Сварка сборка металлоконструкций – Технология сварки металлоконструкций: особенности
alexxlab | 02.12.2020 | 0 | Вопросы и ответы
технология ручной дуговой сварки металлоизделий
Сварка металлоконструкций – технология соединения деталей из металла различной степени сложности в единое целое при помощи специального оборудования.
Она может активно применяться в промышленном масштабе на крупных производствах опытными специалистами, а также для выполнения бытовых операций сварщиками-любителями. В любом варианте, соединения металлоконструкций характеризуется определенными особенностями, которые важно понимать при работе.
Требования к сварке металлических конструкций
Процесс сварки в технологическом плане должен обеспечить выполненным соединениям требуемые геометрические параметры, размеры и высокое качество. Конструкция должна получиться прочной и долговечной, а риск ее деформации – нулевым.
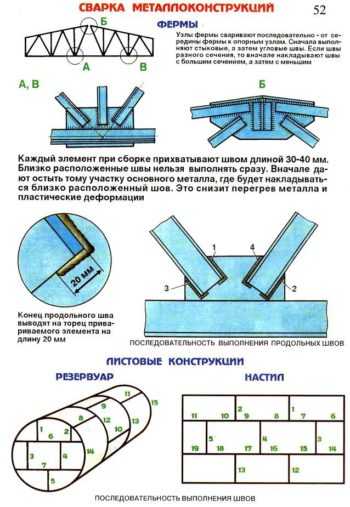
Сварка металлических конструкций.
Именно поэтому технология сварки металлоконструкций должна реализовываться с учетом некоторых требований, что во многом определит качество созданных сварных швов:
- Если создаются простые соединения без применения кондуктора, а также при создании сложных швов перед включением данного инструмента важно оставить зазор между скрепляемыми деталями.
Тогда при смещении элементов шов не пострадает. Но размеры зазора должны соответствовать допустимой норме, иначе система не будет прочна и долговечна. - При выполнении сварки ответственных металлоконструкций сварщики проверяют строгое соответствие установленной детали своему местоположению, согласно карте.
При поступлении заготовки на стапель стоит подготовить каждую из них к завершающему этапу. - Все детали должны строго соответствовать по виду и размеру, указанным в проекте частям будущей конструкции.
Это позволит сохранить функциональные возможности изделия. - Корневые слои шва при ручном методе выполнения дуговой сварки важно накладывать электродами с диаметром, не превышающим 3-4 мм.
- Металлоконструкции при укреплении потребуется располагать так, дабы можно было накладывать швы преимущественно в нижнем положении.
Это необходимо для обеспечения сварщика безопасными условиями работы. - Важно взять под строгий контроль углы металлоконструкции, для чего стоит воспользоваться специальными инструментами и кондуктором.
Все углы между плоскостями должны быть прямыми, если это предусмотрено проектом. Иначе произойдет перекос деталей, что повлечет за собой нарушение целостности механизма, потере им своей функциональности. - Готовая конструкция должна иметь минимальные усадочные напряжения и деформации, для чего сварные работы нужно осуществлять в стабильном режиме с отклонениями от заданных значений величины тока и напряжения на дуге не более ±5 %.
Описанные рекомендации важно учитывать уже на этапе сборки деталей в целостную конструкцию, а не только перед непосредственным выполнением сварочных работ. Особенно, если выбран автоматический режим, при котором не выйдет откорректировать допущенные ошибки.
В целом же, именно этот вид сварных работ и считается наиболее приемлемым, так как при автоматизировании сварных процессов влияние человеческого фактора на качество выполненных швов сводится к нулю.
На заметку! Если при испытании образца на статическое растяжение предел прочности изготовленного шва оказался меньшим, чем предел прочности основного металла, то изделие браковано.
Также важно заварить технологическую пробу в условиях, которые полностью совпадают с условиями сварки конструкций на месте производства.
Если работать сварочным аппаратом придется при низкой температуре воздуха, стоит сварить стыковые образцы перед началом операций при отрицательном температурном режиме, предусмотренном технологическим процессом. Это позволит в дальнейшем провести их механические испытания.
Если нужно выполнить сварные работы с особо ответственными металлоконструкциями из новых марок сталей или с применением новых сварных расходников, мастеру потребуется изготовить контрольные образцы в таком же пространственном положении и с теми же материалами, оборудованием, что и при сварке монтируемых конструкций.
Это позволит сварщику оценить ситуацию со всех сторон перед началом работы и не допустить ошибок в процессе ее выполнения.
На заметку! Качество созданных соединений металлоконструкций во многом зависит не только от мастерства сварщика, но и от качества сварочного аппарата, примененного в работе. Лучше остановить свой выбор на модели известного бренда, качество которого проверено временем.
Классическая технология сварки конструкций из металла
Сварка – уникальный способ получения неразъемных металлических соединений, открывающих человеку широкие возможности по снижению трудоемкости создания и установки металлоконструкций.
Она позволяет использовать рациональные типы сечений в металлоконструкциях, что приводит к снижению показателей металлоемкости в несколько раз, по сравнению с применением иных технологий.
Сегодня сварные работы выполняются с помощью разных методов, но все они создавались на основе знаний о классической технологии. Она проста и может реализовываться, как для бытовых целей, так и в промышленных масштабах.

Углы сварки металлоконструкций.
Если изготавливать сварочные металлоконструкции по классической технологии, потребуется применить следующие источники энергии:
- электрическая дуга;
- газовое пламя.
Оба варианта предполагают три метода выполнения сварных швов:
Автоматический
Не подразумевает человеческое вмешательство в процесс выполнения сварных работ. Сварочный аппарат настраивается на актуальный режим функционирования с учетом конкретного вида выполняемой операции единственный раз перед началом работы.
Поэтому важно понимать основную цель приобретения сварного оборудования при выборе в магазине. Используя автоматический режим, можно применять контактную и электрошлаковую сварку.
Полуавтоматический
При использовании данного метода сварные швы формируются вручную, а электроды подаются в автоматическом режиме. Такое положение дел позволяет повысить производительность работы без ущерба для качества создаваемых металлоизделий.
При полуавтоматической сварке можно применить газовый флюс, неплавкие электроды, сварочную проволоку.
Ручной
Все действия методом ручной дуговой сварки осуществляются сварщиком без применения автоматизированного оборудования: от контроля подачи электрода до формирования самого соединения.
Зачастую при ручном режиме применяют обыкновенную сварку под флюсом, электродуговую сварку или пайку газосварочным устройством. Данный метод рационально использовать в бытовых целях, а не на крупном производстве, потому что он чрезмерно затратный и характеризуется низкой производительностью.
На заметку! Полуавтоматический метод дуговой сварки металлических конструкций наиболее востребован на отечественном рынке. Он активно применяется в строительстве при монтаже железобетонных строений, в машиностроении при конструировании автомобилей, а также в быту.
Инновационные сварочные технологии
Со временем классический метод выполнения сварных работ совершенствовался, опытные специалисты разрабатывали инновационные способы соединения металлических деталей в единую конструкцию: сварка с применением лазерных установок, ультразвука, теплового эффекта и т. п.
Подобные новаторские идеи могут помочь сварщику в работе, облегчив выполнение некоторых задач и ускорив весь процесс сборки металлоконструкций в целом. По этой причине и сегодня в этой области не прекращаются научные разработки и исследования.
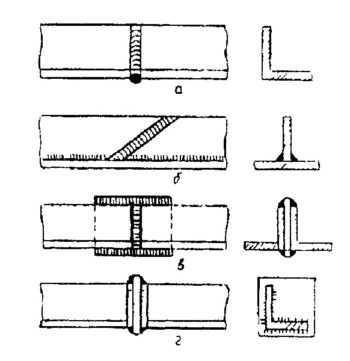
Способы сварки металлоконструкций.
Также применение инновационных технологий выполнения сварных работ позволяет сварщику получить ряд преимуществ:
- снизить показатели коробления металла;
- повысить скорость выполнения работы;
- сократить расходы зачистку сварного шва;
- снизить траты на закупку расходных материалов;
- выполнять соединения тонколистового металла.
Особенно интересны, с точки зрения продуктивности, качества полученных швов и экономичности, следующие технологии сварки:
- Электронно-лучевая сварка применяется при работе с глубокими соединениями – до 20 см, но только при условии определенного соотношения ширины шва и глубины погружения инструмента – 20:1.
