Жаростойкие и жаропрочные сплавы и стали – Лекция 20 Коррозионно-стойкие стали и сплавы. Жаростойкие стали и сплавы. Жаропрочные стали и сплавы
alexxlab | 03.07.2018 | 0 | Вопросы и ответы
Лекция 20 Коррозионно-стойкие стали и сплавы. Жаростойкие стали и сплавы. Жаропрочные стали и сплавы
Коррозия электрохимическая и химическая.
Классификация коррозионно-стойких сталей и сплавов
Хромистые стали.
Жаростойкость, жаростойкие стали и сплавы.
Жаропрочность, жаропрочные стали и сплавы
Классификация жаропрочных сталей и сплавов
Коррозия электрохимическая и химическая.
Разрушение металла под воздействием окружающей среды называют коррозией.
Коррозия помимо уничтожения металла отрицательно влияет на эксплуатационные характеристики деталей, содействуя всем видам разрушения.
Коррозия в зависимости от характера окружающей среды может быть химической и электрохимической.
Электрохимическаякоррозия имеет место в водных растворах, а так же в обыкновенной атмосфере, где имеется влага.
Сущность этой коррозии в том, что ионы металла на поверхности детали, имея малую связь с глубинными ионами, легко отрываются от металла молекулами воды.
Металл, потеряв часть положительно заряженных частиц, ионов, заряжается отрицательно за счет избыточного количества оставшихся электронов. Одновременно слой воды, прилегающий к металлу, за счет ионов металла приобретает положительный заряд. Разность зарядов на границе металл – вода обуславливает скачок потенциала, который в процессе коррозии изменяется, увеличиваясь от растворения металла, и уменьшаясь от осаждения ионов из раствора на металле.
Если количество ионов переходящих в раствор и осаждающихся на металле одинаково, то скорости растворения и осаждения металла равны и процесс коррозии (разрушения металла) не происходит. Этому соответствует равновесный потенциал .
За нулевой потенциал принимают равновесный потенциал водородного иона в водном растворе при концентрации положительных ионов водорода, равной 1 моль ионов +на 1 литр.Стандартные потенциалы других элементов измерены по отношению к водородному потенциалу.
Металлы, стандартный потенциал которых отрицательный – корродируют в воде, в которой растворен кислород тем активнее, чем отрицательней значение электрохимического потенциала.
Уходящие ионы металла, взаимодействуя с ионами , образуют гидроксиды, нерастворимые в воде, которые называютржавчиной,а процесс их образования –ржавлением.
Схема ржавления железа:
;
Гидроксид железа в присутствии кислорода, растворенного в воде, превращается в. Так как это нерастворимое соединение, то равновесный потенциал не может быть достигнут и коррозия будет продолжаться до полного разрушения.
В зависимости от структуры коррозия имеет разное проявление: при однородном металле – коррозия происходит равномерно по всей поверхности. При неоднородном металле – коррозия избирательная и называется точечной. Это явление наиболее опасно, так как приводит к быстрой порче всего изделия. Избирательная коррозия создает очаги концентрации напряжений, что содействует разрушению.
Химическая коррозияможет происходить за счет взаимодействия металла с газовой средой при отсутствии влаги. Продуктом коррозии являются оксиды металла. Образуется пленка на поверхности металла толщиной в 1…2 периода кристаллической решетки. Этот слой изолирует металл от кислорода и препятствует дальнейшему окислению, защищает от электрохимической коррозии в воде. При создании коррозионно-стойких сплавов – сплав должен иметь повышенное значение электрохимического потенциала и быть по возможности однофазным.
Классификация коррозионно-стойких сталей и сплавов
Коррозионная стойкость может быть повышена, если содержание углерода свести до минимума, если ввести легирующий элемент, образующий с железом твердые растворы в таком количестве, при котором скачкообразно повысится электродный потенциал сплава.
Важнейшими коррозионно-стойкими техническими сплавами являются нержавеющие стали с повышенным содержанием хрома: хромистые и хромоникелевые. На рис. 20.1 показано влияние количества хрома в железохромистых сплавах на электрохимический потенциал сплава.
Рис 20.1. Влияние хрома на потенциал сплавов
Хромистые стали.
Содержание хрома должно быть не менее 13% (13…18%).
Коррозионная стойкость объясняется образованием на поверхности защитной пленки оксида .
Углерод в нержавеющих сталях является нежелательным, так как он обедняет раствор хромом, связывая его в карбиды, и способствует получению двухфазного состояния. Чем ниже содержание углерода, тем выше коррозионная стойкость нержавеющих сталей.
Различают стали ферритного класса08Х13, 12Х17, 08Х25Т, 15Х28. Стали с повышенным содержанием хрома не имеют фазовых превращений в твердом состоянии и поэтому не могут быть подвергнуты закалке. Значительным недостатком ферритных хромистых сталей является повышенная хрупкость из-за крупнокристаллической структуры. Эти стали склонны к межкристаллитной коррозии (по границам зерен) из-за обеднения хромом границ зерен. Для избежания этого вводят небольшое количество титана. Межкристаллитная коррозия обусловлена тем, что часть хрома около границ зерна взаимодействует с углеродом и образует карбиды. Концентрация хрома в твердом растворе у границ становится меньше 13% и сталь приобретает отрицательный потенциал.
Из-за склонности к росту зерна ферритные стали требуют строгих режимов сварки и интенсивного охлаждения зоны сварного шва. Недостатком является и склонность к охрупчиванию при нагреве в интервале температур 450…500oС
Из ферритных сталей изготавливают оборудование азотно-кислотных заводов (емкости, трубы).
Для повышения механических свойств ферритных хромистых сталей в них добавляют 2…3 % никеля. Стали 10Х13Н3, 12Х17Н2 используются для изготовления тяжелонагруженных деталей, работающих в агрессивных средах.
После закалки от температуры 1000oC и отпуска при 700…750oС предел текучести сталей составляет 1000 МПа.
Термическую обработку для ферритных сталей проводят для получения структуры более однородного твердого раствора, что увеличивает коррозионную стойкость.
Стали аустенитного класса– высоколегированные хромоникелевые стали.
Никель – аустенитообразующий элемент, сильно понижающий критические точки превращения. После охлаждения на воздухе до комнатной температуры имеет структуру аустенита.
Нержавеющие стали аустенитного класса 04Х18Н10, 12Х18Н9Т имеют более высокую коррозионную стойкость, лучшие технологические свойства по сравнению с хромистыми нержавеющими сталями, лучше свариваются. Они сохраняют прочность до более высоких температур, менее склонны к росту зерна при нагреве и не теряют пластичности при низких температурах.
Хромоникелевые стали коррозионностойки в окислительных средах. Основным элементом является хром, никель только повышает коррозионную стойкость.
Для большей гомогенности хромоникелевые стали подвергают закалке с температуры 1050…1100oCв воде. При нагреве происходит растворение карбидов хрома в аустените. Выделение их из аустенита при закалке исключено, так как скорость охлаждения велика. Получают предел прочности= 500…600 МПа, и высокие характеристики пластичности, относительное удлинение= 35…45%.
Упрочняют аустенитные стали холодной пластической деформацией, что вызывает эффект наклепа. Предел текучести при этом может достигнуть значений 1000…1200 МПа, а предел прочности – 1200…1400 МПа.
Для уменьшения дефицитного никеля часть его заменяют марганцем (сталь 40Х14Г14Н3Т) или азотом (сталь 10Х20Н4АГ11).
Аустенитно-ферритные стали12Х21Н5Т, 08Х22Н6Т являются заменителями хромоникелевых сталей с целью экономии никеля.
Свойства сталей зависят от соотношения ферритной и аустенитной фаз (оптимальные свойства получают при соотношении – Ф:А=1:1 ). Термическая обработка сталей включает закалку от температуры 1100…1150oC и отпуск-старение при температуре 500…750oC.
Аустенитно-ферритные стали не подвержены коррозионному растрескиванию под напряжением: трещины могут возникать только на аустенитных участках, но ферритные участки задерживают их развитие. При комнатных температурах аустенитно-ферритные стали имеют твердость и прочность выше, а пластичность и ударную вязкость ниже, чем стали аустенитного класса.
Кроме нержавеющих сталей в промышленности применяют коррозионно-стойкие сплавы – это сплавына никелевой основе.Сплавы типахастеллойсодержат до 80 % никеля, другим элементом является молибден в количестве до 15…30 %. Сплавы являются коррозионно-стойкими в особо агрессивных средах (кипящая фосфорная или соляная кислота), обладают высокими механическими свойствами. После термической обработки – закалки и старения при температуре 800 oС – сплавы имеют предел прочностиМПа, и твердость. Недостатком является склонность к межкристаллической коррозии, поэтому содержание углерода в этих сплавах должно быть минимальным.
Жаростойкость, жаростойкие стали и сплавы.
Жаростойкость (окалиностойкость)– это способность металлов и сплавов сопротивляться газовой коррозии при высоких температурах в течение длительного времени.
Если изделие работает в окислительной газовой среде при температуре 500..550oC без больших нагрузок, то достаточно, чтобы они были только жаростойкими (например, детали нагревательных печей).
Сплавы на основе железа при температурах выше 570oC интенсивно окисляются, так как образующаяся в этих условиях на поверхности металла оксид железа(вюстит) с простой решеткой, имеющей дефицит атомов кислорода (твердый раствор вычитания), не препятствует диффузии кислорода и металла. Происходит интенсивное образование хрупкой окалины.
Рис. 20.2. Влияние хрома на жаростойкость хромистой стали
Для повышения жаростойкости в состав стали вводят элементы, которые образуют с кислородом оксиды с плотным строением кристаллической решетки (хром, кремний, алюминий).
Степень легированости стали, для предотвращения окисления, зависит от температуры. Влияние хрома на жаростойкость хромистой стали показано на рис.20.2.
