Самодельный станок для изготовления – Делаем сами самодельные станки своими руками
alexxlab | 28.07.2018 | 0 | Вопросы и ответы
Самодельные приспособления для мастерской своими руками: домашний фрезерный станок
Дрель электрическая — это компактная, лёгкая, простая в эксплуатации и транспортировке машина. Она незаменима в домашней мастерской, в гараже и на стройке. Кроме сверлильных операций, её можно приспособить для выполнения токарных, фрезерных, шлифовальных и других работ. Многие умельцы на базе дрели создают самодельные станки и приспособления для домашней мастерской. Их используют в гараже для простых токарных работ по дереву и металлу.
Содержание материала
Оборудование мастерской
Не всегда с помощью ручной дрели можно просверлить точное отверстие. Если возникла такая необходимость, применяют стационарный сверлильный станок. Он, безусловно, точный и безопасный, что и нужно при обработке твёрдых элементов сверлом большого диаметра.
В гараже или мастерской редко встретишь такой станок в основном из-за цены, он дорогой, кроме того, громоздкий, занимает много места, используется редко. Дрель на штативе — лёгкая, удобная в транспортировке конструкция, при этом выполнит все требования, предъявляемые к настольному сверлильному станку.
Также рекомендуем прочитать:
Стационарное сверлильное устройство
Самодельный станок на базе дрели обеспечит высокую точность сверления в любых условиях — устанавливается на столешницу верстака или на полу. Он состоит из нескольких элементов. Главными, конечно, являются основание и колонна. Первая деталь отвечает за стабильность машины, установленной на ровной поверхности. Вторая, в свою очередь, позволяет плавно и очень точно перемещать дрель вверх и вниз при бурении.
Стальная колонна не деформируется даже под воздействием наибольшего давления, чтобы обеспечить перпендикулярность сверления. Помимо высокой точности, стоит упомянуть о безопасности работы. Если надёжно закрепить заготовку в тисках на рабочем столе, то во время сверления не возникнет риска травмы.
Настольный станок на базе дрели обеспечивает точное сверление отверстий в деталях сложных форм, например, круглых, овальных, а также под углом в 90 градусов. Без него не обойтись домашнему мастеру, где инструмент не используется интенсивно. Для изготовления настольного вертикально-сверлильного станка на базе дрели можно использовать готовые стойки или штативы. Они вполне пригодные для применения.
Как гарантирует производитель, стойка для вертикального бурения пригодится везде, где существует необходимость выполнения сверлильных операций при ремонте металлических конструкций, деревянных деталей. Изделие изготовлено из качественных материалов, обеспечивает стабильность и надёжность крепления, благодаря чему качество работы хорошее. Продукт этого типа отлично сокращает время на работу.
В частных гаражах можно встретить самодельные станки, где в качестве стойки для дрели приспособлены штативы от фотоувеличителей и кодоскопов, домкраты и автомобильные рулевые рейки подходящей конструкции. Есть станки, изготовленные полностью из дерева. Дрель представляет собой универсальный механизм, при помощи которого можно конструировать самодельные станки по дереву.
Деревообрабатывающий станок
Используя дрель в качестве электрического привода, можно собрать самодельные станки и приспособления для гаража. Например, токарный станок по дереву за несколько дней из доски и горсти шурупов. Чертежей для изготовления станков никто не делает, всё создаётся по придуманному проекту.
Начать нужно с поиска подходящей доски для основания, на котором будет крепиться передняя бабка с отверстием под шейку дрели.
- Затем сделать заднюю бабку. Для этого к бруску, который будет скользить по станине, прикрепить стойку для центра задней бабки. В стойке сделать гнездо под подшипник. По диаметру внутреннего кольца подшипника из болта выточить центр, запрессовать в подшипник.
- Задняя бабка имеет прорезь, а в станине установлена шпилька, на которую надевается бабка и фиксируется гайкой с барашком. В патрон дрели зажимается трезубец, на который одним концом крепится заготовка, другой поджимается центром задней бабки. Простой, рабочий станок по дереву для домашней мастерской готов.
Кроме самодельного сверлильного и токарного оборудования домашней мастерской, своими руками можно сделать фрезерный станок по дереву. Для привода можно выбрать электродрель или ручной фрезер.
Станина для болгарки
Болгарка, как и электродрель, стремительно вошла в нашу жизнь и заняла место универсального инструмента. С её помощью можно резать трубы, листовой металл и прутки, камень и плитку, шлифовать и полировать. Широкое применение она нашла в автосервисе при ремонте кузовов машин. Для удобства в работе можно сделать отрезной станок.
Чтобы было дешевле и проще, делают его из дерева. Как и в каждом станке делается основание, материалом может быть древесно-стружечная плита размером 400 х 400 х 20 миллиметров. Снизу к плите шурупами присоединить ножки в виде двух реек 40 х 40 миллиметров. Сверху к плите прикрепить брусок высотой 100 миллиметров, толщиной 50 миллиметров. К бруску шурупами крепится дверная петля с длинной пластиной. К пластине крепится болгарка при помощи хомута. Все, самодельное приспособление для домашней мастерской, выполняющее роль отрезного станка готово. Для безопасной работы на основание устанавливают машинные тиски.
Точило для гаража
Наждак, электроточило, станок заточной — так называют инструмент, без которого не обходится мастерская, частный гараж, автосервис. Точило самое нужное приспособление при ремонте автомобилей, изготовлении слесарных изделий, заточке инструмента, шлифовке металлической поверхности поделок. Необязательно покупать этот полезный механизм, вполне можно обойтись самоделкой на базе электродрели. Для начала необходимо выбрать место на столе и при помощи двух деревянных скоб толщиной 40 миллиметров и двух шурупов закрепить дрель.
Для упора руки или инструмента надо сделать подручник. Для этого можно применить толстослойную фанеру толщиной 20 миллиметров. Крепится подручник к столу, выставляется под наждачным кругом. Для того чтобы стружка свободно падала на пол и была возможность использовать наждачные круги разного диаметра в подручнике вырезается прямоугольное отверстие шириной чуть больше толщины абразивного инструмента. Для регулировки подручника на разную высоту необходимо установить набор пластин из фанеры, и закрепить шурупами. Верхнюю плоскость подручника закрыть стальной пластиной. Всё, полезный электроинструмент для дома готов к эксплуатации.