Процесс формирования шва осуществляется в вакууме, поэтому использовать такую технологию в быту практически невозможно. Она применяется в сфере узкопрофильных производств. - Термитная сварка подразумевает нанесение особой смеси на контуры соединения деталей в процессе горения.
Технологию применяют для ответственных конструкций из металла в готовом виде, когда с помощью наплавки металла надо устранить имеющийся дефект в виде трещины или скола. - Плазменная сварка подразумевает применение ионизированного газа, проходящего сквозь электроды с высокими сварочно-техническими характеристиками и выполняющего функцию дуги.
Технология имеет более широкие возможности применения по сравнению с электронным типом, так как позволяет выполнить сварщику резку и сварку металлической конструкции с любой шириной металла. - Орбитальная аргонодуговая сварка с помощью вольфрамового электрода применяется для работы со сложными деталями из металла.
Например, для неповоротных стыков труб с диаметром 20-1440 мм. В процессе работы активирующий флюс наносится 1 г/м шва. Это позволяет решить ряд важных технологических задач: уменьшить объем и вес сварной ванны за счет ведения операций пониженным током; благодаря давлению дуги на жидкий металл шов получается качественным в любом пространственном положении; сварку можно автоматизировать без разделки кромки. - Щадящие технологии сварки в смесях защитных газов Ar+CO2 и Ar+O2+CO2.
При использовании такого метода выполнения сварочных работ можно получить более качественные соединения при сравнении со сваркой в СО2. При этом актуальный объем расходных материалов сократиться на 20 % за счет резкого снижения набрызгивания электродного материала, а переход к свариваемым частям металлоконструкции станет плавным.
На заметку! Каждая из них имеет ряд недостатков, отличается своеобразными особенностями и принципами осуществления, которыми важно овладеть до начала применения на практике.
Современная наука многогранна и непредсказуема.
Она предоставляет человеку возможности применить на практике достоинства нано-технологий, поэтому ближайшее будущее сварочных операций представляется связанным с совершенствованием схем компьютерного управления сваркой, а также применением новых сварных материалов.
Заключение
Если соблюдать все требования к сварке металлоконструкций, можно получить высококачественные швы: долговечные, прочные и стойкие к воздействию. Использовать при этом можно как классический вид сварки, так и новые технологии.
Несмотря на то, что они в большей степени касаются профессионального уровня сварки, но при желании развивать свои навыки в этой сфере, ознакомиться с такой информацией будет не лишним и для новичка в подобных вопросах.
tutsvarka.ru
Сварка металлоконструкций — технология и особенности
Для соединения металлоконструкций различной степени сложности уже давно широко используется сварка. Её успешно применяют как любители, так и профессионалы своего дела. И те и другие, при наличии нужного опыта, делают это достаточно успешно в бытовых условиях и в масштабах крупного производства.
Сварка крупных металлоконструкций на сегодняшний день стала более эффективной. Это происходит из-за постоянного прогресса и усовершенствования методов сварки и самих сварочных аппаратов. Соединение конструкций из металла имеет свои особенности и наиболее действующие методы, о которых и пойдёт речь в данной статье.
Принципы и особенности
Процесс соединения конструкций подразумевает не только соединение изделий из металла, но и возможность работать с другими материалами, например, пластмассой. Сама сварка нужна для того, чтобы расплавить соединяемые части деталей, что позволит надёжно скрепить их между собой (перед сваркой для сборки используют кондуктор – инструмент который позволяет закрепить свариваемые детали между собой) и приступить к следующему этапу.
Но самая ответственная работа, происходит при сборке металлоконструкций под сварку. От неё будет зависеть надёжность и долговечность проекта. Если сварщиком упущена из виду малейшая деталь, пострадать может вся структура соединений. Поэтому, исходя из нормативов времени, которое требуется на создание конструкции в целом, большая его часть потратится непосредственно на сборку системы соединений, после того как заготовки были поданы на стапель. Но некоторые сварщики используют кое-какие приёмы, позволяющие ускорить процесс. Для этого нужно иметь соответствующий опыт и навыки работы с кондуктором.
Правильный подход к сборке конструкции
Существует некий алгоритм действий и правила, которые ведут к успешной сборке и высокой надёжности готовой конструкции, рассмотрим это в деталях:
- Перед скреплением деталей кондуктором и при более простых соединениях без его участия, нужно допускать вероятность смещения элементов, для этого нужно предоставить деталям требуемое пространство для отклонения от нормы;
- Все детали для сварки должны быть строго на своих местах. Когда заготовки поступили на стапель, они должны быть строго подготовлены к последнему этапу соединения согласно карте сварки;
- Чтобы не нарушить функциональные возможности конструкции, стоит правильно подобрать все её составляющие, детали должны соответствовать по виду и размеру тем, которые указаны в проекте;
- Нужно обратить внимание на размеры зазоров. Они не должны отклоняться от допустимой нормы, так как превышенная их величина приведёт к нарушениям прочности системы, а если их не сделать вовсе, к поломке движимых частей;
- Нужно взять под строгий контроль углы конструкции, для этого используются специальные инструменты и кондуктор. Крайне важно, чтобы каждый угол между плоскостями был прямым, но только там, где это предусмотрено проектом. В противном случае механизм может быть нарушен и прийти в негодность за счет перекоса или завала всей системы соединений.
Всех этих правил нужно придерживаться в процессе сборки и поступления деталей на стапель, а не начинать проверку на их наличие перед сваркой металлоконструкций. Это крайне важно учитывать при автоматической сварке, так как откорректировать недостатки уже не получится. В целом роботизированная сварка будет более приемлемой и надёжной в этом случае, так как отсутствует влияние человеческого фактора, это позволит уберечь конструкцию от многих погрешностей.
Технология профессиональной сварки металлоконструкций
Сварка металлоконструкций, как и любой другой её вид, имеет свои нюансы. Они четко проявляются в сравнении соединений на любительском уровне и в масштабах глобального производства конструкций из металла, которые собираются на больших стапелях. Нужно понимать от чего зависит качество профессиональной работы и как им воспользоваться в своих целях. Весь процесс регулируют такие положения:
- для умения правильно формировать швы, существует соответственный раздел, с которым стоит ознакомиться. Это напрямую влияет на качество соединений, а их количество на сложность конструкции;
- ГОСТ 27772-88, а также СНИП II 23-81, эта часть рассказывает о деталях. Здесь каждый сможет ознакомиться с возможностью в тех или иных ситуациях использовать разные материалы для сварки, и понять в каких случаях их применение будет целесообразным;
- классификация сварки подразумевает раздел сварочных работ на те, что под силу любителю с базовыми знаниями и те, с которыми справится только профессионал. Вся подробная информация хранится в документе Минтопэнерго РФ РД 15.132-96.
- раздел о контроле сварочных работ, с которым также стоит обязательно ознакомиться.
Все требования будут относиться к сварщику с повышенным уровнем умений. Но если есть желание развить свои способности, ознакомится с подобной информацией, не будет лишним, это позволит расширить своё понимание процесса сварки и сборки конструкций. Также документы объяснят, какой металл подойдет в том или ином случае, и дадут понять, кто сможет выполнить требуемые виды соединений. Не стоит забывать и о контроле сварки.
Стандартная схема соединения металлоконструкций
Этот способ предполагает использование проверенных временем два источника сварки, пламя газа и дуга (электрическая). И в том, и в другом случае существует три метода для накладки швов:
- Автоматический;
- Полуавтомат;
- Ручной.
Первый способ имеет такое название из-за отсутствия человеческого вмешательства в процесс сварки. Аппарат стоит лишь настроить на правильный режим работы, учитывая вид проводимых работ. При покупке такого устройства, нужно четко понимать, для чего он будет использоваться чаще всего, все они имеют свои особенности и механизм работы. Всё это подробно описывается в инструкции к агрегату. Целесообразнее использовать его в массовом производстве, его полезность проявится в экономии на стоимости работ при большом объеме сварочных соединений.
В случае с ручным методом, все действия осуществляются самостоятельно сварщиком. К ним относят контроль подачи электрода и формирование соединения. При этом чаще используется обыкновенная сварка под флюсом, электродуговая сварка или пайка с использованием газосварочного устройства. Этот способ популярен при соединениях в бытовых целях, при работе с крупным производством его использование будет неуместным и затратным.
