Химико термическая обработка металлов и сплавов – Химико-термическая обработка сплавов.
alexxlab | 09.09.2017 | 0 | Вопросы и ответы
Химико-термическая обработка сплавов.
Химико – термическая обработка – технологический процесс, сочетающий термическое воздействие с изменением химического состава поверхностного слоя детали. Технология ХТО состоит в нагреве деталей в специальных активных атмосферах (твердых, жидких, газообразных), т.е. в атмосферах с повышенной концентрацией элемента, изменяющего химический состав поверхностного (приповерхностного) слоя.
Существуют две разновидности ХТО:
1. Диффузионное насыщение сталей и сплавов элементами-металлоидами с меньшим размером атома, чем металл-основа (железо, титан и др.): углеродом, азотом, бором. При этом слой, обогащенный данными элементами, располагается в глубь от поверхности («внутри сплава») (рис. 2.32).
2. Диффузионное насыщение сталей и сплавов металлами: алитирование (Al), хромирование (Cr), цинкование (Zn) и другими элементами. При этом слой, обогащенный данными элементами, располагается на поверхности, образуя покрытие, и частично проникает внутрь металла (рис.2.33).
Рис. 2.32. Химико-термическая обработка сплавов металлоидами
Рис. 2.33. Химико – термической обработка сплавов металлами
Хто с диффузионным насыщением углеродом и азотом
Цементация – вид ХТО, при котором производится диффузионное насыщение поверхностного слоя металла (сплава) углеродом.
Целью обработки является повышение твердости, износостойкости (при хорошем сопротивлении ударным нагрузкам), сопротивления циклическим нагрузкам, циклическим контактным нагрузкам. При этом сохраняется пластичная и вязкая сердцевина детали, что обеспечивает работоспособность в сложных условиях нагружения (рис. 2.34).
Рис. 2.34. Свойства цементованной стальной детали, обеспечивающие сопротивление различным видам нагрузок
Процесс цементации проводят на сталях, содержащих 0,08 – 0,25 % С; это могут быть как углеродистые стали, так и легированные. В результате цементации концентрация углерода в поверхностном слое возрастает до 0,8 – 1,4 % С.
Наиболее распространенные детали, к которым применяется ХТО, это зубчатые колеса, пары трения, кулачки, опоры валов под посадку подшипников.
При химико-термической обработке к параметрам, необходимым любому процессу термообработки, – температуре, времени выдержки, скорости охлаждения, добавляется еще один – среда насыщения (или активность среды насыщения).
Нагрев цементуемых деталей проводится в аустенитной области при температурах 900 – 1000ºС.
Время выдержки зависит от марки стали и от той толщины слоя, который необходимо получить для данной детали. Так, например, на низкоуглеродистых сталях для получения науглероженного слоя глубиной 2 мм при температуре 900 ºС требуется 16 часов, при температуре 950ºС – 10 часов.
Насыщающая среда при цементации называется карбюризатором. Карбюризатор может быть твердым, жидким, газообразным.
При этом цементация всегда протекает через газовую фазу. В насыщающей среде протекают следующие реакции:
В твердой фазе:
ВаСО3 + С → ВаО + 2СО.
На поверхности детали протекает ведущая реакция:
2СО → СО2 + С.
При газовой цементации используется в качестве карбюризатора природный газ (основная часть его – метан), и реакция имеет следующий вид:
СН4 → 2Н2 + С.
В ряде случаев исходную газовую среду активизируют ионизацией в тлеющем разряде. Углерод в виде ионов переносится на насыщаемую поверхность, адсорбируется на ней. Проникновение ионов углерода в глубь детали, т.е. диффузионное насыщение, происходит в аустенитной области. Скорость охлаждения после выдержки при температуре цементации замедленная, с печью. Таким образом, после цементации сталь имеет структуру отжига. После цементации проводят закалку и низкий отпуск. Поверхность детали, которая должна сопротивляться износу и контактным нагрузкам, состоит из высокоуглеродистого мартенсита отпуска и частиц цементита. Толщина упрочненного слоя после цементации составляет 1,5 – 2 мм (но может достигать и 6 мм).
«Двухслойная» структура всей цементованной детали – высокоуглеродистый мартенсит на поверхности и малоуглеродистый мартенсит в сердцевине, различные удельные объемы этих составляющих – обуславливает возникновение сжимающих напряжений в поверхностном слое, которые благоприятны для работы деталей в условиях циклических нагрузок.
Азотирование – процесс насыщения сплавов азотом из газовых сред.
Технология процесса азотирования (температуры, продолжительность), а также сопутствующая термическая и механическая обработки, химический состав применяемых сталей и окончательные свойства отличаются от процесса цементации. Азотирование применяется для сталей, содержащих более сильные нитридообразующие элементы, чем железо: хром, молибден, алюминий. Такими сталями являются низко – и среднеуглеродистые легированные стали марок 38ХМЮА, 20Х2Н4ВА, 30Х3ВА и др.
Азотирование проводят в среде аммиака, который при нагреве диссоциирует в соответствии с реакцией:
2NH3
→ N2 + 3H2.Нагрев проводится в α – области при температурах 500 – 600ºС. Поскольку эти температуры находятся в интервале температур отпуска или старения (для ряда сталей), то процесс насыщения может быть совмещен с термообработкой. Длительность составляет 24 – 60 часов (из-за пониженной по сравнению с цементацией температуры насыщения).
Азотирование является более дорогим процессом, чем цементация, из-за повышенной длительности процесса. Его применяют для ответственных деталей – коленчатых валов, гильз цилиндров, червяков, для деталей сложной формы и тонких сечений, которые не подвергаются последующему шлифованию.
Недостатки: большая длительность процесса, более низкие контактные нагрузки, чем для цементованных деталей, из-за меньшей толщины упрочненного слоя.
Современным прогрессивным способом азотирования является ионное азотирование. Его проводят в специальных установках, в которых детали являются катодом, стенки вакуумной камеры – анодом. В разреженной атмосфере чистого азота при давлении 500 – 1300 Па и напряжении 300 – 800 В возбуждается тлеющий разряд и при этом происходит ионизация азота. Преимущества ионного азотирования состоят в экономичности, хорошей управляемости процессом, применимости не только к легированным, но и к высоколегированным (коррозионностойким) сталям, высокой производительности.
