Термообработка алюминиевых сплавов: Термическая обработка алюминиевых сплавов | Завод “Алюмлит”
alexxlab | 14.04.2023 | 0 | Разное
Термическая обработка алюминиевых отливок
Металлургия алюминия и его сплавов предлагает ряд возможностей для использования методов термической обработки для получения желаемых сочетаний механических и физических свойств.
Металлургия термической обработки алюминиевых отливок
Режимы термической обработки
Термин “термическая обработка” используется для описания всех термических методов, направленных на изменение металлургической структуры изделий таким образом, чтобы физические и механические характеристики контролируемо изменялись в соответствии с конкретными техническими критериями.
Диаграмма состояния на Fig. 1 дает следующие возможности для термического воздействия на свойства алюминиевых сплавов:
- annealing
- solution heat treatment
- quenching
- ageing (precipitation hardening)
- overageing.
Fig. 1 – Typical temperature ranges for various thermal operations for aluminum alloy castings superimposed
on a binary aluminum-copper phase diagram.
The vertical dashed lines represent alloys containing (a) 4.5% Cu and (b) 6.3% Cu [1].
Термическая обработка алюминиевых сплавов основана на различной растворимости металлургических фаз в алюминии. Растворимость эвтектической фазы с повышением температуры увеличивается. Поэтому управляя образованием и распределением вылеляющихся осажденных фаз можно влиять на свойства материала.
Различие между деформируемыми и литейными алюминиевыми сплавами
В целом, принципы и режимы термической обработки деформируемых и литых сплавов аналогичны. Основные различия между условиями обработки на твердый раствор для отливок и деформируемых изделий заключаются во времени выдержки и типе закалочной среды. Растворение относительно больших микрокомпонентов, присутствующих в отливках, требует более длительных периодов выдержки, чем те, которые применяются для изделий, которые получены методами обработки металлов давлением. Уменьшение напряжений и деформации при закалке также важно, поскольку отливки обычно имеют сложную форму с различной толщиной сечения.
Различные процессы литья и методы литейного производства также приводят к различиям в микроструктуре, имеющим отношение к практике термообработки. Более грубая микроструктура, связанная с медленными скоростями затвердевания, требует, например, более длительного времени при нагреве для достижения твердого раствора. Поэтому, время, необходимое достижения полного растоворения легирующих компненетов в алюминии соотвественно уменьшается, напрмимер, для отливок при лите по выплавляемым моделям, в песчаные формы и в постоянные лиейные формы.
Различие между немодифицированными и модифицированными литейными сплавами
Существует также принципиальная разница между немодифицированными и модифицированными литейнфми сплавами.
В модифицированных размер и форма кристаллов кремния модифицируются добавками таких элементов, как кальций, натрий, стронций или сурьма. Модифицированные сплавы претерпевают быструю сфероидизацию, в то время как в немодифицированных сплавах полная сфероидизация не достигается даже по прошествии очень длительного времени. Практическое значение заключается в том, что для полностью модифицированных отливок може применяться более короткая термообработка на твердый раствор.
Закалочные среды
Закалку алюминиевых отливок часто проводят в кипящей воде или в более мягкой среде, чтобы уменьшить напряжения закалки в сложных формах, например, в смеси полиалкиленгликоля и воды.
Влияние методов литья
На Fig. 2 показано влияние методов литья на развитие свойств. Из-за более тонкой структуры литья и более высокого пересыщения более быстро затвердевающей отливки в постоянной форме их свойства при растяжении превосходят свойства песчаных отливок того же состава, прошедших аналогичную термическую обработку.
Fig. 2 – C.omparison of the precipitation-hardeningc haracteristics of 356.0-T4 sand and permanent-mold castings [2]
Состояния
В алюминиевой промышленности для литейных отливок применяются следующие основные стандартизированные виды термического воздействия (состояния) и их обозначения:
• F, литой
• О, отожженный
• T4, термообработка на твердый раствор и закалка
• T5, искусственно состаренный из литого состояния
• T6, термообработка на твердый раствор, закалка и искусственное старение
• T7, термообработка на твердый раствор, закалка и перестаривание
Для обозначения вариантов состояний от T4 до T7 могут применяться дополнительные цифры, например, такие как T5x, T5xx, T6x и т. д.
Состояния Т5 и Т6
итые изделия из термообрабатываемых алюминиевых сплавов имеют наивысшие сочетания прочности, пластичности и ударной вязкости при изготовлении в состоянии типа Т6. Для получения состояния типа Т6 в литых изделиях требуется та же последовательность операций, что и деформируемых изделий: термическая обработка на твердый раствор, закалка и старение.
Состояние типа Т5 получают просто обработкой на старение литой отливки без предварительной обработки на твердый раствор. Умеренный прирост прочности достигается без коробления и последующей правки. Высокая твердость, размерная и прочностная стабильность при повышенных температурах обуславливают почти универсальное использование материалов в состоянии типа Т5 для поршней и других деталей двигателя.
Состояние Т7
Для некоторых применений требуется сочетание прочности, ударной вязкости и стабильности размеров, чего нельзя достичь при термообработке на состояние типа Т5 или Т6. Для этих применений состояние типа Т7 получают путем:
- термообработки на твердый раствор,
- закалки в среде, обеспечивающей умеренную скорость охлаждения, а затем
- термообработки на искусственное старение при температуре выше, чем те, которые используются для получения отпуска типа Т5 и Т6.
Термическая обработка до отпуска типа Т7 приводит к снижению прочности по сравнению с прочностью материала в отпусках типа Т6, развивает высокую пластичность и ударную вязкость, а выделение осадков происходит достаточно далеко, чтобы свести к минимуму дальнейшее осаждение во время эксплуатации.
