Пресс ковочный – Ковочный пресс
alexxlab | 01.07.2019 | 0 | Вопросы и ответы
Ковочный пресс
Такое оборудование, как ковочный пресс, относится к кузнечно-штамповочному оборудованию. Использовать такие махины на предприятиях приема металлолома нецелесообразно — они имеют большие габариты и высокую стоимость. Эти прессы используются на металлургических комбинатах при изготовлении проката из переработанного лома.
Конструкция
Рассматриваемое оборудование относится к гидропрессам, которые осуществляют деформированием в результате силового воздействия несжимаемой рабочей жидкости. Чаще всего применяется масло типа «Индустриальное 20», хотя иногда в качестве рабочей жидкости используют и воду (вариант значительно более дешёвый, однако вызывающий коррозию рабочих деталей пресса).
Ковочный пресс может иметь рамную или колонную конструкцию. В первом случае привод имеет верхнюю компоновку, а во втором – нижнюю. Типовое исполнение ковочного пресса включает следующие узлы:
- Насосную установку (чаще используются насосы ротационно-плунжерного типа).
- Рабочие цилиндры, управляющие прямым, рабочим ходом машины (у мощных прессов их может быть несколько).
- Возвратные цилиндры, в результате работы которых обратный ход. Число возвратных цилиндров равно числу рабочих.
- Систему управления, которая осуществляет перекачку рабочей среды попеременно, то в рабочие, то в возвратные цилиндры.
- Силовой орган – траверсу, к которой прикрепляется штамп или инструментальная переходная плита.
- Станину, включающую в себя направляющие устройства, по которым перемещается траверса.
- Наполнительного бака – резервуара, где размещается масло.
- Сливного бака, который служит для спуска рабочей жидкости во время возвратного хода.
- Электродвигателя.
Для ковочных прессов номинальным усилием более 3150 кН в конструкции предусматривается аккумулятор — узел, производящий дополнительное повышение рабочего давления в гидросистеме. В этом случае в качестве привода применяются насосы кривошипно-плунжерного типа, более сложными являются и органы управления машиной.
В ковочных прессах относительно небольших усилий (до 3150 кН) могут применяться два исполнения столов: обычный выдвижной, либо поворотный.
Видео — работа гидравлического ковочного пресса 4000 тонн:
Ковочные прессы особо больших усилий (от 25 МН) часто строят парогидравлическими, т.е. применяют комбинированную энергию пара и жидкости высокого давления. В качестве ломоперерабатывающего оборудования подобные конструкции применяются редко.
Ковочные прессы, согласно принятому в нашей стране обозначению маркируются буквой П, после которой следует четыре цифры, причём две последние указывают на главный параметр машины – номинальное усилие, а две первых – на конструктивное исполнение оборудования.
Принцип работы
Ковочные прессы, не имеющие аккумуляторов, работают так. Масло от питающего насоса поступает в рабочие цилиндры. На линии высокого давления предусматривается установка предохранительного клапана, который регулирует текущий расход масла. Этим обеспечивается постоянство рабочего давления в напорной магистрали пресса. Пропускная способность клапана соответствует номинальной производительности насосной установки.
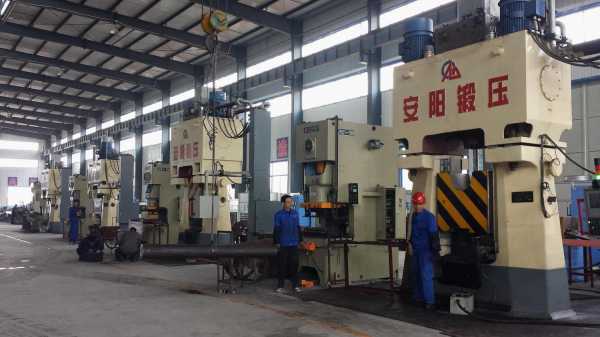
Цех с ковочными прессами в Китае
При переключении управляющего элемента – золотника – масло перетекает в возвратный цилиндр, для того, чтобы поднять траверсу пресса. Безопасность трубопроводов высокого давления обеспечивает предохранительный клапан, при помощи которого устанавливается ход траверсы.
Отличительной особенностью гидравлических и парогидравлических ковочных прессов является возможность поддержания номинального усилия на траверсе в течение необходимого промежутка времени. Эта функция особенно полезна при спрессовывании металлоконструкции, подлежащей утилизации, поскольку помогает преодолеть механическую инерцию деформируемого материала.
При переключении управляющего золотника выполняется возвратное перемещение траверсы пресса. Для этого масло из рабочего цилиндра перекачивается в сливной бак, из которого насос перемещает его в наполнительный бак. После этого рабочий цикл можно повторять.
Ковочные гидропрессы, оснащённые аккумулятором, действуют иначе. Масло под высоким давлением поступает вначале в аккумулятор, а уже оттуда (при помощи насоса через клапанный распределитель) оно подводится то в рабочий, то в возвратный цилиндры.
Ковочные прессы могут оснащаться функцией текущего изменения скорости перемещения траверсы. Она может быть ускоренной, на начальной стадии перемещения, и замедленной, при непосредственном выполнении деформирования металла. Это увеличивает производительность оборудования.
Основные технические характеристики и обслуживание
ГОСТом на ковочные прессы нормируются следующие показатели:
- Номинальное усилие, МН;
- Максимальное значение хода траверсы/рамы, мм;
- Размеры рабочей зоны в свету (между направляющими колоннами), мм;
- Габариты рабочего стола (для столов выдвижного исполнения регламентируется также и его ход), мм;
- Число ходов траверсы в минуту, которое обычно указывается отдельно для номинального усилия, а также при усилиях в 25% и 75% от номинального;
- Мощность привода, кВт.
Надёжная работа ковочных прессов обеспечивается вследствие выполнения следующих мероприятий:
- Постоянной поверки измерительных приборов – манометров, датчиков давления и т.д.;
- Плавности срабатывания элементов системы управления, в противном случае возможно появление гидроудара, сопровождающееся разрывом трубопроводов;
- Контроля плавности перемещения траверсы и состояния направляющих элементов;
- Контроля уровня рабочей жидкости в наполнительном баке;
- Проверки работы смазочной станции, отвечающей за смазку насоса.
Видео — демонстрация работы кузнечного ковочного пресса
xlom.ru
Гидравлический пресс. Гидравлический ковочный пресс. Пресс цилиндр.
Гидравлические прессы являются кузнечными машинами статического действия. В зависимости от технологического назначения их подразделяют на ковочные, штамповочные, листоштамповочные, гибочные, профильные и др.
Привод гидравлических прессов осуществляется с помощью жидкости высокого давления, подаваемой в гидроцилиндры от насосных или насосно-аккумуляторных станций. Скорость рабочих органов в гидравлических прессах не превышает 0,5 м/с.
Ввиду отсутствия в гидропрессах механических передач эти машины имеют сравнительно простую конструкцию. Ковочные гидравлические прессы конструируют усилием до 150 МН, штамповочные – до 750 МН.
Основными узлами гидравлических прессов являются станина, подвижная поперечина, рабочие и возвратные цилиндры, стол (подвижный или неподвижный), гидравлические выталкиватели.
В верхней части станин размещается главный силовой орган пресса, развивающий основное технологическое усилие и представляющий собой один или группу цилиндров, обычно плунжерного типа. Плунжеры гидроцилиндров опираются на подвижную поперечину пресса, скользящую по колоннам станины или по направляющим. К нижней плоскости подвижной поперечины крепится верхняя половина рабочего инструмента. Нижняя половина инструмента устанавливается на столе, расположенном на нижней неподвижной поперечине.
Ход подвижной поперечины вверх осуществляется с помощью возвратных цилиндров обычно плунжерного типа. Цилиндры монтируются или на нижней или на верхней неподвижной поперечине. Плунжеры возвратных цилиндров воздействуют на подвижную поперечину.
Изучаемый гидравлический пресс усилием 2000 кН модели П-457 представлен на рисунке 1.
Рисунок 1 -Гидравлический пресс модели П-457
1 – цилиндр рабочий; 2 – плунжер; 3 – цилиндр возвратный; 4 – плунжер;
5 – колонна; 6 – гайка колонны; 7 – поперечина верхняя; 8 – поперечина подвижная;
9 – поперечина нижняя; 10 – гидроцилиндр выталкивателя; 11 – ограничитель хода
Пресс предназначен для ковки, горячей объемной и холодной листовой штамповки из углеродистых и легированных сталей, а также прессования изделий из цветных металлов и их сплавов.