Чем выше содержание хрома, тем более окалиностойки стали (например, сталь 15Х25Т является окалиностойкой до температуры 1100…1150oC).
Высокой жаростойкостью обладают сильхромы, сплавы на основе никеля – нихромы, стали 08Х17Т, 36Х18Н25С2, 15Х6СЮ.
Жаропрочность, жаропрочные стали и сплавы
Жаропрочность– это способность металла сопротивляться пластической деформации и разрушению при высоких температурах.
Жаропрочные материалы используются для изготовления деталей, работающих при высоких температурах, когда имеет место явление ползучести.
Критериями оценки жаропрочности являются кратковременная и длительная прочности, ползучесть.
Кратковременная прочностьопределяется с помощью испытаний на растяжение разрывных образцов. Образцы помещают в печь и испытывают при заданной температуре. Обозначают кратковременную прочность=, например300oС= 300МПа.
Прочность зависит от продолжительности испытаний.
Пределом длительной прочностиназывается максимальное напряжение, которое вызывает разрушение образца при заданной температуре за определенное время.
Например = 200 МПа, верхний индекс означает температуру испытаний, а нижний – заданную продолжительность испытания в часах. Для котельных установок требуется невысокое значение прочности, но в течение нескольких лет.
Ползучесть – свойство металла медленно пластически деформироваться под действием постоянной нагрузки при постоянной температуре.
При испытаниях образцы помещают в печь с заданной температурой и прикладывают постоянную нагрузку. Измеряют деформацию индикаторами.
При обычной температуре и напряжениях выше предела упругости ползучесть не наблюдается, а при температуре выше 0,6Тпл, когда протекают процессы разупрочнения, и при напряжениях выше предела упругостинаблюдается ползучесть.
В зависимости от температуры скорость деформации при постоянной нагрузке выражается кривой состоящей из трех участков (рис. 20.3):
Рис. 20.3. Кривая ползучести
ОА – упругая деформация образца в момент приложения нагрузки;
АВ – участок, соответствующий начальной скорости ползучести;
ВС – участок установившейся скорости ползучести, когда удлинение имеет постоянную скорость.
Если напряжения достаточно велики, то протекает третья стадия (участок СД), связанная с началом разрушения образца (образование шейки).
Для углеродистых сталей ползучесть наблюдается при нагреве выше 400oС.
Предел ползучести– напряжение, которое за определенное время при заданной температуре вызывает заданное суммарное удлинение или заданную скорость деформации.
НапримерМПа, где верхний индекс – температура испытания вoС, первый нижний индекс – заданное суммарное удлинение в процентах, второй – заданная продолжительность испытания в часах.
Классификация жаропрочных сталей и сплавов
В качестве современных жаропрочных материалов можно отметить перлитные, мартенситные и аустенитные жаропрочные стали, никелевые и кобальтоавые жаропрочные сплавы, тугоплавкие металлы.
При температурах до 300oC обычные конструкционные стали имеют высокую прочность, нет необходимости использовать высоколегированные стали.
Для работы в интервале температур 350…500oC применяют легированные стали перлитного, ферритного и мартенситного классов.
Перлитные жаропрочные стали. К этой группе относятся котельные стали и сильхромы. Эти стали применяются для изготовления деталей котельных агрегатов, паровых турбин, двигателей внутреннего сгорания. Стали содержат относительно мало углерода. Легирование сталей хромом, молибденом и ванадием производится для повышения температуры рекристаллизации (марки 12Х1МФ, 20Х3МФ). Используются в закаленном и высокоотпущенном состоянии. Иногда закалку заменяют нормализацией. В результате этого образуются пластинчатые продукты превращения аустенита, которые обеспечивают более высокую жаропрочность. Предел ползучести этих сталей должен обеспечить остаточную деформацию в пределах 1 % за время 10000…100000 ч работы.
Перлитные стали обладают удовлетворительной свариваемостью, поэтому используются для сварных конструкций (например, трубы пароперегревателей).
Для деталей газовых турбин применяют сложнолегированные стали мартенситногокласса12Х2МФСР, 12Х2МФБ, 15Х12ВНМФ. Увеличение содержания хрома повышает жаростойкость сталей. Хром, вольфрам, молибден и ванадий повышают температуру рекристаллизации, образуются карбиды, повышающие прочность после термической обработки. Термическая обработка состоит из закалки от температур выше 1000oС в масле или на воздухе и высокого отпуска при температурах выше температуры эксплуатации.
Для изготовления жаропрочных деталей, не требующих сварки (клапаны двигателей внутреннего сгорания), применяются хромокремнистые стали – сильхромы:40Х10С2М, 40Х9С2, Х6С.
Жаропрочные свойства растут с увеличением степени легированности. Сильхромы подвергаются закалке от температуры около 1000oС и отпуску при температуре 720…780oС.
При рабочих температурах 500…700oC применяются сталиаустенитного класса. Из этих сталей изготавливают клапаны двигателей, лопатки газовых турбин,сопловые аппараты реактивных двигателей и т.д.
Основными жаропрочными аустенитными сталями являются хромоникелевые стали, дополнительно легированные вольфрамом, молибденом, ванадием и другими элементами. Стали содержат 15…20 % хрома и 10…20 % никеля. Обладают жаропрочностью и жаростойкостью, пластичны, хорошо свариваются, но затруднена обработка резанием и давлением, охрупчиваются в интервале температур около 600oС, из-за выделения по границам различных фаз.
По структуре стали подразделяются на две группы:
1. Аустенитные стали с гомогенной структурой17Х18Н9, 09Х14Н19В2БР1,12Х18Н12Т. Содержание углерода в этих сталях минимальное. Для создания большей однородности аустенита стали подвергаются закалке с 1050…1100oС в воде, затем для стабилизации структуры – отпуску при 750oС.
2. Аустенитные стали с гетерогенной структурой 37Х12Н8Г8МФБ, 10Х11Н20Т3Р.
Термическая обработка сталей включает закалку с 1050…1100oС. После закалки старение при температуре выше эксплуатационной (600…750oС). В процессе выдержки при этих температурах в дисперсном виде выделяются карбиды, карбонитриды, вследствие чего прочность стали повышается.
Детали, работающие при температурах 700…900oC, изготавливают из сплавов на основе никеля и кобальта (например, турбины реактивных двигателей).
Никелевые сплавы преимущественно применяют в деформированном виде. Они содержат более 55 % никеля и минимальное количество углерода (0,06…0,12 %). По жаропрочным свойствам превосходят лучшие жаропрочные стали.
По структуре никелевые сплавы разделяют на гомогенные (нихромы) и гетерогенные (нимоники).
Нихромы.Основой этих сплавов является никель, а основным легирующим элементом – хром (ХН60Ю, ХН78Т).
Нихромы не обладают высокой жаропрочностью, но они очень жаростойки. Их применяют для малонагруженных деталей, работающих в окислительных средах, в том числе и для нагревательных элементов.
Нимоники являются четвертными сплавами никель – хром (около 20 %) – титан (около 2%) – алюминий (около 1 %) (ХН77ТЮ, ХН70МВТЮБ, ХН55ВМТФКЮ). Используются только в термически обработанном состоянии. Термическая обработка состоит из закалки с 1050…1150oС на воздухе и отпуска – старения при 600…800oС.
Увеличение жаропрочности сложнолегированных никелевых сплавов достигается упрочнением твердого раствора введением кобальта, молибдена, вольфрама.
Основными материалами, которые могут работать при температурах выше 900oC (до 2500oС), являютсясплавы на основе тугоплавких металлов– вольфрама, молибдена, ниобия и других.
Температуры плавления основных тугоплавких металлов: вольфрам – 3400oС, тантал – 3000oС, молибден – 2640oС, ниобий – 2415oС, хром – 1900oС.
Высокая жаропрочность таких металлов обусловлена большими силами межатомных связей в кристаллической решетке и высокими температурами рекристаллизации.
Наиболее часто применяют сплавы на основе молибдена. В качестве легирующих добавок в сплавы вводят титан, цирконий, ниобий. С целью защиты от окисления проводят силицирование, на поверхности сплавов образуется слой MoSi2толщиной 0,03…0,04 мм. При температуре 1700oС силицированные детали могут работать 30 часов.
Вольфрам – наиболее тугоплавкий металл. Его используют в качестве легирующего элемента в сталях и сплавах различного назначения, в электротехнике и электронике (нити накала, нагреватели в вакуумных приборах).
В качестве легирующих элементов к вольфраму добавляют молибден, рений, тантал. Сплавы вольфрама с рением сохраняют пластичность до –196oС и имеют предел прочности 150 МПа при температуре 1800oС.
Для сплавов на основе вольфрама характерна низкая жаростойкость, пленки образующихся оксидов превышают объем металла более, чем в три раза, поэтому они растрескиваются и отслаиваются Изготавливают изделия, работающие в вакууме).
studfiles.net
5.6. Жаростойкие стали и сплавы
составу и состоянию обработки. В некоторых случаях прочность таким способом может быть повышена до750 МПа, по сравнению с обычной прочностью двухкомпонентных бронз – 400–500МПа.
Бронзы называют по наличию легирующего элемента в её составе:
алюминиевые, оловянистые, кремнистые, бериллиевыеи т. д. Бронзы мар-
кируют буквами «Бр» (бронза), за которыми следуют буквы и цифры, указывающие на состав и содержание легирующих элементов, в %. Например: Бр ОЦС 4–4–2,5содержит 4 % олова, 4 % цинка, 2,5 % свинца, остальное медь; Бр КМц3–1содержит 3 % кремния, 1 % марганца, остальное медь.
