Ультразвуковая сварка металлов: Ультразвуковая сварка металлов | Публикации Виндэк
alexxlab | 13.07.1985 | 0 | Разное
Ультразвуковая сварка металлов | Публикации Виндэк
Тарас Никифоров
Технический центр «Виндэк» (Россия, г. Подольск)
Владимир Гуреев
TELSONIC AG (Швейцария)
На мировом рынке только за последнее десятилетие объем продаж оборудования для ультразвуковой сварки увеличился в несколько раз, и эксперты пророчат ему дальнейший рост. Благодаря новым достижениям в разработке технологии данные сварочные системы позволяют решать уникальные задачи в электронной, электротехнической, автомобильной промышленности, а также при производстве аккумуляторов, конденсаторов, солнечных батарей и систем нагрева воды.
В наши дни ультразвуковая сварка металлов находит все более широкое применение и позиционируется чуть ли ни как инновационный продукт. Вместе с тем, мало кто знает, что данный метод был открыт еще в 30-40 годы прошлого столетия, причем, совершенно случайно. При подготовке поверхности алюминия к контактной сварке экспериментаторы, применившие для этой вспомогательной цели ультразвуковые колебания, неожиданно для себя отметили, что соединение металлических пластин происходит еще до пропускания через них сварочного тока. Вот так и было положено начало совершенно новому виду сварки.
Как работает?
Область применения такого метода соединения простирается в диапазоне от пластмасс до цветных металлов. Однако, независимо от свариваемых материалов, оборудование для ультразвуковой сварки традиционно состоит из высокочастотного генератора, блока управления, механической колебательной системы и привода давления.
Ультразвуковой генератор преобразует ток электрической сети в ток высокой частоты, который по получении сигнала с блока управления подается на пьезоэлементы колебательной системы. Преобразование колебаний электрического тока высокой частоты в механические и введение их в зону сварки обеспечивается механической колебательной системой. Последняя, в свою очередь, состоит из конвертера (преобразователь), бустера (усилитель) и волновода (сонотрод) и является главным узлом технологии ультразвуковой сварки.
Для доступности понимания сравним колебательную систему, обеспечивающую практическую реализацию метода, например, с автомобилем (Рис. 2). Конвертер выступает в роли мотора, преобразовывая ток высокой частоты в механические колебания с соответствующей частотой. Далее бустер, действуя как коробка передач, изменяет амплитуду колебаний в зависимости от передаточного числа и переадресует их на волновод. Волновод, увеличивая при необходимости амплитуду механических колебаний высокой частоты, передает их непосредственно в зону сварки, приводя в движение верхнюю свариваемую деталь.
В основу работы пьезокерамического конвертера положен хорошо известный многим еще со школьной скамьи пьезоэлектрический эффект. При воздействии на пьезоэлемент переменного давления возникает переменное электрическое напряжение, а под воздействием переменного электрического поля возникают механические напряжения, которые вызывают упругие деформации материала в следствии чего пьезоэлемент начинает сжиматься и увеличиваться на определенную величину с частотой равной частоте тока.
Величина изменения размера пьезоэлемента соответствует амплитуде механических колебаний (Рис. 3), которая зависит от мощности и конфигурации конвертера. Так, при частоте 20кГц амплитуда колебаний пьезокерамического конвектора, как правило, не превышает 10мкм. Однако, за счет увеличения амплитуды бустером и волноводом можно получить максимальную амплитуду в зоне сварки — до 70мкм. Для ультразвуковой сварки обычно используется частота от 20кГц и выше. Применение той или иной частоты зависит от материала и габаритов свариваемого изделия.
Применительно к реальным технологиям это явление может иметь очень положительный эффект. Вот и в процессе ультразвуковой сварки металлов колебательные движения волновода совместно с усилием прижатия передаются на верхнюю свариваемую деталь. Она по определению должна быть подвижной относительно нижней детали, прочно закрепленной на наковальне. В результате между деталями возникает трение с определенной частотой и амплитудой, способствующее их сращиванию между собой (Рис.4). Именно поэтому ультразвуковую сварку можно еще классифицировать, как механическую сварку трением с высокой частотой без ввода сварочного тока в зону сварки.
В процессе сварки микроскопические смещения деталей относительно друг друга вызывают стирание шероховатостей, разрушение оксидных пленок и возникновение узлов схватывания. При повышение температуры в зоне сварки, за счет трения и дальнейшей деформации свариваемых деталей, наблюдается повышение пластичности поверхностных слоев металла, вытеснение оксидных пленок и загрязнений из зоны сварки. Все это приводит к интенсивному разрастанию зон схватывания, диффузии одного материала в другой, локальному плавлению верхних атомарных слоев, появлению новых и стойких межатомных связей. Данные структурные изменения можно воочию наблюдать на фотографии микрошлифа покрытых серебром медных проводов, которые были сварены между собой при помощи ультразвука.
Плюсы применения
Ультразвуковая сварка металлов обладает уникальными технологическими свойствами, которые в практическом применении дают ей сто очков вперед на многих направлениях. Перечислим только главные из них.
Прежде всего, это возможность производить сварку без предварительной подготовки поверхности соединяемых деталей и при весьма незначительном температурном воздействии, оказываемом непосредственно на них. Отсюда вытекает такое существенное преимущество ультразвуковой сварки, как умение накрепко и без печальных последствий соединять между собой термочувствительные элементы.
Более того, допустима сварка деталей разной толщины, а также разнородных металлов (медь-алюминий, алюминий-никель и др.). При ультразвуковой сварке достигаются отличные электрические свойства и незначительное переходное сопротивление.
Что очень даже существенно, прочность обеспечиваемых ультразвуком соединений приближается к 70% от прочности основного материала. Дополнительно следует отметить высокую скорость, экологическую чистоту и экономичность процесса.
Проверено практикой
Как уже было сказано, инновационная технология ультразвуковой сварки металлов благодаря своим особым свойствам находит все более широкое применение в самых различных отраслях промышленности. Например, в автомобилестроении метод активно используется при соединении медных многожильных проводов жгутов электропроводки (Рис.6). В России данную технологию весьма успешно применяют, в частности, такие производители автокомпонентов, как Leoni Group, Prettl, ИВК, Завод радиоаппаратуры, ПТОО ОАО «АВТОВАЗ» и другие. Конкурентными преимуществами собственной продукции они во многом обязаны внедрению у себя ультразвуковой технологии. Так ультразвуковые системы TelsoSplice, выпускаемые швейцарской фирмой Telsonic AG, способны сваривать многожильные медные провода суммарным сечением от 0,5 до 45мм2. Также ультразвуковая сварка используется при производстве электромоторов и патронов для подушек безопасности.
Масштабное применение ультразвуковая сварка обрела в электронной и электротехнической промышленности. И ничего удивительного здесь нет. Ведь ультразвук умеет соединять как миниатюрные изделия, так и проводку большого суммарного сечения до 200мм2 . Впрочем, в последнем случае описываемые нами системы оснащаются генераторами мощностью в 10кВт и наделяются способностью оказывать усилие в 8000Н.
С помощью ультразвуковой технологии, например, на «Свердловском заводе трансформаторов тока» к медному контакту присоединяют многожильные провода. Тем же способом специалисты ОАО «Протвинский опытный завод «ПРОГРЕСС» приваривают многожильные медные провода к шинам электрических шкафов. Наглядной демонстрацией преимуществ ультразвуковой сварки можно назвать и ее применение в компании Bosch. В частности, там при изготовлении электродвигателей соединяют провода с контактами без снятия с них защитной эмали, что позволило полностью автоматизировать процесс сборки автомобильных электромоторчиков.Или еще примеры. Растущая потребность в солнечных батареях и системах нагрева воды повлекла за собой использование ультразвуковой шовной сварки металлов в процессе создания и такого рода устройств. Компания «Элеконд» применяет ультразвук в соединении алюминиевой фольги и контактов. Кстати будет сказать, что технология применима также и в изготовлении самой алюминиевой фольги. Но продолжим о применениях, так сказать, по прямому назначению.
При производстве литий-ионных аккумуляторов компания VARTA при помощи ультразвука сваривает между собой алюминиевую, медную и никелевую фольгу. На заводе им. Фрунзе при изготовлении предохранителей тем же способом сваривают медные и биметаллические пластины. ФГУП ВНИИА им. Н.Л. Духова, используя технологию ультразвуковой сварки, соединяет алюминиевую фольгу толщиной всего от 5мкм.
Примером уникальности метода и его нацеленности на решение сложных задач, недоступных другим технологиям, может служить и соединение медных проводников с контактами в керамической подложке (Рис. 8). Впрочем, как в оценке всего нового, не будем спешить с конечным выводом. В самом ближайшем будущем нам еще предстоит узнать, на что еще способна ультразвуковая сварка.
А о том, что это обозримая перспектива свидетельствует опыт уже упомянутой компании TELSONIC AG. Она выпускает прецизионные сварочные системы, способные работать как автономно, так и в составе автоматизированных линий. Причем, неустанно продолжает поиск новых применений. Официальным дилером этой компании в России является ООО «Технический центр «Виндэк» из подмосковного Подольска.
Подводя итог, следует сказать, что использование ультразвуковых технологий существенно облегчает получение требуемых характеристик сварного соединения и повышает эффективность производства.
Технология ультразвуковой сварки: особенности, принцип действия, аппараты и оборудование
В данной статье мы разберем суть сварки ультразвуком (будем говорить преимущественно об ультразвуковой сварки металлов), рассмотрим особенности УЗ-микросварки, опишем принцип действия установок и аппаратов ультразвуковой сварки.
Ультразвуковая сварка металлов
Технология ультразвуковой сварки представляет собой соединение деталей под воздействием ультразвуковых волн, которые преобразуются в механические колебания и вызывают пластическую деформацию плоскостей в месте их соприкосновения, одновременно разрушая оксидные пленки. Свойства металлов почти не изменяются. Установка ультразвуковой сварки состоит из следующих компонентов:
- источник питания;
- преобразователь;
- сварочная головка;
- волноводы.
Электричество преобразуется в звук высокой частоты, необходимый для сварки, головка обеспечивает сжатие рабочих деталей, волноводы передают энергию в ту точку, где сваривают поверхности.
Сфера промышленного применения данного вида сварки достаточно широка. Ее используют для соединения проволоки, фольги, термочувствительных материалов. Также используется при изготовлении мобильных телефонов, микросхем, оптических и других приборов. Современное автомобилестроение и производство звуковой техники также не обходится без сварки ультразвуковым способом. Данный метод ценят за высокую производительность, точность и прочность, а также за возможность сваривать различные сплавы, для которых обычная сварка недоступна.
Преимущества ультразвуковой сварки
Данный вид сварки широко используется и успел доказать многочисленные преимущества:
- Отсутствие сильного нагревания позволяет сваривать даже те металлы, которые характеризуются химической активностью.
- Сварка осуществляется с высокой скоростью.
- Повышается прочность соединения разнородных материалов, которое при высокой температуре, сопровождающей обычную сварку, оказалось бы хрупким.
- Устраняются технологические ограничения, касающиеся сварки алюминия или меди.
- Толщина свариваемых ультразвуковым способом деталей не ограничена, они могут быть тонкими или даже сверхтонкими (например, фольга), причем толщина соединяемых сваркой элементов может различаться.
- Требования к чистоте поверхностей при использовании ультразвука менее строги, чем при обычном способе сварки, допускается наличие оксидной или изоляционной пленки.
- Сварочное усилие невелико, что позволяет избежать сильной деформации в зоне стыка.
- Конструкция установки для УЗ сварки не отличается сложностью.
Экологическая безопасность и гигиеничность также относится к числу достоинств ультразвуковой технологии. Такая сварка требует меньших трудозатрат, ведь она может быть автоматизирована. Сварка ультразвуком не предполагает расходных материалов, что делает ее чрезвычайно экономичной.
Ультразвуковая микросварка
Одной из разновидностей ультразвуковой сварки является УЗ микросварка. Основная сфера ее применения – это микроэлектроника. Когда монтируются полупроводниковые кристаллы, между контактными площадками и выводами создаются проволочные или ленточные перемычки, которые обеспечивают электрическое соединение. Сваривать сверхтонкие детали можно только с помощью ультразвука, контролируя с помощью специальной установки его параметры:
- мощность;
- давление;
- время воздействия.
Процесс сварки основан на взаимодействии электронов со смежными молекулами, соединение тончайшей проволоки происходит на уровне атомов методом диффузии. Современные аппараты для ультразвуковой микросварки позволяют максимально снизить трудоемкость процесса и расширить круг материалов, которые можно сваривать таким методом. Сварка с применением ультразвука используется не только для металлических деталей, но и для изделий из пластика при наложении точечных швов.
Установки ультразвуковой микросварки
Ультразвуковая сварка в микроэлектронике нашла широчайшее применение. В современном мире устройства, собранные по нанометровым техпроцессам, есть практически у каждого обывателя (например мобильный смартфон). Так, потребность в устройстве рабочего места специалиста-микросварщика становится очевидной, а необходимость в специализированном микросварочном оборудовании – все более насущной.
Разберем основные аппараты ультразвуковой микросварки.
- Установка УМС-1АК предназначена для автоматической и полуавтоматической ультразвуковой и термозвуковой сварки золотой проволоки методом «шарик-клин» и алюминиевой, золотой проволоки методом «клин-клин». Управление автоматической установкой производится с помощью специализированной системы управления на базе персонального компьютера, позволяющая производить программирование до 100 технологических параметров: высота, длина, угол наклона перемычки и т.
Установка оснащена системой машинного зрения для распознавания образов контактных площадок полупроводниковых приборов. Установка комплектуется ультразвуковым генератором с возможностью автоматической подстройки резонансной частоты в процессе сварочного импульса, при этом используются ультразвуковые пьезокерамические преобразователи с резонансной частотой 62 кГц; 108 кГц. - Аппарат ультразвуковой микросварки УМС-1УТ используется для ультразвуковой сварки внахлест алюминиевой и золотой проволоки «клин-клин». Установка комплектуется дополнительным ручным механическим приводом для опускания сварочной головки по оси Z с помощью – «ручки» с целью точного позиционирования сварочного электрода относительно контактной площадки и для оперативной коррекции уровня сварки с разновысотностью до 6 мм и глубиной «колодца» до 18 мм (при длине электрода 21мм, 3 мм остаются на закрепления электрода в ультразвуковом преобразователе).
- Установка УМС-2ШК предназначена для автоматизированной термозвуковой сварки золотых проволочных выводов методом «шарик-клин», с дополнительным закреплением «клина» «шариком», с возможностью присоединения золотых шариков на контактные площадки (бампирование) и «внахлест» методом «клин-клин» Кроме того установка предназначена для автоматизированной ультразвуковой сварки алюминиевой проволоки и сварки ленты.
- Установка УЗ сварки УМС-21У используется для ультразвуковой сварки алюминиевой проволоки диаметром от 100 мкм до 500 мкм внахлест методом «клин-клин». Установка изготавливается в двух вариантах: при сборке приборов проволокой диаметром от 100 до 350 мкм, отделение проволоки от второго сварного соединения происходит с помощью зажимных губок; при монтаже проволокой диаметром 400-500 мкм с обрезкой сварочной проволоки после второй сварки с помощью «ножа».
- Установка сварки ультразвуком УМС-2ТКУ, предназначенная для точечного присоединения золотых проволочных выводов диаметром от 15 до 50 мкм к контактным площадкам без корпусных диодов методом термокомпрессионной и термозвуковой микросварки (для проволочного монтажа гибридных интегральных микросхем).
Что такое ультразвуковая сварка металлов?
Екатерина
На данный момент существует около сотни самых разнообразных способов сварки металлов. У каждого из них есть свои достоинства и недостатки, особенности и сферы применения. Какие-то методы незаменимы на опасных объектах, а какие-то становятся основополагающими в практике домашних мастеров. Но существуют и такие способы сварки, о которых мы мало что слышим в силу узкого применения.
Один из таких способов — сварка ультразвуком. Ультразвуковая сварка нечасто на слуху, но она все же широко применяется при сварке микроэлектроники, проволоки, листового металла и прочих тонких или просто маленьких изделий. В этой статье мы подробно объясним, что такое ультразвуковая сварка и как работает данный метод соединения металлов.
Содержание статьи
- Общая информация
- Технология
- Достоинства и недостатки
- Оборудование
- Вместо заключения
Общая информация
Ультразвуковая сварка металлов — метод сварки, в основе которого лежит применение ультразвуковых колебательных волн. Широко применяется не только для сварки металлов, но и для соединения деталей из пластмассы, ткани, натуральной кожи. Также с помощью ультразвука вы сможете сварить стекло с металлом. Вы можете комбинировать ультразвуковую сварку с точечной, контурной или шовной сваркой.
Интересный факт: в конце 60-х годов прошлого века с помощью ультразвуковой сварки был собран автомобиль, изготовленный из пластмассы. Именно благодаря ультразвуковому оборудованию этот проект удалось успешно завершить.
Читайте также: Ультразвуковая сварка пластмасс
Существуют даже специализированные приборы для ультразвуковой сварки. Например, большой популярностью пользуется ультразвуковая швейная машина для сварки полимеров (брезента или подобных изделий). Но про оборудование мы подробнее поговорим позже.
Технология
Ультразвуковая сварка металлов может выполняться с использованием самых разнообразных типов сварных соединений. Вы можете сварить две детали внахлест, раздавить кромки и сварить их, можете встык сварить круглую деталь с плоской, и так далее. Словом, возможности практически безграничны.
Достоинства и недостатки
У ультразвуковой сварки (как и у любого другого метода) есть достоинства и недостатки. Давайте рассмотрим их подробнее, чтобы вы могли понять, в каких целях стоит применять ультразвук, а в каких от этой идеи лучше отказаться.
Первое достоинство — отсутствие необходимости в тщательной подготовке металла под сварку. Единственное, что необходимо сделать — обезжирить поверхность. Все. Можно даже не удалять грязь или ржавчину. При других методах сварки подготовительный процесс отнимает много времени и сил, а вот с применением ультразвука эта проблема легко решается.
Второй плюс — местный нагрев. Металл нагревается только в том месте, где планируется сварное соединение. По этой причине исключены какие-либо деформации металла из-за избыточного нагрева. Это достоинство особенно заметно при сварке пластмассовых деталей.
Третий плюс — возможность варить даже в труднодоступных местах, при этом вся сварка производится очень быстро, ведь металл успевает нагреться менее чем за секунду. К тому же, вы без труда сварите очень тонкий металл. И говоря «тонкий» мы подразумеваем даже металлические листы толщиной не более 0,001 миллиметра. Впечатляет!
Но, поскольку наш материал объективен, мы расскажем и о недостатках. Учтите, что все они не так существенны.
Во-первых, в некоторых ситуациях все же приходится приобретать дорогие генераторы ультразвуковых волн, если бюджетные модели не справляются. Но, справедливости ради, случается это крайне редко. В нашей практике еще не было ни одного случая, когда бы недорогой ультразвуковой генератор не справился со своей работой.
Также иногда бывают ситуации, когда ультразвук не может сварить толстый металл. Эту проблему можно решить, если подбирать вогнутые детали. Они будут фокусировать ультразвук в зоне сварки и тем самым даже толстый металл быстро расплавится.
Оборудование
Раз уж мы дважды упомянули оборудование, остановимся подробнее на этой теме. Существует три типа аппаратов для ультразвуковой сварки:
- Аппараты, выполняющие точечно-контурную сварку
- Сварочники, выполняющие шовную или шовно-шаговую сварку
- Мобильные (переносные) аппараты малой мощности, например, сварочные пистолеты.
При этом мощность аппарата может быть от 100 до 1500Вт, в зависимости от его цены, назначения и размеров.
На сварочных аппаратах, произведенных до конца 70-х, использовался магнитострикционный принцип генерации ультразвука. Но на данный момент такие аппараты не выпускаются, им на смену пришли установки, в которых ультразвук генерируется с помощью встроенного пьезоэлектрического преобразователя.
На данный момент такое оборудование производят многие страны Европы и мира, в том числе Россия. Качество отечественной продукции вполне приемлемо, особенно учитывая невысокую стоимость по сравнению с зарубежными конкурентами. Вообще производство ультразвуковых сварочных аппаратов началось еще в Советском союзе. Тогда такие аппараты в основном использовались для сварки микросхем. Сейчас же сфера применения стала куда шире.
Вместо заключения
Сварка ультразвуком незаменима при работе с маленькими и тонкими деталями, которые просто невозможно сварить вручную или с применением других технологий. Благодаря ультразвуку металл не деформируется и не растекается, а образует прочное соединение. Также сварка ультразвуком позволяет беспроблемно варить металлы, покрытые окисной пленкой. Например, алюминий, с которым у сварщиков обычно много проблем.