Фрезерные машины
Среди специалистов по деревообработке бытует мнение, что фрезер самый необходимый инструмент для столярной мастерской. Он может даже заменить некоторые электроинструменты, например, циркулярную пилу, дрель и даже фуганок. Существует два основных вида фрезеров:
- погружные;
- кромочные.
Погружной работает следующим образом: фреза погружается в материал и движется по заданному контуру. Кромочный не позволяет погружать фрезу, у него глубина фрезерования выставляется заранее и фиксируется. По мощности фрезеры делятся на три категории:
- малый от 500 до 1200 ватт;
- средний от 1100 до 1900 ватт;
- мощный от 1900 до 2400 ватт.
Фрезеры малой мощности лёгкие, компактные, манёвренные, удобные в эксплуатации и позволяют выполнять все задачи домашней мастерской — это лучший выбор для дома. Правда, малая мощность накладывает свои ограничения. Устройство работает с фрезами диаметром до 32 миллиметров, есть ограничения по длине. Если предстоит изготовлять шкатулки, рамки, этой машины вполне достаточно.
Используя электродрель или фрезер можно изготовить полезное приспособление для электроинструмента своими руками — фрезерный стол. Такое приспособление пригодится, если придётся изготавливать профильные изделия из дерева. Для этих целей можно приспособить обыкновенный стол, усилив столешницу листовым металлом толщиной два миллиметра.
Под столом к столешнице крепится фрезер. На столе устанавливается упорная доска, которая двигается под установленный размер и фиксируется прижимными болтами. Механизм подачи фрезы — лифт, изготавливается из обычного автомобильного домкрата, который устанавливается на металлических кронштейнах под столом. Готовая самоделка радует глаз.
Меняя фрезы можно выполнять различные фрезерные работы. В целом устройство представляет собой профессиональный фрезерный станок по дереву для домашней мастерской. На нём удобно выбирать пазы, фрезеровать четверть на рамках, обрабатывать конфигурацию плинтусов.
Электродрель, болгарка, ручной фрезер — инструменты, на базе которых можно создавать приспособления и многофункциональные станки, значительно облегчающие работу домашнего мастера.
pochini.guru
Самодельные станки | Мастер-класс своими руками
Бормашинка и ручная дрель
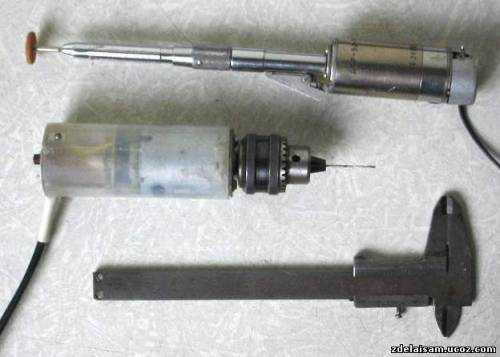
Бормашинка – двигатель ДПР-52, встречается в принтерах и фенах. Ручная дрель – двигатель от автомобильного компрессора, встречается в небольших тепловых пушках и фенах.
Бормашина 2
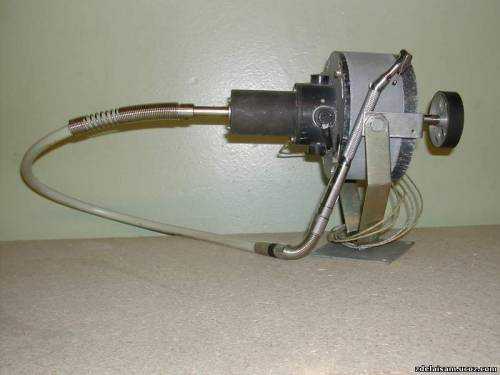
Бормашина со сменными наконечниками. Мотор PIV MTM, из лентопротяги вертикального магнитофона, болгарский. Таходатчик удален, на его месте закреплен гибкий вал бормашины. Вращение от оси мотора перадается на вал с помощью туго надетой пружины. Справа на оси укреплен алмазный диск для правки боров.Весь механизм закреплен в держателе с двумя степенями свободы и легко вращается влево-вправо, вперед-назад. Вся конструкция подвешена на рабочем столе справа вверху, не мешает работе. Можно утопить мотор в стол так, чтобы шланг бормашины выходил вертикально вверх.
Бормашина для гравировки
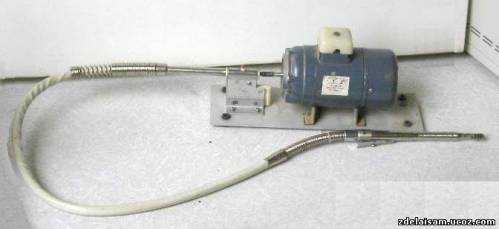
Бормашина для граверных работ. Мотор на 8000 об., шланг терпит до 10000. Мотор и шланг соединены пружиной, надетой на оси.
Дрель 1
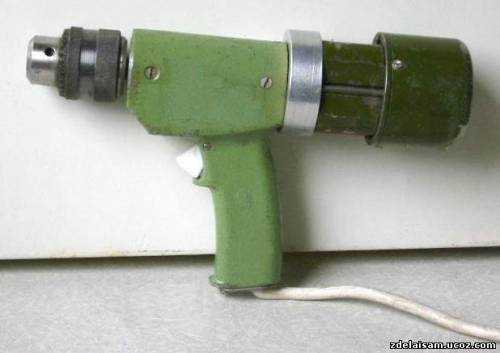
Рукоять с механизмом от пневмодрели. Мотор передает вращение на турбину, насажен через переходное кольцо. В корпусе дрели уже находится планетарный редуктор примерно 3:1. Очень мощная машинка. Потребовались токарные работы: переходное кольцо, втулка на валу, подгонка конуса Морзе под размер 2а. Трудно было установить сильнотоковую кнопку.
