Закалка и отпуск – —
alexxlab | 19.12.2019 | 0 | Вопросы и ответы
Закалка и отпуск в кустарных условиях – Кузнечное дело
Нагрев под закалку можно осуществить различными способами,но поскольку у меня только кузнечный горн(угольный) буду плясать от него.И так разжигаем даём разгореться ждём появления жара,если греем малоуглеродистую и низколегированную сталь греть можно быстро и сразу до температуры закалки(или ковки).Если сталь с большим содержанием углерода или высоколегированная,то кладём на жар и сразу перекрываем подачу воздуха в горн,таким сталям требуется медленный нагрев до температуры примерно в 600гр,после этого можно включить форсированное дутьё и греть до температуры закалки быстро.В связи с чем такая тактика с нагревом?Всё потому что малоуглеродистые(и низколегированные) стали имеют хорошую теплопроводность и тепло с наружных слоёв быстро достигает глубины,чем больше процент углерода(хрома,вольфрама и тд) тем теплопроводность ниже и при нагреве возникнут большие внутренние напряжения которые могут перейти в трещины,после 600гр теплопроводность повышается и поэтому можно греть быстро.Так же скорость нагрева зависит от размера и формы детали,соответственно чем более крупную деталь хотим закалить тем медленнее греем(особенно если там легирующих добавок куча) .Детали с неравномерным сечением толстой частью кладём в жар,её больше тепла для нагрева нужно,мелкие детальки лучше греть в подходящей посудине(совке,плошке,куске трубы с приваренным дном,
www.chipmaker.ru
8 (916) 934-09-47 WhatsApp: +7(916) 934-09-47 Viber: +7(916) 934-09-47 E-mail: |
Для закалки изделия нагревают до высокой температуры, а затем быстро охлаждают в специальных охлаждающих средах. В зависимости от режима закалки одна и та же сталь получает различ-ные структуры и свойства. Для получения наилучших результатов изделие равномерно нагревают до температуры 740-850°С… Назначение закалки заключается в том, чтобы придать изделию высокую твердость и прочность. Однако при закалке с повышением твердости сталь становится более хрупкой. Для закалки изделия нагревают до высокой температуры, а затем быстро охлаждают в специальных охлаждающих средах. В зависимости от режима закалки одна и та же сталь получает различ-ные структуры и свойства. Для получения наилучших результатов изделие равномерно нагревают до температуры 740-850°С и затем быстро охлаждают до 400-450°С. Скорость охлаждения долж-на быть не менее 150°С в секунду, т. е. охлаждение должно произойти в течение всего 2-3 с. Дальнейшее охлаждение, ниже 300°С, может протекать при любой скорости, так как полученная при закалке структура достаточно устойчива и скорость дальнейшего охлаждения на нее не оказы-вает влияния. В качестве охлаждающих сред чаще всего употребляются вода и трансформатор-ное масло. Скорость охлаждения в воде больше, чем в масле. При температуре воды 18°С скорость охлаждения достигает 600°С в секунду, а в масле — до 150°С в секунду. Для придания изделию большей твердости закалку производят в проточной воде. При охлаждении горячей поковки в стоячей воде между водой и поковкой возникает слой пара, который изолирует нагретую поковку от охлаждающей среды. Поэтому во избежание этого пользуются проточной водой. Иногда для повышения закаливающей способности в воду добавляют поваренную соль (до 10%) или серную кислоту (до 10-12%). Нагрев изделия выше критической точки придает металлу крупнозернистое строение, а это приво-дит к нежелательным последствиям: короблению, деформации и появлению трещин. К этому же приводит и быстрое охлаждение. При закалке инструментов применяются закалочные печи, которые делятся на камерные, или пламенные, где изделие нагревается открытым пламенем; электрические муфельные; печи-ванны, представляющие собой тигли, наполненные расплавами солей, например хлористым барием. Нагревание в ваннах наиболее удобно, вследствие того что температура ванны всегда постоянная и закаливаемый инструмент не может нагреться выше этой температуры. Кроме того, нагрев в жидких средах идет в два раза быстрее, чем в воздушной среде, а в расплавленном металле-в четыре раза быстрее. Например, для закалки мелких стальных изделий используют расплавлен-ный свинец. Мелкие заготовки погружают в ванны и сверху кладут древесный уголь, который при горении на поверхности свинца создает восстановительное пламя — свинец не окисляется. Чтобы свинец не оседал на стальных изделиях, их смазывают мучным клейстером с поваренной солью. При нагревании инструмента в муфелях применяются следующие режимы
В последнее время для нагрева под закалку применяют токи высокой частоты. акаливаемую деталь помещают в специальный индуктор, по которому пропускают ток высокой частоты, и деталь очень быстро нагревается до необходимой температуры. После закалки необходимо произвести отпуск. Он смягчает действия закалки, повышает вязкость и уменьшает хрупкость и твердость изделия. Кроме того, отпуск устраняет или снижает напряже-ние, вызванное закалкой. Для определения температуры отпуска очень часто до сих пор пользу-ются цветами побежалости. Если очищенное от окалины стальное изделие нагревать, то начиная с температуры 220°С на нем образуется тонкая пленка оксидов железа, придающая изделию различные цвета от светло-желтого до серого. С повышением температуры или увеличением времени пребывания изделия при данной температуре оксидная пленка утолщается и цвет ее изменяется. Цвета побежалости одинаково появляются как на сырой, так и на закаленной стали. При отпуске закаленных инструментов применяют два способа.
