Термообработка молибдена – Способ термообработки молибдена и вольфрама
alexxlab | 16.02.2020 | 0 | Вопросы и ответы
Способ термообработки молибдена и вольфрама
О П И С А Н И Е «1;666 66
ИЗОБРЕТЕНИЯ
К АВТОРСКОМУ СЬИДЮТВЛЬСТЬУ
Союз Советских
Социалистииеских
Республик (б1} Дополнительное к авт. свил-ву
{22) Заявлено 08.1 2.7 5 (21) 21967 21/02 с присоединением заявки № (23) Приоритет (43) Опубликовано 25.04.77.Бюллетень № 15 (45) Дата опубликования описания08.06.77
Р1) М, К.i
С 22 F 1/18
Гасударственный номитет
Совета Министров СССР па делам изобретений и открытий (53) УДК 621.785.34.. 062 (088,8) Н. П. Бондаренко, А. И. Сомов и Б. И. Шаповал (72) Авторы изобретения (71) Заявитель (54) СПОСОБ ТЕРМООБРАБОТК1! МОЛИБДЕНА
И ВОЛЬФРАМА
Изобретение отностттся к метаппургии.
Известен способ термообработки попуфабрикатов в виде попас, лент, прутков из молибдена и вольфрама путем. отжига в вакуум.е . 5
Однако из-за низкой пластичности и прочности этих металлов в рекристаллизованном состоянии их применение в качестве конструкпионного материала ограничено.
Известен способ термообработки изде- )p пий из мопибдена и вольфрама путем кратковременного окунания в ванну с расплавом олова при температуре 1100 1200 С з в вакууме 10 мм рт.ст.
Обработанные таким образом. изделия 15 или полуфабрикаты покрываются зашитной пленкой олова, однако пластические характеристики (относительное удлинение д ) при этом. сушественно не изменяются, не превышая 4%. 20
Белью изобретения является способ тер мообработки мопибдена и вопьфрама, позвопяюший получить изделия и полуфабрикаты в рекристаппизованном состоянии с высокими пластическими свойствами. 25
Способ состоит в том, что заготовки из вольфрама ипи молибдена отжигают, поместив в тигель с расплавом меди, темпео ратура расплава составляет 1250-1500 С, и выдерживают в течение от 0,5 до 2 час.
После окончания отжига заготовку извлекают из тигля и охлаждают в инертной атмосфере. После обработки относитепьное удлинение с достигает 40-45 %.
Отличительным признаком является отжиг в расппаве жидкой меди, температура которого выше температуры рекристаллизации обрабатываемого метаппа.
Зничитепьное увеличение пластических свойств связано с тем, что в расплав меди при высокой температуре и достаточном времени выдержки с границ зерен обрабатываемого метапла диффундируют охрупчиваюшие примеси, которые обладают большей растворимостью в меди.
Способ бып применен дпя термообработ ки листового молибдена. Лист молибдена в виде разрывного образца предварительно протравили в смеси серной, азотной и ортофосфорной кислот в соотношении 30:30:40%
555166
Составитепь Г. Кандыва
Редактор М. Рогова Техред М. Ликович Корректор С. Бопдижар
Заказ 422/14 Тираж 802 Подписное
БНИИПИ Государственного комитета Совета Министров СССР по делам изобретений иоткрытий
113035, Москва, Ж-35, Раушская наб., д. 4/5
Филиал ППП “Патент», г, Ужгород, ул. Проектная, 4 и погрузили в тигель с расплавом меди температура которого составляла 1300 С.
Ь
После выдержки в течение 1 час образец был извлечен из тигля и охлажден в,среде аргона. Измеренное относительное удлинение образца составило 45 %.
Изделия и полуфабрикаты, обработанные таким образом., могут быть широко использованы в качестве конструкционных матери. алов. !О
Кроме того, полуфабрикаты и готовые изделия из молибдена и вольфрама, подвер« гнутые отжигу по предлагаемому способу, могут быть в дальнейшем нагреты до температур, превышаюших температуру рекристаллизации, без потери ппастических и прочностных свойств.
Формула изобретения
Способ термообработки молибдена и вольфрама путем отжига, о т л и ч а юш и и с я тем, что, с целью повышения пластических характеристик, отжиг ведут в расплаве меди при температуре
1250 1500оС.
www.findpatent.ru
Молибден и его сплавы – свойства, производство, обработка и применение
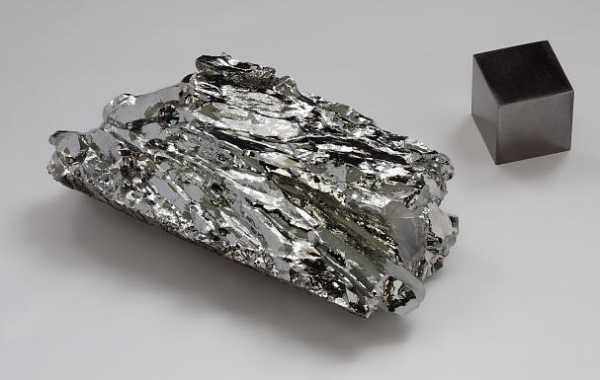
Молибден (лат. molybdaenum) — химический элемент с атомным номером 42 и атомной массой 95,94. Обозначается символом Mo. Это ковкий переходный металл, который имеет серый цвет со стальным оттенком в свободном состоянии и становится серо-черным в диспергированном виде. Открыто порядка 20 минералов молибдена, а в свободном виде он не встречается.
Название металла происходит из греческого слова «молибдос», что в переводе означает «свинец». Такое название было выбрано из-за того, что минеральный молибден имеет характерный блеск, очень похожий на блеск свинца.
В 1778 году шведский химик К. Шееле впервые получил минеральный молибденит путем прокаливания молибденовой кислоты. Еще один шведский химик П. Гьельм получил молибден в виде нечистого металла в 1781 году и только в 1817 году Й. Берцелиусу удалось вывести этот элемент в чистом виде.
Присутствие в природе
В земной коре находится 0,003 % молибдена в составе минералов. Он распространен относительно равномерно, более концентрирован в породах, в которых содержится диоксид кремния. Для кристаллизации металла необходимы высокая кислотность и восстановительная среда. Наименьшее содержание молибдена фиксируется в карбонатных и ультраосновных породах.
