Токарная обработка наружных поверхностей – Обработка наружных цилиндрических поверхностей – Токарное дело
alexxlab | 30.07.2019 | 0 | Вопросы и ответы
Обработка наружных цилиндрических поверхностей – Токарное дело
Обработка наружных цилиндрических поверхностей
Категория:
Токарное дело
Обработка наружных цилиндрических поверхностей
Если вращать прямоугольник АБСД вокруг оси АД, получим цилиндрическую поверхность. Любая точка на поверхности цилиндра одинаково удалена от оси АД, которую называют осью цилиндра. В зависимости от требований, предъявляемых к точности обработки и параметрам шероховатости обработанной поверхности, различают черновое» получистовое, чистовое и тонкое (алмазное) обтачивание.
В зависимости от длины заготовки обтачивание производят в патроне без поджатия центром, если 1,5, в патроне с поджатием задним центром, если L/d 1,5, в патроне с неподвижным люнетом, если L/d> >12. Если L/d< 12, обтачивание в центрах производят без люнета.
Частоту вращения заготовки и подачу инструмента назначают в зависимости от глубины резания, материала заготовки и инструмента. Частоту вращения и подачу устанавливают посредством рукояток, расположенных на передней стороне коробки скоростей и подач. При продольном точении в патроне соблюдают следующую последовательность. Устанавливают трехкулачко-вый самоцентрирующий патрон на шпиндель. Закрепляют резцы для черновой и чистовой обработки в резцедержателе так, чтобы их вершины совпадали с линией центра станка. Зажимают заготовку в патроне. Устанавливают на станке 1К62 требуемую частоту вращения и подаче рукоятками. Закрепляют в патроне заготовку и проверяют ее биение. Включают станок и подводят резец к заготовке до соприкосновения с ее поверхностью для определения толщины срезаемой стружки. Отводят резец вправо от торца заготовки и по лимбу устанавливают глубину резания. Включают продольную подачу, протачивают заготовку на длине 5—10 мм и отводят резец. Выключают станок и измеряют штангенциркулем обточенный диаметр. Если диаметр обработанной части заготовки не соответствует заданному, то корректируют глубину резания по лимбу. Включив станок и установив рукоятку продольной подачи, обтачивают заготовку на требуемую длину I. Выключают подачу, отводят резец и выключают станок. Проверяют полученный диаметр заготовки. Если он соответствует заданному, то разжимают кулачки и вынимают деталь из патрона.
Рис. 173. Крепление энсцентриновых заготовон
Рис. 174. Установка нопенчатого вала на токарном станне
Рис. 175. Установка нопенчатого вала в центросместитепе и эксцентрических деталей в центрах
При обтачивании заготовки в центрах необходимо проделать следующее.
1. Установить центры в шпинделе передней и задней бабки.
2. Совместить центры и в зависимости от условий обработки установить открытый или закрытый (с предохранительным кожухом) поводковый патрон 2.
4. Закрепить резец в резцедержателе по линии центров.
5. Установить заготовку с хомутиком в центрах и резец под углом 90° к оси центров станка.
6. Для определения правильности установки заготовки и резца обработать поверхность на длине 3—5 мм и отвести резец. Затем установить требуемый размер заготовки. Включить станок, проточить заготовку на длине 10—15 мм. Выключить рукоятку подачи и отвести резец за торец заготовки. Измерить штангенциркулем диаметр обточенной части заготовки и при необходимости внести коррекцию. Включить станок и рукоятку подачи, обточить заготовку на заданную длину. Выключить рукоятку подачи, отвести резец и выключить станок. Измерить обработанный диаметр заготовки микрометром и при необходимости обточить снова.
Рис. 176. Центрование заготовок
Рис. 177.Инструменты и приспособления для разметни и сверления центрового отверстия
Рис. 178. Образование цилиндричесной формы поверхности
Рис. 179. Схемы применения центров и люнетов в зависимости от длины заготовки
Взять левой рукой заготовку, правой рукой отвести задний центр и снять заготовку со станка. Открепить хомутики и закрепить его на обработанной поверхности заготовки через разрезную втулку. Установить заготовку в центрах станка. Подвести резец на заданный размер по лимбу, включив подачу, проточить необработанную поверхность заготовки. Выключить станок и измерить диаметр обработанной поверхности. Снять деталь со станка, затем с детали хомутик и разрезную втулку.
Для установки резца на требуемую глубину на винте поперечной и продольной подачи установлены лимбы, на которых нанесены деления. При касании резца поверхности заготовки лимб устанавливают на нулевую отметку. На большинстве станков лимб имеет 100 делений. При шаге Р — 5 мм винта поперечной подачи и полном обороте лимба резец перемещается на длину 5 мм. Следовательно, при перемещении лимба на одно деление резец переместится на 5/100 = 0,05 мм, а диаметр обработанной поверхности уменьшится на 0,1 мм. Необходимо помнить, что при установке резца на требуемую глубину резания рукоятку лимба следует повернуть назад на один оборот для устранения зазора.
Рис. 180. Последовательность действий при продольном точении
Продольный и поперечный зазор в суппорте устраняют, перемещая подвижные гайки 2 в осевом направлении гайкой и винтами.
Для безопасной работы на токарном станке необходимо учесть следующее.
1. Нельзя обрабатывать заготовку, если кулачки выступают из корпуса патрона более чем на 1/4 своей длины.
2. Часть резца, выступающая из резцедержателя, -должна быть как можно короче.
3. Нельзя обрабатывать заготовки, ось которых не совпадает с осью станка (отклонение Я), в том числе изогнутые заготовки.
4. Нельзя работать с большими значениями подачи и глубины резания, так как резец «затягивается» под заготовку, что приводит к его поломке и вылету заготовки из патрона.
5. При большом продольном и поперечном зазоре между заготовкой и центрами заготовка может выскочить из центров.
6. Искривленные заготовки перед установкой на станке необходимо выправить с помощью винтового пресса.
Широкие канавки обрабатывают за несколько рабочих ходов, если ширина с резца меньше ширины h канавки. Сначала прорезают правую часть канавки с припуском Д на глубину канавки. Затем прорезают левую часть канавки на втором рабочем ходе. За третий рабочий ход канавку проходят за всю глубину. Затем резцом снимают припуск Л на всей шарине h канавки, перемещая резец к правой стенке канавки.
Рис. 181. Последовательность обработни заготовни в центрах
Рис. 182. Лимбы для установни глубины резания
Рис. 183. Устранение продольного и поперечного зазора суппорта
Реклама:
Читать далее:
Обработка торцовых поверхностей
Статьи по теме:
pereosnastka.ru
ОБРАБОТКА НАРУЖНЫХ ЦИЛИНДРИЧЕСКИХ И ТОРЦОВЫХ ПОВЕРХНОСТЕЙ
§ 1. Общие сведения1. Виды наружных поверхностей. По форме наружные поверхности цилиндрических деталей могут быть разделены на цилиндрические, торцовые, уступы, канавки, фаски (рис. 25).
Цилиндрические поверхности 1 получаются вращением прямой линии (образующей) вокруг параллельной ей линии, называемой осью цилиндра. В продольном сечении такие поверхности прямолинейны, в поперечном — имеют форму окружности.
Крайние плоские поверхности 2, перпендикулярные к оси детали, называют торцами.
Переходные плоские поверхности 5 между цилиндрическими участками, перпендикулярно расположенные к оси детали, принято называть уступами.
Занижения 4, выполненные по окружности цилиндрической или торцовой поверхности, называются канавками.
Фасками называются небольшие скосы 3 на кромках детали.