Полуавтоматический режим имеет характерные отличия. Работая с данным способом, шов всегда накладывается вручную, а вот подача электродов осуществляется автоматически. Это позволяется добиться хорошей производительности, увеличив её в несколько раз за счет смешивания преимуществ ручного и автоматического способа сварки. Именно поэтому полуавтоматическая технология является самой популярной, так как охватывает аудиторию профессионалов и сварщиков любителей.
Инновационное развитие в сфере сварочных технологий
Со временем методы работы совершенствовались и вносили такие инновационные способы работы, как с использованием лазера, ультразвука, теплового эффекта и т. д. Такие новшества помогают специалисту облегчить и ускорить процесс сборки деталей конструкции на стапели с дальнейшим их соединением.
Особой популярностью пользуются такие технологии, как:
- электронно-лучевая;
- термитная;
- плазменная.
Любая из них имеет свои недостатки, принципы работы и особенности, с которыми нужно ознакомиться до начала их использования.
Лучевая предусматривает работу с глубоким швом, до 20 см. Но только при определённом соотношении ширины соединения и глубины погружения лазера – 20 к 1. Всё это происходит в вакуумной среде. Поэтому эта технология практически не используется в домашних условиях, а наоборот только в сферах узкопрофильного производства.
Используя плазменный способ, применяется ионизированный газ, он проходит через два электрода с высокими сварочно-техническими характеристиками и играет роль дуги, но её возможности намного шире, чем обычной электронной. Об этом говорит то, что при использовании газа плавлению поддаётся металл с любой шириной. Также это позволит, если есть такая необходимость, разрезать его.
Термитную используют в случаях нанесения специальной смеси на контуры шва соединяемых деталей. Это происходит в процессе горения. Эту технологию часто используют при сварке ответственных металлоконструкций. Когда конструкция уже готова, термитная сварка используется для устранения различного рода брака, трещин и дефектов при помощи наплавки металла.
Преимущества
Подводя итоги темы, хотелось бы до конца разобраться в том, чем же так полезны все эти способы и методики:
- Используя все советы можно с легкостью подобрать оборудование для домашнего и более профессионального использования. На сегодняшний день оно является доступным для каждого как по цене, так и по своей простоте использования;
- При правильном подборе модели сварочного агрегата, он не только быстро окупится, но и позволит сэкономить денежные средства;
- Всегда есть возможность работать с различного рода материалами, сталью, алюминием и т. д.;
- Отсутствуют проблемы с соединением мелких деталей;
- Нет ограничения по толщине металла, которое будет препятствовать соединению или разрезке материала;
- Экономить рабочий материал можно при помощи только двух рабочих элементов. В результате спайка вернёт надёжность детали в её первоначальное состояние;
- Различные аппараты позволяют быстро приступить к работе, исправить поломки деталей и вернуть поверхность в её исходное состояние;
- В процессе работы, можно легко держать под контролем форму изделия, а также при необходимости внести требуемые изменения;
- Ни один способ соединения не имеет возможности похвастаться таким высоким уровнем герметичности стыков.
Вывод
Всегда стоит помнить, что успешной, работа будет лишь тогда, когда выполняются все рекомендации и правила по работе со сваркой и сварочными аппаратами. Также нужно учитывать вид требуемого соединения, материала, разновидности конструкций, а также их соединений. Это напрямую будет влиять на качество шва и на функциональные возможности металлических конструкций.
Если пренебрегать всеми правилами и советами, швы могут приходить в негодное состояние, а именно лопаться, расходится или трескаться. Из всего вышесказанного стоит сделать вывод о том, что не стоит браться за работу, не зная о чем идёт речь, для начала нужно хорошо разбираться в теории и попрактиковаться на соединениях с начальным уровнем сложности.
electrod.biz
Сварка металлоконструкций: технология и особенности
Одним из наиболее часто применяемых в производстве массовых и мелкосерийных изделий способов соединения деталей является сварка. С ее помощью можно собрать практически любое сопряжение элементов – тавровое, угловое, торцевое и нахлесточное. С течением времени технологические приемы, при помощи которых осуществляется сварка металлоконструкций, улучшаются, становясь более эффективными.
Классические способы сварки
Стандартные способы сварки металлических элементов подразумевают под собой использование двух основных источников энергии: газового пламени либо электрической дуги.
Газовая и дуговая сварка может быть автоматической, полуавтоматической и полностью ручной. Последний вариант подразумевает формирование сварочного шва только собственными руками мастера. Помимо этого, ручная дуговая (РД) сварка металлоконструкций включает в себя и ручное управление процессами подачи электрода, или присадочной проволоки, и самим процессом сваривания деталей.
Ручной режим наиболее эффективен только в бытовых условиях. При его использовании применяют в основном технологии сварки под флюсом, пайки газосварочным аппаратом или классический способ электродуговой сварки.
В основе первого варианта – автоматической сварки – лежит процесс наложения на участок шва без прямого участия человека. Всей работой занимается специальный механизм, который предварительно настраивается. Естественно, что у данного агрегата спектр функций весьма ограничен, однако это значительно снижает стоимость готовых изделий, благодаря чему в крупносерийном производстве она становится весьма популярной.
Сборка металлоконструкций, сварка в автоматическом режиме позволяет применять контактную технологию, включающую нагрев и опрессовку элементов, электрошоковую сварку и прочие «ручные» способы. Единственная разница – всем заправляет не мастер, а специально созданный и запрограммированный робот.
Полуавтоматический режим подразумевает наложение сварочного шва мастером, однако электроды либо проволока в зону работы подаются автоматически, что значительно увеличивает производительность работ на участке.
В таком режиме используется практически любая технология сварки металлоконструкций, применяющая неплавкие электроды, газовые флюсы и автоматизированную подачу в зону нагрева присадочной проволоки. В быту и мелкосерийном производстве полуавтоматическая сварка металлоконструкций является наиболее выгодным и эффективным вариантом технического процесса.
Технологические новинки
В современной сварке для соединения металлических деталей применяют не только пламя перегретого газа и электрическую дугу, но и тепловой эффект трения, лазерную энергию, ультразвук и даже силу пучков электронов.
Проще говоря, сама технология сварки постоянно совершенствуется. Достаточно регулярно изобретаются новые способы реализации данного технического процесса. К числу таких новинок можно отнести следующие виды сварки – плазменную, термитную и электронно-лучевую.
Посредством термитной технологии осуществляется сварка ответственных металлоконструкций, составляющие которых по шву расплавляются во время горения специальной смеси, вводимой в место соединения. Термит также используется для устранения дефектов и трещин в уже готовых металлоконструкциях путем «наплыва» металла.
Плазменная сварка осуществляется в условиях пропускания через два электрода ионизированного газа. Последний выступает в качестве электрической дуги, но при этом эффективность ее значительно выше. Перегретый газ используют не только для сварки металла, но и для его резки, благодаря чему вокруг плазменного генератора можно создать автоматическую и многофункциональную сварочную систему.
При помощи электронно-лучевых технологий производят сварку глубоких швов до 20 сантиметров, при этом ширина такого шва не будет превышать одного сантиметра. Единственным минусом такого генератора является то, что работать с ним можно только в полном вакууме. Соответственно, подобную технологию используют только в узкоспециализированных областях.
Для сборки небольших по размеру металлоконструкций эффективнее всего использовать газовую либо электродуговую ручную сварку. Полуавтоматический аппарат окупается при осуществлении работ с мелкосерийными объектами. Современные технологии сварки, соответственно, применяются только в серийном производстве.
Сварка металлоконструкций: особенности
Технология сварки применяется не только при работе с металлом, но и с различными полимерами. Весь процесс представляет собой нагрев и деформацию поверхностей, которые затем соединяются в одно целое.
Все сварочные работы состоят из двух основных этапов: сборки и соединения.
Самым трудоемким и сложным является первый этап. Надежность и прочность конструкции во многом зависит от соблюдения всех требований. Больше половины всего времени приходится именно на сборку составляющих.
Обеспечение правильной сборки металлоконструкций
Высокое качество, прочность и надежность конечного результата обеспечивается соблюдением определенных требований.
- При выборе деталей необходимо строго придерживаться заложенных в проекте размеров.
- Зазоры должны быть определенного размера – при их увеличении прочность готового изделия значительно снизится.
- Углы измеряются и контролируются при помощи специальных инструментов. Важно, чтобы они полностью соответствовали указанным в проекте, иначе появится риск обрушения всей конструкции.
Преимущества сварки
Помимо того, что сварка металлоконструкций значительно экономит время проведения всех работ, а шов получается качественным, процесс обладает и другими характеристиками:
- Масса готовой спайки не изменяется, поскольку используются только две основных детали, что позволяет сэкономить материал.
