Токарный станок своими руками по металлу чертежи: чертежи самодельных вариантов, описание создания простейших настольных конструкций + видео
alexxlab | 15.06.2023 | 0 | Токарный
Cтанок по металлу своими руками в домашних условиях
Благодаря токарным станкам по металлу человек получает возможность изготовить некоторые детали самостоятельно. Не всегда есть возможность купить деталь для автомобиля или спецтехники.
И чаще всего не потому что денег не хватает, просто если речь идет о старой советской спецтехнике или продукции автопрома, многие модели уже не выпускаются. Но тем не менее, это не лишает пользователя возможности ими пользоваться. Токарные станки по металлу своими руками дают возможность в домашних условиях делать все что вам нужно.
Зачем покупать токарный станок по металлу, если его можно сделать самостоятельно. Это не так сложно, а все что вам потребуется — наличие чертежей, немного терпения и старая электротехника. Давайте рассмотрим, как сделать такое оборудование самому.
Содержание
- 1 Основное предназначение токарного станка
- 1.1 Есть определенная классификация токарного оборудования. Они делятся следующим образом
- 2 Как устроен станок — важные конструктивные элементы
- 3 Особенности конструкции токарно-винторезного станка своими руками
- 3.
1 Для работы по созданию станка из подручных средств, потребуется несколько простых инструментов, который найдутся у каждого человека
- 3.
- 4 Проектировка будущего изделия
- 5 Создаем токарный станок на базе электромотора
Основное предназначение токарного станка
ТВ 16 токарно-винторезный
В принципе работы любого токарного станка лежит обработка детали при ее вращении. Таким образом резак вставленный в плоскость вращения, при контакте с заготовкой будет удалять лишние элементы. Такое оборудование поддается автоматизации, благодаря чему оператор получает возможность для следующего:
- Выполнять продольное точение цилиндрической заготовки с гладкой или ступенчатой поверхностью;
- Обрабатывать уступы или канавки в будущей детали;
- Выполнять проточку наружных или внутренних поверхностей конической формы;
- Осуществлять нарезку резьбы, как внутренней, так и наружной при помощи резца или сверла;
- Делать развертку или зенкерование отверстий металлической заготовки;
- Отрезать лишние части или прорезать канавки;
- Выполнить накатку рифлёной поверхности заготовки.
Главным назначением в применении токарного станка по металлу является обработка валов, втулок или дисков. Таким образом человек получает возможность из заготовки сделать ось, маховик, звездочки, различные вкладыши, прочее. Также на универсальном токарном станке можно выполнять обработку корпусных деталей.
Есть определенная классификация токарного оборудования. Они делятся следующим образом
- По токарному признаку. Существует целых 9 подгрупп, при делении оборудования таким образом.
- Размерному ряду. Классификация выполняется в зависимости от диаметра заготовки, которую вы будете обрабатывать.
- Уровню специализации. В зависимости от профиля выполняемых работ и возможностей оборудования.
- Классу точности станка.
Самыми известными и применяемыми для домашней мастерской являются токарно-винторезные станки.
Они получили свою популярность еще в советские годы, когда на них обучали молодое поколение обрабатывать металлические детали. Основное назначение станков этой группы, как раз подготовка специалистов для работы с более сложным оборудованием.
Это подразумевает простоту работы и освоения станка. А также высокий уровень безопасности и минимальные требования к технике безопасности при работе оператора.
Сейчас подобное оборудование выпускают современного образца. У таких моделей повышенный функционал, рассчитанный для работы предприятия, следовательно, подобное оборудование нецелесообразно устанавливать у себя дома.
Это будет дорого — нет смысла переплачивать за функционал, которым вы никогда в своей жизни не воспользуетесь.
Старые станки ТВ-16, которыми оборудовались практически все кабинеты труда и производственные мастерские для обучения специалистов в учебных заведениях, идеально подойдут для дома. Проблема заключается в том, что достать такое оборудование даже с резервации очень проблематично.
Можно конечно, купить по фото на Авито, но вы купите с рук, и не факт, что станок прослужит у вас долго, после старого хозяина.
Лучше всего сделать его самостоятельно, тем более, ничего сложного в этом нет. Потребуются инструменты и материалы, которые достать не проблема. Соорудив станок по металлу своими руками, вы не только получите оборудование для работы с заготовками, но и сэкономите массу средств на покупке и услугах токарей.
Как устроен станок — важные конструктивные элементы
Схема конструкции.
У любого оборудования обязательно есть базис, без которого функционировать оно не будет. В токарно-винторезном станке, такими конструктивными элементами являются:
- Передняя и задняя бабки;
- Станина или рама, которая является основой для оборудования;
- Электропривод;
- Центры управления — ведомая и ведущая части станка;
- Подручник, куда оператор будет упирать режущие инструменты для обработки детали.
Сюда же можно включить заземление и защитный экран. Первое обеспечит вам безопасность от поражения электрическим током, а второе защитит от попадания стружки в лицо.
Агрегат будет устанавливаться на специальной станете. Если вы самостоятельно изготавливаете данное оборудование, такой станиной является рама.