Металл также содержится в нефти, углях, золе растений и воде — речной и морской. Морские воды на глубине более обогащены молибденом, чем воды у берега. В космосе зафиксировано аномально высокое содержание молибдена внутри красных гигантов с нейтронными звездами.
Самые крупные месторождения металла находятся в США, России, Армении, Канаде, Мексике, Чили, Австралии и Норвегии.
Физические свойства
Свойство |
Значение |
Группа металлов |
Тугоплавкий |
Плотность при 20°С |
10,2 г/cм3 |
Температура плавления |
2610 °С |
Температура кипения |
4612 °С |
Теплопроводность |
142 Вт/(м*К) |
Теплота плавления |
28 кДж/моль |
Теплота испарения |
590 кДж/моль |
Удельная теплоемкость |
0,256 Дж/(г*К) |
Электросопротивление |
5,70 мкОм*см |
Молярный объем |
9,4 см3/моль |
Модуль сдвига |
122 ГПа |
Твердость |
125 НВ |
Коэффициент линейного расширения |
4,9 10-6 К-1 |
Химические свойства
Молибден устойчив при нормальных условиях. Окисление начинается, когда металл нагревается до температуры 400 ⁰С. После 600 ⁰С происходит быстрый переход в триоксид молибдена.
Основные химические свойства металла представлен в таблице:
Свойство |
Значение |
Ковалентный радиус: |
130 пм |
Радиус иона |
(+6e) 62 (+4e) 70 пм |
Электроотрицательность (по Полингу): |
2,16 |
Электродный потенциал: |
0 |
Степени окисления |
6, 5, 4, 3, 2 |
Производство молибдена
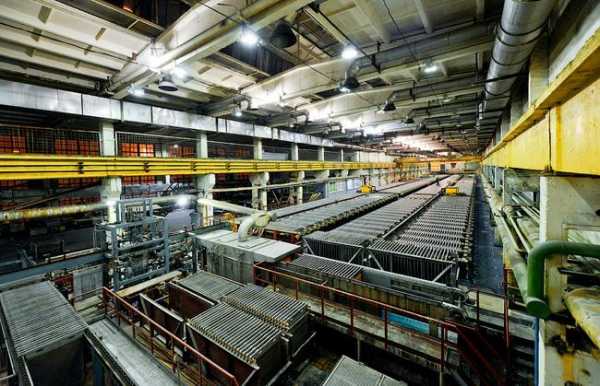
Для производства молибдена в России и мире в качестве сырья используются молибденитовые концентраты, из которых получается чистый металл — основа для сплавов. В концентратах содержится около 20 % примесей, 1-9% оксида кремния, 28-32% серы и примерно 50 % молибдена.
Этапы производства:
- Концентрат подвергают окислительному обжигу при температуре 600 ⁰С. На выходе получают оксид молибдена, который содержит значительное количество примесей.
- Оксид очищают от примесей путем выгонки или выщелачивания огарка и дальнейшей нейтрализации.
- В трубчатой печи из чистого оксида получают порошковый металлический молибден. Для этого процесса применяют ток сухого водорода.
- Порошок превращают в металл. Как правило, для этого используют один из двух методов — плавка или порошковая металлургия.
Для получения ферромолибдена применяется реакция восстановления молибденитового концентрата, который предварительно подвергается обжигу.
Обработка молибдена
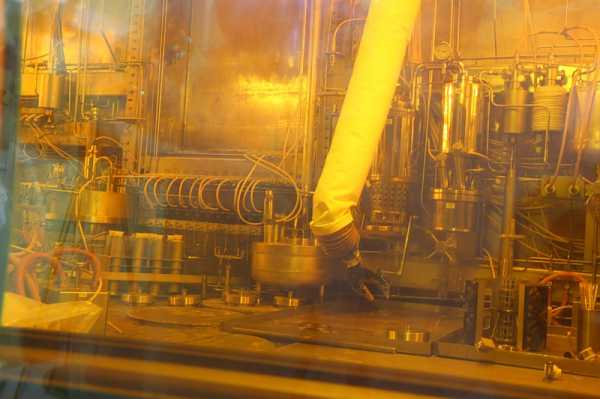
Как правило, используется термообработка молибдена, так как у него невысокая вязкость, а при низких температурах металл показывает низкую пластичность. Небольшие штабики обрабатывают на обжимных машинах, а для крупных заготовок применяют спекание и горячую прокатку.
Иногда возможна механическая обработка молибдена резанием. Для этого используют инструменты из быстрорежущей стали с такими же углами заточки резцов, как и при резании чугуна.
Достоинства и недостатки молибдена
Достоинства |
Недостатки |
Благодаря низкой плотности молибдена сплавы на его основе имеют большую удельную прочность. Высокий модуль упругости. Термостойкость. Жаропрочность. Высокая коррозионная устойчивость. Молибден не реагирует с плавиковой, соляной, серной кислотами и с большей частью щелочных растворов. Металл имеет малый температурный коэффициент расширения. |
При использовании молибденовых сплавов сварные швы отличаются хрупкостью. При низких температурах обладает малой пластичностью. При нагартовке можно упрочнять металл только до температуры 800 ⁰С. При дальнейшем нагревании происходит образный эффект — металл разупрочняется. Низкий уровень окалийности. |
Молибден в организме человека
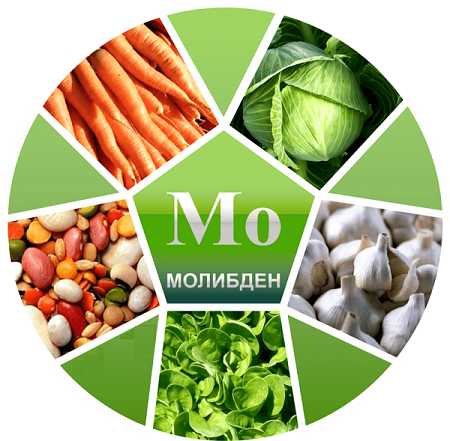
Молибден относится к микроэлементам, необходимым человеку. Он содержится преимущественно в костях, почках и печени, а также в головном мозге, щитовидной и поджелудочной железах, надпочечниках.
Роль и функции молибдена для организма:
- Участвует в углеводном, белковом и липидном обмене, в процессах очищения от мочевой кислоты, альдегидов и прочих вредных веществ.
- Снижает интоксикацию после употребления алкоголя.
- Укрепляет кости и зубы.
- Улучшает половую функцию.
- Препятствует возникновению подагры и анемии.
- Участвует в тканевом дыхании и синтезе витамина С.
