Размеры шпоночное соединение – . .
alexxlab | 22.01.2021 | 0 | Вопросы и ответы
Шпонка и шпоночное соединение: обозначение, виды, чертежи, материал
Шпоночное соединение – разновидность соединения, состоящего из шпонки на валу и ступицы. Шпонкой называется деталь, которая соединяет узлы путем установки в пазы. Основной ее функцией является передача вращающего момента между узлами. Существует определенная стандартизация их разновидностей. Шпонка имеет специальные пазы, вырезанные путем фрезерования.
Применение
Основным применением шпоночных соединений является монтаж на вал с помощью пазового соединения. В большинстве своем шпоночный паз напоминает клин. Такой тип соединения деталей позволяет валу и ступице не проворачиваться относительно оси друг друга. Фиксированное положение ступицы к валу со шпонкой позволяет добиться высокого КПД при передаче усилия.
Наиболее часто шпоночное соединение можно встретить в машиностроении, при строительстве станков. Часто она используется при производстве автомобилей и других механизмов, где требуется повышенная надежность фиксации деталей машин. Высокая надежность достигается благодаря функции предохранительного узла вала со шпоночным пазом.
Шпонка выступает предохранителем в случаях превышения максимального уровня крутящего момента. В подобных случаях происходит срез шпонки, поглощая чрезмерную нагрузку она снимает ее из вала и ступицы.
Благодаря своим свойствам она стала широко распространенной в машиностроении, она отличается высокой эффективностью, простотой изготовления и монтажа, а также низкой стоимостью. Подобные характеристики особо важны в промышленном производстве, особенно в сельском хозяйстве. В разгар сезона часто возникают случаи поломок отдельных узлов, которые нужно заменить максимально быстро. Чаще всего можно встретить в узлах пресс-подборщиков.
Учитывая все вышесказанное, выделяются основные позиции, для чего нужна шпонка:
- Обеспечение безопасность соединяемых узлов при повышенных нагрузках.
- Достижение высокой степени фиксации отдельных элементов механического узла.
- Выполняет функцию предупреждения проворачивания узла и ступицы.
- Надежность подобного соединения превышает надежность аналогов при фиксации вала с деталями.
В общем, встретить шпоночное соединение можно практически в любом сложном механизме, что обусловлено его техническими характеристиками.
Виды шпонок
Основные виды шпонок делят на два типа: напряженные и ненапряженные. Среди которых выделяются такие типы шпонок:
- Клиновые. Особый тип, который отличаются углом наклона верхней грани. В общем разделение на виды происходит исходя из классификации шпоночных соединений. Устанавливается в паз с помощью физической силы, ударным методом. Применение такого типа соединения позволяет добиться необходимого напряжения. Нарезанный клин, находясь в пазе, распирает его изнутри. За счет силы прижатия, вал и ступица совместно вращаются.Используется довольно редко, так как ее использование предусматривает индивидуальный подгон. Это можно считать недостатком для массового производства механизмов. Основное назначение — применение в тихоходных передачах и узлах неподвижного соединения.
Среди клиновых шпонок выделяют:
- врезные;
- на лыске;
- фрикционные;
- без головки и с головкой.
- Сегментные. Производятся в виде сегментной пластины, загоняемой в паз. Производиться методом фрезерования. Широко применяются в производстве, так как просты в изготовлении, не требуют особой точности при нарезании и легко устанавливается. Отличается установкой в боле глубокий паз, в сравнении с аналогами. Глубокий паз не подходит для больших нагрузок, так как значительно снижает прочность вала, поэтому используется при небольших крутящих моментов.
На длинных ступицах может устанавливаться несколько шпонок, так как они имеют фиксированную длину. Выполняют предохранительную функцию на срез и смятие.
- Призматические. Отличаются параллельными гранями, которые устанавливаются в паз и фиксируют ступицу. Рабочими гранями в таки случаях являются боковые. Относятся к ненапряженному типу шпоночных соединений, поэтому существует вероятность возникновения коррозии в месте соединения. Для исключения коррозии, муфта и вал соединяются с натягом. Концы производятся обычно со скругленными или плоскими концами. Для скругленного типа рабочей поверхностью считается длина прямых краев. Паз нарезается с помощью фрезы.Передача усилия происходит путем давления поверхности паза на шпонку, которая передает крутящий момент на паз ступицы. Данный тип соединения призматической шпонкой часто используется для подвижных соединений, поэтому используют дополнительное крепление с помощью винтов. Как и многие другие типы выполняет функцию предохранителя при смятии и срезе.
- Цилиндрические. Штифты в таких шпонках изготавливаются в виде цилиндров. Работаю в натяжении с отверстием на торце вала, которое высверливается под соответствующие размеры шпонок. Используется в тех случаях, когда ступица устанавливается на конце вала. Требует особого подхода к монтажу шпоночных соединений.Позволяют работать на срез и смятие. Поэтому выбор шпонки производят исходя из прочности на смятие.
- Клиновые. Особый тип, который отличаются углом наклона верхней грани. В общем разделение на виды происходит исходя из классификации шпоночных соединений. Устанавливается в паз с помощью физической силы, ударным методом. Применение такого типа соединения позволяет добиться необходимого напряжения. Нарезанный клин, находясь в пазе, распирает его изнутри. За счет силы прижатия, вал и ступица совместно вращаются.Используется довольно редко, так как ее использование предусматривает индивидуальный подгон. Это можно считать недостатком для массового производства механизмов. Основное назначение — применение в тихоходных передачах и узлах неподвижного соединения.
Исходя из типа посадки выделяются:
- Свободная – применяется в случаях, когда выполнять сварочные работы довольно сложно и есть необходимость подвижного сцепления деталей во время работы.
- Плотная – нужна для создания сцеплений, движение которых во время работы выполняется в одном пространственном положении.
Обозначения на чертежах
На чертежах обозначение призматических шпонок происходит исходя из нормативного документа ГОСТ. Они делятся на шпоночные пазы: высокие, нормальной высоты и направляющие. Рабочими гранями у них являются боковые.
На сборочном чертеже обозначение выполняется с учетом диаметра вала, крутящего момента, сечения и длины.
Например:
Шпонка 3–20Х12Х120 ГОСТ 23360-78;
Где 3 – исполнение, 20Х12 – сечение, 120 – длина.
Скачать ГОСТ 23360-78
Обозначение остальных типов шпонок на изображениях выполняется таким же образом, исходя из соответствующих ГОСТов, разработанных для каждой отдельной модели.
Указанное обозначение должно четко характеризировать деталь, что очень важно для получения надежного соединение. Ведь даже малейший зазор может стать причиной быстрого износа рабочих узлов и потери эффективности во время работы.
Достоинства и недостатки
Как и любой тип соединений, шпоночные имеют ряд достоинств и недостатков. К достоинствам шпоночных соединений можно отнести простоту большинства типов шпонки. При этом монтаж и замена такой детали выполняется легко и быстро. Благодаря чему они получили широкое применение в машиностроении. Также обеспечивает функцию предохранения.
К недостаткам относиться ослабление ступицы и вала. Оно возникает исходя из повышенного напряжения и уменьшения поперечного сечения. Также ослабление деталей вызвано из-за нарезанного паза, который снижает осевую прочность вала.
Чтобы минимизировать недостатки, нужно добиться отсутствия перекоса шпонки в пазе. Для этого нужно обеспечить отсутствие зазора, что делается путем индивидуального изготовления и подгона шпонки. Из-за этого в крупносерийном производстве редко применяют любые разновидности шпоночных соединений. Если добиться отсутствия перекоса не удалось, площадь рабочего контакта уменьшается, в следствие чего степень максимальной нагрузки уменьшается.
Также наличие зазора вызывает эффект биения, особенно на высоких скоростях. Это приведет к быстрому износу рабочих деталей. Из-за этого подобное соединение редко применяется для быстровращающихся валов. Для подбора подходящей шпонки лучше использовать таблицу шпоночных соединений.
