Штамповка и ковка металла: Ковка и штамповка. В чем различия?
alexxlab | 30.05.2020 | 0 | Разное
Ковка и штамповка. В чем различия?
Эти два процесса обработки металлов похожи один на другой, но все же, есть существенные различия. При ковке изменение формы не обусловлено какими-либо контурами, при штамповке оно строго ограничено формами штампа. Под ударами молотка металл деформируется и, вращая деталь, кузнец может получить заготовку различной формы.
При штамповке требуется создание специальных форм — штампов, форму которых в последующем будет принимать металл. Инструмент, изготовленный способом «горячего штампования» производиться следующим путем: металлическая заготовка нагревается до ковочной температуры и помещается под штамповочный пресс, где ей при помощи матрицы придается нужная форма. Под механическим воздействием, так же как и при нагревании, происходят изменения в кристаллической решетке металла, его свойства меняются.
Теперь представьте, насколько сильно изменяются свойства металла при многократных ударах молота (ручная ковка) и всего лишь однократном ударе пресса (промышленный способ). Разумеется, при ручной ковке многократно усиливаются прочностные свойства металла, а также его твердость.
Еще существует такое понятие, как «холодная штамповка» – сущность способа заключается в процессе, где в качестве заготовки используют полученные прокаткой лист, полосу или ленту, свёрнутую в рулон, которую обрабатывают путем давления. Этот процесс, обычно осуществляется без нагрева заготовки, что существенно снижает такие характеристики как прочность и твердость металла. Заметьте, ключевое слово здесь – «без нагрева», т.е. с кованым инструментом, стамески изготовленные таким способом, вообще ничего общего не имеют.
В нашем магазине я предлагаю приобрести кованый инструмент для резьбы по дереву, который наша семья изготавливает не один десяток лет. При этом передавая от отца к сыну, накопленный опыт по обработке инструментальных сталей, старательно сохраняя традиции и секреты мастерства.
На весь инструмент наноситься клеймо мастера, на котором присутствует буква “Н” – заглавная буква нашей фамилии (Наумов).
Первая часть статьи здесь: http://www.livemaster.ru/topic/1059725-kovanyj-instrument-mif-ili-realnost?inside=1&wf=0&vr=1
Ковка и штамповка
Ковкойназывается обработка металла, находящегося в пластическом состоянии, статическим или динамическим давлением. При ковке изменяется как внешняя форма, так и структура металла. Изделие, полученное ковкой, называют поковкой. Существуют два вида ковки: свободна и в штампах.
Ковка производится либо ударным (динамическим) воздействием на металл, где используется энергия падающих частей молота (механическая ковка), либо медленным (статическим) воздействием, где используется давление пресса.
Свободна ковка
Свободную ковку применяют в условиях серийного и мелкосерийного производства. К операциям ковки относятся вытяжка, осадка, гибка, пробивка, прошивка, рубка и т.д.
При вытяжкедлина поковки увеличивается за счет уменьшения ее поперечного сечения. Разновидностью вытяжки является протяжка, при которой заготовку кантуют после каждого удара.
Осадка – операция, обратная вытяжке. При осадке поперечное сечение поковки увеличивается за счет высоты.
Прошивка отверстий производится с помощью пробойника, называемого прошивнем. Прошивкой получают сквозное отверстие или углубление – (глухая прошивка). На рис.37приведены схемы некоторых операций свободной ковки.
Ковку выполняют на ковочных молотах или гидравлических прессах.
Молоты– машины динамического, ударного воздействия. Продолжительность деформации на них составляет тысячные доли секунды. Металл деформируется за счет энергии, накопленной подвижными (падающими) частями молота к моменту их соударения с заготовкой. Одним из основных типов молотов для ковки являются паровоздушные молоты.
Гидравлические прессы – машины статического действия; продолжительность деформации составляет несколько секунд. Металл деформируется приложением усилия, создаваемого с помощью жидкости, подаваемой в рабочий цилиндр пресса.
Рис.38. Схемы операций ковки: а – двусторонняя прошивка, б-сквоз-
ная прошивка, в-прошивни, г-отрубка, д-топоры, е-гибка,
ж-штамповка в подкладных штампах, з-протяжка
Штамповка
Штамповкой называют ковку в стальных формах-штампах. Производительность штамповки в десятки раз больше, чем свободной ковки. Кроме того, при штамповке достигается значительно большая, чем при свободной ковке, точность размеров и чистота поверхности. Однако штамповка выгодна лишь в массовом и серийном производстве, потому что затраты на изготовление штампового инструмента оправдываются лишь при изготовлении большой партии деталей. Штамповка бывает горячей и холодной, объемной и листовой.
Горячая объемная штамповка(ковка в штампах). Если при свободной ковке металл, теснимый бойками сверху и снизу, может свободно течь в стороны, то при штамповке течение металла ограничивается поверхностями штампа, и заготовка принимает форму его фасонной полости (ручья).
Припуск на механическую обработку при горячей объемной штамповке примерно вдвое меньше, чем при свободной ковке. Горячая штамповка производится на молотах и ковочных машинах.
Штамповка на молотах– наиболее распространенный способ горячей штамповки. Штамп (рис.39,а)состоит из двух частей: верхней 1 и нижней 2. Нижняя часть крепится на штамподержателе, установленным на шаботе, а верхняя – в бабе; крепление каждой части штампа осуществляется клином и шпонкой. Места крепления выполняют в виде “ласточкиного хвоста”. Обе части имеют полости, составляющие ручей, который соответствует форме поковки.
Рис.39. Штамповка заготовок зубчатых колес в одноручьевом штампе
Для штамповки заготовка нагревается до температуры ковки и помещается в нижнюю полость 2 штампа. Под действием ударов верхней части штампа металл течет и заполняет ручей. Излишек металла выдавливается из ручья в кольцевую полость и образует так называемый облой (заусенец) 3 (рис.39,б), который способствует лучшему заполнению полости штампа, препятствуя дальнейшему течению металла в полости разъема штампа. Заусенцы обрезают на прессе в специальном обрезном штампе в горячем или холодном состоянии. По количеству ручьев штампы разделяются на одноручьевые и многоручьевые.
Одноручьевые штампыприменяют для изготовления простых изделий и для штамповки заготовок, предварительно подготовленных свободной ковкой. Эта подготовка состоит в приближении формы заготовки к форме готовой поковки.
Многоручьевые штампы имеют заготовительные, штамповочные и отрезные ручьи. В заготовительных ручьях выполняются операции вытяжки и гибки, в штамповочных – придания заготовке окончательной формы, в отрезных отделения штамповки от прутка (катанной заготовки).
Заготовительные ручьи располагаются по краям штампа, а штамповочные в середине. На рис.40 приведен многоручьевой штамп, а также эскизы исходной заготовки, ее деформирование при выполнении последовательных переходов штамповки и готовая поковка. Заготовка поступает сначала в протяжной ручей 4, где протягивается. Затем ее деформируют в прокатном ручье 3 для утолщения на концах, далее передают в гибочный ручей 1, после чего ее штампуют сначала в предварительном ручье 2, а потом в окончательном ручье 5.
Рис.40. Многоручьвой штамп
В последние годы распространяется безоблойная штамповкав закрытых штампах. При этом достигается значительная экономия металла, отпадает надобность в обрезных прессах и штампах, а также в обрезке облоя и повышаются механические свойства поковок. Для горячей штамповки применяют кривошипные прессы, фрикционные и паровоздушные молоты.
Штамповка на горизонтально-ковочных машинах (ГКМ). В отличие от молотов у ковочных машин ползун движется горизонтально, поэтому эти машины называют горизонтально-ковочными. Такие машины применяют для изготовления поковок, имеющих форму полых или сплошных стержней с утолщением (болтов, заклепок и т.п.), а также для изготовления поковок кольцеобразной формы (втулок, гаек, колец).
Эти машины имеют высокую производительность, обеспечивают получение большой точности, чем при штамповке на молотах, и почти не дают отходов.
Рис.41.Схема штамповки кольца на ГКМ
Штамповка на ГКМ обычно сводится к выполнению операции высадки нагретой прокатанной заготовки. Штамп имеет два ручья. В первом ручье проводится высадка для получения наружного контура кольца (рис.41,а), во втором ручье (рис.41,б) пуансонП прошивает и выталкивает заготовку. Давление, развиваемое ГКМ, колеблется от 500 до 3000 кН.
Холодная листовая штамповкаприменяется для изделий из листовой стали, алюминия и его сплавов, меди, латуни и др. Простая штамповка сводится к вырезке, вытяжке и гибке. Сложная штамповка представляет собой сочетание перечисленных операций.
Вырубкуприменяют для изготовления из листа плоских деталей; форма контура может быть любой: круг, квадрат и т.д. Этим методом могут также пробиваться отверстия. У штампа для вырубки имеются две основные части (рис.42): матрица 4 и пуансон 1.
При движении вниз пуансон 1 острыми краями рабочего контура срезает часть заготовки. При обратном движении – остаток заготовки 3 упирается в съемник 2 и снимается с пуансона.
Вытяжкойполучают полые изделия из листовой заготовки. Заготовку диаметромD кладут в выточку матрицы (рис.43,а) и вытягивают пуансоном в стакан (
Рис.43. Схема вытяжки из листовой заготовки
Если зазор амежду матрицей и пуансоном равен толщине заготовки, то толщина стенок изделия остается такой же; если же этот зазор меньше, то стенки становятся тоньше. Для местного изменения формы, например для получения ребер жесткости, заготовку дополнительно формуют в штампах.
Холодную штамповку производят механическими кривошипными, гидравлическими или фрикционными прессами.
