Твердость hrb это – works.doklad.ru – Учебные материалы
alexxlab | 07.11.2019 | 0 | Вопросы и ответы
Сущность метода измерения по Роквеллу
Кто впервые предложил метод?
Впервые метод предложили уроженцы штата Коннектикут Хью М. Роквелл и Стэнли П. Роквелл в 1990 году в Швеции.
В чем заключается сущность метода Роквелла?
Сущность метода определения твердости по Роквеллу заключается во внедрении индентора в испытуемый образец, c измерением глубины отпечатка во время испытания.
- где:
- Рпр– предварительная нагрузка;
- Росн– основная нагрузка;
- h0 – глубина вдавливания индентора при предварительной нагрузки Рпр;
- h – глубина вдавливания индентора при основной нагрузки Росн;
Какой индентор используют для определения твердости по Роквеллу?
Для определения твердости используют твердосплавный шарик (диаметром 1,588 мм) или алмазный конус (120 градусов).
Как вычисляют твердость?
Твердость по Роквеллу (HR) вычисляют как разность между глубиной отпечатка при максимальных нагрузках и глубиной отпечатка при предварительной нагрузке.
Области применения по твердостям HRA, HRB и HRC?
Для измерения твердости по Роквеллу существуют 11 шкал, применяемых в зависимости от целевой задачи и отличающиеся друг от друга усилием и формой индентора. Наиболее распространенные шкалы – тип A, тип B и тип C.
Тип шкалы | Вид индентора | Усилие, кгс | Обозначение твердости | Область применения | |
---|---|---|---|---|---|
Pпр | Pпр+Pосн | ||||
A | Алмазный конус с углом при вершине 120° | 10 | 60 | HRA | Для особо твердых материалов: керамика, твердые и хрупкие материалы и покрытия, поверхности после химико-термической обработки |
B | Стальной закаленный шарик диаметром 1,588 мм | 10 | 100 | HRB | Для относительно мягких материалов: пластичные материалов, тонкой фольги и покрытий |
C | Алмазный конус с углом при вершине 120° | 10 | 150 | HRC | Твердые материалы после термической обработки |
По какой формуле рассчитывается твердость алмазным наконечником?
При определении твердости алмазным наконечником (120 градусов) по шкале A и C применяют формулу:
где H-h-разность глубин внедрения индентора (в мм) после снятия основной нагрузки и до ее приложения.
По какой формуле рассчитывается твердость закаленным стальным шаровым индентором?
При определении твердости закаленным стальным шаровым индентором (диаметром 1,588 мм) по шкале B:
metrotest.ru
Метод Роквелла
Метод Роквелла является методом проверки твёрдости материалов. Из-за своей простоты этот метод является наиболее распространённым и основан на проникновении твёрдого наконечника в материал и измерении глубины проникновения.
Шкалы твёрдости по Роквеллу
Существует 11 шкал определения твердости по методу Роквелла (A; B; C; D; E; F; G; H; K; N; T), основанных на комбинации «индентор (наконечник) — нагрузка». Наиболее широко используются два типа индентеров: шарик из карбида вольфрама диаметром 1/16 дюйма (1,5875 мм) или такой же шарик из закаленной стали и конический алмазный наконечник с углом при вершине 120°. Возможные нагрузки — 60, 100 и 150 кгс. Величина твёрдости определяется как относительная разница в глубине проникновения индентора при приложении основной и предварительной (10 кгс) нагрузки.
Для обозначения твёрдости, определённой по методу Роквелла, используется символ HR, к которому добавляется буква, указывающая на шкалу по которой проводились испытания (HRA, HRB, HRC).
Наиболее широко используемые шкалы твердости по Роквеллу
Шкала | Индентор | Нагрузка, кгс |
---|---|---|
А | Алмазный конус с углом 120° при вершине | 20 кгс |
В | Шарик диам. 1/16 дюйма из карбида вольфрама (или закаленной стали) | 100 кгс |
С | Алмазный конус с углом 120° при вершине | 150 кгс |
Формулы для определения твёрдости
Чем твёрже материал, тем меньше будет глубина проникновения наконечника в него. Чтобы при большей твёрдости материала не получалось большее число твёрдости по Роквеллу, вводят условную шкалу глубин, принимая за одно её деление глубину, равную 0.002 мм. При испытании алмазным конусом предельная глубина внедрения составляет 0.2 мм, или 0.2 / 0.002 = 100 делений, при испытании шариком — 0.26 мм, или 0.26 / 0.002 = 130 делений. Таким образом формулы для вычисления значения твёрдости будут выглядеть следующим образом:
- при измерении по шкале А (HRA) и С (HRC):
Разность представляет разность глубин погружения индентора (в миллиметрах) после снятия основной нагрузки и до её приложения (при предварительном нагружении). - при измерении по шкале B (HRB):
Проведение испытания
- Выбрать подходящую для проверяемого материала шкалу (А, В или С).
- Установить соответствующий индентор и нагрузку.
- Перед тем, как начать проверку, надо сделать два неучитываемых отпечатка, чтобы проверить правильность посадки наконечника и стола.
- Установить эталонный блок на столик прибора.
- Приложить предварительную нагрузку в 10 кгс, обнулить шкалу.
- Приложить основную нагрузку и дождаться до приложения максимального усилия.
- Снять нагрузку.
- Прочесть на циферблате по соответствующей шкале значение твёрдости (цифровой прибор показывает на экране значение твёрдости).