Искусственное старение
Наиболее важным видом термической обработки для алюминиевых отливок является старение, обычно – искусственное старение.
Процесс искусственного старения
Необходимым условием для того, чтобы в алюминиевом сплаве происходило упрочнение старением, является уменьшение растворимости в твердом растворе алюминия одного или нескольких компонентов сплава с понижением температуры.
Как правило, процесс искусственного старения включает три стадии:
- При нагреве на твердый раствор (нагреве под закалку) происходит растворение в твердом растворе алюминия достаточного количества компонентов сплава, которые обеспечивают упрочнение старением.
- При достаточно быстром охлаждении при закалке эти компоненты остаются в твердом растворе. В этом состоянии отливки остаются относительно мягкими.
- При старении – для литых изделий, в основном, искусственном – происходит выделение этих растворенных компонентов в форме мельчайших субмикроскопических фаз, которые дают повышение твердости и прочности алюминиевого сплава. Эти мельчайшие фазы, которые по-научному называют «когерентными или полукогерентными фазами», представляют собой препятствия для движения дислокаций в металле и поэтому упрочняют до этого мягкий металл.
Термически упрочняемые литейные алюминиевые сплавы
Термической обработке старением поддаются следующие типы алюминиевых литейных сплавов:
- алюминий-медь;
- алюминий-медь-магний;
- алюминий-кремний- магний;
- алюминий-магний-кремний;
- алюминий-цинк-магний.
Нагрев на твердый раствор (нагрев под закалку)
Для того, чтобы ввести упрочняющие компоненты сплава в твердый раствор так быстро, как это только возможно, температура нагрева на твердый раствор должна быть максимально высокой, не ближе чем 15 °С к температуре ликвидус, чтобы избежать локального подплавления. По этой причине часто литейные алюминиевые сплавы, содержащие медь, подвергают нагреву на твердый раствор в два этапа: сначала до 480 °С, потом до 520 °С.
Длительность нагрева под закалку зависит от толщины стенки отливки и метода литья. По сравнению с литьем в песчаные формы, литье в кокиль требует более короткий нагрев под закалку для растворения упрочняющих компонентов сплава благодаря более измельченной микроструктуре. В принципе, нагрева около одного часа обычно достаточно. Более длительный нагрев под закалку – до 12 часов – применяют, например, для сплавов алюминий-кремний-магний для сфероидизации или округления эвтектического кремния, чтобы повысить пластические свойства сплава (относительное удлинение).
В ходе нагрева под закалку прочность отливок остается еще очень низкой. Поэтому необходимо принимать меры по предотвращению их прогиба и коробления. Для этого большие и сложные отливки закрепляют в специальных приспособлениях.
Закалка алюминиевых отливок
Горячую отливку необходимо охладить в воде как можно быстрее – за 5-20 секунд в зависимости от толщины ее стенок, чтобы подавить любое нежелательное и преждевременное выделение растворенных компонентов сплава.
После закалки отливки имеют высокую пластичность. Резкое охлаждение отливки при закалке может приводить к образованию больших внутренних напряжений и короблению изделия. Эту проблему решают выбором закалочной среды и способа ее подачи: погружение в воду или подача воды через спрейеры – вода холодная, вода горячая или масло.
В любом случае, любые действия по правке изделия должны производиться после закалки, но до старения.
Операция старения
Операция старения приводит к значительному увеличению твердости и прочности литейной структуры за счет выделения мельчайших упрочняющих фаз. Только после этой операции изделие получает свои заданные свойства, свою окончательную форму и размеры.
Искусственное старение – это старение при повышенных температурах, в отличие от естественного старения, которое проводят при температуре окружающей среды («комнатной» температуре).
Температура старения и ее длительность могут быть различными в зависимости от требуемых свойств алюминиевого сплава в отливке. Например, механические свойства можно «отрегулировать» так, чтобы получить высокую твердость и прочность, но за счет более низкой пластичности (относительного удлинения) материала отливки. И наоборот, можно достичь более высокой пластичности (относительного удлинения), но в ущерб твердости и прочности. При выборе температуры старения и длительности его выдержки применяют диаграммы старения конкретного сплава, которые разработаны для многих сплавов (Figs. 3-6).
Fig. 3 – Yield strength of gravity die cast test bars (Diez die) in Al Si10Mg alloy [3]
Fig. 4 – Elongation of gravity die cast test bars (Diez die) in Al Si10Mg alloy [3]
Fig. 5 – Зависимость предела прочности литейного алюминиевого сплава
Al Si10Mg от температуры его искусственного старения [3]
Fig. 6 – Brinell hardness of gravity die cast test bars (Diez die) in Al Si10Mg alloy [3]
Сплавы алюминий-кремний-магний
В сплавах алюминий-кремний-магний имеется дополнительная возможность влиять на уровень предела прочности и относительного удлинения материала отливки путем изменения содержания магния в комбинации с варьированием параметров термической обработки (Fig. 7).
Рисунок 7 – Influence of Magnesium on the tensile strength (Diez bars) [3]
Типичные параметры искусственного старения для различных типов литейных алюминиевых сплавов представлены в Tabl. 1.
Table 1 – Procedures used in artificial ageing 1) [3]
Источники:
- Aluminum Alloy Castings. Properties, Processes, and Applications / J. Gilbert Kaufman, Elwin L. Rooy – ASM International – 2004
- Heat Treating // Aluminun and Alumunum Alloys – ASM Speciality Handbook – 1996
- Aluminium Casting Alloys – Aleris International – 2011
Обозначение и маркировка термообработки алюминиевых сплавов
Классификация по способам упрочнения
Алюминиевые сплавы разделяют на две основные группы по применимым режимам термообработки.