Чтобы снять наклеп, некоторые изделия отжигают. Если штампуют в несколько переходов с большой деформацией, то отжигают многократно.
Ковка и штамповка – Ковка, сварка, кузнечное дело
При изготовлении изделий из металла очень часто применяются два распространенных метода – штамповка и ковка металла. Способ, при котором используется листовая штамповка изделия, осуществляется несколькими довольно простыми операциями. Первая – разделительная, которая осуществляет заготовки одну от другой. Вторая – формоизменяющая операция, при которой части заготовок двигаются относительно друг друга без разрушения и деформации самих заготовок.
Разделительные операции также имеют свою структуру.
- Такая операция, как холодная листовая штамповка – это вырубка, пробивка отверстий, отрезка листа металла.
- Горячая штамповка – это гибка металла, обжим, формовка, отбортовка и вытяжка изделия.
Проводятся операции по разделению при помощи гидравлического пресса или механических ножниц.
- Отделение некоторой части изделия по незамкнутому контуру – это отрезка.
- Вырубка заготовки – это полное отделение необходимой части.
- Пробивка металла – полное отделение части изделия с последующей его утилизацией (отходы).
При штамповке деталей горячим методом важно, чтобы заготовка имела хорошие пластические свойства, иначе возможны механические повреждения. Упругость металла также учитывается при гибке и отбортовке металла, так как после распружинивания деталь может деформироваться. Все штампованные элементы, каким бы способом они не обрабатывались, имеют высокую точность заданных размеров и технологические параметры.
К операции листовой штамповки относится и раскрой заготовок. Такой способ обработки заготовок использует несколько последовательных операций. Их необходимое количество всегда разное и определяется конфигурацией и размерами заготовки. Здесь важно правильно определить число проводимых операций с целью получения наименьшего количества отходов. Для соблюдения более точного размера изделия вырубка проводится перемычками, то есть в несколько заходов.
Все кузнечно штамповочное оборудование должно соответствовать определенным требованиям, которые указываются в технических требованиях. При увеличении производительности труда возрастает и нагрузка на оборудование. Модернизация и контроль состояния кузнечного оборудования – необходимость, заданная временем. Стандартный список требований к оборудованию:
- 1. Повышенные требования к надежности в эксплуатации некоторых деталей – новых и модернизированных, при длительном режиме работы.
- 2. Повышение точности и надежности исполнительных систем, устойчивости ко внешним помехам (в частности – к вибрациям).
- 3. Снижение себестоимости модернизированных субъектов. Уменьшение сроков ремонта и первоначальных затрат за счет эксплуатационных издержек при технологических процессах.
Помимо штампованных изделий и элементов, готовые изделия из металла производятся методом последующей или полной ковки изделия. В настоящее время усовершенствованное кузнечно-штамповочное оборудование позволяет получить штампованные кованые элементы без задействования горячей ковки и кузнечного горна, что положительно сказывается на себестоимости продукции при полном сохранении качество продукции.
Ручная горячая ковка, холодная ковка металла, штамповка (горячая или холодная) с последующей ковкой – вариантов изготовления изделий достаточно. Полностью композиция из металла собирается клепкой отдельных элементов, сваркой (газовой или электродуговой) или обжимкой хомутами. При изготовлении штампованных кованых элементов можно добиться бесконечного разнообразия форм и высокого дизайна изделия, которое не будет иметь аналогов.
Ковка и штамповка | Обработка металлов давлением
Свободной ковкой называется процесс горячей обработки давлением с помощью универсального инструмента (молота или пресса с гладким бойком). Нагретый слиток кладут на нижний боек, и последовательными ударами верхнего бойка деформируют его (рис. 3.4,а). Ковка существенно улучшает структуру и свойства металла. Грубая, крупнозернистая структура слитка приобретает волокнистое строение с более мелким зерном, повышенными пластичностью и ударной вязкостью.
Рис. 3.4. Принцип устройства штампов при ковке и штамповке металла: а —свободная ковка; б — объемная штамповка; в — листовая штамповка 1 — поковка; 2 — облой
Свободную ковку применяют в основном при производстве единичных поковок сложной конфигурации. К преимуществам ковки по сравнению с другими способами обработки металлов следует отнести ее малую зависимость от массы, формы и размеров заготовок; малую стоимость необходимой технологической оснастки; возможность использования менее мощного оборудования благодаря концентрированному приложению усилий к небольшому объему деформируемого металла. Методом свободной ковки из слитков получают все крупные поковки массой 250 т и более. Заготовками для мелких и средних -поковок служат слитки, блюмы, болванки и прутковые катаные заготовки.
Основные операции свободной ковки: осадка— уменьшение высоты заготовки; протяжка—удлинение заготовки или ее части; прошивка —получение отверстий путем продавливания; обрубка — отделение части заготовки; гибка и скручивание. Разработка технологического процесса свободной ковки включает также составление чертежа поковки с назначением припусков, допусков и напусков; определение размеров и массы заготовки; выбор кузнечных операций и необходимого инструмента; выбор машинного оборудования. Определяют также режим нагрева заготовки, подбирают тип и размеры нагревательных устройств.
По размерам поковки определяют массу заготовки: Qзаг = Qпок+Qотх+Qуг+Qобс, где Qпок— масса поковки; Qотх — масса отходов; Qуг—масса угара; Qобс — масса отходов при обсечке лишнего металла. Отходы от слитка составляют 25— 30% (прибыль 5—10 %). Угар в результате окисления металла составляет 2—3 % массы заготовки на каждый нагрев. Величина отходов обсечки зависит от сложности поковок и способа их изготовления. Для простых поковок она не превышает 5— 8%, а для сложных поковок достигает 30%.
При серийном и массовом производстве используют штамповку, производительность которой в десятки раз больше производительности свободной ковки, а необходимая квалификация рабочих значительно ниже. Кроме того, при штамповке достигаются большие, чем при свободной ковке, точность размеров и чистота поверхности поковок. Однако штамповка выгодна лишь для такого производства, когда затраты на изготовление штампов оправдываются количеством выпускаемых поковок. Основными методами штамповки являются объемный и листовой (рис. 3.4,6, в). Различают горячую и холодную объемную штамповку. Листовая штамповка может быть холодной и с нагревом.
При горячей объемной штамповке (см. рис. 3.4,6) формообразование поковок осуществляется в специальных инструментах—штампах, рабочие полости (ручьи) которых допускают течение деформируемого металла только в определенном направлении и до необходимых пределов, в результате чего обеспечивается принудительное получение поковки заданной формы и размеров. Общий технологический процесс горячей штамповки складывается из отрезки заготовок, их нагрева, штамповки, отрезки облоя, образовавшегося вследствие вытекания металла из разъемов штампа, и зачистки заусенцев, термической обработки, правки и калибровки и, наконец, отделки поверхности. Штамповка может быть осуществлена в открытых и закрытых штампах. В открытых штампах поковка получается с облоем. Отход металла в облой составляет в среднем 10—20 % массы поковки.
Что такое поковка? Процесс изготовления поковки. Ковка, штамповка
Сегодня обработка металлов давлением является наиболее распространенным и технически обоснованным методом получения заготовок, именуемых поковками, которые в дальнейшем подвергаются механической обработке для достижения требуемых размеров и конфигурации детали.
Поковка – это промежуточная заготовка, полученная методом пластической деформации металла, особенность которой является ее схожесть с будущей деталью или изделием по габаритным размерам и форме.
Процесс изготовления поковки проходит следующие этапы:
1. Резка проката различной конфигурации на необходимые размеры.
Используемый прокат может иметь круглое, квадратное, прямоугольное и многоугольное сечения. Иногда допускается применение заготовки в виде специального профиля (уголок, двутавр, швеллер)
2. Процесс деформации метала.
3. Термическая обработка поковки (нормализация и отпуск)
4. Прием готовой поковки отделом технического контроля.
Методы, используемые для изготовления поковки
Сегодня существует два основных метода получения поковки:
• Ковка – процесс деформации металлической заготовки, которая находится в пластическом состоянии и придания ей нужной формы путем воздействия ударной нагрузки бойков молота или пресса. К ковке также относят гибку, вытяжку, волочение. Отличительной особенностью ковки является то, что заготовка находится в свободном положении в процессе деформации, она не имеет четкой базировки.
Припуск под обработку кованой поковки практически в 2 раза больше, нежели у поковки полученной методом штамповки. На производстве ковку применяют только в мелкосерийном и единичном производстве двумя основными методами, это ручной или машинный.
• Штамповка – процесс деформации металлической исходной заготовки под давлением, протекающий с использованием дополнительной оснастки (специального штампа). Процесс пластической деформации осуществляется в матрице штампа, форма которой полностью идентична изготовляемой поковке. Ударным элементом, оказывающим нагрузку, выступает пуансон.
Штамповка может быть выполнена с предварительным нагревом исходной заготовки, так и без него.
Штамповка, в отличие от ковки, имеет достаточно высокую производительность, она не требует высокой квалификации рабочих, а на выходе поковка имеет более высокую точность размеров и малую шероховатость поверхностного слоя. Однако применение штампов целесообразно только в массовом и серийных производства, чтобы оправдать затраты на их дорогостоящее изготовление.
Легированная сталь марки 5ХНМ (инструментальная штамповая) широко применяется в отраслях, где к изготавливаемой продукции предъявляются высокие требования по твердости, прочности, износоустойчивости, а также где необходима высокая точность изготовления. Зачастую это инструментальное производство и станкостроение.
Поковка, полученная из стали 5ХНМ, нашла свое основное применение в конструировании и производстве прессовых штампов, ковочных агрегатов, молотов.