- Порядок действий при проверке твёрдости испытуемого образца такой же, как и на эталонном блоке. Допускается делать по одному измерению на образце при проверке массовой продукции.
Факторы, влияющие на точность измерения
- Важным фактором является толщина образца. Не допускается проверка образцов с толщиной менее десятикратной глубины проникновения наконечника.
- Ограничивается минимальное расстояние между отпечатками (3 диаметра между центрами ближайших отпечатков).
- Недопущение параллакса при считывании результатов с циферблата.
Сравнение шкал твёрдости
Простота метода Роквелла (главным образом, отсутствие необходимости измерять диаметр отпечатка) привела к его широкому применению в промышленности для проверки твёрдости. Также не требуется высокая чистота измеряемой поверхности (например, методы Бринелля и Виккерса включают замер отпечатка с помощью микроскопа и требуют полировку поверхности). К недостатку метода Роквелла относится меньшая точность по сравнению с методами Бринелля и Виккерса. Существует корреляция между значениями твёрдости, измеренной разными методами (см. рисунок — перевод единиц твёрдости HRB в твёрдость по методу Бринелля для алюминиевых сплавов). Зависимость носит нелинейный характер. Имеются нормативные документы, где приведено сравнение значений твёрдости, измеренной разными методами (например, ASTM E-140).

Оценка механических свойств по испытаниям на твёрдость
Связь между результатами проверки на твёрдость и прочностными характеристиками материалов исследовались такими учёными-материаловедами, как Н. Н. Давиденков, М. П. Марковец и др. Используются методы определения предела текучести по результатам проверки на твёрдость вдавливанием. Такая связь была найдена, например, для высокохромистых нержавеющих сталей после различных режимов термообработки. Среднее отклонение для конического алмазного индентора составляло всего +0,9%. Были проведены исследования по нахождению связи между значениями твёрдости и другими характеристиками, определяемыми при растяжении, такими как предел прочности (временное сопротивление), относительное сужение и истинное сопротивление разрушению.
tochpribor-nw.ru
Определение твердости по Роквеллу
Числа твердости по Роквеллу обозначают НR и вычисляют по формуле
где hо – глубина внедрения наконечника (мм) под действием предварительной нагрузки Р0 ; h – глубина внедрения наконечника (мм) под действием общей нагрузки Р после ее снятия и оставления предварительной нагрузки Р0 ; к – постоянная величина, равная для шарика 0,26 и для алмазного конуса 0,2 ; с – цена деления циферблата индикаторного прибора, соответствующая углублению наконечника на 0,002 мм.
Таким образом, твердость по Роквеллу не имеет размерности и выражается в условных единицах. На практике числа твердости по Роквеллу не вычисляют, а отсчитывают по шкале индикаторного прибора непосредственно в процессе испытания.
Значения твердости по Роквеллу могут быть переведены в значения твердости по Бринеллю (прил. 4). Прибор типа ТК-2 для определения твердости по Роквеллу приведен на рис. 11.
Порядок проведения испытаний :
Выбрать нагрузку и наконечник в зависимости от твердости испыты ваемого металла (прил. 3).
2. В конец шпинделя 1 закрепить оправку с выбранным индентором и установить необходимую нагрузку.
3. Подготовленный для испытания образец установить на стол 7 прибора.
4. Приложить предварительную нагрузку: вращением маховика 8 по часовой стрелке стол 7 поднимать до тех пор, пока малая стрелка индикатора не встанет против красной точки, а большая с погрешностью 5 делений – на нуль черной шкалы индикатора. Если отклонение будет больше чем 5 делений, необходимо вращением маховика против часовой стрелки опустить стол (снять предварительную нагрузку) и испытания провести вновь в другом месте образца.
5. Приложить общую нагрузку плавным нажатием руки на клавишу 10. После окончания вдавливания основная нагрузка автоматически снимается и
остается предварительная нагрузка. При этом большая стрелка индикатора перемещается по часовой стрелке и указывает на шкале число твердости. При испытании алмазным конусом отсчет ведут по черной шкале, а при испытании шариком – по красной.
6. Вращением маховика 8 против часовой стрелки опустить стол, образец передвинуть и повторить испытания. На каждом образце должно быть проведено не менее трех испытаний, за величину твердости принимается среднее арифметическое.
П р и м е ч а н и е. Независимо от того, что вдавливается в образец – конус или шарик, большая стрелка индикатора всегда совмещается с нулем черной шкалы (шкалы С ). С нулевым штрихом красной шкалы (шкалы В ) стрелку не совмещают.
studfiles.net
Метод Роквелла – это… Что такое Метод Роквелла?
Ме́тод Рокве́лла является методом проверки твёрдости материалов. Из-за своей простоты этот метод является наиболее распространённым и основан на проникновении твёрдого наконечника в материал и измерении глубины проникновения.
История
Измерение твёрдости по относительной глубине проникновения индентора было предложено в 1908 году венским профессором Людвигом (Ludwig) в книге «Die Kegelprobe» (дословно «испытание конусом»)[1]. Метод определения относительной глубины исключал ошибки, связанные с механическими несовершенствами системы, такими как люфты и поверхностные дефекты.
Твердомер Роквелла, машина для определения относительной глубины проникновения, был изобретен уроженцами штата Коннектикут Хью М. Роквеллом (1890—1957) и Стэнли П. Роквеллом (1886—1940). Потребность в этой машине была вызвана необходимостью быстрого определения эффектов термообработки на обоймах стальных подшипников. Метод Бринелля, изобретенный в 1900 году в Швеции, был медленным, не применимым для закалённых сталей, и оставлял слишком большой отпечаток, чтобы рассматриваться как неразрушающий.