К тому же, оборудование для ультразвуковой сварки стоит не так уж дорого. Поэтому рекомендуем испробовать в своей практике этот метод соединения металлов. Если вы когда-либо выполняли ультразвуковую сварку своими руками, то расскажите об этом. Ваш опыт будет полезен для многих новичков. Желаем удачи в работе!
Похожие публикации
Ультразвуковая сварка металлов: как совершается
Содержание
- Кратко об ультразвуке
- За счет чего происходит сварка
- Принцип действия
- Выделение тепла во время процесса
- Виды УЗС
- Прерывная и непрерывная
- Точечная сварка
- Роликовая сварка
- Сварка по контуру
- Применение сварки ультразвуком
- Возможности ультразвуковых волн
- Установленные ограничения
- Прочность получаемых швов
- Используемое в работе оборудование
- Изменяемые параметры
- Как работают сварочные машины
- Инструкция: как вести процесс ультразвуковой сварки
- Особенности работы с металлами
- Полимеры и иные материалы
- Плюсы ультразвуковой сварки
- Недостатки УЗС
- Частые дефекты
- Полезная литература
Ультразвуковая сварка не предполагает плавления металла. Этим она выгодно отличается от газовой, электродуговой и контактной. Данное преимущество особенно востребовано при производстве мелких изделий, например микросхем.
Кратко об ультразвуке
Механическое воздействие на твердую, жидкую или газообразную среду приводит к возникновению в ней области сжатия, распространяющейся во все стороны за счет упругих сил.
Серия таких волн образует звук. В процессе их распространения частицы среды совершают механические колебания вдоль направления движения импульса.
Данное явление характеризуется 2 физическими величинами:
- Количеством волн, проходящих через точку среды за единицу времени (частотой). Эта величина определяет тон звука.
- Амплитудой колебаний частиц. Зависит от интенсивности излучения (силы звука).
Приставка «ультра» означает, что частота колебаний превышает порог слышимости человека (18 кГц).
За счет чего происходит сварка
Заготовки сращиваются под влиянием 3 факторов:
- ультразвуковых колебаний;
- сжатия с усилием 10-200 кгс;
- предварительного нагрева.
Последний применяют только в отношении толстостенных заготовок и материалов с повышенной твердостью.
Принцип действия
Сварка ультразвуком основана на явлении рекомбинации. Оно заключается в разрыве одних жестких связей между атомами и молекулами твердого тела и возникновении других. Интенсивность процесса растет с увеличением амплитуды колебаний частиц. В «горячих» технологиях сваривания им для этого сообщают тепловую энергию, в данном методе – воздействуют звуком.
Схема ультразвуковой сварки.Слияние материалов происходит в следующем порядке:
- Производимые звукогенератором волны «раскачивают» молекулы одной из заготовок.
- Жесткие связи между некоторыми из них разрушаются.
- Одновременно возникают новые с молекулами второй заготовки. Этому способствует оказываемое на изделие давление.
Выделение тепла во время процесса
В зоне соединения наблюдается нагрев заготовок. Он обусловлен следующими причинами:
- пластической деформацией;
- звуковыми колебаниями;
- трением заготовок друг о друга из-за вибраций.
Тепло выделяется в количестве несоизмеримо меньшем, чем при газовой или электродуговой сварке. К нему чувствительны только наиболее тонкие заготовки. Для работы с ними сварочный аппарат оснащают системой охлаждения. В большинстве случаев ее приходится применять при 2-сторонней сварке.
Трение соединяемых поверхностей одна о другую приводит к разрушению оксидных и прочих пленок. Эта особенность позволяет исключить из технологического процесса предварительную зачистку заготовок, хотя она все же остается желательной. Образованию поверхностной окисной пленки наиболее подвержен алюминий.
Виды УЗС
Данная методика включает в себя несколько направлений. Они отличаются видом оборудования, способом применения ультразвука и пр.
Прерывная и непрерывная
Непрерывная технология предполагает безостановочное движение рабочего органа вдоль области соединения с неизменной скоростью и постоянным воздействием ультразвука. Образуется сплошной герметичный шов, востребованный, например, при изготовлении надувных изделий или пластиковой упаковки.
В прерывистом методе рабочий орган тоже движется равномерно, но звук излучается короткими импульсами.
Точечная сварка
Выставив излучатель в нужную позицию, производят импульс. Затем смещают рабочий орган на некоторый шаг, прижимают к деталям и снова активируют ультразвуковой генератор.
Точечная сварка устанавливается в нужную позицию.Точечная сварка позволяет быстро выполнить соединение на большой площади. Расстояние между точками определяется требуемой прочностью шва.
Роликовая сварка
Используется автоматизированное оборудование. Детали перемещаются между роликами, один из которых является излучателем.
Данный способ обеспечивает высокие точность и качество соединения.
Сварка по контуру
Детали соединяют по замкнутой линии любой конфигурации. По способу подачи энергии различают 2 разновидности сварки:
- Контактную. Предполагает равномерное распределение импульса по всему поперечному сечению заготовки. Метод используют для соединения внахлест пленок и деталей толщиной до 1,5 мм из мягкой пластмассы.
- Передаточную. Применяют для соединения жесткого пластика с высокими модулем упругости и коэффициентом затухания ультразвуковых колебаний. Импульс генерируется в нескольких точках.
Применение сварки ультразвуком
Данный метод создания неразъемных соединений используется при производстве:
- Деталей и схем электроники. Формируют полупроводниковые p-n переходы, подсоединяют выводы микросхем и т.
д.
- Игрушек.
- Упаковки.
- Товаров широкого потребления с тонкостенными элементами. Например, с помощью УЗС изготавливают оправы очков.
- Аккумуляторов, батареек.
- Фреонопроводов в холодильных камерах.
- Медицинских изделий.
- Автомобильных узлов.
Также данный метод применяют для устройства электрических и теплопроводных соединений.
Возможности ультразвуковых волн
Метод позволяет соединять заготовки из следующих материалов:
- металлов;
- пластмассы;
- стекла;
- ткани;
- кожи;
- керамики;
- композитов.
Минимальная толщина изделия составляет 1 мкм. Например, в микроэлектронике методами УЗС к проволоке приваривают фольгу.
Ультразвук позволяет соединять разнородные материалы, например металл и стекло. Распространяясь по изделию, волны проникают в любые места, в т.ч. наиболее труднодоступные.
Установленные ограничения
Соединяют заготовки со следующими параметрами:
- Толщиной до 1,5-2 мм.
- Размерами не более 25-30 см.
Ограничения обусловлены затуханием звуковых колебаний в материале. Применение метода для соединения крупногабаритных заготовок является экономически нецелесообразным из-за непропорционального увеличения мощности оборудования.
Прочность получаемых швов
Сопротивление разрыву в зоне соединения достигает 70% величины, свойственной основному материалу. Для этого следует подобрать оптимальные параметры процесса.
Для образования соединения требуется около четверти секунды.Используемое в работе оборудование
Машина для УЗС состоит из следующих компонентов:
- Генератора ультразвука.
- Трансформатора упругих колебаний (бустера).
- Волновода (сонотрода). Может снабжаться наконечником.
- Опоры (наковальни).
- Охлаждающей установки.
- Блока питания.
Дополнительные узлы (присутствуют на некоторых моделях):
- Пресс, развивающий усилие до 200 кгс.
- Кронштейн для фиксации машины над рабочей зоной.
- Выносной блок управления.
- Роликовый механизм.
Оборудование делится на:
- Механизированное. Машина поддерживает параметры на заданном пользователем уровне, специальное устройство подает деталь под наконечник.
- Автоматизированное. Применяется на крупносерийном производстве. Участие оператора не требуется, все операции, в т.ч. выбор и ввод параметров, машина выполняет самостоятельно.
- Ручное. Исполнитель сам контролирует параметры процесса и ведет наконечник волновода вдоль шва. Выпускаются переносные модели.
Мощность аппаратов для УЗС составляет 100-1500 Вт.
Изменяемые параметры
Перед началом работы в настройках задают следующие величины:
- Частоту ультразвука.
- Амплитуду колебаний. Зависит от интенсивности излучения.
- Длительность импульса.
- Прижимное усилие (на моделях с прессом).

В некоторых случаях дополнительно вводят:
- Температуру предварительного нагрева заготовок.
- Высоту установки наконечника.
Оптимальное значение каждого параметра устанавливают в лаборатории опытным путем. Варят пробные образцы на разных настройках, затем подвергают их испытаниям на прочность. Комбинацию, давшую наиболее стойкое соединение, переносят на производство.
Как работают сварочные машины
Принцип действия оборудования выглядит так:
- Блок питания преобразует сетевой ток в высокочастотный. Обработка осуществляется в 2 этапа. Сначала выпрямитель превращает сигнал в постоянный, затем инвертор (электронный узел под управлением микросхемы) – в переменный с заданной частотой. Показатель в десятки кГц обеспечивают быстропереключающиеся транзисторы.
- В генераторе ультразвука пьезоэлектрический преобразователь превращает ток в механические колебания той же частоты. Стандартом являются 20 или 40 кГц, реже используют 60. В исследовательской практике частоту повышают до 180 (кГц).
- Трансформатор упругих волн увеличивает амплитуду колебаний в 5 раз. Для сваривания материалов она должна достигать 10-15 мкм. Трансформатор может дополняться концентратором.
- Импульс передается по волноводу к заготовке.
При 2-сторонней сварке опора, на которой лежат детали, выступает в роли второго волновода.
Инструкция: как вести процесс ультразвуковой сварки
Оператор действует в следующем порядке:
- Включает машину.
- Фиксирует одну из заготовок на опоре.
- Устанавливает в проектное положение привариваемую деталь. Их может быть несколько.
- Опускает на заготовки пресс со сварочным наконечником.
- Подает команду на генерацию импульса.
- Поднимает пресс.
- Визуально оценивает качество шва.
Непрерывная сварка производится в том же порядке, только после опускания пресса оператор активирует роликовый механизм для перемещения деталей под наконечником.
Волновод ручного аппарата снабжен пистолетом. Оператор прижимает его к заготовке и нажатием курка активирует генератор. Оптимальное усилие подбирают опытным путем.
Особенности работы с металлами
Соединение металлических заготовок должно совершаться при повышенных температуре и давлении. Поэтому перед сваркой их подвергают индукционному нагреву, а на прессе устанавливают следующее прижимное усилие (кгс):
- для алюминиевых деталей толщиной 0,1 мм – 7-15;
- для титановых размером 0,2 мм – 40.
Метод позволяет соединять тугоплавкие сплавы, а также пары металлов, плохо совместимые при других способах сваривания. Например, алюминий с медью или никелем.
Полимеры и иные материалы
Соединение пластмасс и композитов производят без предварительного нагрева. На прессе устанавливается относительно небольшое прижимное усилие. Например, для сварки полиэтиленовой пленки толщиной 0,02 мм оно составляет 1,5 кгс.
Полимеры производят без предварительного нагрева.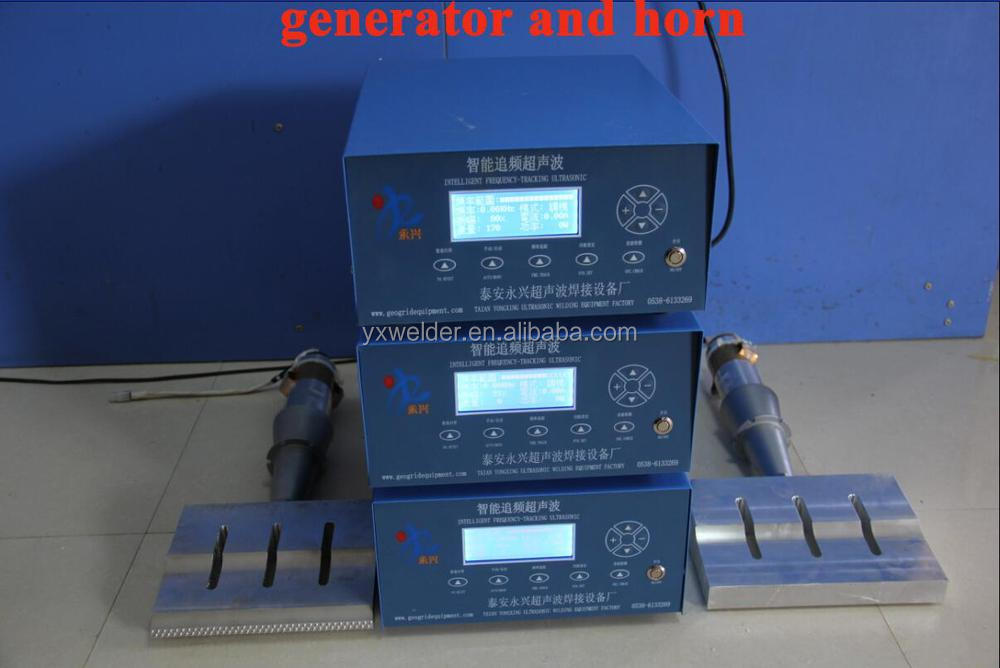
Если используется металлизированная версия материала, усилие повышают до 15 (кгс).
Плюсы ультразвуковой сварки
К достоинствам метода относят:
- Высокую скорость. Операция длится менее 3 секунд, что сравнимо только с контактной сваркой.
- Низкие энергозатраты.
- Отсутствие потребности в расходных материалах. Не нужны присадочный материал, флюс или защитный газ, как в электродуговой технологии.
- Отсутствие деформаций. Обусловлено низкой температурой нагрева.
- Высокое качество шва. Прочность сочетается с аккуратным внешним видом – отсутствуют валик и окалина. В зоне соединения образуются зерна небольшого размера, что придает стыку пластичность.
- Возможность соединять детали любой конфигурации.
- Отсутствие вредных для здоровья испарений.
- Низкие требования к квалификации сварщика.
- Возможность соединять заготовки без зачистки поверхности. Требуется только обезжиривание.
- Малую допустимую толщину детали – до 1 мкм.
- Широкий перечень соединяемых материалов.
- Возможность сваривать разнородные вещества.
- Отсутствие электромагнитного излучения и наводок, вызванных протеканием тока в детали.
К недостаткам технологии относят:
- Ограничения по размеру заготовок.
- Высокую стоимость оборудования.
- Чувствительность к влажности.
- Следы от прижатого с большим усилием инструмента. Остаются на пластике и других мягких материалах.
С развитием технологий стоимость оборудования снижается.
Ограничения по толщине в некоторых случаях удается преодолеть за счет придания заготовке особой формы. В результате возникает эффект акустической линзы: волны не рассеиваются, а фокусируются в нужной точке.
Частые дефекты
В большинстве случаев приходится сталкиваться со следующими нарушениями:
- Подрезами. Представляют собой канавки вдоль шва.
- Непроваром.
- Свищами.
Представляют собой трубчатые полости в материале, образованные выходящим газом.
- Прожогами.
Подрезы образуются в мягких материалах из-за сильного давления наконечника. Сечение детали в этом месте уменьшается, а с ним и прочность. Кроме того, канавка служит концентратором напряжения, что повышает вероятность разрушения. Для предотвращения появления подрезов требуется качественно заточить рабочий торец волновода или наконечника.
Свищи появляются при заваривании банок с жидким продуктом. Об их наличии свидетельствует туман, окружающий стык в процессе обработки. Причиной является «ультразвуковой ветер» – движение воздуха от излучателя, вытесняющее жидкость из емкости. Необходимо подобрать оптимальную комбинацию параметров в соответствии с вязкостью продукта.
Непроваренные участки появляются при заниженной интенсивности излучения, не соответствующей размерам заготовок. В большинстве случаев подобные дефекты возникают при сваривании деталей с разной толщиной стенки. Интенсивность излучения настраивают на минимальный размер. Когда волновод подходит к более толстому участку, ее оказывается недостаточно. Требуется изменить конструкцию изделия либо применить программируемую машину с возможностью регулировки параметров в процессе выполнения шва.
Прожоги возникают по следующим причинам:
- неправильная настройка системы охлаждения;
- прилипание размягченного полимера к волноводу.
Опытным путем было установлено, что наиболее качественные швы получаются при наличии насечек или накатки на торце наконечника. Выступы необходимо скруглить, чтобы избежать внедрения инструмента в материал.
Полезная литература
Для освоения УЗС рекомендуется ознакомиться со следующими источниками:
- В.
Ю. Вероман, А. Б. Аренков: «Ультразвуковая обработка материалов».
- И. Г. Хорбенко: «Ультразвук в машиностроении».
- И. Д. Клеткин, В. П. Полухин и др.: «Ультразвуковая сварка при изготовлении одежды».
Полезно иметь справочники с указанием оптимальных параметров для разных условий сварки.
Технология и оборудование ультразвуковой сварки металлов (4часть)
Установки типа УЗС (рис. 16) и УЗС-2 предназначены для присоединения круглых (диаметром 0,03—0,1) и плоских проводников толщиной до 0,1 мм из пластичных металлов (золота, алюминия) к тонким золотым, алюминиевым и медным пленкам, напыленным на диэлектрические подложки. Установки комплектуются ламповыми ультразвуковыми генераторами.
Полуавтомат МС41П2-1 предназначен для соединения деталей микросхем в круглом и плоском корпусах ультразвуковой сваркой золотыми и алюминиевыми проводниками диаметром 20—25 мкм. Высокая производительность станка (до 800 сварок в час) обеспечивается автоматической подачей и обрывом проволоки.
Электрическая схема управления машиной выполнена на транзисторных конических элементах с бесконтактной коммутацией цепей. Ультразвуковой генератор на транзисторах имеет автоматическую подстройку частоты, чем достигается стабильность амплитуды колебания сварочного инструмента. Кинематическая схема полуавтомата МС41П2-1 приведена на рис. 17.
Корпус сварочной головки 1 может перемещаться вертикально в направляющих. Ее подъем и опускание осуществляются кулачком 2. В установленном положении сварочная головка фиксируется стопором. Механическая колебательная система 6 укреплена в корпусе на оси 5. Поворот системы достигается с помощью кронштейна 8 от кулачка 12, который поворачивается от перемещения тяги 13 при нажатии на педаль 14.
Установка для ультразвуковой сварки с импульсным косвенным нагревом УЗСКН-I (рис. 18) предназначена для изготовления полупроводниковых приборов, тонкопленочных и полупроводниковых интегральных схем.
Рис. 16. Установка УЗС
Рис.17.Кинематическая схема полуавтомата МС41П2-1
В установке использован комбинированный цикл — ультразвуковая сварка в сочетании с импульсным косвенным нагревом. Установка предусматривает возможность сварки как комбинированным циклом с любой последовательностью импульсов ультразвука и нагрева и с разной длительностью смещения моментов их включения, так и сварке только ультразвуком или только косвенным нагревом. Свариваемые элементы нагреваются за счет теплопередачи от сварочного инструмента (пуансона), нагреваемого импульсом проходящего через него тока промышленной частоты (50 Гц).
Для осуществления токоподвода к сварочному инструменту применена конструкция «расщепленного» преобразователя ультразвуковых колебаний, в котором волновод разрезан на две равные части, между которыми расположен тонкий слой изоляции (рис. 19). Сварочный инструмент в виде V-образной иглы вставляется в отверстие на рабочем конце «расщепленного» волновода между его обеими частями и стягивается винтом для обеспечения хорошего акустического и электрического контакта.
На установке УЗСКН-1 можно приваривать круглые (диаметром 0,03—0,1 мм) и плоские (толщиной до 0,05 мм) проводники из алюминия, золота, меди к контактным площадкам из золота, алюминия, меди, тантала, никеля, напыленные на диэлектрические полупроводниковые подложки.
Опыт эксплуатации сварочных ультразвуковых установок показал, что этот метод наиболее перспективный в микроэлектронике, так как обеспечиваем получение высоконадежных соединений, исключает общий разогрев изделия, позволяет соединять трудносвариваемые обычными методами сочетания материалов и т. п.
ВНИИЭСО разработан ряд ультразвуковых сварочных машин типа КТУ и МТУ (табл. 7). Акустический узел (рис. 20) этой серии машин состоит из резонирующего стержня со сварочным наконечником 1, концентратора с магнитострикционным преобразователем 2 с обмоткой. Диаметр контактной площади наконечника определяется технологическими требованиями к сварной точке.
Рис.18.Установка для ультразвуковой сварки с импульсным косвенным нагревом УЗСКН-1
Рис.19.Преобразователь ультразвуковых колебаний к установке УЗСКН-1
Рис.20. Акустический узел машины МТУ-0,4
Технические характеристики машин типа МТУ и КТУ
Показатели | МТУ-0,4 | МТУ-1,5 | КТУ-1,5 | МТУ-4 |
Мощность, кВт | 0,4 | 1,5 | 1,5 | 4,0 |
Частота, кГц | 22,0 | 22,0 | 22,0 | 18,0 |
Усилие сжатия, кгс | 6—60 | 15—150 | 15—120 | 50—550 |
Толщина свариваемых металлов (медь), мм | 0,01—0,2 | 0,1—0,5 | 0,1—0,5 | 0,3—1,2 |
Масса машины, кг | 76 | 82 | 80 | 105 |
Примечание. |
Сварочный наконечник изготовлен из высоколегированной стали, применение которой исключает налипание свариваемых металлов (медь, алюминий) на наконечник и не требует зачистки даже после сварки 5—20 тыс. точек. Усилие сжатия свариваемых деталей создается приводом давления. Акустический узел в горизонтальном направлении может перемещаться специальным приводом.
