Легированные инструментальные стали – Легированные инструментальные стали
alexxlab | 08.12.2019 | 0 | Разное
Легированные инструментальные стали
Легированные инструментальные стали получают на базе углеродистых инструментальных сталей путем легирования их хромом, вольфрамом, ванадием, марганцем, кремнием и другими элементами. Легирование приводит к большей устойчивости переохлажденного аустенита и большей прокаливаемости, чем у углеродистых инструментальных сталей. Эти стали отличаются также повышенной вязкостью, меньшей склонностью к деформациям и трещинообразованию при закалке. Из легированных инструментальных сталей марок 9ХС, ХВГ, Bl, XB5 и других изготавливают различные режущие инструменты, имеющие сложную конфигурацию.
Для получения массивного инструмента и инструмента сложной формы предназначена сталь 9ХС (0,95-1,25% С; 1,2-1,6% Is).
Стали марок ХВГ (0,9% С; 0,9-1,2% Сr; 1,2-1,6% W; 0,8-1,1% Мn) и ХГ относятся к малодеформирующимся. Их используют для изготовления калибров, длинных метчиков, бритвенных ножей и лезвий и другого инструмента, для которого весьма важно сохранение размеров в процессе термической обработки, а также для изготовления деталей точных приборов.
Сталь ХВ5 (1,25-1,50% С) называется алмазной, обладает исключительно высокой твердостью в закаленном состоянии (HRC 67-69). Применяется для изготовления фильер холодного волочения, отделочного инструмента, снимающего стружку с твердых материалов (белый чугун, стекло, камень).
Быстрорежущие стали
Быстрорежущие стали широко используют для изготовления режущего инструмента, обладающего большой твердостью и работающего при высоких скоростях резания. При обработке с большими скоростями резания твердых материалов и при снятии стружки большого сечения режущая кромка инструмента нагревается до высокой температуры. Поэтому режущий инструмент, работающий в тяжелых тепловых условиях, следует изготовлять из стали, обладающей красностойкостью, т.е. способностью сохранять высокую твердость при нагреве до высокой температуры (600…650° С). Для обеспечения красностойкости сталь легируют большим количеством вольфрама в сочетании с молибденом и ванадием. Кроме этих элементов все быстрорежущие стали легированы хромом (примерно 4%), а некоторые – кобальтом. Среднее содержание углерода во всех быстрорежущих сталях несколько меньше 1%.
Быстрорежущие стали (high speed steel) маркируют буквой Р (rapid – быстрый), выпускают следующих марок: Р6, Р9, Р12, Р18 (цифра в марке стали означает процент вольфрама – основного легирующего элемента).
Вольфрам – дефицитный и дорогой элемент, поэтому его содержание в быстрорежущей стали стремятся уменьшить. Частично вольфрам заменяют молибденом из расчета, что 1% молибдена оказывает такое же влияние на свойства быстрорежущей стали, как 1,5-1,6% вольфрама. Содержание молибдена в быстрорежущих сталях обычно не превышает 5%. Такое сочетание вольфрама и молибдена имеется в широко применяемой стали Р6М5.
Быстрорежущие стали условно разделяют на стали умеренной красностойкости и стали повышенной красностойкости. В первую группу входят стали, легированные вольфрамом и молибденом и с небольшим содержанием ванадия (1-2%): Р18, Р12, Р9, Р6М5. Эти стали сохраняют высокую твердость (не ниже HRC 60) при нагреве до 620°С.
В настоящее время основной маркой быстрорежущих сталей (80% от общего объема производства) является Р6М5. Для повышения эксплуатационных свойств сталь дополнительно легируют азотом (Р6АМ5).
В группу сталей повышенной теплостойкости входят стали с высоким
(> 2%) содержанием ванадия, а также стали, дополнительно легированные кобальтом (Р9К5, Р12ФЗ, Р18К5Ф2 и др.). Стали этой группы сохраняют высокую твердость при нагреве до 630.. .650°С.
Быстрорежущие стали по структуре в отожженном состоянии относятся к карбидному (ледебуритному) классу сталей. В их структуре имеется эвтектика (ледебурит), в состав которой входят карбидообразующие элементы – хром, вольфрам, ванадий, кобальт, молибден.
Эвтектика, которая располагается в виде сетки по границам зерен, снижает вязкость стали, поэтому литая быстрорежущая сталь отличается повышенной хрупкостью. При горячей обработке давлением (ковке) сетка эвтектики дробится и первичные (эвтектические) карбиды распределяются в структуре более равномерно.
Горячедеформированную быстрорежущую сталь подвергают отжигу при 840…860° С для снижения твердости, облегчения обрабатываемости резанием и подготовке структуры к закалке. Структура после отжига мелкозернистый сорбитообразный перлит, состоящий из феррита и мелких карбидов, и избыточные карбиды – вторичные и первичные. Твердость стали после отжига должна быть не более НВ 255-285.
В настоящее время все шире применяют быстрорежущие стали, полученные методом порошковой металлургии. В этих сталях карбидная фаза очень мелкая, что способствует более полному растворению карбидов в аустените и повышению теплостойкости. Основные порошковые стали, предложенные для замены сталей Р18 и Р6М5 – Р0М2ФЗ-МП, М6Ф1-МП, М6ФЗ-МП мало содержат дефицитного вольфрама. Несмотря на высокое содержание ванадия, стали хорошо шлифуются. Применяются и другие порошковые стали, например, Р6М5К5-МП и Р12МЗК8. Стойкость режущего инструмента из порошковых сталей по сравнению со стойкостью инструмента из аналогичных сталей обычного производства в 1,2-2 раза выше.
Инструмент, изготовленный из быстрорежущей стали, подвергают закалке и трехкратному отпуску (рис. 44, а).
Быстрорежущие стали обладают пониженной теплопроводностью, медленный или ступенчатый нагрев позволяет выровнять температуру по сечению инструмента и предупредить образование больших внутренних напряжений. При ступенчатом нагреве инструмент подогревают при 800…850°С. Для сложной формы инструмента применяют два подогрева: при 500°С и 800…850° С. Быстрый окончательный нагрев позволяет предупредить окисление и обезуглероживание стали. Выдержку при высокой температуре в интервале температур 1210…1290°С дают очень непродолжительную (10-12 с на каждый миллиметр диаметра или наименьшей толщины инструмента при нагреве в расплавленной соли).
