Хим состав 20 стали – 20
alexxlab | 10.08.2020 | 0 | Вопросы и ответы
Сталь 20хн3а и ее характеристики
В этой статье речь пойдет об одной из наиболее распространенных и широко используемых марок стали. Мы вкратце опишем то, для чего она применяется, расскажем об одной крайне любопытной термической процедуре, даже посоветуем вам ознакомиться с несколькими документами, такими как ГОСТ 8479-70, а также поведаем о химическом составе стали и расскажем, как он влияет на ее характеристики.
Применение
Итак, начнем с самого, на наш взгляд, очевидного, но не менее важного вопроса, а именно с того, для чего используется сталь 20хн3а. Чаще всего из этого сорта стали изготавливаются детали, которые в дальнейшем подвергаются процессу цементации. Это значит, что подобного рода деталям необходимо будет в дальнейшем совмещать в себе поверхностную твердость и внутреннюю пластичность.
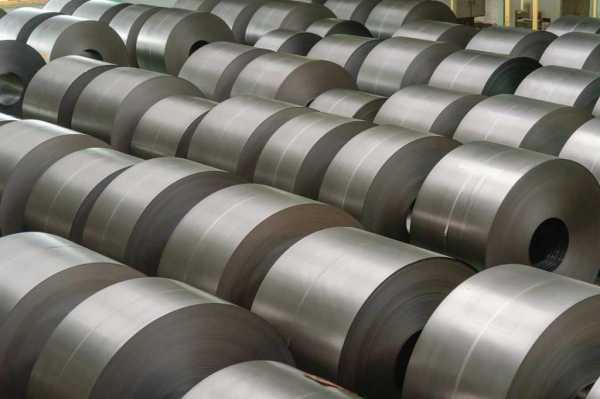
Подобные требования обычно предъявляются изделиям, которые за время своей эксплуатации так или иначе будут подвержены нагрузкам, в том числе и ударным. В данном случае твердый поверхностный слой будет препятствовать деформации детали, а внутренний мягкий слой будет принимать на себя все физические последствия удара и поглощать их без вреда для детали. В данную категорию можно зачислить валы, шпильки, болты, зубчатые колеса и втулки, а также многое другое.
Цементация стали
И раз уж мы упомянули цементацию стали 20хн3а, то стоит рассказать вам, пусть и вкратце, о том, что собой представляет данный процесс. Сама суть процесса состоит в том, чтобы заведомо низкоуглеродистую (обычно до 0,2 % С) сталь насытить этим самым углеродом, тем самым придав ей твердости. Однако надо понимать, что подобный процесс науглеродит только поверхностный слой металлоизделия в пределах от 0,5 до 2 миллиметров, оставив середину мягкой и податливой.
Сам же процесс цементации, который и придает стали 20хн3а характеристики повышенной прочности, протекает при повышенных температурах (850-950 °С) в углеродсодержащей среде. На предприятиях обычно применяется газовая цементация с использованием метана или окиси углерода, однако подобную процедуру можно проводить и с использованием древесного угля или раствором углекислой натриевой соли.
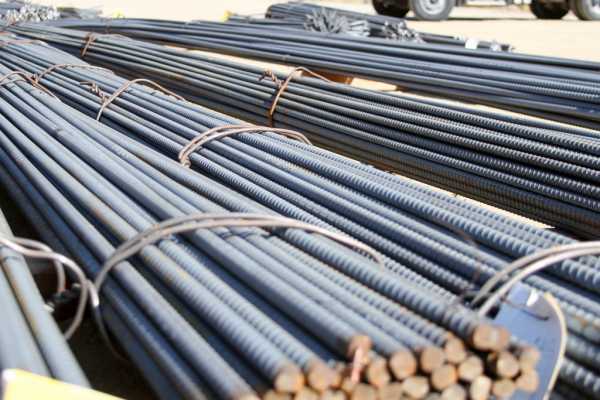
При нагреве до вышеупомянутой температуры сталь переходит в активную фазу и адсорбирует в себя углерод из внешней среды. Однако этот процесс довольно медленный. Для науглероживания слоя в один миллиметр тратится от 4 до 10 часов, в зависимости от способа цементации.