studfiles.net
Химико-термическая обработка металлов — Мегаэнциклопедия Кирилла и Мефодия — статья
Хи́мико-терми́ческая обрабо́тка мета́ллов, одновременное термическое и химическое воздействие на металл с целью изменения состава, структуры и свойств поверхностного слоя обрабатываемого материала. Химико-термической обработке подвергаются изделия из различных сортов стали, чугуна, чистых металлов, сплавов на основе никеля, молибдена, вольфрама, кобальта, ниобия, меди, алюминия. В результате химико-термической обработки можно получить упрочнение поверхностных слоев этих материалов (повышение твердости, усталостной прочности, износостойкости), изменение физико-химических и других свойств (коррозионных, фракционных). От поверхностной закалки данный вид обработки отличается тем, что предварительно производят насыщение поверхности обрабатываемых изделий различными элементами: углерода — цементация, азота — азотирование, углерода и азота — нитроцементация, цианирование, бора — борирование, алюминия — алитирование, кремния — силицирование, хрома — хромирование. Проникая в основную решетку металла, атомы соответствующего элемента образуют твердый раствор внедрения или замещения, либо химическое соединение. Процесс химико-термической обработки протекает в три последовательные стадии. На первой стадии происходит образование активных атомов в насыщающей среде вблизи поверхности или непосредственно на поверхности металла. Этот процесс обусловлен диссоциацией, которая заключается в распаде молекул и образовании активных атомов диффундирующего элемента (например, диссоциацией окиси углерода, сопровождающейся выделением элементарного углерода, или диссоциацией аммиака с выделением азота).Толщина диффузионного слоя, а, следовательно, и толщина упрочненного слоя поверхности изделия, является наиболее важной характеристикой химико-термической обработки. Чем выше концентрация диффундирующего элемента на поверхности, тем больше толщина слоя. Чем выше температура процесса, тем больше скорость диффузии атомов, а следственно, возрастает толщина диффузионного слоя. Границы зерен являются участками, где диффузионные процессы облегчаются из-за наличия большого числа дефектов кристаллического строения. Если растворимость диффундирующего элемента в металле мала, то часто наблюдается преимущественная диффузия по границам зерен
Концентрация диффундирующего элемента на поверхности металла и сплава, а также структура и свойства диффузионного слоя зависят от метода химико-термической обработки. Химико-термическая обработка придает изделиям повышенную износостойкость, жаростойкость, коррозионную стойкость, усталостную прочность.megabook.ru
38. Химико-термическая обработка стали. Назначение, виды и общие закономерности. Диффузионное насыщение сплавов металлами и неметаллами
38. Химико-термическая обработка стали. Назначение, виды и общие закономерности. Диффузионное насыщение сплавов металлами и неметаллами
Химико-термической обработка (ХТО) – обработка с сочетанием термического и химического воздействия для изменения состава, структуры и свойств поверхностного слоя детали в необходимом направлении, при котором происходит поверхностное насыщение металлического материала соответствующим элементом (С, Т, В, Аl, Сг, Si, Т и др.) путем его диффузии в атомарном состоянии из внешней среды при высокой температуре.
ХТО металлов и сплавов как с целью их поверхностного упрочнения, так и для зашиты от коррозии повышает надежность и долговечность деталей машин.
ХТО включает основные взаимосвязанные стадии:
1) образование активных атомов в насыщающей среде и диффузию их к поверхности обрабатываемого металла;
2) адсорбционно-образовавшихся активных атомов поверхностью насыщения;
3) диффузионно-перемещение адсорбированных атомов внутри металла. Развитие процесса диффузии приводит к образованию диффузионного слоя – материала детали у поверхности насыщения, отличающегося от исходного по химическому составу, структуре и свойствам.
Материал детали под диффузионным слоем, не затронутый воздействием насыщающей активной среды, называется сердцевиной. Общая толщина диффузионного слоя – кратчайшее расстояние от поверхности насыщения до сердцевины. Эффективная толщина диффузионного слоя – кратчайшее расстояние от поверхности насыщения до мерного участка, которое отличается установленным предельным номинальным значением базового параметра.
Базовый параметр диффузионного слоя – параметр материала, служащий критерием изменения качества в зависимости от расстояния от поверхности насыщения. Переходная зона диффузионного слоя – прилегающая к сердцевине внутренняя часть диффузионного слоя, протяженность которой определяется разностью общей и эффективной толщин.
Этап ХТО – диффузия. В металлах при образовании твердых растворов замещения диффузия в основном происходит по вакансионному механизму. При образовании твердых растворов внедрения реализуется механизм диффузии по междоузлиям.
Цементация стали – ХТО, заключающаяся в диффузионном насыщении поверхностного слоя стали углеродом при нагревании в карбюризаторе, проводят при 930–950 °C, когда устойчив аустенит, растворяющий углерод в больших количествах.
Для цементации используют низкоуглеродистые, легированные стали. Детали поступают на цементацию после механической обработки с припуском на шлифование.
Основные виды цементации – твердая и газовая. Газовая цементация является более совершенным технологическим процессом, чем твердая. В случае газовой цементации можно получить заданную концентрацию углерода в слое; сокращается длительность процесса; обеспечивается возможность полной механизации и автоматизации процесса; упрощается термическая обработка деталей.
Термическая обработка необходима чтобы: исправить структуру и измельчить зерно сердцевины и цементованного слоя; получить высокую твердость в цементованном слое и хорошие механические свойства сердцевины. После цементации термическая обработка состоит из двойной закалки и отпуска. Недостаток такой термообработки – сложность технологического процесса, возможность окисления и обезуглероживания.
Заключительная операция – низкий отпуск при 160–180 °C, переводящий мартенсит закалки в поверхностном слое в отпущенный мартенсит, снимающий напряжения и улучшающий механические свойства.
Азотирование стали – ХТО, заключающаяся в диффузионном насыщении поверхностного слоя стали азотом при нагревании в соответствующей среде. Твердость азотированного слоя стали выше, чем цементованного, и сохраняется при нагреве до высоких температур (450–500 °C), тогда как твердость цементованного слоя, имеющего мартенситную структуру, сохраняется до 200–225 °C. Азотирование чаще проводят при 500–600 °C.
Диффузионное насыщение сплавов металлами и неметаллами
Борирование – насыщение поверхности металлов и сплавов бором с целью повышения твердости, износостойкости, коррозионной стойкости. Борированию подвергают стали перлитного, ферритного и аустенитного классов, тугоплавкие металлы и никелевые сплавы.
Силицирование. В результате диффузионного насыщения поверхности кремнием повышаются коррозионная стойкость, жаростойкость, твердость и износостойкость металлов и сплавов.
Хромирование – насыщение поверхности изделий хромом. Диффузионному хромированию подвергают чугуны, стали различных классов, сплавы на основе никеля, молибдена, вольфрама, ниобия, кобальта и метал-локерамические материалы. Хромирование производят в вакуумных камерах при 1420 °C.
Алитирование – процесс диффузионного насыщения поверхности изделий алюминием с целью повышения жаростойкости, коррозионной и эрозионной стойкости. При алитировании железа и сталей наблюдается плавное падение концентрации алюминия по толщине слоя.
Назначение поверхностной закалки – повышение твердости, износостойкости и предела выносливости поверхности обрабатываемых изделий. При этом сердцевина остается вязкой и изделие воспринимает ударные нагрузки.
39. Старение. Назначение, изменение микроструктуры и свойств сплавов при старении
Отпуск и старение – это разновидности термической обработки, в результате которой происходит изменение свойств закаленных сплавов.
Термин отпуск принято применять только к тем сплавам, которые были подвергнуты закалке с полиморфным превращением, а термин старение – в случае закалки без полиморфного превращения (после такой закалки фиксируется пересыщенный твердый раствор).
Цель отпуска стали – улучшение ее свойств. Отпуск стали смягчает действие закалки, уменьшает или снимает остаточные напряжения, повышает вязкость, уменьшает твердость и хрупкость стали. Отпуск производится путем нагрева деталей, закаленных на мартенсит до температуры ниже критической.
В отличие от отпуска после старения увеличиваются прочность, твердость, уменьшается пластичность.
Главный процесс при старении – это распад пересыщенного твердого раствора, который получается в результате закалки.