2. Способы установки заготовок на станке. При токарной обработке наиболее часто применяются четыре основных способа установки заготовок на станке: в патроне, в патроне и заднем центре, в центрах и на оправках.
В патроне 1 (рис. 26, а) устанавливают короткие заготовки с длиной выступающей части l из кулачков до 2—3 диаметра d.
Для повышения жесткости более длинные заготовки устанавливают в патроне 1 и заднем центре 2 (рис. 26, б).
Установку в центрах (рис. 26, в) применяют в основном для чистового обтачивания длинных валов, когда необходимо выдержать строгую соосность обрабатываемых поверхностей, а также в случаях последующей обработки детали на других станках с такой же установкой. Заготовку опирают центровыми отверстиями на передний 4 и задний 2 центры, а вращение от шпинделя к ней передается поводковым патроном 1 и хомутиком 3.
Установка на оправке 1 (рис. 26, г) используется для обработки наружных поверхностей, когда заготовка имеет ранее обработанное отверстие (см. гл. IV).
§ 2. Обработка цилиндрических поверхностей
1. Обтачивание гладких поверхностей. Технические требования. При обработке цилиндрической поверхности токарь должен выдержать ее размеры (диаметр, длину), правильную форму и требуемую чистоту..
Точность размеров ограничивается допустимыми отклонениями, проставляемыми на чертеже. Размеры без допусков должны
выполняться по 7-му или реже 8—9-му классам точности. В этом случае на наружные размеры допустимые отклонения устанавливаются на минус от номинального размера, на внутренние-—на плюс.
Точность цилиндрической формы определяется отклонениями цилиндра в продольном направлении — конусообразностью, бочкообразностью, седлообразностью и в поперечном — овальностью (рис. 38). Первые три погрешности характеризуются разностью диаметров обработанной поверхности по краям и в середине, четвертая — разностью диаметров одного сечения во взаимно перпендикулярных направлениях. Если на чертеже отсутствуют указания точности формы поверхности, то ее погрешности не должны превышать допуска на диаметр.
Чистота обработки характеризуется степенью шероховатости поверхности, остающейся на ней. после точения. Допустимая шероховатость обозначается на чертеже треугольником, справа от которого проставляется число, соответствующее классу чистоты.
Например, V.5 означает пятый класс чистоты.
Точность обработки должна соответствовать техническим требованиям рабочего чертежа. При этом следует учитывать, что нормально достижимая точность обтачивания на токарных станках составляет 3—4-й класс и чистота до 7-го класса. Поверхности более высокой точности и чистоты обычно обрабатывают точением предварительно с припуском 0,3—0,6 мм на диаметр для последующего шлифования.
Применяемые резцы. Обтачивание наружных поверхностей выполняют проходными резцами (рис. 39). По форме они делятся на прямые а, отогнутые б и упорные в.
Первые два типа резцов преимущественно применяют для обработки жестких деталей; ими можно обтачивать, снимать фаски, а отогнутыми и подрезать торцы. Наибольшее распространение в токарной практике получили упорные резцы, которые, кроме указанных работ, позволяют подрезать уступы. Эти резцы особенно рекомендуются для обтачивания нежестких валов, так как они создают наименьший по сравнению с другими резцами поперечный прогиб детали.
Проходные резцы имеют различную стойкость (время непосредственной работы от заточки до переточки). При равных условиях наименее стойки упорные резцы, так как их острая вершина менее прочна и быстрее нагревается. Эту особенность упорных резцов следует учитывать при назначении режимов резания.
При универсальных работах проходные резцы с различным радиусом закругления вершины применяют как для чернового, так и чистового точения. У черновых резцов вершину закругляют радиусом r=0,5—I мм, у чистовых- r = 1,5—2 мм. С увеличением радиуса закругления вершины чистота обработки улучшается.
Для выполнения только чистового обтачивания рекомендуется применять чистовые двусторонние резцы (рис. 39, г) с увеличенным радиусом закругления вершины г=2—5 мм, ими можно работать с продольной подачей в обе стороны.
Установка резцов на станке. Резцы должны быть правильно установлены и прочно закреплены в резцедержателе суппорта. Первое условие определяется положением резца относительно оси центров станка. Резцы для наружного точения устанавливаются так, чтобы вершина их находилась на уровне оси центров. В некоторых случаях, например при черновом обтачивании и обработке нежестких валов, рекомендуется выполнять такую установку выше линии центров на 0,01—0,03 диаметра детали.
Высоту установки резца регулируют стальными подкладками 1 (рис. 40, а), обычно не более чем двумя. При этом размеры подкладок должны обеспечивать устойчивое положение резца по всей опорной поверхности. Токарь должен иметь набор таких подкладок разной толщины для компенсации уменьшения высоты резца по мере переточки.
Установку резца по высоте проверяют совмещением вершин резца и одного из центров или пробной подрезкой торца заготовки.
В последнем случае при правильной установке резца в центре торца заготовки не должна оставаться бобышка.
Закрепление резца должно быть прочное, не менее чем двумя винтами. Для повышения жесткости крепления вылет резца из резцедержателя устанавливают наименьшим, не более 1,5 высоты стержня. Кроме того, резец располагают перпендикулярно к оси обрабатываемой детали (рис. 40, б).
Приемы обтачивания. Чтобы получить необходимый диаметр обрабатываемой поверхности, резец устанавливают на глубину резания. Для этого его подводят до касания с поверхностью вращающейся заготовки. Когда появится слабо заметная риска, резец отводят вправо за торец заготовки, лимб поперечной подачи устанавливают на нуль и подают суппорт поперечно вперед на требуемый размер по лимбу. Механическую продольную подачу включают после того, как резец врежется в металл ручным перемещением суппорта.
Установку резца на точный размер выполняют аналогично пробным обтачиванием конца заготовки на длину 3—5 мм. По результатам измерения диаметра полученной поверхности штангенциркулем (рис. 41, а) или при более высокой точности — микрометром (рис. 41, б) резец подают на окончательный размер по лимбу. Когда требуемый размер достигнут, лимбовое кольцо устанавливают на нуль для возможности обработки всех последующих деталей из партии без пробных отсчетов.
Длину обтачивания выдерживают разметкой заготовки или по лимбу продольной подачи. В первом случае на заготовке протачивают риску на определенном расстоянии от торца, расположение
которой устанавливают линейкой (рис. 42) или штангенциркулем. При пользовании для этой цели лимбом продольной подачи резей подводят к торцу заготовки, устанавливают лимб на нуль и руч-
ным продольным перемещением суппорта врезаются в металл. Затем включают продольную подачу и выполняют обтачивание. Подачу выключают, не доходя 2—3 мм до требуемого размера длины. Оставшуюся часть обрабатывают ручным перемещением суппорта.
Чистоту обработки определяют сравнением поверхности детали с эталонами чистоты 2 (рис. 43).
Особенности пользования лимбами. Подавая резец на глубину резания по лимбу поперечной подачи, следует иметь в виду, что он перемещается по радиусу к оси детали. Следовательно, диаметр последней после обтачивания уменьшается на величину, вдвое большую глубины резания. Например, если заготовку диаметром 30 мм надо обточить до диаметра 27 мм, т. е. уменьшить диаметр на 3 мм, то резец следует переместить поперечно на 1,5 мм.
Чтобы определить необходимый поворот лимба, следует разделить глубину резания на цену его деления.
Ценой деления называется величина перемещения резца, соответствующая повороту лимба на одно деление. Допустим, требуется подать резец на глубину резания 1,5 мм при цене деления лимба 0,05 мм. Число делений поворота лимба будет равно 1,5 : 0,05 = = 30.