Химический состав
Как известно, характеристики абсолютно всех марок стали зависят в первую очередь от легирующих элементов в ее конечном составе. Именно добавки химических элементов в итоге и придают стали необходимые свойства, будь то твердость или, наоборот, пластичность, устойчивость к коррозии либо ударным нагрузкам. Именно поэтому так важно порой бывает изучить состав стали. Проще всего это сделать, заглянув в соответствующий ГОСТ. Сталь 20хн3а упоминается во множестве ГОСТов, поэтому, дабы облегчить вам поиски, мы приведем перечень всех элементов и значения их массовой доли в составе стали прямо в этой статье.
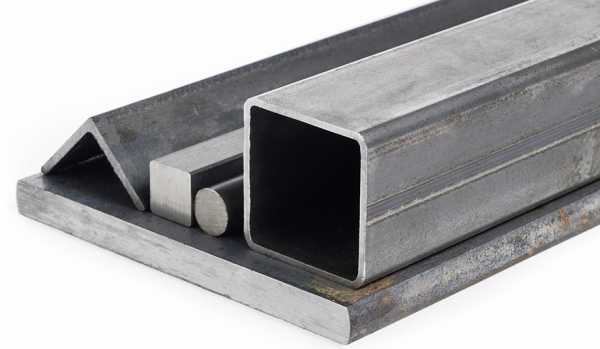
Выглядит он следующим образом:
- Углерод – 0,2 %.
- Хром – 0,75 %.
- Никель – 2,95 %.
- Марганец – 0,45 %.
- Кремний – 0,27 %.
- Медь – 0,3 %.
- Сера и фосфор – 0,025 %.
Характеристики
Все основные свойства любой из марок стали неминуемо исследуются, далее проверяются и в конечном итоге заносятся в нормативно-технический документ, то бишь ГОСТ. К примеру, дабы лучше разобраться в теме статьи и в теме металлургии в целом, советуем вам обратить внимание на ГОСТ 8479-70, а также на ГОСТы 4543-71, 7417-75 и 103-2006. Изучая эти документы, вам, скорее всего, будут встречаться непонятные термины и обозначения, с которыми вам тоже не мешало бы ознакомиться, чтобы изучение подобных документов не давалось так тяжело.
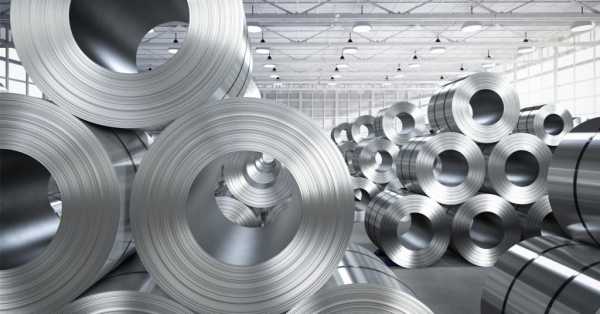
Однако мы немного отвлеклись от темы. Так как мы уже ознакомились с химическим составом стали 20хн3а, то можем довольно точно определить основные ее свойства. Данная сталь, благодаря примесям никеля, хрома и меди, наделена неплохой устойчивостью к коррозии, что весьма важно для многих деталей, изготавливаемых из этого сорта стали. Помимо этого, повышенное содержание никеля повышает прокаливаемость, что, несомненно, облегчит процесс цементации.
За твердость здесь отвечает в первую очередь углерод, которого, несомненно, крайне мало для обеспечения изначальной твердости стали 20хн3а. Незначительно улучшает ситуацию кремний и хром, однако их воздействие на прочность и твердость стали крайне малозначительно.
fb.ru
Доска объявлений | Сталь 20Х – характеристика, химический состав, свойства, твердостьСталь 20ХОбщие сведения
Химический состав
Механические свойстваМеханические свойства при повышенных температурах
Механические свойства проката
Механические свойства поковок
Механические свойства в зависимости от температуры отпуска
Технологические свойства
Температура критических точек
Ударная вязкостьУдарная вязкость, KCU, Дж/см2
Предел выносливости
ПрокаливаемостьЗакалка 860 С. Твердость для полос прокаливаемости HRCэ.