Сталь 5ХНМ обладает следующими механическими свойствами:
Предел прочности в – 1570 МПа
Предел текучести T – 1420 МПа
Твердость после отжига – 241 МПа
Ударная вязкость KCU – 340 кДж / м2
Анализируя физические свойства и состав базовых легирующих элементов стали 5ХНМ можно отметить, что благодаря высокому содержанию хрома – до 0,8 % и никеля до 1,8 % сталь обладает высокой твердостью, прочностью и упругостью, что позволяет избежать трещин на поверхности поковки после ее термической обработки. Входящий в состав молибден до 0,3% способствует хорошей ударной вязкости, тем самым предотвращая появление хрупкости стали после отпуска.
Поковки из штамповой стали 5ХНМ подвергают отжигу, подготавливая ее их для последующей термической обработки и обеспечивая снятия внутренних напряжений в структуре.
Для того чтобы инструмент, изготовленный из штамповой легированной стали 5ХНМ обладал максимальной твердостью и имел длительный срок службы требуется финишная термообработка. Закалка осуществляется при температуре, которая достигает 850°C, а затем производится последующий отпуск при температуре 460-520°C.
Среда, в которой будет производиться закалка и отпуск, а также температурный режим выбирается технологом в зависимости от условий работы и испытываемой ударной нагрузки изготовляемого инструмента. Однако нужно помнить, что высокие температуры в процессе закалки могут стать причиной увеличения прокаливаемости стали и как следствие снижение ударной вязкости.
Существует также и зарубежные аналоги штамповой легированной стали 5ХНМ, которая также приобрела большую популярность в США и странах Евросоюза.
Здесь ее маркируют в соответствии своих стандартов, действующих на территории страны. Например, Т61206 или L6 на территории США и 55NiCrMoV7 в странах Евросоюза.
Штамповка металла: технологии, ГОСТ, изготовление штампов
Штамповка металла — это формоизменение материала под действием внешней силы с целью получения нужной детали. Для обработки заготовки таким способом требуется большое усилие. Для этого существует оборудование, которое выпускается усилием от 16 до 500 тонн. Оснастка, устанавливаемая в пресс, носит название штамп. В ней происходит непосредственное соприкосновение рабочего инструмента с металлом. За 1 ход машины получается деталь высокой степени точности.

История возникновения процесса
Штамповка изделий из металла впервые начала проводится в XVI в. Связано это было с развитием оружейного производства, где требовалось получение большого количества одинаковых деталей. В XIX веке началось бурное развитие штамповочного производства. Выпускаются предметы домашнего обихода. Возникает потребность изготовления качественных серийных изделий.
С появлением автомобилестроения и судостроения, обработка металлов давлением заняла ключевую позицию в развитии этих отраслей. С помощью штамповки начали производиться габаритные детали.
Сферы использования
Промышленное производство не обходится без холодной и горячей штамповки. С помощью этих методов за небольшой промежуток времени можно создать как мелкие, так и крупные детали. Горячая штамповка применяется там, где нужно получить объемные детали.
При штамповке фланцев применяются 2 метода:
- В процессе ковки используются гидравлические прессы. Здесь под действием давления идет затекание металла в полость, которая изготовлена в бойке. Это пространство соответствует форме получаемой детали.
- При использовании листового металла в качестве заготовки применяются кривошипно-шатунные прессы. В них вставляется штамп и подается листовой металл. Под давлением происходит вытяжка фланца.
Технология штамповки
Технология изготовления деталей штамповкой как горячим, так и холодным способом предполагает наличие оснастки. Для обоих видов изготавливаются штампы, которые имеют определенные отличия. Применяются они для металла, который имеет разную степень толщины.
Заготовки большого размера предварительно нагреваются, а затем идет процесс ковки. В холодном состоянии толщина листа редко превышает 1 мм. С таким материалом проводятся разные операции, например, штамповка значков.

Холодная штамповка
В процессе холодной штамповки листового металла нагрев не проводится. Усилия пресса хватает, чтобы проводить разделительные или формоизменяющие операции. Как результат полученная деталь, не подверженная процессу усадки. Для экономии материала штамповку проводят согласно правилам раскроя листа, которые регламентируются ГОСТом.
К холодной штамповке относятся такие операции:
- Вырубка-пробивка. В процессе вырубки готовая деталь падает в контейнер, а снаружи остаются отходы. При пробивке, наоборот, отход падает в контейнер, а деталь формируется снаружи. Конструкция штампов одинаковая. В процессе работы проводится разделительная операция, в которой участвует пуансон и матрица штампа.
- Гибка. Относится к несложной операции. Деталь укладывается между упорами на матрицу и давится сверху пуансоном.
- Вытяжка. Часто получается за несколько переходов. Для этого изготавливаются отдельные штампы. В процессе работы из круглой заготовки получается стакан, конус или полусфера. Получается это за счет перераспределения металла в исходной заготовке.
- Отбортовка. Пуансон ловит фиксатором отверстие в детали и расширяет его, отбортовывая стенки.
Важным моментом является правильный выбор зазора между пуансоном и матрицей. Эта величина зависит от толщины и вида материала. Чем толще металл, тем больше зазор. Для алюминия и других мягких материалов этот размер уменьшается. В противном случае будут образовываться заусенцы.
Горячая штамповка
В процессе изготовления деталей из металла путем горячего прессования заготовки поступают в камеру нагрева. Горячая объемная штамповка металла начинается после достижения ими температуры 1200°С. Нагретые изделия закладываются в штамп, где имеются специальные ручьи, для предварительной и окончательной штамповки.
Если нужно осадить нагретую поковку, то она ставится в пространство между двумя плоскими бойками. Оборудование запускается, и заготовка осаживается на нужный размер.
Альтернативные методы штамповки
Штамповка металла может происходить и под действием других сил:
- Взрывом. Процесс проводится в воде. Материал располагается на матрице, в которой сделано углубление нужной формы. Сверху производится взрыв. В результате заготовка заполняет ручей и приобретает нужную форму.
- Электрогидравлическая. В водной среде подается напряжение. Происходит нагрев воды. Под действием высокой температуры возникает ударная волна, которая формирует заготовку.
- Протяжка металла через валки. Этот метод позволяет придать заготовке нужную форму.
Штампованные значки изготавливаются в штампе, где в углубление пуансона закладывается эмаль.
Для изготовления штамповки из заготовки конструируются штампы по металлу. На первом этапе идет разработка чертежей со спецификацией и деталировкой.
Штампы состоят из следующих деталей:
- Рабочие части — пуансон и матрица. Изготавливаются из инструментальной стали У8а, У10а, Х12М. После термообработки получают закалку до 60 единиц по Роквеллу.
- Пуансонодержатель. Материал — Ст.3
- Прокладки. Изготавливаются из конструкционной стали со степенью закалки 45 единиц по Роквеллу.
- Съемник. Делается из Ст.3
- Верхняя и нижняя плиты. Их толщина зависит от усилия, затрачиваемого на штамповку.
- Колонки и втулки. Материалом является Сталь 20. По поверхности ведется цементация на глубину 1–1,5 мм. Затем проводится закалка этого слоя.
- Хвостовик. Вставляется в ползун пресса.

Оборудование и инструменты
Для формирования металлических изделий изготавливаются штампы, вставляющиеся в прессах, которые бывают 2 типов:
- Кривошипно-шатунные. Основным элементом в них является ползун, двигающийся по направляющим. Сверху располагается электродвигатель, который дает толчок движению кривошипно-шатунного механизма. Снизу имеется плита, на которую ставится штамп. Оборудование быстроходное. К недостаткам относится большая сила удара при соприкосновении пуансона с металлом. В результате инструмент выкрашивается.
- Гидравлические прессы. Обладают большой мощностью. К преимуществам относится плавность движения ползуна. Благодаря этому при работе отсутствует механический удар, что приводит к длительной службе инструмента. Величина хода движения ползуна обеспечивает большую открытую высоту пространства пресса. Это дает возможность совершать операции глубокой вытяжки или гибки заготовок с высокими бортами.
Обработка металлов давлением позволяет получить за короткое время большое количество деталей. При этом они все будут иметь одинаковую форму. Точность их изготовления регламентируется ГОСТом.
Ковка и штамповка цветных металлов. Справочник :: Книги по металлургии
МЕТОДЫ КОВКИ И ШТАМПОВКИ
Предварительно деформированные прессованием сплавы цветных металлов обладают достаточным запасом пластичности и их можно обрабатывать давлением даже при напряженных состояниях с наличием растягивающих деформаций и напряжений. Однако слитки большинства сплавов и предварительно деформированные высокопрочные сплавы следует обрабатывать, по возможности, при более мягких напряженных состояниях прессованием в контейнерах и штамповкой в открытых штампах с ограниченным уширением, а также в закрытых штампах.
Высоколегированные сплавы обладают пониженной пластичностью при наличии в деформируемом объеме растягивающих напряжений и отсутствии сил, препятствующих разрушению. Поэтому такие сплавы в виде прессованных прутков надо обрабатывать в открытых штампах с ограниченным уширением, а также в закрытых штампах с вертикальными поверхностями гравюр, не имеющими углов наклона, например, на горизонтальных ковочных машинах или под молотом или прессом в закрытых штампах с выталкивателем.
Малопластичные и хрупкие сплавы следует обрабатывать прессованием с противодавлением, когда пластическая деформация осуществляется при неравномерном всестороннем сжатии с высокими главными сжимающими напряжениями и при малых деформациях и напряжениях растяжения.
АЛЮМИНИЕВЫЕ СПЛАВЫ.