Некоторые станки имеют лимбы поперечной подачи, цена деления которых указывается «на диаметр». В таком случае величину поворота лимба определяют делением разности диаметров заготовки до и после обтачивания на цену деления. Например, заготовка диаметром 25 мм обтачивается до диаметра 20 мм при цене деления лимба 0,05 на диаметр. Число делений, на которое потребуется повернуть лимб, будет равно (25—20): 0,05=100.
При пользовании лимбами необходимо учитывать наличие и величину люфта (зазора) в передачах движения суппорта. Если, например, выдвинутый вперед суппорт отводить назад, то при некоторой части оборота маховичка ручной подачи он будет стоять на месте. Это и характеризует величину люфта в передаче. Поэтому во время отсчетов размеров на станке маховичок ручной подачи необходимо плавно поворачивать только в одну сторону (рис. 44, а). Если допущена ошибка и лимб повернут на большее число делений, чем требуется, то маховичок поворачивают в обратную сторону на величину немного больше люфта (примерно 0,5—1 оборота), а затем, вращая в прежнем направлении, доводят лимб до нужного деления (рис. 44, б). Так же поступают, когда надо отвести резец от поверхности детали на определенный размер. Для этого суппорт отводят на величину, больше необходимой, а затем, подавая его к детали, доводят лимб до необходимого} деления.
Автор – nastia19071991
mgplm.org
1. Методы обработки наружных поверхностей вращения
Детали, имеющие форму тел вращения, можно разделить на валы, втулки и диски. Однако наиболее характерным видом деталей тел вращения, состоящих из сочетания наружных поверхностей (цилиндрических, конических, сложной формы), является вал. Валы могут быть изготовлены из проката, поковок, штампованных заготовок и отливок. По форме валы бывают: гладкие, ступенчатые, эксцентриковые, коленчатые. По размерам – мелкие (длиной до 200 мм), средние (длиной от 200 до 1000 мм) и крупные (длиной более 1000 мм). Перед механической обработкой заготовки валов (например, прокат) подвергают правке и резке на мерные заготовки и выполнению центровых отверстий.
Обработка наружных поверхностей вращения лезвийным инструментом
Обработку наружных поверхностей вращения лезвийным инструментом (точение) производят на станках токарной группы: токарно-винторезных, гидрокопировальных, токарно-револьверных, многорезцовых, токарно-карусельных, лоботокарных, одно- и многошпиндельных токарных полуавтоматах и автоматах.
Заготовки устанавливают в центрах станка или патронах различных типов: 3-кулачковых, самоцентрирующих, цанговых и др.Черновую обработку ступенчатых валов выполняют по разным вариантам (рис. 2). Схема с наименьшей продолжительностью обработки считается предпочтительной.
Удаляя припуск, исходят из соображений последовательного уменьшения жесткости вала, т.е. ступени меньшего диаметра обрабатывают в последнюю очередь. При черновом точении точность обработки достигает 14-го квалитета, а шероховатость Rz = 40…80 мкм).
|
Рис. 2. Схемы обтачивания ступенчатого вала: 1–4 – номера переходов; А, Б, В – ступени вала |
Получистовое точение обеспечивает точность обработки 9–12-го квалитета и шероховатость поверхности Rz = 10…20 мкм.
При получистовом точении обработку производят с глубиной резания t, равной 3–6 мм на сторону, продольной подачей S = 0,2–0,5 мм/об и скоростях резания от 100 до 140 м/мин (при обработке резцами, снабженными пластинами из твердого сплава типа Т15К6). В качестве СОЖ применяют эмульсию.
Чистовое точение обеспечивает точность обработки 7–8-го квалитета и шероховатость поверхности Ra = 1,25…2,5 мкм. При чистовом точении устанавливают глубину резания порядка 0,15–1,5 мм на сторону, продольную подачу от 0,05 до 0,15 мм/об и скорость резания порядка 150 м/мин (при работе резцами с пластинами из твердого сплава типа Т30К4, ВК2 или ВК3). В качестве СОЖ применяют эмульсию.
Тонкое (алмазное) точение – это отделочный метод обработки. При наружном точении алмазными (эльборовыми) резцами цветных сплавов достигается точность 5–6-го квалитета и шероховатость поверхности Ra = 0,16…0,32 мкм. Обработку производят на режимах: глубина резания t = 0,05…0,1 мм, продольная подача S = 0,01…0,03 мм/об, скорость резания V = 300…3000 м/мин. Алмазное точение, как правило, производят без применения СОЖ, так как при этом методе обработки смазочно-охлаждающей технологической средой (СОТС) является воздух. Для алмазного точения должны применяться станки особо высокой точности и жесткости.
В качестве инструмента при тонком точении сталей можно использовать широкие резцы, оснащенные пластинами из твердого сплава Т30К4, а для обработки чугунов – резцы с пластинками из твердого сплава ВК2 или ВК3. Передние и задние поверхности режущих пластин должны быть доведены до шероховатости поверхности Ra = 0,02…0,04 мкм.
Тонкое точение резцами с твердосплавными пластинами производят при глубине резания t = 0,05…0,15 мм, продольной подаче S = 0,01…0,05 мм/об и скорости резания V = 200…350 м/мин. При этом достигается точность 6–7-го квалитета и шероховатость поверхности Ra = 0,32…0,63 мкм. В качестве СОЖ обычно применяют эмульсию.
В табл.1 приведены значения экономической точности и шероховатости поверхности при точении и подрезке торцов деталей из разных материалов.
Таблица 1
Значения экономической точности и шероховатости поверхности при наружном точении и подрезке торцов
Вид обработки | Шероховатость поверхности, мкм | Точность (квалитет) | ||||
Неметаллические | Сплавы на основе Mg и Al | Латунь, бронза | Сталь | |||
Наруж-ное точение | Черновое | — | Rz = 40…80 | Rz = 40…80 | Rz = 40…80 | 12–14 |
Получистовое | — | Rz = 5…10 | Rz = 5…10 | Rz = 10…20 | 9–12 | |
Чистовое | Ra = 5…10 | Ra = 1,25 | Ra = 1,25 | Ra = 1,25…2,5 | 7–8 | |
Тонкое | — | Ra = 0,3 | Ra = 0,3 | Ra = 1,2…0,3 | 5–7 | |
Подрезка торцов | Черновая | — | Rz = 40…80 | Rz = 40…80 | Rz = 40…80 | 13–14 |
Получистовая | — | Rz = 10…20 | Rz = 10…20 | Rz = 10…20 | 11–12 | |
Чистовая | Ra = 2,5…10 | Ra = 1,2…2,5 | Ra = 1,2…2,5 | Ra = 1,2…2,5 | 7–9 | |
Тонкая | — | Ra = 0,6 | Ra= 0,6 | Ra = 0,6 | 6–7 |
При обработке длинных маложестких валов применяют неподвижные (рис.1,а) и подвижные люнеты (рис.1,б). Обрабатывая полые валы с контролируемой разностенностью стенки, используют кольцевые (вертлюжные) люнеты.
Люнеты служат дополнительной опорой, испытывающей нагрузки. Подвижный люнет, следуя за резцом, воспринимает силу резания. Обрабатываемая поверхность опирается на кулачки люнета. В тех случаях, когда следует обеспечить соосность обтачиваемой поверхности с ранее обработанной, кулачки люнета устанавливают впереди резца, то есть на ранее обработанную поверхность.