Физические свойства
[ Назад ] |
s-metall.com.ua
Доска объявлений | Сталь 20Г – характеристика, химический состав, свойства, твердостьСталь 20ГОбщие сведения
Химический состав
Механические свойстваМеханические свойства
Механические свойства в зависимости от температуры отпуска
Механические свойства в зависимости от сечения
Технологические свойства
Температура критических точек
Ударная вязкостьУдарная вязкость, KCU, Дж/см2
Предел выносливости
Прокаливаемость
Физические свойства
[ Назад ] |
s-metall.com.ua
20 ФЛАНЦЫ МАТЕРИАЛ СТ. 20 СТАЛЬ 20, МЕХ. СВОЙСТВА СТАЛИ 20 ХИМ. СОСТАВ СТАЛИ 20
Характеристика материала ст. 20.
Химический состав в % материала 20
C | Si | Mn | Ni | S | P | Cr | Cu | As |
0.17 – 0.24 | 0.17 – 0.37 | 0.35 – 0.65 | до 0.25 | до 0.04 | до 0.04 | до 0.25 | до 0.25 | до 0.08 |
Температура критических точек материала 20.
Ac1 = 724 , Ac3(Acm) = 845 , Ar3(Arcm) = 815 , Ar1 = 682 |
Механические свойства при Т=20°C материала 20.
Сортамент | Размер | Напр. | sв | sT | d5 | y | KCU | Термообр. |
– | мм | – | МПа | МПа | % | % | кДж / м2 | – |
Прокат горячекатан. | до 80 | Прод. | 420 | 250 | 25 | 55 | Нормализация | |
Пруток | Прод. | 480 | 270 | 30 | 62 | 1450 | Отжиг 880 – 900oC, | |
Пруток | Прод. | 510 | 320 | 30.7 | 67 | 1000 | Нормализация 880 – 920oC, |
Твердость материала 20 после отжига, | HB 10 -1 = 163 МПа |
Твердость материала 20 калиброванного нагартованного, | HB 10 -1 = 207 МПа |
Физические свойства материала 20.
T | E 10- 5 | a 10 6 | l | r | C | R 10 9 |
Град | МПа | 1/Град | Вт/(м·град) | кг/м3 | Дж/(кг·град) | Ом·м |
20 | 2.13 | 52 | 7859 | |||
100 | 2.03 | 11.6 | 50.6 | 7834 | 486 | 219 |
200 | 1.99 | 12.6 | 48.6 | 7803 | 498 | 292 |
300 | 1.9 | 13.1 | 46.2 | 7770 | 514 | 381 |
400 | 1.82 | 13.6 | 42.8 | 7736 | 533 | 487 |
500 | 1.72 | 14.1 | 39.1 | 7699 | 555 | 601 |
600 | 1.6 | 14.6 | 35.8 | 7659 | 584 | 758 |
700 | 14.8 | 32 | 7617 | 636 | 925 | |
800 | 12.9 | 7624 | 703 | 1094 | ||
900 | 7600 | 703 | 1135 | |||
1000 | 695 | |||||
T | E 10- 5 | a 10 6 | l | r | C | R 10 9 |
Технологические свойства материала 20.
Свариваемость: | без ограничений. |
Флокеночувствительность: | не чувствительна. |
Склонность к отпускной хрупкости: | не склонна. |
Литейно-технологические свойства материала 20.