Технический алюминий (АЛ1 и АЛ) имеет высокую пластичность. Он может деформироваться холодной и горячей ковкой и штамповкой при разных видах нагружения. При этом изменение скорости деформации не вызывает значительного понижения пластичности алюминия. Технический алюминий подвергают ковке и штамповке на прессах, ковочных машинах и молотах преимущественно на плоских бойках и в открытых штампах.
Алюминиевые сплавы мягкие (АВ, АМц, АМН, АМг2, АД31, АДЗЗ и др.) и средней прочности (Д1, АК2, АК4, АК6, ВД17, АМгб и др.) имеют хорошую пластичность. Они обрабатываются ковкой и горячей штамповкой при напряженно-деформированных состояниях, в которых действуют деформации и напряжения растяжения. Ковка сплавов этих групп производится на молотах и гидравлических прессах на плоских бойках и в открытых и полузакрытых штампах. Горячую штамповку мягкой и средней прочности сплавов выполняют на молотах, ковочных машинах, кривошипных и гидравлических прессах.
Мелкие и средние детали машин штампуют на кривошипных прессах, а крупные — на гидравлических прессах. Крупные штамповки могут штамповаться и на молотах. Алюминиевые сплавы высокопластичные и средней пластичности могут обрабатываться давлением при напряженно-деформированном состояниях от самых жестких (осадка с свободным уширением) до мягких (штамповка в закрытом штампе без уширения) механических схем деформации.
Алюминиевые сплавы высокой прочности (В93, В95, В96, АКЗ, В АД 23 и др.) имеют пониженную пластичность по сравнению со сплавами других групп.
Эти сплавы обрабатывают ковкой и горячей штамповкой при более мягких напряженно-деформированных состояниях и преимущественно на гидравлических и кривошипных прессах. Обработка сплавов с такой скоростью деформирования при соблюдении установленных параметров ковки и горячей штамповки не переводит их в хрупкое состояние.
Штамповку мелких и средних размеров деталей производят на кривошипных прессах, крупных — на гидравлических прессах. Сплавы высокой прочности могут обрабатываться ковкой и горячей штамповкой и на молотах.
Для обработки малопластичных сплавов необходимо применять закрытые и полузакрытые методы деформации.
Хрупкие алюминиевые сплавы, например, типа системы Be— А1 и «САП» должны обрабатываться новыми методами прессования и штамповки с противодавлением и с применением пластичных оболочек.
Деформация слитков всех алюминиевых сплавов, как правило, для исключения действия значительных растягивающих напряжений и деформаций должна производиться прессованием на деформацию 50— 60%.
Определение методов ковки и штамповки и вида напряженно-деформированного состояния в зависимости от.пластичности алюминиевых и других сплавов должно производиться по классификации методов обработки давлением по напряженному и пластическому состояниям обрабатываемого сплава.
МАГНИЕВЫЕ СПЛАВЫ.
Сплавы системы магний — марганец с небольшими добавками церия (MAI, МА8) обладают высокой пластичностью при горячей и холодной обработке давлением и подвергаются деформации при мягких и жестких напряженных состояниях (ковке, штамповке и др.).
Сплавы магния с различным содержанием алюминия и добавками небольших количеств цинка и марганца (МА2, МА2-1, МАЗ, МА5) имеют более высокие прочностные характеристики и пониженный запас пластичности. Пластичность этих сплавов существенно понижается с увеличением содержания в них алюминия. Наибольшей пластичностью в горячем состоянии обладает сплав МА2, который удовлетворительно подвергается ковке и горячей штамповке .даже и при жестких механических схемах деформации. Однако скорость деформации при этом не должна быть высокой. Примерно такая же закономерность установлена и для сплава МАЗ, который при таких видах нагружения или ковке и штамповке обладает удовлетворительной пластичностью. Сплав МА5 имеет пониженный запас пластичности и горячую обработку давлением производят при мягких видах напряженно-деформированного состояния (прессование в контейнере, штамповку в закрытых штампах и др’.).
Сплавы магния с цирконием (ВМ65-1 и др.) относятся к группе малопластичных сплавов. Ковку и горячую штамповку сплавов этой группы производят также- при мягких видах напряженно-деформированного состояния с минимальными растягивающими напряжениями.
Высоколегированные сплавы, обладающие низким запасом пластичности, необходимо подвергать ковке и горячей штамповке методом прессования — штамповки с противодавлением, обеспечивающим деформацию с высокими главными сжимающими напряжениями.
ТИТАНОВЫЕ СПЛАВЫ.
Технический титан (ВТ1) при осадке на прессе при комнатной температуре не разрушается до деформации 50%; при повышении температуры пластичность повышается и он может деформироваться без образования трещин при 600° С на 80%, а при 900° С на 90%.
Титановые сплавы ВТЗ-1 и ВТ5 при комнатной температуре без перевода в хрупкое состояние деформируются статической осадкой на 10—15%. В случае осадки на прессе при 600° С допустимая деформация составляет 60%, а при 900° С — увеличивается до 90%.
В случае динамического деформирования под молотом пластичность титановых сплавов снижается на 10—20%. Так, для сплавов
ВТЗ-1 п ВТ5 при осадке под молотом при 600° С допустимая деформация равна 50%, а при 900°— 80%.
Титан при холодной свободной ковке осадкой и штамповкой допускают ограниченные деформации. Допустимые деформации при холодной обработке могут быть увеличены применением ковки в вырезных бойках и штамповке в закрытых и открытых штампах с ограниченным уширением, когда действуют напряженно-деформированные состояния, при которых деформации и напряжения растяжения относительно невелики.
При горячем деформировании и, особенно, при температурах 900° С и выше, когда развиваются разупроч-няющие процессы, титан и титановые сплавы имеют достаточно высокую пластичность. Из титановых сплавов ковкой и горячей штамповкой изготовляются сложные по геометрической форме детали машин (лопатки, диски компрессоров и другие детали).
Титан и титановые сплавы мало-и среднелегированные могут обрабатываться ковкой и горячей штамповкой всеми применяемыми методами, практически при многих видах нагружения. Эти сплавы при изменении напряженно-деформированного состояния, в пределах применяемых технологических процессов ковки и штамповки, сохраняют достаточно высокую технологическую пластичность.
Для трудно деформируемых титановых сплавов могут применяться полузакрытые и закрытые методы ковки и горячей штамповки — вытяжки в фигурных бойках, осадка в пластичной оболочке, штамповка в закрытых штампах с уширением и без уширения. Такие методы с мягким напряженным состоянием допускают ковку и штамповку с большими деформациями. Кроме возможности обработки с большой деформацией и повышения технологической пластичности, такой технологический процесс обработки давлением обеспечивает более равномерную деформацию и получение мелкозернистой структуры и высоких и равномерных механических свойств.
Пластичность титана и титановых сплавов резко понижается при наличии на поверхности альфированного слоя. Были проведены опыты по ковке — осадкой титановых сплавов, имевших на поверхности остатки альфированного слоя.
Испытанию на осадку подвергались образцы, у которых после обточки альфированного слоя остались на поверхности вдоль образующей черновины — необработанные полоски. Образцы осаживались на механическом кривошипном ковочном прессе на неподогретых штампах при 1000° С.
После осадки со степенью деформации выше 50% на боковой поверхности заготовок, где оставался альфированный слой, появлялись широкие трещины. Причина появления трещин на боковой поверхности заключается в том, что более хрупкий, чем основной металл, альфированный слой, в результате растяжения боковой поверхности образца в начале осадки разрушается, образуя сетку мелких трещин. Эти трещины как концентраторы напряжений, с увеличением степени деформации способствуют резрушению основного металла. Глубина таких трещин находится в пределах 1—2 мм.
Образование трещин при осадке образцов из титановых сплавов с альфированным слоем происходит при покрытии образца густыми смазками (жидкого стекла, графита и др.). Появление трещин в случае применения густых смазок объясняется тем, что пленка смазки между контактными поверхностями создает значительные растягивающие напряжения. Хрупкий альфированный слой этих напряжений не выдерживает и разрушается. С другой стороны гладкие без трещин образцы получаются после деформирования осадкой без смазки и с применением жидких смазок — мазута, машинного масла, компрессорного масла и др.
Смазки жидкой консистенции не вызывают значительной величины поперечной деформации и напряжений растяжения.
Наличие альфированного слоя резко снижает технологическую пластичность титана и титановых сплавов. Металл, имеющий альфированный слой, крайне чувствителен при ковке и горячей штамповке к изменению напряженно-деформированного состояния с увеличением напряжений и деформаций растяжения. Поскольку, практически, при всех методах ковки и штамповки действуют растягивающие напряжения и деформации, при нагреве под горячую механическую обработку титана и титановых сплавов следует избегать образование альфированного слоя. Это достигается нагревом под ковку и штамповку в нагревательных печах с нейтральной или безокислительной атмосферой. Наиболее подходящей средой для нагрева титана и титановых сплавов является аргон.
Титан и титановые сплавы нагреваются в воздушных печах с покрытием заготовок эмалями.
Медные сплавы имеют узкий интервал температур ковки и горячей штамповки, невысокий запас пластичности при свободной ковке и высокую теплопроводность в конечной стадии обработки, вследствие чего эти сплавы приобретают пониженную пластичность. Поэтому для медных сплавов следует применять вид нагружения при ковке и горячей штамповке с возможно наименьшими растягивающими деформациями и напряжениями. Руководствуясь этим, слитки медных сплавов деформируют преимущественно прессованием в контейнерах, а горячую штамповку обычно производят или закрытыми методами обработки (штамповка в закрытых штампах), или полузакрытыми методами, или открытыми, но с ограниченным уширением. При этом технологические процессы применяют с возможно наименьшим числом операций, а в большинстве случаев штампуют детали на одно давление или один удар молота. Для повышения пластичности металла койнтейнеры и штампы подогревают до 300—500° С.