Таким образом, старение сплавов связано с переменной растворимостью избыточной фазы, а упрочнение при старении происходит в результате дисперсных выделений при распаде пересыщенного твердого раствора и возникающих при этом внутренних напряжений.
В стареющих сплавах выделения из пересыщенных твердых растворов встречаются в следующих основных формах: тонкопластинчатой (дискообразной), равноосной (обычно сферической или кубической) и игольчатой. Энергия упругих искажений минимальна для выделений в форме тонких пластин – линз. Основное назначение старения – повышение прочности и стабилизация свойств.
Различают старение естественное, искусственное и после пластической деформации.
Естественное старение – это самопроизвольное повышение прочности (и уменьшение пластичности) закаленного сплава, которое происходит в процессе его выдержки при нормальной температуре. Нагрев сплава увеличивает подвижность атомов, что ускоряет процесс.
Твердые растворы при низких температурах чаще всего распадаются до стадии образования зон. Данные зоны являются дисперсными областями, которые обогащены избыточным компонентом. Они сохраняют ту кристаллическую структуру, которую имел первоначальный раствор. Зоны носят название в честь Гинье и Престона. При использовании электронной микроскопии данные зоны можно наблюдать в сплавах Al – Ag, которые имеют вид сферических частиц диаметром ~10А. Спалавы Al – Cu имеют зоны-пластины, которые имеют толщину <10А.
Искусственное старение – это повышение прочности, происходящее в процессе выдержки при повышенных температурах. Если закаленный сплав, имеющий структуру пересыщенного твердого раствора, подвергнуть пластической деформации, то это ускоряет протекающие при старении процессы. Этот вид старения носит название деформационного. Термическая обработка алюминиевых сплавов состоит из двух циклов – закалки и старения. Старение охватывает все процессы, происходящие в пересыщенном твердом растворе, – процессы, подготавливающие выделение, и процессы выделения. Превращение, при котором происходят только процессы выделения, называется дисперсионным твердением.
Для практики большое значение имеет инкубационный период – время, в течение которого в закаленном сплаве совершаются подготовительные процессы, время, в течение которого закаленный сплав сохраняет высокую пластичность. Это позволяет проводить холодную деформацию непосредственно после закалки.
Если при старении происходят только процессы выделения, без сложных подготовительных процессов, то такое явление называют дисперсионным твердением.
Практическое значение явления старения сплавов очень велико. Так, после старения увеличивается прочность и уменьшается пластичность низкоуглеродистой стали в результате дисперсных выделений в феррите цементита третичного и нитридов.
Старение является основным способом упрочнения алюминиевых сплавов, некоторых сплавов меди, а также многих жаропрочных и других сплавов. В настоящее время все более широко используют мартенситностарею-щие сплавы.
Сегодня достаточно часто вместо термина «естественное старение» используют термин – «низкотемпературное старение», а вместо «искусственного старения» – «высокотемпературное старение». Самыми первыми металлами, которые были упрочнены при помощи старения, были алюминиевые сплавы. Упрочнение проводилось при температурах выше 100 °C.
В разных температурных интервалах наблюдаются различия в процессе распада. Поэтому для получения оптимального комплекса свойств в сплавах применяется сложное старение, проходящее в определенной последовательности, при низких и более высоких температурах.
Старение сплавов, вызванное процессом распада пресыщенного твердого раствора, является наиболее важным. После охлаждения сплавов появляется состояние пресыщения твердого раствора. Это вызвано тем, что при высокой температуре увеличивается растворимость примесей и легирующих компонентов.
Поделитесь на страничкеСледующая глава >
tech.wikireading.ru
Химико-термическая обработка стали, металлов и сплавов: виды, назначение
Существуют различные способы воздействия на сталь с целью придания ей требуемых свойств. Один из комбинированных методов — химико-термическая обработка стали.
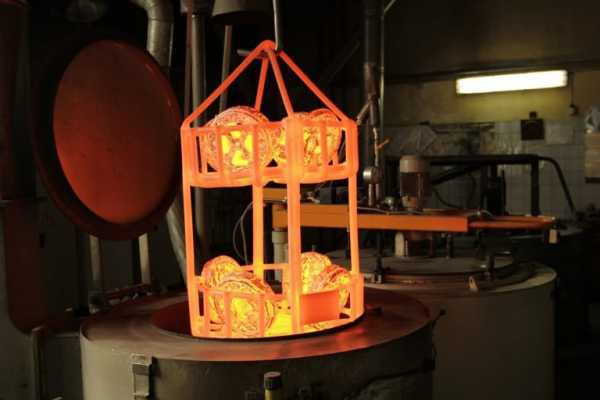
Общие принципы
Суть данной технологии состоит в преобразовании внешнего слоя материала насыщением. Химико-термическая обработка металлов и сплавов осуществляется путем выдерживания при нагреве обрабатываемых материалов в средах конкретного состава различного фазового состояния. То есть, это совмещение пластической деформации и температурного воздействия.
Это ведет к изменению параметров стали, в чем состоит цель химико-термической обработки. Таким образом, назначение данной технологии — улучшение твердости, износостойкости, коррозионной устойчивости. В сравнении с прочими технологиями химико-термическая обработка выгодно отличается тем, что при значительном росте прочности пластичность снижается не так сильно.
Основные ее параметры — температура и длительность выдержки.
Рассматриваемый процесс включает три этапа:
- диссоциацию;
- адсорбцию;
- диффузию.
Интенсивность диффузии увеличивается в случае формирования растворов внедрения и снижается, если вместо них формируются растворы замещения.
Количество насыщающего элемента определяется притоком его атомов и скоростью диффузии.
На размер диффузионного слоя влияют температура и длительность выдержки. Данные параметры связаны прямой зависимостью. То есть с ростом концентрации насыщающего элемента возрастает толщина слоя, а повышение интенсивности теплового воздействия приводит к ускорению диффузии, следовательно, за тот же промежуток времени она распространится на большую глубину.
Большое значение для протекания процесса диффузии имеет растворимость в материале обрабатываемой детали насыщающего элемента. В данном случае играют роль пограничные слои. Это объясняется тем, что ввиду наличия у границ зерен множества кристаллических дефектов диффузия происходит более интенсивно. Особенно это проявляется в случае малой растворимости насыщающего элемента в материале. При хорошей растворимости это менее заметно. Кроме того, диффузия ускоряется при фазовых превращениях.
Классификация
Химико-термическая обработка стали подразделяется на основе фазового состояния среды насыщения на жидкую, твердую, газовую.
В первом случае диффузия происходит на фрагментах контакта поверхности предмета со средой. Ввиду низкой эффективности данный способ мало распространен. Твердую фазу обычно используют с целью создания жидких или газовых сред.
Химико-термическая операция в жидкости предполагает помещение предмета в расплав соли либо металла.
При газовом методе элемент насыщения формируют реакции диссоциации, диспропорционирования, обмена, восстановления. Наиболее часто в промышленности для создания газовой и активной газовой сред используют нагрев твердых. Удобнее всего проводить работы в чисто газовой среде ввиду быстрого прогрева, легкого регулирования состава, отсутствия необходимости повторного нагрева, возможности автоматизации и механизации.
