Расшифровка 40хн2ма – Сталь 40ХН2МА. Характеристики, применение, цены и аналоги
alexxlab | 11.02.2020 | 0 | Вопросы и ответы
Стали 40ХН2МА и 40ХНМА: характеристики, расшифровка, состав, применение
Легированные сплавы получили самое широкое распространение по причине высоких эксплуатационных характеристик. Сталь 40ХН2МА и сталь 40ХНМА относятся к группе конструкционных металлов со средней концентрацией легирующих элементов. Расшифровка, которая проводится в соответствии с ГОСТ 19281-2014, позволяет определить количество основных химических элементов, а описание – область применения и другие качества.
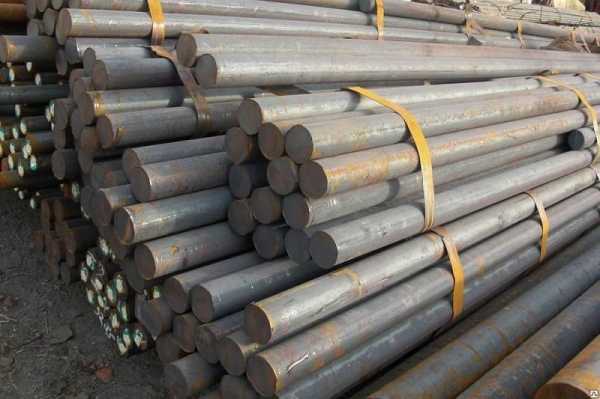
Характеристика и химический состав материалов
Добавление в состав определенных веществ позволяет существенно изменить основные свойства металла. Рассматриваемые стали 40ХН2МА и 40ХНМА имеют следующий химический состав:
- В качестве основного элемента принял углерод, так как даже незначительно изменение его концентрации может привести к повышению или снижению прочности, пластичности и других качеств. Сталь 40ХН2МА и 40ХНМА характеризуются повышенной концентрацией углерода, показатель находится в диапазоне от 0,37% до 0,44%.
- Легирование проводится хромом и молибденом. Концентрация первого вещества составляет 0,6-0,9%. Сталь 40ХН2МА, характеристики которой определяют устойчивость к воздействию жара, имеет 0,15-0,25% молибдена. Сталь 40ХНМА, характеристики которой практически идентичны, имеет молибдена менее 0,1%.
- В состав также вхожи кремний (0,17-0,37%), марганец (0,5-0,8%) и некоторые другие вещества в небольшом составе.
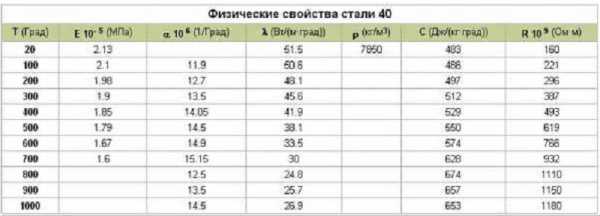
Физические свойства стали 40
Как ранее было отмечено, во многом механические свойства определяются количество углерода. Слишком большая концентрация этого элемента приводит к повышению твердости и прочности, но снижает степень свариваемости.
Скачать ГОСТ 19281-2014
Если нужно провести сварку подобных металлов, то заготовка предварительно подогревается, работа проводится только при применении технологии РНД. Образующуюся деталь подвергают термической обработке, так как полученные швы хрупкие и не устойчивые к вибрационным нагрузкам. Твердость без проведения термической обработки составляет 269 МПа. Может проводится ковка и закалка, отпуск. Добавление молибдена определяет устойчивость к высокой температуре, поэтому нагрев на момент термической обработки проводится до 1000 градусов Цельсия и выше.
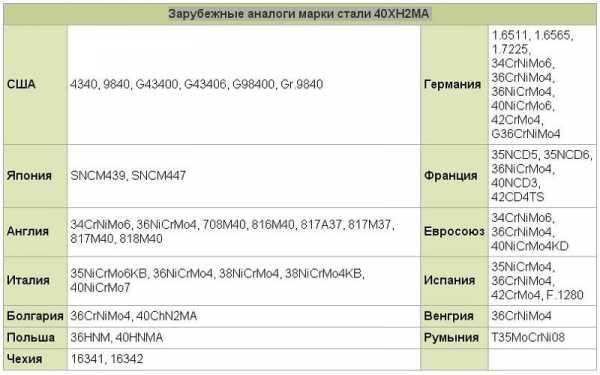
Аналоги стали 40ХН2МА
Применение в производстве
Сталь 40ХНМА и Ст 40ХН2МА в большинстве случае используются для получения цельнокатаных колец, клапанов или коленчатых валов, болтов и других крепежных материалов. Получаемые изделия могут эксплуатироваться при температуре до 500 градусов Цельсия. На производство может поступать в виде следующих заготовок:
- Калиброванного прутка.
