Химическая полировка – :
alexxlab | 15.02.2020 | 0 | Разное
Электрохимическая полировка: технология электрополировки металла
Электрохимическая полировка – это процесс обработки поверхности детали путем погружения ее в кислотный раствор. Металлическое изделие подключается к положительно заряженному аноду, и через электролит пропускается ток с напряжением 10–20 В. В результате металл покрывается оксидной или гидроксидной пленкой, под которой происходит полировка путем сглаживания выступающих микронеровностей. Примерно такой же эффект дает химполировка, но здесь заготовки не подвергаются влиянию электрического тока.
Качество работы зависит от однородности материала. Полирование чистых металлов приводит к получению гладкого блестящего изделия. Полировка сложных сплавов не дает такого результата. По окончании работы обработанная поверхность повышает свою чистоту шероховатости на 2 класса.
Полирование деталей ведется только после их визуального осмотра. Не допускается наличие на них глубоких царапин или раковин, поскольку такие дефекты не устраняются в процессе полировки. Оптимальным вариантом является работа с цилиндрическими деталями. Плоские заготовки хуже поддаются полировке.
По окончании процедуры изделия приобретают ряд положительных качеств: у них увеличивается коррозионная стойкость, повышается прочность поверхностного слоя и понижается коэффициент трения.
Технология электрохимического полирования металла
При электрополировке металла его поверхность становится блестящей. Технологический процесс состоит из ряда операций:
- Предварительно заготовка подвергается механической обработке с целью доведения шероховатости поверхности до 6–7 класса.
- Промывка для удаления грязи.
- Обезжиривание.
- Подсоединение к положительно заряженному электроду.
- Электрохимическое полирование.
- Промывка в щелочной среде с целью устранения кислотных остатков.
- Сушка. Для этого используется горячий воздух или опилки.
- Выдержка деталей в горячем масле, подогретом до температуры 120 °C.
При полировке происходит устранение неровностей с поверхности детали. Поэтому любой процесс сопровождается:
- Макрополированием. При этом идет растворение крупных выступающих вершин.
- Микрополированием. Сглаживаются мелкие неровности.
Погружаемое в электролит изделие покрывается оксидной пленкой, которая является защитной средой между металлом и электролитом. В продолжение всего процесса она постоянно растворяется и образуется вновь. Правильность технологического процесса заключается в том, чтобы ее толщина оставалась стабильной.
Непосредственно под пленкой происходит полировка металла. Осуществляется она за счет обмена электронами и ионами между анодом и электролитом. Толщина формируемой пленки всегда меньше на выступающих частях вершин неровностей. Именно здесь и происходит усиленное растворение металла. В углублениях слой пленки толще, и здесь обмен заряженных частиц уменьшенный.
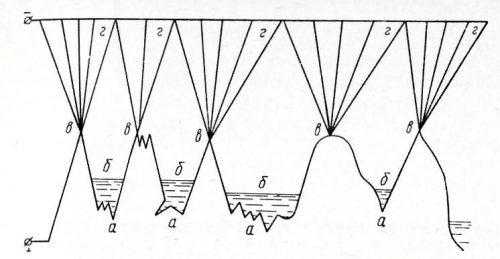
Образование вязкой пленки толще во впадинах неровностей
Существуют другие факторы, влияющие на скорость полирования поверхности:
- перемешивание электролита;
- повышение его температуры;
- увеличение силы тока и напряжения.
Все эти факторы уменьшают поверхностный слой, что ускоряет полировку.
Для каждого изделия существует свой временной режим. В зависимости от продолжительности процедуры пропорционально увеличивается снимаемый слой металла. Этого не следует допускать, потому что шероховатость поверхности, выйдя на свой уровень, остается неизменной. Происходит ненужное растворение слоя изделия, что не оказывает влияния на качество поверхности.
Электролитно-плазменное полирование
Во время электролитно-плазменного полирования наблюдаются схожие процессы. Однако тут в качестве среды используются растворы солей аммония. Под воздействием высокого напряжения 200–350 В на поверхности детали, которая является анодом, образуется парогазовая оболочка. Формируется она за счет вскипания электролита. Через нее постоянно протекает электрический ток, вызывая появление плазменных разрядов, которые оказывают влияние на сглаживание поверхности. В результате время полировки составляет до 5 мин., а устранение небольших заусенцев – несколько секунд.
Важным условием является поддержание высокой температуры химической среды. Она необходима для создания условий пленочного кипения. Однако и превышать верхний предел нельзя. Например, для низкоуглеродистой стали интервал температур составляет 70–90 °C. За пределами этого интервала снижается качество полировки.
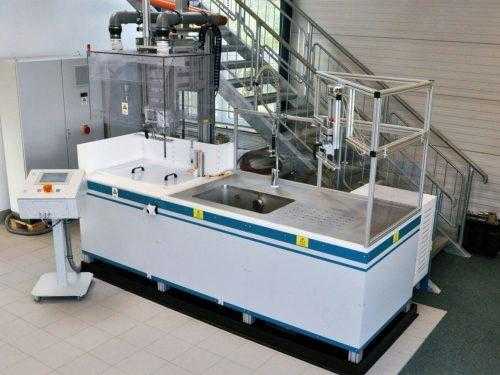
Электроплазменное полирование
Отличия электрополирования от химического
Электрополирование, как и электроплазменная обработка, отличается от химического процесса тем, что через электролит подается электрический ток.
