Твердость меди по бринеллю – ГОСТ 9012-59 Металлы. Метод измерения твердости по Бринеллю
alexxlab | 05.09.2019 | 0 | Вопросы и ответы
Твердость по Бринеллю
Прибор Бринелля служит для определения твердости относительно мягких металлов и сплавов.
Испытание на твердость по Бринеллю производится вдавливанием в испытываемый образец стального шарика определенного диаметра под действием заданной нагрузки в течение определенного времени.
Испытание проводят на твердомере Бринелля − автоматический рычажной пресс, кинематическая схема которого показана на рис. 1.2.
В некоторых конструкциях давление осуществляется гидравлическим способом, а в других грузами, передвижение которых осуществляется электродвигателем.
Процесс измерения твердости состоит из следующих операций:
1. Подготовка прибора к испытанию, выключающаяся, в основном, в подборе необходимой нагрузки; шарика определенного диаметра и продолжительности вдавливания.
В качестве индентора используется стальной закаленный шарик стандартных размеров диаметром D 10 мм, 5 мм или 2,5 мм в зависимости от толщины изделия.
При испытании материала толщиной более 6 мм применяют шарик диаметром 10 мм, для материала толщиной от 6 мм до 3 мм − диаметром 5 мм; для материала толщиной менее 3 мм − диаметром 2,5 мм.
Рис. 1.2. Схема прибора для измерения твердости методом Бринелля:
1− Столик для центровки образца;2 − маховик; 3 − грузы; 4 − шарик; 5− электродвигатель
Нагрузка Р на шарик выбирается в зависимости от рода материала и должна быть пропорциональна квадрату диаметра шарика. Условные стандартные нормы, принятые для различных материалов, следующие:
− для стали и чугуна Р = 30D2,
− для меди и медных сплавов P = 10D2,
− для алюминия, баббитов, свинцовистых бронз и
других очень мягких металлов Р = 2,5D2.
Кроме того, нагрузка считается выбранной правильно, если выдерживается соотношение
0,2 D < d < 0,6 D (1.1)
Стандартными условиями являются D = 10 мм; Р = 3000 кгс; τ = 10 с. В этом случае твердость по Бринеллю обозначается НВ250, в других случаях указываются условия: НВ D/P/τ, НВ 5/250/30–80.
Более подробные сведения по выбору нагрузки, времени приложения нагрузки для различных материалов приводятся в соответствующей таблице в лаборатории испытания твердости.
2. Подготовка образца к испытанию, которая заключается в обработке его горизонтальной поверхности с нужной степенью чистоты.
Необходимо, чтобы поверхность испытываемого образца была ровной и гладкой, чтобы на ней не было окалины и других дефектов.
3. Вдавливание шарика в испытуемый образец, осуществляется автоматически.
Продолжительность выдержки:
− для стали и чугуна – 10 с,
− для латуни и бронзы – 30 с.
На рис. 1.3, а показан отпечаток от шарика.
4.Измерение диаметра отпечатка производится специальной лупой Бринелля или микроскопом-лупой (рис. 1.3, б). Она имеет шкалу, малое деление которой (или цена деления) равно 0,05 мм.
Полученный отпечаток измеряется в двух взаимно перпендикулярных направлениях и определяют как среднее арифметическое из двух измерений.
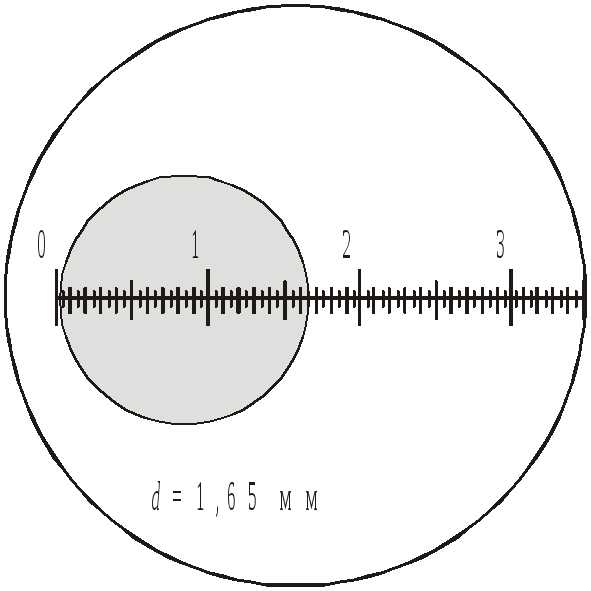
а) б) в) г) д)
Рис. 1.3. Лупа для замера отпечатка:
а– отпечаток шарика;б− внешний вид лупы;
в− правильное положение лупы при замере отпечатка;
г− неправильное положение лупы;д– отсчет по шкале
Лупу нижней опорной частью надо плотно установить на поверхность образца над отпечатком (рис. 1.3, в, г).
