Токарный чпу станок своими руками: Модернизация токарного станка под работу с ЧПУ / Хабр
alexxlab | 23.05.2023 | 0 | Токарный
Токарный станок и токарный патрон из пластика с ЧПУ……… Почти настоящий.
RepRap
Подпишитесь на автора
Подписаться
Не хочу
73
После удачного результата с ЧПУ фрезером , напечатанном на 3D принтере решил попробовать сделать настольный токарный станочек. А то самый маленький токарный станок с суппортом стоит каких то “конских” денег, а имеет кучу негативных отзывов.
Если делать правильно и не экономить на пластике – то все работает нормально.
Всё началось с печати токарного патрона 2,5 дюйма (63 мм) по готовой модели с Твинги.
Там есть две модели
Я напечатал и патрон не держит заготовку – в стальном патроне
есть такая деталь
И она работает нормально, когда выполнена из стали, а из пластика ей жесткости не хватает.
Я напечатал такое кольцо на винтах
И патрон стал нормально зажимать. Переделал модель под ось 8мм – на этот диаметр есть шкивы под кольцевой ремень GT2. Эти детали у меня были в наличии.
Ну вот это ………наверное..
И смотрим – по этим станкам -игрушкам…. Народ меняет чаще всего патроны и двигатель….
Значит надо двигатель по мощнее…. в ближайшем магазине для самодельщиков была одна модель с валом 5 мм – остальные с валами 3,175 мм …. а шкиф у меня только на 5мм, а переходную втулку сделать дороже, чем купить двигатель с валом 5 мм.
Приобрёл такой двигатель с валом 5 мм.
В итоге
Получилась такая вот передняя бабка
Суппорт – ставим проверенный вариант от фрезера……. и
А из чего сделать резцы – Сверла для керамической плитки имеют накладки из твердого сплава – стоят по сравнению с резцами мало и по размерам подходят для очень маленького станка.
И первая стружка.
Итак… по размерам получилось следующее
Рабочий ход по осям
По Х – ход суппорта 100 мм, а ход резца в текущем варианте (патрон есть возможность проточить) – от кулачков патрона до ограничения хода – 60 мм….. но если переставить резце держатель на другое крепление то можно и все 100 мм выбрать но нужно заднюю бабку делать.
По У – ход каретки 90 мм – то есть ход больше, чем расстояние от центра до осей – ограничение только по диаметру зажима. Для чего такой большой ход сделан – чтобы можно было установить фрезерный электро шпиндель – у меня как раз две штуки разных есть – можно сделать делительную головку или вместо ходового двигателя постоянного тока установить шаговик- конструктивно возможность предусмотрена.
Пластик он обрабатывает…. А что если попробовать проточить гвоздь – сотку?
И точит ведь – крайне медленно , с очень маленьким съёмом, но точит.
Правда , напильником вышло бы быстрее…. но так ровно напильником не сделать…Но напильником можно и на станке – на зажатой заготовке в патроне…..
ЧПУ -управление перепрошил автономный блок от фрезера…. Но вот только осталось освоить программу для подготовки управляющих кодов…..
Блок – Ардуино НАНО 3,0+ шилд “Control by GRBL 111330″+MKS TFT2.4 с прошивкой для CNC (для 3-х координатных ЧПУ)+ силовой ключ….
Вот такой маленький токарник получился…..Всем здоровья и удачи.
Токарка без токарного
Здравствуйте, товарищи!
Мечтаю о токарном станке, но его, к сожалению, в ближайшее время у меня не предвидится. А пока я мечтаю, придется выполнить токарные работы без него и на самодельном фрезере с ЧПУ.
Под катом будет много фоток, небольшая покупка на AliExpress’е, немного вредной/полезной информации и, конечно же, DIY…
Да, я на самом деле давно хочу приобрести настольный токарный станок, но, если честно, то не так уж он прям и нужен в повседневной деятельности
(«Ну да, ну да…» — сказало шило в одном месте).
Сейчас на YouTube’е так много каналов, где классно точат всякие клёвые «пиптики», что ты сидишь на своём диване, завидуешь белой/черной завистью и хочешь точить также, и даже круче! Но дальше хотелок дело обычно не доходит…
Все силы были брошены на поиски решения, с учетом того, что в моем распоряжении уже имеется самодельный фрезерный станок с ЧПУ, хоть и игрушечный, но всё же не пластилиновый.