Материал шпонок
Для изготовления шпоночного соединения применяют калибровочный металлопрокат. Чаще всего используется сталь марки 45. Она относиться к углеродистым сталям обычного типа, которая часто применяется для производства деталей высокой прочности. Сталь используется в виде бруска длиной 1 м.
В некоторых случаях может применять углеродистая сталь марки 50. Она необходима, когда требуется повышенные прочностные свойства полученных шпонок. Реже применяются легированные стали, например, марки 40х, для которой характерен высокий показатель твердости, достигаемый путем термической обработки.
Скачать ГОСТ 8787-68
Стальные заготовки обрабатываются с помощью фрезы, сверлильных станков, станков для рубки, шлифовальных машин и других инструментов. Используемые станки имеют блок управление, который позволяет с помощью числовых программ изготовить деталь необходимых параметров.
Цена полученной шпонки довольно низка, поэтому приобрести необходимую деталь довольно легко. Но в некоторых случаях, когда есть необходимость срочного получения шпонки, изготовить ее можно самостоятельно. Чаще всего подобная необходимость возникает в сельском хозяйстве, где во время сезонных работ часто возникают поломки, которые нужно отстранить. При этом ближайшие точки продажи необходимых деталей находиться на расстоянии в несколько десятков километров.
Имея небольшое количеству инструмента под рукой и заготовку из соответствующего материала, можно быстро изготовить временную замену. При соблюдении технических характеристик, полученная деталь сможет полноценно заменить заводскую, но лучше всего при первой возможности приобрести шпонку нужной прочности и геометрических параметров. Это необходимо для избежание преждевременного износа механизмов.
Иногда для производства могут использовать другие материалы, например, пластик высокого качества. В качестве материала может использоваться дерево, чаще всего при изготовлении мебели.
В качестве материала лучше использовать разные породы дерева, для шпонки подойдет более мягкий материал чем основной. Это позволит обезопасить основную конструкцию от повреждений в случае повышенной нагрузки. Легче заменить шпонку чем большой конструкционный узел.
Для предотвращения проникания влаги в железобетонные конструкции используются специальные шпонки – ватерстоп. Изготавливают их из резины высокого качества и ПВХ. Это позволяет добиться необходимой степени водонепроницаемости и стойкости к растворам агрессивных химических веществ.
Заключение
Такой тип соединения отличается простотой и достаточно высокой надежностью, из-за чего получил высокую популярность в промышленности. Разнообразие видов позволяет подобрать оптимальный тип соединения, что позволит добиться высокой эффективности, надежности готовой конструкции и страховку узлов от повреждений при повышении допустимых нагрузок. Подобрав шпонку исходя из соответствующих ГОСТов, можно добиться высокой эффективности работы соединения.
На сегодняшний день можно легко подобрать необходимую деталь, что позволяет быстро сделать монтаж и замену в случае необходимости.
Если вы нашли ошибку, пожалуйста, выделите фрагмент текста и нажмите Ctrl+Enter.
stankiexpert.ru
Соединения шпоночные
Шпонки применяются при соединении шкивов, зубчатых колес, муфт и других деталей с валом. Такое соединение называется шпоночным.
Шпонка представляет собой деталь, часть которой помещается в специальном углублении (пазу) на валу, а выступающая часть входит в углубление (паз), сделанное в детали, соединяемой с валом. Шпонки бывают скрепляющие и направляющие; скрепляющие шпонки делятся на клиновые, призматические и сегментные.
Шпонки клиновые: (смотри фигуру – 477, а) создают неподвижное напряженное соединение. По виду эти шпонки разделяются на забивные и закладные и бывают с головкой (ГОСТ 8793-58) и без головки (ГОСТ 8792-58).
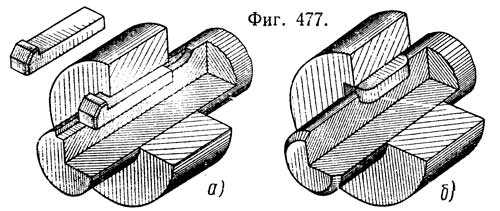
Шпонки призматические: (показана на фигуре – 477, б) обеспечивают неподвижное или скользящее (ненапряженное) соединение. Призматические шпонки разделяются на обыкновенные (ГОСТ 8789-58), применяемые для неподвижных соединений, и направляющие (ГОСТ 8790-58), применяемые для скользящих соединений. Призматические шпонки изготовляются из чистотянутой стали для шпонок (ГОСТ 8787-58), имеющей поперечное сечение в виде прямоугольника со срезанными или закругленными вершинами. Концы шпонок бывают плоские (исполнение Б) и скругленные (исполнение А) (фиг. 478).
Размеры сечений призматических шпонок, пазов и длин шпонок подбираются в зависимости от диаметра вала по ГОСТ 8788-58. Смотри таблицу размеров № 26. Пример условного обозначения шпонки исполнения А с размерами b = 20 мм; h = 12 мм;
На рабочем чертеже следует проставлять один размер в зависимости от принятой базы обработки и измерения: D + t1 – для втулки и D – t или t – для вала. На фигуре 480 приведены три примера изображения деталей со шпоночными пазами для призматической шпонки: два варианта конца вала (480, а, б) и диск муфты (480, в).
Сегментные шпонки: (изображена на фигуре – 481) создают ненапряженное соединение. Сегментные шпонки изготовляются из чистотянутой шпоночной сегментной стали (ГОСТ 8786-58).
Поперечное сечение прутка представляет собой сегмент. Размеры сегментных шпонок установлены ГОСТ 8795-58, а размеры шпонок и пазов в зависимости от диаметра вала – ГОСТ 8794-58 (табл. 27 и фиг. 482).
Исполнения I и II выбираются из условия равнопрочности элементов шпоночного соединения в зависимости от материала втулки. Пример условного обозначения шпонки сегментной с размерами b = 7 мм; h = 11 мм: Шпонка сегментная 7 X 11 ГОСТ 8795-58.
Соединения зубчатые (шлицевые)
www.viktoriastar.ru
Шпоночные соединения размеры пазов – Энциклопедия по машиностроению XXL
После сборки шпоночного соединения (рис. 364, между пазом вту лки и верхней г ранью шпонки должен быть небольшой зазор (рис. 364,6) размеры пазов на валу и во втулке выбирают по СТ СЭВ 189-75. [c.204]Выбрать тип шпоночного соединения и подобрать шпонку для соединения втулки с валом (рис. 13.8, а). Наметить посадки по сопрягаемым размерам рассчитать предельные зазоры и натяги начертить схему полей допусков указать на чертеже шпоночного соединения предельные отклонения определить размеры и предельные отклонения несопрягаемых размеров шпонки и пазов привести условное обозначение шпонки.
Основным критерием работоспособности шпоночных соединений является прочность. Шпонки выбирают по таблицам ГОСТов в зависимости от диаметра вала, а затем соединения проверяют на прочность. Размеры шпонок и пазов в ГОСТах подобраны так, что прочность их на срез и изгиб обеспечивается, если выполняется условие прочности на смятие, поэтому основной расчет шпоночных соединений — расчет на смятие. Проверку шпонок на срез в большинстве случаев не производят. [c.75]
Шпоночное соединение показано на рис. 20. Допуски па размеры шпонок и пазов назначают [c.531]
Для шпоночных соединений, работающих с повышенными ударными нагрузками или с частым изменением направления вращения, необходимо применять шпонку большего сечения (усиленную). Размеры сечений усиленных шпонок и пазов и их предельные отклонения приведены в табл. 9.8. [c.212]
В зависимости от принятых баз обработки и измерения на рабочих чертежах должны указываться следующие размеры для глубины паза шпоночного соединения [c.212]
Предельные отклонения размеров пазов вала и втулки (для шпоночных соединений) [c.102]
При выполнении шпоночного соединения по первому и второму вариантам требуется подбор или пригонка шпонки по месту. При сборке шпоночных соединений больших размеров шпонки и шпоночный паз пришабривают. Точность пригонки проверяют щупами. [c.729]
Метод совместной обработки применяют для устранения необходимости выдерживать точные размеры стыковых поверхностей при обработке деталей большого веса и размеров. Так, правая и левая станины рабочей клети соединяются между собой с помощью фланцев, траверс, распорок. У станин, которые соединяются между собой с помощью фланцев, обычно начинают обрабатывать первыми поверхности фланцевых приливов. Поверхности разъемов фланцевых соединений располагаются по торцам лап и по верхней поперечине и являются наиболее возвышенными обрабатываемыми поверхностями. Они должны лежать строго в одной плоскости. Несовпадение плоскостей вызывает большие слесарно-пригоночные работы. Парные станины обычно фиксируются одна по отношению к другой с помощью шпоночных соединений. Для этого три шпоночных паза располагаются вдоль продольной оси станины на разъемах фланцевых приливов. Положение всех трех шпоночных пазов у обеих парных станин должно быть строго одинаковым.
