Титановая сталь – Характеристики сплавов на основе титана, свойства металла и области применения
alexxlab | 06.06.2020 | 0 | Вопросы и ответы
Титан или сталь?
Очень популярный вопрос, который мучает многих: «Какие клапана купить: стальные или титановые». В этой статье мы постараемся помочь вам определиться с выбором.
В чем же отличия титановых и стальных клапанов, и почему нет победителя в общем зачете?
Масса клапана.
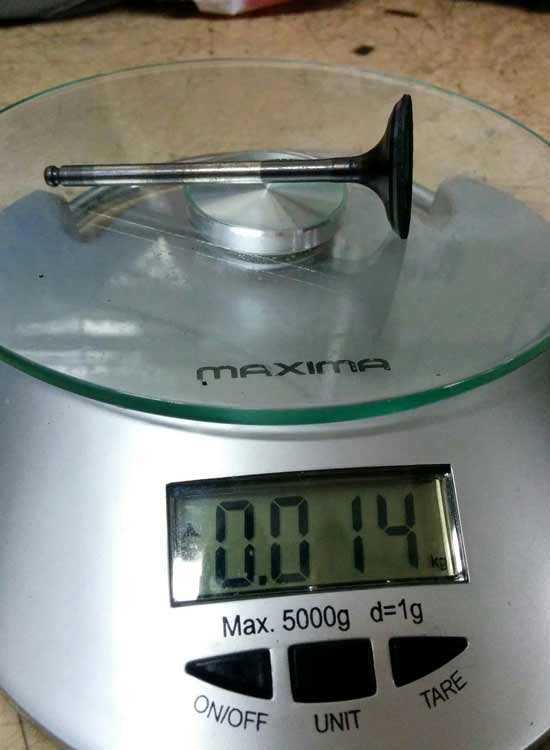
Первое отличие, которое бросается в глаза – это масса клапана. Титановый клапан при одинаковых размерах значительно легче свое стального брата. Пружина быстрее закроет клапан, масса которого меньше, по этому, чем меньше вес клапана, тем выше можно поднять планку максимальных оборотов с меньшим риском догнать клапан поршнем. При этом снижается нагрузка на ГРМ в целом, это дает некоторую прибавку к мощности за счет небольшого увеличения КПД. Например: практически на всех современных кроссовых мотоциклах и мотоциклах для кольцевых гонок используется титановые клапана.
Стальные клапана при том же размере имеют больший вес, поэтому с ними используются более жесткие пружины. При недостаточной жесткости пружин растет вероятность удара клапанов поршнем при работе двигателя на высоких оборотах. Жесткость пружин и больший вес клапанов создают повышенную нагрузку на ГРМ. Даже на маленьких двигателях кроссовых мотоциклов с объемом 125куб.см. со стальными клапанами используются достаточно жесткие, и даже двойные пружины.
Износостойкость.
Титановые сплавы сильно уступают стали, когда речь идет об износостойкости. Плохие антифрикционные свойства титана обусловлены налипанием титана на многие материалы и его взаимодействием с азотом и водородом при высоких температурах, из-за которых верхний слой становится хрупким и выкрашивается в процессе эксплуатации.

Для улучшения антифрикционных свойств, повышения износостойкости и защиты от внешней среды титановые клапана покрывают защитными покрытиями различных типов. Толщина таких покрытий, в зависимости от типа, варьируется от нескольких тысячных до сотых миллиметра. Это делает невозможным притирку клапана к седлу с целью герметизации камеры сгорания, т.к. во время притирки неизбежно будет повреждено защитное покрытие, и клапан быстро «провалится» в седло. Поэтому при установке титановых клапанов предъявляются повышенные требования к форме, чистоте фасок на седлах и их соосности относительно направляющей втулки.
Износостойкость и антифрикционные свойства стали на порядок выше, чем у титана, но значительно ниже, чем у защитных покрытий, которыми покрыт титановый клапан. При этом износостойкость фаски стального клапана сохраняется по всей толщине тарелки, а фаска титанового клапана сохраняет свои свойства и параметры ровно до тех пор, пока держится защитное покрытие.
Теплопроводность, коэффициент расширения и тепловой зазор
Теплопроводность и стойкость к высоким температурам у титановых сплавов ниже, чем у жаропрочных сталей. Охлаждение тарелки клапана играет еще более важную роль при использовании титановых клапанов. Именно по этому с титановыми клапанами рекомендуется использовать бронзовые седла клапанов, которые лучше отводят тепло от горячей тарелки клапана.
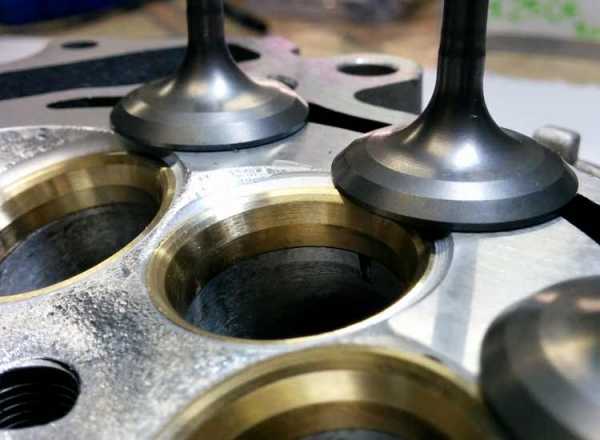
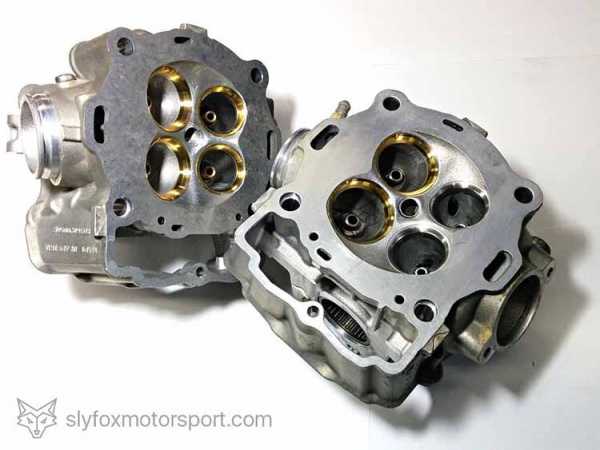
Коэффициент расширения титана намного меньше чем у стали. При использовании титановых клапанов допускается меньший тепловой зазор между направляющей втулкой и клапаном, чем при использовании стальных клапанов. Это положительно сказывается на точности посадки клапана в седло, что увеличивает ресурс пары седло-клапан.
Стоимость клапана и ремонта
В среднем титановые клапана дороже стальных. Во первых, потому что титан гораздо дороже в производстве чем сталь. Во вторых при производстве титановых клапанов необходимы дополнительные этапы производства (нанесение покрытий). И наконец- маркетинг.
Хотя порой можно встретить стальные клапана стоимость которых соизмерима с титановыми. Чаще такая картина наблюдается с оригинальными запчастями, где основной процент от стоимости занимает маркетинг.
В случае повреждения фаски, восстановление стального клапана обойдется в 3-4 раза дешевле, чем титанового.
Ресурс
Очень много слухов про капризность и не большой ресурс титановых клапанов. Также часто можно услышать про то, что титановые клапана часто “обрывает”. На самом деле обрывает и стальные и титановые клапана одинаково часто, но одинаково предсказуемо на кривых седлах. Об этом явлении более подробно мы рассказывали в статье “Срок службы клапанов”.
“Обрыв” титанового клапана Yamaha Phazer 500 и “обрыв” стального клапана KTM EXC 450
Из-за тонкого защитного покрытия титановые клапана действительно более капризны, чем стальные, особенно при небрежном отношении и неквалифицированном обслуживании. Но, по опыту, и стальные и титановые клапана при должном внимании и обслуживании служат одинаково долго.
За время работы нам приходилось видеть «убитые» клапана при небольших пробегах, как на стальных, так и на титановых комплектах.
Итоги и рекомендации.
В большинстве случаев мы рекомендуем своим клиентам использовать оригинальные клапана и пружины, особенно если техника используется по прямому назначению.