Закаливают инструмент из быстрорежущей стали в масле. Для инструмента сложной формы применяют ступенчатую закалку с выдержкой при 450…500°С в течение 2-5 мин в соляной ванне для выравнивания температуры по сечению инструмента и дальнейшим охлаждением на воздухе.
Структура быстрорежущей стали после закалки состоит из высоколегированного мартенсита, содержащего 0,3-0,4% С, нерастворенных избыточных карбидов и остаточного аустенита.
Сохранение
в структуре закаленной стали большого
количества остаточного
аустенита объясняется тем, что аустенит
высоколегированный и
для него температура начала мартенситного
превращения М
Отпуск при 500…560°С приводит снова к повышению твердости до HRC 63-65. Такое повышение твердости обменяется выделением из мартенсита дисперсных специальных карбидов. К этому превращению добавляется также превращение остаточного аустенита. Высоколегированный остаточный аустенит достаточно устойчив при температурах отпуска до 500°С. В процессе выдержки при отпуске с температурой 550…570° С из аустенита выделяются в дисперсном виде специальные карбиды. Аустенит обедняется углеродом и легирующими элементами и становится менее устойчивым. В процессе охлаждения от температуры отпуска остаточный аустенит превращается в мартенсит (вторичная закалка). Превращение не заканчивается полностью при однократном отпуске. Для того, чтобы достигнуть почти полного превращения остаточного аустенита в мартенсит, необходимо двух-трехкратное повторение отпуска при 550…570° С с выдержкой при каждом отпуске 45-60 мин (рис. 44, а) . Следует отметить, что аустенит превращается в мартенсит не при нагревании и не в процессе выдержки, а во время охлаждения.
Цикл термической обработки быстрорежущей стали может быть сокращен, если сразу после закалки сталь обработать холодом при -75° С…-80° С. В этом случае вместо трехкратного отпуска назначают однократный отпуск (рис. 44, б).
Микроструктура стали после закалки и отпуска состоит из мартенсита и карбидов. Если температура отпуска или во время выдержки недостаточны (сталь недоотпущена), то в структуре сохраняется некоторое количество остаточного аустенита. При отпуске выше 600°С твердость быстрорежущей стали снижается в связи с распадом мартенсита и коагуляцией выделившихся карбидов.
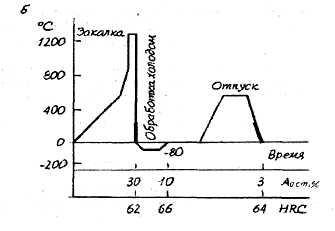
Рис. 44. Режимы термической обработки инструмента из быстрорежущей стали:
а – с трехкратным отпуском; б – с обработкой холодом
studfiles.net
Марки легированных инструментальных сталей, их применение в производстве
SolidIron.ru > Сталь > Какие бывают легированные инструментальные стали их марки и применение
Легированной инструментальной сталью называют сталь, в которую добавлены определённые химические элементы. За счёт легирования получилось расширить спектр применения нержавеющих металлов.
Это могут быть элементы:
- Вольфрама.
- Титана.
- Молибдена.
- Кобальта.
- Никеля.
- Хрома.
Это требуется для того, чтобы воздействовать на структуру и получить определённые свойства металла. За счёт процентных составляющих легирующих добавлений в составы металла, разделить сталь можно на такие типы, как:
- Низколегированные (меньше чем 2.5%).
- Среднелегированные (меньше 2.5-10%)
- Высоколегированные (больше 10).
Для низколегированного типа, как правило, добавляют соединения никеля, хрома и молибдена. Свойства данного типа стали даёт возможность уменьшить вес конструкций, увеличить эксплуатационные показатели итоговой детали и снизить затраты на металл, так как она обладает большим уровнем текучести.
В составе среднелегированных типах может быть такой элемент, как соединение вольфрама, молибдена, никеля, ванадия. С помощью термических и механических обработок, получается получить оптимальный уровень соотношения пластичности, прочности и вязкости. Данный тип стали незаменим в машиностроительных, судостроительных отраслях. Применяется для таких деталей, как свёрла, развёртки.
Высоколегированные типы стали, в которых в качестве основного элемента добавлены частицы хрома и никеля, имеют резистентные свойства к температурам, коррозийную стойкость, жаропрочность. Данный тип стали имеет свои особенные характеристики, которые достигнуты не только благодаря составу, но и с помощью последующей обработки.
к содержанию ↑Маркировка легированной инструментальной стали
На инструментальные легированные стали маркировка происходит с помощью цифровых и буквенных обозначений. Буквы говорят о каждом химическом элементе, который входит в состав, а цифра о процентном соотношении. Ниже приведён список добавления элементов и их расшифровка на маркировках.
- Cr(хрома) – Х.
- Ni(никеля) – Н.
- Mo(молибдена) – М.
- Si(кремния) – С.
- Mn(марганца) – Г.
- W(вольфрама) – В.
- Ti(титана) – Т.
- Al(алюминия) – Ю.
- Cu(меди) – Д.
- Nb(ниобия) – Б.
- Co(кобальта) – К.
Стоящая вначале марок цифра, показывает усреднённое количество углерода (когда цифра единственная, значит, показаны десятые доли %, когда 2 – сотые). В случаях, в которых поначалу указана литера, значит что углерод содержится в количестве 1% и выше. В некоторых случаях маркировка указывает добавленную вспомогательную русскую букву в начале марки:
- Быстрорежущая – Р.
- Электротехническая – Э.
- Автоматная – А.
- Шарикоподшипниковая – l.
- И т.д.
Совет: нет определённых универсальных обозначений для марок. В России – это будет ГОСТ, Европе – EN, Америке – Aisi, Германии – DIN.
Где применяют легированные инструментальные стали
Применяются марки легированных инструментальных сталей прямо пропорционально от типа сталей.
Y7, YА7
- Используются на производстве деревообрабатывающего инструмента.
- Пневмоинструмента небольшого размера.
- Зубил, обжимок, бойков.
- Кузнечного штампа. Игольной проволоки.
- Слесарного и монтажного инструмента. Молоток, кувалда, бородка, отвёртка, плоскогубцы, острогубцы, боковые кусачки, рыболовные крючки и пр.
Y8, Y8А, Y8Г, Y8ГА, Y9, Y9A
- Используются при производстве инструментов, что могут работать в ситуации, когда отсутствует разогрев режущих кромок. Сюда относится деревообработка, фрезы, зенковки, поковки, топоры, стамески, долота, пилы продольные и дисковые. Накатных роликов, плит и стержней для литья форм из оловянного и свинцового сплава, который находится под давлением.