Патентную заявку на новое устройство подали 15.07.1914, и, после ее рассмотрения, был выдан патент № 1294171 от 11.02.1919 [2].
Во время изобретения Хью и Стэнли Роквеллы (не прямые родственники) работали в компании New Departure Manufacturing (г. Бристоль, Коннектикут). New Departure, бывшая крупным производителем шарикоподшипников, в 1916 году стала частью United Motors, а, вскоре, корпорации General Motors.
После ухода из компании в Коннектикуте, Стэнли Роквелл переехал в г. Сиракьюс (штат Нью-Йорк), и 11.09.1919 подал заявку на усовершенствование первоначального изобретения, которая была утверждена 18.11.1924. Новый прибор имел патент № 1516207[3][4]. В 1921 году Роквелл переехал в Западный Хартфорд, Коннектикут, где сделал дополнительные усовершенствования[4].
В 1920 году Стэнли сотрудничал с производителем инструментов Чарльзом Вильсоном (Charles H. Wilson) из компании Wilson-Mauelen, с целью коммерциализации изобретения и разработки стандартизированных испытательных машин
Около 1923 года Стэнли основал фирму по термообработке Stanley P. Rockwell Company, которая всё еще существует в Хартфорде, шт. Коннектикут. Через несколько лет она, переименованная в Wilson Mechanical Instrument Company, сменила владельца. В 1993 году компанию приобрела корпорация Instron.
Шкалы твёрдости по Роквеллу
Существует 11 шкал определения твердости по методу Роквелла (A; B; C; D; E; F; G; H; K; N; T), основанных на комбинации «индентор (наконечник) — нагрузка»[6]. Наиболее широко используются два типа индентеров: шарик из карбида вольфрама диаметром 1/16 дюйма (1,5875 мм) или такой же шарик из закаленной стали и конический алмазный наконечник с углом при вершине 120°. Возможные нагрузки — 60, 100 и 150 кгс. Величина твёрдости определяется как относительная разница в глубине проникновения индентора при приложении основной и предварительной (10 кгс) нагрузки.
Для обозначения твёрдости, определённой по методу Роквелла, используется символ HR, к которому добавляется буква, указывающая на шкалу по которой проводились испытания (HRA, HRB, HRC).
Шкала | Индентор | Нагрузка, кгс |
---|---|---|
А | Алмазный конус с углом 120° при вершине | 60 кгс |
В | Шарик диам. 1/16 дюйма из карбида вольфрама (или закаленной стали) | 100 кгс |
С | Алмазный конус с углом 120° при вершине | 150 кгс |
Формулы для определения твёрдости
Чем твёрже материал, тем меньше будет глубина проникновения наконечника в него. Чтобы при большей твёрдости материала не получалось большее число твёрдости по Роквеллу, вводят условную шкалу глубин, принимая за одно её деление глубину, равную 0.002 мм. При испытании алмазным конусом предельная глубина внедрения составляет 0.2 мм, или 0.2 / 0.002 = 100 делений, при испытании шариком — 0.26 мм, или 0.26 / 0.002 = 130 делений. Таким образом формулы для вычисления значения твёрдости будут выглядеть следующим образом:
а) при измерении по шкале А (HRA) и С (HRC):
Разность представляет разность глубин погружения индентора (в миллиметрах) после снятия основной нагрузки и до её приложения (при предварительном нагружении).
б) при измерении по шкале B (HRB):
Проведение испытания
Циферблат прибора для проверки твёрдости по Роквеллу- Выбрать подходящую для проверяемого материала шкалу (А, В или С)
- Установить соответствующий индентор и нагрузку
- Перед тем, как начать проверку, надо сделать два неучитываемых отпечатка, чтобы проверить правильность посадки наконечника и стола
- Установить эталонный блок на столик прибора
- Приложить предварительную нагрузку в 10 кгс, обнулить шкалу
- Приложить основную нагрузку и дождаться до приложения максимального усилия
- Снять нагрузку
- Прочесть на циферблате по соответствующей шкале значение твёрдости (цифровой прибор показывает на экране значение твёрдости)
- Порядок действий при проверке твёрдости испытуемого образца такой же, как и на эталонном блоке. Допускается делать по одному измерению на образце при проверке массовой продукции
Факторы, влияющие на точность измерения
- Важным фактором является толщина образца. Не допускается проверка образцов с толщиной менее десятикратной глубины проникновения наконечника
- Ограничивается минимальное расстояние между отпечатками (3 диаметра между центрами ближайших отпечатков)
- Недопущение параллакса при считывании результатов с циферблата
Сравнение шкал твёрдости
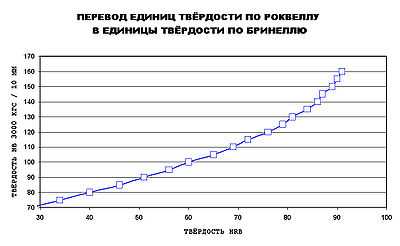
Простота метода Роквелла (главным образом, отсутствие необходимости измерять диаметр отпечатка) привела к его широкому применению в промышленности для проверки твёрдости. Также не требуется высокая чистота измеряемой поверхности (например, методы Бринелля и Виккерса включают замер отпечатка с помощью микроскопа и требуют полировку поверхности). К недостатку метода Роквелла относится меньшая точность по сравнению с методами Бринелля и Виккерса. Существует корреляция между значениями твёрдости, измеренной разными методами (см. рисунок — перевод единиц твёрдости HRB в твёрдость по методу Бринелля для алюминиевых сплавов). Зависимость носит нелинейный характер. Имеются нормативные документы, где приведено сравнение значений твёрдости, измеренной разными методами (например, ASTM E-140).
