Резьбонакатные станки – технические характеристики и принцип работы
alexxlab | 11.08.2019 | 0 | Вопросы и ответы
Резьбонакатной станок
Станки резьбонакатные имеют такое назначение как накатка резьбы и винтов, находящихся на вращающихся деталях. Причем и резьба, и поверхность винта могут быть абсолютно любого типа. Нашли свое применение на предприятиях по обслуживанию автотранспорта, мастерских по ремонту автомобилей, станциях для технического обслуживания.
Обычно станки весьма удобны в применении и имеют хорошие технические характеристики. Накатка при помощи таких станков проводится двумя методами:
1. радиальная подача. Используется он для того, чтобы можно было обрабатывать винтовые поверхности короткого типа.
2. осевая подача заготовок. Есть возможность обработать винтовые поверхности совершенно любого типа.
Принцип действия резьбонакатных станков
Резьбонакатные станки имеют в составе:
1. силовую систему, предназначенную в свою очередь для включения привода механики, используемого при синхронизации двух вращающихся валов и роликов наката, а также устройства, которое необходимо для встречного перемещения вышеуказанных валов в процессе накатывания резьбы.
2. накатную систему – состоит из одной неподвижной шпиндельной головки и еще одной передвигающейся головки. Находятся они в одной плоскости и имеют в установочной зоне накатные ролики пазы шпоночной, которые работают в одной фазе. Кроме того есть опорные поверхности, необходимые для продольной установки роликов накатного типа. Они также находятся в одной и той же плоскости, но заход резьбы и на одном и на другом роликах сделан в равном положении, если смотреть относительно шпоночных пазов.
Обработка металла происходит с помощью давления, которое оказывается на него. Чаще всего применяется резьбонакатной станок, имеющий два ролика и два шпинделя. Первый из них сделан так, чтобы было возможно радиальное смещение от привода. Все это выглядит как система рычагов, которые связаны напрямую с подачей сжатого воздуха.
В станке для наката резьбы полностью исключены шарниры. А плоскопараллельное передвижение шпинделя с роликом подвижного типа осуществляется за счет крепления шпиндельных головок на одном валу. Вращательное движение получается в результате работы двух конических шестерен.
Для того чтобы создать нужную силу для работы в ход идет не сжатый воздух из специальной пневматической сети, а кинематическая схема от токарного станка обычно предназначенная для обработки металла. От него вместе с силой вращающей основные ролики используется и энергия суппорта станка для подвижной шпиндельной головки.
Особенности устройства резьбонакатных станков
Резьбонакатный станок является весьма быстросъемным. Объясняется это тем, что он локализуется в жестком переднем и в заднем вращательном центрах. А передача крутящегося момента осуществляется путем осевого зажатия вала находящегося в центре в 3-хкулачковом патроне.
Механический привод вышеописанного станка сделан в форме центрального вала, необходимого для укомплектовки в двух противоположных вращающихся центрах с зажимом в 3-хкулачковом патроне. Предназначен он для объединения центрального вала с валами, которые представлены накатными роликами, также 2-х одинаковых конических передач.
Та часть, которая является накатной, сделана в виде своеобразной приставки. Эта часть резьбонакатного станка является быстросменной. Но ее головки как неподвижная, так и подвижная, устанавливаются на основной вал. Кроме того они подпружинены между собой для разжимания. Причем подвижная головка находится в задней части центра и необходима для полного контакта токарного станка с суппортом, который нужен для нажима на закрепленный на ней накатной ролик; который, в свою очередь, прижимается к детали.
Резьбонакатные станки имеют следующие особенности:
1. изготовлены из высокопрочного чугуна, полностью виброустойчивы. Имеющиеся направляющие полностью закалены и отшлифованы;
2. имеется свободный доступ к рабочей зоне;
3. управление станком производится посредством программируемого контроллера.
promplace.ru
Накатка резьбы с использованием роликов – действенная технология
Востребованным и по-настоящему универсальным вариантом накатывания на сегодняшний день признается накатка резьбы с применением специальных роликов. Этот способ отличается уникальным технологическим потенциалом при производстве резьб разной точности, протяженности и сечения.
1 Накатка резьбы с помощью роликов – достоинства и недостатки методики
Под накатыванием роликами понимают операцию пластического холодного деформирования поверхности обрабатываемой детали, при которой металл подвергается высокому давлению.
В результате этого между резьбовыми витками наблюдается явление заполнения впадины, что приводит к формированию требуемой резьбы. Причем подобное деформирование происходит без снятия стружки с заготовки.