Совет: лучше всего подобрать для основы качественный и прочный металл. Чем крепче станина, тем надежней будет фиксироваться оборудование. Это исключает дребезжание токарно-винторезного агрегата.
Вдоль рамы будет установлена задняя бабка. Это устройство является подвижным. Передняя — неподвижная. Она связывается ременной передачей с приводом, который и заставляет заготовку двигаться.
У токарно-винторезного оборудования центр, является ведущим, будет соединять двигатель вместе с передаточным для вращения устройством. Сам электропривод лучше всего установить на станине. В домашних условиях для создания станины лучше всего подойдут прочные металлические уголки, профили. Вам также потребуется несколько деревянных брусков, которые будут устанавливаться в качестве подставки, чтобы устранить вибрации оборудования.
Тут важно не столько что вы будете использовать, сколько устойчивость готовой рамы. В качестве электропривода подойдет мотор, лучше всего, чтобы он был из-под стиральной машины высокой мощности.
Запитываться вся установка будет напряжением 380В, поэтому вам обязательно будет провести в гараж провода способные обеспечить это требование. Также нужен будет старый стол, который будет подставкой для станка. Лучше всего выбрать крепкий стол из древесины или металла.
Передача оборотов на валы может выполняться при помощи цепной, фрикционной или ременной передачи. Ремень лучше всего подойдет, потому как является самым эффективным, простым и надежным видом.
Особенности конструкции токарно-винторезного станка своими руками
Общий вид самодельного станка.
Не сложно изготовить в домашних условиях самодельный токарный станок. Главное соблюдать ряд правил, которые помогут вам это сделать. Первым делом следует заместить ведомы и ведущие центры оборудования на одной оси. Таким образом пользователь удаляет вибрации, которые могут возникать в процессе обработки металлических заготовок.
Важно! При использовании оборудования с одним ведущим центром нужно устанавливать специальный кулачковый патрон либо же планшайбу.
Благодаря этим элементам у пользователя получится закрепить деталь для дальнейшей обработки режущими инструментами.
Важно! Ни в коем случае не следует устанавливать движки в качестве электропривода коллекторного типа.
Если не обеспечить такой агрегат дополнительной противодействующей нагрузкой, вращательный момент будет слишком сильным. Вытачивать что-либо при таких оборотах не получится. Кроме того, деталь может просто вылететь из зажимов, которые не обеспечат достаточной силы прихвата.
Таким образом можно не только повредить саму заготовку, но и хорошо пострадать при попадании ее в человека. Для этой цели используйте асинхронный двигатель. Суть его работы в том, что даже при увеличении или уменьшении нагрузки, частота вращения, передаваемая на валы меняться не будет.
Такой агрегат позволит оператору выполнять обработку деталей следующих габаритов:
- Толщина — 10 см;
- Ширина — до 70 см.
Задняя бабка — это уникальная конструктивная часть станка, где монтируется ведомый центр. Он может быть неподвижным или динамическим. Чтобы передвигать его используется элементарный болт. Подкручивая или раскручивая, бабка будет двигаться по направлению, нужному оператору.
Прежде чем устанавливать такой болт, смажьте его машинным маслом, для более лучшего и комфортного скольжения. Только потом его допустимо вставлять в резьбу, которая предназначена для передвижения задней бабки установки.
Для работы по созданию станка из подручных средств, потребуется несколько простых инструментов, который найдутся у каждого человека
- Электросварка;
- Болгарка;
- Станок для шлифовки;
- Дрель с набором сверл;
- Гаечные ключи;
- Инструменты измерения — штангенциркуль вместе с рулеткой или линейкой;
- Ручка, карандаш или маркер для разметки.
Первым делом стоит продумать чертеж, а потом уже приступать к монтажу.
Проектировка будущего изделия
Чертежи с размерами.
Следует оговориться, что рекомендуется для домашних целей делать оборудования с такими же размерами, как и ТВ-16. Оно маломощное, вполне удовлетворит потребности для физического лица. Габариты на чертежи берем следующие:
- Длина — до 115 см;
- Ширина до 62 см;
- Высота оси оборудования 18 см.
Важно! Не следует превышать эти габариты при изготовлении станка в кустарных условиях. Это может привести к нарушению его геометрии в процессе работы.
Когда вы составляете проект прорисуйте все детали, либо скачайте чертежи с размерами из интернета и работайте по готовому плану. Если пытаться держать все моменты в голове, вы обязательно допустите ошибку, которая испортит все оборудование.
От точности проекта и чертежа будущего оборудования вы будете отталкиваться не только в процессе работы, но и во время закупки необходимых расходных материалов.
Создаем токарный станок на базе электромотора
Теперь давайте рассмотрим последовательность сборки домашнего токарного станка по металлу.
- Изготавливаем раму. Мы, согласно чертежу, обрабатываем швеллер или уголок профиля. Вымеряем и обрезаем ненужное. При помощи сварки надежно завариваем станину, так чтобы получился ровный прямоугольник.
- Монтаж реек и бабок. На него будет монтироваться рейка с задней бабкой, с одной стороны. И привариваться передняя бабка с другой.