Оловянистые бронзы известны с бронзового века. Они, как и другие сплавы, делятся на деформируемые(<10 %Sn) и литейные (>10 %Sn). В прошлом бронзы получили название в зависимости от их назначения:ко-
локольная (20–30% олова),зеркальная (30–35% олова),монетная (4–10%
олова), пушечная (8–18% олова). Оловянистые бронзы отличаются хорошими литейными свойствами – высокой жидкотекучестью и малой усадкой. С целью экономии олова в бронзы добавляют цинк в таком количестве, чтобы он полностью растворялся в меди, образуя твёрдый раствор, тем самым повышая механические свойства. Для улучшения обрабатываемости резанием в оловянистые бронзы добавляют свинец (например, БрО6Ц4С17: 6 %Sn, 4 %Zn, 17 %Pb, остальноеCu). Литейные оловянистые бронзы, обладая высокой коррозионной стойкостью в воде и на воздухе, применяются для пароводяной арматуры.
Деформируемые оловянистые бронзы характеризуются более низким содержанием олова (например: Бр ОЦ4–3содержит 4 %Sn, 3 %Zn, остальное медь) и имеют однофазную структуру твёрдого раствора. После холодной обработки давлением бронзы подвергаются отжигупри600–700°С. Они пластичны и более прочны, чем литейные. Кроме того, деформируемые оловянистые бронзы обладают высокими упругими свойствами, поэтому их используют для получения пружин, мембран и др.
Алюминиевые бронзы обычно содержат от 5 до 10 % алюминия. Механические и коррозионные свойства этих бронз выше, чем у оловянистых. Алюминиевые бронзы можно подвергать закалке и старению. Однофазные алюминиевые бронзы (Бр А7) более пластичны, чем двухфазные, и относятся к деформируемым. Они обладают высокой прочностью и пластичностью (σВ =400–450МПа,δ = 60 %).
Легируют алюминиевые бронзы железом, никелем, марганцем и др.
для устранения литейных недостатков и увеличения механических свойств после упрочняющей термической обработки(закалки с последующим старением). Например, у бронзы Бр АЖН10–4–4(10 %Al, 4 %
Fe, 4 %Ni, остальное медь) твёрдость увеличивается от 1500 до 4000 НВ; из неё изготавливают седла клапанов, направляющие втулки, шестерни и др.
studfiles.net
Жаростойкие стали и сплавы
Жаростойкость – способность металла сопротивляться окислению в газовой среде или в других окислительных средах при повышенных температурах. Жаропрочные сплавы в принципе должны быть и жаростойкими, иначе они быстро выходят из строя из-за быстрого окисления. Однако, жаростойкие сплавы не всегда бывают жаропрочными.
К жаростойким относятся стали и сплавы, работающие в ненагруженном или слабонагруженном состоянии при температурах выше 550 0С и обладающие стойкостью против химического разрушения поверхности в газовых средах.
Повышение жаростойкости сплавов заключается в легировании добавками, которые, не снижая показателей жаропрочности и других свойств, снижают скорость окисления сплавов за счет образования на их поверхности плотной защитной пленки окислов, хорошо связанных с основой. Диффузия (особенно кислорода) через оксидные пленки затруднена, что приводит к торможению процесса дальнейшего окисления.
Жаростойкость стали достигается введением хрома, никеля, алюминия или кремния, образующих в процессе нагрева защитные пленки оксидов (Cr,Fe)2O3, (Al,Fe)2О3. Введение в сталь 5-8 % хрома повышает жаростойкость до 700-750 0С, до 17% – до 10000С, 25% – 11000С. Дополнительное легирование к 25% хрома 5% алюминия – 1300 0С.
Жаростойкие стали и сплавы разделены на следующие группы:
хромистые и хромоалюминиевые стали ферритного класса;
хромокремнистые мартенситного класса;
хромоникелевые аустенитные стали;
сплавы на хромоникелевой основе.
К группе ферритных хромистых и хромоалюминиевых сталей отнесены высокохромистые стали на основе 13 − 28 % Сг, которые при достаточно низком содержании углерода или легирования их ферритообразующими элементами имеют однофазную ферритную структуру. Эти стали применяют для изготовления теплообменников, деталей аппаратуры химических производств, печного оборудования и других изделий, которые не испытывают значительных нагрузок и работают при высоких температурах длительное время (08Х17Т, 15Х25Т, 15Х28, 1Х13Ю4).
Чем выше содержание хрома, алюминия и кремния в сталях, тем больше температуры, при которых они сохраняют требуемые эксплуатационные свойства.
Стали ферритного класса обладают невысокой прочностью и жаропрочностью, высокой пластичностью и удовлетворительными технологическими свойствами.
Изделия из хромоалюминиевых сталей (содержание А1 от 3,5 до 5,8 %) устойчивы в атмосфере воздуха, в среде сернистых газов, но резко теряют работоспособность в восстановительных средах, содержащих окись углерода, пары воды, а также хлорсодержащих средах. При длительной работе в азотсодержащих средах образуются нитриды алюминия, которые устойчивы до высоких температур и не оказывают вредного влияния на свойства сталей.
Хромистые и хромоалюминиевые стали имеют крупный недостаток: они могут охрупчиваться в процессах технологических нагревов и длительных выдержек при повышенных температурах во время эксплуатации
Жаростойкие стали, имеющие повышенное содержание углерода (до 0,5 − 0,8 %) и легированные совместно хромом (6 − 14%) и кремнием (1 − 3 %) (15Х6СЮ, 40Х10С2М), имеют после закалки или нормализации мартенситную структуру и обычно называются сильхромами. Они обладают хорошим сопротивлением газовой коррозии в продуктах сгорания различных топлив и высокой износостойкостью при трении и ударных нагрузках.
Основное назначение сталей этой группы − клапаны автомобильных, тракторных и авиационных двигателей средней мощности. Кроме того, сильхромы используют в качестве жаростойких сплавов для изготовления регуляторов, теплообменников и колосниковых решеток в котельном и химическом машиностроении.
Термическая обработка сильхромов состоит чаще всего из закалки на мартенсит и высокого отпуска.
Жаропрочные свойства сильхромов достаточно высоки до 600 °С, а при более высоких температурах резко снижаются.
В качестве жаростойких сталей аустенитного класса, главным образом, применяются стали на хромоникелевой основе. Эти стали не имеют больших преимуществ по жаростойкости перед высокохромистыми сталями ферритного класса, но выгодно отличаются от них по уровню механических свойств, в том числе жаропрочных, технологичности (способности к глубокой вытяжке, штамповке, свариваемости), они также менее склонны к охрупчиванию после длительных выдержек при высоких температурах.
Недостатком сталей этого класса является их сравнительно высокая стоимость, использование в больших количествах дефицитного никеля, низкие теплопроводность и сопротивление газовой коррозии в средах.
Аустенитные стали (08X18Н9Т, 12Х18Н9, 12Х18Н9Т, 20Х25Н20С2) используют в качестве жаростойкого материала для выхлопных систем, труб, листовых и сортовых деталей при температурах 600—800 °С и невысоких нагрузках. Повышение жаростойкости аустенитных сталей достигается увеличением содержания в стали хрома, никеля, а также дополнительным легированием кремнием. В качестве жаростойких материалов для работы в науглероживающих средах до 1100°С (например, печные контейнеры и арматура) используют стали с повышенным содержанием углерода (сталь 36Х18Н25С2).
Термическая обработка аустенитных жаростойких сталей заключается обычно в закалке от температур 1000—1050 °С.
Жаростойкие сплавы на никельхромовой основе (нихромы) получили значительное распространение в качестве материалов для работы при 800—1100°С, а при кратковременной работе до 1200 °С. Эти сплавы применяют для изготовления деталей газовых турбин, не испытывающих больших рабочих нагрузок и работающих при высоких температурах (камеры сгорания, жаровые трубы, нагревательные элементы электрических печей и других деталей).
Сплавы представляют собой в основном твердый раствор хрома (15—27%) в никеле с г. ц. к. решеткой, слабо упрочняются при термической обработке, имеют высокую пластичность, высокое электросопротивление и хорошие технологические свойства.
В качестве элементов, дополнительно повышающих жаростойкость, применяется алюминий (до 3,5 %), титан, молибден, ниобий в небольших количествах, а также вольфрам.
studfiles.net
Жаростойкие стали и сплавы
Жаростойкость – способность металла сопротивляться окислению в газовой среде или в других окислительных средах при повышенных температурах. Жаропрочные сплавы в принципе должны быть и жаростойкими, иначе они быстро выходят из строя из-за быстрого окисления. Однако, жаростойкие сплавы не всегда бывают жаропрочными.
К жаростойким относятся стали и сплавы, работающие в ненагруженном или слабонагруженном состоянии при температурах выше 550 0С и обладающие стойкостью против химического разрушения поверхности в газовых средах.
Повышение жаростойкости сплавов заключается в легировании добавками, которые, не снижая показателей жаропрочности и других свойств, снижают скорость окисления сплавов за счет образования на их поверхности плотной защитной пленки окислов, хорошо связанных с основой. Диффузия (особенно кислорода) через оксидные пленки затруднена, что приводит к торможению процесса дальнейшего окисления.
Жаростойкость стали достигается введением хрома, никеля, алюминия или кремния, образующих в процессе нагрева защитные пленки оксидов (Cr,Fe)2O3, (Al,Fe)2О3. Введение в сталь 5-8 % хрома повышает жаростойкость до 700-750 0С, до 17% – до 10000С, 25% – 11000С. Дополнительное легирование к 25% хрома 5% алюминия – 1300 0С.
Жаростойкие стали и сплавы разделены на следующие группы:
хромистые и хромоалюминиевые стали ферритного класса;
хромокремнистые мартенситного класса;
хромоникелевые аустенитные стали;
сплавы на хромоникелевой основе.
