Виды дефектов сварных швов – .
alexxlab | 12.09.2019 | 0 | Вопросы и ответы
Дефекты сварных соединений, контроль сварочных швов и устранение недостатков
Сварка относится к числу основных процессов большинства машиностроительных производств. Кроме того, сварка часто применяется в быту для соединения металлических конструкций, поскольку имеет преимущества перед другими способами.
К плюсам метода стоит отнести:
- Обеспечивает лучшую герметичность при соединении трубопроводов, чем резьбовые соединения.
- Снижает материальные затраты на закупку метизов при изготовлении оград, лестниц и прочих металлических конструкций.
- Органично смотрится в составе сборных металлических изделий, поскольку качественно выполненный сварной шов всегда аккуратен. За счет этого сварка широко применяется при производстве высокохудожественных металлических конструкций, в том числе для соединения элементов, выполненных с помощью художественной ковки.
Но сварные швы не всегда бывают выполнены качественно. Это становится особенно заметно, если в сварке одного изделия вместе принимали участие мастер с большим производственным опытом и новичок. Профессионально выполненный шов при визуальном осмотре никогда не вызовет вопросов, в отличие от свисающих наплывов или непроваренных участков шва, сделанного новичком. А ведь это только внешняя картина. Важно и то, в каком состоянии находится металл внутри. От этого очень сильно зависит прочность сварного соединения и другие характеристики.
Рассмотрим дефекты, которые могут возникать в сварных швах, причины их возникновения, способы недопущения их появления, а также варианты устранения.
Причины возникновения дефектов
Есть два типа факторов, влияющих на качество сварочных работ:
Объективные — имеющие отношение к свойствам свариваемых материалов, поведению металлов в условиях, диктуемых технологическим процессом. Недаром одной из важных характеристик любого сплава является свариваемость. Иногда возникает необходимость сварить материалы с плохой свариваемостью. Такие задачи иногда ставятся в мелкосерийном или единичном производстве. Даже при полном соблюдении требований технологического процесса может сохраняться определенный процент брака, который приходится официально считать допустимым.
- Субъективные — зависящие от исполнителей. Причем к исполнителям следует относить не только рабочих, выполняющих сварку, но и технологов, которые несут ответственность за правильность параметров технологического процесса, верный выбор оборудования и режимов сварки.
Основными субъективными причинами возникновения дефектов сварочных швов являются:
- ошибки при подготовке свариваемых поверхностей;
- применение инструмента, отличного от указанного технологом;
- неисправность сварочного инструмента;
- малый опыт работы и низкая квалификация сварщика;
- отступление от требуемых режимов сварки.
Виды дефектов сварных швов
Дефекты сварных соединений принято делить на две группы:
- Внешние, наличие которых становится очевидным при осмотре шва невооруженным глазом.
- Внутренние, выявление которых требует применения специальных приборов контроля.
В некоторых источниках сквозные дефекты выделяют в отдельную группу, однако с научной точки зрения они относятся к внешним, поскольку выявляются при осмотре.
Внешние недостатки
Поскольку внешние дефекты являются видимыми, они связаны с нарушением геометрии шва и прилегающих участков материала. При ручной сварке в подавляющем большинстве случаев брак связан с низкой квалификацией сварщика или небрежностью при выполнении работ. Часто можно наблюдать ошибки в направлении электрода и его перемещении. При автоматической сварке брак может быть вызван работой на неисправном сварочном оборудовании.
Наиболее часто встречаются следующие виды внешних дефектов:
- Отклонение по ширине и высоте. В качестве основных причин возникновения обычно выступают плохая подготовка свариваемых кромок и неудовлетворительная их подгонка, неравномерное перемещение электрода, отступление от необходимых режимов. Данный дефект не только портит внешний вид изделия, но и снижает механические характеристики, ведь наплавленный металл остывает неравномерно, что может приводить к возникновению внутреннего напряжения и даже пластическим деформациям.
Наплывы. Являются основной проблемой многих новичков, недавно освоивших профессию сварщика. Возникают в процессе чрезмерного натекания металла электрода на стыкуемые поверхности без сплавления. Возникновению наплывов способствует наличие окалины на свариваемых элементах, что свидетельствует о плохой подготовке поверхностей. При недостаточной скорости перемещения электрода образуются излишки расплавленного металла, который затвердевает без соединения с основным материалом. Низкое напряжение дуги, длинная дуга, завышенный ток также могут стать причиной появления наплывов. Даже смещение электрода относительно оси выполняемого сварного шва может привести к этому распространенному дефекту. Стоит отметить, что наплывы не всегда влияют на механические свойства и герметичность соединения. Поэтому в отдельных случаях допускается эксплуатация сварных соединений с наплывами, если внешний вид изделия не имеет особой важности.
- Подрез — дефект, который можно считать противоположным наплыву. Представляет собой канавку по обе стороны от сварного шва. В результате происходит местное снижение толщины, отрицательно сказывающееся на прочностных характеристиках изделия. Подрез может возникать при завышении скорости сварки, большом напряжении. Если при выполнении углового шва между горизонтальной и вертикальной поверхностями сместить электрод выше оси шва, расплавленный металл будет интенсивно стекать вниз, а выше оси возникнет подрез.
- Непровар — еще один распространенный вид дефекта, возникающий чаще всего по вине неопытного сварщика. Непровар заключается в отсутствии сплавления между стыкуемыми элементами или между наплавленным металлом и основным материалом. При многослойной сварке возможно возникновение непровара между отдельными слоями. Основными причинами появления этого брака являются плохая подготовка поверхностей, наличие ржавчины или окалины, заниженный зазор между стыкуемыми поверхностями, завышенная скорость сварки, смещение электрода относительно выполняемого шва, заниженная сила тока. Непровар резко снижает прочность сварного соединения, а для герметичности часто является критичным.
- Незаплавленные углубления. Их называют кратерами. Представляют собой углубления, образующиеся обычно в местах резкого отрыва дуги. Могут сопровождаться усадочными рыхлостями, которые становятся причиной образования трещин.
Наружные трещины. Могут располагаться как продольно, так и поперечно. Образуются не только в наплавленном, но и в основном металле. В последнем случае они располагаются в зоне термического влияния сварки, то есть близко к шву. Причиной образования трещин могут стать напряжения, возникающие при неравномерном нагреве и охлаждении. Наличие пор и непроваров может спровоцировать возникновение трещин.
- Прожог — сквозное проплавление, сопровождающееся вытеканием жидкого металла с изнаночной стороны выполняемого шва. Возникают прожоги обычно ввиду больших значений тока, увеличенного зазора между стыкуемыми кромками или плохой их подгонки, низкой скорости перемещения электрода.
Внутренние дефекты
Наличие в сварном шве внутренних дефектов не всегда является очевидным. Скрытый брак особенно опасен, поэтому все сварные соединения должны подвергаться тщательному контролю.