Что такое штамповка металла? | ESI Engineering
Основы штамповки металлов
Следующее руководство иллюстрирует передовые методы и формулы, обычно используемые в процессе проектирования штамповки металлов, и содержит советы по учету соображений снижения затрат в деталях.
Основы штамповки
Штамповка – также называемая прессованием – включает помещение плоского листового металла в рулон или заготовку в штамповочный пресс. В прессе инструмент и поверхность штампа придают металлу желаемую форму.Пробивка, вырубка, гибка, чеканка, тиснение и отбортовка – все это методы штамповки, используемые для придания формы металлу.
Перед формированием материала специалисты по штамповке должны спроектировать инструмент с помощью инженерных технологий CAD / CAM. Эти конструкции должны быть максимально точными, чтобы каждый пуансон и изгиб сохранял надлежащий зазор и, следовательно, оптимальное качество детали. 3D-модель одного инструмента может содержать сотни деталей, поэтому процесс проектирования часто бывает довольно сложным и требует много времени.
После того, как конструкция инструмента определена, производитель может использовать различные услуги механической обработки, шлифования, электроэрозионной обработки и другие производственные услуги для завершения своего производства.
Типы штамповки металла
Существует три основных метода штамповки металла: прогрессивная, четырехсторонняя и глубокая вытяжка.
Прогрессивная штамповка
Прогрессивная штамповка включает несколько станций, каждая из которых выполняет уникальную функцию.
Сначала полоса пропускается через пресс прогрессивной штамповки.Полоса равномерно раскатывается из рулона и попадает в штамповочный пресс, где каждая станция в инструменте затем выполняет различную резку, пробивку или изгиб. Действия каждой последующей станции добавляются к работе предыдущих станций, в результате чего получается завершенная часть.
Производителю, возможно, придется многократно менять инструмент на одном прессе или использовать несколько прессов, каждое из которых выполняет одно действие, необходимое для готовой детали. Даже при использовании нескольких прессов для полной обработки детали часто требовались услуги вторичной обработки.По этой причине прогрессивная штамповка является идеальным решением для металлических деталей со сложной геометрией , чтобы соответствовать:
- Более быстрый ремонт
- Более низкие затраты на рабочую силу
- Более короткая длина пробега
- Более высокая повторяемость
Fourslide Stamping
Fourslide, или мульти-слайд, включает горизонтальное выравнивание и четыре разных слайда; Другими словами, для придания формы заготовке одновременно используются четыре инструмента. Этот процесс позволяет выполнять сложные разрезы и изгибы даже самых сложных деталей.
Штамповка металла Fourslide может предложить несколько преимуществ по сравнению с традиционной штамповкой на прессе, что делает его идеальным выбором для многих областей применения. Вот некоторые из этих преимуществ:
- Универсальность для более сложных деталей
- Большая гибкость для изменения конструкции
Как следует из названия, четырехслайд имеет четыре слайда, что означает, что можно использовать до четырех различных инструментов, по одному на слайд для одновременного выполнения нескольких изгибов. По мере того, как материал поступает в ползун, он быстро изгибается каждым валом, оснащенным инструментом.
Штамповка с глубокой вытяжкой
Глубокая вытяжка заключается в вытягивании заготовки из листового металла в матрицу с помощью штампа для придания ей определенной формы. Этот метод называется «глубокой вытяжкой», когда глубина вытянутой детали превышает ее диаметр. Этот тип формовки идеально подходит для создания компонентов, которым требуется несколько серий диаметров, и является экономичной альтернативой токарным процессам, которые обычно требуют использования большего количества сырья. Распространенные области применения и продукты, изготовленные методом глубокой вытяжки, включают:
- Автомобильные компоненты
- Запчасти для самолетов
- Электронные реле
- Посуда и кухонная утварь
Штамповка коротких тиражей
Штамповка металла короткими тиражами требует минимальных предварительных затрат на инструмент и может быть идеальным вариантом решение для прототипов или небольших проектов.После создания заготовки производители используют комбинацию пользовательских компонентов оснастки и штамповочных вставок для гибки, штамповки или сверления детали. Операции формовки по индивидуальному заказу и меньший размер тиража могут привести к более высокой цене за штуку, но отсутствие затрат на инструмент может сделать краткосрочный тираж более рентабельным для многих проектов, особенно тех, которые требуют быстрого выполнения.
Изготовление инструментов для штамповки
Изготовление штамповки металла состоит из нескольких этапов. Первый шаг – это разработка и изготовление самого инструмента, используемого для создания продукта.
Давайте посмотрим, как создается этот начальный инструмент: Макет и дизайн полосы запаса: Дизайнер использует для проектирования полосы и определения размеров, допусков, направления подачи, минимизации брака и многого другого.
Обработка инструментальной стали и штампов: ЧПУ обеспечивает более высокий уровень точности и повторяемости даже для самых сложных штампов. Такое оборудование, как 5-осевые фрезерные станки с ЧПУ и электроэрозионные станки, может обрабатывать закаленную инструментальную сталь с очень жесткими допусками.
Вторичная обработка: Термическая обработка применяется к металлическим деталям, чтобы повысить их прочность и сделать их более долговечными для применения. Шлифование используется для чистовой обработки деталей, требующих высокого качества поверхности и точности размеров.
Wire EDM: Электроэрозионная обработка проволоки формирует металлические материалы с помощью электрически заряженной жилы латунной проволоки. Электроэрозионный станок позволяет резать самые сложные формы, включая небольшие углы и контуры.
Процессы проектирования штамповки металла
Штамповка металла – это сложный процесс, который может включать в себя ряд процессов штамповки металла – вырубку, штамповку, гибку, прошивку и многое другое. Вырубка: Этот процесс заключается в вырезании грубого контура или формы изделия. На этом этапе необходимо свести к минимуму и избежать заусенцев, которые могут повысить стоимость вашей детали и увеличить время выполнения заказа. На этом этапе вы определяете диаметр отверстия, геометрию / конусность, расстояние от края до отверстия и вставляете первую пробивку.
Гибка: Когда вы проектируете изгибы штампованной металлической детали, важно предусмотреть достаточно материала – убедитесь, что ваша деталь и ее заготовка спроектированы таким образом, чтобы было достаточно материала для выполнения изгиба .Некоторые важные факторы, о которых следует помнить:
- Если изгиб сделать слишком близко к отверстию, оно может деформироваться.
- Пазы и выступы, а также прорези должны иметь ширину, которая как минимум в 1,5 раза превышает толщину материала. Если сделать их меньше, их будет сложно создать из-за силы, прилагаемой к ударам, вызывающих их поломку.
- Каждый угол в вашей заготовке должен иметь радиус, составляющий не менее половины толщины материала.
- Чтобы свести к минимуму количество и серьезность заусенцев, по возможности избегайте острых углов и сложных вырезов.Если таких факторов невозможно избежать, обязательно отметьте направление заусенцев в своей конструкции, чтобы их можно было учесть во время штамповки
Чеканка: Это действие происходит, когда края штампованной металлической детали ударяются, чтобы сплющить или сломать заусенец; это может создать более гладкую кромку в области геометрической формы детали; это также может добавить дополнительную прочность локализованным областям детали, и это можно использовать, чтобы избежать вторичных процессов, таких как удаление заусенцев и шлифование. Некоторые важные факторы, о которых следует помнить:
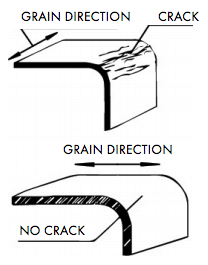
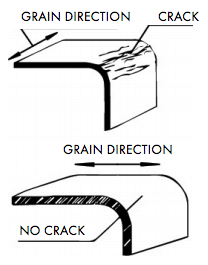
Пластичность и направление волокон – Пластичность – это мера постоянной деформации, которой подвергается материал под действием силы.Металлы с большей пластичностью легче формировать. Направление волокон важно в высокопрочных материалах, таких как закаленные металлы и нержавеющая сталь. Если изгиб проходит по волокну с высокой прочностью, оно может растрескиваться.
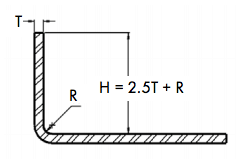
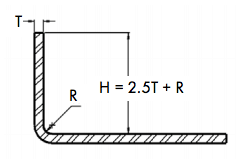
Высота изгиба – Общая высота изгиба имеет минимальные требования для эффективного формирования и должна быть как минимум в 2,5 раза больше толщины материала + радиус изгиба
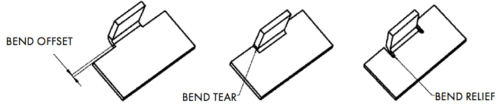
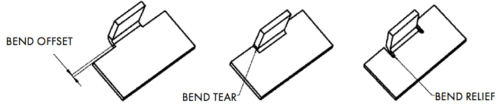
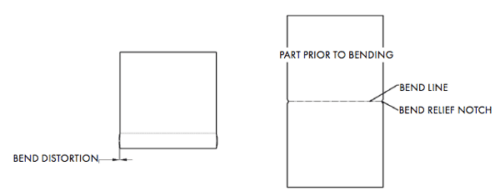
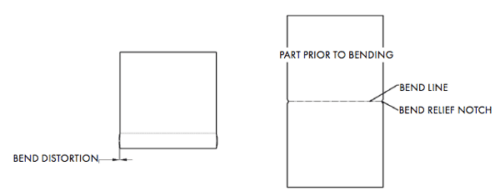
Разгрузка изгиба – Добавьте небольшие выемки, расположенные непосредственно рядом с частью детали, которую нужно согнуть – они должны быть как минимум в два раза шире, чем толщина материала, и равны радиусу изгиба плюс толщина материала.