- Монтаж привода. С тыльной стороны рамы, устанавливается электродвигатель. Ставиться он как можно ближе к передней бабке, чтобы при помощи валов и ремня можно было практично обеспечить возможность передачи вращения на рабочую часть.
- Установка подручника. Когда предыдущий этап пройден — ставим подставку для инструментов. Она не приваривается, а делается подвижной при помощи гаек и болтов.
- Установка защитного кожуха и накидывание ремня на валы передачи.
- Подключение двигателя к сети и заземление.
- Визуальный осмотр на правильность сборки и пробный запуск.
Совет: Чтобы лучше понимать, как сделать станок — смотрите видео ниже.
Вас можно поздравить — домашний токарный станок готов. Теперь можно без особых усилий изготавливать любые нужные детали из металла на спецтехнику или автомобиль. Также вы теперь сможете самостоятельно ремонтировать те или иные запчасти транспортного средства или бытового инструмента.
Собери свои часы
Токарный станок Rose Engine. Что это такое? Что оно делает?
Токарный станок Rose Engine — механический инструмент, созданный на основе геометрического станка примерно в 1790 году и предназначенный для гравировки круглых и криволинейных узоров на металле. Используемый в дизайне ювелирных изделий, а также для печати рисунков, которые невозможно воспроизвести на марках и деньгах, что затрудняет их подделку, токарный станок Rose Engine является единственным в своем роде станком, который может гравировать изогнутые геометрические формы.
Изображение Брайана Джексона.
Джон Джейкоб Хольцапффель в настоящее время цитируется за создание компании Holtzapffel & Co, которая использовала обновления для геометрического токарного станка, изобретая и создавая один из первых, если не самый первый, токарно-карусельный станок Rose.
Прочитать историю токарного станка от Египта до токарного станка Rose Engine.
Как работает токарный станок Rose Engine?
Токарный станок Rose Engine использует серию сферических шестерен, вращаемых силой большого шпинделя, который вращается вручную или ногой. Шестерни расположены на стержне, а на конце стержня находится патрон. Шестерни и патрон вращаются вместе. Весь блок будет слегка раскачиваться в зависимости от того, какое оборудование использует артист.
Затем художник нажимает рукой, чтобы приложить режущее устройство или сверло к металлу, вставленному в патрон. (На картинке выше патрон отсутствует на изображении справа) Когда художник вручную проворачивает токарный станок с розовым двигателем, патрон также вращается и слегка качается. Если художник прижимает сверло к металлу рукой, одновременно вращая токарный станок, выгравированный узор может изгибаться и искривляться в зависимости от настроек художника.
Художественный дизайн для королевской семьи
Ниже представлено знаменитое яйцо Фаберже, новое яйцо, ежегодно изготавливаемое вручную Петром Карлом Фаберже для царя России Александра III, а затем его преемника Николая II с использованием токарного станка с розами и эмали в качестве основного слоя яйца.
Изображение Стэна Шебса, CC BY-SA 3.0, Link
Ранние часовщики использовали токарный станок Rose Engine Lathe для создания легких изогнутых орнаментов почти на всех компонентах карманных и наручных часов. Однако вы не найдете ручной гравировки на часах стоимостью менее 5000 долларов.
Создайте свои собственные часы с гордостью предлагает ручную гравировку с использованием токарного станка Rose Engine на роторе ваших часов в качестве премиального обновления. В Соединенных Штатах очень мало станков Rose Engine Lathe и еще меньше мастеров, которые умеют ими пользоваться.
Рик Белл знакомится с художником
История о том, как Рик Белл познакомился с мастером токарного станка Rose Engine из Цинциннати, удивительна.
Заполняя старый склад, который раньше производил то или иное, с непрозрачными окнами на сформированных бетонных стенах, мастер токарного станка Rose Engine по имени Майкл Дорса годами изготавливает на заказ эмалированные украшения.
Майкл Дорса изготавливает украшения на одном из двух токарных станков Rose Engine, которыми он владеет и управляет. Его работы можно найти на рынке Финдли, старейшем рынке под открытым небом в Огайо, и онлайн здесь
Рик однажды оказался на рынке Финдли за покупками (наши друзья из новостной рассылки знают, почему он делал покупки!) и он хотел получить подарок на его жена. Он наткнулся на будку Майкла. Узоры на украшениях мгновенно установили в его сознании связь с часовым делом, даже не осознавая, на что он смотрит.
Когда Рик разговаривал с помощницей Майкла, она сказала ему, что он использует токарный станок Rose Engine, Рик был потрясен! Он попросил встретиться с художником прямо на месте. Когда Майкл появился и встретил Рика, он отвел его в машинное отделение.
Рик был поражен, увидев эти токарные станки начала 1900-х годов в действии, представляя часы, которые они, возможно, вырезали за эти годы. Он спросил Майкла, может ли он разрезать роторы на наших механизмах. Майкл согласился, и отношения зародились.
Майкл прошел через несколько итерационных проектов для наших роторов, и, поскольку токарный станок предназначен для вырезания кругов, он создал специальный патрон для удержания ротора в двигателе Rose. В результате вы можете выбрать один из двух замечательных гильошированных дизайнов ротора ваших часов Series 1: Barely и Sine Wave.