При химическом полировании изделие опускается в емкость с химическим раствором кислоты или щелочи. Здесь происходит растворение поверхностного слоя. Это сопровождается бурным кипением содержимого сосуда. Деталь приобретает нужную шероховатость за несколько секунд. В отличие от электрополирования такой метод менее затратный. Здесь не требуется сложного оборудования. Но присутствуют и недостатки:
- Сложность контроля над протеканием процесса.
- Без применения электрического тока качество получаемого изделия ниже. У него отсутствует блеск. Поэтому такому способу обработки больше подвергаются изделия из цветного металла, имеющие сложную конфигурацию, которым не предъявляется высоких требований.
Применяемое оборудование и материалы
В качестве оборудования для электрополировки применяются ванны. Технология схожа с хромированием деталей.
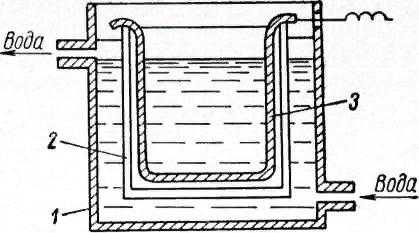
Конструкция ванны для электрополирования
Ванна имеет следующую конструкцию:
- Наружный корпус.
- Внутренний корпус.
- Внутренняя часть ванны облицовывается термостойким материалом, способным противостоять химической среде. Применяется эмаль марки ЛК-1, фарфор, жаростойкое стекло, керамика.
- Электронагреватели.
- Между корпусами располагается водяная рубашка. Она необходима для регулировки температуры. На первой стадии подготовки электролита он нагревается до 120 °C. Рабочая же температура составляет 70–80 °C.
- Подключаются трансформаторы с выпрямителями. С их помощью идет регулирование подачи электрического тока.
Ведется подбор электролита, который должен отвечать следующим характеристикам:
- безопасностью в процессе применения;
- хорошей способностью для качественного сглаживания поверхности металла;
- длительностью работы;
- возможностью полировки разных металлов.
Исследования показали, что оптимальным составом является смесь фосфорной кислоты, серной и хромового ангидрида. Использование такого электролита позволяет вести полировку сталей как инструментальных, так и легированных. Обработке поддаются медь, алюминий, а также нержавейка.
Присутствие кислот позволяет вести контроль над плотностью электрического тока. Фосфорное соединение его понижает, а серная кислота повышает. За счет правильного формирования концентрации смеси можно оптимально наладить проведение процесса полирования.
Остались вопросы? Обязательно задайте их в комментариях к статье!
wikimetall.ru
Полировка химическая – Справочник химика 21
Химическое полирование в отличие от электрохимического не получило еш,е широкого применения в промышленности, так как с его помощью не удается достигнуть интенсивного блеска. Однако в тех случаях, где механическая полировка затруднена, а поверхность изделий не требует зеркального блеска (изделия из цветных металлов сложной формы и малых размеров), следует отдать предпочтение химическому полированию. [c.159]Химически чистое железо по внешнему виду напоминает платину, оно отличается большой способностью к полировке и вязкостью. Щар из чистого железа легко расплющивается без нагревания в тонкую жесть — без разрывов по краям. Ювелирные изделия из чистого железа очень похожи на платиновые. [c.348]
Этим металлографическим методом можно определять не только число дислокаций, но и ориентировку поверхностей пластинок, вырезанных из кристалла, а также степень неоднородности кристаллов. Чтобы выявить дислокации на пластине германия, сначала ее шлифуют, затем тщательно очищают, подвергают химической полировке, например смесью концентрированной азотной кислоты (7,5 мл), 48%-НОЙ плавиковой кислоты (5 мл), ледяной уксусной кислоты (10 мл) и дистиллированной воды (1,2 мл). Полируют и травят под тягой с соблюдением правил безопасной работы. После полирования пластину отмывают дистиллированной водой и травят для выявления дислокаций, например, в травителе 00 млН О, 12 г КОН и 8 г КзРе(СК)в.
Блеск электролитических покрытий может быть достигнут путем механической, электрохимической или химической полировки. Однако при использовании этих методов безвозвратно теряется до 20% от веса покрытия, что приводит к значительному ухудшению защитных свойств покрытия кроме того, требуются дополнительные расходы на оборудование и материалы, электроэнергию, ра- [c.136]
Обсуждение результатов и выводы. Автору неизвестны старые наблюдения образования подобных поверхностных дендритов серебра в процессе электролиза кристаллов при низкой температуре. Результаты описанных выше опытов позволяют утверждать, что такие дендриты образуются только в оптических плоских пластинках, полученных. методом, исключающим механическую полировку (химическое растворение). В присутствии трещин или поверхностных дефектов образуется лишь беспорядочная сетка из нитей серебра. Даже при температуре жидкого воздуха галогениды серебра не легко раскалываются вдоль плоскостей (100), что отличает их от щелочных галогенидов. Гиппель [5] наблюдал образование аналогичных систем дендритов на поверхностях кристаллов галогенидов щелочных металлов, полученных скалыванием по спайности. [c.97]
Реальная поверхность кре.мния содержит весьма тонкий слой оксида кремния (1,0—1,5 нм), который образуется в ходе технологических процессов полировки монокристалла и очистки его поверхности от примесей при химическом удалении поверхностного слоя, нарушенного механической обработкой и окончательной промывкой монокристалла в растворителях и воде. При этом поверхностные атомы кремния оксидной пленки могут быть связаны с гидроксильными группами, кроме того, на поверхности физически адсорбируются молекулы воды. Аналогичная картина имеет место и на поверхности кристаллического оксида кремния— кварца. Исходя из этого химическая гомогенизация поверхности указанных материалов должна включать, с одной стороны, удаление физически сорбированной воды, а с другой — достижение максимальной степени гидроксилирования поверхности. Последнее оказывается одним из важнейших условии при использовании поверхности твердых веществ в качестве матрицы для осуществления на ней направленного синтеза, например, оксидных структур методом молекулярного наслаивания. Предельная степень гидроксилирования обусловливает максимальное заполнение поверхности элемент-кислородными структурными единицами, и, таким образом, вопрос стандартизации гидроксильного покрова поверхности при подготовке к синтезу является одним из важнейших, определяющим сплошность синтезированного методом молекулярного наслаивания слоя.
