Станок детали – . —
alexxlab | 20.01.2021 | 0 | Вопросы и ответы
ТИПОВЫЕ ДЕТАЛИ И МЕХАНИЗМЫ СТАНКОВ
СТАНИНЫ И НАПРАВЛЯЮЩИЕ. Несущую систему станка образует совокупность его элементов, через которые замыкаются силы, возникающие между инструментом и заготовкой в процессе резания. Основные элементы несущей системы станка: станина и корпусные детали (поперечины, хоботы, ползуны, плиты, столы, суппорты и т.д.).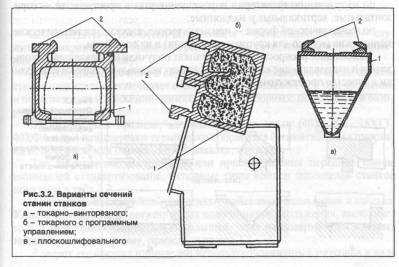
Станина 1 (рис.3.2) служит для монтажа деталей и узлов станка, относительно нее ориентируются и перемещаются подвижные детали и узлы. Станина так же, как и другие элементы несущей системы, должна обладать стабильностью своих свойств и обеспечивать в течение срока службы станка возможность обработки заготовок с заданными режимами и точностью. Это достигается правильным выбором материала станины и технологией ее изготовления, износостойкостью направляющих.
Основной материал для изготовления станин: чугун — для литых станин, сталь — для сварных, для изготовления станин тяжелых станков иногда применяют железобетон, для станков высокой точности — искусственный материал — синтегран, изготовляемый на основе крошки минеральных материалов и смолы и характеризующийся незначительными температурными деформациями.
Направляющие 2 (см.рис.3.2) обеспечивают требуемое взаимное расположение и возможность относительного перемещения узлов, несущих инструмент и заготовку. Направляющие для перемещения узла допускают только одну степень свободы движения благодаря конструкции.
По назначению и конструктивному исполнению направляющие классифицируют:
по виду движения — главного движения и движения подачи; направляющие для перестановки сопряженных и вспомогательных узлов, неподвиж¬ных в процессе обработки;
по траектории движения — прямолинейного и кругового движения;
по направлению траектории перемещения узла в пространстве — горизонтальные, вертикальные и наклонные;
по геометрической форме — призматические, плоские, цилиндрические конические (только для кругового движения) и их сочетания.
Наибольшее распространение в станках получили направляющие скольжения и направляющие качения, в последних используют шарики или ролики в качестве промежуточных тел качения.
Материал для изготовления направляющих скольжения (рис.3.3) — серый чугун. Он используется в тех случаях, когда направляющие изготовляют как одно целое со станиной. Износостойкость направляющих повышают поверхностной закалкой с твердостью HRC3 42-56.
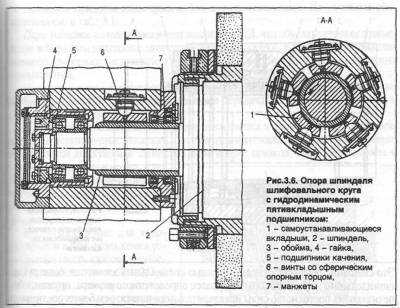
Стальные направляющие выполняют накладными, обычно закаленными с твердостью HRC3 58-63. Чаще всего используют сталь 40Х с закалкой ТВЧ, пали 15Х и 20Х с последующей цементацией и закалкой.
Надежная работа направляющих зависит от защитных устройств, предохраняющих рабочие поверхности от попадания на них пыли, стружки, грязи (рис.3.4). Защитные устройства изготовляют из различных материалов, в том числе полимерных.
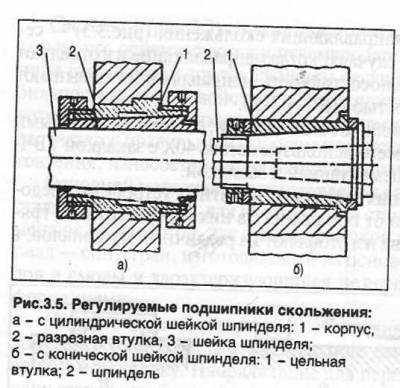
ШПИНДЕЛИ И ИХ ОПОРЫ. Шпиндель — разновидность вала, — служит для закрепления и вращения режущего инструмента или приспособления, несущего заготовку.
Для сохранения точности обработки в течение заданного срока службы станка шпиндель обеспечивает стабильность положения оси при вращении поступательном движении, износостойкость опорных, посадочных и базирующих поверхностей.
Шпиндели, как правило, изготавливают из стали (40Х, 20Х, 18ХГТ, 40ХФА и др.) и подвергают термической обработке (цементации, азотиров¬нию, объемной или поверхностной закалке, отпуску).
Для закрепления инструмента или приспособления передние концы шпинделей стандартизованы. Основные типы концов шпинделей станков показаны в табл.3.2.
В качестве опор шпинделей применяют подшипники скольжения и качения. Конструктивная схема регулируемых коническую форму, приведена на рис.3.5.
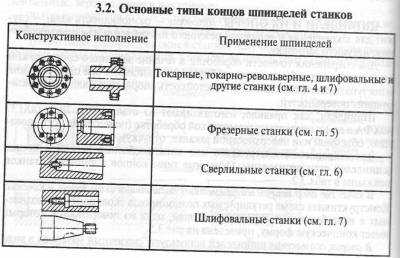
В опорах скольжения шпинделей используют смазочный материал в виде жидкости (гидростатические и гидродинамические) или газа (аэродинамические и аэростатические) подшипников скольжения, выполняемых в виде бронзовых втулок-вкладышей, одна из поверхностей которых имеет.
Гидродинамические подшипники выполняются одно- и многоклиновыми. Одноклиновые наиболее просты по конструкции (втулка), но не обеспечивают стабильного положения шпинделя при больших скоростях скольжения и малых нагрузках. Этот недостаток отсутствует в многоклиновых подшипниках, имеющих несколько несущих масляных слоев, охватывающих шейку шенделя равномерно со всех сторон (рис 3 6).