Оценка механических свойств по испытаниям на твёрдость
Связь между результатами проверки на твёрдость и прочностными характеристиками материалов исследовались такими учёными-материаловедами, как Н. Н. Давиденков, М. П. Марковец и др. Используются методы определения предела текучести по результатам проверки на твёрдость вдавливанием. Такая связь была найдена, например, для высокохромистых нержавеющих сталей после различных режимов термообработки. Среднее отклонение для конического алмазного индентора составляло всего +0,9 %. Были проведены исследования по нахождению связи между значениями твёрдости и другими характеристиками, определяемыми при растяжении, такими как предел прочности (временное сопротивление), относительное сужение и истинное сопротивление разрушению.
Ссылки
- ↑ G.L. Kehl, The Principles of Metallographic Laboratory Practice, 3rd Ed., McGraw-Hill Book Co., 1949, p 229.
- ↑ H.M. Rockwell & S.P. Rockwell, “Hardness-Tester, ” US Patent 1 294 171, Feb 1919.
- ↑ S.P. Rockwell, “The Testing of Metals for Hardness, Transactions of the American Society for Steel Treating, Vol. II, No. 11, Aug 1922, p 1013—1033.
- ↑ 1 2 S.P. Rockwell, “Hardness-Testing Machine, ” US Patent 1 516 207, Nov 1924.
- ↑ V.E. Lysaght, Indentation Hardness Testing, Reinhold Publishing Corp., 1949, p 57-62.
- ↑ ISO 6508-1:2005 Metallic materials. Rockwell hardness test. Part 1: Test method (scales A, B, C, D, E, F, G, H, K, N, T)
Список литературы
- Я. Б. Фридман. Механические свойства металлов. Изд. 3, в 2-х частях. М., «Машиностроение», 1974
- М. Л. Бернштейн, В.А Займовский. Механические свойства металлов. Изд. второе, М., «Металлургия», 1979.
Нормативные документы
- ГОСТ 9013-59 Металлы. Метод измерения твердости по Роквеллу
- Стандарт ISO 6508-1 : Metallic Materials — Rockwell Hardness Test
Part 1: Test Method (Scales A, B, C, D, E, F, G, H, K, N, T) - Стандарт ASTM E-18 Standard Methods for Rockwell Hardness and Rockwell Superficial Hardness of Metallic Materials
- Стандарт ASTM E-140 Standard Hardness Conversion Tables for Metals. Relationship Among Brinell Hardness, Vickers Hardness, Rockwell Hardness, Superficial Hardness, Knoop Hardness, and Scleroscope Hardness
См. также
dic.academic.ru
Твёрдость по Роквеллу Википедия
Цифровой прибор для измерения твёрдости по методу РоквеллаМе́тод Рокве́лла — метод неразрушающей проверки твёрдости материалов. Основан на измерении глубины проникновения твёрдого наконечника индентора в исследуемый материал при приложении одинаковой для каждой шкалы твердости нагрузкой, в зависимости от шкалы обычно 60, 100 и 150 кгс.
В качестве инденторов в методе применяются прочные шарики и алмазные конусы с углом при вершине 120° со скруглённым острым концом.
Из-за своей простоты, скорости по сравнению с другими методами и воспроизводимости результатов он является одним из наиболее распространённых методов испытаний материалов на твёрдость.
История
Измерение твёрдости по относительной глубине проникновения индентора было предложено в 1908 году венским профессором Людвигом (Ludwig) в книге «Die Kegelprobe» (дословно «испытание конусом»)[1].
Метод определения относительной глубины проникновения индентора, предложенный Хью и Стэнли Роквеллами, исключал ошибки, связанные с механическими несовершенствами измерительной системы, такими, как люфты и поверхностные дефекты и загрязнения испытуемых материалов и деталей.
Твердомер Роквелла, прибор для определения относительной глубины проникновения, был изобретён уроженцами штата Коннектикут Хью М. Роквеллом (1890—1957) и Стэнли П. Роквеллом (1886—1940). Потребность в этом устройстве была вызвана необходимостью оперативного определения результатов термообработки обойм стальных шарикоподшипников. Метод Бринелля, изобретённый в 1900 году в Швеции, был медленным, не применимым для закалённых сталей, и оставлял слишком большой отпечаток, чтобы считать этот метод методом неразрушающего контроля.
Патентную заявку на новое устройство они подали 15 июля 1914 года; после её рассмотрения был выдан патент № 1294171 от 11 февраля 1919 года[2].
Во время изобретения Хью и Стэнли Роквеллы (они не были прямыми родственниками) работали в компании New Departure Manufacturing (Бристоль, Коннектикут). New Departure, бывшая крупным производителем шарикоподшипников, в 1916 году стала частью United Motors, а затем — корпорации General Motors.
После ухода из компании в Коннектикуте, Стэнли Роквелл переехал в Сиракьюс (штат Нью-Йорк) и 11 сентября 1919 года подал заявку на усовершенствование первоначального изобретения, которая была утверждена 18 ноября 1924 года. Новый прибор был также запатентован под № 1516207[3][4]. В 1921 году Роквелл переехал в Западный Хартфорд, в Коннектикуте, где сделал дополнительные усовершенствования[4].