Стальные клапана имеет смысл менять на титановые в случаях если:
– двигатель регулярно эксплуатируется на повышенных оборотах
-планируется модернизация двигателя с целью увеличения мощности
-производится регулярное качественное обслуживание техники
-происходит смена назначения техники (из эндуро в кросс, например)
Титановые клапана имеет смысл менять на стальные если:
-двигатель не эксплуатируется на повышенных оборотах
-сложности с обслуживанием (проведение самостоятельного обслуживания и ремонта)
-нет возможности обрабатывать седла (есть возможность притереть клапана)
-титановый аналог слишком дорогой
Всегда используйте только те пружины, которые предназначены для данного типа клапанов!
При использовании новых клапанов настоятельно рекомендуем обрабатывать седла (формировать фаски) на хорошем оборудовании. Это особенно важно при использовании титановых клапанов. Притирка титановых клапанов не допускается.
Надеемся, что данные рекомендации помогут вам определится с выбором клапанов. Вы всегда можете оставить заявку на обратный звонок или позвонить мастеру и проконсультироваться.
slyfoxmotorsport.com
Сварка сталей с титаном и титановыми сплавами
Темы: Сварка стали, Сварка титана, Технология сварки.
Титан с железом образуют систему ограниченной растворимости и эвтектоидным распадом β-фазы. Предел растворимости титана в железе снижается от 12 % при 1200 ОС до 4 % при 300°с. Растворимость железа в α-титане составляет 0,5 и 0,05 … 0, 1 % соответственно при 615 и 20°С.
Другие страницы, относящиеся к теме
Сварка стали, титана, титановых сплавов
:
Титан и железо дают химические соединения TiFe, TiFe2, Ti2Fe и эвтектики β-фаза + TiFe (1100оС), TiFe + TiFe2 (1280оС), TiFe2 + а-фаза (1298оС), содержащие 32; 62,5 и 82,5 % железа соответственно. Поэтому при затвердевании расплава уже при содержании железа порядка 0,1 % будут образовываться интерметаллиды TiFe и TiFe2, которые резко снижают пластические свойства материала.
Титан и железо существенно различаются по кристаллическому строению и физическим свойствам.
Аналогичную картину металлургического взаимодействия титан имеет с легирующими компонентами в сталях (никель и др.).
Положительные результаты могут быть получены при использовании методов сварки давлением, а также барьерных слоев и вставок из третьего металла, не образующего при высоких температурах со свариваемыми материалами хрупких фаз. Особенностью титана и титановых сплавов является их высокая активность с атмосферным газом, что требует ведения процесса в условиях, обеспечивающих их защиту (инертные газы, вакуум, жидкие среды).
Сварка взрывом осуществляется с промежуточными прокладками и без прокладок. В последнем случае могут появиться интерметаллиды ТiFe и TiFe2 в местах вкрапления литого металла и перемешивания. При отжиге таких соединений идет дальнейший рост интерметаллидной фазы, выделяются карбиды титана. В зоне контакта может наблюдаться появление пор. В качестве прокладок используют ниобий, ванадий, никель, медь, серебро, железо и сплавы из тугоплавких металлов.
Получила применение двойная прокладка из ванадия или ниобия со стороны титана и медная со стороны стали. Нагрев соединений, полученных с использованием барьерных подслоев, до 800оС не ведет к охрупчиванию шва. Некоторое снижение предела прочности при этом связано со снятием эффекта наклепа. Уменьщение толшины медной прослойки до 0,1мм повышает предел прочности соединенная, что объясняется проявлением эффекта контактного упрочнения. Разрушение соединений при испытаниях идет по слою меди и имеет вязкий характер при положительных и отрицательных температурах (+300…-269 оС).
При диффузионной сварке удовлетворительные механические характеристики получаются, когда ширина слоя интерметаллидов ≤3 … 5 мкм, а в ЗТВ имеет место α-твердый раствор железа в титане. При испытаниях зона разрушения наблюдается в переходе титан железо (сталь). На прочность соединения влияет ширина зоны, обогашенная углеродом.
Механические характеристики стыковых соединений, выполненных диффузионной сваркой в вакууме на материалах ВТ1-0 + 12Х18Н9Т и ОТ4 + 12Х18Н9Т (температура 750 …850 оС, время сварки 15 мин), оказываются ниже прочности основного материала. Применение прокладок из ванадия и меди при сварке ВТ6, ВТ5-1 со сталью 12Х18Н9Т позволило получить предел прочности вплоть до 530… 570 МПа. В соединении не обнаруживается интерметаллидных фаз даже после длительного нагрева при высокой температуре (1000
Для получения стабильных результатов целесообразно в качестве прокладочного материала использовать тонкую многослойную ленту (V + Cu + Ni), полученную горячей прокаткой в вакууме. Благодаря такой ленте предел прочности соединений ВТ5-1 и АТ3 со сталью 12Х18Н10Т при растяжении составляет 500… 590 МПа.
При сварке титана с низкоуглеродистыми сталями хорошие результаты дают прослойки из серебра.
Положительные результаты получаются при диффузионной сварке в расплаве солей (70 % BaCI2 + 30 % NaCI). При этом обеспечиваются быстрый к равномерный нагрев, хорошая защита металла в процессе сварки и охлаждения.
Сварка прокаткой осуществляется в вакууме. Выявлено отрицательное влияние углерода на механические характеристики соединения из-за образования карбида титана (TiC). Увеличение содержания углерода в стали с 0,02 до 0,45 % ведет к снижению уровня прочности с 260 до 140 МПа. При использовании про кладок из ванадия содержание углерода в нем должно быть <0,02 %. В случае применения прокладок металлографическими и микрорентгеноспектральными методами обнаружить образование в биметалле на границе сваренных заготовок хрупких фаз не удалось.
При сварке ВТ6 со сталью 12Х18Н10Т с комбинированной прокладкой из Nb + Cu (вакуум 0,00266 Па, температура 350oС, степень обжатия 45 … 50 %) получаются равнопрочные соединения (разрушение образцов при испытаниях – по меди). На границе ниобия с титаном образуются зоны твердых растворов, имеющие повышенную твердость.
На границе ниобия и меди имеет место диффузионная зона протяженностью порядка 40 мкм. В переходе ниобий – титан зона диффузии не наблюдается. Толщины прокладок ниобия берутся порядка 0,05 … 0,2 мм, меди 0,1 … 0,46 мм.
Контактная и ультразвуковая сварка листовых заготовок проводится с применением промежуточных прокладок.
При контактной сварке не допускается подплавления поверхности титана и стали. Наилучшие результаты контактная сварка дает через прослойку ниобия, а ультразвуковая через слой серебра.
Получены положительные результаты по клинопрессовой сварке в аргоне титановых сплавов со сталью 12Х18Н9Т через прокладку алюминия или медь. Нагрев при использовании алюминия 350oС, меди – 850oС. Толщина прослойки 0,1 … 0,2 мм.
Из способов сварки плавлением наибольшее распространение получили электронно-лучевая и аргонодуговая сварка титана со сталью с применением вставок из ванадия и его сплавов. Для получения более высокой прочности целесообразно при менять ванадий, легированный вольфрамом и хромом (5 … 10 %).
Предложен способ сварки титана со сталью в гелии с использованием интенсивно охлаждаемой прокладки. Возможна дуговая сварка в аргоне с применением в качестве присадочного материала медно-серебряного сплава (28 и 72 % соответственно), расплавляемой прокладки из монель-металла.
При сварке плавлением через ванадиевую вставку необходимо учитывать особенности сварки ванадия с титаном и сталью.
- < Химический состав углеродистых сталей
- Аустенитные стали >
weldzone.info
Титановые сплавы: обработка, свойства, применение, марки
Одним из самых распространенных элементов, который находится в земле, можно назвать титан. Согласно результатам проведенных исследований, он занимает 4-е место по степени распространенности, уступая лидирующие позиции алюминию, железу и магнию. Несмотря на столь большое распространение, титан стал использоваться в промышленности лишь в 20 веке. Титановые сплавы во многом повлияли на развитие ракетостроения и авиации, что связано с сочетанием малой плотности с высокой удельной прочностью, а также коррозионной стойкостью. Рассмотрим все особенности данного материала подробнее.