Задание. 1. Определить при помощи химического травления глубину нарушений, вызванных механической обработкой поверхности кремния. 2. Провести химическую полировку поверхности кремния. [c.106]
Инфракрасная (ИК) спектроскопия используется в различных областях науки, и в каждой из них придается- этому термину различный смысл. Для химика-аналитика это удобный метод решения таких задач, как, например, определение пяти изомеров гексахлорциклогексана, качества парафина, смолы, полимера, эмульгатора в эмульсии для полировки, опознание страны, из которой вывезен контрабандный опиум. Физику ИК-спектроскопия представляется методом исследования энергетических уровней в полупроводниках или определения межатомных расстояний в молекулах. Она может быть также полезна и при измерении температуры пламени ракетного двигателя. Для химика-органика это метод идентификации органических соединений, позволяющий выявлять функциональные группы в молекулах и следить за ходом химических реакций. Для биолога ИК-спектроскопия – перспективный метод изучения транспорта биологически активных веществ в живой ткани, ключ к структуре многих естественных антибиотиков и путь познания строения клетки. Физикохимику метод позволяет приблизиться к пониманию механизма гетерогенного катализа и кинетики сложных реакций. Он служит дополнительным источником информации при расшифровке структуры кристаллов. В этих и многих других областях знания ИК-спектроскопия служит исследователям мощным средством изучения тайн вещества. Вероятно, справедливо будет сказать, что из всех инструментальных методов ИК-спектроскопия наиболее универсальна.
Электронно-лучевые приборы в течение первых 2 месяцев теряют товарный вид. Такие детали, как штырьки, кольца, корпуса, предварительно полированные, за это время значительно прокорродировали. Через год после начала испытаний кольца и корпуса из ковара с химической полировкой покрылись продуктами коррозии приблизительно на 85% всей поверхности. Никелевые покрытия по латуни Л62 в течение 6 месяцев оказались более коррозионностойкими по сравнению с коваром, но затем происходит разрушение поверхности примерно на 70%. [c.80]
Химическое Т. применяют в технологии монокристаллов, стекол и поликристаллов (металлов, сплавов, полупроводников и др. неорг. материалов) для очистки от окалины и др. поверхностных загрязнений, выявления дефектов структуры и двойников, определения кристаллографич. ориентации, удаления нарушенных слоев, придания пов-сти определенных св-в (полировка, шлифовка, загрубление, изменение к.-л. характеристик), для повышения мех. прочности изделий, для изготовления рельефа или деталей определенной формы, в частности в планарной технологии полупроводниковых приборов, при изготовлении резонаторов, частотных фильтров, хям. сенсоров и т. п.
Если образец представляет собой полированный шлиф, покрытие можно легко удалить, подвергая образец одной из окончательных операций полировки (алмазным порошком размером – 6 мкм или порошком АЬОз с размером зерна – 1 мкм). Если поверхность образца шероховатая или плоский образец нельзя подвергнуть повторной полировке, для удаления покрытия
www.chem21.info
Химическая полировка металла
При химическом полировании воздействие раствора на металл сочетается с действием гальванических пар на его поверхности, что вызывает образование пассивирующей оксидной пленки. Непосредственным результатом химического полирования является сглаживание микронеровностей и образование блеска поверхности с одновременным растворением верхнего слоя. Увеличение блеска связано с предотвращением травления металла вследствие образования на его поверхности пассивирующей окисной пленки, которая возникает под влиянием взаимодействия обрабатываемого металла с компонентами раствора. Однако электрохимическая полировка приводит к получению лучшего блеска поверхности чем при химической.
Качество полированной поверхности зависит от соотношения скоростей формирования пленки и ее растворения в жидкости. Преобладание первой приводит к оксидированию, второй — к травлению металла. Наибольший блеск поверхности достигается при минимальной толщине оксидной пленки, которая должна быть достаточной для предотвращения травящего действия раствора на металл, а это возможно при равенстве скоростей процессов формирования и химического растворения образующейся окисной пленки. Толщина пленки при химическом полировании меньше, чем при электрохимическом. Это объясняет меньшую эффективность сглаживания микронеровностей и повышение блеска поверхности металла.