Гидростатические подшипники – подшипники скольжения, в которых масляный слой между трущимися поверхностями создается путем подвода к ним масла под давлением от насоса, – обеспечивают высокую точность положения оси шпинделя при вращении, имеют большую жесткость и обеспечивают режим жидкостного трения при малых скоростях скольжения
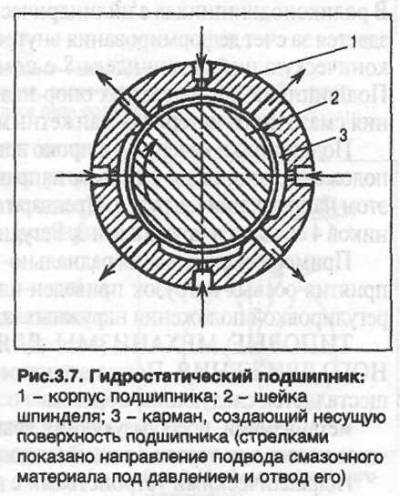
Подшипники с газовой смазкой (аэродинамические и аэростатические) по конструкции подобны подшипникам гидравлическим, но обеспечивают меньшие потери на трение. Эта особенность позволяет применять такие подшипники в опорах быстроходных шпинделей.
Подшипники качения в качестве опор шпинделей широко применяют в ланках разных типов. В связи с повышенными требованиями к точности вращения шпинделей в их опорах применяют подшипники высоких классов точности, устанавливаемые с предварительным натягом, который позволяет устранить вредное влияние зазоров. Натяг в радиально-упорных шариковых и конических роликовых подшипниках создается при их парной установке благодаря осевому смещению внутренних колец относительно наружных.
Это смещение осуществляется с помощью специальных элементов конструкций шпиндельного узла — проставочных колец определенного размера; пружин, обеспечивающих постоянство силы предварительного натяга; резьбовых соединений. В роликоподшипниках с цилиндрическими роликами предварительный натяг создается за счет деформирования внутреннего кольца 6 (рис.3.8) при затяжке его на коническую шейку шпинделя 8 с помощью втулки 5, перемещаемой гайками L Подшипники шпиндельных опор надежно защищены от загрязнения и вытекания смазочного материала манжетными и лабиринтными уплотнениями 7.
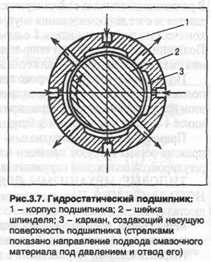
Подшипники качения 4 широко используют в качестве упорных, фиксирующих положение шпинделя в осевом направлении и воспринимающих возникающее в этом направлении нагрузки. Предварительный натяг шариковых упорных подшипников 4 создается пружинами 3. Регулирование пружин осуществляется гайками 1
Пример использования радиально-упорных шариковых подшипников для вос¬приятия осевых нагрузок приведен на рис.3.6. Предварительный натяг создается регулировкой положения наружных колец подшипников 5 с помощью гайки 4.
ТИПОВЫЕ МЕХАНИЗМЫ ДЛЯ ОСУЩЕСТВЛЕНИЯ ПОСТУПАТЕЛЬНОГО ДВИЖЕНИЯ. Поступательное движение в рассматриваемых станках осу¬ществляется следующим образом:
механизмами, преобразующими вращательное движение в поступательное — зубчатое колесо или червяк с рейкой, ходовой винт — гайка и другие механизмы;
гидравлическими устройствами с парой цилиндр — поршень;
электромагнитными устройствами типа соленоидов, используемыми в ос¬новном в приводах систем управления.
Приведем примеры некоторых из указанных механизмов. Их условные обо¬значения см. в табл.3.1.
Пара зубчатое колесо-рейка имеет высокий КПД, что обуславливает ее применение в большом диапазоне скоростей движения рейки, в том числе в приводах плавного движения, передающих значительную мощность, и вспомогательных перемещений.
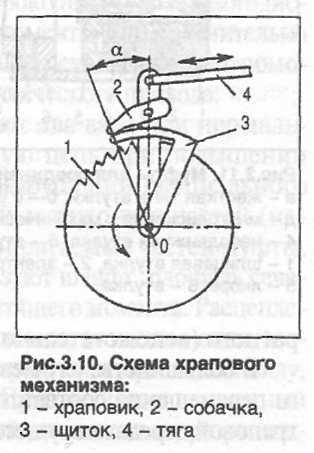
Червячно-реечная передача отличается от пары зубчатое колесо — рейка повышенной плавностью движения. Однако эта передача сложнее в изготовлении и имеет более низкий КПД.
Механизм ходовой винт-гайка широко применяется в приводах подач, вспомогательных и установочных движений. Он обеспечивает: малое расстояние, на которое перемещается движущийся элемент за один оборот привода; высокую плавность и точность перемещения, определяемую главным образом точностью изготовления элементов пары; самоторможение (в парах винт — гайка скольжения).
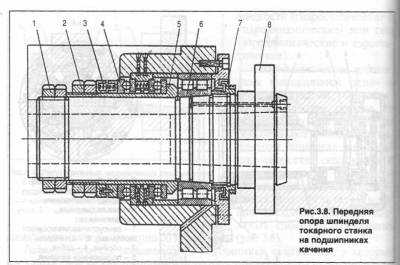
В станкостроении для ходоки винтов и гаек скольжения установлено шесть классов точности: 0 — наиболее точный; 1,2,3,4 и 5-й классы, которыми регулируются допустимые отклонения по шагу, профилю, диаметрам и пo параметру шероховатости поверхности. Конструкция гаек зависит от назначения механизма. В связи с низким КПД пары ходовой винт — гайка скольжения заменяют винтовыми парами качения (рис.3.9). В этих парах устраняется износ, уменьшаются потери на трение и могут быть устранены зазоры за счет создания предвари¬тельного натяга.
Недостатки, присущие парам винт — гайка скольжения и винт — гайка качения, связанные с особенностями их эксплуатации и изготовления, исключены в гидростатической передаче винт — гайка. Пара работает в условиях трения со смазоч¬ным материалом; КПД передачи достигает 0,99. Масло подается в карманы, выполненные на бо¬ковых сторонах резьбы гайки.
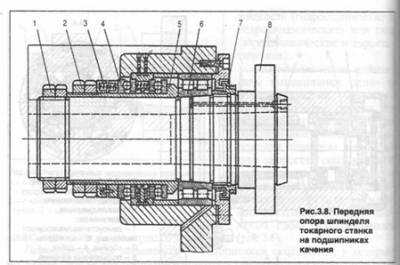
ТИПОВЫЕ МЕХАНИЗМЫ ДЛЯ ОСУЩЕСТВЛЕНИЯ ПЕРИОДИЧЕСКИХ ДВИЖЕНИЙ. Для некоторых станков рабочий процесс построен таким образом, что для его осуществления требуется периодическое перемещение (изменение положения) отдельных узлов или элементов станка.