Соберите свои собственные часы Мы очень гордимся тем, что можем предложить нашим клиентам возможность премиум-класса, чтобы ротор ваших автоматических часов был выгравирован вручную американским художником на токарном станке Rose Engine.
Когда художник выгравирует ручную гравировку ротора с помощью токарного станка Rose Engine, вы приобретаете единственный в своем роде драгоценный камень, которого нет в коллекции большинства любителей часов.
Ручная обработка не умирает. Подобно скорописи и струнной музыке, ручные инструменты — это основная механическая функция того, как все работает; как длины волн и зрительно-моторная координация, сделанные вручную, не полагаясь ни на что, кроме ручной рукоятки и художественного взгляда. Например, Движение ваших автоматических часов.
Токарный станок Rose Engine представляет начало и будущее Америки; мы великие строители и дизайнеры. Соберите свои собственные часы, и вы тоже почувствуете связь и сопричастность, которые американские мастера чувствовали годами, наблюдая, как их прекрасные творения служат поколениям.
Представляем мастера токарного станка Rose Engine Майкла Дорса.
Майкл Дорса из Rocker Box Productions
Разбираемся в гайках и болтах. Буквально.
Build Your Own Watch — первая часовая компания, предоставившая вам возможность собрать свои собственные часы вручную. Мы предоставляем компоненты и видео-инструкцию, вы предоставляете инструменты и развлекаетесь, собирая свои собственные часы.
В качестве опции премиум-класса местный мастер может выгравировать ручную гравировку ротора ваших часов на токарном станке Rose Engine. Узнайте больше о часах Series 1 и посмотрите, как могут выглядеть ваши часы, с помощью нашего онлайн-конфигуратора.
Спасибо.
Пожалуйста, не стесняйтесь оставлять комментарии на нашем форуме, мы будем рады услышать ваше мнение.
Токарный станок – Ручка из латуни и алюминия – Blondihacks
Новые технологии, новые инструменты, новые материалы, о боже!
Этот проект основан на всех предыдущих статьях этой серии о токарных станках, чтобы сделать что-то действительно особенное. Это будет последняя статья в этой «учебной» серии, хотя, конечно, она не будет последней, которую вы увидите здесь.
Вот ручка из латуни и алюминия. Крышка удерживается вакуумом. Задняя часть из алюминия интересна с эстетической точки зрения, но при этом удерживает вес вперед по направлению к наконечнику. Ручка сверху (прототип) разобрана, чтобы показать детали, которые мы будем делать. Окончательная версия внизу — это то, что я показываю в этом посте.
Чернильный картридж в этой ручке является заправкой для ручки марки TUL, которая мне больше всего нравится. Я разработал этот проект вокруг этих заправок. Если у вас есть любимая ручка, создайте свой собственный проект на основе ее внутренностей!
Для этого нам понадобится пара новых инструментов, помимо тех, что мы использовали во всех предыдущих статьях:
- Шариковый подшипник. Это приспособление для задней бабки, которое поддерживает работу таким образом, что металл не подвергается воздействию тепла или трения.
Это будет важно для данного конкретного проекта.
- 0-1″ микрометр. На этот раз мы будем делать по-настоящему точную работу, и наши старые штангенциркули больше не помогут. Да, они дорогие, но тратьте больше на качественный бренд. Здесь это действительно важно!
- Файлы. Подойдет любой качественный набор машинных файлов. В этом проекте мы будем использовать только один — 10-дюймовый гладкий фрезерный напильник. Вы должны также получить дескрипторы для них. Никогда не используйте напильник без ручки вблизи станков.
В качестве материалов мы будем использовать 10 дюймов ½ дюйма из латуни 360 свободной обработки и 5 дюймов ½ дюйма из алюминия 6061.
До сих пор у нас не было чертежей для наших проектов механической обработки. Тем не менее, этот достаточно сложен, поэтому будет полезно иметь его. Это было сделано в Sketchup, поэтому это не настоящий инженерный чертеж САПР, но он точен и соответствует масштабу.
Слева направо: задняя часть, передняя часть и колпачок.
Я понимаю, что изображение плохо читается, поэтому вот собственно рисунок в формате SketchUp или в формате PDF.
Глядя на переднюю часть ручки, вы увидите отверстия двух диаметров, которые встречаются в трапециевидной части, показанной фиолетовым цветом. Это трапециевидное сечение представляет собой точную геометрию конца сверла (118°) и рассчитано таким образом, чтобы мы могли сделать переход от широкой части чернильного стержня к узкой части в сужающейся области носа. Чуть позже мы увидим, как это делается на практике.
А пока давайте начнем с самого простого — с кепки!
Подбросьте латуни 360. Я использую здесь 3/4″, но 1/2″ было бы удобнее. Все, что у вас есть, будет работать, вопрос лишь в том, сколько фишек вы захотите убрать позже.
Торцевание и центрирование конца. Для торцевания и токарной обработки используйте латунный токарный инструмент, который вы сделали для проекта разметчика. Помните, что у латуни есть особые потребности!
