Шероховатость 5 ra: Ra, Rz, параметры, обозначение, виды
alexxlab | 01.07.2021 | 0 | Разное
Шероховатость поверхности. Основные понятия
Шероховатостью поверхности называется совокупность микронеровностей, образующих рельеф поверхности и рассматриваемых в пределах участка, длина которого равна базовой длине.
Параметры шероховатости
В большинстве случаев шероховатость поверхности определяется одним из параметров Ra или Rz.
Высота неровностей профиля по десяти точкам Rz – является суммой средних абсолютных значений высот точек пяти наибольших выступов профиля и глубин пяти наибольших впадин в пределах базовой длины, измеренных от произвольной линии АВ
Среднее арифметическое отклонение профиля Ra – это среднее арифметическое абсолютных значений отклонений профиля yi от
средней линии m в пределах базовой длины
Рисунок 1.
Механизм возникновения шероховатости
Все причины возникновения шероховатости можно разбить на 3 группы:
- Расположение режущих кромок инструмента, относительно обрабатываемой поверхности;
- Упругая и пластическая деформация обрабатываемого металла;
- Вибрации в технологической станочной системе.
Рисунок 2.
Образование неровностей на обработанной поверхности можно представить как след от движения режущих кромок инструмента. Назовём такой профиль регулярным (рис.2).
На образование регулярного профиля влияет геометрия резца, в частности – углы в плане, а так же величина подачи S. Их
влияние описывается формулой
В реальном процессе резания впереди резца и под обработанной поверхностью образуется зона пластической деформации, которая вносит некоторую погрешность в регулярный профиль. Пластически деформированный металл в отдельных местах как бы наволакивается на микронеровности, а в где-то вырываются отдельные куски металла. Потому реальное значение Rz может быть записано как:
где – приращение высоты микронеровностей, вызванное пластической деформацией металла.
Следовательно, чем меньше пластическая деформация, тем меньше высота микронеровностей. Величина пластической деформации зависит, в
большей степени, от твёрдости обрабатываемого материала и, в меньшей — от глубины резания — t.
Методы и средства оценки шероховатости поверхности
Шероховатость поверхности оценивают двумя основными методами:
качественным и количественным.
Качественный метод оценки основан на визуальном сопоставлении обработанной поверхности с эталоном невооруженным глазом или под микроскопом, а также по ощущениям при ощупывании рукой (пальцем, ладонью, ногтем). Визуальным способом можно достаточно точно определять шероховатость поверхности, за исключением весьма тонко обработанных поверхностей. Эталоны, применяемые для оценки шероховатости поверхности визуальным способом, должны быть изготовлены из тех же материалов, с такой же формой поверхности и тем же методом, что и деталь. Качественную оценку весьма тонко обработанных поверхностей следует производить с помощью микроскопа или лупы с пятикратным и большим увеличением.
Количественный метод оценки заключается в измерении микронеровностей поверхности с помощью приборов: профилографов и
профилометров.
Профилографы
Профилографы – это приборы, позволяющие получатть изображение микронеровностей профиля в увеличенном масшттабе на каком-либо носителе (фотоплёнке, фотобумаге).
Профилометры – минуя этап получения изображения, производят необходимые измерения профиля микронеровностей.
Рисунок 3.
Схема профилографа Б. М. Левина приведена на рис. 3. Луч света от лампы 1, проходя через линзу 2, щель 3 и оптическую
систему 5, падает на зеркала 8 и 7. Зеркало 8 связано с ощупывающей иглой 9. Луч света, отраженный от зеркала 7 и затем от зеркала 8, проходит оптическую систему 6 и, попадая на зеркала 4 и далее на цилиндрическую линзу 14, проецирует изображение щели 3 на
светочувствительную пленку 13,расположенную на барабане 12. Изображение щели проецируется в виде световой точки. Деталь 10, на
поверхности которой измеряют шероховатость, располагается на верхнем диске предметного стола 11. При вращении синхронного двигателя
стол вместе с деталью движется поступательно относительно иглы 9, а барабан 12 вращается.
Рисунок 4.
Принцип действия профилометра конструкции В. М. Киселева заключается в возбуждении колебаний напряжения в результате движений ощупывающей иглы. На рис. 4 приведена схема этого профилометра (модель КВ-7). Игла 1 с алмазным наконечником, радиус закругления которого 12 мкм, подвешена на пружинах 2. Нижний конец ее ощупывает неровности поверхности детали, а верхний связан с индукционной катушкой 3, которая перемещается в магнитном поле полюсов 4 и 6 магнита 5. Возбуждаемый этим перемещением ток подают на усилитель и затем на гальванометр. Перемещение иглы по поверхности осуществляют с помощью электропривода со скоростью 10…20 мм/с. Давление иглы на поверхность проверяемой детали составляет 5…25 кПа. При подключении к профилометру осциллографа можно получить профилограмму исследуемой поверхности.
Рисунок 5.
Для измерения шероховатости предназначен также двойной микроскоп В. П. Линника (рис. 5). Прибор состоит из двух частей: микроскопа А для освещения исследуемой поверхности, микроскопа Б для наблюдения и измерения профиля поверхности. Оси обеих частей микроскопа, наклоненные под углом 45° к исследуемой поверхности, пересекаются между собой в предметной точке объективов.
В плоскости изображения объектива 3 микроскопа А перпендикулярно плоскости оси микроскопа расположена щель 2, освещаемая источником света 1. Объектив 3 дает уменьшенное изображение а щели 2 на проверяемой плоскости Р в виде узкой светящейся линии. При отсутствии на участке поверхности Р микронеровностей объектив 4 микроскопа Б в плоскости сетки окуляра 5 даст изображение а 2 той же узкой светящейся линии, а также изображение близлежащего участка исследуемой поверхности.
При том же расположении микроскопов А и Б при наличии микронеровностей h часть пучка света, отраженная от участка поверхности P 1 при наблюдении будет казаться выходящей из точки a 1 или из точки а 1 поверхности Р 1, расположенной на расстоянии 2h ниже поверхности Р. Тогда изображение точки из на сетке окуляра 5 будет на расстоянии h от оси микроскопа Б, равном h = 2xh sin 45°, где х — увеличение объектива 4.
Для измерений высоты неровностей в микроскопе Б установлен окулярный микрометр. Двойной микроскоп В. П. Линника позволяет также фотографировать исследуемую поверхность с высотой неровностей 0,9…60 мкм.
Образцы шероховатости поверхности (сравнения) ОШС-ФТ Ra (фрезерование торцевое, форма образца плоская 6,3;3,2;1,6;0,8;0,4) стальные
Фото может не соответствовать внешнему виду. Производитель оставляет за собой право изменять внешний вид изделия с целью улучшения эксплуатационных характеристик.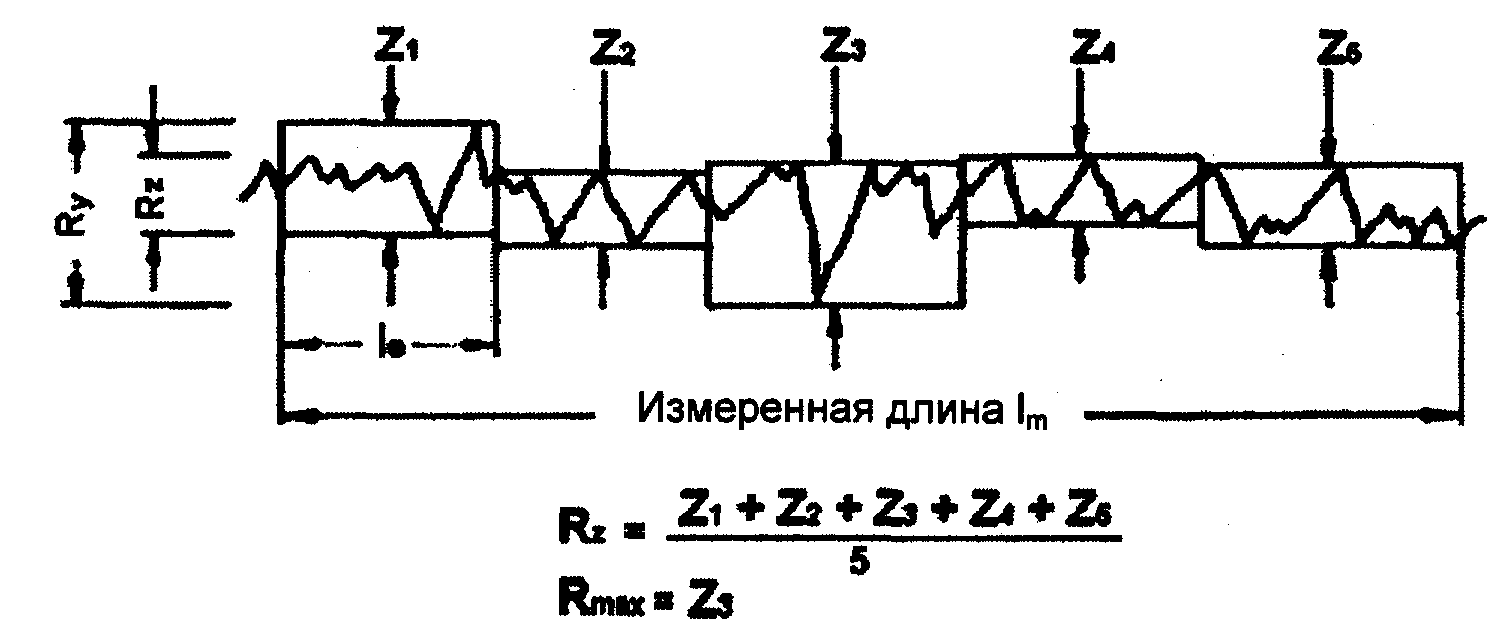
Характеристики
Тип | Ra |
Материал | Сталь |
Шероховатость, мкм | 0,4 … 6,3 |
Поверка/Калибровка | с поверкой |
Комплектация | Набор |
Описание
Набор ОШС ФТ – фрезерование торцеове – образцы шероховатости, предназначенные для оценки шероховатости поверхности, полученной после обработки.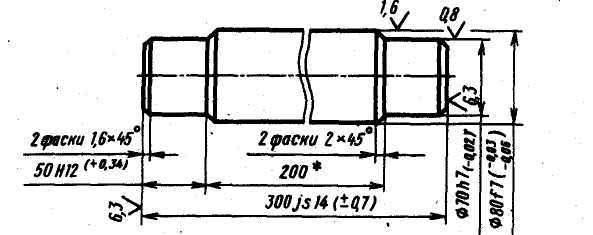
Контроль поверхности заготовки осуществляется методом сравнения с образцом визуально и на ощупь. Ширина каждого образца составляет не менее 20 мм. Выпускаются по ГОСТ 9378-93.
Комплектация набора: 5 пластин со средним арифметическим отклонением профиля (Ra) 0,4; 0,8; 1,6; 3,2; 6,3 мкм.
Форма образца: плоская, расположение неровностей: дугообразное. Материал: сталь.
Образцы поставляются в жестком пластиковом или деревянном кейсе.
цена по запросу
Под заказ
В корзину Самовывоз – Москва Доставка по РФ – ПодробнееОбразцы шероховатости | Прогресс – оборудование для неразрушающего контроля
Образцы шероховатости являются профессиональным инструментом и служат для оценки шероховатости поверхностей, полученных тем или иным способом обработки, путем сравнения — визуально и на ощупь.
Образцы шероховатости входят в обязательный перечень оборудования для аттестации лаборатории НК по визуальному методу, а так же в табель технической оснащенности лабораторий контроля качества ПАО «Транснефть». Параметры и характеристики шероховатости определяются в соответствии с ГОСТ 2789, обозначения шероховатости поверхностей — по ГОСТ 2.309. Методика поверки образцов шероховатости регламентируется МИ 1850. Протокол поверки образцов шероховатости можно скачать здесь. Образцы шероховатости входят в область аккредитации метрологической службы НТЦ «Эксперт» (образец сертификата) оказывающей услуги по контролю шероховатости с выдачей сертификата о калибровке системы Росаккредитации. При необходимости проведения комплексного неразрушающего контроля, можете ознакомиться с услугами штатной лаборатории НК.
Количественно шероховатость оценивают следующими параметрами:
- Ra — среднее арифметическое отклонение профиля;
- Rz — высота неровностей профиля по десяти точкам;
- Rmax — наибольшая высота неровностей профиля.
Ряды номинальных значений параметра шероховатости Ra в зависимости от способа обработки образцов и базовые длины должны соответствовать требованиям ГОСТ 9378 (см. таблицу). По требованию заказчика шероховатость может дополнительно оцениваться другими параметрами (Rz, Rmax и др.), значения которых приводятся как справочные по результатам измерений. Примерная переводная таблица параметров шероховатости Ra / Rz с привязкой к классам шероховатости из утратившего силу ГОСТа 2789-59 приведена ниже.
Класс чистоты поверхности | Среднеарифметическое отклонения профиля Ra, мкм |
Высота неровностей Rz, мкм | Базовая длина l, мм |
не более | |||
1 | 80 | 320 | 8 |
2 | 40 | 160 | 8 |
3 | 20 | 80 | 8 |
4 | 10 | 40 | 2,5 |
5 | 5 | 20 | 2,5 |
6 | 2,5 | 10 | 0,8 |
7 | 1,25 | 6,3 | 0,8 |
8 | 0,63 | 3,2 | 0,8 |
9 | 0,32 | 1,6 | 0,25 |
10 | 0,16 | 0,8 | 0,25 |
11 | 0,08 | 0,4 | 0,25 |
12 | 0,04 | 0,2 | 0,25 |
13 | 0,02 | 0,1 | 0,08 |
14 | 0,01 | 0,05 | 0,08 |
Условное обозначение эталона шероховатости должно содержать номинальное значение параметра Ra (Rz), условное обозначение способа обработки и обозначение стандарта. Пример условного обозначения образца для оценки стальных поверхностей, полученного расточкой, с номинальным значением Ra 3,2 мкм: Образец шероховатости 3,2 Р сталь, ГОСТ 9378.
Параметры шероховатости поверхности измеряются с помощью профилометра. В данном приборе сигнал получается от датчика с алмазной иглой, которая перемещается перпендикулярно исследуемой поверхности. Сигнал проходит электронное усиление и интегрируется для формирования усредненного параметра. Результаты измерения отсчитываются на шкале в виде численных значений. Метрологическая аттестация образцов шероховатости может проводиться по методике МИ 1850 с оформлением сертификата о калибровке. Гарантийный срок эксплуатации образцов — 24 месяца со дня ввода в эксплуатацию.
Комплект поставки:
- Образец шероховатости
- Упаковка
- Паспорт
- Сертификат о калибровке собственной метрологической службы (по заявке)
В следующей таблице перечислены основные способы обработки образцов их обозначения и параметры.
Способ обработки | Форма образца | Обозначение способа обработки | Фото образца | Параметр шероховатости Ra , мкм 1 |
Шлифование периферией круга | Плоская Цилиндрическая выпуклая Цилиндрическая вогнутая | ШП ШЦ ШЦВ | 0,050; 0,100; 0,200; 0,400; 0,800; 1,600; 3,200 | |
Шлифование торцовое | Плоская | ШТ | ||
Шлифование чашеобразным кругом | Плоская | ШЧ | ||
Фрезерование цилиндрическое | Плоская | ФЦ | 0,4; 0,8; 1,6; 3,2; 6,3; 12,5 | |
Фрезерование торцовое | Плоская | ФТ | ||
Фрезерование торцовое (перекрещивающееся) | Плоская | ФТП | ||
Точение | Цилиндрическая выпуклая | Т | 0,4; 0,8; 1,6; 3,2; 6,3; 12,5 | |
Расточка | Цилиндрическая вогнутая | Р | ||
Точение торцовое | Плоская | ТТ | ||
Строгание | Плоская | С | 0,8; 1,6; 3,2; 6,3; 12,5; 25,0 | |
Дробеструйная обработка | Плоская | ДС | 0,2; 0,4; 0,8; 1,6; 3,2; 6,3; 12,5; 25,0 | |
Пескоструйная обработка | Плоская | ПС | ||
Полирование | Плоская Цилиндрическая выпуклая | ПП ПЦ | 0,0125; 0,025; 0,050; 0,100; 0,200 | |
Ручное опиливание | Плоская | РО | Rz 80; 40; 20; 10; 5; 2,5 |
Шероховатость поверхностей деталей – Inzhener-Info
Качество поверхностного слоя определяется совокупностью характеристик: физико-механическим состоянием, микроструктурой металла поверхностного слоя, шероховатостью поверхности. Состояние поверхностного слоя влияет на эксплуатационные свойства деталей машин: износостойкость, виброустойчивость, контактную жесткость, прочность соединений, прочность конструкций при циклических нагрузках и т. д.