- Отсутствие ограничений по толщине металла.
- Возможность контроля и корректировки форм металлоконструкций.
- Доступность сварочного оборудования.
- Возможность применять сварку для ремонта и реконструкции.
- Высокая герметичность и прочность стыков.
Дополнительные моменты
Для того чтобы полученная конструкция была качественной и надежной, необходимо соблюдать все технологические требования.
Правильно подобранные материалы, комплектующие и оборудование позволяют получить швы высокого качества. В противном случае готовая конструкция не только теряет товарный вид, но и свои эксплуатационные характеристики.
Дефекты сварочных швов
Для получения точных размеров и упрощения работы при создании металлоконструкции применяют кондуктор. Несмотря на это, РД сварка металлоконструкций, кранов может обернуться во время процесса определенными дефектами – наплывами, трещинами, прожогами, пористостью, пережогами, подрезами и прочими.
Причины появления дефектов
Наплывы формируются на металлоконструкциях в результате натекания расплавленного металла. Чаще всего такой дефект характерен для проведения работ по созданию горизонтальных швов. Удаляют их молотком, после чего проверяют изделие на наличие непроваров.
Причинами появления прожога может быть некачественная обработка кромок конструкций, увеличение зазора, низкая скорость проведения работ и малая мощность пламени. Устраняют его путем вырубки и заварки шва.
Самым опасным видом дефекта считается непровар, поскольку он отрицательно сказывается на надежности и прочности сварочного шва. Такие участки устраняются полностью, металлоконструкции зачищаются и заново завариваются.
fb.ru
Сварка металлоконструкций
Тема сварка металлоконструкций – это обширная сфера, потому что разнообразие металлических конструкций огромно и по назначению, и по специфики проведения технологических процессов, и по проектированию. Но есть в этой сфере один критерий, который присущ всем видам металлических конструкций, собираемых методом сварки. Это сама сварка. Именно с ее помощью появляется возможность использовать в металлических конструкциях рациональные виды сечения металлических профилей, соединение элементов под разными углами и в разных плоскостях, снижение такого показателя, как металлоемкость.
К тому же появляется возможность использовать для сооружения конструкций металлов с разными техническими характеристиками. Кстати, прокат, который используется для сборки металлоконструкций, должен соответствовать своду норм и правил под названием «Стальные конструкции». Основной материал, который в них используется, это сталь, поставляемая в виде листов, профилей различной формы, труб, стержней, рулонов, гнутых профилей и так далее.
Но, как известно, сталь бывает разная. А для разных металлоконструкций, где учитываются нагрузки разного назначения (на разрыв, на изгиб, на давление), и стальные профили применяются разные. К примеру, по ГОСТ 19281-89 для сталей повышенной прочности, есть девять классов показателей, определяющих прочность стальных изделий. И таких ГОСТов несколько. Поэтому еще на стадии проектирования металлических конструкций определяется и выбирается тот или иной вид стальных изделий, которые станут основной металлоконструкции.
Если металлоконструкция соединяется сваркой, то необходимо учитывать показатели качества свариваемости металла. На это влияет содержание углерода в стали. Этот же элемент влияет на прочность металла. В общем, правильно подобрать стальной прокат для конструкции – это важная составляющая качества конечного результата.
Виды сварки для сборки металлоконструкций
Как правильно сварить конструкцию из металла? Вопрос на самом деле серьезный. И ответ на него зависит не только от выбранных стальных профилей, их толщины и марки стали. Большое значение имеет и вид выбранной сварки.
Если говорить о ручной сварке, то она применяется, и это качественный вид сваривания металлов, который все-таки зависит от квалификации сварщика. Единственный ее недостаток – низкая производительность. Поэтому все чаще ручную сварку в цехах заменяют механизированной (порошковыми проволоками) и автоматической в защитных инертных газах или в слое защитных флюсов. Обычно механизированный вид применяют для сварки угловых, потолочных и вертикальных швов. Автоматический для нижних положений.
Внимание! Применяемая ранее электрошлаковая сварка сегодня практически не используется. Исследования показали, что швы, выполненные данным видом сварки, при низких температурах теряют свои прочностные характеристики. А это снижает несущую способность самих металлических конструкций.
Из всего вышесказанного можно сделать вывод, что для сборки металлоконструкций можно использовать любой вид сварки как в цеховых помещениях, так и на монтажных открытых участках. Самое интересное, что многие зарубежные компании, оснащенные современными видами сварочных видов оборудования, предпочтение отдают ручной дуговой электросварке. К примеру, в Японии многие крупные компании, занимающиеся возведением ответственных металлоконструкций, используют до 65% ручной сварки.
Температурный режим сварочного процесса
Температура окружающей среды сильно влияет на технологию проведения сварочных работ и на качество самого сварочного шва.
- Нельзя проводить сварку металлоконструкций, если температура металлической заготовки ниже -18С. Температуру обычно контролируют вблизи стыка двух деталей. Для проведения сварки саму заготовку необходимо подогреть. Греть весь металл нет необходимости, достаточно на расстоянии толщины заготовки от края соединяемых кромок. Или на расстоянии не менее 76 мм во всех направлениях.
- Если соединяются две заготовки из разных марок сталей, то подогрев производится по температуре более высокопрочной стали. Конечно, показатель нагрева будет зависеть и от толщины заготовки. К примеру, марку А514 при толщине детали не более 38 мм надо нагревать до +205С. Более толстые заготовки этой марки надо уже нагревать до +230С.
- Оптимальный нагрев для всех видов сталей – +21С.
Виды сварных соединений металлоконструкций
Классификация сварных соединений разделяется по нескольким признакам.
- Расположение примыкания двух заготовок.
- Тип сварного шва.
- Технология сварочной операции.
- Условия, при которых проводится сварочный процесс.
- Толщина заготовок.
- Марка стали заготовок.
Что касается первого пункта, то есть, геометрии расположения заготовок, то здесь четыре вида стыковых соединений.
- Встык, когда две заготовки примыкают друг к другу в одной плоскости.
- Внахлест, когда две детали перекрывают своими краями друг друга.
- Угловое соединение. Это когда две металлические заготовки соединяются под каким-либо углом.
- Соединение тавровое. Это когда одна из деталей примыкает к другой своей торцевой плоскостью.
Чаще всего в металлоконструкциях применяются соединения встык и угловые. Как правильно проводить эти соединения двух заготовок.
Что касается стыкового соединения, то его выполняют прямым полным проваром сварного шва на всю толщину заготовок. Или используют для сварки технологию с применением выводных планок. Если сварка проводится не в цеху, то соединение можно проводить с односторонней сваркой и с дальнейшей подваркой корня сварного шва. То есть, заполнение зазора между кромками производится по одной из кромок, постепенно заполняя весь зазор.
Технология с выводными подкладками сильно отличается от предыдущей. Во-первых, подкладки устанавливаются со стороны кромок свариваемых деталей. Во-вторых, зазор между кромками должен быть в пределах 7 мм – это при ручной сварке. При механизированной – 16 мм. В-третьих, придется выбирать толщину подкладки так, чтобы при проведении сварки на них не образовался прожог. При этом учитывается сам режим сварочного процесса с выставлением необходимой величины тока.
Нередко в металлических конструкций в стыковых соединениях стыкуются две заготовки разной толщины. При этом способом фрезеровки или строжкой выбирается угол наклона кромки толстого металла, который равен уклону 1:8 для растянутых элементов металлоконструкции (к примеру, подвески и консоли), и 1:5 для сжатых элементов (опоры и стойки).
Угловые сварочные соединения подвергаются большим нагрузкам, чем стыковые. Особенно необходимо отметить нагрузки на растягивание по толщине заготовки. Поэтому существуют определенные требования к этому виду сварного соединения.
- Нельзя использовать односторонний угловой стык для нагружаемых металлических конструкций. Оптимальный вариант – двусторонний шов, с помощью которого уменьшается концентрация деформаций в самой верхней части валика.
- Если по каким-то причинам двусторонний шов нанести не удается, то применяют односторонний. При этом разделку кромок не применяют, а количество наплавляемого металла должно быть как можно меньше. То есть, в этом случае полная проплавка шва не применяется.
- Если металлоконструкция подвергается статическим нагрузкам, то применяется сварка неполным швом с разделкой кромок двух заготовок.
- Лучше использовать К-образную разделку кромок, а не V-образную.