Теперь подпираем заготовку задней бабкой и загибаем ее до внешнего диаметра нашей шляпки 400тыс.

Отметьте окончательную длину кепки (2,250″) и отрежьте ее немного длиннее.
Удерживая заглушку защитным алюминием, высверлите ее на глубину 2,1″ с помощью сверла 359 тыс.
Переверните колпачок в патроне, затем расправьте его по длине и скосите край.
Вот и все, что касается шапки. Это очень простая часть, использующая навыки, которые вы уже изучили. Теперь идет передняя часть ручки, которая является самой сложной частью. Показанный здесь порядок операций был достигнут с некоторым трудом, как мы увидим позже. Я думаю, что этот порядок хорошо работает и дает хорошие результаты.
Начните с торцовки и центрового сверления конца. Используйте маленькое центрирующее сверло № 1, потому что мы собираемся просверлить очень маленькое отверстие. Просто поцелуйте его центровым буром, затем пробурите скважину 93 тысячи на глубину 300 тысяч.
Это маленькое отверстие, которое мы просверлили в конце, должно держать кончик ручки. Глубина 300 тыс. не критична, но должна быть больше 285 тыс.
Следующим шагом является сужение носа. Может показаться странным делать это так скоро, но это последний шанс, который у нас будет.
Установите конус 18°, как показано здесь. Обратите внимание, что стержень инструмента выровнен с компаундом, который размещает инструмент перпендикулярно тому, что станет нашей конической поверхностью.
Заблокируйте каретку и, используя компаунд в качестве боковой подачи (и, как обычно, поперечного суппорта), отогните конус на 18°. Сейчас это будет выглядеть немного комично, потому что наш шток гораздо большего диаметра, чем будет ручка. Это нормально!
Поворачивайте конус вниз до тех пор, пока вокруг маленького отверстия не будет примерно столько материала, сколько показано выше. Не делайте эту область тонкой, как бумага, потому что через минуту она понадобится нам для поддержки.
Далее мы собираемся отогнуть корпус до самой большой открытой области ручки, которая представляет собой четвертьдюймовую «полосу» в середине (между колпачком и алюминиевой задней частью). Этот диаметр равен 400 тыс., как и цоколь.
Обратите внимание, что здесь мы поддерживаем тело с живым центром. На кончике пера нет тонны материала для поддержки, поэтому нам не нужны тепло и стресс, которые может вызвать мертвая точка.
Затем с помощью штангенциркуля отметьте плечевые зоны. Спереди есть узкая часть, где сидит колпачок, затем область декоративной полосы, за которой следует область резьбы сзади.
Теперь нам нужно отогнуть область, где находится крышка, а это очень важный размер. Здесь мы собираемся использовать посадку с трением скольжения с всасывающим действием, что означает, что нам нужно достичь этого размера с точностью до пары десятитысячных. Это, вероятно, превышает точность вашего поперечного скольжения (если только вы не потратили на свою машину намного больше, чем я). Напомним, что внутренний диаметр колпачка – 359 тыс., поэтому мы стремимся к 358,5 тыс. Для этого уменьшим до 360 тыс., а остальное сделаем вручную.
Чтобы правильно измерить следующие несколько измерений, нам понадобится микрометр. Наш верный друг штангенциркуль просто больше не собирается его резать. Штангенциркуль по-прежнему очень полезен для быстрого определения того, сколько материала вам нужно удалить в ходе большой операции. Однако, когда точность действительно имеет значение, избавьтесь от микрометра. Существует правильная техника использования одного из них, и они не особенно интуитивно понятны. Рекомендую отличное видео Tubalcain по теме.
После того, как вы прибьете размер в 360 тысяч по длине области крышки, пора закончить работу с напильником. Измерьте текущий размер в трех точках по длине. Если вы не выровняли свой токарный станок, вы можете обнаружить, что он поворачивает конус на четверть или полтысячной по 2-дюймовому размеру, с которым мы здесь работаем. Обычно вы, вероятно, этого не заметите, но для этого измерения это будет иметь значение. К счастью, мы можем легко компенсировать это, заполнив одни области больше, чем другие. Никогда не недооценивайте силу ручной работы.
Чтобы перейти к размеру 358,5 тыс. , мы воспользуемся техникой, называемой «токарная обработка». Это включает в себя запуск токарного станка с нормальной скоростью вращения и применение напильника к работе, одновременно двигая рукой вперед. Это сложно описать, но у Tom’s Techniques есть отличное видео на эту тему.
Важное замечание по технике безопасности: использование напильника без рукоятки на токарном станке похоже на езду на велосипеде под гору с мечом, приставленным к груди. Если вы надеетесь когда-нибудь сделать свое лучшее впечатление от Росомахи, втиснув инструментальную сталь в свою мясистую руку, во что бы то ни стало уберите ручки напильника и позвольте токарному станку делать то, что делают токарные станки.
После пары проходов файлом у нас осталось 359,5 тысячных. Еще один ты идти. Ошибаетесь в том, что делаете это медленно и часто проверяете. Если вы промахнетесь сейчас, вам будет очень грустно. Этот процесс проходит быстрее, чем вы могли бы ожидать, потому что напильники очень твердые, а латунь очень мягкая.