К группе ферритных хромистых и хромоалюминиевых сталей отнесены высокохромистые стали на основе 13 − 28 % Сг, которые при достаточно низком содержании углерода или легирования их ферритообразующими элементами имеют однофазную ферритную структуру. Эти стали применяют для изготовления теплообменников, деталей аппаратуры химических производств, печного оборудования и других изделий, которые не испытывают значительных нагрузок и работают при высоких температурах длительное время (08Х17Т, 15Х25Т, 15Х28, 1Х13Ю4).
Чем выше содержание хрома, алюминия и кремния в сталях, тем больше температуры, при которых они сохраняют требуемые эксплуатационные свойства.
Стали ферритного класса обладают невысокой прочностью и жаропрочностью, высокой пластичностью и удовлетворительными технологическими свойствами.
Изделия из хромоалюминиевых сталей (содержание А1 от 3,5 до 5,8 %) устойчивы в атмосфере воздуха, в среде сернистых газов, но резко теряют работоспособность в восстановительных средах, содержащих окись углерода, пары воды, а также хлорсодержащих средах. При длительной работе в азотсодержащих средах образуются нитриды алюминия, которые устойчивы до высоких температур и не оказывают вредного влияния на свойства сталей.
Хромистые и хромоалюминиевые стали имеют крупный недостаток: они могут охрупчиваться в процессах технологических нагревов и длительных выдержек при повышенных температурах во время эксплуатации
Жаростойкие стали, имеющие повышенное содержание углерода (до 0,5 − 0,8 %) и легированные совместно хромом (6 − 14%) и кремнием (1 − 3 %) (15Х6СЮ, 40Х10С2М), имеют после закалки или нормализации мартенситную структуру и обычно называются сильхромами. Они обладают хорошим сопротивлением газовой коррозии в продуктах сгорания различных топлив и высокой износостойкостью при трении и ударных нагрузках.
Основное назначение сталей этой группы − клапаны автомобильных, тракторных и авиационных двигателей средней мощности. Кроме того, сильхромы используют в качестве жаростойких сплавов для изготовления регуляторов, теплообменников и колосниковых решеток в котельном и химическом машиностроении.
Термическая обработка сильхромов состоит чаще всего из закалки на мартенсит и высокого отпуска.
Жаропрочные свойства сильхромов достаточно высоки до 600 °С, а при более высоких температурах резко снижаются.
В качестве жаростойких сталей аустенитного класса, главным образом, применяются стали на хромоникелевой основе. Эти стали не имеют больших преимуществ по жаростойкости перед высокохромистыми сталями ферритного класса, но выгодно отличаются от них по уровню механических свойств, в том числе жаропрочных, технологичности (способности к глубокой вытяжке, штамповке, свариваемости), они также менее склонны к охрупчиванию после длительных выдержек при высоких температурах.
Недостатком сталей этого класса является их сравнительно высокая стоимость, использование в больших количествах дефицитного никеля, низкие теплопроводность и сопротивление газовой коррозии в средах.
Аустенитные стали (08X18Н9Т, 12Х18Н9, 12Х18Н9Т, 20Х25Н20С2) используют в качестве жаростойкого материала для выхлопных систем, труб, листовых и сортовых деталей при температурах 600—800 °С и невысоких нагрузках. Повышение жаростойкости аустенитных сталей достигается увеличением содержания в стали хрома, никеля, а также дополнительным легированием кремнием. В качестве жаростойких материалов для работы в науглероживающих средах до 1100°С (например, печные контейнеры и арматура) используют стали с повышенным содержанием углерода (сталь 36Х18Н25С2).
Термическая обработка аустенитных жаростойких сталей заключается обычно в закалке от температур 1000—1050 °С.
Жаростойкие сплавы на никельхромовой основе (нихромы) получили значительное распространение в качестве материалов для работы при 800—1100°С, а при кратковременной работе до 1200 °С. Эти сплавы применяют для изготовления деталей газовых турбин, не испытывающих больших рабочих нагрузок и работающих при высоких температурах (камеры сгорания, жаровые трубы, нагревательные элементы электрических печей и других деталей).
Сплавы представляют собой в основном твердый раствор хрома (15—27%) в никеле с г. ц. к. решеткой, слабо упрочняются при термической обработке, имеют высокую пластичность, высокое электросопротивление и хорошие технологические свойства.
В качестве элементов, дополнительно повышающих жаростойкость, применяется алюминий (до 3,5 %), титан, молибден, ниобий в небольших количествах, а также вольфрам.
studfiles.net
75 группа 2 вариант / Материаловедение / Лекции / 21 Коррозионно-стойкие стали и сплавы. Жаростойкие стали и сплавы. Жаропрочные стали и сплавы
Лекция 20
Коррозионно-стойкие стали и сплавы. Жаростойкие стали и сплавы. Жаропрочные стали и сплавы
Коррозия электрохимическая и химическая.
Классификация коррозионно-стойких сталей и сплавов
Хромистые стали.
Жаростойкость, жаростойкие стали и сплавы.
Жаропрочность, жаропрочные стали и сплавы
Классификация жаропрочных сталей и сплавов
Коррозия электрохимическая и химическая.
Разрушение металла под воздействием окружающей среды называют коррозией.
Коррозия помимо уничтожения металла отрицательно влияет на эксплуатационные характеристики деталей, содействуя всем видам разрушения.
Коррозия в зависимости от характера окружающей среды может быть химической и электрохимической.
Электрохимическаякоррозия имеет место в водных растворах, а так же в обыкновенной атмосфере, где имеется влага.
Сущность этой коррозии в том, что ионы металла на поверхности детали, имея малую связь с глубинными ионами, легко отрываются от металла молекулами воды.
Металл, потеряв часть положительно заряженных частиц, ионов, заряжается отрицательно за счет избыточного количества оставшихся электронов. Одновременно слой воды, прилегающий к металлу, за счет ионов металла приобретает положительный заряд. Разность зарядов на границе металл – вода обуславливает скачок потенциала, который в процессе коррозии изменяется, увеличиваясь от растворения металла, и уменьшаясь от осаждения ионов из раствора на металле.
Если количество ионов переходящих в раствор и осаждающихся на металле одинаково, то скорости растворения и осаждения металла равны и процесс коррозии (разрушения металла) не происходит. Этому соответствует равновесный потенциал .
За нулевой потенциал принимают равновесный потенциал водородного иона в водном растворе при концентрации положительных ионов водорода, равной 1 моль ионов +на 1 литр.
Стандартные потенциалы других элементов измерены по отношению к водородному потенциалу.
Металлы, стандартный потенциал которых отрицательный – корродируют в воде, в которой растворен кислород тем активнее, чем отрицательней значение электрохимического потенциала.
Уходящие ионы металла, взаимодействуя с ионами , образуют гидроксиды, нерастворимые в воде, которые называютржавчиной,а процесс их образования –ржавлением.
Схема ржавления железа:
;
Гидроксид железа в присутствии кислорода, растворенного в воде, превращается в . Так как это нерастворимое соединение, то равновесный потенциал не может быть достигнут и коррозия будет продолжаться до полного разрушения.
В зависимости от структуры коррозия имеет разное проявление: при однородном металле – коррозия происходит равномерно по всей поверхности. При неоднородном металле – коррозия избирательная и называется точечной. Это явление наиболее опасно, так как приводит к быстрой порче всего изделия. Избирательная коррозия создает очаги концентрации напряжений, что содействует разрушению.
Химическая коррозияможет происходить за счет взаимодействия металла с газовой средой при отсутствии влаги. Продуктом коррозии являются оксиды металла. Образуется пленка на поверхности металла толщиной в 1…2 периода кристаллической решетки. Этот слой изолирует металл от кислорода и препятствует дальнейшему окислению, защищает от электрохимической коррозии в воде. При создании коррозионно-стойких сплавов – сплав должен иметь повышенное значение электрохимического потенциала и быть по возможности однофазным.
Классификация коррозионно-стойких сталей и сплавов
Коррозионная стойкость может быть повышена, если содержание углерода свести до минимума, если ввести легирующий элемент, образующий с железом твердые растворы в таком количестве, при котором скачкообразно повысится электродный потенциал сплава.
Важнейшими коррозионно-стойкими техническими сплавами являются нержавеющие стали с повышенным содержанием хрома: хромистые и хромоникелевые. На рис. 20.1 показано влияние количества хрома в железохромистых сплавах на электрохимический потенциал сплава.
Рис 20.1. Влияние хрома на потенциал сплавов
Хромистые стали.
Содержание хрома должно быть не менее 13% (13…18%).
Коррозионная стойкость объясняется образованием на поверхности защитной пленки оксида .
Углерод в нержавеющих сталях является нежелательным, так как он обедняет раствор хромом, связывая его в карбиды, и способствует получению двухфазного состояния. Чем ниже содержание углерода, тем выше коррозионная стойкость нержавеющих сталей.
Различают стали ферритного класса08Х13, 12Х17, 08Х25Т, 15Х28. Стали с повышенным содержанием хрома не имеют фазовых превращений в твердом состоянии и поэтому не могут быть подвергнуты закалке. Значительным недостатком ферритных хромистых сталей является повышенная хрупкость из-за крупнокристаллической структуры. Эти стали склонны к межкристаллитной коррозии (по границам зерен) из-за обеднения хромом границ зерен. Для избежания этого вводят небольшое количество титана. Межкристаллитная коррозия обусловлена тем, что часть хрома около границ зерна взаимодействует с углеродом и образует карбиды. Концентрация хрома в твердом растворе у границ становится меньше 13% и сталь приобретает отрицательный потенциал.
Из-за склонности к росту зерна ферритные стали требуют строгих режимов сварки и интенсивного охлаждения зоны сварного шва. Недостатком является и склонность к охрупчиванию при нагреве в интервале температур 450…500oС
Из ферритных сталей изготавливают оборудование азотно-кислотных заводов (емкости, трубы).