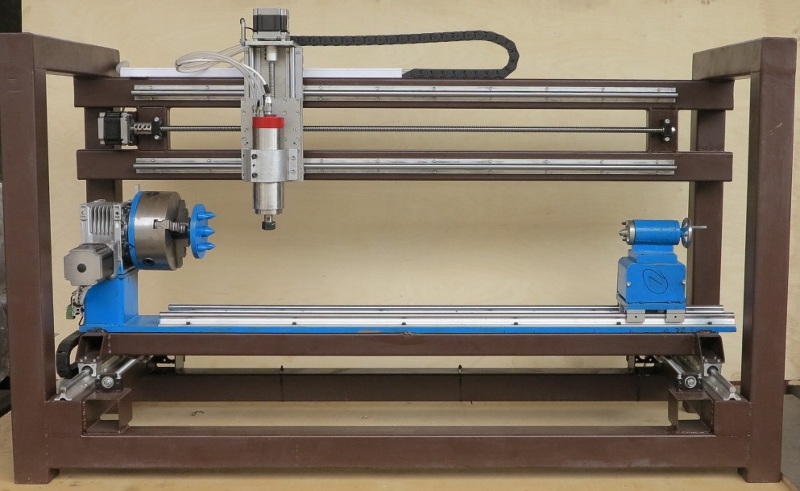
Вот такой (правда жертвенный стол из МДФ на фото временно снят).
Изначально я подумал про самое очевидное решение — прикрепить вместо шпинделя токарный резец, а на рабочий стол приделать какой-нибудь двигатель, к которому можно было бы прикрутить патрон и вращать, вращать в нем что попало, ну чем не токарный станок с ЧПУ?
Но нет, идея не пришлась мне по вкусу, тем более шахматные фигурки не требуют большого патрона. Внезапно, я подумал, что у меня есть заготовки — прутки из латуни диаметром 6 мм, а у шпинделя цанги тоже под 6 мм. Совпадение? 🙂
Я думаю, что в очередной раз столкнулся с изобретением велосипеда, но сознательно решил не спрашивать про такое решение у Google’а, чтобы не вносить погрешностей в стройный ход моих мыслей.
Для неискушенных читателей, которые еще не до конца поняли, что я задумал, внесу ясность. В качестве передней бабки токарного станка в моем случае будет выступать подвижный шпиндель, который имеет ход во всех направлениях. А вот токарный резец (или резцы) будет неподвижным, зафиксированным на рабочем столе. Соответственно, переворачиваем всё с ног на голову и заставляем перемещаться вращающуюся заготовку относительно неподвижного резца.
А дальше снова проблема – у меня нет токарных резцов. Хотел попробовать заточить старые обломанные фрезы, но, как и их, меня тоже обломало, ведь на AliExpress’е я видел резцы со сменными твердосплавными пластинами – идеальный вариант для тех, кто не настоящий токарь и не умеет правильно затачивать резцы.
Заказал я два резца (державки+пластинки) – проходной и отрезной (прошу поправить меня, если ошибаюсь с терминологией), а также наборы сменных пластин к ним.
Ссылка на магазин для тех, кому нужно
Проходной резец — ссылка обычная, не хитровыдуманная ))
По закону жанра я должен был их обмерить и обвешать, но речь немного не о том, поэтому просто приведу маркировки и параметры, а в конце компенсирую котиками
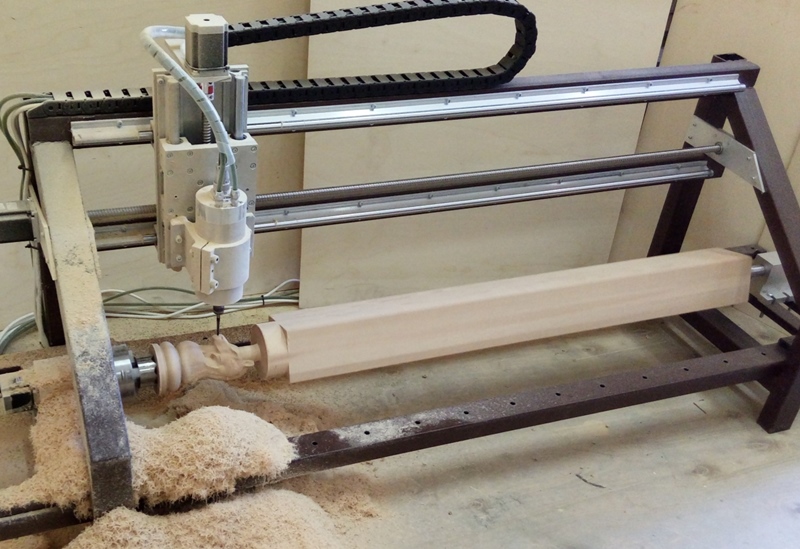
Отрезной резец.
