Hb это твердость: Таблица твердости по Бринеллю, Роквеллу, Виккерсу, Шору
alexxlab | 09.08.2018 | 0 | Разное
Твердость по бринеллю формула
Метод Бриннеля — один из основных методов определения твёрдости.
Этот метод относится к методам вдавливания. Испытание проводится следующим образом: вначале дают небольшую предварительную нагрузку для установления начального положения индентора на образце, затем прилагается основная нагрузка, образец выдерживают под её действием, измеряется глубина внедрения, после чего основная нагрузка снимается. При определении твёрдости методом Бринелля, в отличие от метода Роквелла, измерения производят до упругого восстановления материала. Индентор (полированный закалённый стальной шарик) вдавливают в поверхность испытуемого образца (толщиной не менее 4 мм) с регламентированным усилием. Через 30 с после приложения нагрузки измеряют глубину отпечатка. В другом варианте усилие прилагается до достижения регламентированной глубины внедрения.
Твёрдость по Бринеллю HB рассчитывается как «приложенная нагрузка», делённая на «площадь поверхности отпечатка»:
,
где — приложенная нагрузка, H;
— диаметр шарика, мм;
— диаметр отпечатка, мм,
,
где — глубина внедрения индентора.
Нормативными документами определены диаметры индентора, время экспозиции, глубина внедрения индентора.
- В России регламентированные нагрузки 49 Н, 127 Н, 358 Н, 961 Н, диаметр шарика 5 мм, глубины внедрения от 0,13 до 0,35 мм. В разных спецификациях эти значения различны.
- Наиболее распространённые диаметры шарика — 10, 5, 2,5 и 1 мм и нагрузки 187,5 кгс, 250 кгс, 500 кгс, 1 000 кгс и 3 000 кгс.
- Для выбора диаметра шарика обычно используют следующее правило: диаметр отпечатка должен лежать в пределах 0,2—0,7 диаметра шарика.
- В методиках ISO и ASTM объединены метод с одним шариком и разными нагрузками и метод с применением разных шариков, а также дана формула вычисления твёрдости, не зависящей от нагрузки.
Твёрдость по шкале Бринелля выражают в кгс/мм². Для определения твёрдости по методу Бринелля используют различные твердометры, как автоматические, так и ручные.
Типичные значения твёрдости для различных материалов
Материал | Твёрдость |
---|---|
Мягкое дерево, например сосна | 1,6 HBS 10/100 |
Твёрдое дерево | от 2,6 до 7,0 HBS 10/100 |
Алюминий | 15 HB |
Медь | 35 HB |
Дюраль | 70 HB |
Мягкая сталь | 120 HB |
Нержавеющая сталь | 250 HB |
Стекло | |
Инструментальная сталь | 650—700 HB |
Преимущества и недостатки
Недостатки
- Метод можно применять только для материалов с твердостью до 450 HB, если применять стальной закаленный шарик.
Как альтернатива, применяют шарики из твёрдого сплава на основе карбида вольфрама (WC), это позволяет повысить верхний предел измерения твёрдости до 600 HBW.
- Твёрдость по Бринеллю зависит от нагрузки, так как изменение глубины вдавливания не пропорционально изменению площади отпечатка.
- При вдавливании индентора по краям отпечатка из-за выдавливания материала образуются навалы и наплывы, что затрудняет измерение как диаметра, так и глубины отпечатка.
- Из-за большого размера тела внедрения (шарика) метод неприменим для тонких образцов.
Перевод результатов измерения твёрдости различными методами
Результаты измерения твёрдости по методу Бринелля могут быть переведены с помощью таблиц в единицы твёрдости по методам Виккерса и Роквелла. В свою очередь, измерения твёрдости двумя последними методами могут быть переведены в единицы твёрдости по методу Бринелля. Следует отметить, что таблицы перевода в разных нормативных документах отличаются.
Метод первопроходец. Звание заслуживает система определения твердости материалов, разработанная Августом Бринеллем. Это инженер из Швеции. Его метод стал первым стандартизированным и широко используемым. Шкалу Бринелля мир «взял на вооружение» в 1900-ом году. Разберемся, в чем суть системы, твердость каких материалов можно узнать с ее помощью, и есть ли у метода минусы.
Твердость по Бринеллю – суть метода
Для определения твердости используют прибор, составленный из измерительного блока и пресса. Наконечник пресса – стальной шарик. Его именуют индентором. Диаметр шарика соответствует ГОСТу 9012 – 59 (ИСО 6506-81, ИСО 410-82), установленному в 1990-лм году. Разрешены 3 показателя: 2,5, 5 и 10 миллиметров.
Нужный индентор выбирают так, чтобы отпечаток от него лежал в пределах 0,2-0,7 диаметра шарика. Измерение твердости по Бринеллю производится либо стальным шариком, либо шариком из карбида вольфрама. Последний, позволяет узнать твердость материалов, превышающих показатель обычной стали.
Карбидный индентор, как правило, нужен для инструментальных сплавов. Шарик из обычной стали используют, измеряя твердость древесины, меди, алюминия, дюраля, нержавейки, стекла. То есть, твердомер применяют не только к металлам.
Метод измерения твердости по Бринеллю состоит из 2-х нагрузок. Сначала, пресс опускают для пробной. Небольшим надавливанием устанавливают начальное положение индентора. После, сообщают уже солидный вес, держат определенное время, потом, измеряют диаметр следа. Звучит «стройно», но есть сложность.
По краям отпечатка образуются навалы и наплывы материала. Из-за них диаметр, глубина могут быть неточными. Твердость по методу Бринелля измеряют до упругого восстановления, то есть до возвращения материала в первоначальную форму. Это возвращение может быть неполным. Тогда, фиксируется его степень.
В схожем методе Роквелла упругого восстановления не дожидаются, да и в качестве индентора используют не только металлические шары, но и алмазные конусы. Это стоит учитывать, замеряя твердость по Бринеллю и Роквеллу. Для чистоты эксперимента можно добавить еще один метод, главное, соблюсти нюансы исследований и уметь соотнести их результаты. Об этом и поговорим.
Определение твердости по Бринеллю – о цифрах и буквах
Результаты исследований выражаются в буквенно-цифровой записи. Из букв в ней присутствуют либо HB, либо HBW. Первое обозначение актуально для стального шарика. Вторая запись указывает на то, что вдавливали сферу из карбида вольфрама. К буквам добавляют 2 или 3 числа. Первое – показатель твердости. Максимально возможный по Бринеллю – 650. Такой показатель измеряется карбидным индентором. Стальной вдавливается в материалы твердостью до 450-ти единиц.
Второе число в записи – диаметр шарика-наконечника. Он не указывается лишь в том случае, если максимальный, то есть равен 10-ти миллиметрам. Третье число в обозначении – сила, с которой давили на испытуемый образец. Рассмотрим такой перевод твердости по Бринеллю: 500 HBW 5/800. Запись HBW свидетельствует о применение карбидного шарика. Его диаметр составил 5 миллиметров.
Сила давления была равна 800-от килограммов силы (кгс). 500- итоговая твердость материала. Вычисляется она по формуле отношения приложенного усилия к площади отпечатка. Интересно, что со значениями шкалы Бринелля совпадает еще одна – Виккерса. Обе начинаются со 100 единиц. Правда наивысшая твердость по Виккерсу и Бринеллю разнится.
У Виккерса значения доходят до 1 200-от. Записи результатов отличаются лишь буквами. Шкала Виккерса обозначается HV. Стоит учитывать это, выбирая товары с указанием твердости. То, что по Бринеллю тверже стали, по Виккерсу – материал весьма податливый.
Кстати, согласно большинству словарей, твердость – это свойства пластичности, упругости и сопротивления деформациям, или иным разрушениям, при вдавливании в верхний слой испытуемого образца другого, более твердого вещества. Ну, вот, уточнили о чем речь. Пора разобраться, какая твердость и для каких материалов считается приемлемой.
Твердость по Бринеллю – таблица значений
Твердость стали по Бринеллю может быть от 103-ти до 200-от единиц. Показатель зависит от марки. Не стоит забывать, что существует мягкая, нержавеющая и закаленная сталь. Сплав Ст0, к примеру, занимает нижнюю планку твердости. СТ2пс – марка со 116-ю HB. У СТ3пс показатель равен 131. 170 HB отличают сталь СТ5Гпс и СТ5пс. 200 единиц у марок ВСт6сп, СТ6пс и СТ6сп.
Твердость металлов по Бринеллю, в том числе и их сплавов, к коим причисляется сталь, важна при эксплуатации многих предметов. Пример – подшипники. Они подвергаются трению. Будь сплав для подшипников мягким, машина не отходит и гарантийного срока. Сопротивляемость деталей износу, зависящая от твердости, важна и при конструировании космических аппаратов, летной техники, строительных конструкций.
Твердость стали по Брюнеллю
для арматуры высотных зданий, к примеру, должна быть не ниже 150-ти единиц. Если брать усредненные цифры для металлов, то черные, как правило, маркируются числом 140 HB, а твердость цветных не превышает 130-ти.
Так, твердость платины по Бринеллю – всего 50. Выше говорилось, что шкала начинается со 100. Однако, современные технологи нередко дополняют ее, доводя до единицы. Твердость некоторых цветных металлов щелочноземельной группы составляет всего 30 HB.
Если вопрос не о строительстве и конструировании машин, а о ремонте, людей больше интересуют показатели древесины. Ее твердость тоже иногда измеряют по Бринеллю. Для сплавов металлов есть ГОСТы. Массы изначально «замешивают» в соответствии с техническими требованиями. Для древесины условия иные. Твердость зависит не только от породы, но и от условий произрастания.
Липа из разных местностей может отличаться на 10-20 баллов, как и сосна, дуб, ольха. Поэтому, лучше смотреть не из чего сделаны стол, или паркет, а какая твердость указана в документах к ним.
Для паркета берется древесина, как минимум, средней твердости. Если отбросить, погрешность на условия произрастания, точно подойдут блоки из белой акации, самшита, железной березы, граба и кизила.
Твердость этих пород приближенна к 100 HB. Это на торцах. Радиальный и тангенциальный показатели неизбежно ниже процентов на 30. Древесину по Бринеллю мерят в странах Европы. Россия к ним примыкает. Продукция из США соответствует шкале Янка. Этот тест узконаправлен, применим только к дереву.
В Америке прилагаемую к материалу силу записывают не в килограммах, а в фунтах. Диаметр металлического шарика выражен в дюймах, составляет 0,444. В миллиметрах это около 11-ти.
Итоговый результат измерений не бывает ниже 660 единиц. Высший показатель – 4 500. Таким «хвастается» гваяковое дерево. Оно одно из самых дорогих, поскольку из-за твердости сложно обрабатывается, к тому же, редко встречается.
В общем, число 4 500, даже на товарах из Штатов, встретишь редко. А вот значения Бринелля проставлены на большинстве продукции, изготавливаемой в России, и завозимой из-за рубежа. Это шкала, в премудростях которой стоит разобраться.
Таблица твёрдости по Бринеллю
Твёрдость по Бринеллю определяется по формуле, указанной в таблице (когда усилие выражено в кгс). При определении твёрдости по Бринеллю за диаметр отпечатка d принимают среднеарифметическое значение результатов измерений.
Обозначается твёрдость по Бринеллю численным значением и символом HB, после которых указывается диаметр шарика и приложенное усилие. Только когда твёрдость по Бринеллю определяется шариком диаметром 10 мм при усилии 3000 кгс и продолжительности выдержки 30 секунд, обозначение результата представляет собой лишь числовое значение и HB, например 285 HB.
Таблица некоторых (с точностью до 0,1) значений твёрдости по Бринеллю, диаметр шарика 10 мм; d (mm) – диаметр отпечатка шарика | ||||
d (mm) | Druckkraft P (kp) | |||
3000 | 1000 | 500 | 250 | |
2 | 945,76 | 315,25 | 157,63 | 78,81 |
2,1 | 856,93 | 285,64 | 142,82 | 71,41 |
2,2 | 779,93 | 259,98 | 129,99 | 64,99 |
2,3 | 712,75 | 237,58 | 118,79 | 59,40 |
2,4 | 653,79 | 217,93 | 108,96 | 54,48 |
2,5 | 601,76 | 200,59 | 100,29 | 50,15 |
2,6 | 555,61 | 185,20 | 92,60 | 46,30 |
2,7 | 514,50 | 171,50 | 85,75 | 42,87 |
2,8 | 477,71 | 159,24 | 79,62 | 39,81 |
2,9 | 444,65 | 148,22 | 74,11 | 37,05 |
3 | 414,85 | 138,28 | 69,14 | 34,57 |
3,1 | 387,88 | 129,29 | 64,65 | 32,32 |
3,2 | 363,40 | 121,13 | 60,57 | 30,28 |
3,3 | 341,10 | 113,70 | 56,85 | 28,43 |
3,4 | 320,75 | 106,92 | 53,46 | 26,73 |
3,5 | 302,11 | 100,70 | 50,35 | 25,18 |
3,6 | 285,00 | 95,00 | 47,50 | 23,75 |
3,7 | 269,25 | 89,75 | 44,88 | 22,44 |
3,8 | 254,73 | 84,91 | 42,46 | 21,23 |
3,9 | 241,31 | 80,44 | 40,22 | 20,11 |
4 | 228,88 | 76,29 | 38,15 | 19,07 |
4,1 | 217,35 | 72,45 | 36,23 | 18,11 |
4,2 | 206,63 | 68,88 | 34,44 | 17,22 |
4,3 | 196,65 | 65,55 | 32,77 | 16,39 |
4,4 | 187,33 | 62,44 | 31,22 | 15,61 |
4,5 | 178,63 | 59,54 | 29,77 | 14,89 |
4,6 | 170,49 | 56,83 | 28,41 | 14,21 |
4,7 | 162,85 | 54,28 | 27,14 | 13,57 |
4,8 | 155,69 | 51,90 | 25,95 | 12,97 |
4,9 | 148,96 | 49,65 | 24,83 | 12,41 |
5 | 142,63 | 47,54 | 23,77 | 11,89 |
5,1 | 136,66 | 45,55 | 22,78 | 11,39 |
5,2 | 131,03 | 43,68 | 21,84 | 10,92 |
5,3 | 125,71 | 41,90 | 20,95 | 10,48 |
5,4 | 120,68 | 40,23 | 20,11 | 10,06 |
5,5 | 115,92 | 38,64 | 19,32 | 9,66 |
5,6 | 111,41 | 37,14 | 18,57 | 9,28 |
5,7 | 107,14 | 35,71 | 17,86 | 8,93 |
5,8 | 103,07 | 34,36 | 17,18 | 8,59 |
5,9 | 99,21 | 33,07 | 16,54 | 8,27 |
6 | 95,54 | 31,85 | 15,92 | 7,96 |
6,1 | 92,04 | 30,68 | 15,34 | 7,67 |
6,2 | 88,71 | 29,57 | 14,79 | 7,39 |
6,3 | 85,53 | 28,51 | 14,26 | 7,13 |
6,4 | 82,50 | 27,50 | 13,75 | 6,87 |
6,5 | 79,60 | 26,53 | 13,27 | 6,63 |
6,6 | 76,82 | 25,61 | 12,80 | 6,40 |
6,7 | 74,17 | 24,72 | 12,36 | 6,18 |
6,8 | 71,62 | 23,87 | 11,94 | 5,97 |
6,9 | 69,19 | 23,06 | 11,53 | 5,77 |
7 | 66,85 | 22,28 | 11,14 | 5,57 |
Примечание к таблице твёрдости по Бринеллю: значения, выделенные серым цветом, являются расчётными и на практике применены быть не могут.