Температура плавления, °C : | 1.1 – 2.2 |
Температура горячей обработки,°C : | 3.3 – 4.4 |
Температура отжига, °C : | 5.5 – 66 |
Обозначения:
Механические свойства : | |
sв | – Предел кратковременной прочности, [МПа] |
sT | – Предел пропорциональности (предел текучести для остаточной деформации), [МПа] |
d5 | – Относительное удлинение при разрыве, [ % ] |
y | – Относительное сужение , [ % ] |
KCU | – Ударная вязкость, [ кДж / м2] |
HB | – Твердость по Бринеллю, [МПа] |
Физические свойства: | |
T | – Температура, при которой получены данные свойства, [Град] |
E | – Модуль упругости первого рода, [МПа] |
a | – Коэффициент температурного (линейного) расширения (диапазон 20o – T ), [1/Град] |
l | – Коэффициент теплопроводности (теплоемкость материала), [Вт/(м·град)] |
r | – Плотность материала, [кг/м3] |
C | – Удельная теплоемкость материала (диапазон 20o – T ), [Дж/(кг·град)] |
R | – Удельное электросопротивление, [Ом·м] |
Свариваемость: | |
без ограничений | – сварка производится без подогрева и без последующей термообработки |
ограниченно свариваемая | – сварка возможна при подогреве до 100-120 град. и последующей термообработке |
трудносвариваемая | – для получения качественных сварных соединений требуются дополнительные операции: подогрев до 200-300 град. при сварке, термообработка после сварки – отжиг |
www.12821-80.ru
Химический состав: Сталь 20ХФ — Мегаобучалка
МИНИСТЕРСТВО ОБРАЗОВАНИЯ, НАУКИ, МОЛОДЕЖИ И СПОТРУ УКРАИНЫ
ОДЕССКИЙ НАЦИОНАЛЬНЫЙ ПОЛИТЕХНИЧЕСКИЙ УНИВЕРСИТЕТ
ИПТДМ
Кафедра технологий конструкционных материалов и материаловедения
![]() |
Курсовая работа
по дисциплине “Материаловедение и технология материалов”
По теме:
«Упрочнение деталей работающих на износ»
Студент: Чуба С.А.
Руководитель: Клименко Н.Н.
Одесса 2012
![]() |
Введение:
В настоящее время все, в основном, пальцы шаровых шарниров характеризуются наличием стержня округлой формы, сочетающейся резьбовой цилиндрической частью с конической. В нижней части стержня расположена головка шарового пальца, выполненная в форме шара.
Рис. 1 Палец шарнира.
1–палец шарнира;
2–грязезащитныйколпачок;
3–корпусшарнира;
4–вкладыш;
5–пружина;
Заглушка
Палец шарнира, это деталь шаровой опоры, которая в свою очередь используется в подвеске автомобиля.
Шаровая опора – узел, соединяющий ступицу колеса и рычаг подвески.
Рис. 2 Общий вид шаровой опоры.
Задача шаровой опоры – позволять колесу (ступице колеса, если быть точным) двигаться в вертикальном направлении, сохраняя его положение в горизонтальной плоскости. Конструктивно шаровая опора это конусообразный «палец» с шаровидной или грибовидной основой, укрепленной внутри корпуса. Современные шаровые опоры часто изготавливаются неразъемными, и корпус после установки пальца просто завальцовывают так, чтобы сохранить движение «пальца» на небольшие углы.
При езде шаровая опора испытывает на себе огромные нагрузки, так как в отдельные моменты времени на ней может сосредотачиваться изрядная часть веса автомобиля, не считая постоянных ударов.
Рис. 3 Подвеска автомобиля.
Выбор сталей и их химические составы.
Углеродистая сталь.
Из углеродистой я выбрал Сталь 10она подходит для изготовления шайб, бачков, заклепок, пальцев и т.д.
После цементации она используется для деталей, от которых требуется высокая твердость поверхности и допускается низкая прочность сердцевины.