Для повышения механических свойств ферритных хромистых сталей в них добавляют 2…3 % никеля. Стали 10Х13Н3, 12Х17Н2 используются для изготовления тяжелонагруженных деталей, работающих в агрессивных средах.
После закалки от температуры 1000oC и отпуска при 700…750oС предел текучести сталей составляет 1000 МПа.
Термическую обработку для ферритных сталей проводят для получения структуры более однородного твердого раствора, что увеличивает коррозионную стойкость.
Стали мартенситного класса20Х13, 30Х13, 40Х13. После закалки и отпуска при 180…250oС стали 30Х13, 40Х13 имеют твердость 50…60 HRC и используются для изготовления режущего инструмента (хирургического), пружин для работы при температуре 400…450o, предметов домашнего обихода.
Стали аустенитного класса– высоколегированные хромоникелевые стали.
Никель – аустенитообразующий элемент, сильно понижающий критические точки превращения. После охлаждения на воздухе до комнатной температуры имеет структуру аустенита.
Нержавеющие стали аустенитного класса 04Х18Н10, 12Х18Н9Т имеют более высокую коррозионную стойкость, лучшие технологические свойства по сравнению с хромистыми нержавеющими сталями, лучше свариваются. Они сохраняют прочность до более высоких температур, менее склонны к росту зерна при нагреве и не теряют пластичности при низких температурах.
Хромоникелевые стали коррозионностойки в окислительных средах. Основным элементом является хром, никель только повышает коррозионную стойкость.
Для большей гомогенности хромоникелевые стали подвергают закалке с температуры 1050…1100oCв воде. При нагреве происходит растворение карбидов хрома в аустените. Выделение их из аустенита при закалке исключено, так как скорость охлаждения велика. Получают предел прочности = 500…600 МПа, и высокие характеристики пластичности, относительное удлинение = 35…45%.
Упрочняют аустенитные стали холодной пластической деформацией, что вызывает эффект наклепа. Предел текучести при этом может достигнуть значений 1000…1200 МПа, а предел прочности – 1200…1400 МПа.
Для уменьшения дефицитного никеля часть его заменяют марганцем (сталь 40Х14Г14Н3Т) или азотом (сталь 10Х20Н4АГ11).
Аустенитно-ферритные стали12Х21Н5Т, 08Х22Н6Т являются заменителями хромоникелевых сталей с целью экономии никеля.
Свойства сталей зависят от соотношения ферритной и аустенитной фаз (оптимальные свойства получают при соотношении – Ф:А=1:1 ). Термическая обработка сталей включает закалку от температуры 1100…1150oC и отпуск-старение при температуре 500…750oC.
Аустенитно-ферритные стали не подвержены коррозионному растрескиванию под напряжением: трещины могут возникать только на аустенитных участках, но ферритные участки задерживают их развитие. При комнатных температурах аустенитно-ферритные стали имеют твердость и прочность выше, а пластичность и ударную вязкость ниже, чем стали аустенитного класса.
Кроме нержавеющих сталей в промышленности применяют коррозионно-стойкие сплавы – это сплавына никелевой основе.Сплавы типахастеллойсодержат до 80 % никеля, другим элементом является молибден в количестве до 15…30 %. Сплавы являются коррозионно-стойкими в особо агрессивных средах (кипящая фосфорная или соляная кислота), обладают высокими механическими свойствами. После термической обработки – закалки и старения при температуре 800oС – сплавы имеют предел прочности МПа, и твердость . Недостатком является склонность к межкристаллической коррозии, поэтому содержание углерода в этих сплавах должно быть минимальным.
Жаростойкость, жаростойкие стали и сплавы.
Жаростойкость (окалиностойкость)– это способность металлов и сплавов сопротивляться газовой коррозии при высоких температурах в течение длительного времени.
Если изделие работает в окислительной газовой среде при температуре 500..550oC без больших нагрузок, то достаточно, чтобы они были только жаростойкими (например, детали нагревательных печей).
Сплавы на основе железа при температурах выше 570oC интенсивно окисляются, так как образующаяся в этих условиях на поверхности металла оксид железа (вюстит) с простой решеткой, имеющей дефицит атомов кислорода (твердый раствор вычитания), не препятствует диффузии кислорода и металла. Происходит интенсивное образование хрупкой окалины.
Рис. 20.2. Влияние хрома на жаростойкость хромистой стали
Для повышения жаростойкости в состав стали вводят элементы, которые образуют с кислородом оксиды с плотным строением кристаллической решетки (хром, кремний, алюминий).
Степень легированости стали, для предотвращения окисления, зависит от температуры. Влияние хрома на жаростойкость хромистой стали показано на рис.20.2.
Чем выше содержание хрома, тем более окалиностойки стали (например, сталь 15Х25Т является окалиностойкой до температуры 1100…1150oC).
Высокой жаростойкостью обладают сильхромы, сплавы на основе никеля – нихромы, стали 08Х17Т, 36Х18Н25С2, 15Х6СЮ.
Жаропрочность, жаропрочные стали и сплавы
Жаропрочность– это способность металла сопротивляться пластической деформации и разрушению при высоких температурах.
Жаропрочные материалы используются для изготовления деталей, работающих при высоких температурах, когда имеет место явление ползучести.
Критериями оценки жаропрочности являются кратковременная и длительная прочности, ползучесть.
Кратковременная прочностьопределяется с помощью испытаний на растяжение разрывных образцов. Образцы помещают в печь и испытывают при заданной температуре. Обозначают кратковременную прочность =, например 300oС= 300МПа.
Прочность зависит от продолжительности испытаний.
Пределом длительной прочностиназывается максимальное напряжение , которое вызывает разрушение образца при заданной температуре за определенное время.
Например = 200 МПа, верхний индекс означает температуру испытаний, а нижний – заданную продолжительность испытания в часах. Для котельных установок требуется невысокое значение прочности, но в течение нескольких лет.
Ползучесть – свойство металла медленно пластически деформироваться под действием постоянной нагрузки при постоянной температуре.
При испытаниях образцы помещают в печь с заданной температурой и прикладывают постоянную нагрузку. Измеряют деформацию индикаторами.
При обычной температуре и напряжениях выше предела упругости ползучесть не наблюдается, а при температуре выше 0,6Тпл, когда протекают процессы разупрочнения, и при напряжениях выше предела упругости наблюдается ползучесть.
В зависимости от температуры скорость деформации при постоянной нагрузке выражается кривой состоящей из трех участков (рис. 20.3):
Рис. 20.3. Кривая ползучести
ОА – упругая деформация образца в момент приложения нагрузки;
АВ – участок, соответствующий начальной скорости ползучести;
ВС – участок установившейся скорости ползучести, когда удлинение имеет постоянную скорость.
Если напряжения достаточно велики, то протекает третья стадия (участок СД), связанная с началом разрушения образца (образование шейки).
Для углеродистых сталей ползучесть наблюдается при нагреве выше 400oС.
Предел ползучести– напряжение, которое за определенное время при заданной температуре вызывает заданное суммарное удлинение или заданную скорость деформации .
НапримерМПа, где верхний индекс – температура испытания вoС, первый нижний индекс – заданное суммарное удлинение в процентах, второй – заданная продолжительность испытания в часах.
Классификация жаропрочных сталей и сплавов
В качестве современных жаропрочных материалов можно отметить перлитные,мартенситные и аустенитныежаропрочные стали,никелевые и кобальтоавыежаропрочные сплавы,тугоплавкиеметаллы.
При температурах до 300oC обычные конструкционные стали имеют высокую прочность, нет необходимости использовать высоколегированные стали.
Для работы в интервале температур 350…500oC применяют легированные стали перлитного, ферритного и мартенситного классов.
Перлитные жаропрочные стали. К этой группе относятся котельные стали и сильхромы. Эти стали применяются для изготовления деталей котельных агрегатов, паровых турбин, двигателей внутреннего сгорания. Стали содержат относительно мало углерода. Легирование сталей хромом, молибденом и ванадием производится для повышения температуры рекристаллизации (марки 12Х1МФ, 20Х3МФ). Используются в закаленном и высокоотпущенном состоянии. Иногда закалку заменяют нормализацией. В результате этого образуются пластинчатые продукты превращения аустенита, которые обеспечивают более высокую жаропрочность. Предел ползучести этих сталей должен обеспечить остаточную деформацию в пределах 1 % за время 10000…100000 ч работы.
Перлитные стали обладают удовлетворительной свариваемостью, поэтому используются для сварных конструкций (например, трубы пароперегревателей).
Для деталей газовых турбин применяют сложнолегированные стали мартенситногокласса12Х2МФСР, 12Х2МФБ, 15Х12ВНМФ. Увеличение содержания хрома повышает жаростойкость сталей. Хром, вольфрам, молибден и ванадий повышают температуру рекристаллизации, образуются карбиды, повышающие прочность после термической обработки. Термическая обработка состоит из закалки от температур выше 1000oС в масле или на воздухе и высокого отпуска при температурах выше температуры эксплуатации.
Для изготовления жаропрочных деталей, не требующих сварки (клапаны двигателей внутреннего сгорания), применяются хромокремнистые стали – сильхромы:40Х10С2М, 40Х9С2, Х6С.
Жаролрочные свойства растут с увеличением степени легированности. Сильхромы подвергаются закалке от температуры около 1000oС и отпуску при температуре 720…780oС.
При рабочих температурах 500…700oC применяются сталиаустенитного класса. Из этих сталей изготавливают клапаны двигателей, лопатки газовых турбин,сопловые аппараты реактивных двигателей и т.д.
Основными жаропрочными аустенитными сталями являются хромоникелевые стали, дополнительно легированные вольфрамом, молибденом, ванадием и другими элементами. Стали содержат 15…20 % хрома и 10…20 % никеля. Обладают жаропрочностью и жаростойкостью, пластичны, хорошо свариваются, но затруднена обработка резанием и давлением, охрупчиваются в интервале температур около 600oС, из-за выделения по границам различных фаз.