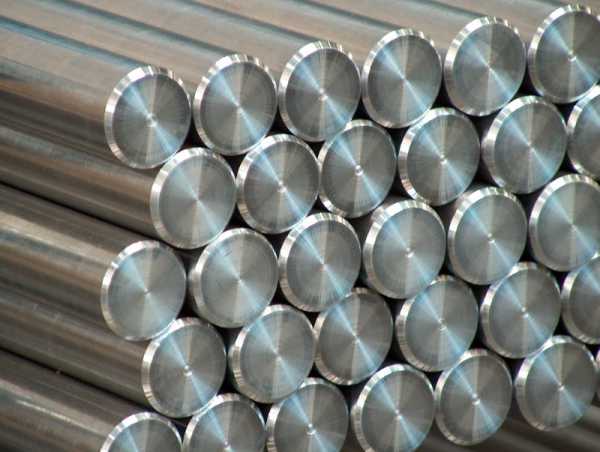
Общая характеристика титана и его сплавов
Именно основные механические свойства титановых сплавов определяют их большое распространение. Если не уделять внимание химическому составу, то все титановые сплавы можно охарактеризовать следующим образом:
- Высокая коррозионная стойкость. Недостатком большинства металлов можно назвать то, что при воздействии высокой влажности на поверхности образуется коррозия, которая не только ухудшает внешний вид материала, но и снижает его основные эксплуатационные качества. Титан менее восприимчив к воздействию влажности, чем железо.
- Хладостойкость. Слишком низкая температура становится причиной того, что механические свойства титановых сплавов существенно снижаются. Часто можно встретить ситуацию, когда эксплуатация при отрицательных температурах становится причиной существенного повышения хрупкости. Титан довольно часто применяется при изготовлении космических кораблей.
- Титан и титановые сплавы имеют относительно низкую плотность, что существенно снижает вес. Легкие металлы получили широкое применение в самых различных отраслях промышленности, к примеру, в авиастроении, строительстве небоскребов и так далее.
- Высокая удельная прочность и низкая плотность – характеристики, которые довольно редко сочетаются. Однако именно за счет подобного сочетания титановые сплавы сегодня получили самое широкое распространение.
- Технологичность при обработке давлением определяет то, что сплав применяется часто в качестве заготовки при прессовании или другом виде обработки.
- Отсутствие реакции на воздействие магнитного поля также назовем причиной, по которой рассматриваемые сплавы получили широкое применение. Часто можно встретить ситуацию, когда проводится производство конструкций, при работе которых образуется магнитное поле. Применение титана позволяет исключить вероятность возникновения связи.
Эти основные преимущества титановых сплавов определили их достаточно большое распространение. Однако, как ранее было отмечено, многое зависит от конкретного химического состава. Примером можно назвать то, что твердость изменяется в зависимости от того, какие именно вещества применяются при легировании.
Важно, что температура плавления может достигать 1700 градусов Цельсия. За счет этого существенно повышается устойчивость состава к нагреву, но также усложняется процесс обработки.
Виды титановых сплавов
Классификация титановых сплавов ведется по достаточно большому количеству признаков. Все сплавы можно разделить на несколько основных групп:
- Высокопрочные и конструкционные – прочные титановые сплавы, которые обладают также достаточно высокой пластичностью. За счет этого они могут применяться при изготовлении деталей, на которые оказывается переменная нагрузка.
- Жаропрочные с низкой плотностью применяются как более дешевая альтернатива жаропрочным никелевым сплавам с учетом определенного температурного интервала. Прочность подобного титанового сплава может варьироваться в достаточно большом диапазоне, что зависит от конкретного химического состава.
- Титановые сплавы на основе химического соединения представляют жаропрочную структуру с низкой плотностью. За счет существенного снижения плотности вес также снижается, а жаропрочность позволяет использовать материал при изготовлении летательных аппаратов. Кроме этого с подобной маркой связывают также высокую пластичность.
Маркировка титановых сплавов проводится по определенным правилам, которые позволяют определить концентрацию всех элементов. Рассмотрим некоторые из наиболее распространенных разновидностей титановых сплавов подробнее.
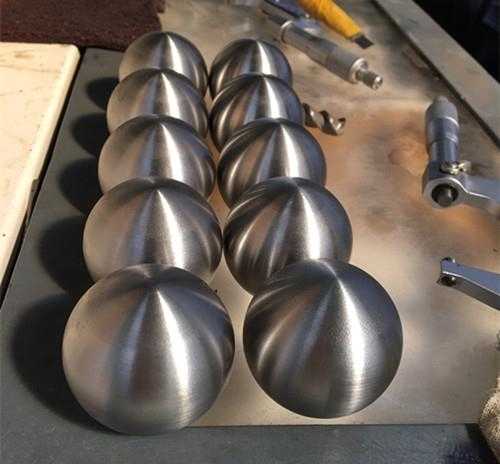
Сферы из титанового сплава
Рассматривая наиболее распространенные марки титановых сплавов, следует обратить внимание ВТ1-00 и ВТ1-0. Они относятся к классу технических титанов. В состав данного титанового сплава входит достаточно большое количество различных примесей, которые определяют снижение прочности. Однако за счет снижения прочности существенно повышается пластичность. Высокая технологическая пластичность определяет то, что технический титан можно получить даже при производстве фольги.
Очень часто рассматриваемый состав сплава подвергается нагартовке. За счет этого повышается прочность, но существенно снижается пластичность. Многие специалисты считают, что рассматриваемый метод обработки нельзя назвать лучшим, так как он не оказывает комплексного благоприятного воздействия на основные свойства материала.
Сплав ВТ5 довольно распространен, характеризуется применением в качестве легирующего элемента исключительно алюминия. Важно отметить, что именно алюминий считается самым распространенным легирующим элементом в титановых сплавах. Это связано с нижеприведенными моментами:
- Применение алюминия позволяет существенно повысить модули упругости.
- Алюминий также позволяет повысить значение жаропрочности.
- Подобный металл один из самых распространенных в своем роде, за счет чего существенно снижается стоимость получаемого материала.
- Снижается показатель водородной хрупкости.
- Плотность алюминия ниже плотности титана, за счет чего введение рассматриваемого легирующего вещества позволяет существенно повысить удельную прочность.
В горячем состоянии ВТ5 хорошо куется, прокатывается и штампуется. Именно поэтому его довольно часто применяют для получения поковки, проката или штамповки. Подобная структура может выдержать воздействие не более 400 градусов Цельсия.
Титановый сплав ВТ22 может иметь самую различную структуру, что зависит от химического состава. К эксплуатационным особенностям материала можно отнести следующие моменты:
- Высокая технологическая пластичность при обработке давлением в горячем состоянии.
- Применяется для изготовления прутков, труб, плиты, штамповок, профиля.
- Для сваривания могут использоваться все наиболее распространенные методы.
- Важным моментом является то, что после завершения процесса сварки рекомендуется проводить отжиг, за счет чего существенно повышаются механические свойства получаемого шва.
Существенно повысить эксплуатационные качества титанового сплава ВТ22 можно путем применения сложной технологии отжига. Она предусматривает нагрев до высокой температуры и выдержки в течение нескольких часов, после чего проводится поэтапное охлаждение в печи также с выдержкой в течение длительного периода. После качественного проведения отжига сплав подойдет для изготовления высоконагруженных деталей и конструкций, которые могут нагреваться до температуры более 350 градусов Цельсия. Примером можно назвать элементы фюзеляжа, крыла, детали системы управления или крепления.
Титановый сплав ВТ6 сегодня получил самое широкое распространение за рубежом. Назначение подобного титанового сплава заключается в изготовлении баллонов, которые могут работать под большим давлением. Кроме этого, согласно результатам проведенных исследований, в 50% случаев в авиакосмической промышленности применяется титановый сплав, который по своим эксплуатационным качествам и составу соответствует ВТ6. Стандарт ГОСТ сегодня практически не применяется за рубежом для обозначения титановых и многих других сплавов, что следует учитывать. Для обозначения применяется своя уникальная маркировка.
ВТ6 обладает исключительными эксплуатационными качествами по причине того, что в состав добавляется также ванадий. Этот легирующий элемент характеризуется тем, что повышает не только прочность, но и пластичность.