Как видно, классификация по фазе среды не всегда отражает сущность процесса, поэтому была создана классификация на основе фазы источника насыщения. В соответствии с ней химико-термическая обработка стали подразделена на насыщение из твердой, паровой, жидкой, газовой сред.
Кроме того, химико-термическая технология подразделена по типу изменения состава стали на насыщение неметаллами, металлами, удаление элементов.
По температурному режиму ее классифицируют на высоко- и низкотемпературную. Во втором случае производят нагрев до аустенитного состояния, а в первом — выше и оканчивают отпуском.
Наконец, химико-термическая обработка деталей включает следующие методы, выделяемые на основе технологии выполнения: цементацию, азотирование, металлизацию, нитроцементацию.
Диффузионная металлизация
Это поверхностное насыщение стали металлами.
Возможно проведение в жидкой, твердой, газовой средах. Твердый метод предполагает использование порошков из ферросплавов. Жидкой средой служит расплав металла (алюминий, цинк и т. д.). Газовый метод предполагает использование хлористых металлических соединений.
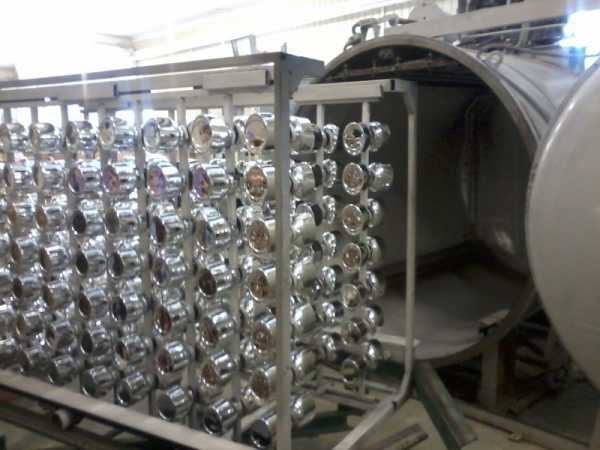
Металлизация
Металлизация дает тонкий слой. Это объясняется малой интенсивностью диффузии металлов в сравнении с азотом и углеродом, так как вместо растворов внедрения они формируют растворы замещения.
Такая химико-термическая операция производится при 900 — 1200°С. Это дорогостоящий и длительный процесс.
Основное положительное качество — жаростойкость продуктов. Ввиду этого металлизацию применяют для производства предметов для эксплуатационных температур 1000 — 1200°С из углеродистых сталей.
По насыщающим элементам металлизацию подразделяют на алитирование (алюминием), хромирование, борирование, сицилирование (кремнием).
Первая химико-термическая технология придает материалу стойкость к окалине коррозии, однако на поверхности после нее остается алюминий. Алитирование возможно в порошковых смесях либо в расплаве при меньшей температуре. Второй способ быстрее, дешевле и проще.
Хромирование тоже увеличивает стойкость к коррозии и окалине, а также к воздействию кислот и т. д. У высоко- и среднеуглеродистых сталей оно также улучшает износостойкость и твердость. Данная химико-термическая операция в основном производится в порошковых смесях, иногда в вакууме.
Основное назначение борирования состоит в улучшении стойкости к абразивному износу. Распространена электролизная технология с применением расплавов боросодержащих солей. Существует и безэлектролизный метод, предполагающий использование хлористых солей с ферробором или карбидом бора.
Сицилирование увеличивает стойкость к коррозии в соленой воде и кислотах, к износу и окалине некоторых металлов.
Науглероживание (цементация)
Это насыщение поверхности стальных предметов углеродом. Данная операция улучшает твердость, износостойкость, а также выносливость поверхности материала. Нижележащие слои остаются вязкими.
Данная химико-термическая технология подходит для предметов из низкоуглеродистых сталей (0,25%), подверженных контактному износу и переменным нагрузкам.
Предварительно необходима механическая обработка. Не цементируемые участки покрывают слоем меди либо обмазками.
Температурный режим определяется содержанием углерода в стали. Чем оно ниже, тем больше температура. Для адсорбирования углерода и диффузии в любом случае она должна составлять 900 — 950°С и выше.
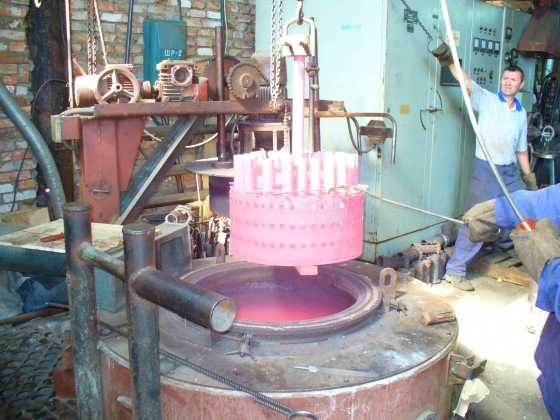
Цементация стали
Таким образом, путем насыщения поверхности стальных деталей углеродом достигают концентрации данного элемента в верхнем слое 0,8 — 1%. Большие значения ведут к повышению хрупкости.
Цементацию осуществляют в среде, называемой карбюризатором. На основе ее фазы технологию подразделяют на газовую, вакуумную, пастами, в твердой среде, ионную.
При первом способе применяют каменноугольный полукокс, древесный уголь, торфяной кокс. С целью ускорения используют активизаторы и повышают температуру. По завершении материал нормализуют. Ввиду длительности и малой производительности данная химико-термическая технология используется в мелкосерийном выпуске.
Вторая технология предполагает использование суспензий, обмазок либо шликеров.
Газовую среду наиболее часто применяют при цементации ввиду скорости, простоты, возможности автоматизации, механизации и достижения конкретной концентрации углерода. В таком случае используют метан, бензол или керосин.
Более совершенный способ — вакуумная цементация. Это двухступенчатый процесс при пониженном давлении. От прочих методов отличается скоростью, равномерностью и светлой поверхностью слоя, отсутствием внутреннего окисления, лучшими условиями производства, мобильностью оборудования.
Ионный метод подразумевает катодное распыление.
Цементация — промежуточная химико-термическая операция. Далее осуществляют закалку и отпуск, определяющие свойства материала, такие как износостойкость, выносливость при контакте и изгибе, твердость. Главный недостаток — длительность.
Азотирование
Данным термином называют насыщение материала азотом. Этот процесс производят в аммиаке при 480 — 650°С.
С легирующими данный элемент формирует нитриды, характеризующиеся дисперсностью, температурной устойчивостью и твердостью.
Такая технология химико-термической обработки увеличивает твердость, стойкость к коррозии и износу.
Необходима предварительная механическая и термическая обработка для придания окончательных размеров. Не азотируемые фрагменты покрывают оловом либо жидким стеклом.
Обычно используют температурный интервал от 500 до 520°С. Это дает за 24 — 90 ч. 0,5 мм слой. Толщина определяется длительностью, составом материала, температурой.