Рис. 3.2. Люнеты: а – с роликовыми опорами; б – подвижный люнет-виброгаситель
При скоростном резании кулачки создают значительное трение. Чтобы уменьшить трение, применяют люнеты с роликовыми опорами (см. рис. 3.2, а). При скоростном точении часто возникают вибрации, которые увеличивают шероховатость поверхности и снижают точность обработки. Для устранения вибраций используют люнеты с виброгасителем (см. рис.1,б). Тарельчатые пружины, помещенные в корпусе виброгасителя, поглощают вибрации детали.
При высоких скоростях резания стружка имеет сливную форму и сходит из-под резца непрерывной лентой. Такая стружка весьма опасна, так как может явиться причиной травматизма (порезов и (или) ожогов). Для размельчения такой стружки применяют специальные устройства – стружколоматели.
В массовом и крупносерийном производствах обработку валов часто производят на многорезцовых станках, которые имеют два суппорта – передний и задний. Передний суппорт служит для точения. Задний суппорт, совершающий поперечное движение, предназначен для подрезки торцов и прорезания канавок. Резцы настраивают так, чтобы обработка всех участков заканчивалась одновременно. Многорезцовое обтачивание выполняют тремя способами.
Первый способ – деление общего припуска по глубине. При этом способе припуск на одной из ступеней снимается последовательно несколькими резцами, и передний суппорт совершает путь L, равный сумме обрабатываемых ступеней L = l1 + l2 + l3 (рис. 2,а).
Второй способ – деление длины заготовки на несколько участков (рис. 3.3, б). Применяется, когда максимальный припуск может быть удален резцами за один проход. При такой схеме обработки длина хода резца l = L/n, где n – количество ступеней.
Рис. 2. Способы обработки ступенчатого вала на многорезцовом станке: а – способ деления припуска; б – способ деления длины обработки вала; в – способ деления длины максимальной ступени |
Третий способ – деление максимальной ступени вала (рис. 2, в). Более длинная ступень l1 протачивается несколькими резцами, установленными на одинаковую глубину съема.
Установка резцов производится либо по обработанной заготовке, либо по специальному эталону.
Многорезцовую обработку применяют, как правило, на предварительных операциях. Чистовое точение можно выполнять на гидрокопировальных станках 1708, 1Н713, 1Б732 и др., имеющих два суппорта, расположенных в вертикальной плоскости, что позволяет облегчить сход стружки из зоны резания. Точение по копиру осуществляется одним резцом, расположенным на верхнем суппорте. Подрезка торцов осуществляется резцами, расположенными в нижнем суппорте. Точение на многорезцовых станках осуществляется со скоростью резания 30–50 м/мин, а чистовое точение на гидрокопировальных станках – со скоростью резания 150–200 м/мин. В качестве СОЖ обычно применяют эмульсию.
В серийном и мелкосерийном производствах валы обрабатывают на станках с числовым программным управлением или ручным управлением.
В единичном производстве обработку валов обычно осуществляют на универсальном оборудовании с ручным управлением.
studfiles.net
Turning – grease monkey
The largest share in the processing of the external surfaces of the rotation processing has to Capstans group, which make up 25…50% of general machine-building plant machinery equipment.
The most common type of treatment of external surfaces of bodies of rotation on turning machines is Turning the longitudinal movement of the caliper with the cutting tool (rice. 107, α).
shaped Grinding, t. it is. complex configuration of surface treatment (spherical, stupenchatыh, etc. conical.), performed while moving the cutting tool in the longitudinal and transverse directions (rice. 107, б), and the processing shaped incisors. Shaped Turning on cam, whose contour corresponds to the contour of the workpiece (rice. 107, at), significantly simplifies the handling of workpieces.
tapping (rice. 107, g) It is also a very common operation. On modern lathes can cut metric, inch thread and other, as well as multiple threads of different profiles.
Turning consists of rough (roughing) and finishing operations. In some cases, also apply roughing and finishing (thin) processing. In roughing operations, associated with the removal of most of the allowance, get a rough surface with a roughness Rz = 40 m. Roughing turning improves the surface roughness to Rα = 6,3 m, This is achieved with a higher accuracy processing. When finishing operations the workpiece give final shape to within an accuracy of 8… 11-th Kvalitet, and surface roughness Rα= 1,6…6,3 m. Thin turning can replace grinding, It is, таким образом, finishing operation. It provides a machined surface roughness Rα = 0,4 m.
The simplest form of a shaped grinding is the treatment of the conical surface. The narrow conical surfaces, eg, chamfer, installing treated rectilinear cutting edge of the cutter at a predetermined angle. The cone can also handle when rotating at top slide caliper angle, equal to half the angle at the apex of the cone. When a small taper part can be treated transverse displacement of the tailstock. However, this method does not give high accuracy, since offset tailstock moves along with it and the workpiece, whereby the length projected on a plane, passing through the center line of the machine, distortion.
The large scale and mass production of a variety of widely used semi-automatic and automatic lathes. The main processing circuitry is on these machines:
- parallel – The processing of each product in each position participates several tools, concurrent, the beginning and end of individual tools do not necessarily reflect, but must, so that for some time the tools working simultaneously;
- consistent – In the processing of each product involves several tools, come into effect one after the other, the beginning of the next tool comes only after the end of the previous;
- parallel serial – In the processing of each product involved several groups of instruments, Group tools working in parallel, and the groups themselves instruments – series;
- rotatsionnaya – In the processing of each product involved one or a group of tools while the rotary motion of workpieces and tools, every detail is handled tools, which do not participate in the processing of other parts;
- continuous – In the processing of each product involved one or more instruments with the uninterrupted supply of billets.
Rotational and continuous processing schemes vary considerably among themselves: rotation schemes when there is a retraction and supply tools (возвратно-поступательное движение), machines in the continuous transport movement coincides with the filing of the motion. Under favorable conditions, a continuous contact of the tool machines the workpiece is supported all the time, It is impossible in rotary type machines.
On the basis of these signs of turning semi-automatic and automatic machines are divided into the following types: Moulding machines for cutting and veil-but-longitudinal turning, Turret lathe machines, single-spindle turning machines, CNC multi-spindle automatic and semi-automatic, automated copying machines.
Moulding-cutting machines designed for grinding of short shaped workpieces, threading thread, and drilling the central hole. Turning shaped surfaces and a segment of the rod blanks produced using 2…5 incisors, mounted on the cross slide. With longitudinal slide drilled hole and cut the thread. На рис. 108, α shows typical details, processed on the fitting-cutting machines, and Figure. 108, b – the technological details of the processing circuit pas machine, fitted with additional devices for centering, drilling and deployment.
Moulding-automatic lathes for longitudinal turning differ from those described above machines, that they grind the workpiece laterally moving cutters with longitudinal cutting feed processed rod. Longitudinal feed by moving the headstock. На рис. 109 shows typical details, processed on automatic-interlocking longitudinal turning.
Capstan and turret machines equipped with six-position turret with horizontal axis of rotation, perpendicular to the spindle axis, and three cross slides – front, the rear and the top.
На рис. 110, α shows typical details, processed on the lathe turret machines, and Figure. 110,6 – Technological scheme for the setting up of the machine part (caps) from bar material. instruments, established in the first three nests, reaming produced billet, whereupon tools, established in the 4th and 5th slots, Grinding is done on top and boring holes workpiece, and 6, 7 and 8th slots – the same, nadrezkoy with blanks. Then tools, established in the 9th and 10th slots, made in trimming the size of the final hole design, and cutter in the 11th slot – segment with support from lock, placed in the 12th slot. Movement of the turret and cross slide on the revolving machines controls the camshaft with fixed and interchangeable cams.