- Сортового проката.
- Поковок.
- Валка.
- Поковок из стали 40ХН2МА
- Круг стальной
Как правило, применяется сталь 40ХН2МА и 40ХНМА для получения деталей, которые эксплуатируются в тяжелых условиях. Примером назовем элементы ДВС, на которые оказывается воздействие повышенной температуры, давление и постоянная или переменная нагрузка. Закалка и отпуск существенно повышают устойчивость поверхности к истиранию и деформации. Сплав применяется также при изготовлении основных элементов различных других ответственных механизмов, к примеру, редуктора.
Термообработка
Проводимая термообработка стали 40ХН2МА существенно расширяет ее область применения.
Чаще всего заготовки или конечные изделия подвергают:
- Закалке – процесс перестроения кристаллический решетки и насыщения поверхностного слоя углеродом, увеличения плотности структуры металла под воздействием высокой температуры и быстром охлаждении. В большинстве случаев металл закаливается для повышения твердости поверхностного слоя. Ответственные изделия охлаждаются в масле, которое обеспечивает равномерное снижение температуры. При использовании воды может образоваться окалина и придется выполнять финишную обработку.
- Отпуск – процесс, который способен снизить внутренние напряжения, возникающие после закалки. Как правило, закалка приводит к повышению хрупкости. Температуры отпуска значительно ниже, нагревается изделие постепенно, охлаждение может проходить в различных средах. Валы и другие ответственные детали после закалки всегда подвергаются отпуску, так как возникающая нагрузка может привести к появлению структурных трещин и снижению прочности.
- Может проводится для уплотнения структуры ковка. При сечении менее 80 мм заготовку дополнительно подвергают отжигу и двум переохлаждениям, а также отпуску. За счет этого получается поверхность с большим показателем износостойкости.
Для обработки рассматриваемого сплава требуется специальное оборудование. Зачастую применяются электродуговые печи, которые характеризуются компактными размерами и высоким КПД. Подобная сталь 40ХН2МА и 40ХНМА не склонна к отпускной хрупкости, поэтому получаемые детали могут прослужить в течение длительного периода даже в тяжелых эксплуатационных условиях.
Если вы нашли ошибку, пожалуйста, выделите фрагмент текста и нажмите Ctrl+Enter.
stankiexpert.ru
Механические свойства стали 40ХН2МА | ||||||||||
ГОСТ | Состояние поставки, режим термообработки | Сечение, мм | КП | σ0,2 (МПа) | σв(МПа) | δ5 (%) | ψ % | KCU (Дж / см2) | НВ, не более | |
ГОСТ 4543-71 | Пруток. Закалка 850 °С, масло. Отпуск 620 °С, вода | 25 | – | 930 | 1080 | 12 | 50 | 78 | – | |
Пруток. Закалка 850 °С, масло. Отпуск 620 °С, масло. | 25 | – | 835 | 980 | 12 | 55 | 98 | – | ||
ГОСТ 8479-70 | Поковки. Закалка. Отпуск | 500-800 | 440 | 440 | 635 | 11 | 30 | 39 | 197-235 | |
300-500 | 490 | 490 | 655 | 12 | 35 | 49 | 212-248 | |||
100-300 | 540 | 540 | 685 | 13 | 40 | 49 | 223-362 | |||
100-300 | 590 | 590 | 735 | 13 | 40 | 49 | 235-277 | |||
100-300 | 640 | 640 | 785 | 12 | 38 | 49 | 248-293 | |||
100-300 | 685 | 685 | 835 | 12 | 38 | 49 | 262-311 | |||
До 100 | 735 | 735 | 880 | 13 | 40 | 59 | 277-321 | |||
До 100 | 785 | 785 | 930 | 12 | 40 | 59 | 293-331 | |||
Механические свойства стали 40ХН2МА в зависимости от температуры отпуска | ||||||||||
Температура отпуска, °С | σ0,2 (МПа) | σв(МПа) | δ5 (%) | ψ % | KCU (Дж / см2) | HB | ||||
Закалка 850 °С, масло | ||||||||||
200 | 1600 | 1750 | 10 | 50 | 59 | 525 | ||||
Механические свойства стали 40ХН2МА при повышенных температурах | ||||||||||
Температура испытаний, °С | σ0,2 (МПа) | σв(МПа) | δ5 (%) | ψ % | KCU (Дж / см2) | |||||
Закалка 850 °С, масло. Отпуск 580 °С. | ||||||||||
20 | 950 | 1070 | 16 | 58 | 78 | |||||
Образец диаметром 5 мм, длиной 25 мм, прокатанный. | ||||||||||
700 | – | 185 | 17 | 32 | – | |||||
Предел выносливости стали 40ХН2МА | ||||||||||
σ-1, МПА | J-1, ÌÏÀ | n | Термообработка | |||||||