Параметры и характеристики шероховатости поверхности установлены ГОСТ 2789–73, требования к другим характеристикам поверхностного слоя назначают по руководящим материалам предприятия.
Для оценки шероховатости поверхности ГОСТ 2789–73 предусматривает шесть параметров:
высотные: Ra — среднее арифметическое отклонение профиля; Rz — высота неровностей профиля по десяти точкам; Rmax — наибольшая высота профиля;
шаговые: S — средний шаг неровностей профиля по вершинам; Sm — средний шаг неровностей профиля по средней линии;
высотно-шаговый tp — относительная опорная длина профиля.
Базой для отсчета высот выступов и впадин неровностей, свойства которых нормируются, служит средняя линия профиля (рис. 279) — базовая линия, имеющая форму номинального профиля и проведенная так, что в пределах базовой длины среднее квадратическое отклонение профиля до этой линии минимально.
Через высшую и низшую точки профиля в пределах базовой длины l проводят линии выступов и впадин профиля, эквидистантно средней линии. Расстояние между этими линиями определяет наибольшую высоту неровностей профиля Rmax.
Среднее арифметическое отклонение профиля Ra определяется как среднее арифметическое абсолютных значений отклонений профили в пределах базовой длины:
или приближенно:
Высота неровностей профиля по десяти точкам Rz равна средней арифметической суммы абсолютных отклонений точек пяти наибольших минимумов Нi min и пяти наибольших максимумов Hi max профиля в пределах базовой длины:
Вместо средней линии, имеющей форму отрезка прямой, определяют расстояние от высших точек пяти наибольших максимумов himax и низших точек пяти наибольших минимумов himin до линии, параллельной средней и не пересекающей профиль.
Тогда
Средний шаг неровностей S вычисляют как среднее арифметическое значение шага неровностей Smi в пределах базовой длины:
Средний шаг неровностей профиля по вершинам S — среднее арифметическое значение шага неровностей профиля по вершинам Si в пределах базовой длины
Под опорной длиной профиля ηр понимают сумму длин отрезков в пределах базовой длины, отсекаемых на заданном уровне в материале выступов профиля линией, эквидистантной средней линии.
Относительная опорная длина профиля tp определяется как отношение опорной длины профиля ηр к базовой длине:
Требования к шероховатости поверхности по ГОСТ 2789-73 устанавливают указанием числовых значений параметров. В дополнение к количественным параметрам для более полной характеристики шероховатости указывают направление неровностей (условное обозначение — см. рис. 280), вид обработки поверхности или последовательность видов обработки (рис. 281 — 283).
В обозначении шероховатости поверхности, вид обработки которой конструктором не устанавливается, применяют знак, приведенный на рис. 282, а; если поверхность образована с удалением слоя материала — знак, приведенный на рис. 282, б; и для поверхности, образованной без удаления слоя материала, — знак, приведенный на рис. 282, в.
Значение параметра Ra указывают без символа, например, 0,5. Для остальных указывают символы, например, Rmах 6,3.
ГОСТ 2789-71 установлено 14 классов шероховатости поверхности. Причем классы 1—5, 13 и 14 определены через параметр Rz, классы 6—12 через параметр Ra. Каждый класс определен только по одному параметру и базовой длине. Числовые значения параметров заданы в виде диапазонов, верхние пределы которых полностью соответствуют ранее действовавшим.
Требования к шероховатости поверхности устанавливают путем задания значения параметра (параметров) и базовой длины. Причем целесообразно пользоваться предпочтительными значениями параметра Ra (графа 2, табл. 29). Эти значения находятся вблизи середины диапазона, определяющего данный класс шероховатости. В других случаях могут назначать величины параметров по графам 3 или 4.
Требования к шероховатости поверхности определяются условиями работы поверхности в машине. В общем случае, чем выше требования по точности, тем выше требования и по шероховатости поверхности.
Для грубых квалитетов с расширенным полем допусков класс шероховатости можно снижать, что уменьшает стоимость изготовления.
Минимальный класс шероховатости поверхности обработки, необходимый для получения различных квалитетов, можно выбрать по табл. 30.
Классы шероховатости поверхностей, соответствующие различным видам обработки, приведены и табл. 31.
При выборе класса шероховатости должны быть учтены свойства материала и твердость поверхности детали. Высокие показатели для сталей можно получить при твердости не ниже HRC 30—35. Стальные изделия, подлежащие чистой обработке, должны быть по меньшей мере подвергнуты улучшению или нормализации. Термически необработанные низкоуглеродистые стали тонкой обработке поддаются плохо.
По условиям обработки получить чистую отделку и точные размеры в отверстиях труднее, чем на валах. Поэтому, как правило, требование к шероховатости поверхности в отверстиях назначают на 1—2 класса ниже, чем на валах.
В интересах уменьшения стоимости изготовления рекомендуется применять менее высокие требования к шероховатости, совместимые с условием надежной работы деталей.
В некоторых случаях (соединения с натягом, подшипники скольжения) существуют оптимальные параметры поверхности, отклонения от которых в ту или другую сторону снижают работоспособность соединений.
Свободные поверхности (не входящие в соединения или расположенные с зазором по отношению к ближайшим поверхностям) следует в интересах экономичности обрабатывать по низким классам шероховатости. Исключение составляют напряженные циклически нагруженные детали. Для повышения сопротивления усталости такие детали обрабатывают так, чтобы обеспечить высокий класс шероховатости поверхности, полируют и дополнительно упрочняют поверхностным пластическим деформированием.
Ниже приведены ориентировочные значения классов шероховатости поверхностей для типовых машиностроительных деталей, основанные на опыте общего машиностроения.
Шероховатость поверхностей типовых машиностроительных деталей
Классы шероховатости | |
---|---|
Подшипники скольжения: | |
малонагруженные, работающие при умеренных окружных скоростях: | |
– отверстие | 7—9 |
– вал | 8—10 |
высоконагруженные, работающие при больших окружных скоростях: | |
– отверстие | 8—9 |
– вал | 9—10 |
Упорные подшипники скольжения (рабочие поверхности): | |
– малонагруженные | 7—9 |
– высоконагруженные, работающие при больших окружных скоростях | 8—10 |
Сферические поверхности самоустанавливающихся подшипников и т.![]() | 9—12 |
Неподвижные соединения с посадкой скольжения [Н(h)]: | |
– отверстие | 8—9 |
– вал | 9—11 |
Соединения с переходными посадками: | |
– отверстие | 7—9 |
– вал | 8—10 |
Прессовые и конусные соединения: | |
– отверстие | 7—10 |
– вал | 8—11 |
Упорные буртики неподвижных цилиндрических соединений (рабочие поверхности) | 6—8 |
Посадки подшипников качения: | |
отверстие в корпусе при классе точности подшипника: | |
– нормальном 0 | 8—9 |
– повышенном 6 | 9—10 |
– высоком 5 | 10—11 |
– прецизионном 4 | 11—12 |
вал при классе точности подшипника: | |
– нормальном 0 | 8—10 |
– повышенном 6 | 10—11 |
– высоком 5 | 11—12 |
– прецизионном 4 | 12—13 |
Тела качения в контактно-нагруженных сочленениях | 10—12 |
Цилиндры под поршни: | |
– с мягкими уплотнениями (манжеты) | 7—10 |
– с металлическими кольцами (с притиркой) | 9—12 |
Поршни (рабочая поверхность): | |
– чугунные и стальные | 9—10 |
– из легких сплавов | 10—12 |
Поршневые пальцы: | |
– отверстие | 8—11 |
– палец | 9—12 |
Скальчатые насосы высокого давления: | |
– цилиндры (с притиркой) | 10—12 |
– плунжеры(с притиркой) | 12—14 |
Золотники цилиндрические: | |
маслораспределительные: | |
– отверстие (с притиркой) | 8—10 |
– золотник (с притиркой) | 9—11 |
газораспределительные: | |
– отверстие (с притиркой) | 9—11 |
– золотник (с притиркой) | 10—12 |
Золотники плоские: | |
– корпус (с притиркой) | 9—10 |
– золотник (с притиркой) | 11—12 |
Конические пробковые краны (рабочие поверхности): | |
– отверстие (с притиркой) | 9—10 |
– пробка (с притиркой) | 10—12 |
Клапаны с коническими поверхностями: | |
направляющими: | |
– втулка штока | 9—10 |
– шток | 10—11 |
уплотняющими: | |
– рабочая поверхность седла (с притиркой) | 9—11 |
– рабочая фаска клапана (с притиркой) | 10—12 |
Кулачковые механизмы (рабочие поверхности): | |
– кулачок | 9—11 |
– приводной ролик | 9—12 |
– плоский толкатель | 8—11 |
Копиры (рабочие поверхности): | |
– копир | 8—10 |
– ролик | 9—11 |
Шлицевые соединения, центрирование: | |
по наружному диаметру: | |
– отверстие | 7—10 |
– вал | 8—10 |
по внутреннему диаметру: | |
– отверстие | 9—12 |
– вал | 7—9 |
по граням шлицев: | |
– охватывающие поверхности | 7—10 |
– охватываемые поверхности | 8—11 |
Шлицевые соединения с зазором: | |
– рабочие грани | 7—10 |
– отверстие | 8—11 |
– вал | 7—8 |
Шпоночно-пазовые соединения (рабочие грани): | |
– пазы | 5—7 |
– шпонка | 6—8 |
Направляющие призматические поверхности: | |
– охватывающие | 8—10 |
– охватываемые | 9—12 |
Резьбы наружные: | |
– рядовые | 5—6 |
– повышенной точности | 6—7 |
– точные | 8—9 |
Резьбы внутренние: | |
– рядовые | 4—5 |
– повышенной точности | 5—6 |
– точные | 7—8 |
Винты ходовые (рабочие поверхности): | |
– гайка | 8—10 |
– винт | 10—12 |
Прямозубые колеса (рабочие поверхности зубьев): | |
– неответственного назначения | 6—7 |
– работающие с умеренными нагрузками и окружными скоростями | 7—8 |
– работающие со средними нагрузками и окружными скоростями | 9—10 |
– тяжелонагруженные, подверженные ударной нагрузке и работающие при высоких скоростях (с притиркой или обкатыванием) | 10—12 |
Косозубые и шевронные колеса (рабочие поверхности зубьев): | |
– работающие при умеренных нагрузках и окружных скоростях | 6—8 |
– тяжелонагруженные и работающие при высоких окружных скоростях | 8—10 |
Конические зубчатые колеса (рабочие поверхности зубьев): | |
– работающие при умеренных нагрузках и окружных скоростях | 6—8 |
– тяжелонагруженные и работающие при высоких окружных скоростях | 8—10 |
Червячные колеса (рабочие поверхности зубьев): | |
– работающие при умеренных нагрузках | 7—8 |
– тяжелонагруженные | 8—10 |
Червяки (рабочие поверхности витков): | |
– работающие при умеренных нагрузках | 8—9 |
– тяжелонагруженные | 10—11 |
Храповые колеса (рабочие поверхности зубьев) | 8—9 |
Колеса свободного хода роликовые (рабочие поверхности): | |
– охватывающая обойма | 8—10 |
– охватываемая обойма | 10—12 |
– ролики | 12—13 |
Фрикционы, тормоза (рабочие поверхности): | |
– цилиндрические | 9—12 |
– плоские | 8—10 |
Уплотнения цилиндрические контактные (рабочие поверхности валов): | |
– с мягкими элементами (манжеты) | 10—11 |
– с металлическими элементами | 11—12 |
Уплотнения торцовые (рабочие поверхности дисков): | |
– с мягкими элементами | 9—10 |
– с металлическими элементами (с притиркой) | 10—12 |
Уплотняющие поверхности ниппелей, штуцеров и т.![]() | 7—9 |
Шкивы (рабочие поверхности): | |
– под плоские ремни (с полированием) | 9—12 |
– клиноременных передач | 8—10 |
Стыки герметичные, собираемые на прокладках: | |
– мягких | 6—8 |
– твердых | 8—9 |
– из мягких металлов | 9—10 |
Стыки герметичные (металл по металлу) (с притиркой) | 10—12 |
Приваленные плоскости (без прокладок): | |
– рядовые | 5—7 |
– точные | 8—10 |
Свободные поверхности деталей (торцы и ненесущие цилиндрические поверхности валов, фаски, нерабочие поверхности зубчатых колес, шкивов, маховиков, рычагов и т. п.): | |
– малонагруженных | 4—6 |
– нагруженных высокими циклическими нагрузками (вплоть до полирования) | 6—9 |
Галтели: | |
– неответственного назначения | 5—6 |
– деталей, нагруженных высокими циклическими нагрузками (вплоть до полирования) | 8—10 |
Шестигранники, четырехгранники, лыски, пазы под ключ и т.![]() | 4—5 |
Отверстия под крепежные детали, устанавливаемые с зазором | 4—5 |
Опорные поверхности под гайки и головки болтов: | |
– рядовые соединения | 5—6 |
– ответственные, циклически нагруженные соединения | 7—8 |
Центрирующие буртики (фланцев, крышек, корпусных деталей и т. д.): | |
– отверстие | 5—6 |
– буртик | 6—7 |
Детали управления, рукоятки, ручки, маховички и т. п. (с полированием) | 8—10 |
Пружины сжатия (заправка торцов) | 4—5 |
Мерительный инструмент (рабочие поверхности) (с доводкой) | 12—14 |
Обозначение шероховатости поверхностей на чертежах
1. Обозначение шероховатости поверхностей на чертежах
Совокупность неровностейповерхности с относительно малыми
шагами, выделенная на определенной
(базовой) длине, называется
шероховатостью поверхности.
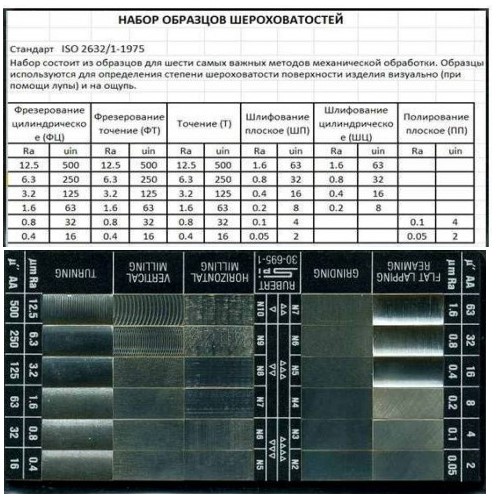
Шероховатость поверхностей регламентируется следующими
стандартами:
– ГОСТ 25142 – 82. Шероховатость поверхностей. Термины и
определения.
– ГОСТ 2789 – 73. Шероховатость поверхностей. Параметры и
характеристики.
– ГОСТ 2.309 – 73. Обозначения шероховатости поверхностей.
3. Параметры для нормирования шероховатости поверхностей
ГОСТ 2789-73 устанавливает шестьпараметров: три высотных (Ra, Rz,
Rmax), два шаговых (S, Sm ) и
параметр относительной опорной
длины
профиля
(tp).
Кроме
количественных
параметров
стандарт
устанавливает
типы
направлений неровностей
Л и н и я в ы с ту по в
Si
Smi
p
bn
l
1
1 n
Ra y x dx yi
l 0
n i 1
где l – базовая длина;
n – число выбранных точек профиля на
базовой длине;
y – отклонение профиля от средней линии.
Высота неровностей по
десяти точкам Rz
yp5
bi
5
x
yv5
y1
yv1
m
b1
yv2
yp1
yp2
yi
Si
Rmax
y
Среднее арифметическое
отклонение профиля Ra
Smi
Линия впадин
l
Профиль поверхности
yn
Rz
y
i 1
5
pi
yvi
i 1
5
где y pi – высота
i-го наибольшего
выступа профиля;
yvi – глубина i-й наибольшей
впадины профиля.