Поворачивая окуляр, надо добиться, чтобы края отпечатка были резко очерчены. Затем, передвигая лупу, надо один край отпечатка совместить с началом шкалы (рис. 1.3, д). Прочитать деление шкалы, с которым совпадает противоположный край отпечатка.
Твердость определяется как отношение приложенной нагрузки
(1.2)
где Р – приложенная нагрузка, кгс;
D – диаметр шарика, мм;
d – диаметр отпечатка, мм.
Число твердости по Бринеллю по ГОСТ 9012-59 записывают без единиц измерения. На практике при измерении твердости расчет по указанной выше формуле не производят, а используют заранее составленные таблицы, указывающие значение НВ в зависимости от диаметра отпечатки и выбранной нагрузки (см. приложение 1). Чем меньше диаметр отпечатка, тем выше твердость.
Способ измерения по Бринеллю не является универсальным. Его используют для материалов малой и средней твердости: сталей с твердостью < 450 НВ, цветных металлов с твердостью < 200 НВ и т. п.
Для них установлена корреляционная связь между временным сопротивлением (МПа) или пределом прочности σ в и числом твердости НВ по Бринеллю, которая может быть представлена эмпирической формулой:
σв = 10 С НВ [МПа], (1.3)
где С – коэффициент пропорциональности:
Для сталей С = 0,33-0,36
Для алюминия С = 0,4
Для меди С = 0,48
Для дуралюмина С = 0,37
Для латуни, бронзы С = 0,53
Следует отметить, что для хрупких материалов (чугун, силумин) надежной корреляции между твердостью и пределом прочности получить не удается. В частности, для определения предела прочности серого чугуна пользуются следующей эмпирической формулой:
[МПа]. (1.4)
В процессе вдавливания наряду с пластической деформацией измеряемого металла происходит также упругая деформация вдавливаемого шарика. Величина этой деформации, искажающей результаты определения, возрастает при измерении твердых материалов. Поэтому испытания вдавливанием шарика ограничивают измерением металлов небольшой и средней твердости (для стали с твердостью не более
studfiles.net
Определение твердости металлов по Бринеллю
На поверхности испытываемого образца металла напильником или абразивным материалом зачищают площадку размером 3-5 см2. Образец ставят на столик прибора (твердомер шариковый ТШ) и поднимают столик до соприкосновения со стальным шариком, который укреплен на шпинделе прибора. После этого нажимают на кнопку «Пуск». Груз опускается и вдавливает шарик в испытываемый образец. На поверхности металла образуется отпечаток, чем больше отпечаток, тем мягче металл. Диаметр отпечатка замеряют штангенциркулем.
Одинаковые результаты измерения твердости при различных размерах шариков получают только в том случае, если отношения усилия к квадратам диаметров шариков остаются постоянными. Исходя из этого, усилие на шарик необходимо подбирать по следующей формуле:
(3)
Значение Квыбирают в зависимости от металла и его твердости в соответствии с табл. 3.
Диаметр шарика Dи соответствующее усилиеF выбирают (приложение 4) таким образом, чтобы диаметр отпечатка находился в пределах:
(4)
Если отпечаток на образце получают меньше или больше допустимого значения d,то нужно увеличить или уменьшить усилиеF
Коэффициент К имеет различное значение для металлов разных групп по твердости. Численное же значение его должно обеспечивать выполнение требования, предъявляемого к размеру отпечатка (приложение 5). Толщина образца должна не менее, чем в 8 раз превышать глубину отпечатка.
По найденному диаметру отпечатка определяют, пользуясь таблицей или по формуле, значение числа твердости HB.