Данный сплав хорошо деформируется в горячем состоянии, что также можно назвать положительным качеством. При его применении получают трубы, различные профили, плиты, листы, штамповки и многие другие заготовки. Для сваривания можно применять все современные методы, что также существенно расширяет область применения рассматриваемого титанового сплава. Для повышения эксплуатационных качеств также проводится термическая обработка, к примеру, отжиг или закалка. На протяжении длительного времени отжиг проводился при температуре не выше 800 градусов Цельсия, однако результаты проведенных исследований указывают на то, что есть смысл в повышении показателя до 950 градусов Цельсия. Двойной отжиг зачастую проводится для повышения сопротивления коррозионному воздействию.
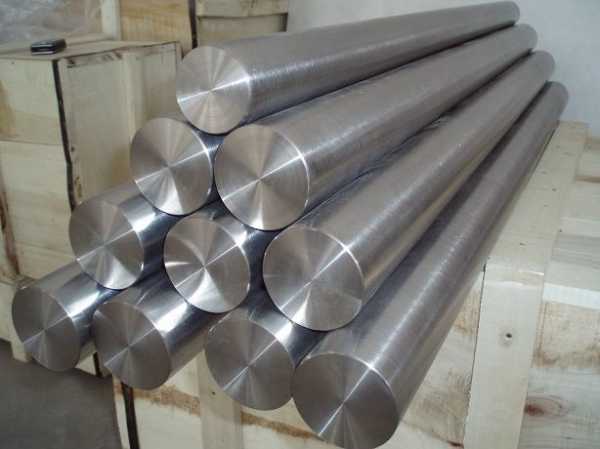
Внешний вид титановых сплавов
Также большое распространение получил сплав ВТ8. В сравнении с предыдущим он обладает более высокими прочностными и жаропрочными качествами. Достигнуть уникальных эксплуатационных качеств смогли за счет добавления в состав большого количества алюминия и кремния. Стоит учитывать, что максимальная температура, при которой может эксплуатироваться данный титановый сплав около 480 градусов Цельсия. Разновидностью этого состава можно назвать ВТ8-1. Его основными эксплуатационными качествами назовем нижеприведенные моменты:
- Высокая термическая стабильность.
- Низкая вероятность образования трещин в структуре за счет обеспечения прочных связей.
- Технологичность при проведении различных процедур обработки, к примеру, холодной штамповки.
- Высокая пластичность вместе с повышенной прочностью.
Для существенно повышения эксплуатационных качеств довольно часто проводится двойной изотермический отжиг. В большинстве случаев данный титановый сплав применяется при производстве поковок, прудков, различных плит, штамповок и других заготовок. Однако стоит учитывать, что особенности состава не позволяют проводить сварочные работы.
Применение титановых сплавов
Рассматривая области применения титановых сплавов отметим, что большая часть разновидностей применяется в авиационной и ракетостроительной сферах, а также в сфере изготовления морских судов. Для изготовления деталей авиадвигателей другие металлы не подходят по причине того, что при нагреве до относительно невысоких температур начинают плавиться, за счет чего происходит деформация конструкции. Также увеличения веса элементов становится причиной потери КПД.
- Нож из титанового сплава
- Применение титановых сплавов в медицине
Применим материал при производстве:
- Трубопроводов, используемых для подачи различных веществ.
- Запорной арматуры.
- Клапанов и других подобных изделий, которые применяются в агрессивных химических средах.
- В авиастроении сплав применяется для получения обшивки, различных креплений, деталей шасси, силовых наборов и других агрегатов. Как показывают результаты проводимых исследований, внедрение подобного материала снижает вес примерно на 10-25%.
- Еще одной сферой применения является ракетостроение. Кратковременная работа двигателя, движение на большой скорости и вхождение в плотные слои становится причиной, по которой конструкция переживает серьезные нагрузки, способные выдержать не все материалы.
- В химической промышленности титановый сплав применяется по причине того, что он не реагирует на воздействие различных веществ.
- В судостроении титан хорош тем, что не реагирует на воздействие соленой воды.
В целом можно сказать, что область применения титановых сплавов весьма обширна. При этом проводится легирование, за счет чего существенно повышаются основные эксплуатационные качества материала.
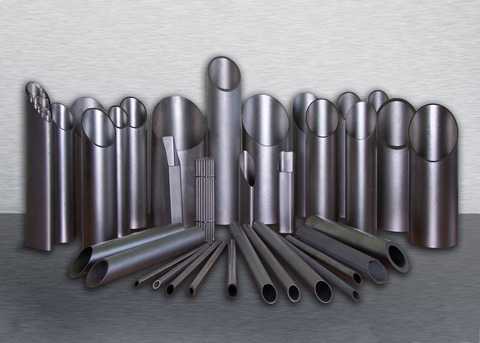
Трубы из титановых сплавов
Термообработка титановых сплавов
Для повышения эксплуатационных качеств проводится термическая термообработка титановых сплавов. Данный процесс существенно усложняется по причине того, что перестроение кристаллической решетки поверхностного слоя проходит при температуре выше 500 градусов Цельсия. Для плавов марки ВТ5 и ВТ6-С довольно часто проводят отжиг. Время выдержки может существенно отличаться, что зависит от толщины заготовки и других линейных размеров.
Детали, изготавливаемые из ВТ14, на момент применения должны выдерживать температуру до 400 градусов Цельсия. Именно поэтому термическая обработка предусматривает закалку с последующим старением. При этом закалка требует нагрева среды до температуры около 900 градусов Цельсия, в то время как старение предусматривает воздействие среды с температурой 500 градусов Цельсия на протяжении более 12-и часов.
Индукционные методы нагрева позволяют проводить самые различные процессы термической обработки. Примером можно назвать отжиг, старение, нормализацию и так далее. Конкретные режимы термической обработки выбираются в зависимости от того, какие нужно достигнуть эксплуатационные характеристики.
Если вы нашли ошибку, пожалуйста, выделите фрагмент текста и нажмите Ctrl+Enter.
stankiexpert.ru
Титановый нож (плюсы и минусы)
В современных реалиях можно встретить ножи, изготовленные как из старой доброй стали, так и из новомодного пластика. В ход идут самые неожиданные материалы, открывая перед мастерами ножеделами все новые и новые горизонты. Все это обилие и разнообразие сырья вызвано стремлением человека найти универсальное решение для производства ножевой продукции. К сожалению, за всю свою долгую историю человечество так и не сумело изобрести сферического коня в вакууме. А значит, любой материал обладает как своими плюсами, так и минусами.
Так коррозионно-стойкие стали с содержанием углерода в пределах 0,65% грешат своим излишне мягким нравом. Другими словами они плохо держат заточку и обладают низкой износоустойчивостью. Нож из 420-ой стали приходится часто править и приводить в надлежащий вид. В противовес «мягким» сталям (твердостью в 52-56 HRC) образцы, с содержанием углерода достигающим 1% и твердостью 59-61 HRC, выигрывают в плане износостойкости, но уже не являются столь коррозийно-устойчивыми.
Казалось бы, что проблемы с коррозионной устойчивостью можно решить при помощи обработки клинка специальными материалами от напыления пластмасс до твердосплавного покрытия рабочей поверхности ножа. Однако, первый вариант решает проблему коррозии и устойчивости клинка к агрессивным средам, но является недолговечным – пластмассовое покрытие быстро царапается и обладает слабой износостойкостью. А, твердосплавное покрытие, в свою очередь, даже при небольшом повреждении требует капитального ремонта, с заменой покрытия целиком.
Керамические ножи остры, легки, химически нейтральны и уже много лет радуют как домохозяек, так и шеф-поваров. Но при всех своих несомненных плюсах керамические инструменты хрупки, далеко не универсальны и требуют особого подхода к заточке.
Ножи из различных видов пластмасс тоже нельзя считать вершиной ножевой продукции. Качественный пластиковый нож требует высокотехнологичного, затратного, да еще и вредного для окружающей среды производства. В противном случае нож будет скорее бестолковой игрушкой, нежели полезной в хозяйстве вещью. Эстетически привлекательный вид и легкость ножа не смогут заменить, надлежащую хорошему инструменту, прочность и надежность.