Державка – MGEHR1010-1.5, сечение квадрата 10×10 мм, рассчитана под резцы шириной 1.5 мм.
Пластина – MGMN150-G PC9030, ширина режущей части 1.5 мм.
Да, не сказал, в комплекте к каждой державке идет шестигранный ключ.
Проходной резец.
Державка – SVVBN1010h21, сечение квадрата так же 10×10 мм.
Пластина – VCGT110302-AK, угол 35 градусов, радиус скругленного кончика 0.2 мм, 11 мм длина рабочей режущей части.
Я сразу забегу немного вперед и скажу, что отрезной резец применить мне не удалось, всё-таки нужно больше жесткости станка, а иначе это не точение, а какое то дробление с выбиванием :). Поэтому далее я упоминать его не буду и оставлю до лучших времен.
А в связи с этим еще одна проблема – как отрезать фигурки без отрезного резца… Сначала я думал, что буду переставлять державку проходного резца под углом (17.5 градусов), так чтобы одна грань пластины была параллельно рабочему столу, ну тут думаю понятно.
В качестве материала дополнительных державок я выбрал благородный «дюралюминь». Ну уж, простите, другие металлы грызть на своем фрезере я не могу, ну разве что еще латунь.
Кто-то скажет: «Да жесткости не хватит!», «Да это не дело!». А я соглашусь, да, жесткости не хватит, да, это не дело… для серьезной работы и серьезных нагрузок. Я же планирую за проход снимать не более 0.2 мм при черновой обработке, и не более 0.1 мм при чистовой. Кроме того, постараюсь сделать минимальный вылет державок из резцедержки, которая, к слову, скоро тоже появится в этом повествовании.
Итак, для самодельных державок я нашел квадрат 12×12 мм из дюрали. Особо процесс пояснять смысла нет. Думаю, из картинок всё будет понятно – станок работал, а я только его в розетку включил, да кнопку нажал.
Для обеспечения перпендикулярности сначала я сделал для заготовки посадку в зажатом в тисках кусочке МДФ, а затем уже выполнил все остальные операции по фрезеровке.
Вот, что получилось. Выглядит нормально, почти как державка нормального человека — в деле проверим.
Как я уже говорил, переустановка резцов после выполнения каждого этапа не планируется, учитывая, что изготовление это хоть и мелкая, но всё же серия (32 фигурки) и время тратить не целесообразно. Поэтому я решил зафиксировать на столе три резца сразу. Завершается выполнение одного этапа, переключаемся в новую систему координат, переезжаем к другому резцу и выполняем следующий. План неплохой, попробую воплотить в жизнь.
Для резцедержки на три резца я снова воспользовался дюралевой заготовкой (остался кусочек толщиной 16 мм от боковин портала станка). Я понимаю, что мог просто закрепить резцы на рабочем столе на саморезы, но захотелось установить их относительно точно и с комфортом.
Вот как выглядит эта приспособа. Наделал кучу отверстий с резьбой, чтоб можно было фиксировать резцы винтами, а также сквозных отверстий, для прикрепления этой резцедержки к столу.
Первый резец – основной, почти для всех операций, второй – для изготовления ладьи, у которой плоская макушка, а третий — исключительно для отрезания фигурок. На рисунке постарался изобразить конфигурации установки резцов, для каждой операции, как я (НЕ ТОКАРЬ) себе это представляю.
С этим всё понятно, едем дальше.