Деформация / выпуклость изгиба: Выпуклость, вызванная деформацией изгиба, может достигать ½ толщины материала. По мере увеличения толщины материала и уменьшения радиуса изгиба деформация / выпуклость становится более серьезной. Несущая перемычка и разрез «несоответствие»: Это когда требуется очень небольшой врезание или выпуклость на детали, обычно глубиной около 0,005 дюйма. В этой функции нет необходимости при использовании составного инструмента или инструмента трансферного типа, но требуется при использовании инструмента с прогрессивной головкой.
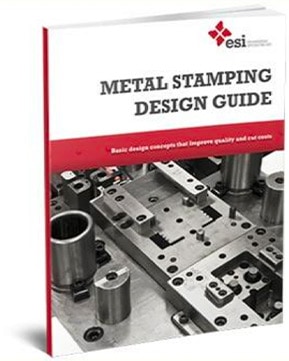
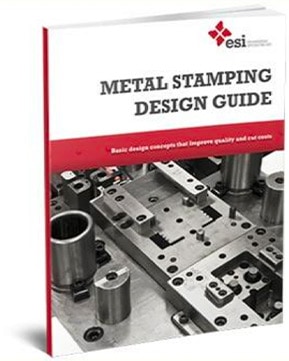
Хотите снизить производственные затраты на штампованные металлические детали?
Загрузите наше Руководство по проектированию штамповки металлов.
Внутри мы рассмотрим:
- Как избежать дорогостоящих ошибок проектирования
- Экономичные процессы штамповки для замены дорогостоящих вторичных услуг
- Рисунки, иллюстрирующие разгрузку при изгибе, пластичность, угол излома и многое другое
Загрузите бесплатное руководство по проектированию
Штамповка металла по индивидуальному заказу
Штамповка металла по индивидуальному заказу описывает процессы формования металла, которые требуют специальных инструментов и методов для производства деталей, указанных заказчиком.В широком спектре отраслей и сфер применения используются индивидуальные процессы штамповки для удовлетворения потребностей крупносерийного производства и обеспечения точного соответствия всех деталей спецификациям.
Проекты по штамповке металла на заказ
Инженеры-конструкторы могут работать над широким спектром проектов штамповки металла для клиентов из различных отраслей. Чтобы лучше проиллюстрировать универсальность штампованных металлических деталей по индивидуальному заказу, ниже мы описали несколько недавних проектов, выполненных инженерами ESI.
Изготовленная на заказ деталь для оборудования для мониторинга жизнедеятельности в медицинской промышленности
Клиент из медицинской отрасли обратился к ESI с просьбой изготовить индивидуальную металлическую штамповку на детали, которая будет использоваться в качестве пружины и электронного экрана для контроля жизненно важных функций оборудование в медицинской сфере.
- Им требовалась коробка из нержавеющей стали с пружинными язычками, и возникли проблемы с поиском поставщика, который предоставил бы высококачественный дизайн по доступной цене в разумные сроки.
- Чтобы удовлетворить уникальную просьбу клиента покрыть только один конец детали, а не всю деталь, мы заключили партнерские отношения с ведущей в отрасли компанией по лужению, которая смогла разработать усовершенствованный процесс селективного покрытия одной кромки.
ESI смогла удовлетворить сложные требования к проектированию, используя технику штабелирования материалов, которая позволила нам вырезать сразу несколько заготовок деталей, что ограничило затраты и сократило время выполнения заказа.
Штампованный электрический соединитель для электропроводки и кабеля
В другом случае нас попросили изменить дизайн существующей крышки электрического соединителя; Заказчик, компания AFC Cable Systems, искал продукт более высокого качества по более низкой цене и в более короткие сроки.
- Конструкция была очень сложной; эти крышки предназначались для использования в качестве шлейфовых кабелей внутри электрических каналов в полу и под полом; поэтому это приложение по своей сути имело строгие ограничения по размеру.
- Производственный процесс был сложным и дорогостоящим, так как некоторые работы клиента требовали полностью завершенного покрытия, а другие – нет, то есть AFC создавала детали из двух частей и при необходимости сваривала их вместе.
- Работая с образцом крышки разъема и одним инструментом, предоставленным клиентом, наша команда в ESI смогла реконструировать деталь и ее инструмент. Отсюда мы разработали новый инструмент, который можно использовать в нашем 150-тонном прогрессивном штамповочном прессе Bliss.
- Это позволило нам изготавливать деталь как одно целое со сменными компонентами, а не производить две отдельные детали, как это делал заказчик.
Это позволило значительно сэкономить – 80% от стоимости заказа из 500 000 деталей – а также сократить время выполнения заказа на четыре недели вместо 10.
Специальная штамповка для автомобильных подушек безопасности
Заказчику автомобильной отрасли потребовалась высокопрочная, устойчивая к давлению металлическая втулка для использования в подушках безопасности Ford Transit Vans.
- При вытяжке 34 мм x 18 мм x 8 мм втулка должна выдерживать допуск в 0,1 мм, а производственный процесс должен учитывать уникальное растяжение материала, присущее конечному применению.
- Из-за своей уникальной геометрии втулку нельзя было изготовить с использованием трансферного пресса, а ее глубокая вытяжка представляла собой уникальную проблему.
Команда ESI создала прогрессивный инструмент с 24 станциями, чтобы обеспечить надлежащее развитие вытяжки, и использовала сталь DDQ с цинкованием для обеспечения оптимальной прочности и коррозионной стойкости. Штамповку металла можно использовать для создания сложных деталей для самых разных отраслей промышленности. Хотите узнать больше о различных приложениях для штамповки металлов, над которыми мы работали? Посетите нашу страницу тематических исследований или обратитесь непосредственно к команде ESI, чтобы обсудить ваши уникальные потребности с экспертом.
Мы очень довольны тем, что являемся клиентами ESI в течение последних 10 лет.Они чрезвычайно профессиональны, обеспечивают отличное качество и, что самое главное, делают работу с ними увлекательной.
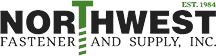
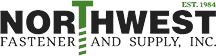
Len Odegaard
President
Northwest Fastener Sales
Я бы порекомендовал ESI для будущих штампованных деталей (деталей из листового металла) в будущем. Щиты Близнецов, похоже, не так-то просто изготовить, и, как вы знаете, нам было сложно найти подходящего продавца. Качество работы отличное, а точность размеров – выдающаяся.Я считаю, что с ними очень легко работать и они очень удобны для развития. Цены разумные, и приятно работать с местным представителем.
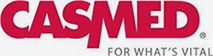
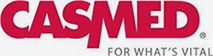
Рой Абрамс
Старший инженер-механик
Casmed Medical Systems, Inc.
Штамповка листового металла 101, Часть I
Примечание редактора: в этой серии представлен обзор штамповки металлов. Часть I посвящена различным профессиям в индустрии штамповки металлов. В Части II обсуждаются штамповочные материалы и оборудование; Часть III. основное внимание уделяется штампам и резке, а часть IV предлагает более подробную информацию о процессах резки. В последней части, части V, исследуются методы формования.
Чтобы оставаться занятым в сегодняшней экономике, вы должны быть разносторонне развиты в отношении своих навыков.С сокращениями у компаний теперь меньше ресурсов для выполнения работы. Сотрудники часто носят много головных уборов. В одну минуту вы специалист по обслуживанию инструментов и штампов, в следующую – контроль качества, а затем вы оказываетесь в отделе котировок. Вы уловили идею.
Поскольку моя серия “Die Basics 101” настолько популярна, я решил выпустить новую серию, которая расширяет основы штамповки штампов и процессов и дает более глубокое представление о процессе штамповки металла в целом.
Вы, вероятно, читаете эту статью, потому что либо работаете с штампами, либо хотели бы заняться этим в будущем.Эта вводная статья предназначена для тех, кто практически не имеет опыта штамповки листового металла. Как инженер-технолог, разработчик штампов, изготовитель штампов, установщик или техник по обслуживанию штампов, вам будет полезно знать, какой частью более крупной головоломки вы являетесь.
Как штамповка влияет на нашу жизнь
Несомненно, штамповка кардинально изменила нашу жизнь. Обычные предметы домашнего обихода, такие как стиральные машины и сушилки, изготавливаются с использованием процесса штамповки из листового металла.Предметы, которые мы часто принимаем как должное, такие как столовые приборы, которые мы используем для еды, кастрюли и сковороды, которыми мы готовим, и автомобиль, на котором мы ездим, частично производятся методом штамповки листового металла. Бидоны для напитков, зажигалки, патроны для оружия, даже некоторые виды ювелирных изделий из чистого золота производятся с использованием этого процесса. Компьютер, на котором вы читаете эту статью, содержит штампованные детали.
Как выглядит штамповка
Мне очень интересно, как восприятие штамповки листового металла и штамповщиков меняется от человека к человеку.Некоторые люди думают, что штамповка – это типично грязная «фабричная работа», в то время как другие думают, что штамповщики – это высококвалифицированные люди, которые хорошо владеют своими руками. По правде говоря, проектирование и изготовление штампов, устранение неисправностей и техническое обслуживание – это профессиональных карьерных путей . Хорошо Конструкторы и производители лучше владеют мозгом, чем руками. Многие практические навыки, необходимые в прошлом, были заменены новыми процессами, такими как прожигание проволоки и ЧПУ.