Дрель 2
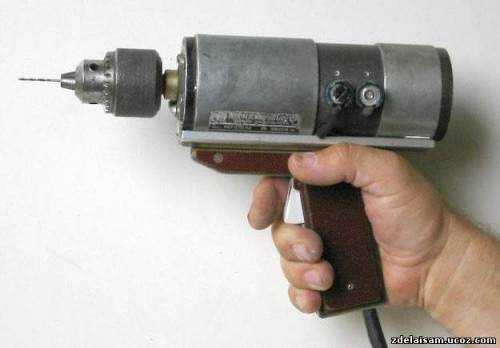
Мотор PIV 6 25/3A болгарского прозводства, работает от 5 до 40 В, от вертикального магнитофона/накопителя. Таходатчик (сзади) не используется, но хорошо уравновешивает всю конструкцию. Кнопка воздействует на контактную группу от утюга, мощная и не обгорает.
Отрезной станок 1
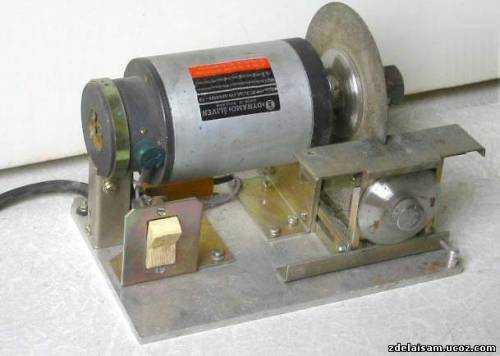
Отрезной станок 1 сделан под неармированные абразивные диски толщиной 0,5-2 мм. Перемещаемый столик. Виден “тормозной” резистор.
Отрезной станок 2
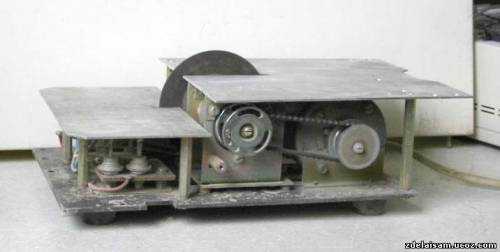
Отрезной станок 2 сделан под неармированные абразивные диски толщиной 0,5-2 мм. Два рабочих положения, с верхнего и нижнего столиков, так что мотор с реверсом. Отрезаю платы, делаю ключи, вырезаю каркасы для трансформаторов.
Сверлильный станок 1
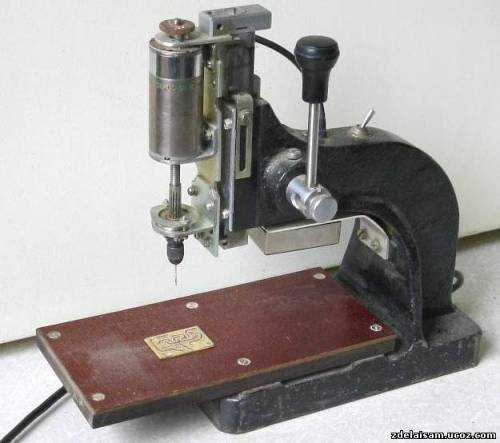
Сверлильный станочек с цанговым патроном на 0,8 мм. Сделан из остатков механизма, который назывался “пресс для изготовления аллюминиевых бирок”. Двигатель ДПР-52, ось я удлинил только для красоты всей конструкции. Ход сверла – 20 мм. Видна коробка для сверл и абразивный диск на оси движка вверху для правки сверл.
Свелильный станок 2
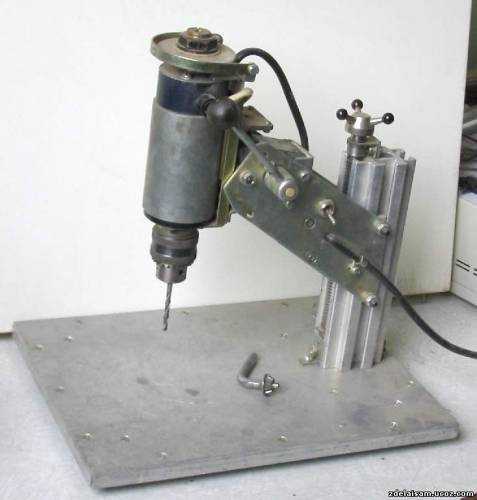
Свелильный станок под патрон 2а. Стойка из аллюминиевого профиля в нем червячная передача, с ее помощью каретка на подшипниках перемещается на 80 мм под сверла разной длины. Ручкой перещается собственно мотор еще на 20 мм. Вверху на оси мотора – абразивный диск для доводки сверл, защищен рамкой. Мотор болгарский, от магнитофона, профиль от витрины, червяк от водопроводного вентиля, подшипники от выдвижного столика.
Свелильный станок 3

Просто красивый станочек получился. Основа – рамка для линейного перемещения головок 8-дюймового накопителя. На шести подшипниках. Патрон закреплен в втулке от вентилятора этого же накопителя. Червячная передача – от 5-дюймового флоппика, круглая ручка вверху. Последние 20 мм хода сверла – отдельной ручкой. Передача с мотора – резиновый пассик, но лучше плоский ремень. Мотор поставлю посильнее.
Свелильный станок 4
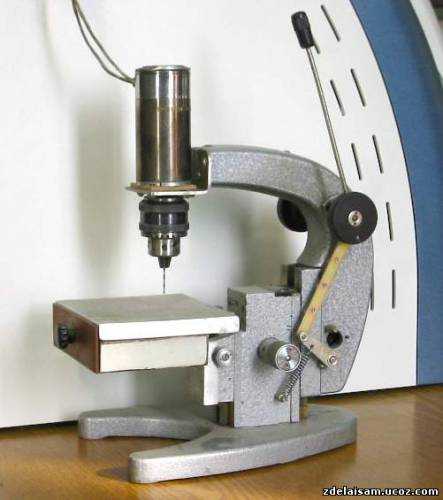
Сверлилка из микроскопа. Один винт перемещает столик под сверла разной длины, второй был поврежден, поэтому на нем сделан ход на последние 20 мм, видны тяги, пружина и ручка. Двигатель ДПР-74. Под столиком ящик для сверл.