Работы по конструктивной нормализации и унификации деталей и отдельных элементов, как например, применение ограниченного ряда нормальных диаметров, длины ступиц, размеров шпоночных пазов и другие, в сочетании с групповым запуском, создают условия для достаточно широкого применения протягивания даже в условиях мелкосерийного и единичного производства. Так, например, на некоторых предприятиях в диапазоне диаметров 70— 230 мм установлено всего восемь нормальных значений размеров шлицевых соединений. Для шпоночных соединений в диапазоне ширины шпонок 5—100 мм принято двадцать нормальных значений размеров и т. д. [c.32]
Смятие или выработка шпоночного паза Внешний осмотр. Замер размеров шпоночного соединения Смятие и выработка шпоночного паза не допускаются. Разрешается установка для каждых двух дисков коротких отдельных шпонок, закрепляемых двумя винтами. Отклонение шпоночного паза от направления оси вала. не должно быть более 0,15 мм на длине 1 м, но не более 0,3 мм на всей длине паза Фрезеровка нового шпоночного паза на роторе и строжка паза на диске. Перед установкой дисков после ремонта шпоночного паза проверить соосность посадочных отверстий дисков, отверстий под пальцы и шпоночных пазов
В любом шпоночном соединении имеется две разные посадки посадка шпонки в паз вала и посадка ее в паз втулки, что предопределяет применение системы вала. В системе вала посадочным размером является ширина шпонки Ь, по которой предусмотрено три вида соединения свободное, нормальное, плотное (табл. 2.4). [c.104]
Шпоночное соединение имеет стандартные соотношения размеров сторона квадрата шпонки — /4 глубина паза на валу — /8 от- [c.388]
В шпоночных соединениях применяют клиновые, призматические и сегментные шпонки. Требуемая точность сборки шпоночных соединений обеспечивается изготовлением их элементов с допусками. Вследствие того, что посадки в пазах вала и охватывающей детали различны, размеры шпонок выполняют в системе вала. [c.916]
Контроль шпоночных соединений в серийном и массовом производстве осуществляется специальными предельными калибрами ширина пазов Ь — пластинами, размер D -г отверстия) — пробками и размер t (у вала) — кольцами. Симметричность пазов относительно осевой плоскости проверяют у отверстия пробкой со шпонкой, а у вала-накладной призмой с контрольным стержнем. [c.445]
Шпоночные соединения. Допуски и посадки Шпонки призматические. Размеры сечений шпонок и пазов Шпонки призматические. Размеры [c.216]
Ниже рассмотрены способы восстановления шпоночных пазов. При большем износе шпоночный паз ремонтируют наваркой грани (рис. 52, а) с последующим фрезерованием. При этом выдерживают размер паза, установленный стандартом. Возможен и такой ремонт паз расширяют и углубляют, полностью устраняя следы износа, затем к нему изготовляют ступенчатую шпонку (рис. 52, б). Однако при таком ремонте не обеспечивается высококачественное соединение и поэтому его применяют в исключительных случаях (при осмотрах и текущих ремонтах). Поэтому когда на чертеже нет указаний о фиксированном положении шпоночного паза, допускают изготовление нового шпоночного паза на другом месте без заделки старого (не более одного на сечение). Его фрезеруют параллельно старому пазу в диаметральной плоскости, расположенной относительно этого паза под углом 90, 135 или 180°. [c.100]
Шпонки выбирают по таблицам стандарта в зависимости от диаметра вала, а затем соединение проверяют на прочность. Размеры шпонок и пазов подобраны так, что прочность их на срез и изгиб обеспечена, если выполнено условие прочности на смятие, поэтому основной расчет шпоночных соединений -расчет на смятие. [c.51]
Для шпоночных соединений с клиновыми шпонками размеры элементов соединения в соответствии с ГОСТ 24068—80 даны в табл. 4.69.1, а предельные отклонения несопрягаемых размеров — в табл. 4.69.2. Для шпоночных соединений с тангенциальными нормальными и усиленными шпонками размеры их и соответствующих им шпоночных пазов на валах и во втулках (с указанием предельных отклонений) даны соответственно в табл. 4.70.1 И4.70.2. [c.270]
Шпоночные соединения валов со втулками, передающие крутящие моменты, имеют широкое распространение в машиностроении. Стандартизованы размеры сечений шпонок и пазов, а также теоретические веса шпонок [c.236]
Допуски и посадки установлены для призматических и сегментных шпоночных соединений (ГОСТ 7227—58). Эти ГОСТы не распространяются на шпоночные посадки с пригонкой или с подбором шпонок, а также на специальные посадки (ходовые валики, сердечники электромашин и т. п.). Обозначения размеров шпонок и пазов призматических шпоночных соединений показаны на рис. 1.141, а, а сегментных на рис. 1.141, б. [c.236]
В соединениях деталей, осуществляемых посредством шпонок, различают преимущественно клиновые, призматические и сегментные шпонки. В процессе сборки шпоночных соединений с клиновыми шпонками ось охватывающей детали смещается по отношению к оси вала на величину посадочного зазора е (фиг. 151). Таким образом, для уменьшения биения охватывающей детали после сборки шпоночного соединения посадочный зазор желательно сокращать до минимума. При сборке соединения с клиновой шпонкой необходимо добиваться, чтобы дно паза охватывающей детали имело уклон, соответствующий уклону шпонки, так как иначе ступица будет сидеть на валу с перекосом (фиг. 152). Шпонка и пазы значительных размеров нередко при сборке пришабриваются. Точность пригонки контролируется проверкой зазоров щупом между шпонкой и дном паза ступицы, а также между ступицей и валом с обоих торцов. [c.206]
Пазы вала и втулки выполнены в системе вала с различными посадками 5 зависимости от требуемого характера соединения. Для повышенной точ-тости шпонка выполняется с отклонениями по для нормальной — по а для грубой — по А4. Допускаемые отклонения в размерах шпонок и пазов для клиновых шпоночных соединений при шпонках из поковок даны по ЭСТ/НКМ 4087. [c.245]
При небольшой разработке шпоночный паз расширяют н ставят новую шпонку. Так как расширить паз в отверстии трудно, то расширяют паз на валу и ставят ступенчатую шпонку. При большой разработке паза и шпонки паз переносят на новое место (под углом 90, 120 или 180°), новую шпонку изготовляют из металла более мягкого, чем вал. Подгонку шпонки к пазу производят на краску, а размеры шпонки выбирают так, чтобы по высоте шпоночного соединения был небольшой просвет. [c.308]
Шпоночные соединения. В соединениях применяют клиновые, призматические, сегментные и тангенциальные шпонки. Размеры шпонок и пазов регламентированы следующими стандартами шпонки призматические обыкновенные—ГОСТ 8789—68 шпонки призматические высокие— ГОСТ 10748—68 шпонки призматические на- [c.34]
Шпонки применяют для разъемного соединения деталей (шкивов, маховиков, зубчатых колес и т. п.) с валом для передачи крутящего момента и осевой силы. Шпоночные соединения состоят из вала, шпонки и детали (колеса, втулки и т. п.), подлежащей соединению с валом. В таком соединении шпонка входит одновременно в паз вала и в паз колеса (рис. 309, а). При работе соединения боковые грани шпонки передают вращение от вала колесу или наоборот. Форма и размеры паза в обеих деталях [c.303]
Размеры пазов под шпонки стандартизованы. При выполнении чертежей шпоночных соединений необходимо руководствоваться для определения размера паза под призматические шпонки ГОСТ 8788—68, клиновые — ГОСТ 8791—68, сегментные — ГОСТ 8794—68. [c.305]