Периодические движения могут осуществляться храповыми и мальтийскими механизмами, механизмами кулачковыми и с муфтами обгона, электро-, пневмо, и гидромеханизмами.
Храповые механизмы (рис.3.10) наиболее часто используют в механизмах подачи станков, в которых периодическое перемещение заготовки, режущего (резца, шлифовального круга) или вспомогательного (алмаз для правки шлифовального круга) инструмента производится во время перебега или обратного (вспомогательного) хода (в шлифовальных и других станках).
В большинстве случаев храповые механизмы используют для прямолинейного перемещения соответствующего узла (стола, суппорта, пиноли). С помощью храповой передачи осуществляют также и круговые периодические перемещения.
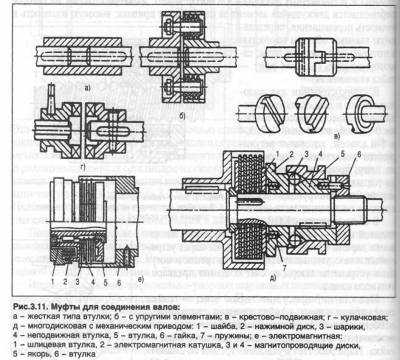
Муфты служат для соединения двух соосных валов. По назначению различают муфты нерасцепляемые, сцепляемые и предохранительные.
Нерасцепляемые муфты (рис.3.11, а, б, в) служат для жесткого (глухого) соединения валов. Например, соединения с помощью втулки, через упругие элементы или через промежуточный элемент, имеющий на торцовых плоскостях два взаимно перпендикулярных выступа и позволяющий компенсировать несоосность соединяемых валов.
Сцепляемые муфты (рис.3.11, г, д, е) применяют для периодического соединения валов. В станках используют сцепляемые кулачковые муфты в виде дисков с торцовыми зубьями-кулачками и зубчатые муфты. Недостатком таких сцепляемых муфт является трудность их включения при большой разнице в угловых скоростях ждущего и ведомого элементов. Фрикционные муфты не имеют недостатка, присущего кулачковым муфтам, и позволяют включить их при любых скоростях вра-
щения ведущего и ведомого элементов. Фрикционные муфты бывают конусные и дисковые. В приводах главного движения и подачи широко применяют многодисковые муфты, передающие значительные крутящие моменты при сравнительно небольших габаритах. Сжатие ведущих дисков с ведомыми осуществляется с помощью механического, электромагнитного и реже гидравлического привода.
Предохранительные муфты (рис.3.12), соединяют два вала при нормальных условиях работы и разрывают кинематическую цепь при повышении нагрузки. Разрыв цепи может происходить при разрушении специального элемента или путем проскальзывания сопрягаемых и трущихся частей (например, дисков) или расцепления кулачков двух сопрягаемых частей муфты.
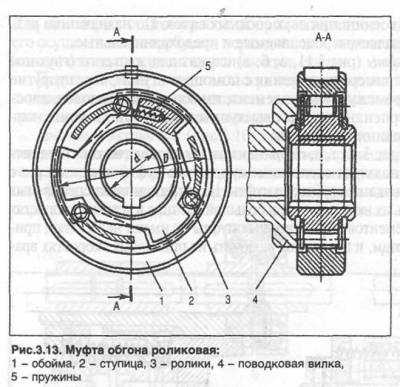
В качестве разрушаемого элемента обычно используют штифт, площадь сечения которого рассчитывают на передачу заданного крутящего момента. Расцепление сопрягаемых элементов муфты происходит при условии, что осевая сила, возникающая на зубьях, кулачках 1 или шариках 5, при перегрузках превышает силу, создаваемую пружинами 3 и регулируемую гайкой 4. При смещении подвижный элемент 2 муфты воздействует, например, на концевой выключатель, разрывающий электрическую цепь питания двигателя привода.
Муфты обгона (рис.3.13) предназначены для передачи крутящего момента при вращении звеньев кинематической цепи в заданном направлении и для разъединения звеньев при вращении в обратном направлении, а также для передачи валу различных по частоте вращений (например, медленного — рабочего вращения и быстрого —
вспомогательного. Муфта обгона позволяет передавать дополнительное (быстрое) вращение без выключения основной цепи. В станках наиболее широко применяют муфты роликового типа. Эта муфта может передавать крутящий момент в двух направлениях.
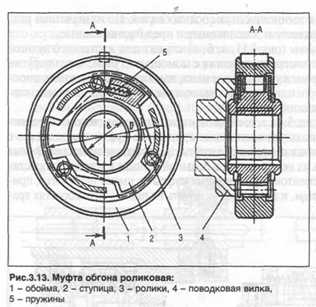
В качестве муфт обгона используют также храповые механизмы.