4. Выбор значений параметров шероховатости
Ряды значений среднегоарифметического
отклонения профиля
Ra, мкм
100
80
63
50
40
32
25
20
16,0
12,5
10,0
8,0
6,3
5,0
4,0
3,2
2,5
2,0
1,60
1,25
1,00
0,80
0,63
0,50
0,40
0,32
0,25
0,20
0,160
0,125
0,100
0,080
0,063
0,050
0,040
0,032
0,025
0,020
0,016
0,012
0,010
0,008
–
Ряды значений высоты
неровностей профиля
Rz и Rmax, мкм
1600
1250
1000
800
630
500
400
320
250
200
160
125
100
80
63
50
40
32
25
20
16,0
12,5
10,0
8,0
6,3
5,0
4,0
3,2
2,5
2,0
1,60
1,25
1,00
0,80
0,63
0,50
0,40
0,32
0,25
0,20
0,160
0,125
0,100
0.
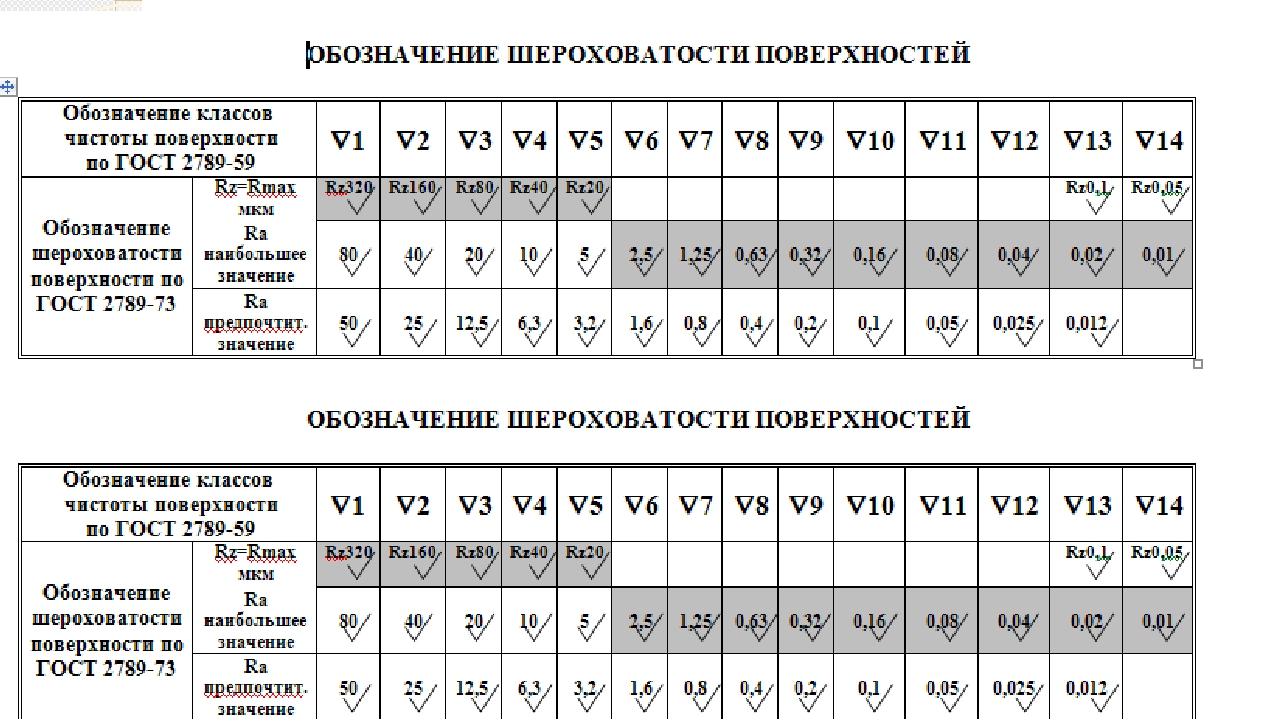
0,063
0,050
0,040
0,032
0,025
0,020
–
5. Знаки, применяемые для обозначения шероховатости поверхностей
Знаки, применяемые для обозначения60Е
60Е
H
60Е
h
H
60Е
h
H
60Е
h
шероховатости поверхностей
60Е
– основной знак; для обозначения шероховатости наиболее
предпочтителен и наиболее часто применяется. Означает, что
разработчику безразличен вид обработки детали, и изготовитель может
применить любой вид обработки – со снятием или без снятия материала
– применяется для обозначения шероховатости, которая должна быть
образована удалением поверхностного слоя материала каким-либо
режущим инструментом
Ra 12 ,5 ) – применяется для
– с числовым значением (например,
обозначения шероховатости, которая должна быть образована без
удаления слоя материала
– без числового значения – применяется для поверхностей, по данному
чертежу вообще не подлежащих обработке, т.

поверхностей находится «в состоянии поставки».
6. Структура обозначения
Способ обработки поверхностии (или) другие дополнительные
указания
Полка знака
Базовая длина по ГОСТ 2789- 73/
/ Параметр (параметры) шероховатости
по ГОСТ 2789- 73
Условное обозначение
направления неровностей
Пример обозначения шероховатости на чертежах
Полировать
0,8/ Ra 0,1
0,8/ Sm 0,063
0,040
M 0,25/ t 80±10%
50
наибольшее значение
диапазон значений
номинальное значение с
предельными отклонениями
7. Обозначение направления неровностей
8. Основные правила нанесения обозначений шероховатости поверхностей на чертежах
1. Шероховатость поверхностей обозначают на чертеже для всехвыполняемых по данному чертежу поверхностей изделия,
независимо от методов их образования, кроме поверхностей,
шероховатость которых не обусловлена требованиями конструкции.
2.

разрезах, на которых поставлены размеры, относящиеся к
соответствующим частям детали.
3. Знаки располагаются на:
а) линиях контура элементов детали;
б) выносных линиях, при этом по
возможности ближе к размерной линии;
в) полках выносных линий;
г) размерных линиях или их продолжениях
при недостатке места, при этом
разрешается разрывать выносную
0,1
линию;
д) на рамке допуска формы;
е) на линии невидимого контура только в
случаях, когда от этой линии
нанесен размер.
4.
Знаки, имеющие полку, должны располагаться относительно
основной надписи чертежа так, как указано на рис.1, а знаки без полки
(без указания параметра и способа обработки) располагают как на рис.2.
При расположении поверхности в заштрихованной зоне обозначение
наносят только на полке линии-выноски.
30Е
30Е
рис. 1
рис. 2
5.
При
изображении
изделия
с
разрывом обозначение шероховатости
наносят
только
на
одной
части
изображения, по возможности ближе к
месту указания размеров.
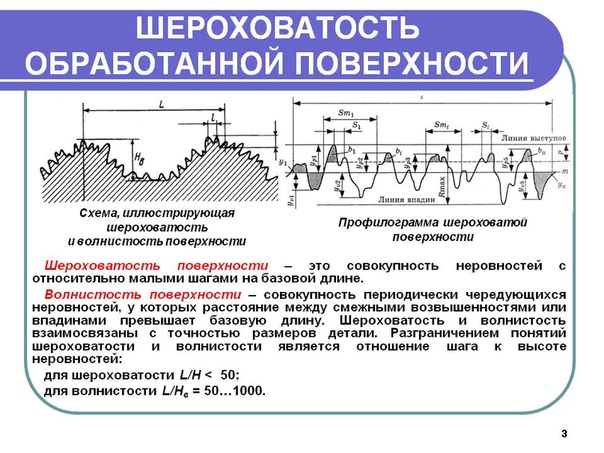
З
Ra 1,6
Ra 3,2
Ra 1,6
Ra 3,2
З
З
6. Если шероховатость одной и той же
поверхности различна на отдельных
участках, то эти участки разграничивают
сплошной тонкой линией с нанесением
соответствующих
размеров
и
обозначений
шероховатости.
Через
заштрихованную зону линию границы
между участками не проводят.
Ra 1,6
7. Когда на чертеже поверхности детали мало
места для размещения знака шероховатости,
то
допускается
применять
упрощенное
обозначение с разъяснением этого обозначения
в технических требованиях чертежа. При этом
используют знак
и строчные буквы русского
алфавита
в
алфавитном
порядке,
без
повторений и, как правило, без пропусков.
8. Если одинаковую шероховатость имеет
поверхность сложной конфигурации,
допускается обозначение шероховатости
приводить в технических требованиях чертежа со
ссылкой на буквенное обозначение поверхности,
например: “Шероховатость поверхности
А – Ra 6,3 При этом буквенное обозначение
поверхности наносят на полке линии-выноски,
проведенной от утолщенной штрих-пунктирной
линии, которой обводят поверхность на
расстоянии 0,8…1 мм от линии контура.

б
а
Полировать
а =
M 0,8/ Ra 0,4
б =
Ra 0,8
A
9. Если одинаковую шероховатость имеют поверхности, образующие контур,
обозначение шероховатости наносят один раз (рис. 1). Диаметр
вспомогательного знака – 4…5 мм. В обозначении одинаковой
шероховатости поверхностей, плавно переходящих одна в другую, знак
не приводят (рис. 2).
R
R
R
Ra 12,5
Ra 6,3
R
Ra 6,3
рис. 1
рис. 2
10. Обозначение шероховатости поверхности повторяющихся
элементов изделия (отверстий, пазов, зубьев и т.п.), количество
которых указано на чертеже, а также обозначение шероховатости
одной и той же поверхности наносят один раз, независимо от числа
изображений.
Ra 6,3
З
З
Ra
6,3
4отв. З
Ra 1,6
Ra 6,3
З
Ra 3,2
Ra 3,2
или
или
,2
3
Ra
Ra 3,2
M
M
или
3,2
a
R
M
Ra 3
,2
или
З
Ra 3,2
Ra 3,2
К .
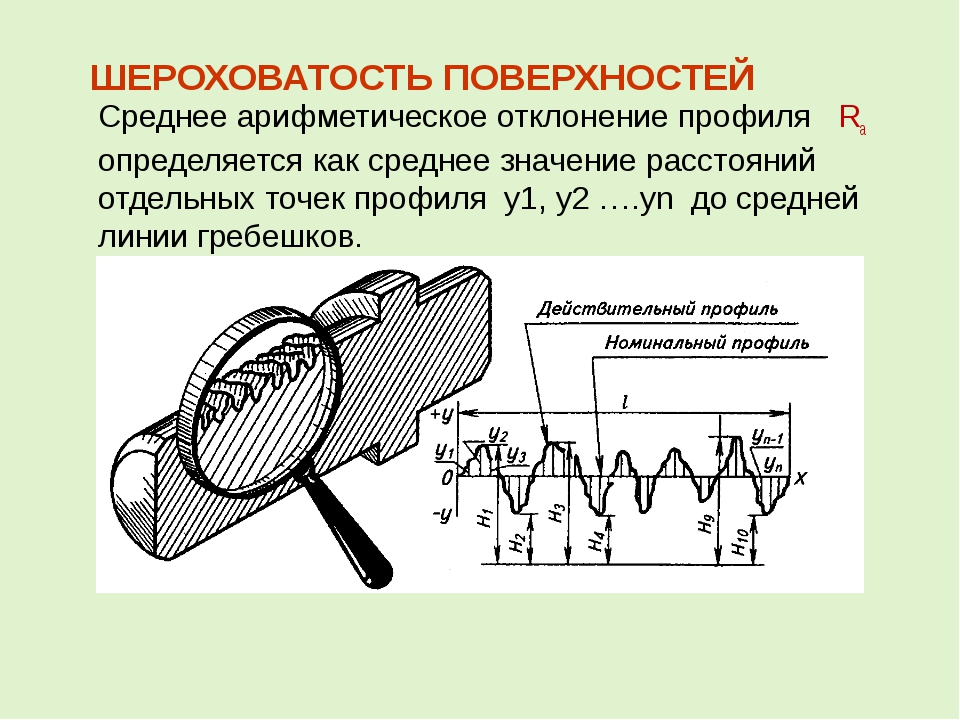
Ra
3,2
Ra 1,6
З
G
M
или
Ra 3,2
M
M
11. Обозначение шероховатости поверхности профиля резьбы наносят по
общим правилам при изображении профиля (в том числе для резьбы с
нестандартным профилем) или условно на выносной линии для указания
размера резьбы, на размерной линии или на ее продолжении.
Ra 3,2
Перв.
Инв. №подл.
Подп. и дата
Ra 6,3
10
19
24
50
Взам. инв. № Инв. №дубл.
КПГД. 420120.001
Подп. и дата
Справ. №
12. Если требования к шероховатости одинаковы для всех
поверхностей детали, то знак указывают один раз и помещают в
правом верхнем углу чертежа, а на поверхностях элементов детали
знаков не наносят. Размеры и толщина линий знака в обозначении
шероховатости, вынесенном в правый верхний угол чертежа, должны
быть приблизительно в 1,5 раза больше, чем в обозначениях,
нанесенных на изображении.
4
КПГД.

Изм. Лист №докум. Подп. Дата
Разраб. Иванов П. И.
1.12.08
Пров.
Петров И.П.
2.12.08
Т.контр.
Н.контр.
Утв.
Фланец
Cт3 ГОСТ380- 88
Копировал
Лит.
у
Масса Масштаб
–
Лист
1:1
Листов
СПбГПУ
гр. 2042
Формат
A5
1
Не допускается
обозначение
шероховатости или
знак
выносить в
правый верхний угол
чертежа при наличии в
изделии поверхностей,
шероховатость
которых не
нормируется (не
обусловлена
требованиями
конструкции).
Ra 3,2 (
)
60
25
Взам. инв. № Инв. №дубл.
Подп. и дата
Инв. №подл.
R3
50
КПГД. 420120.004
Подп. и дата
Справ. №
13. Если поверхности нескольких элементов детали имеют
одинаковую шероховатость, то ее обозначение помещают в правом
верхнем углу чертежа и рядом в скобках указывают условный знак
без каких-либо требований.
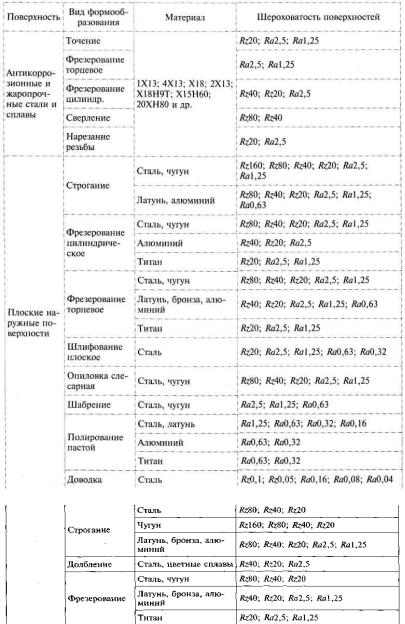
на которых на чертеже не нанесены обозначения шероховатости или
знак
, должны иметь шероховатость, указанную перед знаком ( )
Размеры знака ( ) должны быть одинаковыми с размерами
знаков, нанесенных на изображении.
R3
30
Ra 12,5
КПГД. 420120.004
Изм. Лист №докум. Подп. Дата
Разраб. Иванов П. И.
1.12.08
Пров.
Петров И.П.
2.12.08
Т.контр.
Н.контр.
Утв.
Стакан
Сталь 08 кп ГОСТ 1050- 88
Копировал
Лит.
Масса Масштаб
у
–
Лист
Листов
1:2
СПбГПУ
гр. 2042
Формат
A5
1
)
КПГД. 420120.002
Перв. примен.
Ra 6,3 (
20,7
1,6
4
Справ. №
8
Полировать
Ra 0,8
0,8•45
23
Инв. №подл.
Подп. и дата
Взам. инв. № Инв. №дубл.
Подп. и дата
25
КПГД. 420120.002
Изм. Лист №докум. Подп. Дата
Разраб. Иванов П.И.
Пров.

Петров И П.
Т.контр.
Н.контр.
Утв.
Ось
Сталь 45 ГОСТ 1050- 88
Копировал
Лит.
у
Масса Масштаб
4:1
–
Лист
Листов
СПбГПУ
гр. 2042
Формат
A4
1
Деталь содержит поверхность,
которая должна быть
образована удалением
поверхностного слоя
материала каким-либо
режущим инструментом
(точение, шлифование,
сверление и т.д.). Знак
применяется для
поверхности, требуемые
эксплуатационные свойства
которой обеспечиваются
только при ее окончательной
обработке удалением слоя
материала, чаще используется
в сочетании с указанием
единственно возможного вида
обработки.
КПГД. 420120.003
Перв. примен.
Ra 25 (
Деталь имеет
поверхности, которые
должны быть обработаны
без снятия материала
(литье, штамповка,
ковка) с заданным
значением
шероховатости.
)
Взам. инв. № Инв. №дубл.