Гидравлический пресс модели П-457 является одноцилиндровым. Рабочий цилиндр 1 плунжерного типа с опорой на бурт смонтирован в верхней неподвижной поперечине 7, его плунжер 2 под давлением рабочей жидкости перемещает подвижную поперечину 8 вниз. Обратный ход подвижной поперечины 8 осуществляется с помощью двух возвратных цилиндров 3 с плунжерами 4, установленных диагонально в приливах нижней поперечины прес-са 9.
Верхняя неподвижная поперечина 7 связана с основанием 9 четырьмя колоннами 5. Колонны установлены в расточках верхней поперечины и основания и жестко в них закреплены с помощью гаек 6. Таким образом, две неподвижных попе-речины (7 и 9) и четыре колонны 5 образуют жесткую пространственную конструкцию, внутри которой расположена подвижная поперечина 8.
Колонны проходят через отверстия в подвижной поперечине и служат для неё направляющими. На колоннах станины у нижней поперечины смонтированы разъемные ограничители хода 11 подвижной поперечины. С их помощью предупреждается возможность аварийного выхода плунжера 2 из рабочего цилиндра 1. В нижней попе-речине по оси пресса смонтирован выталкиватель в виде гидроцилиндра 10. Пресс установлен на бетонном фундаменте и скреплен с ними анкерными болтами. Привод пресса – насосный, рабочая жидкость – водная эмульсия, номинальное рабочее давление – 20 МПа.
Устройство рабочего цилиндра пресса показано на рисунке 2. Рабочий цилиндр пресса состоит из следующих деталей: литого корпуса 1 цилиндра (сталь 35Л), рабочего плунжера 2, направляющей бронзовой втулки (буксы) 3, уплотнительных шевронных манжет 4, нажимной втулки 5, фланца 6, поджимаемого гайками 7 на шпильках 8. В верхней части цилиндра имеется отверстие 9 для подвода рабочей жидкости. Снаружи корпуса цилиндра в его нижней части имеется бурт 10, которым рабочий цилиндр опирается на станину при воздействии плунжера на поковку. От выпадения из верхней поперечины вниз рабочий цилиндр удерживается фланцем (на рисунке 2 не показан).
Рабочим пространством пресса является пространство (см. рисунок 1) между подвижной и нижней неподвижной поперечинами (по вертикали) и между ходоограничителями 11 колонн в свету (по горизонтали). В этом пространстве устанавливаются рабочие бойки (при ковке) или штампы (при штамповке).
При подаче жидкости от насоса в рабочий цилиндр пресса поперечина движется вниз, совершая сначала холостой ход (ход приближения к поковке), а затем рабочий ход. Жидкость из возвратных цилиндров при этом вытесняется в сливной бак. После совершения рабочего хода жидкость от насоса подается в возвратные цилиндры, а рабочий цилиндр соединяется со сливным баком, и подвижная поперечина 8 совершает возвратный ход. Управление потоками жидкости осуществляется с помощью клапанного распределителя и рукоятки управления.
Рисунок 2 — Рабочий цилиндр пресса
1 – цилиндр; 2 – плунжер; 3 – втулка направляющая;
4 – манжета уплотнительная; 5 – втулка нажимная; 6 – фланец; 7 – гайка;
8 – шпилька; 9 – отверстие для подвода жидкости; 10 – бурт
www.mtomd.info
Ковочные прессы и их особенности
Ковочные прессы и их особенности
Категория:
Кузнечные работы
Ковочные прессы и их особенности
Ковочные прессы строят на усилия от 3 до 20 МН (300—2000 тс).
Одной из особенностей ковочных прессов является их быстроходность, которая оценивается числом ходов в минуту и скоростью подвижной поперечины. Благодаря высокой быстроходности удается получать сложные поковки с одного нагрева заготовки (или небольшого числа нагревов) и обеспечить хорошее качество изделий, а также высокую производительность пресса.
Для прессов усилием до 20 МН целесообразно использовать насосно-аккумуляторные станции с давлением 20—32 МПа. Связано это с тем, что для различных операций ковки требуется в очень широких пределах изменять скорость подвижной поперечины. При насосном приводе скорость определяется подачей насосов. К сожалению, пока еще нет насосов большой производительности с достаточно глубокой регулировкой подачи.
В ковочных прессах наиболее широко используются четырех-колонные станины, причем колонны располагают по углам прямоугольника с отношением сторон, равным 2 : 3. Это обеспечивает удобство маневрирования заготовкой. Четырехколонный ковочный пресс усилием 60 МН (6000 тс) показан на рис. 1. В небольших ковочных прессах станина иногда выполняется одностоечной, что обеспечивает подход к заготовке с трех сторон.
Максимальное расстояние между столом и подвижной поперечиной у ковочных прессов достаточно велико, что позволяет осаживать высокие слитки и производить раскатку колец.
Ковочные прессы больших усилий обычно обеспечиваются выдвижным столом для инструмента и облегчения маневрирования заготовкой. Кроме того, они оборудуются выталкивателями. Усилие цилиндров привода стола и выталкивателя обычно составляет 2—6 % от усилия пресса.
В мощных прессах используют, как правило, не один, а два-три рабочих цилиндра, что упрощает изготовление последних. Кроме того, трехцилиндровая конструкция позволяет получать три ступени усилия, подавая давление в один центральный, два крайних или во все три цилиндра. В результате повышается экономичность работы пресса при ковке заготовок, не требующих полного усилия.
Рис. 1. Четырехколонный ковочный пресс усилием 60 МН (6000 тс):
1 — выталкиватель. 2 — верхняя поперечина. 3 — подвижная поперечина. 4 — основание
Рис. 2. Схема верхней части пресса с центральным хвостовиком:
1 — подвижная поперечина, 2 — хвостовик. 3 — верхняя поперечина
Рис. 3. Схема верхней части пресса с плунжером-хвостовиком:
Конструкция ковочного пресса должна допускать возможность работы с эксцентричным приложением нагрузки. При таком нагру-жении колонны пресса не только растягиваются, но и изгибаются. Чтобы уменьшить изгиб колонн, в ряде случаев рабочий плунжер заделывают жестко в подвижную поперечину пресса. Тогда он передает изгибающий момент через цилиндр на верхнюю поперечину. Колонны частично разгружаются от изгиба, однако уплотнения в таких цилиндрах изнашиваются более интенсивно.
Для облегчения условий работы колонн применяется также конструкция, в которой подвижная поперечина имеет центральный хвостовик, закрепленный в верхней поперечине. Но в этом случае пресс имеет только два цилиндра, что не позволяет получить несколько ступеней усилий.
Этот недостаток устраняется, если хвостовик одновременно служит поршнем, но тогда центральный цилиндр имеет диаметр значительно больший, чем боковые, что неудобно при эксплуатации.
В последние годы резко повысились требования к точности обрабатываемых на прессах поковок. Для удовлетворения этих требований современные прессы оснащаются аппаратурой, которая позволяет автоматически получать нужную величину хода подвижной поперечины пресса, а следовательно, заданные размеры поковок (допуски не превышают 2—5 мм). Использование для управления такими агрегатами электронно-вычислительных машин привело к созданию нового вида оборудования — ковочных комплексов.
В качестве примера рассмотрим такой комплекс, разработанный Уральским заводом тяжелого машиностроения. В его состав помимо пресса и манипулятора входят устройство для смены основного ковочного инструмента (бойков), устройство для подачи вспомогательного инструмента (топоров, уголков и т. д.), подъемно-поворотный стол для укладки и поворота слитков и поковок перед захватом их манипулятором и в процессе ковки.
Устройство для смены бойков состоит из подвижного стола с помещенными на нем четырьмя-пятью комплектами бойков, упоров, фиксирующих стол в нужном положении, фартука с реечно-гидравлическим приводом, соединяющегося с тем комплектом бойков, который нужно подать в пресс.
Подвижный стол может перемещаться параллельно основному столу пресса. На нем помещены направляющие, по которым при необходимости сменные бойки передвигаются в поперечном направлении. Устройство для подачи вспомогательного инструмента находится на фартуке устройства смены бойков. При перемещении нужного комплекта бойков соответствующий комплект вспомогательного инструмента движется вместе с фартуком и занимает рабочую позицию.
Такое устройство одновременно служит местом складирования инструмента. Подачу инструмента в рабочую зону пресса в ковочном комплексе можно облегчить и другим способом. Комплекс можно оборудовать специальным инструментальным манипулятором, который подает в рабочую зону пресса заранее подготовленный инструмент. Вместо подъемно-поворотного стола используются тележки, движущиеся от печей перпендикулярно оси ковочного манипулятора.
Рис. 4. Ковочный комплекс, разработанный УЗТМ:
1 — ковочный манипулятор, 2 — пресс, 3 — устройство для смены ос новного ковочного инструмента, 4 — стол
Рис. 5. Ковочный манипулятор с независимым захватом:
а — внешний вид, б — конструкция: 1 — захват, 2 — хобот. 3 — тележка
Прессы усилием свыше 20 МН (2000 тс) часто оснащаются двумя манипуляторами разной грузоподъемности.