Автор – nastia19071991
mgplm.org
Рекомендуем приобрести: Установки для автоматической сварки продольных швов обечаек – в наличии на складе! Сварочные экраны и защитные шторки – в наличии на складе! В процессе резания металлов действует сила резания. Со стороны режущего инструмента она приложена к сечению среза, а следовательно, к детали и затем к станку. Со стороны сечения среза она приложена к резцу, суппорту и следовательно, также к станку. Таким образом, при резании образуется замкнутая упругая система станок — деталь — инструмент, находящаяся под воздействием силы резания. В связи с этим все элементы системы упруго деформируются, что является одной из причин появления погрешностей обработки. Это можно показать на следующих примерах. Пусть валик (фиг. 2) консольно закреплен в патроне токарного станка. Упруго деформируясь под действием силы резания, приложенной к нему со стороны резца, он изогнется подобно тому, как изгибается под действием груза консольная балка. Деформируются также шпиндель станка и его опора. В результате деформации ось валика у конца вылета его удалится от нормального положения в радиальном направлении, т. е. в направлении оси у, на величину у Фиг. 2. Погрешности обработки, возникающие в связи с упругими деформациями при обработке детали, зажатой в патроне консольно. Вследствие упругих деформаций валик, обточенный в центрах станка, примет бочкообразную форму (фиг. 3, а), особенно если длина его больше десятикратного значения диаметра Если обтачиваемый вал более жесткий, нежели его опоры — шпиндель и пиноль задней бабки,— то после обточки он может принять так называемую корсетную форму (фиг. 3, б). Обработанное на расточном станке отверстие получится коническим (фиг. 3, в), так как по мере увеличения вылета консоли шпинделя жесткость его уменьшается, а величина упругих отжатий возрастает. Фиг. 3. Погрешности обработки, возникающие в связи с упругими деформациями: а — при обработке нежесткой детали в жестких центрах: б — при обработке жесткой детали при малой жесткости опор-центров; в — при расточке отверстия оправкой, жесткость которой уменьшается при увеличении вылета оправки. Упругие деформации пропорциональны нагрузкам: чем больше нагрузка, в данном случае сила резания, тем больше упругие деформации. Поэтому, если величина припуска на обработку на отдельных участках поверхности детали будет различной, то при обработке возникнут дополнительные погрешности формы и размеров. Это объясняется тем, что в местах с большим припуском будет больше сила резания и упругое отжатие. Упругими отжатиями обусловливается явление копирования погрешностей формы заготовки, т. е. перенесение этих погрешностей на обработанную деталь. Например, вал (фиг. 4,а), заготовка которого имеет неодинаковый припуск на диаметр по длине (z 1<z2), после обточки получит ступенчатую форму (D1<D2). При неодинаковом припуске по окружности поперечные сечения будут искажены (фиг. 4, б). Профрезерованная на станке деталь с непостоянным припуском по длине будет иметь после обработки искажения, которые называют неплоскостностью и непрямолинейностью. Фиг. 4. Погрешности обработки, возникающие в связи с неодинаковой величиной припуска на обработку. Искажения формы и размеров возникают также при непостоянной твердости металла заготовок, так как на участках с большей твердостью величина упругих деформаций возрастает. При механической обработке детали погрешности формы и размеров заготовки значительно уменьшаются. Это явление принято называть уточнением. Отношение величины погрешности формы и размеров заготовки к соответствующей погрешности, перенесенной на деталь, называют коэффициентом уточнения. При нормальных условиях работы коэффициент уточнения колебнется в пределах 20—100. Величина упругих отжатий зависит также от степени затупления режущих инструментов и их геометрии. При затуплении режущего инструмента сила резания возрастает, и радиальная составляющая ее может достичь двукратного увеличения. В такой же мере возрастет величина радиального упругого отжатия и соответственно связанная с этим погрешность. Из геометрических элементов режущих инструментов на величину упругих отжатий наиболее существенно влияют главный угол в плане и передний угол. С уменьшением главного угла в плане радиальная составляющая Рy и величина радиального отжатия возрастают. Например, если уменьшить главный угол в плане резца с 90 до 45°. то радиальная составляющая Рy увеличится в два раза. При увеличении переднего угла сила резания и упругие отжатия уменьшаются. Причины, обусловливающие погрешности, связанные с упругими деформациями, рассмотрены независимо друг от друга. Однако в процессе резания они возникают одновременно и взаимодействуя, определяют общую величину погрешности от упругой деформации. Установлено, что величина ее может достигать больших значений и составлять до 80% общей погрешности обработки. Влияние упругих отжатий на точность обработки может быть значительно уменьшено повышением жесткости системы. Жесткость системы — это способность ее сопротивляться деформациям под действием нагрузки — силы резания. Фиг. 5. Влияние на точность обработки упругих отжатий х и z. Величину упругого отжатия, возникающего под действием силы резания, можно представить как геометрическую сумму отжатий z, у и х в направлении действия составляющих Рz, Рy, и Рx. Эти отжатия влияют па точность обработки неодинаково: влияние отжатия х всегда равно нулю; влияние отжатия z весьма незначительно и сказывается лишь при точении. Приращение диаметра ΔD (фигура 5) значительно меньше отжатия z. Приращение размера, т. е. погрешность, возникающая в связи с отжатием у, равно величине отжатия; при точении приращение диаметра равно 2у. Это объясняется тем, что отжатие у направлено перпендикулярно к обработанной поверхности, а отжатия х и z — касательно к ней. Следовательно, наибольшее влияние на точность обработки оказывает упругое отжатие у. Поэтому под жесткостью системы понимают в первую очередь жесткость ее в радиальном направлении. Если сила, действующая в этом направлении, равна Р j=Py/y кг/мм. При Рy, равном, например, 500 кг, и у=0,1 мм j=500/0,1=5000 кг/мм; при у=0,05 мм и том же значении Py получим j=500/0,05=10 000 кг/мм. Следовательно, чем больше жесткость системы, тем меньше ее деформации и связанные с ними погрешности обработки. Жесткость системы определяют экспериментально или теоретически. Пользуясь данными, характеризующими жесткость системы, во многих случаях можно заранее определить величину погрешности или, наоборот, задавшись допустимой величиной погрешности, определить режимы резания и число необходимых для этого проходов. Увеличить жесткость системы — это значит увеличить жесткость станка, детали, инструмента, приспособления. Необходимая жесткость станка предусматривается конструкторами при проектировании его. Она определяется не только величиной поперечных сечений основных деталей станка, но и качеством подгонки соединений, величиной зазоров в опорах, стыках, соединениях и т. д. В процессе эксплуатации качество соединений ухудшается, величина зазоров увеличивается. Поэтому их следует тщательно регулировать и восстанавливать при ремонте При наладке станков для увеличения жесткости системы следует стремиться максимально уменьшать вылеты пинолей, патронов и других деталей. Жесткость детали увеличивают применением подвижных и неподвижных люнетов, направляющих втулок, уменьшением вылета детали при закреплении ее в патроне и т. д. Жесткость фрезерных станков увеличивают, скрепляя кронштейнами консоли столов с хоботами и станинами. С целью увеличения жесткости инструмента следует стремиться к уменьшению его вылета и к увеличению поперечных сечений державок и оправок. На фрезерных станках следует стремиться к уменьшению расстояний между опорами оправок для фрез. Увеличение жесткости системы наиболее эффективно влияет на снижение погрешностей от деформаций. Оно также уменьшает возможность возникновения в процессе резания вибраций Однако на практике бывает и так, что все возможности по увеличению жесткости системы использованы, а результаты обработки получаются все еще неудовлетворительными. В этих случаях следует сначала выяснить, что является причиной неудовлетворительной точности обработки, а затем попытаться подобрать наиболее рациональный способ либо устранения, либо уменьшения ее влияния. Точность обработки повышается при уменьшении неравномерности припуска на заготовках, неравномерности твердости заготовок и при уменьшении затупления режущего инструмента. Чтобы уменьшить погрешности, необходимо установить допустимую при данных условиях величину износа инструмента. Принудительная смена его после установленного срока работы или после обработки определенного количества деталей является лучшим способом устранения погрешностей, обусловленных затуплением. Кроме того, принудительной сменой достигается удлинение срока службы инструмента. Иногда бывает целесообразно изменить геометрию режущих инструментов, увеличив передние углы и главные углы в плане. Необходимую точность обработки можно получить увеличением числа проходов. Если коэффициент уточнения в этом случае равен n (например n = 30), то при двукратном проходе величина уточнения равна n Не все из методов, кроме метода увеличения жесткости системы, могут быть одинаково эффективно применены для повышения точности обработки. Наряду с положительным влиянием, применение многих из них дает и отрицательные результаты. Например, увеличение степени точности заготовок на предшествующих операциях требует дополнительных затрат труда на этих операциях; увеличение главного угла в плане и переднего угла вызывает уменьшение стойкости инструмента, увеличение количества настроек и, следовательно, приводит к снижению производительности труда. Увеличение количества проходов также связано с дополнительными затратами труда. Знакомство с особенностями каждого из методов, с их достоинствами и недостатками дает возможность творчески применять их на практике с целью достижения наибольшей производительности труда. В.И. Ишуткин. Настройка металлорежущих станков. Машгиз. 1960. |
www.autowelding.ru
Детали ЧПУ станков – изготовление деталей ЧПУ
ИЗГОТОВЛЕНИЕ ДЕТАЛЕЙ ИЗ ПОЛИМЕРОВ ДЛЯ СТАНКОВ ЧПУ
На нашем предприятии для изготовления деталей для ЧПУ мы используем современные станки с числовым программным управлением, чем обеспечивается высокая точность выполнения, что впрочем, было бы невозможно без соответствующей исполнительной части. Высокая подвижность резца, сверла или другого исполнительного инструмента сочетается с возможностью его перемещения на любые расстояния в пределах технологического процесса, вплоть до нескольких микрон.