Сплавы, не способные к упрочнению при термообработке. Увеличение прочности таких сплавов достигают путем холодной деформации (прокатка, экструдирование и т.д.) и назывыется нагартовкой или деформационное упрочнением, а упрочненный сплав называют нагартованным.
Сплавы, упрочняемые термообработкой. Ряд сплавов увеличивают прочность / механические свойства после закалки с последующим охлаждением и естественным или искусственным старением. Такая термообработка обозначается буквой Т.
Термоупрочняющиеся сплавы
Термическая обработка твердого раствора (сплава) – процесс нагрева алюминия до заданной температуры в течение заданного времени, а затем быстрое охлаждение, обычно путем закалки в воду. Вода для закалки может подогреваться для уменьшения поводок и деформации полуфабрикатов.
Естественное старение (T1, T2, T3, T4) – процесс, который происходит самопроизвольно при нормальной (25С) температуре, пока металл не достигнет стабильного состояния. Это упрочняет алюминиевый сплав после термической обработки.
Искусственное старение (T5, T6, T9)
– процесс нагрева в течение заданного периода (2-30 часов) при определенной температуре (100-200ºC) до тех пор, пока металл не достигнет стабильного состояния.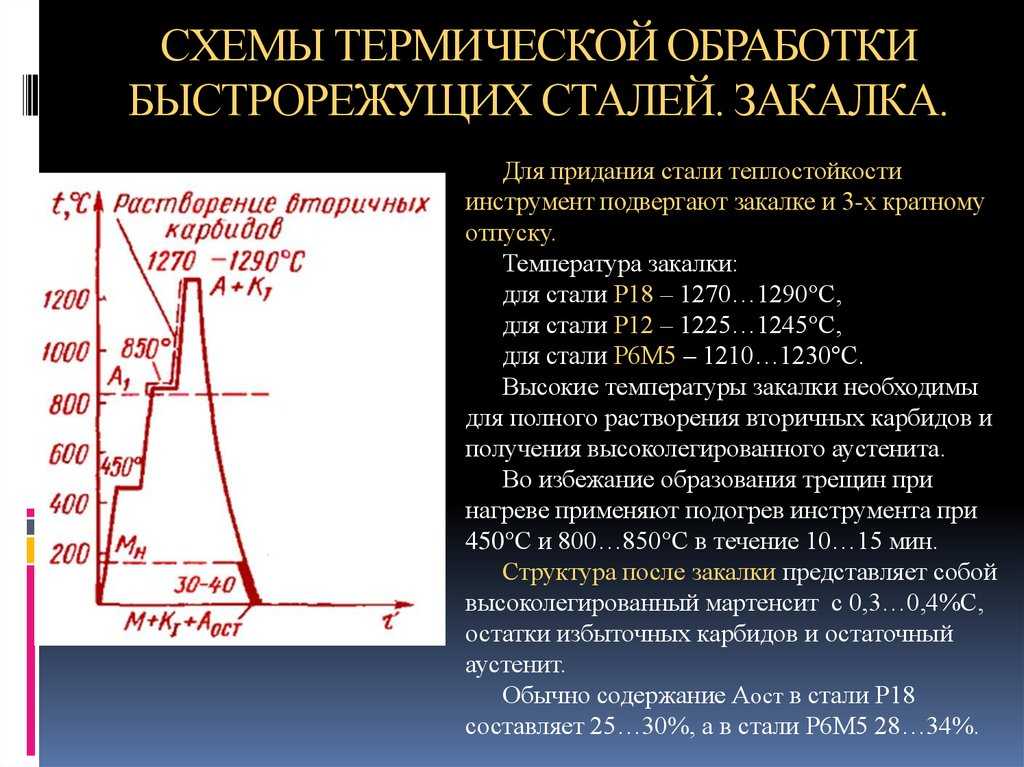
Сплавы, не упрочняющиеся термообработкой
Деформационное упрочнение (нагартовка) h24 – Общий термин для процессов, которые увеличивают прочность алюминия и снижают пластичность (например, прокатка, волочение, прессование, штамповка).
Частичный отжиг (h34) – процесс нагрева, который снижает прочность и увеличивает пластичность алюминия после деформационного упрочнения. Иногда называется отпуском.
Стабилизация (h44) – низкотемпературная термическая обработка или нагрев при производстве, которое стабилизирует механические свойства. Этот процесс обычно улучшает пластичность и применяется только к тем сплавам, которые без стабилизации постепенно стареют при комнатной температуре (то есть, не подвергаются термической обработке). Целью стабилизации является снятие остаточного внутреннего напряжения в металле. В основном используется для сплавов серии 5000 или АМг.
- О – полный отжиг. Применяется для обозначения деформированных полуфабрикатов, подвергаемых отжигу для получения наиболее низких значений прочности, и литых деталей для повышения пластичности и размерной стабильности. После символа О может следовать другая цифра.
- F – как произведено, без термической обработки. без какой-либо дополнительной обработки после изготовления. Применяется для обозначения полуфабрикатов, при операциях формообразования которых отсутствует специальный контроль режимов термообработки или нагартовки. Для деформированных полуфабрикатов не указываются пределы механических свойств.