447 | 274 | 106 | Сечение 100
мм. Закалка 850 °C, масло. Отпуск 580 °C, σв=880 МПа. | |||||||
| Ударная вязкость стали 40ХН2МА KCU, (Дж/см2) | |||||||||
Т= +20 °С | Т= -40 °С | Т= -60 °С | Термообработка | |||||||
103 | 93 | 59 | Закалка 860 °С, масло. Отпуск 580 °С | |||||||
Механические свойства стали 40ХН2МА в зависимости от сечения | ||||||||||
Сечение, мм | Место вырезки образца | σ0,2 (МПа) | σв(МПа) | δ4 (%) | ψ % | KCU (Дж / см2) | HRCЭ | |||
Пруток. Закалка 850 °С, масло. Отпуск 620 °С | ||||||||||
40 | Ц | 880 | 1030 | 14 | 57 | 118 | 33 25 | |||
Закалка 850 °С, масло. Отпуск 540-660 °С | ||||||||||
до 16 | Ц | 1000 | 1200-1400 | 9 | – | 90 | – | |||
Прокаливаемость стали 40ХН2МА | ||||||||||
Расстояние от торца, мм | Примечание | |||||||||
1,5 | 3 | 6 | 9 | 12 | 15 | 21 | 27 | 33 | 42 | Закалка 840 °С |
49-59,5 | 40,5-60 | 50-60 | 50-59,5 | 49-59 | 48-59 | 45-56 | 41,5-53 | 41-50,5 | 36,5-48,5 | Твердость для полос прокаливаемости, HRC |
Количество мартенсита, % | Критическая твердость, HRCэ | Критический диаметр в воде | Критический диаметр в масле | |||||||
50 | 44-47 | 153 | 114 | |||||||
Физические свойства стали 40ХН2МА | ||||||||||
T (Град) | E 10– 5 (МПа) | a 10 6 (1/Град) | l (Вт/(м·град)) | r (кг/м3) | C (Дж/(кг·град)) | R 10 9 (Ом·м) | ||||
20 | 2.15 |
| 39 | 7850 |
| 331 | ||||
100 | 2.11 | 11.6 | 38 |
| 490 |
| ||||
200 | 2.01 | 12.1 | 37 |
| 506 |
| ||||
300 | 1.9 | 12.7 | 37 |
| 522 |
| ||||
400 | 1.77 | 13.2 | 35 |
| 536 |
| ||||
500 | 1.73 | 13.6 | 33 |
| 565 |
| ||||
600 |
| 13.9 | 31 |
|
|
| ||||
700 |
|
| 29 |
|
|
| ||||
800 |
|
| 27 |
|
|
| ||||
Краткие обозначения: | ||||||||||
σв | – временное сопротивление разрыву (предел прочности при растяжении), МПа |
| å | – относительная осадка при появлении первой трещины, % | ||||||
σ0,05 | – предел упругости, МПа |
| Jê | – предел прочности при кручении, максимальное касательное напряжение, МПа | ||||||
σ0,2 | – предел текучести условный, МПа |
| σизг | – предел прочности при изгибе, МПа | ||||||
δ5,δ4,δ10 | – относительное удлинение после разрыва, % |
| σ-1 | – предел выносливости при испытании на изгиб с симметричным циклом нагружения, МПа | ||||||
σсж0,05 и σсж | – предел текучести при сжатии, МПа |
| J-1 | – предел выносливости при испытание на кручение с симметричным циклом нагружения, МПа | ||||||
ν | – относительный сдвиг, % |
| n | – количество циклов нагружения | ||||||
sв | – предел кратковременной прочности, МПа |
| R и ρ | – удельное электросопротивление, Ом·м | ||||||
ψ | – относительное сужение, % |
| E | – модуль упругости нормальный, ГПа | ||||||
KCU и KCV | – ударная вязкость, определенная на образце с концентраторами соответственно вида U и V, Дж/см2 |
| T | – температура, при которой получены свойства, Град | ||||||
sT | – предел пропорциональности (предел текучести для остаточной деформации), МПа |
| l и ë | – коэффициент теплопроводности (теплоемкость материала), Вт/(м·°С) | ||||||
HB | – твердость по Бринеллю |
| C | – удельная теплоемкость материала (диапазон 20o – T ), [Дж/(кг·град)] | ||||||
HV | – твердость по Виккерсу |
| pn и r | – плотность кг/м3 | ||||||
HRCэ | – твердость по Роквеллу, шкала С |
| а | – коэффициент температурного (линейного) расширения (диапазон 20o – T ), 1/°С | ||||||
HRB | – твердость по Роквеллу, шкала В |
| σtТ | – предел длительной прочности, МПа | ||||||
HSD | – твердость по Шору |
| G | – модуль упругости при сдвиге кручением, ГПа |
xn--402-8cd3de9c.xn--p1ai
Доска объявлений | Сталь 40ХН2МА – характеристика, химический состав, свойства, твердостьСталь 40ХН2МАОбщие сведения
Химический состав
Механические свойстваМеханические свойства
Механические свойства при повышенных температурах
Механические свойства в зависимости от температуры отпуска
Механические свойства в зависимости от сечения
Технологические свойства
Температура критических точек
Ударная вязкостьУдарная вязкость, KCU, Дж/см2
Предел выносливости
ПрокаливаемостьЗакалка 840 С.