Рассмотрим основные виды внутренних дефектов:
- Поры. Появляются при поглощении расплавленным металлом водорода, окиси углерода и других газов, которые не успели выделиться на поверхность металла при его застывании. Поры представляют собой пузырьки, заполненные газом. Обычно возникают при неправильно подобранных электродах или их хранении во влажной среде, наличии в месте стыковки ржавчины или окалины.
- Окислы и включения шлака. Образуются при чрезмерно длинной дуге. Существенно снижают прочностные характеристики шва. В ответственных конструкциях допускаются лишь единичные включения.
- Непровар корня или кромки шва. По своей сути сходен с внешним непроваром, но визуально незаметен, так как находится в толще металла.
- Внутренние трещины. Механизм появления аналогичен возникновению наружных трещин.
- Перегрев. Суть дефекта — в крупнозернистом строении. Крупные зерна имеют меньшую поверхность сцепления между собой, вследствие этого снижаются прочность и пластичность. Иногда этот дефект поддается исправлению термообработкой.
- Пережог — появление окисленных зерен, сцепление которых между собой существенно ослабевает, что резко увеличивает хрупкость. Пережог, в отличие от перегрева, является неисправимым браком.
Методы контроля
Для предупреждения появления дефектов должен проводиться систематический контроль на всех этапах производства: до, в процессе сварки, и после окончания.
- Перед сваркой проверяется подготовка стыкуемых поверхностей, их геометрия.
- В процессе — тщательно контролируется соблюдение всех параметров технологического процесса, в том числе режимов сварки.
- После сварки следует контроль готового изделия.
Основные способы выявления дефектов сварных швов:
- Визуальный осмотр и проверка геометрии. Предполагается использование лупы для обнаружения мелких поверхностных трещин и пор. Участок металла зачищается наждачной бумагой и протравливается раствором азотной кислоты. Образуется матовая поверхность, на которой трещины более заметны. После осмотра остатки кислоты удаляют.
Испытание механических свойств. Вместе с изделием производят сварку образцов, которые направляют в лабораторию для определения временного сопротивления, относительного удлинения, ударной вязкости.
- Контроль макроструктуры. Проводится на образцах, прошедших шлифовку и протравливание.
- Контроль микроструктуры. Проводят на образцах с применением микроскопа. Данный метод исследования позволяет обнаружить пережог, окислы границ зерен, изменение структуры металла, микротрещины.
- Гидравлические и пневматические испытания. Применяются для контроля сосудов и трубопроводов.
- Рентгеновский контроль. Просвечивание рентгеновскими лучами позволяет выявить поры, непровары, трещины, шлаковые включения.
- Ультразвуковой контроль. Производится с помощью ультразвукового дефектоскопа. Высокочастотные колебания проникают в металл и отражаются от трещин, пор и других дефектов.
- Контроль на наличие межкристаллитной коррозии. Проводят только для изделий, подвергающихся воздействию агрессивных сред.
Способы устранения дефектов
Зачастую выявленные дефекты сварочных швов не подлежат устранению и ведут к браковке изделия. Разумеется, никто не будет выбрасывать секцию ограды с наплывами, но для ответственных деталей контроль всегда необходим жесткий.
Некоторые дефекты вполне можно устранить:
- Наплывы удаляют механическим путем с применением абразивного инструмента.
- Крупные трещины подлежат заварке. Место появления трещины засверливается и зачищается с помощью абразива.
- Мелкие трещины и непровары ликвидировать сложнее. Обычно требуется полное разрушение выполненного шва, новая тщательная зачистка и повторная сварка.
- Подрезы устраняют наваркой тонких слоев металла.
- Перегрев возможно устранить при определенных режимах термической обработки.
После устранения всех недостатков деталь подлежит повторному, еще более тщательному контролю, который позволит удостовериться, что дефекты отсутствуют. В случае повторного обнаружения недостатков допускается произвести дополнительные исправления. Однако повторять такие процедуры можно не более трех раз, иначе высока вероятность резкого снижения механических свойств материала.
Зачастую трудно выполнить сварку совсем без дефектов. Однако постоянная практика и неукоснительное соблюдение технологии позволят свести их количество к минимуму. А знание теоретической базы поможет правильного организовать технологический процесс с целью получения изделий высокого качества.
tokar.guru
Виды дефектов сварных швов и методы их устранения
Что такое дефекты сварных швов?
Дефекты бывают нескольких видов – наружные и внутренние. Наружными являются дефекты, которые можно обнаружить визуально при осмотре сварочного шва.
Внутренние дефекты, наоборот, находятся внутри сварочных соединений и их можно увидеть лишь после дефектоскопии, включая рентген и механическую обработку.
Дефекты бывают допустимыми и не допустимыми, в зависимости от требований, предъявляемых к сварочным соединениям и конструкции в целом.
Однако, исходя из самого определения, любые дефекты являются дефектами и требуют их полного устранения либо сведения к минимуму их количества и размеров.
Так как дефекты сварных швов являются причиной, в результате которой есть риск поставить под угрозу стабильность соединения и функциональность сварной конструкции, есть ряд операций, чтобы их устранить. Чтобы свести к минимуму вероятность появления дефектов следует обязательно учитывать:
- 1) Технологию сварки и квалификацию сварщика
- 2) Присадочный материал и свариваемый металл
- 3) Подготовку поверхности под сварку и защитный газ
- 4) Режимы и применяемое сварочное оборудование
Наружные дефекты
К наружным дефектам относятся нарушения геометрических размеров (подрезы, наплывы), непровары и прожоги, незаваренные кратеры.
Основной причиной непроваров является недостаточный сварочный ток, так как он в большей степени влияет на проникновение в металл.
Устранение дефектов этого вида обычно происходит путем повышения мощности сварочной дуги, уменьшением длины дуги и увеличением её динамики.
Также причиной непроваров может быть большая скорость сварки или недостаточная подготовка кромок сварного соединения.
Непровары могут быть нескольких видов:
- – когда сварочный шов проникает не на всю толщину металла при односторонней сварке (см. верхнюю часть на рисунке)
- – при двусторонней сварке встык швы не стыкуются друг с другом, образуя несплавление между собой (см. нижнюю часть на рисунке)
- – при сварке в тавр сварочный шов не проникает вглубь, а лишь цепляется за свариваемые кромки
Также причиной непроваров может быть большая скорость сварки или недостаточная подготовка кромок сварного соединения.
Подрезом называется дефект в виде канавки в основном металле по краям сварочного шва.
Это наиболее распространенный дефект при сварке тавровых или нахлесточных соединений, но может также возникнуть и при сварке стыковых соединений. Этот вид дефекта обычно вызван неправильно подобранными параметрами, особенно скоростью сварки и напряжением на дуге.
При угловой сварке (например при сварке длинных швов при сварке балок) подрезы часто возникают из за того, что сварочная дуга направлена больше на вертикальную поверхность.
Расплавленный металл стекает на нижнюю кромку и его не хватает для заполнения канавки.