Химический состав: Сталь 10
Химический элемент | % |
Кремний (Si) | 0.17-0.37 |
Медь (Cu), не более | 0.25 |
Мышьяк (As), не более | 0.08 |
Марганец (Mn) | 0.35-0.65 |
Никель (Ni), не более | 0.25 |
Фосфор (P), не более | 0.035 |
Хром (Cr), не более | 0.15 |
Сера (S), не более | 0.04 |
Углерод (С) не более | 0.7-0.14 |
Легелированая сталь
Из легелированой я выбрал Сталь 20ХФона предназначена для не крупных деталей (в связи с небольшой прокаливаемостью), подвергаемых цемантации и закалке с низким отпуском (зубчатые колеса, пальцы шарниров, распределительные валики)
Сталь 20ХФ может применятся в качестве улутшаемой.
Химический состав: Сталь 20ХФ
Химический элемент | % |
Бор (B) | 0.001-0.005 |
Кремний (Si) | 0.17-0.37 |
Медь (Cu), не более | 0.30 |
Марганец (Mn) | 0.60-0.90 |
Никель (Ni) | 0.80-1.10 |
Титан (Ti), не более | 0.06 |
Фосфор (P), не более | 0.035 |
Хром (Cr) | 0.70-1.10 |
Сера (S), не более | 0.035 |
Углерод (С) не более | 0.17-0.23 |
Роль легирующих элементов и углерода
Сталь является многокомпонентным сплавом, содержащим углерод и ряд постоянных или неизбежных примесей Мп, Si, S, Р, О, N, Н и др., которые оказывают влияние на ее свойства. Присутствие этих примесей объясняется трудностью удаления части из них при выплавке (Р, S), переходом их в сталь в процессе ее раскисления (Мп, Si) или из шихты — легированного металлического лома (Cr, Ni и др.). Эти же примеси, но в больших количествах, присутствуют и в чугунах.
Влияние углерода. Структура стали после медленного охлаждения состоит из двух фаз — феррита и цементита. Количество цементита возрастает в стали прямо пропорционально содержанию углерода.
Частицы цементита повышают сопротивление деформации, и, кроме того, они уменьшают пластичность и вязкость. Вследствие этого с увеличением в стали углерода возрастает твердость, временное сопротивление, предел текучести, уменьшаются относительное удлинение, относительное сужение и ударная вязкость.
Влияние кремния и марганца. Содержание кремния в углеродистой стали в качестве примеси обычно не превышает 0,35—0,4 %, а марганца 0,5—0,8 %. Кремний и марганец переходят в сталь в процессе ее раскисления при выплавке. Они раскисляют сталь, т. е. соединяясь с кислородом закиси железа FeO, в виде окислов переходят в шлак; раскисление улучшает свойства стали. Кремний, дегазируя металл, повышает плотность слитка.
Кремний, остающийся после раскисления в твердом растворе (в феррите), сильно повышает предел текучести. Это снижает способность стали к вытяжке и особенно холодной высадке. В связи с этим в сталях, предназначенных для холодной штамповки и холодной высадки, содержание кремния следует брать пониженным.
Влияние серы. Сера является вредной примесью в стали. С железом она образует химическое соединение FeS, которое практически нерастворимо в нем в твердом состоянии, но растворимо в жидком металле. Соединение FeS образует с железом легкоплавкую эвтектику с температурой плавления 988 °С. Эта эвтектика образуется даже при очень малых содержаниях серы. Кристаллизуясь из жидкости по окончании затвердевания, эвтектика преимущественно располагается по границам зерна. При нагревании стали до температуры прокатки или ковки (1000—1200 °С) эвтектика расплавляется, нарушается связь между зернами металла, вследствие чего при деформации стали в местах расположения эвтектики возникают надрывы и трещины. Это явление носит название красноломкости.
Присутствие в стали марганца, обладающего большим сродством к сере, чем железо, и образующего с серой тугоплавкое соединение MnS, практически исключает красноломкость. В затвердевшей стали частицы MnS располагаются в виде отдельных включений. В деформированной стали они вытянуты в направлении прокатки.