А дальше я, наверное, спрячу информацию под спойлер, не всем интересно будет читать про системы координат ЧПУ станка и их переключения. Про это можно было вообще не писать, но я рассматриваю это как памятку для себя же.
Здесь я оговорюсь, выхожу на минное поле – я хоббийщик-любитель и теория управления станками с ЧПУ это далеко не мой конёк, поэтому всё, что я напишу дальше может быть спорным и прошу не забрасывать меня тапками.
Про системы координат
Каждую операцию я планирую выполнять в своей системе координат. Почему так? Просто потому, что расчет всех управляющей программ (под каждую операции) я планирую сделать в одной системе, чтобы на этапе расчетов не задумываться о том, как и где у меня будут установлены резцы. А когда все программы будут готовы, в начале каждой я допишу команду перехода в нужную систему. В моем случае это команды G54(базовая система), G55 и G56.
На картинке показано, что да как я собираюсь сделать.
Но перед началом работы, мне придется задать точки на рабочем поле, чтобы определить нулевые точки для каждой системы, а если сказать более правильно – указать смещения относительно машинных координат (механических) станка – G53.
Если я правильно воспринял информацию из описания G-кодов, то нужные смещения для каждой системы координат выполняются следующей командой
G10 L2 Pppp Xxxx Yyyy Zzzz, где
ppp – порядковый номер системы координат (1 — G54, 2 – G55, 3 – G56, …)
xxx, yyy, zzz – смещения относительно машинных координат G53.
Ну и как пример, если нулевая точка для выполнения 2-й операции (в системе G55) отстоит от нулевой точки машинных координат на X100 Y50, то перед началом работ нужно выполнить следующий код
G10 L2 P2 X100 Y50 Z0
а затем переключиться в эту систему, вызвав код G55
Кстати, наблюдение — в LinuxCNC после выполнения управляющей программы в системе отличной от базовой (например, в G56), по окончании происходит автоматическое переключение в базовую (G54). Таким образом, целесообразно указывать переход в ту или иную систему принудительно в начале файла с управляющей программой, а иначе возможны неприятные казусы, если после завершения вы захотите повторить выполнение управляющей программы
Перед тем как приступить к настройке станка, мне необходимо выполнить расчет управляющих программ для каждой фигурки.
И вот тут я принял решение не пользоваться специализированным ПО для расчета УП для токарной обработки, хотя прекрасно понимаю, что, например, в том же Fusion360 это сделать не долго и не сложно.
Расчет траектории обработки я выполню почти ручным способом. Для чего это мне нужно?
Во-первых, спортивный интерес, во-вторых, лучшее понимание процесса. Кроме того, не все и не всегда хотят или имеют время разбираться с новым разнообразным ПО при решении одноразовых задач. При этом, сделаю уточнение – я за прогресс и за развитие, поэтому, когда это возможно, то нужно пользоваться готовыми решениями, это значительно сэкономит вам время.
А в данном посте просто предлагаю один из миллиона способов решения задачи здесь и сейчас.
Профили фигур я нарисовал в MS Visio (кроме коня, конь это отдельная история) и выглядят они вот так:
Я художник – я так вижу 🙂
А дальше начинается всё веселье. Для разработки УП я воспользуюсь программой Vectric Aspire (можно это также осуществить во всеми любимом ArtCam’е).
На примере пешки я покажу основные этапы ручной подготовки УП для станка.
Но перед этим схематично покажу, как выглядит резец, это важный момент и пригодится при расчетах.
Нас интересует скругленное острие, с радиусом скругления 0.2 мм. Просто запомним.
Дальше все действия я выполняю в Vectric Aspire:
1. Беру эскиз пешки, отсекаю от него лишюю половинку и располагаю относительно 0, как мне удобно.
2. После этого, учитывая радиус скругления резца 0.2 мм, создаю векторный контур, который отстоит от контура фигуры как раз на 0.2 мм. Этот контур будет использоваться как траектория для чистового прохода резца.
3. После этого делаю «ход конем» — чистовой проход я планирую сделать со съемом 0.1 мм, поэтому необходимо создать еще один контур со смещением относительно чистового контура на 0.1 мм. Этот контур будет ограничивать черновые проходы, оставляя на чистовой проход 0.1 мм материала.