При слишком высокой скорости сварки и повышенном напряжении, сварной шов образуется «горбатым». Из-за быстрого затвердевания сварочной ванны, в этом случае также образуются подрезы. Уменьшение скорости сварки постепенно сокращает размер подреза и в конечном итоге устраняет этот дефект.
На подрезы влияет также длина сварочной дуги. При слишком длинной сварочной дуге ширина шва увеличивается, тем самым увеличивая количество расплавленного основного металла. Так как при увеличении длины дуги тепловложение остается прежним, его не хватает на весь сварочный шов, кромки быстро остывают, образуя подрезы. Уменьшение длины дуги не только избавляет от подрезов, но и увеличивает проплавление и устраняет такие дефекты, как непровар.
Данный дефект появляется в результате натекания присадочного материала на основной металл без образования сплавления с ним. Обычно причиной этого дефекта является неправильно подобранные режимы сварки и окалина на свариваемой поверхности. Подбор правильного режима (соответствие сварочного тока со скоростью подачи присадочного материала, повышение напряжения на дуге) и предварительная очистка кромок устраняют появления наплывов.
Данный дефект – отверстие насквозь в сварочном шве. В основном причинами прожога являются большой ток, медленная скорость сварки или большой зазор между кромками сварного соединения. В результате происходит прожог металла и утечка сварочной ванны.
Понижение сварочного тока, увеличение скорости сварки и соответствующая подготовка геометрии кромок позволяют устранить прожоги. Прожоги являются очень частым дефектом при сварке алюминия, из его низкой температуры плавления и высокой теплопроводности.
Кратер появляется в конце сварочного шва в результате резкого обрыва дуги. Выглядит он в виде воронки в середине сварочного шва при его окончании. Современное сварочное оборудование имеет специальные программы для заварки кратера. Они позволяют проводить окончание сварки на пониженных токах, в результате чего кратер заваривается.
Внутренние дефекты
К внутренним основным дефектам сварных швов относят трещины (холодные и горячие) и поры.
- Горячие трещины
Горячие трещины появляются в то время, когда металл сварного шва находится в состоянии между температурами его плавления и затвердевания. Они могут быть в двух направлениях – вдоль и поперек сварного шва. Горячие трещины обычно являются результатом использования неправильного присадочного материала (в частности, алюминиевых и CrNi сплавов) и его химического состава (например, высокое содержание в составе углерода, кремния, никеля и др.)
Горячие трещины могут появиться в результате неправильной заварки кратера, в результате резкого прекращения сварки.
- Холодные трещины
Трещины, которые возникают после того, как сварочный шов полностью остывает и затвердевает, называются холодными трещины. Эти дефекты также появляются тогда, когда сварочный шов не соответствует действующим на него нагрузкам и разрушается.
Пористость является одним из основных дефектов сварки, с которыми сталкиваются все сварщики при всех сварочных процессах. Пористость может быть вызвана загрязнением, плохой защитой ванны потоком сварочного газа, маслом, краской, сваркой несовместимых сплавов или даже ржавчиной и окислением металла.
Поры могут различаться по размеру и, как правило, распределяются в случайном порядке по сварочному шву. Они могут находиться как внутри шва, так и на его поверхности.
Основные причины появления пористости:
- 1) Недостаточный поток защитного сварочного газа
- 2) Чрезмерный поток защитного газа. Это может вызвать подсос воздуха в поток газа.
- 3) Сквозняк в зоне сварки. Он может сдувать защитный газ.
- 4) Засорение сварочного сопла или повреждение системы подачи газа (утечка в шлангах, соединениях и т.д.)
Надеюсь, что описанные в этой статье основные виды дефектов сварных швов и соединений, а так же методы их устранения сделают вашу сварку качественной и высокопроизводительной. Помните, что правильный выбор сварочного оборудования и технологии сварки имеет большое влияние как на весь процесс сварки в целом, так и в отдельности на каждые его составляющие.
© Смарт Техникс
Данная статья является авторским продуктом, любое её использование и копирование в Интернете разрешена с обязательным указанием гиперссылки на сайт www.smart2tech.ru
www.smart2tech.ru
Виды дефектов сварных швов и методы их устранения
Сварка – наиболее эффективная и экономичная технология, применяемая для создания неразъемных металлических соединений. На сегодняшний день существует около 50 видов сварки.Сварка – наиболее эффективная и экономичная технология, применяемая для создания неразъемных металлических соединений. На сегодняшний день существует около 50 видов сварки. Область её применения огромна: строительство, ремонт, под водой и даже в космосе. Именно поэтому к качеству данного вида соединений применяются жeсткие требования.
Обратите внимание, качественные металлические сварные ограждения Вы можете заказать в компании «Надежные конструкции» (http://нк37.рф/metallicheskie_svarnyue_ograjdeniya), перейдя по нашей ссылке.
Классификация дефектов сварочных швов и причины их появления
Сварка – сложный технологический процесс. Незначительные отклонения от заданных условий или требований чертежей могут привести к ухудшению качества соединения и появлению дефектов. Условно, все дефекты разделяют наружные и внутренние. К первым относят нарушения, которые можно обнаружить при внешнем осмотре соединения. Чаще всего они возникают из-за низкой квалификации сварщика, неисправности инструмента, неправильной подготовке соединяемых поверхностей, перепадов напряжения или нарушений режимов сварки. Наиболее опасными являются внутренние дефекты. Они возникают в результате поглощения окиси водорода расплавленным металлом. Углерод не успевает выделиться из застывшего металла и остается в нем в виде пузырьков.
Наружные дефекты сварочных швов и способы их устранения
Наружными являются следующие виды отклонений:
- Наплывы. Чаще всего данный дефект возникает при горизонтальном сваривании вертикальных поверхностей. На кромки основного металла натекает расплавленный металл, имеющий большую температуру. Данный дефект срезают или срубывают. Место сруба проверяют на наличие непровара.
- Непровар – отсутствие соединения между наплавляемым и основным металлом. Снизить вероятность возникновения данного вида дефекта можно с помощью предварительного нагрева деталей, тщательной зачистки их кромок. Участки шва с непровором необходимо удалить.
- Прожоги представляют собой сквозные отверстия в сварочном шве. Как правило, причиной их появления является применение большого тока при низкой скорости сварки. Участок шва с прожогом зачищается и повторно заваривается.
- Подрезы. Этот вид дефекта встречается чаще всего. Представляет собой углубление у кромки сварного шва, в результате чего происходит утоньшение основного металла. Для устранения применяют повторное заваривание с предварительной зачисткой.
- Свищ – небольшие углубления в сварочном шве. Дефект устраняется путем переварки.
Разновидности и способы устранения внутренних дефектов
- Поры. Внутришовные полости, заполненные газом. Могут иметь разную форму и размер. Спровоцировать появление пористости могут повышенное содержание углерода, плохая обработка поверхностей или наличие примесей в металле. Дефектный участок подлежит зачистке и перевариванию.