У манипуляторов, используемых в ковочных комплексах для обеспечения повышенного быстродействия при работе в автоматическом режиме, захват (хобот) устанавливается на основной тележке так, что может перемещаться по ней. Такие манипуляторы называются манипуляторами двойного действия. Его хобот приводится в движение гидравлическими цилиндрами через рычажную систему. Благодаря тому, что хобот движется независимо от тележки, обеспечивается высокая скорость манипулирования заготовкой, поскольку она не зависит от массы основной тележки, станины манипулятора, его механизмов и аппаратуры.
В некоторых прессах подвижная траверса с рабочими цилиндрами располагается ниже основания и движется вместе с рамой. Достоинство такой конструкции состоит в том, что она позволяет удобно маневрировать с поковками, что очень важно для ковочного пресса. Однако в этом случае сильно увеличиваются размеры фундамента, кроме того, если по такой схеме выполняются небольшие прессы, в них возникают значительные динамические нагрузки (особенно при шлихтовке), поскольку масса подвижных частей достигает 75% общей массы пресса (при верхнем расположении рабочих цилиндров подвижная поперечина составляет 15% массы пресса). Поэтому прессы с нижним приводом строятся в основном с усилиями от 150 до 800 МН (15 000— 80 000 тс).
Наличие в составе ковочного комплекса большого числа механизмов делает целесообразным изменение конструкции самого пресса таким образом, чтобы обеспечивалось удобство расположения всех агрегатов и свобода маневрирования поковкой не только в рабочей зоне, но и вблизи ее. С этой целью созданы, например, двухколонные прессы с нижним и верхним расположением рабочих цилиндров, размещаемые под углом к направлению движения ковочного манипулятора, что позволяет удобно расположить и инструментальный манипулятор.
Рис. 6. Ковочный комплекс, включающий пресс с подвижной станиной нижним расположением рабочих цилиндров
Рис. 7. Ковочный двухколонный пресс усилием 20 МН (2000 тс), имеющий верхнее расположение рабочих цилиндров и размещенный наискось по отношению к манипулятору
Важнейшей составной частью ковочных комплексов является электронно-вычислительная машина (ЭВМ). Наиболее совершенные из ЭВМ, обслуживающих ковочные комплексы, включают следующие элементы:
— центральный процессор — «сердце» и «мозг» ЭВМ, выполняющий вычислительные и логические действия и контролирующий работу всей системы;
— запоминающее устройство (память), которое служит для хранения исходных данных, промежуточных и конечных результатов и выдачи их другим устройствам;
— устройства ввода и вывода информации, необходимой для работы машины и анализа человеком результатов этой работы.
Все механизмы ковочного комплекса управляются с одного пульта. Они могут работать как при управлении вручную, так и в автоматическом режиме. При работе в автоматическом режиме с использованием ЭВМ в нее в закодированном виде вводятся данные о характере движения заготовки (например, ступенчатое вращение или перемещение в том или ином направлении), виде операции (шлихтовка, протяжка и т. д.), скорости подвижных частей пресса, верхнем и нижнем положениях подвижных частей, положении хобота манипулятора на каждой операции и т. д.
Устройства доставки слитков и поковок к манипулятору и от него оборудованы мессдозами, определяющими массу заготовок и готовых поковок, аппаратурой для измерения температуры, определения марки материала поковки. Все эти сведения ЭВМ обрабатывает, определяет оптимальные технологические параметры и формирует программу ковки в автоматическом режиме.
Оператор может и сам составить программу из отдельных, ранее записанных в памяти ЭВМ подпрограмм. При необходимости он имеет возможность получить от ЭВМ интересующую его информацию о работе комплекса во время любого цикла.
Быстродействие современных ковочных комплексов можно проиллюстрировать следующими цифрами: пресс усилием 20 МН (2000 тс) в составе комплекса т1ри протяжке делает 30—35 ходов в мин, а при шлихтовке —до 100.
Таким образом преимущества ковочных комплексов, управляемых ЭВМ, заключаются в возможности ведения точной ковки; улучшении контроля качества поковок; уменьшении времени манипулирования заготовкой, что позволяет заканчивать ковку в нужном интервале температур; повышении КПД использования пресса благодаря более детальной информации о его работе; возможности автоматизации работы по разработке технологии ковки и т. д.
Реклама:
Читать далее:
Особенности конструкции штамповочных и трубопрофильных прессов
Статьи по теме:
pereosnastka.ru
Пресс штамповочный и другое оборудование для ковки и штамповки
Пресс штамповочный, при помощи которого выполняется ковка металлических заготовок, работает по достаточно простой схеме. Принцип его работы, по сути, схож с принципом действия обычного молотка, которым наносятся удары по металлическому изделию, чтобы деформировать его и придать ему требуемую конфигурацию.
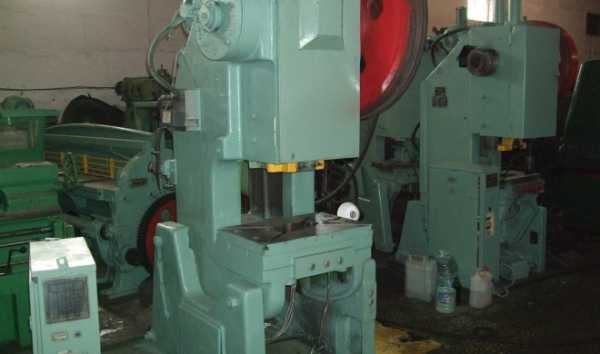
Механические прессы типа К2130 применяются на участках холодной листовой штамповки
Штамповочные прессы гидравлического и кривошипного типа
С того момента, как люди научились выполнять обработку металла давлением, работа специалиста, который ей занимался, считалась одной из самых почетных. С течением времени потребность в металлических изделиях, полученных по технологии ковки, только возрастала, в них стала нуждаться и активно развивающаяся промышленность. Все это привело к тому, что для ковки стал использоваться не ручной труд кузнецов, а специальное оборудование для штамповки.
Достаточно распространенным типом устройств, используемых для ковки, является своеобразный аналог молота – штамповочный пресс. Применяя такое штамповочное оборудование, можно выполнять целый перечень технологических операций, а именно: изменение формы заготовки путем ее пластической деформации, формирование на ее поверхности заданного рельефа, вырубание отдельных фрагментов и др. На таком устройстве, в частности, придают форму заготовкам, для изготовления которых было использовано литье. Прессы, применяемые для штамповочных операций, могут быть кривошипными или гидравлическими.
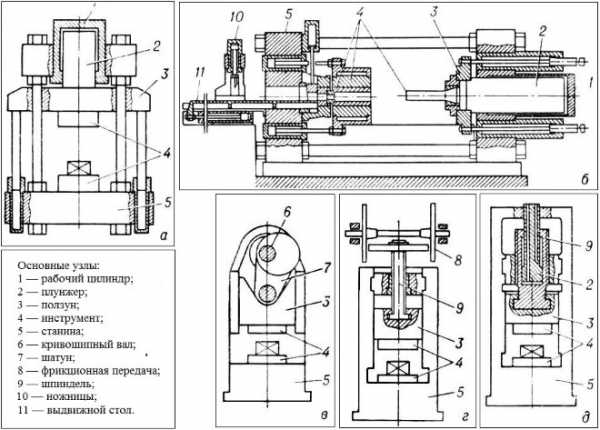
Схемы прессов: а – вертикальный гидравлический; б – горизонтальный; в – кривошипный; г – фрикционный; д – гидровинтовой
Пресс кривошипный применяют в тех случаях, когда необходимо выполнить несложную обработку металла давлением. Основным элементом такого оборудования, который преобразует вращательное движение вала приводного электродвигателя в возвратно-поступательное перемещение ползуна, является кривошипно-шатунный механизм. Именно поэтому пресс кривошипный часто называют штамповочным кривошипно-шатунным прессом. Он очень популярен как среди производственников, так и среди частных мастеров, существуют даже модели настольного кривошипного пресса. Объясняется такая популярность не только высокой эффективностью и функциональностью этого оборудования, но также и тем, что обслуживание и ремонт кривошипных прессов не вызывает особых проблем.