Положительные результаты полирования нержавеющих аустенитных сталей типа 12Х18Н10Т достигаются в растворе следующего состава: серная кислота — 34%, соляная кислота — 6,5%, азотная кислота — 4,5%, хлористый натрий — 0,5%, вода — 54%, краситель кислотный черный 3М — 0,5%. Корректирование раствора состоит в периодическом добавлении воды и азотной кислоты. Обработку проводят в течение 3–10 минут при температуре 70–75
С увеличением содержания в растворе солей железа время обработки увеличивается до 15–20 минут. Качество поверхности при химическом полировании зависит от объемной плотности загрузки деталей в ванне. При слишком большой загрузке возникает неравномерность обработки поверхности, возможно ее травление и образование других дефектов вследствие затрудненного доступа раствора к поверхностям изделий.
После химического полирования детали необходимо тщательно промыть в проточной воде и высушить. Целесообразно проводить химическое пассивирование полированных изделий. Следует отметить меньшие трудоемкость и энергоемкость химического полирования по сравнению с механическим. Однако процесс химического полирования сопряжён со следующими недостатками:
- Технологическая сложность
- Высокий процент брака
- Токсичность и пожароопасность
- Коррозия оборудования
- Дорогостоящая утилизация отходов.
plasmacraft.ru
2.3. Электро-химическое полирующее травление поверхности
Электрохимическая обработка основана на законах анодного растворения металлов при электролизе.
При прохождении электрического тока через электролит на поверхности заготовки происходят химические реакции, и поверхностный слой металла превращается в химическое соединение.
Продукты электролиза переходят в раствор или удаляются механическим способом.
Производительность этого способа зависит от электрохимических свойств электролита, обрабатываемого материала и плотности тока.
Электрохимическое полированиеосуществляется в ванне, заполненной электролитом (растворы кислот и щелочей).
Обрабатываемую заготовку подключают к катоду (рис. 21.5). Катодом служит металлическая пластинка из свинца, меди, стали (иногда электролит подогревают).
Рис. 2.7. Схема электрохимического полирования:
1 – ванна; 2 – обрабатываемая заготовка; 3 – пластина-электрод; 4 – электролит; 5 – микровыступ; 6 – продукты анодного растворения
При подаче напряжения начинается процесс растворения металла заготовки (в основном на выступах микронеровностей). В результате избирательного растворения, микронеровности сглаживаются, и обрабатываемая поверхность приобретает металлический блеск.
Улучшаются электрофизические характеристики деталей: уменьшается глубина микротрещин, поверхностный слой не деформируется, исключаются упрочнения и термические изменения структуры, повышается коррозионная стойкость.
Этим методом получают поверхности под гальванические покрытия, доводят рабочие поверхности режущего инструмента, изготовляют тонкие ленты и фольгу, очищают и декоративно отделывают детали.
Механизм анодного растворения при электрохимическом полировании
Удаление металла при электрохимическом полировании происходит под действием электрического тока в среде электролита без непосредственного контакта катоды (инструмента) и заготовки. В основе процесса электрохимического полирования лежит явление анодного растворения металла. Анодное растворение может протекать в электролитах различного состава, в том числе в неагрессивных электролитах — водных растворах хлорида натрия, нитрата натрия и др. Эти соли дешевы и безвредны для обслуживающего персонала.
Под действием тока в электролите материал анода растворяется и в виде продукта реакции выносится из промежутка потоком электролита. В результате реакции образуются газообразные продукты, которые удаляются в атмосферу. Катод не изнашивается, что является одним из достоинств процесса электрохимического полирования.
При растворении в воде молекулы, например, солей, распадаются на положительные (катионы) и отрицательные (анионы). Молекулы воды поляризуются и располагаются в виде сферы вокруг какого-то центрального иона (рис. 1.20).
H2O
_
– H2O
+ + +
– + +
– + H2O
Na Cl
+ +
+ +
– + _
+
_
Рис. 2.8. Схема растворения солей
Если электроды погружены в электролит, то на их поверхности протекает обратимая реакция
Ме Меn++ nе,
где n- валентность металла; Меn+ ион в растворе, е – электрон.
На поверхности металла возникает положительный заряд, и к нему притягиваются отрицательно заряженные ионы из раствора. На границе электролита с металлом образуется так называемый двойной электрический слой, подобный тому, какой возникает на обкладках конденсатора (рис.1.21). Один слой представляет поверхностные заряды в металле (+), другой — ионы в растворе (-). За счет этого на электродах возникают скачки электрического потенциала. Протекание процесса электрохимического полирования становится возможным, если приложить внешнее напряжение, превышающее разность а — к, гдеа– скачок потенциала на аноде, ак – скачок потенциала на катоде. При подключении электродов к источнику напряжения ионы начинают двигаться в электролитическом поле через межэлектродный промежуток от электрода к электроду.
Ме
Рис. 2.9. Схема образования двойного электрического слоя.
На катодепроисходит ускоренное разложение молекул воды с выделением молекулярного водорода:
H2O + eH++ OH—
H++ H+ H2
На аноде справедлива следующая схема перехода металла в нерастворимый гидроксид:
Me — ne Men+
Men+ + n OH — Me (OH) n
Одновременно образуется молекулярный кислород:
2 OH — — 2eH2O + O+
O++ O+O2
Таким образом, в результате реакции выделяются свободные H2иO2и выпадает осадок на аноде в виде гидроокиси металла. Нерастворимые продукты выносятся потоком электролита из зоны обработки.
При большой силе тока возможны другие реакции в результате которых могут образовываться оксиды. Это нежелательные реакции, потому что оксиды покрывают поверхность металла и ухудшают растворение металла, а следовательно и обрабатываемость.