- Горячие трещины. Являются следствием резкого ухудшения пластических свойств металла. Появляются в диапазоне температур от 10000 °С до 13000 °С. Горячие трещины – один из наиболее опасных дефектов сварного шва. Возникают на шве и в прилегающих зонах.
- Холодные трещины возникают при температуре до 1300 °С. Могут возникнуть либо после остывания шва, либо через длительное время. Швы с трещинами должны быть либо переварены, либо полностью вырублены.
- Шлаковые, оксидные и вольфрамовые включения. Наиболее опасными являются шлаковые включения. Они образовываются при высокой скорости сварки, плохой защите сварной ванны или некачественной подготовке сварных материалов.
Участок шва с таким дефектом подлежит вырубке. Оксидные включения проявляются образованием тугоплавких пленок на поверхности шва. Как правило, появляются на загрязненных поверхностях. Вольфрамовые включения возникают при высокой плотности тока или вследствие коротких замыканий.
www.technoflax.com
Дефекты сварочных швов: внешние и внутренние
Дефектами сварных швов и соединений называют различные отклонения от требований чертежа и условий выполнения сварочных работ, ухудшающих качество соединения (его эксплуатационные свойства, герметичность, сплошность и др.). От возникновения брака не застрахован никто, поэтому сварщик должен знать возможные дефекты, причины их возникновения, а также методы устранения, о чем дальше и пойдет речь.
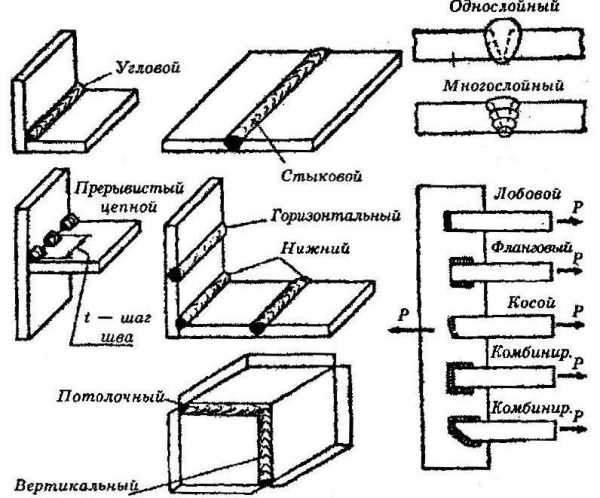
Классификация сварочных швов.
Причины возникновения дефектов сварочных соединений
Сварочный процесс осложняется многими факторами, к которым можно отнести как объективные (свойства соединяемых материалов), так и субъективные (точное соблюдение технологичности процесса, правильность выбора технологии). Оправдать возникновение брака у профессионального сварщика можно только объективными причинами, да и то лишь в какой-то мере.
Основными причинами, которые приводят к образованию дефектов сварочных швов, являются:
- неправильная подготовка свариваемых поверхностей;
- несоответствие или неисправность сварочного инструмента;
- неправильный выбор защитных флюсов или газов и нарушение технологии их использования;
- недостаточная квалификация сварщика;
- несоблюдение в полной мере требуемых режимов сварки (мощность рабочего тока, длина дуги и др.).
Разновидности дефектов сварочных швов
Таблица дефектов сварочных швов.
Все дефекты таких соединений можно разделить на 2 основных типа:
- Внешние, которые можно обнаружить невооруженным глазом. Они могут проявляться в виде прожога, непровара и других признаков.
- Внутренние, которые проявляются в виде трещин, пор и других нежелательных образований.
Далее будут рассмотрены обе категории более подробно.
Внешние дефекты сварочных соединений
К данным дефектам относятся нарушения геометрических размеров сварных соединений (наплывы, подрезы), а также прожоги, непровары и незаваренные кратеры.
Наплывы (натеки) наиболее часто появляются при горизонтальной сварке вертикальных поверхностей. Это приводит к натеканию расплавленного металла на кромки основного металла, имеющего намного меньшую температуру (рис. 1). Они могут возникать на небольшом участке или же иметь большую протяженность вдоль сварной зоны.
Причинами возникновения наплывов являются:
- длинная дуга;
- большая величина сварного тока;
- неправильное положение электрода.
Рисунок 1. Наплывы чаще выявляются при горизонтальной сварке.
При кольцевом соединении наплывы могут появляться при большом или недостаточном смещении электрода с зенита. В местах наплывов достаточно часто могут возникать и другие дефекты. Не допустить образование наплывов можно подбором правильного режима сварки и качественной подготовкой свариваемой поверхности (удаление окалины и др.).
Подрез — дефект в виде канавки в основном металле по краям сварочного шва (рис. 2). Данный дефект является самым распространенным при сварке нахлесточных или тавровых соединений, но иногда возникает при создании стыковых соединений. В большинстве случаев он возникает из-за неправильно подобранных параметров сварочного процесса.
При угловой сварке подрезы могут возникать из-за того, что дуга направляется больше на вертикальную поверхность, чем на горизонтальную. Это приводит к тому, что расплавленный металл стекает на нижнюю кромку и его не хватает для полного заполнения ванны. При слишком большой скорости сварки и большом напряжении сварочные швы могут выйти горбатыми. Из-за быстрого затвердевания сварочной ванны также могут образовываться подрезы. Снижение скорости сварки позволяет устранить этот дефект.
На возникновение подрезов влияет и длина дуги. При увеличении величины дуги возрастает и размер шва, что приводит к увеличению количества расплавленного основного металла. Так как при увеличении длины дуги тепловложение остается прежним, его не хватает на весь шов, кромки быстро остывают, в результате чего образуются подрезы. Уменьшение длины дуги не только может избавить от подрезов, но и увеличивает проплавление.
Рисунок 2. Подрез представляет собой дефект, проявляющийся в виде канавки по краям сварочного шва.
Прожогами называются дефекты сварки, которые проявляются в сквозном проплавлении и вытекании жидкого металла через сквозное отверстие в шве. При этом с другой стороны места соединения может образоваться натек. Прожоги возникают из-за слишком большого значения рабочего тока, большого зазора между кромками металла, недостаточной скорости перемещения электрода, недостаточной толщины подкладки или ее неплотного прилегания к основному металлу. Устранение данного дефекта выполняется снижением рабочего тока и увеличением скорости перемещения электрода. При этом особое внимание следует обратить на качество подгонки кромок детали, чтобы расплавленный металл не выливался из сварной ванны.
Непровары — это локальные несплавления наплавленного металла с основным металлом или слоев шва между собой. К этому дефекту можно отнести и незаполнение сечения шва (рис. 3).
Непровары существенно уменьшают качество состыковки и могут привести к тому, что сварочное соединение со временем разрушится.
Этот дефект возникает из-за недостаточной величины рабочего тока, высокой скорости сварки, плохой подготовки свариваемых поверхностей, присутствия на кромках детали посторонних веществ (шлака, ржавчины и др.) и загрязнений. Не допустить возникновение непроваров можно выбором требуемого значения сварочного тока.