- Если есть возможность, то лучше избегать углового соединения металлических деталей. Предпочтение нужно отдавать тавровому стыку.
Режим сварки также является важным фактором, который определяет качество сварного шва. Если говорить о токе, то его повышенная величина может создать неравномерное распределение металла в зоне стыка. Могут даже образоваться прожоги, если ток большой, а толщина свариваемых заготовок маленькая. Небольшой ток тоже является причиной низкого качества шва. Могут образоваться участки с недоваром, который ведет к снижению прочности соединения и образованию трещин внутри сплавляемого металла.
Скорость сварки также может повлиять на качество. К примеру, если скорость большая, то это гарантия непроварки стыка. Заполнение зазора может быть неполным. Если скорость маленькая, то могут образоваться прожоги, заполняемый зазор металл образует выпуклости и растекание. Поэтому контролировать скорость ручной сварки надо обязательно. Ее среднее значение 20 м/ч.
Сварные узлы в металлоконструкциях
Сварные узлы являются основными стыковыми соединениями, на которых и держится вся металлическая конструкция. Поэтому еще на стадии проектирования инженеры стараются создать благоприятные условия для проведения сварки в стыковых узлах. А именно:
- Чтобы в сварных узлах проводилось или стыковочное соединение, или угловое.
- Чтобы положение сварки было нижним.
- Использовать не ручную сварку, а механизированную или автоматическую, как залог гарантированного качества.
Существует много видов сварных узлов, к которым предъявляются разные требования. К примеру, балочный узел. В нем очень важно обращать внимание на расположение между собой сварочных швов, это к вопросу, как правильно варить стыки металлоконструкций. Расстояние между ними не должно быть меньше десятикратной толщины самого толстого металлического профиля, который входит в состав этого узла.
И еще один момент, который влияет на прочность металлической конструкции. Есть два термина: местная прочность и непрочность. К первой относятся именно сварочные участки, к которым приварены косынки, ребра жесткости, накладки и так далее. Ко второй относятся всевозможные вырезы на элементах металлоконструкций, отверстия, непровары швов, зазоры и щели в стыках. Если оба участка присутствуют в конструкции, то сама по себе она уже считается непрочной.
Все дело в том, что физические законы в сварочных соединениях действуют так:
- Где больше жесткость и прочность соединения, здесь появляется большая концентрация сил, действующих на всю конструкцию в целом.
- И, наоборот, где меньше жесткости, там меньше действующих сил.
То есть, если в металлоконструкции присутствует местная непрочность, то самый хорошо проваренный стык является местом большой опасности. Как не парадоксально, но это именно так. Вот почему необходимо избегать появления местной непрочности. То есть, непровары и низкое качество сварного шва даже на самых небольших участках или не на самых нагружаемых узлах все равно приведет к выходу из строя всей конструкции.
Поэтому вопрос, как правильно варить стыки в металлоконструкциях – это самый важный вопрос, который касается качества и надежности всей конструкции в целом.
Поделись с друзьями
0
0
0
0
svarkalegko.com
Сварка металлоконструкций, начиная от составления технологической карты и заканчивая проверкой качества
В основу процесса термической обработки объёмных металлоконструкций заложены строго регламентируемые принципы, определяемые как типовые технологии сварочного процесса. С этой точки зрения подготовка и сопровождение сварки невозможны без применения специальных аналитических методов, являющихся составной частью общих работ.
Оптимизация технологического процесса сварки металлоконструкций предполагает несколько различных вариантов его проведения. Для этого применяются проверенные на практике приёмы, сводящиеся, в частности, к составлению специальных сопровождающих документов (технологических карт).
Технологические карточки
Технологическая карта сварки включает в себя ряд пунктов и граф, указывающих на следующие характеристики процесса сварки металлоконструкций:
- наименование изделия;
- единицы измерения объёма проведённых работ;
- цифровой код осуществляемой операции;
- обозначение нормативов, на основании которых она реализуется;
- уровень автоматизации, код степени квалификации оператора и многие другие параметры.
С содержанием типовой технологической карты можно ознакомиться в Таблице
Основное назначение этого учёного документа – зафиксировать всю информацию о проведённой операции по возведению металлоконструкций и хранить её коды в компьютерной базе как типовой образец.
На основании этих карт на предприятиях и в организациях подготавливаются и постоянно пополняются информационные массивы, позволяющие оперативно ссылаться на уже реализованный ранее технологический процесс.
Вся указанная в карточках информация вводится в базу только в кодированном виде.
При разработке новой технологии сварки металлоконструкции она учитывается после того, как проводится экспертная оценка эффективности предстоящих операций (исходя из особенностей отдельных сборных изделий).
Количественная оценка технологичности этих операций производится с учётом следующих факторов:
- последовательность их выполнения;
- разбивка металлоконструкции на независимые технологические узлы;
- виды используемой оснастки и специальных приспособлений;
- токовые режимы сварки, предполагаемые напряжения в конструкции и степень деформации отдельных составляющих.
По завершении проверки эффективности новой технологической цепочки сварки данные и коды отправляются на хранение в компьютерную базу предприятия.
Сборка деталей
Сварка металлоконструкций, подготавливаемых в виде отдельных сборных узлов, осуществляется согласно ГОСТ 5264-80, в котором определяются принципы монтажа на основе электродугового метода.
В соответствии с положениями этого документа определяется порядок подготовки металлоконструкции к сборке, включая способы подачи его отдельных элементов к месту сварки.
Устанавливаются режимы сплавления отдельных узлов металлоконструкций, которые выбираются в соответствии с данными, указанными в составленной ранее технологической карте на этот вид сварных работ.
Окончательный монтаж металлоконструкции осуществляется в определённой последовательности, включающей предварительную зачистку кромок и ближайших к ним участков. При этом подгонка элементов под сварку производится либо с помощью механических средств, либо посредством газовой резки.
При сборке уже подготовленного изделия руководствуются не только чертежами, но и уже упомянутыми ранее технологическими картами. В них, помимо режимов работы и порядка сборки должны указываться способы крепления деталей, а также методы контроля собранных изделий.
В процессе подготовки металлоконструкций следует исходить из того, что при их сварке предполагается использовать электрическую дугу, температура плавления которой может достигать 7000 °.
К особенностям этого метода сборки сложных объектов следует отнести и то, что при его реализации применяются специальные приспособления для сварки.
Вспомогательное оборудование
Процесс сварки металлических заготовок предполагает их объёмную фиксацию в заданном положении, что удаётся сделать лишь с помощью дополнительных приспособлений особой конструкции (кондукторов).
Кондуктор может выполняться в виде стенда или станины произвольной формы, обеспечивающей приём и крепление очередной заготовки, входящей в состав монтируемой металлоконструкции.
В зависимости от условий и технологических особенностей каждого конкретного процесса сварки кондукторы могут иметь самые различные исполнения. В упрощённом виде эти приспособления имеют форму, позволяющую сформировать прямой угол в зоне стыка металлических изделий.
Помимо этих фиксирующих элементов сварочные работы с металлоконструкциями предполагают использование специальных подающих механизмов, называемых стапелями.
Сварочный стапель представляет собой сооружение в виде Г-образного подъёмного приспособления, используемое для размещения заготовок, над которыми располагается площадка с оператором.
Таким образом, установленный порядок работы со стапелями, значительно облегчающий труд сварщика, предписывает использование их в качестве опорных конструкций, предназначенных для укладывания свариваемых балок или пролётов.
Непосредственно над ними по проложенным вдоль стапелей рельсам перемещается сварочный портал (площадка) с находящимся в нём сварщиком.
Применение стапелей при сварке металлоконструкций позволяет получать непрерывный (сплошной) шов без отрыва от сварочного процесса.
Также отметим, что при фиксировании небольших заготовок посредством углового кондуктора допускается нормируемое отклонение от предполагаемой линии стыковки (в пределах, предусмотренных технологическим процессом).
Особенности ручного метода
Сборка строительных металлических конструкций посредством дуговой сварки – сложный технологический процесс, справиться с которым способны лишь хорошо обученные специалисты.
В его основу заложено термическое воздействие электрической дуги, для получения которой используется основное и вспомогательное оборудование.
К первой из этих составляющих относятся источник энергоснабжения и преобразующий силовой трансформатор или инвертор, а ко второй – соединительные шины (провода), а также держатель с рабочим электродом.