4. Далее сделаю вспомогательные линии с интервалом 0.2 мм друг относительно друга, эти линии будут использовать для съема лишнего материала (я не поясняю, как отсекаю лишни линии, это не тема данного поста)
5. Теперь можно сделать траекторию для чернового съёма лишнего материала. Для этого, убирая лишние линии, получим некую змейку. Для этой змейки применим стратегию «2D Profile» с параметром «On» (то есть по контуру). Думаю по рисунку всё понятно.
6. Для неохваченных остатков используем ту же тактику. Это всё еще черновые проходы.
7. Теперь остается только чистовой проход, этот тот контур, который отстоит от очертания пешки на 0.2 мм, а материала для съема осталось только 0.1 мм. Стратегия всё та же «2D Profile».
8. Для того, чтобы отрезать фигуру будет использована вот такая траектория
Можно заметить, что резец не полностью отрезает фигуру и остается небольшой хвостик.
Я сознательно не вдаюсь в мелочи и нюансы, мне кажется, если кто-то захочет повторить процесс – направление понятно, дальше только ваш опыт работы с программами для создания УП и чуть-чуть фантазии.
Единственное, на что хотелось бы обратить внимание так это на оси. Как вы понимаете, моделирование и создание управляющих программ осуществляется в плоскости XY, но как мы помним, заготовка относительно резцов будет перемещаться в станочной плоскости XZ.
Чтоб правильно запустить процесс выполнения программы есть два варианта:
1. Поправить G-коды заменой координат, Z на Y, Y на Z. Но этот фокус пройдет только в случае, если вы не применяете круговую интерполяцию. В этом случае придется делать замены параметров арок I, J, K, но мне показалось, что это долго и бесперспективно.
2. Перенастроить станок, таким образом, чтобы при выполнении управляющей программы перемещение по Z реально происходило по оси Y, а Y по Z.
Я выбрал второй способ. Для управления станком я использую LinuxCNC и могу создавать разные конфигурации станка, запуская нужную (на рабочем столе создаются ярлыки под запуск каждой конфигурации).
Покажу на примере основную конфигурацию для фрезеровки и дополнительную для токарных работ.
А теперь, если вы еще со мной, переходим к практической более интересной части моего опуса.
Первым делом с помощью поверочного угольника выставлю резцы так, чтоб вылет был одинаковый – это избавит от проблем в будущем.
А дальше возьму небольшой брусочек из МДФ и вырежу на нем посадочное место под резцедержку.
Такая, казалось бы лишняя процедура, необходима, чтобы установить резцедержку длинной стороной вдоль оси Y (а учитывая, что координаты я переназначил, то вдоль оси Z) и соблюсти перпендикулярнось резцов к оси Х.
Можно сказать, что все приготовления закончены, осталось лишь задать системы координат – скажу честно это самая неприятная часть работы и я потратил некоторое время, чтобы определить, какие смещения необходимо указать для каждого резца.
На бумажке я неправильно записал смещение по оси Х, на самом деле оно отрицательное.
Я думаю, по одинаковости смещений по Х, понятно, для чего я выставлял вылеты резцов — это действительно избавило от проблем.
И перед тем как запустить токарный процесс, выполню команды, задающие нулевые точки для систем координат G55 и G56.
Ну всё! Погнали! Начну с пехоты 🙂
Черновую обработку и чистовой проход делается на первом резце. Обороты шпинделя выставил 2000.
После того, как основа пешки готова, отправляем ее на третий резец для обрезки и снова точим.
Вот собственно процесс и завершен. Скажу честно – ощущения от процесса непередаваемые и визуально это выглядит очень залипательно.
На всякий случай уточню — диаметр основания фигур 5 мм
Чтобы вы тоже ощутили процесс, приложу видео — чисто токарная процедура, без подготовки и прочей мишуры, которую вы и так прочитали в тексте.
Изготовление пешки
И еще на закуску – изготовление ферзя из прутка Д16Т(дюрали)
youtube.com/embed/zu6mc5Ku-0U?autoplay=0&hl=ru_RU&rel=0″ frameborder=”0″ allowfullscreen=””>
Я конечно уже и так порядком затянул публикацию, но думаю многих интересует, как я делал коня (по крайней мере три человека в офф-лайне уже об этом спросили)
С конями я решил поступил так — сделалтокарным способом вот такие заготовки
А затем закрепил эти заготовки и отфрезеровать, вот так
Как по мне, это больше единороги какие то получились ))), но в целом нормально, учитывая размеры фигур.