On revolving machines can produce turning of longitudinal and cross feed, tapping, as well as drilling holes and other operations.
Single-spindle lathes semi-automatic divided into the cartridge and pivot. Between them there are no sharp structural differences: pivot machines without any changes can be converted into a cartridge, and vice versa. In all variants of single-spindle semi-automatic machines have two or three slide, but when handling long items number of supports can be increased. Calipers have a cross, complex and longitudinal rectilinear or curvilinear movement.
In semiautomatic cartridge is sometimes treated with internal cones and recess, which are obtained by sequentially or simultaneously longitudinal and transverse movements of the cutting tool. On these machines handle parts with a diameter of 75 до 1000 mm.
The large scale and mass production of the most common single-spindle pivot semi mnogoreztsovy. Figure. 111 shows a semi-automatic model 1E713. Станина 1 Stanka – zhestkaya cast, in which the upper part at an angle of 35 ° to the vertical slide upper rails arranged 4, and at the bottom – the guides, which moves the lower caliper 8. The upper guide is also posted tailstock 5. headstock 2 mounted on the vertical frame plane. The left side of the drive cylinders tannins are located upper and lower supports. To clamp the workpiece 3 Spindle set pneumatic device management feeder. The tailstock has a tailstock 6, moved by means of a hydraulic cylinder, managed pedal 7. The lower caliper 8 gets a longitudinal movement of the hydraulic drive, located under the headstock, lateral movement of the upper part of the slide 8 (infeed) by means of a cone, mounted on a special carriage, mounted on the lower guide frame. The incisors are removed from the workpiece rulers “rebound”, placed under the copier. Upper saddle 4 similar to the lower, but has only one transverse operating displacement with the help of the copier, in the longitudinal direction of the insertion movement is performed only by the screw.
На рис. 112, α is a flow diagram of workpiece centering on semiautomatic. In longitudinal Holders (lower) caliper 1 has two through-cutter 2 and 6; incisor 2, A conical surface grind the workpiece, It operates the copier 7. The cross (top) supporte 4, having a radial feed, established shaped cutters 3 and 5.
На рис. 112, b shows a flow diagram of the processing of the outer ring of tapered roller bearing in the machine spindle chuck.
Turning many spindle automatic and semi-divided into horizontal with rotating or stationary workpiece and vertical continuous or sequential steps.
Horizontal multi-spindle semi-automatic rotating the workpiece are widespread in the industry, semi-automatic with a stationary workpiece and rotating tools are less common.
Vertical semi-automatic multi-spindle continuous (rotatsionnыe) intended for machining, installed in the centers or in fixed cartridges. At each position, except for the installation, They produce the same operation. In this way, Machine is a kind of multiple single-spindle semi-automatic vertical mnogoreztsovyh, spindles, which are placed on a rotating carousel. Loading spindles supports occurs when continuously rotating table, thus all calipers, except for the feed position located in the caliper, constantly continue work.
Multi-spindle vertical semi-automatic sequential steps, produced with six, eight or more spindles, primarily intended to work cartridge. На рис. 113 shows a general view shestishpindelny vertical lathe semiautomatic sequential steps. The carousel 1, periodically rotated by 60 °, placed vertical spindles with cartridges 2 for securing workpieces. The cartridges are rotated with the necessary speed, regardless of the carousel rotation. In the center of the table is placed hexagonal column 4, where there are five slides 3. They can be moved in the vertical and horizontal directions. In the five positions in the sequence of technological transitions simultaneously treated with five blanks, each, moving from one position to another, runs full loop.
At the end of the workpiece machining cycle is coming to the sixth position, t. it is. to the loading and unloading zone, where the spindle rotation stops, which makes it possible to remove the workpiece machined and installed in a new cartridge.
On multi-spindle semi-automatic machines can simultaneously handle two different workpiece or workpiece same on both sides. In this case, the two positions are the loading and unloading, and spindles via position switch (double indexing carousel).
На рис. 114 is a flow diagram of processing the workpiece on a vertical multi-spindle semi-automatic six-position. On the I position the finished part is removed a
tehnar.net.ua
Токарная обработка. Основные виды и способы
Здравствуйте друзья! Токарная обработка вот про, что поговорим мы сегодня. Данный вид обработки металлов это пожалуй самый распространенный метод получения цилиндрических поверхностей. Ну а теперь немного поподробней.
Токарная обработка.
Суть данного метода заключается в снятии металла (припуска) путем движения (подачи) режущего инструмента.Тоесть движение заготовки является вращательным, а режущего инструмента поступательным. Главное движение или попросту говоря скорость резания при токарной обработке совершает заготовка. Она вращается вокруг своей оси а резец описывает необходимый контур снимая металл. Про режимы резания мы поговорим подробнее в следующих постах. На токарных станках обрабатываются тела вращения такие как валы, втулки, фланцы, прутки, стаканы и различные фасонные поверхности такие ка галтели, сферы, конусы и др.
Основные виды токарной обработки.
На данном чертеже представлены основные виды токарной обработки. Давайте про них поговорим:
- а) Обтачивание цилиндрической поверхности. Происходит обтачивание наружной поверхности заготовки.
- б) Растачивание. Устанавливаем заготовку с предварительно обработанным отверстием и производим растачивание (увеличение внутреннего диаметра) с помощью расточного резца.
- в) Точение конической поверхности. Этот вид токарной обработки чем то похож на первый (а) только резец движется под углом образуя конусную поверхность.
- г) Токарная обработка фасонной поверхности. Режущий инструмент (фасонный резец) совершает поступательное движение в направлении перпендикулярно оси вращения детали
- д) Образование резьбы. С помощью резьбового резца наносим контур резьбы на обрабатываемую поверхность.
- е) Отрезание и точение канавок. Есть такие резцы которые называются отрезные. Врезаясь в тело заготовки мы можем как обрезать ее так и выточить канавку нужной нам глубины.
- ж) Подрезка торца. Если необходимо подрезать торец в детали подходит именно такой вид точения.
- з) Точение спиральных канавок. Данный метод хорош если вам необходимо прорезать спиральную канавку на торце детали. Для этого подача резца происходит в радиальном направлении.
Токарная обработка. Заключительная часть.
Ну вот наверно и все по данной теме. Вообще токарная обработка это довольно обширная тема и мы будет рассматривать все, что с ней связано постепенно. Поэтому, чтобы ничего не пропускать советую вам подписаться на обновления моего блога. Всем пока и до скорой встречи!!!
