Ручная дуговая сварка покрытыми электродами – Ручная дуговая сварка покрытыми электродами
alexxlab | 18.03.2018 | 23 | Вопросы и ответы
Ручная дуговая сварка покрытыми электродами
Существуют различные методики получения неразъемных соединений. Сварка ручная дуговая считается наиболее рациональной и универсальной. Соответствует ли это действительности, как она ведется покрытыми электродами, особенности технологии, способы повышения ее эффективности – все это станет предметом разговора.
Когда лучше использовать
- При частой смене положения электрода. С помощью дуговой сварки можно получить качественный шов в различных направлениях – горизонтальном, вертикальном, под любым углом.
- Когда работы ведутся в сложных условиях, в том числе, труднодоступных местах.
- Если необходимо создать неразъемное соединение между разнородными металлами (сплавами), или быстро переориентироваться с одного на другой, что часто и бывает в процессе монтажа.
- Для получения швов небольшой протяженности.
Технология дуговой сварки
Любой покрытый электрод – металлический стержень, внешний слой которого (обсыпка силикатная, флюсовая, стеклянная) при сгорании образует или газовой облако, или шлак. Именно они и являются защитной средой, препятствующей проникновению в рабочую зону воздуха.
Классификация компонентов покрытия
По типу образующихся газов
- Ионизирующие.
- Защитные.
По виду шлаков
- Легирующие.
- Рафинирующие.
- Раскислители.
- Защитные, создающие «корку».
В зависимости от типа электродов шлаки также могут быть пластифицирующими и связывающими.
Существует несколько видов сварки – током постоянным, импульсным (в/ч), переменным. При подаче напряжения он идет по цепи «электрод – обрабатываемая заготовка», но только в момент касания детали. Это приводит к образованию дуги. В зоне высокой температуры (до 6 800 – 7 000 ºС) плавятся и кромки образца, и стержень. В результате дальнейшей кристаллизации металлов, которая происходит при ее снижении (так как электрод перемещается вдоль намеченной линии), получается шов.
В ручном режиме сварка ведется током переменным или постоянным. Профессионалы предпочитают последний вариант, причем с прямой полярностью. В результате электрод остается холодным, а нагревается металл в рабочей зоне.
Что учесть? Для разных видов сварки применяются свои электроды, для «=» или «~» тока.
Условия качественного ведения дуговой сварки
- Сухие срезы образцов и электрод.
- Бесперебойная подача тока.
- Целостность изоляции заземлителя. Ее дефекты нередко вызывают порчу шва, «залипание» электрода в рабочей зоне из-за «утечки» тока.
Необходимое оборудование
- Балансный реостат. С его помощью, меняя силу тока, можно выполнять не только сварочные работы, но и ряд других – резку, наплавку, стягивание.
- Кабель-заземлитель. Он является элементом эл/цепи и образует замкнутый контур, по которому протекает ток.
- «Держак».
Техника выполнения дуговой сварки
Зажигание дуги
Сила тока устанавливается, исходя из типа шва, его пространственной ориентации, марки покрытого электрода, вида металла и ряда других особенностей работы. В таблице указаны наиболее применяемые значения.
Способы «розжига»
№1 – легкое касание металла с последующим подъемом электрода на 20 – 25 мм.
№2 – применяется при обрыве дуги. Касание впереди кратера, с отведением в обратном направлении, до зоны наплава. Одновременно происходит удаление из него шлаков.
Рекомендация
Оптимальным считается диаметр дуги, лежащий в пределах 0,7 – 1,0 от сечения металлического стержня электрода. В процессе сварочных работ желательно выдерживать этот параметр в указанных рамках. Тогда шов получится качественный и ровный.
Положение покрытого электрода
Зависит от пространственной ориентации шва: потолочное, вертикальное или горизонтальное, нижнее. При накладке вертикальных швов электрод может перемещаться в обоих направлениях, как удобнее сварщику. При нижнем положении – наклон в направлении сварки. Движение – или «от себя», «или на себя».
Характеристики швов
Ширина валика зависит от специфики выполняемой операции и соотносится с диаметром покрытого электрода.
- От 0,8 до 1,5 d – «ниточный» (узкий) шов накладывается, если он первичный в многослойном. Также применяется, если толщина свариваемых образцов сравнительно небольшая (тонкий прокат).
- 2,2 – 4,0 d – самый распространенный (средний) шов. Наиболее практикуемые (но не единственно возможные) движения электрода показаны на рисунке.
Длина – зависит от специфики ведения сварки. Швы: короткие – до 30 см, средние – от 0,35 до 1 м и длинные – более 100 см.
Толщина – зависит от глубины «разделки». Исходя из этого, швы делаются одно- или многопроходными, в несколько слоев или в один.
Что лучше?
На получение шва, сделанного за 1 проходку, времени тратится меньше. Следовательно, повышается производительность. Существенный минус – недостаточная эластичность соединения, возможный перегрев металла на отдельных участках.
Многослойный шов получается более прочным, так как при повторной проходке нижележащий уровень подвергается дополнительному термическому воздействию. Структура соединения становится однородной, что напрямую сказывается на его надежности. При такой технологии сварки швы делаются разными способами: «горкой», «каскадами», последовательным наложением каждого очередного слоя по всей протяженности линии стыка. Последний вариант наиболее распространен, а два первых применяются в основном при сварке образцов большой толщины (или при глубоких разделах).
Качество нижнего слоя – гарантия прочности всего соединения. Именно первой проходке должно быть уделено повышенное внимание.
Полезные советы
- Овладевать технологией дуговой сварки желательно на том же типе аппарата, с которым предполагается работать в дальнейшем.
- Защитные фильтры имеют разные номера. Для конкретного сварщика он подбирается индивидуально, с учетом особенностей его зрения (диоптрии, чувствительность). Критерий один – сварочную ванну работник должен видеть четко.
- От правильно выбранного зазора деталь – электрод зависит качество соединения. Если он слишком мал, то получится выпуклый шов, так как прогрев металла будет недостаточным. При его величине, большей рекомендуемой, укладка расплава будет неравномерной из-за того, что дуга станет «прыгать» (отклоняться от линии сварки).
Основные правила ТБ
При дуговой ручной сварке запрещается прокладка заземлителя по сырой основе, тем более лужам, подтаявшему снегу и тому подобное.- Все операции проводятся только в резиновых перчатках. Перед началом работы в обязательном порядке проверяется их целостность.
- Лицо мастера должно быть защищено от раскаленных брызг металла, а глаза – еще и от яркого света.
Если перчатки всего лишь прорезиненные, то они должны быть абсолютно сухими. В противном случае в момент смены электрода есть риск поражения током по цепи: реостат – «держак» – работник – земля.
Остается добавить, что в статье даны лишь «азы» технологии и способов дуговой ручной сварки. Все ее преимущества могут быть реализованы лишь при условии, если работник обладает необходимыми знаниями и практическими навыками. Только в этом случае будет обеспечено высокое качество шовного соединения.
Успехов вам в овладении навыками сварщика!
ismith.ru
Ручная дуговая сварка покрытыми электродами — Осварке.Нет
Ручная дуговая сварка — дуговая сварка с использованием покрытого металлического электрода, при которой операции подачи электрода, его перемещения вдоль оси шва и поперечные манипуляции выполняется сварщиком вручную. Наиболее старый и универсальный метод сварки, требующий хорошей квалификации и опыта сварщика.
Сущность метода ручной дуговой сварки
Сварка деталей покрытым металлическим электродом возможна благодаря высокой тепловой мощности сварочной дуги, под воздействием которой металлы расплавляются. При сварке покрытым электродом сварная дуга расплавляет основной металл и в то же время металлический электрод. Участок расплавленного металла называют сварной ванной. Капли электродного металла расплавляются и переносятся в сварную ванну, увеличивая ее объем, поэтому покрытый электрод является еще присадочным материалом.