- Слесарный и монтажный инструмент. Обжимка для заклёпки, корнера, бородка, отвёртка, острогубцы, боковые кусачки.
- Для калибра простой формы и пониженного класса точности. Холоднокатаная термообработанная лента, имеющая толщину 2.5-0.02 мм, предназначенная для производства плоской и витой пружины и пружинящей детали сложной конфигурации, клапана, щупа, берда, ламели двоильного ножа, конструкционных маленьких деталей, включая детали для часов.
Y10А, Y12А
Для сердечника
Y10, Y10A
Для игольных проволок.
Y10, Y10A, Y11, Y11A
- Чтобы производить инструменты, которые работают при условиях, которые не вызывают разогрев режущей кромки.
- Деревообработки. Ручной и поперечной столярной пилы, машинной столярной пилы, спирального свёрла.
- Штампа холодной штамповки маленького размера, без грубого перехода по сечению.
- Калибра простой формы и пониженного класса точности.
- Накатных роликов, напильников, слесарных шаберов и пр.
- Для напильников, шаберов холоднокатаных термообработанных лент, имеющих толщину 2.5-0.02 мм, что предназначенные для создания плоской и витой пружины и пружинящих деталей со сложными конфигурациями. Это клапан, щуп, берда, ламель, двоильный нож, конструкционная мелкая деталь, включая детали на часы.
Y12, Y12A
- Используются для ручных метчиков, напильников, слесарных шабер.
- Штампа для холодного штампования обрезных и вырубных маленьких габаритов и без перехода сечения, холодновысадочных пуансонов и штемпелей маленького размера, калибра несложной формы и пониженного класса точности.
Y13, Y13A
- Используется чтобы создать инструменты увеличенной стойкости к износу на среднем и увеличенном уровне давления, если нет разогрева режущей кромки.
- Напильник, бритвенное лезвие и нож, острых хирургических инструментов, шаберов, гравировальных инструментов.
Данные легированные инструментальные стали их марки и применение довольно популярны по всему миру. Покупать их стоит только у надёжного поставщика, только так можно быть уверенным в действительно качественном изделии.
solidiron.ru
Инструментальные легированные стали | Учебные материалы
Легированные стали предназначены для изготовления режущего и измерительного инструмента и имеют, по сравнению с углеродистыми инструментальными сталями, большую прокаливаемость, износостойкость и теплостойкость.
Стали для измерительных инструментов
Измерительные инструменты (плитки, калибры, шаблоны) должны сохранять свою форму и размеры в течение продолжительного времени. В них не должны совершаться самопроизвольные структурные превращения, вызывающие изменение размеров инструмента в процессе эксплуатации.
Коэффициент линейного расширения должен быть минимальным. Этими свойствами обладают стали с мартенситной структурой. Для изготовления измерительных инструментов используют стали марок Х, Х9, ХГ, Х12Ф1. Закалка проводится при температурах 850…870 0С в масле. Для устранения остаточного аустенита после закалки проводится обработка холодом при минус 70 0С, а затем низкий отпуск при 120…140 0С. Твердость после термообработки составляет 63…64 НRС.
Стали для режущих инструментов
Основными требованиями к режущему инструменту являются следующие:
- длительное время сохранять высокую твердость и износостойкость режущей кромки в условиях трения;
- иметь высокую теплостойкость (красностойкость), т.е. способность сохранять высокую твердость и режущую способность при продолжительном нагреве (устойчивость против отпуска при нагреве инструмента в процессе работы).
Режущий инструмент изготовляют из сталей, имеющих пониженную или повышенную прокаливаемость, или из быстрорежущих сталей.
К сталям повышенной прокаливаемости относятся легированные стали, содержащие до 5 % легирующих элементов, марок 9ХС, ХВСГ, 9Х5С.
Подобно углеродистым сталям они обладают низкой теплостойкостью – до 300 0С, но более высокой прокаливаемостью. Из них изготовляют инструменты для резания материалов невысокой прочности с небольшой скоростью: ручные сверла, развертки, плашки и др.
Закалку проводят с температуры 800…860 0С в масле, отпуск при 150…200 0С. Твердость составляет 61…66 НRС.
Быстрорежущие стали
К ним относятся высоколегированные стали, предназначенные для изготовления инструментов высокой производительности. Основное свойство этих сталей — высокая теплостойкость (красностойкость), т.е. сохранение мартенситной структуры и высокой твердости, прочности, износостойкости при повышенных температурах, возникающих в режущей кромке при резании с большой скоростью.
Теплостойкость обеспечивается введением большого количества вольфрама совместно с другими элементами: молибденом, хромом, ванадием.
Вольфрам и молибден в присутствии хрома связывают углерод в специальные труднокоагулируемые при отпуске карбиды типа М6С, МС и задерживают распад мартенсита. Выделение дисперсных карбидов, которое происходит при повышенных температурах отпуска (500…600 0С), вызывает дисперсионное твердение мартенсита. При отпуске ванадий, выделяясь в виде карбидов, усиливает дисперсионное твердение.
Увеличению теплостойкости способствует также кобальт. Он не образует карбидов, но, повышая энергию межатомных сил связи, затрудняет коагуляцию карбидов и увеличивает их дисперсность.
За счет комплексного легирования инструменты из быстрорежущей стали сохраняют высокую твердость до 640 0С и допускают в 2…4 раза более производительные режимы резания, чем инструменты из углеродистых и низколегированных сталей.
Быстрорежущие стали обозначаются буквой Р (“рапид” — скорость), после которой ставится цифра, показывающая содержание вольфрама в процентах. Далее указываются легирующие элементы и их содержание в %.
Быстрорежущие стали по эксплуатационным свойствам делятся на две группы:
- нормальной производительности;
- повышенной производительности.
К 1-й группе относятся стали марок Р9, Р18, Р12, Р9Ф5, Р6М3, Р6М5.
Они сохраняют твердость не ниже 58 НRС до температуры 620 0С, лучше обрабатываются давлением, резанием, имеют высокую прочность и вязкость.
Ко 2-й группе относятся стали, содержащие кобальт и повышенное количество ванадия: Р6М5К5, Р9М4К8, Р9К5, Р9К10, Р10К5Ф5, Р18К5Ф2. Они превосходят стали 1 группы по теплостойкости (630…640 0С), твердости (НRС ³ 64) и износостойкости, но уступают по прочности и пластичности. Эту группу сталей применяют для обработки высокопрочных сталей, коррозионно-стойких и жаропрочных сталей с аустенитной структурой, других труднообрабатываемых материалов.