Примечания 1. См. примечания 2. 3. 4, 6, 7 к табл. 4.64. 2. Длины шпонок св. 500 мм должны выбираться нз ряда / 20 по ГОСТ 6636—69. 3. Допускается при условии сохранения взаимозаменяемости соединений применение пазов с глубинами tx и 2 отличными от указанных в данной таблице. 4. Пример условного обозначения шпонки исполнения 1 с головкой) с размерами Ь — 18 мм, й = 11 мм, / = 100 мм Шпонка ЗХ 11X100 ГОСТ 24068 — 80, то же исполнения 2 Шпонка 2 — 18X11X100 ГОСТ 24068 — 80, Должен соблюдаться в ответственных шпоночных соединениях. Размер /а относится к большей глубине паза [c.242]
Пазы в ступице выполняют долблением или протягиванием одношлицевой протяжкой, на валу — фрезерованием пальцевой ис. 249, а) или дисковой (рис. 249, б) фрезой. Фрезерование дисковой фрезой производительнее и обеспечивает более высокую точность и малую шероховатость боковых граней паза. Однако при этом способе увеличиваются осевые размеры шпоночного соединения, особенно в соединениях с упорными буртиками (рис. 250), а при заданных габаритах сокращается длина шпонки. Кроме того, необходима фиксация шпонки в осевом направлении. [c.234]
Для соединения втулок, шкивов, муфт, рукояток и других деталей машин с валами, когда к точности центрирования соединяемых деталей не предъявляют особых требований, применяют шпонки. Размеры, допуски и посадки большинства типов шпонок и пазов для них унифицированы для всех стран — членов СЭВ. Для получения различных посадок призматических шпонок установлены поля допусков на ширину Ь шпонок, пазов валов и втулок (ГОСТ 23360—78). Для ширины шпонки установлено поле допуска h9 (для высоты шпонки hll и для длины hl4), что делает возможным их централизованное изготовление независимо от посадок. Установлены следующие три типа шпоночных соединений свободное, нормальное и плотное. Для свободного соединения установлены ноля допусков ширины Ь для паза на валу Н9 и для паза во втулке D10, что дает посадку с зазором для нормального соединения — еоот-ветственно N9 и J,9 для плотного соединения — одинаковые поля допусков на ширину Ь для паза на валу и паза во втулке Р9. Нормальные и плотные соединения имеют переходные 1осадки. [c.334]
Анализ конструкций разных типов шпоночных соединений показывает, что на качество шпоночных соединений с призматическими, сегментными и клиновыми шпонками больше всего влияют посади по размеру Ь (ширина шпонки) в соедине-ииях шпонки с пазами вала и втулки, а также форма шпоночных пазов и иж расположение относительно цилиндрических посадочных поверхностей вала и В1улки. [c.203]
Стандарты СЭВ, введенные в соответствующие 1 ОСТы на шпоночные соединения, унифицируют нормы точности, что облегчает технологическую и метрологическую подготовку производства. Они устанавливают нормы точности посадок только по размеру Ь. Допуски формы и расположения пазов необходимо определять при конструировании соединений в зависимости от предт.являемых к ним требований. [c.203]
Если нет особых требований к диаметру фрезы (заданная разность ступеней в наборах фрез, заданная ширина паза и т. д.), то достаточно пользоваться следующим рядом наружных диаметров фрез 16 20 25 32 и т. д. — по основному ряду R10 предпочтительных чисел ГОСТа 8032—56, до 630 мм. Допускаемые отклонения на диаметр— по Be, конусность не должна превышать (в ту или другую сторону) 0,02 >1,и для фрез шириной L 50 мм. Диаметры шпоночных фрез нормализованы в соответствии с размерами шпоночных соединений в ряд 3 4 (5) 6 8 10 12 14 16 18 20 22 н т. д. Допускае.мые отклонения по диаметру — в зависимости от посадки и класса точности шпоночной канавки. [c.252]
Разрабатываемый проект СТ СЭВ на допуски шпоночных соединений с призматическими шпонками соответствует СТ СЭВ 57—73. Дополнительно для тер-мообработанных деталей допускаются предельные отклонения размера Ь паза вала по НИ, если это не влияет на работоспособность соединения. [c.211]
Шпоночные тангенциальные соединения для переменных и ударных нагрузок. Сечения umo-нок и их пазов Шпонки сегментные. Шпонки и шпоночные пазы. Размеры Соединения шпоночные клиновые низкие. Сечения шпонок и пазов. Размеры Шпонки призматические низкие. Размфы Шпоночные соединения призматические низкие. Сечения шпоночных пазов [c.216]
Соединения вал — ступица. Шпоночные соединения о призматическими шпонками рассчитывают на смятие боковых рабочих поверхностей паза или шпонки и на срез шпонки. Призматические шпонки стандартных размеров необходи1 10 проверять только на смятие. [c.233]
Соединения с клиновыми и тангенциальными шпонками встречаются значительно реже. Например, клиновые шпонки недопустимы при высоких требованиях к соосности соединяемых деталей, так как смещают их геометрические оси ка размер посадочного зазора. Эти соединения используют в тех случаях, когда подобные смещения осей не имеют Существенного значения (шкивы, маховики и т. п.). Клиновые шпоночные соединения бывают врезные (на валу паз в виде плоской канавки, а во втулке канавкй с уклоном 1 100), на лыске (на валу плоский срез, уклон 1 100 только в ступице детали), фрикционные, (канавка с уклоном 1 100 только в детали, поверхность шпонки, прилегающей к валу, цилиндрическая). Такие соединения применяют в тихоходных> передачах низкой точности. По ГОСТ 24068-Г-80 клиновые щпонки выполняют с головкой и без нее, пазы на валах и во втулках — в зависимости от конструкции шпонки. [c.269]
Качество сборки соединения зависит от перекосов и смещений в расиоложении шпоночных пазов как во втулках, так и на валах- Шероховатость, поверхностей деталей, образующих шпоночные соединения, влияет на точность и dnределенность посадок указания шероховатости на чертежах в табл. 4.64, 4.67, 4.69.1 не стандартизованы изменения к ГОСТ 8790—79 ГОСТ 24u71–80 , ГОСГ 24068- 80, ГОСТ 24069 -8U и ГОСТ 24070—80 включают общие рекомендации по взаимосвязи-шероховатости с квалитетами размеров — см. п. 2.5 ч. 1. [c.288]
На фиг. 541 представлен вал, в котором профрезерованы три шпоночных паза А, Б и С. Эти пазы были спроектированы и выполнены различной ширины. Паз В, профрезерованный в ступени большего диаметра, был сделан шире, чем пазы А и С, профрезерованные в ступенях меньших диаметров. При обработке каждого вала приходилось менять фрезы, что увеличивало вспомогательное время, между тем анализ работы этих шпоночных соединений показывает полную необоснованность различия в размерах шпонок. Крутяш,ий момент передается валу птонкой В и от вала шкиву итонкой А. Учитывая, что диаметр средней части вала больше, чем у конца, а момент [c.668]
В основу этих нормалей положено шпоночно-пазовое соединение элементов с размером паза 12 мм. Проект нормалей на малогабаритные детали и узлы с пазом 8 мм разрабатывает Научно-исследовательский институт технологии машиностроения (НИИТМАШ) Ленинградского совнархоза. [c.263]
mash-xxl.info
Соединения призматическими шпонками
Обратная связь
ПОЗНАВАТЕЛЬНОЕ
Сила воли ведет к действию, а позитивные действия формируют позитивное отношение
Как определить диапазон голоса – ваш вокал
Как цель узнает о ваших желаниях прежде, чем вы начнете действовать. Как компании прогнозируют привычки и манипулируют ими
Целительная привычка
Как самому избавиться от обидчивости
Противоречивые взгляды на качества, присущие мужчинам
Тренинг уверенности в себе
Вкуснейший “Салат из свеклы с чесноком”
Натюрморт и его изобразительные возможности
Применение, как принимать мумие? Мумие для волос, лица, при переломах, при кровотечении и т.д.
