Сталь конвертерная – Свойства конвертерной стали
alexxlab | 09.07.2019 | 0 | Вопросы и ответы
Свойства конвертерной стали
Причиной ограниченного развития начальных вариантов конвертерного производства — бессемеровского, и томасовского — являлось низкое качество выплавленного металла, значительно уступающего по своим свойствам мартеновской стали с тем же содержанием углерода. Бессемеровская и томасовкая сталь обнаруживала пониженную ударную вязкость, особенно при низких температурах, а также неудовлетворительную электросвариваемость. Одновременно проявлялась повышенная склонность к старению металла. Низкие свойства обычной конвертерной стали вызывались наличием в ее составе сочетания примесей — азота кислорода, фосфора и серы, особенно резко влияющих на свойства малоуглеродистого металла в связи с ограниченной растворимостью этих элементов в α-железе.
Переход к использованию в конвертерном производстве дутья, практически не содержащего азота (смесь О2 + Н20 и технически чистый кислород), позволил резко улучшить качество выплавляемого металла вследствие сильного снижения содержания [N].
Новые варианты процесса с подачей кислорода сверху обеспечили также раннюю и более полную дефосфорацию и сокращение периодов повышения окисленности металла в конце процесса продувки. Для получения низких концентраций азота в кислородно-конвертерной стали требуется высокая степень чистоты применяемого газообразного кислорода, не менее 99,5% О2. Глубокая дефосфорация и низкие конечные содержания фосфора в металле достигаются за счет соответствующего шлакового режима кислородно-конвертерной плавки (процесс с двумя шлаками и др.).
В целом, особенности технологии плавки в кислородных конвертерах позволяют получить сталь массового производства, а также легированную и высококачественную сталь, не уступающую по своим свойствам стали, выплавленной в мартеновских печах, а в некоторых случаях и в электропечах. В настоящее время в промышленном масштабе освоено производство кислородно-конвертерной стали мягкой (малоуглеродистой) кипящей и спокойной, рельсовой, низколегированной. В опытном порядке выплавлялась трансформаторная, динамная, канатная, инструментальная, хромистая, а в последнее время — и высоколегированные нержавеющие стали. Значения ударной вязкости кипящей кислородно-конвертерной и мартеновской сталей при различных температурах практически находятся на одном уровне (абсолютные значения для кислородно-конвертерной стали даже несколько выше, рис. 1).
Рисунок 1. Ударная вязкость кипящей кислородно-конвертерной стали (1) и мартеновской (2) при различных температурах испытания
При освоении выплавки в кислородных конвертерах судостроительной стали, например марки 10ХСНД (0,06—0,11% С; 0,65-0,88% Мп; 0,74—1,05% Si; 0,56—0,96% Cr; 0,56—0,7% Ni 0,50—0,66% Cu; 0,024—0,036% S , 0,019—0,027% P; 0,0020—0,0033% О; 0,0030—0,0064% N) была успешно решена проблема легирования металла феррохромом при его угаре не выше, чем в мартеновских печах.
Для стали, выплавленной в кислородных конвертерах, наблюдаются более высокие прочностные свойства при тех же характеристиках пластичности, что и у мартеновской стали (табл. 1).
Кислородно-конвертерная динамная сталь после различных вариантов холодной прокатки (на лист толщиной 0,5 мм) и отжига (в вакууме) обладает свойствами электростали марки Э1300. Горячекатаная сталь по магнитным свойствам находится на уровне мартеновской динамной стали.
Выплавленная в кислородных конвертерах трансформаторная сталь по всем показателям: химическому составу, механическим свойствам, электротехническим характеристикам (удельным ваттным потерям), — отвечает требованиям, предъявляемым к трансформаторной электростали.
Обработка конвертерного металла в ковше синтетическими шлаками состава: 52,5—55,3% СаО; 42,5—44,2% А12О3; 1,9—2,2% SiO2; 0,7—0,8% MgO; 0,65—0,70% FеО; 0,15—0,90% Сг2O3 дает металл, не уступающий по качеству электросталям. В плавках применяли двукратное скачивание шлака. Полученный конвертерный металл по механическим свойствам не уступал электростали.
Таблица 1. – Сравнение свойств кислородно-конвертерной и мартеновской стали
Таким образом, при условии небольших дополнительных затрат (по приготовлению синтетического шлака, организации скачивания и уборке увеличенных количеств шлака и др.) в кислородных конвертерах может быть получена сталь широкого сортамента, вплоть до легированных марок, при малых затратах на передел и высокой производительности агрегатов.
Однако вопросы качества и сортамента кислородно-конвертерной стали еще не являются полностью решенными. Отмечается высокая чувствительность конечных содержаний азота в металле к примесям азота в дутье, а по некоторым данным и к возможному подсосу воздуха через горловину конвертера. Поэтому целесообразно применять кислород повышенной чистоты — 99,5%. Механические характеристики конвертерного металла не во всехслучаях отличаются высокой стабильностью и анизотропностью (при испытаниях образцов вдоль и поперек направления прокатки).
Выплавка высоколегированных сталей в кислородных конвертерах без привлечения вспомогательных агрегатов и процессов еще сопряжена с большими потерями легирующих.
Технико-экономические показатели.
Главными технико-экономическими показателями выплавки стали в кислородных конвертерах являются их производительность и себестоимость стали. При этом качество металла должно полностью отвечать требованиям по соответствующим маркам.
Производительность конвертеров определяется массой плавки, продолжительностью цикла плавки между последовательными заливками чугуна, частотой ремонтов, т. е. стойкостью футеровки, затратами времени на ремонт и разогрев агрегатов.
Продолжительность цикла плавки не пропорциональна емкости конвертеров, а изменяется более слабо. Это определяет более высокую часовую и суточную производительность конвертеров большой емкости. Так, цикл плавки в 25- и 100-т конвертерах различается в 1,65 раза (28 и 43,5 мин соответственно), это дает повышение производительности 100-т конвертеров по сравнению с 25-т в (100:43,5) : (25 : 28) = 2,64 раза. Высокая производительность достигнут на 50-т конвертерах Криворожского металлургического завода. Цех в составе четырех конвертеров (с учетом резервного) дает 300 т/ч готового металла. Максимальная часовая производительность получена в конвертерном цехе завода в Торонто (Италия) — 524т/ч на один конвертер при массе плавки 303 т.
Основными статьями себестоимости кислородно-конвертерной стали является стоимость перерабатываемых материалов и расходы по переделу. Расход основных материалов на 1 стали в условиях Криворожского металлургического комбината следующий в (кг):
Расходы по переделу для цеха с годовой производительностью 1,5 млн. составляют лишь 55,5% от таковых для мартеновского цеха той же производительности. Относительно меньшую долю составляет стоимость топлива и энергетических затрат (около 45%), огнеупорных и вспомогательных материалов (около 30%) от соответствующей стоимости для мартеновской стали. Соотношение затрат на перерабатываемые шихтовые материалы и на передел в кислородно-конвертерном производстве отличается от соотношения этих затрат в мартеновском производстве в сторону относительно больших затрат на шихтовые материалы (около 89% против 79% для мартеновского производства). Следовательно, дополнительные резервы снижения себестоимости могут быть использованы при правильном подборе составляющих шихты, особенно доли жидкого чугуна и твердого скрапа в зависимости от конкретной их стоимости и степени дефицитности для данного металлургического района.
metallurgy.zp.ua
2. Конверторный способ получения стали
Производство стали
Сталью называют сплавы железа с углеродом и другими элементами. Такие сплавы обладают пластическими свойствами как в нагретом, так и в холодном состоянии и могут подвергаться прокатке, волочению, ковке и штамповке. Сталь содержит до 2% углерода и некоторое количество марганца, кремния, а также вредные примеси фосфора и серы. Кроме этого, в стали могут содержаться и легирующие элементы хром, никель, ванадий, титан и др.