Суточная потребность в молибдене составляет от 70 до 300 мкг в зависимости от массы тела. В случае дефицита микроэлемента в организме и болезней, которые им вызваны, суточная норма увеличивается.
Основные марки молибдена
В промышленности используется чистый молибден и с различными присадками. Среди наиболее распространенных можно выделить следующие марки:
- МЧ — чистый металл: в нем содержится не менее 99,96 % молибдена и до 0,04 % примесей. Эта марка находит применение в изготовлении проволоки, которая используется в производстве источников света и электронных приборов. Также МЧ применяют в изготовлении деталей электровакуумных приборов.
- МЧВП — чистый молибден, который производится методом вакуумной плавки.
- МРН — еще один вид чистого молибдена, однако в отличие от МЧ и МЧВП в его составе содержится большее количество примесей — до 0,08 %. Основная область применения МРН — производство проволоки для источников света и электронных приборов.
- МК — молибден с кремнещелочной присадкой. Из него также изготавливают проволоку.
- ЦМ — металл с присадкой циркония или титана.
Сплавы молибдена
Используется два сплава на основе данного металла: с вольфрамом (МВ) и рением (МР).
Сплавы молибдена с вольфрамом необходимы для повышения жаропрочности первого. При этом ухудшается деформируемость и повышается удельный вес. В таких сплавах содержится от 48 % вольфрама и от 49 до 51 % молибдена, остальное — примеси. МВ является тугоплавким, отличается высокой прочностью и устойчивостью к коррозии. Используется для изготовления тонкой проволоки, которая сворачивается в катушки или бухты.
Рений необходим для повышения пластичности молибдена. Сплавы МР содержат более 50 % рения и около 47 % молибдена. Они также используются для производства тонкой проволоки, которая применяется в специальном приборостроении.
Применение молибдена
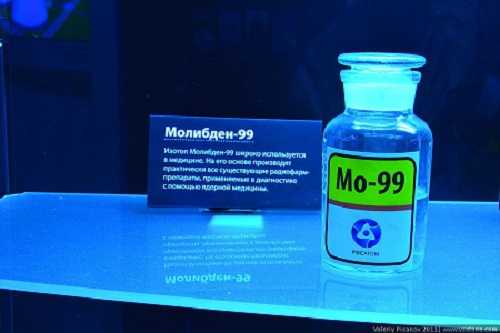
Металл используется в разных областях:
- В самолетостроении и ракетостроении.
Молибден и его сплавы применяются для обшивки сверхзвуковых самолетов и ракет, а также в производстве головных частей самолетов и ракет: они могут использоваться в качестве основного конструкционного материала или служить тепловым экраном.
- В цветной металлургии.
Молибден значительно повышает прокаливаемость стали, прочность, устойчивость к коррозии и вязкость. Сплавы стали с добавлением молибдена применяют для изготовления ответственных изделий и деталей.
Использование молибдена в цветной металлургии также охватывает сплавы кобальта и хрома. Такая добавка повышает твердость, в результате чего сплав может быть использован для истирающихся кромок деталей. Молибден также входит в состав жаростойких кислотоупорных сплавов на основе хрома, никеля и кобальта.
Так как молибден имеет высокую температуру плавления, его применяют при изготовлении инструментов для горячей обработки стали. Из него также производят стержни для литья под давлением различных сплавов.
- В химической промышленности.
Из молибдена делают оборудование, работающее в кислотной среде. Из него также изготавливают нагревательные элементы для печей, которые работают в атмосфере водорода.
Многие соединения молибдена служат катализаторами реакций. Некоторые из них также входят в состав глазурей и красок.
- В стекольной промышленности.
Этот металл устойчив в расплавленном стекле, благодаря чему его применяют при плавке стекла и производстве электродов.
- В радиоэлектронной промышленности и рентгенотехнике.
Из молибдена изготавливают детали вакуумных приборов — рентгеновских трубок, электронных ламп и др.
ferrolabs.ru
Пластичность – молибден – Большая Энциклопедия Нефти и Газа, статья, страница 1
Пластичность – молибден
Cтраница 1
Пластичность молибдена и его сплавов существенно зависит от чистоты внешней среды при отжиге. Так, при отжиге в атмосфере аргона, загрязненного примесями углеводородов, происходит насыщение углеродом, понижение прочности и охрупчивание. [1]
Пластичность молибдена определяется чистотой исходного металла, легированием, методом выплавки, деформацией, термической обработкой и структурой. Особое влияние на пластичность оказывают примеси внедрения. [2]
Пластичность молибдена и его сплавов определяется также исходной структурой слитка. Металл, выплавленный в индукционной печи, имеет более мелкокристаллическую структуру, и слитки такого металла, как правило, обладают более высокой пластичностью. Сплавы, полученные дуговым методом плавки, отличаются сильно развитой грубой транскристаллической структурой, пронизывающей все сечения, что является одной из причин пониженной пластичности молибдена, выплавляемого этим методом. [3]
Пластичность молибдена и способность к глубокой вытяжке в значительной степени определяется металлургическими факторами ( содержание примесей, струк-тура, степень предварительной деформации и пр. [4]
Падение пластичности молибдена после рекристал-лизационного отжига некоторые авторы [28, 206] связывают с сегрегацией примесей внедрения на границах зерен. [5]
Прочность и пластичность молибдена, довольно высокие на холоду и в отожженном состоянии, заметно изменяются в зависимости от температуры, вида механической и термической обработки, а также от чистоты металла. Способ изготовления молибдена значительно сказывается на всех свойствах, в том числе и на механических. В настоящее время компактный и достаточно чистый металл изготовляется методом порошковой металлургии и методом дуговой плавки в атмосфере водорода, а также плавкой в электронном пучке. Порошок чистого молибдена получается восстановлением окислов или кислоты Н2МоО4 водородом. [7]
Механическая прочность и пластичность молибдена, довольно высокие на холоду и в отожженном состоянии, заметно изменяются в зависимости от температуры, вида механической и термической обработки, а также от чистоты металла. Способ изготовления молибдена значительно сказывается на всех свойствах, в том числе и на механических. В настоящее время компактный и чистый металл изготовляют методом порошковой металлургии с последующей ковкой или с переплавкой в вакууме в дуговых и электронно-лучевых печах. Порошок чистого молибдена получают, восстанавливая окислы водородом. [8]
Столь поразительное улучшение пластичности молибдена с 35 % атомн. [9]
Вследствие невысокой вязкости и пластичности молибдена при низкой температуре обработка его производится не в холодном состоянии, а при нагреве до сравнительно невысокой температуры, за исключением, обработки тонкой проволоки и листа. [10]
Вследствие невысокой вязкости и пластичности молибдена при низкой температуре обработка его производится не в холодном состоянии, а при нагреве до сравнительно невысокой температуры, за исключением обработки тонкой проволоки и листа. [11]
Углерод повышает прочность и понижает пластичность молибдена. В отдельных случаях малые количества углерода могут несколько повысить пластичность вследствие раскисляющего действия и уменьшения величины зерна. [12]
Отсюда ясно следует, что пластичность молибдена или его хрупкость ( хладноломкость) есть функция чистоты. [13]
В связи со значительным повышением пластичности молибдена и сплавов на его основе после предварительной деформации ковку и штамповку деформированных заготовок осуществляют при более низких температурах с предварительным вакуумным отжигом в течение 5 ч для сплава с содержанием циркония до 0 4 % при 1450 С, а с содержанием циркония до 0 2 % при 1400 С. [14]
Повышение содержания легирующих элементов также понижает пластичность молибдена. [15]
Страницы: 1 2 3 4
www.ngpedia.ru
Высокопрочные термически улучшаемые стали с молибденом
Из сталей такого рода высокими эксплуатационными свойствами обладают термически улучшенные стали с молибденом, приобретающие после закалки в воде структуру мартенсита. Химический состав и механические свойства этих сталей подробно рассматривались в ряде работ.