Принцип построения механической колебательной системы сварочной головки ультразвуковых сварочных клещей КТУ-1,5 (рис. 21) аналогичен системе, принятой в сварочных ультразвуковых машинах.
Имеющийся опыт применения сварки ультразвуком выявил следующие преимущества этого способа:
Рис.21. Сварочная головка клещей КТУ-1,5
Рис.22. Медные проводники диаметром 0,3 мм, покрытые лаковой изоляцией, приваренные с помощью ультразвука к клеммной колодке
1. Сварка ультразвуком происходит в твердом состоянии без существенного нагрева места сварки, что позволяет соединять химически активные металлы или пары металлов, склонные образовывать хрупкие интерметаллические соединения в зоне сварки.
2. Возможны соединения тонких и ультратонких деталей, приварка тонких листов и фольги к деталям неограниченной толщины, сварка пакетов из фольги.
3. Снижены требования к чистоте свариваемых поверхностей, в связи с чем возможна сварка плакированных и оксидированных поверхностей и вообще сварка металлических изделий, поверхности которых покрыты различными изоляционными пленками.
4. Небольшие сдавливающие усилия (10—250 кгс 98—2450 Н) вызывают незначительную деформацию поверхности деталей в месте их соединения (вмятина, как правило, не превышает 5—10%).
5. Применяется оборудование малой мощности и несложной конструкции (если, например, для контактной точечной сварки алюминия толщиной 1 мм необходима машина мощностью 100—150 кВА, то при сварке ультразвуком аналогичного соединения — всего 5—2,5 кВА).
Ультразвуковая сварка нашла достаточно широкое применение для соединения тонких деталей из однородных и разнородных материалов в приборостроении и радиоэлектронной промышленности.
Рис.23. Контакты, приваренные к контактным пружинам с помощью ультразвука
Рис.24.Сварные корпусы приборов типа П6
- Назад
- Вперед
Ультразвуковая сварка металлов
Главная » Статьи » Ультразвуковая сварка металлов
Ультразвуковая сварка металлов
Тарас Никифоров
Технический центр «Виндэк» (Россия, г. Подольск)
Владимир Гуреев
TELSONIC AG (Швейцария)
На мировом рынке только за последнее десятилетие объем продаж оборудования для ультразвуковой сварки увеличился в несколько раз, и эксперты пророчат ему дальнейший рост. Благодаря новым достижениям в разработке технологии данные сварочные системы позволяют решать уникальные задачи в электронной, электротехнической, автомобильной промышленности, а также при производстве аккумуляторов, конденсаторов, солнечных батарей и систем нагрева воды.
В наши дни ультразвуковая сварка металлов находит все более широкое применение и позиционируется чуть ли ни как инновационный продукт. Вместе с тем, мало кто знает, что данный метод был открыт еще в 30-40 годы прошлого столетия, причем, совершенно случайно. При подготовке поверхности алюминия к контактной сварке экспериментаторы, применившие для этой вспомогательной цели ультразвуковые колебания, неожиданно для себя отметили, что соединение металлических пластин происходит еще до пропускания через них сварочного тока. Вот так и было положено начало совершенно новому виду сварки.
Как работает?
Область применения такого метода соединения простирается в диапазоне от пластмасс до цветных металлов. Однако, независимо от свариваемых материалов, оборудование для ультразвуковой сварки традиционно состоит из высокочастотного генератора, блока управления, механической колебательной системы и привода давления (Рис.1).
Ультразвуковой генератор преобразует ток электрической сети в ток высокой частоты, который по получении сигнала с блока управления подается на пьезоэлементы колебательной системы. Преобразование колебаний электрического тока высокой частоты в механические и введение их в зону сварки обеспечивается механической колебательной системой. Последняя, в свою очередь, состоит из конвертера (преобразователь), бустера (усилитель) и волновода (сонотрод) и является главным узлом технологии ультразвуковой сварки.
Для доступности понимания сравним колебательную систему, обеспечивающую практическую реализацию метода, например, с автомобилем (Рис.2). Конвертер выступает в роли мотора, преобразовывая ток высокой частоты в механические колебания с соответствующей частотой. Далее бустер, действуя как коробка передач, изменяет амплитуду колебаний в зависимости от передаточного числа и переадресует их на волновод. Волновод, увеличивая при необходимости амплитуду механических колебаний высокой частоты, передает их непосредственно в зону сварки, приводя в движение верхнюю свариваемую деталь.
В основу работы пьезокерамического конвертера положен хорошо известный многим еще со школьной скамьи пьезоэлектрический эффект. При воздействии на пьезоэлемент переменного давления возникает переменное электрическое напряжение, а под воздействием переменного электрического поля возникают механические напряжения, которые вызывают упругие деформации материала в следствии чего пьезоэлемент начинает сжиматься и увеличиваться на определенную величину с частотой равной частоте тока.
Величина изменения размера пьезоэлемента соответствует амплитуде механических колебаний (Рис.3), которая зависит от мощности и конфигурации конвертера. Так, при частоте 20кГц амплитуда колебаний пьезокерамического конвектора, как правило, не превышает 10мкм. Однако, за счет увеличения амплитуды бустером и волноводом можно получить максимальную амплитуду в зоне сварки – до 70мкм. Для ультразвуковой сварки обычно используется частота от 20кГц и выше. Применение той или иной частоты зависит от материала и габаритов свариваемого изделия.
Применительно к реальным технологиям это явление может иметь очень положительный эффект. Вот и в процессе ультразвуковой сварки металлов колебательные движения волновода совместно с усилием прижатия передаются на верхнюю свариваемую деталь. Она по определению должна быть подвижной относительно нижней детали, прочно закрепленной на наковальне. В результате между деталями возникает трение с определенной частотой и амплитудой, способствующее их сращиванию между собой (Рис. 4). Именно поэтому ультразвуковую сварку можно еще классифицировать, как механическую сварку трением с высокой частотой без ввода сварочного тока в зону сварки.
В процессе сварки микроскопические смещения деталей относительно друг друга вызывают стирание шероховатостей, разрушение оксидных пленок и возникновение узлов схватывания. При повышение температуры в зоне сварки, за счет трения и дальнейшей деформации свариваемых деталей, наблюдается повышение пластичности поверхностных слоев металла, вытеснение оксидных пленок и загрязнений из зоны сварки. Все это приводит к интенсивному разрастанию зон схватывания, диффузии одного материала в другой, локальному плавлению верхних атомарных слоев, появлению новых и стойких межатомных связей. Данные структурные изменения можно воочию наблюдать на фотографии микрошлифа покрытых серебром медных проводов, которые были сварены между собой при помощи ультразвука (Рис.5).
Плюсы применения
Ультразвуковая сварка металлов обладает уникальными технологическими свойствами, которые в практическом применении дают ей сто очков вперед на многих направлениях. Перечислим только главные из них.
Прежде всего, это возможность производить сварку без предварительной подготовки поверхности соединяемых деталей и при весьма незначительном температурном воздействии, оказываемом непосредственно на них. Отсюда вытекает такое существенное преимущество ультразвуковой сварки, как умение накрепко и без печальных последствий соединять между собой термочувствительные элементы.
Более того, допустима сварка деталей разной толщины, а также разнородных металлов (медь-алюминий, алюминий-никель и др.). При ультразвуковой сварке достигаются отличные электрические свойства и незначительное переходное сопротивление.
Что очень даже существенно, прочность обеспечиваемых ультразвуком соединений приближается к 70% от прочности основного материала. Дополнительно следует отметить высокую скорость, экологическую чистоту и экономичность процесса.
Проверено практикой
Как уже было сказано, инновационная технология ультразвуковой сварки металлов благодаря своим особым свойствам находит все более широкое применение в самых различных отраслях промышленности. Например, в автомобилестроении метод активно используется при соединении медных многожильных проводов жгутов электропроводки (Рис.6). В России данную технологию весьма успешно применяют, в частности, такие производители автокомпонентов, как Leoni Group, Prettl, ИВК, Завод радиоаппаратуры, ПТОО ОАО «АВТОВАЗ» и другие. Конкурентными преимуществами собственной продукции они во многом обязаны внедрению у себя ультразвуковой технологии. Так ультразвуковые системы TelsoSplice, выпускаемые швейцарской фирмой Telsonic AG, способны сваривать многожильные медные провода суммарным сечением от 0,5 до 45мм2. Также ультразвуковая сварка используется при производстве электромоторов и патронов для подушек безопасности.
Масштабное применение ультразвуковая сварка обрела в электронной и электротехнической промышленности. И ничего удивительного здесь нет. Ведь ультразвук умеет соединять как миниатюрные изделия, так и проводку большого суммарного сечения до 200мм2 (Рис.7). Впрочем, в последнем случае описываемые нами системы оснащаются генераторами мощностью в 10кВт и наделяются способностью оказывать усилие в 8000Н.
С помощью ультразвуковой технологии, например, на «Свердловском заводе трансформаторов тока» к медному контакту присоединяют многожильные провода. Тем же способом специалисты ОАО «Протвинский опытный завод «ПРОГРЕСС» приваривают многожильные медные провода к шинам электрических шкафов. Наглядной демонстрацией преимуществ ультразвуковой сварки можно назвать и ее применение в компании Bosch. В частности, там при изготовлении электродвигателей соединяют провода с контактами без снятия с них защитной эмали, что позволило полностью автоматизировать процесс сборки автомобильных электромоторчиков.Или еще примеры. Растущая потребность в солнечных батареях и системах нагрева воды повлекла за собой использование ультразвуковой шовной сварки металлов в процессе создания и такого рода устройств. Компания «Элеконд» применяет ультразвук в соединении алюминиевой фольги и контактов. Кстати будет сказать, что технология применима также и в изготовлении самой алюминиевой фольги. Но продолжим о применениях, так сказать, по прямому назначению.
При производстве литий-ионных аккумуляторов компания VARTA при помощи ультразвука сваривает между собой алюминиевую, медную и никелевую фольгу. На заводе им. Фрунзе при изготовлении предохранителей тем же способом сваривают медные и биметаллические пластины. ФГУП ВНИИА им. Н.Л. Духова, используя технологию ультразвуковой сварки, соединяет алюминиевую фольгу толщиной всего от 5мкм.
Примером уникальности метода и его нацеленности на решение сложных задач, недоступных другим технологиям, может служить и соединение медных проводников с контактами в керамической подложке (Рис. 8). Впрочем, как в оценке всего нового, не будем спешить с конечным выводом. В самом ближайшем будущем нам еще предстоит узнать, на что еще способна ультразвуковая сварка.
А о том, что это обозримая перспектива свидетельствует опыт уже упомянутой компании TELSONIC AG. Она выпускает прецизионные сварочные системы, способные работать как автономно, так и в составе автоматизированных линий. Причем, неустанно продолжает поиск новых применений. Официальным дилером этой компании в России является ООО «Технический центр «Виндэк» из подмосковного Подольска.
Подводя итог, следует сказать, что использование ультразвуковых технологий существенно облегчает получение требуемых характеристик сварного соединения и повышает эффективность производства.
windeq.ru
Технология и оборудование ультразвуковой сварки металлов (1часть)
Ультразвук находит широкое применение в науке для исследования некоторых физических явлений и свойств веществ. В технике ультразвуковые колебания используют для обработки металлов и в дефектоскопии.
В сварочной технике ультразвук может быть использован в различных целях. Воздействуя им на сварочную ванну в процессе кристаллизации, можно улучшить механические свойства сварного соединения благодаря измельчению структуры металла шва и удалению газов.
Ультразвук может быть источником энергии для создания точечных и шовных соединений. Ультразвуковые колебания активно разрушают естественные и искусственные пленки, что позволяет сваривать металлы с окисленной поверхностью, покрытые слоем лака и т. п. Ультразвук снижает или снимает собственные напряжения и деформации, возникающие при сварке. Им можно стабилизировать структурные составляющие металла сварного соединения, устраняя возможность самопроизвольного деформирования сварных конструкций со временем.
В качестве источника энергии при сварке металлов ультразвук еще не нашел широкого применения, хотя этот способ имеет ряд преимуществ и особенностей по сравнению с контактной и холодной сваркой.
При сварке ультразвуком неразъемное соединение металлов образуется при совместном воздействии на детали механических колебаний высокой частоты и относительно небольших сдавливающих усилий. В принципе этот метод сварки имеет много общего с холодной сваркой сдвигом.
Для получения механических колебаний высокой частоты обычно используется магнитострикционный эффект, состоящий в изменении размеров, некоторых металлов и сплавов под действием переменного магнитного поля. Для ультразвуковых преобразователей обычно используют чистый никель или железо-кобальтовые сплавы. Изменения размеров магнитострикционных материалов очень малы: так, для никеля магнитострикционное удлинение составляет 40-10-6. Поэтому для увеличения амплитуды смещения и концентрации энергии колебаний, а также Для передачи механических колебаний к месту сварки используют волноводы или концентраторы, которые в большинстве случаев имеют сужающуюся форму.
Эксперименты показывают, что для сварки металлов достаточно иметь волноводы с коэффициентом усиления около 5, при этом амплитуда на конце волновода при холостом ходе должна быть 20—30 мкм. Магнитострикционный преобразователь и волноводы должны быть рассчитаны и изготовлены на заданную частоту ультразвукового генератора.
Основной узел машины для выполнения точечных соединений с помощью ультразвука — магнитострикционный преобразователь (рис. 8).
Рис.8. Схема установки для точечной сварки ультразвуком:1—магнитострикционный преобразователь;2— диафрагма;3 — механизм нажатия;4 — выступ;5 — маятниковая опора;6 — волновод;7 — кожух водяного охлаждения;8 — изделие
Его обмотка питается током высокой частоты от ультразвукового генератора. Охлаждаемый водой магнитострикционный преобразователь 1 изготовлен из пермендюра (К49Ф2), он служит для превращения энергии тока высокой частоты в механические колебания, которые передаются волноводу 6. На конце волновода имеется рабочий выступ 4. При сварке изделие 8 зажимают между рабочим выступом 4 и механизмом нажатия 3, к которому прикладывают усилие, необходимое для создания давления в процессе сварки.
Сварка происходит при включенном преобразователе. Высокочастотные упругие колебания передаются через волновод на рабочий выступ 4 в виде горизонтальных механических перемещений высокой частоты. Длительность процесса сварки зависит от свариваемого металла и его толщины, для малых толщин она исчисляется долями секунды.
Основные узлы машины для выполнения шовных соединений при помощи ультразвука (рис. 9): вращающийся магнитострикционный преобразователь 1 н волновод 2. Конец волновода имеет форму ролика 3. Изделие 5, подлежащее соединению, зажимают между вращающимся роликом 3 волновода и холостым роликом 4, Высокочастотные упругие колебания передаются через волновод на ролик, который вращается вместе с волноводом.
Рис.9.Схема установки для роликовой сварки ультразвуком:1—магнитострикционный преобразователь; 2 — волновод; 3 — сваривающий ролик;4 — прижимной ролик; 5 — изделие; 6 — кожух преобразователя; 7 — подвод тока от ультразвукового генератора;8 — привод; 9 — подвод охлаждающей воды
Изделие, зажатое между роликами, перемещается, и одновременно создается герметичное соединение.
Сварка по контуру, разработанная в МВТУ — МЭИ, обеспечивает получение герметичного шва практически самого сложного контура. Простейший ее вид — сварка по кольцу. В этом случае конический штифт, вставляемый в волновод, имеет форму трубки (рис. 10). При равномерном поджатии деталей к сваривающему штифту получается герметичное соединение по всему контуру.
Процесс ультразвуковой сварки происходит при воздействии сдвигающих высокочастотных колебаний, давления, приложенного перпендикулярно к поверхности листа, и теплового эффекта, сопровождающего процесс сварки. В результате в зоне сварной точки наблюдается небольшая пластическая деформация.
Исследование процесса образования сварного соединения при ультразвуковой сварке медных пластин толщиной 0,35 + 0,35 мм показывает, что при малом времени пропускания ультразвука (менее 0,05 с) сварка не происходит.
Рис.10.Схема установки для ультразвуковой сварки по контуру:1— волновод;2 — сменный полый штифт; 3 — сменный прижимной штифт; 4 — прижимная опора; 5 — свариваемое изделие
Рис.11. Макроструктура мест разрушения сварных соединений меди после различной продолжительности пропускания ультразвука. Х16
После разъединения образцов на их поверхности непосредственно под сваривающим выступом наблюдается пятно, имеющее полированную поверхность (рис. 11, а). Диаметр полированного пятна возрастает при увеличении времени сварки (рис. 11, а—д). При пропускании ультразвука в течение 0,1 с в местах контакта обнаруживаются не только зашлифованные поверхности, но и вы- рывы металла, свидетельствующие об образовании прочных соединений, так называемых узлов схватывания. На рис. 11, б виден один узел схватывания на зашлифованной поверхности.
Пропускание ультразвука в течение 0,73 с привело к дальнейшему увеличению площади зашлифованного пятна, при этом площадь узла схватывания также возросла. Вокруг основного узла схватывания возникли отдельные небольшие участки схватывания, удлиненные в направлении ультразвуковых колебаний. С увеличением времени пропускания ультразвука более 0,73 с площадь зашлифованного участка почти не изменяется (рис. 11, г, д), но площадь узлов схватывания начинает увеличиваться более интенсивно. При пропускании ультразвука свыше 1,06 с происходит разрушение сварного соединения с вырывом точки по всему контуру.
Проведенные измерения микротвердости поверхности зашлифованного пятна и основного металла вблизи пятна показали, что микротвердость поверхностного слоя зашлифованного пятна выше (Н50 42—44), чем у основного металла (Н50 28—30). Образование полированного пятна на свариваемых поверхностях указывает на то, что оно возникло вследствие трения под действием высокочастотных колебаний соприкасающихся поверхностей непосредственно под контактным выступом.
Таким образом, процесс ультразвуковой сварки происходит под действием трения, вызванного микроскопическим возвратно-поступательным перемещением трущихся поверхностей.
www.prosvarky.ru
Ультразвуковая сварка металлов и пластмасс
Ультразвуковая сварка металлов и пластмасс – эта еще одна разновидность классической сварки давлением. Данный технологический процесс основан на сжимании двух заготовок, свариваемые кромки (плоскости) которых вибрируют (смещаются в тангенциальном направлении) с ультразвуковыми (до 40 КГц) частотами.
В итоге, при контакте «деталь в деталь», на кромках шва возникает пластическая деформация, перетекающая в объединение кристаллических решеток или полимерных цепочек стыкуемых элементов.
В данной статье мы разберем процесс ультразвуковой сварки с физической и технологической точки зрения. Кроме того, на этой странице вы сможете найти описание типового оборудования, необходимого для сварки заготовок ультразвуковыми колебаниями. А в завершении мы разберем технологические приемы реализации этого процесса.
Ультразвуковая сварка пластмасс и металлов: суть процесса
Процесс ультразвуковой сварки основан на совмещении тангенциальных колебаний и вертикальной нагрузки в зоне контакта двух деталей.
В результате такого воздействия истираются микронеровности, покрывающие контактные поверхности, и разрушается оксидная пленка.
Кроме того, возникает эффект перетекания кинетической энергии возвратно-поступательных колебаний в тепловое излучение, расплавляющее поверхностные слои деталей. И в этих условиях, даже относительно небольшая вертикальная нагрузка приводит к образованию межкристаллических (у металла) или межмолекулярных (у полимера) связей, скрепляющих соединяемые детали.
Таким образом, все установки ультразвуковой сварки функционируют на основе термомеханической технологии получения неразъемного соединения. Причем такие аппараты не нуждаются во внешнем нагреве. Выделяемой при трении деталей энергии вполне достаточно для образования новых межатомных или межмолекулярных связей.
Где используют ультразвуковую сварку?
Ввиду дороговизны оборудования классическое применение ультразвуковой сварки – монтаж элементов металлоконструкций – было бы экономически неоправданным. Однако с помощью этой технологии удается сваривать не только металлы, но и полимеры, и даже органические соединения.
Поэтому ультразвуковая технология используется в приборостроении, электронике и прочих отраслях, где есть спрос на эффективные способы сопряжение металлических и неметаллических элементов.
Кроме того, ультразвуковой способ подходит и для сварки материалов с чрезвычайно прочной оксидной пленкой. Хороший пример такого случая — ультразвуковая сварка алюминия, покрытого тугоплавким оксидом (температура плавления более 2000 градусов Цельсия). В данном случае ультразвуковые аппараты действуют более эффективно, чем классическая аргонодуговая технология.