При закалке инструмента с двумя концами, например кирки, молотка и т. д., трудность заключается в том, что в изделии только два рабочих конца должны быть закалены, а середина должна быть незакаленной. Закалку производят за один нагрев. Изделие равномерно нагревают до нужной температуры и в воду опускают в первую очередь конец, имеющий меньшую массу, т. е. тот, который может быстрее охладиться. При охлаждении в воде конца только рабочей части нужно внима-тельно следить за нагретым вторым концом, чтобы он не охладился. Быстро вынув первый конец и зачистив его шкуркой, второй (только рабочую часть) погружают в воду. При этом следят за цвета-ми побежалости первого конца; когда появляется нужный цвет, снова опускают первый конец в воду, второй быстро зачищают и следят за цветами на втором конце. При появлении нужного цве-та также замачивают в воде. Так, периодически меняя положение концов, изделие остужают. Запас температуры должен оставаться в средней части инструмента, поэтому при закалке пользуются клещами с узкими губками. Большие плоскости холодных губок клещей отбирают теплоту в зоне прикосновения. Для закалки более мелких изделий можно использовать клещи с массивными губками, изделие в этом случае нагревают вместе с клещами. Прием с клещами применяется при местном отпуске, когда в каком-то участке стального закаленного изделия нужно сделать отвер-стие, а его, твердость не позволяет это сделать. Для этого берут клещи нужного размера, нагре-вают их до красного, или светло-красного каления и захватывают металл в зоне будущего отверстия. За отпуском металла можно следить по цветам побежалости. Этот прием используется при отпус-ке тонких стальных изделий кос, пил и т. д. В процессе нагрева стальных изделий происходит их окисление и обезуглероживание. Получение на поверхности окалины идет за счет образования оксидов железа.
Обезуглероживание состоит в выгорании углерода с поверхности изделия. Обезуглероженный слой обладает пониженной твердостью и прочностью. В наше время больших научных и технических достижений древнее ремесло кузнеца не исчезло. Изделия современных кузнецов находят применение в нашем быту. Творения, созданные руками художников-кузнецов, гармонично сочетаются с фасадами и внутренней архитектурой зданий, яв-ляясь одновременно самостоятельным художественным произведением. Ажурный орнамент кова-ных решеток красиво сочетается со стройными линиями современной архитектуры. Умелое ис-пользование новых видов обработки металла электросварки, газовой, автогенной и т. д. дают художникам-кузнецам более широкие возможности использования и применения своего ремесла. Старые технологические приемы оживают вновь при восстановлении разрушенных памятников культуры. Кузнечное дело, как и всякая рукодельная работа, является средством пропаганды эсте-тической мысли и чувств и не теряет своего значения в период высокоразвитой промышленности. В заключение следует отметить, что для успешной работы в области художественной обработки металлов, прежде всего необходимо овладеть простейшими слесарными операциями, т. е. уметь работать зубилом, молотком, напильником, сверлом, шабером и др. Навыки по выполнению этих слесарных работ необходимы мастерам и художникам прикладного искусства, так как они постоянно применяются при первоначальной обработке деталей, их сборке и монтировке в целые готовые изделия. |
www.tsibar.ru
Как осуществляется закалка и отпуск стали
Закалка и отпуск стали проводятся с целью придания сплаву максимальной твердости, прочности и упругости. Обработанный металл обладают лучшими свойствами, чем обыкновенный материал, лучше переносит работу в неблагоприятных условиях и в агрессивных средах. Основной способ закалки состоит в нагревании стали до определенной температуры и поддержании достигнутого уровня в течение установленного времени, а затем резком охлаждении материала. Это позволяет подготовить металл к последующей эксплуатации.
Структура стали после закалки приобретает аустенитный вид. Это означает, что атомы углерода внедряются в кристаллическую решетку железа, что придает сплаву максимальную устойчивость связей и, как следствие, повышенную прочность на износ. Такой способ обработки является одним из самых дешевых методов продления эксплуатационного цикла использования стальных изделий. Он не требует применения дорогостоящих материалов, которые внедряют в сплав для улучшения физических и химических свойств.
Закалка стали производится на том же оборудовании, что и выплавка, поэтому нет необходимости в покупке новых производственных линий или открытии дополнительных заводов. Этот метод был открыт человечеством еще в древние времена. Кузнецы, изготавливая различные изделия, нагревали их при помощи простейших плавильных печей, а затем резко опускали в емкость с холодной водой. Это делало продукцию намного прочнее. Современные виды закалки стали сделали огромный скачок в плане технологий, но суть осталась прежней.
Режимы закалки сталей
Существует несколько режимов закалки сталей. Каждый режим используется для обработки металла под конкретную отрасль производства. Все способы имеют свои достоинства и недостатки, и на текущий момент нет какого-либо универсального метода, лишенного слабых сторон. Поэтому рассмотрим все варианты. Первый подразумевает закалку углеродистой стали с применением одного охладителя. Это самый простой способ, так как не требует соблюдения каких-либо особых условий. Его недостатком является очень сильное закалочное напряжение, которое испытывает металл при обработке. Если неправильно рассчитать температурный режим, то закалка может привести к разрушению сплава.
Второй метод подразумевает охлаждение металла в двух разных средах. Сначала нагретую сталь кладут в воду, где охлаждают до 300 градусов по Цельсию, а затем переносят в масло, где она проходит окончательное охлаждение. Это позволяет значительно снизить напряжение, но метод имеет сложную реализацию, так как трудно рассчитать, когда именно необходимо менять среду охлаждения.
Ступенчатая закалка применяется для небольших предметов. Она делается в несколько этапов. На первом горячее изделие помещают в расплав солей или металлов, который имеет температуру на 50 градусов выше точки начала мартенситного превращения. А когда температуры сплава и среды уравняются, сталь переносят в воду, где она окончательно остывает. Этот метод дает очень хорошие результаты, но требует дополнительных затрат на создание технологических условий.