Быстрорежущие стали относятся к карбидному (ледебуридному) классу. В структуре литой стали присутствует сложная эвтектика, напоминающая ледебурит и располагающаяся по границам зерен.
Для придания стали теплостойкости инструмент подвергают закалке и многократному отпуску (рисунок 51).
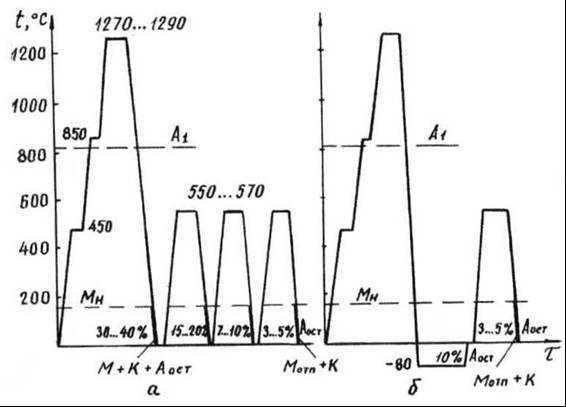
а — без обработки холодом; б — с обработкой холодом
Рисунок 51 — Схемы режимов термической обработки инструментов из быстрорежущих сталей
Температура закалки стали Р18 — 1220…1290 0С, Р6М5 — 1210…1230 0С. Высокие температуры необходимы для более полного растворения вторичных карбидов и получения высоколегированного аустенита.
Из-за низкой теплопроводности стали при закалке нагревают медленно с прогревами при 450 и 850 0С. Для уменьшения окисления и обезуглероживания нагрев производится в соляных ваннах (чаще ВаСl2).
Выдержка при температуре закалки должна обеспечить растворение в аустените части карбидов в пределах возможной их растворимости. Для получения более высокой твердости стали Р6М5 (63 НRС) и теплостойкости (59 НRС при 620 0С) выдержку при нагреве под закалку увеличивают на 25 %.
Для уменьшения деформации инструментов применяют ступенчатую закалку в расплавленных солях температурой 400…500 0С. Охлаждение ведется в масле (мелкие детали можно охлаждать на воздухе).
После закалки не достигается максимальная твердость сталей 6HRC, т. к. в структуре, кроме мартенсита и первичных карбидов, содержится 30…40 % остаточного аустенита (Мк ниже 0 0С). Он снижает механические свойства стали, ухудшает шлифуемость и стабильность размеров инструмента. Остаточный аустенит превращается в мартенсит при отпуске или обработке холодом.
Отпуск проводят при температуре 550…570 0С. В процессе выдержки при отпуске из М и Аост выделяются дисперсные карбиды М6С, МС. Аустенит обедняется углеродом и легирующими элементами, становится менее устойчивым и при охлаждении ниже Мн испытывает мартенситное превращение. Применяют двух, трех кратный отпуск с выдержкой по 1 ч и охлаждением на воздухе. При этом Аост снижается до 3…5 %. Обработка холодом сокращает цикл термической обработки. Структура — мартенсит отпуска и карбиды; твердость составляет 65 HRC.
dprm.ru
2.2 Инструментальные стали
Для режущих инструментов применяют быстрорежущие стали, а также, в небольших количествах, заэвтектоидные углеродистые стали с содержанием углерода 0,7-1,3% и суммарным содержанием легирующих элементов (кремния, марганца, хрома и вольфрама) от 1,0 до 3,0%.
2.2.1Углеродистые и легированные инструментальные стали.
Ранее других материалов для изготовления режущих инструментов начали применять углеродистые инструментальные стали марок У7, У7А…У13, У13А. Помимо железа и углерода, эти стали содержат 0,2…0,4% марганца. Инструменты из углеродистых сталей обладают достаточной твердостью при комнатной температуре, но теплостойкость их невелика, так как при сравнительно невысоких температурах (200…250С) их твердость резко уменьшается.
Легированные инструментальные стали, по своему химическому составу, отличаются от углеродистых повышенным содержанием кремния или марганца, или наличием одного либо нескольких легирующих элементов: хрома, никеля, вольфрама, ванадия, кобальта, молибдена. Для режущих инструментов используются низколегированные стали марок 9ХФ, 11ХФ, 13Х, В2Ф, ХВ4, ХВСГ, ХВГ, 9ХС и др. Эти стали обладают более высокими технологическими свойствами – лучшей закаливаемостью и прокаливаемостью, меньшей склонности к короблению, но теплостойкость их равна 350…400С и поэтому они используются для изготовления ручных инструментов (разверток) или инструментов, предназначенных для обработки на станках с низкими скоростями резания (мелкие сверла, метчики).
Следует отметить, что за последние 15-20 лет существенных изменений этих марок не произошло, однако наблюдается устойчивая тенденция снижения их доли в общем объеме используемых инструментальных материалов.
2.2.2 Быстрорежущие стали.
В настоящее время быстрорежущие стали являются основным материалом для изготовления режущего инструмента, несмотря на то, что инструмент из твердого сплава, керамики и СТМ обеспечивает более высокую производительность обработки.
Широкое использование быстрорежущих сталей для изготовления сложнопрофильных инструментов определяется сочетанием высоких значений твердости (до HRC68) и теплостойкости (600-650С) при высоком уровне хрупкой прочности и вязкости, значительно превышающих соответствующие значения для твердых сплавов. Кроме того, быстрорежущие стали обладают достаточно высокой технологичностью, так как хорошо обрабатываются давлением и резанием в отожженном состоянии.
В обозначении быстрорежущей стали буква Р означает, что сталь быстрорежущая, а следующая за буквой цифра – содержание средней массовой доли вольфрама в %. Следующие буквы обозначают: М – молибден, Ф – ванадий, К – кобальт, А – азот. Цифры, следующие за буквами, означают их среднюю массовую долю в %. Содержание массовой доли азота составляет 0,05-0,1%.
Современные быстрорежущие стали можно разделить на три группы: нормальной, повышенной и высокой теплостойкости.