Перед и после каждого прохода напильником делайте пробную посадку колпачка (поэтому мы сделали его первым).
Продолжайте пробную установку колпачка по ходу дела. Если вы попали в высшую точку, как здесь, измерьте эту область микрометром и подпилите еще немного.
Продолжайте пробную подгонку и подпиливание до тех пор, пока не получите плотную скользящую посадку. Она должна легко сниматься, но быть достаточно липкой, чтобы не отвалилась. Когда вы сделаете это правильно, вы должны получить небольшой вакуум при извлечении со слышимым хлопком (как показано ниже).
Если вы промахнулись и колпачок стал слишком свободным, есть одно последнее средство. Салон кепки 359тыс, если помните. Ну, есть буровое долото длиной 358 тысяч, которое называется «Т». В любом хорошем наборе индексов есть сверла с буквами, в число которых, конечно же, входит буква T. Вы можете переделать колпачок с нуля и высверлить его размером T. Это вернет вам еще одну тысячную, и вы сможете установить крышку, используя описанный выше метод. Это единственная «переделка», которую вы получите, поэтому лучше не торопиться и делать это осторожно.
После идеальной подгонки колпачка вставьте острый инструмент и очистите сопрягаемый буртик.
В последний раз примерьте кепку, чтобы убедиться, что плечо красивое и прямое.
Затем отрежьте переднюю часть ручки немного дальше желаемой длины.
Переверните деталь, зафиксируйте ее защитным алюминием, затем просверлите торец встык и отцентрируйте.
Теперь мы собираемся сделать область с резьбой, которая скрепит половинки ручки. Резьба 5/16-24, то есть номинальный диаметр нашей резьбы 312 тыс. Так как это латунь, и поэтому легко нарезать резьбу, мы пойдем ровно к 312. На тысячу или две меньше это тоже нормально.
Отверните резьбовую часть до 312. Я использую остроконечный инструмент, потому что отделка не имеет значения (мы собираемся нарезать резьбу), и это экономит время на замену инструментов для очистки плеча.

С помощью острого наконечника или отрезного лезвия сделайте надрез прямо на только что сделанном плече. Он не должен быть глубоким – достаточно нескольких тысяч. Это обеспечит плотное прилегание половинок пера друг к другу.
Проденьте конец, используя технику, которую мы изучили в проекте Magic Tube.
Теперь мы готовы разбурить основное отверстие на загоне до диаметра 234 тысячи. Он удерживает часть стержня большого диаметра. Глубина этой дыры действительно критична, поэтому мы собираемся делать это поэтапно. Начните с бурения на глубину 2,1″, как показано на рисунке. Нам нужна очень точная глубина отверстия, но обычные спиральные сверла на самом деле не особенно хороши для этого (и, честно говоря, токарный станок не лучший инструмент для этой операции). Вместо этого мы собираемся «подкрадываться» к измерению, делая понемногу, пока оно не станет правильным.
При первом проходе мы сверлим до безопасной глубины 2,1″.
Цель состоит в том, чтобы большое отверстие совпало с маленьким отверстием, которое мы просверлили в самом начале. Это образует плечо, на которое опирается стержень пера (фиолетовая область на рисунке). Глубина этого основного отверстия определяет величину кончика пера, выходящего за пределы корпуса. Начальная глубина 2,1 дюйма должна быть меньше маленькой дырочки, которую мы просверлили.
Через люк снаружи станка загляните в отверстие шпинделя. Если вы можете видеть дневной свет через кусок (как мы можем здесь), отверстия соединились.
Если отверстия не совпали, сверлите каждый раз на 20 тысяч глубже, пока они не совпадут. Затем приступайте к пробной установке наполнителя.
После каждого прохода сверления проверяйте выступ на кончике пера. Идите по 20 тысяч за раз, пока не будете удовлетворены.
Между каждым проходом необходимо вынимать деталь из патрона, чтобы проверить посадку насадки. Ничего страшного, просто сбросьте измерения глубины, полностью вставив сверло в деталь до упора (при выключенном токарном станке), обнулив шкалу маховика задней бабки и заблокировав заднюю бабку. Затем немного отодвинуть сверло, запустить станок, и можно пробурить еще 20 тыс. по шкале маховика задней бабки. Выключите машину, разблокируйте заднюю бабку, вытащите ее, снимите деталь, проверьте посадку и повторите.
Это хороший выступ наконечника, поэтому мы остановимся здесь.
Самая сложная часть, передняя, теперь убрана. На спину! Однако здесь возникают новые проблемы. Мы используем алюминий, чего раньше не делали в этой серии. Обработка алюминия похожа на попытку отрезать кусок жевательной резинки заостренной палкой. Вы можете сделать это, но это разочаровывающее усилие. Проблема в том, что алюминий липкий. Он прилипает к резаку, не любит срезаться, стружка не ломается. Есть некоторые методы, чтобы смягчить все это, но, по моему опыту, это никогда не забавный материал для обработки.