Высокая экономическая эффективность применения сталей с σт ≥ 600 Н/мм2, содержащих ~0,2 % Мо, привела к созданию за рубежом большого числа марок стали такого типа. В этих сталях сочетание 0,2 % Мо + В служит обычно основой легирования, обеспечивающей требуемую прокаливаем ость в тол стол истовом прокате толщиной до 30 мм. В качестве других легирующих элементов выбирали следующие: хром, введение которого подавляет перлитное превращение; марганец и никель, расширяющие γ-область; малые количества сильных карбидообразующих элементов (ванадия, титана, циркония), повышающих стойкость стали против разупрочнения при высоком отпуске и в зоне термического влияния сварки. Кроме того, никель улучшает сопротивление стали хрупким разрушениям. В некоторых марках стали присутствует медь, повышающая сопротивление низколегированных сталей коррозии. В сталях рассматриваемого типа содержание углерода не превышает 0,2 %, кремния — 0,9%, марганца — 1,3%. Стали с 0,2 % Мо содержат меньше Si, Мn, другие легирующие элементы используются в различных сочетаниях.
Для окончательного выбора оптимального состава стали в 5-т электродуговых печах выплавили сталь разных химических составов, выбранных по результатам проведенных механических испытаний, разливали ее в слитки массой 3,9 т и прокатывали на листы размером 30x2000x6000 мм по принятой на заводе технологии.
Результаты, полученные при механических испытаниях плавки 3, показывают, что высокопрочную низколегированную сталь для сварных металлических конструкций можно создать без применения никеля и меди. Анализ прочностных характеристик проката из исследованных плавок еще раз подтверждает важную упрочняющую роль сильных карбидообразующих элементов (например, ванадия) при использовании сталей в термически улучшенном состоянии. Установлено также, что у закаленных низкоуглеродистых сталей с пределом текучести σт≥600 Н/мм2, поставляемых после отпуска при температуре 650° С, снизить содержание углерода до 0,1 % практически невозможно.
Рассмотрим некоторые свойства проката толщиной до 40 мм из стали 14ГСМФР промышленных партий. Определение прокаливаемое методом торцовой закалки показало, что в исследованном диапазоне толщин прокат обладает сквозной прокаливаемостью.
Исследования показали, что ударная вязкость при температуре —40° С после закалки и отпуска стали 14ГСМФР при различных температурах не зависит от скорости охлаждения после отпуска; исследуемая сталь не склонна к обратимой отпускной хрупкости. Чувствительность стали 14ГСМФР к деформационному старению определяли методом сериальных испытаний на ударный изгиб образцов с γ-образным надрезом после равномерной деформации на 5 % и отпуска при температуре 250° С в течение 1 ч. Результаты позднейших работ изменили точку зрения авторов на рассматриваемые стали. Наиболее перспективной и предпочтительной для применения в строительных конструкциях оказалась многокомпонентная комплекс-нолегированная сталь 14ХГСНМФР.
Для уменьшения себестоимости молибденсодержащих сталей было предложено выпускать их полуспокойными.
Была разработана сталь марки 18Г2АМФпс, себестоимость которой меньше аналогичной по составу спокойной стали. Термически улучшенный прокат толщиной 12-50 мм из стали 18Г2АМФпс обладает механическими свойствами стали класса прочности С590.
Рассмотрим особенности сварки высокопрочных сталей, содержащих 0,2 % Мо. При выборе теплового режима сварки рассматриваемой стали следует соблюдать два условия: во-первых, предупреждать образование холодных трещин в зоне термического влияния и в шве и, во-вторых, обеспечивать минимально возможное разупрочнение основного металла в зоне термического влияния.
Наличие в стали молибдена, ванадия и других карбидообразующих элементов обеспечивает существенное уменьшение степени разупрочнения ее в зоне термического влияния сварки и уменьшение протяженности разупрочненного участка. Благодаря этому при ограничении погонной энергии сварки получают сварные соединения, в которых при проектировании сварных конструкций можно не учитывать разупрочнение. Этому способствует эффект контактного упрочнения мягкой прослойки, проявление которого не снижает агрегатную прочность при растяжении сварного соединения, имеющего ширину зоны разупрочнения и степень разупрочнения металла в этой зоне, не превышающие определенных значений. Диапазон допустимых тепловложений при сварке стали таков, что термически улучшенные стали с молибденом отнесены к разряду неразу-прочняемых при сварке. Так, поданным работы, стыковые соединения проката толщиной 12-20 мм из стали марок 15ХГ2МФР и 14ГСМФР могут свариваться при погонной энергии дуги 8-32 кДж/см без снижения агрегатной прочности соединения. Необходимо также отметить, что чрезмерное увеличение погонной энергии сварки (более 36 кДж/см для элементов толщиной 20 мм) вызывает заметное уменьшение ударной вязкости металла околошовной зоны, особенно при температурах ниже -20° С.