Требования предъявляемые к электролитам для электрохимического полирования.
От состава электролита сильно зависит электропроводность и скорость растворения металла. Для хороших технологических показаний процесса необходимо:
1) в электролите не должны протекать вовсе или протекать в минимальном объёме побочные реакции. Это снижает производительность.
2) растворение заготовки должно происходить только в зоне обработки
3) на всех участках обрабатываемой поверхности должен протекать расчётный ток
Универсальных электролитов, которые отвечают всем требованиям не существует. Поэтому для каждой детали подбирают свой состав электролита. Не существует расчётных методик определения оптимальных режимов, поэтому всё подбирается экспериментально.
Требования к электролитам при электрохимическом полировании:
1) содержащиеся в водном растворе электролита анионы и катионы должны хорошо диссоциировать при любых условиях
2) необходимо чтобы потенциал материала электрода был более положителен, чем потенциал осаждения катиона. Это нужно для того, чтобы катод не покрывался слоем металла
3) обеспечение в ходе реакции в электролите перехода продуктов реакции анодного растворения в нерастворимое состояние
4) скорость образования пассивной анодной плёнки и скорость её растворения должны быть равны
5) толщина удаляемого слоя при полировании должна быть минимальной
6) электролит не должен быть агрессивным к металлу при отсутствии тока. Для предотвращения разъедания металла в момент выключения тока вводится окислитель
7) электролит должен обеспечивать полирование в широком диапазоне температур и плотности тока и иметь продолжительный срок службы
8) в процессе полирования не должны выделяться вредные газы
Назначение и суть электрохимического полирования металлов.
Электрохимическое полирование поверхности детали применяют в качестве способа подготовки поверхности детали для проведения дальнейших операций покрытия (осаждение химическое и гальваническое металлов, оксидирование, анодирование, фосфорирование и т.д.)
Кроме того, электрохимическое полирование применяют для удаления заусенцев и полирования деталей сложной формы.
Преимущества метода:
нет механического воздействия на материал детали, поэтому такая обработка не нарушает поверхностного слоя, это особенно важно при полировании полупроводниковых заготовок.
Считается, что при электрополировке поверхность состоит из активных и пассивных участков. Полирование в электролите происходит вследствие неодинаковой пассивации выступов и впадин поверхности,а также различных условий диффузии анионов и катионов сквозь вязкий прианодный слой (рис.1.22). Пассивными являются микроуглубления, потому что в них скапливаются продукты анодной реакции, которые являются нерастворимыми. На активных микровыступах возрастает плотность тока и значит скорость их растворения, так как энергия необходимая для перевода иона в растворе максимальна на микровыступах детали.
+ —
Рис. 2.10. Схема электрополирования
Энергия отрыва иона состоит из суммы собственной энергии отрыва и энергии, необходимой для диффузии сквозь прианодный слой.
Для выяснения процесса химического полирования рассмотрим зависимость силы тока от напряжения на клеммах ванны.
Характеристика электрохимического процесса.
Рис. 2. 11. Влияние плотности тока на процесс полирования
При различных условиях на аноде электролитической ванны могут происходить:
1) растворение металлического анода
2) окисление металла анода
3) выделение газообразного кислорода
4) окисление различных веществ – компонентов раствора
5) электрополирование металла анода
Эти процессы протекают при режимах, соответствующих различным участкам характеристики процесса.
На участке АВ плотность тока увеличивается пропорционально приложенному напряжению. Анод при этом находится в активном состоянии (анод растворяется).
Участок ВС соответствует нестабильному состоянию процесса. При этом происходит пассивация анода и формируется вязкий слой электролита.
На участке CDпротекает процесс полирующего травления анода. Вязкий слой стабильный и участки анода находятся в пассивированном состоянии и идёт травление выступающих участков.
На участке DEплотность тока повышается за счёт разрядов анионовOH–. Всё это сопровождается выделением кислорода. Полирование меди на участкеCEв ортофосфорной кислоте не позволяет получить гладкой поверхности, это вызвано тем, что пузырьки выделяющегося кислорода задерживаются некоторое время на поверхности детали, что вызывает поверхностное выкрашивание –питтинг.
Участок EKне является рабочим участком электрохимического полирования.
Такие режимы используют для создания обратных процессов.
Процесс протекает при режимах, приведенных ниже:
T= 70 – 95oC
плотность тока J = 2,5 – 10А/дм2(встречаются до 100А/дм2)
U= 7 – 15 В
При электрохимическом полировании применяют ток, такой плотности, при котором вместе с растворением анода происходит разряд анионов: OH–, SO4—,PO4—.
При меньших плотностях тока металл просто растворяется.
Если плотность тока слишком велика, то происходят отрицательные явления: перегрев, бурное выделение газов на аноде, сильное растравливание металла.
Температура электролита очень важный технологический параметр, если она черезчур низкая, то увеличивается вязкость прианодного слоя, при этом ухудшается диффузия через прианодный слой и требуется повышеное напряжение в ванне.
Повышение температуры снижает вязкость прианодного слоя, при слишком большой температуре наблюдается простое травление металла.
Эффективное полирование зависит также и от времени. Увеличение длительности не улучшает качество полировки, а наоборот приводит к растравливанию отдельных участков. Необходимо установить оптимальную длительность процесса полировки, которая зависит от состояния поверхности металла, свойств металла, свойств электролита, от режимов токовых и температурных.