Токарный станок
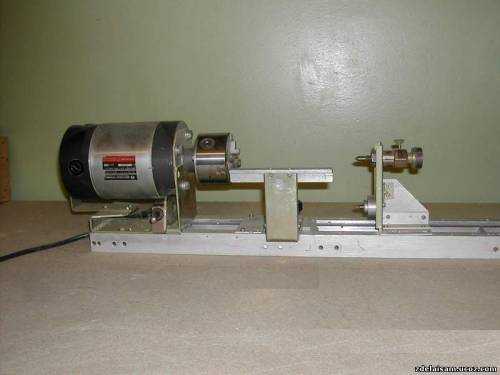
Токарный станок для дерева. Мотор ПИК 12-3/10.1 от болгарского магнитофона/ накопителя. Патрон польский, до 150 мм. Правая бабка с вращающимся центром и подачей на 20 мм. Суппорт фиксируемый, перемещается по горизонтали. Точу на нем ручки для напильников, мелочь вроде солонок, пуговиц. Суппорт получился слабый, вибрирует на твердом дереве, буду переделывать.
Источник: plazon.ru
sdelaysam-svoimirukami.ru
Самодельный станок для скручивания квадрата (32 фото изготовления)
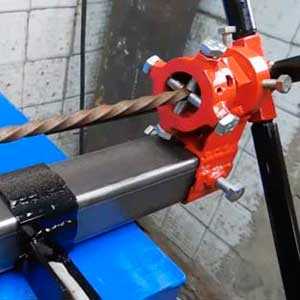
Представляем Вашему вниманию, подробный процесс изготовления самодельного станка для продольного скручивания квадрата.
С помощью такого приспособления, можно скручивать квадрат для самых разнообразных декоративных конструкций.
Материалы:
- Профильная труба.
- Резцы.
- Плашкодержатели.
- Шайба.
- Подшипник.
Подробный фото отчёт по изготовлению станка:
Самодельный станок для холодной ковки готов, можно приступать к испытаниям. Это еще один пример того, как у себя в мастерской без токарно-фрезерных работ можно собрать отличный станок для продольного скручивания квадрата.
Станок уверенно гнёт 8, 10 и 12-ти миллиметровый квадрат.
Также рекомендуем посмотреть видео автора: изготовление станка своими руками.
Популярные самоделки из этой рубрики
Самодельное приспособление из колёс от садовой тач…
Самодельный домкрат своими руками…
Самоделка из старого насоса ГУРа…
Самодельный компрессор своими руками…
Отрезной станок своими руками…
Приспособление для заточки сверл из гайки…
Ямобур своими руками
Сверлильный станок из дрели своими руками…
Отрезной станок сделанный из болгарки…
Насадка на дрель своими руками…
Отрезной станок своими руками…
Стенд для проверки свечей зажигания своими руками…
Загрузка…sam-stroitel.com
Cамодельный станок для изготовления рамок для ульев
Ведение пчеловодческого хозяйства, вне зависимости от его размеров, требует починки старых или производства новых ульев, рамок, переносных ящиков, ловушек для роев. Кто-то выбирает путь постоянных инвестиций или реинвестиций – вкладывает деньги в приобретение перечисленных изделий. Другие проявляют творческий подход – мастерят все своими руками, получая немалое удовольствие от столярных работ.
Самодельный станок для изготовления рамок для ульев, как раз, относится к тому типу оборудования, которое должен иметь в хозяйстве каждый пчеловод-умелец. Конечно, заниматься сборкой подобной самоделки можно только при достаточном владении необходимыми навыками.
Содержание статьи
Специфика работы
Теоретически выпилить заготовки для рамок можно с помощью пилы, оснащенной мелкозубчатым полотном. Некоторые народные умельцы используют электрический лобзик. С его помощью вырезаются отдельные детали. Но все это полумеры.
Деревообрабатывающий станок ощутимо ускоряет и упрощает работу. Рамка изготавливается буквально двумя-тремя выверенными движениями.
Разумеется, скорость вращения дисковой пилы станка требует от домашнего мастера особого внимания к технике безопасности. На филигранной работе необходимо сосредоточиться полностью. Только в этом случае можно рассчитывать на успех в изготовлении и безопасность для своего здоровья.
Возможно вас заинтересует:
Как сделать ульевые рамки
На следующие моменты стоит обратить особое внимание:
- Самодельный станок должен заземляться точно так же, как любая качественная заводская модель этого типа.
- Его габариты подбираются в зависимости от потребностей хозяина. Хорошо известны случаи, когда громоздкий «дедушкин станок из деревни», отлично работающий стационарно, невозможно перевезти на другую пасеку.
Неплохой альтернативой в этом случае будет небольшой бытовой станочек, например, такой, как на этом фото:
Очевидно, что ориентироваться на габариты придется и при изготовлении самоделки, если идет речь об ее свободной транспортировке или перемещении в пределах мастерской.
Примеры самодельных станков
В сети представлено множество вариантов изготовления самодельного станка, предназначенного для производства ульевых рамок. Мастера охотно делятся своими идеями в коротких видео, правда, не предоставляя при этом подробных инструкций по сборке. Зачастую зрителю приходиться полагаться на собственную смекалку и имеющиеся в багаже знания.
Команда vseopaseke.ru сделала небольшую подборку таких видео-обзоров, чтобы вдохновить своих читателей и подать им интересные творческие идеи.
Видео 1
В этом деревообрабатывающем станке используется трехножевой барабан с шириной лезвий в 250 мм. Подающий и принимающий стол сделаны из листовой стали толщиной в 8 мм. В качестве привода используется однофазный двигатель с конденсатором заводской сборки 2,2 кВт на 2 780 оборотов (производство Могилев, Белоруссия). Его можно заказать в интернет-магазине.
Двигатель установлен на стол из листовой стали 8 мм. Привод собран из двух шкивов – 80 и 110 мм, на которые надет ремень генератора КАМАЗа. Запуск осуществляется через магнитный пускатель. Оборудование рассчитано на производство соторамок и ульев.
Видео 2
А в этом варианте мастер сделал дополнительный стол из морской фанеры, устойчивой к влаге и нагрузкам, который закрывает фуганок. Приобрести фанеру можно в организациях, занимающихся ремонтом лодок.
Имеется удобное в эксплуатации приспособление для нарезания планок, брусков.
Видео 3
Ниже представлен простой строгально-пиловочный станок, станина которого собрана из уголка 40 на 40 мм. Для ее изготовления требуется:
- 4 уголка длиной 450 мм;
- 9 уголков длиной 550 мм;
- 2 уголка длиной 270 мм;
- шпильки М12;
- гайки;
- шайбы;
- барабан, приобретенный на барахолке;
- ножи, купленные в хозяйственном магазине, длиной в 200 мм;
- 2 планки под электродвигатель;
- 2 строгальных стола длиной в 300 и шириной в 220 мм;
- 1 пиловочный стол длиной 600 мм и шириной 220-230 мм.