В 1920 году Стэнли Роквелл начал сотрудничество с производителем инструментов Чарльзом Вильсоном (Charles H. Wilson) из компании Wilson-Mauelen с целью коммерциализации изобретения и разработки стандартизированных испытательных машин[5].
Около 1923 года Стэнли Роквелл основал фирму по термообработке Stanley P. Rockwell Company, которая существует до сих пор в Хартфорде, в Коннектикуте. Через несколько лет она, переименованная в Wilson Mechanical Instrument Company, сменила владельца. В 1993 году компанию приобрела корпорация Instron.
Шкалы твёрдости по Роквеллу
Циферблат прибора для проверки твёрдости по РоквеллуСтандартами нормировано 11 шкал определения твердости по методу Роквелла (A; B; C; D; E; F; G; H; K; N; T), эти шкалы различаются типом индентора, испытательной нагрузкой и константами в формуле для вычисления твёрдости по результатам измерения[6].
Наиболее широко используются два три инденторов: сферический в виде шарика из карбида вольфрама или инструментальной закалённой стали диаметром 1/16 дюйма (1,5875 мм) или шарик диаметром 1/8 дюйма и конический алмазный наконечник с углом при скруглённой вершине 120°. Стандарты предусматривает в зависимости от шкалы 3 фиксированные нагрузки при вдавливании индентора — 60, 100 и 150 кгс.
Численная величина твёрдости определяется по формуле, коэффициенты в которой зависят от шкалы. Для снижения ошибки измерения от состояния испытуемой поверхности принимается относительная разница в глубине проникновения индентора при приложении основной и предварительной (10 кгс) нагрузки (см. рисунок).
Для обозначения твёрдости, определённой по методу Роквелла, используется сокращение HR, с 3-й буквой, указывающая на шкалу, по которой проводились испытания (HRA, HRB, HRC и т. д. до HRT). Например, HRC 64.
Шкала | Индентор | Нагрузка, кгс |
---|---|---|
А | Алмазный конус с углом 120° при вершине | 60 |
В | Шарик диаметром 1/16 дюйма из карбида вольфрама (или закалённой стали) | 100 |
С | Алмазный конус с углом 120° при вершине | 150 |
Формулы для определения твёрдости
Чем твёрже материал, тем меньше будет глубина проникновения наконечника в него. Чтобы при большей твёрдости материала не получалось меньшее число твёрдости по Роквеллу, твёрдость определяют по формуле:
- HR=N−H−hs{\displaystyle HR=N-{\frac {H-h}{s}}}
- где разность H−h{\displaystyle H-h} — относительная глубина проникновения индентора под предварительной и основной нагрузками в мм,
- N,{\displaystyle N,} s{\displaystyle s} — константы, зависящие от конкретной шкалы Роквелла (см. таблицу).
Таким образом, твердость по Роквеллу является безразмерной величиной.
Шкала | Сокращённое обозначение | Испытательная нагрузка | Тип индентора | Область применения | N | s |
---|---|---|---|---|---|---|
A | HRA | 60 кгс | 120° алмазный сфероконический* | Карбид вольфрама | 100 | 0,002 мм |
B | HRB | 100 кгс | Диаметр 1⁄16 дюйма (1,588 мм) стальной, сферический | Алюминиевые сплавы, бронза, мягкие стали | 130 | 0,002 мм |
C | HRC | 150 кгс | 120° алмазный, сфероконический | Твёрдые стали с HRB > 100 | 100 | 0,002 мм |
D | HRD | 100 кгс | 120° алмазный, сфероконический | 100 | 0,002 мм | |
E | HRE | 100 кгс | Диаметр 1⁄8 дюйма (3,175 мм) стальной, сферический | 130 | 0,002 мм | |
F | HRF | 60 кгс | Диаметр 1⁄16 дюйма (1,588 мм) стальной, сферический | 130 | 0,002 мм | |
G | HRG | 150 кгс | Диаметр 1⁄16 дюйма (1,588 мм) стальной, сферический | 130 | 0,002 мм | |
*Радиус сферического скругления вершины конуса 0,2 мм |
Методика проведения испытания промышленным твердомером Роквелла
Метод Роквелла.- Выбрать подходящую для проверяемого материала шкалу (А, В или С).
- Установить соответствующий индентор и нагрузку.
- Перед тем, окончательным измерение надо сделать два пробных, неучитываемых отпечатка, чтобы проверить правильность установки индентора и стола.
- Установить эталонный блок на столик прибора.
- Приложить предварительную нагрузку в 10 кгс, обнулить шкалу.
- Приложить основную нагрузку и дождаться достижения максимального усилия.
- Снять нагрузку.
- Прочесть на циферблате по соответствующей шкале значение твёрдости (цифровой прибор показывает на экране значение твёрдости).
- Порядок действий при проверке твёрдости испытуемого образца такой же, как и на эталонном блоке. Допускается делать по одному измерению на образце при проверке массовой продукции.
Факторы, влияющие на точность измерения
- Важным фактором является толщина образца. Не допускается проверка образцов с толщиной менее десятикратной глубины проникновения наконечника.
- Ограничивается минимальное расстояние между отпечатками (3 диаметра между центрами ближайших отпечатков).
- Параллакс при считывании результатов с циферблата стрелочных приборов.
Сравнение шкал твёрдости

Простота метода Роквелла (главным образом, отсутствие необходимости измерять диаметр отпечатка) привела к его широкому применению в промышленности для проверки твёрдости. Также не требуется высокая чистота измеряемой поверхности (например, методы Бринелля и Виккерса включают замер отпечатка с помощью микроскопа и требуют полировки поверхности).