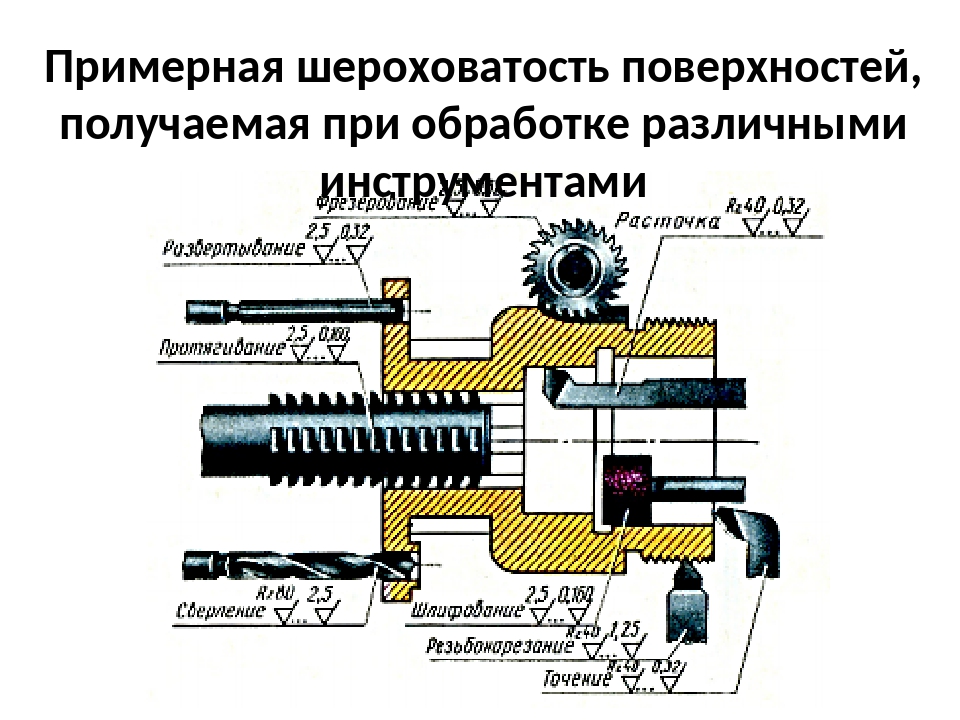
Подп. и дата
Инв. №подл.
120
60
50
70
3
Ra 3,2
Ra 1,6
10
Подп. и дата
Справ. №
R6
50
10
60*
1. * Размер для справок.
2. Неуказанные литейные радиусы не болee 3 мм.
КПГД. 420120.003
Изм. Лист №докум. Подп. Дата
Разраб. Иванов П. И.
1.12.08
Пров.
Петров И.П.
2.12.08
Т.контр.
Н.контр.
Утв.
Крышка
СЧ 15 ГОСТ 1412- 85
Копировал
Лит.
у
Масса Масштаб
–
Лист
1:1
Листов
СПбГПУ
гр. 2042
Формат
A4
1
12,6*
Ra 12,5
16
Ra 12,5
* Размер для справок.
КПГД. 420120.005
Изм. Лист №докум. Подп. Дата
Разраб. Иванов П. И.
1.12.08
Пров.
Петров И П
2.12.08
Т.контр.
Н.контр.
Утв.
Лит.
Труба
Масса Масштаб
у
–
Лист
Труба 17х2,2 ГОСТ 3262- 75
Копировал
Листов
Формат
1
A5
Ra 12,5 (
)
12,6*
Ra 6,3
2:1
СПбГПУ
гр.
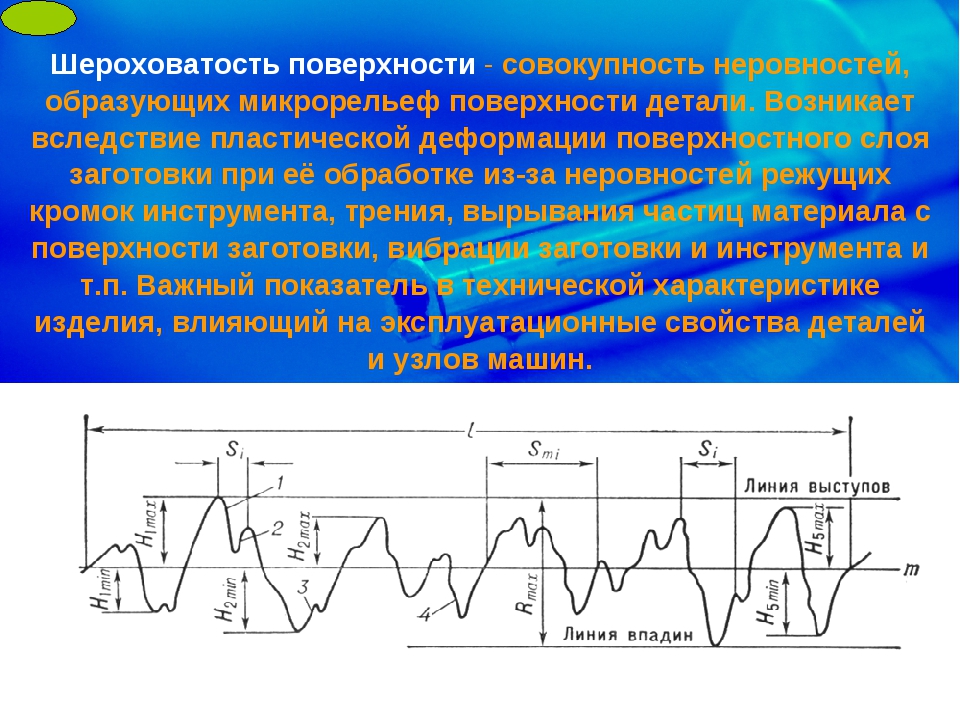
16
Взам. инв. № Инв.Перв.
№дубл.
примен.Подп. и дата
Подп.
Справ.
и дата
№
Инв. №подл.
Подп. и дата
Взам. инв. № Инв. №дубл.
Подп. и дата
Деталь изготавливается из
проката или литой,
штампованной или другой
заготовки; часть
поверхностей находится «в
состоянии поставки».
100
КПГД. 420120.005
Инв. №подл.
КПГД. 420120.005
( )
Ra 6,3
* Размер для справок.
КПГД. 420120.005
Изм. Лист №докум. Подп. Дата
Разраб. Иванов П. И.
1.12.08
Пров.
Петров И П
2.12.08
Т.контр.
Н.контр.
Утв.
Труба
Труба 17х2,2 ГОСТ 3262- 75
Копировал
Лит.
Масса Масштаб
у
–
Лист
Листов
2:1
СПбГПУ
гр. 2042
Формат
A5
1
Требования к шероховатости
поверхностей, обозначенной
знаком
, определены
стандартом на сортамент
(на этот стандарт должна
быть ссылка в графе
«Материалы» основной
надписи чертежа).

КПГД. 420120. 006
Перв. примен.
120
Ra 3,2
3,2
Ra 1,6
15
14
140
100
Подп. и дата
Взам. инв. № Инв. №дубл.
4 отв.
14
Ra
15
Ra 1,6
150
Справ. №
90
120
R20
Подп. и дата
Деталь изготовлена без
снятия материала (литье,
штамповка, ковка) часть
поверхностей находится «в
состоянии поставки».
30
Ra 3,2
Ra 3,2
Инв. №подл.
( )
100
160
200
1. Шероховатость необработанных поверхностей по ТУ № … на
поставку отливок.
2. Неуказанные радиусы скруглений 3 мм.
КПГД. 420120. 006
Изм. Лист №докум. Подп. Дата
Разраб. Иванов П. И.
Пров.
Петров И.П.
Т.контр.
Н.контр.
Утв.
Корпус
СЧ 15 ГОСТ 1412- 85
Копировал
Лит.
у
Масса Масштаб
–
Лист
1:2,5
Листов
СПбГПУ
гр. 2042
Формат
A4
1
Требования к шероховатости
поверхностей, обозначенной
знаком
, определены
техническими условиями на
литье в технических
требованиях чертежа (в
учебных чертежах часто не
записываются).
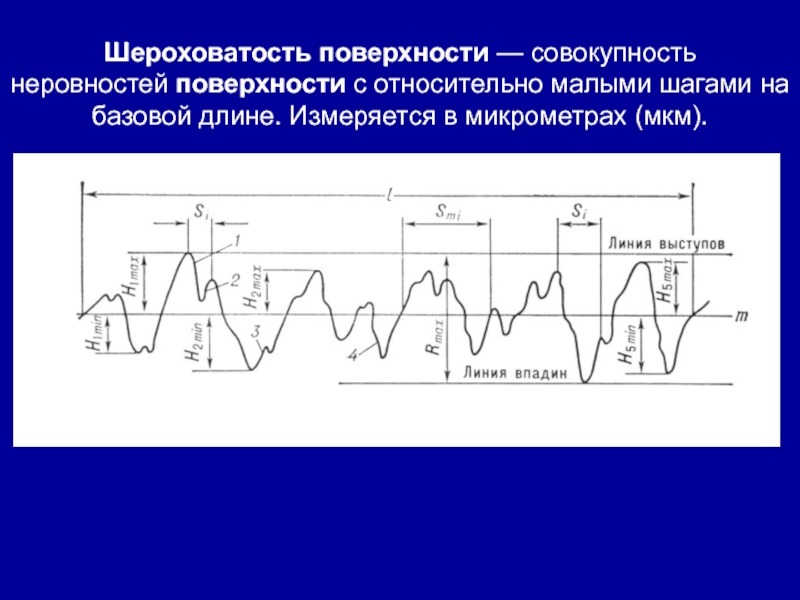
* Размеры для справок.
100
60*
КПГД. 420120.007
Изм. Лист №докум. Подп. Дата
Разраб. Иванов П. И.
1.12.08
Пров.
Петров И.П.
2.12.08
Т.контр.
Н.контр.
Утв.
Взам. инв. № Инв. №дубл.
Подп. и дата
120*
Ra 6,3
Взам. инв. № Инв. №дубл.
Перв. примен.
Подп. и дата
Подп.Справ.
и дата
№
Инв. №подл.
4 отв.
9
Лит.
Крышка
Масса Масштаб
у
–
Лист
1:1
Листов
1
СПбГПУ
гр. 2042
Заготовка КПГД.420120.003
Копировал
Формат
Чертеж доработки.
Требования к шероховатости
остальных поверхностей
обусловлены другим
чертежом (по которому
изготовлялась заготовка). На
этот чертеж должна быть
ссылка в графе «Материалы»
основной надписи.
A5
КПГД. 420120.008
Подп. и дата
КПГД. 420120.007
Инв. №подл.
( )
Ra 3,2
2
КПГД. 420120.008
Изм.
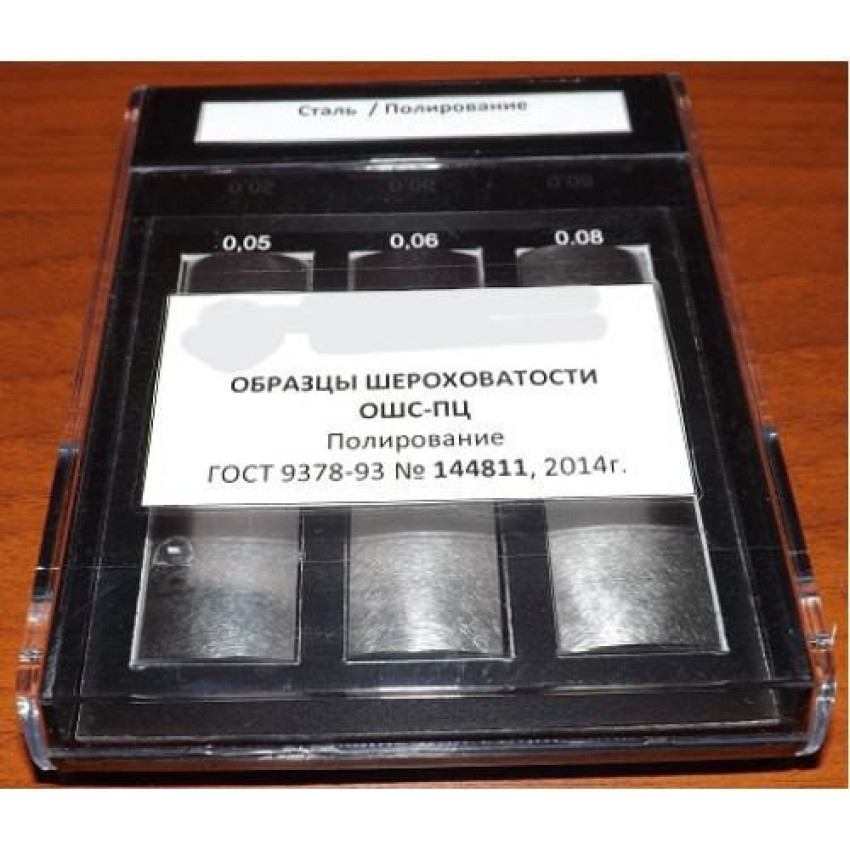
Разраб. Иванов П. И.
1.12.08
Пров.
Петров И.П.
2.12.08
Т.контр.
Н.контр.
Утв.
Винт
Заготовка- винт М6х12
ГОСТ1481- 84
Копировал
Лит.
Масса Масштаб
у
–
Лист
Листов
4:1
СПбГПУ
гр. 2042
Формат
A5
1
Если заготовкой является
стандартное
изделие,
ссылка на стандарт также
приводится
в
основной
надписи чертежа.
1
3
Ra 6,3
ГОСТ 14771- 76- Т1-
27*
8
2
M10•1
M10*
Справ. №
1,6•45
Ra 1,6
35*
25
Ra
6,3
Перв. примен.
КПГД. 420120.100 СБ
2
1,6•45
Инв. №подл.
Подп. и дата
Взам. инв. № Инв. №дубл.
Подп. и дата
150*
* Размеры для справок.
КПГД. 420120.100 СБ
Изм. Лист №докум.
Разраб. Иванов П.И.
Пров.
Петро И.П.
Т.контр.
Н.контр.
Утв.
Подп. Дата
1.

2.12.08
Корпус
Сборочный чертеж
Копировал
Лит.
Масса Масштаб
у
1:1
Лист
Листов
СПбГПУ
гр. 2042
Формат
A4
1
14. На сборочных чертежах
обозначение шероховатости
или знак
в правый
верхний угол чертежа не
выносится (за исключением
особых случаев).
Проставляются размеры и
соответственно
шероховатость поверхностей,
обрабатываемых в процессе
(отверстия под установочные
винты, штифты и т.п.) или
после сборки (отверстия
масляных каналов, резьбы
после сварки и т.д.).
При недостатке места для размещения знаков
шероховатости мелких однотипных элементов
допускается данные о шероховатости
поверхностей приводить в технических
требованиях записью типа:
1. * Размеры для справок.
2. Шероховатость поверхностей фасок –
Ra 6,3.
(на поверхности фасок при этом знаки
шероховатости не ставятся)
Допуски размеров, формы, расположения поверхностей,
волнистость и шероховатость
Предельных отклонений формы и размеров
поверхности деталей
Шероховатость и квалитет таблица
Чтобы достичь заданной точности размеров детали и установить при контроле, действительно ли получен заданный размер, необходимо обеспечить при обработке надлежащий класс шероховатости поверхности.
Необходимая точность обработки, отвечающая требованиям заданного класса точности, достигается на различных станках разными способами.
Точность выполнения размеров определяется квалитетами (в системе ОСТ – классы точности). Квалитет (по стандартам СЭВ – Совет Экономической Взаимопомощи) показывает относительную точность изготовления детали.
В зависимости от величины допуска на размер установлено 19 квалитетов точности (IT01, IT0, IT1, IT2. IT17; IT – Intеrnational Tolerance – международный допуск). IT8 – допуск системы по 8 квалитету ISO (ISO – международная организация по стандартизации).
Практикой определены взаимосвязи между видами обработки и шероховатостью поверхности. Так, например, установлено, что средняя высота неровностей не должна превышать 10-25% от допуска на обработку. Это позволило установить достижимую шероховатость поверхности для различных видов обработки, а с учётом затрат при любом другом способе обработки – и экономически достижимую шероховатость поверхности.
Различные методы обработки по-разному влияют на качество поверхности.