Поиск новых решений в сфере ножевого производства, привел светлые умы современности к идее использования титановых сплавов. Титан уже давно наличествует в производстве ножей, преимущественно используясь для изготовления мелких деталей: штифтов, винтов, ручек и т.д. Легкий, прочный и биологически нейтральный материал зарекомендовал себя в таких стратегически важных отраслях как самолето — и судостроение. Но, несмотря на все это, длительное время об изготовлении полностью титановых ножей не могло быть и речи.
Титановые сплавы можно разделить на три группы:
- Сплавы с альфа-структурой;
- Сплавы альфа+бета-структурой;
- Сплавы с бета-структурой.
Из всех трех видов, для производства ножей подходят только сплавы, обладающие бета-структурой. Подобные сплавы содержат 25% ванадия, 2% алюминия, 15% хрома, 0,15% кислорода и до 0,3% углерода. Такой состав позволяет сочетать пластичность, прочность, упругость, высокую коррозионную устойчивость, небольшой вес и антибактериальные свойства. Твердость клинка из бета-сплава титана достигает 48 HRC. Следовательно, резать такой нож будет примерно так же как нож, выполненный из 420-ой стали.
Рассмотрим подробнее все плюсы и минусы титановых ножей. Начнем с качеств положительных.
- Парамагнитность титана. Другими совами титан является материалом немагнитным. Не знаю, чем это может помочь в повседневной жизни, но все поклонники титановых ножей в один голос рассказывают про то, как удобно и безопасно титановыми ножами обезвреживать взрывные устройства, оснащенные магнитным взрывателем. Собственно говоря, как раз в этой области и отметилась компания Mission Knives, со своими знаменитыми подводными ножами — «MPK-Ti». Поскольку вышеозначенная функция титановых ножей является весьма специфичной и узконаправленной, то плюс (для обычных пользователей) получается сомнительный. Но раз он есть, то о нем стоило упомянуть.
- Биологическая нейтральность. В отличие от первого свойства, биологическая нейтральность титановых ножей, является свойством полезным даже для рядовых домохозяек. Клинок не вступает в химическую реакцию при контакте с продуктами питания, а значит, гигиеничность процесса приготовления пищи остается на должном уровне. Кроме того именно биологическая нейтральность титана, обеспечила ему надежное место в производстве медицинского оборудования.
- Коррозионная стойкость. Титановые ножи нисколько не боятся ржавчины. Нож из титанового сплава спокойно выдерживает, разрушительное для большинства металлов, воздействие морского воздуха и воды. Тонкая оксидная пленка, покрывающая титан, надежно противостоит воздействиям щелочной среды.
- Небольшой вес. Титановые ножи не в пример легче большинства металлических инструментов. Если сравнивать аналогичные по габаритам ножи из титана и стали, то второй выиграет в весе примерно на 40%. Согласитесь, это является несомненным плюсом. Более легкий нож положительно скажется как на весе снаряжения туриста, так и на усталости руки профессионального повара.
- Механические характеристики. Этот пункт является довольно спорным. Все познается в сравнении, а значит, если сравнивать титановые ножи с ножами пластиковыми и стальными, то результат получится неоднозначным. Титан проигрывает высоколегированным сталям, но тем ни менее является довольно прочным материалом.
- Эстетическая привлекательность. Анодирование титана позволяет получить фантастически красивые и насыщенные цвета. Визуальная привлекательность титановых ножей делает их все более востребованными на мировом рынке.
За всеми, вышеперечисленными плюсами, скрываются и недостатки ножей из титана.
- Невысокая износостойкость. Хорошо заточенный титановый нож не сможет удерживать свою заточку в идеальном состоянии длительное время. По сравнению со сталью титан гораздо менее твердый и быстрее теряет заточку.
- Трудность обработки титана. Титан в отличии от других металлов плохо поддается шлифовке. Обычные станки для шлифования металлов абсолютно не подходят, для обработки титановых сплавов. Они попросту ломаются, не справляясь с колоссальными нагрузками. Для производства титановых ножей необходимо специальное оборудование.
- Высокая цена материала. Титан является дорогим металлом, а сложность его обработки только лишь увеличивает и без того заоблачную цену.
В общем и целом титан является материалом неоднозначным и подчас непредсказуемым. Использование титановых ножей в бытовых целях является спорным. Однако, если идея поработать ножом из титана кажется Вам привлекательно, то дерзайте.
Автор: Lis
steel-knife.ru
Сталь с добавкой титана – Справочник химика 21
Применение элементов подгруппы титана. Титан вдвое легче стали, а титановые сплавы в. 3 раза прочнее алюминиевых, в 5 раз прочнее магниевых сплавов и превосходят некоторые специальные стали, в то время как их плотность значительно меньше, чем последних. Поэтому титан и сплавы на его основе широко используются в авиа- и судостроении, космической технике. Кроме того, титан и цирконий используются как в качестве легирующих добавок к черным и цветным сплавам, так и в качестве основы конструкционных материалов, способных работать в экстремальных условиях. Для легирования сталей и модифицирования чугунов обычно используют ферротитан и ферроцирконий (сплавы с железом, содержащие 20—40% Ti или Zr). Добавка к стали уже 0,1% Ti способствует повышению ее твердости и эластичности. Такая сталь идет на изготовление рельсов, вагонных осей и т. п. Добавки циркония в таком же количестве резко повышают вязкость стали (броневые плиты). [c.244]Как видим, в отмеченных марках стали добавками являются в основном никель (8—14%) и хром (16—21%). Для общей устойчивости хромоникелевых сталей к ним добавляются молибден и титан, что придает им прочность в процессах с коррозионноактивными реагентами при повышенных температурах. [c.162]
Имеется два метода термической обработки для предупреждения МКК — закалка, обеспечивающая полное растворение карбидов хрома или уменьшение влияния сегрегирующих примесей и стабилизирующий отжиг. Для большинства аустенитных сталей обычно принят режим закалки, состоящий в быстром охлаждении (в воде или на воздухе) после нагрева при 1020—1060 °С. Для низкоуглеродистых сталей, особенно в присутствии добавок бора и для молибденсодержащих сталей, предназначенных для работы в окислительных средах, температура закалки должна быть повышена [1.361. Стабилизирующий отжиг проводится обычно в интервале 850—950 °С при продолжительности 2—4 ч. Наиболее эффективен стабилизирующий отжиг для сталей с титаном или ниобием. В этом случае в процессе стабилизирующего отжига происходит более полное связывание углерода стабилизирующими добавками, а также образование крупных разобщенных карбидов хрома. При последующем провоцирующем нагреве не происходит опасное образование пограничных карбидов и МКК отсутствует. Стабилизирующий отжиг применим для повышения стойкости против МКК и нестабилизированных сталей, однако полное устранение склонности к МКК в этом случае невозможно из-за сохранения значительного пересыщения твердого раствора углеродом. Следует иметь в виду, что при стабилизирующем отжиге могут повышаться прочностные свойства и снижаться пластичность стали, а также могут образовываться избыточные фазы (например, сг-фаза), снижающие стойкость, особенно в окислительных средах. [c.70]
Металлургия. Ниобий и тантал — важнейшие компоненты металлических жаропрочных сплавов для газовых турбин. Присадки до 5% Nb или сплава Nb и Та повышают жаропрочность, жаростойкость, предел текучести сплавов с алюминием, молибденом, медью, титаном, цирконием. Добавка ниобия (в меньшей степени тантала) к нержавеющей стали (содержаш,ей 8% Ni, 18% Сг) устраняет межкристаллит-ную коррозию стали. Ниобием легируют также инструментальные стали. Его вводят в сталь в виде феррониобия (сплав железа с ниобием, до 60% Nb). [c.61]
При высокой температуре титан соединяется с галогенами, кислородом, серой, азотом и другими элементами. На этом основано применение сплавов титана с железом (ферротитана) в качестве добавки к стали. Титан соединяется с находящимися в расплавленной стали азотом и кислородом и этим предотвращает выделение последних при затвердевании стали, — литье получается однородным и не содержит пустот. [c.650]