В первую очередь нам нужен новый тип насадки. Аналогично латуни, мы точим обычную насадку, за исключением другой задней рейки. На самом деле, алюминий требует тревожного угла наклона 35°! Этот крайний угол необходим для более или менее правильного отделения материала от фрезы.
Заточка с наклоном 35° настолько экстремальна, что помогает визуализировать ее перед шлифовкой. Вот боковой профиль насадки, и я начертил на ней угол 35°. Затем я могу глазом зафиксировать спину параллельно этому.
Речь идет о задних граблях. Это как крючок для мяса, но для алюминия. Алюминиевый крючок.
Вот бита в держателе. Во всем остальном это нормальный инструмент.
Для начала просверлите алюминиевую ложу по торцу и центру. Обратите внимание, что даже плохое центрирующее сверло оказывается в липкой каше с алюминием.
Далее подпираем задней бабкой и поворачиваем корпус вниз на 400тыс.
При токарной обработке алюминия очень легко получить это – большое скопление птиц, которое портит резцедержатель, патрон и вашу веру во все хорошее в мире.
Если у вас есть такие большие птичьи гнезда, вам нужно настроить некоторые параметры. Прежде всего, алюминий любит скорость. Включите токарный станок настолько высоко, насколько это возможно (скажем, 1000 об/мин), и увеличьте подачу. Убедитесь, что ваш инструмент острый. Алмазный точильный станок здесь неплохая идея, чтобы сделать его максимально острым. В лучшем случае вы получите тугие завитые нити, которые не будут мешать вам. Это цель с алюминием – сделать его как можно менее раздражающим.
Когда все параметры указаны правильно, вы получите тугие кудри, как на дне. Если что-то не идеально, вы получаете Satan’s Razor Blade сверху.
Еще одна проблема с алюминием заключается в том, что он накапливается на кромке режущего инструмента, затупляя ее. Если вы поворачиваетесь какое-то время, и дела больше не идут хорошо, возможно, у вас есть накопление. Лучший способ предотвратить образование отложений — использовать легкое несульфурированное масло для резки в больших количествах. Для этого хорошо подходит WD-40. Не стесняйтесь — вам нужно ровное покрытие на всем, что вы режете. Даже с этой предосторожностью вы можете получить некоторое накопление.
Трудно сфотографировать, но видите светло-серую область на режущей кромке (вверху слева) этого инструмента? Это алюминиевый нарост.
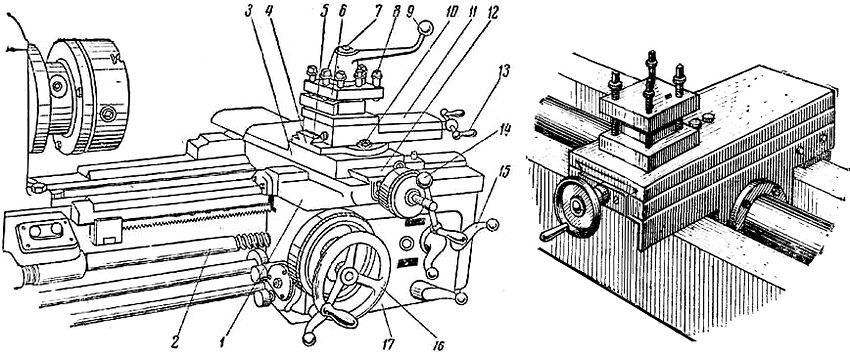
Если все сделано правильно, алюминий дает действительно красивую поверхность. Однако, как вы можете видеть здесь, за моей машиной, вы получаете груду спиральной проволоки, которую нужно очистить, даже если вы все делаете правильно.
Сделав наружный диаметр, отрежьте деталь и переверните ее в патроне (как обычно, защищая ее от кулачков алюминиевой банкой).
Просверлите отверстие большего диаметра, показанное на чертеже (270 тыс.). Это для внутренних нитей в этой половине ручки. Просверлите на большую глубину 0,75 дюйма, чтобы оставить место для конца метчика.
Нажмите на резьбу 5/16-24. Здесь я демонстрирую вариант техники постукивания, показанной в проекте Magic Tube. Рукоятка метчика опирается на станок, и я вручную поворачиваю патрон, а другой рукой поддерживаю давление задней бабки внутрь. Это работает хорошо, но будьте осторожны с небольшими нажатиями.