- W – закаленное состояние, нестабильное. Применимо только для сплавов, самопроизвольно стареющих при комнатной температуре после закалки (естественно стареющие сплавы), при этом специально указывается длительность естественного старения
Деформационно упрочненные
H – обозначает механическое (деформационное) упрочнение; первая цифра обозначает вид термообработки, вторая – степень твердости и прочности:
- Н1 – деформационное упрочнение без термообработки
- Н2 – деформационное упрочнение и частичный отжиг
- Н3 – деформационное упрочнение с стабилизационный отжиг при низкой температуру
- Н4 – деформационное упрочнение с последущим покрытием или покраской, при которых возможен частичный отжиг
-
- вторая цифра( х – первая):
- Нх2 – ¼ твердости
- Нх4 – ½ твердости
- Нх6 – ¾ твердости
- Нх8 – полная твердость
- Нх9 – повышенная твердость
Обозначение нагартованного плоского проката
- Н111 – деформационное упрочнение при прокатке, но меньшее, чем при h21
- Н112 – частичный отжиг после деформационного упрочнения, степень деформационного упрочнения и термообработки не контролируется; гарантируется предел прочности
- Н321 – деформационное упрочнение меньшее, чем при h421
- Н323 – вариант h42, деформационное упрочнение с последущим отжигом для увеличения стойкости к коррозионному растрескиванию под напряжением
- h44 –cтабилизированный, полутвердый – низкотемпературная термическая обработка или тепло, вводимое в процессе производства, которое стабилизирует механические свойства и снимает остаточное внутреннее напряжение, обычно улучшает пластичность.
Применяется только для сплавов, которые, если не стабилизированы, постепенно размягчаются при комнатной температуре.
- h443 – вариант h44, для увеличения стойкости к коррозионному растрескиванию под напряжением
- Н115 – броневые плиты
- Н116 – специальный отжиг для повышения стойкости к коррозии
Термически упрочненные
Т — термическая обработка для получения более стабильных состояний, чем F, O или W. Применяется для полуфабрикатов, подвергаемых термической обработке с дополнительной нагартовкой или без нее. Вслед за символом Т всегда следуют одна или несколько цифр. Естественное старение при комнатной температуре может происходить между или после операций, указанных для состояния Т. Контроль длительности естественного старения производят в случаях, когда это важно с металлургической точки зрения. Цифрами от 1 до 10 обозначают последовательность операций.
Закалка или обработка на твердый раствор состоит в нагреве литых или деформированных полуфабрикатов до соответствующей температуры, выдержке при этой температуре, продолжительность которой достаточна для перехода составляющих в твердый раствор, и быстром охлаждении для фиксации твердого раствора.
Для обозначения деформированных полуфабрикатов, в которых остаточные термические напряжения уменьшают посредством холодной деформации, используют цифры, начиная со второй :Т3511, Т42
- Т1 – охлаждение от температур горячей деформации (или формообразования) с последующим естественным старением для получения более стабильного состояния. Применимо для полуфабрикатов, не подвергаемых холодной деформации после охлаждения от температур деформации или в которых влияние холодной деформации при прогладке или растяжке не учитывают при установлении гарантируемых механических свойств.
- Т2 – охлаждение от температур горячей деформации (или формооб¬разования), нагартовка и последующее естественное старение для получения более стабильного состояния. Применимо для полуфабрикатов, подвергаемых холодной деформации для повышения прочности после охлаждения от температур горячей деформации или в которых влияние холодной деформации при прогладке или растяжке оговаривается при установлении гарантируемых механических свойств.
- Т3 – закалка, холодная деформация и последующее естественное старение. После закалки полуфабрикаты подвергают холодной деформации для повышения прочности, при этом влияние холодной деформации при прогладке или растяжке оговаривается в технической документации.
-
- Т351 – закалка на твердый раствор без полиморфного превращения, уменьшение остаточных напряжений после закалки путем деформации растяжением в среднем на 2%, но не менее чем 1,5% и не более чем 3%, и естественное старение. Не производится дополнительное выравнивание после растяжки.
Применяется для листов, катаных и холодно деформированных полос и прутков из алюминиевых сплавов, не подвергаемых дополнительной правке после растяжки
- Т3511 – уменьшение остаточных напряжений после закалки или охлаждения от температур горячей деформации посредством растяжки со степенью деформации 1-1,5%, но не менее чем 1,5% и не более чем 3% и естественное старение. Отличие от Т351 – незначительная правка после растяжки для обеспечения стандартных требований по допускам. Режим Т3511 применяют для плит из алюминиевых сплавов, т. к. поводки после закалки характерны для массивных полуфабрикатов.
- Т352 – уменьшение остаточных напряжений сжатием. Применяется для полуфабрикатов, в которых уменьшение остаточных напряжений после закалки или охлаждения от температур горячей деформации производится посредством правки сжатием с остаточной деформацией в пределах 1 – 5%. Естественное старение.
- Т36 – закалка на твердый раствор или охлаждение от температур горячей деформации, холодная деформация около 6%, стественное старение.
- Т361 – закалка на твердый раствор или охлаждение от температур горячей деформации, холодная деформация по толщине листа или плиты около 6%, стественное старение.
- Т351 – закалка на твердый раствор без полиморфного превращения, уменьшение остаточных напряжений после закалки путем деформации растяжением в среднем на 2%, но не менее чем 1,5% и не более чем 3%, и естественное старение. Не производится дополнительное выравнивание после растяжки.
- Т4 – закаленное и естественно состаренное состояние. Холодная деформация после закалки отсутствует или влияние ее при прогладке или растяжке не оговаривается в технической документации.
-
- Т42 – закалка из состояний О или F и последующее естественное старение до получения устойчивого состояния.
- Т451 – уменьшение остаточных напряжений после закалки или охлаждения от температур горячей деформации посредством прокатки или холодной деформации со степенью деформации 1,5%, но не менее чем 1% и не более чем 3% и естественное старение. Дополнительная правка после деформации не обязательна.
- Т4510 – закалка на твердый раствор или охлаждение от температур горячей деформации, деформация растяжением со степенью деформации 1,5%, но не менее чем 1% и не более чем 3%, стественное старение.
