основанные на пневматических, электроконтактных и других способах измерения.
Промышленность располагает также автоматами с механическими измерительными устройствами и с электроконтактными датчиками, электроизмерительные устройства которых позволяют с высокой точностью проверять различные геометрические и физические параметры деталей.
Приборы для автоматического контроля деталей в процессе их обработки наиболее часто применяются при шлифовании валов, отверстий, плоскостей и пр. Эти приборы, устанавливаемые на станках, подают сигнал при достижении деталью заданного размера или автоматически изменяют режим обработки и останавливают станок.
* Нониус — вспомогательное отсчетное устройство, повышающее точность оценки долей делений основной шкалы измерительного инструмента
cherch.ru