Рекомендуем ознакомиться
Достоинствами данной методики признаются далее приведенные факты:
- верхняя часть детали характеризуется очень малым уровнем шероховатости;
- показатель усталостной прочности изделия находится на высоком уровне;
- производительность операции в несколько раз выше, нежели при использовании стандартной методики, когда резьба нарезается;
- высокая величина твердости и стойкости против эксплуатационного износа, а также прочностного показателя поверхности заготовки, обусловленная наклепом.
К недостаткам накатки роликами относят то, что, во-первых, по сравнению с процессом шлифования металла она менее точна, во-вторых, требуются достаточно дорогие приспособления для осуществления технологического процесса. Кроме того, при использовании роликов важно грамотно выбирать режим обработки и очень точно рассчитывать геометрические параметры рабочего инструмента и детали. Если эти условия не будут выполнены, возрастает вероятность образования ряда негативных явлений:
- отслаивание металла по резьбе;
- чешуйчатость заготовки;
- большой перенаклеп.
Все упомянутые недостатки и преимущества технологии обусловили то, что чаще всего выполнение резьбы роликами используется в крупносерийном и массовом производстве.
2 Кратко о популярном инструменте для накатывания резьбы
Для упорных, метрических, трапецеидальных и других по профилю резьб применяются плоские резьбонакатные плашки. Данный вид инструмента хорошо зарекомендовал себя также для выполнения винтовых и кольцевых канавок на пластичных деталях, разнообразных рифлений и шурупных резьб.
Используются не отдельные плашки, а их комплект из двух штук. Одна из них соединена с ползуном металлообрабатывающего агрегата, что позволяет ей осуществлять движение возвратно-поступательного характера. Вторая монтируется на рабочей поверхности станка неподвижным образом. Движущаяся плашка при перемещении агрегата захватывает изделие, которое требуется обработать, и по неподвижной плашке осуществляет его прокатку.
Для нанесения внутренних резьб применяют раскатники – похожие на машинные метчики специальные стержни, на которых уже имеется резьба. Они снабжены хвостовиком, калибрующей и заборной частью. Резьба на заготовке получается за счет пластического деформирования (аналогично обработке роликами). Раскатники рекомендуется применять для работы с цветными листовыми металлами, мягкими и вязкими марками стали, материалами с высоким уровнем пластичности.
3 Особенности использования роликов для накатки резьбы
Все описанные выше способы выполнения резьбы по своим технологическим возможностям ощутимо уступают методике, при которой используются ролики. Как правило, применяется два ролика (иногда их может быть три или четыре). А сам рабочий процесс производится на универсальных либо специальных станках для накатки резьбы.
Существует три варианта накатывания резьбы роликами в зависимости от того, каким образом резьбонакатной станок подает рабочий инструмент и изделие: с тангенциальной подачей детали; с радиальной подачей роликов; с осевой подачей заготовки.
Тангенциальная схема обеспечивает высокую производительность агрегата. Она может выполняться подачей:
- двух роликов цилиндрической формы, каждый из которых имеет собственную окружную скорость;
- двух пар роликов затылованного типа либо просто двух таких роликов;
- двух роликов затылованного типа в центрах.
Отличие цилиндрических приспособлений от затылованных заключается в том, что у вторых имеется не только калибрующая и заборная части, но еще и сбрасывающая. По стоимости затылованные ролики дороже обычных, а использовать их можно как на простых станках, на которых шпиндельные узлы находятся в фиксированном положении, так и на специальных полуавтоматических резьбонакатных установках.
В тех случаях, когда применяются две пары затылованных роликов, процесс накатывания резьбы ускоряется. Резьбу можно наносить одновременно на два конца изделия или же обрабатывать сразу две детали. А при монтаже заготовки в центрах станка следует пользоваться крупными по сечению роликами (от 20 до 30 сантиметров).
Более популярным способом накатки резьбы является вариант, когда ролики подаются радиально. Востребованность этой методики обусловлена в первую очередь простотой используемого инструмента и необходимой для выполнения операции оснастки. Обычно накатка производится при помощи двух вращающихся роликов. Радиальную подачу при этом имеет лишь один из них.
При радиальной подаче применяются только цилиндрические ролики, которые соответствуют положениям Государственного стандарта 9539. Они бывают нормальной и повышенной точности, предназначены для нарезания резьбы сечением от 3 до 68 миллиметров (шаг варьируется от 0,5 до 6 миллиметров). Посадочное отверстие таких цилиндрических приспособлений может иметь следующие размеры – 45, 80, 54 или 63 миллиметра.
Геометрические параметры роликов цилиндрической формы устанавливают посредством проведения специальных расчетов, при которых во внимание принимается уровень точности, шаг, сечение и протяженность резьбы, которую требуется произвести. Очень важным представляется и то, чтобы винтовая линия на резьбе и на роликах характеризовалась идентичными углами подъемов. Именно по этой причине на роликах резьба выполняется многозаходной.