Правка после растяжения на проводится. От Т451 отличается способом деформации – растяжением
- Т4511 – уменьшение остаточных напряжений после закалки или охлаждения от температур горячей деформации посредством прокатки или холодной деформации со степенью деформации 1,5%, но не менее чем 1% и не более чем 3% и естественное старение. От Т451 отличается тем, что обязательно проводится незначительная правка после растяжки, чтобы обеспечть стандартные требования по допускам
- Т5 – охлаждение от температур горячей деформации (или формообразования) и последующее искусственное старение. Используется для полуфабрикатов, не подвергаемых холодной деформации после охлаждения от температур горячей деформации или для которых влияние холодной деформации при прогладке или растяжке не оговаривается в технической документации. Практически, режим Т5 проходит как завершающая часть формирования полуфабриката штамповкой или вытягивания профиля, а , например, режим Т6 – отдельная технологическая операция.
- Т6 – дисперсионное упрочнение путем закалки без полиморфного превращения и искусственного старения. Полуфабрикаты не подвергают холодной деформации после закалки или влияние холодной деформации при прогладке или правке не оговаривается в технической документации.
-
- Т61 – дисперсионное упрочнение путем закалки без полиморфного превращения и искусственного старения. Заготовки закаливаются в воду с температурой 80-85°С
- Т611 – закалка без полиморфного превращения на дисперсионное твердение, искусственное старение, низкие остаточные напряжения. Допустима незначительная правка после растяжки для обеспечения стандартных требований по допускам
- Т62 – закалка без полиморфного превращения, искусственное старение
- Т651 – закалка на твердый раствор без полиморфного превращения, уменьшение остаточных напряжений после закалки путем деформации растяжением в среднем на 2%, но не менее чем 1,5% и не более чем 3%, и искусственное старение.
Не производится дополнительное выравнивание после растяжки.
- Т6510 – закалка на твердый раствор без полиморфного превращения, уменьшение остаточных напряжений после закалки путем деформации растяжением в среднем на 1,5%, но не менее чем 1% и не более чем 3%, и искусственное старение. Не производится дополнительное выравнивание после растяжки.
- Т6510 – закалка на твердый раствор без полиморфного превращения, уменьшение остаточных напряжений после закалки путем деформации растяжением в среднем на 2%, но не менее чем 1,5% и не более чем 3%, и искусственное старение. Заготовки могут незначительно выравниваться до требований стандарта.
- Т652 – закалка на твердый раствор без полиморфного превращения, деформационное сжатие 1,5-5% и искусственное старение на десперсионное упрачнение. Сжатиее направлено аксиально.
- Т66 – закалка и искусственное старение
- Т7 – закаленное и перестаренное состояние.
Перестаривание обеспечивает получение свойств за максимумом прочности на кривой старения при некоторых специально контролируемых характеристиках.
-
- Т71 – закалка и искусственное старение на дисперсионое твердение
- Т73 – аналог Т74
- Т7351 (Т74351) – закалка на твердый раствор без полиморфного превращения, уменьшение остаточных напряжений после закалки путем деформации растяжением в среднем на 2%, но не менее чем 1,5% и не более чем 3%, и искусственное старение на дисперсионное твердение. Плоский прокат не выравниванивается после растяжки.
- Т73510 – закалка на твердый раствор без полиморфного превращения, уменьшение остаточных напряжений после закалки путем деформации растяжением в среднем на 1,5%, но не менее чем 1% и не более чем 3%, и искусственное старение на дисперсионное твердение. Заготовка не выравниванивается после растяжки.
- Т7311 – закалка на твердый раствор без полиморфного превращения, уменьшение остаточных напряжений после закалки путем деформации растяжением в среднем на 2%, но не менее чем 1,5% и не более чем 3%, и искусственное старение на дисперсионное твердение.
Заготовки могут минимально выравниваться до достижение значений, определяемых стандартом на допуски в размерах
- Т7352 – закалка на твердый раствор без полиморфного превращения, деформационное сжатие 1-5% и искусственное старение на десперсионное упрочнение. Метод и направление сжатия согласовывается с заказчиком или потребителем
- Т736 – аналог Т74
- Т73651 – закалка на твердый раствор без полиморфного превращения, уменьшение остаточных напряжений после закалки путем деформации растяжением в среднем на 2%, но не менее чем 1,5% и не более чем 3%, и искусственное старение на дисперсионное твердение
- Т736511 (Т73652) – закалка на твердый раствор без полиморфного превращения, растяжение 1-5% и искусственное старение на десперсионное упрачнение. Заготовка из сплава алюминия выравнивается до стандартных допусков на кривизну
- Т74 – закалка на твердый раствор без полиморфного превращения и искусственное старение для устойчивости с коррозии под напряжением
- Т7452 – закалка на твердый раствор без полиморфного превращения, деформационное сжатие 1-5% и искусственное старение на десперсионное упрочнение.
- Т76 – закалка на твердый раствор без полиморфного превращения и искусственное старение на увеличение сопротивления расслаивающей коррозии алюминиевых сплавов
- Т761 – закалка на твердый раствор без полиморфного превращения и искусственное старение. Режим обработки Т7 требует тщательного контроля за параметрами старения: время, температура, скорость нагрева и т. д.
- Т761 – закалка на твердый раствор без полиморфного превращения, уменьшение остаточных напряжений после закалки путем деформации растяжением в среднем на 2%, но не менее чем 1,5% и не более чем 3%, и искусственное старение на дисперсионное твердение
- Т7651 – закалка на твердый раствор без полиморфного превращения, растяжение на 2%, но не менее чем 1,5% и не более чем 3% и искусственное старение на увеличение сопротивления расслаивающей коррозии и коррозии под напряжением алюминиевых сплавов. Плоский прокат не выравниванивается после растяжки.