Именно поэтому наши детали изготавливаются на таких станках. Они достаточно индивидуальны и к ним не подходят шаблонные образцы. Благодаря этому изделия, сделанные на этих станках, являются более точными.
Станок полностью находится на программном управлении. Это значит, что запуск системы, проверка рабочего процесса и регулировка условий происходит полностью под контролем программы. ЧПУ-станок значительно ускоряет работу производства деталей, а это уже поможет вам быстрее приобрести необходимые для вашего предприятия комплектующие.
Особенности
Станки с ЧПУ обладают большим преимуществом перед другими благодаря своей автоматизации. Они обладают высокой точностью, и у них практически отсутствует возможность сбоя производства или брака. Точность изготовления и обработки деталей достигается благодаря особой жесткости станка, которая гораздо больше, чем жесткость любых других подобных механизмов. Стоит отметить удобство загрузки сырья и выгрузки готового продукта.
Где можно купить
Наше предприятие занимается выпуском изделий, сделанных на станках с ЧПУ. Мы предлагаем изготовление опытных партий, а также серийное производство из полимеров по техническому заданию заказчика. На всю продукцию распространяются гарантийные обязательства. Уточнить информацию и сделать заказ Вы можете, связавшись с нашим менеджером по указанному ниже номеру телефона.
Похожие статьи:plastmass-group.ru
Запчасти на токарный станок
Наиболее распространенный метод при обработке металлов резанием – это токарная обработка. Цель такого метода снятие лишнего метала с детали-заготовки, путем вращения заготовки на токарном станке. При этом специальным резцом срезается лишний метал в виде стружки, и деталь доводится до конечного состояния.
Токарный станок служит также для нарезания наружной и внутренней резьбы, изготовления рифлений, сверления, зенкеровки, развертывания отверстий, а также других видов работ.
Наиболее распространенное изготовление таких деталей типа тел вращения как, валы, диски, оси, фланцы, втулки, гайки, муфты, кольца и многие другие детали. Принцип обработки заключается в следующем, станок сообщает заготовке вращение, а режущему инструменту движение относительно нее. Благодаря разным режимам и движениям заготовки и резца происходит процесс резания. Материалы, которые поддаются такой обработке разные по своей структуре, химического состава, механического воздействия, плотности и массе.
Нередко при работе из строя выходят патроны для токарных станков. Они имеют особенное строение и форму и существенно отличаются от патронов, например сверлильных станков, так как размещены вертикально и имеют намного, большие размеры. Токарные патроны способны зажимать деталь любого диаметра, все зависит от размеров и мощности самого станка. Патроны для токарных станков, имеют довольно сложное строение внутри, а наличие пружин в подвижных кулачках практически всегда является первой причиной поломки. Также это может сопровождаться и другими не менее неприятными износами деталей. Например, разбитием задней втулки, зазор для ключа патрона, износ подшипника, повреждения кулачков, все эти поломки следствие достаточно высоких оборотов станка.
Запчасти на токарный станок не являются сложностью в наше время, так как рынок может предложить достаточное количество, все зависит от станка и поломки. Их можно приобрести, начиная от обычного рынка и заканчивая онлайн заказом в интернет магазине. Поэтому в любой момент каждый желающий может найти именно то, что ему нужно для проведения ремонта оборудования. Широкий выбор позволяет найти оптимальное соотношение цены и качества, а также приобрести запчасти определенного производителя, которому более всего доверяют. После оформления заказа вам доставят в кратчайшие сроки любые запчасти на токарный станок, начиная с маленького болтика и заканчивая длинным шпинделем.