Факторы, влияющие на межкристаллитную коррозию. Состав стали. Коррозионностойкие аустенитные стали содержат наряду с хромом, никелем и другие легирующие добавки молибден, кремний, титан, ниобий, марганец и т. д. [c.446]
Чтобы избежать межкристаллитного коррозионного растрескивания трубопроводов, теплообменников, печных труб установок гидроочистки, их систематически продувают азотом после регенерации, промывают щелочным раствором, переходят на стали с легированием стабилизирующими добавками (титан, ниобий, молибден), применяют стабилизирующий отжиг. Эти мероприятия не снижают стойкость оборудования к высокотемпературной сероводородной коррозии. Торкрет-бетонные покрытия, наносимые для понижения рабочих температур стенок наиболее ответственных аппаратов, изолируют металл от доступа агрессивного сероводорода [19, 57]. [c.169]
Щелочные растворы применяют главным образом при нанесении покрытий на коррозионно-стойкую сталь, алюминий, титан, магний, различные неметаллы, а также при необходимости осаждения многокомпонентных покрытий (сплавов) на основе никеля или кобальта (например, никель-кобальт-фосфорных или кобальт-вольфрам-фосфорных и других покрытий). При корректировании щелочные растворы могут работать длительное время благодаря наличию в их составе комплексообразователей (таких как лимоннокислый натрий и аммиак). Но в результате регулярного добавления гипофосфита в ванне растет концентрация фосфитов. Добавка хлористого никеля и аммиака увеличивает концентрацию хлористого аммония, что нежелательно. Так, в растворе при pH 8—9 следующего состава (г/л) хлористый никель 45 гипофосфит натрия 20 хлористый аммоний 45 лимоннокислый натрий 45 максимальная [c.24]
Практика показала, что для безгрунтового эмалирования наиболее пригодны стали, легированные небольшими добавками титана, ванадия, хрома, ниобия и циркония. Особый интерес представляет сталь, легированная титаном, так называемая титанистая сталь [151], которая обладает рядом преимуществ перед другими сортами стали (стр. 109). Однако высокая стоимость и дефицитность легированных сталей ограничивают их применение в эмалировочном производстве. [c.235]
Введение небольшого количества благородного металла в неблагородный металл, например в нержавеющую сталь или титан, может привести к возникновению центров низкого перенапряжения катодного восстановления растворенного кислорода или ионов водорода. Это позволяет получить большие токи и, следовательно, более положительные потенциалы в анодной области, что в некоторых условиях способствует пассивации [27]. Такой эффект был продемонстрирован для нержавеющих сталей [28], но иа практике он не применяется, так как в других условиях добавки благородного металла могут ускорять коррозию [c.225]
Щелочные растворы применяют главным образом при нанесении покрытий на нержавеющую сталь, алюминий, титан, магний, различные неметаллы, а также при необходимости осаждения многокомпонентных покрытий (сплавов) на основе никеля или кобальта (например, никель-кобальт-фосфорных или кобальт-вольфрам-фос( юрных и других покрытий). Благодаря наличию в составе щелочных растворов таких комплексообразователей, как лимоннокислый натрий и аммиак, они могут при корректировании работать длительное время. Однако в результате регулярного добавления гипофосфита в ванне растет концентрация фосфитов добавка хлористого никеля и [c.28]
Черные металлы — чугун и сталь, занимая исключительно важное место в промышленности и технике, часто служат объектом анализа. Число элементов, которое может находиться в железных сплавах, очень велико, чем и определяется большое разнообразие их физико-механических и химических свойств. Наряду с давно применяемыми легирующими элементами (такими, как хром, никель, кобальт, ванадий, вольфрам), в практику черной металлургии и в последние десятилетия вошли новые компоненты (например, редкоземельные, цирконий, гафний, титан, тантал, ниобий), добавки которых позволяют получать черные металлы с еще более ценными качествами. Кроме того, растет внимание и к ряду элементов, присутствие которых даже в малых количествах, может существенно изменять качество металла. Сюда относятся мышьяк, медь, олово, сурьма, алюминий, цинк и др. Содержание этих компонентов также контролируется, особенно в высококачественных сталях. [c.473]
Увеличенное содержание хрома и никеля способствует повышению стойкости стали к точечной коррозии. Аналогичное действие оказывают молибден, кремний и рений, препятствующие зарождению и вызывающие репассивацию питтингов. Углерод, титан и ниобий снижают стойкость хромоникелевой стали к точечной коррозии, такое же действие оказывает марганец при одновременном снижении содержания хрома и никеля. В отличие от хрома никель и марганец способствуют аустенизации стали. Никель, как правило, повышает коррозионную стойкость и уменьшает вероятность коррозии под действием напряжения. Добавка никеля к хромистым сталям позволяет сохранять их аустенитную структуру. Типичный представитель никельсодержащих сталей — сталь 18/8 (18% Сг, 8% Ni), содержащая 0,02— 0,12% углерода. Скорость коррозии этой стали в морской воде равна 0,010—0,012 мм/год. [c.25]
Предупреждению или уменьшению щелевой коррозии способствуют те компоненты сплава, которые помогают сохранить пассивность при низкой концентрации в среде растворенного кислорода и наличии кислых продуктов коррозии. К этой категории относятся добавки молибдена к нержавеющей стали 18-8 (марка 316) или добавки палладия к титану. [c.315]
Применение сУ-металлов четвертого периоде. Титан и его сплавы, устойчивые к коррозии, являются важными конструкционными материалами новой техники. По удельной прочности титан превосходит все другие металлы. Различают а-сплавы титана (с А1 и Сг), предназначенные для эксплуатации при температурах ниже 800 и Р-сплавы (с Мо и V) — для работы в высокотемпературных условиях. Получаемый сплав титана с железом (ферротитан) используется как добавка к сталям, повышающая их прочность. Титаном покрывают внутри емкости, предназначенные в пищевых производствах для особо агрессивных сред, например для получения пектина из плодов. [c.420]
При выплавке сталей в них вводят легирующие добавки, в качестве которых используют кремний, марганец, кобальт, никель, ванадий, хром, вольфрам, молибден, титан, алюминий и другие металлы. Изменяя состав, можно получить стали, обладающие повышенной прочностью, износостойкостью, коррозионной стойкостью (нержавеющие стали). [c.287]
Имеющиеся данные о влиянии титана на склонность стали к хрупкому разрушению весьма противоречивы. Добавки 0,10—0,25% титана [59] снижают величину ударной вязкости материала при понижении температуры. Дальнейшее увеличение титана до 0,4% существенно улучшает свойства стали, В качестве раскислителя титан оказывает положительное действие на свойства стали за счет измельчения зерен, изменения соотношения феррита и перлита и понижения склонности к перегреву. При получении мелкодисперсной структуры (зерна с 5-го до 10-го номера) при добавках титана 0,3—0,4% на каждый номер измельчения зерна критическая температура хрупкости, определенная а =2 кгс-м/см , понижается в среднем на 10°С [41]. [c.41]
Элементы ЫЬ и Т1 вводят в сплав для повышения стойкости к сенсибилизации, поскольку они образуют карбиды. Однако присутствие таких добавок уменьшает стойкость против КР в хлоридных средах [66, 67, 81, 82, 89]. Установлено [94], что в малых количествах как ниобий, так и титан уменьшают ЭДУ нержавеющей стали. В то время как малые добавки титана снижают стойкость против КР [81, 82, 87], введение 2% Ti дало положительный эффект [91]. Таким образом, может существовать некоторое значение его концентрации, при котором стойкость против КР достигает минимума. Как и в случае кремния, положительное влияние больших добавок титана может быть связано со стабилизацией б-феррита. В работах [66, 91] для объяснения положительного влияния больших добавок Т1, 51, V и А1 предполагается, что уже 5%-ная объемная доля б-феррита способна вызывать притупление трещин, распространяющихся в аустените. Этот вопрос будет рассматриваться в дальнейшем, а здесь еще раз следует отметить, что титан и ниобий в таких количествах, которые заведомо остаются в растворе, отрицательно влияют на стойкость сталей. [c.73]
Добавка Концентрация,. оль/л Сталь 18%Сг-8%К1 Титан [c.182]
В литературе имеются также сведения по адгезии композиций на основе алюмохромфосфатного связующего АХФС-1 (с добавками различных металлических порошков) к бронзе БрХ08, стали 1Х18Н9Т, титану, молибдену, графиту [15]. [c.116]