А еще, существует особая технология ультразвуковой сварки костной ткани, использующая в качестве присадочного материала эфир цианакриловой кислоты. Введенный в разлом кости циакрин твердеет под действием ультразвука и образует высокопрочный шов между обломками органической ткани.
Оборудование для ультразвуковой сварки
Работающая на ультразвуке сварочная установка состоит из следующих блоков:
- Генератора ультразвуковых колебаний, формирующего переменное электромагнитное поле, частота которого выходит за пределы 20 КГц.
- Вибратора, трансформирующего волновые колебания в механическую вибрацию. Вибратор состоит из пакета пластин (толщиной не более десятой части миллиметра), изготовленных их особого материала, который меняет линейные габариты под действием магнитного поля. В итоге, магнитное поле, передаваемое от генератора на пластины, то удлиняет, то укорачивает их размер и электромагнитная волна перетекает в механическую вибрацию.
- Вибратор соединяется волноводом конической или цилиндрической формы, который транслирует механическую вибрацию на поверхность внешней детали. Причем конический волновод работает еще и как резонатор, усиливая амплитуду и повышая эффективность процесса.
Помимо указанных блоков в конструкцию аппарата входит еще и особый сварочный стол, на котором покоятся соединяемые детали. Причем аппарат ультразвуковой сварки транслирует вибрацию на внешнюю деталь в продольном, продольно-поперечном или в продольно-вертикальном направлении. Кроме того, возможно и взаимное кручение стыкуемых элементов.
В завершении описания оборудования следует отметить, что стыкуемые детали попадают на рабочий стол аппарата в следующей последовательности: вниз укладывают толстую деталь, на которую помещают тонкую заготовку. Соотношение толщины верхней и нижней заготовок может достигать значения 1/1000.
Технологические приемы сварки ультразвуком
В процессе сварки ультразвуком используют следующие варианты стыковки деталей:
- Сопряжение внахлест, когда поверх одной плоской заготовки укладывают аналогичную.
- Сопряжение по рельефу, когда нижняя плита соприкасается с рельефной поверхностью верхней детали.
- Сопряжение по кромкам, когда торцы изделий либо накладываются друг на друга, либо стыкуются под углом.
- Сопряжение «крест-накрест» и тавровое сопряжение, когда два прутка накладываются внахлест, при несовпадении осей стыкуемых деталей, или когда торец прутка стыкуют с плоскостью.
- Многослойное сопряжение, когда стыкуют больше двух заготовок.
Кроме того, существует и схема параллельной сварки двух прутков (вдоль оси), прутка и плоскости.
Указанные варианты соединения реализуются за счет трансляции колебаний в продольном (внахлест, рельеф), продольно-поперечном (встык под углом) или крутящем направлении (тавровое или прямое стыковое направление).
steelguide.ru
Технология и оборудование ультразвуковой сварки металлов (4часть)
Установки типа УЗС (рис. 16) и УЗС-2 предназначены для присоединения круглых (диаметром 0,03—0,1) и плоских проводников толщиной до 0,1 мм из пластичных металлов (золота, алюминия) к тонким золотым, алюминиевым и медным пленкам, напыленным на диэлектрические подложки. Установки комплектуются ламповыми ультразвуковыми генераторами.
Полуавтомат МС41П2-1 предназначен для соединения деталей микросхем в круглом и плоском корпусах ультразвуковой сваркой золотыми и алюминиевыми проводниками диаметром 20—25 мкм. Высокая производительность станка (до 800 сварок в час) обеспечивается автоматической подачей и обрывом проволоки. В полуавтомате для повышения стабильности прочностных показателей использован сопутствующий подогрев. Полуавтомат состоит из следующих узлов: сварочной головки, кассеты с проволокой, ультразвукового генератора, блока регулирования температуры подогрева, манипулятора и микроскопа МБС-2.
Электрическая схема управления машиной выполнена на транзисторных конических элементах с бесконтактной коммутацией цепей. Ультразвуковой генератор на транзисторах имеет автоматическую подстройку частоты, чем достигается стабильность амплитуды колебания сварочного инструмента. Кинематическая схема полуавтомата МС41П2-1 приведена на рис. 17.
Корпус сварочной головки 1 может перемещаться вертикально в направляющих. Ее подъем и опускание осуществляются кулачком 2. В установленном положении сварочная головка фиксируется стопором. Механическая колебательная система 6 укреплена в корпусе на оси 5. Поворот системы достигается с помощью кронштейна 8 от кулачка 12, который поворачивается от перемещения тяги 13 при нажатии на педаль 14. Обратный ход кулачка происходит под действием пружины 12. Начальное положение сварочного наконечника 7 относительно свариваемой детали регулируют перемещением ползуна 9 с роликом 10 в пазу кронштейна 8. Усилие сжатия регулируют ручкой 3 механизма 4 давления.
Установка для ультразвуковой сварки с импульсным косвенным нагревом УЗСКН-I (рис. 18) предназначена для изготовления полупроводниковых приборов, тонкопленочных и полупроводниковых интегральных схем.
Рис. 16. Установка УЗС
Рис.17.Кинематическая схема полуавтомата МС41П2-1
В установке использован комбинированный цикл — ультразвуковая сварка в сочетании с импульсным косвенным нагревом. Установка предусматривает возможность сварки как комбинированным циклом с любой последовательностью импульсов ультразвука и нагрева и с разной длительностью смещения моментов их включения, так и сварке только ультразвуком или только косвенным нагревом. Свариваемые элементы нагреваются за счет теплопередачи от сварочного инструмента (пуансона), нагреваемого импульсом проходящего через него тока промышленной частоты (50 Гц).
Для осуществления токоподвода к сварочному инструменту применена конструкция «расщепленного» преобразователя ультразвуковых колебаний, в котором волновод разрезан на две равные части, между которыми расположен тонкий слой изоляции (рис. 19). Сварочный инструмент в виде V-образной иглы вставляется в отверстие на рабочем конце «расщепленного» волновода между его обеими частями и стягивается винтом для обеспечения хорошего акустического и электрического контакта.
На установке УЗСКН-1 можно приваривать круглые (диаметром 0,03—0,1 мм) и плоские (толщиной до 0,05 мм) проводники из алюминия, золота, меди к контактным площадкам из золота, алюминия, меди, тантала, никеля, напыленные на диэлектрические полупроводниковые подложки.
Опыт эксплуатации сварочных ультразвуковых установок показал, что этот метод наиболее перспективный в микроэлектронике, так как обеспечиваем получение высоконадежных соединений, исключает общий разогрев изделия, позволяет соединять трудносвариваемые обычными методами сочетания материалов и т. п.
ВНИИЭСО разработан ряд ультразвуковых сварочных машин типа КТУ и МТУ (табл. 7). Акустический узел (рис. 20) этой серии машин состоит из резонирующего стержня со сварочным наконечником 1, концентратора с магнитострикционным преобразователем 2 с обмоткой. Диаметр контактной площади наконечника определяется технологическими требованиями к сварной точке.
Рис.18.Установка для ультразвуковой сварки с импульсным косвенным нагревом УЗСКН-1
Рис.19.Преобразователь ультразвуковых колебаний к установке УЗСКН-1
Рис.20. Акустический узел машины МТУ-0,4
Технические характеристики машин типа МТУ и КТУ
Показатели | МТУ-0,4 | МТУ-1,5 | КТУ-1,5 | МТУ-4 |
Мощность, кВт | 0,4 | 1,5 | 1,5 | 4,0 |
Частота, кГц | 22,0 | 22,0 | 22,0 | 18,0 |
Усилие сжатия, кгс | 6—60 | 15—150 | 15—120 | 50—550 |
Толщина свариваемых металлов (медь), мм | 0,01—0,2 | 0,1—0,5 | 0,1—0,5 | 0,3—1,2 |
Масса машины, кг | 76 | 82 | 80 | 105 |
Примечание. |
Сварочный наконечник изготовлен из высоколегированной стали, применение которой исключает налипание свариваемых металлов (медь, алюминий) на наконечник и не требует зачистки даже после сварки 5—20 тыс. точек. Усилие сжатия свариваемых деталей создается приводом давления. Акустический узел в горизонтальном направлении может перемещаться специальным приводом.
Принцип построения механической колебательной системы сварочной головки ультразвуковых сварочных клещей КТУ-1,5 (рис. 21) аналогичен системе, принятой в сварочных ультразвуковых машинах.
Имеющийся опыт применения сварки ультразвуком выявил следующие преимущества этого способа:
Рис.21. Сварочная головка клещей КТУ-1,5
Рис.22. Медные проводники диаметром 0,3 мм, покрытые лаковой изоляцией, приваренные с помощью ультразвука к клеммной колодке
1. Сварка ультразвуком происходит в твердом состоянии без существенного нагрева места сварки, что позволяет соединять химически активные металлы или пары металлов, склонные образовывать хрупкие интерметаллические соединения в зоне сварки.
2. Возможны соединения тонких и ультратонких деталей, приварка тонких листов и фольги к деталям неограниченной толщины, сварка пакетов из фольги.
3. Снижены требования к чистоте свариваемых поверхностей, в связи с чем возможна сварка плакированных и оксидированных поверхностей и вообще сварка металлических изделий, поверхности которых покрыты различными изоляционными пленками.
4. Небольшие сдавливающие усилия (10—250 кгс 98—2450 Н) вызывают незначительную деформацию поверхности деталей в месте их соединения (вмятина, как правило, не превышает 5—10%).
5. Применяется оборудование малой мощности и несложной конструкции (если, например, для контактной точечной сварки алюминия толщиной 1 мм необходима машина мощностью 100—150 кВА, то при сварке ультразвуком аналогичного соединения — всего 5—2,5 кВА).
Ультразвуковая сварка нашла достаточно широкое применение для соединения тонких деталей из однородных и разнородных материалов в приборостроении и радиоэлектронной промышленности.
Рис.23. Контакты, приваренные к контактным пружинам с помощью ультразвука
Рис.24.Сварные корпусы приборов типа П6
www.prosvarky.ru
Сварка металлов (ультразвуковая) | Ультразвуковые резонаторы
- Точечная сварка
- Система язычковых клиньев
- Система бокового привода
- Сравнение систем
- Зажимное усилие
- Системы боковой поддержки привода
- Примеры усилия зажима
- Регулировка амплитуды сварочного наконечника
- Настройка
- Доступность
- Техническое обслуживание и износ
- Адаптивность
- Зажимное усилие
- Инструменты
- Инструментальные материалы
- Образцы оснастки
- Обработка
- Шовная сварка
- Рога
- Цифры
- Рисунок 1.
Аппараты для ультразвуковой сварки металлов — типичные конфигурации оборудования
- Рисунок 2. Сменный металлический сварочный наконечник для сварочного аппарата Weedge-reed .
- Рисунок 3. Металлический сварочный рожок с боковым приводом, поддерживаемый двумя вертикальными элементами
- Рисунок 4. Стальной металлический сварочный рожок с боковым приводом и встроенной сварочной поверхностью
- Рисунок 5. Металлический сварочный рожок с боковым приводом со сменным наконечником под шайбу
- Рисунок 6. Крепление на полюс для сварочного аппарата с боковым приводом
- Рисунок 7. Жесткое крепление с использованием гибкой диафрагмы и ограничительного кольца
- Рисунок 8. Жесткое крепление с использованием узлового крепления корпуса
- Рисунок 9. Микросвязывание (обычно > 60 кГц)
- Рисунок 10. Устройство для сварки швов с креплением на полюс
- Рисунок A1.
Размеры сменной металлической сварочной шайбы
- Рисунок A2. Размеры сменной металлической шайбы с припаянной износостойкой вставкой
- Рисунок 1.
- Столы
- Таблица 1. Сводная информация о характеристиках материалов инструмента (износ и адгезия)
- Таблица 2. Компоненты шовного сварочного аппарата с полярным креплением
Ультразвуковая сварка металлов представляет собой процесс соединения двух металлических деталей с применением ультразвуковых колебаний в режиме сдвига (скребка). Ультразвуковая вибрация вытесняет поверхностные оксиды и загрязняет границы раздела двух частей, тем самым обеспечивая плотный контакт металла с металлом, из которого происходит сварка. Температура сварки относительно низкая и не связана с плавлением.
Ультразвуковая сварка металлов больше всего подходит для более мягких металлов (алюминий, медь, латунь и т. д.), хотя можно также сваривать более твердые материалы (например, титан). Разнородные материалы (например, медь с алюминием) можно сваривать, если их твердость примерно одинакова. Ультразвуковая сварка металлов может использоваться с материалами с высокой электропроводностью, для которых контактная сварка не подходит.
На рис. 1 (Al‑Sarraf[1], стр. 9) показаны две основные конфигурации сварки металла — система клиновидного язычка и система бокового привода.
|
Система Wedge-reed
Система Wedge-reed была разработана Aeroprojects (патент Johnes[4] 2,946,119, 1960) и в настоящее время используется Sonobond Ultrasonics (преемником Aeroprojects). Привод этой системы состоит из горизонтально установленного преобразователя и клиновидного рупора; Рупор припаян к вертикально установленному резонансному язычку. Рупор изгибает язычок, который, в свою очередь, приводит в движение сменный приварной наконечник с конусной посадкой (рис. 2) на свободном конце язычка. Требуемое сварочное усилие прикладывается к массе, расположенной на противоположном конце берда.
В зависимости от применения система может быть оснащена двумя коллинеарными противоположными язычками, один из которых действует как наковальня. Они работают в противофазе, тем самым эффективно удваивая амплитуду сварки и доступную мощность.
Эта система работает с относительно большой силой и малой амплитудой.
|
Система бокового привода
После разработки системы Wedge-reed компания Aeroprojects разработала систему поперечного привода (патент Johnes[5] 3,209,447, 1965). Branson Ultrasonics позже разработала систему бокового привода с изгибно-резонансными опорными элементами в пучностях (патент Shoh[1] 3,752,380, 1973, рис. 3). Дальнейшие разработки и вариации этой системы (особенно в способах крепления) используются и сегодня.
|
Рупор может быть сплошным (обычно из закаленной стали, рис. 4) или может иметь сменный многолепестковый сварочный наконечник (патент Holze[1] 3 813 006; см. рис. 5 и Приложение A; см. установку). Ультразвуковой пакет часто устанавливается в какой-либо цилиндрической оболочке (например, полярное крепление на рисунке 6), которая позволяет вращаться вокруг оси пакета (полярной), так что многолепестковый наконечник может быть правильно ориентирован по отношению к заготовке. Из-за своей осевой симметрии эта компоновка также хорошо подходит для шовной сварки. (Примечание. Усилитель на рис. 6а показан в неправильной ориентации. Штифт должен быть обращен к датчику.)
Двойной привод
|
|
| ||||||||||
|
Сравнение систем
Качество сварки
Качество сварки определяется многими факторами (главным образом, в том числе управлением процессом с помощью источника питания, что выходит за рамки данного обсуждения). Одной из областей, в которой две системы несколько отличаются, является применение движения наконечника. В обеих системах наконечник применяет сдвигающие движения к заготовке. Однако, кроме того, наконечник Wedge-Reed также имеет некоторое колебательное движение из-за изгиба трости. Неизвестно, в какой степени это может повлиять (возможно, улучшить) на качество сварки.
Коллапс амплитуды?
Зажимное усилие
Согласно документации по продуктам Sonobond, «система Wedge-Reed отличается низкой амплитудой вибрации и высокой вибрационной силой, подходящей для сварки металлов». Для сравнения: «Система бокового привода характеризуется высокой амплитудой вибрации и низкой силой вибрации, подходящей для сварки пластмасс». «Из-за консольного подхода [боковой системы] сила зажима прикладывается на некотором расстоянии от сварного шва, что приводит к изгибающему моменту на муфте, который ограничивает статическую силу. приводная система не способна обеспечить приемлемые сварные швы для луженых или окисленных проводов и клемм».
Примечание — Система бокового привода характеризуется ориентацией рупора по отношению к свариваемой детали, а не методом поддержки рупора .
Системы поддержки поперечного привода
В патенте Shoh 3,752,380 (рис. 3) показана система поперечного привода, в которой рупор (16) со сварным наконечником (40) поддерживается между двумя вертикальными (резонансными при изгибе) элементами (30 и 32). В этой конструкции на наконечнике отсутствует изгибающий момент. Следовательно, допустимая сила зажима ограничена только прочностью опорных элементов. (Также см. – патент Джонса [5] 3,209,447, который решает ту же проблему; Патент Roberts[3] 6 078 125 обсуждается здесь.)
В системе бокового привода, в которой рупор является консольным (рис. 1, внизу; рис. 5), усилие зажима вызывает вертикальное и, возможно, горизонтальное отклонение сварочного наконечника. Из-за кантилевера вертикальное отклонение слегка наклонит сварочную поверхность наконечника по отношению к наковальне (как открывание ножниц). Величина отклонения и результирующего смещения будет зависеть от жесткости штабеля и опорной конструкции, а также от силы зажима.
Для многих применений (например, герметизация труб) это отклонение не вызовет проблем. Кроме того, если наконечник закруглен, это может не быть проблемой, поскольку наконечник по существу самоориентируется. Однако для некоторых применений, таких как сращивание проводов и заделка проводов, может потребоваться более тщательное выравнивание. Например, в патенте Патрикиоса [1] 8 113 258 говорится, что «положение сварочного наконечника должно поддерживаться в пределах 3 микрон (0,001 дюйма)» (столбец 1, строка 42). (Обратите внимание, что 3 микрона (3*10 -6 м) переводится как 0,0001 дюйма, а не 0,001 дюйма, поэтому указанное требование неясно. Тем не менее, любое требование является довольно жестким.)
Когда рупор является консольным, существуют методы уменьшения вертикального отклонения рупора.
- Используйте очень жесткую опору. Например, в патенте Патринкиоса [1] 5772100 (рис. 7) показана конструкция с воротником (102), который опирается на узел рупора через поверхность 108. Этот хомут удерживается неподвижно, так что поверхность 108 ограничивает вертикальное отклонение рупора.
Ошейник изолирован ультразвуком от рупора с помощью диафрагмы (100) в пучности рупора, аналогично диафрагме с полярным креплением в патенте Shoh [3] 3,9.55 740. (Интересно, что в патенте Partikios патент Shoh не упоминается как предшествующий уровень техники.) Подобно полярному креплению, эта конструкция не ограничивает поперечное (осевое) движение рупора. По сравнению с полярным креплением эта конструкция имеет три дополнительных преимущества:
- В полярной установке бустер должен быть настроен так, чтобы он соответствовал длине корпуса, или, в качестве альтернативы, корпус должен быть подогнан под существующую длину бустера. Поскольку в конструкции Patrikios задняя диафрагма не используется, длина бустера не ограничена. Таким образом, можно использовать любой готовый бустер.
- В полярной монтировке диаметр бустера ограничен внутренним диаметром корпуса. Так как дизайн Патрикиоса не имеют оболочку, окружающую ракету-носитель, ее диаметр не ограничен.
- Поскольку требуется только одна противоузловая диафрагма, усилитель может быть исключен, а стек может быть короче.
Это предполагает, что коэффициент усиления рупора достаточен для обеспечения требуемой амплитуды сварки, когда рупор приводится в действие непосредственно датчиком.
- С другой стороны, если эта конструкция соответствует рисунку 7 (т. е. любая поверхность за поверхностью 108 превышает диаметр 108), то рупор можно заменить, только полностью сняв кольцо с диафрагмы. Поскольку полярная монтировка не имеет воротника вокруг рупора, рупор можно легко заменить, и можно использовать рупор любого диаметра.
- В другом монтажном устройстве патент Патрикиоса[1] 8,113,258 (рис. 8) ограничивает как поперечное, так и боковое отклонение сварочного наконечника. Оболочка (28) жестко устанавливается между двумя узлами (сужением 18а и 18b) на полноволновом рупоре (17). Это устраняет несколько гибкие диафрагмы полярного крепления и связанные с ними соединения, которые в противном случае способствуют податливости при изгибе.
- Используйте жесткий материал для звукового сигнала и/или усилителя.
Например, модуль Юнга для стали почти вдвое больше, чем для титана. Обратите внимание, однако, что сталь имеет потери при высоких амплитудах, поэтому это необходимо учитывать. Также можно использовать монель.
- Используйте жесткий материал для изолирующих диафрагм. Обычно используется титан, но его можно заменить сталью, если ее усталостная долговечность приемлема. (Первоначальные полярные диафрагмы были рассчитаны на пиковую амплитуду 10 микрон при частоте 20 кГц. Однако это было сделано без использования FEA для анализа напряжений (Culp[0]), поэтому коэффициент запаса неизвестен, но может быть большим.)