На заметку: Столы могут быть не только железными, но и деревянными, текстолитовыми.
Порядок сборки смотрите в предложенном автором видео:
Недостатки конструкции: станок нерегулируемый, а длительная работа агрегата может привести к ослаблению гаек станины. Несомненные достоинства: дешевизна и простота.
Видео 4
А это многофункциональный и очень компактный станок, оснащенный строгальным столом с перепадом между принимающей и подающей стороной в 6 мм. Длина стола рассчитана таким образом, что по ней при обработке можно свободно отмерить треть боковой планки. Сверление отверстий под проволоку производится с использованием специального шаблона.
В заключение
Вот такие интересные решения предлагают народные умельцы для самодельных станков, рассчитанных на изготовление рамок и ульев. Какую творческую идею реализовать, зависит только от вас.
В зависимости от модели для изготовления отдельных деталей станка понадобится фрезерное, токарное, сварочное оборудование. Либо придется обратиться за помощью к соответствующим специалистам.
Альтернатива самоделкам – «Мастер-Универсал» 2500Е от компании «Белмаш». Это универсальный станок для обработки дерева, обладающий функцией сверления, распиловки, строгания и фрезерования пальчиковой или дисковой фрезой. В качестве привода используется асинхронный электродвигатель мощностью в 2,5 киловатта, без проблем подключающийся к бытовой электросети. Для установки станка требуется рабочий стол.
vseopaseke.ru
Самодельные станки и приспособления для домашней мастерской
Содержание статьи:
Для работы по дому или в гараже необходимы профессиональные инструменты. Но в некоторых случаях целесообразнее сделать оборудование своими руками. За основу можно взять заводские модели, адаптированные для выполнения конкретного типа работ в мастерской.
Станки для обработки металлов
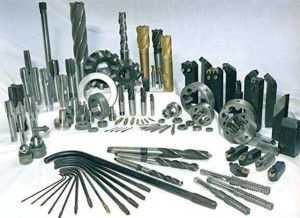
Ручной инструмент для обработки металлических изделий
Самыми востребованными являются станки и оборудование для обработки металлических изделий. Они применяются не только для изготовления и ремонта, но и во время обслуживания другого инструмента.
Помимо ручных приспособлений для комплектации ремонтной базы частного гаража или мастерской понадобятся мини-станки различных типов, сделанные своими руками. Речь идет не о профессиональном заводском оборудовании, а о его аналоге меньшей производительности. Однако несмотря на это она должна обладать оптимальным набором функций для осуществления всех типов работ.
Точильное оборудование
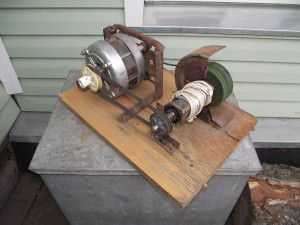
Самодельный точильный станок
Станком первой необходимости считается точильное оборудование. Оно предназначено для обработки металлических поверхностей — заточка, шлифовка, полировка.
Для его изготовления своими руками потребуется минимум инструментов и комплектующих. Конструкция состоит из силового агрегата (электродвигатель) и точильных камней. Оптимальным вариантом станка является наличие двухстороннего вала. Это позволит установить два точильных круга для различных типов обработки.
Комплектующие для изготовления мини-оборудования для гаража:
- электродвигатель мощностью от 0,8 до 1,5 кВт. Оптимальная частота оборотов — 800 об/мин;
- основание. Это может быть заводская станина или изготовленная самостоятельно. Важно чтобы она обеспечила устойчивость конструкции;
- блок крепления наждака. Заточные круги могут быть установлены на вал двигателя или в отдельном блоке.
Важно правильно подобрать виды наждака и другие приспособления. Для заточки инструментов, изготовленных из специальных сортов стали, чаще всего применяют корундовые или алмазные круги.
Для устойчивости самодельная конструкция должна иметь монтажные элементы, с помощью которых заточной станок будет крепиться на рабочий стол.
Фрезерный (сверлильный) станок по металлу
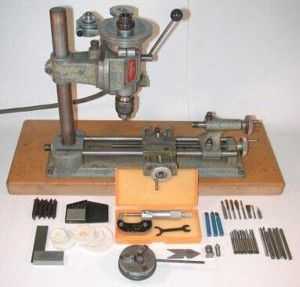
Фрезерный станок
Другой разновидностью работы является сверление отверстий на поверхности металлических изделий. Для выполнения потребуется фрезерный станок. За основу можно взять чертеж заводской модели, которую в дальнейшем адаптируют для изготовления своими руками в мастерской.
Так как приспособление будет выполнять ряд определенных функций — рекомендуется продумать компоновку инструмента. Чаще всего в качестве силового агрегата выбирают электродрель. Она устанавливается на съемный монтажный элемент и в случае надобности может быть оперативно демонтирована для выполнения других работ.
Рекомендации по изготовлению самодельного фрезерного станка своими руками:
- в качестве подъемного механизма можно использовать рулевую рейку. Согласно его размерам рассчитываются остальные компоненты оборудования;
- для увеличения функциональности делают координатный стол. После закрепления на нем детали он сможет смещаться относительно режущей части;
- дополнительно можно установить механизм углового фрезерного сверления.
Если потребуется сверление с помощью вышеописанного станка заготовок большой толщины — лучше всего использовать мощный электродвигатель вместо дрели. Тогда обязательно устанавливается блок передачи крутящего момента.
Некоторые производители предлагают фрезерный стол с опорной стойкой, специально предназначенные для монтажа дрели.
Самодельные станки по дереву
Самодельный токарный станок по дереву
Для работы по дереву необходимы три типа станков: отрезной, шлифовальный и токарный. При их наличии можно осуществлять все типы работ в домашних условиях. Однако следует учитывать конструктивные отличия, характерные для каждого типа оборудования.
Перед выбором оптимальной модели следует определиться с видом выполняемых работ. На параметры будущей конструкции оказывают влияние размеры заготовки, необходимая степень ее обработки, породы древесины. Оптимальным вариантом инструмента будет изготовление универсального инструмента своими руками исходя из выполненного анализа и габаритов места в мастерской.