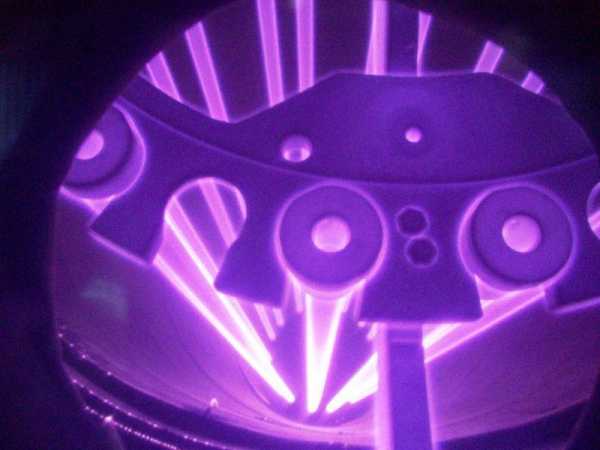
Азотирование
Азотирование приводит к увеличению обрабатываемых деталей вследствие возрастания объема верхнего слоя. Величина роста напрямую определяется его толщиной и температурным режимом.
При жидком способе применяют цианосодержащие, реже бесцианитные и нейтральные соли. Ионная химико-термическая операция отличается повышенной скоростью.
Азотирование подразделяют по целевым свойствам: им достигается или улучшение устойчивости к коррозии, либо повышение стойкости к износу и твердости.
Цианирование, нитроцементация
Это технология насыщения стали азотом и углеродом. Таким способом обрабатывают стали с количеством углерода 0,3 — 0,4%.
Соотношение между углеродом и азотом определяется температурным режимом. С его ростом возрастает доля углерода. В случае пересыщения обоими элементами слой обретает хрупкость.
На размер слоя влияет длительность выдержки и температура.
Цианирование проводится в жидкой и газовой средах. Первый способ называют также нитроцементацией. Кроме того, по температурному режиму оба типа подразделяют на высоко- и низкотемпературные.
При жидком способе используют соли с цианистым натрием. Основной недостаток — их токсичность. Высокотемпературный вариант отличается от цементации быстротой, большими износостойкостью и твердостью, меньшей деформацией материала. Нитроцементация дешевле и безопаснее.
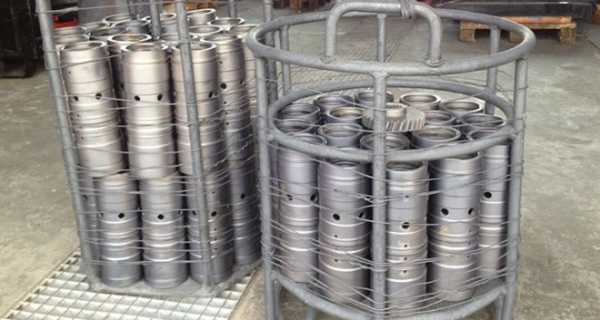
Нитроцементация стали
Предварительно производят окончательную механическую обработку, а не подлежащие цианированию фрагменты покрывают слоем меди в 18 — 25 мкм толщиной.
Сульфидирование, сульфоцианирование
Это новая химико-термическая технология, направленная на улучшение износостойкости.
Первый метод состоит в насыщении материала серой и азотом путем нагрева в серноазотистых слоях.
Сульфоцианирование подразумевает насыщение углеродом, помимо названных элементов.
Если вы нашли ошибку, пожалуйста, выделите фрагмент текста и нажмите Ctrl+Enter.
stankiexpert.ru
Химико-термическая обработка металлов | Термообработка металла
Химико-термическая обработка металлов и сплавов заключается в нагреве и выдержке их при высокой температуре в активных средах, в результате чего изменяются химический состав, структура и свойства поверхностных слоев металлов и сплавов. Для создания такой среды используют твердые, жидкие и газообразные вещества, химический состав н свойства которых определяют изменение химического состава поверхностных слоев обрабатываемого металла. В промышленности широко применяют насыщение углеродом, азотом, совместное насыщение азотом и углеродом, хромом, алюминием. Все шире применяют насыщение бором, кремнием, вольфрамом, а также совместное насыщение несколькими элементами.
Химико-термической обработке подвергаются самые различные металлы и сплавы для придания им специальных свойств: усталостной прочности, износо-, коррозийно- и жаростойкости и пр. За счет применения химико-термической обработки дефицитные металлы можно заменять на более дешевые, легируя соответствующим образом их поверхность. Химико-термическая обработка применяется для тугоплавких металлов, металлокерамических конструкционных материалов и твердых сплавов. Ведутся работы по разработке агрегатов для этой обработки. Продолжаются теоретические и экспериментальные исследования для создания научных основ управления процессами, происходящими при химико-термической обработке.
Химико-термическая обработка состоит из следующих стадий:
- образование активных веществ в окружающей среде или отдельном реакционном объеме;
- транспортировка веществ к поверхности металла, если они возникли в стороне от поверхности насыщаемого металла.
- абсорбция активных атомов или молекул поверхностью металла;
- отвод продуктов реакции в окружающее пространство;
- диффузия.
Абсорбционный процесс
Абсорбционный процесс может включать простую физическую абсорбцию, при которой полнатомиый абсорбционный слой на всей поверхности изделия или в ее активных участках образуется вследствие действия ваи-дер-ваальсовых сил притяжения. Возможна химсорбция с возиикновеиием сильных химических связей между абсорбированными атомами и атомами металлической поверхности.
Условием абсорбции является наличие растворимости и образование химического соединения. Имеются две точки зрения на первичные образования. По первой вначале образуется химическое соединение, а затем идут процессы растворения и диффузии, по второй вначале происходит растворение абсорбирующих атомов, а затем возможно образование химического соединения. Экспериментально наблюдается второй случай.
Ускорение процесса
Для ускорения процессов химико-термической обработки перспективно применение электрического тока (электро-химико- термическая обработка ЭХТО): метод тлеющего разряда, метод цементации с применением ТВЧ, ТПЧ и электроконтактного нагрева.
Это позволяет повысить скорость процессов химико-термической обработки, во много раз сократить время (часто до нескольких минут). Применение ЭХТО позволяет управлять структурой диффузионного слоя, повышать его пластичность и работоспособность. По методу тлеющего разряда электрический ток пропускается через слой частиц проводящих материалов, находящихся в недосжиженном состоянии, и изделие. Применение тлеющего разряда, например при азотировании, приводит к расщеплению молекулы азота. Образовавшиеся атомы азота абсорбируются поверхностью стали. Метод тлеющего -разряда в небольшом размере применяется на практике и при других видах насыщения. Возникновение тлеющего разряда
Происходит при включении тока высокого напряжения (900 – 1100 В) между изделиями, которые служат катодом и крышкой (анодом). При этом в контейнере, где находятся изделия, поддерживается низкое давление (1 – 10 мм рт. ст.). При использовании тлеющего разряда интенсифицируются химические -реакции в окружающей среде, ускоряются процессы абсорбции, хемсорбции, диффузии, изменяются активность и структурное состояние поверхностных слоев металла.
Диффузионное насыщение
Для диффузионного насышения металлов и сплавов применяют порошковый (твердофазный), жидкий (жидкофазный), безэлектролизный, электролизный, газовый (газофазный) методы. Разрабатывают также вакуумный, гальвано-диффузионный, шликерный методы (из паст и суспензий) в кипящем или виброкипящем слое, в тлеющем разряде и другие методы насыщения.