К сталям нормальной теплостойкости относятся вольфрамовая Р18 и вольфрамомолибденовая Р6М5 стали (табл. 2.2). Эти стали имеют твердость в закаленном состоянии 63…64 HRC, предел прочности при изгибе 2900…3400Мпа, ударную вязкость 2,7…4,8Дж/м2 и теплостойкость 600…620С. Указанные марки стали получили наиболее широкое распространение при изготовлении режущих инструментов. Объем производства стали Р6М5 достигает 80% от всего объема выпуска быстрорежущей стали. Она используется при обработке конструкционных сталей, чугунов, цветных металлов, пластмасс.
Стали повышенной теплостойкости характеризуются повышенным содержанием углерода, ванадия и кобальта.
Среди ванадиевых сталей наибольшее применение получила марка Р6М5Ф3.
Наряду с высокой износостойкостью, ванадиевые стали
обладают плохой шлифуемостью из-за присутствия карбидов ванадия (VC), так как твердость последних не уступает твердости зерен электрокорундового шлифовального круга (Al2O3). Обрабатываемость при шлифовании – «шлифуемость», – это важнейшее технологическое свойство, которое определяет не только особенности при изготовлении инструментов, но и при его эксплуатации (переточках).
Таблица 2.2Химический состав быстрорежущих сталей
Марка стали | Массовая доля, % | ||||||
Углерод | Хром | Вольфрам | Ванадий | Кобальт | Молибден | Азот | |
Стали нормальной теплостойкости | |||||||
Р18 | 0,73-0,83 | 3,80-4,40 | 17,00-18,50 | 1,00-1,40 | н.б. 0,50 | н.б. 1,00 | – |
Р6М5 | 0,82-0,90 | 3,80-4,40 | 5,50-6,50 | 1,70-2,10 | н.б. 0,50 | 4,80-5,30 | – |
Стали повышенной теплостойкости | |||||||
11РЗАМ3Ф2 | 1,02-1,12 | 3,80-4,30 | 2,50-3,30 | 2,30-2,70 | н.б. 0,50 | 2,50-3,00 | 0,05-0,10 |
Р6М5Ф3 | 0,95-1,05 | 3,80-4,30 | 5,70-6,70 | 2,30-2,70 | н.б. 0,50 | 4,80-5,30 | – |
Р12Ф3 | 0,95-1,05 | 3,80-4,30 | 12,0-13,0 | 2,50-3,00 | н.б. 0,50 | н.б. 0,50 | – |
Р18К5Ф2 | 0,85-0,95 | 3,80-4,40 | 17,0-18,50 | 1,80-2,20 | 4,70-5,20 | н.б. 1,00 | – |
Р9К5 | 0,90-1,0 | 3,80-4,40 | 9,00-10,00 | 2,30-2,70 | 5,00-6,00 | н.б. 1,00 | – |
Р6М5К5 | 0,94-0,92 | 3,80-4,30 | 5,70-6,70 | 1,70-2,10 | 4,70-5,20 | 4,80-5,30 | – |
Р9М4К8 | 1,0-1,10 | 3,00-3,60 | 8,50-9,50 | 2,30-2,70 | 7,50-8,50 | 3,80-4,30 | – |
Р2АМ9К5 | 1,0-1,10 | 3,80-4,40 | 1,50-2,00 | 1,70-2,10 | 4,70-5,20 | 8,00-9,00 | 0,05-1,10 |
Стали высокой теплостойкости | |||||||
В11М7К23 | 0,10 | – | 11,00 | 0,50 | 23,00 | 7,00 | – |
В14М7К25 | 0,10 | – | 14,00 | 0,50 | 25,00 | 7,00 | – |
3В20К20Х4ф | 0,25 | 4,00 | 20,00 | 1,00 | 20,00 | – | – |
По шлифуемости быстрорежущие стали можно разделить на 4 группы:
Группа 1 Содержание ванадия до 1,4% и относительная шлифуемость 0,9-1 (за единицу принята «обрабатываемость при шлифовании» стали Р18, обладающая наилучшей шлифуемостью).
Группа 2 Содержание ванадия 1,7-2,2%, относительная шлифуемость 0,5- 0,95, в эту группу, в частности, входят стали Р6М5, Р6М5К5, Р2АМ9К5 и др.
Группа 3 Содержание ванадия 2,3-3,3%, относительная шлифуемость 0,3-0,5 (11РЗАМ3Ф2, Р6М5Ф3, Р12Ф3, Р9, Р9М4К8 и др.)
Группа 4 Содержание ванадия более 4%, относительная шлифуемость 0,2-0,3 (Р12Ф4К5 и др.).
Порошковые быстрорежущие стали, независимо от содержания ванадия, относятся к группам 1 и 2 т.е. обладают хорошей шлифуемостью.
Стали с пониженной шлифуемостью склонны к прижогам, т.е. к изменению структуры приповерхностных слоев стали после шлифования или заточки, появлению вторичной закалки или зон вторичного отпуска с пониженной твердостью.
Следствием прижогов может быть значительное снижение стойкости инструмента.
Однако, проблема «шлифуемости» высокованадиевых быстрорежущих сталей, успешно решается если при заточке и доводке режущих инструментов применяются абразивные круги с зернами из СТМ на основе кубического нитрида бора (КНБ).
Ванадиевые быстрорежущие стали находят применение для инструментов несложных форм при чистовых и получистовых условиях резания для обработки материалов, обладающих повышенными абразивными свойствами.
Среди кобальтовых сталей наибольшее применение нашли марки Р6М5К5, Р9М4К8, Р18К5Ф2, Р9К5, Р2АМ9К5 и др. Введение кобальта в состав быстрорежущей стали наиболее значительно повышает ее твердость (до 66-68 HRC) и теплостойкость (до 640-650С). Кроме того, повышается теплопроводность стали, так как кобальт является единственным легирующим элементом, приводящим к такому эффекту.
Это дает возможность использовать их для обработки жаропрочных и нержавеющих сталей и сплавов, а также конструкционных сталей повышенной прочности. Период стойкости инструментов из таких сталей в 3-5 раз выше, чем из сталей Р18, Р6М5.
Стали высокой теплостойкости характеризуются пониженным содержанием углерода, но весьма большим количеством легирующих элементов – В11М7К23, В14М7К25, 3В20К20Х4Ф. Они имеют твердость 69…70 HRC и теплостойкость 700…720С. Наиболее рациональная область их использования – резание труднообрабатываемых материалов и титановых сплавов. В последнем случае период стойкости инструментов в 60 раз выше, чем из стали Р18, и в 8-15 раз выше, чем из твердого сплава ВК8.