Измерение твёрдости по Бринеллю
(метод Бринелля)
Метод измерения твёрдости по Бринеллю [по имени шведского инженера Ю.А.Бринелля (J.A.Brinell)] – это способ определения твёрдости материалов вдавливанием в испытываемую поверхность стального закалённого шарика диаметром 1; 2; 2,5; 5 и 10 мм пр нагрузке P от 625 H до 30 кН. Стальной шарик должен иметь твёрдость не менее 850 HV10. Шарик из твёрдого сплава должен иметь твёрдость не менее 1500 HV10. Измерение твёрдости по Бринеллю возможно для металлов и сплавов с твёрдостью не более 650 единиц.
Число твёрдости по Бринеллю HB – отношение нагрузки (кгс) к площади (мм 2 ) поверхности отпечатка. Для получения сопоставимых результатов относительной твёрдости материалы (HB свыше 130) испытывают при отношении P:D 2 =30, материалы средней твёрдости (HB 30-130) – при P:D 2 =10, мягкие (HB 2 =2,5. Испытания по методу Бринелля проводят на стационарных твердомерах – прессах Бринелля, обеспечивающих плавное приложение заданной нагрузки к шарику и постоянство её при выдержке в течение установленного времени (обычно 10-15 или 30 секунд).
Метод измерения твердости металлов по Бринеллю регламентирует ГОСТ 9012-59. Металлы. Метод измерения твердости по Бринеллю: Стандарт устанавливает метод измерения твердости по Бринеллю металлов с твердостью не более 650 единиц. Сущность метода заключается во вдавливании шарика (стального или из твердого сплава) в образец (изделие) под действием усилия, приложенного перпендикулярно к поверхности образца, в течение определенного времени, и измерении диаметра отпечатка после снятия усилия. ГОСТ 9012-59, в частности, определяет требования, предъявляемые к отбору образцов металла для измерения твёрдости по Бринеллю – размер образцов, шероховатость поверхности и др.
Твёрдость сталей по Бринеллю
Поскольку, как было описано выше, при определении твёрдости по Бринеллю используется стальной закалённый шарик, можно сделать вывод, что использование этого способа для измерения твёрдости сталей не всегда целесообразно. Поэтому в технической литературе чаще встречается обозначения твёрдости сталей не по Бринеллю, а по Роквеллу или по Виккерсу. Тем не менее измерять твёрдость сталей по Бринеллю иногда можно.
Автор: Корниенко А.Э. (ИЦМ)
Лит.:
- ГОСТ 9012-59. Металлы. Метод измерения твердости по Бринеллю.
- ГОСТ 23677-79. Твердомеры для металлов. Общие технические требования.
- Иванов В.Н. Словарь-справочник по литейному производству. – М.: Машиностроение, 1990. – 384 с.: ил.
Конкурс “Я и моя профессия: металловед, технолог литейного производства”. Узнать, участвовать >>>
Шкала Бринелля – Brinell scale
«BHN» перенаправляется сюда. Для использования в других целях, см BHN (значения) . Диаграмма силыШкалы Бринелля характеризует отступ твердость материалов по шкале проникновения индентор, загруженную на материал образец. Это одно из нескольких определений твердости в материаловедении .
История
Предложенный шведским инженером Йоханом Августом Бринеллем в 1900 году, это был первый широко используемый стандартизированный тест на твердость в машиностроении и металлургии . {2}}} \ right)}}}
где:
- BHN = число твердости по Бринеллю (кгс / мм 2 )
- P = приложенная нагрузка в килограммах-силе (кгс)
- D = диаметр индентора (мм)
- d = диаметр вдавливания (мм)
Твердость по Бринеллю иногда указывается в мегапаскалях; число твердости по Бринеллю умножается на ускорение свободного падения, 9,80665 м / с 2 , чтобы преобразовать его в мегапаскали.
BHN может быть преобразовано в предел прочности на разрыв (UTS), хотя соотношение зависит от материала и, следовательно, определяется эмпирически. Взаимосвязь основана на индексе Мейера (n) из закона Мейера . Если индекс Мейера меньше 2,2, то отношение UTS к BHN составляет 0,36. Если индекс Мейера больше 2,2, то коэффициент увеличивается.
BHN обозначается наиболее часто используемыми стандартами испытаний (ASTM E10-14 и ISO 6506–1: 2005) как HBW ( H от твердости, B от твердости по Бринеллю и W от материала индентора, карбида вольфрама (вольфрама)). {2}}} \ right)}}}
где:
- F = приложенная нагрузка (ньютоны)
- D = диаметр индентора (мм)
- d = диаметр вдавливания (мм)
Общие ценности
При цитировании числа твердости по Бринеллю (BHN или чаще HB) необходимо указать условия испытания, используемого для получения числа. (HB не имеет отношения к степени твердости карандаша «HB» .) Стандартный формат определения тестов можно увидеть в примере «HBW 10/3000». «HBW» означает, что использовался шариковый индентор из карбида вольфрама (от химического обозначения вольфрама или от шведско-немецкого названия вольфрама «Wolfram»), в отличие от «HBS», что означает шарик из закаленной стали. Цифра «10» – это диаметр шара в миллиметрах. «3000» – это сила в килограммах.
Твердость также может отображаться как XXX HB YY D 2 . XXX – это сила, прилагаемая (в кгс) к материалу типа YY (5 для алюминиевых сплавов, 10 для медных сплавов, 30 для сталей). Таким образом, можно записать типичную твердость стали: 250 HB 30 D 2 . Это может быть максимум или минимум.
Символ твердости | Диаметр индентора мм | F / D2 | Испытательная сила Н / кгс |
---|---|---|---|
HBW 10/3000 | 10 | 30 | 29420 (3000) |
HBW 10/1500 | 10 | 15 | 14710 (1500) |
HBW 10/1000 | 10 | 10 | 9807 (1000) |
Преимущества
Его можно использовать для испытаний на неоднородные материалы (материалы, свойства которых не являются постоянными по всему образцу). Бринель дает возможность проводить испытания с использованием разных сил и разных инденторов. Процесс тестирования деструктивен.
Стандарты
- Международный ( ISO ) и Европейский ( CEN ) стандарт
- Стандарт США ( ASTM International )
Смотрите также
использованная литература
внешние ссылки
- Испытание на твердость по Бринеллю – методы, преимущества, недостатки, применения
- Видео об испытании твердости по Бринеллю на YouTube
- Таблица преобразования Роквелла в Бринелл (Бринелл, Роквелл A, B, C)
- Таблица преобразования твердости Струерса (по Виккерсу, Бринеллю, Роквеллу B, C, D)
- Таблица преобразования твердости по Бринеллю HB (МПа, Бринелля, Виккерса, Роквелла C)

5. Меры твёрдости металлов – советы и помощь в выборе.
5. Меры твёрдости металлов – советы и помощь в выборе.
5. Меры твёрдости металлов – советы и помощь в выборе.
Меры твёрдости предназначены для воспроизведения твёрдости металлов по стандартизированным шкалам твердости: Роквелл (ГОСТ 9013-59), Супер-Роквелл (ГОСТ 22975-78), Бринелль (ГОСТ 9012-59), Виккерс (ГОСТ 2999-75), Шор (ГОСТ 23273-78), Либ (ASTM A956, DIN 50156-3).
Меры твёрдости необходимы для 2-х основных целей:— контроля исправности и точности показаний твердомеров. Как Вы проверяете точность хода часов по 6-му сигналу службы эталонного времени, также все международные стандарты рекомендуют ПЕРЕД началом серии измерений проверить точность показаний твердомера на мере твёрдости той шкалы и того диапазона в котором предполагается измерять твёрдость изделия.

— калибровки твердомеров. Если при контроле исправности и точности показаний твердомера на мере твёрдости выявлено завышение или занижение показаний твёрдости за пределами паспортной погрешности твердомера – такой твёрдомер необходимо КАЛИБРОВАТЬ. Процесс калибровки представляет собой приведение в соответствие (равенство) СРЕДНЕГО значения меры твёрдости (из 3…5 измерений твердомером) и её НОМИНАЛЬНОГО значения (выгравировано на мере твёрдости). Калибровка по шкалам твёрдости HRC, HB, HV, HSD и пр. позволяет ввести поправку (коррекцию) к калибровке твердомера, установленной предприятием-изготовителем. Проще говоря, как Вы подводите стрелку часов вперёд или назад по 6-му сигналу службы эталонного времени чтобы часы показывали точное время, также и твердомеры с помощью мер твёрдости необходимо калибровать для точности измерения твёрдости.
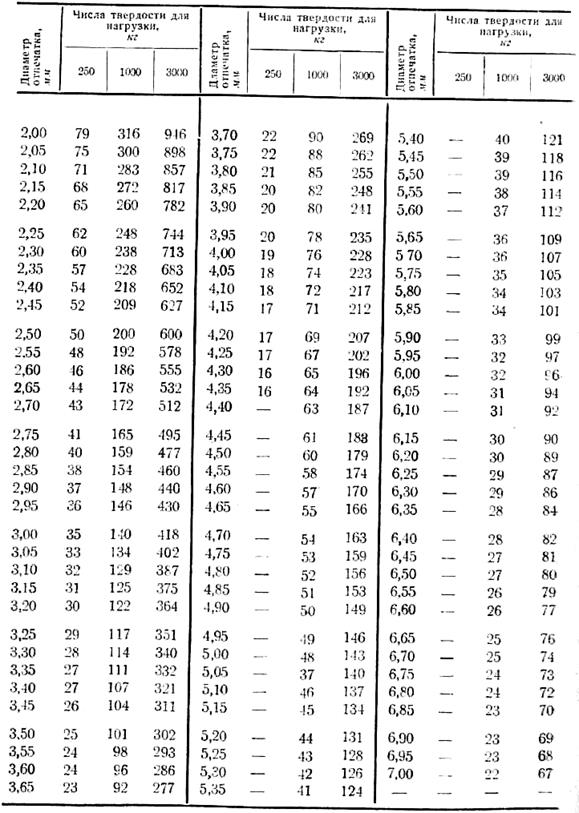
Выбор мер твёрдости металлов максимально прост:
- Уточните по какой из шкал твёрдости: Роквелл (HRC, HRD, HRA), Супер-Роквелл (HRN, HRT), Бринелль (HB), Виккерс (HV), Шор (HSD) или Либ (HLD) необходимо измерить твёрдость изделия. Эта шкала должна быть указана в технической документации на контролируемое изделие.
- Уточните в каком диапазоне (низкой, средней или высокой твёрдости) выбранной шкалы необходимо производить измерения твёрдости – это также должно быть указано в технической документации на изделие.
- Подберите меры твёрдости из нашего каталога согласно вышеуказанным двум пунктам.
Пример 1. В технической документации на изделие указана твёрдость в диапазоне 61 HRC … 66 HRC (это диапазон высокой твёрдости по шкале Роквелла). Вам необходимо приобрести Меру Твёрдости Роквелла HRC: 65±5.
Пример 2. В технической документации на изделие указана твёрдость в диапазоне 105 HB … 185 HB (это диапазон низкой и средней твёрдости по шкале Бринелля). Вам необходимо приобрести Меру Твёрдости Бринелля HB: 100±25 и Меру Твёрдости Бринелля HB: 200±50.
НАШИ РЕКОМЕНДАЦИИ:
- Возьмите за правило как Вы моете руки перед едой, также и перед крупной серией измерений проверяйте точность показаний твердомера на мерах твёрдости.
- Не экономьте на мерах твёрдости – если рабочая поверхность меры использована более чем на 70% (следы от уколов индентора твердомера), то используйте новую меру твёрдости. Эта рекомендация предписана многими стандартами, в т.ч. российскими, из-за высокой вероятности “попадания” нового измерения в след от “старого” измерения и, как следствие, получение некорректного результата измерения твёрдости. Меры твёрдости металлов имеют только одну рабочую поверхность – это та поверхность, на которой имеется градуировка (значение меры твёрдости, либо поверочное клеймо).