Коррозионные свойства
Физические свойства
|
s-metall.com.ua
Cталь 40ХН2МА механические, физические, технологические свойства, химический состав. Сталь 40ХН2МА круг стальной пруток
Справочная информация
Характеристика материала сталь 40ХН2МА.
Марка стали | сталь 40ХН2МА ( сталь 40ХНМА ) |
Заменитель стали | сталь 40ХГТ, сталь 40ХГР, сталь 30Х3МФ, сталь 45ХН2МФА |
Классификация стали | Сталь конструкционная легированная ГОСТ 4543-71 |
ГП “Стальмаш” поставляет сталь 40ХН2МА в следующих видах металлопроката: круг ст 40ХН2МА ГОСТ 2590-2006 (ГОСТ 2590-88) круг (пруток) стальной горячекатаный круг ст 40ХН2МА круг (пруток) калиброванный шестигранник ст 40ХН2МА ГОСТ 2879-2006 (ГОСТ 2879-88) шестигранник горячекатаный шестигранник ст 40ХН2МА ГОСТ 8560-78 шестигранник калиброванный | |
Применение стали 40ХН2МА | коленчатые валы, клапаны, шатуны, крышки шатунов, ответственные болты, шестерни, кулачковые муфты, диски и другие тяжелонагруженные детали. Валки для холодной прокатки металлов. |
Химический состав в % материала сталь 40ХН2МА
C | Si | Mn | Ni | S | P | Cr | Mo | Cu |
0.37 – 0.44 | 0.17 – 0.37 | 0.5 – 0.8 | 1.25 – 1.65 | до 0.025 | до 0.025 | 0.6 – 0.9 | 0.15 – 0.25 | до 0.3 |
Температура критических точек материала сталь 40ХН2МА
Ac1 = 730 , Ac3(Acm) = 820 , Ar3(Arcm) = 550 , Ar1 = 380 , Mn = 320 |
Механические свойства при Т=20oС материала сталь 40ХН2МА
Сортамент | Размер | Напр. | sв | sT | d5 | y | KCU | Термообр. |
– | мм | – | МПа | МПа | % | % | кДж / м2 | – |
Пруток | Ж 25 | 1080 | 930 | 12 | 50 | 780 | Закалка и отпуск |
Твердость материала сталь 40ХН2МА после отжига , | HB 10 -1 = 269 МПа |
Физические свойства материала сталь 40ХН2МА
T | E 10– 5 | a 10 6 | l | r | C | R 10 9 |
Град | МПа | 1/Град | Вт/(м·град) | кг/м3 | Дж/(кг·град) | Ом·м |
20 | 2.15 | 39 | 7850 | 331 | ||
100 | 2.11 | 11.6 | 38 | 490 | ||
200 | 2.01 | 12.1 | 37 | 506 | ||
300 | 1.9 | 12.7 | 37 | 522 | ||
400 | 1.77 | 13.2 | 35 | 536 | ||
500 | 1.73 | 13.6 | 33 | 565 | ||
600 | 13.9 | 31 | ||||
700 | 29 | |||||
800 | 27 | |||||
T | E 10– 5 | a 10 6 | l | r | C | R 10 9 |
Технологические свойства материала сталь 40ХН2МА
Свариваемость: | трудносвариваемая. |
Флокеночувствительность: | чувствительна. |
Склонность к отпускной хрупкости: | не склонна. |
Зарубежные аналоги материала сталь 40ХН2МАВнимание! Указаны как точные, так и ближайшие аналоги.
