Самый большой станок токарный – Самые большие металлообрабатывающие станки | ООО Роста
alexxlab | 17.12.2019 | 0 | Токарный
Самые большие металлообрабатывающие станки | ООО Роста
Самый большой в мире токарный станок – это немецкий WALDRICH SIEGEN (Вальдрих Зиген) был поставлен в 1973 году в ЮАР, город Рошервиль, на предприятие ESCOM (Комиссия по электроснабжению Южной Африки). Станок занесён в книгу рекордов Гиннеса. Вес самого большого токарного станка: 458,6 тонны, длина станины 38,4 метра, максимальный вес заготовки 330 тонн, максимальный диаметр обработки: 5 метров.
Самый большой в мире фрезерный станок – портальный 5-осевой станок с ЧПУ HSM-Modal. Этот быстродействующий обрабатывающий центр является изделием германской компании EEW Maschinenbau. Как и все остальные обрабатывающие платформы с ЧПУ, HSM-Modal, по сути, является механической рукой с инструментом, перемещающейся в трехмерном пространстве по командам, вырабатываемым специализированным программным обеспечением CAD. Однако, габаритные и функциональные размеры центра HSM-Modal выделяют его из всей массы оборудования с ЧПУ.
Рабочая область центра HSM-Modal просто огромна, ее длина по оси Х составляет 150 метров, 9 метров по оси Y и 4 метра по оси Z. Рука манипулятора может вращаться на угол 270 градусов, а инструментальная головка – на 190 градусов. Конструкция центра HSM-Modal выполнена из алюминия и углеродного пластика, благодаря чему она чрезвычайно легка. Несмотря на ее размеры, установка во время работы потребляет всего от 5 до 7 кВт энергии в час.
Центр HSM-Modal является весьма универсальным, все зависит от вида используемого инструмента. С помощью HSM-Modal можно выполнять операции фрезеровки, пилить, шлифовать, резать струей воды, песка или лучом лазера. При этом точность обработки составляет одну десятую миллиметра.
Обрабатывающий центр HSM-Modal уже используется на некоторых промышленных предприятиях. С его помощью изготавливают макеты для песчаных литейных форм, то, что ранее делалось исключительно вручную. Каждая форма делается с высокой точностью и в четыре раза быстрее, чем это делалось ранее. На других предприятиях центр HSM-Modal используется для изготовления корпусов судов, а в автомобильной промышленности его используют при изготовлении макетов автомобилей в масштабе 1:1.
Самый большой четырехвалковый листогибочный станок произведен фирмой DAVI Promau (Италия) для российского лидера в производстве морских буровых платформ и конструкций для атомных электростанций, компании “Петрозаводскмаш”. В станочном парке предприятия это самая точная, быстрая и легкая в управлении установка, задействованная в изготовлении деталей для АЭС. Ее начали использовать в вальцовке листового металла толщиной до 255 мм и шириной листа до четырех метров с минимальной длиной прямого участка обечайки. Вальцовка листа на листогибах серии выполняется за один проход без поворота и повторного позиционирования листа для предварительной подгибки. Она осуществляется в автоматическом режиме и требует предварительной операции только для ведущего края листа.
По материалам: dailytechinfo.org, riamotor.ru
www.rosta.spb.ru
Самые большие станки
WALDRICH SIEGEN
Благодаря своим размерам станок занесен в книгу рекордов Гиннеса как самый большой токарный станок в мире. Его габариты впечатляют:
- – вес 458,6 тонны,
- – длина корпуса 38,4 метра.
Способен обрабатывать заготовки весом до 330 тонн с диаметром обработки до 5 метров.
Оборудование немецкого происхождения, В 1973 году установлено на предприятии ESCOM (Комиссия по электроснабжению Южной Африки, город Рошервиль, ЮАР), на котором исправно работает уже более 30 лет.
ЧПУ HSM-Modal
Еще один гигант — портальный 5-осевой станок с ЧПУ HSM-Modal — крупнейший фрезерный станок в мире. Также немецкого происхождения, произведен компанией EEW Maschinenbau.
Как и все модели с ЧПУ, HSM-Modal — механический прототип руки с инструментом, осуществляющей движения во всех плоскостях по специальным командам, вырабатываемым программным обеспечением CAD. Но, в отличие от своих аналогов, центр HSM-Modal не имеет себе равных по габаритам и разнообразию функций.
Размеры рабочей части центра HSM-Modal:
- длина по оси Х составляет 150 метров,
- по оси Y — 9 метров,
- по оси Z — 4 метра.