Сернистые включения сильно снижают механические свойства, особенно ударную вязкость и пластичность в поперечном направлении вытяжки при прокатке и ковке, а также предел выносливости. Работа зарождения трещины а3 не зависит от содержания серы, а работа развития трещины ар с увеличением содержания серы резко падает. Свариваемость и коррозионную стойкость сернистые включения ухудшают. Содержание серы в стали строго ограничивается, оно не должно превышать 0,035—0,06 %.
Влияние фосфора. Фосфор является вредной примесью, и содержание его в стали допускается не более 0,025—0,045 %.
Растворяясь в феррите, фосфор сильно искажает кристаллическую решетку, при этом увеличиваются временное сопротивление и предел текучести, а пластичность и вязкость уменьшаются. Снижение вязкости тем значительнее, чем больше в стали углерода. Фосфор повышает порог хладноломкости стали и уменьшает работу развития трещины. Сталь, содержащая фосфор на верхнем пределе, для промышленных плавок (0,045 %), имеет работу распространения трещины в 2 раза меньшую, чем сталь, содержащая менее 0,005 % Р. Каждая 0,01 % Р повышает порог хладноломкости стали на 20—25 °С.
Вредное влияние фосфора усугубляется тем, что он обладает большой склонностью к ликвации. Вследствие этого в серединных слоях слитка отдельные участки обогащаются фосфором и имеют резко пониженную вязкость. Современные методы получения стали не обеспечивают глубокого очищения металла от фосфора.
Влияние азота, кислорода и водорода. Азот и кислород присутствуют в стали в виде хрупких неметаллических включений, как твердые растворы или в свободном виде; они располагаются в дефектных участках металла (раковинах, трещинах и др.). Примеси внедрения (азот, кислород), концентрируясь в зернограничных объемах и образуя выделения нитридов и оксидов по границам зерен, повышают порог хладноломкости и понижают сопротивление хрупкому разрушению. Неметаллические включения (оксиды, нитриды, частицы шлаков и т. п.), являясь концентраторами напряжений, могут сильно понизить, если они присутствуют в значительных количествах или располагаются в виде скоплений, предел выносливости и вязкость разрушения.
Очень вредным является растворенный в стали водород, который сильно охрупчивает сталь. Поглощенный при выплавке стали водород не только охрупчивает сталь, но приводит к образованию в катаных заготовках и крупных поковках флокенов. Флокены представляют собой очень тонкие трещины овальной или округлой формы, имеющие в изломе вид пятен — хлопьев серебристого цвета. Флокены резко ухудшают свойства стали. Металл, имеющий флокены, нельзя использовать в промышленности.
Влияние водорода при сварке проявляется в образовании холодных трещин в наплавленном и основном металле.
Широко применяемые в последние годы выплавка или разливка в вакууме значительно уменьшают содержание водорода и других газов в стали.
Молибден, ванадий, вольфрам, хром повышают прочность и вязкость сталей, ухудшая их обрабатываемость. Эти элементы образуют твердые растворы с железом и карбиды различного состава и твердости, как следствие возрастает истирающая способность материала.
Хром значительно снижает теплопроводность стали.
Никель способствует упрочнению стали и снижает обрабатываемость резанием.
megaobuchalka.ru
Доска объявлений | Сталь 20кп – характеристика, химический состав, свойства, твердостьСталь 20кпОбщие сведения
Химический состав
Механические свойстваМеханические свойства
Механические свойства стали после ХТО
Технологические свойства
Температура критических точек
Ударная вязкостьУдарная вязкость, KCU, Дж/см2
Физические свойства
[ Назад ] |
s-metall.com.ua
Доска объявлений | Сталь 20Х – характеристика, химический состав, свойства, твердостьСталь 20ХОбщие сведения
Химический состав
Механические свойстваМеханические свойства при повышенных температурах
Механические свойства проката
Механические свойства поковок
Механические свойства в зависимости от температуры отпуска
Технологические свойства
Температура критических точек
Ударная вязкостьУдарная вязкость, KCU, Дж/см2
Предел выносливости
ПрокаливаемостьЗакалка 860 С. Твердость для полос прокаливаемости HRCэ.
Физические свойства
[ Назад ] |
s-metall.com.ua