К недостатку метода Роквелла относится меньшая точность по сравнению с методами Бринелля и Виккерса.
Существует корреляция между значениями твёрдости, измеренной разными методами (например, см. рисунок — перевод единиц твёрдости HRB в твёрдость по методу Бринелля для алюминиевых сплавов). Зависимость носит нелинейный характер. Существуют нормативные документы, где приведено сравнение значений твёрдости, измеренной разными методами (например, ASTM E-140).
Оценка механических свойств по испытаниям на твёрдость
Связь между результатами проверки на твёрдость по Роквеллу и прочностными характеристиками материалов исследовались такими учёными-материаловедами, как Н. Н. Давиденков, М. П. Марковец и др.
Используются методы определения предела текучести по результатам проверки на твёрдость вдавливанием. Такая связь была найдена, например, для высокохромистых нержавеющих сталей после различных режимов термообработки. Среднее отклонение результатов методов для конического алмазного индентора составляло всего +0,9 %.
Были также проведены исследования по нахождению связи между значениями твёрдости и другими прочностными характеристиками, определяемыми при растяжении, такими, как предел прочности (временное сопротивление), относительное сужение и истинное сопротивление разрушению.
См. также
Примечания
- ↑ Kehl G. L. The Principles of Metallographic Laboratory Practice, 3rd Ed., McGraw-Hill Book Co., 1949, p. 229.
- ↑ H. M. Rockwell & S. P. Rockwell Hardness-Tester, US Patent 1294171, Feb 1919.
- ↑ S. P. Rockwell The Testing of Metals for Hardness // Transactions of the American Society for Steel Treating, Vol. II, № 11, Aug 1922, p. 1013—1033.
- ↑ 1 2 S. P. Rockwell Hardness-Testing Machine, US Patent 1516207, Nov 1924.
- ↑ Lysaght V. E. Indentation Hardness Testing, Reinhold Publishing Corp., 1949, p. 57-62.
- ↑ ISO 6508-1:2005. Metallic materials. Rockwell hardness test. Part 1: Test method (scales A, B, C, D, E, F, G, H, K, N, T)
- ↑ Smith, William F. & Hashemi, Javad (2001), Foundations of Material Science and Engineering (4th ed.), McGraw-Hill, с. 229, ISBN 0-07-295358-6
Литература
- Фридман Я. Б. Механические свойства металлов. Изд. 3-е, в 2-х частях. — М.: «Машиностроение», 1974
- Бернштейн М. Л., Займовский В. А. Механические свойства металлов. Изд. 2-е. — М.: «Металлургия», 1979.
Нормативные документы
- ГОСТ 9013-59. Металлы. Метод измерения твердости по Роквеллу
- ISO 6508-1: Metallic Materials — Rockwell Hardness Test. Part 1: Test Method (Scales A, B, C, D, E, F, G, H, K, N, T)
- ASTM E-18 Standard Methods for Rockwell Hardness and Rockwell Superficial Hardness of Metallic Materials
- ASTM E-140 Standard Hardness Conversion Tables for Metals. Relationship Among Brinell Hardness, Vickers Hardness, Rockwell Hardness, Superficial Hardness, Knoop Hardness, and Scleroscope Hardness
wikiredia.ru
Измерение твердости металлов: методы Бринелля, Роквелла, Виккерса
Существует довольно большое количество различных механических характеристик металла, которые учитываются при производстве различных деталей. Многие из них зависят от химического состава материала, другие от особенностей эксплуатации. Измерение твердости металла проводится чаще других испытаний, так как это качество во многом определяет особенности эксплуатации материала. Рассмотрим особенности определения твердости подробнее.
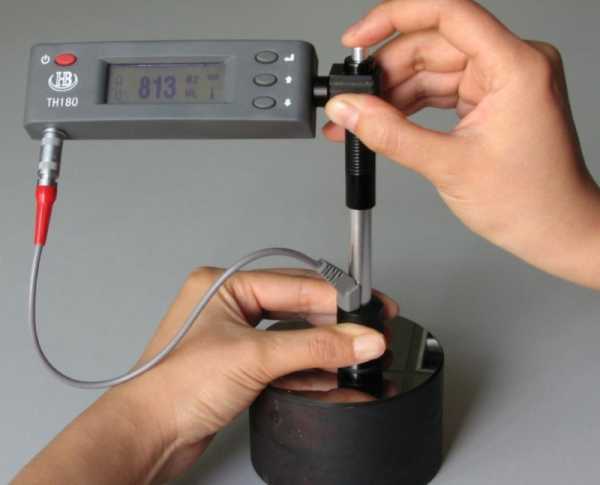
Понятие твердости
Твердость – свойство материалов, характеризующее способность проникновения одного, более твердого, тела в другое. Также эта характеристика определяет устойчивость к пластической деформации или разрушению поверхностных слоев при оказании сильного давления.
Измеряется показатель в самых различных единицах в зависимости от применяемого метода.
Все методы определения твердости материалов можно разделить на несколько основных групп:
- Статические. Подобные методы характеризуются тем, что нагрузка постепенно возрастает. Время выдержки может быть разным — все зависит от особенностей применяемого метода.
- Динамические характеризуются тем, что нагрузка на образец подается с определенной кинетической энергией. При этом показатель твердости является менее точным, так как при динамической нагрузке возникает определенная отдача из-за упругости материала. Результаты подобных испытаний зачастую называют твердостью материалов при ударе.