Под воздействием сварочной дуги расплавляется покрытие нанесенное на поверхность электрода. В состав покрытия входят измельченные компоненты разного назначения — шлакообразующие, газообразующие, связывающие, раскислители и другие. Шлак, полученный плавлением покрытия, обволакивает сварную ванну и защищает жидкий металл от взаимодействия из атмосферными газами. Считается, что при ручной сварке наблюдение за формированием шва ограниченное из-за наличия на поверхности сварной ванны шлака. Также покрытие выделяет газы при расплавлении его компонентов, защищающие дугу и зону сварки от воздуха. Это способствует стабильному и стойкому горению дуги.
По мере того как сварщик формирует шов, перемещая электрод и дугу вдоль оси сварного соединения, сварная ванна с жидким металлом постепенно кристаллизуется. На поверхности кристаллизованного шва застывает шлак и превращается в шлаковую корку.
После обрыва сварочной дуги необходимо очистить шов от шлаковой корки при помощи специального молотка, кирки и/или щетки. Если были выбраны правильные режимы сварки без ошибок в техники выполнения шва, под шлаковой коркой получим сварной шов необходимой формы, качества и геометрических размеров. Качество сварного шва в значительной степени будет зависеть от профессионализма сварщика.
Схема оборудования для сварки покрытым электродом
Ручная дуговая сварки имеет наиболее универсальную и простую схему оборудования необходимого для сварки. В комплект оборудования для сварки покрытым электродом входит источник питания сварочной дуги, комплект кабелей, электрододержатель и электропроводящий зажим подключаемый на кабель массы. Этого оборудования достаточно для выполнения работ. В зависимости от используемого источника питания, вида сварочного поста и технологии сварки может применяться вспомогательной сварочное оборудование.
Сварка покрытым электродом может выполняться от источника питания постоянного и переменного тока. Для сварки переменным током используют сварочные трансформаторы, а для постоянного тока — выпрямители и преобразователи.
В последнее время с развитием технологий, для сварки используют также инверторе источники питания. Преимуществами сварочных инверторов является меньшие габариты и вес оборудования, более стабильное горение дуги, простое регулирование силы тока, дополнительный функционал, — антич-залипание, горячий старт, пульсирующий ток. Появление и распространение инверторных источников питания сделало оборудование для дуговой сварки более мобильным.
Для сварки в местах где отсутствует сеть питания можно использовать сварочные агрегаты. Агрегаты позволяют вырабатывать электрический ток при помощи сварочного генератора и двигателя внутреннего сгорания.
К вторичной обмотке источника питания подключается комплект кабелей. В зависимости от силы тока сечение кабелей можно ориентировочно выбрать используя таблицу ниже.
Эдектрододержатель предназначен фиксирования сварочного электрода, его быстрой замены и подведения к нему тока, а также для комфортного управления дугой сварщику.
Токопроводящий зажим крепится к кабелю массы для подведения тока к изделию, хорошего контакта и крепления его с основным металлом.
Дополнительное оборудование
Дополнительно в электрическую цепь при сварке могут включаться балластный реостат и осциллятор.
С помощью балластного реостата можно ступенчато регулировать силу сварочного тока. Балластный реостат формирует падающую вольт-амперную характеристику источника питания, а также компенсирует постоянную составляющую тока при сварке от трансформатора.
Осциллятор предназначен для бесконтактного зажигания и стабилизации горения сварочной дуги.
Покрытые электроды для дуговой сварки
Согласно истории развития сварки до 1935 года использовались металлические электроды без покрытия или с тонким ионизирующим покрытием. Основными функциям покрытых электродов являются: подведение тока к сварочной дуге; защита дуги, расплавленного металла и зоны сварки от атмосферных газов; дополнительная подача расплавленного металла для заполнения зазора между кромок и наплавки валика шва.
Существует большое количество марок сварочных электродов отличающихся химическим составом металлического стержня, покрытием, предназначением и т. д. Краткую классификацию покрытых электродов можно посмотреть на рисунках ниже.
Нажмите для увеличениия | Нажмите для увеличениия |
Техника ручной дуговой сварки
По сравнению с другими видами сварки, ручная сварка требует больше навыков и умений от сварщика, так как все операции выполняются вручную.
Условно выполнение сварочного шва можно разделить на три этапа: зажигание дуги, выполнение шва, окончание сварки или заварка кратера.
Существует два способа зажигания сварочной дуги — касанием и чирканьем. По окончанию сварки нельзя сразу обрывать дугу, иначе в месте окончания образуется кратер. Перед тем как оборвать дугу ее сначала перемещают на верхний край сварной ванны, а потом резко обрывают. При окончании сварки можно также использовать технику заварки кратера.
Техника выполнения шва зависит от пространственного положения, типа соединения, толщины сварных деталей, протяжности соединения и доступности шва. Во время сварки покрытым электродом от сварщика требуется одновременно перемещать электрод в трех направлениях.
Ручная сварка в нижнем положении
Стыковые швы
Сварка деталей толщиной до 4 мм встык выполняется без разделки кромок. При этом диаметр электрода подбирается равный толщине основного металла. | |
Стыковые соединения без скоса кромок толщиной до 6 мм выполняются односторонним швом. | |
Листы без скоса кромок толщиной от 2 до 8 мм можно сваривать двусторонним швом. | |
Если толщина металла более 8 мм необходимо выполнять разделку кромок. | |
Чтобы избежать прожогов при выполнении корневого шва или сварке тонких деталей используют съемные медные или стальные подкладки.
Угловые швы
Сварка угловых швов в нижнем положении выполняется при сварке угловых, тавровых и нахлесточных соединений. Угловые швы в нижнем положении с катетом шва до 10 мм свариваются за один проход, электродами до 5 мм без колебательных движений концом электрода.
Угловые швы без скоса кромок с катетом более 10 мм выполняют за одни проход с поперечными колебательными движениями электрода треугольником с задержкой конца электрода в корне шва для лучшего провара. При этом дугу зажигают на горизонтальной полке, а не вертикальной, чтобы избежать натекания металла на холодную горизонтальную полку. | |
По возможности угловые швы рекомендуется сваривать в лодочку. Для избежания непроваров в таком положении лучше вести сварку опирая покрытие электрода на кромки. Сварку швов в лодочку лучше вести углом назад. | |
Сварка в симметрическую лодочку, когда между электродом и поверхностью детали образуется угол, примерно, 45 градусов. | |
В не симметрическую лодочку, когда угол между деталью и электродом по одной из сторон детали равняется, примерно, 30 градусам. | |
Ручная сварка в вертикальном положении
При сварке вертикальных швов сварку можно вести снизу вверх (на подъем) и сверху вниз (на спуск). Силу сварочного тока при сварке в вертикальном положении уменьшают на 10% по сравнению из нижним положением, а сварку ведут короткой дугой. Это необходимо для того, чтобы жидкий металл не вытекал из сварочной ванны. Использовать сварочные электроды допускающие сварку в вертикальном положении.
Сварка способом снизу вверх используется чаще всего. Это удобный и производительный метод сварки вертикальных швов, для которого используются электроды диаметром до 4 мм. Поперечные колебательные движения: полумесяцем, углом или елочкой. Дугу возбуждают в нижней части сварного шва. После этого колебательными движениями наплавляется полочка размером равным сечению шва. Наибольшая глубина плавления достигается при перпендикулярном положении электрода к основному металлу. Чтобы избежать стекания металла электрод наклоняют вниз. | |
Способ сверху вниз при ручной сварке используется редко. Его можно использовать для сварки тонкого металла до 5 мм с разделкой кромок. Не все электроды позволяют вести сварку на спуск, поэтому необходимо смотреть информацию в паспорте на электроды. | |
Дугу возбуждают в верхней части сварного шва. Когда образования капли жидкого металла необходимо наклонить электрод вниз, чтобы дуга направлялась на жидкий металл.
Ручная сварка горизонтальных швов
Сварка горизонтальных швов выполняется вертикально расположенным электродом. Ток уменьшается на 15-20% по сравнению с нижним положением, а сварку ведут короткой дугой. При подготовке кромок делается скос только верхней кромки, скос нижней кромки не требуется. Начинают сварку на нижней кромке, а потом перемещают дугу на верхнюю кромку. Соединения толщиной более 8 мм сваривают многопроходными валиками.