Таблица 1. Характеристики точности и качества, характерные для различных способов обработки резанием
№ п/п | Вид обработки | Точность размеров формы | Качество поверхности |
квалитет | степень точности | Rа мкм | |
Доводка | 3-4 | 0,08-0,01 | |
Суперфиниширование | 3-4 | 0,16-0,01 | |
Хонингование | 3-4 | 0,63-0,01 | |
Полирование | Предшествующ. | Пр.обработка | 0,63-0,02 |
Тонкое точение – строгание – шлифование – фрезерование – растачивание | 5-6 | 5-6 6-7 3-4 6-7 5-6 | 1,25-0,32 6,3-1,2 0,63-0,16 1,6 1,25-0,32 |
Чистовое шлифование – фрезерование – точение -растачивание – строгание -развертывание – зенкерование | 5-6 6-7 5-6 5-7 6-7 | 6-7 8-9 8-9 6-7 9-10 | 1,25-0,63 6,3-3,2 10-1,25 5-2,5 6,3-3,2 1,25-0,32 6,3-3,2 |
Черновое точение – шлифование – растачивание – сверление – зенкерование – развертывание – фрезерование – строгание – долбление | 9-10 7-9 7-9 11-13 10-11 7-9 | 6-7 9-10 13-15 8-10 7-9 9-10 9-10 9-10 | 40-20 2,5-1,25 80-50 25-5 25-12,5 2,5-1,25 50-25 25-12,5 25-12,5 |
Сверление по кондуктору | 11-12 | 8-9 | 25-6,3 |
Координатное растачивание | 4-5 | 1,25-0,32 | |
Нарезание резьбы: метчиком (плашкой) резцом фрезой | 10-5 5-1,25 5-1,6 |
Для достижения заданного взаимного расположения поверхностей, формы и размеров деталей, их шероховатости и физико-механических свойств при производстве машиностроительной продукции применяют различные методы обработки: резание лезвийным и абразивным инструментами; поверхностное пластическое деформирование; электрофизические, электрохимические и другие методы. По мере приближения размера обрабатываемой поверхности к заданному размеру по чертежу обработка заготовки может быть нескольких видов: обдирочная, черновая, получистовая, чистовая, тонкая, отделочная.
Обдирочная обработка применяется для крупных поковок и отливок 16-18-го квалитетов точности. Она уменьшает погрешности формы и пространственных отклонений грубых заготовок, обеспечивая 15-16-й квалитеты точности, шероховатость поверхности Ra больше 100 мкм.
Черновая обработка выполняется в большом диапазоне точности (12-16-й квалитеты). Шероховатость поверхности Ra = 100-25 мкм.
Получистовая обработка применяется для заготовок, к точности которых предъявляются повышенные требования. Этот вид обработки обеспечивает 11-й, 12-й квалитеты точности. Шероховатость поверхности
Ra = 50,0-12,5 мкм.
Чистовая обработка применяется как окончательный вид обработки для тех заготовок, заданная точность которых укладывается в точность, достигаемую чистовой обработкой (8-11-й квалитеты). Шероховатость поверхности обеспечивается в пределах Ra = 12,5-2,5 мкм.
Тонкая обработка применяется для окончательного формирования поверхностей детали и при малых операционных припусках. Шероховатость поверхности находится в пределах значений Ra = 2,5-0,63 мкм.
Отделочная (финишная) обработка используется для получения требуемой шероховатости поверхности детали на точность обработки влияния почти не оказывает. Выполняется, как правило, в пределах допуска предшествующей обработки. Отделочная обработка обеспечивает получение шероховатости поверхности Ra = 0,63-0,16 мкм.
В современном машиностроении наиболее распространены обработка заготовок лезвийным и абразивным инструментами, которые формируют точность и качество поверхностей деталей. Лезвийным инструментом из сверхтвердых материалов можно обрабатывать заготовки с твердостью до 45 HRC, а абразивным инструментом целесообразно выполнять обработку металлов с более высокой твердостью.
Обработка лезвийным инструментом используется как процесс чистовой и тонкой обработки: тонкое точение, тонкое фрезерование, тонкое развертывание, протягивание, прошивание.
Сущность тонкого точения заключается в снятии стружки малого по толщине сечения при больших скоростях резания (100-1000 м/мин): для чугунных заготовок скорость резания составляет 100-150 м/мин; для стальных – 150-250 м/мин; для цветных сплавов – до 1000 м/мин. Подача устанавливается для предварительного хода – 0,15 мм/об, а для окончательного – 0,01 мм/об. Глубину резания принимают 0,2-0,3 и 0,05-0,01 мм соответственно.
Малые по толщине сечения стружки не вызывают больших усилий резания и значительных деформаций технологической системы СПИД, что обеспечивает 6-8-й квалитеты точности (при обработке цветных металлов и сплавов – 5-6-й квалитеты). Шероховатость поверхности у заготовок из черных металлов Ra = 2,50-0,63 мкм; цветных металлов – Ra = 0,32-0,16 мкм.
Тонкое точение применяется перед хонингованием, суперфинишированием, полированием и выполняется на высокооборотных станках (10-15 тыс. мин -1 ). Радиальное биение шпинделя не должно превышать 0,005 мм. Все вращающиеся детали должны быть точно отбалансированы.
Резцы оснащаются твердыми сплавами, алмазом, эльбором и другими режущими материалами с высокой износостойкостью. Тонкое обтачивание обеспечивает допуск размеров 5-80 мкм, овальность и конусообразность не более 3 мкм.
Тонкое фрезерование осуществляется преимущественно торцовыми фрезами при обработке плоских поверхностей. Фрезу устанавливают с уклоном 0,0001, чтобы исключить контакт с поверхностью зубьев, не участвующих в резании. При тонком фрезеровании снимается припуск 0,2-0,5 мм, а отклонение от плоскостности на 1 м длины составляет 0,02-0,04 мм. Шероховатость поверхности Ra= 2,5-0,63 мкм.
Тонкое развертывание обеспечивает высокую точность и малую шероховатость, однако не исправляет положения оси обрабатываемого отверстия, поскольку снимает равномерный припуск по всей поверхности. Тонкое развертывание обеспечивает точность, соответствующую 5-7-му квалитетам, Ra = 1,25-0,63 мкм, и чаще всего выполняется после сверления и зенкерования или чернового и чистового растачивания отверстий.
Протягивание применяется для обработки внутренних и наружных поверхностей. При чистовом протягивании цилиндрических отверстий обеспечивается точность 6-9-го квалитетов (шероховатость поверхности
Ra = 2,50-0,63 мкм), протягивание наружных поверхностей обеспечивает точность 11-го квалитета. Протягивание выполняется на горизонтальных и вертикальных станках, универсальных и специальных полуавтоматах и автоматах.
Прошивание осуществляется специальным инструментом (прошивкой), который проталкивают через обрабатываемое отверстие в заготовке с помощью пресса.
Таблица соотношений значений параметров шероховатости Ra, Rz, Rmax (ГОСТ 2789-73) и классов шероховатости (ГОСТ 2789-59).
Предпочтительные значения параметров шероховатости выделены жирным шрифтом.
Параметры шероховатости | Базовая длина, мм | Классы шероховатости | |
---|---|---|---|
Rz, Rmax, мкм | Ra, мкм | ||
1600 1250 1000 800 630 500 400 |
– – – – – – 100 |
25 | Грубее 1-ого класса |
320 250 200 160 |
80 63 50 40 |
8 | 1-й |
160 125 100 80 |
40 32 25 20 |
2-й | |
80 63 50 40 |
20 16 12,5 10 |
3-й | |
40 32 25 20 |
10 8 6,3 5 |
2,5 | 4-й |
20 16 12,5 10 |
5 4 3,2 2,5 |
5-й | |
10 8 – 6,3 |
2,5 2 1,6 1,25 |
0,8 | 6-й |
6,3 5 4 3,2 |
1,25 1 0,8 0,63 |
7-й | |
3,2 2,5 2 1,6 |
0,63 0,5 0,4 0,32 |
8-й | |
1,6 1,25 1 0,8 |
0,32 0,25 0,2 0,16 |
0,25 | 9-й |
0,8 0,63 0,5 0,4 |
0,16 0,125 0,1 0,08 |
10-й | |
0,4 0,32 0,25 0,2 |
0,08 0,063 0,05 0,04 |
11-й | |
0,2 0,16 0,125 0,1 |
0,04 0,032 0,025 0,02 |
12-й | |
0,1 0,08 0,063 0,05 |
0,02 0,016 0,012 0,01 |
0,08 | 13-й |
0,05 0,04 0,032 0,025 |
0,01 0,008 – – |
14-й |
Таблица параметров шероховатости типовых поверхностей деталей
Параметры шероховатости, мкм | Типовые поверхности и детали |
---|---|
Rz 400 | Поверхности заготовок в состоянии поставки, не прошедшие механической обработки.![]() |
Rz 200 | Нерабочие контуры детали, поверхности после литья, ковки, штамповки. |
Ra 25 | Поверхности деталей под сварные швы. Опорные поверхности пружин сжатия. Опорные поверхности станин, корпусов, лап. Отверстия масляных канатов на силовых валах. |
Ra 12,5 | Несопрягаемые поверхности неответственных деталей: оснований, кронштейнов, корпусов, свободные поверхности крепежных деталей. Отверстия на проход под болты, винты, головки винтов; поверхности пазов под головки болтов, винтов, гаек. Свободные несопрягаемые торцовые поверхности валов, муфт, втулок. Поверхности головок винтов. |
Ra 6,3 | Поверхности деталей, прилегающие к другим поверхностям, но не являющиеся посадочными: опорные плоскости корпусов, кронштейнов, крышек, торцы бобышек. Нерабочие торцы валов, втулок, планок. Торцовые поверхности под подшипники качения. Наружные свободные поверхности зубчатых колес. Канавки, фаски, выточки, зенковки, закругления и т.![]() |
Ra 3,2 | Торцы ответственных валов, втулок, планок, поверхности канавок, выточек, дисков. Несопрягающиеся поверхности зубчатых колес, шлицевых валов и втулок. Рабочие поверхности шпонок и шпоночных пазов; эвольвентные поверхности профиля зуба стальных зубчатых колес. Шаровые поверхности ниппельных соединений, канавки под уплотнительные резиновые кольца подвижных и неподвижных торцовых соединений. |
Ra 1,6 | Поверхности выступающих частей быстровращающихся деталей. Поверхности направляющих. Опорные плоскости реек. Поверхности эвольвенты зуба стальных цилиндрических и конических колес, шлицевых валов, крепежной резьбы нормальной точности. Посадочные поверхности зубчатых колес, червяков. |
Ra 0,8 | Трущиеся поверхности малонагруженных деталей. Посадочные поверхности отверстий и валов под неподвижные посадки. Рабочие поверхности дисков трения. Поверхности резьбы ходовых винтов. Поверхности цилиндров, работающих с манжетами.![]() |
Ra 0,4 | Посадочные поверхности с длительным сохранением заданной посадки: оси эксцентриков, точные червяки, зубчатые колеса. Притираемые поверхности в герметичных соединениях. Поверхности штоков и шеек валов, работающих в уплотнениях. Торцовые поверхности поршневых колец. |
Ra 0,2 | Трущиеся поверхности сильнонагруженных деталей. Поверхности, работающие в условиях трения, например, наиболее ответственные оси и валы повышенной точности; рабочие поверхности коленчатых и распределительных валов быстроходных двигателей; поверхности ответственных цилиндрических и призматических направляющих. |
Ra 0,1 | Поверхности деталей, работающих на трение, от износа которых зависит точность работы механизма. Внутренние поверхности цилиндров поршневых машин, наружные поверхности пальцев поршневых колец, поверхности трения. |
Ra 0,05 | Рабочие шейки валов прецизионных быстроходных станков и механизмов. Рабочие поверхности деталей измерительных приборов в подвижных соединениях средней точности, измерительные поверхности калибров. |
Ra 0,025 | Зеркальные валики координатно-расточных станков, поверхности прецизионных шкал с оптическим отсчетом. |
Ra 0,012 | Зеркальные поверхности концевых мер длины. |
Отверстия под резьбу
Таблица сверл для отверстий под нарезание трубной цилиндрической резьбы.
Размеры гаек под ключ
Основные размеры под ключ для шестигранных головок болтов и шестигранных гаек.
G и M коды
Примеры, описание и расшифровка Ж и М кодов для создания управляющих программ на фрезерных и токарных станках с ЧПУ.
Типы резьб
Типы и характеристики метрической, трубной, упорной, трапецеидальной и круглой резьбы.
Масштабы чертежей
Стандартные масштабы изображений деталей на машиностроительных и строительных чертежах.
Режимы резания
Онлайн калькулятор для расчета режимов резания при точении.
Отверстия под резьбу
Таблица сверл и отверстий для нарезания метрической резьбы c крупным (основным) шагом.
Станки с ЧПУ
Классификация станков с ЧПУ, станки с ЧПУ по металлу для точения, фрезерования, сверления, расточки, нарезания резьбы, развёртывания, зенкерования.
Режимы резания
Онлайн калькулятор для расчета режимов резания при фрезеровании.
Форматы чертежей
Таблица размеров сторон основных и дополнительных форматов листов чертежей.
CAD/CAM/CAE системы
Системы автоматизированного проектирования САПР, 3D программы для проектирования, моделирования и создания 3d моделей.
Чтение чертежей
Техническое черчение, правила выполнения чертежей деталей и сборочных чертежей.
Изначально производство было единоличным делом. Один человек изготавливал какой-либо механизм от начала и до конца, не прибегая к посторонней помощи. Соединения подгонялись в индивидуальном порядке. На одной фабрике невозможно было найти 2 одинаковые детали. Так продолжалось вплоть до середины 18 века, пока люди не осознали эффективность разделения труда. Это дало большую производительность, но следом возник вопрос о взаимозаменяемости изделий. Для этого разработали систему нормирования уровней точности изготовления деталей. В ЕСДП установлены квалитеты (иначе степени точности).
Нормирование уровней точности
Разработка методов стандартизации производства — сюда входят допуски, посадки, квалитеты точности – осуществляется метрологическими службами. Прежде чем приступить непосредственно к их изучению, нужно понимать смысл слова «взаимозаменяемость». Что скрывается под этим определением?
Взаимозаменяемость — это свойство деталей собираться в единый узел и выполнять свои функции без проведения их механической обработки. Условно говоря, одна деталь изготавливается на одном заводе, другая на втором, и при этом они могут быть собраны на третьем и подходить друг к другу.
Целью такого разделения является повышение производительности, которое образуется в силу следующих причин:
- Развитие кооперирования и специализации. Чем более разнообразна номенклатура производства, тем больше времени необходимо для наладки оборудования под каждую конкретную деталь.
- Сокращение разновидностей инструмента. Меньшее количество типов инструмента также повышает эффективность изготовления механизмов. Происходит это по причине сокращения времени на его замену в процессе производства.
Понятие о допуске и квалитете
Понять физический смысл допуска без введения термина «размер» затруднительно. Размер — это физическая величина, характеризующая расстояние между двумя точками, лежащими на одной поверхности. В метрологии существуют следующие его разновидности:
- Действительный размер получается непосредственным измерением детали: линейкой, штангенциркулем и прочим мерительным инструментом.
- Номинальный размер показан непосредственно на чертеже. Он является идеальным с точки зрения точности, так что получение его в реальности является невозможным в силу наличия определенной погрешности оборудования.(+1).
Диаметр 14 является номинальным размером, «+1» – верхним предельным отклонением, а «-1» – нижним предельным отклонением. Тогда вычитание из верхнего предельного отклонения нижнего даст нам значение допуска вала. То есть в нашем случае он составит +1- (-1) = 2.
Все размеры допусков стандартизированы и объединены в группы – квалитеты. Иными словами, квалитет показывает точность изготовляемой детали. Всего существует 19 таких групп или классов. Схема их обозначения представлена определенной последовательностью чисел: 01, 00, 1, 2, 3. 17. Чем точнее размер, тем меньший квалитет он имеет.