Вышеизложенное показывает, что возможно очень жесткое крепление сварочных аппаратов с боковым приводом. Следовательно, при надлежащей конструкции, ограничивающей прогибы, система бокового привода по своей природе не уступает системе клиновидного язычка в своей способности воспринимать высокое усилие зажима.
| ||||||||||
|
|
Примеры усилия зажима
Требуемое усилие зажима зависит от области применения. Ниже приведены некоторые избранные примеры.
Регулировка амплитуды сварочного наконечника
Система бокового привода позволяет использовать рупоры и усилители различного усиления. Это позволяет механически регулировать амплитуду сварочного наконечника с помощью этих компонентов (а не с помощью источника питания), чтобы при необходимости источник питания мог работать почти на полной мощности. Похоже, что Wedge-reed не допускает таких альтернативных конфигураций.
Сварочные поверхности обычно (но не обязательно) имеют насечки, чтобы «захватить» металлическую заготовку. Проблемы включают прилипание сварочных поверхностей к заготовке («прилипание») и износ зубцов. Эти проблемы могут быть смягчены в системе Wedge-Reed из-за ее меньшей амплитуды.
Установка
В большинстве систем поперечного привода используется сменный наконечник с шайбой (рис. 4) или рупор со встроенной свариваемой поверхностью (рис. 4), а не вертикально ориентированный наконечник (рис. 3, объект 40), который ввинчивается, запрессовывается , или аналогичным образом прилагается. Когда поверхность сварки в таких системах нуждается в очистке или замене (например, из-за прилипания или износа), новая поверхность сварки обычно изначально не параллельна поверхности заготовки. Если эта неправильная ориентация значительна, то весь ультразвуковой пакет необходимо повернуть вокруг своей оси, чтобы получить правильную ориентацию. (Для сменного наконечника шайбы эта проблема может быть уменьшена за счет использования приспособления для выравнивания во время установки. В качестве альтернативы, наконечник можно прикрепить к рогу — см. Патринкиос [2], патент 8,113,258.) Напротив, свариваемая поверхность клина- Наконечник язычка всегда ориентирован параллельно наковальне, поэтому при замене наконечника регулировка не требуется.
Сварочный наконечник с клинообразным язычком имеет охватываемый конус Морзе, который запрессован в ответный охватывающий конус в вертикальном язычке. (Конус Морзе является самоблокирующимся с внутренним углом приблизительно 3 °.) Таким образом, во время установки наконечник может вращаться вокруг своей оси, чтобы выровняться с гнездом наковальни. Это позволяет ориентировать приспособление в наилучшем положении по отношению к оператору или заготовке. Для системы бокового привода ориентация наконечника фиксирована по отношению к рупору, поэтому гнездовое крепление должно быть ориентировано по отношению к фиксированному наконечнику. Это может быть не оптимальной ориентацией крепления гнезда.
Доступность
Глубина горловины. Сварочный аппарат с клиновидным язычком имеет С-образный зажим между сварочным наконечником и наковальней. Глубина горловины этого С-образного хомута может быть сделана довольно большой (с учетом только соображений жесткости), чтобы можно было сваривать детали с большими поперечными размерами (например, листовые детали). Фактически, если бы сварочная головка и наковальня были установлены на отдельных тележках, размер заготовки был бы ограничен только длиной перемещения тележки. В системе бокового привода размер боковой части ограничен возможным вмешательством в рупор или опоры изоляции.
Досягаемость. Если сварка должна производиться внутри полости (например, на дне банки), то сварочный аппарат с клинообразным язычком имеет преимущество благодаря увеличенному радиусу действия. (Это предполагает, что поверхность сварки системы бокового привода не предназначена для вибрации при изгибе — например, в соответствии с микросклеиванием на рис. 9.) Теоретически радиус действия сварочного аппарата с клинообразным язычком можно увеличить, просто добавив дополнительные изгибные половинки. волны на тростник.
|
Техническое обслуживание и износ
Для системы поперечного привода, показанной на рис. 5, рупор обычно изготавливается из Ti-6Al-4V. При высоких нагрузках ультразвуковой сварки поверхность рупора, примыкающая к сварочному выступу наконечника, может испортиться. Компания Branson Ultrasonics решила эту проблему, заменив сплав Ti-6Al-4V на Ti-7Al-4Mo. Другим решением является замена титанового рупора на рупор из закаленной стали.
В качестве альтернативы в системе бокового привода может использоваться цельный стальной рупор со встроенной свариваемой поверхностью (см. рис. 4). Затем, однако, необходимо заменить весь рупор, когда поверхность сварки изнашивается и ее уже невозможно восстановить. Система Wedge-reed не имеет этих проблем, поскольку и наконечник, и язычок изготовлены из закаленной стали, а конусный наконечник можно легко заменить.
Адаптивность
С добавлением подшипников и контактных колец система бокового привода может быть преобразована в ротационный сварочный аппарат (рис. 10). Это невозможно с системой Wedge-reed.
Длина сварного шва.
Инструментальная оснастка
Инструментальные материалы
Хорошие инструментальные материалы должны обладать следующими характеристиками —
- Высокая износостойкость. Высокая износостойкость обычно характеризуется сочетанием высокой ударной вязкости и высокой твердости. Эти свойства должны сохраняться при повышенных температурах сварки.
- Неадгезивный. Инструменты не должны прилипать или прилипать к заготовкам. (Это может частично зависеть от конструкции рабочих поверхностей инструментов, например, зубцов.)
- Обоснованная потеря. Если инструмент наконечника является неотъемлемой частью рупора (рис.
4), то потери на рупоре должны быть разумными при амплитуде сварки. (См. потери стали.)
Обратите внимание, что производительность инструмента зависит как от материала инструмента, так и от его взаимодействия с материалом заготовки. Следовательно, инструмент, который хорошо работает с одним материалом заготовки, не обязательно будет хорошо работать с другим материалом заготовки (см. таблицу 1). Что касается твердости, Блосс [1] (стр. 96) обнаружил, что «отношение требуемой твердости инструмента к твердости сварочного материала четко не определено». Например, рассмотрим сварку заготовок из нержавеющей стали 304 (таблица 1) — кованый вольфрам (HV 356) имел «удовлетворительные» характеристики, тогда как M2 (HV 926; 2,6x твердость) имел «плохую» производительность.
В следующем разделе обсуждается несколько материалов, которые прошли оценку износа и адгезии для ультразвуковой оснастки. Этот список материалов не является исчерпывающим, поэтому могут быть доступны и другие (возможно, более качественные) материалы.
В таблице 1 приведены сводные данные об износе и адгезии для различных материалов инструментов, которые были исследованы Блоссом[1] (стр. 89).
| ||||||||||||||||||||||||||||||||||||||||||||||||||||||||||||||||
|
Примечания к таблице —
- Ссылки ниже взяты из Bloss[1], если не указано иное.
Дополнительную информацию смотрите там. Блосс отмечает: «Трудно сравнивать характеристики инструментов из-за разных материалов, которые они использовали для сварки, разных параметров сварки, использованных во время испытаний, и непостоянного количества циклов сварки, применяемых к каждому инструменту».
- HV = твердость по Виккерсу; см. таблицу Блосса 3, с. 46.
- Материалы, выделенные курсивом, показали себя перспективными или используются при сварке трением с перемешиванием (FSW), требования которой аналогичны ультразвуковой сварке металлов.
- AISI M2 (5% Mo, 6% W, 2% V) является наиболее часто используемым материалом для оснастки из-за его высокой твердости и хорошей износостойкости. Однако компонент ванадия в M2 легко образует соединения с алюминиевыми заготовками, способствуя прилипанию наконечника. Кроме того, при сварке современных материалов, таких как титан, инструменты M2 быстро изнашиваются и легко сцепляются с некоторыми
материалы. (стр.
28, 70) Упрочнен до 60-65 RC закалкой от 1200°С; не закаленный. (стр. 61) HV 926.
- 350M = мартенситностареющая сталь AISI марки 18Ni (18 % Ni, 12 % Co, 4,8 % Mo). Наконечники, изготовленные из стали 350M, имеют повышенный срок службы и износостойкость. свыше M2 при сварке AHSS (усовершенствованных высокопрочных сталей) и UHSS (сверхвысокопрочных сталей). (стр. 28) Он показал хорошие результаты при сварке технически чистого (CP) титана, но при работе с другими материалами заготовок возникали проблемы с залипанием наконечника. (стр. 71) Дисперсионное твердение при 500°C в течение 8-12 часов. (стр. 61) HV 778.
- Elkon 100W = слитки порошка чистого вольфрама, прессованные и спеченные путем прокатки и обжатия. (стр. 45) Прочность связи между частицами вольфрама была недостаточной. (стр. 76) HV 432.
- Wrought-W = чистый кованый вольфрам с повышенной прочностью и пластичностью по сравнению с Elkon 100W из-за повышенной деформации и механической обработки.
(стр. 45) Однако чистый вольфрам по-прежнему имеет плохую пластичность при комнатной температуре (стр. 27), поэтому были опробованы сплавы W-25Re и W-La. ХВ 356.
- W-25Re = вольфрам-25% рения. Улучшенная пластичность и прочность по сравнению с чистым вольфрамом. (стр. 27) Чрезвычайная прочность и коррозионная стойкость. (стр. 45) HV 509.
- W-La = запатентованный вольфрамово-лантановый сплав. По-видимому, он обладает улучшенной пластичностью благодаря легирующим элементам и усиленной ковке и штамповке. (стр. 86) HV 440.
- Вольфрам и его сплавы дороги и их трудно обрабатывать обычными способами. Кроме того, эти материалы имеют высокую плотность, поэтому полный наконечник был бы слишком тяжелым для работы в допустимом диапазоне частот ультразвукового сварочного оборудования. По этим причинам небольшие вставки из этих материалов припаивались к заготовкам сварочных наконечников М2. (стр. 59) Однако паяные соединения были проблематичными. (стр. 90) Вставки W-La изначально были припаяны паяльной фольгой Incusil ABA, но во время сварки паяные соединения разрушились.
Позднее вставки припаивались BNi‑9.(более высокотемпературный и высокопрочный припой), который оказался более удовлетворительным. (стр. 104)
Инструментальная сталь - T1 (не показана выше) была испытана, но ее характеристики были хуже, чем у инструментальной стали 350M. (стр. 28)
- Керамика имеет очень высокую твердость, но низкую ударную вязкость. (стр. 30)
Sonobond рекомендовал Udimet 700 компании Stittsworth[1] (стр. 12) для сварки «более твердых» материалов (по сравнению с алюминием и медью). Наковальня закалена до HRC 60–64 (стр. 30). (Примечание — это 1973 рекомендация может быть устаревшей.)
Прочная “керамическая” вставка Branson.
Образцы оснастки
Накатки. Блосс[1] (стр. 27) предлагает накатку (двунаправленную) примерно в ½ толщины материала для сварки усовершенствованных сплавов более толстой толщины. Концы получившихся мужских накаток (пирамид) сплющиваются. В нижней части накатки был добавлен небольшой радиус для улучшения
усталостные свойства. (стр. 71)
Лизеганг [1A] оценил пирамидальную накатку и однонаправленную накатку для вращательной шовной сварки титана. МКЭ напряжений накатки при сварке показало, что усредненные напряжения по Мизесу с однонаправленной накаткой в три раза выше, чем с пирамидальной накаткой. (стр. 11) Пирамидальная накатка на конце также обеспечивает более высокую прочность соединения сварных образцов. (стр. 15)
Текстуры. Блосс[1] (стр. 89) предполагает, что инструмент без наката может быть возможен в ситуациях, когда возможны высокие зажимные усилия (т. е. когда имеется достаточная мощность сварки, чтобы избежать остановки). Тогда износ можно было бы лучше контролировать, а наконечник можно было бы периодически полировать. Блосс также сообщает, что часто подходят наконечники в форме купола, где радиус купола должен в 50-100 раз превышать толщину образца.
Stittsworth[1] (стр. 12, 25) использовал электроэрозионную обработку (электроэрозионную обработку) для создания текстурированных поверхностей сварки (шероховатость 250 RMS). Полученные наконечники использовались в оборудовании Sonobond Wedge-Reed для сварки тонких (~ 0,13 мм) медных и алюминиевых полос и проволоки.
Механическая обработка
Некоторые инструментальные материалы трудно обрабатывать «обычными» средствами. Для этих материалов Блосс[1] использовал лазерную обработку, шлифовку и электроэрозионную обработку (электроразрядную обработку).
Амплитуда сварки
Блосс – 58 микрон
Шовная сварка, используемая здесь, определяется как сварка, при которой рог и заготовка перемещаются относительно друг друга для создания непрерывного или полунепрерывного сварного шва. В типичном устройстве весь ультразвуковой пакет вращается, поскольку цилиндрический диск или цилиндрический рупор выполняет сварку. Однако возможен и невращающийся рупор, особенно для сварки фольги. Оборудование может быть сконструировано таким образом, что рожок перемещается по заготовке, или заготовка может двигаться под стационарным рожком, подобно работе швейной машины. Шов может быть узким или широким.
Если ультразвуковой блок должен вращаться, можно адаптировать боковой привод, добавив подшипники и электрические токосъемные кольца (например, рис. 10). Wedge-reed не может быть адаптирован.
Примечание. Для шовной сварки биение поверхности сварки должно быть достаточно небольшим. Это несколько сложно в конструкции полярной установки на рисунке 10 из-за допусков наложения поверхностей раздела между рупором (52) и диафрагмой (39a), а также между диафрагмой (39a) и оболочкой (28). Более подходящей является конструкция, показанная на рисунке 8, в которой отсутствуют диафрагмы.
|
| ||||||||||||||||||
|
Если верхняя заготовка относительно тонкая (например, фольга), то поверхность сварки рупора может быть либо гладкой, либо иметь легкое травление или текстурный рисунок. Для более толстых заготовок может потребоваться более агрессивная поверхность свариваемой поверхности рога.
Рупоры
Если этот пакет предназначен для вращения, рупоры могут быть либо адаптациями обычных резонаторов, либо могут быть спроектированы так, чтобы вибрировать в каком-либо изгибном режиме.
См. также — Ультразвуковое аддитивное производство (УАМ).
В этом приложении показаны типичные размеры металлических сварочных наконечников с частотой 20 кГц для патента Holze[1] 3 813 006 на рис. 5 (от Bloss[1]). Рисунок накатки на наконечнике и форма сварочного выступа зависят от конкретного применения сварки.
|
|
Многообещающая технология для сварки пластмасс и металлов
Крепление, сшивание и склеивание — некоторые из популярных методов, которые мы используем для соединения двух материалов. Однако нельзя отрицать тот факт, что сварка дает наилучшие результаты.
Сварные швы обеспечивают прочное соединение, которое длится значительно дольше, чем большинство других форм соединений. В настоящее время используется множество способов сварки. Каждый тип отличается по-своему и используется в зависимости от требований и типа используемого материала.
Одним из самых современных методов сварки является ультразвуковая сварка.
СВЯЗАННЫЕ С: ПОДВОДНАЯ СВАРКА: ОДНА ИЗ САМЫХ ОПАСНЫХ ПРОФЕССИЙ В МИРЕ
Ультразвуковая сварка использует ультразвуковую вибрацию для соединения различных материалов. Одним из самых больших преимуществ ультразвуковой сварки является то, что ее можно использовать не только с металлами, но и с термопластами.
При воздействии ультразвуковой вибрации на точки контакта высокая вибрация вызывает плавление материала. Типичный частотный диапазон, используемый при ультразвуковой сварке, составляет от от 15 до 40 кГц .
Поскольку ультразвуковое сварочное оборудование может концентрировать вибрацию в очень ограниченном месте, сварка получается очень точной.
Детали ультразвуковой сварки
Ультразвуковые сварочные аппараты созданы для эффективного преобразования электроэнергии в механические колебания. Машины оснащены микропроцессором, который считывает температуру и соответствующим образом регулирует нагрев.
Некоторые другие компоненты, входящие в состав аппарата:
Источник питания: Аппарат для высокочастотной ультразвуковой сварки требует источника питания высокого напряжения.
Преобразователь: Преобразователь принимает ток высокого напряжения и преобразует его в высокочастотные колебания.
Усилитель: Работает как усилитель, захватывая высокие частоты и делая их еще более мощными.
Сонотрод или рожок: Сонотрод или рожок, как его обычно называют, является посредником между свариваемыми материалами и машиной. Он фокусирует ультразвуковые колебания в определенной точке.
Свариваемые материалы обычно закрепляют на наковальне или приспособлениях, удерживающих их вместе. К машине часто прикрепляют пневматический пресс, чтобы можно было передать давление на материалы с помощью рога.
Как ультразвуковая сварка расплавляет материалы?
Ультразвук используется при сварке для создания небольших, но быстрых вибраций. Когда рупор или сонотрод прикреплены к материалам, ультразвуковые колебания заставят материалы колебаться примерно на полмиллиметра или около того при движении вперед и назад.
Такого незначительного движения достаточно, чтобы расплавить материал, потому что скорость вибрации довольно высока. Эти вибрации заставляют материалы тереться друг о друга, и в результате трения между ними выделяется тепло.
Вы можете воспроизвести подобное окружение, быстро потирая руки. Вы почувствуете тепло, выделяющееся между ладонями.
Самое популярное
И если вы продолжите быстро тереть, становится довольно неудобно. Представьте себе тепло, выделяющееся внутри материалов, когда они трутся друг о друга со скоростью, которую трудно уловить человеческому глазу!
Трение повышает температуру до такой степени, что точки контакта между материалами плавятся, прокладывая путь для молекулярной связи. Вот как ультразвуковая сварка сваривает пластмассы.
Однако при сварке металлов есть небольшая разница. Ультразвуковая сварка используется для нагрева металла до одной трети его температуры плавления.
В этот момент молекулы двух металлов будут пересекать друг друга, создавая прочную молекулярную связь. В металлах нет плавления.
Преимущества ультразвуковой сварки
Ультразвуковая сварка имеет много преимуществ по сравнению с традиционными технологиями сварки. Многие отрасли промышленности используют ультразвуковую сварку из-за этих специфических комбинаций достоинств.
Не требует внешнего источника тепла: Основным преимуществом ультразвуковой сварки является отсутствие необходимости во внешнем источнике тепла. Тепло самогенерируется между материалами.
Быстрый: Поскольку частота вибрации очень высока, ультразвуковая сварка является одним из самых быстрых методов сварки, доступных в отрасли.
Возможность автоматизации: Ультразвуковая сварка несложна во многих отношениях, поэтому ее легко автоматизировать. Ультразвуковая машина оснащена датчиками, которые постоянно контролируют температуру.
Чистое и прочное соединение: Контактные поверхности плавятся/плавятся при сварке, что обеспечивает очень чистое и прочное соединение.
О чем следует помнить при использовании аппарата для ультразвуковой сварки
Ультразвуковая сварка очень эффективна при герметизации или сварке пластмасс. Однако, вы не можете сваривать все виды пластика.
Как и металлы, пластмассы также бывают разных видов. И очень важно следить за тем, чтобы свариваемые пластмассы были химически совместимы.
Если попробовать сварить полиэтилен и полипропилен, они могут расплавиться, но химической связи не будет. Химическая связь важна для создания прочных сварных соединений.
Еще один фактор, о котором следует помнить при сварке любого материала с помощью ультразвуковой сварки, — поддержание однородной площади контакта. При сварке металлов ультразвуковые колебания распространяются параллельно плоскости.
Недостатки ультразвуковой сварки
Как и все процессы соединения, ультразвуковая сварка также имеет некоторые недостатки, которые могут повлиять или не повлиять на вас в зависимости от вашего варианта использования. Однако вы должны понимать их.
Ограничено только соединениями внахлестку: Ультразвуковая сварка может использоваться только для сварки соединений внахлестку. Ее нельзя использовать для других типов соединений, так как для этого потребуются специально разработанный рупор и приспособления, и опять же, успех не гарантировано.
Ограниченная область сварки: Мы обсудили, как ультразвуковая сварка создает высоко локализованные сварные швы. Следовательно, вы не можете ожидать, что сварка обеспечит более крупные швы, чем площадь 250×250 мм 2 .
Невозможно сваривать толстые и твердые металлы: Толстые и твердые металлы не вибрируют так сильно, как тонкие и мягкие. Это предохраняет их от механических колебаний.
Ультразвуковая сварка используется в самых разных областях. Один из лучших примеров его использования — спортивная обувь. Соединения, которые вы видите в верхних частях, выполнены не сшиванием, а ультразвуковой сваркой.
Ультразвуковая сварка обеспечивает гораздо лучшую отделку, чем сшивание или склеивание.
СВЯЗАННЫЕ: МОЩНЫЙ АЛЮМИНИЕВЫЙ СПЛАВ ТЕПЕРЬ ПОДХОДИТ ДЛЯ СВАРКИ БЛАГОДАРЯ НАНОТЕХНОЛОГИИ
Ультразвуковая сварка термопластов широко используется в медицинской промышленности, автомобилестроении и производстве бытовой техники. Поскольку для надежного соединения не требуются дополнительные материалы, ультразвуковая сварка не увеличивает общий вес готового изделия.