По структуре стали подразделяются на две группы:
1. Аустенитные стали с гомогенной структурой17Х18Н9, 09Х14Н19В2БР1,12Х18Н12Т. Содержание углерода в этих сталях минимальное. Для создания большей однородности аустенита стали подвергаются закалке с 1050…1100oС в воде, затем для стабилизации структуры – отпуску при 750oС.
2. Аустенитные стали с гетерогенной структурой 37Х12Н8Г8МФБ, 10Х11Н20Т3Р.
Термическая обработка сталей включает закалку с 1050…1100oС. После закалки старение при температуре выше эксплуатационной (600…750oС). В процессе выдержки при этих температурах в дисперсном виде выделяются карбиды, карбонитриды, вследствие чего прочность стали повышается.
Детали, работающие при температурах 700…900oC, изготавливают из сплавов на основеникеля и кобальта(например, турбины реактивных двигателей).
Никелевые сплавы преимущественно применяют в деформированном виде. Они содержат более 55 % никеля и минимальное количество углерода (0,06…0,12 %). По жаропрочным свойствам превосходят лучшие жаропрочные стали.
По структуре никелевые сплавы разделяют на гомогенные (нихромы)игетерогенные(нимоники).
Нихромы.Основой этих сплавов является никель, а основным легирующим элементом – хром (ХН60Ю, ХН78Т).
Нихромы не обладают высокой жаропрочностью, но они очень жаростойки. Их применяют для малонагруженных деталей, работающих в окислительных средах, в том числе и для нагревательных элементов.
Нимоники являются четвертными сплавами никель – хром (около 20 %) – титан (около 2%) – алюминий (около 1 %) (ХН77ТЮ, ХН70МВТЮБ, ХН55ВМТФКЮ). Используются только в термически обработанном состоянии. Термическая обработка состоит из закалки с 1050…1150oС на воздухе и отпуска – старения при 600…800oС.
Увеличение жаропрочности сложнолегированных никелевых сплавов достигается упрочнением твердого раствора введением кобальта, молибдена, вольфрама.
Основными материалами, которые могут работать при температурах выше 900oC (до 2500oС), являютсясплавы на основе тугоплавких металлов– вольфрама, молибдена, ниобия и других.
Температуры плавления основных тугоплавких металлов: вольфрам – 3400oС, тантал – 3000oС, молибден – 2640oС, ниобий – 2415oС, хром – 1900oС.
Высокая жаропрочность таких металлов обусловлена большими силами межатомных связей в кристаллической решетке и высокими температурами рекристаллизации.
Наиболее часто применяют сплавы на основе молибдена. В качестве легирующих добавок в сплавы вводят титан, цирконий, ниобий. С целью защиты от окисления проводят силицирование, на поверхности сплавов образуется слой MoSi2толщиной 0,03…0,04 мм. При температуре 1700oС силицированные детали могут работать 30 часов.
Вольфрам – наиболее тугоплавкий металл. Его используют в качестве легирующего элемента в сталях и сплавах различного назначения, в электротехнике и электронике (нити накала, нагреватели в вакуумных приборах).
В качестве легирующих элементов к вольфраму добавляют молибден, рений, тантал. Сплавы вольфрама с рением сохраняют пластичность до –196oС и имеют предел прочности 150 МПа при температуре 1800oС.
Для сплавов на основе вольфрама характерна низкая жаростойкость, пленки образующихся оксидов превышают объем металла более, чем в три раза, поэтому они растрескиваются и отслаиваются Изготавливают изделия, работающие в вакууме).
studfiles.net
Жаростойкость и жаропрочность – это важные характеристики сталей
Жаростойкость и жаропрочность являются очень важными характеристиками. Некоторые изделия машиностроения работают в очень сложных условиях при повышенных температурах. Обычные конструкционные стали при нагреве скачкообразно меняют свои механические и физические свойства, начинают активно окисляться и образовывать окалину, что совершенно неприемлемо и создает угрозу выхода из строя всего узла, а возможно, и серьезной аварии. Для работы при повышенных температурах инженеры-материаловеды при помощи металлургов создали ряд специальных сталей и сплавов. В данной статье дается их краткая характеристика.
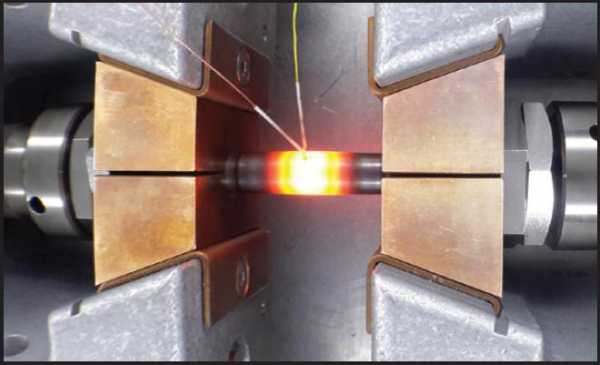
Жаропрочные стали
Многие люди отождествляют понятие жаростойкости с таким понятием, как жаропрочность. Этого делать ни в коем случае нельзя. Жаропрочность еще называют красноломкостью. И под этим понятием подразумевают способность металла (либо сплава) сохранять высокие механические свойства при работе в условиях повышенных температур. То есть такой металл, даже будучи нагретым до красного свечения (оно характерно для температур выше 550 °С), не поползет и сохранит достаточную жесткость.
Говоря простым языком, жаропрочность – это способность материала сохранять работоспособность при нагреве до высоких температур. Обычные конструкционные стали даже при незначительном нагреве становятся пластичными, что исключает возможность их применения для изготовления изделий, работающих при высоких температурах.
Разные марки металлов и сплавов обладают различной жаропрочностью. Этот показатель зависит от химического состава материала. Испытания на жаропрочность могут проводиться на протяжении длительного времени. Но чаще всего образцы, нагретые в печи до определенной температуры, испытывают на растяжение в течение короткого отрезка времени.
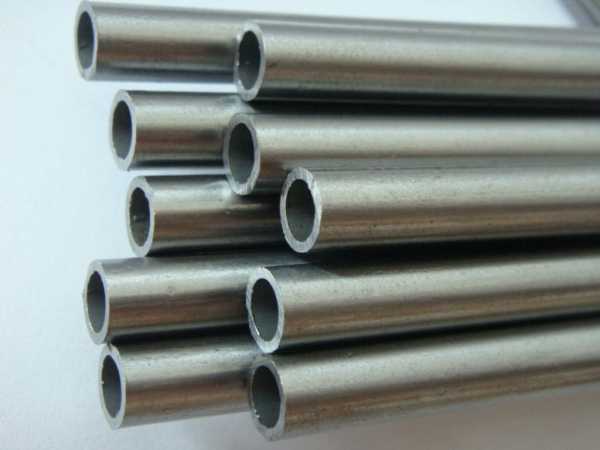
Жаростойкие стали
Жаростойкость, в отличие от жаропрочности, – это способность материалов противостоять развитию коррозионных процессов при работе в условиях высоких температур. Обычные стали, если их подвергнуть нагреву (за исключением термической обработки в защитной атмосфере или в вакууме), начинают окисляться. Кроме того, при длительном нагреве углерод на поверхности изделия начинает выгорать. В результате поверхность обедняется углеродом, что приводит к резкому изменению механических свойств (прежде всего, твердости) на поверхности. Износостойкость падает. Получает развитие такое негативное явление, как задиры. Данная группа сталей может работать при температурах около 550 °С.
С целью увеличить жаростойкость стали, ее расплав легируют кремнием, алюминием и хромом. Иногда достаточно повысить жаростойкость поверхности детали. В таком случае прибегают к силицированию или алитированию (насыщению поверхностного слоя соответственно атомами кремния или алюминия) в порошковой среде.
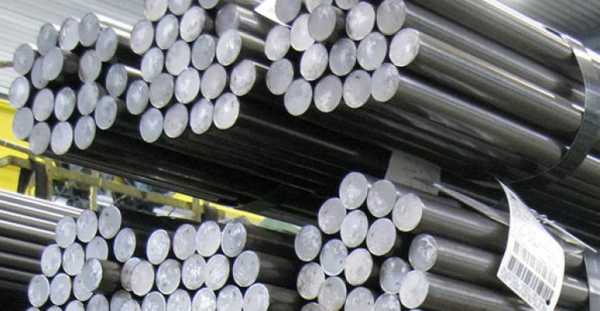
Материалы с высокой температурой плавления
При эксплуатации в условиях особенно высоких температур рассмотренные материалы не могут использоваться, так как при температуре в районе 2000 °С начинает протекать оплавление (выделяется жидкая фаза). Для этих целей используют тугоплавкие металлы: вольфрам, ниобий, ванадий, цирконий и так далее. Эти материалы довольно дорогие, но инженеры еще не нашли для них достойной альтернативы.
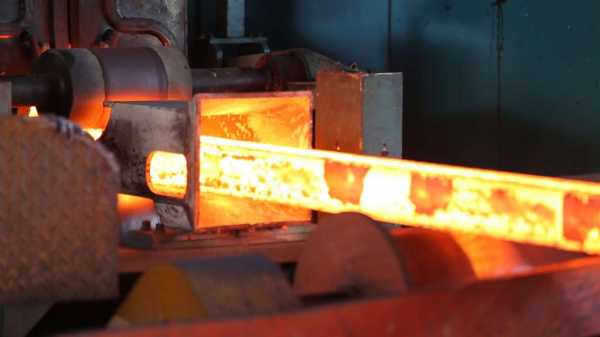
Характеристика сплавов на основе хрома и никеля
Сплавы, обладающие большой жаропрочностью, очень востребованы в энергетическом машиностроении (лопатки паровых турбин, части двигателей летательных аппаратов и так далее). Причем потребность в подобных материалах постоянно растет. Более того, производство требует от ученых получения все более и более совершенных материалов, способных сохранять свою работоспособность при очень высоких температурах. Поэтому постоянно ведутся работы по увеличению показателей жаропрочности. Никель, точнее легирование этим элементом стали, способствует этому.