omashinostroenie.com
Деталь – станок – Большая Энциклопедия Нефти и Газа, статья, страница 1
Деталь – станок
Cтраница 1
Деталь станка, входящая в зацепление с ходовой гайкой и обеспечивающая в паре с ней прямолинейное движение поперечной или продольной подачи разл. [1]
Деталь станка с конусным концом, который служит для поддержки вращающихся заготовок при их обработке. [2]
Деталей станка является необходимым условием для наиболее полного использования деталей по долговечности. [3]
Какая деталь станка передает вращательное движение инструменту. [5]
Износ деталей станка в процессе длительной работы понижает точность станка и влияет на точность обработки. Планово-предупредительный ремонт имеет целью поддержание регламентированной точности станка и обеспечение точности обработки. Станки, выходящие из капитального ремонта, должны соответствовать по точности ГОСТам на новые станки. [6]
Износ деталей станка в процессе длительной работы понижает точность станка и влияет на точность обработки. Планово-предупредительный ремонт имеет целью поддержание регламентированной точности станка и обеспечение точности обработки. Станки, выходящие из капитального ремонта, должны соответствовать по точностям ГОСТам на новые станки. [7]
Износ деталей станка в процессе длительной работы понижает точность станка и влияет на точность обработки. Планово-предупредительный ремонт имеет целью поддержание регламентированной точности станка и обеспечение точности обработки. [8]
Износ деталей станка в значительной мере зависит от содержания станка в чистоте и регулярности его промывки и смазки. Наличие абразивной пыли повышает износ трущихся поверхностей деталей станка. [9]
Жесткость детали станка влияет на точность его работы. [10]
Расчет деталей станка на статическую прочность при действии постоянной нагрузки осуществляется по общеизвестным формулам сопротивления материалов. При расчете деталей станков основными показателями, характеризующими механические свойства материала, являются пределы текучести от и пределы прочности ав при растяжении. [11]
Нагрев деталей станка вследствие трения также оказывает влияние на точность механической обработки. Особенно сильно эго влияние проявляется в начале работы, после пуска станка, когда температура деталей станка еще не установилась. Наиболее чувствительными к изменению температуры являются шпиндели резьбошлифэ-вальных станков. [12]
Нагрев деталей станка вследствие трения также оказывает влияние на точность механической обработки. Особенно сильно это влияние проявляется в начале работы, после пуска станка, когда температура деталей станка еще не установилась. Наиболее чувствительными к изменению температуры являются шпиндели резьбошлифовальных станков. Пока шпиндель и подшипник не нагрелись до определенной температуры, зазор между ними не соответствует той величине, на которую он был отрегулирован при установившейся температуре, и поэтому шпиндель работает ненормально, что отражается на точности работы станка и качестве обрабатываемой поверхности. [13]
Узлы и детали станка располагаются на вертикальной раме, которую уста – навливают на полу или закрепляют на стене. На станке имеется шесть откидывающихся люлек. Каждое гнездо люльки оборудуется головкой и краном переключения коммуникаций. [14]
Если же детали станка в процессе работы нагреты до 200 С, масляная пленка, которая прочно охватывает поверхность детали, разрушается и износ трущихся поверхностей увеличивается, что неизбежно приведет к катастрофическому износу сопрягаемых деталей, а следовательно, и к поломке механизмов станка. [15]
Страницы: 1 2 3 4
www.ngpedia.ru
Строповка корпусных деталей станков и оборудования
Строительные машины и оборудование, справочник
Строповка корпусных деталей станков и оборудования
Категория:
Строповка грузов
Строповка корпусных деталей станков и оборудования
Строповка уникальных деталей (станин прокатных станов, траверс мощных прессов, дробилок и других деталей, масса которых превышает 75 т) иногда и не сложна, но трудоемка в связи с их большой массой. Строповку очень тяжелых изделий выполняют стальными канатами диаметром 50—65 мм на несколько ветвей, а поднимают их чаще двумя кранами. При строповке станины прокатного стана в обычном положении (масса 136 т) для обвязки ее применяют стальной строп диаметром 62 мм из восьми ветвей, из которых четыре ветви охватывают горловину, а остальные— цапфы. В горловину станины с двух сторон вставлены втулки с радиусными закруглениями, выполняющие функцию подкладок под стропы. Чтобы подкладки не выпали в момент подъема или кантования, их скрепляют. Деталь транспортируют двумя кранами.
При строповке станины с помощью коромысла к последнему приваривают скобы для центрирования стропов. Для уменьшения изгибающего момента коромысла под него подкладывают переходное кольцо с внутренним диаметром, меньшим, чем диаметр горловины.
Строповку, транспортирование и кантование уникальных изделий необходимо выполнять по заранее разработанным технологическим схемам опытным стропальщикам под непосредственным руководством инженерно-технических работников.
Строповку машин и оборудования нужно производить за самые надежные места и, в первую очередь, за имеющиеся в нем специальные захватные устройства: проушины, крюки, цапфы, рымы и т. п. Если несколько механизмов смонтировано на общей раме, то весь узел нужно поднимать за нее. При строповке машин и оборудования особое внимание следует уделять устойчивости и равновесию их во время подъема, транспортирования и установки на место. Машины и оборудование, снабженные инструкциями, паспортами, в которых указаны места зацепки груза, стропят в соответствии с предписываемой технологией.
Электродвигатели, редукторы, вентиляторы и другие узлы, машины и оборудование, снабженные рымами, проушинами, цапфами, стропят за эти приспособления облегченными или групповыми стропами. При подъеме вентилятора, смонтированного на одной раме с электродвигателем, главный строп нужно зацепить за вентилятор, а вспомогательный — за электродвигатель, чтобы уравновесить груз.
Рис. 1. Строповка оборудования, станков и узлов: а — станины прокатного стана в горизонтальном положении; б— то же, за стойку; в — станины прокатного стана в вертикальном положении; г — электродвигателя за рым; д — строгального станка; е — редуктора с электродвигателем в сборе за рымы; ж — редуктора за цапфы; з — компрессора; и — приводного вала; к — контейнера на поддоне; л — токарно-револьверного станка; м — фильтра холодильника; н, о, п — сверлильного, фрезерного и шлифовального станков; р — грузового автомобиля с помощью траверсы
Поперечно-строгальный станок стропят за его ползун. Обвязанный таким образом станок хорошо уравновешен, а ползун, являясь надежной частью станка, обеспечивает безопасность подъема. При строповке токарного станка основной строп с коромыслом, опущенным под станину станка, крепят в точке, немного смещенной от центра тяжести вправо, к задней бабке, а дополнительный — к передней бабке за выступающую часть шпинделя или за вставленный в него штырь.
Строповку компрессора массой 900 кг производят за основание по центру тяжести двумя облегченными стропами. Поскольку центр тяжести агрегата находится значительно выше места захвата, то транспортирование его в таком виде опасно: груз неустойчив, поэтому вверх компрессор привязывают дополнительным стропом к ветвям основного стропа. Дополнительный строп следует применять во всех случаях, когда груз неустойчив и когда невозможно выполнить крепление выше центра тяжести.
Цилиндрические детали, например приводной вал дробилки, фильтр холодильника, устанавливаемые на железнодорожные платформы вместе с деревянными рамами-прокладками, стропят облегченными или универсальными стропами простым обхватом или петлей-удавкой непосредственно за деталь.
Машины и оборудование в упаковке стропят за рамы упаковки способом обвязки универсальными или облегченными стропами. В большинстве случаев рама упаковки несет незначительные изгибающие нагрузки, так как принимает ее вместе с находящимся в таре грузом и работает, главным образом, на сжатие. На упаковке часто делают пометки центра тяжести груза и точек застропки, обязательно указывается масса груза (нетто) и общая масса с тарой (брутто).