Холодные трещины — один из наиболее часто встречающихся и опасных дефектов сварных соединений высокопрочных строительных сталей, возникающих в процессе мартенситного превращения. Протекая со значительным изменением объема, мартенситное превращение способствует возникновению и росту субмикротрещин по границам зерен. Растворенный в металле водород, который адсорбируется на поверхности микротрещин, стимулирует их рост.
Одним из методов оценки сопротивляемости стали образованию холодных трещин является расчетное определение углеродного эквивалента Сэ. По существующим представлениям, при Сэ > 0,45 % имеется потенциальная возможность образования в сварных соединениях холодных трещин. Эта возможность реализуется при неблагоприятном сочетании основных факторов, обусловливающих образование трещин: наличия структурных составляющих мартенситного типа, содержания определенного количества водорода в металле, растягивающих сварочных остаточных напряжений. Считалось, что в высокопрочной стали с пределом текучести 600-700 Н/мм2 можно предупредить образование трещин в зоне термического влияния в том случае, если в ней меньше 90% мартенсита и твердость меньше НУ415.
Основные технологические меры по предупреждению образования трещин при сварке высокопрочных сталей следующие.
- Замедление охлаждения сварного соединения после сварки, для чего чаще всего применяют предварительный подогрев. Температуру предварительного подогрева принимают в пределах 70-200° С; ее устанавливают в зависимости от состава стали, толщины проката, вида сварки и конструкции сварного соединения; применяется также подогрев, сопутствующий сварке, а также послесварочный подогрев.
- Применение низководородных электродов с фтористокальциевым покрытием при ручной дуговой сварке и основного низкокремнистого флюса (АН-17М, АН-17) при автоматической сварке под флюсом.
- Прокалка и просушка электродов и флюсов, предназначенных для сварки, с целью удаления из них влаги. Считают, что содержание влаги в электродном покрытии не должно превышать 0,2 %.
- Сварка на постоянном токе обратной полярности, позволяющая сократить проникновение водорода из атмосферы в расплавленную ванну шва.
При многослойной сварке стыковых швов применяют «мягкие прослойки» — первые слои шва выполняют с использованием сварочных проволок марок Св-08Г2С, Св-ЮНМА, дающих менее прочный и более пластичный металл шва по сравнению с последующими слоями. Такой технологический прием также повышает стойкость сварных соединений против образования холодных трещин.
Для обеспечения необходимого уровня прочностных свойств металла шва при сварке используют легированные электродные проволоки следующих марок: при сварке под флюсом — Св-08ХН2ГМЮ, Св-08ХМФ, Св-08ХГСМФ и др.; при сварке в среде углекислого газа — Св-10ХГ2СМА, СВ-10ХГ2СН2МЮ и др.
Из высокопрочных сталей, содержащих 0,15-0,25 % Мо, для строительных конструкций наиболее часто применяли сталь марки 12ГН2МФАЮ. Эта сталь была создана на базе стали 12Г2СМФ путем дополнительного легирования никелем, азотом, алюминием; такое легирование привело к повышению хладостойкости из-за специфического влияния никеля и дополнительного измельчения аустенитного зерна.
Способность стали различных марок гасить движущуюся хрупкую трещину при статических нагрузках изучали с помощью испытаний по Робертсону при инициировании трещин статической нагрузкой. Полученные результаты свидетельствуют о том, что по температуре «увязания» трещины (-55° С) исследованный прокат из стали 12ГН2МФАЮ значительно превосходил прокат из других строительных сталей повышенной и высокой прочности. У этой стали К\0 примерно вдвое больше, чем у стали СтЗсп.
Проведенные исследования технологических свойств стали 12ГН2МФАЮ позволили разработать рекомендации по режимам ее холодной механической обработки, гибки, штамповки, вальцовки и т. п. Оказалось, что исследуемая сталь мало склонна к механическому старению: под действием растяжения на 5 % и отпуска при температуре 250° С в течение 1 ч критическая температура хрупкости стали повысилась всего на 3-12° С.
Сталь 12ГН2МФАЮ обладает достаточно хорошей свариваемостью. Анализ изменения твердости в околошовной зоне и результатов испытания поперечных образцов сварных соединений на растяжение показал, что она практически не разупрочняется при сварке. При сварке стали с малыми тепловложениями (1,46 МДж/м2) сопротивление хрупкому разрушению вблизи границы сплавления остается высоким.
Эта сталь применена для изготовления наиболее ответственных сварных конструкций, сосудов высокого давления, резервуаров большого объема, в том числе работающих при расчетной температуре ниже -40° С.
Строительные нормы (СНиП II-2-B) в качестве материала с наиболее высокой прочностью предусматривали стали класса прочности С85/75; однако в СНиП II-В.3-81 отсутствуют рекомендации по применению конкретных марок стали этого класса для несущих конструкций. Одной из наиболее характерных сталей этого класса является термически улучшенная сталь марки 12ХГН2МФБАЮ. Ее химический состав приведен выше. При разработке стали 12ХГН2МФБАЮ за основу приняли химический состав стали 12ГН2МФАЮ. Для получения в прокате предела текучести более 750 Н/мм2 в сочетании с достаточно высокой хладостойкостью в стали увеличили содержание хрома и молибдена и дополнительно ввели ниобий.
Способность стали 12ХГН2МФБАЮ гасить быстрораспространяющуюся трещину изучали с помощью испытаний по методике Робертсона при инициировании страгивания трещины статической нагрузкой. Установлено, что по полученным при этих испытаниях показателям рассматриваемая сталь превосходит даже сталь 12ГН2МФАЮ. Исследуемая сталь практически не склонна к обратимой отпускной хрупкости, имеет высокое сопротивление коррозии под напряжением и достаточно высокий уровень вязкости разрушения.
Сталь 12ХГН2МФБАЮ мало чувствительна к деформационному старению, обладает удовлетворительной свариваемостью; ее углеродный эквивалент составляет 0,6 %. Полученная максимальная твердость ЯК380-400 при сварке с малой погонной энергией не слишком высока. При сварке сталь 12ХН2МФБАЮ даже на режимах с максимальным тепловложением не склонна к разупрочнению в околошовной зоне. Плоские образцы, вырезанные из сварного соединения поперек стыковых швов, при испытаниях на растяжение разрушаются по основному металлу вдали от зоны сварки.
Приведенные данные показывают, что сталь 12ХГН2МФБАЮ особенно рекомендована для использования в несущих конструкциях, работающих, в том числе, и при расчетных температурах ниже —40° С.