Ультразвуковая сварка — это технология, появившаяся в 1940-х годах, но она по-прежнему используется для создания чистых и прочных соединений между различными материалами. Разработки в области ультразвуковой сварки все еще ведутся, чтобы увеличить масштабы ее использования.
Еще новости
инновации
Видео показывает, как дрон спасает тонущего мальчика из опасного моря
Крис Янг| 06.07.2022
наука
Молекулярная терапия, эффективная против болезни Паркинсона у крыс, также безопасна для человека
Rupendra Brahambhatt| 09.06.2022
здоровье
Лаборатория Джеффа Безоса наняла нобелевского лауреата ведущих ученых, чтобы победить смерть
Амейя Палеха| 21.01.2022
Технология ультразвуковой сварки металлов соединяет цветные металлы
Автор Joe Stacy
Национальный менеджер по продажам ультразвуковой сварки металлов
Emerson Automation Solutions
Вот уже почти 30 лет ультразвуковая сварка металлов предлагает производителям уникальное надежное решение для соединения различных мягких проводящих цветных металлов. от меди, алюминия и никеля до лития, латуни, серебра и золота. Этот процесс особенно полезен для соединения разнородных комбинаций материалов в приложениях, в которых используются батареи, устройства накопления энергии, жгуты проводов и сборки, электрические выключатели и выключатели, бытовая электроника и сотовые телефоны, а также имплантируемые медицинские устройства.
В отличие от сварки сопротивлением и лазерной сварки, ультразвуковая сварка металлов соединяет металлы, не расплавляя их, поэтому в процессе не образуются интерметаллические соединения или частицы и не возникает коррозия. Этот низкоэнергетический твердотельный процесс соединяет металлы в нескольких конфигурациях, включая тонкую фольгу или листы, многожильные провода и шины (толщиной до 2 мм), создавая соединения с высокой электропроводностью для максимальной электрической эффективности.
Преобразование электрической энергии в энергию ультразвуковой сварки
Одним из наиболее важных применений технологии является транспорт, где почти все аккумуляторы, используемые в электромобилях, используют ультразвуковую сварку металлов для соединения их самых маленьких и основных компонентов. К ним относятся тонкие пленки из никеля, меди и сплавов, используемые в анодах, и алюминиевая фольга, обычно используемая в катодах, а также анодные и катодные выступы, которые связывают воедино их генерирующие энергию химические вещества.
Вариант процесса, ультразвуковое сращивание металлов, обеспечивает целостность жгутов проводов и концевых заделок, необходимых для подачи электроэнергии, входов датчиков или управляющих сигналов во множестве других приложений по всему миру.
Ультразвуковая сварка металлов в процессе работы
Как показано на приведенной выше схеме Преобразование энергии в энергию ультразвуковой сварки , источник питания берет стандартное напряжение электрической сети (обычно 50 или 60 Гц) и преобразует его в частоту требуется для сварки металлов (40 кГц для более мелких или более тонких деталей и 20 кГц для более крупных и толстых деталей).
Электрическая энергия передается по радиочастотному кабелю на преобразователь. В преобразователе используется пьезоэлектрическая керамика для преобразования электрической энергии в механические колебания на рабочей частоте источника питания. Эти колебания либо увеличиваются, либо уменьшаются в зависимости от конфигурации бустера и рупора. Надлежащая степень колебаний, известная как амплитуда, обычно определяется инженером по применению. Точный контроль амплитуды необходим для воспроизводимой сварки металлов.
Склеивание осуществляется с помощью высокочастотной вибрации металлов, которые находятся под давлением и приводятся в действие приводом. Нижняя металлическая часть удерживается неподвижно в инструменте, называемом наковальней, а верхняя часть прижимается к ней, подвергаясь движению колеблющегося рупора или «сонотрода». Сонотрод проходит горизонтально от источника питания сварочного аппарата и является источником ультразвуковой энергии, которая создает соединение металл-металл.
Ультразвуковое сращивание металлов металлургически соединяет многожильные цветные провода с помощью вибрационного движения и давления.
Когда начинается процесс сварки, верхняя часть колеблется рогом, создавая силу сдвига, которая «счищает» окисление поверхности и загрязнения и создает гладкий контакт металла с металлом.
По мере продолжения колебаний металлические поверхности нагреваются, пластифицируются и смешиваются на границе раздела — и связываются на молекулярном уровне. В результате получается сплошной шов с мелкозернистой структурой, аналогичной структуре нагартованных металлов.
Весь процесс очень быстрый, сварка обычно занимает доли секунды.
Несколько методов контроля
В дополнение к способности соединять цветные металлы без их расплавления или повреждения, ультразвуковая сварка металлов предлагает несколько методов контроля, которые могут решить несколько производственных задач.
Наиболее важными из этих режимов управления являются:
• Регулирование энергии сварки, которое позволяет выполнять сварку в течение фиксированного периода времени (режим времени), до определенной конечной высоты сварного шва (режим высоты) или до фиксированного уровня энерговклад (энергетический режим). В энергетическом режиме ультразвуковой сварочный аппарат автоматически компенсирует, изменяя продолжительность сварки, чтобы адаптироваться к обычно возникающим различиям в состоянии поверхности (например, степени окисления и загрязнения) соединяемых металлов.
• Регулятор амплитуды сварки, который регулирует длину колебаний (амплитуду), подаваемых в зону сварки каждого соединения, и использует возможности источника питания сварки, преобразователя, сонотрода и узла рупора.
• Регулятор прижимной силы сварки регулирует давление, прикладываемое к свариваемому соединению. Достижения в области автоматизации управления прижимной силой работают в обоих направлениях, позволяя применять большее и меньшее давление с исключительной точностью.
Ультразвуковая сварка позволяет соединить 100 или более слоев тонкой медной или алюминиевой фольги, упрощая сборку многослойных аккумуляторов с высокой плотностью энергии, используемых в новейших электромобилях.
Одним из примеров является Branson GSX, ультразвуковой сварочный аппарат от Emerson, который включает в себя новую «легкую» электромеханическую приводную систему, которая измеряет прижимную силу с такой точностью, что может многократно инициировать ультразвуковую сварку с незначительной прижимной силой, необходимой для более старого оборудования.
Еще один новый метод ультразвуковой сварки, разработанный в Лаборатории прикладных программ Emerson, использует более высокое давление срабатывания для уложенных друг на друга металлических пленок, что позволяет создавать прочный сварной шов более «щадяще», используя меньшую общую амплитуду сварки.
Ультразвуковая сварка и соединение металлов: преимущества процесса
• Работает с широким спектром цветных металлов
• Создает прочную металлургическую связь между разнородными металлами
• Не требует плавления — нет никаких изменений в химическом или металлургия материалов
• Соединение высокопроводящих сплавов — химическая активность материалов не имеет значения
• Не образует интерметаллических соединений, твердых частиц или реакций, вызывающих коррозию
• Склеивает тонкие, хрупкие металлические пленки и конструкции
• Предлагает несколько методов управления, позволяющих настраивать процесс, повторяемость и SPC
• Обеспечивает низкое энергопотребление (до 30 раз ниже, чем при сварке плавлением или контактной сваркой) и не требует расходных материалов
• Предлагает самую низкую общую стоимость за шов любой технологии сварки
Ультразвуковая сварка металлов | Бельгийский институт сварки NPO
Ультразвуковая сварка — это сварочный процесс, в котором используется высокочастотная энергия вибрации. Это процесс сварки в твердом состоянии, что означает, что свариваемые материалы не расплавляются, а переводятся в пластичное состояние для их соединения. Процесс был разработан в 1960-х годов и в основном используется для пластмасс, но есть и очень интересные применения для металлов.
Принцип работы
Детали удерживаются вместе за счет относительно небольшой статической силы. Наконечник сонотрода находится в непосредственном контакте с одной из свариваемых деталей. Другая заготовка крепится к наковальне так, чтобы она не могла двигаться во время сварки.
Ультразвуковые колебания
Система посылает небольшие линейные циклические движения на кончик сонотрода (рис. 1), так называемые ультразвуковые колебания. Эти вибрации гарантируют, что зубчатый рисунок сонотрода вдавливается в верхнюю заготовку, позволяя эффективно передавать ультразвуковую энергию на поверхность сварки. В результате сонотрод и верхняя деталь будут вибрировать с одинаковой фазой и амплитудой. Эти вибрации создают тепло трения между свариваемыми материалами. Это гарантирует, что материалы станут пластичными, что позволит верхнему компоненту легко соединиться с нижним компонентом. По этой причине соединение создается в точке зацепления кончика сонотрода.
Для металлов процесс обычно состоит из 2 фаз: во-первых, с металлических поверхностей удаляются оксидные слои, так что между металлическими частями получается прямой контакт, затем атомы могут связываться в области контакта. Ультразвуковая сварка может выполняться на самых разных металлах и пластмассах, включая комбинации разнородных металлов или материалы с покрытием (см. рис. 2).
Рисунок 1: Принцип работы ультразвуковой сварки (Источник: Alpha bvba) | Рисунок 2: Ультразвуковая сварка меди с медью с серебряным покрытием (Источник: Alpha bvba) |
Metals
Many metals can be joined by ultrasonic welding. Возможные комбинации материалов показаны в таблице свариваемости (см. рис. 3). Материалы не должны быть слишком толстыми, а ультразвуковая сварка лучше всего подходит для мягких металлов, таких как цветные материалы и их сплавы, или материалов, покрытых медью, золотом, серебром или никелем.
Рисунок 3: Комбинации материалов, свариваемых ультразвуковой сваркой (Источник: Alpha bvba) | Рисунок 4: Ультразвуковая сварка электронных устройств: медь с медью с золотым покрытием (Источник: Alpha bvba) |
Сварочное оборудование
Ультразвуковой сварочный аппарат состоит из следующих компонентов:
- пресс удерживает обе части вместе с определенным усилием во время сварки.
- наковальня, на которую помещаются компоненты. Форма наковальни такова, что вибрации доводятся до места сварки.
- источник вибрации состоит из пьезоэлектрического преобразователя, усилителя и сонотрода. Sonotride передает вибрации на заготовку (рис. 5).
- источник переменного тока высокой частоты. Частота соответствует частоте сварки; 20, 30, 35 или 40 кГц.
- система для позиционирования или подачи деталей.
Рис. 5: Сонотрод для ультразвуковой сварки (Источник: Belgisch Instituut voor Lastechniek)
По умолчанию процесс выполняется продольно. Трение линейное. Существуют и другие варианты процесса, в которых трение применяется аксиально или радиально. В этом случае возможна сварка с меньшими вибрациями или с очень высокой мощностью в центральной точке.
Рис. 6: Продольная и торсионная ультразвуковая сварка (Источник: Alpha bvba)

Рисунок 7: Ультразвуковая сварка меди с алюминиевой фольгой (Источник: Alpha bvba)
Ограничения :
- Только для мягких металлов.
- Защита органов слуха в мастерской обязательна. Используемые частоты выше воспринимаемых человеком частот. Однако могут возникать случайные субгармонические колебания, вызывающие неприятный звук. При сварке в диапазоне от 15 до 20 кГц (все еще слышно) возможно повреждение слуха.
- Сварной шов имеет типичный вид с ребрами из-за трения и вдавливания.
- Только для соединений внахлест.
- толщина свариваемого шва зависит от материала. Однако можно сваривать тонкие материалы с толстыми (см. рис. 8).
Области применения
Ультразвуковая сварка уже имеет множество применений; в упаковочной промышленности, электронике, автомобильной, медицинской или аэрокосмической промышленности. Примерами применения являются медно-никелевые соединения для аккумуляторов, кабелей, сборных шин или соединителей. Интересным применением является сварка взрывоопасных или горючих продуктов, когда продукт уже находится в упаковке.
Рисунок 8: Ультразвуковая сварка 50 мм2 алюминия и меди (Источник: Alpha bvba) |
Рисунок 9: Ультразвуковая сварка алюминиевой крышки аккумуляторного отсека с медным проводником (Источник: Telso nic) |
Рис. 10: Ультразвуковая сварка медных кабелей (Источник: Alpha bvba) и уплотнение кабеля (Источник: Telsonic)
Разнородные материалы
Процесс также подходит для соединения разнородных материалов, напр. сварка алюминия с медью, алюминия со сталью или пластика с металлом. Технология ультразвуковой сварки также используется для сварки пластмасс, очистки, резки/штамповки или просеивания.
Рисунок 11: Приварка медной фольги (30 мкм) к никелированной медной шине для аккумуляторного элемента (Источник: Alpha bvba)
Подробнее
- Электромагнитно-импульсная сварка и опрессовка
- Точечная сварка трением
- Сварка трением
- Сварка трением с перемешиванием
- Сварка FRIEX
- Электронно-лучевая сварка 70 90 90 909
Ультразвуковая сварка | Металлургия для чайников
Ультразвуковая сварка — это самый быстрый и экономичный метод, используемый сегодня для соединения и сборки пластиковых деталей и цветных металлов. Ультразвуковая сварка является экономичной и экологичной технологией. Ультразвуковая сварка устраняет необходимость использования крепежа, клея и/или растворителей.
Ультразвуковой сварочный аппарат
Ультразвуковая сварка может использоваться для соединения всех жестких термопластов, синтетических тканей и пленок.
При ультразвуковой сварке используется акустический инструмент, называемый ультразвуковым рупором, изготовленный в соответствии с конструкцией ваших деталей. Ультразвуковая сварка преобразуется в тепло посредством трения, которое плавит пластик или металл.
Основными компонентами системы ультразвуковой сварки являются привод и источник питания, преобразователь/усилитель и ультразвуковой рупор, называемый блоком, часть, удерживающая сварочное приспособление/оправку. Выбор материала, поверхностный контакт, область сварки, конструкция соединения и амплитуда сварки — все это факторы, определяющие правильную конструкцию усилителя и рупора для любого конкретного применения.
Базовая конструкция пневматической ультразвуковой сварочной машины
Ультразвуковая сварка — это промышленный метод, при котором высокочастотные ультразвуковые акустические колебания локально воздействуют на заготовки, удерживаемые вместе под давлением, для создания твердотельного сварного шва. При ультразвуковой сварке нет соединительных болтов, гвоздей, материалов для пайки или клея, необходимых для соединения материалов вместе.
Ультразвуковая сварка — это промышленный метод, при котором два куска пластика или металла бесшовно соединяются друг с другом посредством высокочастотных акустических колебаний. Один свариваемый компонент помещается на неподвижную наковальню, а второй компонент помещается сверху. Акустическая энергия преобразуется в тепловую за счет трения, а детали свариваются менее чем за секунду.
Ультразвуковая сварка уникальна тем, что для соединения двух деталей не требуются соединительные болты, гвозди, материалы для пайки или клей. Поскольку ультразвуковая сварка — это в значительной степени автоматизированный процесс, все, что нужно сделать техническому специалисту, — это потянуть за рычаг, и сварка будет завершена. Недостатком ультразвуковой сварки является то, что она применима только к небольшим компонентам — часам, кассетам, пластиковым изделиям, игрушкам, медицинским инструментам и упаковке. Шасси автомобиля, например, не может быть собрано с помощью ультразвуковой сварки, потому что энергия, необходимая для сварки более крупных компонентов, будет непомерно высокой.
Для соединения сложных деталей из термопластов, отлитых под давлением, оборудование для ультразвуковой сварки можно легко настроить в соответствии с точными характеристиками свариваемых деталей.
(Примечание: при ультразвуковой сварке термопластов обычно используются частоты 15 кГц, 20 кГц, 30 кГц, 35 кГц, 40 кГц и 70 кГц). При сварке пластмасс интерфейс двух частей специально разработан для концентрации процесса плавления.
Ультразвуковая энергия расплавляет точечный контакт между деталями, создавая соединение. Ультразвук также может использоваться для сварки металлов, но обычно ограничивается небольшими сварными швами тонких, ковких металлов, например. алюминий, медь, никель. Ультразвук не будет использоваться при сварке шасси автомобиля или при сварке частей велосипеда из-за требуемых уровней мощности. Ультразвуковая сварка термопластов вызывает локальное плавление пластика за счет поглощения энергии вибрации. Вибрация передается поперек свариваемого соединения.
В металлах ультразвуковая сварка происходит из-за диспергирования поверхностных оксидов под высоким давлением и локального движения материалов. Вибрации привносятся вдоль свариваемого стыка.
Практическое применение ультразвуковой сварки жестких пластиков было завершено в 1960-х годах. На этом этапе можно было сваривать только твердые пластмассы. Патент на ультразвуковой метод сварки жестких термопластичных деталей был выдан Роберту Солоффу и Сеймуру Линсли в 1965 году. Солофф, основатель Sonics & Materials Inc., был руководителем лаборатории Branson Instruments, где из тонких пластиковых пленок сваривались пакеты и трубы. с помощью ультразвуковых датчиков. Первый автомобиль, полностью сделанный из пластика, был собран с помощью ультразвуковой сварки в 1969. Несмотря на то, что пластиковые автомобили не прижились, ультразвуковая сварка прижилась. Ультразвуковая сварка может использоваться как для твердых, так и для мягких пластиков, таких как полукристаллические пластики и металлы.
Ультразвуковые сварочные аппараты теперь также имеют гораздо большую мощность. Понимание ультразвуковой сварки расширилось благодаря исследованиям и испытаниям. Ультразвуковая сварка продолжает оставаться быстро развивающейся областью.
Преимущество ультразвуковой сварки заключается в том, что она намного быстрее, чем обычные клеи или растворители. Сварку можно легко автоматизировать, получая чистые и точные соединения; место сварки очень чистое и редко требует какой-либо подкраски.
Ультразвуковая сварка широко применяется во многих отраслях промышленности, включая электротехническую и компьютерную, автомобильную и аэрокосмическую, медицинскую и упаковочную. Ультразвуковая сварка является очень популярным методом соединения термопластов. Этот тип сварки часто используется для создания сборок, которые слишком малы, слишком сложны или слишком деликатны для более распространенных методов сварки.
В электротехнической и компьютерной промышленности ультразвуковая сварка часто используется для соединения проводных соединений и создания соединений в небольших, чувствительных цепях.
Соединения жгутов проводов часто соединяют с помощью ультразвуковой сварки. Электродвигатели, катушки возбуждения, трансформаторы и конденсаторы также могут быть собраны с помощью ультразвуковой сварки. Было обнаружено, что ультразвуковая сварка компьютерных дисков имеет время цикла менее 300 мс.
Полупроводниковые приборы, транзисторы и диоды часто соединяют тонкими алюминиевыми и золотыми проводами с помощью ультразвуковой сварки. Одним из различий между ультразвуковой сваркой и традиционной сваркой является способность ультразвуковой сварки соединять разнородные материалы. При создании компонентов аккумуляторов и топливных элементов тонкие медные, никелевые и алюминиевые соединения, слои фольги и металлические сетки часто свариваются вместе ультразвуковой сваркой.
В автомобилях ультразвуковая сварка, как правило, используется для сборки крупных пластиковых и электрических компонентов, таких как приборные панели, панели дверей гаража, лампы, воздуховоды, рулевые колеса, обивка и компоненты двигателя.
Некоторыми из преимуществ ультразвуковой сварки являются короткое время цикла, автоматизация, низкие капитальные затраты и гибкость. Кроме того, ультразвуковая сварка не повреждает отделку поверхности, что является важным фактором для многих производителей автомобилей, поскольку высокочастотные вибрации предотвращают образование следов.
Ультразвуковая сварка обычно используется в аэрокосмической промышленности при соединении тонколистового металла и других легких материалов. Алюминий трудно сваривается традиционными методами из-за его высокой теплопроводности. Тем не менее, это один из самых простых материалов для сварки с использованием ультразвуковой сварки, потому что это более мягкий легированный металл, и, следовательно, легко получить сварку в твердом состоянии. Многие предметы повседневного обихода создаются или упаковываются с использованием методов ультразвуковой сварки. Ультразвуковая сварка также применяется при упаковке опасных материалов, таких как взрывчатые вещества, фейерверки и другие химически активные вещества.
В пищевой промышленности ультразвуковая сварка предпочтительнее традиционных методов соединения, поскольку она является быстрой, гигиеничной и позволяет создавать герметичные швы. Контейнеры для молока и сока являются примерами некоторых продуктов, которые часто герметизируются с помощью ультразвуковой сварки.
Склеиваемые бумажные детали покрываются пластиком, обычно полипропиленом или полиэтиленом, а затем свариваются вместе для создания воздухонепроницаемого уплотнения. Например, если происходит избыточная сварка, концентрация пластика в зоне сварки может быть слишком низкой, что может привести к разрыву шва. Если он недоварен, уплотнение будет неполным. Различия в толщине материалов могут привести к изменению качества сварки. Некоторые другие продукты питания, которые запечатываются с помощью ультразвуковой сварки, включают обертки от шоколадных батончиков, упаковки для замороженных продуктов и контейнеры для напитков.