США | Германия | Япония | Франция | Англия | Евросоюз | Италия | Испания | Болгария | Венгрия | Польша | Румыния | Чехия | ||||||||||||||||||||||||||||||||||||||||
– | DIN,WNr | JIS | AFNOR | BS | EN | UNI | UNE | BDS | MSZ | PN | STAS | CSN | ||||||||||||||||||||||||||||||||||||||||
|
|
|
|
|
|
|
Обозначения:
Механические свойства : | |
sв | – Предел кратковременной прочности , [МПа] |
sT | – Предел пропорциональности (предел текучести для остаточной деформации), [МПа] |
d5 | – Относительное удлинение при разрыве , [ % ] |
y | – Относительное сужение , [ % ] |
KCU | – Ударная вязкость , [ кДж / м2] |
HB | – Твердость по Бринеллю , [МПа] |
Физические свойства : | |
T | – Температура, при которой получены данные свойства , [Град] |
E | – Модуль упругости первого рода , [МПа] |
a | – Коэффициент температурного (линейного) расширения (диапазон 20o – T ) , [1/Град] |
l | – Коэффициент теплопроводности (теплоемкость материала) , [Вт/(м·град)] |
r | – Плотность материала , [кг/м3] |
C | – Удельная теплоемкость материала (диапазон 20o – T ), [Дж/(кг·град)] |
R | – Удельное электросопротивление, [Ом·м] |
Свариваемость : | |
без ограничений | – сварка производится без подогрева и без последующей термообработки |
ограниченно свариваемая | – сварка возможна при подогреве до 100-120 град. и последующей термообработке |
трудносвариваемая | – для получения качественных сварных соединений требуются дополнительные операции: подогрев до 200-300 град. при сварке, термообработка после сварки – отжиг |
yaruse.ru
свойства, характеристики, применение сплава 40хн2м
Рассматривая химический состав этой стали, стоит отметить относительное большое количество легирующих добавок, которые в данном случае повышают не только коррозионную стойкость материала, но и прочность, значительно снижая вероятность хрупкого разрушения металла под воздействием каких-либо сред или механических нагрузок. Уникальные свойства, которыми обладает высокопрочная хромоникельмолибденовая легированная конструкционная сталь 40хн2ма, находят применение в изготовлении наиболее ответственных деталей промышленных машин и агрегатов: шатунов, клапанов, коленчатых валов и прочих тяжелонагруженных деталей.
Набор химических элементов в данном сплаве подобран следующим образом:
- Ni – 1,25-1,65%
- Cr – 0,60-0,90%
- Mn – 0,50-0,80%
- Si – 0,17-0,37%
- Cu – до 0.30%
- Mo – 0,15-0,25%
- P – до 0,025%
- S – до 0,025%
Сталь 40хн2ма принадлежит к числу трудносвариваемых, т.е. перед сварными работами она требует предварительного подогрева (200-300оС), а также подвергается отжигу после сварки.
Технологические свойства стали 40хн2ма и ГОСТы выпуска
Помимо трудносвариваемости этой легированной стали присуща флокеночувствительность: при нарушении технологии изготовления сплава в материале часто возникают дефекты внутреннего строения, сильно снижающие вязкость и пластичность стали. Температура ковки этого высокопрочного материала – 1200оС (начало процесса) и 800оС (конец процесса). При этом финишным этапом данной обработки будет включать отжиг с перекристаллизацией, 2 переохлаждения и последующий отпуск.
Хромоникельмолибденовый конструкционный сплав 40хн2ма может выпускаться в виде фасонного и сортового проката. В своей работе производители пользуются следующими ГОСТами:
- ГОСТ 8479-70 и ГОСТ 1133-71 – изготовление поковок и прочих кованых заготовок
- ГОСТ 103-76 – изготовление полос
- ГОСТ 14955-77 – производство серебрянки и шлифованного прутка
- ГОСТ 7417-75, ГОСТ 1051-73, ГОСТ 10702-78, ГОСТ 8559-75, ГОСТ 8560-78 – изготовление калиброванного прутка
- ГОСТ 4543-71, ГОСТ 2879-69, ГОСТ 10702-78, ГОСТ 2590-71, ГОСТ 2591-71 – фасонный прокат
Иностранные аналоги данной марки стали представлены в следующей таблице:
Сферы применения легированного сплава 40хн2ма
Благодаря относительно высокому содержанию молибдена, этот материал характеризуется полным отсутствием обратимой отпускной хрупкости. Высокая прочность улучшенной хромоникелевой конструкционной стали 40хн2ма позволяет применять данный сплав для изготовления высокоответственных тяжелонагруженных деталей промышленного оборудования.