Если на изделие необходимо накатать длинную резьбу, в большинстве случаев применяется схема осевой подачи детали. Она производится на средней скорости порядка 9 тысяч миллиметров в минуту. Данная схема реализуется крайне редко, так как при ней отмечается уменьшение прочности инструмента, вызванное проскальзыванием витков обрабатываемого изделия и роликов, а также наличие погрешности шага (на каждые 10 сантиметров длины около 10 микрометров).
4 Информация о резьбонакатных станках
Для накатки резьбы используются полуавтоматические станки с двумя либо тремя роликами. Любой резьбонакатной станок состоит из двух основных частей:
- гидравлического привода, который необходим для формирования накатывающего усилия для деформирования изделия и формирования требуемой резьбы;
- устройства для вращения в одном направлении роликов.
Такие агрегаты могут функционировать в следующих рабочих режимах: автоматический и полуавтоматический; наладочный; работа без отвода резьбонарезной головки на упоре.
Некоторые станки, кроме того, оснащаются дополнительными приспособлениями, что значительно расширяет их рабочие возможности и ускоряет процесс накатывания резьбы роликами. Например, механизм поворота шпиндельного узла дает возможность выполнять операцию с осевой подачей, а устройства автозагрузки и автовыгрузки изделий позволяют интегрировать оборудование в линии и мощные комплексы крупносерийного производства.
Небольшой обзор популярных резьбонакатных агрегатов:
- “PEE-WEE”: экономичные, высокотехнологичные и надежные установки из Германии с различными показателями давления накатки (5–60 тонн). Все модели снабжаются на заводе механизмом автоматической загрузки деталей, могут оснащаться шпинделями наклонного типа, что обеспечивает возможность работы с профилями большой длины.
- “PROFIROLL”: немецкие станки, отличающиеся простой переналадкой, оборудованные качественной и понятной системой управления. Нельзя не отметить их долговечность и простоту обслуживания.
- “В28”: недорогое белорусское оборудование для радиальной и осевой обработки с усилием сжатия от 80 (модель “В28-80”) до 630 (“В28-630”) кН.
- Станки от Азовского комбината кузнечно-прессового оборудования: “A9527”, “A9524”, “AA9521.02 (03)” и другие.
tutmet.ru
Резьбонакатный станок | Все Станки
Для формирования резьбы у заготовок будущих метизов используется резьбонакатный станок. Формирование резьбового профиля может производиться и у винтов, которые предназначены для вращающихся крепежных элементов. Данные виды станков для производства метизов широко используются в сфере технического обслуживания автотранспорта.
Можно выделить следующие способы формирования резьбового профиля:
- Радиальная подача винтов – применяется для работы с заготовками малой длины.
- Осевая подача винтов – используется для обработки заготовок любого вида.
Особенности работы резьбонакатного станка
Прежде чем купить оборудование для производства метизов с резьбонакатной функцией, необходимо изучить технические параметры моделей и принципы их работы.
Все составляющие данного оборудования для саморезов, винтов и метизов можно разделить на две основные системы:
- Силовая система – необходима для приведения в действие механического привода, главной функцией которого является синхронность движений пары вращающихся валиков и накатных роликов. Еще сюда относится устройство, позволяющее валикам вращаться в обратном направлении во время самого процесса накатки.
- Накатная система — состоит из двух шпиндельных головок: неподвижной и движущейся. Указанные элементы установлены в одной плоскости и снабжены накатными роликами, действующими в одной фазе.
Формирование резьбы происходит под действием давления. Обычно станок оборудован несколькими роликами и несколькими шпинделями. В данном случае существует возможность радиального смещения от механического привода. Фактически это совокупность всех рычагов, на которые непосредственно подается сжатый воздух.
В устройстве резьбонакатного станка отсутствуют шарниры. При этом шпиндели вращаются в одной плоскости с роликами благодаря креплению шпиндельных головок на одном валу. Специальные конические шестеренки обеспечивают вращательное движение.
Для достижения определенного уровня давления станок оборудован пневматическим устройством, подающим сжатый воздух. Кинематическая схема резьбонакатного оборудования схожа с токарным станком.
Техническое устройство резьбонакатного оборудования
Механический привод станка представляет собой центральный вал (как в круглошлифовальном оборудовании для обработки металла), соединенный с двумя противоположно расположенными центрами, имеющими зажим в трехкулачковом патроне. Привод используется для соединения с валами, имеющими накатные ролики.