Ручная сварка в потолочном положении
При сварке в потолочном положении расплавленный металл пытается вытечь вниз из сварочной ванны, поэтому сварку выполняют только короткой дугой. Силу сварочного тока уменьшают на 15-20% по сравнению с нижним положением. Детали толщиной более 8 мм сваривают многопроходными швами.
Газы, которые выделяются при плавлении электродных покрытий, поднимаются вверх и могут остаться в сварном шве. Чтобы избежать этого используют только хорошо просушенные электроды.
Валики шва накладываются в разделку тремя способами: лесенкой, полумесяцем и обратнопоступательно.
Лесенкой. При сварке потолочных швов лесенкой электрод располагают к плоскости под углом 90-130 градусов, подносят к металлу и возбуждают дугу. После образования небольшой капли металла электрод отводят на 5-10 мм от металла и возвращают. Возвращаясь необходимо перекрыть предыдущую порцию металла на 1/2 или 1/3 ее длины. Такая техника позволяет постепенно кристаллизоваться металлу и избежать стеканию вниз. | |
Полумесяцем. Сварочный электрод располагают под углом 90-130 градусов, зажигают дугу и выполняют колебательные движения полумесяцем, беспрерывно заводя дугу на отвердевшую часть шва. | |
Обратнопосупательно. Сварщик возвращает конец электрода назад, на кристаллизовавшуюся часть шва, постоянно удлиняя. валик. | |
Ручная дуговая сварка толстостенных сварных соединений
Сварку толстостенных конструкций невозможно выполнить однослойным швом за один проход, поэтому сварка металла большей толщины выполняется слоями за один проход или за несколько проходов.
Многослойный шов — шов выполняющийся несколькими слоями, каждый за один проход. Используется чаще для стыковых швов. Однопроходные швы рекомендуется использовать при ширине шва не более 14-16 мм. При таком подходе остаточные деформации наименьшие. | |
Многопроходный шов — шов выполняющийся за несколько проходов. Многопроходный шов является одновременно и многослойным. Подходит больше для угловых и тавровых соединений. При толщине шва более 15 мм не рекомендуется выполнять сварку каждого слоя за проход. Первый слой в металле такой толщине успевает остыть, и в нем возникают трещины. | |
Способы наложения швов при толщине соединения более 15 мм
Для равномерного нагревания конструкции по всей длине используют несколько техник наложения швов: двойным слоем, каскадом, блоками, горкой и поперечной горкой.
При способе двойного слоя сразу после наложения первого слоя и очистки соединения от шлака накладывают второй. Второй слой необходимо накладывать в обратном направлении на длину 200-400 мм.
Сварка каскадным методом требует предварительно разбить шов на короткие участки по 200 мм. После сварки первого участка его очищают от шлака. Второй слой необходимо начинать на втором участке и вести до полного перекрытия первого. Таким образом выполняется каждый следующий слой, перекрывающий предыдущие и не дающий им остыть. | |
Сварка горкой это техника похожая на каскадный метод, но для ее реализации необходимо участие двух сварщиков. В этом случае сварка ведется от середины сварного соединения до краев. В обоих случаях сварка обратно ступенчатая не только по длине, но и по сечению шва, а зона сварки всегда остается горячей. | |
Сварка блоками прежде всего предназначена для сталей склонных к закалыванию во время сварке. При сварке блоками шов накладывают отдельными ступенями по всей высоте сечения шва. | |
Преимущества ручной сварки покрытыми электродами
Универсальная и сравнительно недорогая схема оборудования для сварки. Мобильность оборудования. Сварка ручным дуговым методом выполняется во всех пространственных положениях и в местах с ограниченным доступом. Благодаря большому количеству различных марок электродов можно сваривать разные стали и металлы, а переход между свариваемыми материалами происходит очень быстро.
Недостатки ручной сварки покрытыми электродами
Производительность труда и КПД по сравнению с другими видами сварки очень низкие. Качество сварных соединений зависит от квалификации сварщика. Дуговая сварка покрытыми электродами оказывает вредное воздействие на организм человека.
osvarke.net
Ручная дуговая сварка покрытыми электродами: особенности и применение
Существует множество типов сварки, но среди них особняком стоит ручная дуговая сварка с помощью покрытых электродов. Ручная дуговая сварка покрытыми электродами — это один из самых популярных способов соединить металлические конструкции в условиях мелкого производства или домашней сварки. Электроды с покрытием заменяют флюс и газ, с их помощью можно сделать качественный и надежный шов, не применяя дорогостоящего оборудования и не имя навыков профессиональной сварки.
Современный рынок предлагает разные типы электродов с покрытием, и начинающему сварщику довольно сложно разобраться в таком разнообразии. Мы упростим вам задачу и кратко расскажем все, что нужно знать о покрытых электродах, научим пользоваться ими в домашних условиях и поведаем обо всех особенностях, которые стоит учесть.
Содержание статьи
Виды покрытия
Виды покрытия электродов:
- А — кислые электроды. Кислые электроды содержат в своем составе окись железа, марганец, кремний и титан. Состав может отличаться, в зависимости от производителя и назначения электрода. Обратите внимание, что электроды с кислым покрытием способствуют образованию горячих трещин, так что применять их нужно осторожно.
- Б — основное покрытие электродов. Электроды с основным покрытием (наравне с рутиловым) являются самыми востребованными на рынке. Такое покрытие состоит из фтористого кальция и карбонада кальция. Чтобы шов получился качественным и надежным, установите на сварочном аппарате постоянный ток и работайте в обратной полярности. Кстати, электроды с основным покрытием почти не способствуют образованию трещин, так что рекомендуем новичкам использовать такие стержни.
- Ц — электроды с целлюлозным покрытием. Как не трудно догадаться, основа таких стержней — это целлюлоза. Иногда используется мука или другие органические вещества. При плавлении покрытия образуется газовое облако, защищающее шов от образования шлака и улучшающее его механические свойства. Электроды с целлюлозным покрытием чаще всего используют для сварки тонких металлов.
- Р — электроды с рутиловым покрытием. Это самый популярный тип покрытия и самый универсальный. Основа стержня — рутил, а также различные органические вещества, гарантирующие отсутствие шлака. Можно варить и переменным, и постоянным током. При этом металл практически не разбрызгивается, дуга стабильна, легко зажигается. Швы получаются качественными даже у начинающих сварщиков.
- П — прочие.
Иногда встречаются смешанные покрытия, они обозначаются несколькими буквами. Например, рутилово-целлюлозное покрытие — РЦ, и так далее по аналогии.
Маркировка электродов
Марка электрода играет важную роль, от ее выбора во многом зависит качество работы. На картинке ниже вы можете видеть марки покрытых электродов, используемые при сварке углеродистых и низколегированных сталей.
Для сварки иных типов металлов существуют свои марки, но в целом можно выделить наиболее распространенные: АНО-1, ОЗС-6, МР-3, УОНИ 13/45. Они вполне универсальны и подойдут для сварки большинства металлов. Но несмотря на это рекомендуем все же ознакомиться с остальными марками, чтобы в дальнейшем опираться на свой опыт и знания.
Особенности сварки покрытыми электродами
Первое, что вам нужно сделать — правильно выбрать диаметр электрода (в соответствии с типом и толщиной металла), а также установить оптимальную силу тока на сварочном аппарате. Сделав это вы уже существенно упростите дальнейшую работу и результат будет заметно лучше. Ниже вы можете видеть таблицу с рекомендуемыми значениями для рутиловых электродов.
Затем нужно разжечь дугу. Существует два способа, на картинке справа они промаркированы как «А» и «Б».
Метод «А» самый популярный. Нужно электродом коснуться поверхности металла и затем поднять его на несколько сантиметров. Также можно заменить касание на легкое постукивание. Метод «Б» используется реже, но его тоже нужно уметь использовать. Нужно коснуться электродом сварочной зоны и отвести его в сторону, по аналогии с тем, как вы зажигаете спичку. Этот метод также называется «чирканьем». Также важно уметь определять правильный диаметр электрической дуги. Опытные мастера считают, что диаметр не должен превышать 0,7 – 1,0 от сечения металлического конца электрода. И мы согласны с этим. Конечно, допустимы небольшие отклонения, но все же рекомендуем придерживаться именно этого показателя. Это поспособствует образованию качественного прочного шва.