В любом случае, как штамповщики, мы должны быть мастерами своего дела и мириться ни с чем, кроме совершенства.Помните, что совершенство в производстве инструментов и штампов означает, что все важное должно подходить и функционировать должным образом. Подгонка и функциональность – ключ к успеху. Некоторые компоненты штампа должны изготавливаться с предельной точностью размеров, в то время как другие не требуют такой точности. Ключ в том, чтобы взять время, чтобы сделать точные компоненты точными по размеру, и не тратить время на менее важные элементы.
Красота идет только так далеко
Как консультант, я нахожу несколько неприятным видеть кубик, который выглядит так же хорошо, как ювелирное изделие, когда им нужны только его части.Хотя производитель инструментов может гордиться внешним видом инструмента, тратить время на полировку в штампе вещей, которые не нужно полировать, – расточительство. Компании обычно покупают матрицы не по их внешнему виду, а по характеристикам. Гордимся в производительности инструмента, а не в его внешнем виде.
Наука – не искусство
Работа в качестве мастера по изготовлению инструментов и штампов или дизайнера может оказаться отличным выбором для многих людей. Сначала давайте отбросим некоторые злобные слухи о постройке штампов и торговле штампами.Несмотря на то, что вам могут сказать некоторые инструментальщики, профессия – это не вид искусства. Это наука и профессиональная карьера. Хорошие мастера и дизайнеры не принимают решений на основе на вдохновении, которое они получили ранее в тот день. Их намерение не в том, чтобы создавать что-то, что призвано «вдохновлять» эмоции.
Не путайте творчество с искусством. Мастера инструментов и дизайнеры должны быть очень креативными в своем мыслительном процессе. В отличие от художника, который стремится вызывать эмоции, дизайнер должен создать что-то, что работает правильно.
Чтобы быть хорошим мастером или дизайнером, каждое решение, которое вы принимаете в отношении штампа, должно основываться на хорошем понимании физики. Это очень просто: если подбросить яблоко в воздух, оно упадет. Неважно, насколько вы артистичны.
Карьера мастера по изготовлению инструментов и штампов не только очень сложна, но и требует большого образования. Часть этого образования носит академический характер, в то время как большая часть вашего обучения будет связана с фактическим опытом работы в цехе.Хотя вы можете не получить степень Университета X, будьте уверены, это профессиональный путь к карьере. Я работаю со многими профессионалами в области образования, некоторые с докторами наук, которые консультируют меня по проектам. Только совместными усилиями академического и реального опыта мы можем добиться успеха.
Как производитель штампов или дизайнер, вы можете нести ответственность за принятие решений, которые в конечном итоге будут стоить тысячи, а иногда и миллионы долларов. К суждениям нельзя относиться легкомысленно; плохое решение может разрушить организацию.Пекарь может проглотить свои ошибки, но плохой кубик нельзя использовать даже в качестве якоря для лодки. Больше повод стремиться к совершенству.
Почему штамповка листового металла?
Система . Вы слышали фразу «необходимость – мать изобретений», которую можно описать одним словом: потребность. Крупные компании, такие как производители автомобилей, самолетов или бытовой техники, часто испытывают потребность в инструментах для листового металла. Эти компании называются производителями оригинального оборудования (OEM).
Если OEM-производитель видит потребность в детали или новой линейке продуктов, он будет определять наилучший способ их производства.Здесь важны обширные знания о множестве различных процессов. Например, если деталь большого объема можно штамповать, а не отливать, эта деталь может быть изготовлена со значительно меньшими затратами.
Некоторые производители оригинального оборудования могут сами создавать инструменты и запускать штампы; однако они часто передают на аутсорсинг производство деталей. Это означает, что они могут нанять компанию, которая предоставит запчасти для удовлетворения их потребностей. Эти внешние компании, которые работают напрямую с OEM-производителями, называются поставщиками первого уровня.
В сфере штамповки листового металла поставщик уровня 1 обычно владеет несколькими штамповочными прессами и надеется получить контракт на поставку деталей OEM. Но OEM не просто раздает контракты с поставщиками. Поставщик уровня 1 должен подать заявку на контракт. После того, как компания заключила контракт на поставку деталей, она должна построить штамп, который работает в ее прессах для изготовления деталей. В Компания может иметь подразделение, которое производит штампы, но многие должны найти источник инструментов для поставки штампа, который, в свою очередь, должен подать заявку на заключение контракта на его изготовление.
Что такое операция штамповки листового металла? Операция штамповки листового металла – это операция, при которой листовой металл разрезается и формируется желаемая форма или профиль. Хотя в процессе штамповки листового металла могут использоваться различные типы специальных станков, важны три основных элемента: листовой металл, из которого должна быть изготовлена деталь; штамповочный пресс; и штамп для штамповки.
За исключением специального процесса штамповки листового металла, обычно называемого горячей штамповкой, большинство операций штамповки листового металла включают холодную штамповку.По сути, это означает, что в матрицу или листовой материал намеренно не вводится тепло. Однако имейте в виду, что, хотя штамповка является процессом холодной штамповки, выделяется тепло. Резка или формовка листового металла создает трение между матрицей и металлом – очень похоже на трение и тепло, возникающие при трении рук друг о друга.
Поскольку тепло выделяется из-за трения в процессе резки и формовки, штампованные детали часто очень горячие на выходе из штампов.
Какие профессии связаны со штамповкой листового металла? Вы можете заниматься многими видами деятельности, связанными со штамповкой, например, инженером-технологом, проектировщиком штампов, машинистом, изготовителем штампов или техником по обслуживанию штампов.
Инженер-технолог отвечает за определение шагов, необходимых для превращения плоского металлического листа в готовую деталь – критическая задача и важная позиция. Одна ошибка процесса может быстро привести к сбою.
Разработчики штампов несут ответственность за разработку инструментов для эффективного выполнения установленного процесса.Многие люди одновременно работают инженерами-технологами и проектировщиками штампов. Эффективные конструкторы штампов хорошо разбираются в механическом движении, а также в прочности материалов и типах инструментальной стали. Они имеют опыт работы с САПР или компьютерным программным обеспечением.
Машинисты несут ответственность за вырубку компонентов штампа из указанных материалов до их надлежащих размеров.
Изготовители штампов собирают и конструируют инструмент. Они также должны протестировать штамп, чтобы убедиться, что он работает должным образом и стабильно производит приемлемую деталь.
Специалисты по обслуживанию производственных штампов обслуживают, ремонтируют и устраняют неисправности штамповочных штампов.
Следите за выходом следующего выпуска из серии “Штамповка листового металла 101”. Пожалуйста, не стесняйтесь обращаться к редактору этой публикации, чтобы предложить будущие темы.
.Новый процесс улучшает формуемость материала, уменьшает образование складок
Объект
Исследования, проведенные в Университете штата Огайо в течение последних нескольких лет, показали, что когда материал растягивается с высокой скоростью, он менее склонен к разрыву, чем при медленном растяжении. Это потому, что действие разрыва материала вызывает изменение направления. Если это делается очень быстро (как это происходит на высоких скоростях), инерция и ускорение сопротивляются этому изменению скорости.Гленн С. Даен, доктор философии и профессор Департамента материаловедения и инженерии штата Огайо называет эту расширенную пластичность в условиях высоких скоростей как гиперпластичность .
Работая с производителями и промышленными партнерами, группа Daehn разработала ряд стратегий, которые можно использовать для экономичного формования алюминиевых компонентов, демонстрируя, что электромагнитное формование (ЭМП) предлагает элегантные подходы к формированию сложных компонентов и может улучшить формование. пределы в металлах.
Как работает ЭДС
Формовка листового металла с высокой скоростью может улучшить формуемость материала (степень растяжения без разрывов) и значительно уменьшить образование складок. «ЭДС – это очень удобный способ гибкого создания высокоскоростной деформации», – говорит Даен.
В ЭДС, когда электрический ток быстро накладывается на электрический проводник, он создает магнитное поле. «Это магнитное поле индуцирует вихревые токи в любом близлежащем проводнике, и эти вихревые токи создают собственное магнитное поле и вызывают взаимное отталкивание между заготовкой и приводом», – говорит Даен.
Daehn описывает эту технику как подходящую для любой детали, сделанной из хорошего проводника, при условии, что импульс тока имеет достаточно высокую частоту.
Создание этой техники – результат «большой интуиции», – говорит Даен. «Около 12 лет назад компания обратилась в Университет штата Огайо с просьбой об использовании электрогидравлической формовки для сборки компонентов вентиляции. Оборудование было оставлено после проекта. Имея опыт работы в гидропластике, я интересовался, что с ним можно сделать.
Он продолжает: «С середины 1970-х годов в этой области было очень мало специальной работы. Несмотря на то, что сегодня все еще практикуется некоторая взрывная формовка, а ЭДС используется в качестве метода сборки, техническое сообщество в значительной степени утратило это видение ». скоростных процессов и думаю, что это коренным образом изменит способ формования листового металла
Весь анализ листового металла предполагает, что материал движется очень медленно без инерции.Этот метод обеспечивает выгодный способ использования инерции путем добавления новых степеней свободы и изготовления деталей, которые иначе невозможно изготовить.
С ростом спроса на экономичные автомобили автопроизводители продолжают исследовать возможности повышения топливной эффективности. Снижение веса, безусловно, является наиболее эффективным методом, однако существуют только два основных метода снижения веса автомобиля: оптимизация конструкции или использование легкого материала.
Алюминий предлагает уникальное сочетание свойств, включая легкую массу, с некоторыми сплавами, более прочными, чем конструкционная сталь, согласно исследованию Центра инженерных исследований профессора Тайлана Алтана по производству формы сетки при Университете штата Огайо.