К недостаткам обсуждаемых сталей в первую очередь следует отнести упомянутое выше положение о том, что высокое сопротивление хрупким разрушениям эти стали обеспечивали лишь в том случае, если при высокотемпературном отпуске в ферритной матрице с достаточной полнотой протекали процессы полигонизации и первые стадии рекристаллизации (рекристаллизация на месте), однако эти температуры не должны превышать точку ACl. Эта рациональная температурная область режимов отпуска для стали с σт ≥ 600 Н/мм2 оказалась слишком узкой для практических целей (она составляет 20…30° С), вследствие чего при серийном изготовлении проката не всегда обеспечивается необходимая структура, а следовательно, свойства проката. Рассматриваемые стали оказались не вполне технологичными, на что указывали данные статистического анализа механических свойств изученных партий. Кроме того, введение в стандартную сталь 12ГН2МФАЮ азота как легирующего элемента снижает вязкость материала, особенно в околошовной зоне, о чем подробно изложено в предыдущем параграфе.
Эти недостатки были устранены при создании на АО «Ижорские заводы» стали 13ХГСН1МД. Эта сталь, в принципе близкая по составу к остальным, особенно к сталям 14ХГСНМФР, 12ГН2МФАЮ, Т-1, тип В. Характерными особенностями ее являются: 1 — пониженное содержание марганца, что обеспечивает расширение области рациональных температур отпуска, достаточное для практических целей; 2 — отсутствие азота как легирующего элемента; 3 — отсутствие бора.
Оба последних обстоятельства способствуют также улучшению технологичности стали настадях изготовления проката и сварных конструкций.
При производстве этой стали на АО «Ижорские заводы» осуществляют весь комплекс ковшовой металлургии: металл подвергают очистке от вредных примесей, предусматривают мероприятия по модифицированию и глобулированию неметаллических включений присадками Ti, Zr, SiCa и т. in., перемешиванию металла инертными газами, подогреву металла при обработке его в агрегате печь—ковш и т. п. Прокатку листов заканчивают при температурах не выше 930° С, между прокаткой и закалкой проводят нормализацию. При прохождении металла в потоке производства качество каждого листа на всех стадиях передела оценивают индивидуально. В случае необходимости проводят специальную антифлокенную обработку, подбирают индивидуальные режимы термического улучшения и т.п. Все эти мероприятия позволяют не только выполнить высокие требования, предъявляемые к прокату, описанные выше, но в ряде случаев превзойти их.
Распад аустенита стали типа 16Г2АФ с молибденом и никелем происходит по механизму промежуточного превращения. Такая сталь характеризуется бейнитной структурой. Более высокие температуры отпуска и его продолжительность приводят к значительному выделению карбидов и повышению прочностных характеристик. При температурах отпуска 600° С и выдержках в течение 12 и 72 часов предел текучести составлял 750 и 670 Н/мм2 соответственно, а при температурах 630 и 660° С и выдержках в два часа — 600 и 500 Н/мм2.
После нормализации листов ударная вязкость поперечных образцов с острым надрезом (АСУ) при температурах -40 и -70° С равнялась 50 и 30 Дж/см2 соответственно. С увеличением температуры и продолжительности выдержки при отпуске нормализованной стали ударная вязкость практически не изменялась.
www.uniexo.ru
: Металлургия: образование, работа, бизнес :: MarkMet.ru
СВОЙСТВА И ПРИМЕНЕНИЕ МОЛИБДЕНА
Молибден (Мо) — металл серебристо-серого цвета. По виду и химическим свойствам молибден похож на вольфрам. Элемент открыт в 1778 г. Название его происходит от минерала молибденита, содержащего элемент.
Физические и механические свойства молибдена приведены ниже:
Атомная масса | 95,95 |
Плотность при 20°С, г/см3 | 10,2 |
Температура, °С: |
|
плавления | 2625 |
кипения | 4880 |
Коэффициент теплопроводности при 20 °С, кал/(см·сек·град) | 0,35 |
Удельное электросопротивление, Ом*мм2/м | 0,0517 |
Временное сопротивление при растяжении, кГ/мм2 | 70 |
Твердость НВ | 125 |
На воздухе при комнатной температуре молибден мало окисляется, с водородом он не реагирует вплоть до температуры плавления. При нагревании >400°С молибден легко окисляется на воздухе, поэтому нагревать его перед горячей обработкой давлением следует в восстановительной атмосфере или в защитных средах.
С соляной и серной кислотами молибден заметно реагирует только при 80—100°С. Азотная кислота и царская водка растворяют его и на холоду, однако быстро только при 100°С.В холодных растворах щелочей молибден устойчив, а в горячих медленно разрушается.
Молибден термической обработкой не упрочняется. Его упрочнение достигается лишь полугорячим наклепом, поэтому необходимое сочетание механических свойств молибденовых полуфабрикатов достигается деформацией и отжигом.
Примеси углерода, кислорода, азота, кремния, железа, алюминия, кальция, фосфора, серы и другие, присутствующие в техническом молибдене от сотых до стотысячных долей процента, оказывают заметное влияние на его свойства. Особенно вредной примесью является кислород, легкоплавкие окислы которого, располагаясь по границам зерен молибдена в виде тонкой пленки, вызывают резкое охрупчивание металла. При содержании кислорода >0,004% снижается способность молибдена к пластической деформации, особенно в присутствии углерода и азота. При содержании кислорода в пределах 0,008— 0,015% молибден становится хрупким и не поддается обработке давлением.
В технике молибден используют как тугоплавкий металл, сохраняющий прочность при нагреве вплоть до 2000°С. Примерно 75% всего получаемого молибдена расходуют на легирование сталей и производство никелевых сплавов. Добавки молибдена в сталь увеличивают ее прокаливаемость и закаливаемость, уничтожают отпускную хрупкость, увеличивают теплоустойчивость.
В виде проволоки и прутков молибден используют в электроламповой и радиотехнической промышленности. Из него изготовляют листовые аноды, сетки, пружины катодов.
Коэффициент теплового расширения молибдена почти одинаков с коэффициентом расширения стекла, поэтому его применяют для электрических контактов, впаиваемых в стекло. Из окисла молибдена делают электроды стекольных ванн при варке оптического стекла.