При твердофазном насыщении могут протекать два процесса: а) образование и доставка (перенос) активных атомов, насыщающих элементов через газовую фазу, заполняющую все зазоры между частицами порошковой смеси; б) твердофазная диффузия в местах контакта (плотного соприкосновения) частиц порошковой смеси с насыщаемым металлом. Эффект насыщения зависит от размера частиц насыщающей порошковой смеси и активатора процесса. Скорость насыщения зависит от площади контактной поверхности взаимодействующих составляющих смеси и растет с повышением ее. Толщина слоя увеличивается с уменьшением размеров зерна. Однако, вероятно, значение твердофазной диффузии при насыщении в порошковых смесях мало.
Перспективным методом диффузионного насыщения, особенно многокомпонентного, является электронно-лучевое напыление с последующим диффузионным отжигом Предварительно изготавливаются заготовки из материала, имеющего в своей’ составе требуемые для насыщения элементы, затем при помощи электронной пушки напыляют на деталь слой, состоящий из; требуемых компонентов. Деталь с напыленным слоем отжигают для получения заданной глубины слоя.
Похожие материалы
www.metalcutting.ru
Химико-термическая обработка
Химико-термической обработкой называется процесс поверхностного насыщения стали различными элементами, путем их диффузии из внешней среды при высокой температуре. Цель химико-термической обработки-поверхностное упрочнение металлов и сплавов и повышение их стойкости против воздействия внешних агрессивных сред при нормальной и повышенной температурах.
Процессы химико-термической обработки состоят из трех стадий :
диссоциации, которая заключается в распаде молекул и образовании активных атомов
диффундирующего элемента .Например, диссоциации окиси углерода 2СО-СО2+С или аммиака 2НN3-3Н2+2N;
адсорбиции, т.е. кантактирования атомов диффундирующего элемента с поверхностью стального изделия и образования химических связей с атомами металла; диффузии, т.е. проникновения насыщающего элемента в глубь металла.
Скорость диффузии при проникновении диффундирующих атомов в решетку растворителя будет выше, если при взаимодействии образуется твердые растворы внедрения, и значительно ниже, если образуются твердые растворы замещения.
Концентрация диффундирующего элемента на поверхности зависит от притока атомов этого элемента к поверхности и от скорости диффузионных процессов, т.е. отвода этих атомов в глубь металла.
Толщина диффузионного слоя зависит от температуры нагрева, продолжительности выдержки при насыщении и концентрации диффундирующего элемента на поверхности.
Чем выше концентрация диффундирующего элемента на поверхности детали, тем выше толщина слоя. Чем выше температура процесса, тем больше скорость диффузии атомов, а следственно, возрастает толщина диффузионного слоя.
Границы зерен являются участками, где диффузионные процессы облегчают из-за наличия большого числа дефектов кристаллического строения. Если растворимость диффундирующего элемента в металле мала, то часто наблюдается преимущественная диффузия по границам зерен. При значительной растворимости диффундирующего элемента в металле роль пограничных слоев уменьшается. В момент фазовых превращений диффузия протекает быстрее.
Цементация
Цементацией называется процесс насыщения поверхностного слоя стальных изделий углеродом. Цементация осуществляется с целью получения высокой твердости на поверхности изделия при сохранении вязкой сердцевины, она способствует повышению износостойкости и предела выносливости.
Цементацией подвергают детали из низкоуглеродистых сталей (до 0,25% ), работающие в условиях контактного износа и знакопеременных нагрузок (втулки, поршневые пальцы, кулачки, колонки и т.д.) .
Для цементации детали поступают после механической обработки с припуском на шлифование 0,05-0,10мм. Участки, не подлежащие цементации, защищают тонким слоем меди, наносимым электрическим способом, или специальными обмазками ,состоящими из смеси огнеупорной глины, песка и асбеста, замешанных на жидком стекле.
Цементация осуществляется при температурах выше 900-950с. Чем меньше углерода в стали, тем выше температура нагрева для цементации. При этих температурах атомарный углерод адсорбируется на поверхности стали и диффундирует в глубь металла.
В результате цементации содержание углерода в поверхностном слое составляет 0,8-1,0 %. Более высокая концентрация углерода способствует охрупчиванию цементованного слоя.
Среда, в которой проводят цементацию, называют карбюризатором.
Цементация в твердой среде.
Карбютизатором является активированный древесный уголь, а также каменноугольный полукокс и торфяной кокс. Для ускорения процесса к древесному углю добавляют активизаторы – углекислый барий, кальцинированную соду, поташ в количестве 10-40% от массы угля.
Обычная рабочая смесь, применяется для цементации, состоит из 25-35% свежего карбюризатора и 65-75% отработанного.
Подготовленнные для цементации изделия укладывают в металлический ящик. Предварительно в ящик насыпают слой карбюризатора 20-30см. Детали укладывают слоями на расстоянии 10-15 мм друг от друга. Каждый слой детали засыпают карбюризатором и на него укладывают следующий слой деталей.
Повышенная температура цементации до 950-1000с позволяет значительно ускорить процесс, но такой режим применим для наследственно мелкозернистых сталей.
После цементации детали подвергают нормализации для измельчения зерна, повторной закалке и низкотемпературному отпуску. В результате такой обработки поверхностный слой приобретает структуру мартенсита отпуска с включениями избыточных карбидов с твердостью HRC 60-63.
Структура сердцевины зависит от состава стали и режима закалки. У углеродистых сталей она состоит из феррита и сорбита или троостита, а у легированных из малоуглеродистого мартенсита.
Цементация пастами.
Процесс заключается в нанесение на поверхность обрабатываемой детали слоя вещества в виде суспензии, обмазки или шликера, в сушке и последующим нагреве. Вид пасты определяет технологию ее нанесения. Паста сравнительно жидкой консистенции наносится на детали окунанием, а более густо-с помощью кисти. Толщина слоя пасты должна быть в 6-8 раз больше заданной глубины цементованного слоя. Основными компонентами паст являются сажа и кальцинированная сода, кокс малосернистый, сода или поташ.
Высушенные детали аккуратно, чтобы не повредить слой пасты, укладывают одна на другую в ящик и закрывают его крышкой. Ящик загружают в печь с температурой 950-1050с; чем выше температура нагрева, тем меньше длительность процесса. Кроме того, для нагрева деталей можно применять токи высокой и промышленной частоты.
По окончанию выдержки детали охлаждают в ящиках на воздухе. Можно осуществить также подсуживание до закалочной температуры и произвести закалку непосредственно с цементационного нагрева.
Газовая цементация. В настоящие время газовая цементация является основным процессом цементации на заводах массового производства. При газовой цементации сокращается длительность процесса, так как отпадает необходимость прогрева ящиков, можно обеспечивать более полную механизацию и автоматизацию процесса, упрощается последующая термическая обработка и, самое главное, можно получить заданную концентрацию углерода в слое.
Цементацию выполняют в шахтных, муфельных или безмуфельных печах непрерывного печах непрерывного действия.
При цементации в шахтных печах для получения науглероживающей атмосферы применяют метан, керосин, синтин, бензол.
В печах непрерывного действия чаще используют метан. Для получения заданной концентрации углерода применяют атмосферы с регулируемым потенциалом углерода .
Под углеродным потенциалом атмосферы понимают определенную концентрацию углерода на поверхности цементованного слоя. Для ускорения процесса углеродный потенциал атмосферы в печи меняют по зонам. Вначале его поддерживают высоким, обеспечивающим получение в поверхностном слое концентрации углерода 1,3-1,4%, а затем его снижают для получения в этом слое оптимального содержания углерода 0,8%.