Из материала марки 40ХН2МА производят цельнокатаные кольца, ответственные болты, кулачковые муфты, крепежные детали, диски, валки. Материал находит применение и в производстве трубопроводной арматуры, и в изготовлении деталей для авиастроительной промышленности, которые должны выдерживать рабочие температуры до +500оС.
fx-commodities.ru
40ХН2МА :: Металлические материалы: классификация и свойства
Сталь 40ХН2МА ГОСТ 4543-71
Группа стали – хромоникельмолибденовая
Массовая доля элементов, % | ||||||||
Углерод | Кремний | Марганец | Хром | Никель | Молибден | Алюминий | Титан | Ванадий |
0,37-0,44 | 0,17-0,37 | 0,50-0,80 | 0,60-0,90 | 1,25-1,65 | 0,15-0,25 | – | – | – |
Ac1 | Ac3(Acm) | Ac3(Arcm) | Ar1 | Mн |
730 | 820 | 550 | 380 | 320 |
Число твердости, НВ, не более | |
Отожженный или высокоотпущенный прокат | 269 |
Нагартованный прокат | 269 |
Термообработка | Передел текучести σт, Н/мм2 (кгс/мм2) не менее | Временное сопротивление σв, Н/мм2 (кгс/мм2) | Относительное удлинение δ5,% | Относительное сужение ψ, % | Ударная вязкость KCU, Дж/см2 (кгс·м/см2) | Размер сечения заготовок для термической обработки (диаметр круга или сторона квадрата), мм | |||||
Закалка | Отпуск | ||||||||||
Температура, оС | Среда охлаждения | Температура, оС | Среда охлаждения | ||||||||
1-й закалки или нормализации | 2-й закалки | ||||||||||
не менее | |||||||||||
850 | – | Масло | 620 | Вода или масло | 1)930(95) 2)835(85) | 1080(110) 980(100) | 12 12 | 50 55 | 78(8) 98(10) | 25 25 |
Температура отпуска, ºС | Предел текучести ,σ0,2 МПа | Временное сопротивление σв, МПа | Относительное удлинение δ5 | Относительное сужение ψ | KCU, Дж/см2 | НВ |
% | ||||||
Закалка 850 ºС, масло | ||||||
200 300 400 500 600 | 1600 1470 1240 1080 860 | 1750 1600 1370 1180 960 | 10 10 12 15 20 | 50 50 52 59 62 | 59 49 59 88 147 | 525 475 420 350 275 |
Температура испытания, ºС | Предел текучести ,σ0,2 МПа | Временное сопротивление σв, МПа | Относительное удлинение δ5 | Относительное сужение ψ | KCU, Дж/см2 |
% | |||||
Закалка 850 ºС, масло. Отпуск 580 ºС | |||||
20 250 400 500 | 950 830 770 680 | 1070 1010 950 700 | 16 13 17 18 | 58 47 63 80 | 78 109 84 54 |
Образец диаметром 5 мм, длиной 25 мм, прокатанный. Скорость деформирования 2 мм/мин. Скорость деформации 0,001 1/с | |||||
700 800 900 1000 1100 1200 | – – – – – – | 185 89 50 35 24 14 | 17 66 69 75 72 62 | 32 90 90 90 90 90 | – – – – – – |
Сечение, мм | Место вырезки образца | Предел текучести, σ0,2 | Временное сопротивление σв, | Относительное удлинение δ5 | Относительное сужение ψ | KCU, Дж/см2 | НRCЭ |
МПа | % | ||||||
Пруток. Закалка 850 ºС, масло. Отпуск 620 ºС | |||||||
40 60 80 100 120 | Ц Ц 1/2R 1/2R 1/3R | 880 830 730 670 630 | 1030 980 880 850 830 | 14 16 17 19 20 | 57 60 61 61 62 | 118 127 127 127 127 | 33 32 29 26 25 |
Закалка 850 ºС, масло. Отпуск 540-560 ºС | |||||||
до 16 16-40 40-100 100-160 160-250 | Ц Ц Ц Ц Ц | 1000 900 800 700 650 | 1200-1400 1100-1300 1000-1200 900-1100 850-1000 | 9 10 11 12 12 | – – – – – | 90 50 60 60 60 | – – – – – |
Предел выносливости | Состояние стали | |
σ-1, МПа | τ-1, МПа | |
447 392 512(n=106) | 274 235 | Сечение 100 мм. Закалка 850 ºС, масло. Отпуск 580 ºС, σв=880 МПа Сечение 400 мм. Закалка 850 ºС, масло. Отпуск 610 ºС, σв=790 МПа σ0,2=880 МПа, σв=1080 МПа |
Температура, ºС | Термообработка | ||
20 | -40 | -60 | |
Ударная вязкость KCU, Дж/см2 | |||
103 | 93 | 59 | Закалка 860 ºС, масло. Отпуск 580 ºС |
Расстояние от торца, мм | Примечание | ||||||||||
1,5 | 3 | 6 | 9 | 12 | 15 | 21 | 27 | 33 | 42 | Закалка 840 ºС | |
Прокаливаемость | |||||||||||
49-59,5 | 49,5-60 | 50-60 | 50-59,5 | 49-59 | 48-58 | 45-56 | 41,5-53 | 41-50,5 | 36,5-48,5 | Твердость для полос прокаливаемости, HRCЭ | |
Количество мартенсита, % | Критическая твердость, HRCЭ | Критический диаметр, мм | |
в воде | в масле | ||
50 90 | 44-47 49-53 | 153 137-150 | 114 100-114 |
Среда | Температура, ºС | Коррозионная стойкость, глубина мм/год |
Вода | 300 | 0,05-0,1 |
Заменитель – стали: 40ХГТ, 40ХГР, 30Х3МФ, 30ХН2МФА.