Обратите внимание на положение электрода. Оно напрямую зависит от того, в какой пространственной ориентации вы проводите сварку: горизонтальная, вертикальная, нижняя, потолочная, угловая и так далее. Если нужно сварить вертикальный шов, то электрод может располагаться параллельно свариваемой поверхности и перемещаться в любую сторону, на усмотрение сварщика. Если вы варите в нижнем положении, то электрод должен двигаться от себя. Допускается движение на себя, но только если другой вариант недоступен.
Полезный совет! Если вам предстоит сварка потолочного или вертикального шва на высоте, то уменьшите силу тока на вашем сварочном аппарате до минимального значения. Так вы сможете контролировать плавление электрода и сформируете шов раньше, чем расплавленный стержень начнет капать вниз.
Также не забудьте о самих швах. В большинстве случаев их ширина должна быть сопоставима с диаметром электрода. Да, бывают специфичные работы, где шов очень широкий, но к ручной сварке это не относится. На рисунке ниже вы можете видеть наиболее распространенные траектории ведения шва. Они не единственно верные, но их будет достаточно для начинающего сварщика.
Еще швы могут быть однослойными и многослойными. Однослойные состоят, как не трудно догадаться, из одного слоя наплавленного металла, а многослойные — из нескольких. В многослойных соединениях есть так называемый нижний слой (или шов) и средний слой. От качества нижнего шва напрямую зависит долговечность сварного соединения. Даже если закрыть некачественный нижний шов более качественным средним, через время все равно появится коррозия и соединение начнет разрушаться.
Часто сварщики спорят о том, какой тип шва лучше. Конечно, однослойные швы делаются гораздо быстрее многослойных, но они не обладают должной эластичностью и долговечностью. Выбирайте тип шва исходя из поставленной задачи. Если вам нужно сварить стеллаж для гаража, то многослойные швы ни к чему.
Вместо заключения
Ручная дуговая сварка покрытыми электродами — это относительно недорогой и простой способ выполнить большинство сварочных работ в домашних условиях. Электроды с покрытием продаются в любом сварочном магазине и их ассортимент очень широк. Вы можете приобрести стержни исходя из своих задач и бюджета. Мы рекомендуем покупать комплектующие от проверенных производителей, не гнаться за самой низкой ценой и не покупать откровенно контрафактную продукцию.
Мы рассказали вам всю основную информацию об электродах с покрытием. Не поленитесь и изучите дополнительные материалы, например, сварочные нормативные документы. В них вы сможете узнать дополнительные особенности дуговой сварки с помощью покрытых электродов и правила сварки в целом. Делитесь этой статьей в социальных сетях и опишите свой опыт использовать покрытых стержней в комментариях. Желаем удачи!
svarkaed.ru
РУЧНАЯ ДУГОВАЯ СВАРКА МЕТАЛЛИЧЕСКИМИ ЭЛЕКТРОДАМИ С ПОКРЫТИЕМ
Под техникой сварки обычно понимают приемы манипулирования электродом, выбор режимов сварки, приспособлений и способы их применения для получения качественного шва и т.п. Качество швов зависит не только от техники сварки, но и от других факторов, таких как состав и качество применяемых сварочных материалов, состояние свариваемой поверхности, качество подготовки и сборки кромок под сварку и т.д.
Дуговая сварка металлическими электродами с покрытием в настоящее время остается одним из распространенных методов, используемых при изготовлении сварных конструкций. Это объясняется простотой и мобильностью применяемого оборудования, возможностью выполнения сварки в различных пространственных положениях и в местах, труднодоступных для механизированных способов сварки.
Существенный недостаток ручной дуговой сварки металлическим электродом – малая производительность процесса и зависимость качества сварного шва от практических навыков сварщика. В первые годы применения дуговой сварки использовались металлические электроды с тонким ионизирующим покрытием, повышающим стабильность дуги. Однако свойства металла шва при этом были низкими. Поэтому в настоящее время подобные электроды для сварки не применяют.
Сущность способа. К электроду и свариваемому изделию для образования и поддержания сварочной дуги от источников сварочного тока подводится постоянный или переменный сварочный ток (рис. 3.12). Дуга расплавляет металлический стержень электрода, его покрытие и основной металл. Расплавляющийся металлический стержень электрода в виде отдельных капель, покрытых шлаком, переходит в сварочную ванну. В сварочной ванне электродный металл смешивается с расплавленным металлом изделия (основным металлом), а расплавленный шлак всплывает на поверхность.
Глубина, на которую расплавляется основной металл, называется глубиной проплавления. Она зависит от режима сварки (силы сварочного тока и диаметра электрода), пространственного положения сварки, скорости перемещения дуги по поверхности изделия (торцу электрода и дуге сообщают поступательное движение вдоль направления сварки и поперечные колебания), от конструкции сварного соединения, формы и размеров разделки свариваемых кромок и т.п. Размеры сварочной ванны зависят от режима сварки и обычно находятся в пределах: глубина до 7 мм, ширина 8 … 15 мм, длина 10 … 30 мм. Доля участия основного металла в формировании металла шва (см. гл. 2) обычно составляет 15 … 35 %.
Расстояние от активного пятна на расплавленной поверхности электрода до другого активного пятна дуги на поверхности сварочной ванны называется длиной дуги. Расплавляющееся покрытие электрода образует вокруг дуги и над поверхностью сварочной ванны газовую атмосферу, которая, оттесняя воздух из зоны сварки, препятствует взаимодействиям его с расплавленным металлом. В газовой атмосфере присутствуют также пары основного и электродного металлов и легирующих элементов. Шлак, покрывая капли электродного металла и поверхность расплавленного металла сварочной ванны, способствует предохранению их от контакта с воздухом и участвует в металлургических взаимодействиях с расплавленным металлом.
Рис. 3.12. Ручная дуговая сварка металлическим электродом с покрытием:
1 – металлический стержень; 2 – покрытие электрода; 3 – газовая атмосфера дуги; 4 – сварочная ванна; 5 – затвердевший шлак; 6 – закристаллизовавшийся металл шва; 7 – основной металл; 8 – капли расплавленного электродного металла; 9 – глубина проплавления
Кристаллизация металла сварочной ванны по мере удаления дуги приводит к образованию шва, соединяющего свариваемые детали. При случайных обрывах дуги или при смене электродов кристаллизация металла сварочной ванны приводит к образованию сварочного кратера (углублению в шве, по форме напоминающему наружную поверхность сварочной ванны). Затвердевающий шлак образует на поверхности шва шлаковую корку.
Ввиду того, что от токоподвода в электрододержателе сварочный ток протекает по металлическому стержню электрода, стержень разогревается. Этот разогрев тем больше, чем дольше протекание по стержню сварочного тока и чем больше величина последнего. Перед началом сварки металлический стержень имеет температуру окружающего воздуха, а к концу расплавления электрода температура повышается до 500 … 600°С (при содержании в покрытии органических веществ – не выше 250°С). Это приводит к тому, что скорость расплавления электрода (количество расплавленного электродного металла) в начале и конце различна. Изменяется и глубина проплавления основного металла ввиду изменения условий теплопередачи от дуги к основному металлу через прослойку жидкого металла в сварочной ванне. В результате изменяется соотношение долей электродного и основного металлов, участвующих в образовании металла шва, а значит, и состав и свойства металла шва, выполненного одним электродом. Это – один из недостатков ручной дуговой сварки покрытыми электродами.
Зажигать дугу можно двумя способами. При одном способе электрод приближают вертикально к поверхности изделия до касания металла и быстро отводят вверх на необходимую длину дуги. При другом – электродом вскользь “чиркают” по поверхности металла. Применение того или иного способа зажигания дуги зависит от условий сварки и от навыка сварщика.