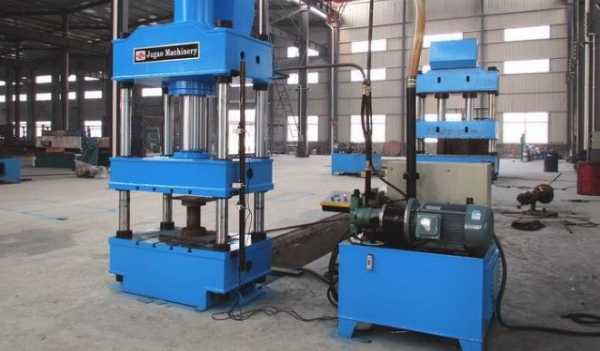
Пресс штамповочный гидравлический 4-х колонный
Гидравлические штамповочные прессы оснащаются двумя рабочими камерами, в которых в рабочей жидкости создается требуемое давление. Жидкость под давлением поступает в цилиндр с другим поршнем, посредством которого и сообщается возвратно-поступательное движение ползуну.
Радиально-ковочное оборудование для горячей обработки металла
Радиально-ковочный станок используется для того, чтобы с высокой производительностью изготавливать валы различного диаметра. На таком агрегате можно наладить производство до 300 тысяч готовых изделий в год, чего вполне достаточно для того, чтобы обеспечить ими крупное производственное предприятие.
Ограниченность использования такого станка для штамповки металла объясняется не только его высокой стоимостью, но еще и тем, что настройка его рабочих режимов представляет собой достаточно сложный процесс, поэтому выполнять ее целесообразно лишь в том случае, если планируется выпускать изделия определенного диаметра большими партиями.
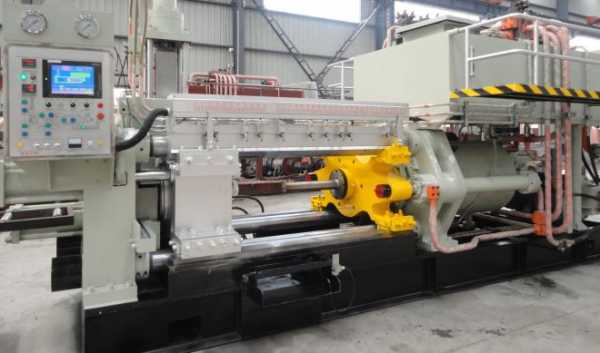
Радиально-ковочная машина (РКМ) обеспечивает высокую точность штамповки, выдавая детали с минимальными припусками
Последовательность действий, в процессе которых выполняется радиальная ковка, выглядит следующим образом.
- Деталь, чтобы довести ее до требуемой температуры нагрева, подают в индукционное устройство.
- После того как металл приобретет требуемую степень пластичности, деталь по роликовому контейнеру (рольтангу) отправляют к захватному устройству, с помощью которого она подается в зону обработки.
- Там заготовка фиксируется элементами другого захватного устройства, после чего на нее воздействуют посредством специальных бойков.
- Для равномерной обработки со всех сторон деталь постоянно вращают, для чего используется специальный захватный механизм.
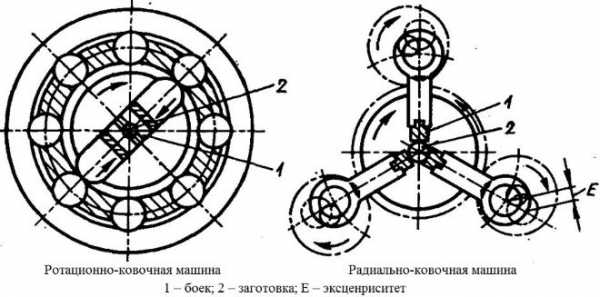
Схемы действия ковочных машин радиального и ротационного типа
Для того чтобы привести в движение рабочий механизм оборудования для радиальной ковки, используют кинематическую схему, элементами которой являются:
- приводной электродвигатель;
- клиноременная передача;
- четыре установленных вертикально вала с эксцентриковыми буксами;
- шатун с закрепленными на нем бойком и ползуном.
Основные элементы автоматики станка – это копирные барабаны, которые отвечают как за синхронное сближение бойков, так и за последующее движение заготовки. Вращение захвату, в котором удерживается обрабатываемая деталь, сообщается электродвигателем через элементы червячной передачи. Торможение данного механизма, которое осуществляется в момент ковки, обеспечивает пружинная муфта.
Одной из разновидностей ковочного оборудования является горизонтально-ковочный станок, в котором обрабатываемая деталь также располагается параллельно земле. Устройства данного типа используются преимущественно для формирования торцевых утолщений на заготовках стержневого типа. Деталь при обработке располагается в разъемной матрице, каналы которой ориентированы в горизонтальной плоскости.
Процесс обработки, выполняемой на таком станке, происходит в следующей последовательности.
- Заготовка укладывается в неподвижную часть матрицы.
- Подвижная часть матрицы, соединенная с ползуном, приводится в действие посредством коленчатого вала.
- Приближаясь к неподвижной половине формы, подвижная часть матрицы плотно охватывает обрабатываемый стержень.
- После зажима детали верхней частью формы коленчатый вал, соединенный с шатуном, приводит в действие ударные пуансоны.
- По окончании обработки все подвижные части станка возвращаются в исходное положение, а подвижная и неподвижная части формы размыкаются.
Ковочный молот с пневмоприводом
Пневматический пресс – это эффективное, но в то же время доступное по стоимости ковочное оборудование, отличающееся, кроме того, компактными габаритами. Работает такой станок за счет энергии сжатого воздуха, за подачу которого к механизмам отвечает встроенный компрессор. Работу компрессора, поршни которого, двигаясь в его главном цилиндре, как раз и создают поток воздуха с требуемым давлением, обеспечивает приводной электродвигатель.
Поскольку работу ударного механизма пневматического ковочного станка обеспечивает кривошип, то его конструкция напоминает устройство кривошипного пресса. Перед запуском такого оборудования компрессорный и рабочий поршни в главном цилиндре находятся в крайнем верхнем и крайнем нижнем положениях. Когда станок запускается в действие, поршни начинают двигаться по направлению друг к другу, сжимая находящийся между ними воздух, давление которого передается на кривошип, напрямую соединенный с бойком. На один удар рабочей части молота пневматического станка приходится один оборот кривошипного механизма. Соответственно, чтобы воздействие молота на заготовку выполнялось с более высокой частотой, необходимо обеспечить более интенсивную работу компрессора. Даже несмотря на свои небольшие габариты, пневматический пресс может обеспечить массу удара молота, доходящую до 1 тонны.
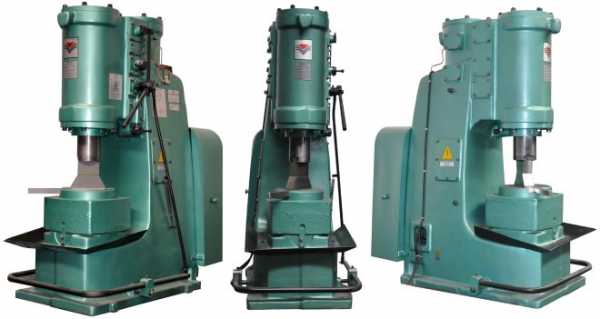
Молот кузнечный пневматический МА-4129 предназначен для горячей штамповки в открытых штампах
По похожему с пневматическим прессом принципу работает паровоздушный молот, в котором энергию удара обеспечивает горячий пар, подающийся непосредственно из котла или через специальный компрессор. Масса ударов, которой позволяет добиться такое оборудование, может доходить до 8 тонн, а скорость их нанесения составляет 50 м/сек. Работать оно в зависимости от модели может в автоматическом режиме, когда удары по детали наносятся непрерывно, или в ручном, когда для запуска в действие бойка необходимо нажать на соответствующую кнопку или педаль.
Механические молоты могут использоваться для:
- свободной ковки или ковочных операций, при выполнении которых для формирования готового изделия используется прессформа;
- штамповочных операций с деталями из листового металла – резки по ровной или кривой линии, вырубки по различному контуру, пробивки отверстий (дыропробивной пресс) и др.;
- выколотки – изготовления изделий с использованием специального шаблона.
Ковочное оборудование ротационного и вальцевого типа
На крупных производственных предприятиях для выполнения ковочных операций часто применяется конвейерное оборудование вальцевого типа. Заготовки на нем обрабатываются методом обжима, который выполняют вращающиеся вальцы. По похожему принципу работают и ротационно-ковочные машины, обработка деталей в которых также осуществляется в процессе вращения рабочих органов.