Внутренние дефекты сварочных соединений
К самым распространенным внутренним дефектам относятся горячие, холодные трещины и поры.
Рисунок 3. Непровары значительно уменьшают качество состыковки и приводят к разрушению сварочного соединения.
Горячие трещины появляются при нагреве металла до температуры более 1200 °С, в результате чего происходит быстрое уменьшение пластических свойств металла (кристаллизация). Горячие трещины возникают на границах зерен кристаллической решетки. Их возникновению способствует наличие большого количества в металле различных примесей. Распространяться такие трещины могут как поперек, так и вдоль шва.
Холодные трещины появляются при температуре металла ниже 130°С. Иногда такие дефекты могут возникать и со временем. Причинами их появления могут быть сварочные напряжения, образующиеся во время фазовых превращений, или растворенный атомарный водород, который не успел выделиться при сварке.
Поры — это полости внутри шва, заполненные газом, который не успел выделиться в процессе сварки. Они могут иметь различную форму и размеры, которые зависят от размеров пузырьков газа. Основными причинами возникновения такого дефекта являются:
- наличие примесей в присадочном или основном металле;
- некачественная обработка свариваемых поверхностей;
- повышенное содержание углерода;
- нарушения защиты сварочной ванны.
Одиночные поры не несут большой опасности, но их цепочка снижает механические характеристики изделия. Участок сварочного шва, на котором обнаружены поры, подлежит переварке с предварительной механической зачисткой.
Способы выявления дефектов сварочных соединений
Дефекты сварных швов можно выявить такими способами:
Схема прожога сварного шва.
- внешним осмотром и обмером швов;
- испытанием непроницаемости;
- специальными приборами.
Внешний осмотр проводится только после качественной очистки соединения от шлака, брызг металла и других загрязнений. При этом проверке подлежат правильность размеров и формы швов и отсутствие каких-либо дефектов. Размеры швов можно проверить с помощью специальных шаблонов.
Испытание непроницаемости позволяет выявить поры, сквозные непровары и трещины. Контроль качества сварных швов с использованием специальных приборов позволяет обнаружить внутренние дефекты соединений. Такой контроль может осуществляться следующими способами:
- просвечиванием рентгеновскими лучами или гамма-лучами радиоактивных изотопов;
- намагничиванием, то есть нахождением внутренних дефектов с помощью магнитного поля;
- прозвучиванием, то есть обнаружением дефектов с помощью ультразвуковых колебаний;
- засверливанием с частичным разрушением шва в месте контроля.
Следует отметить, что выполнить ряд сварочных соединений без дефектов практически невозможно. При этом следует обеспечить в шве минимум допустимых дефектов. При осуществлении сварочных работ необходимо помнить, что правильный выбор оборудования и технологии сварки имеет большое влияние на весь процесс сварки.
moyasvarka.ru
Дефекты сварочных швов и причины их образования | Строительный справочник | материалы – конструкции
Все отклонения от технологических параметров, вызванные небрежностью в работе, нарушением режимов и внешними причинами, часто не зависящими от сварщика, могут привести к возникновению дефектов в сварочном шве и околшовной зоне, попадающей в область термического воздействия. К дефектам приводит и нарушение технологических приемов как самого процесса сварки, так и некачественная подготовка, неисправность оборудования, отклонения от норм качества сварочных материалов, влияние погодных условий, низкая квалификация сварщика.
Возникновение дефектов часто связано с металлургическими и тепловыми явлениями, возникающими в процессе образования сварочной ванны и ее кристаллизации (горячие и холодные трещины, поры, шлаковые включения и т.д.; Эти дефекты снижают прочность и надежность сварного соединения, его герметичность и коррозионную стойкость. Все это может оказать значительное влияние на эксплуатационные возможности всей конструкции и даже вызвать ее разрушение.
Дефекты сварочных швов могут быть наружными и внутренними.
Наружные дефекты сварочных швов
К наружным дефектам сварных швов (рис.1) относят нарушение размеров и формы шва, подрезы и другие отклонения, которые могут быть обнаружены при внешнем осмотре сварного соединения.
Нарушение формы и размеров сварного шва чаще всего вызваны колебаниями напряжения в электрической сети, небрежностью в работе или низкой квалификацией сварщика, проявляющейся в неправильном выборе режимов, неточном направлении электрода и методике его перемещения. Дефекты проявляются в неодинаковой ширине сварочного шва по его длине, в неравномерности катета угловых швов, чрезмерной выпуклости и резких переходах от основного металла к наплавленному. Отклонения от размеров и формы сварного соединения, проявляющиеся в угловых швах, связаны с неправильной подготовкой кромок, неравномерной скоростью сварки, а также с несвоевременным контрольным обмером шва. При автоматической и полуавтоматической сварке эти дефекты чаще всего связаны с колебаниями напряжения, проскальзыванием проволоки в подающих роликах, нарушениями режимов сварки.
Непровар — местное отсутствие сплавления между свариваемыми элементами, между основным и наплавленным металлом или отдельными слоями шва при многослойной сварке. Причинами непровара являются некачественная подготовка свариваемых кромок (окалина, ржавчина, малый зазор, излишнее притупление и т.д.), большая скорость сварки, смещение электрода с оси стыка, недостаточная сила тока. В результате непровара снижается сечение шва и возникает местная концентрация напряжений, что в конечном итоге снижает прочность сварного соединения. При вибрационных нагрузках даже мелкие непровары могут снижать прочность соединения до 40%. Большие непровары корня шва могут снизить прочность до 70%. Поэтому если непровар превышает допустимую величину, участок шва подлежит удалению с последующей переваркой.
Подрез — дефект, наиболее часто встречающийся при сварке. Он выражен в виде углубления по линии сплавления сварного шва с основным металлом. В результате подреза происходит местное уменьшение толщины основного металла, что приводит к снижению прочности. Особенно опасен подрез в случаях, когда он расположен перпендикулярно действующим рабочим напряжениям. Подрез возникает обычно при повышенном напряжении дуги с завышенной скоростью сварки, когда одна из кромок проплавляется глубже, жидкий металл стекает на горизонтальную плоскость и его не хватает для заполнения канавки. При сварке угловых швов подрезы возникают в основном из-за смещения электрода в сторону вертикальной стенки, что вызывает значительный разогрев, плавление и стекание металла на горизонтальную полку. В стыковых швах подрезы образуются при сварке на больших токах и при неправильном положении присадочного материала. К подрезу могут привести увеличенные углы разделки кромок. Этот дефект обнаруживается визуально и при отклонениях выше установленной нормы полежит переварке с предварительной зачисткой. Подрезы небольшой протяженности, ослабляющие сечение шва не более чем на 5% в конструкциях, работающих под действием статических нагрузок можно считать допустимыми. В конструкциях, работающих на выносливость, подрезы недопустимы.