Отрезные станки по дереву
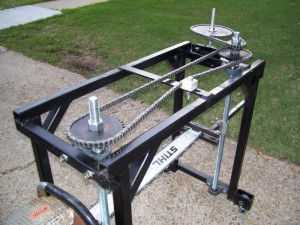
Самодельная пилорама из бензопилы
Самая простая модель мини-отрезного оборудования для обработки древесины — электро или бензопила. С ее помощью можно делать резы различной точности и конфигурации. Однако из-за относительно больших физических нагрузок время работы будет ограничено. Поэтому для обработки больших объемов древесины рекомендуется делать пилорамы своими руками.
Подобные станки могут быть нескольких видов:
- дисковая. Самый простой вариант приспособления, состоящий из опорного стола, режущего диска и силовой установки. Может применяться для реза листовых материалов, брусков и досок;
- пилорама из бензопилы. Предназначена для обработки стволов. Применяется для формирования досок и брусьев. Отличаются относительно небольшой сложностью изготовления;
- ленточная пилорама. Имеет те же функции, что и конструкции из бензопилы. Различие заключается в скорости обработки бревна.
Для фигурного реза можно использовать электролобзики. Однако изготовить этот инструмент своими руками будет проблематично.
При изготовлении самодельной пилорамы необходимо учитывать максимальный размер бревна — диаметр ствола и его длину. Исходя из этого рассчитывается оптимальный размер и характеристики приспособления.
Шлифовальное оборудование для обработки дерева
Самодельный шлифовальный станок по дереву
Для шлифовки дерева можно применять станки, сделанные своими руками, аналогичные устройствам для обработки металлов. Разница будет заключаться в абразивном материале, а также площади обработки.
Самая простая модель приспособления состоит из рабочего стола, двигателя и вертикального шлифовального вала. Последний может иметь лезвие либо монтажные элементы для установки абразивной ленты. С помощью этого оборудования можно обрабатывать торцевые края деревянных заготовок, выполнять их шлифовку.
В видеоматериале показан оптимальный набор инструментов для работы по дому своими руками:
Примеры чертежей станков
stanokgid.ru
Как сделать самодельный станок для изготовления воблеров. ВИДЕО.
Как сделать самодельный станок для изготовления воблеров своими руками? Одной из лучших искусственных приманок, которые используют при ловле спиннингом хищника, является воблер – приманка своим видом и игрой имитирующая естественную добычу хищной рыбы. Это главное и первостепенное преимущество воблера перед другими используемыми приманками. Его разная степень плавучести позволяет вести успешный лов рыбы на различных глубинах.
Его широкое распостранение способствовало росту изготовлению самодельных приманок рыбаками. Рыбаки начали заниматься воблеростроением. Да, можно купить воблер в магазине, но куда приятнее выловить хищника на приманку изготовленную своими руками!!! Материалом для изготовления – дерево, пластик, пенопласт… Выбор огромен. Лучше всего обрабатывается дерево, но требуется выбирать древесину плотную и в тоже время легкую, легко поддающуюся обработке. Воблер можно изготовить из ореха, ольхи, липы… Но руками обрабатывать трудно, малейшая ошибка и … и все начинаем вновь. Многие из рыбаков изготавливают самодельные станки для своих нужд.
В одном из постов я публиковал видео о работе самодельного станка по изготовлению воблеров. На данной странице приведены чертежи изготовления станочка ав тором которого является Сергей Ронжин.
ИНСТРУКЦИЯ
по изготовлению и сборке.
Чертежи, эскизы и Инструкцию составил Сергей Ронжин.
Инструменты и комплектующие.
1.Подшипник шариковый №200 (размер 10х30х9мм.) – 5 шт.
2.Дисковая пила: 22х125х2 (или аналог) – 1 шт.
3. Маленькая болгарка
4. Гайки М10х1 под ключ на 17 – 20 шт.
5. Болты М4 разных длин, гайки М4
6. Сверла диаметрами: 4 мм, 4,5мм, 10,1мм и др.
7. Сверло перьевое на диаметр 30мм.
8. Винты-саморезы разных длин диаметром 5 мм.
9. Уголок 20х20х4 мм. сталь.
10. Круг (пруток) стальной (но не проволока, Сталь10 или аналог) диаметром 10мм.
11. Полоска 20х3 или 20х4мм.
12. Уголок дюрал. 10х10х1,5мм.
13. Шестигранник на 17.
14. Круг диаметром 13мм. ( можно использовать любой металл соответствующего диаметра для изготовления деталей)
15. Круг стальной (латунь, бронза) диаметром 5 мм.
16. Велосипедные спицы для штифтов.
17. Резина средней твердости для фрикционных прокладок.
18. Самозажимной патрон для дрели (в расчете принят с внутренней глубиной погружения оси
равной 35мм. и максимального диаметра не менее 10мм)
Изготовление боковых стенок и средней опоры.
Шаг 1.
Изготовление Дет. №1 – боковые стенки.
Количество – 2 шт.
Материал – фанера толщиной 12 мм. (Примечание: тоньше фанеру брать не рекомендую;
если будет толще, то необходимо ввести корректировки по размерам в соответствующие детали).
Особое внимание необходимо уделить соблюдение прямых углов 90 град. по плоскостям А и Б
После выпиливания двух Дет. №1 их накладывают друг на друга и выравнивают по плоскостям А и Б, скрепляют двумя струбцинами. Для этого лучше использовать уголок в качестве упора. Далее на верхней детали размечают отверстия Отв.№3 – 4 шт., накернивают (в дальнейшем после разметки все места под сверление накернить ОБЯЗАТЕЛЬНО на любых деталях) и просверливают сверлом диаметром 4мм.
Шаг 2.
Изготовление Дет.№2 – средняя опора.
Количество – 1 шт.
Материал – фанера толщиной 12 мм.
Особое внимание необходимо уделить соблюдение прямых углов 90 град. по плоскостям А и Б
После выпиливания на Дет.№2 накладывают Дет.№1, выравнивают их по плоскостям А и Б, скрепляют двумя струбцинами, просверливают Отв.№3 – 2шт.
Шаг 3.
По Отв. №3 с помощью болтов и гаек М4 скрепляют Дет.№1 + Дет.№2 + Дет.№1. На верхней Дет.№1 размечают Отв.№1 и Отв.№2 и просверливают сверлом диаметром 4мм.