Изотермическая закалка также подразумевает использование в качестве охлаждающей среды не воды или масла, а расплава солей или щелочей. Но в отличие от предыдущего метода здесь материал проходит полный цикл охлаждения в расплаве. Твердость стали после закалки такого типа является наивысшей, так как аустенит переходит в состояние цементита. Это означает, что атомы углерода еще более глубоко внедряются в структуру железа, создавая очень прочные межмолекулярные связи.
Последний способ – закалка с самоотпуском. Он подразумевает, что нагретую деталь помещают в охлаждающую среду, но не дают ей полностью остыть. Изделие вынимают из охладителя, вследствие чего поверхность снова нагревается за счет сохраненной внутренней теплоты. Такой способ позволяет получать особый вид стали, который сочетает твердость на поверхности и вязкость внутри. Все перечисленные режимы закалки стали используются в равной мере в зависимости от необходимости.
Частичная закалка стали
Также существуют методы частичной закалки одного изделия, когда определенная часть должна быть тверже остального металла. В частности такой обработке подвергается лезвие катаны и многих других режущих инструментов. Для правильной закалки очень важным условием является соблюдение правильного температурного режима на всех технологических этапах. Его выбор зависит от марки обрабатываемой стали и процентном соотношении различных примесей в сплаве.
Температура закалки стали должна быть на 30-50 градусов выше точки мартенситного превращения. Такой уровень позволяет достичь оптимальной активности атомов углерода, которые начинают перемещаться и внедряться в железо на межмолекулярном уровне. Быстрое охлаждение используется, чтобы сохранить этот эффект, так как при постепенной потере температуры углерод постепенно возвращается в исходное состояние и закалка не сохраняется.
Кроме перечисленных режимов существуют также отдельные виды обработки. Один из них – это поверхностная закалка стали. Она подразумевает обработку лишь верхних слоев металла без манипуляций с внутренним строением. Технология абсолютно идентична полной закалке, но необходимость нагрева лишь поверхностного слоя заставляет корректировать способы.
Способы повехностной закалки стали
Существует 4 основных метода поверхностной закалки: с индукционным нагревом при помощи высокочастотного тока, с электроконтактным нагревом, с нагревом при помощи газопламенных горелок и закалку при помощи использования электролитического раствора. Для обработки мелких деталей зачастую используют последний метод.
Для средних изделий применяются первые два, а для крупногабаритных элементов лучше всего подходит нагрев при помощи газовых горелок. Для охлаждения используют те же жидкости, что и при полной закалке. В редких случаях, для особо крупных конструкций применяются газовые холодильные установки. И последний вид обработки называется неполной закалкой стали. Он подразумевает медленное охлаждение нагретого материала, в результате чего часть атомов углерода успевают покинуть молекулярную сетку железа и вернуться к нормальному состоянию.
Таким образом, образуется частично закаленный металл. Такой тип обработки применяется, когда необходимо специально оставить в структуре материала слабые места. Этот подход используется в автомобильной промышленности для создания так называемой контролируемой деформации при аварии. Он разработан специально для уменьшения травматизма пассажиров и снижения количества смертельных случаев.
promplace.ru
Термообработка закалкой и отпуском стали: важность, отличия, этапы термической обработки
Металлы и сплавы обладают характерными показателями твердости и прочности. Эти характеристики можно найти в специальных таблицах. Современные технологии позволяют изменить базовые параметры, применяя технологию термообработки. Сам процесс термической обработки достаточно прост: металл доводят до необходимой температуры и затем охлаждают. В этом процессе важны два показателя:
-
Температура, до которой нагревается металл;
-
Время нагрева и последующего охлаждения.
Эти два показателя формируют режим термообработки, который состоит из нескольких этапов.
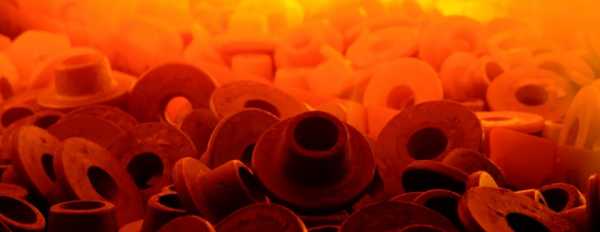
Этапы термообработки: отжиг и нормализация
В процессе термической обработки металлы проходят четыре основных этапа: отжиг, нормализацию, закалку, отпуск.
-
Отжиг. Этот процесс происходит при температуре 750 градусов Цельсия и выше. Широко применяется при термообработке стали. В результате отжига увеличивается вязкость стали, стабилизируются ее основные свойства. Охлаждается сталь вместе с печью не более чем на 60 градусов Цельсия в час. Главным показателем скорости охлаждения является легированность, чем она выше, тем скорость ниже.
-
Нормализация. Для этого процесса подъем температуры для обработки сталь идентичен предыдущему процессу, но вот процесс охлаждения резко отличается. В данном процессе охлаждения производится не в печи, а вне ее. При этом существуют два варианта с обдувом и без него. Процесс нормализации используется для низкоуглеродистых сталей, при этом их структура уплотняется за счет уменьшения диаметра зерен. Такую сталь легче обрабатывать и подвергать последующей шлифовке.
Закалка и отпуск
Эти два процесса наиболее важны, так как металлы, прошедшие закалку и отпуск, обладают особой прочностью и износоустойчивостью.
-
Закалка осуществляется в печах при температурах 770 или 960 градусов Цельсия в зависимости от вида металла. Охлаждение осуществляют в воде для углеродистых сталей, и в маслах для легированной. Подъем температуры и резкое охлаждение стали изменяет ее физическое состояние, сталь становится хрупкой. Для удаления этого эффекта, а также для снятия внутреннего структурного напряжения применяют следующий процесс.
-
Отпуск. Этот процесс заключается в повторном нагревании уже закаленной стали до температур 600 градусов Цельсия с последующим медленным охлаждением. При этом чем ниже скорость охлаждения, тем лучше снимается внутреннее напряжение металла.