- Кинетические основаны на непрерывной регистрации показателей во время проведения испытаний, что позволяет получить не только конечный, но и промежуточный результат. Для этого применяется специальное оборудование.
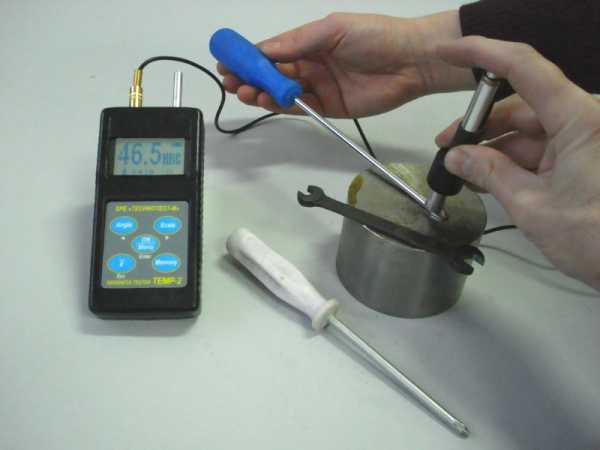
Измерение твердости инструмента
Кроме этого, классификация методов определения твердости проводится по принципу приложенной нагрузки. Выделяют следующие способы испытания образца:
- Вдавливание является на сегодняшний день наиболее распространенным способом определения рассматриваемого показателя.
- При отскоке проводится замер того, как высоко боек отлетит от поверхности испытуемого образца. В данном случае просчет твердости проводится по показателю сопротивления упругой деформации. Методы подобного типа довольно часто применяются для контроля качества прокатных валиков и изделий с большими размерами.
- Методы, основанные на царапании и резании, сегодня применяются крайне редко. Были они разработаны два столетия назад.
Как правило, в твердомерах есть деталь, которая оказывает воздействие на испытываемую заготовку. Примером можно назвать стальные шарики различного диаметра и алмазные наконечники с формой пирамиды. Некоторые из применяемых на сегодняшний день методов рассмотрим подробнее.
Измерение твердости по Бринеллю
Чаще всего проводится измерение твердости по Бринеллю. Этот метод регламентирован ГОСТ 9012. К особенностям испытания металлов и сплавов подобным методом можно отнести следующие моменты:
- В качестве тела, которое будет оказывать воздействие на испытуемый образец, используется стальной шарик.
- Для тестирования применяется шарик с определенным диаметром, который изготавливается из закаленной стали. К нему прилагается постоянно нарастающая нагрузка.
- Главным условие применения этого метода тестирования металлов и сплавов является то, что шарик должен изготавливается из более твердого материала, чем испытуемый образец.
- После завершения теста проводится измерение полученного отпечатка на поверхности.
- Данный способ позволяет получить данные, которые указываются в HB. Именно это обозначение сегодня встречается чаще других в различной справочной документации.
- Для удобства применения данного способа были созданы специальные таблицы, которые основаны на зависимости диаметрального размера шарика, твердости и полученного отпечатка.
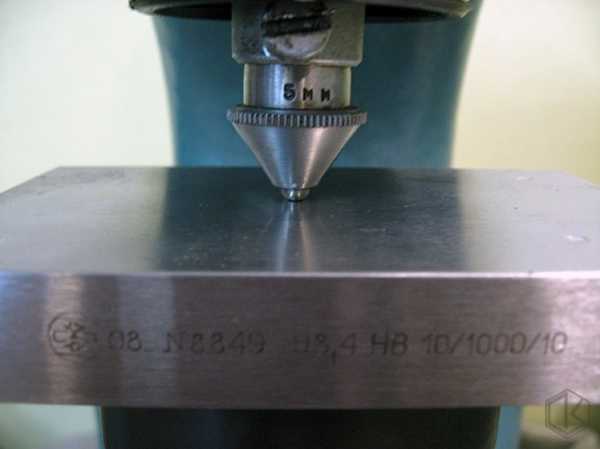
Измерение по методу Бринеллю
Стоит учитывать, что по Бринеллю не рекомендуется тестировать стали и сплавы, твердость которых превышает значение 450HB. Цветные металлы должны обладать показателем ниже 200 HB.
Измерение твердости по Виккерсу
Также выделяют метод измерения твердости по Виккерсу, который регламентирован ГОСТ 2999. Получил он распространение при определении твердости деталей и заготовок, который имеют небольшую толщину. Кроме этого, он может применяться для измерения твердости деталей, имеющих поверхностный твердый слой.
К особенностям этого способа тестирования образца можно отнести нижеприведенные моменты:
- Применяется так называемый алмазный наконечник, который имеет форму пирамиды с четырьмя гранями и равными сторонами.
- Выбирается определенное время выдержки.
- После того, как снимается нагрузка, проводится измерение размеров диагоналей получившегося отпечатка и вычисляется среднее арифметическое значение.
- Величина прилагаемой нагрузки регламентирована, может выбираться в зависимости от типа тестируемого материала.
- Полученные результаты в ходе проведения исследований обозначаются HV.
Метод Виккерса
В некоторых случаях после полученного значения указывается время выдержки и величина прилагаемой нагрузки, что позволяет с большей точностью определить значение твердости.
Измерение твердости по Роквеллу
Данный метод регламентируется ГОСТ 9013. Для его проведения используется специальный прибор для измерения твердости, который позволяет создать две последовательные нагрузки, прилагаемые к поверхности образца. К особенностям проведения подобного теста можно отнести:
- Сначала оказывается предварительная нагрузка, после чего добавляется вторая.