Методы, более широко применяемые в настоящее время для устранения склонности к интеркристаллитной коррозии, основаны на добавке других элементов, причем наиболее часто добавляется титан. Если сталь содержит титан, который -имеет большее сродство к углероду, чем хром, выпадают преимущественно карбиды титана, а хром остается в твердом растворе. Содержание титана, необходимое для предупреждения интеркристаллитной коррозии, естественно, увеличивается с содержанием углерода кривые Гудремона и Шафмайстера [c.566]
Лигатур Ы.1Б металлургии черных и цветных металлов титан применяется в качестве раскислителя и деазотизатора, так как он энергично соединяется с кислородом и азотом, образуя соединения, уходящие в шлак.сЛля этой цели используют ферротитан (18—25% Т1), купротитан (5—12% Т1), алютит (40% А1, 22—50% Т1 и до 40% Си). Очистка от кислорода способствует образованию тонкой плотной структуры стали, обладающей повышенными механическими свойствами. Титан связывает и серу, вызывающую красноломкость стали, х/ При введении титана в качестве легирующей добавки в хромо-никелевые нержавеющие стали (до 0,8%) образуются включения карбидов титана, повышающие жаростойкость и уменьшающие склонность к межкристаллитной коррозии при сварке и термической обработке. У Присадка 0,05—0,15% титана к обычной углеродистой стали облагораживает ее и улучшает механические свойства. Введение титана в алюминиево-магниевые сплавы (до 0,6%) улучшает их механические свойства, повышает коррозийную стойкость и устойчивость к окислению при нагревании [II, 35]. [c.242]
Применение. Титан очень важный конструкционный материал для современной техники. Титан и его сплавы отличаются высокой прочностью, легкостью, тугоплавкостью, химической стой- костью при обычной температуре. Титан используют в качестве легирующей добавки и как вещество, связывающее кислород, азот, водород и другие примеси в металле в малорастворимые соединепия (последние удаляются в шлак). Ферротитан добавляют в специальные марки сталей для повышения их коррозионной стойкости и механической прочности при высоких температурах [ферротитан получают алюмотермическим восстановлением (флюс СаО) предварительно обожженного (для удаления серы) концентрата РеТЮз], Устройства, изготовленные из титана и его сплавов, [c.511]
Некоторые промышленные сплавы Сг—N1—Ре—Шо, соот ветствующие по составу нержавеющим сталям с высоким содержанием никеля, содержат также несколько процентов меди. Помимо других сред, они предназначены для использования в растворах серной кислоты в широком интервале концентраций и обладают в них достаточной коррозионной стойкостью. Легирующие добавки меди выполняют ту же роль, что и добавки палладия к титану (см. разд. 5.4) за счет ускорения катодного процесса [c.362]
Велика роль азота в металлургических процессах. Обычно его присутствие ухудшает свойства металлов, поэтому стремятся предотвратить взаимодействие металла с азотом или удалить из металла содержаи ийся в нем азот. В частности, при юлучении высококачественных сталей азот удаляют добавкой титана (в виде сплава с железом-ферротнтана). Титан образует очень прочный нитрид, который переходит в шлак. Вместе с тем проводят азотирование поверхности стали, образовавшиеся нитриды железа значительно увеличивают твердость поверхностного слоя изделий. [c.411]
Использование титана, циркония, гафния и их соединений. По коррозионной стойкости даже в морской воде титан превосходит все нержавеющие стали и цветные металлы. Поэтому он и его сплавы находят различное применение в машиностроении, авиа- и судостроении, турбостроении, в производстве вооружения. Добавка 0,1% Т1 резко повышает качество стали. Сталь с добавкой 2г используется в изготовлении броневых плит и щитов, стволов орудий и пр. Эти металлы связы-вакзт азот и кислород, растворенные в стали, что предотвращает образование раковин и сообщает ей однородность. [c.332]
Несмотря на перечисленные достоинства, применс-Н1 с окислителей связано со следующими недостатками. Обычно предварительная подготовка пробы к анализу состоит в переведении анализируемого материала в раствор посредством обработки различными кислотами чаще всего применяют азотную кислоту или ее смесь с хлороводородной или серной кислотой. Так, медные сплавы растворяют в азотной кислоте, причем содержащиеся в них элементы — железо, олово и другие—превращаются в соединения высших степеней окисления. При анализе различных чугунов и сталей необходимо определять ванадий, молибден, вольфрам, титан и нс-которые другие легирующие элементы, которые вследствие обработки пробы окислительными агентами также содержатся в полученном растворе в высших степенях окисления. Железные руды содержат оксиды железа растворяя их в хлороводородной кислоте с добавками различных окислителей, получают железо в степени окисления +3 и т. д. [c.435]
В составе малоуглеродистой стали обычно присутствуют углерод, марганец, кремний, сера, фосфор, кислород, азот, водород, а также могут быть добавки легирующих элементов, используемых в качестве раскислителей хром, алюминий, бор, ванадий, титан, молибден. Содержание каждого из указанных элементов в малоуглеродистой стали составляет десятые либо сотые доли процента. Между тем, их влияние на склонностъ стали к хрупкости при понижении температуры может оказаться значительным, хотя удельный вес влияния каждого элемента определить весьма трудно. Поэтому исследователи рассматривают свойства чистых сплавов а-желе-за с регулируемыми добавками различных элементов [48], а промышленные стали оценивают с применением методов статистического анализа [49]. [c.39]
Методы определения марганца в титане и его сплавах аналогичны методам определения этого элемента в сталях. Для определения марганца в титане был предложен объемный метод основанный на окислении марганца персульфатом аммония с добавкой нитрата серебра и титровании образующегося иона перманганата стандартным раствором арсеннта натрия. В присутствии большого количества титана стехиометрия этой реакции зависит от содержания марганца. Поэтому титрование лучше проводить стандартными растворами соли Мора с добавкой перманганата калия [c.59]
Условно стали подразделяют на нпзколегировапные с относительно небольшим количеством облагораживающих добавок и высоколегированные, содержание добавок в которых может превышать содержание железа. Важнейшие легирующие элементы хром, никель, молибден, марганец, кремний, титан, ниобий, вольфрам, ванадий. Добавки отдельных элементов и их сочетание вызь -вают различные измеиеиня конструкционных свойств сталей. [c.20]
ЖАРОСТОЙКАЯ СТАЛЬ – сталь, отличаюЕцаяся жаростойкостью. Стойка против интенсивного окисления на воздухе или в других газовых средах при т-ре выше 550° С. Используется с конца 19 в. Жаростойкость обусловлена наличием на поверхности Ж. с. плотной и тонкой пленки окислов, достаточно прочно сцепленной с осн. металлом. Пленка состоит преим. из окислов легирующих элементов — хрома, кремния и алюминия, термодинамически более стойких, чем окислы железа. Содержание этих элементов определяет класс Ж. с. (табл. 1). Хром, являясь осн. легирующим элементом Ж. с., повышает жаростойкость пропорционально увеличению его содержания (рис.). Никель способствует образованию аустенитной структуры (см. Аустенит). Стали с такой структурой легче обрабатывать, они отличаются хорошими мех. св-вами. Добавки кремния (более 2%) и алюминия (более 0,5%) ухудшают мех. св-ва стали. Титан, ниобий и тантал связывают углерод в карбиды, предотвращая выделение карбидов хрома, которое обедняет близлежащую металлическую основу хромом и приводит к уменьшению жаростойкости. Молибден и вольфрам (в небольших количествах) незначительно повышают жаростойкость, но уменьшают склонность стали к ползучести при высокой т-ре. Если молибдена содержится более 3—4%, жаростойкость стали резко ухудшается из-за образования нестойких и рыхлых его окислов. Церий и бе- [c.420]
chem21.info
Глава 4. ЗНАКОМЬТЕСЬ – ТИТАН!. Металл Века
Брусок металла неяркого серебристо-серого цвета. ”Сталь” — привычно мелькает в сознании. Но стоит взять брусок в руку, как на мгновение возникает ощущение нереальности происходящего: металл оказывается удивительно, неправдоподобно легким. Это не сталь, а титан.