После газовой цементации применяют закалку непосредственно из цементационной печи предварительно сделав подстуживание до температуры 850-830с. Заключительной операцией является низкотемпературный отпуск при температуре 160-180с.
Азотирование
Азотированием называется процесс насыщения поверхности стали азотом. Процесс осуществляется в среде аммиака при температуре 480-650с. При этих температурах выделяется атомарный азот, который диффундирует в поверхностные слои детали.
При азотировании легированных сталей азот образуется с легирующими элементами устойчивые нитриды, которые придают азотированному слою высокую твердость.
Твердость поверхностного слоя деталей после азотирования достигает HV 11000-12000.
Перед азотированием детали подвергают термической обработке, состоящей из закалки и высокотемпературного отпуска. Затем производят механическую обработку, придающую окончательные размеры изделию.
Участки, не подлежащие азотированию, защищают тонким слоем олова, нанесенным электролитическим методом, или жидким стеклом. В процессе азотирования олово расплавляется и благодаря поверхностному натяжению удерживается на поверхности стали в виде тонкой непроницаемой для азота пленки.
Обычно процесс азотирования ведут при температурах 500-520с. В этом случае получают толщиной до 0,5мм за 24-90ч.
В процессе азотирования изменяются размеры деталей за счет увеличения объема поверхностного слоя. Чем выше температура процесса и больше толщина азотированного слоя, тем больше изменение размеров детали.
Процесс жидкого азотирования осуществляется при температуре 570с в расплаве цианосодержащих солей. В ходе процесса расплав непрерывно продувается сухим и чистым воздухом, что обеспечивает превращения цианида в цианат, являющийся поставщиком атомов углерода и азота.
Менее распространены процессы азотирования в бесцианистых солях, содержащих азот и в расплавах нейтральных солей, через которые продувают аммиак.
Широкое применение получает ионное азотирование. По сравнению с газовым азотированием оно имеет ряд преимуществ: меньшую продолжительность процесса, более высокое качество азотированного слоя, пониженную хрупкость слоя.
Рабочее давление в камере печи составляет 130-1300Па. При более высоком давлении тлеющий разряд становится менее стабильным и чаще переходит в дуговой. Это может вызвать перегрев поверхности и даже ее оплавление.
Цианирование и нитроцементация.
Цианирование называется процесс одновременного насыщения поверхности деталей углеродом и азотом.
На состав и свойства цианированного слоя особое влияние оказывает температура процесса. Повышение температуры цианирования ведет к увеличению содержания углерода в слое, снижает температуры- к увеличению содержания азота.
Толщина цианированного слоя также зависит от температуры-и продолжительности процесса. Для цианирования применяют стали, содержащие 0,3-0,4% углерода.
Различают жидкое и газовое цианирование. Газовое цианирование еще называют нитроцементацией. Жидкое цианирование проводят в расплавленных солях, содержащих цианистый натрий NACN. Примерный состав ванны следующий:20-25% NACN; 25-50% Nacl и 25-50% Na2CO3.
Первый состав применяют для цианирования при 820-850С, второй -при 900-950С.
Цианирование при температурах 820-850С позволяет осуществлять закалку непосредственно из ванны. После закалки следует низкотемпературный отпуск. Твердость цианированного слоя после термической обработки HRC 59-62.
Цианирование при температурах 820-850С позволяет получать слои толщиной 0,15-0,35 мм за 30-90 минут. Глубокое цианирование имеет ряд преимуществ по сравнению с цементацией: меньше продолжительность процесса для получения слоя заданной толщины; меньше деформация и коробление; более высокое сопротивление износу и повышенная усталостная прочрость.
После цианирования детали охлаждают на воздухе, повторно нагревают для закалки и проводят низкотемпературный отпуск.
Недостатком цианирования является ядовитость цианистых солей. Поэтому цианирование проводят в специально выделенных помещениях с соблюдением мер предосторожности.
Нитроцементацию осуществляют при температурах 840-860С в газовой смеси из неуглероживающего газа и аммиака. Продолжительность процесса зависит от глубины насыщаемого слоя и составляет 1-10 ч. Толщина слоя колеблется от 0,1 до 1 мм.
После нитроцементации изделия подвергают закалке и низкотемпературному отпуску при температуре 160-180С.
Низкотемпературное цианирование осуществляется при температурах 540-560С в расплавленных цианистых солях.
Низкотемпературному цианированию подвергают инструмент из быстрорежущих сталей для повышения его стойкости при резании. В результате такой обработки образуется нитроцементованный слой толщиной 0,02-0,04мм твердостью HV 9500-11000. Длительность процесса 1-1,5 часа.
Нитроцементация в твердых смесях применяется для повышения стойкости инструментов из быстрорежущей стали. Инструменты укладываются в металлические ящики и пересыпаются смесью, состоящей из 60-80% древесного угля и 20-40% желтой кровяной соли или другого состава. Потом ящики закрывают и устанавливают в печь с температурой 550-560С. После выдержки 2-3ч ящики выгружают из печи и охлаждают до 200-100С. Затем ящики раскрывают и вынимают инструмент, очищая металлическими щетками.
Хрупкость слоя возникает при пересыщении слоя углеродом и азотом, когда образуется сетак или сплошная корка карбонитридов у самой поверхности.
«Темная составляющая» в структуре возникает после нитроцементации в виде темной разорванной или сплошной сетки, обнаруживаемой на нетравленных микрошлифах. Причина: повышенная концентрация азота, увеличение времени выдержки и появление окисляющих газов в рабочем пространстве печи.
Диффузионная металлизация.
Диффузионной металлизация-это процесс диффузионного насыщения поверхностных слоев стали различными металлами. Она может осуществляться в твердых, жидких и газообразных средах.
При диффузионной металлизации в твердых средах применяют порошкообразные смеси, состоящие из ферросплавов с добавлением хлористого аммония в количисве 0,5-5%.
Жидкая диффузионная металлизация осуществляется погружением детали в расплавленный металл (например цинк, алюминий).
При газовом способе насыщения применяют летучие хлористые соединения металлов, образующиеся при взаимодействии хлора с металлами при высоких температурах .
Диффузия металлов в железе идет значительно медленнее, чем углерода и азота, потому что углерод и азот образуют с железом твердые растворы внедрения, а металлы – твердые растворы замещения. Это приводит к тому, что диффузионные слои при металлизации получаются в десятки раз более тонкими.
Поверхностное насыщение стали металлами проводится при температуре 900-1200С.
Алитированием называется процесс насыщения поверхности стали алюминием. В результате алитирования сталь приобретает высокую окалиностойкость и коррозионную стойкость в атмосфере и в ряде сред.
При алитировании в порошкообразных смесях чистые детали вместе со смесью упаковывают в железный ящик.
Алитирование в расплавленном алюминии отличается от алитирования в порошкообразных смесях простотой метода, быстрой и более низкой температурой.
Основным недостатком является- налипание алюминия на поверхность детали.
Алитированные стали металлизацией с последующим диффузионным отжигом в несколько раз дешевле, чем в порошках.
Алитированием подвергают трубы, инструмент для литья цветных сплавов, чехлы термопар, детали газогенераторных машин и т.д.