Накатная часть изготовлена в виде специальной быстросъемной приставки. Обе головки шпинделя установлены на одну ось вала. Между ними имеется пружинное разделение. Подвижная головка расположена в задней части центра, обеспечивает полную связь автомата с суппортом с целью его воздействия на установленный накатной ролик. Тот, в свою очередь, оказывает непосредственное воздействие на заготовку метиза.
Виды резьбонакатных станков различаются между собой прежде всего страной-производителем. Зарубежные модели требуют больших транспортных расходов. Это оказывает прямое влияние на итоговую цену станка для производства метизов.
Еще одна статья расходов, которую важно учесть при составлении бизнес-плана производства метизов, — затраты на доставку, установку и обслуживание резьбонакатного оборудования.
stankiwse.ru
Резьбонарезные электрические станки для труб: характеристики, модели, видео
Резьбовое соединение повсеместно используется при изготовлении различных конструкций. Его особенностью можно назвать надежную фиксацию элементов, а также возможность неоднократного сбора и разбора конструкции. Несмотря на то, что подобный тип соединения используется на протяжении последних нескольких лет, создать резьбу сложно и при современных технологиях. Для этого используется электрический резьбонарезной станок, который предназначен исключительно для выполнения подобной работы, а также токарные и фрезеровальные резьбонарезные станки определенных моделей. Примером можно назвать резьбонарезной станок Rems, пользующийся большой популярностью. Рассмотрим все особенности поставляемого оборудования для нарезания резьбы на заготовках различной формы и изготовленных из разных материалов.
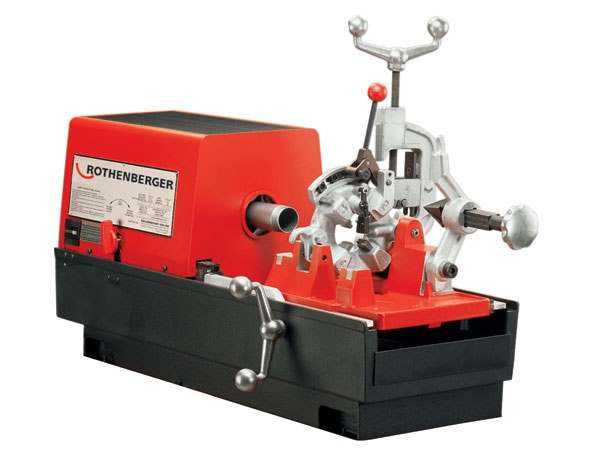
Используемое оборудование для нарезания резьбы
Еще несколько десятилетий назад использовали специальные машины для вытачивания валов и других изделий, а также нарезания на некоторых резьбы. В машиностроении полуавтоматический резьбонарезной станок позволял получить качественную резьбу с различными параметрами, но в большинстве случаев использовали из-за универсальности токарно-винторезные, сверлильные резьбонарезные станки. Качество получаемой резьбы постепенно увеличивалось, так как со временем на смену опыта и умений оператор пришла дополнительная оснастка, которая позволяла существенно упростить проводимую работу. Условно оборудование можно разделить по следующим признакам:
- расположению инструмента;
- какой из элементов, инструмент или заготовка, во время обработки находится в неподвижном состоянии;
- по степени автоматизации;
- по виду используемого инструмента.
Ранее для образования резьбы на цилиндрической поверхности использовали резцы, плашки и метчики. Для их использования приспосабливали обычное оборудование, которое могло работать с рассматриваемым инструментом. Через некоторое время появились резьбонарезной станок Ridgid или резьбонарезной станок Rems, которые специально производятся для выполнения подобной работы.
Основные параметры
Оборудование рассматриваемой группы характеризуется по иным параметрам, нежели оборудование токарной или фрезерной группы. Это связано с тем, что резьбонарезной станок Ridgid или резьбонарезной станок Rems применяется не для изменения формы или качества поверхности, а образования канавок с заданными параметрами, которые и определяют тип резьбы. К основным параметрам, которыми обладает резьбонарезной станок для труб или других заготовок, можно отнести следующее:
- диапазон диаметра заготовки для болтовой резьбы, а также ее шаг;
- диапазон диаметра трубы, на которой можно нанести резьбу, и ее шаг;
- класс точности согласно установленным нормам в гост или ISO;
- протяженность резьбы, которая может зависеть от диаметра заготовки;
- размер наибольшей фаски;
- угол наклона фаски;
- тип резьбы, которые можно получить.
Современное оборудование, к примеру, резьбонарезной станок Ridgid или резьбонарезной станок ВМС обладают высокой производительностью и возможностью точной настройки под заданные параметры. Вышеприведенные технические характеристики указываются в документации. Однако при выборе следует уделить внимание и другим параметрам, которые определяют особенности проводимых работ.