Машины и станки — наиболее разнообразный тип грузов. поэтому строповку их выполняют универсальными стропами. Их используют для подъема сверлильных, фрезерных, шлифовальных и других станков. Однако при разборке машин в отдельных случаях целесообразнее использовать специальные стропы.
На рис. 2, а показана строповка водяного бака трактора групповым стропом со специальными крючьями, вставляемыми в отверстия боковин каркаса бака, радиатор трактора стропят скобой-струбциной (рис. 2, б). Винт струбцины входит в отверстие на ребре бака и надежно удерживает узел. Строповка таких узлов универсальными или облегченными стропами неудобна и трудоемка, а с помощью специальных захватов и захватных средств проста, производительна и безопасна.
При транспортировании кранами тяжеловесных машин и агрегатов, чтобы предохранить их от порчи и облегчить строповку, применяют траверсы, конструкции которых выбирают в зависимости от размеров и массы груза.
Рис. 2. Строповка топливного бака (а) и радиатора (б) трактора
В процессе серийного и массового производства продукции необходимы более уникальные грузозахватные средства.
Для строповки, например, тракторов на Челябинском тракторном заводе используют приспособление, состоящее из рамной траверсы, по углам которой закреплены цепные стропы со специальными захватами на концах. Траверсу через растяжки и серьгу подвешивают на крюк крана, а захваты при строповке трактора закрепляют на рамах гусеничных тележек.
Некоторые станки и агрегаты не имеют удобных мест застропки, поэтому на ряде машиностроительных заводов с целью облегчения строповки применяют различные вспомогательные приспособления (рис. 3). Сверлильный станок, например, удобнее стропить за скобы, закрепляемые на Т-образные пазы стола.
Строповка шлифовального станка становится наиболее практичной, если использовать штыри-вставки (рис. 3, в).
Узлы типа переносного стола (рис. 3, а) или планшайбы (рис, 3,6) станка почти невозможно зацепить без специальных вспомогательных приспособлений: шарнирного захвата (рис. 3,в), накладного крюка (рис. 3,г), скобы (рис. 3, d) или стержня-цапфы (рис. 3, е,ж), укрепляемых в Т-образных пазах столов и планшайб. Вспомогательные приспособления для строповки станков изготовляют различных размеров и грузоподъемностей по тем же техническим условиям, что и типовые грузозахватные средства.
Рис. 3. Вспомогательные приспособления для строповки станков и узлов оборудования: а — переносный стол с Т-образными пазами; б —планшайба; в — шарнирный захват; г — накладной крюк; д — накладная скоба; е — стержень-цапфа; ж— штырь-вставка
Строповку узлов, машин и оборудования нужно вести особенно осторожно, предусмотрительно, не спеша, всегда проверяя надежность обвязки пробными подъемами и дополнительным осмотром; надо постоянно помнить, что груз ответственный, дорогостоящий и при авариях может полностью выйти из строя.
Реклама:
Читать далее: Строповка изделий из металлопроката
Категория: – Строповка грузов
Главная → Справочник → Статьи → Форум
stroy-technics.ru
Тема 1.3. Системы координат станка, детали и инструмента
Тема 1.2.Технологическая документация –>> Рабочий модуль разработана на основе примерного модуля и ФГОС СПО 3-го поколения Работа станка с ЧПУ тесно связана с системами координат. Различают системы координат станка, детали, приспособления и инструмента.
рабочих органов.
В качестве единой системы координат для всех станков с ЧПУ принята стандартная прямоугольная (правая) система, при которой оси X Y, Z (рис.) указывают положительные перемещения инструментов относительно подвижных частей станка. Положительные направления движения заготовки относительно неподвижных частей станка и указывают оси X, У, Z’, направленные противоположно осям X, Y, Z. Таким образом, положительными всегда являются такие движения, при которых инструмент и заготовка удаляются друг от друга.
Стандартная система координат станков с ЧПУ
Круговые перемещения инструмента (например, угловое смещение оси шпинделя фрезерного станка) обозначают буквами А (вокруг оси X), В (вокруг оси У), С (вокруг оси Z), а круговые перемещения заготовки (например, управляемый по программе поворот стола на расточном станке) — соответственно буквами А’, В’, С. В понятие «круговые перемещения» не входит вращение шпинделя, несущего инструмент, или шпинделя токарного станка. Для обозначения вторичных угловых движений вокруг специальных осей используют буквы D и Е.
Для обозначения направления перемещения двух рабочих органов вдоль одной прямой используют так называемые вторичные оси: U (параллельно X), V (параллельно У), W (параллельно Z). При трех перемещениях в одном направлении применяют еще и так называемые третичные оси: Р, Q, R.
У станков различных типов и моделей системы координат размещают по-разному, определяя при этом положительные направления осей и размещение начала координат (нуль станка М).
Размещение координатных систем у различных станков с ЧПУ:
а— карусельный; б— вертикально-фрезерный
Система координат станка является главной расчетной системой, в которой определяются предельные перемещения, начальные и текущие положения рабочих органов станка. При этом положения рабочих
координат органов станка характеризуют их базовые точки, выбираемые с учетом конструктивных особенностей отдельных управляемых по программе узлов станка. Так, базовыми служат точки: для шпиндельного узла — точка N пересечения торца шпинделя с осью его вращения;
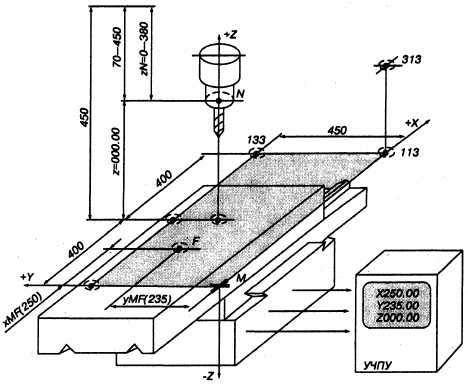
Система координат вертикально-сверлильного станка с ЧПУ
Базовая точка может быть материально выражена точным базовым отверстием в центре стола станка (например, точка F, на рис. Система координат вертикально-сверлильного станка с ЧПУ). В технической документации пределы возможных смещений рабочих органов, как правило, указывают пределами смещения базовых точек.
В стандартной системе координат станка положительные направления осей координат определяются по правилу правой руки. Большой палец (рис. а) указывает положительное направление оси абсцисс (X), указательный — оси ординат (У), средний — оси аппликат (Z). Положительные направления вращении вокруг этих осей определяются другим правилом правой руки. Согласно этому правилу, если расположить
большой палец по направлению оси, то остальные согнутые пальцы укажут положительное направление вращения (рис. б).