угол вращения руки манипулятора — 270 градусов, а инструментальной головки — 190 градусов.
Центр HSM-Modal выполнен из углеродного пластика и алюминия, поэтому, несмотря на внушительные габариты, конструкция легка и эргономична. В час установка потребляет всего от 5 до 7 кВт энергии.
Применение
Используется не только для фрезеровки на промышленных предприятиях, но является универсальным и многофункциональным аппаратом, функция которого зависит от вида установленного инструмента. С его помощью на сегодняшний день шлифуют, пилят и разрезают заготовочные материалы лучом лазера.
При разнообразии функций сохраняется высокая точность обработки в 0,1 мм.
Благодаря ему производство литейных форм стало более точным и автоматизированным. В других отраслях промышленности HSM-Modal используют для создания корпусов судов, макетов автомобилей в натуральную величину.
Четырехвалковый листогибочный станок
Крупнейший четырехвалковый листогибочный станок сконструирован итальянской фирмой DAVI Promau, для Российской компании «Петрозаводскмаш» — лидера страны по изготовлению конструкций для атомных электростанций, морских и буровых платформ. Данная установка является самой точной, оперативной и легкой в управлении среди всей аппаратуры для производства деталей для АЭС.
Применение
Сейчас установку применяют для вальцовки листового металла толщиной до 255 мм и шириной листа до 4 м с минимальной длиной прямого участка обечайки. Особенностью является то, что вальцовку листа можно совершить в автоматическом режиме за один проход в автоматическом режиме. Предварительная настройка требуется однократно только для ведущего края листа.
ruevit-m.ru
Самые большие станки
Самые большие станки – токарный
Самый большой в мире токарный станок – это немецкий WALDRICH SIEGEN (Вальдрих Зиген) был поставлен в 1973 году в ЮАР, город Рошервиль, на предприятие ESCOM (Комиссия по электроснабжению Южной Африки). Станок занесён в книгу рекордов Гиннеса. Вес самого большого токарного станка: 458,6 тонны, длина станины 38,4 метра, максимальный вес заготовки 330 тонн, максимальный диаметр обработки: 5 метров.
Самые большие станки – фрезерный
Самый большой в мире фрезерный станок – портальный 5-осевой станок с ЧПУ – называется HSM-Modal. Он родом из Германии, произведён на предприятии EEW Maschinenbau. Большие станки HSM-Modal применяются для изготовления больших лопастей турбин (положительные и отрицательные формы). Он может изготовит лопасти турбины ветряка, которые составляют 50 м и более. Максимальное продольное перемещение (ось X) на этом станке может составлять до 151 метра. Большие станки HSM-Modal так же могут применяться для изготовления корпусов судов, литейных форм и прочих сложных изделий значительных размеров.
Большие станки HSM-Modal – оснащение
Большие станки HSM-Modal могут быть оснащены различными инструментами: для фрезерования, сверления, шлифовки, полировки; гидроабразивной, плазменной и лазерной резки.
Большие станки HSM-Modal – особенности
- Скорость подачи до 150 м/мин – значительно превышает скорость подач остальных 5-осевых станков.
- Доступны различные варианты перемещений по осям: от 3 до 151 м для оси X (продольное), от 3 до 9 м для оси Y (поперечное), и от 1,75 до 4,25 м по оси Z (вертикальное).
- Точность составляет ± 0,2 мм для осей X и Y и ± 0,17 мм/м для оси Z.
- Относительно малый вес станка требует фундамента не более 200-мм (железобетон).
- Со станком совместимы различные программы CAD и CAM.
Большие станки от “НОВАТОР”
На сегодняшний день в мире есть несколько предприятий, производящих тяжёлые токарные и фрезерные станки. ЗАО ПГ “НОВАТОР” может предложить Вам большие станки от любого производителя, наиболее хорошо подходящие для выполнения задач любой сложности. Если Вам нужны большие станки – обращайтесь к нашим специалистам!
Самые большие станки
www.novator-grp.ru
Российские станки | Журнал Популярная Механика
Во времена СССР ходила такая байка. Японцы купили советский станок, привезли к себе, все железо тут же отправили на переплавку, а из деревянной тары понаделали мебели. Якобы для бедной рудой и лесом Японии это была чрезвычайно выгодная сделка. Ну, а действительно, зачем еще японцам наши станки?
Про нынешнее станкостроение баек уже не рассказывают. Считается, что его нет. Согласно расхожему стереотипу, российская экономика чисто сырьевая, вся наша промышленность — это «отверточная сборка», и уж конечно, индустриальное оборудование исключительно импортное.
