Режимы термообработки стали 40х – Сталь 40Х – Термообработка – Металлический форум
alexxlab | 04.06.2019 | 23 | Вопросы и ответы
Домашнее задание по материаловедению Вариант № д-8
Московский Государственный Технический Университет
им. Н. Э. Баумана
Факультет: Специальное машиностроение
Кафедра: М-2
Студент
Щепетьев Д.Г.
ГруппаA М2-51
Подпись __________
Преподаватель
Силаева В. И.
Подпись __________
2006 Г.
Оптимальный режим термообработки 40Х на твердость HВ 315-330:
Сталь 40Х – доэвтектоидная сталь. Для данной стали оптимальным режимом термической обработки является закалка при 860С. Закаливание производят в масло, с последующим отпуском при 500С.
Комплексную термическую обработку, состоящую из полной закалки и высокого отпуска конструкционных сталей,называют улучшением.
Сталь 40Х относится к сталям мартенситного класса.
1) Закалка – термическая обработка, в результате которой в сплаве образуется неравновесная структура. Конструкционные и инструментальные стали закаливают для упрочнения.
Задача закалки — получение структуры мартенсита с максимальным процентным содержанием углерода.
Рассмотрим закалку 40Х.
Критические температуры для 40Х:
Ас3 = 815С
Ас1 = 743С
t
А+Ц 860 оС А
Ас3 (815 оС)
Ас1 (743 оС)
масло
500 оС
Мн
вода
Высокий
отпуск
Ф+П
Тотп
При нагреве до температуры 743С структура сплава остается постоянной –
Для получения мартенситной структуры необходимо переохладить аустенит до температуры мартенситного превращения, следовательно, скорость охлаждения должна превышать критическую. Такое охлаждение наиболее просто осуществляется погружением закаливаемой детали в жидкую среду (вода или масло), имеющую температуру 20-25С. В результате такой обработки получается мартенсит. Сталь должна иметь структуру мартенсита по всему сечению детали после закалки, т.е. иметь однородную структуру, которая обеспечивается хорошей закаливаемостью и сквозной прокаливаемостью.
studfiles.net
ТО стали 40Х – Термообработка
ycnokou, почитайте еще раз внимательно кто, какие советы давал, вдумайтесь в написаное, потом подымайте кипиш. Кто-нибудь в этой теме писал что весь вал по всему объему нужно калить на 50 ед? Почитайте внимательно мой ответ, вернитесь в первый и обратите внимание на выбранный режим. Там написано в конце закалка ТВЧ и низкий отпуск. Прочитайте еще раз внимательно вопрос (там черным по белому написано, что высокая твердость необходима на поверхности), потом прикиньте зачем мы сначала делаем объемную закалку а потом поверхностную. В начале делается объемная закалка и высокий отпуск (улучшение), для получения необходимых мех. свойств сердцевины и улучшения обрабатываемости металла. Затем с болванки вытачивается вал, заданной геометрии (не будут же его калить готовым, его поведет). После этого на ТВЧ производится закалка повехностей где нужна износостойкость, потом низкий отпуск. Не зависимо от диаметра, на ТВЧ мы закалим сталь 40Х, на поверхности и получим наши 50 ед. Да, там будут переходные зоны с меньшей твердостью, но для диаметра 100 они будут некритичны и особого ущерба прочности конструкции они не нанесут. В противном случае мы бы выбрали цементуемую сталь. А вариации на тему – эта сталь плохая, а эта хорошая, этот пруток дает сколько, а этот столько – оставте при себе. Сталь должна соответствовать ГОСТу и по ГОСТу для нее выбираются режимы и виды термообработки. Я сталкивался с множесвом случаев и множеством сталей которые после калки не давали твердость в той, или иной степени, из-за того, что колличесво легирующих элементов было на нижнем пределе, как-то умудрялись сделать из г… конфетку. Так, что кричать теперь – не берите никакой стали, они все плохие.
Не нужно писать, как сильно расходится теория с практикой если не понимаете до конца теории. В термообработке сначала была практика, а потом когда у людей появилась возможность новых методов исследования, была написана теория, которая объяснила почему получается именно так. Поймите, вы пытаетесь “втолковывать” элементарные вещи, это уже давно съедено и переварено. Скучно.
www.chipmaker.ru
Домашнее задание по материаловедению Вариант № д-8
Московский Государственный Технический Университет
им. Н. Э. Баумана
Факультет: Специальное машиностроение
Кафедра: М-2
Студент
Щепетьев Д.Г.