Любопытно наблюдать за реакцией людей, плохо знакомых с цветными металлами, когда к ним в руки попадает какой- нибудь предмет из титана. Первоначальное удивление (темный металл, а такой легкий!) сменяется недоумением, а затем убеждением, что их “разыгрывают”, и они пытаются разобраться, где же скрывается подвох: вертят предмет в руках, говорят, что внутри металла имеются пустоты и тому подобное. Но никакого подвоха нет. Титан действительно почти вдвое легче железа и всего лишь в полтора раза тяжелее алюминия. Один кубический сантиметр железа имеет массу 7,8 грамма, алюминия — 2,7, титана — 4,5 грамма. Надо признать все же, что 4,5 грамма в кубическом сантиметре не так уж и мало, особенно если учесть, что в кубическом сантиметре магния содержится 1,7 грамма, а такой металл, как литий, вдвое легче воды.
Поскольку к легким относят металлы, удельная масса которых не превышает 5 граммов на кубический сантиметр, то титан, следовательно, самый тяжелый среди легких металлов. Но и ”самый тяжелый”, он все-таки по праву принадлежит к числу легких металлов.
Однако легкость сама по себе еще ничего не решает. Легок натрий, но он плавится уже при температуре около 100 °С и как щелочной металл настолько активен, что его нельзя хранить на открытом воздухе. Хранят этот элемент в керосине. Еще легче и активнее металл литий. Он, как и остальные щелочные металлы, так непрочен, что легко режется обыкновенным ножом.
Мы привыкли к тому, что всякий конструкционный материал имеет свои достоинства и недостатки. Если алюминий,
например, почти в три раза легче стали, то он и в несколько раз менее прочен и плавится уже при 660 градусах, тогда как точка плавления стали находится выше 1500 °С. Примерно то же самое можно сказать и о магнии.
Интересно, а насколько титан уступает стали по прочности? Титан не уступает стали: он в полтора раза прочнее! Но, может быть, этот металл плавится при невысоких температурах? Титан плавится только при 1660 °С, то есть при более высокой температуре, чем железо и сталь. Так что не зря титан отливает стальным блеском: этот отлив не обманывает.
Но, кроме хорошей прочности, конструкционный материал обязательно должен иметь и такое важное качество, как пластичность. Пластичность — это способность материала изменять свою форму не разрушаясь, и именно в этой способности титану долго было отказано. Еще в сороковые годы нашего века о титане писали, что он ”хрупок и легко превращается в порошок при дроблении в ступке”. Любопытна и следующая запись: “Попытки вытянуть проволоку из титана безуспешны”.
Меньше всего хотелось бы иронизировать над автором приведенных строк, тем более что он поставил перед собой задачу ”заполнить досадный пробел в литературе, посвященной столь важному и интересному химическому элементу”.
На протяжении полутора столетий подлинных свойств металла не знал никто в мире. Но как только стали получать титан достаточной степени чистоты, сразу выяснилось, что причиной хрупкости металла являются примеси, а чистый титан очень пластичный материал. Его куют, как железо, вытягивают в проволоку, прокатывают в листы, трубы, ленты и даже в фольгу толщиной в сотые доли миллиметра.
Титан — более упругий металл, чем магний и алюминий, но менее упругий, чем сталь. Он гораздо тверже алюминия, магния, меди, железа и почти не уступает особо обработанным легированным сталям. Титан — один из немногих металлов, которые наряду с высокой прочностью и пластичностью обладают хорошей вязкостью, то есть противостоят воздействию ударов. Этот металл характеризуется еще и таким ценным свойством, как отличная выносливость.
Важный показатель любого металла — предел текучести. Чем он выше, тем лучше металл сопротивляется нагрузкам, стремящимся смять его, изменить размеры и форму изготовленной из него детали. У титана предел текучести весьма высок: в два с половиной раза выше, чем у железа, в три с лишним раза выше, чем у меди, и почти в 18 раз превосходит этот же показатель для алюминия.
Итак, титан гораздо прочнее и легче обычной углеродистой стали, получаемой из чугуна. Но в современном машиностроении широко распространены не столько углеродистые, сколько легированные стали, то есть сплавы на основе железа с добавками никеля, хрома, марганца, молибдена, вольфрама, а также других цветных и редких металлов. Легированные стали значительно прочнее углеродистых и в несколько раз прочнее технического титана. Выходит, что титан все-таки уступает стали? Нет не уступает! Титан тоже можно легировать и тогда получают сплавы, прочность которых в два- три раза больше прочности чистого титана.
Титановые сплавы — это, быть может, самые совершенные материалы, которыми располагает современная техника. Они превосходят все другие распространенные металлы по такому важному показателю, как удельная прочность. Что это такое? Не что иное, как прочность, приходящаяся на единицу массы.
Чтобы нагляднее постичь это, представим себе такую картину. На помост выходят тяжелоатлеты. Вряд ли нас удивит то, что грузный человек поднимает большую тяжесть. Ведь так оно и должно быть: те, кто полегче, обладают, как правило, меньшей силой, а от массивного, с мощными бицепсами атлета мы ждем и высокого результата. Не зря же в тяжелоатлетическом спорте введены различные весовые категории. А теперь вообразим, что после этого тяжелоатлета на помост вышел скромный, на первый взгляд ничем не примечательный спортсмен, худощавый, среднего роста и с первой попытки покорил тот же самый вес. Кто же из них сильнее? Конечно же, худощавый!
Такую же аналогию можно провести относительно титановых сплавов и специальных сталей. Титановые сплавы почти вдвое легче, а нагрузки выдерживают почти такие же.
Если бы все достоинства титана заключались только в его легкости и прочности, то и этого было бы уже достаточно для развития титановой промышленности, так как и в этом случае игра стоила свеч и нашлось бы немало отраслей, заинтересованных в таком материале. Но, помимо прочности и легкости, титан отличается еще и замечательной стойкостью против коррозии.
Поделитесь на страничкеСледующая глава >
tech.wikireading.ru
титан или нержавеющая сталь? Какими данными подтвердить? Спасибо.
Титан – очень мягкий металл и никакой “крепостью” не обладает, типа как аллюминий. Но при добавлении в сталь повышает ее прочность. Многие сорта нержавеющей стали содержат его, например 12Х18Н9Т, они очень прочные. Дешевая нержавеющая сталь, например Х13, не содержит его и менее прочная. Подтверждается это лабораторными испытаниями, данными из гостов и справочников.
зачем вам это надо? титан-легче, прочность не знаю, но при ударе он может треснуть, чего не произойдет с нержавейкой, но у нее раз в 10 больше вес.
у альпинистов титановые замки на страховках -это подтверждение бытовое, а научное ищи в уч физики…
Крепость как оценивать? В оборотах?
титан предел прочности 300-550 Нержавеющие стали (вязкие) с пределом прчности 500- 800
По удельной прочности (прочность/вес) – титановые сплавы По абсолютной – высокопрочные стали. Прочнее в полтора раза любых титановых сплавов. Нержавейка по абсолютной прочности в конкурентах не значится. Если прочность нужна при высоких температурах – хромникелевые сплавы.
В сопромате сравнение на растяжение, изгиб, сдвиг посмотри. Титан крепче.
Крепость – это у самогона или водки… . У металлов и сплавов другие показатели их механических и физических свойств: твёрдость, вязкость, упругость, пластичность, прочность и др
Однозначно титан. Титаном сталь режут. Тот же самый <победит>, как его в народе называют, есть титан. В новейших автомобилях иностранного производства моторы производят из титана, а не из стали (например Bugatti Veyron). Там сталь просто не выдержит. Столько хватит?)
“Титаном сталь режут. Тот же самый <победит>, как его в народе называют, есть титан. ” – От оно как оказывается! Бугагашенька, повеселил аднака!
<a rel=”nofollow” href=”https://ru.wikipedia.org/wiki/Победит” target=”_blank”>https://ru.wikipedia.org/wiki/Победит</a>
титан только по коррозионной стойкости выигрывает и по весу .А так это геморойный материал – то что в быту из него делается – просто понты и не более …
Еще в Советском Союзе, самые совершенные подводные лодки делались полностью из титана и им же, принадлежат все рекорды скорости и погружения. В России, с недавних пор вернулись к этой традиции, и строить титановые подводные лодки могут единицы стран. На ваш вопрос, ответ очевиден.
Руслан Искандаров Ну Вы маханули…” Еще в Советском Союзе, самые совершенные подводные лодки делались полностью из титана…” Одну всем Союзом еле осилили, и та утонула (как путЕн сказал)…))) Дорогое удовольствие!!!
touch.otvet.mail.ru