Из молибдена изготовляют нагревательные элементы печей сопротивления, работающих в вакууме или в нейтральной среде, пуансонов, матриц, штампов для горячей штамповки, оснастку для литья под давлением, сильно нагруженные детали газовых турбин и нагреваемые до высоких температур части ракет.
Молибденовые сплавы применяют в качестве жаропрочных конструкционных материалов. Подавляющее большинство легирующих элементов охрупчивает молибден. Единственным элементом, повышающим пластичность молибдена, является рений. Молибденовый сплав с 40—50% Re может деформироваться при комнатной температуре. Однако из-за малой распространенности рения сплавы его с молибденом применяют редко.
Из молибденовых сплавов, находящих практическое применение, лучшими являются однофазные, содержащие в качестве легирующих добавок цирконий и титан. Эти сплавы при высокой жаропрочности сохраняют деформируемость. Гетерофазные термообрабатываемые сложнолегированные сплавы молибдена, легированные титаном, цирконием, ниобием, углеродом и другими элементами, обладают более высокой жаропрочностью, но они менее пластичны, а их изготовление связано с большими трудностями. Заметно повышается жаропрочность молибдена при добавке в него >20% W, но при этом повышается плотность сплава и ухудшается его деформируемость.
Молибденовые сплавы применяют для вставок критических сечений сопел, обшивки летательных аппаратов, деталей ракет и атомных реакторов, вставок матриц для литья стали под давлением, оснастки и инструмента в металлообрабатывающей промышленности, деталей оборудования нефтяной и стекольной промышленности, деталей радио, электротехнической и электронной техники.
Окислы молибдена летучи (испаряются при температурах >600°С) и легкоплавки, поэтому молибден и молибденовые сплавы нежаростойки. Для длительной работы при температуре >700°С в окислительной атмосфере молибденовые сплавы без защитных покрытий не применяют. Они могут работать только в восстановительной и нейтральной среде и в вакууме.
Для защиты деталей из молибдена и молибденовых сплавов, работающих при высоких температурах в окислительной атмосфере, применяют термодиффузионные покрытия, которые образуют насыщением поверхностных слоев детали различными элементами путем диффузии, эмалевые или стеклохромовые покрытия, электролитические покрытия, наносимые электролизом из расплавленных солей металлов, керамические покрытия, покрытия из окислов металлов.
markmet.ru
Способ химико-термической обработки молибдена и сплавов на его основе
ОЛИCАНИЕ
ИЗОБРЕТЕНИЯ (ii) 443ИВ
Союз Советских
Социалистических
Республик
К АВТОРСКОМУ СВИДЕТЕЛЬСТВУ (61) Зависимое от aar. свидетельства (22) Заявлено 06.05.72 (21) 1781449/22-1 с присоединением заявки № (32) Приоритет
Опубликовано 15.09.74. Бюллетень ¹ 34
Дата опубликования описания 14.05.75 (51) М. Кл. С 23с 9,. 04
Государственный комитет
Совета Министров СССР по делам изобретений и открытий (53) УДК 621.793.6 (088.8 (72) Авторы изобретения
Б. И. Красилов, А. В. Бялобжеский и М. С. Цирлин (71) Заявитель
Ордена Трудового Красного Знамени институт физической химии
АН СССР (54) СПОСОБ ХИМИКО-ТЕРМИЧЕСКОЙ ОБРАБОТКИ
МОЛИБДЕНА И СПЛАВОВ НА ЕГО ОСНОВЕ
Изобретение относится к области химикотермической обработки молибдена и его сплавов.
Известен способ защиты молибдена от окисления путем последовательного борированпя и борсилицирования в порошковых смесях.
Получаемое покрытие имеет жаростойкость при 1300 С вЂ” 3000 ч, при 1500 — 1000 ч, что в ряде областей техники является недостаточным. В начальный период эксплуатации изделия на границе борсилицидного и борпрованного слоев образуется барьерный слой, состоящий из тройной интерметаллической фазы. Это уменьшает эффективную толщину жаростойкого слоя.
По предлагаемому способу жаростойкий слой на основе силицидов молибдена наносят в две стадии с промежуточным отжигом прп
1500 †17 С.
При этом барьерный слой образуется в процессе формирования покрытий, что значительно повышает термическую фазовую стабильность покрытия, т. е. замедляет растворение защитного жаростойкого слоя.
Высокая термическая стабильность композиции обуславливает повышение как жаростойкости, так и термостойкости.
Покрытие наносят путем диффузионного насыщения молибдена и его сплавов в следующие стадии: борирование †борсилицирование — отжиг — нанесение жаростойкого покрытия путем борсилицирования, силпцирования или силпцированпя с добавкой марганца в зависимости от назначения покрытия.
5 Жаростойкий слой на силицидной основе
IIBHocsIT одним из следующих способов: в инертной атмосфере при 1100 — 1200 С в порошковой смеси, содержащей кремний, 5—
50% В4С и 1 — 3% КР; при 900 — 1100 С в по10 рошке кремния с 1 — 10% Мп и 1 — 3% KF; при 1100 — 1350 C в порошке кремния в вакууме 10 — 4 — 10 — мм рт. ст. или инертной атмосфере с активаторами.
Промежуточный отжиг осуществляют в ар15 гоне или вакууме при 1500 — 1700 С.
В результате использования предлагаемого способа обработки молибдена и его сплавов на их поверхности образуется четырехслойное покрытие, состоящее из подслоя борида мо20 либдена Мо2В, барьерного слоя Мо (SiB) 3, переходного слоя Моз$1з и защитного жаростоикого слоя Мо$1з+МоВ пли Мо312 и т. д.
Жаростойкость покрытия составляет не менее 300 ч при 1650, 2000 ч при 1500 С и
25 5000 ч при 1300 С. Термостойкость покрытия составляет не менее 800 — 1000 циклов при охлаждении на воздухе от 1300 С.
Пример. Образцы Мо и сплава ЦМ-2А помещают в порошковую шпхту, содержа30 щую карбид бора и 1 — 3% фтористого калия.
443118
Предмет изобретения
Составитель В. Хацернова
Техред О. Гуменюк
Редактор Н, Аносова
Корректор В. Брыкснна
Заказ 1120/7 Изд. Ко 1232 Тираж 875 Подписное
ЦНИИПИ Государственного комитета Совета Министров СССР по делам изобретений и открытий
Москва, Ж-35, Раушская наб., д. 4/5
Типография, пр. Сапунова, 2
Контейнер пз окиси алюминия с шихтой и образцами помещают в печь электросопротивления, заполненную аргоном и нагревают до
1100 С. Процесс ведут при этой температуре в течение 2 ч.