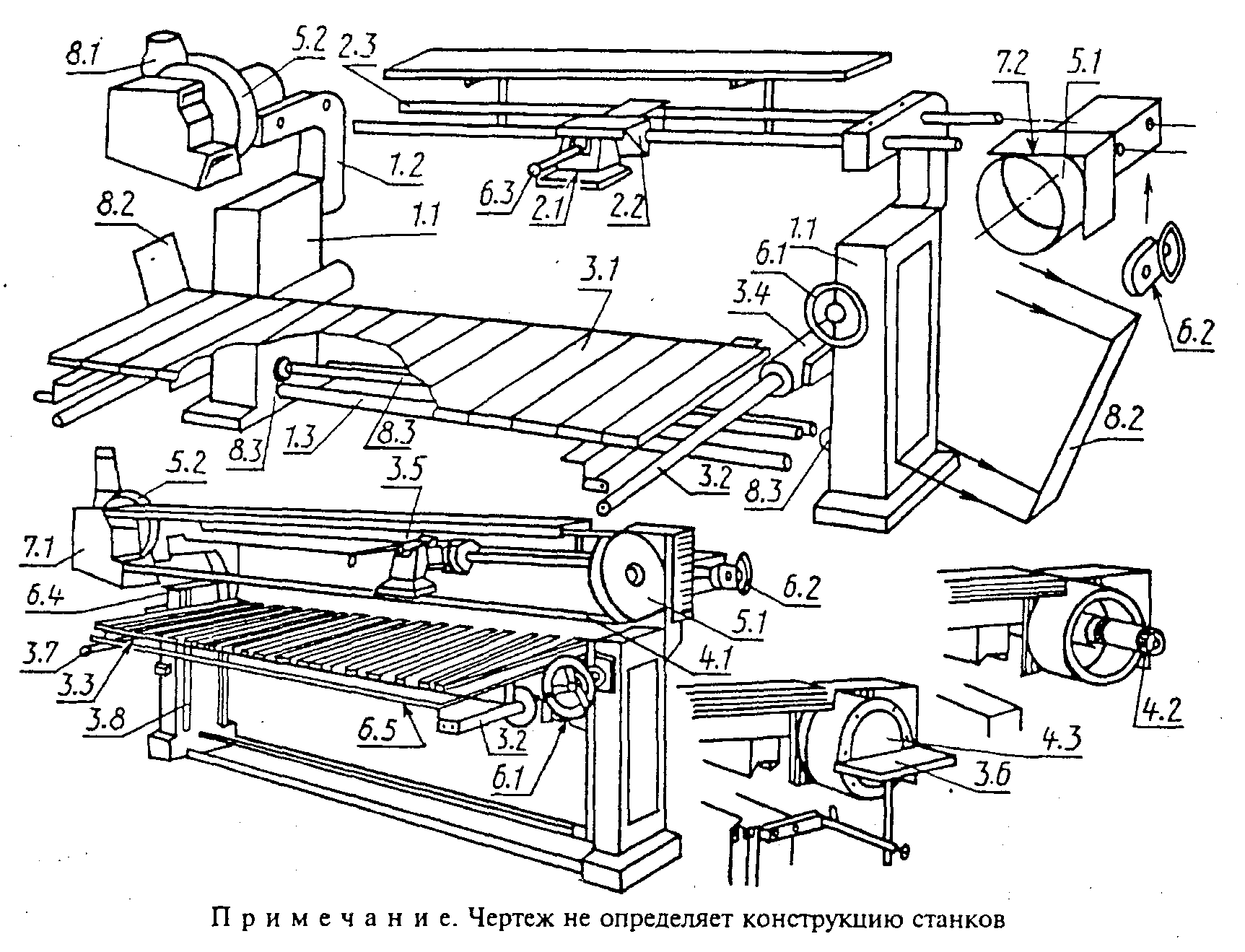
Теперь мы можем просверлить основную часть задней части загона, используя то же сверло на 234 тысячи, что и раньше. Как и раньше, эта глубина очень важна, поэтому просверлите до номинального значения 1,9.″, затем проверьте посадку и повторите сверление оттуда. Эта глубина имеет решающее значение, поскольку она удерживает заднюю часть стержня, чтобы он не соскальзывал вверх, когда вы нажимаете на шариковую ручку. Слишком глубоко, и наполнитель будет скользить внутри тела. Слишком мелкий, две половинки корпуса не будут плотно свинчиваться. Опять же, делайте по 20 тысяч за раз и проверяйте соответствие, пока не получите нужный результат.
Наконец, переверните деталь, затем лицевой стороной и скосите заднюю часть.
Вот и все! Перо готово. Это сложный проект, поэтому не расстраивайтесь, если вы делаете ошибки и вам приходится что-то переделывать. На самом деле, чтобы повысить вашу самооценку, вот лишь несколько ошибок, которые я допустил при изготовлении этих ручек.
Здесь я неправильно переустановил измерение глубины при пробной установке сменной насадки и просверлил слишком глубоко конусную область. Он сразу же выскочил, как медная пробка. Пробка стыда. Медь, как тромбон неудачи.
Вот это забавно. При подрезании резьбы я слишком углубился, деформировав внутреннее пространство. Это привело к тому, что стержень ручки застрял и сломался пополам, когда я попытался его удалить. Это сложно сфотографировать, но внутри тюбика полно осколков пластика и чернил. Это огромный беспорядок, и его невозможно убрать, поэтому деталь была испорчена.
Вот еще три. Слева направо: забыл повернуть конус перед тем, как отрезать его, просверлил колпачок слишком глубоко и загнул область колпачка слишком далеко, что сделало невозможным правильную установку колпачка.
В этом проекте было много ошибок и потраченных впустую рабочих дней, но каждый раз я чему-то учился, и я намного лучше управляюсь с токарным станком, чем когда начинал! Ошибки — важная часть процесса, поэтому очень важно не отчаиваться и возвращаться, чтобы попробовать еще раз.