Наплыв — проявляется в виде натекания металла шва на поверхность основного металла без сплавления с ним. Наплывы резко изменяют очертания швов и тем самым снижают выносливость констукции. Причиной этого дефекта может стать пониженное напряжение дуги, наличие окалины на свариваемых кромках, медленная сварка, когда появляются излишки расплавленного присадочного металла. Чаще всего наплывы возникают при сварке горизонтальных швов на вертикальной плоскости. При сварке кольцевых поворотных стыков наплывы могут возникать при неправильном расположении электрода относительно оси шва. Наплывы большой протяженности недопустимы.
Прожог — сквозное проплавление обычно возникает из-за большого тока при малой скорости сварки. Проявляется он в виде сквозного отверстия в сварочном шве, которое возникает в результате утечки сварочной ванны. При многослойной сварке прожог возникает в процессе выполнения первого прохода шва. Причинами прожога могут стать – завышенный зазор между свариваемыми кромками, недостаточная толщина подкладки или неплотное ее прилегание к основному металлу, что создает предпосылку для утечки сварочной ванны. Прожог может образоваться при внезапной остановке подачи защитного газа. При сварке поворотных кольцевых стыков прожоги вызываются неправильным расположением электрода относительно зенита. Дефект обнаруживается визуально и переваривается после предварительной зачистки. Ожоги вызываются попаданием жидкого металла на участки, которые находятся вне сварного шва.
Незаваренный кратер — дефект сварного шва, который образуется в виде углублений в местах резкого отрыва дуги в конце сварки. В углублениях кратера могут появляться усадочные рыхлости, часто переходящие в трещины. Кратеры обычно появляются в результате неправильных действий сварщика. При автоматической сварке кратер может появляться в местах выводных планок, где обрывается сварочный шов. Кратеры часто являются причиной начала развития трещин и поэтому недопустимы. Их зачищают и заваривают.
Поверхностное окисление — окалина или пленка оксидов на поверхности сварного соединения. Поверхностное окисление зависит от плохой защиты сварочной ванны, качества подготовки свариваемых кромок, неправильной регулировки подачи защитного газа, его составом, большим вылетом электрода.
Свищ — воронкообразное углубление в сварочном шве, развивающееся из раковины или большой поры. Причиной развития свища чаще всего является некачественная подготовка поверхности и присадочной проволоки под сварку. Дефект обнаруживается визуально и подлежит переварке.
![]() | ![]() |
Рис. 1 Наружные дефекты сварных швов, выявляемые внешним осмотром: А — подрез; Б — наплыв; В — прожог; Г — незаваренный кратер; Д —свищ. | Рис. 2. Трещины в сварном шве и околошовной зоне: А — продольная горячая трещина; Б — холодная трещина в околошовной зоне. |
Внутренние дефекты сварочных швов
Трещины бывают холодные и горячие (рис. 2). Трещины могут быть как наружными, так и внутренними. Это самые опасные дефекты сварного соединения, часто приводящие к его разрушению. Проявляются они в виде разрыва в сварном шве или в прилегающих к нему зонах. Сначала трещины образуются с очень малым раскрытием, но под действием напряжений их распространение может быть соизмеримо со скоростью звука, в результате чего происходит разрушение конструкции. Причинами образования трещин являются большие напряжения, возникающие при сварке. Чаще всего трещины проявляются при сварке высокоуглеродистых и легированных сталей в результате быстрого охлаждения сварочной ванны. Вероятность появления трещин увеличивается при жестком закреплении свариваемых деталей.
Горячие трещины — появляются в процессе кристаллизации металла при температурах 1100 —1300°С вследствие резкого снижения пластических свойств и развития растягивающих деформаций. Появляются горячие трещины на границах зерен кристаллической решетки. Появлению горячих трещин способствует повышенное содержание в металле шва углерода, кремния, водорода, никеля, серы и фосфора. Горячие трещины могут возникать как в массиве шва, так и в зоне термического влияния. Распространяться горячие трещины могут как вдоль, так и поперек шва. Они могут быть внутренними или выходить на поверхность.
Холодные трещины — возникают при температурах ниже 120°С, то есть сразу после остывания сварочного шва. Кроме того, холодные трещины могут возникнуть и через длительный промежуток времени. Причиной появления холодных трещин являются сварочные напряжения, возникающие во время фазовых превращений, приводящих к снижению прочностных свойств металла. Причиной появления холодных трещин может стать растворенный атомарный водород, не успевший выделиться во время сварки. Причинами попадания водорода могут служить непросушенные швы или сварочные материалы, нарушения защиты сварочной ванны.
Поры — представляют собой полости внутри шва, заполненные не успевшим выделиться газом (в первую очередь водородом). Они могут быть округлой или вытянутой формы, а их размеры зависят от размеров пузырьков образовавшихся газов. Поры могут быть одиночными или развиваться целой цепочкой вдоль сварочного шва. Основными причинами появления пор являются: присутствие вредных примесей в основном или присадочном металлах, ржавчина или другие загрязнения, не удаленные со свариваемых кромок перед сваркой. Повышенное содержание углерода также способствует появлению пор. Поры могут появляться при нарушениях защиты сварочной ванны, повышенной скорости сварки. Основной причиной появления пор при сварке плавящимся электродом является отсыревшее покрытие. Одиночные поры не опасны, но их цепочка влияет на прочность сварного соединения. Участок сварочного шва, в котором присутствуют поры, подлежит переварке предварительной механической зачисткой.
Шлаковые включения — это дефекты сварного шва, выраженные в наличии полостей, заполненных не успевшим всплыть шлаком. Образование шлаковых включений происходит при некачественной подготовке свариваемых кромок и присадочного материала, завышенной скорости сварки или плохой защите ванны. При сварке в защитных газах шлаковые включения встречаются редко. Шлаковые включения могут иметь размер до нескольких десятков миллиметров и поэтому являются очень опасными. Участок шва, на котором шлаковые включения превышают допустимые нормы, подлежит вырубке переварке.
Вольфрамовые включения — возникают при нарушении защиты сварочной ванны при сварке неплавящимся вольфрамовым электродом. Кроме этого вольфрамовые включения возникают при коротких замыканиях или завышенной плотности тока. Особенно часто встречаются вольфрамовые включения при сварке алюминия и его сплавов, в которых вольфрам нерастворим.
Оксидные включения — образуются в результате образования труднорастворимых тугоплавких пленок. Чаще всего они возникают вследствие значительных поверхностных загрязнений или при нарушениях защиты сварочной ванны. Являясь прослойкой в массиве шва, оксидные включения резко снижают прочность сварного соединения могут привести к его разрушению под приложенной в процессе эксплуатации нагрузкой.
build.novosibdom.ru
Виды дефектов сварных швов и методы их устранения
Отклонения от утвержденных стандартов, технических условий и требований, возникшие при изготовлении различных изделий или соединении конструкций при помощи сварки, называют дефектами сварного шва (соединения). Они классифицируются по ряду признаков: степени воздействия на качество соединения, характеру проявления, местоположения и т.д.