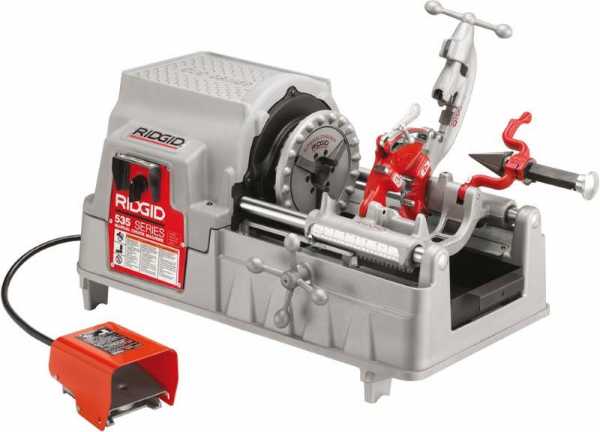
Резьбонарезной станок RIDGID 535
Как выбрать наиболее подходящую модель?
Резьбонарезной станок Ridgid или резьбонарезной станок ВМС 2а востребованы в мелком и крупносерийном производстве. При выборе определенной модели следует обратить внимание на:
- Тип конструкции: вес, компактность, расположение основных элементов, степень защиты подвижных элементов и зоны резания. На рынке продажи подобного оборудования есть большой выбор. К примеру, можно приобрести вертикальный вариант исполнения РЕМС или с горизонтальной компоновкой. Все зависит от поставленных задач.
- Тип установленного привода. На протяжении многих лет устанавливается механический привод, так как он прост в использовании и компактен. Однако стоит учитывать, что есть довольно много типов механического привода, некоторые надежны и точны, другие выходят из строя довольно быстро.
- При рассмотрении электродвигателя следует обратить внимание на то, от какой сети он питается и есть ли защита от перегрева. Большая мощность в данном случае не будет говорить о хорошей производительности.
- Тип установленного зажимного устройства. Во время обработки есть вероятность возникновения довольно большой нагрузки. Для обеспечения высокой точности нарезания резьбы и безопасности работы конструкции зажимное устройство должно быть надежным.
- Наличие подачи охлаждающе-смазывающей жидкости. При обработке твердосплавного материала есть вероятность существенного нагрева режущего инструмента и самой заготовки. При возникновении подобной ситуации быстро изнашивается инструмент, а также изменяются качества материала.
Резьбонарезной станок REMS Торнадо
- Наличие системы автоматизации. В последнее время все большей популярностью пользуются модели с числовым программным управлением, так как они позволяют получать точные детали при высокой производительности. При этом практически весь процесс выполняется без участия человека, то есть управлять резьбонарезным станком Риджид или другого производителя может оператор с малым опытом резьбонарезания.
При выборе также уделяют внимание тому, какая фирма указана производителем. К примеру, Rothenberger является достаточно известным производителем, что определяет высокое качество получаемых изделий. Однако стоимость оборудования Rothenberger будет существенно выше, чем продукция отечественных производителей.
В заключение отметим, что рассматриваемое оборудование может устанавливаться дома, так как имеет небольшие габаритные размеры, может питаться от сети 220 В и не требует жесткого крепления к основанию. Единственным недостатком при покупке оборудования для его бытового применения является его высокая стоимость.
Если вы нашли ошибку, пожалуйста, выделите фрагмент текста и нажмите Ctrl+Enter.
stankiexpert.ru
Thread-rolling machines – grease monkey
Thread-rolling machines are divided into machines with flat and round dies. Machines with flat dies performance and enable us to obtain an accurate thread. The movable flat die 9 (rice. 13.9) receives a reciprocating movement by an electric motor 1 через клиноременную передачу d1/d2, a pair of gears z1 / z2 and crank mechanism 3. Blanks from the hopper 4 fall into the treatment zone along the guide chute 10 with the pusher 6, which is driven by a motor kinematic chain for, a similar circuit for driving the movable die, and then through a pair of wheels z3 / z4, overload coupling 2 and a crank mechanism 5. Tolkatelь 7 directly supplies the workpiece into the space between the movable 9 и неподвижной 8 plashkami.
For machines with round billet dies 2 (rice. 13.10, о) emphasis is placed na 4 between the fixed 1 and mobile 3 round dies (rollers). chaser 3 fast approach to the workpiece, and presses it against the roller 1; happening roll forming thread, which ends after a few revolutions of the workpiece (rice. 13.10, б). Both rollers are rotated by a motor through a mechanical transmission, and linear movement of the movable roller is usually carried out by the hydraulic drive. There are other methods of thread rolling.