Что ж, как говорится, в каждой шутке есть доля правды, да и стереотипы редко возникают на пустом месте. Тем радостней иногда узнать, что реальность сложнее шуток и стереотипов. И гораздо оптимистичнее. Наш автобус медленно катится по асфальтовой дорожке, края которой крошатся как песочный торт. Крошатся прямо в залившие неухоженные газоны лужи мутно-бежевого цвета. Окружающий вид глаз не радует: на советских заводах и так-то не особо баловались ландшафтным дизайном, а тут еще во всем заметны следы двадцатилетнего упадка. Картина очень характерная и виденная не раз.
Славные традиции Трудно придумать лучший способ показать циклопические масштабы станов, которые производил Коломенский завод тяжелого станкостроения. Десятки человек на планшайбе!
Из «софта» в «хард»
Мы на территории Коломенского завода тяжелого станкостроения, которому в этом году исполнилось 100 лет. В Российской империи здесь начинали с конных повозок, потом, в советские времена, делали пушки и, наконец, перешли к станкам. ЗТС был настоящим гигантом советской индустрии и занимал огромную территорию, которая теперь поделена между несколькими юридическими лицами. В общем, случилось то, что обычно случалось с такого рода предприятиями в годы, когда страна увлеклась торговлей и финансами: завод обанкротился. Получилось, что российские станки оказались не нужны не только японцам. И все же столетний юбилей знаменитого завода не стал траурной датой. Потихоньку, шаг за шагом, здесь, в Коломне, а еще в Стерлитамаке, Иванове и других городах российское станкостроение рождается заново.
И вот что интересно. Люди, стоявшие у истоков новой жизни знаменитого коломенского завода, отнюдь не выходцы из тяжелой индустрии. Они пришли из самой что ни на есть «экономики знаний». Еще в 1995 году группа студентов, аспирантов и выпускников московского «Станкина» объединилась в производственный коллектив и стала выполнять заказы западных станкостроительных фирм на разработку ПО для автоматизированных систем управления. Ни о каком «тяжелом металле» не было и речи — то была эпоха, когда программисты и вообще «компьютерщики» были героями дня. Постепенно сфера деятельности и круг партнеров команды — теперь она стала называться ЗАО «Станкотех» — расширялись. Появился интерес не только к созданию ПО для станков, но и к их модернизации, переоборудованию на основе современных средств ЧПУ. Наконец, в 2011-м ЗАО «Станкотех» пришло в Коломну. Компанией было поглощено обанкротившееся предприятие ООО «СКБ-ЗТС», созданное на основе цеха прецизионных станков бывшего Коломенского завода тяжелого машиностроения. На этих площадях со славной историей «станкотеховцы» принялись создавать новое предприятие, которое теперь не только модернизирует старые станки, но и производит новые. В 2013 году ЗАО «Станкотех», управляющее производством в Коломне, объединилось со станкостроительным заводом в Стерлитамаке (НПО «Станкостроение») в группу «СТАН». В октябре этого года было объявлено о присоединении к группе еще двух станкостроительных производств в Рязани и Иванове.
Гибкость и точность На фото станок-трубогиб выполняет свою медленную, но очень тонкую работу. Под управлением компьютера он создает сложные трехмерные конфигурации из труб — такие детали используются, в частности, в топливных системах ракет. Еще одна новинка ЗАО «Станкотех», стоящая в заводском цехе, — обрабатывающий центр модели ОЦП 300, который предназначен для обработки крупногабаритных деталей (плит, рам, корпусов) из легких металлических сплавов и композитных материалов. На станке можно обрабатывать детали любой геометрической формы с пяти сторон без переустановки.
Станки, которые строятся и будут строиться сегодня в Коломне, — это совсем не рядовое оборудование. Изготовлен и работает в цехе уникальный станок-трубогиб, постепенно воплощается в металле универсальный раскатной стан УРС-3200, проектируется станок для вырезания вафельного фона. Нет, кондитерские изделия тут ни при чем, и одного лишь перечисления названий этих машин хватит сведущему человеку, чтобы понять, какой отрасли понадобились новейшие российские станки. Но сначала все-таки о японцах.