Подпись __________
Преподаватель
Силаева В. И.
Подпись __________
2006 Г.
Оптимальный режим термообработки 40Х на твердость HВ 315-330:
Сталь 40Х – доэвтектоидная сталь. Для данной стали оптимальным режимом термической обработки является закалка при 860С. Закаливание производят в масло, с последующим отпуском при 500С.
Комплексную термическую обработку, состоящую из полной закалки и высокого отпуска конструкционных сталей,называют улучшением.
Сталь 40Х относится к сталям мартенситного класса.
1) Закалка – термическая обработка, в результате которой в сплаве образуется неравновесная структура. Конструкционные и инструментальные стали закаливают для упрочнения.
Задача закалки — получение структуры мартенсита с максимальным процентным содержанием углерода.
Рассмотрим закалку 40Х.
Критические температуры для 40Х:
Ас3 = 815С
Ас1 = 743С
t
А+Ц 860 оС А
Ас3 (815 оС)
Ас1 (743 оС)
масло
500 оС
Мн
вода
Высокий
отпуск
Ф+П
Тотп
При нагреве до температуры 743С структура сплава остается постоянной – перлит. Как только пройдена точка Ас1 на границах зерен перлита начинает зарождаться аустенит. В нашем случае мы имеем полную закалку, т.к. температура превышает Ас3 , то весь перлит переходит в аустенит. Таким образом, нагрев до 815С мы получили однофазную структуру – аустенит, при этом при повышении температуры после 815С зерно растет.
Для получения мартенситной структуры необходимо переохладить аустенит до температуры мартенситного превращения, следовательно, скорость охлаждения должна превышать критическую. Такое охлаждение наиболее просто осуществляется погружением закаливаемой детали в жидкую среду (вода или масло), имеющую температуру 20-25С. В результате такой обработки получается мартенсит. Сталь должна иметь структуру мартенсита по всему сечению детали после закалки, т.е. иметь однородную структуру, которая обеспечивается хорошей закаливаемостью и сквозной прокаливаемостью.
studfiles.net
Термическая обработка (термообработка) стали, сплавов, металлов.
Термическая обработка (термообработка) — это технологический процесс изменения структуры сталей, сплавов и цветных металлов посредством широкого диапазона температур: поэтапных нагреваний и охлаждении с определенной скоростью. Такая обработка очень сильно изменяет свойства сталей, сплавов, металлов в сторону улучшения показателей, но при этом не изменяя их химический состав. Можно сказать, что основная цель термической обработки – это улучшение свойств и характеристик изделий из него.
Виды (стадии) термической обработки стали
Отжиг — термическая обработка (термообработка) металла, представляющая собой процесс нагревания до заданной температуры, а затем процесс медленного охлаждения. Отжиг бывает разных видов в зависимости от уровня температур и скорости процесса.
Нормализация — термообработка, принципиально похожая на отжиг. Основное отличие в том, что процесс отжига предполагает печь, а при нормализации охлаждение стали проходит на воздухе.
Закалка — этап термообработки, основанный на нагревании сырья до такого уровня температуры, который является выше критического (перекристаллизация стали). После выдержки в такой температуре в заданном интервале времени происходит охлаждение, быстрое, с заданной скоростью. Закаленной стали (сплавам) свойственна неравновесная структура и поэтому применяется такой вид термообработки как отпуск.
Отпуск — стадия термообработки, необходимая для снятия в стали и сплавах остаточного напряжения или максимального его снижения. Снижает хрупкость и твёрдость металла, увеличивает вязкость. Проводится после стадии закалки.
Старение — иначе еще называется дисперсионное твердение. После стадии отжига металл опять нагревают, но до более низкого уровня температур и с медленной скоростью остужают. Цель такой термообработки в получении особенных частиц упрочняющей фазы.
От степени необходимой глубины обработки различают термообработку поверхностную, которая затрагивает лишь поверхность изделий, и объемную, когда термическому воздействию подвергается весь объем сырья.