В настоящее время сталь производят преимущественно путем передела чугуна, при котором из него удаляется избыток углерода, кремния, марганца, а также вредных примесей для придания стали необходимых свойств. Углерод и другие примеси при высокой температуре соединяются с кислородом гораздо энергичнее, чем железо, и их можно удалить при незначительных потерях железа. Углерод чугуна, соединяясь с кислородом, превращается в газ СО и улетучивается. Другие примеси превращаются в оксиды SiO2, МnО и Р2О, которые вследствие меньшего по сравнению с металлом удельного веса всплывают и образуют шлак. В настоящее время в промышленности в основном применяют конвертерный и мартеновский методы получения стали, кроме того, сталь получают в электрических дуговых и индукционных печах.
Конверторный способ получения стали
Сущность конвертерного способа получения стали заключается в том, что через жидкий чугун, залитый в конвертер, продувается воздух, кислород которого окисляет углерод и другие примеси. Обычно конвертер-емкость имеет грушевидную форму, сваренную из толстой листовой стали и футерованную внутри огнеупорным кирпичом (рис. 2). Снаружи в верхней части конвертера имеются два цилиндрических выступа, называемых цапфами, которые служат для опоры и поворота конвертера. Одна из цапф делается полой и соединяется с воздуховодом. От цапфы к днищу через трубу и воздушную коробку подводится воздух. В днище конвертера имеются отверстия фурмы, через которые под давлением 2,0 — 2,5 ат. воздух подается в конвертер. Для заливки жидкого чугуна конвертер поворачивается из вертикального в горизонтальное положение. После заливки чугуна пускают дутье, и конвертер поворачивают днищем вниз.
Рисунок 2 – Схема конвертора
Слой металла в конвертере составляет от 1/5 до 1/3 высоты его цилиндрической части. Емкость современных конвертеров, работающих на воздушном дутье, достигает 50 т. В конвертерах применяют кислую и основную футеровку. Тепло, необходимое для нагрева жидкой стали до высоких температур, в этих процессах получается за счет химических реакций окисления примесей чугуна. При этом примеси могут окисляться элементарным кислородом и кислородом закиси железа, которая растворяется в металле. При окислении примесей кислородом выделяется значительное количество тепла, окисление происходит кислородом по следующим реакциям:
Si + О2 SiO2 + Q;
Mn + 1/2O2 MnO + Q;
С + 1/2О2 СО + Q;
C + O2 CO2 + Q;
Fe + 1/2O2 FeO + Q;
2P + 2/3 O2 P2O5 + Q.
Окисление примесей чугуна кислородом закиси железа происходит по следующим реакциям:
Si + 2FeO SiO2 + 2Fe + Q;
Mn + FeO MnO + Fe + Q;
С + FeO CO + Fe – Q;
2P + FeO P2O5 + 5Fe + Q.
При окислении элементов наибольшее количество тепла выделяют кремний, фосфор и марганец. Эти вещества используются при продувке чугуна как источник тепла (кремний в кислом процессе, а фосфор – в основном конвертере). Недостаточное количество тепла от реакций компенсируется температурой жидкого чугуна.
Для получения стали методом продувки применяют чугун марки Б-1 и Б-2 — для кислого и Т1 — для основного процесса. Чугун марки Б-1 и Б-2 содержит минимальное количество фосфора (0,07%) и серы (0,06%). Чугун марки Т-1 содержит гораздо больше фосфора (1,6 — 2,0%, иногда до 2,5%). В последнее время для продувки чугуна вместо воздуха применяют технический кислород, который позволяет повысить скорость плавки и выход качественной стали за счет увеличения добавки твердой шихты, а также уменьшения химических примесей в чугуне, подвергающихся окислению. Конвертер, работающий на кислородном дутье, по своей конструкции отличается от обычных конвертеров тем, что в нем имеется сплошное днище. Кислород вовремя плавки подается в него сверху, так как его подача через донные фурмы приводит к их быстрому разрушению. Для этой цели в конвертер опускают трубу, через которую подают кислород и вдувают известь или смесь извести и плавикового шпата. Концентрацию извести и шпата в струе кислорода регулируют в зависимости от состава чугуна. Работают конвертеры на кислородном дутье емкостью 3, 30, 50, 100, 150 и 250 т. Эти конвертеры в основном футеруются магнезитовым кирпичом и доломитовым порошком. Труба, через которую подается кислород, вместе с известью охлаждается водой. Расход воды для трехтонного конвертера составляет 20 м3/ч. Состав извести может изменяться по содержанию окиси кальция от 78 до 92%, окиси кремния SiO2 — от 1,5 до 2,7% и серы — от 0,07 до 0,12%. Возможность применения извести разного состава является большим преимуществом данного способа. Подача извести в струе кислорода обеспечивает исключительно высокую степень соединения и удаления фосфора и серы из металла в шлак. Добавка плавикового шпата к извести еще больше повышает активность шлаков. Кислород применяется технический под давлением 6 — 8 ат. Для понижения температуры металла в конвертер во время плавки загружают стальной лом и железную стружку. При повышенном содержании кремния в чугуне подачу извести увеличивают для того, чтобы получить шлак с необходимой основностью для связывания фосфора. При продувке томассовского чугуна, содержащего 3,6% С; 0,8% Мп; 0,4% Si; 1,7% Р и 0,04% S, после промежуточного скачивания шлака содержание С в металле понижается до 0,6%, а Р — до 0,1%. Полученный шлак является хорошим удобрением для сельского хозяйства. После повторного вдувания извести получают металл с содержанием 0,8% С; 0,31% Мп; 0,017% Р; 0,014% S; 0,001% Ni и следами S , то есть получают сталь, подобную по составу мартеновской. Расход кислорода на 1 т чугуна составляет 60 — 65 м3, а извести 130 — 135 кг. Длительность продувки в тридцатитонном конвертере составляет 20 – 30 мин, расход футеровки – 10 кг на 1 т чугуна.
На современном этапе развития металлургического производства конвертерный способ не решает задачу получения стали сразнообразными свойствами. Для успешного осуществления конвертерного способа требуется чугун строго ограниченного состава.
studfiles.net
Развитие кислородно-конвертерного производства стали
Развитие сталеплавильного производства в ближайшее время заключается в замене мартеновского способа получения стали более прогрессивными —кислородно-конвертерным и электросталеплавильным. Кислородно-конвертерному процессу присущи более высокая производительность, меньшие удельные капиталовложения и затраты по переделу, комплексная механизация производства.
Килородно-конвертерный процесс, благодаря высоким технико-экономическим показателям, занимает ведущее место в современном сталеплавильном производстве.
В настоящее время в кислородных конвертерах выплавляют больше 65% производимой в мире стали.
Конвертерный процесс возник в середине XIX века.
Поставленные XXVII съездом КПСС задачи по техническому перевооружению черной металлургии и повышению качества продукции будут решены, в частности, в результате дальнейшего расширения и совершения кислородно-конвертерного производства стали. Намечено существенное увеличение объема выплавки стали в кислородных конвертерах, строительство новых конвертерных цехов. Важной задачей является также внедрение прогрессивных вариантов технологии плавки и широкое использование в конвертерных цехах методов внепечной обработки, позволяющих значительно повысить качество металла и расширить сортамент выплавляемых в конвертерах сталей.
Конвертерный (бессемеровский) процесс был первым в истории металлургии способом массового производства стали. Существовавшие в то время способы производства стали (пудлинговый и тигельный) не могли в достаточной мере удовлетворить потребности в металле, вызванные увеличением масштабов железнодорожного строительства, судостроения, машиностроения, развитием военной техники и т.п. Пудлинговая печь имела садку (вместимость) 250-500кг (редко до 1т) и позволяла получать до 15т стали за сутки в тестообразном (полутвердом) состоянии, тигельным процессом получали жидкую сталь в огнеупорных тиглях вместимостью до 35кг.