Основные причины появления дефектов сварных соединений:
- Низкое качество соединяемых материалов.
- Некачественное или неисправное сварочное оборудование.
- Нарушение технологии ведения сварки и неверно выбранные параметры.
- Неправильно подобранные расходные материалы для сварки.
- Недостаточно высокая квалификация специалиста, осуществляющего сварку.
Если дефекты сварного шва не оказывают заметного влияния на эксплуатационные качества изделий или прочность конструкций и укладываются в установленные нормы, то их называют допустимыми. Дефекты, наличие которых может привести к разрушению конструкции или детали при воздействии нормативных нагрузок, считаются недопустимыми и требуют устранения. Причем по техническим требованиям допускается не более двух попыток, так как последующие в любом случае ухудшают качество соединения.
В зависимости от местоположения дефекты сварного соединения делят на 3 группы: наружные, внутренние и сквозные. К первым относятся поверхностные трещины, подрезы, наплывы и кратеры, ко вторым – непровары, поры, свищи и посторонние твердые включения, к третьим – сквозные трещины и прожоги.
Несплавление или непровар – дефект сварного шва, при котором отсутствует прочное соединение между основным и наплавляемым металлом из-за недостаточного взаимного проникновения. Непроваром считается и неполное заполнение полости между соединяемыми поверхностями наплавляемым металлом, или наличие просвета между наплавленными слоями при двусторонней сварке. В любом из этих случаев дефект считается недопустимым и требует устранения путем дополнительного наплавления металла.
Основными причинами непровара являются недостаточно высокий для работы с рабочими поверхностями данной толщины сварочный ток, а также чрезмерно быстрое перемещение электрода. В ряде случаев он является следствием неправильного подбора диаметра электрода или полярности подключения кабелей, а также недостаточного зазора между соединяемыми кромками или их перекос. Иногда данный дефект проявляется при попадании шлака между кромками.
Трещины – достаточно опасные дефекты сварного шва, часто приводящие к полному разрушению соединения. Выражаются образованием видимых разрывов в наплавленном или основном металле, а также на стыке между ними. Могут быть продольными, поперечными и продольно-поперечными (звездообразными). Различают горячие и холодные трещины. Первые образуются во время перехода металла из жидкого состояния в твердое и обычно являются результатом неправильного выбора типа присадочных материалов. Холодные трещины проявляются после полного остывания металла, а в некоторых случаях уже после воздействия нагрузок.
Основные причины проявления этого дефекта – превышение допустимых нагрузок при эксплуатации, резкие перепады температур, неправильное расположение швов.
Устранение данного дефекта осуществляется путем сверления отверстий на концах трещины для предупреждения распространения, срезом поврежденной части шва и повторной сваркой с учетом причин появления брака.
Подрезы – дефекты сварного соединения, выражающиеся в образовании продольных углублений в основном металле по одну или обе стороны от шва. Как правило, односторонний подрез встречается при сварке поверхностей, расположенных под углом друг к другу, например, тавровых соединений. В данном случае его причиной является стекание расплава на горизонтальную поверхность (на последней в результате образуется наплав), ввиду того что дуга в большей степени направлена на вертикальную. Двусторонний подрез образуется при излишне высоком сварочном токе, длине дуги или скорости перемещения электрода или горелки.
Подрез уменьшает прочность сварочного соединения пропорционально глубине канавок. Устраняется этот дефект достаточно легко – путем наплавления небольшого количества металла в сами углубления.
Наплывы – достаточно распространенные дефекты, выражающиеся в образовании излишков наплавляемого металла, не соединившегося с основным. Причинами этого явления могут быть некачественная предварительная подготовка кромок или недостаточный прогрев основного металла из-за малого тока.
Сами по себе наплавы не ухудшают прочности сварного соединения, однако чаще всего свидетельствуют о наличии иных дефектов – подрезов или непроваров. В связи с этим их устраняют путем среза для проверки качества шва.
Прожоги – дефекты сварочного шва, выражающиеся в образовании сквозного отверстия в наплавляемом металле в результате его утечки из сварочной ванны. Прожог обычно является итогом превышения сварочного тока или низкой скорости перемещения горелки или электрода, а также недопустимо большое расстояние между кромками соединяемых поверхностей. Обычно проявляется при сварке алюминия.
Так как сквозные отверстия снижают прочность сварного соединения, прожоги требуют устранения, которое осуществляется путем их заваривания.
Кратеры – конические углубления в шве, причиной появления которых является резкий обрыв сварочной дуги. Основная опасность данных дефектов заключается в увеличении риска образования трещин, поэтому кратеры подлежат заварке. В качественных современных сварочных аппаратах образование подобных дефектов предотвращается специальными системами, автоматически снижающими ток при обрыве дуги.
Поры, раковины и свищи – дефекты сварного соединения, выражающиеся в образовании внутри наплавленного металла в виде наполненных газом полостей. Бывают внутренними и поверхностными, различными по размеру, форме и природе появления. Обычно возникают в результате чрезмерно интенсивного процесса образования газа в металле, связанного с неправильной подготовкой соединяемых поверхностей, низким качеством присадок или нарушением условий хранения электродов, а также наличием посторонних примесей в основном и наплавляемом металле.
Наличие пор делает соединение хрупким и неустойчивым к различным видам нагрузок. Устраняется данная проблема путем вырезания части шва и последующим его завариванием с соблюдением требований и технологии.
Твердые (шлаковые, флюсовые, оксидные, металлические и др.) включения в металле шва являются одними самых сложных дефектов, ввиду сложности их обнаружения. Визуально снаружи они незаметны, поэтому могут быть выявлены только при помощи различных инструментальных методов оценки качества соединения.
Основные причины появления посторонних включений в металле – низкое качество расходных материалов и недостаточно качественная подготовка кромок. Устраняются вырезкой шва и повторной сваркой.
www.reseco.ru
Дефекты сварки: причины образования, способы устранения
Сварка играет немаловажную роль в процессе строительства, изготовления инженерных систем и коммуникаций. Потому для достижения надлежащего результата, очень важно соблюсти все нормы при выполнении сварочных работ. Но нередко возникают дефекты сварки.
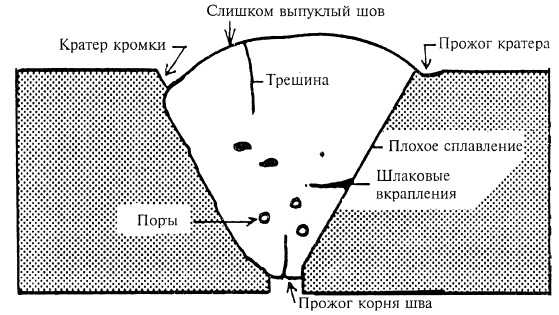
Корневые дефекты шва.
Причинами их возникновения являются как характеристики самого свариваемого материала, так и несоблюдение положений нормативных актов, регулирующих этапы подготовки, сборки, предварительной обработки швов изделия, сварочного процесса. Речь пойдет о классификации дефектов сварки, которые могут встречаться на практике, о причинах их образования и основных способах их предупреждения, устранения и исправления.