Длина дуги зависит от марки и диаметра электрода, пространственного положения сварки, разделки свариваемых кромок и т.п. Нормальная длина дуги считается в пределах Lд = (0,5 … 1,1)dэл (dэл – диаметр электрода). Увеличение длины дуги снижает качество наплавленного металла шва ввиду его интенсивного окисления и азотирования, увеличивает потери металла на угар и разбрызгивание, уменьшает глубину проплавления основного металла. Также ухудшается внешний вид шва.
Во время ведения процесса сварщик обычно перемещает электрод не менее чем в двух направлениях. Во-первых, он подает электрод вдоль его оси в дугу, поддерживая необходимую в зависимости от скорости плавления электрода длину дуги. Во-вторых, перемещает электрод в направлении наплавки или сварки для образования шва. В этом случае образуется узкий валик, ширина которого при наплавке равна примерно (0,8 … 1,5) dэл и зависит от силы сварочного тока и скорости перемещения дуги по поверхности изделия. Узкие валики обычно накладывают при проваре корня шва, сварке тонких листов и тому подобных случаях.
При правильно выбранном диаметре электрода и силе сварочного тока скорость перемещения дуги имеет большое значение для качества шва. При повышенной скорости дуга расплавляет основной металл на малую глубину и возможно образование непроваров. При малой скорости вследствие чрезмерно большого ввода теплоты дуги в основной металл часто образуется прожог, и расплавленный металл вытекает из сварочной ванны. В некоторых случаях, например при сварке на спуск, образование под дугой жидкой прослойки из расплавленного электродного металла повышенной толщины, наоборот, может привести к образованию непроваров.
Иногда сварщику приходится перемещать электрод поперек шва, регулируя тем самым распределение теплоты дуги поперек шва для получения требуемых глубины проплавления основного металла и ширины шва. Глубина проплавления основного металла и формирование шва главным образом зависят от вида поперечных колебаний электрода, которые обычно совершают с постоянными частотой и амплитудой относительно оси шва (рис. 3.13).
При сварке с поперечными колебаниями получают уширенный валик, ширина которого обычно составляет (2 … 4) dэл, а форма проплавления зависит от траектории поперечных колебаний конца электрода, т.е. от условий ввода теплоты дуги в основной металл.
Рис. 3.13. Траектории выполнения сварки
По окончании сварки – обрыве дуги следует правильно заварить кратер. Кратер является зоной с наибольшим количеством вредных примесей ввиду повышенной скорости кристаллизации металла, поэтому в нем наиболее вероятно образование трещин. По окончании сварки не следует обрывать дугу, резко отводя электрод от изделия. Необходимо прекратить все перемещения электрода и медленно удлинять дугу до обрыва; расплавляющийся при этом электродный металл заполнит кратер. При сварке низкоуглеродистой стали кратер иногда выводят в сторону от шва – на основной металл. При случайных обрывах дуги или при смене электродов дугу возбуждают на еще не расплавленном основном металле перед кратером и затем проплавляют металл в кратере.
Положение электрода относительно поверхности изделия и пространственное положение сварки оказывают большое влияние на форму шва и проплавление основного металла (рис. 3.14). При сварке углом назад улучшаются условия оттеснения из-под дуги жидкого металла, толщина прослойки которого уменьшается. При этом улучшаются условия теплопередачи от дуги к основному металлу и растет глубина его проплавления. То же наблюдается при сварке шва на подъем на наклонной или вертикальной плоскости. При сварке углом вперед или на спуск расплавленный металл сварочной ванны, подтекая под дугу, ухудшает теплопередачу от нее к основному металлу – глубина проплавления уменьшается, а ширина шва возрастает (сечения швов на рис. 3.14).
Рис. 3.14. Способы выполнения сварки:
а – углом назад; б – углом вперед; в – на подъем; г-на спуск
При прочих равных условиях количество расплавляемого электродного металла, приходящегося на единицу длины шва, остается постоянным, но распределяется на большую ширину шва и поэтому высота его выпуклости уменьшается. При наплавке или сварке тонколистового металла (толщина до 3 мм) для уменьшения глубины провара и предупреждения прожогов рекомендуется сварку выполнять на спуск (наклон до 15°) или углом вперед без поперечных колебаний электрода.
Для сборки изделия под сварку (обеспечения заданного зазора в стыке, положения изделий и др.) можно применять специальные приспособления или короткие швы – прихватки. Длина прихваток обычно составляет 20 … 120 мм (больше при более толстом металле) и расстояние между ними 200 … 1200 мм (меньше при большей толщине металла для увеличения жесткости). Сечение прихваток не должно превышать 1/3 сечения швов. При сварке прихватки необходимо полностью переплавлять.
Техника сварки в нижнем положении. Это пространственное положение позволяет получать сварные швы наиболее высокого качества, так как облегчает условия выделения неметаллических включений, газов из расплавленного металла сварочной ванны. При этом также наиболее благоприятны условия формирования металла шва, так как расплавленный металл сварочной ванны от вытекания удерживается не расплавившейся частью кромок.
Стыковые швы сваривают без скоса кромок или с V-, Х- и U-образным скосом. Положение электрода относительно поверхности изделия и готового шва показано на рис. 3.15. Стыковые швы без скоса кромок в зависимости от толщины сваривают с одной или двух сторон. При этом концом электрода совершают поперечные колебания с амплитудой, определяемой требуемой шириной шва. Следует тщательно следить за равномерным расплавлением обеих свариваемых кромок по всей их толщине и особенно стыка между ними в нижней части (корня шва).
Рис. 3.15. Положение электрода при сварке в нижнем положении:
а – поперек оси шва; б — сбоку
Однопроходную сварку с V-образным скосом кромок обычно выполняют с поперечными колебаниями электрода на всю ширину разделки для ее заполнения так, чтобы дуга выходила со скоса кромок на необработанную поверхность металла. Однако в этом случае очень трудно обеспечить равномерный провар корня шва по всей его длине, особенно при изменении величины притупления кромок и зазора между ними.
При сварке шва с V-образным скосом кромок за несколько проходов обеспечить хороший провар первого слоя в корне разделки гораздо легче. Для этого обычно применяют электроды диаметром 3 … 4 мм и сварку ведут без поперечных колебаний. Последующие слои выполняют в зависимости от толщины металла электродом большего диаметра с поперечными колебаниями. Для обеспечения хорошего провара между слоями предыдущие швы и кромки следует тщательно очищать от шлака и брызг металла.
Заполнять разделку кромок можно швами с шириной на всю разделку или отдельными валиками (рис. 3.16). В многопроходных швах последний валик (11 на рис. 3.16, в) для улучшения внешнего вида иногда можно выполнять на всю ширину разделки (декоративный слой).
Сварку швов с Х- или U-образным скосом кромок выполняют в общем так же, как и с V-образным скосом. Однако для уменьшения остаточных деформаций и напряжений, если это возможно, сварку ведут, накладывая каждый валик или слой попеременно с каждой стороны. Швы с Х- или U-образным скосом кромок по сравнению с V-образным имеют преимущества, так как в первом случае в 1,6 … 1,7 раза уменьшается объем наплавленного металла (повышается производительность сварки). Кроме того, уменьшаются угловые деформации, а возможный непровар корня шва образуется в нейтральном по отношению к изгибающему моменту сечении. Недостаток U-образного скоса кромок – повышенная трудоемкость его получения.
Рис. 3.16. Поперечные сечения стыковых швов:
а – однопроходных; б – многослойных; в – многопроходных;
I-VI-слои; 1-11 – проходы
Рис. 3.17. Схемы сварки:
а – на весу; б – на остающейся стальной подкладке; в – с предварительным подварочным швом; г – удаление непровара в корне шва для последующей подварки; О- основной шов; П- подваренный шов.
Сварку стыковых швов можно выполнять различными способами (рис. 3.17). При сварке на весу наиболее трудно обеспечить провар корня шва и формирование хорошего обратного валика по всей длине стыка. Требуется большой опыт сварщика для обеспечения провара корня шва и предупреждения прожогов. Для этого применяют электроды малого диаметра, что снижает производительность сварки. В тех случаях, когда имеется доступ к стыку с обеих сторон, возможно применение подкладок: остающейся стальной и съемных медной, керамической, стекловолоконной. Для предупреждения вытекания расплавленного металла из сварочной ванны необходимо плотное поджатие их к свариваемым кромкам. Крепление съемных подкладок под стыком осуществляется различными способами: с помощью магнитов, клиньев, самоклеящейся алюминиевой ленты и др.