12 февраля 1856 г. Г. Бессемер подал заявку на получение патента. В заявке говорилось о том, что, если в достаточных количествах вводить в металл атмосферный воздух или кислород, он вызывает интенсивное горение между частицами жидкого металла и поддерживает температуру последнего или повышает ее до такой степени, что металл остается в жидком состоянии во время перехода его из состояния чугуна до состояния стали или ковкого железа без затраты горючего. К 1860 г. Бессемер закончил разработку конструкции агрегата, предназначеного для продувки чугуна, предложив вращающийся вокруг горизонтальной оси аппарат (названный им конвертером (converter, анг. — преобразователь)).
Сущность процесса, предложенного и разработанного в 1856-1860 гг Г. Бессемером, заключалась в том, что залитый в плавильный агрегат с кислой футеровкой (конвертер) чугун продували снизу воздухом. Кислород воздуха окислял примеси чугуна, в результате этого чугун превращался в сталь. Тепло, выделявшееся при реакциях окисления, обеспечивало нагрев стали до температуры ~ 16000С. В 1878г. С. Томасом был предложен способ изготовления основной (доломитовой) футеровки конвертеров. Так возник томасовский процесс переработки высокофосфорных (1,6-2,0% Р) чугунов в конвертерах с основной футеровкой.
Бессмеровский и томасовский процессы получили широкое распространение. Продолжительность бессемеровской плавки составляла 20-30 минут при вместимости конвертера до 35т, продолжительность томассовской плавки — 20-40 минут при вместимости конвертера ≤ 70т. Оба процесса имели значительный недостаток – выплавляемая сталь содержала большое количество (0,01-0,025%) азота. Это объяснялось тем, что азот воздушного дутья растворялся в металле. Для получения стали с более низким содержанием азота в 1950-1965 гг были разработаны и в ряде стран применялись разновидности этих процессов предусматривавшие продувку снизу воздухом обогащенным кислородом, парокислородной смесью и смесью кислорода с углекислым газом СО2.
Метод продувки жидкого чугуна кислородом сверху был впервые предложен и опробован в ССР в 1933 г. Инженером Н.И. Модговым. В дальнейшем в ССР и в ряде других стран проводили исследования по разработке технологии нового процесса. В СССР эксперименты в 1936г проводили в АН УССР; в 1939г. Юыли продолжены на заводе «Станкоконструкция» (г.Моска) и в 1942г. На Косогорском металлургическом заводе; в 1945 – 1953 гг – ЦНИИ ЧМ, на заводах «Динамо», Мытищенском машиностроительном, Енакиевском и Ново-Тульском металлургических.
В 1954-1955 гг. на Ново-Тульском металлургическом заводе в 10-т конвертере проведена окончательная доработка технологии выплавки стали с продувкой кислородом сверху.
Первая в мире крупная установка с конвертером емкостью 15 тонн была пущена в 1949 году на металлургическом заводе в городе Линц (Австрия) . На ней были достигнуты весьма высокие технологические показатели, что и определило дальнейшую судьбу кислородно-конвертерного процесса. Первые в мире промышленные сталеплавильные цеха, оснащенные конвертерами с кислородным дутьем через погружаемую сверху фурму, были введены в эксплуатацию в 1952-1953 годах в австрийских городах Линц и Донавиц. Собственно успешное функционирование этих цехов и дало окончательное практическое подтверждение тому факту, что использование кислорода для переработки сталеплавильного процесса и исключает применение дорогостоящих энергоносителей для нагрева металла.
В период 1955-1975 гг бессемеровский и томассовкий процессы и их разновидности были вытеснены разработанными к этому времени процессами с продувкой чистым кислородом сверху и через дно.
В СССР в 1956 году на верхнее кислородное дутье был переведен бессемеровский цех переоборудованных на 20-т конвертерах на Днепропетровском металлургическом заводе имени Петровского, а в 1957 – пущен в эксплуатацию кислородно-конвертерный цех с 35-т бессемеровскими конвертерами на меткомбинате «Криворожсталь» . В период 1963-1969 гг. были построены кислородно-конвертерные цеха с 100-130т конвертерами на Нижне-Тагильском комбинате (1963г.), на заводе им. Ильича (1964г.), Криворожском (1965г.), Новолипецком (1966г.), Челябинском (1969г.), Западно-Сибирском (1968г.) и Енакиевском (1968г.) металлургических заводах.
С 1970г. В ССР сооружают кислородно-конвертерные цеха с большегрузными конвертерами. В 1970г. Был построен цех с 250-т конвертерами на Карагандинском, в 1974 г. – с 300 – т конвертерами на Новолипецком, 1974 г. – с 300-т конвертерами на Западно-Сибирском металлургических комбинатах, в 1977г. – с 350-т конвертерами на металлургическом комбинате «Азовсталь», в 1980 г. – с 350-т конвертерами на Череповецком металлургическом заводе и в 1983 г. – с 250-т конвертерами на металлургическом комбинате им. Ф.Э. Дзержинского.
За время существования кислородно-конвертерного процесса было разработано значительное число его разновидностей. Начиная с 1958г., применяют разработанный металлургами Франции, Бельгии и Люксембурга процесс переработки фосфористых чугунов с вдуванием порошкообразной извести в струю кислорода (процесс ЛДЖ-АЦ или ОЛП). Непродолжительное время существовал разработанный в 1952 г. В ФРГ роторный процесс: плавка во вращающееся цилиндрической печи с вдуванием кислорода через две фурмы, одну из них погружали в металл, через вторую подавали кислород для дожигания оксида СО, выделяющегося из ванны. Опытная роторная печь эксплуатировалась на Нижне-Тагильском металлургическом комбинате. Около двух десятилетий в ряде стран применяли разработанный в 1954г. В Швеции процесс Калдо – плавку в наклоненном под углом 17-200 к горизонту вращающемся конвертере с подачей кислорода через фурму, расположенную над ванной под углом 18-260 к ее поверхности. Вследствие сложности эксплуатации оборудования и низкой стойкости футеровки конвертера и других показателей плавки процессы Калдо и роторный в настоящее время не используются.
Длительное время в ССР и за рубежом вели разработку метода вдувания чистого кислорода через дно конвертера, что привело к созданию применяемого в настоящее время процесса с донной продувкой кислородом. В промышленном масштабе этот процесс был впервые осуществлен в ФРГ в 1967.
С 1975 – 1978 ГГ. широкое распространение получают процессы комбинированной продувки в кислородных конвертерах, то есть процессы, предусматривающие продувку кислородом через фурму сверху в сочетании с вдуванием через дно различными способами тех или иных газов (нейтральных, кислорода и др.) Многочисленные разновидности этих процессов разработаны во многих странах Западной Европы, США, Японии и в СССР. Технология комбинированной продувки, позволяя сочетать преимущества способов продувки сверху и через дно, обеспечивает повышение многих показателей конвертерной плавки и поэтому получает все более широкое распространение.
В настоящее время в мире эксплуатируется свыше 160 конвертерных цехов, располагающих приблизительно 660 крупными конвертерами (с учетом мелких агрегатов, работающих преимущественно в Китае, их количество достигает 740. (рисунок 1).
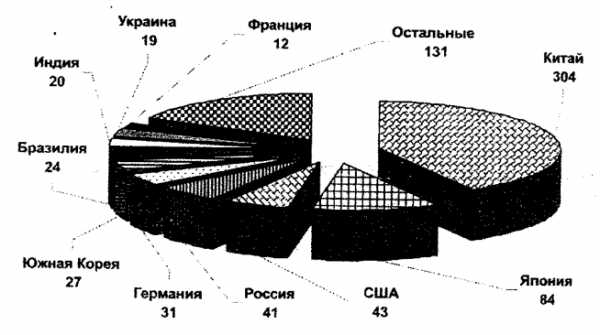
В конвертерах выплавляют 65,4% от всего мирового объема стали (примерно 736 миллионов тонн в 2005 году), рисунок 2.