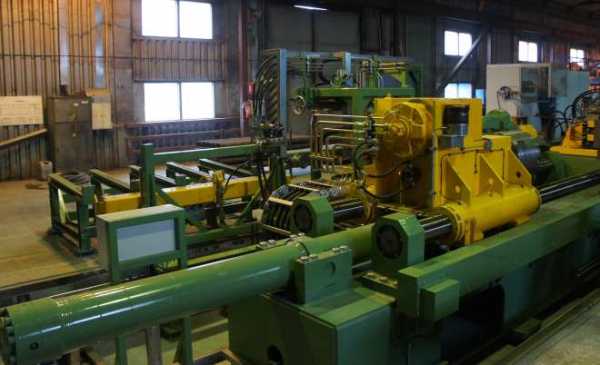
Метод ротационной ковки обеспечивает безотходную обработку заготовок
Специалистам, которые профессионально занимаются ковочными и штамповочными операциями, приходится решать целый ряд вопросов, чтобы получить изделие требуемого качества. В числе таких вопросов, в частности, находятся выбор оборудование, разработка и изготовление пресс-форм, оснащение станков различными инструментами и приспособлениями.
Оценка статьи:
Загрузка…Поделиться с друзьями:
met-all.org
Кузнечно-прессовое оборудование: классификация
Машины для выполнения ковочно-штамповочных операций (так вернее, ибо какое-либо оборудование обычно создаётся под разработанную технологию, а не наоборот) – распространённый вид устройств для металлообработки.
Например, на машино- и приборостроительных предприятиях или заводах по производству металлоконструкций на каждые 5 металлорежущих станков обязательно приходится одна единица оборудования для обработки давлением. Причём не только металлов: например, те же ПЭТ-бутылки производятся на термопластавтоматах, которые тоже представляют специализированное штамповочное оборудование.
Виды кузнечно-прессового оборудования
Всё многообразие конструкций и схем кузнечно-штамповочного оборудования (КШО) классифицируют по следующим показателям:
По температуре обрабатываемой заготовки
Машины для ковки, горячей штамповки, холодной листовой штамповки, холодной объёмной штамповки.
По виду операций, которые выполняются на машине
Различают заготовительное, основное КШО, а также КШО для заключительных стадий обработки давлением.
По способу подачи и удаления изделий из зоны обработки
Неавтоматизированное оборудование, штамповочные комплексы, машины-автоматы, автоматизированные штамповочные линии.
По типу энергоносителя
В качестве которого может использоваться электроэнергия, сжатый воздух, пар, жидкость высокого давления, а также несколько указанных источников одновременно.
По характеру обработки металла
Выделяют машины статического и динамического действия. Сюда же принято относить и установки для высокоэнергетической штамповки.
По основному технологическому параметру
Которым может быть номинальное усилие (для механических прессов), предельное усилие (для гидравлических и пневматических прессов), крутящий момент (для машин ротационного действия), энергия удара (для молотов).
Все остальные классификационные признаки – последовательность размещения основных узлов
Способ управления и т.д. — носят вспомогательный характер
Следует отметить: в вопросах названия определённых типов КШО элемент терминологической путаницы вносят различия в обозначениях технологических процессов, которые исторически приняты в отечественной и иностранной профильной литературе.
Так, машины для холодной объёмной штамповки часто именуют оборудованием для холодной ковки металла. Происходит это из-за буквального перевода английского термина cold forging (холодная ковка), который некритично воспринимается производителями КШО, в частности, из Китая, Тайваня и т.д.
Аналогично случилось и с термином forging (в иностранной литературе понятие hot forging практически не употребляется: всё, что не делает cold forging, автоматически зачисляется в горячештамповочное оборудование). Таким образом, следует точно различать принципиальные различия в областях применения КШО у нас в стране, и за рубежом, и использовать их в дальнейшем:
Оборудование для ковки
Ковка, как операция горячей обработки штучных заготовок давлением, отличается от горячей штамповки тем, что в последнем случае для формоизменения металла обязательно нужна технологическая оснастка – штамп. Чисто ковочное КШО предназначается для заготовительных операций – чаще осадки, расплющивания, открытой прошивки – а потому не содержит повышенных требований к точности полуфабриката (который в дальнейшем ещё будет обрабатываться различными способами, в том числе, и штамповкой). Поэтому оно должно обеспечивать лишь необходимую мощность формоизменения.
Для горячей ковки металла
Применяются два различных вида КШО: ковочные молоты (см. рис. 1) и гидравлические прессы (см. рис.3). Крупные ковочные молоты могут использовать в качестве энергоносителя пар и сжатый воздух, мелкие – только сжатый воздух (см. рис.2). Гораздо реже используются газовые и гидравлические молоты. Молоты имеют преимущественно вертикальную компоновку.
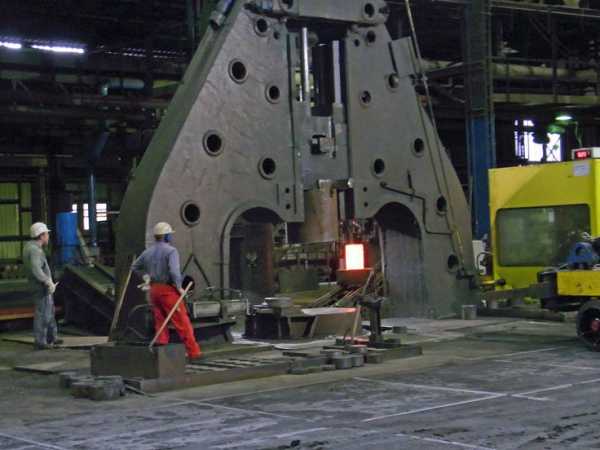
Рисунок 1 – ковочный паровоздушный молот
Поскольку при ковке создаются большие динамические нагрузки, то фундамент ковочного молота с подштамповой плитой обычно отделяется от остальных его узлов, что хорошо заметно на рис.1.
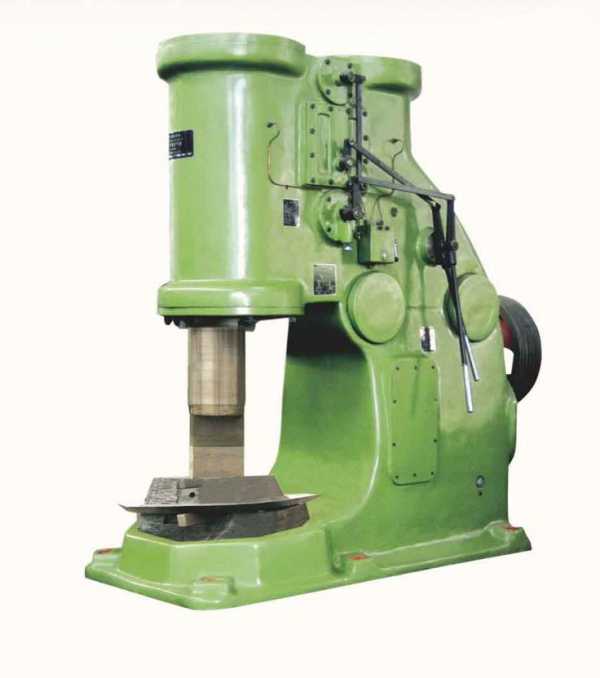
Рисунок 2 – Пневматический ковочный молот.
Молоты
Для свободной ковки отечественного производства маркируются буквой М/МА и четырьмя цифрами, две первых определяют тип энергоносителя (13,15 – паровоздушный молот, 41 – пневматический молот). Две последних цифры обозначают основной параметр оборудования – массу падающих частей в тоннах. Например, марка молота МА 4134 соответствует пневматическому молоту с массой падающих частей (мпч) 250 кг, а М1345 – паровоздушному молоту с мпч 3150 кг.
Гидравлические прессы
Применяются для горячей ковки заготовок, которые отличаются особо большими габаритными размерами. Например, поковку вала океанского судна куют с несколькими нагревами металла в течение суток и даже более. В молоте такая заготовка не сможет разместиться, поэтому деформацию производит ползун ковочного пресса. Такое оборудование отличается весьма большими габаритными размерами, поскольку только в таком случае можно обеспечить необходимое давление на металл.
Для механизации
Транспортных операций – подачи, кантовки заготовки в процессе ковки и т.д. – применяются специальные манипуляторы, которые могут быть безрельсового (для сравнительно небольших поковок) и рельсового типа.
Маркировка ковочных
Гидропрессов отечественного производства выполняется буквой П, после которой указываются конструктивное исполнение пресса (первые две цифры) и его номинальное усилие в тоннах (вторые две цифры). Например, марка ПБ1341 соответствует ковочному гидропрессу усилием 12500 кН.