Хромирование проводят для повышения коррозионной стойкости, кислотостойкости, окалиностойкости и т.д. Хромирование средне- и высокоуглеродистых сталей повышает твердость и износостойкость.
Хромирование чаще всего проводят в порошкообразных смесях. Процесс происходит при температуре 1000-1050С.Диффузионный слой, получаемый при хромировании углеродистых сталей, состоит из карбидов хрома. Карбидный слой имеет высокую твердость HV 12000-13000. Толщина хромированного слоя достигает 0,15- 0,20 мм при длительности процесса 6-15ч.Чем больше углерода в стали, тем меньше толщина слоя.
Иногда применяют хромирование в вакууме. Издели засыпают кусочками хрома в стальном или керамическом тигле и помещают в вакуумную печь.
Хромирование применяют для пароводяной арматуры, клапанов, вентилей.
Борированием называется насыщение стали бором. Борирование проводят с целью повышения стойкости против абразивного износа. Толщина борированных слоев не превышает 0,3мм, твердость HV 18000-20000.
Широкое распространение получил метод электролизного борирования в расплавленных солях, содержащих бор. Деталь служит катодом в ванне с расплавленной бурой. Температура процесса 900-950С. Процесс можно вести и без электролиза в ваннах с расплавленными хлористыми солями, в которые добавляют порошкообразный ферробор или карбид бора.
Борированию подвергают втулки грязевых нефтяных насосов, штампы.
Силицированием называется процесс насыщения поверхности стали кремнием. В результате силицирования сталь приобретает высокую коррозионную стойкость в морской воде, в различных кислотах и повышенную износостойкость. Кроме того, силицирование резко повышает окалиностойкость молибдена и некоторых других металлов и сплавов.
Силицированный слой представляет собой твердый раствор кремния в а-железе. Силицированный слой несмотря на низкую твердость (HV 2000-3000) и пористость после пропитки маслом при температуре 170-200С имеет повышенную износостойкость.
При газовом силицировании при температуре 1000С в течение 2-4ч образуется слой толщиной 0,5-1,0 мм.
Силицированием подвергают детали, применяемые а оборудовании химической, бумажной и нефтяной промышленности.
coolreferat.com
Термическая обработка и химико-термическая обработка металлов и сплавов.
Термическая обработка – один из широко применяемых методов улучшения свойств металлических материалов и изделий из них. Под термической обработкой понимают процесс тепловой обработки, при котором заданные физико-механические свойства (высокая твердость, пластичность, износостойкость) достигаются за счет изменения кристаллической структуры, но без изменения химического состава материалов. Термической обработке подвергаются сталь, чугун и некоторые сплавы цветных металлов.
К термической обработке относятся: отжиг, закалка, отпуск, нормализация (термическое улучшение), обработка холодом.
Любой процесс термической обработки можно описать графиком, показывающим изменение температуры во времени. По такому графику можно определить температуру нагревания, время нагревания и охлаждения, средние и истинные скорости нагревания и охлаждения, время выдержки при температуре нагревания и общую продолжительность производственного цикла. Но по форме этого графика ничего нельзя сказать о том, с каким видом термообработки мы имеем дело. Вид термообработки определяется не характером изменения температуры во времени, а типом фазовых и структурных изменений в металле.
На основе классификации А. А. Бочвара Комиссией по стандартизации Совета Экономической Взаимопомощи были разработаны классификация видов и разновидностей термической обработки сталей и цветных металлов и сплавов, а также соответствующая терминология. На рисунке приведена схема классификации основных видов термической обработки металлов и сплавов.
Рисунок 1.2.2. Схема классификации основных видов термической обработки металлов и сплавов.
Термическая обработка подразделяется на собственно – термическую, химико-термическую и термомеханическую (или деформационно-термическую).
Собственно – термическая обработка заключается только в термическом воздействии на металл или сплав, химико-термическая – в сочетании термического и химического воздействия, термомеханическая – в сочетании термического воздействия и пластической деформации.
Собственно – термическая обработка включает следующие основные виды: отжиг первого рода, отжиг второго рода, закалку с полиморфным превращением, закалку без полиморфного превращений, отпуск и старение. Эти виды термической обработки относятся и к сталям, и к цветным металлам и сплавам.
Каждый из видов собственно термообработки подразделяется на разновидности, специфические для сплавов на разных основах. Химико-термическая и термомеханическая обработки имеют разновидности, рассматриваемые в соответствующих главах.
Химико-термическая обработка – это такая обработка металлов, при которой производится одновременно тепловое и химическое воздействие на обрабатываемое изделие. Для химико-термической обработки детали нагревают в специальной среде (карбюризаторе) до определенной температуры, выдерживают при этой температуре и затем охлаждают.
В процессе нагрева поверхностный слой деталей насыщается активным элементом (углеродом, азотом, алюминием, хромом и др.), в результате чего изменяются его физико-механические свойства.
Химико-термическая обработка предназначена для изменения химического состава поверхностных слоев стальных деталей машин и других изделий и придания им требуемых физико-механических свойств: высокой твердости, износостойкости, коррозионно- и окалиностойкости, а также красностойкости.
К химико-термической обработке относятся цементация (науглероживание), цианирование, азотирование, хромирование, силицирование, сульфидирование, борирование, алитирование и др.
Химико-термическая обработка металлов, совокупность технологических процессов, приводящих к изменению химического состава, структуры и свойств поверхности металла без изменения состава, структуры и свойств его сердцевидных зон. Осуществляется с помощью диффузионного насыщения поверхности различными элементами при повышенных температурах. Выбор элемента (или комплекса элементов) определяется требуемыми свойствами поверхности детали. Насыщение производят углеродом (цементация), азотом (азотирование), азотом и углеродом (нитроцементация, цианирование), металлами, бором (борирование), кремнием (силицирование) и т.д.
В зависимости от физико-химического состояния среды, содержащей диффундирующий элемент, различают химико-термическую обработку из газовой, жидкой, твёрдой или паровой фазы (чаще применяются первые два метода). Химико-термическая обработка проводится в газовых, вакуумных или в ванных печах. Химико-термическая обработка подвергаются изделия из стали, чугуна, чистых металлов, сплавов на основе никеля, молибдена, вольфрама, кобальта, ниобия, меди, алюминия и др.
Физико-химические процессы, происходящие вблизи поверхности при химико-термической обработке, заключаются в образовании диффундирующего элемента в атомарном состоянии вследствие химических реакций в насыщающей среде или на границе раздела среды с поверхностью металла (при насыщении из газовой или жидкой фазы), сублимации диффундирующего элемента (насыщение из паровой фазы), последующей сорбции атомов элемента поверхностью металла и их диффузии в поверхностные слои металла. Концентрация диффундирующего элемента на поверхности металла, а также структура и свойства диффузионного слоя зависят от метода химико-термической обработки. Глубина диффузии элемента возрастает с повышением температуры (по экспоненциальному закону) и с увеличением продолжительности процесса (по параболическому закону). Диффузионный слой, образующийся при химико-термической обработки деталей, изменяя структурно-энергетическое состояние поверхности, оказывает положительное влияние не только на физико-химические свойства поверхности, но и на объёмные свойства деталей. Химико-термическая обработка позволяет сообщить изделиям повышенную износостойкость, жаростойкость, коррозионную стойкость, усталостную прочность и т.д.
cyberpedia.su