Важность термообработки
Термообработку сложно переоценить. Только два показателя температура и время могут изменить физико-химические характеристики стали.
barion-ua.com
§ 6. ТЕРМИЧЕСКАЯ ОБРАБОТКА (ЗАКАЛКА И ОТПУСК)
Назначение закалки заключается в том, чтобы придать изделию высокую твердость и прочность. Однако при закалке с повышением твердости сталь становится более хрупкой.
Для закалки изделия нагревают до высокой температуры, а затем быстро охлаждают в специальных охлаждающих средах. В зависимости от режима закалки одна и та же сталь получает различные структуры и свойства. Для получения наилучших результатов изделие равномерно нагревают до температуры 740—850°С и затем быстро охлаждают до 400-450°С. Скорость охлаждения должна быть не менее 150°С в секунду, т. е. охлаждение должно произойти в течение всего 2—3 с. Дальнейшее охлаждение, ниже 300°С, может протекать при любой скорости, так как полученная при закалке структура достаточно устойчива и скорость дальнейшего охлаждения на нее не оказывает влияния.
В качестве охлаждающих сред чаще всего употребляются вода и трансформаторное масло. Скорость охлаждения в воде больше, чем в масле. При температуре воды 18°С скорость охлаждения достигает 600°С в секунду, а в масле — до 150°С в секунду.
Для придания изделию большей твердости закалку производят в проточной воде. При охлаждении горячей поковки в стоячей воде между водой и поковкой возникает слой пара, который изолирует нагретую поковку от охлаждающей среды. Поэтому во избежание этого пользуются проточной водой.
Иногда для повышения закаливающей способности в воду добавляют поваренную соль (до 10%) или серную кислоту (до 10—12%).
Нагрев изделия выше критической точки придает металлу крупнозернистое строение, а это приводит к нежелательным последствиям: короблению, деформации и появлению трещин. К этому же приводит и быстрое охлаждение.
При закалке инструментов применяются закалочные печи, которые делятся на камерные, или пламенные, где изделие нагревается открытым пламенем; электрические муфельные; печи-ванны, представляющие собой тигли, наполненные расплавами солей, например хлористым барием.
Нагревание в ваннах наиболее удобно, вследствие того что температура ванны всегда постоянная и закаливаемый инструмент не может нагреться выше этой температуры. Кроме того, нагрев в жидких средах идет в два раза быстрее, чем в воздушной среде, а в расплавленном металле—в четыре раза быстрее. Например, для закалки мелких стальных изделий используют расплавленный свинец. Мелкие заготовки погружают в ванны и сверху кладут древесный уголь, который при горении на поверхности свинца создает восстановительное пламя — свинец не окисляется. Чтобы свинец не оседал на стальных изделиях, их смазывают мучным клейстером с поваренной солью.
В табл. 14 приведены составы закалочных солевых ванн.
Таблица 14
Состав солевой, нагревающей среды (массовая доля, %) | Температура плавления, °С | Температура практического применения, °С | |
Калиевая селитра | 55 | 137 | 150-500 |
Нитрат натрия | 45 | ||
Хлористый натрий | 28 | 500 | 540-870 |
» кальций | 72 | ||
» натрий | 44 | 663 | 700-870 |
» калий | 56 | ||
» натрий | 100 | 808 | 850-1100 |
» барий | 100 | 960 | 1100-1350 |
При нагревании инструмента в муфелях применяются следующие режимы.
1. Изделия загружают в холодную печь. Нагревают постепенно, вместе с печью. Время нагрева продолжительное, но температурное напряжение, возникающее в изделиях, наименьшее.
2. Изделия загружают в печь, нагретую до заданной температуры, и прогревают при этой температуре. Время нагрева здесь меньше, но температурные напряжения больше, чем при предыдущем режиме.
3. Изделия загружают в печь, температура которой выше необходимой для закалки, в процессе нагрева температуру снижают до заданной. В этом случае скорость нагрева высокая, но и напряжение, возникающее в изделиях, очень велико.
4. Изделия загружают в печь, температуру которой непрерывно поддерживают выше необходимой. Изделия нагревают до заданной температуры, но ниже температуры печи. Это наиболее форсированный режим, напряжение достигает максимальных величин.
В последнее время для нагрева под закалку применяют токи высокой частоты. Закаливаемую деталь помещают в специальный индуктор, по которому пропускают ток высокой частоты, и деталь очень быстро нагревается до необходимой температуры.
После закалки необходимо произвести отпуск. Он смягчает действия закалки, повышает вязкость и уменьшает хрупкость и твердость изделия. Кроме того, отпуск устраняет или снижает напряжение, вызванное закалкой.
Для определения температуры отпуска очень часто до сих пор пользуются цветами побежалости. Если очищенное от окалины стальное изделие нагревать, то начиная с температуры 220°С на нем образуется тонкая пленка оксидов железа, придающая изделию различные цвета — от светло-желтого до серого. С повышением температуры или увеличением времени пребывания изделия при данной температуре оксидная пленка утолщается и цвет ее изменяется.
В табл. 15 приведены температуры нагрева и соответствующие им цвета побежалостей.
Таблица 15
Температура нагрева, °С | Цвет побежалости | Температура нагрева, °С | Цвет побежалости |
220 | Светло-желтый | 285 | Фиолетовый |
230 | Желтый | 300 | Темно-синий |
240 | Темно-желтый | 325 | Светло-синий |
255 | Коричневый | 330 | Серый |
265 | Коричнево-красный |
Цвета побежалости одинаково появляются как на сырой, так и на закаленной стали.
При отпуске закаленных инструментов применяют два способа.