Значительными недостатками этих сталей является их низкая прочность при изгибе (не выше 2400 МПа) и низкая обрабатываемость резанием в отожженном состоянии (38-40 HRC) при изготовлении инструмента.
В связи со все более возрастающей дефицитностью вольфрама и молибдена – основных легирующих элементов, используемых при производстве быстрорежущей стали, все большее применение находят экономнолегированные марки. Среди сталей этого типа наибольшее применение получила сталь 11Р3АМ3Ф2, которая используется при производстве инструмента, так как обладает достаточно высокими показателями по твердости (HRC 63-64), прочности (и-3400 МПа) и теплостойкости (до 620С).
Экономно легированные стали
Сталь 11Р3АМ3Ф2 технологична в металлургическом производстве, однако, из-за худшей шлифуемости ее применение ограничено инструментами простой формы, не требующими больших объемов абразивной обработки (пилы по металлу, резцы и т.п.).
Порошковые быстрорежущие стали
Наиболее эффективные возможности повышения качества быстрорежущей стали, ее эксплуатационных свойств, и создания новых режущих материалов появились при использовании порошковой металлургии.
Порошковая быстрорежущая сталь характеризуется однородной мелкозернистой структурой, равномерным распределением карбидной фазы, пониженной деформируемостью в процессе термической обработки, хорошей шлифуемостью, более высокими технологическими и механическими свойствами, чем сталь аналогичных марок, полученных по традиционной технологии. Технологическая схема получения порошковых быстрорежущих сталей следующая: газовое распыление в порошок жидкой струи быстрорежущей стали, засыпка и дегазация порошка в цилиндрический контейнер, нагрев и ковка (или прокатка) контейнеров в прутки, окончательная резцовая обдирка остатков контейнера с поверхности прутков. Основным преимуществом порошковой технологии является резкое снижение размеров карбидов, образующихся при кристаллизации слитка в изложнице. Таким образом порошинка, полученная газовым распылением, и является микрослитком в котором не образуются крупные карбиды.
Новая технология позволяет существенно изменить схему легирования с целью направленного повышения тех или иных эксплуатационных характеристик, определяющих стойкость инструмента.
Основные примеры разработки новых составов порошковой быстрорежущей стали сводятся к возможности введения в состав до 7% ванадия и значительного, в связи с этим, повышения износостойкости без ухудшения шлифуемости. А также введение углерода с «пересыщением» до 1,7%, позволяющего получить значительное количество карбидов ванадия и высокую вторичную твердость после закалки с отпуском. В Украине выпускают ряд марок порошковой стали: (Р7М2Ф6-МП, Р6М5Ф3-МП, Р9М2Ф6К5-МП, Р12МФ5-МП и др. ГОСТ 28369-89).
Технология порошковой металлургии также используется для получения карбидостали, которая по своим свойствам может быть классифицирована как промежуточная между быстрорежущей сталью и твердыми сплавами.
Карбидосталь отличается от обычной быстрорежущей стали высоким содержанием карбидной фазы (в основном карбидов титана), что достигается путем смешивания порошка быстрорежущей стали и мелкодисперсных частиц карбида титана. Содержание TiC в карбидостали составляет 20%. Пластическим деформированием спрессованного порошка получают заготовки простой формы. В отожженном состоянии твердость карбидостали составляет HRC 40-44, а после закалки и отпуска HRC 68-70.
При использовании в качестве материала режущего инструмента карбидосталь обеспечивает повышение стойкости в 1,5-2 раза по сравнению с аналогичными марками обычной технологии производства. В ряде случаев карбидосталь является полноценным заменителем твердых сплавов, особенно при изготовлении формообразующих инструментов (деформирующие протяжки).
studfiles.net
34.Инструментальные легированные стали. Общая характеристика, примеры, применение.
Элементы, специально вводимые в сталь в определенных концентрациях с целью изменения ее строения и свойств, называются легирующими элементами, а стали – легированными. Легирующие элементы изменяют механические (прочность, пластичность), физические, эксплуатационные и химические свойства стали.
По отношению к углероду легирующие элементы разделяются на две группы:
1) элементы, образующие с углеродом устойчивые химические соединения – карбиды (хром, марганец, вольфрам, ванадий, титан, молибден)
2) элементы, не образующие в стали карбидов и входящие в твердый раствор – феррит (никель, кремний, кобальт, алюминий, медь).
Содержание легирующих элементов в сталях может изменяться в очень широких пределах. Сталь считают легированной хромом или никелем, если содержание этих элементов составляет 1 % или более. При содержании ванадия, молибдена, титана, ниобия и других элементов более 0,1-0,5 % стали считают легированными этими элементами. Сталь является легированной и в том случае, если в ней содержатся только элементы, характерные для углеродистой стали, марганец или кремний, а их количество должно превышать 1 %.
Для обозначения легирующих элементов приняты следующие буквы: Х- хром, Н – никель, Г – марганец, С – кремний, В – вольфрам, М -молибден, Ф – ванадий, К -кобальт, Т – титан, Ю – алюминий, Д – медь, П – фосфор, Р – бор, Б – ниобий, А -азот, Е – селен, Ц – цирконий. Марка стали обозначается сочетанием букв и цифр. Для инструментальных марок стали первые цифры показывают среднее содержание углерода в десятых долях процента, буквы – наличие соответствующих элементов, а цифры, следующие за буквами, – процентное содержание этих компонентов в стали. Если после какой-то буквы отсутствует цифра, то это значит, что сталь содержит данный элемент в количестве до 1,5 %. Если же в инструментальной легированной стали содержание углерода составляет около 1.0%, то соответствующую цифру в начале ее наименования обычно не указывают. Приведем примеры: сталь 4Х2В5МФ имеет содержание C 0.3 – 0.4%, Cr 2.2 – 3.0%, W 4.5 – 5.5%, Mo 0.6 – 0.9%, V 0.6 – 0.9%, а сталь ХВГ – C 0.9 – 1.05%, Cr 0.9 – 1.2%, W 1.2 – 1.6%, Mn 0.8 – 1.1%.
Инструментальная сталь идет для изготовления различного инструмента: ударно-штампового, измерительного, режущего. Она имеет ряд преимуществ перед инструментальной углеродистой сталью. Штампы из углеродистой стали обладают высокой твердостью и прочностью, но плохо сопротивляются удару. Метчики, развертки и другие длинные и тонкие инструменты из углеродистой стали при закалке получаются хрупкими, они ненадежны в работе и часто ломаются.