Рисунок 2 – Динамика производства конвертерной стали в мире
В мире 19 цехов имеют в своем составе мощнейшие конвертеры емкостью 290-300 и более тонн. Четыре из них находится в России (Череповецкий, Магнитогорский, Новолипецкий и Западно- Сибирский металлургические комбинаты), четыре — в Японии («Kawasaki Steel” на заводе «Mizushima Works”; «Nippon Steel Corp” на предприятии «Yawata Works”; «Nippon Steel Corp» на «Kimitsu Works”; «NKK Corp» на «Keihin Works”), два — в Германии («Thyssen Krupp Stahl» и «Stahlwerke Bremen»), по одному — в Украине (металлургический комбинат «Азовсталь”, в 2007 г. намечен пуск 300-тонного конвертера на Алчевском металлургическом комбинате), Казахстане («Ispat Karmet”), США («Weirton Steel Corp”), Южной Корее («Pohang Iron & Steel Corp»), Польше («Huta Katowice”), Великобритании («Scunthorpe Works»), Франции («Arcelor” на предприятии «Fos-sur-Mer»), Индии (Bokaro, «S.A.I.L.”) и Нидерландах («Hoogovens Ijmuiden BV»). Как показывает практика, конвертерный цех в составе трех 370-400-тонных конвертеров может обеспечить годовой объем производства на уровне 10 миллионов тонн стали. Основными производителями стали в кислородных конвертерах являются Китай, Япония, США, Россия, Южная Корея, Бразилия, Индия, Украина.
Для конвертерного способа производства характерна его высокая концентрация в небольшом количестве промышленно развитых стран. Пять ведущих производителей конвертерной стали обеспечивают более двух третей, а десять ведущих производителей — свыше четырех пятых ее мирового производства. При этом доля конвертерной стали в общем объеме производства в этих странах колеблется весьма существенно: от 45 % в США и 49,9 % в Украине до 87,1 % в Китае и 70-75 % в Бразилии, Южной Корее, Японии. В Австрии, Австралии, Бельгии, Люксембурге доля конвертерной стали составляет более 90 %.
Конвертерное производство России включает 8 конвертерных цехов с 22 кислородными конвертерами (9 — 300-375 тонн и 13 — 130-160 тонн общей мощности 350 млн. тонн).
На российских предприятиях в настоящее время (по данным за 2005г.) 59,3% всей выплавляемой стали производится конвертерным способом (ОАО «ММК», ОАО «Северсталь», ОАО «НЛМК», ОАО «ЧМК», ОАО «НТМК», ОАО «ЗСМК»). Общий объем выплавки конвертерной стали на этих предприятиях в 2005 г. составил 39,3 млн. тонн. При этом за последние 10 лет выплавка кислородно-конвертерной стали увеличилась в 1,7 раза (рисунок 3).
Рисунок 3. — Динамика выплавки кислородно-конвертерной стали в России
Современные российские конвертерные цеха являются крупными сталеплавильными комплексами с конвертерами с комбинированной продувкой, оборудованные газоочистками с системой отвода газов без дожигания. В цехах имеются установки десульфурации чугуна и внепечной обработки стали, высокопроизводительные машины непрерывного литья заготовок, а также автоматические системы управления технологическими процессами.
Наблюдаемый в последнее десятилетие прирост производства конвертерной стали достигнут главным образом за счет Китая. Определенный прирост производства конвертерной стали в России и Украине может наблюдаться в случае реструктуризации цехов с мартеновскими печами (доля мартеновского производства в Украине составляет около 45%, в России — около 25% (рисунок 4).
Рисунок 4 — Изменение доли мартеновского производства стали с 1960 по 2005г
И все же в дальнейшем наиболее вероятен прирост производства конвертерной стали за счет Китая и Индии, где внутреннее потребление металлопродукции постоянно растет (в Китае доля внутреннего потребления стали составляет около 90%, в промышленно развитых странах объем внутреннего рынка потребления металлов достигает 80%, а в Украине не превышает 21%).
При этом следует отметить, что если в странах Евросоюза наблюдается тенденция к повышению эффективности функционирования всей технологической системы производства конвертерной стали в совокупности с расширением мероприятий по защите окружающей среды без существенного наращивания объемов производства, а в КНР в течение нескольких лет происходит скачкообразное наращивание производства конвертерной стали за счет введения в эксплуатацию новых цехов и заводов, базирующихся на последних достижениях европейских и японских технологов и машиностроителей.
В 2005 году в странах ЕС-25 выплавлено 114,2 миллионов тонн конвертерной стали, что составляет 61,0 % от всего сталеплавильного производства. В настоящее время в странах ЕС функционирует 91 конвертер, большинство из которых имеет массу плавки более 100 тонн (таблица 1).
Таблица 1. — Количество конвертеров в странах ЕС-25
При развитии конвертерного производства в ЕС предпочтение отдается технологическим решениям, направленным на уменьшение потерь энергии, железа, огнеупоров и других расходуемых материалов при снижении вредного влияния на окружающую среду. Не обходят вниманием и технологии эффективной переработки металлолома, утилизации технической воды, развитие транспортной системы. Важным направлением инновационного развития в металлургии ЕС является создание новых марок сталей, имеющих максимально высокие технологические и эксплуатационные свойства применительно к конкретным изделиям. Следует ожидать, что в ближайшее время будут интенсивно развиваться направления производства высокопрочных сталей, а также сталей высокой чистоты по вредным примесям.
В 2005 году производство конвертерной стали в Китае превысило 300 миллионов тонн. Сегодня в стране выплавляется более 40 % всего мирового производства конвертерной стали. Характерной особенностью развития конвертерного производства в Китае является быстрое увеличение количества конвертеров при их сравнительно небольшой единичной емкости (таблица 2). Между тем в Китае в последние десятилетия построен ряд конвертерных цехов с агрегатами 200-300 тонн.
Таблица 2. — Количество конвертеров и средняя масса плавки в Китае
Основными тенденциями развития конвертерного производства в Китае являются повышение эффективности работы конвертеров за счет применения комбинированной продувки (реконструкция действующих конвертерных цехов), широкое внедрение автоматических систем контроля производства, снижение удельных расходов энергии, огнеупоров (за счет технологии набрызгивания шлака на стены конвертера), радикальное повышение чистоты стали, расширение объемов природоохранных мероприятий и рециклинга промышленных отходов.
На 01.01.2010г. производственные мощности металлургических предприятий объединения«Металлургпром» по выплавке стали составляют ~ 50 млн. т в год(без учета мощностей сталелитейных цехов предприятий).
В составе сталеплавильного производства имеем на балансе 21 кислородный конвертер с суммарной производственной мощностью 28,4 млн.т в год.
В 2004 г. соотношение между объемами производства конвертерной, мартеновской и электропечной сталью составляло, %: 51,3, 45,3 и3,4, то в 2009г. это соотношение составляет69,2, 26,3 и4,5 соответственно.
Объем стали, разливаемой на МНЛЗ от общего объема производимой стали за эти годы (2004-2009гг.) вырос с 24,2 до 48,4 %. Конечно, в улучшении этих показателей есть и доля влияния кризиса, так как это позитивное перераспределение в пользу уменьшения объёмов мартеновской стали и увеличение объёмов разливки на МНЛЗ зависит от уменьшения общих объемов производства стали. Но перспектива техпереоснащения сталеплавильного производства, которая реально реализуется сегодня на предприятиях, показывает, что начатый процесс улучшения структуры по видам стали и по объемам, разливаемым на МНЛЗ, – необратим.
Рисунок 5. — Производство стали по видам а) – 2009год б) 2008 год
В таблице 3 приведены данные о наличии плавильных агрегатов в сталеплавильном производстве (конвертерном), использовании производственных мощностей, наличии установок МНЛЗ, «печь-ковшей», вакууматоров и перспектив ввода новых агрегатов и т.д. Дальнейшие процессы техпереоснащения и модернизации сталеплавильного производства напрямую связаны с выходом отрасли, из кризиса.
Таблица 3. — Кислородные конвертеры на металлургических предприятиях объединения «Металлургпром» на01.01.2010 г.
Начиная с 2002г., освоение капитальных инвестиций на техпереоснащение на металлургических предприятиях, шло каждый год по нарастающей (рисунок 6).