В отраслевой промышленности, в частности – в машиностроении, термическую обработку чаще всего проходит сталь следующих марок:
– сталь 45 (замещаемость 40Х, 50, 50Г2)
– сталь 40Х (замещаемость 38ХА, 40ХР, 45Х, 40ХС, 40ХФ, 40ХН)
– сталь 20 (замещаемость 15, 25)
– сталь 30ХГСА (замещаемость 40ХФА, 35ХМ, 40ХН, 25ХГСА, 35ХГСА)
– сталь 65Г
– сталь 40ХН
– сталь 35
– сталь 20Х13
Термообработка стали 45
Конструкционная углеродистая. Этап предварительной термической обработки называется нормализация, проходит на воздухе, а не в печи. довольно легко проходит механическую обработку. Точение, фрезеровку и т. д. Получают детали, например, типа вал-шестерни, коленчатые и распределительные валы, шестерни, шпиндели, бандажи, цилиндры, кулачки.
После закалки, которая является конечной стадией термообработки, детали достигают высокого уровня прочности и отличных показателей износостойкости. Подвергаются шлифовке. Высокое содержание углерода (0,45%) обеспечивает хорошую закаливаемость и, соответственно, высокую твёрдость поверхности и прочность изделия. Сталь 45 калят «на воду», когда после калки деталь охлаждают в воде. После охлаждения деталь подвергается низкотемпературному отпуску при температуре 200-300 градусов по Цельсия. При такой термообработке стали 45 достигает твердость порядка 50 HRC.
Изделия: Кулачки станочных патронов, согласно указаниям ГОСТ, изготовляют из сталей 45 и 40Х. Твёрдость Rc = 45 -50. В кулачках четырёх-кулачных патронов твёрдость резьбы должна быть в пределах Rс = 35-42. Отпуск кулачков из стали 45 производится при температуре 220-280°, из стали 40Х при 380-450° в течение 30-40 мин.
Расшифровка марки стали 45: марка 45 означает, что в стали содержится 0,45% углерода,C 0,42 – 0,5; Si 0,17 – 0,37;Mn 0,5 – 0,8; Ni до 0,25; S до 0,04; P до 0,035; Cr до 0,25; Cu до 0,25; As до 0,08.
Термообработка стали 40Х
Легированная конструкционная сталь. Для деталей повышенной прочности такие как оси, валы, вал-шестерни, плунжеры, штоки, коленчатые и кулачковые валы, кольца, шпиндели, оправки, рейки, зубчатые венцы, болты, полуоси, втулки и прочих деталей повышенной прочности. Сталь 40Х также часто используется для производства поковок, штампованных заготовок и деталей трубопроводной арматуры. Однако последние перечисленные детали нуждаются в дополнительной термической обработке, заключающейся в закалке через воду в масле или просто в масле с последующим отпуском в масле или на воздухе.
Расшифровка марки стали 40Х. Цифра 40 указывает на то, что углерод в стали содержится в объеме 0,4 %. Хрома содержится менее 1,5 %. Помимо обычных примесей в своем составе имеет в определенных количествах специально вводимые элементы, которые призваны обеспечить специально заданные свойства. В качестве легирующего элемента в данном случае используется хром, о чем говорит соответствующая маркировка.
Термообработка стали 20
Термообработка стали 20 – сталь конструкционная углеродистая качественная. Широкое применение в котлостроении, для труб и нагревательных трубопроводов различного назначения, кроме того промышленность выпускает пруток, лист. В качестве заменителя стали 20 применяют стали 15 и 25.
По требованиям к механическим свойствам выделяют пять категорий.
– I категория: сталь всех видов обработки без испытания на ударную вязкость и растяжение.
– II категория: образцы из нормализованной стали всех видов обработки размером 25 мм проходят испытания на ударную вязкость и растяжение.
– III категория: испытания на растяжение проводят на образцах из нормализованной стали, размером 26-100 мм.
– IV категория: образцы для испытаний на растяжение и ударную вязкость изготавливают из термически обработанных заготовок размером не более 100 мм. Требования третьей и четвертой категории предъявляют к калиброванной, горячекатаной и кованной качественной стали.
– V категория. Испытания механических свойств на растяжение проводят на образцах из калиброванных термически обработанных (высокоотпущенных или отожженных) или нагартованных сталей.
Химический состав стали 20: углерод (C) – 0.17-0.24 %, кремний (Si) – 0,17-0,37%, марганец (Mn) – 0,35-0,65 %;содержание меди (Cu) и никеля (Ni) допускается не более 0,25%, мышьяка (As) – не более 0,08%, серы (S) – не более 0,4%, фосфора (Р) – 0,035%.
Структура стали 20 представляет собой смесь перлита и феррита. Термическая обработка стали 20 позволяет получать структуру реечного (пакетного) мартенсита. При таких структурных преобразованиях прочность возрастает, и пластичность уменьшается. После термического упрочнения прокат из стали 20 можно использовать для изготовления метизной продукции (класс прочности 8.8).