Таблица квалитета точности
Числовые значения допусков Интервал
номинальных
размеров
ммКвалитет 01 1 2 3 4 5 6 7 8 9 10 11 12 13 14 15 16 17 18 Св. До мкм мм 3 0.3 0.5 0.8 1.2 2 3 4 6 10 14 25 40 60 0.10 0.14 0.25 0.40 0.60 1.00 1.40 3 6 0.4 0.6 1 1.5 2.5 4 5 8 12 18 30 48 75 0.12 0.18 0.30 0.48 0.75 1.20 1.80 6 10 0.4 0.6 1 1.5 2.5 4 6 9 15 22 36 58 90 0.15 0.22 0.36 0.58 0.90 1.50 2.20 10 18 0.5 0.8 1.2 2 3 5 8 11 18 27 43 70 110 0.18 0.27 0.43 0.70 1.10 1.80 2.70 18 30 0.6 1 1.5 2.5 4 6 9 13 21 33 52 84 130 0.21 0.33 0.52 0.84 1.30 2.10 3.30 30 50 0.6 1 1.5 2.5 4 7 11 16 25 39 62 100 160 0.25 0.39 0.62 1.00 1.60 2.50 3.90 50 80 0.8 1.2 2 3 5 8 13 19 30 46 74 120 190 0.30 0.46 0.74 1.20 1.90 3.00 4.60 80 120 1 1.5 2.5 4 6 10 15 22 35 54 87 140 220 0.35 0.54 0.87 1.40 2.20 3.50 5.40 120 180 1.2 2 3.5 5 8 12 18 25 40 63 100 160 250 0.40 0.63 1.00 1.60 2.50 4.00 6.30 180 250 2 3 4.5 7 10 14 20 29 46 72 115 185 290 0.46 0.72 1.15 1.85 2.90 4.60 7.20 250 315 2.5 4 6 8 12 16 23 32 52 81 130 210 320 0.52 0.81 1.30 2.10 3.20 5.20 8.10 315 400 3 5 7 9 13 18 25 36 57 89 140 230 360 0.57 0.89 1.40 2.30 3.60 5.70 8.90 400 500 4 6 8 10 15 20 27 40 63 97 155 250 400 0.63 0.97 1.55 2.50 4.00 6.30 9.70 500 630 4.5 6 9 11 16 22 30 44 70 110 175 280 440 0.70 1.10 1.75 2.80 4.40 7.00 11.00 630 800 5 7 10 13 18 25 35 50 80 125 200 320 500 0.80 1.25 2.00 3.20 5.00 8.00 12.50 800 1000 5.5 8 11 15 21 29 40 56 90 140 230 360 560 0.90 1.40 2.30 3.60 5.60 9.00 14.00 1000 1250 6.5 9 13 18 24 34 46 66 105 165 260 420 660 1.05 1.65 2.60 4.20 6.60 10.50 16.50 1250 1600 8 11 15 21 29 40 54 78 125 195 310 500 780 1.25 1.95 3.10 5.00 7.80 12.50 19.50 1600 2000 9 13 18 25 35 48 65 92 150 230 370 600 920 1.50 2.30 3.70 6.00 9.20 15.00 23.00 2000 2500 11 15 22 30 41 57 77 110 175 280 440 700 1100 1.75 2.80 4.40 7.00 11.00 17.50 28.00 2500 3150 13 18 26 36 50 69 93 135 210 330 540 860 1350 2.10 3.30 5.40 8.60 13.50 21.00 33.00 Понятие посадки
До этого мы рассматривали точность одной детали, которая задавалось только допуском. А что будет с точностью при соединении нескольких деталей в один узел? Как они будут взаимодействовать друг с другом? И так, здесь необходимо ввести новый термин «посадка», который будет характеризовать расположение допусков деталей друг относительно друга.
Подбор посадок производится в системе вала и отверстия
Система вала — совокупность посадок, в которых величина зазора и натяга подбирается за счет изменения размера отверстия, а допуск вала остается неизменным. В системе отверстия все наоборот. Характер соединения определяется подбором размеров вала, допуск отверстия считается постоянным.
В машиностроении 90% продукции производится в системе отверстия. Причина этому служит боле сложный процесс изготовления отверстия с технологической точки зрения, по сравнению с валом. Система вала применяется при возникновении затруднений обработки наружной поверхности детали. Ярким примером этого являются шарики подшипника качения.
Все виды посадочных соединений регулируются стандартами и также имеют квалитеты точности. Целью такого разделения посадок на группы является повышение производительности за счет увеличения эффективности взаимозаменяемости.
Виды посадок
Тип посадки и ее квалитет точности выбирают, исходя из условий работы и способа сборки узла. В машиностроении разделяют следующие их разновидности:
- Посадки с зазором — соединения, которые гарантированно образуют зазор между поверхностью вала и отверстия. Обозначают их буквами латиницы: A, B…H. Они применяются в узлах, в которых детали «ходят» относительно друг друга и при центрировании поверхностей.
- Посадки с натягом — соединения, в которых допуск вала перекрывает допуск отверстия, в результате чего образуются дополнительные напряжения сжатия. Посадка с натягом относится к не разборным типам соединения. Они применяются в высоко нагруженных узлах, главным параметром которых является прочность. Это – крепление на вал уплотнительных металлических колец и седел клапанов головки блока цилиндров, установка крупных муфт и шпонок под шестеренок и т.д и т.п. Посадку вала на отверстие с натягом производят двумя способами. Наиболее простой из них это — запрессовывание. Вал центрируют по отверстию, а затем ставят под пресс. При большем натяге используют свойства металлов расширяться при воздействии на них повышенных температур и ссужаться при понижении температуры. Этот метод отличается большей точностью сопряжения поверхностей. Непосредственно перед соединением вал предварительно охлаждают, а отверстие нагревают. Далее производят установку деталей, которые по истечению некоторого времени возвращают свои прежние размеры, образуя тем самым нужную нам посадку с зазором.
- Переходные посадки. Предназначены для неподвижных соединений, которые часто подвержены разборке и сборке (например, при ремонте). По своей плотности они занимают промежуточное положение среди разновидностей посадок. Данные посадки имеют оптимальное соотношение точности и прочности соединения. На чертеже обозначаются буквами k, m, n, j. Ярким примером их применения является посадка внутренних колец подшипника на вал.
Обычно использование той или иной посадки указано в специальной технической литературе. Мы просто определяем тип соединения и выбираем нужный нам тип посадки и квалитет точности. Но стоит отметить, что в особо ответственных случаях стандартом предусмотрен индивидуальный подбор допуска сопрягаемых деталей. Производится этой с помощью специальных расчетов, указанных в соответствующих методологических пособиях.
Измеритель шероховатости. Измерение профиля и параметров шероховатости Ra, Rz, Rm, Sz древесины и древесных материалов
1.1. Назначение изделия.
1.1.1. Профилометр-профилограф ПМД2-100 ТУ 3943-004-12013730-2009 (в дальнейшем прибор или изделие) предназначен для контактного измерения профиля и параметров шероховатости поверхности по системе средней линии в соответствии с номенклатурой параметров и диапазонами значений, предусмотренными ГОСТ 2789-73 в лабораторных и цеховых условиях.
1.1.2. Профилометр – профилограф ПМД2-100 предназначен для контактного измерения профиля и параметров шероховатости поверхности изделий из древесины и древесных материалов в соответствии с номенклатурой параметров и диапазонами значений, предусмотренными ГОСТ 7016-82 в лабораторных и цеховых условиях деревообрабатывающих предприятий. Измерение параметров шероховатости производится по системе средней линии.
1.1.3. Профилометр – профилограф ПМД2-100 предназначен для измерения при следующих условиях:
– температура окружающего воздуха (10-35) ˚С;
– относительная влажность (45-80) %;
– внешняя вибрация не должна превышать значения, при котором при неподвижном датчике показание профилометра по параметру Ra составляет 0,3 нижнего предела диапазона, а размах колебаний пера профилографа при максимальном увеличении составляет 2 мм.
1.2. Технические характеристики.
1.2.1. Измеряемые параметры шероховатости Ra, Rm, Rz, Sz
1.2.2. Диапазон измерений параметра Ra датчиком (щупом) № 2 0,025…100 мкм
1.2.3. Диапазон измерений параметров Rz, Rm датчиком (щупом) № 1 2,5…400 мкм
датчиком № 2 0,1…400 мкм
1.2.4. Диапазон измерения параметра Sz датчиком № 1 0,025…12,5 мм
1.2.5. Пределы поддиапазонов измерения в соответствии с таблицей 1.
Таблица 1
Измеряемая величина
Ra
Rz,Rm
Sz
Пределы измерения
0,025… 0,4 мкм
0,4…3,2 мкм
3,2…12,5 мкм
12,5…100 мкм
0,1…1,6 мкм
1,6…12,5 мкм
12,5…50 мкм
50…400 мкм
0.025…8 мм
1.2.6. Предел допускаемой основной погрешности DRa, D Rmax, DRz для профиля близкого к трапецеидальному, с шагом не превышающим ¼ базовой длины при измерении параметров шероховатости Ra, Rmax, Rz определяют по формулам:
DRa = 0,02*Raв.п + 0,04*Ra, (1.2.1)
DRm =0,03*Rmв.п + 0,05*Rm, (1.2.2)
DRz = 0,03*Rzв.п + 0,05*Rz, (1.2.3)
где Raв.п, Rmв.п, Rzв.п – верхний предел поддиапазона по параметрам Ra, Rm, Rz соответственно.
1.2.7. Предел допускаемой основной погрешности DSz профилометра при измерении параметра шероховатости Sz определяют по формуле:
DSz = 0,02*Sz в.п + 0,10*Sz, (1.2.4)
где – Sz в.п верхний предел поддиапазона по параметру Sz.
1.2.8. Номинальные значения вертикального увеличения: 100; 200; 500;1000; 2000; 5000; 10000; 20000. 50000;
100000; 200000
1.2.9. Предел допускаемой основной погрешности DУ профилографа на профиле, близком к трапециидальному, определяют по формуле:
DУ = 0,02* Ув.п + 0,03*У (1.2.5)
где Ув.п – верхний предел поддиапазона, соответствующий выбранному значению вертикального увеличения;
У- максимальная по абсолютному значению ордината профиля по профилограмме.
1.2.10. Номинальные значения горизонтальных увеличений: 1; 2; 5; 10; 50, 100; 200; 500; 1000; 2000, 5000
1.2.11. Допускаемое отклонение горизонтальных увеличений
от номинальных значений, не более ± 5%
1.2.12. Размер области печати профилограммы для листа А4
по координате Х, не менее 220 мм,
по координате У, не менее ± 50 мм
1.2.13 Максимальная длина трассы ощупывания 80 (12,5; 40) мм
1.2.14. Значение отсечек шага 0,08; 0,25; 0,8; 2,5; 8,0 мм
1.2.15. Скорость перемещения измерительного щупа 1 мм/сек ± 3%; 0,32 мм/сек ± 5%
1.2.16. Радиус кривизны вершины иглы датчика № 1 (1,5 ± 0,1) мм
1.2.17. Измерительное усилие иглы датчика № 1, не более 0,016 Н
1.2.18. Радиус кривизны вершины иглы датчика № 2 5 (2;10) мкм
1.2.19. Измерительное усилие иглы датчика № 2, не более 0,004 (0,0007) Н
1.2.20. Усилие воздействия опоры, не более 0.5 Н
1.2.21. Шероховатость опоры Rz, не более 0,1 мкм
1.2.22. Вид отсчета результатов измерения цифровой
1.2.23. Максимальная разрешающая способность 0,001 мкм
1.2.24. Напряжение питания 6 В ±10%,
1.2.25. Потребляемая мощность, не более 2,5 вт
1.2.26. Габаритные размеры (без учета датчика) длина*высота*ширина, не более . 185(120)*55*35 мм,
габаритные размеры датчика, не более 100*15*15 мм
1.2.27. Масса профилометра – профилографа ПМД2-100 с установленным измерительным щупом, не более 1,0 кг
1.2.28. Температура окружающего воздуха 10-35 °С
1.2.29. Относительная влажность (45-80)%
1.2.30. Класс защиты от поражений электрическим током III по ГОСТ 12.2.007.0-75.
1.2.31. Степень защиты от пыли и влаги IP30 по ГОСТ 14254 – 96.
Варианты конструкции сменных щупов для профилометра-профилографа ПМД2-100 представлены здесь.
1. Профилометр – профилограф ПМД2-100. Общий вид, щуп выдвинут.
2. Профилометр – профилограф ПМД2-100. Общий вид, щуп задвинут.
3. Профилометр – профилограф ПМД2-100. Главная форма программы.
Подключение к компьютеру производится через последовательный интерфейс RS232 или USB. Компьютер может быть любым ноутбук, нетбук, планшет. Возможна поставка прибора с планшетом в общем кейсе.
Демонстрационную версию профилографа можно скачать здесь 1_pmd2_100. Скачанный файл разархивировать в папку «1_pmd2_100» на диске «D». Запустите исполняемый файл (приложение). В открывшейся главной форме нажмите кнопку «Повтор» на дисплей выведется сохраненный профиль. Устанавливая различные параметры измерения, и нажимая на «Повтор» можно посмотреть возможности профилографа. Для просмотра требуется компьютер c Windows 7 (98, 2000, XP, Vista).
4. Профилометр-профилограф ПМД2-100 в упаковке
Перейти на главную страницу сайта
Что такое шероховатость валка? 5 Roll Ra’s и почему они важны
Шероховатость поверхности валка – важный параметр, который следует учитывать при создании различных продуктов. Слишком гладкая поверхность может вызвать проблемы, а слишком шероховатая поверхность также может вызвать проблемы. При описании шероховатости поверхности можно использовать множество различных единиц для справки. Эти значения определяются на основе микровыступов по длине поверхности. Мы всегда видим значение поверхности для валка, но почему мы выбираем эти значения шероховатости? После обсуждения того, что придает валку значение шероховатости, мы приведем пять примеров валков, требующих различной шероховатости ».Шероховатость поверхности
Что такое шероховатость поверхности?
Шероховатость поверхности, как определил Кейнс, – это форма, которая имеет множество выступов и впадин вдоль формы. Если бы человек посмотрел на поверхность материала в микроскоп, он бы увидел топографический вид этих пиков и впадин. Поверхность с большим изменением амплитуды будет иметь более грубую текстурированную поверхность, тогда как меньшее изменение будет более гладким. Путем определения номинальной оси для этих пиков и впадин, которые будут измеряться, этим точкам могут быть присвоены числовые значения.Что такое общая единица измерения шероховатости поверхности?
Существует множество различных единиц измерения шероховатости поверхности, но средняя шероховатость, или Ra, обычно используется для стандартной металлической отделки. Ra всегда является положительным числом и рассчитывается путем взятия абсолютных средних отклонений на линейном расстоянии. Большее количество отклонений приведет к большему числу Ra!Еще немного технических подробностей для расчета Ra:
Как отмечено в Mikell P.В учебнике Грувера Принципы современного производства, 5-е издание, математическое уравнение для среднего значения шероховатости:
Где:
Ra = Среднее значение шероховатости
y = вертикальное расстояние от заданного номинала
Lm = длина серии коллекцийЭто уравнение можно упростить, что позволяет получить более концептуальное представление:
Где:
n = n-я позиция по длине профиля
y i = Вертикальное расстояние в n-й позиции
Рисунок 1 дает более наглядное представление о том, что происходит в процессе сбора данных.
По длине профиля, Lm, имеется n-е количество отклонений по высоте, собранных вдоль
длина профиля. Эти отклонения собираются (по абсолютной величине) и суммируются. Среднее значение этих значений дает окончательное число Ra. Он может отображаться как в микрометрах, так и в микродюймах – в зависимости от возможностей используемого измерительного инструмента.
Рисунок 1: Отклонения профиля, характеризующие шероховатость поверхностиRa и RMS:
Другой распространенной единицей шероховатости, которую можно встретить в промышленности, является среднее значение
. в квадрате или RMS.Оба метода дают представление о шероховатости, однако RMS по своей природе будет иметь большее число, чем Ra. При вычислении среднеквадратичного значения любое большое отклонение пика может привести к завышению значения, поэтому обычно предпочтительнее Ra. Перейдите по этой ссылке, чтобы узнать больше о разнице между Ra и RMS.
Пять валков различной шероховатости
1. Вальцы для измельчения (130-150)
Шероховатость является важной характеристикой вальцов для измельчения семян в процессе производства масла из семян.Когда масло из семян обрабатывается с помощью набора валков, они сплющиваются и режутся до идеально толстых хлопьев. Если хлопья слишком толстые, все масло не будет удалено с бобов. Более грубый валок необходим для соответствующей обработки хлопьев, что приведет к Ra от 130 до 150.