Как научиться брать на себя ответственность
Зачем нужны границы в отношениях с детьми?
Световозвращающие элементы на детской одежде
Как победить свой возраст? Восемь уникальных способов, которые помогут достичь долголетия
Как слышать голос Бога
Классификация ожирения по ИМТ (ВОЗ)
Глава 3. Завет мужчины с женщиной
Оси и плоскости тела человека – Тело человека состоит из определенных топографических частей и участков, в которых расположены органы, мышцы, сосуды, нервы и т.д.
Отёска стен и прирубка косяков – Когда на доме не достаёт окон и дверей, красивое высокое крыльцо ещё только в воображении, приходится подниматься с улицы в дом по трапу.
Дифференциальные уравнения второго порядка (модель рынка с прогнозируемыми ценами) – В простых моделях рынка спрос и предложение обычно полагают зависящими только от текущей цены на товар.
СОЕДИНЕНИЯ ТИПА ВАЛ-СТУПИЦА
Основные определения
Шпоночное соединение – соединение типа вал-ступица с помощью шпонки
Шлицевое соединение – соединение двух деталей: вала и ступицы колеса (шкива и т.п.), причем вал имеет выступы – зубья, входящие во впадины (шлицы) соответствующей формы в ступице.
Штифтовое соединение – соединение типа вал-ступица с помощью штифта.
Прессование– соединение деталей под прессом, путем запрессования или напрессование детали (изучалось выше, это есть соединение с натягом).
Шпонка – деталь шпоночного соединения, закладываемая одновременно в пазы вала и ступицы.
Штифт – это деталь в виде цилиндрического или конического стержня устанавливаемая с натягом радиально или параллельно оси (круглая шпонка).
Профильное соединение – это неподвижное соединение вала и ступицы, причем вал имеет определенный профиль поперечного сечения и входит в соответствующее отверстие ступицы.
Шариковое шлицевое соединение– это подвижное соединение вала и ступицы, рабочими элементами которого являются шарики входящие в соответствующие пазы вала и ступицы.
Шпоночные соединения
Функциональное назначение
Они предназначены для угловой или осевой фиксации ступиц деталей (зубчатых колес, звездочек, шкивов и т.п.) на валах.
Шпоночные соединения осуществляются при помощи специальных дополнительных деталей-шпонок, которые представляют собой стальной брус, вставляемый в пазы вала и ступицы.
Классификация соединений и виды шпонок
Шпоночные соединения делят на две группы:
– ненапряженные, в которых используют призматические или сегментные шпонки;
– напряженные, осуществляемые клиновыми, тангенциальными и
круглыми шпонками.
Наиболее полная классификация шпоночных соединений дана на рисунке 6.1.
Рисунок 6.1 – Классификация шпоночных соединений
Различают неподвижные и подвижные шпоночные соединения. В неподвижных шпоночных соединениях ступицы не могут перемещаться по валу в осевом направлении, а у подвижных соединений ступицы могут перемешаться по валу, в этом случае используют достаточно длинные направляющие шпонки которые крепятся к валу винтами.
Наибольшее применение в машиностроении имеют ненапряженные соединения, поэтому ограничимся их рассмотрением. Заметим, что в курсе машиностроительного черчения студенты уже знакомились с конструкцией таких соединений, геометрическими параметрами шпонок и их обозначением.
В напряженных шпоночных соединениях используют клиновые шпонки, однако они вызывают радиальное смещение ступиц относительно валов, что приводит к появлению дисбаланса. В настоящее время клиновые шпонки применяются крайне редко. Конструкция наиболее распространенных разновидностей напряженных шпоночных соединений дана на рисунке 6.2.
Рисунок 6.2 – Наиболее распространенные конструкции напряженных шпоночных соединений
Соединения призматическими шпонками
Эти соединения наиболее широко применяют в машиностроении; призматические шпонки стандартизованы и их размеры выбирают по ГОСТ 23360-78.
Достоинства: простота конструкции и низкая стоимость.
Недостатки: вал и ступица ослаблены шпоночными пазами; в зоне шпоночного паза возникает концентрация напряжений, что снижает усталостную прочность деталей соединений; трудно обеспечить их взаимозаменяемость, последнее вызывает необходимость ручной подгонки или подбора шпонки по пазу; малонадежная работа соединений при действии ударных, реверсивных и циклических нагрузок.
Шпонки общемашиностроительного назначения обычно изготавливают из углеродистых сталей 45 и 50 из проката, либо чисто тянутых профилей. В сильно нагруженных соединениях применяют шпонки из легированных сталей, например из стали 40Х с термической обработкой до твердости 35…45 HRC.
Ширину b и высоту h призматических шпонок выбирают по ГОСТ23360-78 в зависимости от посадочного диаметра d соединения.
Наиболее распространенные конструкции призматических шпонок даны на рисунке 6.3.
Рисунок 6.3 – Конструкции призматических шпонок
Обычно призматические шпонки вставляют в паз вала с натягом без дополнительного крепления, а в паз ступицы с небольшим зазором. Осевое фиксирование шпонки на валу наиболее просто осуществляют применением глухого паза, изготовленного концевой (пальцевой) фрезой. Однако. Наиболее предпочтительно изготовление паза на валу дисковой фрезой, при этом достигается более высокая точность изготовления размера b шпоночного паза и меньшая концентрация напряжений, однако, при этом осевая фиксация шпонки менее надежна.
Шпоночные пазы в ступице выполняют долблением (строганием) или протягиванием одношлицевой протяжкой.
Расчет шпоночного соединения с призматической шпонкой представлен на рисунке 6.4.
Рисунок 6.4 – Расчет соединения с призматическими шпонками
Действующий на соединение вращающий момент Т вызывает напряжения среза и напряжения смятия на боковых гранях шпонки. И пазов ступицы и вала. При стандартизации размеры поперечного сечения шпонок , а также глубину врезания шпонок в ступицу и в вал принимают таким образом, чтобы несущую способность соединения определяли напряжения смятия на боковых гранях шпонки. Для упрощения расчетов считают, что напряжения смятия (давление) распределены равномерно по площади контакта боковых граней шпонок и шпоночных пазов, а плечо равнодействующей этих напряжений равно половине диаметра вала в месте установки шпонки При этом, давлением на рабочие поверхности шпонок и пазов , возникающие при посадке шпонок в паз вала с натягом , пренебрегают.
megapredmet.ru
Выбор допусков и посадок шпоночных соединений — Мегаобучалка
Исходные данные
1. Диаметр вала d, мм__________________________
2. Конструкция шпонки__________________________
3. Вид соединения_
4. Условия работы_____
Последовательность выполнения задания
3.1. Определяют основные размеры шпоночного соединения.
3.2. Выбирают поля допусков деталей шпоночного соединения по ширине шпонки. (Таблица 3.1)
3.3. Назначить поля допусков и определить предельные отклонения остальных размеров шпоночного соединения. (Таблицы 3.2 … 3.5)
3.4. Вычертить схему расположения полей допусков размеров шпоночного соединения.
3.5. Подсчитать все размерные характеристики деталей шпоночного соединения и записать их в таблицу 3.6.