Карусели не для развлечений
Выбор, который ЗАО «Станкотех» остановило на Коломенском ЗТС (точнее, пока на его части), был совсем не случаен. Завод, несмотря на свою сложную и типичную для новейших времен судьбу, обладал, как сейчас принято говорить, компетенцией высокого уровня (и частично ее сохранил) в области создания уникального сверхтяжелого промышленного оборудования. В 1970 году специалистами ЗТС был построен карусельный универсальный станок КУ299. На его гигантской планшайбе могли размещаться детали диаметром до 20 м и весом до 560 т. Машина была отправлена на экспорт, став самым сложным крупным станком, когда-либо проданным Советским Союзом за границу. Покупателем стала… японская компания Hitachi — ничего лучше в мире для обработки сверхкрупных деталей (в основном для нужд энергетики) специалисты из Страны восходящего солнца не нашли. В Японию отправился и другой коломенский карусельный станок — КУ153Ф1. Еще более крупный станок — по некоторым данным самый большой в мире — был изготовлен коломенцами для волгодонского «Атоммаша». Деталь, обрабатываемая на станке КУ466, может иметь высоту до 5 м, диаметр заготовки — до 22 м! Сейчас эта машина работает в Китае. Карусельный станок КУ168 изготовили в 1966 году для решения уникальной задачи: на нем шлифовали шестиметровое зеркало Большого азимутального телескопа Специальной астрофизической обсерватории АН СССР, расположенной на Северном Кавказе.
Катать и резать
Новым хозяевам коломенского производства приходится нелегко — они унаследовали не только славные традиции, но и последствия упадка. В цехах вовсю идет работа, строятся и модернизируются станки, при этом на повестке дня остаются многочисленные хозяйственно-организационные проблемы. В некоторых помещениях пришлось чинить кровлю. Решается вопрос об автономном отоплении и водоснабжении для каждого цеха. Ведутся переговоры о возвращении производству тех заводских помещений, которые сегодня занимают другие фирмы. В одном из таких «чужих» цехов стоит печь для отжига огромных деталей (в печи поверхность металла подвергается «искусственному старению» для последующей мехобработки). Длина печи 30 м, ширина и высота — по 5 м. Когда-нибудь дойдут руки до обустройства территории, но главное — производству дан старт.
Когда станок работает — это всегда заметно. Крутятся валы, жужжат фрезы, перемещаются суппорта. Но станок-трубогиб — исключение. Его работа медленная и незаметная, как движение часовой стрелки. Видно лишь, как в месте входа трубы в станок она раскаляется докрасна. Казалось бы, в чем тут техническая сложность? Все просто, если из трубы нужно сделать примитивное «колено». Но если эта труба является, скажем, частью топливной системы ракеты, то ее придется изогнуть в весьма сложную конфигурацию, чтобы она точно вписалась в габариты агрегата. Для того чтобы получить трубу, образующую заданную трехмерную фигуру, нужен станок с ЧПУ. Только компьютер способен управлять этим медленным процессом с прецизионной точностью.
Флагманский проект Стан УРС-3200 предназначен для изготовления особо точных осесимметричных деталей (конусы, цилиндры, оболочки двойной кривизны) методом комбинированной наружной и внутренней раскатки. Технология внутренней и наружной раскатки применяется для получения труб и оболочек специального назначения. Основное ее преимущество — высокая точность геометрических размеров получаемых изделий и упрочнение материала в процессе раскатки. Компоновка стана — вертикальная с трехроликовой клетью и неподвижной в осевом направлении оправкой для наружной раскатки, с трехроликовой клетью и стационарной матрицей для внутренней раскатки. На стане может быть реализован процесс как наружной, так и внутренней раскатки. Переход от одного процесса к другому достигается за счет перенастройки стана и установки соответствующего инструмента.
Другое детище ЗАО «Станкотех» — универсальный раскатной стан УРС-3200, который предназначен для изготовления особо точных осецентричных деталей — конусов, цилиндров, оболочек двойной кривизны — методом комбинированной наружной и внутренней раскатки. 3200 — это максимальный диаметр в миллиметрах той самой цилиндрической или конусообразной детали, которую можно создать на станке, и это очень внушительная цифра. При этом в высоту деталь может достигать 1 м. Стан еще не построен, но его крупногабаритные детали уже складируются в цеху. ЗАО «Станкотех» делает на этот станок особые ставки, ибо его параметры не имеют аналогов в мире. Машина работает с прецизионной точностью и будет создавать детали, в которых нет швов. Раскатка (в отличие от сварки из листа) позволяет за счет уплотнения металла делать стенки изделий на 20% тоньше, чем при традиционных технологиях, и при этом они смогут выдержать гораздо большие нагрузки. Такое оборудование найдет свое применение прежде всего в аэрокосмической промышленности, например при строительстве ракетных двигателей и командных, то есть наиболее критичных с точки зрения конструкции, частей ракет. Ранее отечественная промышленность выпускала подобные машины, но там применялась только внешняя раскатка, к тому же максимальный диаметр детали достигал лишь 2,5 м. Иными словами, новое оборудование поднимет отечественное ракетостроение на более высокий технологический уровень.