Вам также может понравиться
Что такое сварка пластмасс? Сварка пластика Определение Сварка пластмасс. ..
Как работает сварка трением? Что такое сварка трением? Сварка трением… Сварочные изображения Сварка – это процесс изготовления или скульптуры, который… Сварка Что такое сварка? Сварка – это изготовление… Ультразвуковая сварка магний-титановых разнородных металлов: исследование термомеханического анализа процесса сварки экспериментальным путем и методом конечных элементов | Китайский журнал машиностроения
- Исходная статья
- Открытый доступ
- Опубликовано:
- Dewang Zhao 1 ,
- Daxin Ren 2 ,
- Kunmin Zhao ,
- Pan Sun 4 ,
- XIK 1
Китайский журнал машиностроения том 32 , Номер статьи: 97 (2019) Процитировать эту статью
1751 Доступ
2 Цитаты
Сведения о показателях
Abstract
Ультразвуковая сварка представляет собой эффективный способ получения нереактивного/несмешивающегося гетерогенного соединения металлов, например соединения магниевого сплава и титанового сплава.
Но тепловой механизм ультразвуковой сварки магниевого сплава/титанового сплава четко не определен. В этой статье экспериментальный и конечно-элементный анализ были приняты для изучения теплового механизма во время сварки. В ходе испытаний определяется закон изменения температуры в процессе сварки и проверяется точность конечно-элементной модели. Микроскопический анализ показывает, что при времени сварки 0,5 с магниевый сплав в центре паяного соединения частично расплавляется и образует жидкую фазу. Посредством анализа методом конечных элементов коэффициент трения границы раздела ультразвуковой сварки магний-титан можно рассматривать как среднее постоянное значение 0,28. Максимальная температура на границе раздела может превышать 600 °C, чтобы достичь температуры плавления магниевого сплава. Пластическая деформация начинается через 0,35 с и происходит со стороны магния в центре границы раздела.
Введение
Ультразвуковая сварка металлов представляет собой особый метод соединения однородных или разнородных металлов с использованием энергии механических колебаний ультразвуковой частоты.
Под статическим давлением он преобразует энергию упругих колебаний в работу трения, энергию деформации и ограниченное повышение температуры между границами раздела заготовки, чтобы мгновенно активировать атомы в зоне сварки заготовки и обеспечить взаимное проникновение молекул на границы раздела двух фаз, что в конечном итоге обеспечивает прочное соединение сварного соединения [1]. Ультразвуковая сварка широко используется во многих областях, таких как герметизация труб и соединение проводов [2,3,4]. Согласно предыдущим литературным данным можно увидеть, что механизм ультразвуковой сварки одинаковых и разнородных металлов был исследован с точки зрения анализа микроструктуры, анализа механических свойств, распределения температурного поля и распределения напряжений [5,6,7,8, 9,10]. Большинство исследований в области ультразвуковой сварки касалось микроструктуры и свойств при растяжении соединений, выполненных ультразвуковой точечной сваркой [11,12,13,14,15,16,17]. На сегодняшний день механизм ультразвуковой сварки четко не определен.
Причина в том, что процесс сварки чрезвычайно короткий, и многие важные законы механики, такие как тенденция течения материала, закон пластической деформации и распределение температурного поля, не могут быть получены существующими испытаниями [18, 19]. Поэтому численное моделирование стало важным средством исследования механизма ультразвуковой сварки. Чен Кункун провел термомеханический анализ, чтобы количественно изучить влияние ультразвуковой энергии на процесс сварки [20]. Вывод состоит в том, что эффект акустического смягчения значительно увеличивает структурную деформацию, что благоприятно влияет на образование швов. Между тем, тепловыделение как от работы трения, так и от пластической деформации слабо зависит от эффекта акустического смягчения. Кай и др. [21] использовали как Abaqus/Standard, так и Abaqus/Explicit для моделирования связанных механических и тепловых явлений. Результаты показывают, что комбинированная модель (стандартная/явная) может прогнозировать распределение энергии и температуры, связанное с процессом ультразвуковой сварки, а также искажения.
Ким и др. [22] представили модель ультразвуковой точечной сварки методом конечных элементов для имитации процесса сварки алюминиевого сплава. В модели наблюдалось влияние тепла, выделяемого трением, и сопровождающая его большая пластическая деформация. De Vries [23] и Elangovan et al. [24] рассчитали теплоту трения и теплоту пластической деформации по формуле производства тепла, а затем применили теплоту к модели конечных элементов в качестве граничных условий. Проанализировано распределение температур и их влияние на заготовки, сонотрод и наковальню.
Согласно предыдущей литературе можно увидеть, что было проведено множество исследований по моделированию процесса сварки мягких и твердых материалов, таких как алюминий-медь, алюминий-сталь и магний-сталь. Однако о моделировании процесса сварки разнородных металлов магний-титан сообщается редко. Существует много трудностей при соединении разнородных сплавов на основе Mg/Ti. Существуют серьезные различия между неблагородными металлами с точки зрения физических, химических и металлургических свойств.
В предыдущих исследованиях [12] ультразвуковая сварка проводилась на разнородных магниево-титановых сплавах для изучения влияния параметров сварки на прочность соединения. Искусственная нейронная сеть, оптимизированная генетическим алгоритмом, использовалась для создания аналитической модели. На основании продолжения полученных результатов в данной работе возобновляются работы по ультразвуковой сварке магния–титана. Путем экспериментального исследования получен закон изменения температуры при сварке и микроскопическое явление поперечного сечения соединения. Модель конечных элементов используется для создания модели термического анализа ультразвуковой сварки магния и титана. В сравнении с температурными испытаниями и микроанализом поперечного сечения соединения проверяется точность модели, определяется средний коэффициент трения при сварке, а также закон изменения полей температуры и пластической деформации при сварке. полученный с помощью анализа модели методом конечных элементов.
Эксперимент
В этом исследовании были выбраны лист из магниевого сплава AZ31 толщиной 1,0 мм и лист из титанового сплава Ti6Al4V толщиной 1,0 мм.
Образцы имеют длину 100 мм и ширину 25 мм. Наждачной бумагой полировали поверхности образцов перед сваркой. Сварку участка наконечника 10×10 мм 2 проводят при давлении прижима 0,3 МПа, мощности 2500 Вт, частоте 20 кГц, амплитуде 20 мкм и времени сварки от 0,3 с до 1,3 с. с (0,3, 0,5, 0,8, 1,0, 1,3).
В эксперименте по ультразвуковой сварке метод измерения температуры обычно использует инфракрасную камеру и термопару [20,21,22,23,24]. Преимущества инфракрасной камеры в удобстве и скорости. Но он может измерять только изменения температуры поверхности, а не изменения внутренней температуры. Термопары позволяют в режиме реального времени измерять изменения внутренней температуры. Однако при ультразвуковой сварке мягких материалов процесс сварки подвержен большой деформации материала. А это приводит к выходу из строя термопары. В этом эксперименте титановый сплав имеет более высокую твердость и плохо деформируется при сварке. Поэтому термопары используются для получения более точных изменений температуры в процессе сварки.
Рисунок 1Схематическая установка для измерения межфазных температур показана на рисунке 1. Отверстие диаметром 0,5 мм просверливается сбоку в образце Ti6Al4V как можно ближе к верхней поверхности, не проникая в нее. В отверстие вставляли термопару диаметром 0,5 мм. Межфазные поверхности свариваемых образцов затирали наждачной бумагой. Таким образом, можно было измерить температуру на 0,2 мм ниже границы раздела сварных швов, то есть в центре термопары. Фактическая межфазная температура должна быть выше измеренной. Микроструктуры и поверхности изломов суставов наблюдали с помощью оптического микроскопа (ОМ) и сканирующего электронного микроскопа (СЭМ).
a Mg/Ti ультразвуковая сварка; b Межфазное температурное испытание
Изображение с полным размером
Модель материала
Магниевый сплав AZ31 и титановый сплав Ti6Al4V, выбранные в этом эксперименте, являются обычными коммерческими материалами, и многие ученые изучали их механические и теплофизические параметры [25,26,27].
Таблица 1 Механические и теплофизические параметры материалов,28,29], как показано в таблице 1.
Полноразмерный стол
Ультразвуковая сварка под синергетическим эффектом высокочастотной вибрации и вертикального давления быстро выделяет большое количество тепла, и тепло влияет на распределение напряжений и деформацию материалов при генерации и теплопроводности. Этот процесс представляет собой типичную термомеханическую связь. Материалы производят широкий диапазон изменения температуры и пластической деформации. Следовательно, конститутивная модель материалов должна учитывать эти два момента. В этом исследовании модель JC [30] выбрана для моделирования определяющих отношений материалов. Динамическая конститутивная модель JC описывает напряжение течения как произведение трех функций, а именно: упрочнение при деформации, увеличение скорости деформации и термическое размягчение. То есть эта модель обладает вариацией температуры и высокой скоростью деформации.
Таким образом, модель JC применима к данному исследованию. Конкретные формы модели JC следующие: 9{*}} = \dot{\varepsilon }_{eq} /\dot{\varepsilon }_{0}\, где \(\dot{\varepsilon }_{eq}\) – скорость деформации в испытание, а \(\dot{\varepsilon}_{0}\) – эталонная скорость деформации; A , B , C , n и m — параметры материала, измеренные при эталонной температуре или ниже; T безразмерная температура, определяемая как:
$$T \equiv \left\{ {\begin{array}{*{20}l} {0,} \hfill \\ {\left( {t – t_{r} } \right)/\left( {t_{m} – t_{r} } \right),} \hfill \\ {1,} \hfill \\ \end{array} } \right. {\kern 1pt} {\kern 1pt} {\kern 1pt} {\kern 1pt} {\kern 1pt} {\kern 1pt} {\kern 1pt} {\kern 1pt} {\kern 1pt} {\kern 1pt} {\kern 1pt} \begin{array}{*{20}c} {\text{for}} \\ {\text{for}} \\ {\text{for}} \\ \end{array} { \kern 1pt} {\kern 1pt} {\kern 1pt} {\kern 1pt} {\kern 1pt} {\kern 1pt} {\kern 1pt} {\kern 1pt} {\kern 1pt} \begin{array}{ *{20}l} {t < t_{r},} \hfill \\ {t_{r} \le t \le t_{m},} \hfill \\ {t > t_{m},} \hfill \\ \end{массив}$$
(2)
где t – температура испытания, t m – температура плавления металлов, а t 1 r 915 – температура плавления ниже которого температурная зависимость выражения предела текучести отсутствует.
Таблица 2 Параметры в модели материала Джонсона-КукаВ этом исследовании эталонная температура установлена как комнатная температура, а именно 20 °C. Функция T , а также константы A (МПа), B (МПа), C , n и m определяются по соответствующей литературе [25,26,27,28,29] следующим образом (таблица 2).
Полноразмерная таблица
Модель конечных элементов
Процесс ультразвуковой сварки имитируется с помощью КЭ модели термомеханической связи. Модель интегрирована с коммерческим программным обеспечением Abaqus 6.16. Элемент C3D8RT выбран для моделирования деталей в термомеханическом сопряженном анализе. «C3D8RT» представляет собой трехлинейный элемент перемещения и температуры с 8 узлами, с уменьшенной точкой интегрирования и контролем песочных часов. «C» обозначает континуум, «3» — трилинейность, «D» — смещение, «R» — уменьшенное, «T» — температуру. Этот тип элемента подходит для работ по анализу термомеханического соединения, что является ситуацией USW.
Рисунок 2Численное моделирование в этом исследовании использует динамические и явные алгоритмы, а для дальнейшего повышения эффективности расчетов требуются большие вычислительные ресурсы и длительное время сварки. Эта симуляция упрощает сонотрод и фиксирует все степени свободы устройства в месте пайки, соответствующей базовой пластине. Сварка делится на два этапа; на первом этапе непосредственно воздействуют вертикальным давлением на поверхность паяного соединения, а на втором этапе производят периодическую вибрацию ультразвуковой частоты для имитации сварки на поверхности паяного соединения (рис. 2). Эффект этого упрощения заключается в том, что во время фактической сварки поверхность паяного соединения демонстрирует пластическую деформацию, которая согласуется с вдавливанием сонотрода, из-за присутствия сонотрода, а сонотрод проводит часть тепла. Однако основное внимание в данном исследовании уделяется термическому процессу и пластической деформации между контактными поверхностями, которые не оказывают существенного влияния на эволюцию границы.
Поэтому такое упрощение разумно. Размер модели КЭ соответствует эксперименту, как показано на рисунке 2. Сетки более плотные в области сосредоточения сварки, чтобы уменьшить эффект песочных часов и повысить точность вычислений. В частности, размер элемента составляет приблизительно 0,1 мм в направлении толщины, чтобы точно получить изменения температуры.
Схема FEM
Изображение в натуральную величину
Несколько источников тепла, в том числе тепло трения, возникающее на границе сварки, тепло, выделяемое пластической деформацией на границе сварки, и тепло, выделяемое пластиковым вдавливанием на контактной поверхности. между сварочной головкой и материалом существуют при ультразвуковой сварке. Среди них наиболее важным источником тепла является теплота трения, возникающая на поверхности сварки. Этот источник тепла соответствует модели кулоновского трения. При \(\text{|}\tau_{fric} \text{|} = \mu \cdot p\) на границе раздела наблюдается относительное скольжение; в \(\text{|}\tau_{fric} \text{|} \le \mu \cdot p\) интерфейс относительно статичен.
Когда интерфейсы проскальзывают, начинается трение интерфейсов. Уравнение теплопроводности выражается следующим образом:
$$q_{f} = \eta \cdot \mu \cdot v,$$
(3)
где \(\eta\) – доля тепловыделения при трении, \(\mu\) – коэффициент трения, а v – скорость скользящего движения.
В отличие от тепловыделения при трении, хотя тепло, выделяемое пластической деформацией на границе раздела, невелико, его нельзя игнорировать. Вертикальное давление в процессе ультразвуковой сварки обычно не вызывает пластической деформации границы раздела. Однако модуль упругости материалов снижается при постоянном повышении температуры сварки. В дополнение к акустическому размягчению материалов, вызванному вибрацией избыточной частоты, на границе сварки возникает значительная пластическая деформация. Уравнение теплопроводности выражается следующим образом: 9{pl}\) — скорость пластической деформации.
Уравнение нестационарного теплообмена для ультразвуковой сварки выглядит следующим образом [18]: {\ парциальное х} \ влево ( {к_ {х} \ гидроразрыва {\ парциальное Т} {\ парциальное т}} \ справа) + \ гидроразрыва {\ парциальное } {\ парциальное у} \ влево ( {к_ {у} \ frac{\partial T}{\partial t}} \right) + \frac{\partial }{\partial z}\left( {k_{z} \frac{\partial T}{\partial t}} \right ) + Q.
$$
(5)
где \(\rho_{p}\) — плотность материала. \(c_{p}\) – удельная теплоемкость материала. \(k_{x}\) – теплопроводность в x направление. \(k_{y}\) – теплопроводность в направлении y . \(k_{z}\) – теплопроводность в направлении z . T — температура. Q – количество выделяемого тепла.
В кинетическом анализе механическая реакция материала управляется дифференциальным уравнением движения. Формат конечных элементов:
$$\rho \ddot{u} + c\dot{u} + ku = f,$$
(6)
$$M\ddot{u} + C\dot {и} + К\точка{и} = F, $$
(7)
где \(\rho\) – масса материала. c — коэффициент демпфирования. k – коэффициент жесткости. f — объемная сила. M — матрица структурных масс. C — матрица структурного демпфирования. K — матрица структурной жесткости. F — вектор внешней приложенной нагрузки. \(\ddot{u}\) – узловые ускорения. \(\dot{u}\) – узловая скорость.
u — узловое смещение. 9{ – 1} (Q – \varLambda T),$$
(9)
где C – матрица сосредоточенных емкостей. \(\varLambda\) — матрица теплопередачи. Q — вектор, характеризующий источник тепла. T – температура в узле. \(\dot{T}\) – вектор скорости температуры. i — это номер приращения в явном динамическом шаге.
Формула контроля процесса сварки, включая частоту ультразвуковых колебаний и амплитуду колебаний сонотрода, следующая:
$$U = U_{\text{max} } \sin\left( {2 \uppi f \cdot t} \right),$$
(10)
где \(U_{\text{max } }\) — амплитуда вибрации (20 мкм), f — частота вибрации (20 кГц) и t — время сварки. Произведение давления в точке сварки на площадь точки сварки равно произведению давления в цилиндре на площадь сечения. Таким образом, давление в точке сварки составляет 40 МПа, а давление в баллоне равно 0,3 МПа.
Результаты и обсуждение
Анализ эксперимента
На рис.
Рисунок 33(а) показана диаграмма изменения температуры на границе раздела вблизи центра паяного соединения при разном времени пайки: 300, 500, 800, 1000 и 1300 мс. Максимальная температура в каждый момент сварки приходится на конец сварки (возникает небольшая задержка из-за задержки теплопроводности). Максимальные уровни температуры при 300, 500, 1000 и 1300 мс составляют 404,3 °C, 444,2 °C, 472,6 °C и 504,6 °C соответственно.
Измеренная температура внутри титанового сплава на 0,2 мм ниже границы раздела сварного шва
Полноразмерное изображение
Для дальнейшего наблюдения за тенденцией изменения температуры карта истории во времени увеличена и просматривается карта истории первых 1,5 с, как показано на рисунке 3(b). Судя по рисунку, наклон кривой велик до 0,4 с времени сварки, что указывает на быстрое повышение температуры; это повышение является основной фазой повышения температуры ультразвуковой сварки магния и титана.
Согласно следующему анализу методом конечных элементов величина пластической деформации материала на этом этапе невелика, а выделение тепла, вызванное пластической деформацией, минимально; таким образом, основным источником тепловыделения на данном этапе является тепловыделение от трения между границами раздела. Примечательно, что наклон кривой до 0,4 с действительно существенно меняется и приближается к линейности (наклон кривой начинает уменьшаться только примерно через 0,4 с). Этот результат свидетельствует о том, что коэффициент трения существенно не изменяется на основной фазе повышения температуры ультразвуковой сварки магний-титан. Более того, коэффициент трения можно считать средней постоянной величиной, несмотря на динамическое изменение. Когда время сварки приближается к 0,4 с, а температура сварки составляет примерно 430 °C, наклон температурной кривой начинает резко уменьшаться. Этот результат указывает на то, что вначале повышение температуры начинается постепенно и имеет устойчивую тенденцию из-за большого количества тепла, выделяемого предыдущим трением через 0,4 с.
Хотя температура плавления магниевого сплава в это время не достигается, материал размягчается под действием высокой температуры и ультразвуковой акустики. Когда материал размягчается, скорость тепловыделения при трении значительно снижается, а повышенная температура в основном вызвана тепловыделением пластической деформации. Для сравнения, предыдущие исследования ученых показывают, что, несмотря на то, что выделение тепла и пластическая деформация являются основным источником тепла во время ультразвуковой сварки, выделение тепла является основным источником тепла, тогда как пластическая деформация производит меньше тепла; таким образом, существует медленная или даже постоянная тенденция роста температуры.
Определение коэффициента трения и проверка температуры
Трение и износ играют важную роль при скольжении двух поверхностей при циклической нагрузке. В области трения и износа коэффициент трения является важной частью. Сиддик и др. [31] предложил закон трения, который состоит из статической и кинематической составляющих трения.
Рисунок 4Результаты показывают, что в реальных экспериментах работа трения только разрушает оксидный слой на границе сварного шва и рассеивает его вдоль и вблизи границы раздела. Гао и Думанидис [32] предложили коэффициент трения, зависящий от времени, с помощью метода расчета и метода конечных элементов. Результаты показывают, что коэффициент трения увеличивается почти линейно до определенного времени, затем остается неизменным, а затем со временем начинает уменьшаться. Хуанг и др. В работе [33] исследуется взаимосвязь между повышением температуры при ультразвуковой формовке и изменением коэффициента трения. В модели анализа методом конечных элементов использовался постоянный коэффициент трения, основанный на модели трения Кулона. Чтобы смоделировать экспериментальное поведение, коэффициент трения был уменьшен при воздействии на детали ультразвуковой вибрации. Предыдущие исследования установили уравнения изменения повышенного коэффициента трения для величины проскальзывания, контактного давления, количества циклов и температуры материала во время ультразвуковой сварки.