Возврат к списку
Выбор мер твердости
Форма позволяет выбрать стандартные эталонные меры твёрдости 2-го разряда.
Шкала твёрдости:
Диапазон твёрдости меры:
Нагрузка:
Добавлено в заказ:
–
Перейти к оформлению заказа
В случае необходимости заказа нестандартных эталонных мер твёрдости или эталонных мер твёрдости первого разряда, пожалуйста, напишите нам [email protected] или через форму обратной связи
Обзор шкал твердости: Роквелл, Бринелль
Многообразие различных шкал твёрдости пугает. Бринелль, Шор, Виккерс, Роквелл. У последней, помимо всем известной «подшкалы» С (отсюда и обозначение HRC– HardnessRockwell “C”), есть ещё и другие «подшкалы» «A», «B», «D», «E», «F», «H», «K». И это – не говоря о брате-близнеце – шкале Супер-Роквелла. Казалось бы, зачем так много: вдавили наконечник да посмотрели отпечаток. А какой наконечник? Какой формы? Из какого материала? А с каким усилием вдавливать? А если надо измерять твёрдость тонкой пластины? А если по глубине твёрдость разная? А если образец анизотропен в разных направлениях? А какой геометрический параметр отпечатка измерять?
Если коротко, то разные шкалы как раз и дают ответы на эти вопросы. Если чуть подробнее, то читаем дальше.
Шкала Роквелла.
Здесь остановимся только на самых известных «A», «B» и «С». Остальные используют очень редко, хотя меры твёрдости по таким шкалам мы тоже изготавливаем.
Шкала «A» – внедряется алмазный конус с углом при вершине 120˚ и основной нагрузкой 60 кгс. Пожалуй, самая универсальная «подшкала» из шкал Роквелла, т.к. её максимальная твёрдость соответствует максимальной твёрдости для металлов по шкале HRС (значение 83 HRA примерно соответствует значению 65HRC), а минимальная – минимальной по шкале HRB.
Шкала «B» – внедряется стальной шарик диаметром 1.588 мм при нагрузке 100 кгс. Используется для измерения твёрдости мягких материалов, когда шкала HRC уже «кончилась», т.е. мягче 20 HRC. При этом, будьте осторожны, если надавить таким способом в твёрдый материал, твёрдостью выше 40 HRC, то может «кончиться» уже шарик – повредится при вдавливании. В этом смысле международный стандарт ISO 6508 предусматривает шкалу HRBW. Последняя буква «W» в данном случае обозначает твердосплавный шарик из карбида вольфрама. Его можно вдавливать в твёрдые металлы.
Шкала «С» – внедряется алмазный конус с углом при вершине 120˚, как в шкале HRA, но основная нагрузка – не 60 кгс, а 150 кгс. На практике это даёт возможность стабильного измерения на более шероховатых поверхностях, чем при измерении по шкалам HRAили HRB. C другой стороны, возможности шкалы HRCограничены как твёрдостью – нельзя измерять детали мягче, чем 20HRC, так и толщиной детали. Дело в том, что нагрузка 150 кгс заставляет алмазный индентор вдавливаться глубже, чем нагрузка 60 кгс. При этом есть требование ГОСТа 9013-59 на метод Роквелла: «1.1. Толщина образца (или изделия) должна не менее чем в 10 раз превышать глубину внедрения наконечника после снятия основного усилия». Таким образом, использование шкалы HRA или HRB, за счёт меньших нагрузок, позволяет измерять более тонкие детали.
Полезно иметь в виду
- 1.График зависимости минимальной толщины образца от ожидаемой твёрдости. График взят из ГОСТ 9013-59.
- 2.Мало кто учитывает поправки в случае измерения на сферических или цилиндрических поверхностях (приложение 3, ГОСТ 9013-59). А напрасно, они существуют.
Шкала Бринелля.
Самый древний метод измерения твёрдости. Отличие от шкалы Роквелла – измеряется не глубина отпечатка, а диаметр. Поскольку вариантов индентора и нагрузок довольно много, то вместо того, чтобы каждому варианту придумывать название, после твёрдости в HB сразу указываются эти параметры. Например, 105 HB 2.5/62.5/10.
– «105» – понятно, это – число твёрдости в единицах HB
– «2.5» – диаметр шарика в мм (можно от 1 до 10 мм),
– «62.5» – нагрузка в кгс (можно от 5 до 3000 кгс), -
– «10» – время выдержки в нагруженном состоянии в с (почти всегда 10 с, кроме мягких материалов, там до 180 с).
При этом значение твёрдости 105 HBможет быть другим при других параметрах измерения.
Выбор размера шарика и нагрузки зависит от ожидаемой твёрдости и материала (ГОСТ 9012-59, п. 4.6), толщины (ГОСТ 9012-59, приложение 5), качества поверхности (чем больше шероховатость, тем больше должен быть отпечаток), размера отпечатка (ГОСТ 9012-59, п. 4.7), настроения технолога.
Как и со шкалой HRB(W), можно использовать твердосплавный шарик W во всём диапазоне твёрдости (0 – 650 HBW) и нужно при твёрдости более 450 HB.
Используя небольшую нагрузку и маленький диаметр шарика, можно измерять сверхмягкие материалы (даже шкала Роквелла HRB не справится) твёрдостью 0..5 HB 1/10/180. Кстати, мы научились делать меры твёрдости 0..10 HB из оловянного сплава, а также 30..50 HB из алюминиевого.
Пообщаться на данную тему можно по телефону +7(495) 229-75-26 или по электронной почте [email protected]
Полезная информация:
1. ГОСТ 9031-75, официальное издание, М.: ИПК Издательство стандартов, 2004
2. ГОСТ 9012-59, официальное издание, М.: Стандартинформ, 2007
3. ГОСТ 9013-59, официальное издание, М.: ИПК Издательство стандартов, 2001
Измерение твердости металлов | Статьи
Одной из наиболее распространенных характеристик, определяющих качество металлов и сплавов, возможность их применения в различных конструкциях и при различных условиях работы, является твёрдость. Твёрдость – свойство материала сопротивляться проникновению в него другого, более твёрдого тела — индентора. Обычно испытания на твердость производятся чаще, чем определение других механических характеристик металлов: деформации, прочности, относительного удлинения, пластичности и прочее.
Твердостью материала называют способность оказывать сопротивление механическому проникновению в его поверхностный слой другого твердого тела. Для определения твердости в поверхность материала с определённой силой вдавливается тело (индентор*), выполненное в виде стального шарика, алмазного конуса, пирамиды или иглы. По размерам получаемого на поверхности отпечатка судят о твердости материала. Таким образом, под твердостью понимают сопротивление материала местной пластической деформации, возникающей при внедрении в него более твердого тела – индентора. В зависимости от способа измерения твердости материала, количественно ее характеризуют числами твердости по Бринеллю (НВ), Роквеллу (HRC) или Виккерсу(HV).
Существует несколько способов измерения твердости, различающихся по характеру воздействия наконечника. Твердость можно измерять вдавливанием индентора (способ вдавливания), ударом или же по отскоку наконечника – шарика. Твердость, определенная царапаньем, характеризует сопротивление разрушению, по отскоку – упругие свойства, вдавливанием – сопротивление пластической деформации. Перспективным и высокоточным методом является метод непрерывного вдавливания, при котором записывается диаграмма перемещения, возникающего при внедрении индентора, с одновременной регистрацией усилий. В зависимости от скорости приложения нагрузки на индентор твердость различают статическую (нагрузка прикладывается плавно) и динамическую (нагрузка прикладывается ударом).
Таблица 1 – Особенности различных методов измерения твердости.
Далее, мы кратко рассмотрим классические методы измерения твердости металлов:
Твердость по методу Бринелля (ГОСТ 9012-59) измеряют вдавливанием в испытываемый образец стального шарика определенного диаметра под действием заданной нагрузки в течение определенного времени. В результате вдавливания шарика на поверхности образца получается отпечаток (лунка). Число твердости по Бринеллю, обозначаемое HB (при применении стального шарика для металлов с твердостью не более 450 единиц) или HBW (при применении шарика из твердого сплава для металлов с твердостью не более 650 единиц).
Для измерения твердости по методу Бринелля, в нашем каталоге представлен современный стационарный твердомер TH-600 и HB-3000B– более улучшенный твердомер, может быть использован для определения твердости закаленных и незакаленных сталей, чугуна, цветных сплавов, мягких материалов для вкладышей подшипников. Все твердомеры сертифицированы в РФ и могут быть применены на производстве.
Твердость по методу Роквелла – твердость, определяемая разностью между условной максимальной глубиной проникновения индентора и остаточной глубиной его внедрения под действием основной нагрузки, после снятия этой нагрузки, но при сохранении предварительной нагрузки. При этом методе индентором является алмазный конус или стальной закаленный шарик. В отличие от измерений по методу Бринелля твердость определяют по глубине отпечатка, а не по его площади. Глубина отпечатка измеряется в самом процессе вдавливания, что значительно упрощает испытания. Нагрузка прилагается последовательно в две стадии (ГОСТ 9013-59): сначала предварительная, обычно равная 10 кгс (для устранения влияния упругой деформации и различной степени шероховатости), а затем основная.
Твердомер Роквелла TH-320 измеряет разность между глубиной отпечатков, полученных от вдавливания наконечника под действием основной и предварительной нагрузок.
При измерении твердости методом Роквелла необходимо, чтобы на поверхности образца не было окалины, трещин, выбоин и др. Необходимо контролировать перпендикулярность приложения нагрузки и поверхности образца и устойчивость его положения на столике прибора. Расстояние отпечатка должно быть не менее 1,5 мм при вдавливании конуса и не менее 4мм при вдавливании шарика. Толщина образца должна не менее чем в 10 раз превышать глубину внедрения наконечника после снятия основной нагрузки. Твердость следует измерять не менее 3 раз на одном образце, усредняя полученные результаты.
Твердость по методу Виккерса в поверхность материала вдавливается алмазная четырехгранная пирамида с углом при вершине равным 136 градусов. После снятия нагрузки вдавливания измеряется диагональ отпечатка. Число твердости по Виккерсу HV подсчитывается как отношение нагрузки к измеренному значению диагонали отпечатка:
Число твердости по Виккерсу обозначается символом HV с указанием нагрузки и времени выдержки под нагрузкой, причем размерность числа твердости (кгс/мм2) не ставится. Продолжительность выдержки индентора под нагрузкой принимают для сталей 10 – 15 с, а для цветных металлов – 30 с.
При измерении твердости по Виккерсу должны быть соблюдены следующие условия:
• плавное возрастание нагрузки до необходимого значения;
• обеспечение перпендикулярности приложения действующего усилия к испытуемой поверхности;
• поверхность испытуемого образца должна иметь шероховатость не более 0,16 мкм;
• поддержание постоянства приложенной нагрузки в течение установленного времени;
• расстояние между центром отпечатка и краем образца или соседнего отпечатка должно быть не менее 2,5 длины диагонали отпечатка;
• минимальная толщина образца должна быть для стальных изделий больше диагонали отпечатка в 1,2 раза; для изделий из цветных металлов – в 1,5 раза.
Преимущество метода Виккерса по сравнению с методом Бринелля заключается в том, что методом Виккерса можно испытывать материалы более высокой твердости из-за применения алмазной пирамиды.
В нашем каталоге представлена целая линейка стационарных твердомеров по методу Виккерса: HV-10, HV-30 и HV-50.
Твердомеры серии HV представляют собой механические твердомеры, обладающие высокой точностью и удобством в эксплуатации и обслуживании. Данные твердомеры широко применяются на производстве, в научно-исследовательских институтах и лабораториях. Уникальное устройство преобразования и микро окулярное устройство считывания измерений, позволяющие сочетать в приборе легкость использования и высокую точность измерений.
*Индентор (англ. indenter от indent — вдавливать) — изготовленный из алмаза, твёрдого сплава или закаленной стали наконечник прибора, используемого для измерения твёрдости. Иногда инденторами (Nanoindenter) называют сами приборы для измерения нанотвердости.
Твердость HRC. Число твердости инструментов и крепежа.
Выбирая инструмент для работы, мы сталкиваемся с такой его характеристикой как твердость, которая характеризует его качество. Чем выше этот показатель, тем выше его способность сопротивляться пластической деформации и износу при воздействии на обрабатываемый материал. Именно этот показатель определяет, согнется ли зуб пилы при распиловке заготовок, или какую проволоку смогут перекусить кусачки.
Метод Роквелла
Среди всех существующих методов определения твердости сталей и цветных металлов самым распространенным и наиболее точным является метод Роквелла.
Метод Роквелла – определение твердости металла
Проведение измерений и определение числа твердости по Роквеллу регламентируется соответствующими документами ГОСТа 9013-59. Этот метод реализуется путем вдавливания в тестируемый материал инденторов – алмазного конуса или твердосплавного шарика. Алмазные инденторы используются для тестирования закаленных сталей и твердых сплавов, а твердосплавные шарики – для менее твердых и относительно мягких металлов. Измерения проводят на механических или электронных твердомерах.
Методом Роквелла предусматривается возможность применения целого ряда шкал твердости A, B, C, D, E, F, G, H (всего – 54), каждая из которых обеспечивает наибольшую точность только в своем, относительно узком диапазоне измерений.
Для измерения высоких значений твердости алмазным конусом чаще всего используются шкалы «А», «С». По ним тестируют образцы из закаленных инструментальных сталей и других твердых стальных сплавов. А сравнительно более мягкие материалы, такие как алюминий, медь, латунь, отожженные стали испытываются шариковыми инденторами по шкале «В».
Пример обозначения твердости по Роквеллу: 58 HRC или 42 HRB.
Впереди стоящие цифры обозначают число или условную единицу измерения. Две буквы после них – символ твердости по Роквеллу, третья буква – шкала, по которой проводились испытания.