Шаг 4.
Изготовление Дет.№3 – крышка подшипника.
Количество – 6 шт.
Материал – металл (сталь, дюраль, латунь) толщиной 1-1,5мм.
Размечают Отв.№1 и 4 Отв.№2, просверливают сверлом диаметром 4мм.
Шаг 5.
На Дет.№1 на Отв.№1 и Отв.№2, поочередно, накладывают Дет.№3, центруют по Отв.№1, вставляют в сцентрованные отверстия болт М4, и через Отв.№2 Дет.№3 сверлом диаметром 4мм просверливают 4 отверстия вокруг Отв.№1 и Отв.№2 Дет.№1 насквозь через все ТРИ скрепленные детали. Убирают Дет.№3.
Шаг 6.
Собранные вместе детали № 1 и 2 разбирают и болтами соединяют ДВЕ Дет.№1. Берут ПЕРЬЕВОЕ сверло на диаметр 30мм и рассверливают на проход в обеих деталях Отв.№ 1 и 2.
Шаг 7.
В Дет.№2 Перьевым сверлом диаметром 30мм рассверливают Отв.№1 ( не перепутать).
Отв.№2 рассверливают сверлом диаметром 10,1мм (если такого сверла нет, то применяют сверло диаметром 10мм и при сборке круглым напильником в отверстии делают минимальный зазор для
Свободного вращения приводного вала.
Изготовление рамки.
Шаг 1. Нарезают уголок 20х20х4мм. соответствующих длин (см. Чертеж №3 Дет.№4). Распил делают под углом 45 град. Складывают их в прямоугольник на ровной поверхности и соединяют при помощи сварки с соблюдением углов 90 град. и «плоскости» поверхности.
Шаг 2. Размечают по центрам отверстия под приводной вал и сверлят отверстия сверлами 4мм, затем 10,1мм. По размеру болгарки изготавливают хомут. Перед загибом на обеих концах нарезают рему М4. Размечают отверстия под хомут на рамке и сверлят сверлом 4,5мм.
Шаг 3. Ходовую гайку (Чертеж №4) с одной грани обтачивают, чтобы центр резьбового отверстия гайки и центр отверстия на рамке совпадали ПОЛНОСТЬЮ. Вставляют в рамку ходовой вал, надев на него отрезок любой трубки длиной около 200мм.(для защиты резьбы от попадания сварки). Накручивают обточенную ходовую гайку, выступивший конец вставляют в отверстие рамки, на выступивший конец накручивают гайку под ключ №17 с резьбой М10х1 и стягивают гайку и ходовую гайку, зажимая уголок рамки (для центровки). Далее приваривают ходовую гайку к рамке
( массовый провод присоединять к рамке, а не к ходовому валу), дают остыть, расконтряют гаку, скручивают и выкручивают ходовой вал из ходовой гайки. Вал должен ЛЕГКО вращаться в ходовой гайке и в отверстии диаметром 10,1мм. Если будут затирания из-за «увода», то отверстие надо НЕ ЗНАЧИТЕЛЬНО расширить.
Шаг 4. Выпиливают из полоски 20х3 кронштейн крепления болгарки, сверлят соответствующие отверстия и по установочному размеру 33мм. и 65мм.приваривают его к рамке.
Шаг 5. Выпиливают стойку, сверлят отверстие, приваривают к рамке.
Шаг 6. Выпиливают копир из дурал. Уголка 10х10х1,5. Размечают и сверлят отверстие для крепления диаметром 4мм. Крепят болтом с гайкой М4 копир к стойке с соблюдением прямого угла между копиром и стойкой. На примыкающей стороне копира острой чертилкой отмечают край стойки.
Снимают копир и по линии (приклепывают, присоединяют, приклеивают) текстолитовую пластинку 10х20х3мм, которая играет роль УПОРА и будет предотвращать вертикальное перемещение кончика копира.
Изготовление деталей.
1. Выпиливают основание станка из фанеры толщ.12мм. (Чертеж №5). Размечают на нем места расположения боковых стенок и средней опоры. Просверливают в основании сверлом 2мм. отверстия в основании и нижней части стенок и опоры. Затем отверстия в опоре рассверливают сверлом диаметром 4мм. под саморезы 5мм. Производят ПОДсборку станка.
2. Выпиливают из фанеры 12мм. шкивы 1 и 2. Передача вращательного момента будет осуществляться с помощь приводного ремня, изготовленного из кольцевого отрезка автокамеры.
На шкиве 1 прикрепляют рукоятку для вращения. Вращение для ПОДАЧИ будет производится: при виде спереди – «от себя»; при виде со стороны шкивов – «против часовой стрелки».
При данных размерах шкивов и шаге резьбы ходового вала 1мм. при ОДНОМ обороте приводного шкива заготовка будет совершать ДВА оборота, а режущий инструмент будет смещаться на 1мм., т.е. на 1 оборот заготовки режущий инструмент сместится на 0,5мм. Если соприкасающаяся с «оригиналом» часть копира будет большой толщины то копирование малорельефных мест будет не эффективно.
Размеры заготовки надо брать с минимальными допусками на обработку, т.к. толщина снимаемого материала зависит от высоты зуба пильного диска. Если толщина будет превышать высоту зуба, то перемещение пильного диска будет затруднено, т.к.он будет упираться в заготовку
поверхностью, где нет плоскости резания.
3.Изготавливают детали по Черт. 6,7,8,9. Особое внимание обратить на нарезание резьбы на всех
Валах. Она должна производится на токарных станках, т.к. при нарезке «в ручную» возможен наклон резьбы и, как следствие, биение, заклинивание, вращение по «эллипсу».
СБОРКА.
1. Вкручивают ВАЛ 1 коротким резьбовым концом в соединительную гайку (до упора). С другого конца в гайку вкручивают вал привода. Маркируют места соединения валов и гайки. Сверлят отверстия для штифтов. Разбирают.
2. В крышках (Черт.1 Дет.3) рассверливают центральное отверстие до диаметра 14мм.