Про весь проект я не рассказываю, если интересно, то полное видео можно посмотреть у меня на YouTube
Полное видео
А теперь мы с Линуксом сыграем партеечку 🙂
Всем спасибо за внимание!
Домашняя страница – HobbyCNC
HobbyCNC 3 и 4 комплекты платы драйвера шагового двигателя оси.
Компактный, мощный, простой в сборке.
Для фрезерного, фрезерного, токарного станка или робота с ЧПУ своими руками!
Только высококачественные компоненты от основных производителей
Минимальный счет деталей и собирайте его сами
Легко следить до 3 А каждый
С 1999 года HobbyCNC продает различные высококачественные изделия с ЧПУ для хобби: комплекты контроллеров шаговых двигателей, чертежи фрезерных станков с ЧПУ и шаговые двигатели для настольных машинистов и любителей.
Наборы драйверов шаговых двигателей HobbyCNC
PRO 3 Axis Kit
Обновление$ 79
- 3 Axis
- Обновление до 4 TH AXIS
- 42 DCV MAX
- 6,8 ″ x 3,7 ″ (173 x 94mm)
- .0036
- Максимум 3,0 А на фазу
- 5-, 6- или 8-проводные степперы (4-проводные не используются)
- Микрошаговые (1/1, 1/2, 1/4, 1/8 и 1/16)
- Главная/Подключения концевых выключателей
- Радиатор
Узнать больше
PRO 4 Axis Kit
Полностью загружен$ 105
- 4 AXIS
- Обновление до 4 TH AXIS
- 42 DCV MAX
- 6,8 ″ x 3,7 ″ (173 x 94 мм)
- .
0036
- Максимум 3,0 А на фазу
- 5-, 6- или 8-проводные степперы (4-проводные не используются)
- Микрошаговые (1/1, 1/2, 1/4, 1/8 и 1/16)
- Главная/Подключения концевых выключателей
- Радиатор
Узнать больше
PRO 4 Axis
Собрано и протестировано$ 174
- 4 AXIS
- Обновление до 4 TH AXIS
- 42 DCV MAX вход
- 6,8 ″ x 3,7 ″ (173 x 94mm)
- ID.0036
- Максимум 3,0 А на фазу
- 5-, 6- или 8-проводные степперы (4-проводные не используются)
- Микрошаговые (1/1, 1/2, 1/4, 1/8 и 1/16)
- Главная/Подключения концевых выключателей
- Радиатор
Узнать больше
Arduino UNO Shield
Arduino/GRBL для HobbyCNC PRO29,95 $
- Плата Arduino® UNO для подключения к HobbyCNC PRO
- Оптоизолированные входы. Предел X, Y и Z и датчик.
- Внешний источник питания 6 В постоянного тока
- Выход на дополнительную релейную плату.
ШИМ шпинделя, шпиндель + направление, подача охлаждающей жидкости
- Сигнал включения двигателя (контакт 1)
- Переключатель сброса
- Защита от обратного напряжения
- Минимум компонентов для быстрой и легкой сборки
Подробнее
Если вы модифицируете свой существующую настольную мельницу на настольный станок с ЧПУ, или вы строите фрезерный станок с ЧПУ своими руками или станок с ЧПУ DIY любого типа (включая роботов), наша доска – лучший способ заставить двигатели вращаться!
Мы любим наших клиентов и будем рады вашим отзывам и предложениям. Используйте нашу страницу «Свяжитесь с нами», чтобы сообщить нам, что мы делаем правильно или что мы можем улучшить.
Наш HobbyCNC PRO поставляется в виде набора , который вы собираете сами. Вы можете сравнить характеристики продукта здесь. Платы имеют четкую маркировку, а количество деталей сведено к минимуму, чтобы максимально упростить сборку!
Узнайте, что входит в сборку, с пошаговыми наглядными инструкциями в Instructables для HobbyCNC PRO.