The advantages of the method are rolling performance, relatively low cost, great strength and durability grooved threaded products as compared with the strength and durability of cut,
tapping machines
Tapping into the nuts with large scale and mass production is carried out on tapping semi-automatic and automatic machines taps with straight or curved shank. Schematic diagram of the two-spindle tapping machine, working with a bent shank taps, shown in Figure. 13.11. Tap 1 together with a special head 2 receives rotation from the spindle 3. Chopped nuts out of the bunker 4 are fed to a rotating taps and a pusher 5 pressed him. Tolkatelь 5 receives the movement from the eccentric 6, Nut moves taps and curved shank is reset to the zone of finished products.
tehnar.net.ua
Профиленакатной двухроликовый полуавтомат модели А9518
Резьбонакатные станки делят по виду накатного инструмента. Накатным инструментом могут быть два резьбовых ролика, резьбовой ролик и сегмент, плоские плашки, резьбовой ролик и кольцевая плашка. Накатывание резьбы плашками более производительный, но менее точный процесс по сравнению с накатыванием резьбы роликами.
1. Профиленакатной двухроликовый полуавтомат модели А9518
Двухроликовый полуавтомат модели А9518 предназначен для накатывания резьб различного профиля, мелкомодульных червяков, рифлений и калибровки тел вращения. Цикл работы станка полуавтоматический или автоматический, подача заготовок осуществляется вручную. Станок может быть оснащен загрузочным устройством и превращен в автомат.
Техническая характеристика станка
Усилие накатывания, кгс:
наименьшее……………………….500
наибольшее……………………….6300
Диаметр накатываемых резьб, мм…………….3—30
Наибольший шаг накатываемой резьбы, мм…………2
Наибольшая длина накатываемой резьбы, мм…………45
Диаметр накатного ролика, мм………………..90_150
Расстояние между осями накатных роликов, мм 90_180
Наибольшее давление в гидросистеме, кгс/см2…………50
Наибольший ход подвижной головки, мм…………..10
Частота вращения шпинделя, об/мин…………….25_100
Мощность электродвигателя, кВт:
главного привода……………………2,2
гидропривода……………………..1,1
насоса охлаждения……………………0,12
Габаритные размеры станка, мм………………1480Х840Х120
Гидрокинематическая схема двухроликового накатного станка модели А9518 показана на рис. 87, а.
Рис. 87. Гидрокинематическая схема профиленакатного двухроликового полуавтомата модели А9518
Движения в станке: главное вращательное движение шпинделей накатных роликов; движение поперечной подачи подвижной накатной головки; вспомогательные наладочные движения узлов станка.
Цепь главного движения. Шпиндели V и VII накатных роликов 1 и 2 подвижной 31 и неподвижной 32 головок приводятся во вращение от электродвигателя М через вариатор 19, или (при специальном исполнении станка) девятискоростную коробку (рис. 87, б). Движение от вариатора к шпинделю V подвижной накатной головки передается по следующей цепи: шлицевый вал III, червячная пара , цилиндрическая зубчатая передача. Цепь привода шпинделя VII неподвижной накатной головки несколько иная: червяк z5 получает вращение не непосредственно от шлицевого вала III, который свободно проходит в его отверстии, а от фрикционной муфты, одна полумуфта 16 которой жестко связана со шлицевым валом, а другая 17 — через эластичную муфту 18 с червяком z5. Далее от червяка к шпинделю неподвижной головки движение передается по такой же цепи, что и к шпинделю подвижной головки,
т. е. червячное колесо z6 и цилиндрическую зубчатую пару
Цепь подачи. Плавное перемещение подвижной накатной головки, необходимое для постепенного сближения осей роликов 1 и 2 до полного профилирования резьбы, и быстрый ее отвод в исходное положение осуществляется с помощью гидропривода. Гидропривод включает в себя гидробак 33, приемный фильтр 26, насос 27, напорный золотник 29, обратный клапан 28, двухпозиционный распределитель 24, дроссельное устройство 23 с обратным клапаном 22, гидроцилиндр 21 с поршнем 20, шток которого связан с корпусом подвижной накатной головки 31, и напорный золотник 30.
На рис. 87, а гидросхема показана в положении, когда электромагнит золотника 24, включен. В этом случае масло из гидробака через фильтр 26 засасывается насосом 27 и нагнетается по трубопроводу через обратный клапан 28, распределитель 24 и дроссель 23 в правую полость гидроцилиндра, а из левой его полости масло через распределитель 24 и фильтр 25 идет на слив. В результате поршень и связанная с ним подвижная накатная головка совершают рабочий ход, приближаясь к неподвижной головке. Скорость рабочего перемещения накатной головки регулируют дросселем 23, а передаваемое усилие — клапаном 29.