Все жаростойкие стали легируются никелем (не менее 65 %). В обязательном порядке имеется и хром. Содержание этого элемента не должно быть менее 14 %. В противном случае поверхность металла будет интенсивно окисляться.
Стали, дополнительно легируются алюминием, ванадием и другими тугоплавкими элементами. Алюминий, например, даже при комнатной температуре покрывается тонкой окисной пленкой, которая препятствует проникновению коррозии вглубь металла. То есть не образуется окалина.
fb.ru
Лекция 20 Коррозионно-стойкие стали и сплавы. Жаростойкие стали и сплавы. Жаропрочные стали и сплавы
Коррозия электрохимическая и химическая.
Классификация коррозионно-стойких сталей и сплавов
Хромистые стали.
Жаростойкость, жаростойкие стали и сплавы.
Жаропрочность, жаропрочные стали и сплавы
Классификация жаропрочных сталей и сплавов
Коррозия электрохимическая и химическая.
Разрушение металла под воздействием окружающей среды называют коррозией.
Коррозия помимо уничтожения металла отрицательно влияет на эксплуатационные характеристики деталей, содействуя всем видам разрушения.
Коррозия в зависимости от характера окружающей среды может быть химической и электрохимической.
Электрохимическаякоррозия имеет место в водных растворах, а так же в обыкновенной атмосфере, где имеется влага.
Сущность этой коррозии в том, что ионы металла на поверхности детали, имея малую связь с глубинными ионами, легко отрываются от металла молекулами воды.
Металл, потеряв часть положительно заряженных частиц, ионов, заряжается отрицательно за счет избыточного количества оставшихся электронов. Одновременно слой воды, прилегающий к металлу, за счет ионов металла приобретает положительный заряд. Разность зарядов на границе металл – вода обуславливает скачок потенциала, который в процессе коррозии изменяется, увеличиваясь от растворения металла, и уменьшаясь от осаждения ионов из раствора на металле.
Если количество ионов переходящих в раствор и осаждающихся на металле одинаково, то скорости растворения и осаждения металла равны и процесс коррозии (разрушения металла) не происходит. Этому соответствует равновесный потенциал .
За нулевой потенциал принимают равновесный потенциал водородного иона в водном растворе при концентрации положительных ионов водорода, равной 1 моль ионов +на 1 литр.
Стандартные потенциалы других элементов измерены по отношению к водородному потенциалу.
Металлы, стандартный потенциал которых отрицательный – корродируют в воде, в которой растворен кислород тем активнее, чем отрицательней значение электрохимического потенциала.
Уходящие ионы металла, взаимодействуя с ионами , образуют гидроксиды, нерастворимые в воде, которые называютржавчиной,а процесс их образования –ржавлением.
Схема ржавления железа:
;
Гидроксид железа в присутствии кислорода, растворенного в воде, превращается в. Так как это нерастворимое соединение, то равновесный потенциал не может быть достигнут и коррозия будет продолжаться до полного разрушения.
В зависимости от структуры коррозия имеет разное проявление: при однородном металле – коррозия происходит равномерно по всей поверхности. При неоднородном металле – коррозия избирательная и называется точечной. Это явление наиболее опасно, так как приводит к быстрой порче всего изделия. Избирательная коррозия создает очаги концентрации напряжений, что содействует разрушению.
Химическая коррозияможет происходить за счет взаимодействия металла с газовой средой при отсутствии влаги. Продуктом коррозии являются оксиды металла. Образуется пленка на поверхности металла толщиной в 1…2 периода кристаллической решетки. Этот слой изолирует металл от кислорода и препятствует дальнейшему окислению, защищает от электрохимической коррозии в воде. При создании коррозионно-стойких сплавов – сплав должен иметь повышенное значение электрохимического потенциала и быть по возможности однофазным.
Классификация коррозионно-стойких сталей и сплавов
Коррозионная стойкость может быть повышена, если содержание углерода свести до минимума, если ввести легирующий элемент, образующий с железом твердые растворы в таком количестве, при котором скачкообразно повысится электродный потенциал сплава.
Важнейшими коррозионно-стойкими техническими сплавами являются нержавеющие стали с повышенным содержанием хрома: хромистые и хромоникелевые. На рис. 20.1 показано влияние количества хрома в железохромистых сплавах на электрохимический потенциал сплава.
Рис 20.1. Влияние хрома на потенциал сплавов
Хромистые стали.
Содержание хрома должно быть не менее 13% (13…18%).
Коррозионная стойкость объясняется образованием на поверхности защитной пленки оксида .
Углерод в нержавеющих сталях является нежелательным, так как он обедняет раствор хромом, связывая его в карбиды, и способствует получению двухфазного состояния. Чем ниже содержание углерода, тем выше коррозионная стойкость нержавеющих сталей.
Различают стали ферритного класса08Х13, 12Х17, 08Х25Т, 15Х28. Стали с повышенным содержанием хрома не имеют фазовых превращений в твердом состоянии и поэтому не могут быть подвергнуты закалке. Значительным недостатком ферритных хромистых сталей является повышенная хрупкость из-за крупнокристаллической структуры. Эти стали склонны к межкристаллитной коррозии (по границам зерен) из-за обеднения хромом границ зерен. Для избежания этого вводят небольшое количество титана. Межкристаллитная коррозия обусловлена тем, что часть хрома около границ зерна взаимодействует с углеродом и образует карбиды. Концентрация хрома в твердом растворе у границ становится меньше 13% и сталь приобретает отрицательный потенциал.
Из-за склонности к росту зерна ферритные стали требуют строгих режимов сварки и интенсивного охлаждения зоны сварного шва. Недостатком является и склонность к охрупчиванию при нагреве в интервале температур 450…500oС
Из ферритных сталей изготавливают оборудование азотно-кислотных заводов (емкости, трубы).
Для повышения механических свойств ферритных хромистых сталей в них добавляют 2…3 % никеля. Стали 10Х13Н3, 12Х17Н2 используются для изготовления тяжелонагруженных деталей, работающих в агрессивных средах.
После закалки от температуры 1000oC и отпуска при 700…750oС предел текучести сталей составляет 1000 МПа.
Термическую обработку для ферритных сталей проводят для получения структуры более однородного твердого раствора, что увеличивает коррозионную стойкость.
Стали мартенситного класса20Х13, 30Х13, 40Х13. После закалки и отпуска при 180…250oС стали 30Х13, 40Х13 имеют твердость 50…60 HRC и используются для изготовления режущего инструмента (хирургического), пружин для работы при температуре 400…450o, предметов домашнего обихода.
Стали аустенитного класса– высоколегированные хромоникелевые стали.
Никель – аустенитообразующий элемент, сильно понижающий критические точки превращения. После охлаждения на воздухе до комнатной температуры имеет структуру аустенита.
Нержавеющие стали аустенитного класса 04Х18Н10, 12Х18Н9Т имеют более высокую коррозионную стойкость, лучшие технологические свойства по сравнению с хромистыми нержавеющими сталями, лучше свариваются. Они сохраняют прочность до более высоких температур, менее склонны к росту зерна при нагреве и не теряют пластичности при низких температурах.
Хромоникелевые стали коррозионностойки в окислительных средах. Основным элементом является хром, никель только повышает коррозионную стойкость.
Для большей гомогенности хромоникелевые стали подвергают закалке с температуры 1050…1100oCв воде. При нагреве происходит растворение карбидов хрома в аустените. Выделение их из аустенита при закалке исключено, так как скорость охлаждения велика. Получают предел прочности= 500…600 МПа, и высокие характеристики пластичности, относительное удлинение= 35…45%.
Упрочняют аустенитные стали холодной пластической деформацией, что вызывает эффект наклепа. Предел текучести при этом может достигнуть значений 1000…1200 МПа, а предел прочности – 1200…1400 МПа.
Для уменьшения дефицитного никеля часть его заменяют марганцем (сталь 40Х14Г14Н3Т) или азотом (сталь 10Х20Н4АГ11).
Аустенитно-ферритные стали12Х21Н5Т, 08Х22Н6Т являются заменителями хромоникелевых сталей с целью экономии никеля.
Свойства сталей зависят от соотношения ферритной и аустенитной фаз (оптимальные свойства получают при соотношении – Ф:А=1:1 ). Термическая обработка сталей включает закалку от температуры 1100…1150oC и отпуск-старение при температуре 500…750oC.
Аустенитно-ферритные стали не подвержены коррозионному растрескиванию под напряжением: трещины могут возникать только на аустенитных участках, но ферритные участки задерживают их развитие. При комнатных температурах аустенитно-ферритные стали имеют твердость и прочность выше, а пластичность и ударную вязкость ниже, чем стали аустенитного класса.
Кроме нержавеющих сталей в промышленности применяют коррозионно-стойкие сплавы – это сплавына никелевой основе.Сплавы типахастеллойсодержат до 80 % никеля, другим элементом является молибден в количестве до 15…30 %. Сплавы являются коррозионно-стойкими в особо агрессивных средах (кипящая фосфорная или соляная кислота), обладают высокими механическими свойствами. После термической обработки – закалки и старения при температуре 800oС – сплавы имеют предел прочностиМПа, и твердость. Недостатком является склонность к межкристаллической коррозии, поэтому содержание углерода в этих сплавах должно быть минимальным.
Жаростойкость, жаростойкие стали и сплавы.
Жаростойкость (окалиностойкость)– это способность металлов и сплавов сопротивляться газовой коррозии при высоких температурах в течение длительного времени.