Создание собственного фрезерного станка с ЧПУ | Roctech CNC Router
Сорок лет назад в мире крупного корпоративного производства компьютеры начали проникать на фабрики. Фрезерные станки с числовым программным управлением (или ЧПУ), которые запускали стопку перфокарт с пробитыми в них замысловатыми узорами отверстий, управляли огромными фрезерными станками и токарными станками. Они были громоздкими, но быстрыми, и каждая машина стоила больше, чем хороший дом.
Сборка фрезерного станка с ЧПУ
К счастью, для вас, домашнего мастера, те времена прошли. Теперь вполне возможно, практично и доступно иметь свой собственный фрезерный станок с ЧПУ, фрезерный станок с ЧПУ, токарный станок с ЧПУ, лазерный резак с ЧПУ или плазменный резак с ЧПУ. Имея только самый простой ПК, программное обеспечение на пару сотен долларов, аналогичные инвестиции в оборудование и электронику и собственную изобретательность, ВЫ можете иметь станок с ЧПУ в своей домашней мастерской.
Станок с ЧПУ может стать отличным дополнением к хобби, которое у вас уже есть… например, создание моделей самолетов, моделей железных дорог или деревообработка. Если вы увлекаетесь электроникой, небольшой фрезерный станок с ЧПУ может травить и сверлить печатные платы. Если у вас дома есть дети, станок с ЧПУ может быть отличным способом помочь им с проектами научных выставок, проектами по робототехнике или проектами по созданию декоративно-прикладного искусства.
Станки с ЧПУ могут резать или обрабатывать сложные детали и делать это очень быстро. Вы, наверное, восхищались некоторыми из тех замысловатых настенных ковров, которые вырезаны лобзиком…. где мастер провел буквально сотни часов, просверливая заготовку, отсоединяя лезвие пилы, продевая лезвие через отверстие, снова прикрепляя лезвие, делая разрез и повторяя процесс. Фрезерный станок с ЧПУ может выполнить ту же работу за меньшее время и гораздо точнее.
Фрезерный станок с ЧПУ, вероятно, является наиболее универсальным типом станка. Он может делать тяжелые разрезы и лепить в трех измерениях, или вы можете вставить резак с поворотным ножом в патрон фрезера и вырезать виниловые вывески и графику. С помощью соответствующего программного обеспечения вы можете оцифровать (или выполнить «обратный инжиниринг» детали) с помощью датчика, установленного в патроне фрезерного станка, для «отслеживания» контуров детали. Компьютер «запомнит» форму вашего оригинала, а затем позволит вам продублировать деталь с помощью фрезера, вырезав ее из бруска дерева или другого материала.
Фрезерный станок с ЧПУ может стать началом бизнеса на неполный или даже полный рабочий день. Вы можете вырезать красивые деревянные знаки, вырезать деревянные игрушки или моделировать детали самолета или железной дороги. Вы можете вырезать оригинальные узоры и делать из них формы для изготовления фигурок, табличек, рамок для картин или других литых деталей. Вы восхищались деревянными часами? Фрезерный станок с ЧПУ — отличный способ сделать один… или десятки. Если вы разочарованный изобретатель, вы можете вырезать механические детали для прототипов из различных материалов, включая дерево, пластик, алюминий, композитные материалы, такие как ламинат из углеродного волокна, или материалы для печатных плат.
Итак, с чего начать? Лучше всего начать с видео «Азбука ЧПУ». Этот двухчасовой DVD-диск проведет вас через весь рабочий процесс ЧПУ… начиная с основ проектирования станков, G-кода, программного обеспечения CAD и CAM и, наконец, через сам процесс резки. Вы увидите, как образцы деталей начинаются с дизайна, набрасываются на салфетке, передаются через программное обеспечение CAD и переходят в программное обеспечение автоматизированной обработки (CAM), где создаются фактические пути резки для изготовления детали. Выходные данные CAM-программы затем поступают к реальному контроллеру станка, который преобразует цифровую информацию в реальное движение… для резки детали.
У меня много работы, как у фотографа, писателя, редактора и видеопродюсера. Я редактирую журнал HighFlight Magazine, ежеквартальное издание Международной ассоциации миниатюрных самолетов. Эта организация занимается радиоуправляемыми моделями самолетов гигантского масштаба (минимальный «разрешенный» размер — размах крыльев 80 дюймов).