Для возвращения подвижной накатной головки в исходное положение отключают электромагнит распределителя 24. Распределитель под действием пружины переключается, масло от насоса поступает в левую полость гидроцилиндра, поршень движется вправо и вытесняет масло из правой полости гидроцилиндра через обратный клапан 22, распределитель 24 и фильтр 25 в гидробак. Усилие поршня, необходимое для возврата накатной головки в исходное положение, регулируют напорным золотником 30. Величину отвода накатной головки устанавливают регулируемым упором 34. Обратный клапан 28 введен в гидросистему для предохранения насоса от гидроударов.
Настройка и наладка станка. Устанавливают требуемую частоту вращения шпинделей накатных роликов с помощью переключения вариатора или блоков зубчатых колес в коробке скоростей. Закрепляют на шпинделях резьбонакатные ролики и монтируют поддерживающие кронштейны. Совмещают резьбонакатные ролики по торцу и заходу. Совмещение роликов по торцу производят смещением шпинделя вдоль оси с помощью рукоятки 3, вращение которой вызывает перемещение рычага 4 и шпинделя.
Для совмещения роликов по заходу необходимо одному из шпинделей (в данном случае шпинделю неподвижной головки) сообщить независимый поворот на некоторый угол с помощью рукояток 5 и 6. Поворотом рукоятки 6 вала 7 с эксцентриком 10 отклоняют вилку 12, которая через гайку 13, ось 14 и опорную втулку 11 сжимает тарельчатую пружину 15 и освобождает от осевой силы фрикционную муфту, разрывая тем самым кинематическую связь вала III с червяком z5. Вращением рукоятки 5 можно через коническую зубчатую пару повернуть на необходимый угол полумуфту 17 и связанный с ней червяк z5, который передает движение червячному колесу z6, зубчатой паре и, наконец, шпинделю VII с накатным роликом 2. После поворота шпинделя VII на требуемую величину рукоятку 6 возвращают в исходное положение. С рукояткой 6 связан кулачок 8, воздействующий на конечный выключатель 9 и предотвращающий возможность включения станка во время совмещения роликов по заходу.
В зависимости от диаметра и шага накатываемой резьбы в корпус 2 устанавливают сменную ножевую опору 1 (рис. 88). От правильности установки ножевой опоры относительно накатных роликов зависит точность, стабильность и надежность процесса накатывания резьбы. Осевое положение заготовки определяется упором 3, который можно перемещать вдоль оси 4 и паза. Упор фиксируют винтами 5 и 6.
Рис. 88. Ножевая опора
Регулируемым упором 34 (см. рис. 87) устанавливают величину поперечного хода подвижной накатной головки. Включив станок в режим «Наладки», проверяют его работу сначала на холостом, а затем и на рабочем ходу.
Цикл работы станка включает установку заготовки, подвод накатного ролика подвижной головки к заготовке, постепенное выдавливание полного профиля резьбы роликами при непрерывной подаче подвижной накатной головки, калибрование резьбы без подачи подвижной головки, быстрый отвод подвижной головки в исходное положение и снятие со станка накатанной детали.
www.stroitelstvo-new.ru
Станки для накатки резьбы и профилей
ТРАДИЦИОННЫЕ
Накатка резьбы и профилей является высокопроизводительным процессом холодной обработки металлов давлением без образования стружки. Технология формирования наружного профиля на симметричных телах вращения посредством обката профиля инструмента на деталь применяется для производства резьбы, шлицевого, зубчатого и червячного профилей.
Преимущества:
• Снижение затрат основного машинного времени, по сравнению с процессами обработки с образованием стружки
• Экономия дорогостоящих материалов и отсутствие проблем ликвидации отходов стружки
• Высокая износостойкостью и долговечность за счет укрепления поверхностного слоя профиля
• Высокая стойкость на усталостный излом детали за счет целостности направления волокон материала
Резьбонакатные станки серии PR
являются продолжением серии стандартных универсальных резьбонакатных станков выпускаемых в Бад Дюбене с 1943 года до настоящего времени. Тысячи универсальных резьбонакатных станков Universal Profil Walzmaschine различных моделей с табличкой машиностроительное предприятие Бад Дюбен поставлены в различные отрасли промышленности.
Проверенные временем, они зарекомендовали себя, как очень надежные и простые в эксплуатации.
Универсальные резьбонакатные станки:
- работают в режимах продольной и поперечной подачи заготовки
- С-образная литая станина станка гарантирует стабильность и качество, обеспечивает наиболее удобный доступ благодаря открытой сверху рабочей зоне.