Между твердостью по Бринеллю (HB) и пределом прочности пластичных материалов существует следующая зависимость
,
гдеk – коэффициент пропорциональности: для стали с твердостью доHB 1750 k=0,34;сHB 1750 k=0,35; для отожженной меди, бронзы и латуниk=0,55;для алюминиевых сплавов– k=0,36-0,38.
Таблица 3. Рекомендуемые усилия при испытании твердости по Бринеллю (приложение 5)
Диаметр шарика D, мм | Прикладываемое усилие F, Н | ||||
30 | 10 | 5 | 2,5 | 1 | |
10 | 29420 | 9807 | 4903 | 2452 | 980,7 |
5 | 7355 | 2452 | 1226 | 612,9 | 245,2 |
2,5 | 1839 | 612,9 | 306,5 | 153,2 | 61,3 |
1 | 294,2 | 98,1 | 49,0 | 24,5 | 9,81 |
Диапазон твердости HB | 55 – 650 | 35 – 200 | <55 | 8 – 55 | 3 – 20 |
Измеряются | Сталь, чугун, медь и ее сплавы, легкие сплавы | Чугун, сплавы меди, легкие сплавы | Медь и ее сплавы, легкие сплавы | Легкие сплавы | Свинец, олово |
Значения твердости металлов по Бринеллю приведены в таблице 4.
Таблица 4. Твердость металлов по Бринеллю
Металл | НВ | Металл | НВ |
Титан | 160 | Алюминий | 16-25 |
Железо | 70-80 | Серебро | 25 |
Магний | 30-40 | Золото | 18 |
Медь | 40 | Олово | 5 |
Цинк | 33 | Свинец | 4 |
Данные замеров вносятв таблицу 5.
Таблица 5. Результаты определения твердости металлов по Бринеллю
Марка металла | D шарика, мм | F, H (кгс) | Диаметр отпечатка, мм | Среднее
арифметич. | HB (HBW) | |
studfiles.net
Определение твердости по Бринеллю
Лабораторная работа №1.
Определение твердости металлов и сплавов.
Цель работы: ознакомиться с приборами измерения твердости и методикой её определения на приборах Бринелля, Роквелла, Виккерса и ПМТ-3. Приобрести навыки измерения твердости сплавов на указанных приборах.
Оборудование: приборы Бринелля, Роквела, Виккерса и ПМТ-3. Объект исследования: образцы сталей, чугунов, цветных металлов после различной термической обработки.
Одним из методов испытания механических свойств металлов и сплавов является метод определения их твердости. Твердость – это свойство поверхностного свойства материала оказывающие сопротивление упругой и пластической деформации при местных контактных воздействиях со стороны другого более твердого тела. Известные методы определения твердости значительно отличаются друг от друга по форме применяемого индентора, условиям приложения нагрузки и способу расчета чисел твердости. Твердость можно измерять следующими способами:
1. Вдавливаемость наконечника.
2. Царапанием поверхности.
3. Отскакиванием наконечника-шарика (упругая отдача).
Твердость определенная царапанием, характеризует сопротивление разрушению (для большинства материалов путем среза).
Твердость определенная по отскоку, характеризует упругие свойства металла. Твердость, определенная вдавливанием в испытываемый материал индентора-наконечника, изготовленного из более твердого материала (закаленная сталь, алмаз, твердый сплав), показывает сопротивление пластической деформации.
Наиболее распространенным является метод вдавливания, при котором твердость определяют по следующему принципу:
o по величине поверхности отпечатка от вдавливания стального шарика при испытании на прессе типа Бринелля;
o по глубине отпечатка при вдавливании алмазного конуса или стального шарика на приборе типа Роквелла;
o по величине поверхности отпечатка от вдавливания алмазной пирамиды при испытании на приборах типа Виккерса, ПМТ-3.
Во всех методах испытания на твердость очень важно правильно подготовить поверхностный слой образца. Он должен характеризовать материал, твёрдость которого необходимо определить. Всe поверхностные дефекты должны быть удалены. Чем меньше глубина вдавливания индентора, тем выше необходимая чистота поверхности.
Нагрузка должна прилагаться по оси вдавливаемого индентора перпендикулярно к испытываемой поверхности, поэтому её плоскость должна быть строго параллельна опорной поверхности.