И наконец, о вафельном фоне, который, как уже было сказано, не имеет никакого отношения к кондитерской промышленности. У Коломенского ЗТС опыт строительства станков для создания вафельного фона был, а сегодня новые машины с этой функцией уже проектируются в КБ ЗАО «Станкотех». Вафельный фон создается на деталях с криволинейной поверхностью для облегчения изделия при сохранении его прочности. С помощью фрезерной головки станок выбирает часть металла, оставляя на поверхности квадратные углубления (ячейки), разделенные стенками. Здесь требуется высокая точность, так как глубина ячеек и толщина стенок должны иметь строго заданные размеры. Кроме того, в процессе обработки изделие не должно подвергаться деформации. Для решения последней задачи в новой конструкции обработка будет вестись фрезерными головками сразу с двух сторон, то есть усилие одной головки будет компенсировано усилием другой. Одновременная обработка детали будет вестись по 32 осям. Заказчиком станка выступает Роскосмос.
Разумеется, мы перечислили лишь несколько флагманских проектов обновленного коломенского производства, но уже по ним понятно, что одним из моторов возрождения отечественного станкостроения стало появление серьезных заказчиков, в частности в ракетно-космической отрасли. Объединение разрозненных фрагментов бывшей советской промышленности в вертикально интегрированные корпорации (при всей спорности отдельных моментов этого процесса) вызвало все возрастающий спрос на переоснащение предприятий новым промышленным оборудованием. Рядом с только что построенными станками окажутся и модернизированные машины. Тяжелый станок — как корабль, его основные детали могут сохранять работоспособность десятилетиями, а отдельные механизмы и, разумеется, систему управления можно заменить на более современные.
Статья «Тяжелый металл возвращается» опубликована в журнале «Популярная механика» (№12, Декабрь 2014).www.popmech.ru
Токарный станок для гаража: виды, параметры, выбор
Для ремонта машины постоянно требуются металлические детали. Хорошо, если модель распространенная — можно купить. Если же авто редкое, приходится либо долго ждать пока доставят, либо заказывать изготовление. В таком случае можно приобрести токарный станок для гаража. При наличии опыта его можно использовать для подработки.
Какие виды токарных станков подходят для частного использования
Содержание статьи
Всего токарных станков девять видов, но далеко не все нужны в гараже. Чаще всего у частников можно увидеть небольшие токарно-винторезные станки. Наряду с обработкой деталей (шлифовка, сверление, фрезеровка, сверление радиальных отверстий и др.) они выполняют нарезание резьбы разного типа и точение конуса. Именно такой токарный станок для гаража стараются купить — он покрывает почти все потребности автовладельцев.
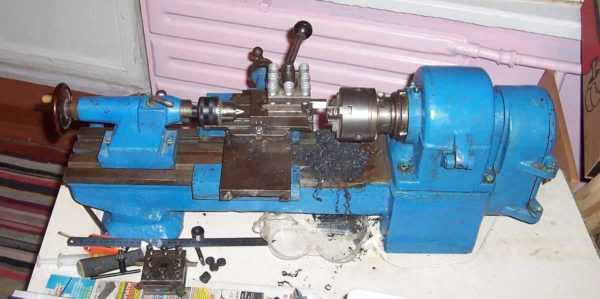
Токарный станок для гаража должен быть не слишком большой
Выпускаются в двух видах — настольные и со станиной (напольные). Настольные — небольшие, с малым весом (до 200 кг) станки. Для них в гараже проще найти место. Недостаток — большие и тяжелые детали на них не обработаешь. Еще один момент: из-за небольшой массы они не всегда в состоянии выдать высокую точность обработки.
Напольные токарные станки (обычно школьные) имеют значительно большую массу и габариты. Для нормальной эксплуатации под них надо делать отдельный фундамент. Возможна установка на виброгасителях, но их найти совсем непросто.
Устройство токарного станка
Для того чтобы выбрать токарный станок желательно знать его устройство, назначение, функции и возможные параметры каждой из частей. Для начала разберем основные узлы.
- Основание или станина. Желательно — тяжелая, литая чугунная плита. Даже у настольных моделей. Очень легкие станки будут нестабильны, из-за чего даже приемлемо точности сложно будет добиться.
- Двигатель и коробка передач. Двигатель может быть с питанием от 220 В или от 380 В. Коробка передач — устройство для обеспечения вращения шпинделя и суппорта (на автоматических и полуавтоматических станках). Станок прослужит дольше, если шестеренки передачи сделаны из металла (бывают пластмассовые).