Применение подкладок позволяет использовать для сварки корневого шва электроды повышенного диаметра и, значит, увеличенного сварочного тока. Однако остающиеся подкладки увеличивают расход металла и не всегда технологичны. При использовании медных подкладок возникают трудности точной установки кромок вдоль формирующей канавки.
Если с обратной стороны возможен подход к корню шва и допустима выпуклость обратной стороны шва, целесообразна подварка корня швом небольшого сечения с последующей укладкой основного шва (рис. 3.17, в). В некоторых случаях при образовании непроваров в корне шва после сварки основного шва дефект в корне разделывают газовой, воздушно-дуговой строжкой или механическими методами (рис. 3.17, г) с последующим выполнением подварочного шва.
Сварку угловых швов в нижнем положении можно выполнять двумя приемами. Сварка вертикальным электродом в лодочку (рис. 3.18, а) обеспечивает наиболее благоприятные условия для провара корня шва и формирования его выпуклости. По существу, этот прием напоминает сварку стыковых швов с V-образным скосом кромок, так как шов формируется между свариваемыми поверхностями.
Рис. 3.18. Положение электрода и изделия при сварке:
а — в лодочку; б — наклонным электродом; в – внахлестку; г – углового соединения
Однако при этом способе требуется тщательная сборка соединения под сварку с минимальным зазором в стыке для предупреждения вытекания из него расплавленного металла.
При сварке наклонным электродом (рис. 3.18, 6 – г) трудно обеспечить провар шва по нижней плоскости (ввиду натекания на нее расплавленного металла) и предупредить подрез на вертикальной плоскости (ввиду отекания расплавленного металла). Поэтому таким способом обычно сваривают швы с катетом 6 … 8 мм. При сварке угловых швов наклонным электродом трудно также обеспечить глубокий провар в корне шва, поэтому в односторонних или двусторонних швах без скоса кромок может образоваться непровар (рис. 3.19, а), который при нагружении шва послужит началом развития трещин. Для предупреждения этого в ответственных соединениях при толщине металла 4 мм и более необходим односторонний скос, а при толщине 12 мм и более -двусторонний скос кромок.
При сварке наклонным электродом многопроходных швов первым выполняют шов на горизонтальной плоскости (рис. 3.19, б). Формирование последующего валика происходит с частичным удержанием расплавленного металла сварочной ванны нижележащим валиком. При сварке угловых швов применяют поперечные колебания электрода. Особенно важен правильный выбор их траектории при сварке наклонным электродом с целью предупреждения возникновения указанных выше дефектов.
Рис. 3.19. Сварка угловых швов:
1-6 – последовательность наложения швов
Сварка швов в положениях, отличающихся от нижнего, требует повышенной квалификации сварщика в связи с возможным под действием сил тяжести вытеканием расплавленного металла из сварочной ванны или падением капель электродного металла мимо сварочной ванны. Для предотвращения этого сварку следует вести по возможности наиболее короткой дугой, в большинстве случаев с поперечными колебаниями.
Расплавленный металл в сварочной ванне от вытекания удерживается в основном силой поверхностного натяжения. Поэтому необходимо уменьшать размер сварочной ванны, для чего конец электрода периодически отводят в сторону от ванны, давая возможность ей частично закристаллизоваться. Ширину валиков также уменьшают до двух-трех диаметров электродов. Применяют пониженную на 10 … 20 % силу тока и электроды уменьшенного диаметра (для вертикальных и горизонтальных швов не более 5 мм, для потолочных не более 4 мм).
Сварку вертикальных швов можно выполнять на подъем (снизу вверх, рис. 3.20, а) или на спуск. При сварке на подъем нижележащий закристаллизовавшийся металл шва помогает удержать расплавленный металл сварочной ванны. При этом способе облегчается возможность провара корня шва и кромок, так как расплавленный металл стекает с них в сварочную ванну, улучшая условия теплопередачи от дуги к основному металлу. Однако внешний вид шва – грубочешуйчатый. При сварке на спуск получить качественный провар трудно: шлак и расплавленный металл подтекают под дугу и от дальнейшего стекания удерживаются только силами давления дуги и поверхностного натяжения. В некоторых случаях их оказывается недостаточно, и расплавленный металл вытекает из сварочной ванны.
Рис. 3.20. Положение электрода при сварке швов:
а – вертикальных; б – потолочных; в – горизонтальных
Сварка горизонтальных стыковых швов (рис. 3.20, в) более затруднена, чем вертикальных, из-за стекания расплавленного металла из сварочной ванны на нижнюю кромку. В результате возможно образование подреза по верхней кромке. При сварке металла повышенной толщины обычно делают скос только одной верхней кромки, нижняя помогает удерживать расплавленный металл в сварочной ванне. Сварка горизонтальных угловых швов в нахлесточных соединениях не вызывает трудностей и по технике не отличается от сварки в нижнем положении.
Сварка швов в потолочном положении (рис. 3.20, б) наиболее сложна и ее по возможности следует избегать. Сварку выполняют периодическими короткими замыканиями конца электрода на сварочную ванну, во время которых металл сварочной ванны частично кристаллизуется, что уменьшает объем сварочной ванны. В то же время расплавленный электродный металл вносится в сварочную ванну. При удлинении дуги образуются подрезы. При сварке этих швов ухудшены условия выделения из расплавленного металла сварочной ванны шлаков и газов. Поэтому свойств металла шва несколько ниже, чем при сварке в других пространственных положениях.
Техника сварки прорезных соединений практически не отличается от рассмотренной выше техники сварки стыковых или угловых швов.
В зависимости от протяженности шва, толщины и марки металла, жесткости конструкции и т.д. применяют различные приемы последовательности сварки швов и заполнения разделки (рис. 3.21). Они позволяют уменьшить деформации и остаточные сварочные напряжения. Сварку напроход обычно применяют при сварке коротких швов (до 500 мм).
Швы длиной до 1000 мм лучше сваривать от середины к концам или об-ратноступенчатым методом. При последнем способе весь шов разбивают на участки по 150 … 200 мм, которые должны быть кратны длине участка, наплавляемого одним электродом. Сварку швов в ответственных конструкциях большой толщины выполняют блоками, каскадом или горкой, что позволяет влиять на структуру металла шва и сварного соединения и его механические свойства.
–
Рис. 3.21. Сварка швов:
а – напроход; б – от середины к концам; в – обратноступенчато; г – блоками; д – каскадом; е – горкой. Стрелками указаны последовательность и направление сварки в каждом слое (1-5)
Похожие статьи:
poznayka.org
Ручная дуговая сварка покрытым электродом
Под техникой ручной дуговой сварки будем понимать манипуляции со сварочным электродом, выбор параметров сварки, приспособлений, способы получения качественных швов.
Качество швов определяется не только техникой сварки, но и зависит от ряда факторов:
– состав и качество применяемых электродов;
– состояние свариваемых поверхностей;
– качество подготовки и сборки под сварку.
Наиболее распространенный способ – ручная дуговая сварка покрытыми электродами, так как позволяет варить в любых пространственных положениях и труднодоступных местах.
Недостатки: малая производительность, зависимость качества шва от практических навыков сварщика.
Сущность метода: к электроду и изделию подается постоянный или переменный сварочный ток, при этом появляется дуга, которая расплавляет металлический стержень, покрытие и основной металл.
Расплавленный металл каплями переходит в сварочную ванну, в которой металл электрода перемешивается с основным, а шлак всплывает на поверхность.
Максимальная глубина, на которую расплавляется основной металл, является количественным показателем и зависит от скорости перемещения относительно изделия, при этом учитываются поперечные колебания относительно и конструктивные особенности разделки шва.
Доля участия основного металла в формировании металла шва – 15-40%.
Длина дуги – расстояние от активного пятна на электроде до активного пятна на поверхности сварочной ванны. Расплавляемое покрытие образует атмосферу, которая оттесняет воздух. В этой атмосфере присутствуют пары основного металла.