Определение твердости по Бринеллю
Методика определения твердости на приборе Бринелля состоит в том, что в испытываемый образец “А” (рис.2) под определенной нагрузкой Р вдавливается стальной закалённый шарик диаметром 2,5; 5; 10 мм.
Рис. 2. Схема испытания на твердость по способу Бринелля.
Образец устанавливается на столике шлифованной поверхностью кверху. Поворотом вручную маховика по часовой стрелке столик с образцом поднимают до упора. Далее включают электродвигатель. Он перемещает коромысло и постепенно нагружает шток. Нагрузка действует в течение определенного времени (10-60с), после чего двигатель автоматически отключается, нагрузка снимается. Поворотом маховика против часовой стрелки опускают столик прибора, образец освобождается. В образце остается отпечаток со сферической поверхностью (лункой).
Число твердости по Бринеллю характеризуется отношением нагрузки к поверхности отпечатка и обозначается НВ:
Н – начальная буква слова Hardness – твердость;
В – начальная буква названия метода определения твердости Brinell.
Твердость выражается через формулу:
, ;
где, Р – нагрузка на шарик, кгс\
F – поверхность отпечатка, мм;
Д -диаметр вдавливаемого шарика, мм;
d – диаметр отпечатка, мм.
Диаметр отпечатка измеряют специальной лупой, на окуляре которой нанесена шкала с делениями, соответствующими десятым долям миллиметра (рис.3).
Рис.3. Отсчет по шкале лупы. Шкала лупы.
Чем меньше диаметр отпечатка, тем выше твердость испытываемого металла.
На приборе Бринелля испытывать можно только те материалы, твердость которых не превышает 450 НВ, так как при большей твердости стальной шарик При вдавливании будет деформироваться, и искажать результат. Чтобы при вдавливании шарика не происходило продавливания материала, толщина образца должна быть не менее десятикратной глубины отпечатка. Поэтому способ Бринелля не позволяет измерять твердость тонкого поверхностного слоя менее -1 мм.
Диаметр шарика, нагрузка и длительность выдержки под нагрузкой устанавливаются в зависимости от испытываемого материала, его твердости и толщины (таблица 1):
Материал образца | Твердость НВ | Величина нагрузки | Д, мм | Нагрузка Р, кгс | Выдержка под нагрузкой, сек |
Стали, чугуны. | 140-250 | Р=30Д2 | 10 5 2,5 | 3000 750 187,5 | 10 10 10 |
Цветные сплавы, медь, латунь, бронза. | 35-150 | Р=10Д2 | 10 5 2,5 | 1000 250 62,5 | 30 30 30 |
Цветные сплавы, алюминий, подшипниковые сплавы. | 8-35 | Р=2,5Д2 | 10 5 2,5 | 250 62,5 15,6 | 60 60 60 |
Таблица 1.
studopedya.ru
Измерение твердости по Бринеллю
⇐ ПредыдущаяСтр 8 из 34Следующая ⇒
Измерение твердости по Бринеллю (ГОСТ 9012-73) заключается во вдавливании в испытываемый образец индентора в виде стального шарика определенного диаметра D под действием заданной нагрузки Р в течение определенного времени, получении отпечатка диаметром d и определении значения твердости НВ (Н – Harte, нем., твердость; В – Brinell, нем., Бринелль), как отношения приложенной нагрузки Р, (Н), к площади сферической поверхности (шарового сегмента) отпечатка F мм2 (рис.4.1):
Рис.4.1. Схема измерения твердости по Бринеллю
Рис.4.2. Общий вид прибора для измерения твердости по Бринеллю марки ТШ-1
Для измерения твердости по Бринеллю применяет специальные приборы (рис.4.2): прессы электромеханического и гидравлического действия. Например, пресс электромеханического действия марки ТШ-1 (Т – твердомер, Ш – шариковый индентор) состоит из нагружающего механизма и электродвигателя, расположенных в станине 1, сменных грузов 2, индентора 3 в виде шарика, столика 4, маховика 5, кнопки включения нагружения 6 и механизма установки времени выдержки под нагрузкой 7. В качестве индентора в зависимости от характера и толщины испытуемого материала используют закаленные шарики из стали типа ШХ15 диаметром 10; 5 и 2,5 мм, а нагрузку выбирают в зависимости от какова материала как
Р = K-D2, где К – постоянный для данного материала коэффициент, равный 294,3 Н/мм2 для стали, чугуна и высокопрочных сплавов; 98,1 и 24,5 Н/мм2 для сплавов на основе меди и алюминия. Время действия нагрузки находится в пределах 10-60 с. Для сравнения получаемых результатов испытаний стандартом регламентированы длительность нагружения и время выдержки под нагрузкой, так как некоторые металлы “текут” при ее действии в течение некоторого времени. Для характеристики условий измерения твердости приводят значение нагрузки, диаметр шарика и длительность нагружения.