В ряде случаев на поверхности анода образуется труднорастворимое соединение или анод покрывается адсорбированными пузырьками, поэтому в таких случаях рекомендуется обеспечивать покачивание детали в электролите.
При покачивании обеспечивается и теплоотвод.
Для процесса важно правильно подобрать размеры, форму и материал катодов. Площадь катода должна быть в несколько раз больше полируемой детали. Форма катода чаще всего плоская, но для полирования детали сложной формы применяют профильные катоды. Материал катода должен быть химически устойчив к электролиту.
Подвесные приспособления рекомендуется выполнять из того же материала, который полируется.
Чаще всего химическая полировка используется для подготовки деталей из сплавов алюминия к последующим покрытиям (от простого окрашивания до анодирования, оксидирования и т.д.)
Существует несколько электролитов для полирования алюминия.
на основе кислот:
H3PO4,H2SO4
на основе щелочных солей:
Na2CO3
В эти электролиты добавляют хромовый ангидрид, который предотвращает разъедание металла в момент отсутствия тока.
Температура 55 – 100 оС
Длительность от 0,5 до 20 мин
Для полирования сталей в основном используют электролиты на основе ортофосфорной кислоты.
Некоторые сорта сталей можно полировать в электролитах на основе серной кислоты. Плотность тока должна быть при этом высокая 250 А/дм2
Температура 100оС
Время 0,5 мин
Скорость съёма материала 1,7 мкм/сек
Недостатки электролитов на основе ортофосфорной и серной кислот:
короткий срок службы из-за образования нерастворимых соединений (для улучшения качества полировки вводят глицерин)
Быстрорежущие стали полируют в электролитах, содержащих азотную кислоту.
Плотность тока высокая.
При полировании быстрорежущих сталей в азотной кислоте получают также
©повышение коррозионной стойкости, так как на поверхности образуются пассивные плёнки: FeO·Cr2O3иNiO·Cr2O3
При полировании быстрорежущих сталей количество снимаемого материала велико – от 20 до 40 мкм.
Если нужно снять меньший слой материала, от применяют химическое полирование, а не электрохимическое.
Серебрянные изделия полируются в цианистых электролитах серебрения.
Плотность тока 2 – 3 А/дм2
Для растворения анодной плёнки рекомендуется импульсный токовый режим.(интервал импульса 3 – 4сек).
Универсальные электролиты для полировки серебра содержат хлорную кислоту и уксусный ангидрид.
Особенность этих электролитов: возможно резкое повышение температуры, которое может привести к взрыву оборудования.
Рассмотрим характерные дефектыэлектрополированных поверхностей.
Они обусловлены дефектами самого материала металла или полупроводника, неверными условиями электрополирования, плохим качеством очистки поверхности и качествами электролита.
Например, наличие загрязнений или неоднородности материала приводит к появлению участков окисных или солевых плёнок.
Неравномерность движения электролита по поверхности или неправильное взаимное расположение деталей и электродов может вызвать как снижение точности обработки, так и искажение геометрической формы, вследствие неравномерного растворения металла.
Направленное движение газовых пузырьков по поверхности деталей могут быть причиной “полосатости” поверхности.
Пониженное напряжение также может вызвать растравливание поверхности.
Электрополирование наряду с прямым результатом даёт поверхности ряддополнительных качеств.
в ряде случаев электрополирование повышает усталостную прочность и коррозионную стойкость металла,
уменьшается коэффициент трения поверхности,
увеличивается способность металла к холодной пластической деформации (молибден),
в отдельных случаях электрополированием получают максимальную отражающую способность (алюминий).
Для ферромагнитных сплавов электрополирование позволяет повысить магнитную проницаемость материала и снизить потери на гистерезис. Это явление носит название критерия неочевидности.
studfiles.net
Технология электрохимического полирования
Особенности технологического процесса
Технологический процесс электрохимического полирования состоит из операций механической и химической подготовки поверхности металла, полирования и последующей обработки полированных деталей. В зависимости от того, какие цели преследует электрохимическое полирование, схема технологического процесса несколько изменяется. Хотя такая обработка повышает на 1—2 класса шероховатость поверхности, она может при этом оставить заметными отдельные глубокие риски, раковины, удаление которых связано с большим съемом металла. В подобных случаях следует провести предварительную обработку абразивными порошками. При этом число переходов будет меньше, чем в случае обработки поверхности без электрохимического полирования, что благоприятно скажется на экономике процесса в целом. Ручное абразивное шлифование может быть иногда заменено галтовкой или гидроабразивной обработкой, что применимо в основном при декоративной отделке. В других случаях, когда указанные дефекты поверхности не влияют на эксплуатационные свойства деталей, механическая подготовка является излишней.
Для очистки поверхности деталей от жировых загрязнений применяется химическая обработка в органических растворителях, водных моющих растворах с добавками поверхностно-активных веществ или электрохимическое обезжиривание. Составы соответствующих растворов и режимы работы идентичны применяемым при подготовке деталей перед осаждением металлических покрытий и приводятся в литературе по гальванотехнике.
Тонкие окисные пленки, окалина, продукты коррозии могут быть удалены с поверхности металла при электрохимическом полировании. Однако этой возможностью не следует злоупотреблять. Для растворения толстого слоя термической окалины приходится увеличивать продолжительность электролиза. Поэтому целесообразно окалину предварительно удалить травлением. Тонкие окисные пленки, прижоги, цвета побежалости не требуют применения этой операции.