- Передняя бабка. Основная функция — надежная фиксация и вращение обрабатываемой детали. Обычно это массивный цилиндр из металла, жестко закрепленный в корпусе. Иногда в передняя бабка и коробка передач совмещены, в некоторых моделях передняя бабка может передвигать суппорт или обрабатывающую головку.
Устройство токарного станка по металлу
- Задняя бабка. Эта часть также необходима для надежной фиксации деталей относительно шпинделя. При обработке небольших деталей используется редко, чаще — с длинными или массивными. В некоторых моделях на задней бабке может крепиться дополнительное оборудование — резец, сверло и т.п. — для возможности обработки с двух сторон без изменения положения детали.
- Суппорт. Это целый узел, от устройство которого зависит перечень выполняемых станком операций. Суппорт удерживает режущий инструмент, сдвигая его при обработке детали сразу в нескольких плоскостях (простейшие — только в одной плоскости). Управляться может автоматически или вручную.
Это основные узлы токарного станка. Есть смысл подробнее рассмотреть сложные узлы, так как от их исполнения зависят возможности и работа оборудования.
Станина
Чаще всего это две параллельные массивные металлические балки/стенки, соединенные поперечинами для придания большей жесткости. По станине перемещается суппорт и задняя бабка. Для этого на станине проточены направляющие салазки. Задняя бабка перемещается по плоским направляющим, суппорт — по призматическим. Очень редко встречаются призматические направляющие для задней бабки.
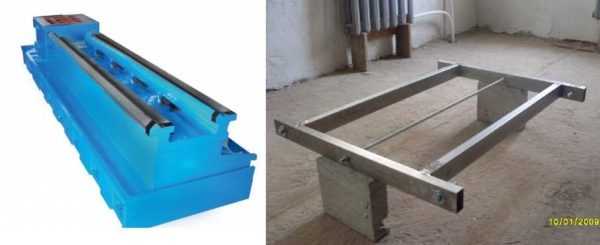
Станина для токарного станка по металлу — заводская и самодельная
При выборе б/у станка обращайте внимание на состояние салазок и на плавность перемещения частей по ним.
Передняя (шпиндельная) бабка
Передняя бабка в современных токарных станках,чаще всего, объединяет в себе держатель детали и устройство изменения скорости вращения шпинделя. Есть несколько типов управления скоростью вращения — при помощи перевода рычагов в определенное положение, при помощи регулятора.
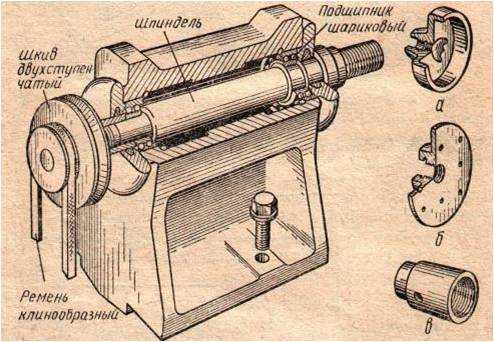
Устройство передней бабки
Управление регулятором с плавным изменением скорости вращения осуществляется на базе управления микропроцессором. В этом случае на корпусе бабки имеется жидкокристаллический дисплей на котором отображается текущая скорость.
Основная деталь передней бабки — шпиндель, который с одной стороны соединяется со шкивом электропривода, с другой имеет резьбу, на которую накручиваются патроны, удерживающие обрабатываемую деталь. Точность выполнения токарных работ напрямую зависит от состояния шпинделя. В этом узле не должно быть биений и люфтов.
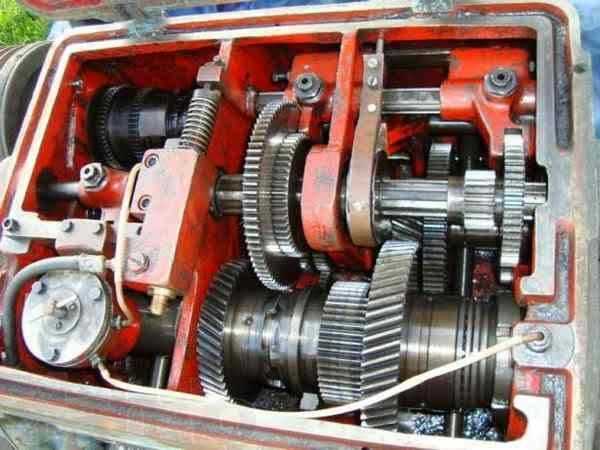
Гитара шестерен — для передачи вращения и изменения его скорости
В передней бабке находится система сменных шестерен для передачи и изменения вращения на вал коробки передач. Когда будете выбирать токарный станок для гаража, обращайте внимание на состояние шестерен и отсутствие люфта шпинделя. От этого зависит точность обработки заготовок.