Во время ручной дуговой сварки металлоконструкций на обрабатываемые заготовки и электроды подаётся ток от преобразовательного устройства, за счёт которого образуется электрическая дуга. Высокая температура в зоне горения расплавляет металл, образуя сварочную ванну, какое-то время находящуюся в жидком состоянии.
В пределах ванны расплавленные металлы электродов и заготовок смешиваются между собой, а выделяющийся в результате шлак всплывает наружу и формирует защитную плёнку.
После остывания и затвердения материала в зоне ванны образуется так называемый «сварной шов». Для получения красивого и прочного стыкового соединения необходимо соблюдение ряда требований, касающихся как режима сварки и качества дуги, так и техники обращения с держателем электродов.
При оценке качества сварки в первую очередь исходят из того, насколько форма шва соответствует заданному стандарту, и из его внешней привлекательности. Но не менее важна и его внутренняя структура, определяющая прочность и надежность получившегося при этом контакта.
Контроль качества
Качеству сварки металлоконструкций в процессе их сборки уделяется особое внимание, поскольку малейшее отклонение от технологических требований способно привести к нежелательному результату (браку).
Основным документом, регламентирующим порядок контроля качества сварных конструкций, является руководство (свод рекомендаций или инструкций) под обозначением РД 34 15.132-96.
Этот нормативный документ помимо перечня требований к сварке конструкций определяет технологические нормы оценки качества образуемых сварных соединений.
Кроме того, он предписывает порядок проведения сварочных работ при укрупнении существующих или монтаже новых металлоконструкций. В этом руководящем документе определяются требования к уровню квалификации операторов сварочного процесса и контролёров, а также общий порядок организации работ.
В отдельном разделе приводятся требования к основным и расходным материалам, использование которых обеспечивает высокое качество сборки и сварки металлоконструкций.
Работа с листовыми заготовками
При рассмотрении технологических особенностей работы с листовыми изделиями особое внимание следует уделить последовательности сварки заготовок. При наличии в обрабатываемой металлоконструкции разнонаправленных сочленений в первую очередь варятся поперечные швы. И лишь по завершении их формирования можно будет переходить к продольным соединениям.
В процессе таких работ должен использоваться метод сварки, при котором потребление энергии минимально.
Для тонколистовой стали расчёт энергозатрат ведётся в единицах мощности, приходящихся на погонный метр изделия.
При вертикальной сварке её предпочтительнее вести по строго фиксированному направлению – сверху вниз. Кроме того, обязательно должно соблюдаться следующее правило: между листовыми заготовками металлоконструкции для предотвращения их коробления перед сваркой должны оставаться небольшие зазоры (не менее 1 мм).
Для этих же целей рекомендуется использовать специальные нагрузочные элементы, обеспечивающие удобство сваривания легко деформируемых участков металлоконструкции. Последовательность сплавления листовых заготовок должна соответствовать порядку, изображённому на графиках.
После их рассмотрения можно сделать вывод, что сварка в этом случае должна вестись от середины к краям.
Ремонт металлоизделий
Текущий ремонт металлоконструкций с использованием электродуговой сварки предполагает выправление повреждённых мест методом их пластического деформирования. Как правило, для этих целей применяются особые приспособления, в состав которых входят домкраты винтового или гидравлического действия.
Ремонт (правка) металлоконструкций этим методом без дополнительного нагрева допускается лишь в редких случаях, когда радиусы деформации не превышают определённой величины.
Крупногабаритные и объёмные металлоконструкции ещё до ремонта разбираются на простые составляющие с одновременным удалением имеющихся на них швов, болтовых соединений и заклепок. Причём первые удаляются с применением сварки электрической дугой с использованием угольных электродов, покрытых медью.
Трещины в теле металлоконструкции, а также её повреждённые составляющие завариваются уже описанными методами при условии введения дополнительных продольных накладок. Длина каждого из таких усилительных элементов должна примерно вдвое превышать ширину участка заготовки, подлежащего ремонту.
Элементы трубопроводов с трещинами или разрывами в стенках восстанавливаются путем заваривания повреждённых мест или их удаления. При этом трубы перед электросваркой разделываются любым из известных механических способов (с применением специальных станков, например).
Ремонт и восстановление мест стыковки элементов трубопроводов помимо обычного механического метода, предполагающего использование типового слесарного инструмента, могут проводиться за счёт наращивания металла электросваркой.
Таким образом, для качественной сварки и ремонта металлоконструкций необходимо технологическое сопровождение этих процессов, сводящееся к выполнению определённых условий нормативного характера.
При этом важно не только следовать указаниям действующих стандартов и нормативов, но и владеть достаточным опытом проведения монтажных работ.
svaring.com
Сварка металлоконструкций, технология сварки по ГОСТ
Уже довольно длительное время для соединения любых металлоконструкций используется сварка. Ее применяют как любители, для домашнего использования, так и профессионалы. Вне зависимости от этого, имея большой опыт, ее можно успешно применять как в домашних условиях, так и в производственных целях.
Благодаря прогрессирующим усовершенствованиям методик, эффективность соединения даже крупных металлоконструкций, на сегодняшний день выросла в разы. В том числе благодаря инновациям и модификациям современных сварочных аппаратов. Об особенностях соединения конкретных конструкции из металла и пойдет речь в данной статье.
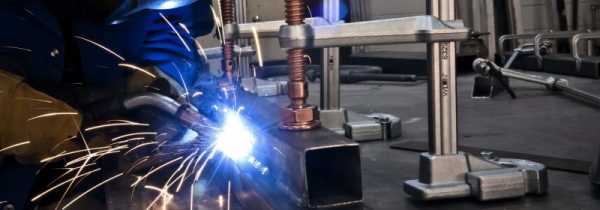
Требования к сварке металлических конструкций
Следующие требования к монтажу металлоконструкций и сварке, в большей степени относятся к профессиональным работникам, но в случае если человек хочет развиваться в данном деле, то неплохо было бы ознакомиться со следующей информацией.
Для определенных видов металлоконструкций используются специальные виды материалов из которых изготавливаются элементы правильной геометрической формы. Также важно чтобы характеристики прочности и свариваемости соответствовали требуемым по регламенту СНИП II 23-81 и ГОСТу 27772-88. Также в этом документе присутствуют разделы посвященные схемам того как правильно создаются швы и каким образом их качество влияет на устойчивость и долговечность всей конструкции. Сложность работы зависит от количества и формы деталей.
Скачать ГОСТ 27772-88
Также не мало важным пунктом является квалификация работника. Так как существуют виды сварки металлоконструкций, собрать которые смогут исключительно работники с давних пор знакомые с таким ремеслом, и работа новичков в просто не допустима. Более подробный список подобных сооружений регламентирован документом РД 15.132-96 Минтопэнерго РФ.

Пример сварки металлоконструкций
Также по ГОСТам Российской Федерации — сварка ответственных металлоконструкций должна быть контролируемой.
Скачать ГОСТ 5264-80
Классическая технология
Классическая технология сварки металлоконструкций основана на проверенных временем методах, таких как газово-огневая и электрическая сварка. В обоих вариантах способы накладки швов делятся на :
- Автоматический.
- Полуавтомат.
- Ручной.
Автоматический способ основывается на отсутствии физического труда человека. Специальный роботизированной аппарат, в зависимости от проводимых работ, переводится в правильный режим и выполняет работу, тем самым заменяя собой человека. Подобные агрегаты имеют ограничения, прокомментированные в их инструкциях. Выгоднее всего использовать подобные машины в массовом производстве компаниями, продукция которых нуждается в большом количестве соединений.
Ручной метод подразумевает наличие физического человеческого труда. В него входят контроль над сварочными электродами и формированием соединения. Чаще всего под ручным методом подразумевается:
- Использование стандартной сварки с нанесением флюса.
- Пайка металлоконструкций газосварочным устройством.
- Электродуговая сварка.
Последний способ популярен при работе в домашних условиях под собственные нужды, либо на небольшом предприятии, так как крупное производство будет иметь большие затраты на поддержание подобного способа сварки конструкций.