3.6. Определить предельные зазоры и натяги в соединениях «шпонка-паз вала» и «шпонка-паз втулки».
3.7.Вычертить эскизы шпоночного соединения и его деталей с указанием всех основных размеров и полей допусков.
Методические указания по выполнению
3.1. Номинальные размеры шпоночного соединения с призматическими шпонками определяют по приложению 8, а с сегментными — по приложению 9.
3.2. Выбор полей допусков деталей шпоночного соединения
по ширине шпонки зависит от вида соединения. Стандарт предусматривает три вида соединений по ширине шпонки: плотное, нормальное и свободное. Каждому из этих видов соединений соответствует определенный набор полей допусков на ширину шпонки, ширину паза вала и паза втулки. Все эти поля допусков для разных видов шпоночных соединений приведены в таблице 3.1. Численные значения предельных отклонений определяют при помощи таблиц приложений 1-3, а предельные отклонения, связанные с глубиной обработки пазов вала и отверстия втулки по таблицам 3.4 и 3.5.
Таблица 3.1_ Рекомендуемые поля допусков в соединениях «шпонка-паз вала» и «шпонка-паз втулки»
Вид соединения и характер производства | Поля допусков | ||
Ширина | |||
шпонки | паза вала | паза втулки | |
Плотные соединения при точном центрировании (индивидуальное производство) | h9 | P9 | P9 |
Нормальные соединения (массовое производство) | h9 | N9 | JS9 |
Свободные соединения (направляющие шпонки) | h9 | H9 | D10 |
3.3. Указания по назначению полей допусков на другие размеры деталей шпоночного соединения представлены в таблице 3.2.
Таблица 3.2_Рекомендуемые поля допусков деталей шпоночного соединения
Параметры деталей шпоночного соединения | Поля допусков | |
Призматические шпонки | Сегментные шпонки | |
Высота шпонки | h21 (при высоте шпонки от 2 до 6 мм – h9) | h21 (при высоте шпонки от 2 до 6 мм – h9) |
Длина шпонки | h24 | - |
Диаметр шпонки | - | h22 |
Глубина фрезерования паза вала | по t1 (см. отклонения по таблице 3.3) | по t1 (см. отклонения по таблице 3.3) |
Глубина протягивания паза втулки | по t2 (см. отклонения раз-меров по таблицам 3.3 и 3.4) | по t2 (см. отклонения раз-меров по таблицам 3.3 и 3.4) |
Длина паза вала | Н15 | - |
Диаметр паза вала | - | Н12 |
Поля допусков шпоночного соединения по номинальному размеру «вал-втулка» устанавливают в зависимости от условий работы по таблице 3.3.
Таблица 3.3_ Рекомендуемые поля допусков в соединениях «вал-втулка»
Условия работы | Тип соединения | Поля допусков | Посадка | |
отверстия | вала | |||
При точном центрировании | нормальное | Н6 | js6, k6, m6 | переходные |
При больших динамических нагрузках | нормальное плотное | Н7 Н8 | S7 х8, u8, s8 | с натягом |
При осевом перемещении втулки по валу | свободные соединения | Н6 Н7 | h6 h7 | с зазором |
Таблица 3.4 _Предельные отклонения глубины пазов и размеров, связанных с глубиной паза для соединений с призматическими шпонками (мм)
Высота шпонки h | Предельные отклонения размеров | ||
t1 | d-t1 | t2 или d+t2 | |
От 2 до 6 | +0,1 | -0,1 | +0,1 |
Св. 6 до 18 | +0,2 | -0,2 | +0,2 |
Св. 18 до 50 | +0,3 | -0,3 | +0,3 |
Примечание. Размеры (d-t1) и (d+t2) допускается контролировать вместо размеров t1 и t2.
Таблица 3.5_Предельные отклонения глубины пазов и размеров, связанных с глубиной паза для сегментных шпонок, мм
Высота шпонки h | Предельные отклонения размеров | ||
t1 | D-t1 | t2 или D+t2 | |
От 1,4 до 3,7 | +0,1 | -0,1 | +0,1 |
Св. 3,7 до 7,5 | +0,2 | -0,2 | +0,1 |
Св. 7,5 до 10 | +0,3 | -0,3 | +0,1 |
Св. 10 до 13 | +0,3 | -0,3 | +0,2 |
Примечание. Размеры (D-t1) и (D+t2) допускается контролировать вместо размеров t1 и t2.
Пример. Исходные данные: d = 40 мм; шпонка призматическая; соединение нормальное; условия работы – при точном центрировании.
3.1. По приложению 8 для d = 40 мм; b = 12 мм; h = 8 мм; t1 = 5,0 мм; t2 = 3,3 мм; l = 40 мм.
3.2. По таблице 3.1. выбираем поля допусков по ширине шпоночного соединения: ширина шпонки – 12h9; ширина паза вала – 12N9; ширина паза втулки – 12Js9.
Таблица 3.6_ Размерные характеристики деталей шпоночного соединения
Наименование размера | Номинальный размер, мм | Поле допуска | Допуск размера, мм | Предельные отклонения, мм | Предельные размеры, мм | ||
верхнее ES(es) | нижнее EI(ei) | max | min | ||||
Ширина паза вала | N9 | 0,043 | -0,043 | 12,000 | 11,957 | ||
Ширина паза втулки | Js9 | 0,042 | +0,021 | -0,021 | 12,021 | 11,979 | |
Ширина шпонки | h9 | 0,043 | -0,043 | 12,000 | 11,957 | ||
Глубина паза вала | по t1 | 0,2 | +0,2 | 5,2 | 5,000 | ||
Высота шпонки | h21 | 0,090 | -0,090 | 8,000 | 7,910 | ||
Глубина паза втулки | 3,3 | по t2 | 0,2 | +0,2 | 3,32 | 3,000 | |
Диаметр втулки | H6 | 0,016 | +0,016 | 40,016 | 40,000 | ||
Диаметр вала | m6 | 0,016 | +0,025 | +0,009 | 40,025 | 40,009 | |
Длина шпонки | h24 | 0,740 | -0,740 | 60,000 | 59,260 | ||
Длина паза вала | h25 | 1,2000 | +1,200 | 61,200 | 60,000 | ||
Диаметр шпонки (для сегментных шпонок) | См. таблицу 3.5 |
3.3. На другие размеры шпоночного соединения поля допусков назначают согласно рекомендациям (см. таблицу 3.2) 8h21; 40h24; 40h25; 5 по t1 (табл. 3.4 и 3.6) для призматических шпонок и (табл. 3.5 для сегментных шпонок) и 3.3 по t2 (табл. 3.4 или по табл. 3.5 для сегментных шпонок).
Поля допусков для гладких цилиндрических соединений назначают по таблице 3.1 (соединения «вал-втулка») Ø40Н6/m6, а отклонения размеров для t1 и t2 устанавливают по таблицам 3.4 и 3.5 (соответственно для призматических и сегментных шпоночных соединений).
3.4. Вычерчивают схему расположения полей допусков деталей шпоночного соединения по ширине шпонки b = 12 мм (рисунок 3.1) и заполняют таблицу 3.6.
Рисунок 3.1_ Схема полей допусков деталей шпоночного соединения
3.5. Определяют предельные зазоры и натяги: «шпонка-паз втулки» – 12Js9/h9 – посадка переходная; Smax = 12,021 – 11,957 = 0,064 мм; Nmax = 12 – 11,979 = 0,021 мм; «шпонка – паз вала» – 12N9/h9 – посадка переходная, Smax = 12 – 11,957 = 0,043 мм; Nmax = 12 – 11,957 = 0,043 мм.
3.6. Чертят эскизы шпоночного соединения и его деталей (рисунок 3.2).
Рисунок 3.2_Эскизы деталей шпоночного соединения и его деталей (для соединения с призматической шпонкой)
Для соединения с сегментной шпонкой схема рисунка несколько отличается (смотри ниже).