Задняя бабка
Задняя бабка подвижна — передвигается по направляющим на станине. Подводится к детали, подстраивается ее положение, пинолью упирается в деталь, удерживая ее в нужном положении, положение пиноли фиксируется поворотом соответствующей рукоятки. После чего закрепляется положение задней бабки еще одной рукояткой фиксации.
В некоторых моделях задняя бабка предназначена не только для поддержки массивных или длинных деталей в заданном направлении, но и для их обработки.
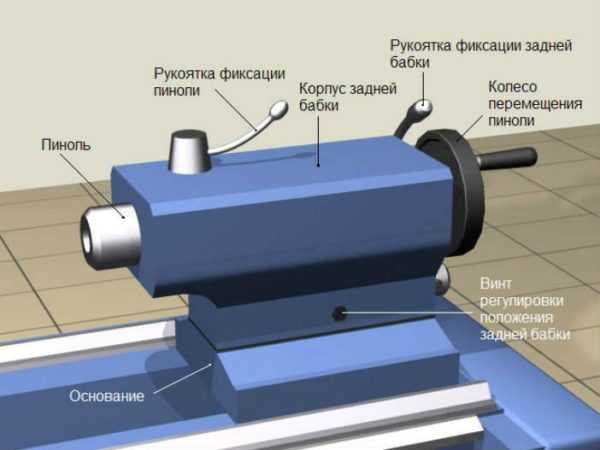
Устройство задней бабки токарного станка
Для этого на пиноли, в зависимости от выполняемых операций, закрепляется соответствующая оснастка — резцы, метчики, сверла. Дополнительный центр станка на задней бабке может быть неподвижным или вращающимся. Вращающийся задний центр делают на высокоскоростных станках, для снятия крупной стружки, вытачивания конусов.
Суппорт
Суппорт токарного станка — подвижная часть, на которой крепятся инструменты для обработки деталей. Благодаря специальной конструкции этого узла передвигаться резец может в трех плоскостях. Перемещение по горизонтали обеспечивается направляющими на станине, продольными и поперечными салазками.
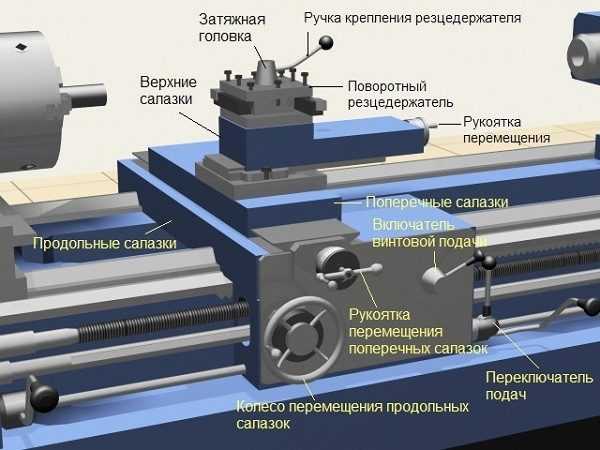
Устройство суппорта
Положение резца относительно поверхности станка (и детали) задается поворотным резцедержателем. В каждой из плоскостей имеется фиксатор, обеспечивающий удержание в заданном положении.
Держатель резца может быть одно или многоместным. Резцедержатель, чаще всего, выполнен в виде цилиндра с боковой прорезью, в которую вставляется резец, фиксирующийся болтами. На несложных станках на суппорте имеется специальный паз, в который вставляется выемка на нижней части держателя. Так происходит фиксация режущего инструмента на станке.
Токарный станок для гаража: параметры
В первую очередь определяетесь с массой и типом подключения. Выбирая массу, не стоит стремиться найти самый легкий станок. Очень легкие не дают устойчивости, могут вибрировать при работе, что скажется на точности работы. Да, тяжелые станки устанавливать проблематично, но установка — это единичное мероприятие, в работать придется регулярно. Потому вес — далеко не самый основной критерий выбора.