Важнейшие легирующие примеси инструментальной легированной стали: хром, вольфрам, молибден, марганец, кремний. Содержание углерода в этой стали может быть ниже, чем в углеродистой, и колеблется от 0,3 до 2,3%. Условия работы отдельных видов инструментов различны, поэтому для каждого вида инструмента необходимо применять сталь, подходящую по своим качествам к данным условиям работы.
Сталь для ударно-штампового и измерительного инструмента.
Для нагруженных штампов, деформирующих металл в холодном состоянии, применяют высоколегированную хромовую сталь (х12), отличающуюся после закалки многократного высокого отпуска весьма высокой твердостью и износоустойчивостью. Примером стали для тяжелонагруженных штампов, деформирующих металл в горячем состоянии (горячая штамповка), может служить сталь марок 5ХНМ и 5ХГМ (для небольших штампов) После закалки и высокого отпуска подобная сталь обладает повышенной прочностью, вязкостью и износоустойчивостью при высоких температурах.
Низколегированная сталь для режущего инструмента.
Низколегированная сталь по своей режущей способности существенно не отличается от углеродистой стали и применяется при небольших скоростях резания, так как понижение твердости стали начинается уже при температуре 200-220С. Однако эта сталь имеет меньшую критическую скорость закалки по сравнению с углеродистой сталью и поэтому обладает более высокой прокаливаемостью, что позволяет получить структуру мартенсита в более крупных сечениях инструмента; кроме того, она менее хрупка. В качестве основного легирующего элемента для стали этих марок применяют хром, а также вольфрам. Наиболее распространенные марки стали для режущих инструментов являются: 9ХС, ХВГ и В1.
Быстрорежущая сталь.
Самые распространенные – Р18,Р6М3. Наиболее массовое употребление получила марка Р6М5.Это высоколегированная инструментальная сталь, обладающая красностойкостью, то есть не теряющая режущих свойств при нагреве до 600-700С. Она способна резать металл со скоростями в 3-4 раза выше допустимых для углеродистых и низколегированных инструментальных сталей.
studfiles.net
Лекция 10. Легированные конструкционные стали. Инструментальные легированные стали. Конструкционные стали
Конструкционные стали должны обладать высокой конструктивной прочностью, обеспечивать длительную и надежную работу конструкции в условиях эксплуатации.
Материалы, идущие на изготовление конструктивных элементов, деталей машин и механизмов, должны наряду с высокой прочностью и пластичностью хорошо сопротивляться ударным нагрузкам, обладать запасом вязкости. При знакопеременных нагрузках должны обладать высоким сопротивлением усталости, а при трении – сопротивлением износу. Во многих случаях необходимо сопротивление коррозии, сопротивление хрупкому разрушению и т.д.
Помимо высокой надежности и конструктивной прочности конструкционные материалы должны иметь высокие технологические свойства – хорошие литейные свойства, обрабатываемость давлением, резанием, хорошую свариваемость.
Строительные стали
К строительным относятся конструкционные стали, применяемые для изготовления металлических конструкций и сооружений, для армирования железобетона.
К низколегированным строительным сталям относятся низкоуглеродистые свариваемые стали, содержащие недорогие и недефицитные легирующие элементы и обладающие повышенной прочностью и пониженной склонностью к хрупким разрушениям по сравнению с углеродистыми сталями. Применение низколегированных сталей позволяет уменьшить массу строительных конструкций, получить экономию металла, повысить надежность конструкций. Низколегированные строительные стали содержат до 0,25% углерода, 2-3% легирующих элементов (Cr, Si, Mn), микродобавки (Y, Nb, Ti, Al, N) и др.
Требования к сталям:
– определенное сочетание прочностных и пластических свойств,
– малая склонность к хрупким разрушениям (низкий порог хладноломкости)
– коррозионная стойкость,
– хорошая свариваемость
– обработка резанием.
Строительные стали для металлических конструкций подразделяются по категориям прочности на: стали нормальной прочности, повышенной прочности и высокой прочности. Каждый класс прочности характеризуется минимально гарантированными значениями временного сопротивления разрыву и предела текучести.
Временное сопротивление при растяжении и предел текучести являются основными расчетными характеристиками при проектировании металлоконструкций и сооружений. От их значений зависит сечение элементов конструкций, а, следовательно, их масса.
Не менее важным критерием, определяющим эксплуатационную надежность строительных конструкций, является их склонность к хрупким разрушениям (порог хладноломкости). По хладостойкости строительные стали делят на стали без гарантированной хладостойкости, стали хладостойкие до -40ºС и стали для эксплуатации конструкций ниже -40 ºС.
Детали строительных конструкций обычно соединяют сваркой, поэтому основным требованием к строительным сталям является хорошая свариваемость. Стали этого класса не должны давать горячих и холодных трещин. Склонность к образованию трещин зависит от содержания углерода. Горячие трещины образуются в сварном шве в период кристаллизации. Образованию горячих трещин способствует расширение интервала кристаллизации металла шва. Интервал кристаллизации растет с увеличением содержания углерода. Металл шва и около шовной зоны нагревается выше критических точек. При охлаждении протекает процесс распада аустенита, сопровождающийся объёмными изменениями. Чем выше содержание углерода, тем выше объёмные изменения, тем больше опасность образования холодных трещин. Поэтому стали, используемые для изготовления строительных конструкций, не должны содержать более 0,25%С и устанавливается тем ниже, чем более легирована сталь.
Строительные стали могут быть углеродистыми и низкоуглеродистыми низколегированными.
Низкоуглеродистые низколегированные стали обычной прочности в горячекатаном или нормализованном состоянии применяют для строительных конструкций, армирования железобетона, магистральных нефте- и газопроводов. Стали поставляются в горячекатаном состоянии с феррито-перлитной структурой. Прочностные свойства этих сталей обеспечиваются на стадии производства.
К низколегированным строительным сталям повышенной прочности относятся стали марок 14Г2, 17ГС, 9Г2С и др. Введение в сталь небольших добавок ванадия и ниобия обеспечивает дополнительное упрочнение за счет образования карбонитридов этих элементов и измельчения зерна. К сталям такого типа (стали повышенной прочности) относятся стали марок 14Г2АФ, 17Г2АФБ, и другие с σ0,2 = 450 МПа после нормализации. Такие стали используются в виде сортового проката для изготовления конструкций без дополнительной термической обработки. В эту же группу входят атмосферостойкие стали, в состав которых вводят в малом количестве Cu, P, Ni, Cr, Si. Они образуют на поверхности продукты коррозии с высокой плотностью и прочностью, обладающие лучшим сцеплением с поверхностью, чем антикоррозийные покрытия (10ХНДП, 15ХСНД).