- После выдержки под общей нагрузкой в течении 3-5 секунд вторая снимается, проводится замер глубины отпечатка, затем снимается предварительная нагрузка.
- Измерение полученных данных проводится в условных единицах, которые равны осевому смещению индикатора на 0,002.
- Определяется число твердости по Роквеллу по специальной шкале прибора.
- Форма применяемого индикатора может существенно отличаться. Именно поэтому было введено несколько типов измерительных шкал, которые соответствуют определенной форме индикатора.
- Для обозначения полученной величины могут применяться обозначения HIRA, HRC, HRB. Они соответствуют форме применяемого индикатора и шкалы обозначения.
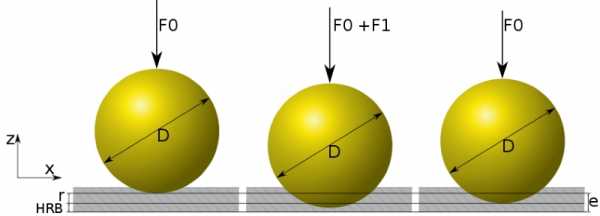
Принцип измерения твердости по Роквеллу
В качестве индикатора могут использоваться стальной шарик и два алмазных конуса различного размера. Этот метод измерения твердости закаленных деталей проводится только при применении алмазного конуса меньшего размера, предварительная оказываемая нагрузка составляет 10 кгс, основная 50 кгс. За счет предварительной нагрузки исключается вероятность того, что из-за упругости материала полученные значения будут менее точными. Кроме этого, предварительная нагрузка позволяет проводить измерение твердости металлов и сплавов, которые прошли предварительную термическую обработку.
Измерение твердости по Шору
Метод определения твердости по Шору применяется для тестирования прокатных валиков на момент их изготовления. Кроме этого, проверка рассматриваемого показателя может проводиться при эксплуатации валиков на прокатных станках, так как из-за оказываемого воздействия структура металла может изменяться, ухудшая эксплуатационные качества. Регламентирован метод Шора ГОСТ 23273.
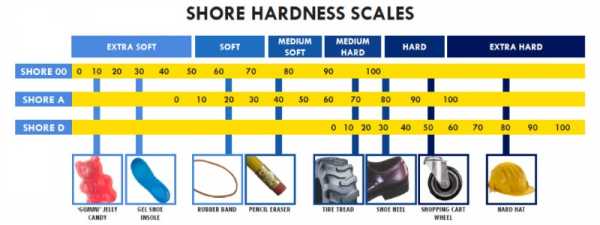
Шкала твердости по Шору
Рассматривая измерение твердости по Шору, следует отметить следующие моменты:
- В отличие от предыдущих способов, рассматриваемый основан на свободном падении алмазного индикатора на тестируемую поверхность с определенной высоты. Для тестирования применяется специальное оборудование, которое позволяет фиксировать точно высоту отскока.
- Масса применяемого бойка с алмазным наконечником составляет 36 грамм. Этот показатель важен, так как учитывается при проводимых расчетах.
- Твердость определяется по высоте отскока, измерение проводится в условных единицах. Падение образца на поверхность происходит с образованием небольшого углубления, а упругость приводит к обратному отскоку. Этот метод хорош тем, что позволяет проводить тестирование образцов, которые прошли предварительную термическую обработку. При постепенном вдавливании возникающая нагрузка может стать причиной деформирования используемого наконечника или шарика. В этом случае вероятность их деформации весьма мала.
- За 100 единиц твердости в этом случае принято считать высоту отскока 13,6 мм с возможностью небольшого отклонения в большую или меньшую сторону. Этот показатель можно получить при тестировании углеродистой стали, прошедшей процесс закалки. В качестве обозначения применяется аббревиатура HSD.
Сегодня этот способ измерения твердости применяется довольно редко из-за высокой погрешности и сложности замера высоты отскока байка от тестируемой поверхности.
Как ранее было отмечено, существует довольно большое количество методов измерения рассматриваемого показателя. Однако из-за сложности проведения тестов и большой погрешности многие уже не применяются.
В некоторых случаях проводится тестирование на микротвердость. Для измерения этого показателя прилагается статическая нагрузка к телу с формой пирамиды, и оно входит в испытуемые образец. Время выдержки может варьироваться в большом диапазоне. Показатель вычисляется примерно так же, как при методе Виккерса.
Соотношение значений твердости
При выборе метода измерения твердости поверхности следует учитывать, что между полученными данными нет никакой связи. Другими словами, выполнить точный перевод одной единицы измерения в другую нельзя. Применяемые таблицы зависимости не имеют физического смысла, так как они эмпирические. Отсутствие зависимости также можно связать с тем, что при тестировании применяется разная нагрузка, различные формы наконечников.
Существующие таблицы следует применять с большой осторожностью, так как они дают только приблизительные результаты. В некоторых случаях рассматриваемый перевод может оказаться весьма точным, что связано с близкими физико-механическими свойствами испытуемых металлов.
В заключение отметим, что значение твердости связано со многими другими механическими свойствами, к примеру, прочностью, упругостью и пластичностью. Поэтому для определения основных свойств металла довольно часто проводят измерение именно твердости. Однако прямой зависимости между всеми механическими свойствами металлов и сплавов нет, что следует учитывать при проведении измерений.
Если вы нашли ошибку, пожалуйста, выделите фрагмент текста и нажмите Ctrl+Enter.
stankiexpert.ru