Если изделие работает в окислительной газовой среде при температуре 500..550oC без больших нагрузок, то достаточно, чтобы они были только жаростойкими (например, детали нагревательных печей).
Сплавы на основе железа при температурах выше 570oC интенсивно окисляются, так как образующаяся в этих условиях на поверхности металла оксид железа(вюстит) с простой решеткой, имеющей дефицит атомов кислорода (твердый раствор вычитания), не препятствует диффузии кислорода и металла. Происходит интенсивное образование хрупкой окалины.
Рис. 20.2. Влияние хрома на жаростойкость хромистой стали
Для повышения жаростойкости в состав стали вводят элементы, которые образуют с кислородом оксиды с плотным строением кристаллической решетки (хром, кремний, алюминий).
Степень легированости стали, для предотвращения окисления, зависит от температуры. Влияние хрома на жаростойкость хромистой стали показано на рис.20.2.
Чем выше содержание хрома, тем более окалиностойки стали (например, сталь 15Х25Т является окалиностойкой до температуры 1100…1150oC).
Высокой жаростойкостью обладают сильхромы, сплавы на основе никеля – нихромы, стали 08Х17Т, 36Х18Н25С2, 15Х6СЮ.
Жаропрочность, жаропрочные стали и сплавы
Жаропрочность– это способность металла сопротивляться пластической деформации и разрушению при высоких температурах.
Жаропрочные материалы используются для изготовления деталей, работающих при высоких температурах, когда имеет место явление ползучести.
Критериями оценки жаропрочности являются кратковременная и длительная прочности, ползучесть.
Кратковременная прочностьопределяется с помощью испытаний на растяжение разрывных образцов. Образцы помещают в печь и испытывают при заданной температуре. Обозначают кратковременную прочность=, например300oС= 300МПа.
Прочность зависит от продолжительности испытаний.
Пределом длительной прочностиназывается максимальное напряжение, которое вызывает разрушение образца при заданной температуре за определенное время.
Например = 200 МПа, верхний индекс означает температуру испытаний, а нижний – заданную продолжительность испытания в часах. Для котельных установок требуется невысокое значение прочности, но в течение нескольких лет.
Ползучесть – свойство металла медленно пластически деформироваться под действием постоянной нагрузки при постоянной температуре.
При испытаниях образцы помещают в печь с заданной температурой и прикладывают постоянную нагрузку. Измеряют деформацию индикаторами.
При обычной температуре и напряжениях выше предела упругости ползучесть не наблюдается, а при температуре выше 0,6Тпл, когда протекают процессы разупрочнения, и при напряжениях выше предела упругостинаблюдается ползучесть.
В зависимости от температуры скорость деформации при постоянной нагрузке выражается кривой состоящей из трех участков (рис. 20.3):
Рис. 20.3. Кривая ползучести
ОА – упругая деформация образца в момент приложения нагрузки;
АВ – участок, соответствующий начальной скорости ползучести;
ВС – участок установившейся скорости ползучести, когда удлинение имеет постоянную скорость.
Если напряжения достаточно велики, то протекает третья стадия (участок СД), связанная с началом разрушения образца (образование шейки).
Для углеродистых сталей ползучесть наблюдается при нагреве выше 400oС.
Предел ползучести– напряжение, которое за определенное время при заданной температуре вызывает заданное суммарное удлинение или заданную скорость деформации.
НапримерМПа, где верхний индекс – температура испытания вoС, первый нижний индекс – заданное суммарное удлинение в процентах, второй – заданная продолжительность испытания в часах.
Классификация жаропрочных сталей и сплавов
В качестве современных жаропрочных материалов можно отметить перлитные,мартенситные и аустенитныежаропрочные стали,никелевые и кобальтоавыежаропрочные сплавы,тугоплавкиеметаллы.
При температурах до 300oC обычные конструкционные стали имеют высокую прочность, нет необходимости использовать высоколегированные стали.
Для работы в интервале температур 350…500oC применяют легированные стали перлитного, ферритного и мартенситного классов.
Перлитные жаропрочные стали. К этой группе относятся котельные стали и сильхромы. Эти стали применяются для изготовления деталей котельных агрегатов, паровых турбин, двигателей внутреннего сгорания. Стали содержат относительно мало углерода. Легирование сталей хромом, молибденом и ванадием производится для повышения температуры рекристаллизации (марки 12Х1МФ, 20Х3МФ). Используются в закаленном и высокоотпущенном состоянии. Иногда закалку заменяют нормализацией. В результате этого образуются пластинчатые продукты превращения аустенита, которые обеспечивают более высокую жаропрочность. Предел ползучести этих сталей должен обеспечить остаточную деформацию в пределах 1 % за время 10000…100000 ч работы.
Перлитные стали обладают удовлетворительной свариваемостью, поэтому используются для сварных конструкций (например, трубы пароперегревателей).
Для деталей газовых турбин применяют сложнолегированные стали мартенситногокласса12Х2МФСР, 12Х2МФБ, 15Х12ВНМФ. Увеличение содержания хрома повышает жаростойкость сталей. Хром, вольфрам, молибден и ванадий повышают температуру рекристаллизации, образуются карбиды, повышающие прочность после термической обработки. Термическая обработка состоит из закалки от температур выше 1000oС в масле или на воздухе и высокого отпуска при температурах выше температуры эксплуатации.
Для изготовления жаропрочных деталей, не требующих сварки (клапаны двигателей внутреннего сгорания), применяются хромокремнистые стали – сильхромы:40Х10С2М, 40Х9С2, Х6С.
Жаропрочные свойства растут с увеличением степени легированности. Сильхромы подвергаются закалке от температуры около 1000oС и отпуску при температуре 720…780oС.
При рабочих температурах 500…700oC применяются сталиаустенитного класса. Из этих сталей изготавливают клапаны двигателей, лопатки газовых турбин,сопловые аппараты реактивных двигателей и т.д.
Основными жаропрочными аустенитными сталями являются хромоникелевые стали, дополнительно легированные вольфрамом, молибденом, ванадием и другими элементами. Стали содержат 15…20 % хрома и 10…20 % никеля. Обладают жаропрочностью и жаростойкостью, пластичны, хорошо свариваются, но затруднена обработка резанием и давлением, охрупчиваются в интервале температур около 600oС, из-за выделения по границам различных фаз.
По структуре стали подразделяются на две группы:
1. Аустенитные стали с гомогенной структурой17Х18Н9, 09Х14Н19В2БР1,12Х18Н12Т. Содержание углерода в этих сталях минимальное. Для создания большей однородности аустенита стали подвергаются закалке с 1050…1100oС в воде, затем для стабилизации структуры – отпуску при 750oС.
2. Аустенитные стали с гетерогенной структурой 37Х12Н8Г8МФБ, 10Х11Н20Т3Р.
Термическая обработка сталей включает закалку с 1050…1100oС. После закалки старение при температуре выше эксплуатационной (600…750oС). В процессе выдержки при этих температурах в дисперсном виде выделяются карбиды, карбонитриды, вследствие чего прочность стали повышается.
Детали, работающие при температурах 700…900oC, изготавливают из сплавов на основеникеля и кобальта(например, турбины реактивных двигателей).
Никелевые сплавы преимущественно применяют в деформированном виде. Они содержат более 55 % никеля и минимальное количество углерода (0,06…0,12 %). По жаропрочным свойствам превосходят лучшие жаропрочные стали.
По структуре никелевые сплавы разделяют на гомогенные (нихромы)игетерогенные(нимоники).
Нихромы.Основой этих сплавов является никель, а основным легирующим элементом – хром (ХН60Ю, ХН78Т).
Нихромы не обладают высокой жаропрочностью, но они очень жаростойки. Их применяют для малонагруженных деталей, работающих в окислительных средах, в том числе и для нагревательных элементов.
Нимоники являются четвертными сплавами никель – хром (около 20 %) – титан (около 2%) – алюминий (около 1 %) (ХН77ТЮ, ХН70МВТЮБ, ХН55ВМТФКЮ). Используются только в термически обработанном состоянии. Термическая обработка состоит из закалки с 1050…1150oС на воздухе и отпуска – старения при 600…800oС.
Увеличение жаропрочности сложнолегированных никелевых сплавов достигается упрочнением твердого раствора введением кобальта, молибдена, вольфрама.
Основными материалами, которые могут работать при температурах выше 900oC (до 2500oС), являютсясплавы на основе тугоплавких металлов– вольфрама, молибдена, ниобия и других.
Температуры плавления основных тугоплавких металлов: вольфрам – 3400oС, тантал – 3000oС, молибден – 2640oС, ниобий – 2415oС, хром – 1900oС.
Высокая жаропрочность таких металлов обусловлена большими силами межатомных связей в кристаллической решетке и высокими температурами рекристаллизации.
Наиболее часто применяют сплавы на основе молибдена. В качестве легирующих добавок в сплавы вводят титан, цирконий, ниобий. С целью защиты от окисления проводят силицирование, на поверхности сплавов образуется слой MoSi2толщиной 0,03…0,04 мм. При температуре 1700oС силицированные детали могут работать 30 часов.
Вольфрам – наиболее тугоплавкий металл. Его используют в качестве легирующего элемента в сталях и сплавах различного назначения, в электротехнике и электронике (нити накала, нагреватели в вакуумных приборах).
В качестве легирующих элементов к вольфраму добавляют молибден, рений, тантал. Сплавы вольфрама с рением сохраняют пластичность до –196oС и имеют предел прочности 150 МПа при температуре 1800oС.
Для сплавов на основе вольфрама характерна низкая жаростойкость, пленки образующихся оксидов превышают объем металла более, чем в три раза, поэтому они растрескиваются и отслаиваются Изготавливают изделия, работающие в вакууме).
studfiles.net