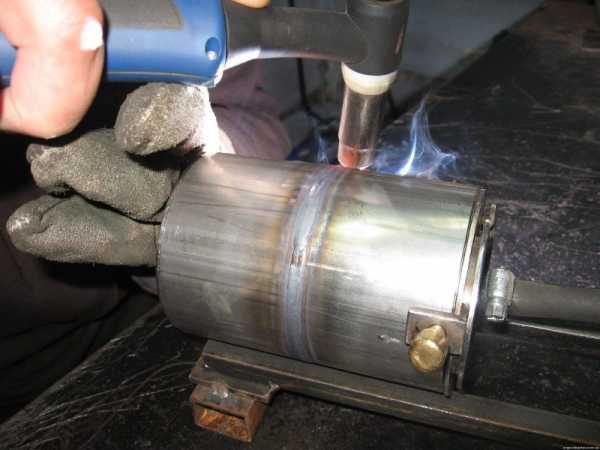
Сварка полуавтоматом
Полуавтомат — подразумевает обработку швов вручную, но подача самого электрода осуществляется автоматически, благодаря чему возрастает производительность труда. И в совокупности человеческого фактора и автоматического способа сварки, роботизированный метод соединения имеет большую популярность, и получил развитие как среди любителей, так и профессионалов данного дела.
Виды сварки для сборки металлоконструкций
Серьезным вопросом является вид сварки, применяемый при соединении швов. Марка стального профиля, его состав и толщина не единственное что имеет вес в вопросе удачности обработки шва. Также большое влияние имеет вид сварки.
Механизация производства повлияла на выбор цеховой сварки в пользу основанных на порошковых проволоках или автоматическом процессе, который выполняется в среде инертных газов либо в слоях флюса. Разница в методах состоит в том что первый из них, в основном, распространяется на соединения угловых швов расположенных под потолком или вертикальные соединения, в то время как второй вариант подходит для соединения деталей в нижних положениях.
Ранее очень распространенным видом соединения была электрошлаковая сварка, которая на данный момент практически не используется, в связи с тем что исследование специалистов в данной области показало ненадежность металлоконструкций возведенных этим способом, и что при отрицательных температурах она теряет свою прочностные характеристики.
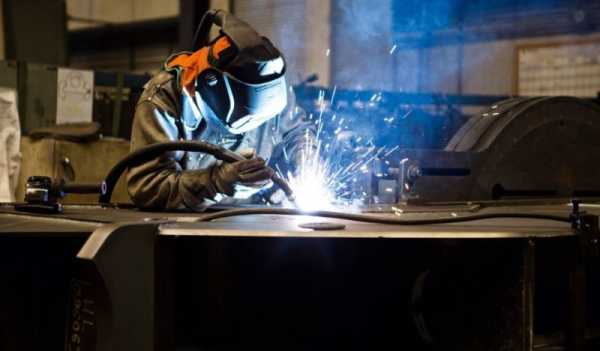
Ручная дуговая сварка
По этим фактам можно рассудить, что в рабочих помещениях и даже на открытых участках, работы можно проводить используя любой вид сварки. Любопытно то, что иностранные фирмы, предприятия которых оснащены современными автоматами, все же большее внимание уделяют ручной дуговой сварке металлоконструкций. Серьезным примером может послужить Япония, значимые предприятия которой используют более 60% ручной сварки для возведения важных металлоконструкций.
Температурный режим сварочного процесса
Температура воздуха имеет большое влияние на выбор применяемой технологии создания шва и на его качество.
Дело в том, что нельзя производить работы по возведению металлоконструкций если температура самих заготовок опускается ниже — 18 °С. В таких условиях температура должна контролироваться измерением в области соединения двух деталей. И если она окажется ниже критической сами заготовки перед созданием шва подвергаются термической обработке. Прогревается не весь элемент, а только на небольшое расстояние от края, равное толщине заготовки, либо на расстояние не менее 75 мм в любом направлении.
Если же шов должен быть создан между деталями, изготовленными из разных сплавов, то подогрев обеих производится по температурному режиму самой прочный из них (по прочности материала). Не стоит забывать также что температура прогрева зависит от некоторых характеристик самого материала.
Как пример послужит сталь марки А514, полотно которой при толщине превышающей 40 мм требует нагрева до 210 °С. Более толстые детали, изготовленные из данной стали, прогреваются уже до 235 °С.
Сварка конструкций — особенности
Само понятие сварки применимо не только к изделиям из металлических сплавов, но также и к изделиям из полимеров, то есть, например из пластмассы. Ведь данное понятие подразумевает термический процесс обработки, при котором две и более деталей объединяются в единую состовляющую.
Сами работы подразделяются на два шага — сборка и соединение. Первый имеет самую большую трудоемкость работы.
Ведь чтобы качество возведенной металлоконструкции было прочным, нужно чтобы все заявленные требования к заготовкам и материал из которого они были выполнены наблюдались до конца работы.
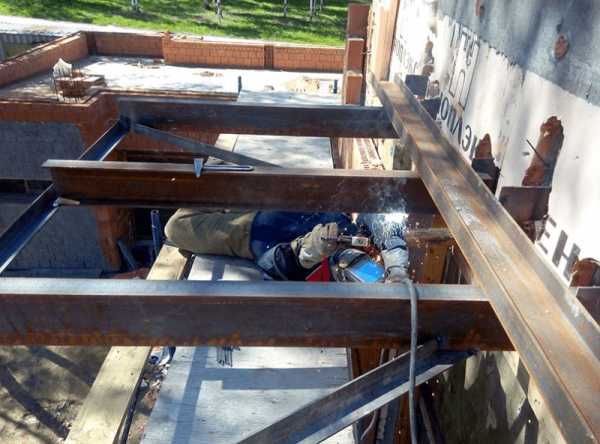
Выполнение сварочных работ
С объективной точки зрения на сборку будущей металлоконструкции и тратится более половины всего периода работ.
Обеспечение правильной сборки
Обеспечение высококачественного завершения работ также основывается на правильном следовании определенному перечню правил по сборке металлоконструкций:
- Подбирая детали из которых будет состоять металлоконструкция, стоит придерживаться чертежей, которые были обрисованы при составлении проекта. Иначе минимальными потерями будет несоответствие внешнего вида конструкции, а в худшем случае она не сможет выполнять возложенные на нее функции.
- Исходя из плана проекта каждый элемент должен находиться на своем месте.
- Ширина зазоров имеет не последнюю роль при возведении конструкций. Если в конечном итоге они будут иметь большие габариты, чем должны были по задумке, то данный факт очень сильно отразится на прочности изделия. Но в свою очередь чересчур мелкие зазоры могут негативно отразиться на правильной работе подвижных деталей.
- Любая конструкция имеет углы, уровень которых должен быть проконтролирован при помощи специальных инструментов. Там, где это требуется углы должны быть исключительно прямые, иначе это очень сильно отразится на положении конструкции и вызовет ее перекос, или даже приведет к полному разрушению.
- Стыковые соединения должны быть обеспечены зазорами с достаточным пространством для допустимого люфта элементов.
- На протяжении возведения всей конструкции данные моменты необходимо учитывать. Особенно в случае с автоматической сваркой, ведь при ручной технологии рабочий может проконтролировать и скорректировать направление детали, что практически невозможно сделать при использовании автоматических приспособлений. Но в тоже время роботизированное вмешательство в сварку практически исключает погрешности, вызываемые человеческим фактором.
Положительные стороны сварки
Помимо сокращения рабочего времени и качества, сварка положительно сказывается и на иных характеристиках:
- В связи с тем, что во время сварочного процесса задействуются лишь два элемента, исключая влияние иных факторов, то финальная спайка по массе никак не отличается от изначального варианта, что в свою очередь позволяет экономить количество материала.
- Из-за своих особенностей, сварка практически полностью лишена ограничений в работе по фактору толщины материала. Вся ответственность за это перекладывается только на использование определенного оборудования.
- Разносортные сварочные аппараты современных образцов позволяют производить соединительные работы практически с любыми материалами без потерь в прочности шва, учитывая даже фактор проведения манипуляций с таким сложным материалом как алюминий.
- Немало важным положительным моментом использования сварки является экономия денег и рабочего времени.
- Чем тяжелее вид сварки, тем сложнее может быть тип конструкции. Также она дает возможность использовать элементы, изготовленные при помощи штамповки или отлитые в формах. При этом материал, из которого они изготовлены не играет особой роли.
- Сварочные агрегаты, представленные на сегодняшнем рынке вполне доступны по цене, а также при использовании правильно подобранной методике можно повысить коэффициент по скорости производства.
- Если имеется возможность, а также желание предприятия возводить конструкции, при сборке которых будут использоваться нестандартные материалы, сварка поможет легко осуществить данную задачу.
- Сварка более чем применима даже для работы с очень мелкими деталями.
- Сварка в целях ремонта или приведения механизмов в рабочее состояние так же очень уместна.