ЗАДАНИЕ 4.
megaobuchalka.ru
Шпоночные соединения — основные типы
Различают ненапряженные (с призматическими и сегментными шпонками) и напряженные (с клиновыми и круглыми шпонками — осевыми штифтами) шпоночные соединения. Шпонки основных типов стандартизованы. [c.157]Основные нормы взаимозаменяемости. Соединения шлицевые эвольвентные с углом профиля 30 . Размеры, допуски н измеряемые величины Сварка под флюсом. Соединения сварные. Основные типы, конструктивные элементы и размеры Основные нормы взаимозаменяемости. Соединения шпоночные с призматическими направляющими шпонками с креплением на валу. Размеры шпонок и сечений пазов. Допуски и посадки Заклепки с полукруглой головкой. Технические условия [c.482]
Назовите два основных типа шпоночных соединений. [c.205]
Основные типы шпоночных соединений. Шпоночные соединения делятся на две группы ненапряженные и напряженные. Ненапряженные соединения осуществляются призматическими и сегментными шпонками, которые не вызывают деформацию ступицы и вала при сборке. Напряженные соединения осуществляются клиновыми шпонками, которые вызывают деформацию вала и ступицы при сборке. [c.295]
Шпоночные соединения состоят из вала, шпонки и ступицы колеса (шкива или другой детали). Шпонка представляет собой ста )ьной брус, вставляемый в пазы вала и ступицы. Она служит для передачи вращающего момента между валом и ступицей колеса, щкива, звездочки и т. п. Основные типы щпонок стандартизованы. Шпоночные пазы у валов получают фрезерованием дисковыми или концевыми фрезами, а в ступице — протягиванием. [c.71]
Основные типы шпонок и шпоночных соединений показаны в табл. 1, 2 и 3. [c.536]
Шпоночные соединения служат в основном для передачи крутящих моментов. Стандартами предусмотрены следующие типы шпонок [c.370]
Основным преимуществом тангенциальных шпонок является их способность передавать больший знакопеременный крутящий момент (при одинаковых геометрических размерах вала и шпонок) сравнительно с другими типами клиновых шпоночных соединений. [c.162]
Существуют два основных типа шпоночных соединений напряженное и ненапряженное. В напряженных шпоночных соединениях применяют клиновые шпонки, создающие при сборке напряжения в деталях соединения до приложения внешних нагрузок. В ненапряженных шпоночных соединениях применяют призматические и сегментные шпонки. [c.378]
Т ипы шпоночных соединений приведены в ОСТ/НКМ 4078, где указаны также номера стандартов на основные размеры отдельных типов шпонок. [c.473]
Основные типы шпонок и шпоночных соединений, находящих применение в машиностроении, указаны в табл. Ь8 и 89. [c.827]
Шпоночные соединения могут быть ненапряженными (соединения призматическими и сегментными шпонками) и напряженными (соединения клиновыми шпонками). Величина момента, передаваемого соединением, образованным при помощи клиновой шпонки, зависит от сил трения, развиваемых на рабочих поверхностях. Для увеличения этих сил необходимо создать на этих поверхностях значительные нормальные давления их получают при забивании шпонки в паз, чем и вызывается напряженность соединения до приложения внешней нагрузки. К клиновым шпонкам относятся врезные, тангенциальные, на лыске и фрикционные. Основные типы шпонок стандартизованы. В некоторых случаях применяют специальные шпонки. [c.143]
Стандарты разработаны на основные типы шпоночных соединений [c.160]
Основные типы шпоночных соединений и размеры шпонок и пазов для них стандартизированы. Существующие конструкции шпонок можно разделить на четыре группы призматические, клиновые, сегментные и тангенциальные. [c.234]
Рис. 79. Основные типы шпоночных соединений. | ![]() |
Рис. 80. Приемы сборки основных типов шпоночных соединений а – пригонка шпонки по валу б – измерение шпоночного паза во втулке в -проверка посадки шпонки в пазах вала г — контроль параллельности поверхностей. | ![]() |
На основные типы шпоночных соединений в СССР имеются ГОСТы, которые предусматривают размеры поперечных сечений шпонок и соответствующих пазов в валу и втулке в зависимости от диаметра вала. Длина шпонки выбирается исходя из длины втулки (ступицы). В случае значительной недогрузки шпоночного соединения, а также для ступенчатых и пустотелых валов допускается применение стандартных шпонок меньших сечений на валах больших диаметров (за исключением выходных концов валов). [c.82]
Основные типы шпоночных соединений [c.374]
Технологический процесс сборки основных типов шпоночных соединений [c.390]
Ряс. 1. Основные типы шпоночных соединений [c.88]
Шпоночные соединения — основные типы 88 — Расчет 88, 89 [c.639]
Все вращающиеся детали узла, объединяемые валом, соединяются между собой различными способами. Существуют три основных типа соединений вращающихся деталей посадка с гарантированным натягом, шпоночное, шлицевое и клиновое соединения. [c.38]
На концах валов малого диаметра вместо шпоночных канавок иногда применяют продольные рифления треугольного профиля. Этим способом крепятся зубчатые колеса, рычаги и т. п. Посаженная на вал деталь должна быть предохранена от осевого смещения (фиг. 85). Если втулку иа среднюю часть вала, то диаметр вала на этой части необходимо увеличить на величину, равную удвоенной высоте зубьев. Основные параметры соединений этого типа (фиг. 86) угол впадин 90°, 72° или 60° модуль от 0,2 до 1,5 мм минимальное число зубьев 15. Центрирование — только по боковым сторонам [c.54]
Основные типы шпоночных соединений стандартизованы. Так, имеются стандарты на размеры сечений шпонок и пазов и на размеры самих шпонок призматических (ГОСТ 8788—58, ГОСТ 8789—58, ГОСТ 8790—58), сегментных (ГОСТ 8794—58, ГОСТ 8795—58), клиновых (ГОСТ 8791—58, ГОСТ 8792—58, ГОСТ 8793—58), тангенциальных (ГОСТ 8796—58, ГОСТ8797—58). Следует отметить, что все размеры шпоночных соединений по перечисленным стандартам унифицированы во всех странах — членах СЭВ, иначе говоря, и сами шпонки, и пазы для них, изготовленные в любой из этих стран, являются взаимозаменяемыми. [c.516]
Шпоночные соединения состоят из вала, шпонки и ст 1ицы колеса (шкива или другой детали). Шпонка представляет собой стальной брус, вставляемый в пазы вала и ступицы. Она служит для передачи враш.аюш.его момента между валом и ступицей. Основные типы [c.41]
Вопросы для самопроверки. 1. Перечислите основные типы шпоночных соединений и дайте их сравнительную характеристику. 2. Укажите разновидности клиновых шпонок. Почему эти шпонки не следует применять в точно изготовленных и быстроходных передачах 3. В каких случаях рекомендуется применять сегментные шпонки 4. Почему размеры поперечного сечения шпонок подбираются в зависимости от диаметра вала 5. Как ведется расчет соединений призматическими и сегментными шпонками 6. Какие шпонки могут о(кспечить не только передачу момента от детали к валу или наеборот, но и неподвижность детали в осевом направлении 7. Укажите основные типы шлицевых (зубчатых) соединений. 8. Каковы преимущества зубчатого соединения по сравнению со шпоночным [c.263]
Наличие стандартов на основные типы шпонок и шпоночных соединений значительно облегчает их расчет. Для каждой конструкции шпонки в зависимости от диаметра вала в в ГОСТах приводятся размеры сечения шпонок Ьхк и размеры паза. Расчет соединений состоит в определении расчетной длины I шпонки прн заданном материале или в проверке напряжений, возникающих на рабочих поверхностях и в опасном сечении шпоики. [c.288]
Колеса с грузошинами погрузчиков 4015, Ф12.3ЕУ06.33,4004, КВЗ и ПТШ-3 -СОСТОЯТ из трех основных элементов — ступицы, цилиндрического обода и соединяющего их диска (первый тип, см. рис. 44). Ступица предназначена для подвижного соединения с осью через радиально-упорные подшипники, либо для неподвижного соединения с ведущим валом (погрузчики 4015, Ф12.3ЕУ06.33). В соответствии с этим ступица имеет либо гнезда для установки подшипников, либо сквозное отверстие (цилиндрическое, коническое) со шпоночной канавкой для жесткого закрепления на приводном валу (см. рис. 39). [c.81]
mash-xxl.info
Разновидность шпоночных соединений
Все шпоночные соединения подразделяют на ненапряженные и напряженные. Ненапряженныесоединения получают при использовании призматических (рис. 3.1) и сегментных (см. рис. 3.2) шпонок. В этих случаях при сборке соединений в деталях не возникает предварительных напряжений.