Например, обозначение НВ 5/2450/30-2000 означает, что значение твердости 2000 МПа получено при измерении шариком диаметром 5 мм под нагрузкой 2450 Н в течение 30с. При использовании предпочтительной нагрузки 29430 Н, индентора в виде шарика 10 мм и длительности нагружения 10-15 с условия измерения твердости не указываются, например НВ 2800. Методом Бринелля испытывают материалы толщиной более 1-2 мм, имеющие твердость НВ не более 4500 МПа.
Перед измерением твердости для получения горизонтальной, ровной, гладкой, без окалины и других дефектов поверхности последняя должна быть обработана в зависимости от качества материала наждачным камнем, шлифовальной шкуркой или напильником. При этом как испытываемая, так и опорная поверхности образца должны быть плоскими и параллельными. Это повышает точность измерения твердости. При подготовке поверхности испытываемый образец не должен нагреваться выше 100°С.
При измерении твердости испытываемый образец помещают на столик 4 подготовленной поверхностью к индентору 3 (см. рис. 4.2). Вращая вручную маховик 5 по часовой стрелке до упора, поднимают столик 4 прибора, вдавливая тем самым шарик прибора в испытываемую поверхность и создавая предварительное нагружение в 981 Н, Нажатием кнопки 6 включают электродвигатель (о чем свидетельствует загорание сигнальной лампочки 8) и нагружающий механизм, вдавливающий шариковый индентор 3 под действием нагрузки 2 в испытываемую поверхность. После выдержки под нагрузкой 2 в течение заданного с помощью механизма 7 времени автоматически выключается электродвигатель сигнальная лампочка потухает), вращением маховика 5 вручную против часовой стрелки опускается столик 4 и с него снимается образец с отпечатком.
Диаметр отпечатка измеряют с помощью измерительного микроскопа или лупы (рис.4.3) в двух взаимно перпендикулярных направлениях, определяя его как среднее арифметическое из двух измерений.
Рис.4.3. Лупа для измерения отпечатков: а – общий вид; б – шкала лупы
Рис.4.4. Схема снятия отпечатка по шкале лупы
Лупа имеет шкалу (рис.4.3.6) с ценой деления 0,05 мм. При измерении диаметра отпечатка лупу нижней опорной частью необходимо плотно установить на испытываемую поверхность образца над отпечатком, обратив нижнюю часть лупы к свету и поворачивая окуляр, добиться чёткого изображения краев отпечатка. Затем передвигая лупу, надо один край отпечатка совместить с началом шкалы. Деление шкалы, совпадающее с противоположным краем отпечатка, и будет соответствовать диаметру отпечатка (на рис.4.4 диаметр отпечатка d = 4,80 мм).
Затем лупу или образец поворачивают на 90е, измеряют диаметр отпечатка второй раз и вычисляют среднее арифметическое значение диаметра отпечатка, по которому с помощью специальных таблиц определяют значение твердости НВ (табл.4.1). При измерении твердости необходимо соблюдать следующие условия:образец должен иметь толщину не меньше, чем 10-кратная глубина отпечатка; центр отпечатка должен быть удален от края образца не меньше, чем на 4d; центр отпечатка при повторных измерениях должен находиться от центра соседнего отпечатка на расстоянии не менее 2D. Для достоверного определения твердости необходимо выполнить массив измерений на нескольких образцах и статистически его обработать.
Опытным путем установлено, что между временным сопротивлением σв и твердостью НВ для пластичных материалов существует определенная зависимость. Например, для незакаленной стали σв = 0,36 НВ.