В экспериментальном анализе настоящей работы повышение температуры и стационарные фазы во время сварки приближаются к линейному тренду, коэффициент трения можно считать постоянным в соответствии с уравнением тепловыделения при трении. (8). Это исследование направлено на использование модели конечных элементов для настройки коэффициента трения, чтобы согласовать результаты моделирования с экспериментальными результатами, таким образом, получая коэффициент трения ультразвуковой сварки магний-титан. Также проверяется точность FEM. Результаты испытаний показывают, что на фазе повышения температуры от начала сварки почти до 0,4 с температура сварки составляет примерно 430 °С; через 0,4 с достигается стационарная фаза, а точкой измерения температуры является центральное положение паяного соединения, которое находится на расстоянии 0,2 мм от границы раздела. Тест согласован, и кривая температурной истории результатов анализа модели конечных элементов также выбирает ту же позицию. В соответствии с тестом кривая истории изменения температуры результатов анализа численной модели занимает такое же положение.
Коэффициент трения методом проб и ошибок очень сложно определить, поскольку присущие динамическим и явным алгоритмам характеристики требуют короткого времени и нескольких шагов, тогда как в этом исследовании время сварки увеличивается, а расчет каждого значения требует много времени. Наконец, значение коэффициента трения составляет 0,28. На рис. 4 показано сравнение между тестом и температурной историей FEM. Проверка температуры показывает, что результаты моделирования и испытаний хорошо согласуются, а максимальная ошибка не превышает 25 °C.
Сравнение между тестом и температурной историей МКЭ
Изображение в полный размер
На рисунке 5(a) показано поперечное сечение стыка гетерогенного металла магний-титан при 500 мс. На рис. 5(b)–(d) показана микроморфология интерфейса локальной части центра паяного соединения, края паяного соединения и несваренной части (красный квадрат на рис. 5(a) соответственно. . Область измельчения зерна в форме полосы находится на локальной границе раздела в центре паяного соединения (рис.
Рисунок 55(a)), а увеличенная структура локального измельчения зерна на границе раздела паяного соединения показана на рис. 6. На рисунках размер зерна магниевого сплава на границе раздела составляет 3–4 мкм, что значительно меньше по сравнению со средним размером зерна 30 мкм основного материала. Как правило, измельчение зерна вызывается жидким металлом при быстром охлаждении. Таким образом, локальный слой измельчения зерна на границе раздела свидетельствует о локальном расплавлении магниевого сплава на границе при сварке гетерогенного металла магний–титан, причем температура в этой точке превышает 600 °С, что достигает температуры плавления магнези эм сплав. По сравнению с поперечным сечением соединения температура в центре паяного соединения численного моделирования также превышает 600 °C, что достигает температуры плавления магниевого сплава; краевая температура паяного соединения 426–480 °С; а несварные детали хорошо согласуются с тестом, что еще раз подтверждает точность результатов численного моделирования.
Морфология поперечного сечения суставной поверхности: макро-вид ; б центр шва; c край сварного шва; d несварная зона
Полноразмерное изображение
Рис. 6Морфология локально измельченных зерен на границе раздела сварного шва с 2000 раз
Полноразмерное изображение
Анализ температурного поля
Рис.– (д) показывают распределение поля температуры вдоль Y – ось в центре паяного соединения при времени сварки 0,05, 0,1, 0,2, 0,4 и 0,6 с. Распределение температурного поля указывает на то, что температура во время сварки создается на границе контакта и передается в окружающую среду. На рис. 7(а) показано, что на начальном этапе сварки повышение температуры начинается на краю края паяного соединения из-за начальной деформации листа магния под действием вертикального давления, что приводит к концентрации напряжений на краю паяного соединения.
Рисунок 7. Контакт на краю плотный при вибрации; таким образом, повышение температуры начинается на краю паяного соединения. В процессе сварки тепло распространяется в окружающую среду, вызывая большую деформацию тепловой силы в центре паяного соединения. Таким образом, центральное положение паяного соединения становится все более плотным, и повышение температуры начинается от интерфейса центрального положения и распространяется на окружающую среду до конца сварки. Учитывая, что теплопроводность магниевого сплава выше, чем у титанового сплава, повышение температуры на стороне магниевого сплава происходит быстрее, чем у другого сплава. Когда время сварки достигает 0,1 с, максимальная температура на границе раздела превышает 289°С; при достижении времени сварки 0,2 с максимальная температура на границе раздела превышает 432 °С; когда время сварки достигает 0,4 с, максимальная температура на границе раздела превышает 548 °С и приближается к 600 °С, а температура продолжает переходить в окружающую среду; когда время сварки достигает 0,6 с, максимальная температура на границе раздела превышает 600 °С.
Примечательно, что в соответствии с результатами испытаний максимальная скорость роста температуры уменьшается, когда время сварки превышает 0,4 с, тогда как диапазон паяных соединений увеличивается при максимальной температуре. Это явление объясняется размягчением магниевого сплава при совместном воздействии высокой температуры и ультразвуковой энергии, а также передачей температуры в окружающую среду. Поэтому при вертикальном давлении в месте пайки существует прочная связь, а диапазон пайки при максимальной температуре непрерывно расширяется под совместным действием теплоты трения и пластической деформации.
Распределение температурного поля в различные моменты времени сварки
Изображение полного размера
Анализ пластической деформации
На рисунке 8 показана временная диаграмма диссипативной пластической энергии всей конструкции. При пластической деформации материала выделяется энергия в виде тепла, что является еще одним источником повышения температуры ультразвуковой сварки; таким образом, уровень рассеянной энергии представляет собой степень пластической деформации.
Рисунок 8На рис. 8 видно, что в первые 0,35 с вся сварная конструкция практически не деформируется пластически из-за ее линейно-упругого состояния; следовательно, тепло в первые 0,35 с происходит за счет тепловыделения при трении на границе раздела сред. Через 0,35 с генерируется пластическая диссипативная энергия, представляющая собой начало пластической деформации. С увеличением времени сварки наклон кривой пластической диссипативной энергии значительно увеличивается, что указывает на увеличение скорости пластической деформации, и степень пластической деформации всей конструкции начинает увеличиваться. Это открытие связано с комбинацией повышения температуры и эффекта ультразвукового смягчения; материал размягчается, и легко происходит пластическая деформация.
Пластическое рассеяние для всей модели
Изображение в полный размер
На рис. 9(a)–(d) показано распределение поля пластической деформации вдоль оси Y в центре паяного соединения в месте сварки.
Рисунок 9время 0,4, 0,5, 0,6 и 0,7 с. На рис. 9 видно, что пластическая деформация всей сварной конструкции в основном возникает на магниевом сплаве. На 0,4 с происходит определенная пластическая деформация преимущественно в центре соединения с небольшой степенью и протяженностью деформации; через 0,5 с область и степень пластической деформации на границе значительно расширяются и распространяются к вершине магниевой пластины; при 0,6 с размах и степень пластической деформации на границе раздела еще больше увеличиваются. Деформация вверх, видимая невооруженным глазом, происходит на краю магниевой пластины из-за деформации всей структуры паяного соединения, что связано с длительным временем сварки под синергетическим эффектом вертикального давления и вибрации ультразвуковой частоты. Эта деформация может существенно повлиять на усталостную характеристику соединения [34] и влияет на форму разрушения поверхности раздела при испытании на прочность на растяжение соединения [35]; при 0,7 с диапазон и степень пластической деформации на границе раздела еще больше расширяются, деформация коробления кромки сварной конструкции становится все более очевидной, а пластическое течение материала в стыке имеет тенденцию происходить в обе стороны при выдавливании вертикальное давление.
Таким образом, общая тенденция к пластической деформации возникает в центре паяного соединения и распространяется в обе стороны и вверх по мере увеличения времени пайки.
Распределение поля пластической деформации вдоль оси Y в центре паяного соединения
Изображение в натуральную величину
Выводы
термомеханический анализ ультразвуковой сварки магния и титана выполнен с использованием МКЭ. Получаются следующие выводы.
Во время сварки первые 0,4 с в основном связаны с фазой повышения температуры. На этой стадии температура быстро растет по линейному тренду. Через 0,4 с магниевый сплав размягчается за счет сочетания высокотемпературного и ультразвукового размягчения, что делает повышение температуры незначительным. Микроскопический анализ показывает, что при времени сварки 0,5 с магниевый сплав в центре паяного соединения частично расплавляется и образует жидкую фазу.
Коэффициент трения границы раздела ультразвуковой сварки магний–титан можно принять за среднее постоянное значение 0,28.
Максимальная температура на границе раздела может превышать 600 °C, чтобы достичь температуры плавления магниевого сплава. До 0,35 с пластическая деформация отсутствует. Затем через 0,35 с начинается пластическая деформация, которая происходит со стороны магния в центре границы раздела. Поскольку время сварки продолжает увеличиваться, диапазон пластической деформации и степень деформации значительно увеличиваются, распространяясь на обе стороны и верхнюю часть магниевой пластины.
Ссылки
H Li, H Choi, C Ma, et al. Измерение переходной температуры и теплового потока при ультразвуковом соединении выводов аккумуляторов с использованием тонкопленочных микродатчиков. Journal of Manufacturing Science and Engineering , 2013, 135(5): 051015.
Статья Google ученый
Л. Си, М. Бану, С. Джек Ху и др. Прогноз производительности для ультразвуковой сварки соединений разнородных материалов.
Журнал производственных наук и техники , 2017, 139(1): 011008.
С. Ли, Т. Хён Ким, С. Джек Ху и др. Анализ формирования шва при многослойной ультразвуковой сварке металлов с использованием высокоскоростных изображений. Journal of Manufacturing Science and Engineering , 2015, 137(3): 031016.
D Lee, E Kannatey-Asibu, W Cai. Моделирование ультразвуковой сварки нескольких слоев выводов литий-ионного аккумулятора. Journal of Manufacturing Science and Engineering , 2013, 135(6): 061011.
Артикул Google ученый
Х. С. Шин, М. де Леон. Параметрические исследования при аналогичной ультразвуковой точечной сварке листов сплава А5052-х42. Журнал технологии обработки материалов , 2015, 224: 222–232.
Артикул Google ученый
Ф.
Хаддади, Ф. Абу-Фарха. Влияние межфазной реакции на развитие вибрации и характеристики точечных ультразвуковых соединений алюминия со сталью высокой мощности. Материалы и дизайн , 2016, 89: 50–57.
Артикул Google ученый
В.К. Патель, С.Д. Бхоле, Д.Л. Чен. Магниевый сплав AZ31, сваренный ультразвуковой точечной сваркой: микроструктура, текстура и прочность на сдвиг внахлестку. Материаловедение и инженерия: A , 2013, 569: 78–85.
Артикул Google ученый
В.К. Патель, С.Д. Бхоле, Д.Л. Чен. Ультразвуковая точечная сварка алюминия с высокопрочной низколегированной сталью: микроструктура, прочностные и усталостные свойства. Metallurgical and Materials Transactions A , 2014, 45(4): 2055–2066.
Артикул Google ученый
В.
К. Патель, С.Д. Бхоле, Д.Л. Чен и др. Твердотельная ультразвуковая точечная сварка композитных листов SiCp/2009Al. Материалы и дизайн , 2015, 65: 489–495.
Артикул Google ученый
А. Пантели, Дж. Д. Робсон, И. Бро и др. Влияние высокоскоростной деформации на интерметаллидную реакцию при ультразвуковой сварке алюминия с магнием. Материаловедение и инженерия: A , 2012, 556: 31–42.
Артикул Google ученый
М. Шакил, Н. Х. Тарик, М. Ахмад и др. Влияние параметров ультразвуковой сварки на микроструктуру и механические свойства разнородных соединений. Материалы и дизайн , 2014, 55: 263–273.
Артикул Google ученый
Д. В. Чжао, К. М. Чжао, Д. Х. Рен и др. Ультразвуковая сварка разнородных металлов магний-титан: исследование влияния параметров сварки на механические свойства с помощью экспериментов и искусственной нейронной сети.
Journal of Manufacturing Science and Engineering , 2017, 139(3): 031019.
Статья Google ученый
Z L Ni, H J Zhao, P B Mi и др. Микроструктура и механические характеристики соединений Al/Cu, сваренных ультразвуковой точечной сваркой, с промежуточным слоем из частиц сплава Al 2219. Материалы и дизайн , 2016, 92: 779–786.
Артикул Google ученый
М. П. Сатпати, А. Кумар, С. К. Саху. Влияние латунного промежуточного листа на микроструктуру и рабочие характеристики соединений меди и стали, сваренных ультразвуковой точечной сваркой. Journal of Materials Engineering and Performance , 2017, 26(7): 3254–3262.
Артикул Google ученый
М. П. Сатпати, С. К. Саху. Механические характеристики и металлургическая характеристика ультразвуковой сварки разнородных соединений.
Журнал производственных процессов , 2017, 25: 443–451.
Артикул Google ученый
Д. Х. Рен, К. М. Чжао, М. Пан и др. Ультразвуковая точечная сварка магниевого сплава с титановым сплавом. Scripta Materialia , 2017, 126: 58–62.
Артикул Google ученый
Ф. А. Мирза, М. А. Акван, С. Д. Бхоле и др. Влияние энергии сварки на микроструктуру и прочность точечной ультразвуковой сварки разнородных соединений алюминия со стальными листами. Материаловедение и инженерия: A , 2016, 668: 73–85.
Артикул Google ученый
К.К. Чен, Ю.С. Чжан. Механический анализ ультразвуковой сварки с учетом наката на наконечнике сонотрода. Материалы и дизайн , 2015, 87: 393–404.
Артикул Google ученый
Чжан Чжан, Л.
Дж. Ли. Парный термомеханический анализ механизма ультразвуковой сварки. Metallurgical and Materials Transactions B , 2009, 40(2): 196–207.
Артикул Google ученый
К.К. Чен, Ю.С. Чжан, Х.З. Ван. Влияние акустического размягчения на термомеханический процесс ультразвуковой сварки. Ультразвук , 2017, 75: 9–21.
Артикул Google ученый
Д. Ли, Э. Каннати-Асибу, В. Кай. Моделирование ультразвуковой сварки нескольких тонких и разнородных металлов для соединения аккумуляторов. Д отдел динамических систем и управления. Международный симпозиум ASME/ISCIE 2012 по гибкой автоматизации , 18–20 июня 2012 г., Сент-Луис, штат Миссури, США, 2012 г.: 573–584.
В. Ким, А. Ардженто, А. Грима и др. Термомеханический анализ фрикционного нагрева при точечной ультразвуковой сварке алюминиевых пластин.
Труды Института инженеров-механиков, часть B: Journal of Engineering Manufacture , 2011, 225(7): 1093–1103.
Артикул Google ученый
Э де Вирес. Механика и механизм ультразвуковой сварки металлов . Университет штата Огайо, 2004 г.
С. Элангован, С. Семер, К. Пракасан. Распределение температуры и напряжения при ультразвуковой сварке металлов: исследование на основе МКЭ. Журнал технологии обработки материалов , 2009, 209(3): 1143–1150.
Артикул Google ученый
D Зонт. Конечно-элементное моделирование обычной и высокоскоростной обработки сплава Ti6Al4V. Журнал технологии обработки материалов , 2008, 196 (1-3): 79–87.
Артикул Google ученый
Ченьянг Се, Чжэнцян Чжу, Сяолун Ван.
Численное моделирование поля температуры и напряжений в процессе ультразвуковой сварки титанового сплава. Технология горячей обработки давлением , 2013, 42: 140–147.
Google ученый
F Feng, S Y Huang, Z H Meng, et al. Конструктивная модель и модель разрушения магниевого сплава АЗ31Б в растянутом состоянии. Материаловедение и инженерия: A , 2014, 594: 334–343.
Артикул Google ученый
Донг Цзя, Цзюнь Мо, Сичэн Хуан и др. О поведении при разрушении магниевого сплава МБ2, подвергнутого высоконапряженному трехосному растяжению. Журнал экспериментальной механики , 2016, 31 (1): 87–95. (на китайском)
Google ученый
Дун Цзя, Сичэн Хуанг и др. Разрушение магниевого сплава МБ2 при квазистатическом и динамическом растяжении на основе модели Джонсона-Кука.
Взрыв и ударные волны , 2017, 37: 1010–1016. (на китайском)
Google ученый
Г. Р. Джонсон, В. Х. Кук. Характеристики разрушения трех металлов при различных деформациях, скоростях деформаций, температурах и давлениях. Инженерная механика разрушения , 1985, 21(1): 31–48.
Артикул Google ученый
А. Сиддик, Э. Гассемия. Термомеханический анализ процесса ультразвуковой сварки с использованием эффектов термического и акустического смягчения. Механика материалов , 2008, 40(12): 982–1000.
Артикул Google ученый
Ю Гао, К. Думанидис. Механический анализ ультразвукового соединения для быстрого прототипирования. Journal of Manufacturing Science and Engineering , 2002, 124(2): 426.
Статья Google ученый
Ч.
Х. Хуан, М. Лукас, М. Дж. Адамс. Влияние ультразвука на осадку модельной пасты. Ультразвук , 2002, 40 (1–8): 43–48.
Артикул Google ученый
Д. В. Чжао. Влияние параметров сварки на растяжение и усталостные свойства ультразвуковой точечной сварки разнородных соединений листов магния с титаном. Journal of Machine Engineering , 2017, 53(24): 118. (на китайском языке)
Статья Google ученый
Д. В. Чжао, Д. Х. Рен, К. М. Чжао и др. Влияние параметров сварки на предел прочности при растяжении соединений алюминия со сталью, сваренных ультразвуковой точечной сваркой – экспериментально и с использованием искусственной нейронной сети. Журнал производственных процессов , 2017, 30: 63–74.
Артикул Google ученый
Ссылки на скачивание
Вклад авторов
DZ и KZ отвечали за все исследование; DZ и DR написали рукопись; PS помогал с экспериментами; XG помогала с FEM.
Все авторы прочитали и одобрили окончательный вариант рукописи.
Информация об авторах
Деванг Чжао, 1986 г.р., в настоящее время имеет докторскую степень в возрасте 9 лет.1612 Школа материаловедения и инженерии, Даляньский технологический университет, Китай . Его исследовательские интересы включают передовое производство и сварку. Тел.: +86-18545051095; Электронная почта: [email protected].
Даксин Рен, 1982 года рождения, в настоящее время преподает в Даляньском технологическом университете , Китай . Его исследовательские интересы включают передовое производство и сварку.
Кунминь Чжао, 1971 г.р., в настоящее время является профессором Государственной ключевой лаборатории структурного анализа промышленного оборудования Даляньского технологического университета, Китай . «Схема тысячи талантов» специально приглашенный Эксперт. Его исследовательские интересы включают в себя передовые технологии производства и обработки металлов давлением.
Пан Сунь, 1987 года рождения, в настоящее время работает инженером на Шанхайской верфи, Китай .
Синлинь Го, 1956 года рождения, в настоящее время профессор Государственной ключевой лаборатории структурного анализа промышленного оборудования Даляньского технологического университета, Китай . Его исследовательские интересы включают структурную вибрацию и усталость.
Лимин Лю, 1967 года рождения, в настоящее время профессор Школы материаловедения и инженерии Даляньского технологического университета, Китай. Его исследовательские интересы включают сварочные технологии и оборудование.
Благодарности
Авторы искренне благодарят профессора Ли-Мин Лю из Даляньского технологического университета за его критические обсуждения и чтение во время подготовки рукописи.
Конкурирующие интересы
Авторы заявляют, что у них нет конкурирующих интересов.
Финансирование
При поддержке Национального фонда естественных наук Китая (гранты № U1764251, 51775160) и фондов фундаментальных исследований центральных университетов Китая (грант № DUT19LAB24).
Информация об авторе
Авторы и организации
Школа материаловедения и инженерии, Даляньский технологический университет, Далянь, 116024, Китай
Деванг Чжао и Лиминг Лю
3 9 Даляньский технологический институт, Даляньский инженерный институт , Далянь, 116024, Китай
Даксин Рен и Кунминь Чжао
Институт технологии промышленности и оборудования, Технологический университет Хэфэй, Хэфэй, 230601, Китай
Куньминь Чжао
Шанхайская верфь 0,00, 92 China 9 Shipyard Co., 20, 0, 0, 0, 0, 0, 0, 0, 0, 0
Pan Sun
Кафедра инженерной механики, Государственная ключевая лаборатория структурного анализа промышленного оборудования, Даляньский технологический университет, Далянь, 116024, Китай
Xinglin Guo
- Деванг Чжао
Просмотр публикаций автора
Вы также можете искать этого автора в PubMed Google Scholar
- Daxin Ren
Посмотреть публикации автора
Вы также можете искать этого автора в PubMed Google Scholar
- Kunmin Zhao
Просмотр публикаций автора
Вы также можете искать этого автора в PubMed Google Академия
- Pan Sun
Посмотреть публикации автора
Вы также можете искать этого автора в PubMed Google Scholar
- Xinglin Guo
Просмотр публикаций автора
Вы также можете искать этого автора в PubMed Google Scholar
- Liming Liu
Просмотр публикаций автора
Вы также можете искать этого автора в PubMed Google Scholar
Авторы
Авторы, переписывающиеся
Соответствие
Даксин Рен или Кунмин Чжао.