Аналогичное Ra: разделительная полка (гранулированная текстура)
2. Рулоны войлока мокрого конца бумагоделательной машины (30-50)
Рулоны войлока мокрого конца бумагоделательной машины обычно имеют значение Ra в пределах 30-50.Эти валки используются для поддержки вращающегося влажного войлока, которое переносит бумажную массу в секцию пресса. Наличие валков между 30 Ra и 50 Ra дает достаточно шероховатости, чтобы сукно могло тянуться вдоль валка, не вызывая проскальзывания. Однако слишком высокая шероховатость может вызвать избыточное трение между ними, что может повредить войлок.
Similar Ra: контейнер для сливок для кофе (гладкая, восковая текстура)
3. Резиновые ролики прессовой секции (10-20)
Ролики прессовой секции – это большие ролики, которые используются для выдавливания воды из бумаги.Когда бумажные волокна попадают в прессовую секцию, продукт обычно на 75% состоит из воды по сравнению с 25% волокна. Прижимные валки используются для сжатия волокон вместе, что имеет решающее значение для характеристик прочности бумаги и снижения процентного содержания воды. Там, где прижимные валки контактируют с бумагой, шероховатость поверхности имеет решающее значение для гладкости продукта.
Аналогичный Ra: шкаф для документов (блеск, гладкая текстура)
4. Каландровая секция (2-5)
Важность каландровых валков бумагоделательной машины заключается в конечных печатных характеристиках продукта.Для бумаги потребуется определенное качество поверхности, которое зависит от того, для чего будет использоваться конечный продукт. Будь то картон или бумага для принтера, необходима надлежащая отделка рулона, чтобы обеспечить наилучший контроль для соответствия характеристикам толщины и гладкости.
Аналогичное значение Ra: Доска (очень гладкая текстура)
5. Покрытия / клеи (0.5-2) Окно
В некоторых процессах клеи наносятся на основной лист с помощью хромового дозирующего валика.Однородность покрытия имеет решающее значение с точки зрения стоимости и качества. Слишком грубый рулон может привести к прилипанию клея на рулоне, что в некоторых местах приведет к избытку или отсутствию материала. Это может привести к потере клея в производственном процессе или к переработке продукта, который может потребоваться переработка из-за проблем с качеством. Равномерно гладкая шероховатость поверхности дозирующего вала позволяет использовать минимальное количество клеящего материала, обеспечивая при этом продукт безупречного качества.
Аналогичное значение Ra: стеклянное окно (очень гладкое, очень небольшая шероховатость)
Не уверены, какой должна быть шероховатость ваших валков? Обратитесь в Precision Roll Grinders для получения бесплатной консультации о валках, используемых в вашем производственном процессе!
Советы по измерению шероховатости: 2- vs.5 микрон
Я написал три статьи об измерении шероховатости боковой поверхности зубчатого колеса для этого журнала (материалы имеют значение; январь 2016 г. и февраль 2016 г., а также тематическая статья в январе 2019 г.). В этих статьях приводятся инструкции по настройке и измерению параметров шероховатости (Ra, Rz, Rmr и т. Д.), Полная диаграмма шероховатости, необходимая для определения шероховатости на чертеже шестерни (галочка), и профилометр контактного щупа в цехе.Целью этих статей было дать читателю общее представление о шероховатости и ее измерении, чтобы можно было проводить надежную и воспроизводимую профилометрию боковых поверхностей зубчатых колес в цехе.
Итак, как насчет следующей статьи о советах по измерению шероховатости? С другой стороны, как насчет нескольких статей с советами? Подожди, говоришь ты! Если бы я правильно выполнил свою работу в своих предыдущих колонках, зачем вам несколько статей с советами по шероховатости?
Что ж, я не говорю о прагматичной цеховой мудрости о грубости или народных историях о профилометрии.Я говорю о контактном игле, в частности о игле с алмазным наконечником 2 или 5 микрон. По определению, наконечник размером 2 или 5 микрон означает радиус конусообразного алмаза, установленного под углом 90 градусов к плоскости иглы. На рисунке 1 показан пример алмазного наконечника 2 микрона.
Рис. 1. Алмазный наконечник с радиусом 2 микрона.Этот наконечник касается измеряемой боковой поверхности и является наиболее чувствительным компонентом в очень надежной измерительной системе. Очевидно, наконечник размером 2 микрона намного более хрупкий и дорогостоящий по сравнению с наконечником размером 5 микрон.Так что было бы здорово, если бы все производители шлифовального оборудования могли использовать наконечники с 5 микронами. К счастью, только для измерения волнистости поверхности вы используете «бесскидный» зонд. Для измерения R-параметров можно использовать скользящий зонд. Зонды без салазок более хрупкие, чем зонды с салазками. Во всех примерах, обсуждаемых ниже, в щупах обоих размеров использовались более прочные подвижные зонды. Тем не менее, 2-микронный зонд на полозьях все еще очень хрупкий и дорогой. Было бы желательно свести к минимуму его использование в цехе.
В следующих статьях этой серии, посвященных «советам», будет обсуждаться использование площадок для калибровки профилометров и проверка состояния иглы с алмазным наконечником.
2-микронные насадки против 5-микронных наконечников
Сегодня прецизионные шлифованные шестерни обычно имеют Ra от 0,2 мкм до 0,8 мкм. Суперфинишированные шестерни будут еще плавнее. Таким образом, для точного измерения шероховатости боковой поверхности зубчатого колеса, как правило, следует использовать тонкий 2-микронный наконечник. Однако здесь есть немного места для маневра. ISO-3274 отмечает, что для поверхностей с Ra> 0.5 мкм и <2 мкм можно использовать наконечник 5 мкм без значительных различий в результатах измерений. Точно так же, если все стороны согласны, и это задокументировано в диаграмме с галочкой или на чертеже шестерни, использование 5-микронного наконечника допустимо на поверхностях с Ra <0,5 мкм в определенных пределах. См. ниже.
Приведет ли 5-микронный наконечник, используемый на боковой поверхности с Ra> 0,5 и <2 мкм, к значительно отличающимся результатам шероховатости по сравнению с 2-микронным наконечником? Что касается характеристик зубчатой передачи, будут ли различия в результатах измерений соответствовать разнице в характеристиках зубчатой передачи, связанной, например, со смазкой или поверхностным повреждением? Давайте сначала посмотрим на разницу в результатах измерения шероховатости, а затем обсудим влияние на характеристики шестерни.
Сравнение шероховатости; Ra 0,3 – 0,4 мкм
Я участвовал в крупном исследовании, в ходе которого были проведены сотни измерений по бокам аналогичных прецизионных шлифованных зубчатых колес с использованием щупов с наконечником 2 и 5 микрон. Характеристики чистовой обработки боковых сторон зуба были Ra <0,5 мкм.
Все измерения были выполнены в соответствии со спецификациями ISO. Измерения на зубчатых колесах проводились на идентифицированных боковых сторонах и многократные измерения шероховатости на каждой боковой поверхности. Усредненные измерения шероховатости приведены в таблице 1.
Таблица 1: Измерения, сравнивающие шероховатость с размером наконечника.В зависимости от используемых методов обработки я ожидаю, что шероховатость боковой поверхности шлифованного зуба будет варьироваться на 20 процентов от одной области к другой на отдельном зубе или от зуба к зубу на шестерне, или от шестерни к шестерне в серийном производственном цикле. Различия в результатах таблицы 1 указывают на хорошо отшлифованные зубчатые колеса с очень стабильной обработкой боковых поверхностей. Что касается производительности, это промышленные редукторы, работающие при установившихся нагрузках и скоростях.Я бы предсказал равные характеристики с точки зрения смазки или поверхностного повреждения, если бы представил результаты шероховатости в таблице 1.
В этом случае шероховатость боковой поверхности обоих щупов варьировалась от Ra> 0,34 до <0,41 мкм и считалась очень постоянной. Результаты измерения шероховатости незначительны при использовании наконечника 5 микрон по сравнению с наконечником 2 микрона. Кроме того, не было предсказано никакой разницы в разнице в характеристиках передач. Вывод: задокументируйте тип иглы и используйте наконечник 5 микрон на этих зубчатых колесах.
Более гладкая боковая поверхность
Как насчет поверхности, более гладкой, чем Ra <0,3 мкм? Помните, что точное шлифование теперь обычно достигает Ra ~ 0,15–0,25 мкм. В таких условиях возникает соблазн подтолкнуть к использованию более прочного 5-микронного зонда. Будет ли существенная разница в измерении шероховатости при использовании 2-микронного или 5-микронного наконечника на такой идеально обработанной поверхности? Насколько велика разница и может ли она повлиять на работу редуктора?
В одном исследовании зубчатых колес, предназначенных для обработки Ra <0.15 мкм возникла проблема, связанная с результатами измерения шероховатости боковых поверхностей, и были поставлены под сомнение характеристики зубчатого колеса. Первоначальные испытания готовых шестерен показали случайные задиры, которые не прогнозировались и были недопустимыми. Условиями эксплуатации считались высокая нагрузка и высокая скорость.
Испытания зубчатых колес были остановлены, и после того, как было обнаружено, что шероховатость некоторых зубчатых колес была измерена на шероховатость с помощью щупа с 5-микронным наконечником, была проведена повторная обработка поверхности. Результаты по шероховатости усреднены в таблице 2.Все измерения проводились в соответствии со спецификациями ISO, за исключением того, что в одном профилометре использовался наконечник 2 микрона, а в другом – наконечник 5 микрон.
Таблица 2: Измерения, сравнивающие размер наконечника.В приведенном выше случае размер наконечника показывает значительную разницу в измеренной шероховатости поверхности. Кроме того, при тестировании шестерни время от времени испытывали задиры. Решение состояло в том, чтобы восстановить зубчатые колеса до указанного качества обработки боковой поверхности с Ra <0,15 мкм, используя 2-микронный наконечник для измерения шероховатости боковой поверхности. Возобновление тестирования дало приемлемые результаты.В этом случае разница в радиусе наконечника была значительной, поскольку можно было точно измерить шероховатость боковой поверхности и спрогнозировать работу зубчатой передачи.
Заключение
Есть точка в степени гладкости, где использование наконечника 2 микрона может дать существенную разницу по сравнению с наконечником радиусом 5 микрон. Более того, в таких условиях эксплуатации, как высокая скорость и высокая нагрузка, эта разница может быть существенной при прогнозировании характеристик редуктора. Для обработки боковой поверхности с Ra <0 рекомендуется использовать наконечник 2 микрона.3 мкм.
Параметры профиля шероховатости поверхности
ПАРАМЕТРЫ ПРОФИЛЯПараметр Имя Ra Средняя шероховатость (Ra) Rq Среднеквадратическое значение (RMS) Шероховатость РТ Максимальная высота профиля Rv, Rm Максимальная глубина впадины профиля Максимальная высота пика профиля об / мин Средняя максимальная высота пика профиля Rz Средняя максимальная высота профиля Rмакс Максимальная глубина шероховатости Rc Средняя высота неровностей профиля Rz (ISO) Высота шероховатости Ry Максимальная высота профиля Вт, Вт Высота волнистости S Среднее расстояние между локальными пиками профиля Sm, RSm Среднее расстояние между неровностями профиля D Пиковая плотность профиля ПК Пиковое количество (пиковая плотность) HSC Подсчет высоких точек la Средняя длина волны профиля лк Среднеквадратичная длина волны профиля Да Средний абсолютный наклон Dq Среднеквадратичный наклон (RMS) Lo Длина развернутого профиля лр Соотношение длины профиля Rsk, Sk Асимметрия Определения шероховатости поверхности:
- Ra: Ra – среднее арифметическое абсолютных значений ординат профиля шероховатости.Также известен как среднее арифметическое (AA), среднее значение средней линии (CLA). Средняя шероховатость – это площадь между профилем шероховатости и его средней линией или интеграл абсолютного значения высоты профиля шероховатости по оценочной длине
- Rz: Rz – среднее арифметическое значение одиночных глубин шероховатости последовательных длин выборки. Z – это сумма высоты самых высоких пиков и самой низкой глубины впадины в пределах длины выборки.
- Отсечка λ c: профильного фильтра определяет, какие длины волн относятся к шероховатости, а какие – к волнистости.
- Длина выборки: является эталоном для оценки шероховатости. Его длина равна длине волны отсечки.
- Длина обхода: – это общая длина, пройденная щупом при получении начерченного профиля.Это общая продолжительность поездок до поездки, продолжительности оценки и после поездки
- Длина оценки: – это часть длины перемещения, из которой определяются значения параметров поверхности.
- Pre-Travel: первая часть длины перемещения.
- Post-Travel: Последняя часть длины перемещения
Выбор отсечки λ c
Профиль Отсечка Длина выборки / оценки Rz (мкм) Ra (мкм) λc (мм) л / л (мм) До.1 До 0,02 .08 .08 / .4 Более 0,1
до 0,5Более 0,02
вплоть до .1,25 ,25 / 1,25 Более 0,5
до 10Более 0,1 наверх 2 ,8 .8/4 Более 10
до 50От 2 до 10 2,5 2,5 / 12,5 Более 50
до 200Более 10 до 80 8 8/40 Качество отделки поверхности – Ra, Rz, Rt Измерение шероховатости поверхности и чистовая обработка Качество обработки Точность Аспекты производственной притирки Время простоя Полировальный стол Расчет цены за единицу Измерение Лазерный прибор для измерения плоскостности Проверка рабочей плиты Какие типы заготовок притираются? Алмазная притирка
Качество обработки поверхности
При заданном размере зерна и вязкости жидкости изменение давления притирки приводит к большему или меньшему съему материала скорость, более толстая или более тонкая пленка и более грубая или более тонкая поверхность.Поэтому на практике давление обычно небольшое в начале процесса, увеличивается по мере выполнения работы и уменьшается к концу. Это приводит к оптимальной скорости съема материала, чистоте поверхности и плоскостности, достигая идеального качества отделки поверхности. Волнистость (также известная как пики и впадины) – это расчет неровностей поверхности с интервалом, превышающим шероховатость поверхности. Обычно это происходит из-за деформации, вибрации или прогиба в процессе обработки.
Размер зерна и чистота поверхности
В качестве примера, на стальной детали с закалкой до 60 HRc, притертой с использованием карбида кремния 500, давление 250 г / см в квадрате даст чистоту поверхности около Ra = 0,2 мкм (N4 ) или Rz 0,6-0,8, тогда как при снижении давления до 50 г / см в квадрате можно получить шероховатость поверхности около Ra = 0,05 мкм (N2) или Rz 0,2-0,3. Взаимосвязь между размером зерна и чистотой поверхности неразрывно связана друг с другом.
Чтобы подчеркнуть, шероховатость поверхности определяется мельчайшими изменениями высоты поверхности данного материала или заготовки.Средняя дисперсия пиков и спадов (значение Ra) или количественная оценка наибольшей разницы между пиками и впадинами (Rz). Шероховатость обычно выражается в микронах. Поверхность с Ra, равным 8, состоит из наивысшего пика и впадин, которые в среднем не превышают 8 мкм на заданном расстоянии. Шероховатость также может быть измерена путем сравнения поверхности заготовки с известным образцом.
Международные стандарты чистоты поверхности (DIN 4762, 4768, ISO 4287 / 1-2. 4288) применяются аналогичным образом, так как качество отделки поверхности указывается в значениях Ra или даже в более точных значениях Rt.На практике также указывается более реалистичное значение Rz, которое определяется путем усреднения 5 отдельно измеренных значений Rt. Подходящее измерительное оборудование для получения этих значений в настоящее время коммерчески доступно (Рисунок 54).
Плоские поверхности и показания
Ra – это целое среднее всех абсолютных отклонений профиля шероховатости от средней линии в пределах измеренной длины. Rz – это абсолютное среднее значение от пика до впадины пяти последовательных длин выборки в пределах измеряемой длины.Ra сравнивает все размеры и не имеет никакого значения, когда дело доходит до отделения брака от подходящих цилиндров.
Рисунок 46: Среднее арифметическое значение шероховатости RaСреднее арифметическое значение шероховатости Ra (DIN 4768) – это среднее арифметическое всех значений профиля шероховатости R в пределах расстояния измерения lm. Следовательно, он определяет среднее отклонение этого профиля поверхности от средней линии.
Рисунок 47: Максимальная высота от пика до впадины RtМаксимальная высота от пика до впадины Rt (DIN 4748) – это расстояние по вертикали между самым высоким пиком и самым низким пиком профиля шероховатости R в пределах общего расстояния измерения lm.Другими словами, это разница высот между самой высокой горой и самой низкой долиной в пределах измеренного диапазона.