Метод Бринелля для определения твердости является весьма точным, но имеет ряд недостатков:
1. Ограниченность области применения. Не рекомендуется испытывать материалы, имеющие твердость больше 4 500, так как в этом случае шарик может деформироваться, что приведет к искажению результатов.
2. Невозможность определения твердости тонких изделий и поверхностного слоя металла. Толщина изделия должна быть не менее десятикратной глубины вдавливания.
3. Получение значительного отпечатка на изделии, что в ряде случаев недопустимо.
Таблица 4.1
Значения твердости по Бринеллю в зависимости от диаметра отпечатка
Рекомендуемые страницы:
lektsia.com
Твердость по Бринеллю ( гост 9012)
Испытание проводят на твердомере Бринелля (рис.7.1 а)
В качестве индентора используется стальной закаленный шарик диаметром D 2,5; 5; 10 мм, в зависимости от толщины изделия.
Нагрузка Р, в зависимости от диаметра шарика и измеряемой твердости: для термически обработанной стали и чугуна – , литой бронзы и латуни –, алюминия и других очень мягких металлов –.
Продолжительность выдержки: для стали и чугуна – 10 с, для латуни и бронзы – 30 с.
Полученный отпечаток измеряется в двух направлениях при помощи лупы Бринелля.
Твердость определяется как отношение приложенной нагрузки Р к сферической поверхности отпечатка F:
Стандартными условиями являются D = 10 мм; Р = 3000 кгс; = 10 с. В этом случае твердость по Бринеллю обозначается НВ 250, в других случаях указываются условия: НВ D / P /, НВ 5/ 250 /30 – 80.
Метод Роквелла гост 9013
Основан на вдавливании в поверхность наконечника под определенной нагрузкой (рис. 7.1 б)
Индентор для мягких материалов (до НВ 230) – стальной шарик диаметром 1/16” (1,6 мм), для более твердых материалов – конус алмазный.
Нагружение осуществляется в два этапа. Сначала прикладывается предварительная нагрузка (10 ктс) для плотного соприкосновения наконечника с образцом. Затем прикладывается основная нагрузка Р1, втечение некоторого времени действует общая рабочая нагрузка Р. После снятия основной нагрузки определяют значение твердости по глубине остаточного вдавливания наконечника h под нагрузкой.
В зависимости от природы материала используют три шкалы твердости (табл. 7.1)
Таблица 7.1.Шкалы для определения твердости по Роквеллу
Метод Виккерса
Твердость определяется по величине отпечатка (рис.7.1 в).
В качестве индентора используется алмазная четырехгранная пирамида.с углом при вершине 136o.
Твердость рассчитывается как отношение приложенной нагрузки P к площади поверхности отпечатка F:
Нагрузка Р составляет 5…100 кгс. Диагональ отпечатка d измеряется при помощи микроскопа, установленного на приборе.
Преимущество данного способа в том, что можно измерять твердость любых материалов, тонкие изделия, поверхностные слои.Высокая точность и чувствительность метода.
Способ микротвердости – для определения твердости отдельных структурных составляющих и фаз сплава, очень тонких поверхностных слоев (сотые доли миллиметра).
Аналогичен способу Виккерса. Индентор – пирамида меньших размеров, нагрузки при вдавливании Р составляют 5…500 гс
Метод царапания.
Алмазным конусом, пирамидой или шариком наносится царапина, которая является мерой. При нанесении царапин на другие материалы и сравнении их с мерой судят о твердости материала.
Можно нанести царапину шириной 10 мм под действием определенной нагрузки. Наблюдают за величиной нагрузки, которая дает эту ширину.
Динамический метод (по Шору)
Шарик бросают на поверхность с заданной высоты, он отскакивает на определенную величину. Чем больше величина отскока, тем тверже материал.
В результате проведения динамических испытаний на ударный изгиб специальных образцов с надрезом (ГОСТ 9454) оценивается вязкость материалов и устанавливается их склонность к переходу из вязкого состояния в хрупкое.
Вязкость – способность материала поглощать механическую энергию внешних сил за счет пластической деформации.
Является энергетической характеристикой материала, выражается в единицах работы Вязкость металлов и сплавов определяется их химическим составом, термической обработкой и другими внутренними факторами.
Также вязкость зависит от условий, в которых работает металл (температуры, скорости нагружения, наличия концентраторов напряжения).
studfiles.net