1. Поверхность закаленного инструмента хорошо отшлифовывают мелкой шкуркой и затем нагревают. По мере того как температура нагрева повышается, на чистой поверхности инструмента появляются цвета побежалости. Когда появится нужный цвет и, следовательно, изделие будет нагрето до определенной температуры, его быстро охлаждают в воде. За цветами нужно следить внимательно, некоторые из них, как, например, светло-красный, сменяются быстро.
2. При закалке многих инструментов, например чеканов, щтихилей, резцов, молотков и т. д., требуется, чтобы закаленной была только рабочая часть, а сам инструмент оставался незакаленным, сырым. В этом случае инструмент нагревают немного выше режущего (рабочего) конца до требуемой температуры, после чего охлаждают в воде только рабочую часть, а место выше рабочей части остается горячим. Быстро вынув инструмент из воды, зачищают рабочую часть (шкуркой или трением о землю). Теплота, оставшаяся в неохлажденной части, поднимает температуру охлажденного конца, и после появления на нем нужного цвета побежалости инструмент окончательно охлаждают.
При закалке инструмента с двумя концами, например кирки, молотка и т. д., трудность заключается в том, что в изделии только два рабочих конца должны быть закалены, а середина должна быть незакаленной. Закалку производят за один нагрев. Изделие равномерно нагревают до нужной температуры и в воду опускают в первую очередь конец, имеющий меньшую массу, т. е. тот, который может быстрее охладиться. При охлаждении в воде конца только рабочей части нужно внимательно следить за нагретым вторым концом, чтобы он не охладился. Быстро вынув первый конец и зачистив его шкуркой, второй (только рабочую часть) погружают в воду. При этом следят за цветами побежалости первого конца; когда появляется нужный цвет, снова опускают первый конец в воду, второй быстро зачищают и следят за цветами на втором конце. При появлении нужного цвета также замачивают в воде. Так, периодически меняя положение концов, изделие остужают.
Запас температуры должен оставаться в средней части
инструмента, поэтому при закалке пользуются клещами с узкими губками. Большие плоскости холодных губок клещей отбирают теплоту в зоне прикосновения. “Для закалки более мелких изделий можно использовать клещи с массивными губками, изделие в этом случае нагревают вместе с клещами. Прием с клещами применяется при местном отпуске, когда в каком-то участке стального закаленного изделия нужно сделать отверстие, а его твердость не позволяет это сделать. Для этого берут клещи нужного размера, нагревают их до красного или светло-красного каления и захватывают металл в зоне будущего отверстия.
За отпуском металла можно следить по цветам побежалости. Этот прием используется при отпуске тонких стальных изделий — кос, пил и т. д.
Температура отпуска и цвета побежалости для некоторых инструментов приведены в табл. 16.
В процессе нагрева стальных изделий происходит их окисление и обезуглероживание. Получение на поверхности окалины идет за счет образования оксидов железа.
Образование на поверхности окалинйг приводит к угару металла, искажению геометрической формы изделий, уменьшению теплопроводности, что понижает скорость нагрева изделия. Кроме того, повышается твердость и затрудняется механическая обработка. Окалина удаляется с изделий либо механическим, либо химическим путем (травлением).
85. Железный кронштейн (XVII в.)
86. Декоративный элемент с использованием скручивания и горновой сварки
Таблица 16
Температура отпуска, °С | Цвет побежалости | Название инструмента |
220 | Светло-желтый | Токарные и строгальные резцы для обработки чугуна и стали |
240 | Темно-желтый | Чеканы для чеканки по литью |
265 | Коричнево-красный | Плашки, метчики, сверла, резцы для обработки меди, латуни, бронзы |
285 | Фиолетовый | Инструмент по дереву, зубила для обработки стали |
300 | Синий | Чеканы для чеканки из листовой меди, латуни и серебра |
Обезуглероживание состоит в выгорании углерода с поверхности изделия. Обезуглероженный слой обладает пониженной твердостью и прочностью.
Интенсивность, с которой происходит окисление и обезуглероживание, зависит от состава печной атмосферы и температуры нагрева. Чем выше нагрев, тем процессы идут быстрее.
Чтобы избежать образования окалины, мелкие изделия (чеканы, стамески и т. п.) помещают в отрезок трубы и вместе с трубой закладывают в горн. Иногда при закалке применяют пасту следующего состава (г): жидкое стекло — 100, огнеупорная глина — 75, графит — 25, бура — 14, карборунд — 30, вода — 200. Пасту наносят на изделие и дают просохнуть, затем изделие нагревают обычным способом. После закалки изделие промывают в горячем содовом растворе.
Для предупреждения образования окалины на инструментах из быстрорежущих сталей их иногда покрывают бурой. Для этого инструмент, нагретый до 850°С, погружают в насыщенный раствор или порошок буры.
* * *
В наше время больших научных и технических достижений древнее ремесло кузнеца не исчезло. Изделия современных кузнецов находят применение в нашем быту. Творения, созданные руками художников-кузнецов, гармонично сочетаются с фасадами и внутренней архитектурой зданий, являясь одновременно самостоятельным художественным произведением. Ажурный орнамент кованых решеток красиво сочетается со стройными линиями современной архитектуры. Умелое использование новых видов обработки металла — электросварки, газовой, автогенной и т. д. — дают художникам-кузнецам более широкие возможности использования и применения своего ремесла.
Старые технологические приемы оживают вновь при восстановлении разрушенных памятников культуры. Кузнечное дело, как и всякая рукодельная работа, является средством пропаганды эстетической мысли и чувств и не теряет своего значения в период высокоразвитой промышленности.
В заключение на рис. 85 и 86 показаны некоторые древнерусские кованые изделия, выполненные из деталей и собранные горновой сваркой или на заклепках.
* * *
В заключение следует отметить, что для успешной работы в области художественной обработки металлов, прежде всего необходимо овладеть простейшими слесарными операциями, т. е. уметь работать зубилом, молотком, напильником, сверлом, шабером и др.