Температура ковки, ºС:
начала 1200,
конца 800.
Сечения до 80 мм – отжиг с перекристаллизацией, два переохлаждения, отпуск.
Свариваемость – трудносвариваемая. Способ сварки – РДС. Необходим подогрев и последующая термообработка.
Обрабатываемость резанием – в горячекатаном состоянии при HB 228-235 и σв=560 МПа, КV т.в. спл =0,7, КV б. ст =0,4.
Флокеночувствительность – чувствительна.
Склонность к отпускной хрупкости – не склонна.
Назначение: коленчатые валы, клапаны, шатуны, крышки шатунов, ответственные болты, шестерни, кулачковые муфты, диски и другие тяжелонагруженные детали. Валки для холодной прокатки металлов.
По требованию потребителя, указанному в заказе, пачки, концы или торцы горячекатаных и кованых прутков, а по согласованию изготовителя с потребителем и калиброванных прутков из стали всех марок в зависимости от группы должны маркироваться краской в соответствии с таблицей
Группа стали | Цвет маркировки |
Хромоникельмолибденовая | Фиолетовый + черный |
Сортамент:
горячекатаная квадратная – ГОСТ 2591-88,
горячекатаная квадратная – ГОСТ 2590-88,
горячекатаная шестигранная – ГОСТ 2879-88,
горячекатаная полосовая – ГОСТ 103-76,
кованая круглая и квадратная – ГОСТ 1133-71,
калиброванная круглая – ГОСТ 7417-75,
калиброванная квадратная – ГОСТ 8559-75,
калиброванная шестигранная – ГОСТ 8560-78,
серебрянка – ГОСТ 14955-77
markmet.ru
Марка стали |
Вид поставки Поковки – ГОСТ 8479–70, ОСТ 108.958.04–85, ТУ 108.13.32–88. Сортовой прокат – ГОСТ 4543–71. |
|||||||||||||||||||||||||||||||||||||||||||||
40ХН2МА (40ХНМА) |
||||||||||||||||||||||||||||||||||||||||||||||
Массовая доля элементов, % по ГОСТ 4543–71 |
Температура критических точек, ºС |
|||||||||||||||||||||||||||||||||||||||||||||
C |
Si |
Mn |
S |
P |
Cr |
Ni |
Mo |
V |
W |
Ti |
Cu |
Ас1 |
Ас3 |
Аr1 |
Аr3 |
|||||||||||||||||||||||||||||||
0,37–0,44 |
0,17–0,37 |
0,50–0,80 |
≤ 0,025 |
≤ 0,025 |
0,60– 0,90 |
1,25– 1,65 |
0,15– 0,25 |
– |
– |
– |
≤ 0,30 |
730 |
820 |
380 |
550 |
|||||||||||||||||||||||||||||||
Механические свойства при комнатной температуре |
||||||||||||||||||||||||||||||||||||||||||||||
НД |
Режим термообработки |
Сечение, мм |
σ0,2, Н/мм2 |
σВ, Н/мм2 |
δ, % |
Ψ, % |
KCU, Дж/см2 |
КП |
НВ |
|||||||||||||||||||||||||||||||||||||
Операция |
t, ºС |
Охлаждающая среда |
не менее |
|||||||||||||||||||||||||||||||||||||||||||
ГОСТ 4543–71 |
Отжиг |
820–840 |
С печью |
Свыше 5 |
Не определяются |
≤ 269 |
||||||||||||||||||||||||||||||||||||||||
Закалка Отпуск |
835–865 570–670 |
Масло Вода |
До 80 Свыше 80 до 150 Свыше 150 |
930 930 930 |
1080 1080 1080 |
12 10 9 |
50 45 40 |
78 70 66 |
– |
|||||||||||||||||||||||||||||||||||||
Закалка Отпуск |
835–865 570–670 |
Масло Вода |
До 80 Свыше 80 до 150 Свыше 150 |
835 835 835 |
980 980 980 |
12 10 9 |
55 50 45 |
98 88 83 |
– |
|||||||||||||||||||||||||||||||||||||
ГОСТ 8479–70, ОСТ 108.958. 04–85 |
Закалка Отпуск |
840–860 550–650 |
Масло Вода или масло |
До 100 100–300 |
785 785 |
930 930 |
12 11 |
40 35 |
59 49 |
785 785 |
293–331 |
|||||||||||||||||||||||||||||||||||
До 100 100–300 |
735 735 |
880 880 |
13 12 |
40 35 |
59 49 |
735 735 |
277–321 |
|||||||||||||||||||||||||||||||||||||||
100–300 |
685 |
835 |
12 |
38 |
49 |
685 |