При электрохимическом полировании независимо от того, выполняется оно в стационарных ваннах, автоматических установках или с применением проточного электролита, необходимо обеспечить строгое поддержание режима электролиза, контроль и корректирование раствора. Особенно важным является соблюдение температурного режима работы ванны. Во избежание перегревания раствора за счет выделяющегося джоулева тепла объемная плотность тока не должна превышать 1—1,5 А/л. Некоторое превышение этого значения допускается при работе с проточным охлаждаемым электролитом и при полировании ленты и проволоки с непрерывным протягиванием их через ванны. Выравнивание температуры в объеме ванны достигается перемешиванием или циркуляцией электролита, перемещением обрабатываемых деталей.
Работая с концентрированными растворами при повышенной температуре, необходимо ежедневно контролировать их плотность и добавлением воды поддерживать ее значение в требуемых пределах.
Подсчет количества воды, необходимой для получения электролита определенной плотности, проводится по формуле
где В — количество воды, необходимой для разбавления электролита, л; b — количество электролита, подлежащего корректированию, л; d1 — плотность электролита до разбавления, г/мл;
d2 — требуемая плотность электролита после добавления воды, г/мл.
Добавление воды следует проводить в конце смены, чтобы электролит 8—10 ч не находился в эксплуатации.
Изменение состава электролита, режима электролиза приводят к ухудшению качества полирования. Причины таких неполадок при обработке в производственных условиях изделий из стали, меди, никеля, алюминия и сплавов этих металлов и рекомендации по их устранению приведены в работе [91 ].
Если электрохимическое полирование является заключительной операцией технологического процесса, детали после тщательной промывки в проточной холодной и горячей воде сушат теплым воздухом или в сушильном шкафу. Протирка деталей теплыми сухими опилками или чистой ветошью благоприятно сказывается на их внешнем виде. Для повышения стойкости против коррозии полированные детали подвергают дополнительной обработке — пассивированию. Как было указано выше, стальные детали обрабатывают в течение 10—15 мин в 10%-ном растворе едкого натра при температуре 60—80° С, детали из меди, алюминия и сплавов этих металлов — в растворах, содержащих хроматы. После такой химической обработки детали быстро и тщательно сушат. Перерыв между операциями полирования и пассивирования не допускается.
В тех случаях, когда на электрохимически полированные детали нужно осадить гальванические покрытия, наличие на металле окисной пленки будет препятствовать прочному сцеплению покрытия с основой. Для активации поверхности после полирования и промывки детали декапируют в 5%-ном растворе соляной кислоты, промывают и сразу же загружают в ванну покрытий. Операция декапирования особенно необходима при осаждении покрытий из щелочных электролитов. При работе с сильно кислыми электролитами, например хромирования, декапирование можно исключить, так как при загрузке полированных деталей в такую ванну без тока происходит разрушение окисной пленки.
Производительность процесса электрохимического полирования не связана ни с величиной и конфигурацией обрабатываемых деталей, ни с механическими свойствами материала, из которого они изготовлены. Она определяется размерами ванн и мощностью источника тока, которые могут быть увеличены без больших затрат. Несложность и универсальность оборудования, возможность одновременной обработки в одной ванне большого количества деталей отличают электрохимический способ от других способов декоративной и чистовой обработки.
www.stroitelstvo-new.ru
Электрохимическая полировка металла
Электрохимическая обработка заменяет трудоемкие механические методы и не приводит к нежелательным структурным изменениям в поверхностном слое изделий. Стравленная поверхность во многих случаях обладает более высокой коррозийной стойкостью и улучшенными механическими свойствами. Электрохимическое полирование — это обработка поверхностей деталей, погруженных в электролит, представляющий собой раствор, обычно содержащий кислоты. В процессе обработки при постоянном напряжении 10–20 В изделие подключается к положительному полюсу (аноду) источника питания.
При анодном электрохимическом полировании процесс сглаживания микрошероховатостей на уровне субмикрорельефа поверхности связан с наличием на металле пассивирующей пленки. Степень уменьшения шероховатостей определяется величиной электрического заряда, прошедшего через электролит. В ходе электролиза, наряду с уменьшением высоты микровыступов, происходит округление их вершин и формирование волнообразного микрорельефа поверхности. Данные процессы вызываются неравномерностью распределения электрического тока по микрорельефу поверхности и концентрационными изменениями электролита в прианодном слое. Качество электрохимической обработки зависит от состава металла или сплава, степени остаточной деформации, толщины обрабатываемой детали.
При использовании электрохимического полирования для получения поверхности хорошего качества необходимо перед обработкой убедиться, что на деталях нет глубоких рисок, забоин, раковин, так как они не устраняются при электрохимической обработке. Наиболее высокий блеск поверхности достигается на небольших деталях, причем плоские поверхности полируются хуже, чем цилиндрические.
Электрохимическое полирование проводится в обычных гальванических ваннах с обязательным плотным контактом подвесного устройства с деталями и электродной штангой. Наиболее долговечна оснастка из титана, который не разрушается в электролитах. Для надежности электрического контакта подвески с деталями рекомендуется образующуюся на них окисную пленку периодически удалять, используя разбавленную серную кислоту.