(!) Два одинаковых значения от разных шкал – это не одно и то же, например, 58 HRC ≠ 58 HRA. Сопоставлять числовые значения по Роквеллу можно только в том случае, если они относятся к одной шкале.
Диапазоны шкал Роквелла по ГОСТ 8.064-94:
A | 70-93 HR |
B | 25-100 HR |
C | 20-67 HR |
Слесарный инструмент
Инструменты для ручной обработки металлов (рубка, резка, опиливание, клеймение, пробивка, разметка) изготавливают из углеродистых и легированных инструментальных сталей. Их рабочие части подвергают закаливанию до определенной твердости, которая должна находиться в пределах:
Ножовочные полотна, напильники | 58 – 64 HRC |
Зубила, крейцмессели, бородки, кернеры, чертилки | 54 – 60 HRC |
Молотки (боек, носок) | 50 – 57 HRC |
Монтажный инструмент
Сюда относятся различные гаечные ключи, отвертки, шарнирно-губцевый инструмент. Норму твердости для их рабочих частей устанавливают действующие стандарты. Это очень важный показатель, от которого зависит, насколько инструмент износостоек и способен сопротивляться смятию. Достаточные значения для некоторых инструментов приведены ниже:
Гаечные ключи с размером зева до 36 мм | 45,5 – 51,5 HRC |
Гаечные ключи с размером зева от 36 мм | 40,5 – 46,5 HRC |
Отвертки крестовые, шлицевые | 47 – 52 HRC |
Плоскогубцы, пассатижи, утконосы | 44 – 50 HRC |
Кусачки, бокорезы, ножницы по металлу | 56 – 61 HRC |
Металлорежущий инструмент
В эту категорию входит расходная оснастка для обработки металла резанием, используемая на станках или с ручными инструментами. Для ее изготовления используются быстрорежущие стали или твердые сплавы, которые сохраняют твердость в холодном и перегретом состоянии.
Метчики, плашки | 61 – 64 HRC |
Зенкеры, зенковки, цековки | 61 – 65 HRC |
Сверла по металлу | 63 – 69 HRC |
Сверла с покрытием нитрид-титана | до 80 HRC |
Фрезы из HSS | 62 – 66 HRC |
Примечание: Некоторые производители фрез указывают в маркировке твердость не самой фрезы, а материала, который она может обрабатывать.
Крепежные изделия
Существует взаимосвязь между классом прочности крепежа и его твердостью. Для высокопрочных болтов, винтов, гаек эта взаимосвязь отражена в таблице:
Болты и винты | Гайки | Шайбы | ||||||||||||||
Классы прочности |
8.8 |
10.9 | 12.9 |
8 |
10 |
12 |
Ст. | Зак.ст. | ||||||||
d<16 мм | d>16 мм | d<16 мм | d>16 мм | |||||||||||||
Твердость по Роквеллу, HRC | min | 23 | 23 | 32 | 39 | 11 | 19 | 26 |
29.![]() |
20.3 | 28.5 | |||||
max | 34 | 34 | 39 | 44 | 30 | 36 | 36 | 36 | 23.1 | 40.8 |
Если для болтов и гаек главной механической характеристикой является класс прочности, то для таких крепежных изделий как стопорные гайки, шайбы, установочные винты, твердость не менее важна.
Стандартами установлены следующие минимальные / максимальные значения по Роквеллу:
Стопорные кольца до Ø 38 мм | 47 – 52 HRC |
Стопорные кольца Ø 38 -200 мм | 44 – 49 HRC |
Стопорные кольца от Ø 200 мм | 41 – 46 HRC |
Стопорные зубчатые шайбы |
43.![]() |
Шайбы пружинные стальные (гровер) | 41.5 – 51 HRC |
Шайбы пружинные бронзовые (гровер) | 90 HRB |
Установочные винты класса прочности 14Н и 22Н | 75 – 105 HRB |
Установочные винты класса прочности 33Н и 45Н | 33 – 53 HRC |
Относительное измерение твердости при помощи напильников
Стоимость стационарных и портативных твердомеров довольно высока, поэтому их приобретение оправдано только необходимостью частой эксплуатации. Многие мастеровые по мере надобности практикуют измерять твердость металлов и сплавов относительно, при помощи подручных средств.
Измерение твердости при помощи напильников
Опиливание образца напильником – один из самых доступных, однако далеко не самый объективный способ проверки твердости стальных деталей, инструмента, оснастки. Напильник должен иметь не затупленную двойную насечку средней величины №3 или №4. Сопротивление опиливанию и сопровождающий его скрежет позволяет даже при небольшом навыке отличить незакаленную сталь от умеренно (40 HRC) или твердо закаленной (55 HRC).
Для тестирования с большей точностью существуют наборы тарированных напильников, именуемые также царапающий твердомер. Они применяются для испытания зубьев пил, фрез, шестерен. Каждый такой напильник является носителем определенного значения по шкале Роквелла. Твердость измеряется коротким царапанием металлической поверхности поочередно напильниками из набора. Затем выбираются два близко стоящие – более твердый, который оставил царапину и менее твердый, который не смог поцарапать поверхность. Твердость тестируемого металла будет находиться между значениями твердости этих двух напильников.
Переводная таблица твердости
Для сопоставления чисел твердости Роквелла, Бринелля, Виккерса, а также для перевода показателей одного метода в другой существует справочная таблица:
Виккерс, HV | Бринелль, HB | Роквелл, HRB |
100 | 100 |
52.![]() |
105 | 105 | 57.5 |
110 | 110 | 60.9 |
115 | 115 | 64.1 |
120 | 120 | 67.0 |
125 | 125 | 69.8 |
130 | 130 | 72.4 |
135 | 135 | 74.7 |
140 | 140 | 76.6 |
145 | 145 |
78.![]() |
150 | 150 | 79.9 |
155 | 155 | 81.4 |
160 | 160 | 82.8 |
165 | 165 | 84.2 |
170 | 170 | 85.6 |
175 | 175 | 87.0 |
180 | 180 | 88.3 |
185 | 185 | 89.5 |
190 | 190 |
90.![]() |
195 | 195 | 91.7 |
200 | 200 | 92.8 |
205 | 205 | 93.8 |
210 | 210 | 94.8 |
215 | 215 | 95.7 |
220 | 220 | 96.6 |
225 | 225 | 97.5 |
230 | 230 | 98.4 |
235 | 235 |
99.![]() |
240 | 240 | 100 |
Виккерс, HV | Бринелль, HB | Роквелл, HRC |
245 | 245 | 21.2 |
250 | 250 | 22.1 |
255 | 255 | 23.0 |
260 | 260 | 23.9 |
265 | 265 | 24.8 |
270 | 270 |
25.![]() |
275 | 275 | 26.4 |
280 | 280 | 27.2 |
285 | 285 | 28.0 |
290 | 290 | 28.8 |
295 | 295 | 29.5 |
300 | 300 | 30.2 |
310 | 310 | 31.6 |
320 | 319 | 33.0 |
330 | 328 |
34.![]() |
340 | 336 | 35.3 |
350 | 344 | 36.3 |
360 | 352 | 37.2 |
370 | 360 | 38.1 |
380 | 368 | 38.9 |
390 | 376 | 39.7 |
400 | 384 | 40.5 |
410 | 392 | 41.3 |
420 | 400 |
42.![]() |
430 | 408 | 42.9 |
440 | 416 | 43.7 |
450 | 425 | 44.5 |
460 | 434 | 45.3 |
470 | 443 | 46.1 |
490 | - | 47.5 |
500 | - | 48.2 |
520 | - | 49.6 |
540 | - |
50.![]() |
560 | - | 52.0 |
580 | - | 53.1 |
600 | - | 54.2 |
620 | - | 55.4 |
640 | - | 56.5 |
660 | - | 57.5 |
680 | - | 58.4 |
700 | - | 59.3 |
720 | - |
60.![]() |
740 | - | 61.1 |
760 | - | 62.0 |
780 | - | 62.8 |
800 | - | 63.6 |
820 | - | 64.3 |
840 | - | 65.1 |
860 | - | 65.8 |
880 | - | 66.4 |
900 | - |
67.![]() |
1114 | - | 69.0 |
1120 | - | 72.0 |
Примечание: В таблице приведены приближенные соотношения чисел, полученные разными методами. Погрешность перевода значений HV в HB составляет ±20 единиц, а перевода HV в HR (шкала C и B) до ±3 единиц.
При выборе инструмента желательно предпочесть модели известных производителей. Это дает уверенность в том, что приобретаемый продукт изготовлен с соблюдением технологий, а его твердость отвечает заявленным значениям.
Соотношение твердости по Роквеллу и Бринеллю различных изделий.
Статьи о продукции 19.11.2020 10:40:56
Дмитрий
Спасибо за статью, как раз то, что искал) Хотел удостовериться, что взял нормальные отвертки, а не фуфлыжные)
02. 04.2020 17:33:07
Способы измерения твёрдости металла, резины, бетона
Первоисточник статьи – https://vostok-7. ru/articles/tverdost/
Единого общепринятого определения термина «ТВЁРДОСТЬ» не существует поскольку методы определения этой метрологической величины настолько разнообразны, что нет возможности их объединить в одной фразе или описании. При этом даже для одного типа материала (напр. металлов) методов определения твердости существует более 5… Также именно по этой причине приборы для измерения твёрдости именуются не только твердомерами, но и другими названиями, указывающими на метод или материал измерения: дюрометр (для резин), склерометр (для минералов) и т.д.
Твёрдость минералов
Шкала твёрдости минералов Мооса (склерометры царапающие) – метод определения твёрдости минералов путём царапания одного минерала другим минералом для сравнительной диагностики твёрдости минералов между собой по системе мягче-твёрже. Испытываемый минерал либо не царапается другим минералом (эталоном Мооса или склерометром) и тогда его твёрдость по Моосу выше, либо царапается – и тогда его твёрдость по Моосу ниже.
Типы исследуемых материалов:
- минералы (природные и искусственные), в т.ч. измеряется твёрдость камней горных пород
- бетон и другие строительные материалы: твёрдость искусственных камней, плитки, стекла и др.
Молотки Шмидта (склерометры-молотки) – метод определения твёрдости и прочности на сжатие без разрушения строительный материалов: бетона, кирпичей, строительного раствора и пр. Оценка материалов происходит по предварительно установленной градуировочной зависимости между прочностью эталонных образцов и значением отскока бойка молотка Шмидта от поверхности материала.
Типы исследуемых материалов:
- бетон
- кирпич
- строительный раствор
- природные камни и горные породы
Твёрдость металлов
Твёрдость металлов – наиболее глубоко изученное и стандартизированное международной практикой измерение твёрдости. Наиболее распространены следующие методы:
Измерение твёрдости металлов по Бринеллю (твердомеры)
Один из старейших методов, твёрдость определяется по диаметру отпечатка, оставляемому металлическим шариком, вдавливаемым в поверхность. Обозначается HB, где H — Hardness (твёрдость, англ.), B — Brinell (Бринелль, англ.)
Измерение твёрдости металлов по Роквеллу (твердомеры)
Это самый распространённый из методов начала XX века, твёрдость определяется по относительной глубине вдавливания металлического шарика или алмазного конуса в поверхность тестируемого материала. Обозначается HR, где H — Hardness (твёрдость, англ.), R — Rockwell (Роквелл, англ.), а 3-й буквой идёт обозначение типа шкалы, напр. HRA, HRB, HRC и т.д.
Измерение твёрдости металлов по Виккерсу (твердомеры и микротвердомеры)
Самая широкая по охвату шкала, твёрдость определяется по площади отпечатка, оставляемого четырёхгранной алмазной пирамидкой, вдавливаемой в поверхность. Обозначается HV, где H — Hardness (твёрдость, англ.), V — Vickers (Виккерс, англ.).
Измерение твёрдости металлов по Шору (твердомеры и склероскопы)
Данный метод крайне редко используется, твёрдость определяется по высоте отскока бойка от поверхности. Обозначается HS, где H — Hardness (твёрдость, англ.), S — Shore (Шор, англ.), а 3-й буквой идёт обозначение типа шкалы, напр. HSD
Измерение твёрдости металлов по Либу (твердомеры)
Это самый широко применяемый на сегодня метод в мире, твёрдость определяется как отношение скоростей до и после отскока бойка от поверхности. Обозначается HL, где H — Hardness (твёрдость, англ.), L — Leeb (Либ, англ.), а 3-й буквой идёт обозначение типа датчика, напр. HLD, HLC и т.д.
Твёрдость резины
Определить твердость резины сегодня можно несколькими методами:
Измерение твёрдости резины по Шору (твердомеры и дюрометры)
Самый широко применяемый на сегодня метод в мире, твёрдость резины определяется по глубине проникновения в материал специальной закаленной стальной иглы (индентора) под действием калиброванной пружины. Твёрдость резины обозначается в международной практике как H, где H — Hardness (твёрдость, англ.), а 2-й буквой идёт обозначение типа шкалы, напр. HA, HB, HC, HD и т.д., в практике России пишется как «твёрдость по Шору тип А» или «твёрдость по Шору тип D».
Измерение твёрдости по Аскеру (твердомеры и дюрометры)
Это национальный японский метод, сходный с методом измерения твёрдости резины по Шору, но отличающийся от него типом инденторов, пружин и пр. Твёрдость резины обозначается в международной практике как Asker (Аскер, англ.), а далее идёт обозначение типа шкалы, напр. Asker С, Asker D и т.д. В России не применяется.
Измерение твёрдости по Роквеллу (твердомеры)
В этом случае используется стандартный твердомер Роквелла для измерения твёрдости металлов, но вместо индентора-конуса используются инденторы со стальными шариками. Твёрдость резины обозначается HR, где H — Hardness (твёрдость, англ.), R — Rockwell (Роквелл, англ.), а 3-й буквой идёт обозначение типа шкалы, напр. HRP, HRL, HRM или HRE.