Напряженныесоединения получаются при применении клиновых (см. рис. 3.3) и тангенциальных (см. рис. 3.4) шпонок. Здесь при сборке возникают предварительные (монтажные) напряжения.
Соединения призматическими шпонками.Конструкции соединений призматическими шпонками изображены на рис. 3.1.Рабочими являются боковые, более узкие грани шпонок высотой h. Размеры сечений призматических шпонок и пазов принимают в зависимости от диаметра d вала (табл. 3.1).
Таблица 3.1 . Шпонки призматические (выборка)
Размеры, мм (рис. 3.1)
По форме торцов различают шпонки со скругленными торцами – исполнение 1 (рис. 3.1,а),с плоскими торцами – исполнение 2 (рис. 3.1,б) и с одним плоским, а другим скругленным торцом – исполнение 3 (3.1,в).
Призматические шпонки не удерживают детали от осевого смещения вдоль вала. Чтобы застопорить колесо от осевого смещения, применяют распорные втулки (1 на рис. 3.1), установочные винты (1 на рис. 3.2).
Соединения сегментными шпонками (рис. 3.2). Сегментные шпонки, так же как и призматические, работают боковыми гранями. Применяются при передаче небольших вращающих моментов. Сегментные шпонки и пазы для них просты в изготовлении, удобны при монтаже и демонтаже (шпонки свободно вставляют в паз и вынимают). Широко применяются в серийном и массовом производстве.
Рис. 3.2. Соединение сегментной шпонкой:
1 – винт установочный, 2 – кольцо замковое пружинное
Соединения клиновыми шпонками (рис. 3.3).Клиновые шпонки имеют форму односкосных самотормозящих клиньев с уклоном 1:100. Такой же уклон имеют пазы в ступицах. Клиновые шпонки изготовляют без головок и с головками. Головка служит для выбивания шпонки из паза. По нормам безопасности выступающая головка должна иметь ограждение (1 на рис. 3.3).
Клиновые шпонки забивают в пазы, в результате создается напряженное соединение, которое передает не только вращающий момент, но и осевую силу. Эти шпонки не требуют стопорения ступицы от продольного перемещения вдоль вала.. При забивании клиновой шпонки в соединении возникают распорные радиальные силы, которые нарушают центрирование детали на валу, вызывая биение.
Соединения клиновыми шпонками применяют в тихоходных передачах.. Онихорошо воспринимают ударные и знакопеременные нагрузки.
Рис. 3.3 Соединение клиновой шпонкой
Соединения тангенциальными шпонками (рис. 3.4). Тангенциальные шпонки состоят из двух односкосных клиньев с уклоном 1:100 каждый. Работают узкими гранями. Вводятся в пазы ударом. Образуют напряженное соединение. Натяг между валом и ступицей создается в касательном (тангенциальном) направлении. Применяются для валов диаметром свыше 60 мм при передаче больших вращающих моментов с переменным режимом работы. В соединении ставят две пары тангенциальных шпонок под углом 120°. В современном производстве применяются ограниченно.
Рис. 3.4 Соединение тангенциальными шпонками
Расчет шпоночных соединений
Основным критерием работоспособности шпоночных соединений является прочность. Шпонки выбирают по таблицам ГОСТов в зависимости от диаметра вала, а затем соединения проверяют на прочность. Размеры шпонок и пазов в ГОСТах подобраны так, что прочность их на срез и изгиб обеспечивается, если выполняется условие прочности на смятие, поэтому основной расчет шпоночных соединений – расчет на смятие. Проверку шпонок на срез в большинстве случаев не производят.
Соединения призматическими шпонками (рис 3.4 и 3.1)проверяют по условию прочности на смятие :
.
Сила, передаваемая шпонкой, Ft= 2 T/d.
При высоте фаски шпонки f ≈0,06h площадь смятия.
Рис. 3.5 Расчетная схема соединения призматической шпонкой
Acм=(h – t1 – f ) lp=(h – t1 – 0,06h) lp= (0,94h – t1) lp, следовательно,
(3.1)
где Т – передаваемый момент;d – диаметр вала;(0,94h – t1) – рабочая глубина паза в ступице (см. табл. 3.1);[σ]см – допускаемое напряжение смятия (см. ниже);lp – рабочая длина шпонки; для шпонок с плоскими торцами lp=l, со скругленными торцами lp=l – b.
Если расчетное напряжение превышает допускаемое более чем на 5%, то увеличивают длину шпонки и соответственно ступицы или шпоночное соединение заменяют шлицевым или соединением с натягом.
При проектировочных расчетахпосле выбора размеров поперечного сечения b и h по табл. 3.1 определяют расчетную длину шпонки lpпо формуле (3.1).
Длину шпонки со скругленными торцами lp=l + b или с плоскими торцами lp=l назначают из стандартного ряда (см. табл. 3.1). Длину ступицы lСТ принимают на 8…10 мм больше длины шпонки. Если длина ступицы больше величины 1,5 d , то шпоночные соединения заменяют шлицевым или соединением с натягом..
Соединения сегментными шпонками(см. рис. 3.2) проверяют на смятие:
(3.2)
где l – длина шпонки; (h – t)- рабочая глубина в ступице.
Сегментная шпонка узкая, поэтому в отличие от призматической ее проверяют на срез.
Условие прочности шпонки на срез
, (3.3)
где b – ширина шпонки; [τ]ср – допускаемое напряжение на срез шпонки (см. ниже).
Стандартные шпонки изготовляютиз специального сортамента среднеуглеродистой, чистотянутой стали с σв≥600Н/мм² – чаще всего из стали 45.
Допускаемые напряжения смятиядля шпоночных соединений:
при стальной ступице и спокойной нагрузке [σ]см = 110…190 Н/мм²;
при чугунной – [σ]см = 70…100 Н/мм².
При переменной нагрузке [σ]см снижают на 50%.
Допускаемое напряжение на срез шпонок [τ]ср = 70…100 Н/мм². Большее значение принимают при постоянной нагрузке.
Расчет шпоночного соединения ведут в последовательности, изложенной в решении примера 3.1.
Пример 3.1.выбрать тип стандартного шпоночного соединения стального зубчатого колеса с валом (см. рис. 3.1,а) и подобрать размеры шпонки. Диаметр вала d=45 мм. Соединение передает момент Т=189,5 Н·м при спокойной нагрузке.
Решение. 1. Выбор соединения. Для соединения вала с колесом принимаем призматическую шпонку со скругленными торцами (исполнение 1).
2.Размеры шпонки и паза.По табл. 3.1 для диаметра вала d=45 мм принимаем размеры сечения шпонки b=14 мм; h =9 мм. Глубина паза t1= 5,5 мм.
3.Допускаемое напряжение.Для стальной ступицы при спокойной нагрузке принимаем [σ]см =100 Н/мм².
4. Расчетная длина шпонки[ формула (3.1)]
Длина шпонки
l=lp+b=(26+14) мм =40 мм – согласуется со стандартом (см. табл. 3.1).
Для ступицы колеса
lст=l+10 мм =(40+10) мм =50 мм, что допустимо.
Не нашли то, что искали? Воспользуйтесь поиском гугл на сайте:
zdamsam.ru