Рисунок 6. Показатели освоения капитальных инвестиций, в т.ч. на охрану окружающей среды предприятий, входящих в объединение»МЕТАЛЛУРГПРОМ»
metallurgy.zp.ua
Конвертерное производство стали | Учебные материалы
Бессемеровский способ
Кислый способ, футеровка конвертера выложена из динасового огнеупорного кирпича. Применяется при переплавке в сталь чугуна марок Б1 и Б2, содержащих строго ограниченное (максимально допустимое в сталях) количество фосфора и серы. Это объясняется тем, что в конвертерах или в других печах с кислой футеровкой невозможно удалять вредные примеси S и Р.
Плавка стали в конвертере состоит в следующем:
- Конвертер ставится в горизонтальное положение.
- Заливается жидкий чугун.
- Подается воздушное дутье под давлением Р = 3÷3,5 атм. (который окисляет примеси) и одновременно с этим конвертер ставится в вертикальное положение.
Во время плавки в кислом конвертере наблюдается 3 периода:
1) Окисление Fe, Mn, Si и образуется шлак
в шлак +Q
далее
раскисление
Длится процесс окисления 3-6 минут.
2) Выгорание углерода, т.е. его окисление, жидкость кипит:
FeO + C → Fe + CO
СО вырвавшись из стали догорает ярким пламенем высотой 8-10 метров
СО + О → СО2
3) Пламя прекращается и появляется бурый дым, что означает горение железа, а сам дым – частицы окислов железа. Необходимо побыстрее прекратить подачу воздуха и процесс плавки окончен.
Если углерода в стали осталось меньше необходимого по марки выплавляемой стали, то состав по С доводится добавлением в стали небольшого количества высокоуглеродистого чугуна и ферросплавов Fe-Mn, Fe-Si и Al.
Процесс плавки длится 20-30 минут, емкость конвертеров всего до 30г.
Этот метод экономичный, эффективный и распространенный. Сталь содержит незначительное количество кислорода (кислород вредная примесь, FeO повышает хрупкость стали, усиливает склонность к старению и повышает порог хладноломкости), поэтому кислая (бессемеровская) сталь более пластичная, следовательно более качественная, по сравнению со сталями выплавляемыми в основных печах.
В настоящее время развитие конвертерного производства идет по расширению кислородно-конвертерного способа, емкость которых до 250-300т.
Томасовский способ
Томасовский способ – продувка через жидкий металл воздуха, но футеровка основная и благодаря этому становится возможным удаление фосфора. Футеровка доломитовая (МgO, СаО). Применяется для переплавки в стали чугунов марок Т-1 и Т-2, содержащих повышенный % фосфора до 2,2% и серы.
В томасовском конвертере процессы окисления протекают в такой же последовательности, как и в бессемеровском, за исключением того, что в третьем периоде идет бурное окисление фосфора, за счет чего резко повышается температура стали и сталь становится более качественной и пластичной.
Для удаления Р и S в конвертер загружается 12-14% от веса заливаемого чугуна – известняк СаСО3:
– 2Р + 5FeO + 4СаО → Р2О5(СаО)4 + 5Fe
шлак
Р2О5(СаО)4 – очень прочное соединение и ценное удобрение для сельского хозяйства.
– FeS + СаО → СаS + FeО, где СаS – непрочное соединение, поэтому вводят Mn:
СаS + MnO → MnS + СаО, где MnS – не переходит в ванну, если остается, то это более тугоплавкое соединение нежели FeS + Fe (t плавл. ≈ 988°С).
В настоящее время томасовский способ в нашей стране почти не применяется, так как высокофосфористых и высокосернистых руд у нас мало.
Рассмотренные конвертерные способы выплавки стали имеют следующие преимущества:
- Высокая производительность (время плавки 20-30 мин.).
- Простота конструкций печей (конвертеров) и следовательно малые капитальные затраты.
- Малые эксплуатационные затраты.
- Не требуется при плавке специально вводить тепло, так как оно получается в конвертерах за счет реакций окисления примесей.
Недостатки:
- Значительный угар железа (до 13%).
- Невозможность переплавлять в больших количествах скрап (металлический лом).
- Более низкое качество стали (главный недостаток конвертирования) – например, за счет продувки воздухом в стали увеличивается содержание азота (до 0,025-0,048%), которое заметно снижает качество стали.
- Из-за непродолжительности процесса невозможно в конвертерах выплавлять стали сложного химического состава, а из-за невысоких температур (наибольшая tплавл. = 1600°С) невозможно добавлять тугоплавкие легирующие компоненты (W, Mo, Nb и т.д.).
Таким образом до настоящего времени конвертерное производство стали было ограничено из-за вышеизложенных недостатков. В конвертерах выплавлялись лишь простые углеродистые стали обыкновенного качества.
Кислородно-конвертерный способ производства стали
В настоящее время промышленная индустрия настолько окрепла, что стало возможным в больших промышленных количествах получать промышленно чистый кислород. Продувая чугун кислородом имеется возможность выплавлять в них стали по качеству близкие к мартеновским. Кроме того благодаря применению О2 в конвертерах производительность их еще более повышается и также повышается температура ванны (tплавл. повышается до ~2500°С), что позволяет уже в большем количестве в конвертерах переплавлять скрап. Кислородно-конвертерное производство позволило в последние годы выплавлять в конвертерах до 40% от общего количества выплавляемой стали.
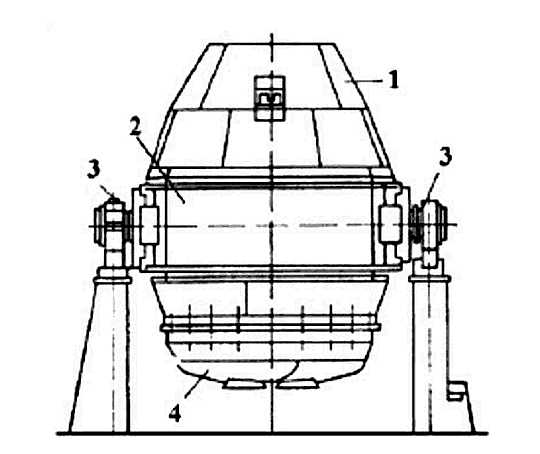
Рисунок 1.2 – Кислородно-конверторный способ:
1 – горловина для загрузки, 2 – цилиндрическая часть,
3 – стальное кольцо с цапфами, 4 – съемное днище
При этом способе кислород подается в ванну жидкого чугуна в конвертере сверху, через охлаждаемую водой фурму.
Конвертерные установки с донной кислородно-топливной продувкой – в 1,5 раза превосходят по производительности 2-х ванную мартеновскую печь (при сохранении баланса металлолома).
dprm.ru
Кислородно конвертерный способ производства стали
Важно отметить, что кислородно-конвертерный способ производства стали имеет ряд особенностей, связанных с технологическими тонкостями, в процессе всего производства. Значительные затраты на конвертерное производство оправдывают окупаемость во время эксплуатации любых изделий, особенно из стали, выплавленной таким путем.
Основные нюансы процесса
Согласно технологическим особенностям, конвертерный способ подразделяется на две разновидности:
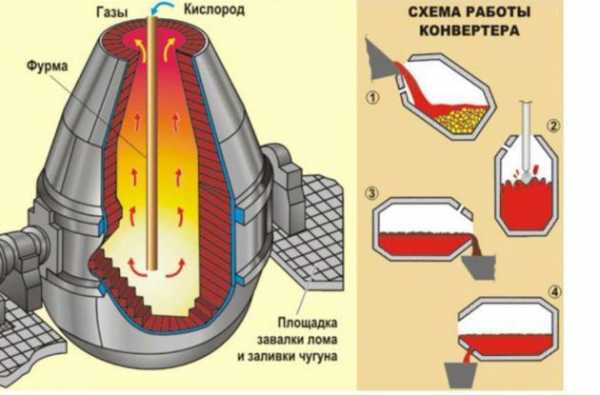
Кислородно-конверторный способ
При воздушном дутье, залитый в конвертерах чугун, продувают снизу воздухом. Благодаря тому, что частицы воздуха окисляют любые примеси чугуна, происходит повышение температуры стали вплоть до 1,6 тыс. градусов. Именно это тепло и превращает чугун в сталь.