Правило правой руки:
а – положительные направления осей координат; б – положительные направления осей координат
Ориентация осей стандартной системы координат станка связывается с направлением движения при сверлении на сверлильных, расточных, фрезерных и токарных станках. Направление вывода сверла из заготовки принято в качестве положительного для оси Z, т. е. ось Z всегда связывается с вращающимся элементом станка — шпинделем. Ось X перпендикулярна оси Z H параллельна плоскости установки заготовки. Если такому определению соответствуют две оси, то за ось X принимают ту, вдоль которой возможно большее перемещение узла станка. При известных осях X и Z ось Y однозначно определяется из условия расположения осей в правой прямоугольной системе координат.
Для того чтобы отсчет перемещений стола по осям X и Y всегда был положительным, нуль станка М принимают размещенным в одном из углов рабочей зоны (см. рис. Размещение координатных систем у различных станков с ЧПУ, б). Естественно, что положение точки М является фиксированным и неизменным, и в этом случае точка М будет являться началом координат станка. Тогда положение (Обозначение координат тремя буквами позволяет однозначно определить эти координаты. Первая буква (например, X) показывает Направление (ось) отсчитываемой координаты, вторая буква (например, М) указывает исходную точку отсчета, третья буква (например, F) определяет конечную точку, т. е. точку данной координаты. Так, обозначение XMF показывает, что координата (расстояние) представляется в направлении оси Х, исходит из точки М и определяет положение точки F) точки F может быть задано координатами xMF и yMF относительно точки М.
При работе станка табло индикации на панели УЧПУ отражает истинное положение базовых точек станка относительно нуля станка. Для рассматриваемого примера это положение точки F относительно точки М и точки N относительно нулевого уровня в соответствующей системе XYZ координат станка.
Таким образом, если на данном станке обрабатывать деталь с использованием абсолютного отсчета, то все ее координаты
Система координат станка (XMY) и детали (XД W YД)
должны быть определены относительно нулевой точки М станка. Обычно в нулевую точку станка рабочие органы можно переместить путем нажатия кнопок на пульте управления станком или соответствующими командами УП. Точный останов рабочих органов в нулевом положении по каждой из координат обеспечивается датчиками нулевого положения. Движения рабочих органов станка задаются в УП координатами или приращениями координат базовых точек в стандартной (правой) системе координат.
Для того чтобы не было путаницы с положительными направлениями рабочих органов, связанных с заготовкой (обозначение осей со штрихом) и с инструментом (обозначение осей без штриха), при подготовке УП всегда исходят из того, что инструмент движется относительно неподвижной заготовки. В соответствии с этим и указывают положительные направления осей координат на расчетных схемах, эскизах и другой документации, используемой при программировании. Другими словами, за основную при программировании принимают стандартную систему координат, в которой определены положения и размеры обрабатываемой детали* относительно которой перемещается инструмент. Принятое допущение корректируется системой УЧПУ таким образом, что если для реализации запрограммированного движения инструмента относительно заготовки необходимо переместить рабочий орган с инструментом, то это движение выполняется с заданным в УП знаком,
а если требуется переместить рабочий орган с заготовкой, то знак направления движения изменяется на
противоположный.
Система координат детали. Система координат детали является главной системой при программировании обработки. Система координат детали — это система, в которой определены все размеры данной детали и даны координаты всех опорных точек контура детали.
Схема определения координат опорных точек контура детали
Система координат детали переходит в систему координат программы — в систему, в которой даны координаты всех точек и определены все элементы, в том числе и размещение вспомогательных траекторий, которые необходимы для составления УП по обработке данной детали. Системы координат детали и программы обычно совмещены и представляются единой системой, в которой и производится программирование и выполняется обработка детали. Система назначается технологом-программистом в соответствии с координатной системой выбранного станка.
В этой системе, которая определяет положение детали в приспособлении, размещение опорных элементов приспособления, траектории движения инструмента и др., указывается так называемая точка начала обработки — исходная точка (О). Она является первой точкой для обработки детали по программе. Часто точку О называют «нуль программы». Перед началом обработки центр Р инструмента должен быть совмещен с этой точкой. Ее положение выбирает технолог-программист перед составлением программы исходя из удобства отсчета размеров, размещения инструмента и заготовок, стремясь во избежание излишних холостых ходов приблизить инструменты к обрабатываемой детали. При многоинструментальной обработке исходных точек может быть несколько — по числу используемых инструментов, поскольку каждому инструменту задается своя траектория движения.
Система координат инструмента. Система координат инструмента предназначена для задания положения его режущей части относительно державки. Инструмент описывается в рабочем положении в сборе с державкой.
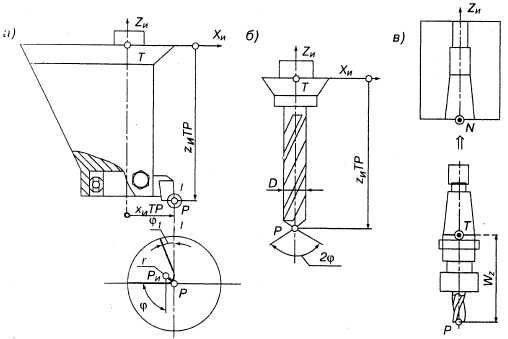
Система координат инструмента:
а – резец; б – сверло; в – схема базирования инструмента
При описании всего разнообразия инструментов для станков с ЧПУ удобно использовать единую систему координат инструмента Хи Zи, оси которой параллельны соответствующим осям стандартной системы координат станка и направлены в ту же сторону. Начало системы координат инструмента располагают в базовой точке Т инструментального блока, выбираемой с учетом особенностей его установки на станке. При установке блока на станке точка Т часто совмещается с базовой точкой элемента станка, несущего инструмент, например с точкой N (рис. Система координат инструмента, в).
Режущая часть инструмента характеризуется положением его вершины и режущих кромок. Вершина инструмента задается радиусом закругления r и координатами хиТР и zиТР ее настроечной точки Р (рис. Система координат инструмента, а), положение которой относительно начала системы координат инструмента обеспечивается наладкой инструментального блока вне станка на специальном приспособлении.
Положение режущей кромки резца задается главным φ и вспомогательным φ углами в плане, а сверла (рис. Система координат инструмента, б) — углом 2φ при вершине и диаметром D. Вершина вращающегося инструмента лежит на оси вращения, и поэтому для ее задания достаточно указать аппликату zиТP.
resheniya.info