262–311 |
|||||||||||||||||||||||||||||||||||||||
100–300 300–500 |
640 640 |
785 785 |
12 11 |
38 33 |
49 44 |
640 640 |
248–293 |
|||||||||||||||||||||||||||||||||||||||
100–300 500–800 |
590 590 |
735 735 |
13 10 |
40 30 |
49 39 |
590 590 |
235–277 |
|||||||||||||||||||||||||||||||||||||||
100–300 300–500 |
540 540 |
685 685 |
13 12 |
40 35 |
49 44 |
540 540 |
223–262 |
|||||||||||||||||||||||||||||||||||||||
300–500 500–800 |
490 490 |
655 655 |
12 11 |
35 30 |
49 39 |
490 490 |
212–248 |
|||||||||||||||||||||||||||||||||||||||
500–800 |
440 |
635 |
11 |
30 |
39 |
440 |
197–235 |
|||||||||||||||||||||||||||||||||||||||
Назначение. Коленчатые валы, клапаны, шатуны, крышки шатунов, ответственные болты и силовые шпильки, шестерни, кулачковые муфты, диски турбокомпрессоров и другие тяжело нагруженные детали сложной конфигурации, работающие при динамических нагрузках, к которым предъявляются требования высокой прочности при достаточной пластичности и вязкости. Сталь теплоустойчива до 450 ºС. |
||||||||||||||||||||||||||||||||||||||||||||||
Предел выносливости, Н/мм2 |
Термообработка |
Ударная вязкость, KCU, Дж/см2, при t, ºС |
Термообработка |
|||||||||||||||||||||||||||||||||||||||||||
σ-1 |
τ-1 |
+ 20 |
0 |
– 20 |
– 40 |
– 60 |
– 80 |
|||||||||||||||||||||||||||||||||||||||
447 |
274 |
Закалка с 850 ºС в масле, отпуск при 580 ºС, σВ = 880 Н/мм2. Сечение 100 мм |
103 |
– |
– |
93 |
59 |
– |
Закалка с 860 ºС в масле, отпуск при 580 ºС |
|||||||||||||||||||||||||||||||||||||
392 |
235 |
Закалка с 850 ºС в масле, отпуск при 610 ºС, σВ = 795 Н/мм2. Сечение 400 мм |
||||||||||||||||||||||||||||||||||||||||||||
Технологические характеристики |
||||||||||||||||||||||||||||||||||||||||||||||
Ковка |
Охлаждение поковок, изготовленных |
|||||||||||||||||||||||||||||||||||||||||||||
Вид полуфабриката |
Температурный интервал ковки, ºС |
из слитков |
из заготовок |
|||||||||||||||||||||||||||||||||||||||||||
Размер сечения, мм |
Условия охлаждения |
Размер сечения, мм |
Условия охлаждения |
|||||||||||||||||||||||||||||||||||||||||||
Слиток |
1220–800 |
До 800 |
Отжиг с перекристаллизацией, два переохлаждения, отпуск |
До 80 |
Отжиг с перекристаллизацией, два переохлаждения, отпуск |
|||||||||||||||||||||||||||||||||||||||||
Заготовка |
1220–800 |
|||||||||||||||||||||||||||||||||||||||||||||
Свариваемость |
Обрабатываемость резанием |
Флокеночувствительность |
||||||||||||||||||||||||||||||||||||||||||||
Трудно свариваемая. Способы сварки: РД, РАД и КТ. Необходимы подогрев и последующая термообработка. |
В горячекатаном состоянии при 228–235 НВ и σВ = 560 Н/мм2 К√ = 0,7 (твердый сплав), К√ = 0,4 (быстрорежущая сталь) |
Чувствительна |
||||||||||||||||||||||||||||||||||||||||||||
Склонность к отпускной хрупкости |
||||||||||||||||||||||||||||||||||||||||||||||
Не склонна |
||||||||||||||||||||||||||||||||||||||||||||||
Коррозионная стойкость |
||||||||||||||||||||||||||||||||||||||||||||||
Вид коррозии |
Среда |
t, ºС |
Длительность, ч |
Балл стойкости |
||||||||||||||||||||||||||||||||||||||||||
Общая |
Вода деминерализованная |
300 |
– |
1–2 |
||||||||||||||||||||||||||||||||||||||||||
Точечная |
Вода деминерализованная |
300 |
– |
Подвержена |
stalmaximum.ru