Компания Honda Research & Development в Точиги, Япония, производит штамповки алюминиевых деталей для Acura NSX. «Мы были впечатлены легкостью, с которой ему можно придать форму, используя широкий спектр методов формования, – говорит Казухико Цунода, главный инженер по конструкции алюминиевых корпусов.
Литые алюминиевые материалы позволяют формировать сложные формы из одной детали, помогая более жестко соединять экструдированные детали с использованием меньшего количества деталей. Таким образом, жесткое тело может быть создано с использованием литого под давлением алюминия для соединения элементов между конструктивными элементами.Таким образом, используя преимущества алюминия, можно добиться повышенной жесткости и защиты пассажиров без ущерба для легкости.
«Алюминиевый кузов по-прежнему стоит дорого, хотя его цена значительно снизилась с тех пор, как мы представили NSX на рынке», – говорит Цунода. «Мы рассмотрим возможность применения алюминия в будущих моделях, если стоимость этого будет соизмерима с их концепцией».
Штамповка металла с использованием EMF
Преимущества штамповки металла с использованием EMF включают:
- Уменьшение количества операций.
- Улучшенная формуемость.
- Улучшенное распределение деформации.
- Меньше складок.
- Контролируемое пружинение.
- Меньшая зависимость от смазочных материалов.
- Никаких опасных химикатов для очистки.
- Нет электромагнитного излучения.
- Более низкая стоимость энергии.
«Хотя это не новый процесс, некоторые работы доктора Даэна действительно современные», – говорит Майкл Плам, генеральный директор Maxwell Magneform в Сан-Диего. «С помощью обычных штампов вы можете формировать сложные радиусы в стальном листе.Если сделать такой же лист из алюминия, удлинения и растяжения не будет.
«Что этот метод привносит в процесс, так это способность материала достигать некоторых из этих контуров. При высоких скоростях материал становится более пластичным, создавая большее удлинение».
Оборудование Maxwell Magneform используется для производства впускных электрических топливных насосов и топливных рам в Delphi Automotive. «В последнее время мы наблюдаем большую активность в области электродвигателей и холодильного оборудования. Это также популярно для медицинских устройств, поскольку оборудование бесконтактное, очень чистое и не требует смазки», – говорит Плам.
Использование ЭМП на алюминии
Использование ЭМП на алюминии дает некоторые преимущества:
- Материалы можно перемещать способами, которые иначе не могли бы перемещаться в результате пластичности.
- Бесконтактное приложение магнитного давления перемещает материалы, не касаясь их.
- Операторы не нуждаются в специальной подготовке для работы с оборудованием.
«Тем не менее, персонал по техническому обслуживанию нуждается в обучении, и мы почти настаиваем на том, чтобы компания послала сюда человека для обучения, прежде чем мы отправим машину на завод», – говорит Плам.
«Если два метода сопоставимы, основная причина, по которой компания выбрала бы этот процесс, – повторяемость. Поскольку он электрический и бесконтактный, ничто не изнашивается. Независимо от того, сделаете ли вы одну деталь или миллион деталей, все они будут выглядеть одинаково», – говорит Слива.
IAP Research, Inc. в Дейтоне, штат Огайо, является одним из пионеров в разработке процессов магнитного формования для промышленного использования. IAP создала Центр технологий магнитного прессования (MPTC) в своей штаб-квартире, чтобы помочь производителям разрабатывать компоненты, использующие технологии магнитного прессования, такие как процессы динамического уплотнения магнитного порошка (DMPC), ЭДС и магнитно-импульсной сварки (MPW).
«Большинство компаний обращаются в центр, потому что у них есть проблема, которую они не могут решить», – говорит Дуэйн Ньюман, менеджер программы EMF в IAP. «Некоторые проблемы поддаются магнитным решениям, но почти все требуют некоторой оценки».
«В ходе этих первых усилий мы пытаемся уйти от того, чтобы определить, является ли проект выполнимым и экономичным, и мы пытаемся определить требования к производственной системе на основе исследований», – говорит Джон Барбер, президент IAP.
«Мы согласны с Dr.Даен, что формование металла использовалось недостаточно, – говорит Ньюман. – С нашей точки зрения, теперь мы можем делать вещи, которые были немыслимы в 1960-х годах. Мы можем переместить много металла ».
Взгляд в будущее
Возможно, единственная проблема состоит в том, что, когда люди видят штамповку металла и ЭДС, они думают, что это может решить любую проблему, но не может». Мы ограничены в смысле – материалы, которые мы можем формировать – только те, которые обладают электропроводностью », – говорит Плам.
При дополнительных разработках высокоскоростная ЭДС может решить серьезные проблемы, которые сейчас существуют при формовании алюминия и других материалов с ограниченной формуемостью.«Благодаря сочетанию проницательности и инженерной мысли, когда-нибудь это станет стандартной техникой обработки металлов давлением», – говорит Даен. «Я бы хотел увидеть это при жизни».
.Die Basics 101: Введение в штамповку
Рисунок 1 |
Когда я провожу конференции, нет ничего необычного в том, что один или два участника являются новичками в мире штамповочных штампов и прессов. . Некоторые из них – молодые новые сотрудники, пытающиеся узнать о штамповке, а другие – люди, которых перевели из другого отдела и бросили волкам в отделе штамповки.
Эта статья является первой из серии, предназначенной для ознакомления начинающих инструментальщиков, техников по ремонту штампов, инженеров и техников по штамповке.Серия определит штамп, а также операцию штамповки. Также будут обсуждаться операции резки и формовки, компоненты и функции, а также различные методы, используемые для штамповки деталей.
Что такое штамп?
Штамповочная матрица – это особый единственный в своем роде прецизионный инструмент, который вырезает и формует листовой металл в желаемую форму или профиль. Режущие и формовочные секции штампа обычно изготавливаются из специальной закаленной стали, называемой инструментальной сталью . Плашки также могут содержать режущие и формовочные части из карбида или других твердых износостойких материалов.
Штамповка – это операция холодной штамповки, при которой тепло не передается намеренно в матрицу или листовой материал. Однако, поскольку тепло выделяется из-за трения в процессе резки и формовки, штампованные детали часто выходят из штампов очень горячими.
Рисунок 2 Типичная обрезная кромка штампованной детали |
Размеры штампов варьируются от тех, которые используются для изготовления микроэлектроники, которые могут поместиться на ладони, до 20 футовквадратные и толщиной 10 футов, которые используются для изготовления всех сторон кузова автомобиля.
Деталь, производимая при штамповке, называется штучной деталью (см. , рис. 1 ). Некоторые штампы могут изготавливать более одной детали за цикл и могут выполнять цикл со скоростью 1500 циклов (ходов) в минуту. Сила пресса позволяет штампу работать.
Сколько существует типов кристаллов?
Существует много видов штамповочных штампов, каждый из которых выполняет две основные операции – резку, формовку или и то, и другое.Матрицы, загружаемые вручную или роботом, называются линейными матрицами. Прогрессивные и передаточные матрицы полностью автоматизированы.
Резка
Рис. 3 Обрезка |
Резка, пожалуй, самая распространенная операция, выполняемая в штампе. Металл разрезают, помещая его между двумя обходными секциями инструментальной стали, между которыми имеется небольшой зазор. Этот зазор или расстояние называется зазором для резки.
Зазоры при резании меняются в зависимости от типа выполняемой операции резания, свойств металла и желаемого состояния кромки детали. Зазор резания часто выражается в процентах от толщины металла. Наиболее часто используемый зазор при резке составляет около 10 процентов толщины металла.
Для резки металла требуется очень большое усилие. Этот процесс часто вызывает сильные удары по штампу и прессу. При большинстве операций резания металл подвергается напряжению до точки разрушения, в результате чего образуется режущая кромка с блестящей частью, называемой полосой разреза или сдвигом, и частью, называемой зоной разрушения или линией разрыва (см. , рис. ).
Рисунок 4 Вырезание |
Существует множество различных операций резания, каждая из которых имеет свое специальное назначение. Вот некоторые общие операции:
Обрезка — Внешний периметр формованной детали или плоского листового металла вырезается, чтобы придать детали желаемый профиль. Избыток материала обычно выбрасывается как металлолом (см. , рис. 3 ).
Надрез — Обычно надрезание связано с прогрессивными штампами, надрез – это процесс, в котором операция резания выполняется постепенно на внешней стороне полосы листового металла для создания заданного профиля полосы (см. , рис. 4 ).
Вырубка – Операция резания двойного назначения, обычно выполняемая в большем масштабе, вырубка используется в операциях, в которых заготовка сохраняется для дальнейшей обработки под давлением. Он также используется для вырезания готовых деталей из листового металла. Заготовка из профилированного листового металла, удаленная с листа с помощью этого процесса, называется заготовкой или исходной частью листового металла, которая будет вырезана или сформирована позже (см. , рис. 5, ).
Пробивка – Пробивка, которую часто называют перфорацией, представляет собой операцию резки металла, при которой в плоском листе или в формованной детали образуется отверстие круглой, квадратной или специальной формы.Основное различие между прошивкой и вырубкой заключается в том, что при вырубке используется заготовка, а при прокалывании заготовка выбрасывается как лом. Режущий пуансон, который производит отверстие, называется пробивным пуансоном, а отверстие, в которое он входит, называется матрицей (см. , рисунок 6, ).
Прокалывание —При прокалывании металл разрезается или разрезается, чтобы высвободить металл, не отделяя его от полосы. Прокалывание часто выполняется в прогрессивных штампах для создания носителя детали, называемого гибким или растягивающимся полотном (см. , рис. 7, ).
Ножницы — Режущие пластины или режущие кромки металла по прямой линии. Этот метод обычно используется для производства прямоугольных и квадратных заготовок (см. Рисунок 8 ).
.