Навыки по выполнению этих слесарных работ необходимы мастерам и художникам прикладного искусства, так как они постоянно применяются при первоначальной обработке деталей, их сборке и монтировке в целые готовые изделия.
Например, кованые художественные изделия: решетки, кроншнейны, ограды, каминные принадлежности и др., выполненные из отдельных частей, собирают также и на резьбовых соединениях.
В табл. 17 даны диаметры сверл для получения отверстий под метрическую резьбу, а в табл. 18 указаны диаметры отверстий для нарезания соответственной резьбы на болтах и винтах.
В табл. 19 приведены характеристики марок обыкновенных углеродистых сталей, которые являются основным материалом для художественной ковки.
Таблица 17
Диаметр резьбы, мм | Диаметр сверла, мм | |
под чугун и бронзу | под сталь и латунь | |
2,0 | 1,6 | 1,5 |
2,3 | 1,9 | 1,9 |
2,6 | 2,15 | 2,15 |
3,0 | 2,5 | 2,5 |
3,5 | 3,0 | 3,0 |
4,0 | 3,3 | 3,5 |
5,0 | 4,1 | 4,2 |
6,0 | 4,9 | 5,0 |
8,0 | 6,7 | 6,7 |
10,0 | 8,3 | 8,4 |
12,0 | 10,0 | 10,1 |
14,0 | 11,7 | 11,9 |
16,0 | 13,8 | 13,9 |
18,0 | 15,1 | 15,4 |
20,0 | 17,1 | 17,4 |
22,0 | 19,1 | 19,4 |
24,0 | 20,5 | 20,6 |
27,0 | – | 23,8 |
30,0 | – | 26,3 |
36,0 | – | 31,8 |
Таблица 18
Диаметр резьбы, мм | Диаметр стержня, мм | Диаметр резьбы, мм | Диаметр стержня, мм |
2,0 | 1,6 | 12,0 | 11,88 |
3,0 | 2,4 | 14,0 | 13,88 |
4,0 | 3,92 | 16,0 | 15,88 |
5,0 | 4,92 | 18,0 | 17,88 |
6,0 | 5,92 | 20,0 | 19,86 |
8,0 | 7,90 | 22,0 | 21,86 |
10,0 | 9,90 | 24,0 | 23,86 |
Таблица 19
Марка стали | Химический состав, % | Степень закаливаемости | Цвет условной окраски | Применение | ||
углерод | марганец | кремний | ||||
Ст0 | ДО 0,23 | _ | _ | Не закаливается | Хорошо сваривается, вязкая; применяется | |
Ст1 | 0,07-0,12 | до 0,5 | – | » | Белый | для художественных, кузнечных и гибочных |
Ст2 | 0,09-0,15 | до 0,5 | – | » | Желтый | работ в виде прутков, полос, проволоки, а |
СтЗ | 0,14-0,22 | до 0,6 | до 0,3 | » | Красный | также листов |
Ст4 | 0,18-0,27 | до 0,7 | до 0,3 | Слабо закаливается | Черный | Профильный прокат, уголок, тавр, швеллер, трубы, болты, заклепки |
Ст5 | 0,28-0,37 | до 0,8 | до 0,35 | » | Зеленый | Крупные поковки |
Стб | 0,38-0,50 | до 0,8 | до 0,35 | Хорошо закаливается | Синий | В художественной промышленности употребляется редко |
Первоисточник:
Техника художественной эмали, чеканки и ковки. А. В. Флеров, М. Т. Демина, А. Н. Елизаров, Ю. А. Шеманов — М., 1986.art-con.ru
Отжиг, нормализация, закалка и отпуск
Отжиг, нормализация, закалка и отпуск
Термическая обработка означает воздействие на металлы, которое изменяет их строение и свойства.
При механической обработке в металлах и сплавах возникают внутренние напряжения. Например, при обработке стали давлением, с повышением степени деформации внутреннее строение ее кристаллической решетки изменяется и кристаллы принимают неестественное напряженное состояние. Этот процесс продолжается до тех пор, пока все кристаллы не вытянутся в виде волокон в направлении действия силы давления. Происходит это при холодной обработке металла. В результате изменяются его различные свойства – твердость и прочность повышаются, а удлинением понижаются. Если продолжать обработку, могут произойти трещины, разрывы. Чтобы вернуть стали первоначальные свойства, необходимо вывести структуры из напряженного состояния и придать им вновь устойчивое положение, иными словами, нужна рекристаллизация. Для этого необходима тепловая или термическая обработка металла.
При термической (тепловой) обработке необходимо нагревание металла до определенной температуры, выдержка при этой температуре и затем охлаждение с нужной скоростью. Различают несколько видов термической обработки: отжиг, нормализацию, закалку, отпуск, химико-термическую обработку.
Отжигом называется вид термической обработки, при котором изделия нагревают до определенной температуры, выдерживают определенное время при этой температуре и затем медленно охлаждают, достигая устойчивой равновесной структуры стали.
Основное назначение отжига – получение равновесной структуры, поэтому при отжиге, как правило, детали охлаждают медленно. К примеру, углеродистые стали – со скоростью примерно 200°С, а легированных – 30-100°С/ч.
Отжиг улучшает обрабатываемость, повышает пластичность, уменьшает остаточные напряжения и т.д. Производят его в электрических печах. Обрабатываемый металл нагревают при температурах 650 – 720°С 2 – 3 часа, а затем охлаждают вместе с печью.
В случае нагрева изделия в кузнечном горне, самой хорошей средой охлаждения является сухая, просеянная зола, которую подогревают в горне и закапывают в нее охлаждаемое изделие. Для этой цели используют еще нагретый чистый песок.
В производстве художественных изделий отжиг применяют при ковке, штамповке, дифовке, чеканке.