- Т76511 – закалка на твердый раствор без полиморфного превращения, уменьшение остаточных напряжений после закалки путем деформации растяжением в среднем на 1,5%, но не менее чем 1% и не более чем 3%, и искусственное старение на дисперсионное твердение.
Заготовка выравниванивается после растяжки.
- Т8 – закалка, холодная деформация и последующее искусственное старение. Применимо для полуфабрикатов, подвергаемых холодной деформации для повышения прочности или для которых влияние холодной деформации при прогладке или растяжке оговаривается в технической документации.
- Т9 – закалка, искусственное старение и последующая холодная деформация. Применимо для полуфабрикатов, подвергаемых в качестве конечной операции холодной деформации для повышения прочности.
- Т10 – охлаждение от температур горячей деформации, холодная деформация и последующее искусственное старение. Применимо для полуфабрикатов, подвергаемых холодной деформации для повышения прочности или для которых влияние холодной деформации при прогладке или растяжке оговаривается в технической документации.
Термическая обработка алюминия – Часть II
В моей статье, опубликованной в прошлом месяце, я обсуждал легирующие элементы, используемые в алюминиевых сплавах. В этой статье я буду обсуждать термообработку алюминия на твердый раствор. В последующих статьях я расскажу о других единичных процессах термообработки алюминия.
Термообработанные алюминиевые сплавы
Алюминиевые сплавы классифицируются как поддающиеся термической обработке или не поддающиеся термической обработке, в зависимости от того, реагирует ли сплав на дисперсионное твердение. В термообрабатываемых системах сплавов, таких как 7XXX, 6XXX и 2XXX, легирующие элементы проявляют большую растворимость при повышенных температурах, чем при комнатной температуре. Общая последовательность термообработки алюминия показана на рис. 1. Обозначение отпуска полностью описывает последовательность процесса. Обозначения темперамента будут обсуждаться в следующей статье о старении.
Рисунок 1: Общая последовательность термообработки алюминиевых сплавов.Термическая обработка на твердый раствор
Целью термообработки на твердый раствор является получение максимальной практической концентрации твердых растворов отверждающих растворов, таких как медь, магний, кремний или цинк. Растворимость этих элементов заметно увеличивается с температурой, особенно сразу после температуры плавления эвтектики. Следовательно, наиболее благоприятная температура для обработки раствора близка к температуре эвтектики, обычно всего на 5–8 °C (10–15 °F) ниже температуры эвтектики.
Обработка раствора проводится при температуре, близкой к эвтектической (Таблица 1), поэтому хороший контроль и однородность температуры в печах необходимы для предотвращения начального (эвтектического) плавления в областях, граничащих с зерном. Это может привести к снижению как прочности, так и пластичности. Кроме того, при превышении нормальной температуры раствора иногда возникает закалочное растрескивание.
Таблица 1: Температуры термообработки на твердый раствор и температуры плавления эвтектики для сплавов 2XXX. Жесткий температурный контроль особенно важен для сплавов 2ххх, таких как 2014, 2017 и 2024, для которых начальная температура плавления эвтектики всего на несколько градусов превышает рекомендуемую максимальную температуру раствора. Для сплавов серии 7ххх, как правило, допускается больший диапазон температур термообработки на твердый раствор, чем для сплавов серии 2ххх.
Повышение температуры термообработки на раствор от 350°С до предела растворимости, затем закалка и искусственное старение способствуют повышению механических свойств сплава. После достижения предела растворимости повышенные температуры термообработки на твердый раствор малоэффективны [1] [2] [3]. Однако сообщалось, что повышение температуры термообработки на твердый раствор ускоряет старение [4] и обеспечивает повышение твердости [5].
Время, необходимое при температуре термообработки на твердый раствор, зависит от типа продукта, сплава, используемой технологии литья или изготовления, а также от толщины сечения. Типичное время выдержки показано на рис. 2. Обычно воздух является теплоносителем, но ванны с расплавленной солью или псевдоожиженный слой обеспечивают более быстрый нагрев. Высокотемпературное окисление, проявляющееся образованием небольших округлых пустот или щелей внутри металла и вздутиями на поверхности, может происходить из-за нагрева алюминиевых изделий при температурах термообработки на твердый раствор во влажных атмосферах.
Влияние времени при температуре термообработки на твердый раствор на повышение механических свойств широко изучалось [1] [6]. Увеличенное время термообработки на раствор дает мало пользы. Длительное время, обычно указанное в спецификациях на термообработку продукта, предназначено для обеспечения того, чтобы весь продукт с заданной нагрузкой термообработки достиг температуры процесса. Увеличение времени может вызвать повышенное окисление, образование пузырей и ухудшение свойств из-за роста зерна [7]. Чрезмерное время выдержки также может привести к чрезмерной диффузии алюминиевой поверхности [8]. Повторная термообработка плакированных изделий толщиной менее 0,75 мм (0,030 дюйма) обычно запрещена техническими условиями.
Скорость нагревания часто называют причиной начального плавления [9]. Это связано с S-фазой (Al2CuMg). S-фаза медленно растворяется. Это может привести к локальному неравновесному плавлению при температурах от 475° до 490°С при быстром нагреве продукта [10] [11] [12]. При малых скоростях нагрева S-фаза (Al2CuMg) успевает раствориться в матрице, и начального плавления не наблюдается. Начальное плавление алюминиевого сплава показано на рисунке 3.
Эвтектическое плавление часто незаметно до тех пор, пока не будут проведены испытания на растяжение или металлографическое исследование. Обычно это проявляется низким удлинением или плохой пластичностью. К счастью, плавление эвтектики часто сопровождается высокотемпературным окислением.