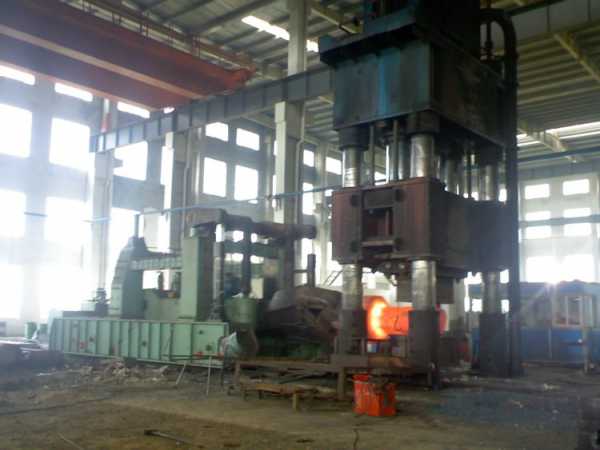
Рисунок 3 – Ковочный гидравлический пресс с манипулятором.
Оборудование для горячей объёмной штамповки
Точность горячей штамповки должна быть по определению выше, чем ковки: во многих случаях непосредственно после деформирования деталь не нуждается в последующей доработке.
Поэтому класс горячештамповочного оборудования дополняется, кроме штамповочных молотов, ещё кузнечными бульдозерами, кривошипными горячештамповочными прессами (КГШП) и горячештамповочными автоматами. В эксплуатации продолжает оставаться некоторое количество горизонтально-ковочных машин (ГКМ).
Паровоздушные
Штамповочные молоты конструктивно отличаются от ковочных меньшими значениями энергии удара и более жёсткой конструкцией, которая связывает между собой шабот, подштамповую плиту и стойки молота (в которых перемещается баба) в единую топологическую систему.
Поскольку усилия, возникающие при штамповке, всегда больше ковочных (сказывается более сложная конфигурация штампованной поковки), то сжатый воздух как энергоноситель в данной ситуации неэффективен.
Даже при использовании мощных паровоздушных штамповочных молотов (ППШМ) по заготовке приходится наносить несколько ударов, пока она не приобретёт форму, установленную штампом. Горячая штамповка выполняется обычно с одного нагрева, поэтому скорость деформирования имеет очень большое значение. Поэтому все ППШМ — молоты двойного действия, в которых баба дополнительно разгоняется основным энергоносителем. Фото общего вида ППШМ с сомкнутым штампом представлено на рис. 4.
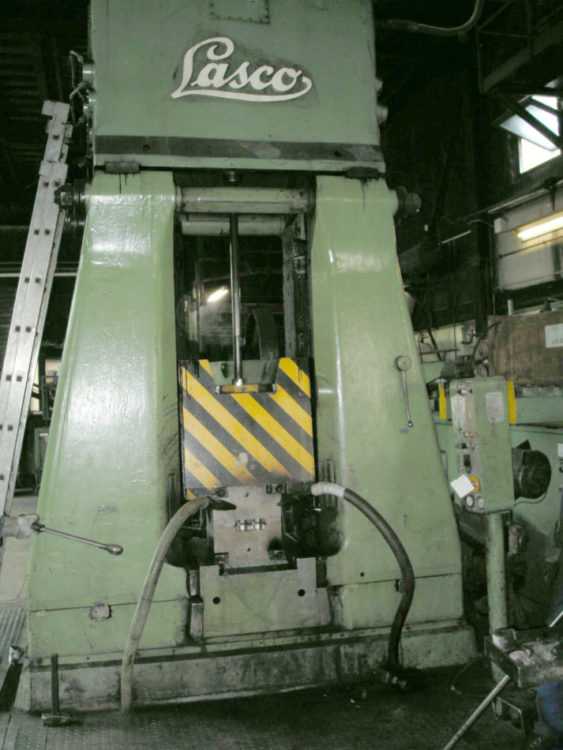
Рисунок 4 – Паровоздушный штамповочный молот.
ППШМ
Простые с конструктивной точки зрения машины, но надлежащую точность горячей объёмной штамповки они не всегда обеспечивают. Причины:
- Вибрация элементов оборудования и штампа;
- Остывание поковки при многократных ударах бабы молота;
- Износ рабочих элементов гравюры штампа.
Кроме того, автоматизировать штамповку на молоте в большинстве случаев невозможно. Поэтому для точной штамповки процесс проектируют на КГШП, а снижение энергии деформирования (КГШП формоизменяют металл с гораздо более низкими скоростями) компенсируют увеличением позиций штамповки.
Виду этого штампы на КГШП – составные (а не цельные, как на молотах), и представляют собой совокупность отдельных вставок, которые располагаются в последовательности, соответствующей стадиям деформирования заготовки. Это облегчает переналадку штампа, оптимизирует время вспомогательных операций и снижает вибрации при работе оборудования.
Фото общего вида современного КГШП представлено на рис. 5.
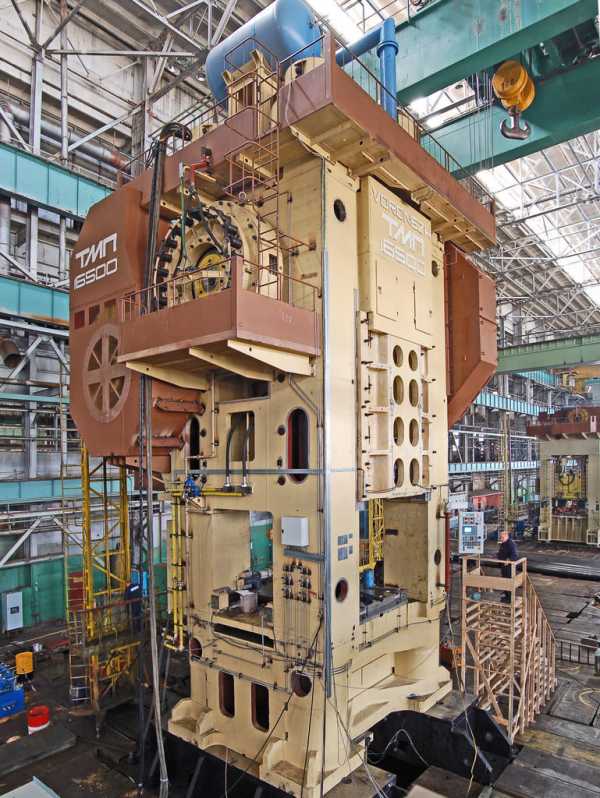
Рисунок 5 – КГШП номинальным усилием 165 МН.
Маркировка
Такого оборудования отечественного производства также представляет собой комбинированное буквенно-цифровое обозначение: первой идёт буква К, последующие две первых цифры (80 или 85) указывают на конструктивные особенность машины, а две последних – на её номинальное усилие. Например, КГШП модели КБ8544 обладает номинальным усилием 25 МН.
В условиях массового производства
Мелких и средних поковок типа толкателей клапанов, железнодорожных костылей, крупных метизов экономически целесообразно применять горячештамповочные автоматы (ГША).
В отличие от ГКМ
Эти машины имеют встроенный механизм перемещения полуфабриката от одной позиции к другой, включают в себя узлы автоматической подачи и удаления отштампованных изделий, а также оснащаются встроенными электронагревательными установками (см. рис. 6). Мировыми лидерами в производстве такого КШО являются фирмы Hatebur (Швейцария), Malmedie (Бельгия-Нидерланды) и Peltzer (Германия).
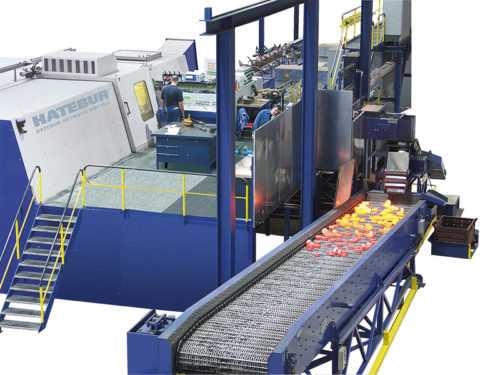
Рисунок 6 – Общий вид горячештамповочного комплекса на базе ГША модели АМР-70.
Свою нишу в производстве поковок методом горячей объёмной штамповки достойно заполняют винтовые прессы с дугостаторным приводом (см. рис. 7).
Эти машины сочетают в себе принципы статического и динамического деформирования, поскольку работают со скоростями ниже, чем молоты, но выше, чем КГШП. Штамповка происходит перемещающимся внгих винтом, который получает движение от гайки, раскручиваемой специализированным дугостаторным двигателем с бегущим электромагнитным полем.
Винтовые прессы
Применяются для производства поковок из алюминиевых сплавов, мелких и средних стальных поковок, изделий, которые имеют тонкие рёбра и перемычки. Из-за простоты управления, возможности автоматизации и низкой стоимости винтовые машины нашли широкое применение и в холодной штамповке.
Маркировка машин включает в себя букву Ф (первоначально источником привода винта являлись не электромагнитные силы, а силы трения от диска, фрикционно сцеплявшегося с элементами приводного вала) с последующими четырьмя цифрами (17 — тип привода: дугостаторный и – далее – две цифры, указывающие на номинальное усилие).