- При применении сварки каждая конструкция будет иметь абсолютную герметичность. Из всех доступных способов соединений стыков — сварка имеет наивысший показатель надежности по этому параметру.
Сварные соединения и их виды
Сварные соединения классифицируются по наличию одного из следующих признаков:
- Месторасположение соединения 2 деталей.
- Тип применяемого сварного шва.
- Сварочные технологии, применяемые при соединении.
- Окружающими условиями, при которых проводился сам процесс
- По толщине деталей.
- Марка сплава, из которого изготовлены детали.
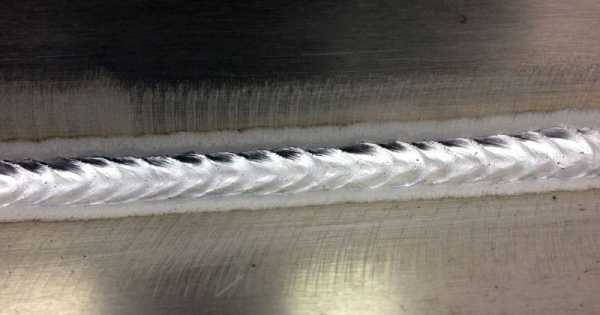
Сварной шов по алюминию
Касательно первого пункта плана, днетали, по геометрическому расположению, имеют четыре вида соединения:
- Встык, одноплоскостное соединение двух заготовок.
- Внахлест, когда заготовки привариваются при наложении края одной детали на край другой.
- Угловые соединения — объединение деталей под определенным углом.
- Тавровое соединения. Сварка при примыкании детали к другой торцевой плоскостью.
Стыковые соединения выполняются проваром по толщине элемента или при создании шва на выводных планках. Если сварочный процесс выполняется вне цехового помещения, то соединение можно организовать односторонней сваркой, с дальнейшей подваркой основания шва, что подразумевает собой заполнение пространства между элементами, производимое по одной из кромок.
Работа основывающаяся на выводных подкладках кардинально разнится с предшествующей. Подкладка должна прилегать к кромке объединяемых деталей — это раз. Образовавшееся пространство должно иметь размеры не более 6 мм. Данное условие распространяется на метод ручной сварки. Если же работа выполняется механизированным способом. То он не должен превышать 15 мм. Подкладки выбираются исходя из параметра толщины, чтобы во время рабочего процесса не случился прожог детали.
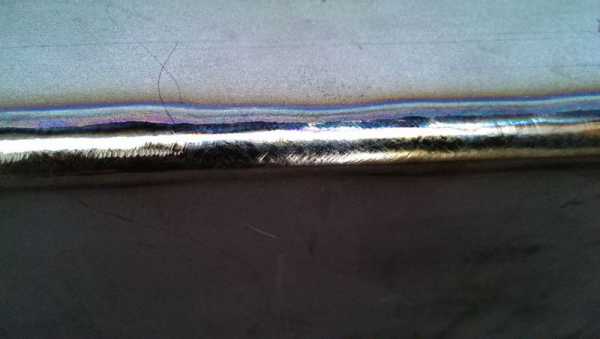
Сварной шов по титану
В возводимых конструкциях, основанных на стыковых соединениях, нередко объединяются заготовки, выполненные в разной толщине. В таком случае применяется метод обработки, при котором уменьшается угол наклона у стали с большей толщиной, который должен соответствовать 1/8 наклона растянутых заготовок металлоконструкции, или 1/5.для сжатых элементов.
Сварные узлы в металлоконструкциях
Все конструкции, выполненные из металла, держатся на основе из сварных узлов, являющихся основой стыковых соединений. При разработке проекта инженеры должны учитывать удобные условия для качественного проведения работ в этих узлах. К ним относятся:
- Условие на то, чтобы узлы были сварены угловым ли стыковочным соединением.
- Нижнее положение сварки является приоритетным.
- В основном использовать механизированную или полностью роботизированную сварку, дабы гарантировать качество выполненной работы.
Среди соединительных узлов есть много подвидов, к большинству из которых заявлены различные требования. Как хороший пример послужит — балочный узел. В нем самое большое внимание сконцентрировано на расстоянии между сварочными швами, так как оно не должно быть короче толщины самого толстого стального элемента деленного на 10, входящего в состав данного узла.
Если вы нашли ошибку, пожалуйста, выделите фрагмент текста и нажмите Ctrl+Enter.
stankiexpert.ru
Как мы собираем и свариваем металлоконструкции на ЗМК Аполло
Мы выделяем 5 основных элементов влияющих на качество сборки и сварки строительных металлоконструкций.
Мы уверены что использование «правильных» материалов и оборудования делают «правильный» результат. Первое на что нужно обратить внимание — это сварочные газы.
Это того стоит?
Ar 82% + CO2 18% Смесь «CORGON» дороже в 5 раз чем углекислота, но эффект стоит того. Повышается скорость, лучше провар, красивый ровный шов, отсутствие шлака и брызг.
Отличие смеси Коргон от углекислоты можно прочитать в буклете «CORGON» прогрессивная замена кислоты”.PDF
Благодарим за непрерывное и качественное снабжение газами нашего Поставщика LINDE- GAS.
Какая проволока ?
Поставщиков проволоки сегодня огромное множество.
Путём испытаний мы остановились на одном производителе.
Продукт не дешёвый, но качество важнее!
И еще мы теперь пользуемся большой упаковкой ESAB MARATHON PAC (Описание упаковки, PDF — файл), описание применяемой сварочной проволоки ESAB Св-08Г2С , PDF файл
Чем варить?
Сварочные аппараты, подающие устройства и даже горелки, важны в сварке.
Удобство регулировки, стабильность дуги — все это залог лучшего шва.
〉2. Технология и процессы
Стандартизация процессов – каждый сварщик и сборщик специализируется на определенных группах конструкций.
Например есть сборщики которые каждый день собирают только колонны. Другие только стропильные фермы. Кто-то только связи и распорки и т.д.
Мы определяем время такта — к примеру 10 полуферм в смену и работаем в таком режиме несколько недель.
Таким образом достигается высокая скорость и стабильное качество.
Стандарты работы
-
- Памятка СВАРЩИКА
-
- Памятка Сварщика ЗМК Аполло 2 лист
Все этапы работы сварщиков и сборщиков описаны в подробных инструкциях и памятках.
Картинки и фотографии облегчают понимание и работа доводится до автоматизма.
〉3. Качество заготовки
Сборка металлоконструкций на «прихватку» это ключевой этап.
Необходимо точное соответствие всех геометрических параметров конструкции. Во многом это определяется качеством заготовки и этому процессу уделяется особое внимание.
Заготовка из листа
Геометрия заготовки, точность отверстий обеспечивается лучшим оборудованием по плазменной резке. Также очень важно зачищать всю заготовку, перед тем как передать сборщику
Заготовка из профильного проката
Качество распила, длина заготовки, входной контроль металлопроката — все это влияет на скорость и качество сборки
〉4. Сварщики и Сборщики

Кадры решают ВСЁ.
Наши сварщики с нами уже более 12 лет.
Многие из них аттестованы в Национальной Ассоциации Контроля Сварки НАКС
Хороший настрой — высокая производительность
Гордость за выполненную работу — вот что является основным стимулом у наших сварщиков. Без спешки и суеты сварщики зарабатывают достойную зарплату.
Благодаря этому они выполняют свою работу с высочайшим качеством.
У всех Сборщиков и Сварщиков — оклады и определенные нормы на производство конструкций, в соответствии с временем такта. ( Например 8 полуферм в смену, т.е. 1 полуферма в час)
〉5. Контроль ОТК
Аттестованная Лаборатория неразрушающего контроля выдаёт Заключение на все ответственные сварные швы. Подробно о процессах и результате работ на нашей странице Качество/Технический контроль/Лаборатория неразрушающего контроля
По результату проверки выдаётся «Заключение»
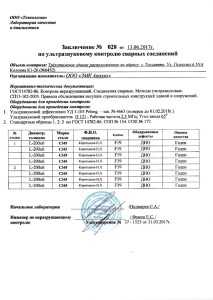
Заключение по УЗК
Контроль качества сварных швов осуществляется несколькими методами — подробнее на странице Качество/Технический контроль/Качество сварки
На всех этапах сборки конструкции на «Прихватку» ведется контроль ОТК — подробнее на странице Качество/Технический контроль/Контроль сборки
apollo-zmk.ru