Во время отжига нужно следить, чтобы не произошло пережога, который вызывает окисление и оплавление границ зерен, резкое падение крепости и пластичности. Иногда изделие совершенно рассыпается.
Структура металла при пережоге не поддается исправлению, изделие подлежит переплавке.
Нормализацией называется вид термической обработки, применяемой в основном для стальных изделий. Изделия нагревают и затем охлаждают на спокойном воздухе.
В зависимости от количества углерода, содержащегося в стали, нормализация вызывает различные измения ее свойств.
Для малоуглеродистых сталей нормализация заменяет отжиг, так как при этом структура получается почти такой же, как и после отжига, однако процесс протекает быстрее и поэтому он более экономичен.
Нормализацию производят для повышения механических свойств стали, а также для улучшения обрабатываемости резанием.
Для высокоуглеродистых, легированных сталей нормализация является по существу закалкой.
Закалкой называют вид термической обработки, при которой изделию придают высокую твердость, упругость и прочность. Однако при закалке с повышением твердости сталь становится более хрупкой. Процесс закалки заключается в нагреве изделия до высокой температуры (740 – 850°С), выдержке и быстром охлаждении до 400 – 450°С с разной скоростью в разных средах – масле, воде, соляных и иных растворах. Как правило, скорость охлаждения должна быть не меньше 150°С в секунду, т.е. охлаждение должно произойти за очень короткий интервал времени – 2 – 3 секунды. Охлаждение ниже 300°С может произойти при любой температуре, так как полученная при закалке структура достаточно устойчива и скорость дальнейшего охлаждения на нее не оказывает влияния.
В зависимости от цвета накала изменяется и приближенная температура стали. Так, при темно-коричневом цвете накала температура стали находится в пределах от 530 до 580°С, при коричнево-красном цвете – 580 – 650 градусов, при темно-вишневом – 650 – 730°С, при светло-красном – 830 – 980 градусов, при оранжевом – 900 – 1050°С, желтый цвет накала возникает при 1050 – 1150°С, светло-желтый – 1150 – 1250°С, ослепительно белый цвет накала возникает при 1250 – 1300°С.
Отпуском называется вид термической обработки, который осуществляют после закалки. Он смягчает действие закалки, повышает вязкость, уменьшает хрупкость и твердость изделия.
Охлаждение может осуществляться на воздухе или в воде. Различают низкий, средний и высокий отпуск.
При низком отпуске закаленное изделие нагревают до 150 – 200°С, что снижает остаточное напряжение и хрупкость, оставляя прежней твердость. Применяется при изготовлении инструментов из углеродистой и легированной стали.
При среднем отпуске закаленное изделие нагревают до 350 – 450°С, что повышает пластичность и упругость, понижает твердость и внутренние напряжения. Используется для опуска пружин, рессор, ударного инструмента.
При высоком отпуске закаленное изделие нагревают до 450 – 650°С.
Для изделий из стали, чувствительной к скорости охлаждения, при изготовлении деталей из улучшенных конструкционных сталей, инструмента из быстрорежущей стали применяют ускоренное охлаждение в воде или масле.
При многократном опуске изделие два-четыре раза нагревают и охлаждают. Этот прием применяют при изготовлении инструмента из быстрорежущей стали.
Для определения температуры при отпуске инструментов пользуются цветами побежалости. Если очищенное от окалины стальное изделие нагреть, то, начиная с температуры 220°С, на нем образуются пленки окислов железа, которые придают изделию различные цвета от светло-желтого до серого.
При светло-желтом цвете побежалости температура изделия нагрева составляет 220°С, при желтом – 230°С, при темно-желтом – 240°С, при коричневом – 255°С, при коричнево-красном – 265°С, при фиолетовом – 285°С, при темно-синем – 300°С, при светло-синем – 325°С, при сером – 330°С.
Поделитесь на страничкеСледующая глава >
diy.wikireading.ru
Термическая обработка стальных поковок. Отжиг, нормализация, закалка и отпуск. Ручная ковка |
Термическая обработка стальных поковок.
В кузнечном производстве при изготовлении стальных поковок используют в основном один или два из четырех видов термической обработки, к которым относятся отжиг, нормализация, закалка и отпуск. Следует отметить, что различные стали имеют свои определенные режимы термической обработки.
Отжиг
Отжиг выполняют путем нагрева металла до температуры фазовых превращений и последующего медленного охлаждения. После отжига структуры стали соответствуют диаграмме железо — углерод: доэвтектоидные стали (С < 0,8 %) будут иметь структуру феррит + перлит, эвтектоидные (С = 0,8 %) — перлит, заэвтектоидные (С > > 0,8 %) — перлит + цементит. Фазовая перекристаллизация при отжиге измельчает зерно, снимает внутренние напряжения, возникшие при ковке, и уменьшает структурную неоднородность. В результате отжига снижаются прочность и твердость металла, увеличивается его пластичность, повышается обрабатываемость резанием. Отжиг обычно применяют при обработке поковок из сталей с высоким содержанием углерода и легирующих элементов. При многопереходной холодной пластической деформации с помощью отжига снимают упрочнение, полученное металлом в процессе промежуточных операций, и восстанавливают пластичность металла перед последующей холодной обработкой давлением.
Полный отжиг заключается в нагреве доэвтектоидных сталей до температуры, на 30 … 50 ° С превышающей температуру перехода стали в аустенитное состояние, выдержке при этой температуре до полного прогрева заготовки и в последующем медленном охлаждении в печи. Время нагрева и выдержки зависит от марки стали, формы и размеров сечения поковок или заготовок, типа печи и способа укладки заготовок в ней. Поковки из углеродистых сталей охлаждают со скоростью 50 . . . 150 град/ч, а поковки из легированных сталей — значительно медленнее (20 … 60 град/ч). Полному отжигу подвергают поковки для максимального уменьшения твердости и прочности металла и повышения его пластичности. Если полный отжиг выполняют для снятия напряжений в поковках сложной формы, то медленное охлаждение ведут почти до температуры цеха. В других случаях поковки медленно охлаждают в печах до 500 . . . 600 ° С с последующим охлаждением на воздухе.