Например, обозначение АКФ 1730 указывает на автоматизированный комплекс на базе винтового пресса с дугостаторным приводом номинальным усилием 1 МН.
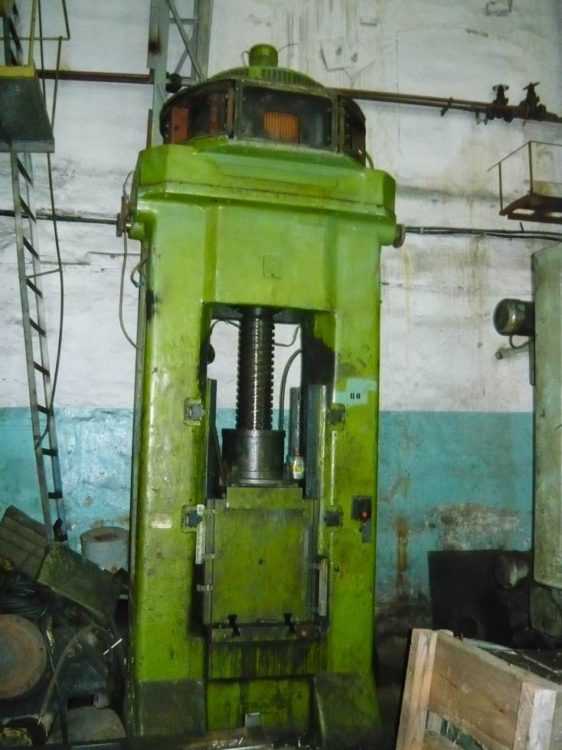
Рисунок 7 – Винтовой пресс с дугостаторным приводом усилием 1600 кН.
Кузнечные бульдозеры
(или горизонтально-гибочные машины, см. рис. 8) применяются для горячей гибки заготовок из толстой полосы.
Это — оборудование, которое отличается простотой конструкции и высокими эксплуатационными показателями. Используются кузнечные бульдозеры преимущественно в средне- и мелкосерийном производстве, поскольку не отличаются высокой производительностью.
Их маркировка
Включает в себя букву И (этот индекс присваивается всем видам КШО, которые выполняют гибку заготовок) и 4 цифры; две последние традиционно указывают на номинальное усилие оборудования. Например, И1230 – горизонтально-гибочная машина усилием 1000 кН.
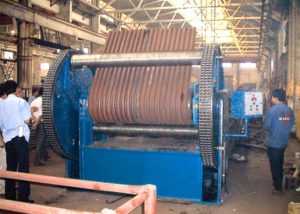
Рисунок 8 – Горизонтально-гибочная машина.
Оборудование для холодной штамповки
Холодноштамповочное КШО различают по выполняемым операциям, среди которых:
- Разделительные/заготовительные.
- Штамповка листового материала.
- Штамповка из полосы или ленты.
- Формообразующие операции с листовым металлом (вытяжка, гибка).
- Холодная объёмная штамповка – выдавливание, высадка.
- Комбинированная штамповка из листа – листообрабатывающие центры.
В качестве заготовительного оборудования используются кривошипные или дисковые ножницы. Первые могут резать как сортовой, так и профильный прокат, в то время, как дисковые ножницы предназначены для роспуска только тонколистового металла в виде рулонов или широкой ленты.
Сортовые ножницы
Для резки прутка чаще встречаются в цехах горячей или холодной объёмной штамповки. Они представляют собой однокривошипные механические прессы с устройствами для подачи прутка и его удерживания во время разрезания.
Листовые ножницы
Машины горизонтального исполнения, которые оснащаются двумя шатунами, поскольку зона реза должна быть несколько больше ширины листа. Листовые ножницы могут иметь гидравлический привод, что используется в моделях, работающих с металлом толщиной более 16 мм.
Комплексы
На базе кривошипных ножниц оснащаются приводными рольгангами, поворотными столами и другими механизмами, снижающими трудоёмкость резки.
Маркировка ножниц отечественного производства начинается в буквы Н. Характерно, что последними двумя цифрами маркировки листовых ножниц обозначают не усилие, а толщину разрезаемого металла (одновременно указывается и предел прочности в МПа, для которого было рассчитано это усилие).
Например, модель Н1830 – кривошипные сортовые ножницы усилием 1000 кН, а НК3414 – листовые ножницы для резки листа толщиной до 2,5 мм. Внешний вид оборудования представлен на рис. 9, 10, 11.
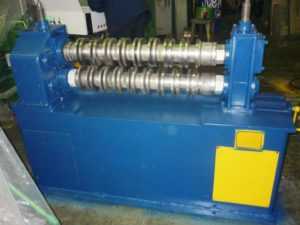
Рисунок 9 – Многодисковые ножницы.
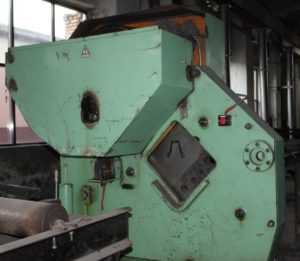
Рисунок 10 – Сортовые ножницы.
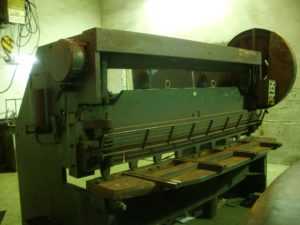
Рисунок 12 – Листовые ножницы с наклонным ножом
Листовую холодную штамповку ведут на механических или гидравлических прессах вертикального исполнения
Механические прессы различаются по следующим характеристикам
Количеству кривошипов
Один, два или четыре.
По форме станины
Открытая или закрытая.
По количеству стоек
Одна или две.
По наличию или отсутствию узлов
Автоматизации штамповки.
По количеству ползунов
Простого или двойного действия.
Для операций листовой штамповки, не требующих большого хода ползуна (пробивка, вырубка, гибка, неглубокая вытяжка) используются однокривошипные открытые прессы вертикального типа. Для глубокой вытяжки применяют прессы двойного действия.
Габаритные заготовки, деформирование которых не сопровождается большими технологическими усилиями, производят на двухкривошипных открытых прессах, а при значительных усилиях деформации применяют закрытые кривошипные прессы.
Гидравлические прессы в холодной штамповке используются реже, поскольку не отличаются высокой производительностью.
Общей тенденцией для холодноштамповочного КШО считается удобство управления оборудованием, для чего прессы часто оснащают автоматическими подачами, сбрасывателями, питателями.
Кривошипные механические прессы
Отечественного производства маркируются буквой К, а гидравлические – буквой Г. Принцип формирования остальных символов в маркировке не отличается от рассмотренного выше.
Отдельную категорию холодноштамповочного КШО составляют
Листообрабатывающие центры
Они особенно эффективны в условиях мелкосерийного производства, когда из одного и того же листа можно штамповать (в основном, вырубкой и пробивкой) одновременно несколько различных по конфигурации деталей. Такое оборудование имеет роторное исполнение.
Типовые представители КШО для холодной листовой штамповки представлены на рис. 13, 14, 15.
КШО
Для холодной объёмной штамповки разделяют на две группы
Прессы для холодного выдавливания, а автоматы для холодной высадки.
Первую группу составляют
Вертикальные (реже – горизонтальные) прессы с механическим или гидравлическим приводом. Поскольку при холодном выдавливании требуется развивать большие технологические усилия, обеспечивая оборудованию одновременно и значительную жёсткость, то вместо традиционной кривошипной схемы в данном случае применяется схема кВ кривошипно-коленчатым механизмом.
Она даёт возможность при сравнительной компактности конструкции обеспечивать необходимые нагрузки деформирования заготовки. Такие машины маркируются обозначением К00 или К83/82 (последние две цифры, которые здесь не указаны, определяют номинальное усилие пресса).
Поскольку холодная высадка – технология, адаптированная под массовый выпуск продукции типа болтов, гаек, винтов и прочего крепежа, то реализуется она исключительно на автоматизированном оборудовании. Выпускаются отдельно автоматы для изготовления стержневых деталей, и для холодной высадки коротких изделий.
Для накатывания резьбы на полуфабрикатах
Выпускаются резьбонакатные станки. Они могут быть трёх исполнений:
Плашечного
Где резьба получается работой двух плашек – подвижной и неподвижной:
Роликового
Пригодного для накатки резьбы на изделиях без головки;
Планетарного
При котором накатка выполняется инструментом типа «ролик-сегмент».
Многие холодновысадочные автоматы снабжаются резьбонакатными головками, и могут производить полностью готовые метизы. Примеры современного оборудования , предназначенного для операций холодной объёмной штамповки показаны на рис. 16 и 17.