Основой промышленных электролитов для электрохимического полирования служат ортофосфорная или хлорная кислоты. В хлорнокислых электролитах обрабатывается алюминий, цинк, свинец, титан. В трехкомпонентных фосфорно-серно-хромовокислых электролитах обрабатываются стали различных марок, а в фосфорно-сернокислых — нержавеющие стали аустенитного класса — 12Х18Н10Т, Х17Г9АН4.
Для повышения стойкости к коррозии рекомендуется обрабатывать стальные детали после электрохимического полирования раствором NaOH в течение 15–20 минут при температуре 60–70оС. В случае нанесения на изделие гальванического покрытия, для улучшения сцепления покрытия с деталью необходимо подвергнуть его электрохимической обработке в 3–5 % растворе соляной кислоты.
Несмотря на достаточно широкую область применения, электрохимический метод имеет существенные недостатки, такие как:
- Высокая энергоёмкость
- Токсичность, пожароопасность и взрывоопасность
- Технологическая сложность
- Ограничение номенклатуры обрабатываемых металлов
- Коррозия оборудования
plasmacraft.ru
Химическая полировка – Большая Энциклопедия Нефти и Газа, статья, страница 1
Химическая полировка
Cтраница 1
Химическая полировка приводит к отрицательному эффекту при очень высоких нагрузках, когда величина фактической площади контакта делается столь велика, что очаги схватывания из отдельных точек распространяются на всю область трения, обусловливая мгновенное заедание. [1]
Электролитическая и химическая полировка металлов взамен механических способов представляет большой интерес, особенно при декоративной отделке изделий из алюминия, меди и ее сплавов, из нержавеющей и углеродистой стали, а также при отделке серебряных и золотых покрытий в ювелирной промышленности. [3]
Иногда химическую полировку сочетают с предварительной механической, осуществляемой с помощью микропорошков ( в виде паст или суспензий) с размером зерна 0 1 – 0 3 мк. [4]
Иногда химическую полировку сочетают с предварительной механической, осуществляемой с помощью микропорошков ( в виде паст или суспензий) с размером зерна 0 1 – 0 3 мкм. [5]
Химическую полировку подложек обычно осуществляют следующим образом. Подложку, закрепленную в платиновом держателе, подогревают над поверхностью кислоты ( в случае гранатов – ортофосфорной), нагретой до 350 – 380 С, и затем опускают в кислоту на несколько секунд. Качество обработанных таким образом подложек определяют с помощью поляризацион-но-оптического и рентгенографического анализов. На рис. 5.7 приведены кривые качания, полученные на двухкристальном дифрактометре для двух подложек гадолиний-галлиевого граната, подвергнутых механической и химической полировкам. Совершенство химически полированной пластины достаточно высокое, так как ширина кривой качания не превышает 15, что близко к теоретическому значению для идеальных кристаллов. [6]
Химическую полировку пластин полупроводников проводят в условиях ламинарного потока травителя относительно поверхности пластины. Под его воздействием подложки приподнимаются и в течение всего процесса травления находятся во взвешенном состоянии. Это обеспечивает одновременную полировку обеих сторон пластин, способствует переносу веществ в растворе, ускоряет и стабилизирует процесс травления и улучшает качество обрабатываемой поверхности. [8]
ПйсЛе химической полировки остается светлым, а на Границах зерен кажется травленым. Кроме того, существует возможность прерывать травление и повторять его до достижения требуемой степени протравливания. Раствор 15 особенно эффективен для сплавов, химический состав которых находится на границе а / ( а – f – р) – твердых растворов по диаграмме состояния. [9]
Кроме химической полировки можно использовать механическую полировку, употребляя для этой цели алмазную пасту с размером зерна 0 25 мк или окись алюминия с размером зерна ОД мк. Такая полировка нарушает поверхность на глубину не более 1 мк. [10]
Опыт химической полировки турбинных лопаток из сплавов ВД-17 показал, что в процессе полировки на поверхности изделий могут образовываться небольшие канавки, возникающие в местах наиболее интенсивного стока пузырьков газа по поверхности. Чтобы избежать таких дефектов, следует периодически встряхивать детали. [11]
После химической полировки плоскости скола ( 110) GaAs выросшие на них пленки германия имеют грубую поверхность. При низких температурах осаждения Ge на GaAs диффузия Ga и As в пленку незначительна. [12]
При химической полировке этим раствором выявляют границы зерен ( рис. 68) и одновременно удаляют деформированный поверхностный слой, образующийся при механическом полировании. Но химическую полировку вследствие образования многочисленных анизотропных рельефов нельзя осуществлять слишком долго. [13]
При химической полировке этим реактивом выявляются границы зерен, а при травлении погружением – их поверхности. [14]
При химической полировке [88, 101] происходит выравнивание поверхности металла; во время процесса на поверхности осаждается тонкая пленка окиси или основной соли. Поверхность сглаживается из-за того, что диффузия ионов металла из микроуглублений происходит медленнее, чем из микровозвышений, пленка на возвышениях растворяется с большей скоростью благодаря анионам полирующего раствора. Химическим путем могут быть отполированы следующие металлы: медь, латунь, бронза, сплав никель – серебро, никель, цинк, алюминий, железо, сталь и большинство сплавов алюминия. Чтобы получить желаемые результаты, полная толщина удаляемого металла должна быть от 0 025 до 0 04 мм. [15]
Страницы: 1 2 3 4
www.ngpedia.ru