Неполный отжиг (в отличие от полного) осуществляют путем нагрева поковок до температуры несколько выше 723 ° С. Для доэвтектоидных сталей неполный отжиг выполняют для снятия напряжений и улучшения обрабатываемости резанием поковок, ковка которых была выполнена в установленном температурном интервале без образования крупнозернистой структуры. Заэвтектоидные стали, как правило, подвергают неполному отжигу, при котором происходит полная перекристаллизация, пластинчатый перлит принимает зернистую структуру, а сталь становится пластичной и имеет низкую твердость.
Нормализация
Нормализацию применяют, как правило, для устранения в поковках крунозернистой структуры, образовавшейся в результате вынужденного или случайного увеличения времени нахождения заготовок в печи или в случае окончания ковки при слишком высокой температуре .
Нормализация заключается в нагреве сталей до температуры, на 50 … 60 ° С превышающей температуру перехода стали в аустенитное состояние, непродолжительной выдержке и охлаждении на воздухе.
Нормализация низкоуглеродистых сталей обеспечивает получение более чистой поверхности при резании. Для среднеуглеродистых сталей она заменяет закалку с высоким отпуском и снижением коробления формы поковки. Для исправления структуры легированных сталей часто вместо отжига применяют нормализацию с последующим высоким отпуском при 600 … 650 ° С.
Закалка
Закалкой называют операцию нагрева до температуры, на 30 … 70 ° С превышающей температуру перехода стали в аустенитное состояние, и охлаждения в воде, масле или другой среде с соответствующей для данной стали скоростью. Время выдержки при температуре закалки должно быть достаточным для завершения полного фазового превращения в металле.
Кузнецы часто выполняют закалку сразу по окончании ковки без дополнительного нагрева. Очевидно, что зто возможно лишь в том случае, если температура поковки по окончании ковки не ниже температуры закалки.
Закалка не является окончательной термической обработкой, так как сталь становится не только прочной, но и очень хрупкой, а в поковке возникают большие закалочные напряжения. Они достигают такого значения, что из-за низкой пластичности металла приводят либо к образованию в поковках трещин, либо к разрушению детали в самом начале ее эксплуатации. Кузнечный инструмент, например молоток, подвергнутый только закалке, не может быть использован по своему назначению, так как при выполнении удара от него будут откалываться кусочки твердого металла.
Вследствие этого для снижения закалочной хрупкости и внутренних напряжений, а также для приобретения требуемых высоких прочностных свойств поковки после закалки подвергают отпуску. Конструкционные стали закаливают и подвергают отпуску для повышения предела прочности, твердости при достаточных показателях пластичности и ударной вязкости, а инструментальные стали — для придания инструменту высоких твердости и изностостойкости.
Отпуск
Отпуск является окончательным видом термической обработки. Он заключается в нагреве закаленной стали до некоторой температуры, выдержке при этой температуре и охлаждении, как правило, на воздухе. В процессе отпуска структурных превращений в металле не происходит, но снижаются закалочные напряжения, несколько уменьшаются твердость и прочность, повышаются пластичность и ударная вязкость. Чем выше температура отпуска, тем больше снижается твердость закаленной стали и повышается ее вязкость.
В зависимости от марки стали и требований, предъявляемых к твердости и прочности детали, применяют три вида отпуска: высоко-, средне- и низкотемпературный (сокращенно их называют соответственно высоким, средним и низким).
Низкий отпуск проводят с нагревом до 150 . . . 250 ° С с целью снижения внутренних напряжений без уменьшения твердости закаленной стали (до HRC3 59 . . . 65). Однако после такого отпуска детали не воспринимают динамических нагрузок, поэтому низкий отпуск используют для обработки режущего и измерительного инструмента из углеродистых и низкоуглеродистых сталей.
Средний отпуск выполняют при 350 .. . 500 ° С и применяют для пружин и рессор, так как он обеспечивает получение стали с небольшим пределом упругости и повышенной вязкостью при твердости HRC3 41 …51.
Высокий отпуск, осуществляемый при 500 . . . 680 ° С, почти полностью ликвидирует закалочные напряжения, повышает пластичность и ударную вязкость, однако заметно снижает прочность и твердость стали. Закалка с высоким отпуском по сравнению с отжигом одновременно повышает пределы прочности и текучести, относительное сужение и ударную вязкость.
Термообработку, состоящую из закалки и высокого отпуска, называют улучшением; она создает наилучшее соотношение между прочностью и вязкостью стали. Улучшению подвергают, как правило, конструкционные стали с содержанием углерода 0,3 … 0,5 %.
Кузнецы ручной ковки при изготовлении слесарного, кузнечного или измерительного инструмента часто применяют закалку и отпуск с одного нагрева. Такую операцию, называемую также закалкой с самоотпуском, выполняют следующим образом. Нагретую под закалку поковку охлаждают в воде или масле не полностью, а до температуры, несколько превышающей температуру отпуска. Извлеченную из закалочной среды поковку выдерживают на воздухе до появления на ее поверхности, предварительно обработанной на наждачном камне, соответствующего цвета побежалости. После этого поковку окончательно охлаждают в масле или воде. Определить примерную температуру поковки можно по цвету побежалости, пользуясь их следующим соответствием: 350 . . . 330 ° С — светло-серый; 320 ° С — сине-васильковый; 250 ° С — красно-коричневый; 240 0 С — коричневый; 280 ° С — фиолетовый; 260 ° С — пурпуровый; 230 ° С — золотистый; 220 ° С — светло-желтый.
dlja-mashinostroitelja.info