Примеры работы различных видов КШО можно посмотреть на многих видео YouTube.
Например, на видеоролике представлена работа паровоздушного молота с мпч 8000 кг.
Здесь:можно наглядно увидеть работу кривошипного пресса для холодной контурной гибки по задаваемой программе.
В ролике разъясняется устройство многопозиционного холодновысадочного автомата для изготовления болтов.
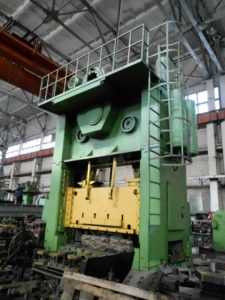
Рисунок 13 – Двухкривошипный пресс простого действия со станиной закрытого типа.
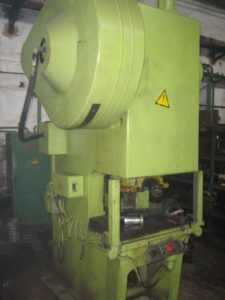
Рисунок 14 – Однокривошипный открытый пресс с С-образной станиной.
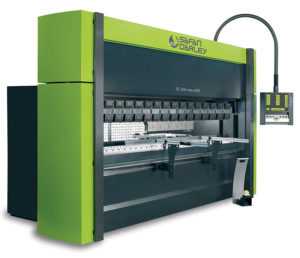
Рисунок 15 – Современный листообрабатывающий центр.
stanki-info.ru
Ковочные молоты и прессы – Ковочное оборудование, его выбор и правила эксплуатации
У молотов простого действия пар или сжатый воздух служит только для подъема падающих частей на определенную высоту для того, чтобы удар осуществить замечет веса их при свободном падении.
У молотов двойного действия энергоноситель служит не только для подъема, но при движении свободно падающих частей вниз, будучи поданным в надпоршневое пространство, увеличивает ускорение и конечную скорость падения (скорость в момент удара). В результате этого эффективная сила удара молота возрастает.
Ковочные паровоздушные молоты выпускаются отечественной промышленностью с номинальным весом падающих частей от 1 до 7,25 Т [9,81 до 71 кн]. Ковочные пневматические молоты выпускаются нашей промышленностью с номинальным весом падающих частей от 50 до 1000 кГ [491 н до 9,81 кн] включительно. В номинальный вес падающих частей молота входит вес бабы, штока, поршня, верхнего бойка и других сопряженных с ними деталей.
Данные для выбора ковочных гидравлических прессов в зависимости от веса и диаметра слитка
Усилие пресса, Т | Вес слитков, кГ | Диаметр слитка, мм | ||
средний | наибольший | наименьший | наибольший | |
600 | 1000 | 3000 | 200 | 550 |
800 | 2000 | 5500 | 300 | 800 |
1000 | 3500 | 8000 | 400 | 900 |
1200 | 5000 | 11000 | 500 | 1000 |
1500 | 8000 | 17000 | 600 | 1150 |
2000 | 14000 | 28000 | 700 | 1300 |
3000 | 30000 | 55000 | 1000 | 1600 |
5000 | 80000 | 120000 | 1400 | 2100 |
6000 | 80000 | 120000 | 1600 | 2300 |
10000 | 160000 | 250000 | 2100 | 2800 |
«Свободная ковка», Я.С. Вишневецкий
Для ковки крупных поковок, требующих применения молота с весом падающих частей более 5 Т [49 кн], промышленность выпускает прессы со все большими усилиями. При ковке небольших и средних деталей иногда применяют механические кривошипные и кривошипноколенные прессы. Работа на прессах по сравнению с работой на паровоздушных молотах имеет следующие преимущества: ударное действие молотов вызывает сотрясение грунта,…
Необходимо отметить, что при ковке некоторых мелких и средних деталей молоты имеют преимущество перед прессами как по чистоте поверхности получаемых на них поковок, так и по производительности. Поверхность детали, кованой под молотом, получается чище потому, что при ударах окалина с заготовки удаляется легче, своевременно и не заковывается в тело поковки. В современном машиностроении все большее…
На гидравлических прессах в основном куют из слитков крупные поковки. Размеры поковок достигают 2500 мм в поперечном сечении, а вес их до 100 Т и более. Кроме того, для работы ковочных прессов применяют воду, масла и эмульсии, находящиеся под высоким давлением, поэтому обслуживание прессов и гидравлических установок должно быть строго организовано. Правила работы и ухода…
Шток является вследствие больших ударных нагрузок наиболее часто разрушающейся деталью паровоздушных молотов. Штоки, как правило, куются из хромоникелевых или хромоникелемолибденовых сталей. Поковку подвергают отжигу, затем после грубой обдирки — термической обработке (закалке и отпуску). Верхняя часть штока соединяется с поршнем методом горячей посадки с последующей чеканкой. На рис. показана схема соединения штока 2 с бабой…
Ковочные прессы в зависимости от вида энергоносителя и способов приведения их в действие разделяются на гидравлические, парогидравлические и механические прессы. Гидравлические и парогидравлические прессы в основном применяются для изготовления крупных поковок методом свободной ковки, механические для свободной ковки при помощи подкладного инструмента и для объемной штамповки и чеканки небольших и средних размеров поковок (деталей). Гидравлические…
www.ktovdome.ru
Ковочный пресс – Большая Энциклопедия Нефти и Газа, статья, страница 1
Ковочный пресс
Cтраница 1
Ковочный пресс обслуживается манипулятором и посадочной машиной, расположенными по разные стороны от оси пресса. Оси продольных перемещений манипулятора и посадочной машины совпадают. [2]
Конструкция ковочного пресса допускает возможность ковки с эксцентричным приложением нагрузки. При этом колонны пресса не только растягиваются, но и изгибаются. С целью уменьшения изгиба колонн в ряде случаев рабочий плунжер заделывают жестко в подвижную поперечину пресса, в результате чего изгибающий момент передается через цилиндр на верхнюю поперечину. Колонны частично разгружаются от изгиба, однако возрастает износ уплотнений. [3]
Применение ковочных прессов повышает производительность труда на 30 – 50 % по сравнению с ковкой на паровоздушных молотах. [4]
Преимуществом ковочных прессов, имеющих С-образную станину ( рис. 3.40), по сравнению с колонными прессами является ничем не стесненный трехсторонний доступ к рабочему пространству. [5]
Для быстроходных ковочных прессов больших усилий требуемые производительность насосов и соответственно мощность электродвигателей могут оказаться чрезмерно большими. Поэтому для обслуживания пресса устанавливают большое число насосов. Известны ковочные прессы, привод которых имеет до 20 насосов. Насосы в этом случае располагают не на верхней поперечине пресса, а в находящемся недалеко от пресса помещении, изолированном от кузнечного цеха. [7]
В агрегате ковочного пресса предусматривают следую – а; щее оборудование: ковочный пресс, насосно-аккумулятор-ную станцию, пульт управления, нагревательные печи, термические печи. Заготовка под ковку имеет вид слитка или блума. [9]
При модернизации ковочных прессов рекомендуется устанавливать дистанционное управление перемещением стола, сосредоточив все управление на одном пульте. Для этого устанавливают гидравлические распределители, управляемые электр омагнитами. [10]
Конструкция станпны ковочного пресса должна допускать ковку при эксцентричном приложении нагрузки. Момент, возникающий при этом, передается подвижной поперечиной либо на архитрав, либо непосредственно на колонны станины. [11]
Схема управления ковочным прессом должна обеспечивать возможность автоматических шлихтовочных ходов. Для облегчения работы на прессе при ковочных операциях на гидравлических ковочных прессах следует иметь указатели действительного положения подвижной поперечины при ее перемещении вверх и вниз. [12]
С на ковочном прессе [5] при относительно малых осадках ( примерно по б мм за проход) для разрушения литой структуры сплава, не вызывая раскалывания концов слитка. [13]
В цехе имеется парогидравлический ковочный пресс давлением 1500 – 1200 т и паро-воздушные ковочные молоты 12; 5; 3 т и ниже. В пролете шириной 12 м находятся нагревательные печи с выдвижными подами. Следует отметить, что установка молотов для свободной ковки с весом падающих частей более 5 от не рекомендуется и они заменяются прессами. Наличие молота 12 т в данном цехе является исключением. [14]
Подвижная рамная станина ковочного пресса ( рис. 34, а и б) [12, 5], состоящая из верхней поперечины, колонн и нижней поперечины, применяется в тех случаях, когда важно иметь небольшие габариты пресса над полом и минимальную ширину верхней поперечины. Рабочие цилиндры монтируются в нижней поперечине и находятся ниже уровня пола. Средняя поперечина с главными плунжерами неподвижна. [15]
Страницы: 1 2 3 4
www.ngpedia.ru