С вам был Андрей!
mextexnologii.ru
Токарная обработка наружных поверхностей – Энциклопедия по машиностроению XXL
Черновая токарная обработка наружных поверхностей и отверстия барабана [c.22]Чистовая токарная обработка наружных поверхностей ступиц [c.25]
Применение скоростного шлифования и алмазных роликов для правки шлифовальных кругов позволяет исключить токарную обработку наружной поверхности, заменив ее шлифованием на круглошлифовальных станках методом врезания. Скорость резания при этом составляет 60—80 м/с радиальная подача 5—10 мм/мин. [c.262]
Обработка поршней двигателей (табл. 13). Предварительная и чистовая токарная обработка наружных поверхностей поршня и предварительное точение канавок производятся на шестишпиндельных роторных токарных автоматах. Скорость резания до 300 м/мин подача при точении наружной цилиндрической поверхности 0,5 мм/об, при точении торца 0,4 мм/об. Обработка ведется твердосплавными резцами. [c.284]
В зависимости от конфигурации, размеров и заданной точности обрабатываемой детали применяют следующие способы токарной обработки наружных поверхностей [c.37]
В качестве примера рассмотрим технологический процесс восстановления гильз цилиндров двигателей СМД-14. Процесс содержит следующие операции мойку, очистку, дефектацию, токарную обработку наружной поверхности, термопластическое обжатие, очистку, обезжиривание поверхности, металлизацию посадочных поясков, шлифование посадочных поясков, расточку внутренней поверхности, протачивание бурта гильзы, чистовое и окончательное шлифование посадочных поясков, предварительное чистовое и окончательное хонингование внутренней поверхности, мойку, очистку, выходной контроль, консервацию и упаковку. Схема расположения технологического оборудования и оснастки на участке восстановления гильз цилиндров показана на рис. 83 перечень технологического обо- [c.428]
ТОКАРНАЯ ОБРАБОТКА НАРУЖНЫХ ПОВЕРХНОСТЕЙ [c.95]
При токарной обработке наружных поверхностей (обточка цилиндра и конуса, проточка канавок, подрезка торца и отрезание) применяются резцы, размеры поперечных сечений стержня которых приведены в табл. 3.1. Основные размеры токарных резцов из быстрорежущей стали (ГОСТ 18868-73, ГОСТ 18869-73, ГОСТ 18871-73, ГОСТ 18884-73, ГОСТ 22708-77… ГОСТ 22712-77), с пластинками из твердого сплава (ГОСТ 18877—73. .. ГОСТ 18882—73 ) и сборных с механическим креплением пластинок (ГОСТ 23075— 78, ГОСТ 23076—78) приведены в табл. 3.2 —3.5 размеры алмазных вставок (ГОСТ 13288—76, 13289—76) — в табл. 3.6. Формы заточки режущей части резцов указаны в табл. 3.7, передний и задний углы — в табл. 1.1, угол наклона главной режущей кромки — в табл. 1.2, главный угол в плане — в табл. 1.3, вспомогательный угол в плане — в табл. 1.4. Геометрия лезвия резца для обработки пластмасс будет приведена в табл. 3.8. [c.95]
Способы устранения брака при токарной обработке наружных поверхностей [c.152]
Л. СОЖ при токарной обработке наружных поверхностей [c.365]
Способы токарной обработки наружных поверхностей тел вращения [c.169]
ОБЩИЕ СВЕДЕНИЯ О ТОКАРНОЙ ОБРАБОТКЕ НАРУЖНЫХ ПОВЕРХНОСТЕЙ ВРАЩЕНИЯ [c.103]
Пример /.Разметка отверстия под цапфу на цилиндрической поверхности поршня (фиг. 204). Разметка эта ведется после чистовой токарной обработки наружной поверхности поршня. [c.221]
Пути повышения производительности труда при токарной обработке наружных поверхностей весьма разнообразны, и во мно- [c.147]
В условиях крупносерийного производства целесообразно получать заготовки шпинделей на горизонтально-ковочных машинах. При этом методе получения заготовки шпинделя коэффициент использования металла доходит до 0,5 при одновременном уменьшении трудоемкости токарной обработки наружных поверхностей шпинделя. [c.223]
Токарную обработку наружных поверхностей выполняют по двум вариантам [c.160]
На рис. 101, а и б показана схема многорезцовой обработки ступенчатого вала с поворотом детали. Токарную обработку наружных поверхностей вала можно выполнять по двум вариантам [c.195]
У полых валов глубокое сверление производится после предварительной токарной обработки наружных поверхностей, так как для выверки при установке заготовки на станке для глубокого сверления должны быть подготовлены базы. При расчете припуска на последующую обработку наружных поверхностей с базированием по отверстию необходимо учитывать увод оси отверстия при глубоком сверлении. [c.408]
Таким образом, черновая и чистовая токарная обработка наружных поверхностей конического колеса начинается на 3-й рабочей позиции станка и полностью заканчивается на 8-й рабочей позиции. [c.221]
При токарной обработке наружных поверхностей значения углов у и а могут изменяться в зависимости от положения режущей кромки относительно оси заготовки. Если резец установлен по оси заготовки (рис. 5.6), то значения углов а, р, у и б соответствуют значениям, полученным при заточке. При установке того же резца выше оси заготовки передний угол у увеличивается, а углы б и а уменьшаются при этом улучшаются условия резания, так как стружка легче сходит по передней поверхности, но незначительная перегрузка отжимает резец вниз и он внедряется в материал детали, что может вызвать выкрашивание режущей кромки или поломку резца. [c.66]
На линии выполняются следующие операции I — полная токарная обработка наружного кольца 2 — черновая токарная обработка внутреннего кольца 3 — чистовая токарная обработка внутреннего кольца 4 — клеймение 5 — магазины задела 5 и 7 — термическая обработка наружного и внутреннего колец 8 — визуальный контроль 9 — плоское шлифование наружного и внутреннего колец (поочередно) а — базового торца б — противоположной поверхности 10 — бесцентровое шлифование наружной поверхности наружного кольца 11 — черновое бесцентровое шлифование дорожки качения наружного кольца 12 — чистовое бесцентровое шлифование дорожки качения наружного кольца 13 — бесцентровая доводка дорожки качения наружного кольца 14 — снятие наката 15 — визуальный контроль 16 — промывка и сушка наружного кольца 17 — автома- [c.465]
Таким образом, рассмотренный вид обработки можно использовать для линейного и плоскостного упрочнения цилиндрических поверхностей деталей. При этом целесообразно вести упрочнение по схеме токарной обработки наружных цилиндрических поверхностей при согласовании продольной подачи и скорости вращения заготовки с подачей лазерных импульсов. [c.82]
Черновая токарная обработка наружных н внутренних поверхностей барабана [c.22]
В приведенном примере обработка наружной поверхности выполняется на токарных многошпиндельных роторных автоматах с последующим шлифованием на бесцентровых автоматах. Скорость резания при точении 120— 150 м/мин подача 0,3—0,5 мм/об. Скорость резания при шлифовании 35 м/с продольная подача 1500— 2000 мм/мин. [c.262]
Обработка колец шариковых подшипников (табл. 9 и 10). Наиболее распространенными являются подшипники с наружным диаметром 30—160 мм. Программы выпуска этих подшипников таковы, что делают автоматизацию их производства экономичной. В АЛ токарная обработка наружных и внутренних колец ведется на многошпиндельных токарных автоматах. В зависимости от конкретных условий различных заводов существует несколько практически равнозначных вариантов обработки колец одного и того же типа. В табл. 9 и 10 приведены варианты, осуществленные на АЛ, поставленных на подшипниковые заводы. В качестве режущего инструмента при токарной обработке широко используют как твердосплавный инструмент, так и инструмент из быстрорежущей стали. Твердосплавный инструмент используют преимущественно при обработке гладких цилиндрических и торцовых поверхностей, прямых фасок. Скорость резания при этом 100—150 м/мин подача до 0,6 мм/об. [c.262]
Обработка колец железнодорожных подшипников (табл. И и 12). Токарная обработка наружных и внутренних колец выполняется на одношпиндельных токарных гидрокопировальных автоматах резцами, оснащенными твердым сплавом. Скорость резания до 100 м/мин подача 0,2—0,8 мм/об в зависимости от вида обрабатываемых поверхностей и выполняемой операции. Особенностью токарной обработки наружных колец является чистовое точение трех торцов одновременно. Операция введена с целью обеспечения равномерного и минимального припуска при шлифовании этих торцов. [c.263]