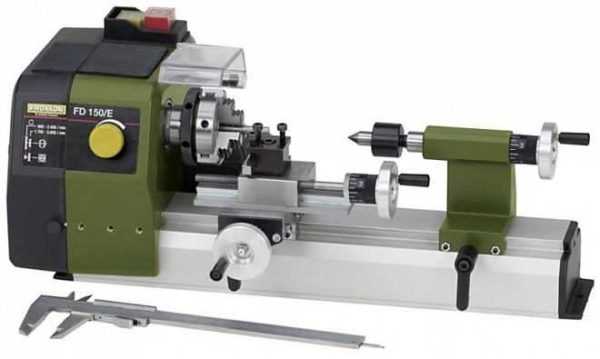
Слишком большие токарные станки не в каждый гараж можно установить, а небольшие и средние — отличный выбор
Тип подключения — однофазный или трехфазный — это уже важнее. И то, трехфазные можно подключить к 220 через специальные пускатели. Из электрических характеристик важна еще мощность двигателя. Чем она выше тем большую скорость вращения может развить токарный станок. Это общие моменты. Есть еще специальные:
- Диаметр заготовки, которую можно на станке обрабатывать. Определяется диаметром обработки над станиной и над суппортом.
- Длинна обрабатываемой детали. Зависит от хода.
- Перечень операций.
- Максимальное число оборотов.
- Способ регулировки — плавный, ступенчатый.
- Возможность обратного хода.
Размеры обрабатываемых деталей напрямую связаны с размерами станка. Так что тут приходится искать разумный компромисс. Обычно не хочется слишком загромождать гараж, но надо обрабатывать габаритные детали.
Микро и мини токарные станки
Чтобы не загромождать гараж можно найти мини- или микро токарные станки. Они отличаются совсем уж небольшими размерами и малой массой. Например, микро-токарный станок для гаража PROMA SM-250Е имеет размеры 540*300*270 мм и массу 35 кг. Обрабатывать может заготовки длиной 210 мм и диаметром 140 мм. Плавная регулировка скоростей от 100 до 2000 об/мин. Для таких размеров не так уж и плохо.
Токарные мини станки — в гараже им самое место
Несмотря на маленькие размеры, может производить следующие операции:
- обтачивание поверхностей,
- нарезание резьбы;
- сверление;
- зенкование;
- развертывание.
Возможны также шлифовка деталей, накатка, заточка инструмента. Основные операции, как видите, присутствуют. Недостаток в том, что на станках такого типа хоть сколько нибудь крупные детали не обработаешь.И еще недостаток конкретно этой модели цена. Стоит этот токарный станок для гаража от 900$.
В той же категории есть китайские JET BD-3 и JET BD-6 (цена 500-600$) и отечественные КРАТОН MML-01 (цена 900$), Энкор Корвет 401 (650$), немецкие Optimum — от 1300$ до 6000$; чешские Proma — от 900$,
Напольные варианты
Тут выбор не так широк, потому что и цены и масса намного выше. Есть несколько проверенных моделей, которые можно установить в гараже.
Напольный токарный станок для гаража ТВ 4
Это так называемые школьные станки — ТВ 4 (его усовершенствованную версию ТВ 6), ТВ 7 и настольное исполнение ТВ 16. При массе 280 кг (ТВ 4) и 400 кг ТВ 7, желательно наличие отдельного фундамента. Если поставить его просто на бетонный пол, он его разобьет.
stroychik.ru
HSM-Modal – самый большой станок в мире
≡ 18 Июль 2012 · Рубрика: ТехникаА А А
Сегодня автоматизация и замена человека машинами приобретает все большую распространенность. В скором будущем на крупных производствах человека могут полностью заменить машины. Такие машины как HSM-Modal — самый большой станок в мире.
Огромная техника была разработана немецкой компанией EEW Maschinenbau. Основным инструментом станка является механическая рука, которая двигается в трехмерном пространстве. Однако в отличии от других подобных аппаратов, HSM-Modal отличается своими впечатляющими размерами. Так к примеру длина действия «руки» составляет 150 метров (ось Х), 4 метра по оси Z, и 9 метров по оси Y. При этом резак может вращаться под углом 190 градусов, а сама «рука» под углом 270 градусов. Потребляемая энергия самого большого станка в мире составляется примерно 6 кВт в час.
Характеристики машины позволяют использовать различные способы обработки материала, к примеру помимо стандартных вариантов резки, также можно использовать луч лазера, струю песка или воды.
Самый большой станок в мире имеет различные сферы применения: при изготовлении корпусов кораблей и яхт, в автомобильной промышленности при изготовлении макетов машин, при производстве литейных форм и так далее. Причем скорость выполнения работ в 4 раза быстрее, чем при ручном изготовлении.
Похожие записи:
hontos.ru