Различия двух способов
Вышеупомянутое производство подразделяется на бессемеровский и томасовский процессы. Различия между ними в основных составляющих футеровках конвертеров.
Бессемеровский путь выплавки стали позволяет использовать низкое содержание фосфора и серы. При томасовском способе, наоборот, чугун переплавляется посредством высокого содержания фосфора.
Суть кислородно-конвертерного производства заключается в выплавке стали посредством футеровки и продувки кислородом из жидкой чугунной основы. В обязательном порядке для этого используется водоохлаждающая форма.
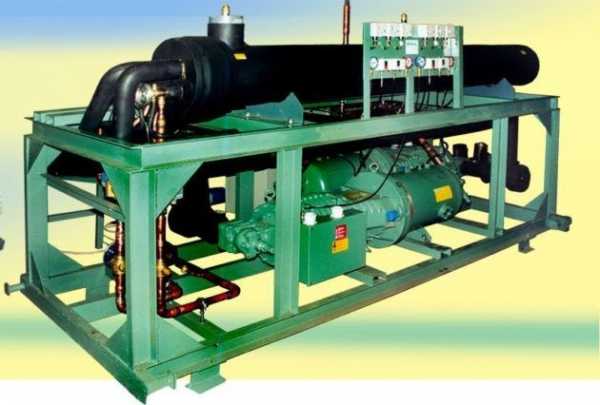
Водоохлаждающая форма
В агрегатах кислород подается снизу. Этот метод наиболее распространен в России. Хотя в зарубежных странах нередко применяется и комбинированный способ продувки. В металлургии кислородно-конвертерный метод выплавки признан практически одним из самых эффективных по нескольким параметрам:
- Воспроизведение одного сталеплавильного агрегата превышает в мощности иные способы в несколько тон.
- В большегрузных конвертерах воспроизведение достигает порядка 500 тонн за 1 час.
- Затратные средства значительно ниже, чем при ином производстве.
- Довольно экономное обустройство любого цеха, даже в независимости от мощности плавильных агрегатов.
- Простота процесса состоит в автоматизации метода выплавки стали.
Благодаря тому, что используется чистый кислород, сталь, получаемая на выходе, не имеет высокого содержания азота. Это позволяет использовать материал в широких спектрах малой промышленности. Важно и то, что сравнительная безопасность для здоровья, позволяет задействовать специалистов среднего звена.
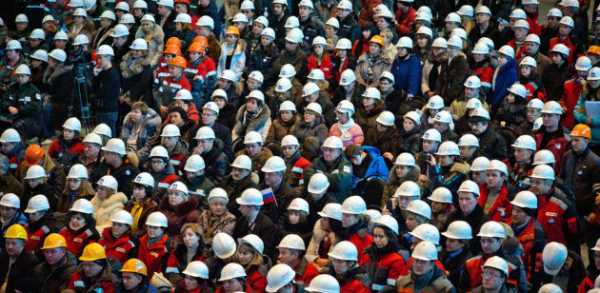
Возможность предоставить работу большему количеству населения
Особенности производства стали кислородно-конвертерным способом
Для создания стали подобным способом используется не только специальное оборудование.
В первую очередь необходимо учитывать технологические требования к подготовительным работам.
Неотъемлемой частью подобных работ является соблюдение техники безопасности. В обязательном порядке инженер по охране труда должен периодически инспектировать каждого занятого на производстве человека. При малейших изменениях условий труда необходимо проинструктировать каждого сотрудника.
Конвертерное производство посредством продувки кислородом происходит в несколько этапов:
- в конвертер загружается металлолом;
- заливается чугунное сырье;
- включается продувка содержимого конвертера кислородом;
- загружаются сливы стали, шлаки и шлакообразующие.
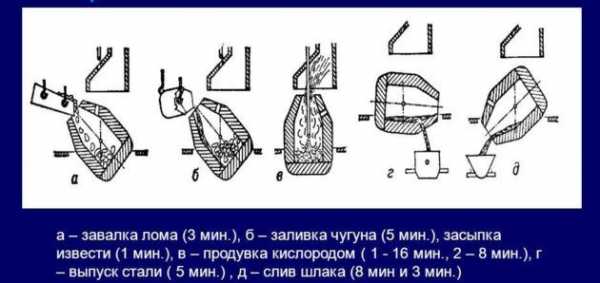
Процесс конвертерной выплавки стали
Каждый из этапов выполняется только в описанной последовательности с правильным учетом пропорций. В наклоненную конвертерную емкость лом любых видов металла загружается с помощью завалочных машин.
На следующем шаге специально установленные заливочные краны позволяют залить необходимое количество чугуна. После этого конвертер нужно установить вертикально и только затем начинать продувку кислородом. Частота которого не менее 99,5% О2.
Как только начинается продувка, важно загрузить часть шлаковых материалов. Весь объем которых, в том числе и железной руды, распределяется в несколько приемов. Важно соблюдать скорость их загрузки, но не позже чем через 5–7 минут после первого этапа выплавки.
Особенности и секреты процесса
От иных способов стального производства подобный метод отличается тем, что завязан на очень высоких скоростях. Весь метод, как правило, проходит буквально за 14–24 минуты. Высокие температуры позволяют задавать мгновенную скорость растворения извести в шлаковых содержимых.
Поэтому и выплавка стали в одном конвертере, включая весь процесс производства, не составляет более 30 минут. Важно отметить, что на качество основного процесса непосредственное влияние оказывает неравномерность окисления каждого из компонента, содержащегося в агрегате.
Ведущий принцип кислородно-конвертерного процесса обусловлен регулированием температурного режима и изменением количества продувок. Необходимое условие для эффективности выплавки – введение охладителей в качестве железной руды, металлолома, известняка.
Очистка пылевых отходов происходит при помощи котла-утилизатора. Все отходящие газы от процесса выплавки попадают в установку для их очистки. Все производство стали кислородным способом управляется мощными современными компьютерами.
Стоит отметить, что при донной продувке удельный объем готовой стали гораздо меньше, чем при верхней продувке. Именно при донном методе скорость получения готовой стали гораздо выше.
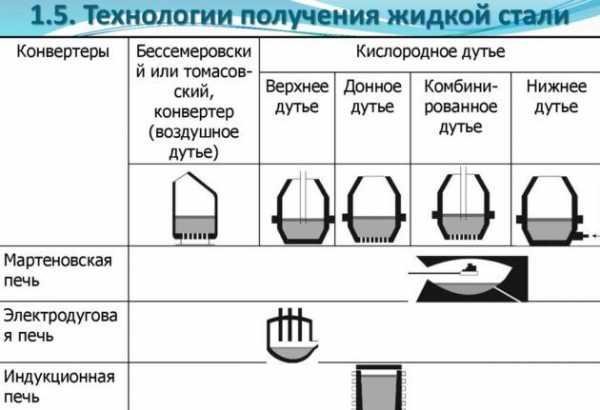
Технологии получения жидкой стали
К тому же что касается готового металла, то по окончании всех производственных работ результат эффективнее на 1–2%.
Дополнительно во время процесса сокращается длительность продувки, происходит ускорение плавления лома. Все это позволяет налаживать конкретный технологический процесс при меньшей высоте производственного здания.
Ведущие принципы выплавки качественной стали
Согласно статистическим показателям каждая десятая тонна выплавленной стали в мире получается в результате кислородно-конвертерного способа при донной продувке.
Весь процесс при низких производственных затратах и адекватных условиях для хода работ, способствует выплавки высококачественной стали. Уникальные технологические мощности конвертерных агрегатов позволяют использовать различные составы сплавов, кроме самого жидкого чугуна.
Определенный интерес в промышленности к этому способу вызван и широким его применением еще с 60-х годов прошлого столетия. Основной типовой ряд емкостей конвертерных агрегатов установлен еще при Советском Союзе. Огромные сосуды представлены в грушевидной форме и имеют объемный ряд от 50 до 400 тонн.