Поступающий воздух двигает вправо поршень 4, а вместе с ним скобу 3, левый поршень 2 и золотник 5. Отработанный воздух выходит по каналам в направлении стрелки с. Таким образом, скоба будет совершать поступательное движение, пока не прекратится поступление сжатого воздуха. В процессе работы под нагрузкой пневмопривод дает от 1500 до 2000 ходов в минуту. Конструктивное оформление головки для обработки наружных поверхностей приведено на фиг. 81,6, из которой видно, что абразивный брусок 8 в кассете 7 крепится непосредственно на скобе пневмопривода. В процессе работы он прижимается к обрабатываемой поверхности пружиной 9. Вся головка своим хвостовиком крепится в суппорте или оправке токарного станка. [c.209]
На токарных станках с ЧПУ последовательность переходов обработки следующая а) предварительная (черновая) обработка основных участков поверхностей детали подрезка торцов, центрование перед сверлением отверстий диаметром до 20 мм, сверление (если используются два сверла, то вначале сверлом большего диаметра), рассверливание отверстий, точение (получистовая обработка) наружных поверхностей, а затем растачивание внутренних поверхностей б) обработка дополнительных участков поверхностей детали (кроме канавок для выхода шлифовального круга, резьбы и т. п.) в тех случаях, когда черновая и чистовая обработки внутренних поверхностей проводятся одним резцом, все дополнительные участки обрабатывают после чистовой обработки в) окончательная (чистовая) обработка основных участков поверхности детали, сначала внутренних, потом наружных г) обработка дополнительных участков поверхностей детали, не требующих черновой обработки сначала в отверстиях или на торцах, затем на наружной поверхности. [c.237]
Координаты 2 н Х я комплекты режущих инструментов для обработки наружных поверхностей деталей на центровых станках с ЧПУ токарной группы [c.246]
В случае токарной обработки наружной цилиндрической поверхности, очевидно, для всех составляющих звеньев при любых значениях /х,-. Кх. = 0. Перемещение 1у. совпадает с направлением действия составляющей силы резания Ру, поэтому оно может 82 [c.82]
Рассмотрим случай токарной обработки наружной цилиндрической поверхности при серийном или массовом изготовлении деталей средних размеров. [c.85]
Точение является основным способом обработки поверхностей тел вращения (см. рис. 31.2, а). Процесс резания осуществляется на токарных станках при вращении обрабатываемой заготовки (главное движение) и перемещении резца (движение подачи). С помощью точения выполняют операции обтачивание — обработку наружных поверхностей растачивание — обработку внутренних поверхностей подрезание — обработку торцевых поверхностей резку — разрезание заготовки на части резьбонарезание — нарезание резьбы. [c.585]
Станок предназначен для полной токарной обработки наружных, внутренних и торцовых поверхностей в патроне или центрах деталей типа тел вращения различного профиля. Обработка ведется в один или несколько рабочих проходов в замкнутом полуавтоматическом режиме. На станке можно нарезать крепежные резьбы. [c.83]
Припуски на токарную обработку наружных и торцовых поверхностей [c.111]
Использование режима диалога с ЭВМ для проектирования станочных операций обработки. Проектирование технологических процессов механической обработки связано с большим количеством трудноформализуемых логических действий. Особенно большие трудности возникают при проектировании станочных операций обработки деталей на многошпиндельном и многопозиционном оборудовании. Например, анализ инструментальной наладки токарно-револьверного автомата (рис. 3.10, а) показывает, что время обработки наружных поверхностей деталей больше, чем время обработки их внутренних поверхностей. Поиск оптимального варианта приводит к решению совместить переходы обработки поверхностей проходным и канавочиым резцами в один сложный инструментальный переход, выполняемый фасонным резцом (рис. 3.10,6). Принять такое решение технологу-проектировщику, работающему с ЭВМ в пакетном режи- [c.116]
Автоматическая линия МЕ436Л1А состоит из восьми шестишпиндельных токарных автоматов 4, объединенных транспортной системой. На автоматической линии выполняется одна технологическая операция — токарная обработка наружных и внутренних поверхностей гильзы со стороны узкого торца. С конвейера-загружателя / гильзы автоматически, по мере освобождения трассы транспортирования от гильз, направляются через приводной конвейер 2 на конвейер-распределитель 7. В случае переполнения конвейера-распределителя 7 гильзы направляются в магазин 3. При отсутствии гильз на конвейере 2 гильзы выдаются на конвейер-распределитель из магазина 5 магазин 3 таким образом регулирует равномерность поступления гильз. По командам токарных автоматов конвейер-распределитель 7 выдает гильзы на поперечные конвейеры 6, с которых гильзы с помощью загружателей 5 подаются в загрузочную зону токарных автоматов. Обработанные гильзы с помощью загружателей 5 опускаются и поступают на нижнюю ветвь поперечных приводных конвейеров 6, а затем на нижнюю отводящую ветвь конвейера-распределителя 7 и направляются через подъемник 9 в транспортную систему автоматической линии МЕ437Л1А. [c.114]
Автоматическая линия МЕ437Л1А состоит из восьми шестишпиндельных токарных автоматов 12, моечного автомата 15. На автоматической линии осуществляется токарная обработка наружных и внутренних поверхностей гильзы со стороны широкого торца и промывка гильзы от прилипшей стружки. Заготовки, поступившие из автоматической линии мод. МЕ4361Л1 А, направляются конвейером-распределителем 11 к токарным автоматам 12. При переполнении транспортера-распределителя 11 гильзы направляются в магазин 10 и выдаются из него при перерывах в поступлении гильз с автоматической линии МЕ436Л1А. Подача гильз к каждому токарному автомату 12 и отвод гильз осуществляется поперечным конвейером 14 и загружателем 13. После токарной обработки гильзы направляются конвейером-распределителем и и поперечным конвейером 18 в моечную машину 15. После промывки гильзы поступают на конвейер 16. С конвейера 16 гильзы вручную снимают и загружают в кассеты для отправки на операцию искусственного старения. После искусственного старения гильзы загружают на конвейер 17, далее они направляются конвейером 17 в магазин 19. [c.116]
Автоматическая линия МЕ439Л1 состоит из восьми шестишпиндельных токарных автоматов 20 и транспортной системы. На автоматической линии выполняется одна технологическая операция — чистовая токарная обработка наружных и внутренних поверхностей со стороны узкого торца. Из магазина 19 заготовки конвейером-распределителем 23 направляются на поперечные конвейеры 22 и загружате-лями 21 подаются к токарным автоматам 20. После токарной обработки гильзы по нижней отводящей трассе конвейера 23 направляются к подъемнику 24 и далее в транспортную систему автоматической линии МЕ440Л4. [c.116]
К токарным относится большая группа станков, предназначенных в основном для обработки поверхностей вращения, соосных оси шпинделя (цилиндрических, конических, фасонных, винтовых, а также торцовых). Для обработки наружных поверхностей деталей типа валов применяют как центровые, так и бесцентровые токарные станки. Концентрические поверхности деталей типа втулок и колец обрабатывают на токарно-центровых и патронных токарных станках. Детали типа дисков (со значительными по размеру торцовыми поверхностями) обрабатывают на лобото-карных станках, которые занимают меньшую площадь, чем центровые станки, и лучше приспособлены для обработки наружных и внутренних торцовых поверхностей детали. Лобо-токарные станки имеют устройства для поддержания постоянной скорости резания, а также устройства для нарезания торцовых резьб (спиралей). [c.224]
Комплекты режущих инструментов, используемые при обработке наружных поверхностей детали на станках с ЧПУ токарной группы, приведены в табл. 1 и 2. Участки поверхности детали, обрабатываемые этим инструментом, указаны в табл. 3. Комплект инструментов для станков 1723ФЗ, 1734ФЗ, [c.237]
Станок предназначен для токарной обработки наружных и внутренних поверхностей заготовок типа тел вращения со ступенчатым или криволинейным профилем, а также для нарезания резьб. Обработка происходит за один или несколько проходов в замкнутом полуавтоматическом цикле. Установка заготовок осуществляется в патроне, а длинномерных заготовок — в центрах. Станок разработан на базе токарного станка 16К20 и имеет традиционную для токарных станков компоновку. [c.80]
mash-xxl.info
Обработка на токарных станках
Обработка на токарных станках
Обтачивание наружных цилиндрических поверхностей выполняют проходными резцами с продольной подачей, гладкие валы, — при установке заготовки в центрах.