Рисунок 48: Средняя глубина шероховатости RzСредняя глубина шероховатости Rz (DIN 4768) – это среднее значение индивидуальной глубины шероховатости пяти человек, измеряющих расстояния последовательно. Другими словами, расчет ведется по пяти значениям Rt. Отклонение от средней линии, особенно с акцентом на самый высокий пик и впадину.
Рисунок 49: Таблица норм шероховатости (стандарт N), составленная для сравнительного чтения в соответствии с А.W. Stahli и DIN 4768/1Системы обозначения шероховатости поверхности
50: Сравнительная таблица производителей станков Рисунок 51: Профиль поверхности токарной заготовки из стали. Ra 7.51, Rt 31.1– Рис. 52: Та же поверхность, что и на Рис. 51, после притирки зерном Si-C 500,
, но вертикальный масштаб увеличился в 10 раз. Ra 0.103, Rt 1.09.– Рисунок 53: Та же поверхность, притертая алмазом 2-3 мкм, такое же увеличение, что и в
Рисунок 52: Ra 0,009, Rt 0,119
54: Блок измерения шероховатости с несколькими оценками Рисунок 55: Оптический полировальный станок
FLM 750-P с охлаждающим устройством
56: Увеличенный вид оптического полировального станка FLM 750-PИзмерительное оборудование
Шероховатость и плоскостность поверхности – это две совершенно разные концепции, которые важно помнить.Многие электронные измерительные приборы, используемые сегодня для определения качества поверхности, имеют микропроцессорные системы управления и принтеры (рис. 54). Однако истинная ценность полученных результатов вызывает сомнения; поскольку большинство из них являются приблизительными и различаются в зависимости от устройства. Подчеркнем, что важно сравнивать тип датчика (радиус), давление иглы, расстояние измерения и фильтрацию (отсечение), см. Стандарт DIN 4768.
Также очень важно учитывать материал заготовки, его микроструктура, твердость и тип обработки, а также направление измерения расстояния по отношению к следам обработки.Даже при приложении давления всего 1 мН алмазный зонд с радиусом 5 микрон сжимает поверхность детали из цветного металла примерно до 50% глубины шероховатости.
Пористость микроструктуры должна быть принята во внимание в случае оксидной керамики
и спеченных металлов. Часто передаточные числа измеряются на разных уровнях шероховатости поверхности и указываются в%. Визуальный осмотр осуществляется путем сравнения полированной поверхности и неполированной поверхности.Видя текстуру поверхности между ними на изображениях ниже.Рис. 57: Показывает матовую алюминиевую деталь при увеличении 1600 и с соответствующей диаграммой измерения.
Рис. 58: Та же заготовка, что и на Рис. 57, но отполированная на полировальном столе тонкой бумагой 4/0, съем материала прибл. 2-5 мкм, радиус зонда 5 мкм, давление измерения 1 мН.Сравнение шероховатости поверхности – точность EDM
Перед чтением приведенной ниже таблицы есть несколько моментов, которые могут помочь
Q – Что такое Ra против Rz?
.
Одно из самых прямых объяснений, которое я смог найти, – это статья в Modern Machine Shop, написанная Джорджем Шютцем, директором по точным датчикам в Mahr Federal“Ra рассчитывается с помощью алгоритма, который измеряет среднюю длину между пиками и впадинами и отклонение от средней линии на всей поверхности в пределах длины выборки.Ra усредняет все пики и впадины профиля шероховатости, а затем нейтрализует несколько крайних точек, так что крайние точки не оказывают значительного влияния на окончательные результаты.
“Rz рассчитывается путем измерения вертикального расстояния от наивысшего пика до самой низкой впадины в пределах пяти отрезков выборки, а затем усреднения этих расстояний. Rz усредняет только пять самых высоких пиков и пять самых глубоких впадин, поэтому экстремумы имеют гораздо большее влияние на окончательное значение ».
Q – А как насчет Rt, Rmax, RMS…
При рассмотрении шероховатости поверхности необходимо учитывать множество важных факторов – не ограничиваясь, но включая направление измеренияЕсли вы хотите узнать больше, то лучше всего начать со следующего Руководства Mitutoyo – Бюллетень № 1894
Сравнительная таблица
Сюда также входит шкала VDI, N и стандартная отметка отделки
VDI – шкала, часто используемая немецкими производителями машин и довольно широко используемая при искровой и проволочной эрозии (Verein Deutscher Ingenieure, Общество немецких инженеров)
N – Новые номера шкалы ISO (степени) ISO 1302Важно
Важно отметить, что использование коэффициентов пересчета для расчета между Ra и Rz не является хорошей идеей – лучше всего установить, какой показатель шероховатости поверхности указал проектировщик (заказчик), и измерить его.Оборудование для измерения поверхности (профилометры), хотя и довольно дорогое, легко доступно, и оно должно быть в состоянии измерить несколько характеристик, чтобы удовлетворить различные требования проектировщиков. Мы не несем ответственности за информацию, содержащуюся в таблице, хотя при ее создании было приложено много усилий.Общая высота профиля (Rt, Pt, Wt) | Параметры шероховатости поверхности | Введение в шероховатость
Параметры шероховатости поверхности в JIS B 0601
- Пики и впадины в направлении высоты
- Средняя амплитуда в направлении высоты
- Средние характеристики в высотном направлении
- Горизонтальное направление
- Гибрид
- Кривая соотношения площадных материалов и функция плотности вероятности
Поиск из списка параметров
Общая высота профиля (Rt, Pt, Wt)
Общая высота профиля – это расстояние по вертикали между максимальной высотой пика профиля и максимальной глубиной впадины профиля на оценочной длине.
Параметры шероховатости поверхности
В этом разделе объясняются основные параметры ISO 4287: 1997. Каждый параметр классифицируется в соответствии с основным профилем (P), профилем шероховатости (R) и профилем волнистости (W) для оценки различных аспектов профиля. (Когда сравниваются длины волн волнистости и компонентов первичного профиля, составляющая шероховатости поверхности является составляющей шероховатости той, которая имеет сравнительно более короткую длину волны.)
Поиск из списка параметров
Пики и впадины в направлении высоты Среднеарифметическое значение роста (Ra, Pa, Wa) Максимальная высота профиля (Rz, Pz, Wz) Максимальная высота выступа профиля (Rp, Pp, Wp) Максимальная глубина впадины профиля (Rv, Pv, Wv) Средняя высота элементов профиля (Rc, Pc, Wc) Общая высота профиля (Rt, Pt, Wt) Средняя амплитуда в направлении высоты Среднеквадратичное отклонение (Rq, Pq, Wq) Средние характеристики в высотном направлении Асимметрия (Rsk, Psk, Wsk) эксцесс (Rku, Pku, Wku) Горизонтальное направление Средняя ширина элементов профиля (RSm, PSm, WSm) Гибрид Среднеквадратичный наклон (RΔq, PΔq, WΔq) Кривая соотношения площадных материалов и функция плотности вероятности Соотношение длины нагрузки (Rmr (c), Pmr (c), Wmr (c)) Перепад высот профиля (Rδc, Pδc, Wδc) Относительное отношение длины нагрузки (Rmr, Pmr, Wmr) Кривая соотношения материалов (BAC) Функция плотности вероятности (ADF)
“Что такое шероховатость линии?” список страниц
Основы обработки поверхности
Обработка поверхности может сбивать с толку, особенно когда дело касается единиц измерения или разницы между Ra и Rz.В этой статье мы дадим общий обзор и ответим на некоторые из наиболее часто задаваемых вопросов…
Что такое обработка поверхности?
Обработка поверхности – это термин, используемый для описания текстуры поверхности, и иногда он используется как синонимы с термином «текстура поверхности». Требования к чистоте поверхности часто встречаются на технических чертежах механических деталей, особенно в тех случаях, когда детали плотно прилегают друг к другу, перемещаются друг относительно друга или образуют уплотнение. Американское общество инженеров-механиков (ASME) опубликовало Y14.Стандарт 36M Surface Texture Symbols, иллюстрирующий правильную спецификацию и использование символов текстуры поверхности на технических чертежах. ASME также публикует Стандарт текстуры поверхности B41.6, который содержит определения и методы измерения качества поверхности.
Обработка поверхности состоит из трех различных элементов – шероховатости, рельефа и волнистости (см. Рисунок 1 ниже). Однако в механических цехах нередко термин «чистота поверхности» используется для описания только шероховатости поверхности.Шероховатость – это наиболее часто определяемый аспект чистоты поверхности, однако, прежде чем мы углубимся в детали, давайте обсудим эти три элемента, которые составляют чистоту поверхности.
Рисунок 1 – Укладка, волнистость и шероховатостьУкладка
Lay – это термин, используемый для описания доминирующего рисунка на поверхности и ориентации этого рисунка. Укладка обычно производится в процессе производства и может быть параллельной, перпендикулярной, круглой, заштрихованной, радиальной, разнонаправленной или изотропной (ненаправленной).Мы обсудим символы и интерпретацию Lay в разделе «Символы» ниже.
Волнистость
Волнистость – это термин используется для наиболее широко разнесенных вариантов отделки поверхности. Эти периодические дефекты поверхности больше длины выборки шероховатости, но маленькие, короткие и регулярные достаточно, чтобы они не считались дефектами плоскостности. Распространенные причины волнистости поверхности включают коробление. из-за нагрева и охлаждения, а также дефекты обработки из-за вибрации или прогиба.
Измеряется волнистость по оценочной длине, и для этой длины создается профиль волнистости. Профиль волнистости не включает никаких неровности поверхности из-за шероховатости, плоскостности или изменения формы. Расстояние между волнами ( Вт / м2, ) – размах расстояние между волнами, а высота волны определяется средней волнистостью ( Wa ) или параметры общей волнистости ( Wt ). Требования к волнистости менее распространены, чем требования к шероховатости, но они могут иметь определенное значение детали, такие как кольца подшипников или уплотнительные поверхности.
Шероховатость поверхности
Шероховатость поверхности, часто сокращаемая до шероховатости, относится к небольшим неровностям геометрии поверхности. Шероховатость является наиболее часто задаваемым, измеряемым и рассчитываемым аспектом чистоты поверхности, и многие люди используют термин «чистота поверхности» только для описания шероховатости.
Измерение шероховатости
Шероховатость поверхности обычно измеряется перпендикулярно направлению укладки с помощью прибора, известного как профилометр (показан на Рисунке 2 ниже).Профилометр формирует график, показывающий изменение высоты поверхности при изменении положения. Этот график известен как измеренный профиль поверхности, и его пример показан ниже. Измеренный профиль покажет не только шероховатость, но и любые дефекты волн и плоскостности, которые могут присутствовать. Чтобы исследовать только шероховатость, необходимо удалить из профиля дефекты волн и плоскостности.
Без сглаживания профиля средняя линия (показанная на Рисунке 2 ниже) будет представлять изменение высоты поверхности из-за дефектов волнистости и плоскостности.Поскольку нас не интересуют вариации из-за этих элементов, нам нужно измерить профиль с выпрямленной средней линией. Для этого сначала мы усредняем высоту поверхности по интервалам, меньшим, чем интервал волнистости, но большим, чем интервал шероховатости, чтобы сгладить большую волнистость. Эта новая, более прямая линия известна как профиль шероховатости поверхности (рис. 3).
Рисунок 2 –
Линия 1: Измеренный профиль и средняя линия – Включает колебания волнистости и плоскостности
Линия 2: Профиль шероховатости и средняя линия, волны и отклонения плоскостности отфильтрованыПараметры и расчеты шероховатости
На технических чертежах шероховатость упрощена до числового значения, которое представляет характеристики профиля шероховатости.Наиболее часто задаваемые параметры шероховатости – Ra и Rz . Ra или средняя шероховатость обычно используется в США, а Rz или средняя глубина шероховатости обычно используется во всем мире. Ra определяется как среднее отклонение профиля шероховатости от средней линии. С математической точки зрения это интеграл абсолютного значения профиля шероховатости, деленный на длину профиля. Из-за этого усреднения значение Ra и ниже, чем фактическая высота отклонений шероховатости.
Уравнение 1 – Уравнение средней шероховатости, где Z (x) – профиль шероховатости длиной L. Рисунок 3 – Средняя шероховатость ( Ra )Для расчета Rz профиль шероховатости делится на пять равных отрезков. Разница высот между самой высокой и самой низкой точкой в каждой из пяти секций известна как общая шероховатость, или Rt , для этой секции. Rz – это среднее из пяти значений Rt . Расчетное значение Rz приблизительно соответствует высоте самых сильных вариаций шероховатости.
Рисунок 4 – Общая шероховатость ( Rt ) для каждого сегмента и средняя глубина шероховатости ( Rz )Поскольку Ra представляет средние значения, а Rz основывается на максимальных значениях, Rz почти всегда больше, чем Ра . Разница между двумя параметрами будет зависеть от однородности профиля шероховатости. Если одно значение известно, можно оценить максимум для другого, но это приближение не следует использовать для критических приложений.Как правило, если известен только Rz , значение Ra можно аппроксимировать делением на коэффициент 7,2. Если известно значение Ra , значение Rz для той же поверхности может быть в 20 раз выше, и его немного сложнее приблизить.
Единицы измерения шероховатости
В США для измерения шероховатости используется микродюйм. Эта единица представляет собой одну миллионную дюйма и обычно записывается как µ в .Соответствующая международная единица (СИ) – микрометры, или для краткости микроны. Эта единица представляет одну миллионную метра и записывается как мкм или мкм . Так же, как один метр составляет 39,37 дюйма в длину, один микрометр эквивалентен 39,37 микродюйма.
Символы
Основной символ шероховатости поверхности – это галочка с точкой, лежащей на поверхности, которую необходимо указать. Варианты этого символа предоставляют дополнительные инструкции, как описано в таблице ниже.
Рисунок 5 – Символы шероховатости поверхности – основные сведенияЦифры рядом с основным символом чистоты поверхности используются для обозначения различных параметров чистоты поверхности. Расположение числа по отношению к символу определяет, какой параметр указывается. Буквы на рисунке ниже показывают правильное расположение каждого параметра в соответствии со стандартом ASME Y14.36M.
Рисунок 6 – Символ шероховатости поверхности – ДеталиГде а представляет собой среднее значение шероховатости ( Ra, ), а b представляет собой способ производства, покрытие, примечание или другая дополнительная информация.Буква c обозначает выборку шероховатости. длина в миллиметрах или дюймах, а d дает направление поверхностная кладка. Стоимость e указывает минимальные требования к удалению материала в миллиметрах. Наконец, если альтернативный параметр чистоты поверхности предоставляется, символ параметра и значение указаны в ячейке f (например: Rz 0,4).
Семь возможных укладок направления указаны в таблице ниже.
Рис. 7 – Символы укладкиВ приведенном ниже примере указано значение Ra не более 32 мкдюймов.при оценочной длине 0,125 дюйма. Rz должен быть не более 160 мкм на оценочной длине 0,75 дюйма. Направление укладки параллельно плоскости обзора чертежа, где появляется символ.
Рисунок 8 – Пример спецификации шероховатости поверхностиПрактические соображения
Чистота поверхности высока. в зависимости от процесса изготовления детали и очень гладкая поверхность отделка обычно требует дополнительной обработки, например шлифовки или полировки.Поскольку дополнительная обработка добавит дополнительные затраты, важно, чтобы инженер или проектировщик не навязывали излишне низкие требования к шероховатости. По возможности, характеристики шероховатости должны быть в пределах ограничений основного производственного процесса.
В пределах возможностей оборудования некоторые производственные процессы позволяют в определенной степени контролировать качество поверхности. Например, при фрезеровании или токарной обработке малая глубина резания и низкая скорость подачи обычно обеспечивают более гладкую отделку, в то время как более глубокие пропилы и более высокие скорости обеспечивают более грубую отделку.Износ режущего инструмента также может повлиять на качество поверхности. В приведенной ниже таблице показан диапазон значений шероховатости поверхности, обычно получаемых при различных производственных процессах.
Рисунок 9 – Средняя шероховатость ( Ra ), полученная с помощью обычных производственных процессов
Изображение предоставлено Emok – WikipediaОсновные выводы
- Шероховатость поверхности состоит из волнистости, укладки и шероховатости, но обычно на технических чертежах указывается только шероховатость.
- Ra – это средняя шероховатость, которая недооценивает вариации высоты поверхности.
- Rz – это средняя глубина шероховатости, которая приближается к размеру самых сильных колебаний высоты поверхности.