Образующаяся корка защищает сварной шов при остывании и участвует в металлургических процессах.
Качество шва определяется длиной электрода, наличием прерываний в процессе сварки. Электрод по мере плавления нагревается, и это все в комплексе влияет на параметры соединения.
Следует учитывать, что теплоотвод в держателе должен быть значителен, так как после сварки температура электрода достигает 500-600 C. Если в покрытии содержатся органические вещества, то температура огарка не превышает 250 C.
Процессы возбуждения, зажигания и поддержания дуги.
Сначала устанавливаются параметры дуги.
При ручной дуговой сварке есть два способа зажечь дугу: вертикальным перемещением электрода с закорачиванием и чирканьем.
Применение того или иного способа определяется навыками сварщика.
Длина дуги зависит от марки и диаметра электрода, пространственного положения и находится в пределах 0,5-1,1 диаметра электрода.
Изменение диаметра дуги может привести к интенсивному окислению, азотированию, увеличив потери на угар и разбрызгивание.
Во время ведения процесса сварщик перемещает электрод в нескольких направлениях:
– по оси шва;
– поперёк шва для заполнения разделки.
Если заканчивается электрод, образуется кратер. Сварщик должен уметь заварить его и завершить процесс сварки.
При аттестации сварщика используется обязательное прерывание швов.
Положение электрода относительно поверхности изделия также оказывает влияние на форму и проплавление основного металла.
Различают:
1. Сварку углом назад .Улучшаются условия оттеснения дуги из жидкого металла и теплоотдачи от дуги к основному металлу, растет глубина его проплавления.
2. Сварку углом вперед.
3. Сварку на подъем.
4. Сварку на спуск.
За счет этих приемов можно изменять теплоотдачу и регулировать глубину проплавления и ширину шва.
Расплавление электродного материала на единицу длины шва остается постоянным, но распределение этого объема на большую ширину будут влиять на величину усиления шва.
То есть, если правильно подобрать разделку кромок, то можно получить различную форму шва.
Сборка под сварку.
Заключается в выдерживании определенных зазоров в стыке. Для фиксации соединений применяются прихватки. Их длина оговаривается отдельно.
При выполнении основного шва все прихватки должны быть переплавлены.
Если нет зазора и это труба, то не будет проплавления.
По СНИПам точно регламентируется количество прихватов.
«Держать дугу» – сварить неповоротный стык.
Также по теме:
Свойства дуги. Свойства сварочной дуги.
ВАХ дуги. Вольт-амперная характеристика дуги.
svarder.ru
Ручная дуговая сварка покрытыми электродами MMA: технология
В наше время существует большое количество разнообразных способов соединения металла с помощью сварки. Было разработано множество методик, но одна из самых первых и простых по-прежнему является самой распространенной. Ручная дуговая сварка покрытыми электродами проводится при помощи сварочного трансформатора или инвертора. Существует масса моделей этой техники, а также марок покрытых электродов, которые могут быть задействованы в данном процессе. Каждая из них обладает своими особенностями, так как выпускаются под определенные марки металла.
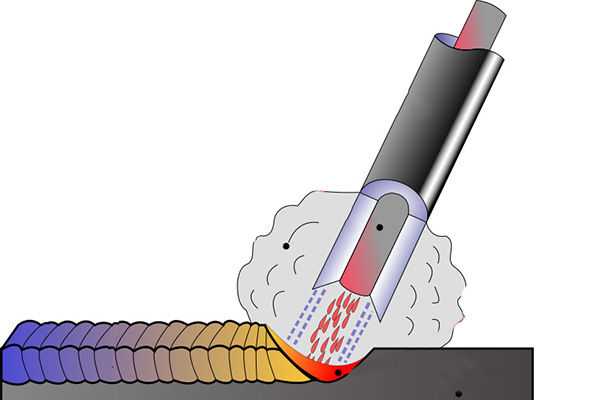
Ручная дуговая сварка покрытыми электродами
Область применения
MMA сварка может использоваться практически в любой сфере. В основном ее применяют для соединения низкоуглеродистых сталей. Это чаще всего применяется в частной сфере, на мелких строительных работах, при ремонте различных деталей, а также на производстве. Существуют электроды, которые рассчитаны на применение в судостроительной области, металлургии, работе в химической промышленности и так далее. Для особенно ответственных мест ее стараются не использовать, так как она уступает многим другим разновидностям, таким как TIG сварка.
Преимущества
К основным преимуществам данной технологии можно отнести следующие факторы:
- Относительно низкая себестоимость получаемых швов;
- Не требуется длительный процесс настройки и подготовки сварочного оборудования и материалов;
- Здесь не возникает большой опасности взрыва, как при работе с газом;
- Сварка может проводиться как с тонкими, так и с толстыми деталями;
- Техника для проведения работ компактна и мобильна;
- Инверторы без проблем работают от обыкновенной бытовой розетки;
- Имеется широкий выбор сварочных трансформаторов и инверторов любой ценовой категории и различных параметров;
- Все материалы являются широкодоступными.
Недостатки
Но здесь имеется и ряд недостатков, среди которых следует отметить следующие:
- Покрытие электрода обеспечивает низкий уровень защиты, если сравнивать с другими технологиями, так что шов уступает по качеству им;
- Покрытие электрода может отсыреть, что приведет к попаданию внутрь ванны водорода;
- Скорость сварки является быстрой, так что неопытные сварщики могут допускать много ошибок по неосторожности;
- Цветные металлы, их сплавы, нержавейка и другие сорта, которые плохо свариваются, оказываются очень проблемными при обработке данным способом;
- Вероятность появления брака сильно зависит от внешних условий;
- Чтобы создать приемлемый уровень качества сварки нужно применять множество дополнительных материалов и видов обработки, таких как флюсы и прочее.
Режимы сварки
Для каждого конкретного случая соединения заготовок требуется подбирать свой режим. Здесь существует огромное количество факторов, которые влияют на параметры техники. Для многих случаев уже заранее подобраны параметры, которые основаны на опыте профессионалов. Но существуют и такие ситуации, когда режим нужно выставлять самостоятельно. На параметры режима оказывают влияние следующие факторы:
- Род используемого электричества;
- Полярность тока;
- Диаметр расходного материала;
- Скорость проведения сварочных работ;
- Сила напряжения;
- Сила тока;
- Пространственное положение шва.
Принцип работы
Принцип работы ручной дуговой сварки достаточно прост. Сварочный аппарат выполняет роль преобразователя электричества из сети под заданные параметры. Из него выходит два вывод – земля и держатель электрода. Каждый из них может быть как плюсом, так и минусом. Держатель проводит ток, который передается электрода, так что основной контакт образуется между ним и основным металлом.
После подачи питания электричество проходит через трансформатор и выводится на плюс и минус.
«Важно!
Сварщик создает электрическую дугу, не замыкая цепь полностью, иначе было бы короткое замыкание, а держа ее в постоянно размыкающемся состоянии, что обеспечивает появление электрической дуги.»
В этом месте температура горения достигает такого уровня, что расплавляет основной металл и электрод, из которого берется основной металл для шва.
Технология сварки
Технологи ручной дуговой сварки покрытыми электродами включает в себя не только выбор правильного режима, но и в правильном порядке действий. Сначала заполняется ванна с расплавленным металлом в достаточном объеме, чтобы можно было сформировать валик нужной формы. Шов может быть беспрерывным, если деталь обладает достаточной толщиной, чтобы противостоять деформации. В ином случае может быть коробление от высокой температуры. Чтобы его не былою нужно делать шов короткими участками.