Высокотемпературное окисление — это неправильно названное состояние диффузии водорода, которое влияет на алюминиевые поверхности при повышенной температуре [13]. Когда влага сталкивается с алюминием при высоких температурах, образуется атомарный водород. Этот водород может диффундировать в металл и собираться на границах зерен и дефектах решетки. Это приводит к образованию пузырей на поверхности и пористости (рис. 4 и рис. 5).
Не все сплавы и формы изделий одинаково уязвимы для этого типа атаки. Сплавы серии 7ххх наиболее восприимчивы, за ними следуют сплавы 2ххх. Выдавливания являются наиболее восприимчивой формой; поковки на втором месте. Низкопрочные сплавы и плакированные листы и плиты относительно невосприимчивы к высокотемпературному окислению.
Влажность можно свести к минимуму путем тщательной сушки деталей и стоек перед их загрузкой. В стеллажах трубчатой конструкции часто необходимы дренажные отверстия, чтобы избежать захвата воды. Другим распространенным требованием является регулировка положения закалочного бака по отношению к дверям печи и воздухозаборнику для уменьшения захвата влаги печью.
Наиболее распространенным методом уменьшения образования пузырей является использование в печи защитного состава, такого как фторборат аммония [14]. Такое соединение обычно эффективно для сведения к минимуму вредного воздействия влаги и других нежелательных загрязняющих веществ, поскольку оно образует барьерный слой или пленку на поверхности алюминия. Другие методы включают анодирование алюминиевых поверхностей.
Выводы
В этой небольшой статье мы описали основные принципы термической обработки алюминия на твердый раствор. Было выявлено несколько проблемных областей и подробно описаны возможные корректирующие действия.
Если у вас есть какие-либо комментарии к этой статье или предложения для других статей, пожалуйста, свяжитесь с редактором или автором.
Ссылки
- P. Brenner, Luftwissen, vol. 7, с. 316, 1940.
- B. W. Mott and J. Thompson, Metal Treatment, vol. 14, с. 228, 1948.
- В. Розенкранц, Алюминий, том. 36, с. 250, 1960.
- K.L.Dreyer and H.J.Seeman, Aluminium, vol. 26, с. 76, 1944.
- В. Фельдман, Metalwirtschaft, vol. 20, с. 501, 1941.
- Д.
С. Маккензи, на Первой международной конференции по цветным металлам и технологиям, Сент-Луис, 1997 г.
- HG Petri, Aluminium, vol. 24, с. 385, 1942.
- Ф. Келлер и Р. Х. Браун, «Диффузия в листе Alclad 24S-T», Trans. АЙМЕ, том. 156, стр. 377-386, 1944.
- Дж. Э. Хэтч, Алюминий: свойства и физическая металлургия, Metals Park, OH: Американское общество металлов, 1984.
- М. Кук, J. Inst. Металл, вып. 79, с. 211, 1951.
- М. Кук, J. Inst. Металлы, вып. 80, с. 449, 1952.
- М. Кук, Proc. Королевский общество, том. 205А, с. 103, 1951.
- B.R. Strohmeier, «Характеристика поверхности алюминиевой фольги, отожженной в присутствии фторбората аммония», App. Серф. наук, вып. 40, стр. 249-263, 1989.
- П. Т. Строуп, «Термическая обработка глиноземистых металлов». Патент США 2092033, 7 сентября 1937 г. .
Термическая обработка алюминия и алюминиевых сплавов
К основным видам термической обработки алюминия и его сплавов относятся: предварительный нагрев или гомогенизация для уменьшения химической сегрегации литых структур и улучшения их обрабатываемости; Отжиг для размягчения деформационно-упрочненных (наклепанных) и термообработанных конструкций из сплавов, снятия напряжений, стабилизации свойств и размеров; Термическая обработка на раствор для получения твердого раствора легирующих компонентов и улучшения механических свойств; Осадительная термообработка, обеспечивающая упрочнение путем осаждения компонентов из твердого раствора
Процессы термообработки алюминия являются прецизионными процессами.
Они должны выполняться в правильно спроектированных и построенных печах.
для обеспечения необходимых тепловых условий и надлежащего оснащения
с контрольными приборами для обеспечения желаемой непрерывности и
равномерность температурно-временных циклов. Для обеспечения окончательного желаемого
характеристики, детали процесса должны быть установлены и контролироваться
тщательно для каждого типа продукта.
К основным видам термической обработки алюминия и его сплавов относятся:
- Предварительный нагрев или гомогенизация для уменьшения химической сегрегации литых структур и улучшения их обрабатываемости
- Отжиг для размягчения деформационно-упрочненных (деформационно-упрочненных) и термически обработанных конструкций из сплавов, для снятия напряжений и стабилизации свойств и размеров
- Термическая обработка на твердый раствор для получения твердого раствора легирующих компонентов и улучшения механических свойств
- Термическая обработка осаждением, обеспечивающая отверждение путем осаждения компонентов из твердого раствора.
ПРЕДВАРИТЕЛЬНЫЙ НАГРЕВ СЛИТКОВ (ГОМОГЕНИЗАЦИЯ)
Начальная термическая обработка слитков перед горячей обработкой составляет называемый «предварительный нагрев слитка», который имеет одну или несколько целей в зависимости от сплава, продукта и производственного процесса. Одной из основных целей является улучшение работоспособности. микроструктура большинства сплавов в литом состоянии довольно неоднородный. Это справедливо для сплавов, образующих твердые растворы. в равновесных условиях и даже для относительно разбавленных сплавов
ОТЖИГ
Деформированная, дислоцированная структура в результате холодной обработки
алюминий менее стабилен, чем бездеформационное отожженное состояние, к которому
он имеет тенденцию возвращаться. Алюминий более низкой чистоты и технические алюминиевые сплавы
претерпевают эти структурные изменения только при отжиге при повышенных
температуры. Структурная реверсия сопровождается изменениями в
различные свойства, затронутые холодной обработкой. Эти изменения происходят в
несколько стадий, в зависимости от температуры или времени, и привели к
концепция различных механизмов или процессов отжига.