Затем образцы помещают в порошковую шихту, состоящую из кремния, карбида бора (8 /о ) и фторида калия (2 /о ) . Процесс ведут в тех же условиях при 1150 в течение
5 ч.
Далее образцы отжигают при 1650 С 5—
10 ч в вакууме 5 — 10- мм рт. ст. либо в аргоне. Отожженные образцы повторно борсилицируют в такой же смеси и при этом же режиме.
Полученное предлагаемым способом покрытие характеризуется низкой скоростью растворения защитного борсилицидного слоя и высокой жаростойкостью.
Способ химико-термической обработки молибдена и сплавов на его основе путем борирования и последующего нанесения слоя на основе силицидов молибдена, о тл и ч а ющи йс я тем, что, с целью повышения термической стабильности покрытия, жаростойкости и его термостойкости, нанесение слоя на основе силицидов молибдена проводят в две стадии с промежуточным отжимом при
1500 †17 С.
www.findpatent.ru
Молибденовая сталь — Знаешь как
Сталь, легированная молибденом. Используется с начала 20 в. Различают М. с. конструкционную (улучшаемую, цементуемую), инструментальную и с особыми физ. и хим. св-вами (жаропрочную, нержавеющую, магнитную). Молибден частично растворяется в феррите, а также образует карбиды типа (Мо, М)С, (Мо, М)2С, (Мо, М)23С6 и (Мо, М)6С, где М — атомы железа или легирующих элементов, замещающие часть атомов молибдена. Карбид (Мо,М)23С6 образуется преим. в сталях, легированных, кроме молибдена, хромом. Молибден значительно увеличивает прокаливаемость, измельчает природное зерно металла, благоприятно влияет на мн. эксплуатационные характеристики стали. В конструкционных улучшаемых сталях (0,3—0,5% С) он способствует улучшению на большую глубину, повышению стойкости против отпуска, уменьшению склонности к отпускной хрупкости второго рода.
Достаточно небольшого (0,2—0,3%) количества молибдена, чтобы избежать отпускной хрупкости при медленном охлаждении после отпуска марганцевой, хромистой и хро-моникелевой сталей. Молибденовые улучшаемые стали характеризуются также более высокой вязкостью при низкой т-ре. Наиболее широко применяют улучшаемые стали марок ЗОХМА, 40ХНМА и 38ХМЮА. Молибденовая сталь марки 38ХМЮА упрочняют азотированием. Из конструкционных улучшаемых молибденовая сталь изготовляют высоконагруженные болты, шпильки, валы, оси, шестерни и др. изделия.
В конструкционных низкоуглеродистых цементуемых сталях молибден, подобно хрому, значительно повышает содержание углерода в поверхностной зоне. Однако макс, концентрация углерода в них несколько ниже, чем в хромистой стали и достигает 1,9% при содержании молибдена около 3%. Молибденовая цементуемая сталь менее склонна к образованию карбидов по границам зерен, чем хромистая. Чаще всего молибден добавляют в цементуемые стали вместе с хромом и никелем (сталь марки 18Х2Н4МА). Легирование хромоникелевых сталей молибденом повышает стойкость переохлажденного аустенита, а следовательно, и прокаливаемость (критический диаметр достигает 100 мм и более), вследствие чего их закаливают на воздухе для уменьшения коробления.
Из конструкционной цементуемой стали марки 18Х2Н4МА изготовляют высоконагруженпые изделия (напр., зубчатые колеса, коленчатые валы, оси). В инструментальных сталях молибден улучшает красностойкость, прокаливаемость, износостойкость, повышает стойкость их против отпуска, жаропрочность, устраняет отпускную хрупкость. Молибденовые низколегированные стали (марок 5ХНМ, 5ХГМ) применяют для изготовления горячих штампов, закалку к-рых даже при относительно больших размерах осуществляют в масле или в струе сжатого воздуха. Из стали марки Х12М изготовляют холодные штампы, накатные ролики, валки, глазки для калибрования и др.
Молибден (от 0,6 до 1,0, а иногда до 2%) добавляют в быстрорежущую сталь для значительного повышения производительности резания, им заменяют часть вольфрама. По сравнению с вольфрамовыми у молиоденовольфрамовых быстрорежущих сталей худшие технологические (большая склонность к росту зерна, к обезуглероживанию), но лучшие мех. св-ва. Из молибденовых быстрорежущих сталей изготовляют режущий инструмент. Повышенная жаропрочность молибденовых жаропрочных сталей обусловлена тем, что молибден повышает т-ру рекристаллизации феррита и способствует образованию тонкодисперсных спец. карбидов (напр., Мо2С) при рабочей т-ре 450—600° С.
Трубы паронагревателей, паропроводов и коллекторов энергетических установок, арматуру паровых котлов и турбин, эксплуатируемых при т-ре 500—580° С и подверженных ползучести, но малонагруженных, изготовляют из низкоуглеродистых молибденовых, хромомолибденовых и хромомолибденованадиевых сталей марок 15М, 12ХМ, 12МФ и 25Х1МФ. Детали и узлы, эксплуатируемые при больших напряжениях и т-ре, изготовляют из сложнолегирован-ных сталей мартенситного класса марки 15Х11МФ. Для получения оптимальной жаропрочности молибденовые жаропрочные стали подвергают нормализации или закалке с последующим старением ние металлов). Эти стали применяют для изготовления изделий, эксплуатируемых в нагруженном состоянии до температуры 800° С.
Нержавеющие стали марок Х17Н13М2Т и Х18Н12МЗТ стойки против коррозии в органических и серной к-тах, в морской воде, а особенно против воздействия хлоридов, что сказывается прежде всего в уменьшении точечной коррозии. Из низко углеродистых (менее 0,06% С) аустенитных сталей марок 0Х23Н28М2Т и 0Х23Н28МЗДЗТ изготовляют сварные конструкции и узлы, стойкие против действия горячих фосфорной и серной к-т. Недостаток этих сталей — большая чувствительность к межкристаллит-ной коррозии, зависящая от содержания углерода. В магнитных сталях (марки ЕХ9К15М) молибден увеличивает коэрцитивную силу.
Лит.: Металловедение и термическая обработка стали и чугуна. Справочник.
Вы читаете, статья на тему молибденовая сталь
znaesh-kak.com