Твердость по Бринеллю
J.A. Бринелл предложил первый широко принятый и стандартизированный испытание на твердость в 1900 году.
Твердомер Wilson Model “J” по Бринеллю – ручной управляемое механическое устройство.Система рывка ограничивает скорость приложение нагрузки, чтобы избежать динамических эффектов. Диаметр 10 мм Закаленный стальной шарик вдавливается в образец. Нагрузка регулируемый. Приложенные нагрузки от 500 кг до 3000 кг создаются при различной установленной массе. Меньшие нагрузки используются для мягких материалов, а большие – для более твердых. Для очень твердых материалов устанавливается шарик из карбида вольфрама диаметром 10 мм.
Образец помещается на опору и поднимается до контакта с
шар, вращая маховик в нижней части колонны наковальни.В
ручка с правой стороны сдвинута назад, чтобы коснуться заднего упора. Система дашпота ограничивает скорость передвижения. Груз держится
в течение 15 секунд, чтобы полностью сформировать пластиковую зону. В
ручка отводится назад, а наковальня опускается.
Число твердости по Бринеллю (HB) – это нагрузка, деленная на площадь отпечатка. Диаметр оттиска составляет измеряется с помощью микроскопа с наложенной шкалой. Бринелль Число твердости HB рассчитывается по формуле:
где
- P – приложенная нагрузка 3000, 1500 или 500 кг.2. Однако результаты обычно сообщаются без единиц измерения.
Объяснение градационной шкалы графита | Pencils.com
Для измерения твердости графитовой сердцевины карандаша используются две шкалы градации графита.
ЧИСЛОВЫЕ ГРАФИТОВЫЕ ШКАЛЫ
Первая градационная шкала графита представляет собой числовую шкалу. По этой шкале твердость сердцевины часто отмечается на карандаше – ищите число (например, «2», «2-1 / 2» или «3»).Чем выше число, тем тверже пишущий стержень и тем светлее остается след на бумаге. По мере того, как стержень карандаша становится мягче (из-за использования глины в меньших количествах), он оставляет более темный след, так как на бумаге остается больше графитового материала. Более мягкие карандаши тускнеют быстрее, чем более твердые грифели, и требуют более частой заточки.
HB ГРАФИТОВАЯ ШКАЛА
Вторая шкала градации графита известна как шкала HB. Большинство производителей карандашей за пределами США используют эту шкалу, используя букву «H» для обозначения твердого карандаша.Точно так же производитель карандашей может использовать букву «B», чтобы обозначить черную отметку карандаша, указывая на более мягкий грифель. Буква «F» также используется для обозначения того, что карандаш острит до тонкости.
Исторически сложилось так, что производители карандашей также использовали комбинации букв, чтобы рассказать нам о графите: карандаш с пометкой «HB» твердый и черный, карандаш с пометкой «HH» очень твердый, а карандаш с пометкой «BBB» действительно черный. ! Однако сегодня большинство карандашей, использующих систему HB, обозначаются цифрами, такими как 2B, 4B или 2H, чтобы указать степень твердости.Например, 4B будет мягче, чем 2B, а 3H жестче, чем H.
СРАВНЕНИЯ ШКАЛЫ ГРАФИТА
Как правило, оценка HB около середины шкалы считается эквивалентом карандаша №2 с использованием системы нумерации США.
Однако в действительности не существует специального отраслевого стандарта для оставления темноты метки в пределах HB или любой другой шкалы твердости. Таким образом, карандаш №2 или HB одной марки не обязательно оставит тот же след, что и карандаш №2 или HB другой марки.Большинство производителей карандашей устанавливают свои собственные внутренние стандарты для классов твердости графита и общего качества сердцевины, некоторые различия носят региональный характер. В Японии потребители, как правило, предпочитают более мягкие и темные провода; Таким образом, свинец HB, произведенный в Японии, обычно мягче и темнее, чем HB европейского производителя.
Выбор того, что лучше всего подходит для ваших собственных художественных и письменных потребностей, обычно зависит от личных предпочтений и экспериментов с карандашами разных марок.
Тест на твердость по Бринеллю
Тест на твердость по Бринеллю
Метод определения твердости по Бринеллю заключается в нанесении отпечатка материал с закаленной сталью диаметром 10 мм или твердосплавным шариком, подвергнутым до нагрузки 3000 кг.Для более мягких материалов нагрузку можно уменьшить до 1500 кг или 500 кг, чтобы избежать чрезмерного вдавливания. Полная загрузка обычно применяется в течение 10-15 секунд для чугуна и стали и для других металлов не менее 30 секунд. Диаметр вдавливание, оставшееся в исследуемом материале, измеряется с низким питаемый микроскоп. Номер привязи по Бринеллю рассчитывается по формуле деление прилагаемой нагрузки на площадь отпечатка.Изображение большего размера
Диаметр слепка – это среднее значение двух показаний справа
углов и использование таблицы чисел твердости по Бринеллю может упростить
определение твердости по Бринеллю. Хорошо структурированный Бринелль
число твердости показывает условия испытаний и выглядит так: “75
HB 10/500/30 “, что означает, что была получена твердость по Бринеллю 75.
с использованием закаленной стали диаметром 10 мм с приложенной нагрузкой 500 кг
в течение 30 секунд. При испытаниях особо твердых металлов a
Шарик из карбида вольфрама заменяет стальной шар. В сравнении с
другие методы испытания на твердость, шар Бринелля делает самые глубокие и
самое широкое вдавливание, поэтому испытание усредняет твердость по более широкому
количество материала, которое будет более точно учитывать несколько
структура зерна и любые неровности однородности
материал.Этот метод лучше всего подходит для достижения объема или
макротвердость материала, особенно материалов с
неоднородные структуры.
Калькулятор числа твердости по Бринеллю
Сила (кгс) | Введите значение | |
Диаметр шарикового индентора (мм) | Введите значение | |
Диаметр углубления (мм) | Введите значение | |
Число твердости по Бринеллю (HB) | Результат |
Ссылки на:
Испытание на твердостьИспытание на твердость по Роквеллу
Испытание на поверхностную твердость по Роквеллу
Испытание на твердость по БринеллюИспытание на твердость по Виккерсу
Испытание на микротвердость
Испытание на твердость по Моосу
Склероскоп и другие методы испытания на твердость
Таблицы преобразования твердости
Таблица преобразования твердости (цветная версия – загрузка может занять некоторое время) Таблица преобразования твердости (версия без цвета)
Таблица преобразования твердости (1) Таблица преобразования твердости
(2) Таблица преобразования твердости (Бринелля, Виккерса и предельная прочность на разрыв) Эквиваленты (1)
Таблица эквивалентов прочности на разрыв по Бринеллю, Виккерсу (2)
Таблица преобразования твердости, относящаяся к шкале твердости С по Роквеллу (твердые материалы) (цвет)
Таблица преобразования твердости, относящаяся к шкале твердости С по Роквеллу (твердые материалы ) (не цвет)
Таблица преобразования твердости, относящаяся к шкале твердости C по Роквеллу (твердые материалы)
Таблица эквивалентной расчетной твердости, относящаяся к шкале твердости C по Роквеллу и по Виккерсу (твердые материалы)
Таблица преобразования твердости, относящаяся к шкале твердости по Роквеллу B (мягкая металлы) (цвет)
Таблица преобразования твердости по шкале твердости B по Роквеллу (мягкие металлы) (не цветные)
Твердость C Таблица преобразования, относящаяся к шкале твердости B по Роквеллу (мягкие металлы)
Таблица минимальной толщины испытательного образца для испытания на твердость по Роквеллу с использованием шариковых инденторов
Таблица минимальной толщины испытательного образца для испытания на твердость по Роквеллу с использованием алмазных инденторов
Преобразование HV, МПа и ГПа Калькулятор
Телефон: +44 (0) 1252 405186
Электронная почта: tsc @ gordonengland.
co.uk
Знакомство с
Характер покрытий, наносимых методом термического напыления
Инженерия поверхности в двух словах
Форум по проектированию поверхностей
Услуги по ремонту пистолетов-распылителей
Расходные материалы для плазменных распылителей
Порошковые расходные материалы для термического напыления
Термораспылительные покрытия на полимерах, армированных углеродным и стекловолокном
HVOF-покрытие рулона для изготовления бумаги
Истираемые покрытия
Микрофотографии
Процессы термического напыления:
Процесс термического распыления Процесс
Процесс термического напыления дуги
Процесс термического напыления плазмой
Процесс термического напыления HVOF
Процесс термического напыления HVAF
Процесс термического напыления с детонацией
Теория плазменного пламени
Процесс нанесения покрытия холодным напылением
Износ и использование покрытий термическим напылением Коррозия и использование покрытий термическим напылением
Глоссарий терминов термического напыления и проектирования поверхностей
Каталог изображений для покрытий термическим напылением
Информация о потоке газа в плазме
Калькулятор коррекции потока газа в плазме
Контакты Форма
Ссылки на другие интересные сайты, связанные с термическим напылением и проектированием поверхностей
Взаимные ссылки
Периодическая таблица элементов
Единицы измерения СИ
Калькуляторы для преобразования единиц измерения
Испытания на твердость
Архив доски сообщений инженерной обработки поверхностей
Индекс архива доски объявлений Surface Engineering
Фотогалерея
Фотогалерея3
© Copyright Gordon England
Разница и преобразование твердости по Роквеллу, твердости по Бринеллю и другой твердости | by MartinaXu
Твердость – это мера мягкости материала.
Существует множество различных методов испытания на твердость, принцип которых определенно отличается, измеренные значения твердости и значения не совсем одинаковы. Твердость по Бринеллю (HB), портативный твердомер по Роквеллу (HRA, HRB, HRC), твердость по Виккерсу (HV), твердость по Шору резины и пластика (HA, HD) и т. Д. Являются наиболее распространенными испытаниями твердости при статической нагрузке, значение которых материала показывают способность его поверхности противостоять давлению твердых предметов. Следовательно, твердость – это не просто физическая величина, она отражает комплексные характеристики, включая эластичность, пластичность, прочность и ударную вязкость материала.
Твердость стали: код стали Твердость – H. В зависимости от различных методов испытаний на твердость,
- Распространенными методами являются твердость по Бринеллю (HB), твердость по Роквеллу (HRC), твердость по Виккерсу (HV), и твердость по Ричарду (HL), среди которых чаще используются HB и HRC.

- HB имеет широкий спектр применения, а HRC подходит для материалов с высокой твердостью, таких как твердость при термообработке. Разница между ними в том, что у них разные датчики.Зонд твердости по Бринеллю представляет собой твердосплавный шарик, а зонд твердости по Роквеллу – алмаз.
- HV подходит для микроскопического анализа. Твердость по Виккерсу (HV) вдавливается в поверхность материала с помощью алмазного квадратного конуса для нагрузки около 120 кг и верхнего угла 136 °, затем площадь поверхности вдавливания материала делится на значение нагрузки, то есть твердость по Виккерсу (HV) .
- HL ручной твердомер легко измерить. Ударный шар ударяет по твердой поверхности, вызывая отскок; твердость рассчитывается как отношение скорости удара и скорости отскока на расстоянии 1 мм между ударным шариком и образцом.Формула: Жесткость HL = 1000 × VB (скорость отскока) / VA (скорость удара).
HB – Твердость по Бринеллю:
Твердость по Бринеллю (HB) обычно используется для мягких материалов, таких как цветные металлы, сталь до термообработки или после отжига.
Твердость по Роквеллу (HRC) обычно используется для материалов с высокой твердостью, таких как твердость после термообработки и так далее.
Твердость по Бринеллю (HB): вдавите шарик из закаленной стали или твердосплавный шарик определенного диаметра в металлическую поверхность, которую нужно измерить, с определенным размером испытательного усилия, чтобы выдержать заданное время, а затем снимите испытательное усилие, измерив измеряемую поверхность. диаметр вдавливания.Значение твердости по Бринеллю – это отношение площади сферической поверхности вдавливания к испытательной силе. Обычно: вдавите шар из закаленной стали определенного размера (обычно диаметр 10 мм) в поверхность материала с определенным испытательным усилием (обычно 3000 кг), чтобы выдержать определенный период времени, затем снимите испытательное усилие, соотношение нагрузки и площадь его вдавливания. твердость по Бринеллю (HB) в кг / мм2 (Н / мм2). (Для получения подробной информации о твердости по Бринеллю (HB) нажмите «Твердомер по Бринеллю PHB-3000»)
Таблица преобразования твердости по Бринеллю HB (Н / мм2, Бринелля, Виккерса, Роквелла C)
Ниже представлена шкала Бринелля , которая показывает твердость материалов при вдавливании по шкале проникновения индентора, нагруженного на образец материала для испытаний.
Это одно из нескольких определений твердости в материаловедении.
Твердость
Таблица преобразования Растяжение Прочность
(Н / мм 2)
по Бринеллю
Твердость
(BHN) по Виккерсу
Твердость
(HV)
Роквелл
Твердость
(HRB)
Роквелл
Твердость
(HRC)
285
86 90 320 95 100 56.
2 350 105 110 62,3 385 114 120 66,7 415 124 130 71,2 450 133 140 75,0 480 143 150 78,7 510 152 160 81.
7 545 162 170 85,0 575 171 180 87,1 610 181 190 89,5 640 190 200 91,5 675 199 210 93,5 705 209 220 95.
0 740 219 230 96,7 770 228 240 98,1 800 238 250 99,5 820 242 255 23,1 850 252 265 24,8 880 261 275 26.
4 900 266 280 27,1 930 276 90 300 290 90 300 28,5 950 280 295 29,2 995 295 310 31,0 1030 304 320 32,2 1060 314 330 33.
3 1095 323 340 34,4 1125 333 350 35,5 1155 342 360 36,6 1190 352 370 37,7 1220 361 380 38,8 1255 90 300 371 390 39.