Восстановление . Наибольшее уменьшение числа вывихов в центре фрагментов зерен, образуя субзернистую структуру с сетями или группами дислокаций на границах субзерен. С увеличением времени и температуры нагрева полигонизация становится приближается к идеальному, а размер субзерен постепенно увеличивается. На этой стадии многие субзерна имеют границы. свободные от клубков дислокаций и скоплений.
Восстановительный отжиг также сопровождается изменением других свойств. из холоднодеформированного алюминия. Полное восстановление после воздействия холода рабочий получается только при перекристаллизации.
Рекристаллизация характеризуется постепенным
образование и появление микроскопически разрешимой зернистой структуры.
Новая структура в значительной степени свободна от деформации – дислокаций мало, если они вообще есть.
внутри зерен и отсутствие скоплений на границах зерен.
Рост зерна после перекристаллизации . Отопление после перекристаллизация может привести к укрупнению зерна. Это может занять одно из несколько форм.
ДИСПЛЕНТОВАЯ ЗАКАЛКА
Общие принципы дисперсионного твердения . Жара обрабатываемые сплавы содержат количество растворимых легирующих элементов, превышающее равновесный предел растворимости в твердом состоянии при комнатной и умеренно выше температуры. Присутствующее количество может быть меньше или больше максимального растворяется при температуре эвтектики.
Природа осадков и источники твердения . Интенсивный
исследования в течение последних сорока лет привели к прогрессивному
накопление знаний об атомной и кристаллографической
структурные изменения, происходящие в пересыщенных твердых растворах при
осаждения и механизмы, посредством которых структуры формируются и
изменить свойства сплава. В большинстве дисперсионно-твердеющих систем сложный
последовательность зависимых от времени и температуры изменений.
Кинетика растворения и осаждения . Относительные ставки при которых реакции растворения и осаждения протекают с разными растворенными веществами зависят от соответствующих скоростей диффузии, в дополнение к растворимости и содержание сплава. Коэффициенты объемной диффузии для некоторых коммерческих важные легирующие элементы в алюминии определялись различными экспериментальные методы.
Зарождение . Образование зон может происходить в по существу непрерывная кристаллическая решетка в процессе гомогенного зарождение. Недавние исследования свидетельствуют о том, что критическая для этого процесса требуется концентрация вакансий и что зародышеобразование модель, включающая кластеры вакансия-растворенный атом, согласуется с некоторыми Влияние температуры раствора и скорости закалки.
На зарождение новой фазы большое влияние оказывает существование
разрывов в решетке. Поскольку в поликристаллических сплавах зерно
границы, границы субзерен, дислокации и межфазные границы
являются местами большего беспорядка и более высокой энергии, чем твердый раствор
матрикс, они являются предпочтительными местами для зародышеобразования преципитатов.
Закалка
Закалка во многих отношениях является наиболее важным этапом в последовательности нагрева. лечебные операции. Цель закалки – максимально сохранить максимально неповрежденным твердый раствор, образовавшийся при термообработке раствора температуры путем быстрого охлаждения до некоторой более низкой температуры, обычно около комнатная температура.
Диапазон критических температур . Основы, связанные с
закалка дисперсионно-твердеющих сплавов основана на теории зародышеобразования
применяется к твердофазным реакциям, контролируемым диффузией. Эффекты
температуры от кинетики изотермического осаждения зависят принципиально
от степени пересыщения и скорости диффузии.
Закалочная среда . Вода является не только наиболее широко используемым гасящая среда, но и наиболее эффективная. Видно, что в закалка погружением, скорость охлаждения можно уменьшить за счет увеличения количества воды температура. Условия, повышающие устойчивость паровой пленки вокруг детали уменьшить скорость охлаждения; различные добавки к воде что более низкое поверхностное натяжение имеет тот же эффект.
Старение при комнатной температуре (естественное старение)
Большинство термообрабатываемых сплавов проявляют старение при комнатной температуре. после закалки скорость и степень такого твердения колеблются от единицы сплав к другому. Заметные микроструктурные изменения не сопровождаются старение при комнатной температуре, так как эффекты упрочнения связаны с исключительно к образованию зонной структуры внутри твердого раствора.
Так как сплавы мягче и пластичнее сразу после закалки
чем после старения, выпрямления или формовки могут быть выполнены операции
легче в свежезакаленном состоянии.
Термическая обработка осаждением (искусственное старение)
Влияние осадков на механические свойства значительно ускоряется и обычно усиливается повторным нагревом закаленного материала примерно до 100-200°С. Эффекты не полностью связаны с изменена скорость реакции; как упоминалось ранее, структурные изменения происходящие при повышенных температурах, принципиально отличаются от происходящие при комнатной температуре. Эти различия отражаются в механические характеристики и некоторые физические свойства. Характерной особенностью воздействия высокотемпературного старения на свойства растяжения заключается в том, что увеличение предела текучести более заметно, чем увеличение прочности на растяжение. Также пластичность, как измеряется процентным удлинением, уменьшается. Таким образом, сплав в Отпуск Т6 имеет более высокую прочность, но более низкую пластичность, чем тот же сплав. в состоянии Т4.
Термическая обработка осаждением без предварительной термообработки раствором
Некоторые сплавы, относительно нечувствительные к скорости охлаждения во время
закалка может быть либо с воздушным охлаждением, либо с водяной закалкой непосредственно из конечной
горячая рабочая операция.