Необходимо отметить, на улучшение показателей готовой стали влияет именно размер конвертера. Оптимальный удельный объем кислородного конвертера способствует интенсивной подаче кислорода и предотвращению выбросов вспенивающихся шлаков и металлов.
Одним из ведущих принципов производства стали в кислородных конвертерах является их проектирование емкостью от 400 до 4,3 тыс. тонн и минимальной высотой 6–8 метров. Слишком низкие агрегаты провоцируют выбросы вспенивающегося металла через узкие горловины. Подобный факт негативно сказывается на всем процессе производства и на качестве самой стали на выходе.
Планирование процесса
Принципиально важно и перед каждой плавкой осуществлять детальное планирование всех оптимальных условий. Они включают в себя:
- расход чугуна и лома;
- уровень подачи кислорода в фурму;
- приблизительные расчеты по концентрации фосфора, серы и шлаков;
- анализ окончательной массы стали и заданных объемов отходов.
Удельная интенсивность выплавки стали кислородным способом в конвертерах позволяет производить высокие объемы сырья при минимальных нагрузках на ход процесса. Немаловажную роль здесь играет фактор проектирования и выбора сопутствующих условий, а также организации технологии производства.
Высококачественную сталь в стране получают не только на огромных заводах, но и на территории малых помещений, для эффективного производства требуется необходимая мощность агрегатов и квалифицированные специалисты.
Видео по теме: Основы кислородно конвертерного производства
promzn.ru
Качество кислородно-конвертерной стали
Качество стали определяется в значительной степени ее химическим составом и содержанием вредных примесей, газов и неметаллических включений. Особое внимание при производстве конвертерной стали уделяется получению металла с низким содержанием газов и прежде всего азота. Содержание азота в конвертерной стали определяется одновременным наложением ряда факторов: 1) содержанием азота в шихте; 2) чистотой кислорода, используемого для продувки ванны; 3) подсосом воздуха в полость конвертера. Подсос воздуха в конвертер, в свою очередь, зависит от многих факторов, основными из которых являются:
- Положение фурмы. При высоком расположении фурмы количество воздуха, эжектируемого при продувке из атмосферы цеха, возрастает.
- Сечение горловины. Чем больше размер горловины, тем больше подсос воздуха. По ходу кампании размер горловины изменяется, по мере разгара футеровки горловины и увеличения ее сечения подсос воздуха в конвертер возрастает.
- Метод утилизации тепла конвертерных газов. При работе с дожиганием между верхом горловины конвертера и нижней кромкой накрывающего конвертер камина засасывается некоторое количество воздуха, который расходуется на дожигание СО до СО2.
Часть этого воздуха попадает в полость конвертера и увеличивает содержание в ней азота. При работе без дожигания имеется возможность создать в верхней части конвертера небольшое положительное давление; подсос воздуха при этом практически исключается. Большое значение имеют чистота кислорода и условия ведения плавки.
На рисунке 1 представлены результаты исследований проф. Е. X. Шахпазова изменения содержания азота в металле по ходу продувки. Видно, что по характеру изменения содержания азота в металле время плавки можно разделить на два отрезка: 1) период деазотации и 2) период роста содержания азота в ванне.
Рисунок 1 — Содержание азота в металле (НЛМК ) в зависимости от содержания в нем углерода при концентрации азота в кислороде
1. Содержание азота в металле начинает интенсивно снижаться уже вмомент слива чугуна в конвертер и в первые минуты продувки, что связано в основном с выделением нитридов титана из жидкой части шихты. Затем по мере роста скорости окисления углерода решающим становится деазотация ванны пузырями СО. Содержание азота снижается до минимума примерно при достижении концентрации углерода в ванне < 1 % и далее остается почти постоянным до содержания углерода ~0,1 %. Минимальное содержание азота, достигаемое при содержании углерода 0,1 %, практически не зависит от чистоты дутья в интервале содержания азота в кислороде от 0,02 до 0,14 %. Видимо, в этот период минимальная концентрация азота определяется в основном развитием процессов обезуглероживания и десорбции азота в пузырях и исходным содержанием азота в шихте, т. е. в чугуне и ломе.
2. Рост содержания азота в металле начинается при снижении содержания углерода менее 0,1 %. В это время отмечено начало снижения скоростей обезуглероживания и количества азота, десорбированного пузырями СО. Постепенно, по мере снижения концентрации углерода в ванне и скорости его окисления, увеличивается скорость поступления азота в металл из газовой фазы. В этот период решающее значение имеют содержание азота в дутье и подсосы атмосферного воздуха. Влияние чистоты дутья четко прослеживается на рисунке 2.
Рисунок 2 — Зависимость содержания азота в металле от содержания азота в кислороде при количестве лома в шихте
Минимальная концентрация азота при [С] = 0,1% достигается в основном за счет регулирования содержания азота в шихте в зависимости от требуемого содержания азота путем изменения доли чугуна в шихте, замены части лома твердым чугуном, железорудными окатышами. Для уменьшения прироста содержания азота в заключительный период плавки нужно прежде всего исключить или свести к минимуму поступление атмосферного азота в струю. При снижении высоты фурмы с 1,5 до 0,9 м (по данным НЛМК) содержание азота в полупродукте снижается в среднем на 0,0015 %. Наряду с заглублением фурмы для более полного уменьшения подсоса воздуха в струю за 2—3 мин до окончания продувки (после снижения количества отходящих газов) эффективны небольшое вспенивание ванны и увеличение газообразования путем присадки до 1 т известняка. В этом случае струя практически защищена от воздуха и поступление азота в металл определяется его содержанием в дутье, т. е. поддается контролю. Исследования показали также, что при выплавке содержащей не более 0,004—0,005 % N стали на обычной шихте, т. е. при обычном количестве лома и недеазотированном чугуне, содержание азота в кислороде не должно превышать 0,05 об. %.
Поглощение азота при выпуске металла в значительной степени зависит от его окисленности. При содержании кислорода более 0,05 % поглощение азота невелико. Чем выше скорость слива металла из конвертера (чем меньше продолжительность выпуска плавки), тем меньше прирост концентрации азота за счет взаимодействия с воздухом.
Содержание кислорода в металле в момент окончания продувки определяется содержанием углерода. Однако в процессе продувки возможно переокисление металла, когда интенсивность подачи кислорода в ванну несколько превышает интенсивность его использования для окисления примесей. Степень этого переокисления невелика, и обычно за период времени от момента отключения подачи кислорода до момента выпуска (время, затрачиваемое на отключение кислорода и подъем фурмы, повалку конвертера, замер температуры, отбор пробы и т. д.) окисленность металла в результате того, что реакция окисления углерода продолжает идти и после отключения подачи кислорода, снижается до значений, соответствующих данному содержанию углерода.
Содержание водорода в конвертерной стали обычно невелико, так как ограничены источники его поступления в металл. Помимо водорода, поступившего в ванну вместе с шихтовыми материалами, основным источником водорода является влага, содержащаяся в кислороде, а также влага воздуха, подсасываемого в полость конвертера. Обычно содержание водорода в металле в конце продувки редко превышает 3—4см3/100г металла.
Однако в процессе выпуска и разливки в результате контакта с атмосферным воздухом содержание водорода в стали может несколько возрасти. В случае прогара кислородной фурмы охлаждающая фурму вода начинает поступать непосредственно в реакционную зону и содержание водорода в ванне заметно возрастает.
Содержание неметаллических включений в конвертерной стали определяется в основном технологией раскисления. Поскольку к концу операции при правильно организованном процессе металл не содержит повышенных количеств серы, кислорода и азота, создаются условия получения стали, содержащей незначительные количества сульфидных, оксидных и нитридных неметаллических включений. Количество их, остающееся в готовом металле, определяется технологией обработки металла в ковше и разливки.
metallurgy.zp.ua
Кислородно-конвертерный способ производства стали: виды и процесс
Около 70% стали от общего объема мирового производства изготавливается конвертерным способом. До середины прошлого столетия для получения стали применялись бессемеровский и томасовский процессы. Однако в дальнейшем сталь начали производить усовершенствованным кислородно-конвертерным способом. В настоящее время предшественники современного метода практически не применяются.