Дефекты сварки: классификация
Виды дефектов при сварке.
Можно отметить, что на сегодня существует несколько классификаций дефектов сварки, составленных в зависимости от различных их критериев (форм, размеров, размещения на шве, причин возникновения). Кроме того, существует официальная классификация, содержащаяся в ГОСТ 30242-97, которая выделяет и детально описывает такие группы дефектов:
- Трещины. Встречаются в сварных соединениях (продольные, радиальные, поперечные и т.д.).
- Полости, поры (могут быть равномерно распределенные по шву, расположены цепочкой или скоплением), свищи, кратеры.
- Твердые включения (шлаковые, металлические, оксидные).
- Несплавления (могут возникать на боковой поверхности, на сварном шве, между его валиками) и непровары (встречаются в случаях несплавления основного металла на шве, когда расплавленный металл не проникает в корень сварного соединения).
- Нарушения формы шва. Выражаются в подрезах, натеках, превышениях проплава, прожогах, смещениях, превышениях выпуклости, наплавах, могут проявляться в виде усадочных канавок и др.
Существуют и иные применяемые классификации, где основными критериями являются дополнительные причины образования дефектов, характерные для металлургических и технологических процессов. В таких случаях за основу может браться разделение трещин на горячие (кристаллизационные, дисперсионного твердения) и холодные (ламелярные, интерметаллидные, мартенситные и т.д).
Причины появления дефектов сварки
Методы ультразвуковой диагностики сварных швов.
Отклонения швов по высоте и ширине является одним из самых распространенных изъянов в сварочной работе. Несоответствие швов предусмотренным нормам является результатом небрежной подготовки кромок сварных соединений. Это приводит к тому, что расстояние между кромками разное и его необходимо заполнить наплавленным металлом. Параметры шва могут меняться из-за неравномерного перемещения электрода по всей свариваемой площади, невыполнения установленных правил процесса сварки. Швы и само сварное соединение в этом случае будут неровными и непрочными.
Трещины могут возникать как в основном металле, так и в сварочном. Они вызваны непроварами, кристаллизацией металла в процессе сварки, напряжением, возникшим из-за несоблюдения температурного режима и слишком быстрого охлаждения деталей, изменением структуры металла в ходе сварочных работ, повышенным содержанием фосфора, серы и пр.
Сварное соединение может содержать поры, заполненные газом округлые полости, которые возникают, когда поглощенный металлом водород, в результате нарушений в работе с горелкой, не успевает выделиться наружу и образует в металле газовые пузырьки. Поводом к появлению пор может стать влажное электродное покрытие, несоответствие химических составов сварных соединений, незачищенные края свариваемых металлов, наличие шлаков. Если в шве имеются поры, то конструкция не прослужит долго, будет уязвима для влияния окружающих факторов. С целью выявления пор используют проверку с помощью давления воды, смазыванием керосином, рентгеновскими лучами.
Подрезы представляют собой углубление по линии сварного соединения, спаивающего основной металл и наплавленный. Появляются из-за применения слишком большого тока или мощного сварочного устройства.
Схема сварного соединения.
Непровар возникает, когда кромки многослойного сварного шва, соединяющего наплавленный и основной металлы, не полностью расплавились, вследствие недостаточной зачистки металлов от ржавчины, окалины, недостаточной мощности, неправильного выбора температуры сварочного аппарата, слишком высокой скорости сварки. Такое изделие становится непрочным, легко подверженным внешним воздействиям, ударам и деформациям.
Наплыв на сварном соединении образуется, если плавление электрода происходит слишком быстро, и жидкий металл натекает на недостаточно прогретый основной металл. Бывают случаи, когда наплывы сопровождаются непроварами, поэтому следует проверить участок и на наличие последних.
Свищи представляют собой дефект сварки углубления в виде воронки. Это сквозные поры, вызванные выделением газа, они видны при внешнем осмотре.
Шлаковые включения появляются при недостаточной очистке краев шва от грязи, напылений, отложений, ржавчины. Из технических причин возникновения шлаковых вкраплений выделяют сварку электродом с несоблюдением угла его наклона, мощности горелки, при слабом токе. Для выявления участков с подобным дефектом используют просвечивание рентгеновскими лучами или ультразвуком, магнитографическими приборами.
Типы сварных соединений.
Кратеры, а именно незаплавленные углубления в шве, образуются, если сварка спонтанно прекращается. В таких местах существует высокая вероятность образования трещин, поэтому сварку нельзя прекращать внезапно.
Перегрев металла является изъяном микроструктуры сварного соединения, вызванным сваркой на большой мощности. Строение такого металла крупнозернистое, что влечет за собой его хрупкость и ломкость.
Пережог металла возникает, если в пламени не хватает кислорода, характеризуется наличием окислительных зерен в металле. Последствием пережога считается хрупкость металла, такой изъян не устраняется.
Способы исправления дефектов сварки
Схемы усиления дефектных соединений: 1 — сварное соединение; 2 — стальная скоба; 3 — накладка; 4 — протяженные сварные швы; 5 — дефект.
Практически в любом случае возникновения вышеперечисленных, проблем самым действенным и надежным способом их исправления станет удаление участка сварного соединения с изъяном и заваривание деталей заново (при наплывах, свищах, прожогах, шлаковых включениях). Это даст возможность избежать в дальнейшем проблем с перегниванием, коррозией, ломкостью изделия.
Исправление дефектов всегда зависит от каждого отдельного случая. Поэтому существуют способы, применимые к конкретным случаям.Например, для борьбы с дефектами швов, подрезов, кратеров следует применять зачистку с дополнительной подваркой шва и срезание лишнего металла.
Чтобы избежать появления прожогов при автоматической сварке, следует плотно прижимать флюсовую подушку и медную прокладку, а при точечной и шовной контрастных сварках продолжительность процесса не должна превышать установленную, края деталей должны быть полностью очищены.
Для устранения трещин применяют, помимо удаления проблемного участка и новой сварки, поверхностную кислородную или воздушно-духовую резку. Участки, на которых имеются поры, тоже вырезают и сваривают заново либо применяют к изделию проковку при надлежащей температуре.
Для того чтобы избежать появления непроваров, следует соблюдать одинаковый температурный режим. Это даст возможность металлу в сварном соединении равномерно прогреться до начала сварочных работ и не смещать электроды от шва.
Нельзя выключать ток до того, как кромки изделия будут полностью сварены. Если все же непровары образовались, необходимо вырезать поврежденный участок (вырубить или выстрогать), зачистить края и вновь заварить.
Во избежание брызг металла, как дефекта сварки, профессионалы рекомендуют применять покрытия П1 или П2, зачищать поверхность. А термообработка поможет для исправления перегрева металла.
Данная классификация дефектов и способов, поможет добиться отличного качества сварки.
moyasvarka.ru