8 1290 380 400 40,8 1320 390 410 41,8 1350 399 420 42,7 1385 409 430 43,6 1420 418 440 44,5 1455 428 450 45.
3 1485 437 460 46,1 1520 447 470 46,9 1555 456 480 47,7 1595 466 490 48,4 1630 475 500 49,1 1665 485 510 49.
8 1700 494 520 50,5 1740 504 530 51,1 1775 513 540 51,7 1810 523 550 52,3 1845 532 560 53,0 1880 542 570 53.
6 1920 551 580 54,1 1955 561 590 54,7 1995 570 600 55,2 2030 580 610 55,7 2070 589 620 56,3 2105 599 630 56.
8 2145 608 640 57,3 2180 618 650 90 300 57,8
Преобразование твердости HB, HR, HV с пределом прочности на разрыв для стального листа – Новости – Новости
Механические свойства холоднокатаных стальных листов могут быть определены с помощью испытания на растяжение или испытания на твердость, что является наиболее удобным методом определения механических характеристик. свойства материалов.На самом деле между прочностью и твердостью стального металла существует соответствие. Как правило, чем выше твердость, тем выше износостойкость. Он широко используется в механической промышленности для измерения в соответствии с DIN 50150 / ISO 18265 / ASTM E140.
Различные материалы представлены разными методами твердости. Твердость по Бринеллю (HB) обычно используется для определения твердости металлических материалов с крупными зернами или составляющих их фаз, таких как чугун, сплавы, медь и медные сплавы, свинец, олово и легкие металлы.Твердость по Роквеллу (HR) используется для закалки стали, отожженной стали, алюминиевого сплава и других твердых сплавов и металлов. Твердость по Виккерсу (HV) используется для тестирования мелких деталей при окислении, азотировании, науглероживании, нанесении покрытий и других процессах. Кроме того, стекло, агат, керамика и другие хрупкие материалы обычно выражаются твердостью по Виккерсу.
Вообще говоря, твердость стального листа s составляет: HB> HR> HR. В следующей таблице приведено сравнение обычно используемого диапазона прочности стального листа на разрыв и HV, BH, HR.
T, S Rm Н / мм2
HV
HB
HRC
250
8062
–
270
85
80,7
–
285
90
85.
2
–
305
95
90,2
–
320
100
62 100
62 335
105
99,8
–
350
110
105
105
370 115
109
–
380
120
114
–
–
00
119
9 0062 –
415
130
124
–
430
135
62
000 450
140
133
–
465
145
138
48070
150
143
–
490
155
147
–
152
–
530
165
156
–
545
170
162
162
162
175
166
–
575
180
171
–
4 –
4 –
4 –
04 –
0
176
–
610
190
181
–
625
50004 5
–
9006 1 640
200
190
–
660
205
195
–
210
199
–
690
215
204
–
705
0
705
0
209
–
720
225
214
–
740
62 2304
0000009 – 755
235
223
–
770
240
228
20.
3
785
245
233
21,3
800
250
238
000 ,2 820
255
242
23,1
835
260
247
24.0
850
265
252
24,8
865
270 25
2562
900,6 880
275
261
26,4
900
280
266
27.1
915
285
271
27,8
930
290
276
000000 950
295
280
29,2
965
300
285
29.
8
995
310
295
31,0
1030
5
5
5 32,2
1060
330
314
33,3
1095
340
5
9004 1125
350
333
35,5
1115
360
342
1190
370
352
37,7
1220
380
361
38.8
1255
390
371
39,8
1290
400
38062
1320
410
390
41,8
1350
420
399
42.
7
1385
430
409
43,6
1420
440
418
000 448000 1455
450
428
45,3
1485
460
437
46.1
1520
470
447
46.9
1555
480
1595
490
(466)
48,4
1630
500
(475)
1 1665
510
(485)
49,8
1700
520
05
1740
530
(504)
51,1
1775
540
(51362)
04 (513620)7
1810
550
(523)
52,3
1845
560
900,0532
1880
570
(542)
53,6
1920
580
(551)
0004 9001 1955
590
(561)
54,7
1995
600
04 (570) 962 9620
2030
610
(580)
55,7
2070
620
620
3 2105
630
(599)
56,8
2145
640
04 (608)
2180
650
(618)
57,8
660
58.
3
670
58,8
680
59,2
6 59,2
6
59,7
700
60,1
720
61.0
740
61,8
760
62,5
6 62,5
6
63,3
800
64,0
820
64.7
840
65,3
860
65.
9
6 65.9
6
66,4
900
67,0
920
67.5
940
68,0
Таблица преобразования твердости – Таблица преобразования HBW в HRC
В этой таблице показаны приблизительные значения твердости для неаустенитных сталей. *
BRINELL РОКВЕЛЛ ВИКЕРС KNOOP
Макс нагрузка 1 кг Предел прочности на разрыв, тыс.