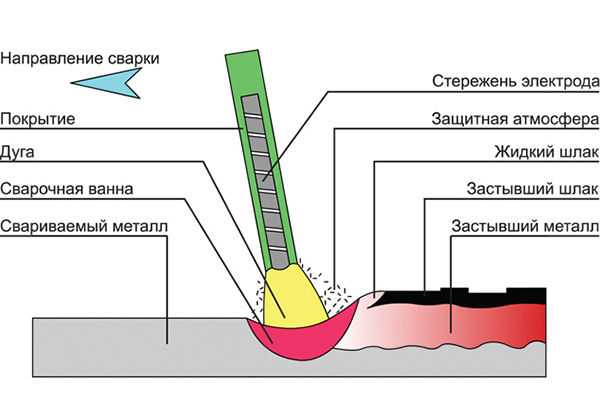
Схема ручной дуговой сварки покрытыми электродами
Сварочные материалы
Здесь используется два основных вида сварочных материалов:
- Покрытые электроды, благодаря которым данная технология и получила свое название. В основном они разделяются по составу, так как он должен быть максимально похож на основной металл. Также есть различные типы покрытия, в зависимости от сферы применения данных материалов.
- Флюс, служащий для улучшений характеристик процесса сварки. Выделяют твердые и жидкие виды, причем некоторые из них могут содержать металлические частицы.
Техника безопасности
Во время работы нужно использовать средства индивидуальной защиты и рабочую огнеупорную одежду. Не допускается нахождение поблизости легко воспламеняемых предметов. Нужно следить за целостностью токоведущих частей и заземлением. Перед свариванием нужно очистить рабочее место от лишних предметов.
Заключение
Для ручной дуговой сварки использование покрытых электродов является наиболее распространенным вариантом. Электроды являются относительно недорогими и для простых процедур дают неплохую защиту от внешних факторов. Главное перед использованием их правильно просушить, а если потребуется, то и прокалить, чтобы не возникало проблем с применением.
svarkaipayka.ru
8.1 Ручная дуговая сварка покрытым электродом. Техника сварки.
Под техникой сварки обычно понимают приемы манипулирования электродом или горелкой, выбор режимов сварки, приспособлений и способы их применения дли получения качественного шва и т. п.
В зависимости от формы и размеров изделия швы можно сваривать в различных пространственных положениях.
Во время сварки сварщик сообщает концу электрода движение в трех направлениях.
Первое движение — поступательное по направлению оси электрода, для поддержания необходимой длины дуги.
Длина дуги оказывает большое влияние на качество сварного шва и его форму. Увеличение длины дуги снижает качество наплавленного металла шва ввиду его интенсивного окисления и азотирования, увеличивает потери металла на угар и разбрызгивание, уменьшает глубину проплавления основного металла. Также ухудшается внешний вид шва.
Второе движение — вдоль оси валика для образования сварного шва. Скорость движения электрода зависит от величины тока, диаметра электрода, типа и пространственного положения, в котором выполняется шов. Правильно выбранная скорость перемещения электрода вдоль оси шва обеспечивает требуемую форму и качество сварного шва. При большей скорости перемещения электрода основной металл не успевает проплавляться, вследствие чего образуется непровар. Недостаточная скорость перемещения электрода приводит к перегреву и прожогу (сквозное проплавление) металла, а также снижает качество и производительность сварки.
Сварной шов, образованный в результате первого и второго движения электрода, называют ниточным. Его применяют при сварке металла небольшой толщины, при наплавочных работах и подварке подрезов.
Третье движение — колебание концом электрода поперек шва для образования уширенного валика, который применяют чаще, чем ниточный. Для образования уширенного валика электроду сообщают поперечные колебательные движения чаще всего с постоянной частотой и амплитудой, совмещенные с поступательным движением электрода вдоль оси подготовленного под сварку соединения и оси электрода. Поперечные колебательные движения электрода разнообразны и определяются формой, размерами, положениями шва в пространстве, в котором выполняется сварка, и навыком сварщика.
Рисунок 25 – Основные виды траекторий движений конца электрода при слабом прогреве (А, Б, В, Г), усиленном прогреве середины (Д), свариваемых кромок (Е-Ж) , усиленном прогреве одной кромки (З, И), прогреве корня шва (К).
9.1 Ручная дуговая сварка покрытым электродом. Сварочные материалы. Режимы сварки.
Электроды для ручной дуговой сварки представляют собой стержни длиной до 450 мм, изготовленные из сварочной проволоки (ГОСТ 2246-70), на поверхность которых нанесен слой покрытия различной толщины. Один из концов электрода на длине 20—30 мм освобожден от покрытия для зажатия его в электрододержателе с целью обеспечения электрического контакта. Торец другого конца очищают от покрытия для возможности возбуждения дуги посредством касания изделия в начале процесса сварки.
Покрытие предназначено для повышения устойчивости горения дуги, образования комбинированной газошлаковой защиты, легирования и рафинирования металла. Для изготовления покрытий применяют различные материалы (компоненты).
Под режимом сварки понимают совокупность условий, создающих устойчивое протекание процесса сварки, а именно: стабильное горение сварочной дуги, получение сварных швов необходимых размеров, формы и качества. Режим сварки складывается из ряда параметров. Параметры режима сварки подразделяют на основные и дополнительные. К основным параметрам режима сварки при ручной дуговой сварке относят величину, род и полярность тока, диаметр электрода, напряжение, скорость сварки и величину поперечного колебания конца электрода, а к дополнительным — величину вылета электрода, состав и толщину покрытия электрода, начальную температуру основного металла, положение электрода в пространстве (вертикальное, наклонное) и положение изделия в процессе сварки.
Выбор диаметра электрода. Диаметр электрода выбирают в зависимости от толщины свариваемого металла; марки свариваемого металла; формы разделки кромок и номера выполненного валика-шва; положения, в котором выполняется сварка; вида соединения.
Величина, род и полярность тока. С увеличением сварочного тока глубина провара увеличивается, ширина шва почти не меняется. Род и полярность тока также влияют на форму и размеры шва. При сварке постоянным током обратной полярности глубина провара на 40-50% больше, чем при сварке постоянным током прямой полярности, что объясняется различным количеством теплоты, выделяющейся на аноде и катоде. Поэтому обратная полярность применяется при сварке тонкого металла с целью исключения прожога и при сварке высоколегированных сталей с целью исключения их перегрева. При сварке переменным током глубина провара на 15—20% меньше, чем при сварке постоянным током обратной полярности.
Род и полярность тока выбирают по типу электродного покрытия, марке свариваемого металла, толщине свариваемого металла.
Напряжение на дуге изменяется пропорционально длине дуги. При увеличении длины дуги возрастает ее напряжение и поэтому увеличивается доля тепла, идущая на плавление электрода и основного металла. В результате этого ширина сварного шва увеличивается, а глубина провара и высота усиления уменьшаются. Напряжение на дуге зависит от величины тока и диаметра электрода. Оно обычно бывает 18-40 В.
С увеличением скорости сварки ширина сварного шва уменьшается, наряду с этим глубина провара увеличивается, что является следствием того, что жидкий металл не успевает подтекать под дугу и толщина его прослойки мала. При дальнейшем увеличении скорости сварки время теплового действия дуги на металл и глубина провара уменьшается, а при значительной скорости сварки будет даже образовываться несплавление основного металла с металлом шва.
Наклон электрода. Ручную дуговую сварку можно выполнять вертикальным электродом, углом вперед и углом назад. В виду того что столб дуги стремится сохранить направление оси электрода, то в каждом из этих случаев форма сварочной ванны и, следовательно, форма шва будет различной. При сварке углом вперед, как правило, жидкий металл подтекает под дугу, поэтому глубина провара и высота усиления уменьшаются, а ширина шва увеличивается. При сварке углом назад жидкий металл давлением дуги вытесняется из-под нее, поэтому глубина провара и высота усиления увеличиваются.
Наклон изделия. В зависимости от расположения соединений на изделии или от наклона изделия ручная дуговая сварка может быть выполнена на горизонтальной плоскости, на подъем и спуск. Влияние наклона изделия и пространственного расположения соединений на изделии на форму шва примерно такое, что и влияние наклона электрода. При сварке на подъем расплавленный металл под действием собственного веса вытекает из-под дуги, в результате чего увеличиваются глубина проплавления и высота усиления, а ширина шва уменьшается. При сварке на спуск жидкий металл подтекает под дугу, что уменьшает глубину проплавления и увеличивает ширину шва.
Предварительный подогрев и последующую термическую обработку выполняют в случаях, когда металл склонен к образованию закалочных структур.
studfiles.net