Суть конвертерного производства
В конвертерном производстве применяются специальные сталеплавильные агрегаты, называемые конвертерами. Производство стали осуществляется путем продувки жидкого чугуна воздухом или кислородом. Данный металл содержит различные примеси, в том числе кремний, углерод и марганец. Примеси окисляются под действием кислорода и удаляются из расплава. Основным преимуществом конвертерного способа является то, что для работы сталеплавильного устройства не требуется топливо. Сталь расплавляется под действием тепла, которое выделяют окисляющиеся примеси.
Принцип бессемеровского способа
Впервые массовое получение жидкой стали стало возможным в 1856 году благодаря Г. Бессемеру – изобретателю из Англии. Он придумал, как нагреть металл до температуры, превышающей 1500°С. Именно такая температура необходима для того, чтобы расплавить металл с пониженным содержанием углерода.
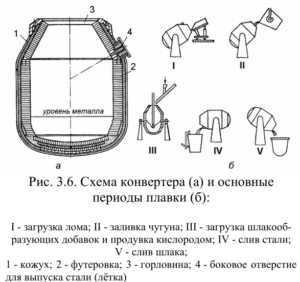
Схема конвертера и основные периоды плавки
Бессемеровский процесс предусматривает продувку расплава атмосферным воздухом. Для этих целей применяются конвертеры, у которых внутренняя часть камеры сгорания защищена динасовым кирпичом. Благодаря такой защите бессемеровский способ называют кислой футеровкой конвертера.
Плавка в бессемеровском сталеплавильном агрегате осуществляется путем заливки чугуна при температуре 1250–1300°С. Следует заметить, что для выплавки бессемеровских чугунов требуются железные руды с низким содержанием серы и фосфора.
Залитый чугун продувают воздухом, в результате чего происходит окисление углерода, марганца и кремния. При окислении образуются оксиды, формирующие кислый шлак. Продувку воздухом заканчивают после того, как углерод окислится до требуемых значений.
Далее металл через горловину сливают в ковш, попутно его окисляя. У такого способа присутствует один существенный недостаток, заключающийся в невысоком качестве конечного продукта, который получается слишком хрупким за счет неполного удаления серы и фосфора.
Принцип томасовского способа
В 1878 году англичанину С.Г. Томасу удалось устранить главный недостаток бессемеровского способа. Кислую футеровку конвертера он заменил основной. Внутренний защитный слой в ванной был выложен смолодоломитовым кирпичом. А чтобы удалить из металла большую часть примесей, он предложил использовать известь, функция которой заключалась в связывании фосфора.
Томасовский процесс позволил перерабатывать чугун с высоким содержанием фосфора. Поэтому наибольшее распространение данный способ получил в странах, где железные руды содержат много фосфора. Во всем остальном метод, изобретенный Томасом, мало чем отличается от предложенного Бессемером:
- и в том, и в другом случае используется сталеплавильный агрегат, в который чугун подается сверху через отверстие в горловине;
- через это же отверстие производится выпуск стали.
- снизу сталеплавильный агрегат снабжен съемным днищем, что позволяет заменять его по мере выработки определенного срока службы;
- дутье в полость сталеплавителя поступает через специальные сопла, расположенные в футеровке днища.
Как уже говорилось выше, слив стали производится через отверстие в горловине. Перевернуть многотонный агрегат позволяют цапфы в цилиндрической части конвертера. При томасовском процессе в сталеплавитель загружают известь, позволяющую получить основной шлак. Далее туда же заливают высокофосфористый чугун, нагретый до 1200–1250°С и подают дутье. При подаче дутья происходит окисление кремния, марганца и углерода. В основной шлак удаляются сера и фосфор. Продувка завершается тогда, когда содержание фосфора снизится до определенных показателей. Окончательным этапом, как и в бессемеровском процессе, является выпуск металла с последующим раскислением.
Принцип работы кислородного конвертера
Впервые кислородное дутье было запатентовано Г. Бессемером. Однако в течение продолжительного времени кислородно-конвертерный процесс не применялся, в связи с отсутствием массового производства кислорода. Первые опыты по продувке кислородом стали возможными в начале сороковых годов прошлого столетия.
Устройство кислородного конвертера осталось прежним:
- камера сгорания изнутри защищена основной футеровкой;
- однако вместо воздуха в нем применяется продувка кислородом;
- подача кислорода осуществляется через водоохлаждаемые сопла.
На территории России применяются сталеплавители с верхней подачей кислорода.
Особенностью конвертерного способа с кислородной продувкой является скоротечность. Весь процесс расплавления металла занимает десятки минут. Однако во время работы требуется тщательно отслеживать содержание в чугуне углерода, температуры его расплава и прочие параметры, чтобы вовремя прекратить продувку.
Процесс сталеплавильного производства упростился, когда кислородные конвертеры оснастили автоматическими системами, усовершенствовали лабораторную технику и измерительные приборы. Усовершенствование кислородно-конвертерного процесса позволило повысить производительность, снизить себестоимость металла и повысить его качество.
Современные кислородные конвертеры могут работать в трех основных режимах:
- с полным дожиганием окиси углерода;
- с частичным дожиганием ОС;
- без дожигания ОС.
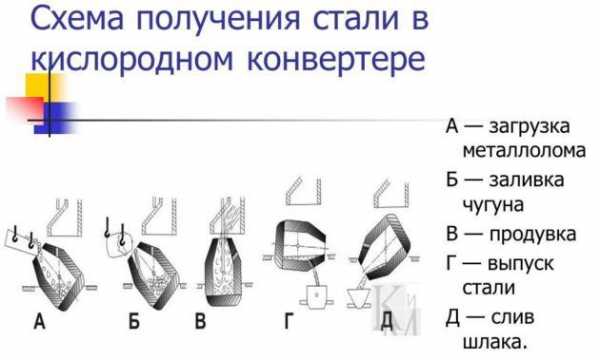
Схема получения стали в кислородном конвертере
Они позволяют производить сталь из чугуна различного состава.
Кислородный конвертер – описание процесса плавки
Кислородный конвертер – это стальной сосуд грушевидной формы. Его внутренняя часть защищена смолодоломитовым (основным) кирпичом. Вместимость сталеплавильного агрегата варьируется от 50 до 350 тонн. Сосуд распложен на цапфах и способен поворачиваться вокруг горизонтальной оси, что позволяет беспрепятственно заливать в него чугун, закладывать другие добавки и сливать металл со шлаком.
Чтобы получить конечный продукт, в конвертер заливается не только чугун, но и закладывают добавки. К ним относятся:
- лом металла;
- шлакообразующие материалы (железная руда, известь, полевой шпат, бокситы).
Конвертерный способ с кислородной продувкой предусматривает заливку в конвертер чугуна, нагретого до 1250–1400°С. Установив конвертер в вертикальное положение, в него подают кислород. Как только началась продувка, в расплавленный чугун вводят остальные компоненты, входящие в состав шлака. Перемешивание чугуна со шлаком осуществляется под действием продувки.
Так как концентрация чугуна гораздо выше, чем примесей, в процессе продувки происходит образование оксида железа, который растворяясь, обогащает металл кислородом. Именно растворенный кислород способствует уменьшению в металле концентрации кремния, углерода и марганца. А когда примеси окисляются, выделяется полезное тепло.
Особенностью основного шлака является большое содержание оксида кальция и оксида железа, которые в начале продувки способствуют удалению фосфора. Если же содержание фосфора превышает требуемый показатель, шлак сливают и наводят новый. Продувку кислородом заканчивают, когда содержание углерода в конечном продукте соответствует определенному параметру. После этого конвертер переворачивают и производят слив стали в ковш, куда добавляют раскислители и другие добавки.
Видео по теме: Основы кислородно конвертерного производства
promzn.ru