Фунтов на кв. Дюйм
Углубление
Диаметр
мм.
HBW
10/3000
HRC
HRB
HV
(диапазон HRC)
HV
(диапазон HRB)
HK
(диапазон HRC)
HK
(диапазон HRB)
Прокрутите вниз, чтобы просмотреть всю таблицу 2.
45
627
58,6
664
703
346.2
2,50
601
57,3
638
677
328.
9
2,55
578
56,1
615
652
313.
7
2,60
555
54,8
591
627
298.
4
2,65
534
53,5
569
603
287.
5
2,70
514
52,2
548
579
274.
5
2,75
495
50,9
528
556
263.
4
2,80
477
49,6
508
533
251.
8
2,85
461
48,3
491
513
241.
7
2,90
444
46,9
472
492
230.
4
2,95
429
45,7
456
474
219.
8
3,00
415
44,4
440
456
211.
5
3,05
401
43,1
425
439
201.
8
3,10
388
41,8
411
424
192.
7
3,15
375
40,5
397
408
184.
4
3,20
363
39,3
383
394
177.
6
3,25
352
38,1
372
382
170.
4
3,30
341
36,8
360
369
164.
1
3,35
331
35,7
349
358
158.
2
3,40
321
34,4
338
347
153.
0
3,45
311
33,0
327
334
149.
0
3,50
302
32,0
318
327
146.
3
3,55
293
30,8
308
317
140.
6
3,60
285
29,7
300
309
137.
6
3,65
277
28,6
291
301
134.
0
3,70
269
27,4
283
293
130.
1
3,75
262
26,3
275
286
127.
0
3,80
255
25,2
268
279
123.
8
3,85
248
24,1
261
272
119.
7
3,90
241
22,9
100
254
241
266
253
116.
3
3,95
235
21,8
99
247
235
260
248
114.
3
4,00
229
20,8
98
241
229
254
242
110.
0
4,05
223
19,7
97
238
223
251
237
105.
5
4,10
217
96
217
232
102.
3
4,15
212
95
212
227
100.
7
4,20
207
95
207
222
98.
8
4,25
201
93
201
217
94.
8
4,30
197
93
197
213
92.
8
4,35
192
92
192
208
90.
8
4,40
187
90
187
202
89.
4
4,45
183
89
183
198
88.
6
4,50
179
89
179
194
87.
5
4,55
174
87
174
189
85.
0
4,60
170
86
170
185
83.
3
4,65
167
85
167
182
82.
5
4,70
163
84
163
178
81.
3
4,75
159
83
159
173
80.
0
4,80
156
82
156
170
77.
0
4,85
152
81
152
166
72.
7
4,90
149
80
149
163
71.
3
4,95
146
79
146
160
69.
7
5,00
143
78
143
157
68.
7
5,05
140
76
140
152
67.
5
5,10
137
75
137
151
66.
0
5,15
134
74
134
147
64.
7
5,20
131
73
131
144
63.
5
5,25
128
71
128
141
62.
3
5,30
126
70
126
139
61.
5
5,35
123
69
123
137
60.
0
5,40
121
68
121
135
59.
0
5,45
118
66
118
132
57.5
* Все преобразования основаны на ASTM E140-12bε1 и ASTM A370-13
Заявление об ограничении ответственности: Хотя информация, изложенная в данном документе, считается правильной, Scot Forge не дает никаких рекомендаций или не предлагает никаких гарантий в отношении предмета или его точности. Scot Forge прямо отказывается от всех гарантий, явных, подразумеваемых или иных, включая, помимо прочего, все гарантии коммерческой ценности, пригодности или пригодности для конкретной цели или применения.
Авторские права принадлежат компании Scot Forge, 2017, все права защищены.
.
Телефон: +44 (0) 1252 405186
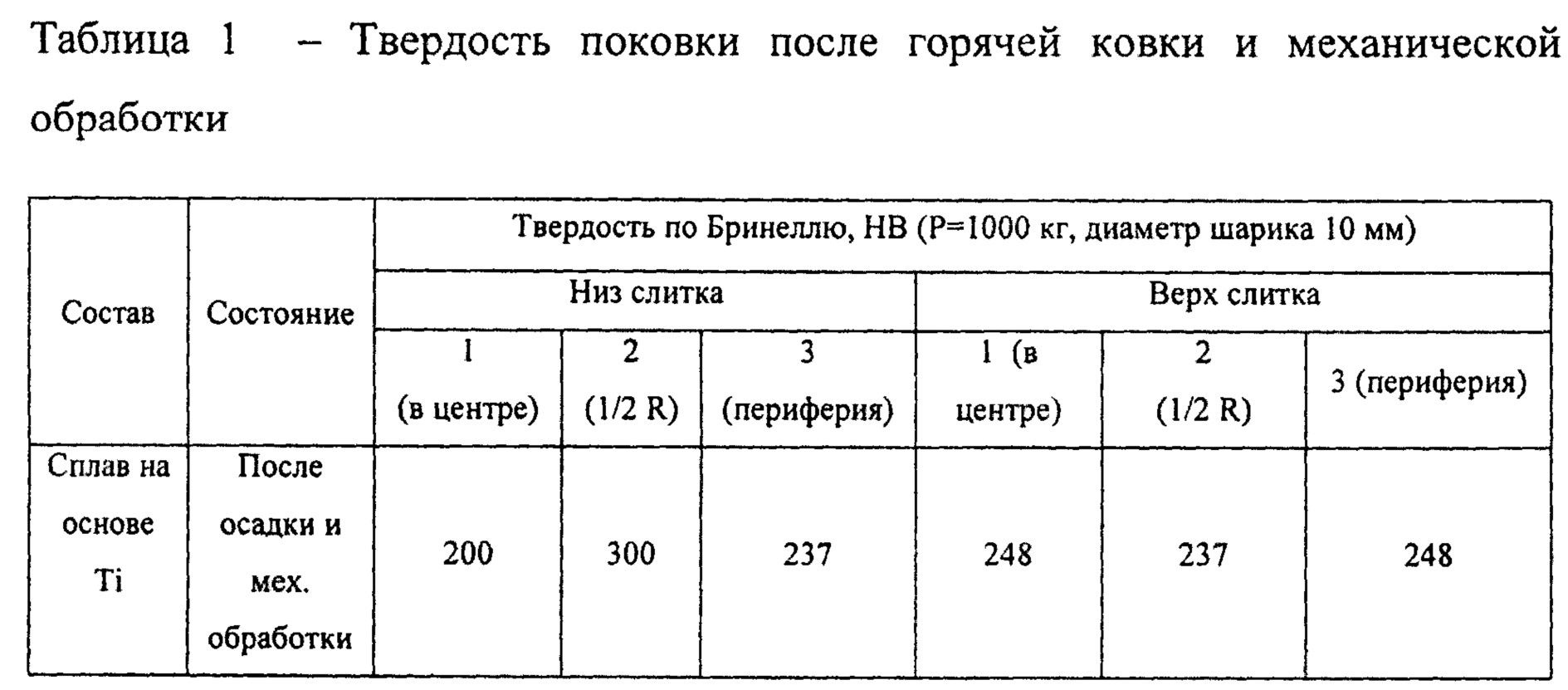
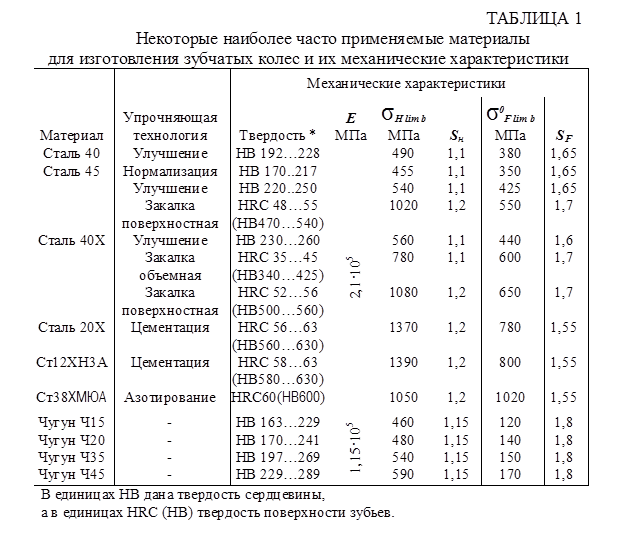
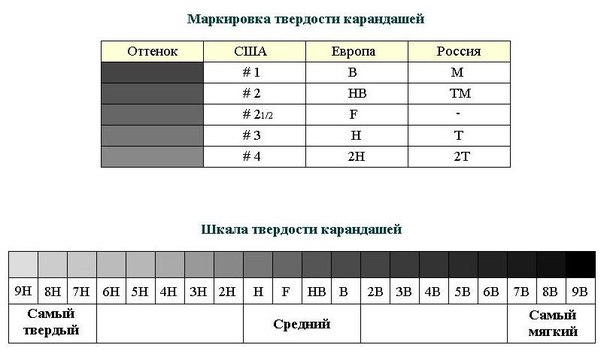


Таблица преобразования
Прочность
(Н / мм 2)
Твердость
(BHN)
по Виккерсу
Твердость
(HV)
Роквелл
Твердость
(HRB)
Роквелл
Твердость
(HRC)
285
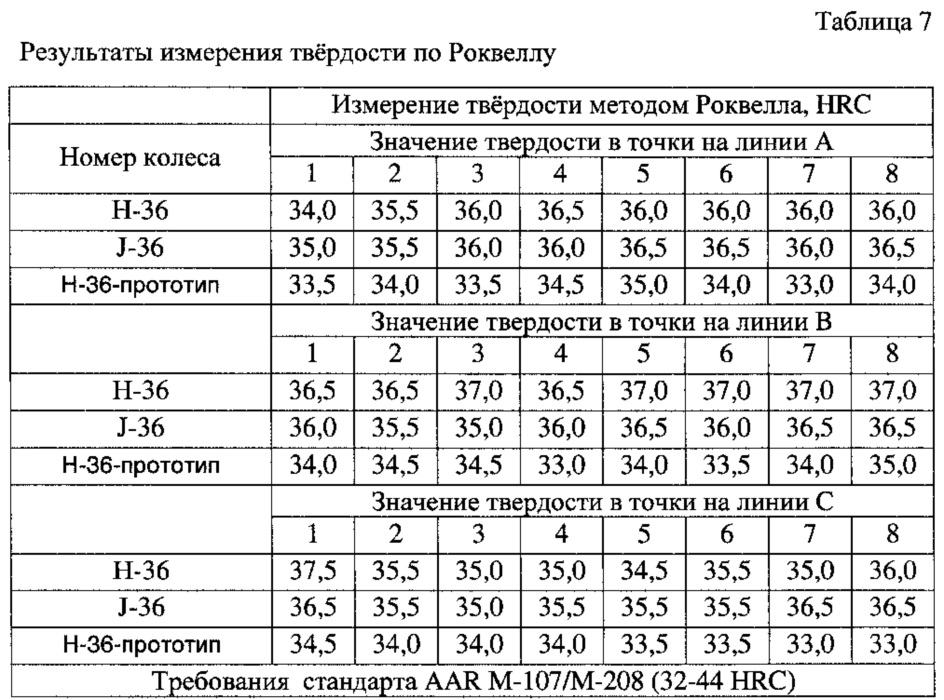
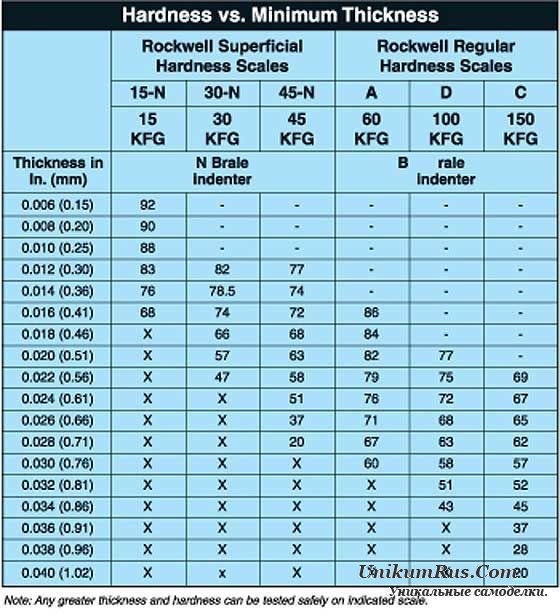




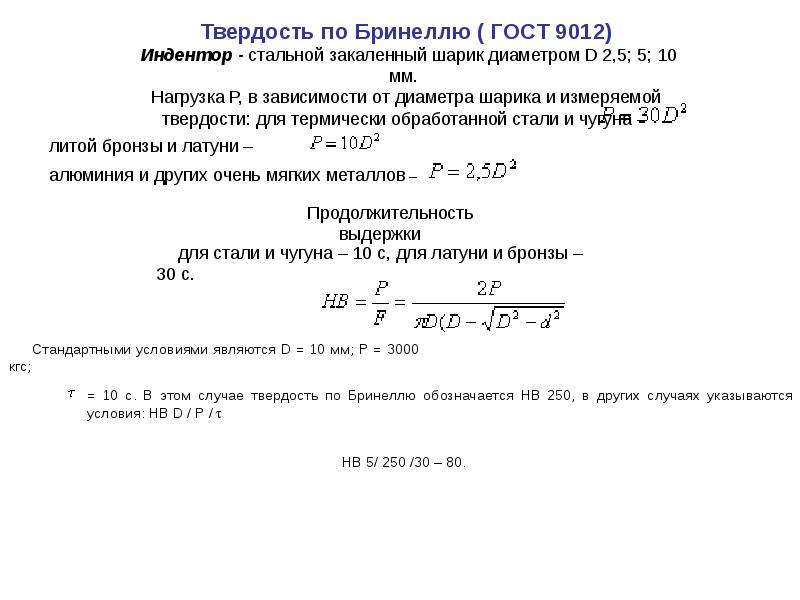

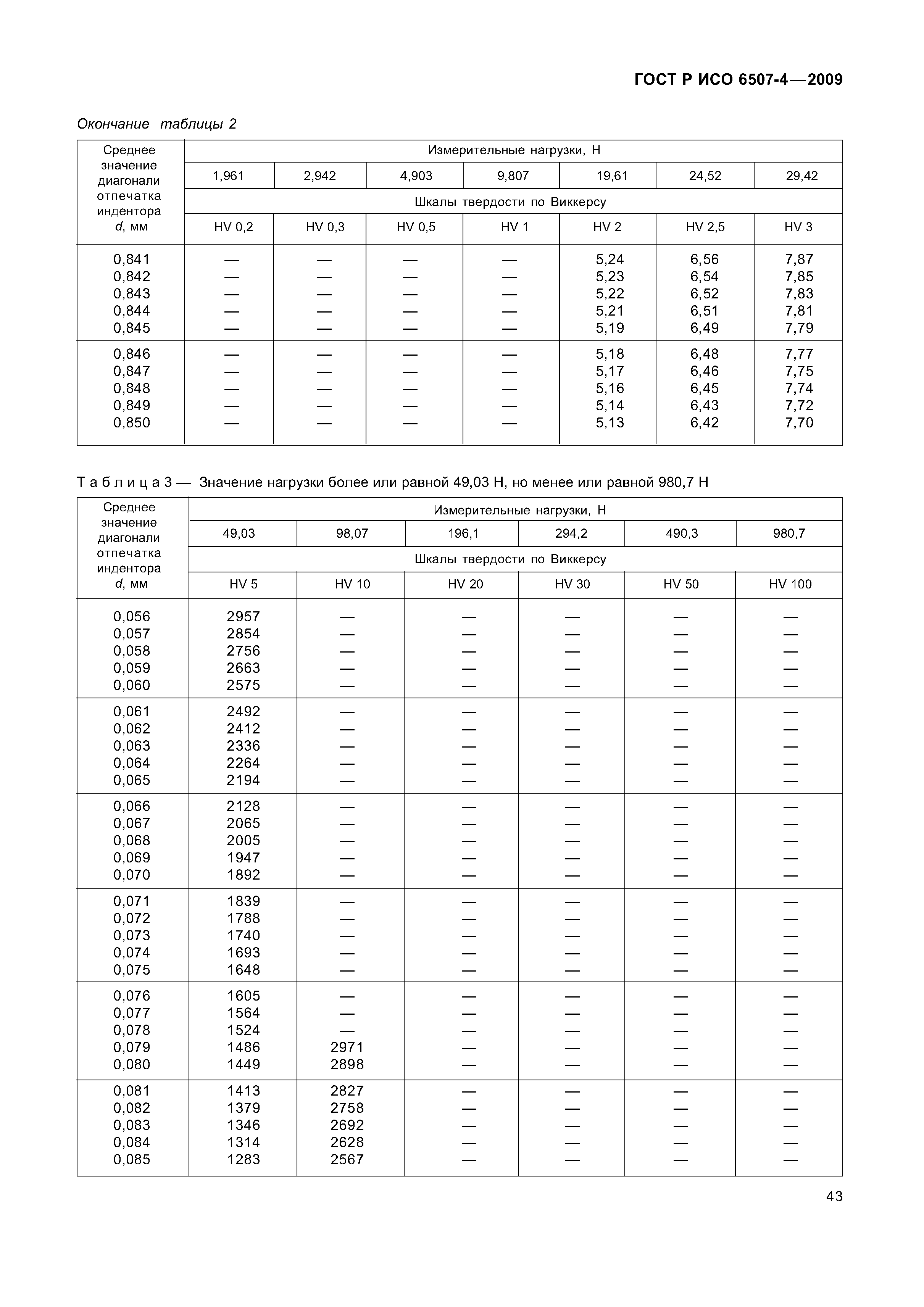
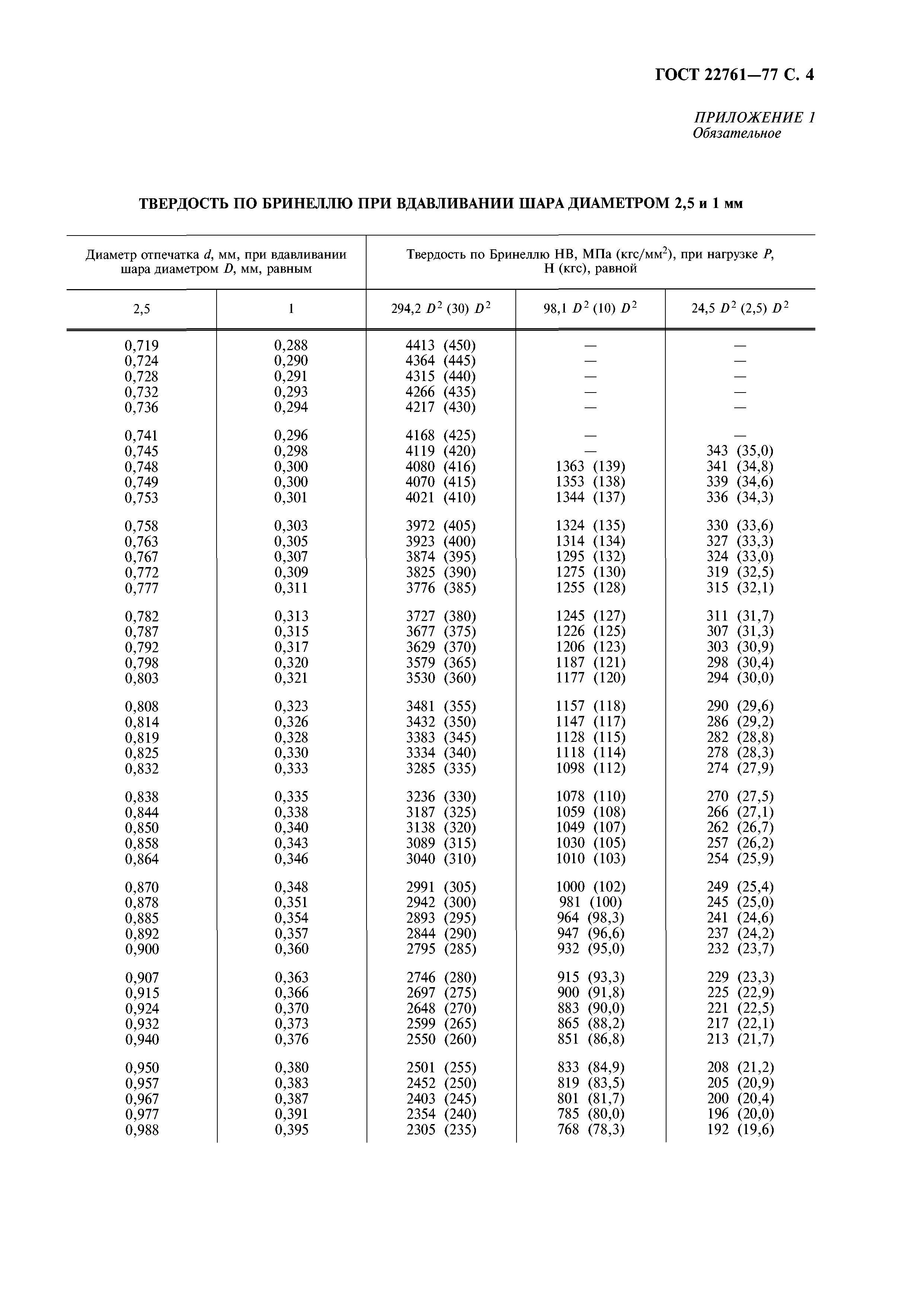

T, S Rm Н / мм2
HV
HB
HRC
250
8062
–
270
85
80,7
–
285
90
85. 2
–
305
95
90,2
–
320
100
100
335
105
99,8
–
350
110
105
105
115
109
–
380
120
114
–
–
00
119
–
415
130
124
–
430
135
62
000450
140
133
–
465
145
138
70
150
143
–
490
155
147
–
152
–
530
165
156
–
545
170
162
162
162
175
166
–
575
180
171
–
–
–
–
04 –
0
176
–
610
190
181
–
625
50004 5
–
9006 1 640
200
190
–
660
205
195
–
210
199
–
690
215
204
–
705
0
705
0
209
–
720
225
214
–
740
62 2304
0000009 – 755
235
223
–
770
240
228
20.
3
785
245
233
21,3
800
250
238
000 ,2 820
255
242
23,1
835
260
247
24.0
850
265
252
24,8
865
270 25
2562
900,6 880
275
261
26,4
900
280
266
27.1
915
285
271
27,8
930
290
276
000000 950
295
280
29,2
965
300
285
29.