- специальная регулировка скорости подачи обеспечивает оптимальные результаты
- возможность быстрой настройки и перенастройки станков
- большой угол поворота накатных шпинделей обеспечивает высокую скорость накатки при осевой подаче заготовки
- управление с помощью контроллера Симатик S-7 гарантирует удобство в работе
- компактное размещение оборудования позволяет экономить производственные площади
для выполнения различных производственный задач имеется большой выбор приспособлений и принадлежностей
ЭКОНОМИЧНЫЕ
Резьбо- и профиленакатные станки этой серии имеют электронное управление процесса накатки, благодаря которому обеспечивается оптимальные режимы работы станка и имеются широкие возможности для автоматизации станка.
С-образная станина станка обеспечивает наиболее удобный доступ благодаря открытой сверху рабочей зоне. Широкий спектр программ для накатки с электронной системой регулирования скорости и величины подачи в процессе накатки, установки диаметра позволяет подобрать оптимальный для обрабатываемого материала режим обработки. В процессе накатки необходимая сила рассчитывается автоматически и не должна задаваться оператором. Движение подвижной головки контролируется точнейшей измерительной системой, при этом реализована обратная связь процесса: на основании фактического движения подвижной головки и возникающей нагрузки на привод, осуществляется регулировка усилия гидравлики. Тип графика кривой подачи подвижной головки задается через дисплей. Выбирая различные типы кривых графика внедрения и отвода инструмента (прогрессивную, прямую, регрессивную и т.д.), а также задавая различное время этапов внедрения, калибровки и вывода инструмента дает широкий выбор режимов обработки, позволяет оптимизировать процесс и увеличить стойкость инструмента. Станок, оснащённый комплексом программ накатки, имеющий сервисные и диагностические программы, гарантирует большую „гибкость” и безотказность в эксплуатации,
С помощью контроллера осуществляется расчет рекомендуемых параметров накатки Контроллер станка сохраняет до 100 типоразмеров деталей, что сокращает время перенастройки станка при переходе с одного типоразмера, материала и инструмента на другой.
Оснащение станка поворотными накатными шпинделями позволяет осуществлять накатку методами радиальной и осевой подачи детали. При осевой подаче детали длина накатываемой резьбы не имеет ограничений по длине накатываемой резьбы. Существенно упрощается техническое обслуживание станка благодаря применению централизованной системы смазки для направляющих салазок и опорных узлов накатных шпинделей.
PR __e PRS
• исполнение с одной или двумя
• подвижными головками
• радиальная и осевая накатка
• возможность полной автоматизации
• электронная регулировка подачи и
• установки диаметра накатки
• централизованная система смазки
• управление скоростью подачи
• и отвода инструмента
• расчет корректировки нитки резьбы
• расчет рекомендуемого времени накатки
• РРчЭ – исполнение с устройством быстрой
• настройки по нитке резьбы
• оснащение сервисным пакетом контроля
• процесса
PR 15e PRS
Резьбы и профили
- метрическая и UN резьба
- резьба Витворта (дюймовая)
- трапециевидная резьба
- круглая резьба
- червячный профиль
- продольные RAA рифления
- косые RGE рифления
- мелкошлицевой профиль
- накатное полирование
- шлицы, пазы, желобки и канавки
- особенные профили
Система быстрой настройки по нитке резьбы (РРБ)
Единственная в своем роде система, позволяющая производить настройку и перенастройку инструментов в течении нескольких минут. С изобретением этой С изобретением этой системы отпадает необходимость традиционная настройка инструментов муфтой сцепления приводных валов. После измерения расхождения по нитке резьбы, на основании введенных величины рассчитывается необходимая величина корректировки. Поворот одного из накатных шпинделей на необходимый угол легко осуществляет поворотом штурвала. Это позполяет существенно сократить время настройки станка и снизить себестоимость продукции.
Узел обеспечения прецизионно синхронного вращения шпинделей
Для осуществления ряда определенных заданий с требованиями повышенного качества необходимо абсолютно синхронное вращение накатных шпинделей.
РЕЗЬБОНАКАТНЫЕ И ПРОФИЛЕНАКАТНЫЕ СТАНКИ CNC/AC
• ОДНО и двух салазочное исполнение
• радиальная и осевая накатка
• возможность полной автоматизации
• многоосевое РгоАгоП СМС/АС управление
• графическое слежение поверхности
• система визуализации процесса
• менеджмент базы данных
• интегрированная помощь пользователю
• централизованная система смазки
Резьбы и профиля высочайшего качества
• метрическая и UN резьба
• резьба Витворта (дюймовая)
• трапециевидная резьба
• круглая резьба
• червячный профиль
• продольные RAA рифления
• косые RGE рифления
• мелкошлицевой профиль
• накатное полирование
• шлицы, пазы, желобки и канавки
• особенные профили ( примеры)
несимметричная резьба и профиль профиль породного бура шарико-винтовой профиль Leacl-Screw-профиль
Станки от компании “СМК”:
smkom.ru