Центровые отверстия обрабатывают на токарных, револьверных, сверлильных и двусторонних центровальных станках. Для центрования применяют типовые наборы инструмента — комбинированные центровочные сверла, а также спиральные сверла и конические зенковки.
Центровые отверстия являются, как правило, установочными базами, и поэтому от точности их исполнения зависит и точность обработки остальных поверхностей заготовки.
В полые заготовки после подрезки торца и обработки отверстия с двух сторон вводят пробки или оправки с зацентрованными отверстиями или на кромке отверстия снимают конические фаски, используемые в качестве технологических баз с последующим удалением их при отделочной обработке.
Ступенчатые валы обтачивают по схемам деления припуска на части или деления длины заготовки на части. В первом случае обрабатывают заготовки с меньшей глубиной резания, однако общий путь резца получается большим и резко возрастает То.
Во втором случае припуск с каждой ступени срезается сразу за счет обработки заготовки с большой глубиной резания. При этом Т0 уменьшается, но требуется большая мощность привода станка.
Нежесткие валы рекомендуется обрабатывать упорными проходными резцами, с главным углом в плане j = 90°. При обработке заготовок валов такими резцами радиальная составляющая силы резания Ру = 0, что снижает деформацию заготовок.
Подрезание торцов заготовки выполняют перед обтачиванием наружных поверхностей. Торцы подрезают подрезными резцами с поперечной подачей к центру или от центра заготовки. При подрезании от центра к периферии поверхность торца получается менее шероховатой.
Обтачивание скруглений между ступенями валов – галтелей выполняют проходными резцами с закруглением между режущими кромками по соответствующему радиусу с продольной или поперечной подачей.
Точение канавок выполняют с поперечной подачей канавочными или фасонными резцами, у которых длина главной режущей кромки равна ширине протачиваемой канавки. Широкие канавки протачивают теми же резцами сначала с поперечной, а затем с продольной подачей.
Обработку отверстий в валах выполняют соответствующими инструментами, закрепляемыми в пиноли задней бабки. На рисунке слева показана схема сверления в заготовке цилиндрического отверстия.
Растачивание внутренних цилиндрических поверхностей выполняют расточными резцами, закрепленными в резцедержателе станка, с продольной подачей.
Гладкие сквозные отверстия растачивают проходными резцами; ступенчатые и глухие — упорными расточными резцами.
Отрезку обработанных деталей выполняют отрезными резцами с поперечной подачей. При отрезке детали резцом с прямой главной режущей кромкой (рисунок слева) разрушается образующаяся шейка и приходится дополнительно подрезать торец готовой детали.
При отрезке детали резцом с наклонной режущей кромкой (рисунок справа) торец получается чистым.
Обтачивание наружных конических поверхностей заготовок осуществляют на токарно-винторезных станках одним из следующих способов.
1. Широкими токарными резцами.
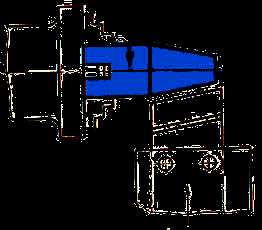
Обтачивают короткие конические поверхности с длиной образующей до 30 мм токарными проходными резцами. Обтачивают с поперечной или продольной подачей. Этот способ можно использовать при снятии фасок с обработанных цилиндрических поверхностей.
2. Поворотом каретки верхнего суппорта.
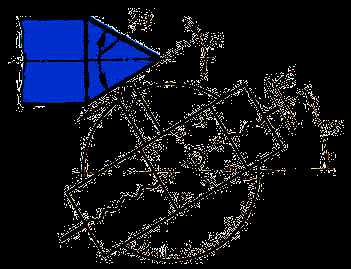
При обработке конических поверхностей каретку верхнего суппорта повертывают на угол, равный половине угла при вершине обрабатываемого конуса. Обрабатывают с ручной подачей верхнего суппорта под углом к линии центров станка (a). Таким способом обтачивают конические поверхности, длина образующей которых не превышает величины хода каретки верхнего суппорта. Угол конуса обтачиваемой поверхности любой.
3. Смещением корпуса задней бабки в поперечном направлении.
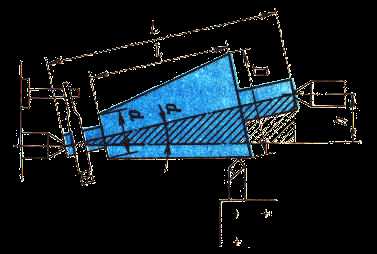
Обрабатываемую заготовку устанавливают на шариковые центры. Корпус задней бабки смещают относительно её основания в направлении, перпендикулярном к линии центров станка. При этом ось вращения заготовки располагается под углом к линии центров станка, а образующая конической поверхности — параллельно линии центров станка. Таким образом обтачивают длинные конические поверхности с небольшим углом конуса (2a < 8°) с продольной подачей резца.
4. С помощью конусной линейки.
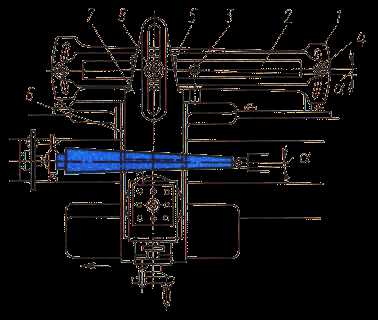
Коническую поверхность обтачивают с продольной подачей. Скорость продольной подачи складывается со скоростью поперечной подачи, получаемой от ползуна, скользящего по направляющей линейке. Сложение двух движений обеспечивает перемещение резца под углом к линии центров станка. Таким способом обтачивают длинные конические поверхности с углом при вершине конуса до 30—40°.
Обтачивание внутренних конических поверхностей выполняют так же как и наружных, но в основном используют специальные конические зенкеры или развёртки.
Обтачивание фасонных поверхностей с длиной образующей до 40 мм выполняют токарными фасонными резцами. Обтачивают только с поперечной подачей Sп.
Для обработки на токарно-винторезных станках применяют, как правило, стержневые, призматические или круглые фасонные резцы; резцами остальных видов обтачивают фасонные поверхности на токарных полуавтоматах и автоматах.
Длинные фасонные поверхности обрабатывают проходными резцами с продольной подачей с помощью фасонного копира, устанавливаемого вместо конусной линейки.
Нарезание резьбы на токарно-винторезных станках выполняют резцами, метчиками и плашками. Форма режущих кромок резцов определяется профилем и размерами поперечного сечения нарезаемых резьб. Резец устанавливают на станке по шаблону. Резьбу нарезают с продольной подачей резца Sпр. При нарезании резьбы продольный суппорт получает поступательное движение от ходового винта. Это необходимо для того, чтобы резец получал равномерное поступательное движение, что обеспечивает постоянство шага нарезаемой резьбы.
osntm.ru