8
995
310
295
31,0
–
0
176
–
610
190
181
–
625
5
–
640
200
190
–
660
205
195
–
210
199
–
690
215
204
–
705
0
705
0
209
–
720
225
214
–
740
62 2304
0000009755
235
223
–
770
240
228
20. 3
785
245
233
21,3
800
250
238
000820
255
242
23,1
835
260
247
24.0
850
265
252
24,8
865
270 25
2562
880
275
261
26,4
900
280
266
27.1
915
285
271
27,8
930
290
276
000950
295
280
29,2
965
300
285
29. 8
995
310
295
31,0
1030
5
5
5 32,2
1060
330
314
33,3
1095
340
5
1125
350
333
35,5
1115
360
342
1190
370
352
37,7
1220
380
361
38.8
1255
390
371
39,8
1290
400
38062
1320
410
390
41,8
1350
420
399
42. 7
1385
430
409
43,6
1420
440
418
0001455
450
428
45,3
1485
460
437
46.1
1520
470
447
46.9
1555
480
1595
490
(466)
48,4
1630
500
(475)
1665
510
(485)
49,8
1700
520
05
1740
530
(504)
51,1
1775
540
(51362)
04 (513620)7
1810
550
(523)
52,3
1845
560
900,0532
1880
570
(542)
53,6
1920
580
(551)
0004 90011955
590
(561)
54,7
1995
600
04 (570) 962 9620
2030
610
(580)
55,7
2070
620
620
2105
630
(599)
56,8
2145
640
04 (608)
2180
650
(618)
57,8
660
58. 3
670
58,8
680
59,2
59,2
59,7
700
60,1
720
61.0
740
61,8
760
62,5
62,5
63,3
800
64,0
820
64.7
840
65,3
860
65. 9
65.9
66,4
900
67,0
920
67.5
940
68,0
Макс нагрузка 1 кг
Предел прочности на разрыв, тыс. Фунтов на кв. Дюйм
Углубление
Диаметр
мм.
HBW
10/3000
HRC
HRB
HV
(диапазон HRC)
HV
(диапазон HRB)
HK
(диапазон HRC)
HK
(диапазон HRB)
Прокрутите вниз, чтобы просмотреть всю таблицу | |||||||||||||||||||||||||||||||||||||||||||||||||||||||||||||||||||||||||||||||||||||||||||||||||||
2. | 627 | 58,6 | 664 | 703 | 346.2 | ||||||||||||||||||||||||||||||||||||||||||||||||||||||||||||||||||||||||||||||||||||||||||||||
2,50 | 601 | 57,3 | 638 | 677 | 328. | ||||||||||||||||||||||||||||||||||||||||||||||||||||||||||||||||||||||||||||||||||||||||||||||
2,55 | 578 | 56,1 | 615 | 652 | 313. | ||||||||||||||||||||||||||||||||||||||||||||||||||||||||||||||||||||||||||||||||||||||||||||||
2,60 | 555 | 54,8 | 591 | 627 | 298. | ||||||||||||||||||||||||||||||||||||||||||||||||||||||||||||||||||||||||||||||||||||||||||||||
2,65 | 534 | 53,5 | 569 | 603 | 287. | ||||||||||||||||||||||||||||||||||||||||||||||||||||||||||||||||||||||||||||||||||||||||||||||
2,70 | 514 | 52,2 | 548 | 579 | 274. | ||||||||||||||||||||||||||||||||||||||||||||||||||||||||||||||||||||||||||||||||||||||||||||||
2,75 | 495 | 50,9 | 528 | 556 | 263. | ||||||||||||||||||||||||||||||||||||||||||||||||||||||||||||||||||||||||||||||||||||||||||||||
2,80 | 477 | 49,6 | 508 | 533 | 251. | ||||||||||||||||||||||||||||||||||||||||||||||||||||||||||||||||||||||||||||||||||||||||||||||
2,85 | 461 | 48,3 | 491 | 513 | 241. | ||||||||||||||||||||||||||||||||||||||||||||||||||||||||||||||||||||||||||||||||||||||||||||||
2,90 | 444 | 46,9 | 472 | 492 | 230. | ||||||||||||||||||||||||||||||||||||||||||||||||||||||||||||||||||||||||||||||||||||||||||||||
2,95 | 429 | 45,7 | 456 | 474 | 219. | ||||||||||||||||||||||||||||||||||||||||||||||||||||||||||||||||||||||||||||||||||||||||||||||
3,00 | 415 | 44,4 | 440 | 456 | 211. | ||||||||||||||||||||||||||||||||||||||||||||||||||||||||||||||||||||||||||||||||||||||||||||||
3,05 | 401 | 43,1 | 425 | 439 | 201. | ||||||||||||||||||||||||||||||||||||||||||||||||||||||||||||||||||||||||||||||||||||||||||||||
3,10 | 388 | 41,8 | 411 | 424 | 192. | ||||||||||||||||||||||||||||||||||||||||||||||||||||||||||||||||||||||||||||||||||||||||||||||
3,15 | 375 | 40,5 | 397 | 408 | 184. | ||||||||||||||||||||||||||||||||||||||||||||||||||||||||||||||||||||||||||||||||||||||||||||||
3,20 | 363 | 39,3 | 383 | 394 | 177. | ||||||||||||||||||||||||||||||||||||||||||||||||||||||||||||||||||||||||||||||||||||||||||||||
3,25 | 352 | 38,1 | 372 | 382 | 170. | ||||||||||||||||||||||||||||||||||||||||||||||||||||||||||||||||||||||||||||||||||||||||||||||
3,30 | 341 | 36,8 | 360 | 369 | 164. | ||||||||||||||||||||||||||||||||||||||||||||||||||||||||||||||||||||||||||||||||||||||||||||||
3,35 | 331 | 35,7 | 349 | 358 | 158. | ||||||||||||||||||||||||||||||||||||||||||||||||||||||||||||||||||||||||||||||||||||||||||||||
3,40 | 321 | 34,4 | 338 | 347 | 153. | ||||||||||||||||||||||||||||||||||||||||||||||||||||||||||||||||||||||||||||||||||||||||||||||
3,45 | 311 | 33,0 | 327 | 334 | 149. | ||||||||||||||||||||||||||||||||||||||||||||||||||||||||||||||||||||||||||||||||||||||||||||||
3,50 | 302 | 32,0 | 318 | 327 | 146. | ||||||||||||||||||||||||||||||||||||||||||||||||||||||||||||||||||||||||||||||||||||||||||||||
3,55 | 293 | 30,8 | 308 | 317 | 140. | ||||||||||||||||||||||||||||||||||||||||||||||||||||||||||||||||||||||||||||||||||||||||||||||
3,60 | 285 | 29,7 | 300 | 309 | 137. | ||||||||||||||||||||||||||||||||||||||||||||||||||||||||||||||||||||||||||||||||||||||||||||||
3,65 | 277 | 28,6 | 291 | 301 | 134. | ||||||||||||||||||||||||||||||||||||||||||||||||||||||||||||||||||||||||||||||||||||||||||||||
3,70 | 269 | 27,4 | 283 | 293 | 130. | ||||||||||||||||||||||||||||||||||||||||||||||||||||||||||||||||||||||||||||||||||||||||||||||
3,75 | 262 | 26,3 | 275 | 286 | 127. | ||||||||||||||||||||||||||||||||||||||||||||||||||||||||||||||||||||||||||||||||||||||||||||||
3,80 | 255 | 25,2 | 268 | 279 | 123. | ||||||||||||||||||||||||||||||||||||||||||||||||||||||||||||||||||||||||||||||||||||||||||||||
3,85 | 248 | 24,1 | 261 | 272 | 119. | ||||||||||||||||||||||||||||||||||||||||||||||||||||||||||||||||||||||||||||||||||||||||||||||
3,90 | 241 | 22,9 | 100 | 254 | 241 | 266 | 253 | 116. | |||||||||||||||||||||||||||||||||||||||||||||||||||||||||||||||||||||||||||||||||||||||||||
3,95 | 235 | 21,8 | 99 | 247 | 235 | 260 | 248 | 114. | |||||||||||||||||||||||||||||||||||||||||||||||||||||||||||||||||||||||||||||||||||||||||||
4,00 | 229 | 20,8 | 98 | 241 | 229 | 254 | 242 | 110. | |||||||||||||||||||||||||||||||||||||||||||||||||||||||||||||||||||||||||||||||||||||||||||
4,05 | 223 | 19,7 | 97 | 238 | 223 | 251 | 237 | 105. | |||||||||||||||||||||||||||||||||||||||||||||||||||||||||||||||||||||||||||||||||||||||||||
4,10 | 217 | 96 | 217 | 232 | 102. | ||||||||||||||||||||||||||||||||||||||||||||||||||||||||||||||||||||||||||||||||||||||||||||||
4,15 | 212 | 95 | 212 | 227 | 100. | ||||||||||||||||||||||||||||||||||||||||||||||||||||||||||||||||||||||||||||||||||||||||||||||
4,20 | 207 | 95 | 207 | 222 | 98. | ||||||||||||||||||||||||||||||||||||||||||||||||||||||||||||||||||||||||||||||||||||||||||||||
4,25 | 201 | 93 | 201 | 217 | 94. | ||||||||||||||||||||||||||||||||||||||||||||||||||||||||||||||||||||||||||||||||||||||||||||||
4,30 | 197 | 93 | 197 | 213 | 92. | ||||||||||||||||||||||||||||||||||||||||||||||||||||||||||||||||||||||||||||||||||||||||||||||
4,35 | 192 | 92 | 192 | 208 | 90. | ||||||||||||||||||||||||||||||||||||||||||||||||||||||||||||||||||||||||||||||||||||||||||||||
4,40 | 187 | 90 | 187 | 202 | 89. | ||||||||||||||||||||||||||||||||||||||||||||||||||||||||||||||||||||||||||||||||||||||||||||||
4,45 | 183 | 89 | 183 | 198 | 88. | ||||||||||||||||||||||||||||||||||||||||||||||||||||||||||||||||||||||||||||||||||||||||||||||
4,50 | 179 | 89 | 179 | 194 | 87. | ||||||||||||||||||||||||||||||||||||||||||||||||||||||||||||||||||||||||||||||||||||||||||||||
4,55 | 174 | 87 | 174 | 189 | 85. | ||||||||||||||||||||||||||||||||||||||||||||||||||||||||||||||||||||||||||||||||||||||||||||||
4,60 | 170 | 86 | 170 | 185 | 83. | ||||||||||||||||||||||||||||||||||||||||||||||||||||||||||||||||||||||||||||||||||||||||||||||
4,65 | 167 | 85 | 167 | 182 | 82. | ||||||||||||||||||||||||||||||||||||||||||||||||||||||||||||||||||||||||||||||||||||||||||||||
4,70 | 163 | 84 | 163 | 178 | 81. | ||||||||||||||||||||||||||||||||||||||||||||||||||||||||||||||||||||||||||||||||||||||||||||||
4,75 | 159 | 83 | 159 | 173 | 80. | ||||||||||||||||||||||||||||||||||||||||||||||||||||||||||||||||||||||||||||||||||||||||||||||
4,80 | 156 | 82 | 156 | 170 | 77. | ||||||||||||||||||||||||||||||||||||||||||||||||||||||||||||||||||||||||||||||||||||||||||||||
4,85 | 152 | 81 | 152 | 166 | 72. | ||||||||||||||||||||||||||||||||||||||||||||||||||||||||||||||||||||||||||||||||||||||||||||||
4,90 | 149 | 80 | 149 | 163 | 71. | ||||||||||||||||||||||||||||||||||||||||||||||||||||||||||||||||||||||||||||||||||||||||||||||
4,95 | 146 | 79 | 146 | 160 | 69. | ||||||||||||||||||||||||||||||||||||||||||||||||||||||||||||||||||||||||||||||||||||||||||||||
5,00 | 143 | 78 | 143 | 157 | 68. | ||||||||||||||||||||||||||||||||||||||||||||||||||||||||||||||||||||||||||||||||||||||||||||||
5,05 | 140 | 76 | 140 | 152 | 67. | ||||||||||||||||||||||||||||||||||||||||||||||||||||||||||||||||||||||||||||||||||||||||||||||
5,10 | 137 | 75 | 137 | 151 | 66. | ||||||||||||||||||||||||||||||||||||||||||||||||||||||||||||||||||||||||||||||||||||||||||||||
5,15 | 134 | 74 | 134 | 147 | 64. | ||||||||||||||||||||||||||||||||||||||||||||||||||||||||||||||||||||||||||||||||||||||||||||||
5,20 | 131 | 73 | 131 | 144 | 63. | ||||||||||||||||||||||||||||||||||||||||||||||||||||||||||||||||||||||||||||||||||||||||||||||
5,25 | 128 | 71 | 128 | 141 | 62. | ||||||||||||||||||||||||||||||||||||||||||||||||||||||||||||||||||||||||||||||||||||||||||||||
5,30 | 126 | 70 | 126 | 139 | 61. | ||||||||||||||||||||||||||||||||||||||||||||||||||||||||||||||||||||||||||||||||||||||||||||||
5,35 | 123 | 69 | 123 | 137 | 60. | ||||||||||||||||||||||||||||||||||||||||||||||||||||||||||||||||||||||||||||||||||||||||||||||
5,40 | 121 | 68 | 121 | 135 | 59. | ||||||||||||||||||||||||||||||||||||||||||||||||||||||||||||||||||||||||||||||||||||||||||||||
5,45 | 118 | 66 | 118 | 132 | 57.5 |
* Все преобразования основаны на ASTM E140-12bε1 и ASTM A370-13
Заявление об ограничении ответственности: Хотя информация, изложенная в данном документе, считается правильной, Scot Forge не дает никаких рекомендаций или не предлагает никаких гарантий в отношении предмета или его точности. Scot Forge прямо отказывается от всех гарантий, явных, подразумеваемых или иных, включая, помимо прочего, все гарантии коммерческой ценности, пригодности или пригодности для конкретной цели или применения.
Авторские права принадлежат компании Scot Forge, 2017, все права защищены.