3. Берут левую боковую стенку. Собирают УЗЕЛ 1:
– у стопорных шайб отгибают «усики» шириной 6мм. и в шкиве сверлят под них отверстия для предотвращения проворачивания шкива;
– накручивают на ВАЛ 1 соединительную гайку, вставляют штифт;
– ставят на вал распорную втулку, крышку, напрессовывают подшипник, запрессовывают подшипник в боковую стенку, смазывают подшипник, ставят на вал распорную втулку, упорное кольцо, крышку и при помощи болтов и гаек М4 соединяют крышки и боковую стенку;
– накручивают на вал до упора гайку, отгибают у стопорной шайбы широкие « усики» размером 18 мм., чтобы между ними было расстояние 17мм под гаку, ставят стопорную шайбу тонкими «усиками» к шкиву, совмещают с просверленными в шкиве отверстиями, ставят с другой стороны шкива стопорную шайбу «усиками» в отверстия, закручивают гайку М10 до упора, контрят другой гайкой, на грани отгибают широкие «усики».
4. Собирают УЗЕЛ 2 аналогично.
5. Собирают УЗЕЛ 3 на средней опоре.
6. Собирают УЗЕЛ 4 и УЗЕЛ 5 на правой боко
masteraru.ru
Самодельные станки своими руками: комплектующие материалы
Если человек часто сталкивается с тем, что ему необходимо что-либо изготовить из дерева, просто любит этим заниматься или производит вещи на заказ, то ему просто необходим станок. Приобретать такие вещи не только дорого, но они еще и не всегда они подходят по размерам, могут быть неудобными или не вписываться в дизайн. А вот самодельный станок своими руками, сделанный по нужным размерам, идеально впишется в пространство комнаты и всегда будет удобным.
Двигатель
Если было принято решение об изготовлении этого прибора своими силами, то тут важно правильно подобрать комплектующие. К примеру, для того чтобы сконструировать фрезерный станок по дереву, обязательно понадобится электродвигатель. Эта деталь может быть нескольких типов.
Первый тип двигателя, который может быть использован при изготовлении станка своими руками, – это асинхронный. Преимущество заключается в том, что он не требует обслуживания, а также позволит работать с более крупной фрезой. Из недостатков можно выделить большое количество шума, которое издает двигатель при работе. Однако тут уже вопрос чисто индивидуальный.
Коллекторный двигатель. Этот вариант несколько хуже, чем предыдущий, по той причине, что с течением времени и работы детали у нее истираются щетки, которые приходится менять. Чем больше и интенсивнее эксплуатируется двигатель, тем чаще придется менять щетки.
Мощность двигателя
Выбрать тип двигателя для самодельного станка своими руками – это еще не все. Нужно обратить внимание на мощность этого элемента. Это очень важный показатель.
Станки с мощностью до 0,5 кВт лучше всего подходят для поверхностной обработки материала. Стоит добавить, что обрабатывать на таком станке можно будет лишь самые мягкие породы дерева и использовать лишь небольшие режущие инструменты.
Второй тип мощности двигателя для самодельного станка своими руками – это 1,2 кВт. Как показывает практика, этот показатель является наиболее универсальным и востребованным. Этой мощности вполне хватит для глубинной обработки дерева. Для домашнего применения 1,2 кВт вполне хватает.
Последний тип мощности – до 2 кВт. Чаще всего такие станки являются уже полупрофессиональными. Они открывают широкие возможности по обработке дерева, позволяют использоваться практически любые виды фрез, а также обрабатывать некоторые типы пластика и мягкого металла – алюминия.
Число оборотов и питание верстака
Если говорить о количестве оборотов для самодельного станка своими руками, то тут все довольно просто и понятно. Чем выше числовой показатель данной характеристики, тем чище и эффективнее будет конечная обработка детали из дерева. Однако тут есть и еще один небольшой плюс. Если число оборотов достаточно высокое, то такому двигателю становятся не страшны такие дефекты дерева, как сучки. Фреза пройдет их без всяких проблем.
С питанием тоже все довольно просто. Чаще всего выбираются те двигатели, которые питаются от 220/50. Установка и подключение такого типа двигателя не вызывает проблем. Несколько больше трудностей возникает при подключении элементов с трехфазным питанием.
Верстак и рама для агрегата
Изготовленный своими руками станок по дереву обязательно должен иметь такой элемент, как верстак. Выбор его размеров должен основываться на том, с какими деталями придется работать в будущем. Габариты стола, на который все это будет монтироваться, особого значения не имеют.
Рама для станка должна быть подобрана так, чтобы она была не просто очень прочной, но еще и стойко могла переносить динамические нагрузки. Основное отличие собранного своими руками станка по дереву электрического от ручного в том, что само устройство не будет перемещаться, а вот заготовку придется активно двигать. С практической точки зрения применение древесины для рамы станка – это не лучшая идея. Все из-за того, что со временем дерево иссыхает, покрывается трещинами и теряет свою прочность. Наиболее оптимальным вариантом станет металлическая труба, которая имеет квадратный или прямоугольный профиль.
Столешница
При выборе этого элемента все в точности как с рамой, да наоборот. Металл будет не лучшим выбором в качестве исходного материала по двум причинам. Во-первых, столешница получится очень массивной и будет иметь слишком грубый вид. Во-вторых, придется использовать сварку, чтобы все надежно закрепить.
Лучше всего использовать один из следующих трех материалов:
- строганные доски;
- плиты из ДСП, ОСВ;
- многослойную фанеру.
Материал для столешницы должен быть довольно прочным, чтобы выдерживать последующие нагрузки. По этой причине толщину и материал для изготовления этого элемента нужно выбирать, опираясь на то, какие работы будут проводиться в дальнейшем. Еще одна важная деталь – это гладкая поверхность стола. Если не соблюдать эту рекомендацию, то сделать точную фрезу не получится. Если важно собрать самодельный станок своими руками так, чтобы на нем можно было выполнять достойного качества заготовки, то это одно из важнейших условий.
Для того чтобы обеспечить идеально ровную поверхность, можно воспользоваться такими способами, как: ламинирование, обивка листовым железом или точная подгонка строганных досок.
Как сделать станок своими руками
Порядок сборки этого устройства начинается с того, что необходимо определить месторасположение двигателя. Наилучшим вариантом считается установка этого элемента под столом. На валу двигателя, который должен быть направлен вертикально вверх, располагают фрезу. Для того чтобы облегчить порядок сборки, лучше всего сделать чертеж станка своими руками, на котором все детали были изображены заранее.
fb.ru