Строительные стали высокой прочности марок 12Х2СМФ, 12ХГН2МФБАЮ применяются в особо ответственных конструкциях, в которых прочность достигается карбонитридным упрочнением, термическим упрочнением и контролируемой прокаткой. Термическое упрочнение этих сталей заключается в закалке от 850 – 9200С и высоком отпуске при 600 – 6800С. После этого получается высокодисперсная смесь продуктов распада мартенсита и нижнего бейнита. Прочность после такой обработки достигает σв = 700МПа.
Присутствие частиц карбонитридов и нитридов способствует заметному измельчению зерна. Стали с карбонитридным упрочнением применяют для ответственных металлоконструкций, пригодных для эксплуатации при температурах ниже – 400С, а также для магистральных газопроводных труб северного исполнения.
studfiles.net
Инструментальная легированная сталь – Большая Энциклопедия Нефти и Газа, статья, страница 1
Инструментальная легированная сталь
Cтраница 1
Инструментальные легированные стали ( ГОСТ 5950 – 73) имеют повышенную по сравнению с углеродистыми сталями теплостойкость ( 250 – 300 С), что позволяет повысить скорость резания в 1 2 – 1 4 раза. Наиболее широко из этой группы сталей применяются: 9ХС – сверла, развертки, метчики, плашки, гребенки, фрезы; ХВГ – протяжки, длинные метчики, плашки. [1]
Инструментальные легированные стали применяют для изготовления режущего инструмента: резцов, фрез, долбяков и др., а также мерительного инструмента. Особое место в этой группе занимают быстрорежущие стали, обладающие способностью сохранять режущие свойства при больших скоростях обработки и высоких температурах – стали марок Р9 и Р18; буква Р обозначает, что сталь относится к группе быстрорежущих, а последующие цифры – процент содержания вольфрама. [2]
Инструментальные легированные стали ( повышенной прокаливаемости) закаливают, как правило, в масле, что уменьшает опасность образования трещин, деформации и коробления. Это имеет важное значение для инструментов сложной формы. Стали с небольшим содержанием легирующих элементов, так же как и углеродистые стали, подвергают закалке в воде. [3]
Инструментальные легированные стали применяют для изготовления трех основных групп инструмента: режущего, измерительного и штампов. К группе легированных инструментальных сталей относится быстрорежущая сталь, обладающая красностойкостью, способностью сохранять режущие свойства при нагреве до 600 – 700 С. Эта сталь может резать металл со скоростями в 5 – 4 раза выше допускаемых для углеродистых инструментальных сталей. [4]
Инструментальные легированные стали применяют для изготовления трех основных групп инструмента: режущего, измерительного и штампов. Эта сталь может резать металл со скоростями, в 3 – 4 раза превышающими допускаемые для углеродистых инструментальных сталей. [5]
Инструментальные легированные стали получают путем введения в инструментальную углеродистую сталь легирующих элементов – хрома, вольфрама, молибдена, ванадия и др. После соответствующей термической обработки эти стали выдерживают в процессе резания, нагрев до температуры 250 – 300 С, что позволяет инструменту, изготовленному из этих сталей, работать со скоростью резания, примерно в 1 2 – 1 4 раза большей по сравнению со скоростью резания инструментов из инструментальной углеродистой стали. [6]
Инструментальные легированные стали обозначаются цифрой, характеризующей массовое содержание углерода в десятых долях процента ( если цифра отсутствует, содержание углерода 1 %), за которой следуют буквы, соответствующие легирующим элементам ( Г – марганец, X -хром, С – кремний, В – вольфрам, Ф – ванадий), и цифры, обозначающие содержание элемента в процентах. Инструментальные легированные стали глубокой прокаливаемости марок 9ХС, ХВСГ, X, 1IX, ХВГ отличаются малыми деформациями при термической обработке. [7]
Инструментальная легированная сталь по режущим свойствам мало отличается от углеродистой ( ввиду низкой красностойкости), производительность ее составляет 30 – 40 % от производительности быстрорежущей стали. Подробные данные о режущих свойствах быстрорежущей стали изложены в разделах, посвященных отдельным маркам стали. [8]
Инструментальные легированные стали для ударно-штампового инструмента должны обладать высокой твердостью и износостойкостью. [9]
Инструментальная легированная сталь входит в группу среднелегированных сталей. Ее применяют для изготовления различного инструмента: ударноштампо-вого, измерительного и режущего. Штампы из углеродистой стали обладают высокой твердостью и прочностью, но плохо сопротивляются удару. Метчики, развертки и другие длинные и тонкие инструменты из углеродистой стали при закалке получаются хрупкими, они ненадежны в работе и часто ломаются. [10]
Инструментальные легированные стали имеют тот же порядок маркировки по легирующим элементам, что и конструкционные стали, но количество углерода в них показывается цифрой в десятых, а не в сотых долях процента. [11]
Инструментальная легированная сталь применяется для изготовления режущих, измерительных, ударно-штамповых инструментов. По качеству инструмент us этой стали значительно превосходит инструмент из углеродистой стали, он тверже, лучше противостоит износу. Режущий инструмент выдерживает большую температуру, не теряя своей твердости. [12]
Инструментальные легированные стали широко применяются для штампованного, мерительного, вспомогательного инструмента и ограниченно – для режущего инструмента. [13]
Инструментальная легированная сталь входит в группу сред-нелегированных сталей. Ее применяют для изготовления различного инструмента: ударно-штамповочного, измерительного и режущего. Эта сталь имеет ряд преимуществ перед инструментальной углеродистой сталью. Штампы из углеродистой стали обладают высокой твердостью и прочностью, но плохо сопротивляются удару. Метчики, развертки и другие длинные и тонкие инструменты из углеродистой стали при закалке получаются хрупкими, они ненадежны в работе и часто ломаются. [14]
Инструментальные легированные стали имеют тот же порядок маркировки по легирующим элементам, что и конструкционные стали, но количество углерода в них показывается цифрой в десятых, а не в сотых долях процента. [15]
Страницы: 1 2 3 4
www.ngpedia.ru