Технологические свойства стали 20: Температура начала ковки стали 20 составляет 1280° С, окончания – 750° С, охлаждение поковки – воздушное. Сталь 20 нефлокеночувствительна и не склонна к отпускной способности. Свариваемость стали 20 не ограничена, исключая детали, подвергавшиеся химико-термической обработке. Рекомендованы способы сварки АДС, КТС, РДС, под газовой защитой и флюсом.
Сталь 20 применяют для производства малонагруженных деталей ( пальцы, оси, копиры, упоры, шестерни) , цементуемых деталей для длительной и весьма длительной службы (эксплуатация при температуре не выше 350° С) , тонких деталей, работающих на истирание. Сталь 20 без термической обработки или после нормализации используется для производства крюков кранов, вкладышей подшипников и прочих деталей для эксплуатации под давлением в температурном диапазоне от -40 до 450°С . Сталь 20 после химико-термической обработки идет на производство деталей, которым требуется высокая поверхностная прочность ( червяки, червячные пары, шестерни) . Широко применяют сталь 20 для производства трубопроводной арматуры, труб, предназначенных для паропроводов с критическими и сверхкритическими параметрами пара, бесшовных труб высокого давления, сварных профилей прямоугольного и квадратного сечения и т. д.
Термообработка стали 30ХГСА
Относится к среднелегированной конструкционной стали. Сталь 30ХГСА проходит улучшение – закалку с последующим высоким отпуском при 550-600 °С, поэтому применяется при создании улучшаемых деталей (кроме авиационных деталей это могут быть различные корпуса обшивки, оси и валы, лопатки компрессорных машин, которые эксплуатируются при 400°С, и многое другое), рычаги, толкатели, ответственные сварные конструкции, работающие при знакопеременных нагрузках, крепежные детали, работающие при низких температурах.
Сталь 30ХГСА обладает хорошей выносливостью, отличными показателями ударной вязкости, высокой прочностью. Она также отличается замечательной свариваемостью.
Сварка стали 30ХГСАтоже имеет свои особенности. Она осуществляется с предварительным подогревом материала до 250-300 °С с последующим медленным охлаждением. Данная процедура очень важна, поскольку могут появиться трещины из-за чувствительности стали к резким перепадам температуры после сварки. Поэтому по завершении сварных работ горелка должна отводиться медленно, при этом осуществляя подогрев материала на расстоянии 20-40 мм от места сварки. Также, не более, чем спустя 8 часов по завершении сварки сварные узлы стали 30ХГСА нуждаются в закалке с нагревом до 880 °С с последующим высоким отпуском. Далее изделие охлаждается в масле при 20-50 °С. Отпуск осуществляется нагревом до 400 – 600 °С и охлаждением в горячей воде. Сварку же необходимо выполнять максимально быстро, дабы избежать выгорания легирующих элементов.
После прохождения термомеханической низкотемпературной обработки сталь 30ХГСА приобретает предел прочности до 2800 МПа, ударная вязкость повышается в два раза (в отличии от обычной термообработки стали 30хгса), пластичность увеличивается.
Термообработка стали 65Г
Сталь конструкционная рессорно-пружинная. Используют в промышленности пружины, рессоры, упорные шайбы, тормозные ленты, фрикционные диски, шестерни, фланцы, корпусы подшипников, зажимные и подающие цанги и другие детали, к которым предъявляются требования повышенной износостойкости, и детали, работающие без ударных нагрузок. (заменители: 70, У8А, 70Г, 60С2А, 9ХС, 50ХФА, 60С2, 55С2).
Термообработка стали 40
Сталь конструкционная углеродистая качественная. Использование в промышленности: трубы, поковки, крепежные детали, валы, диски, роторы, фланцы, зубчатые колеса, втулки для длительной и весьма длительной службы при температурах до 425 град.
Термообработка стали 40ХН
Сталь конструкционная легированная Используется в отраслевой в промышленности: оси, валы, шатуны, зубчатые колеса, валы экскаваторов, муфты, валы-шестерни, шпиндели, болты, рычаги, штоки, цилиндры и другие ответственные нагруженные детали, подвергающиеся вибрационным и динамическим нагрузкам, с предъявляемыми требованиями повышенной прочности и вязкости. Валки рельсобалочных и крупносортных станов для горячей прокатки металла.
Термообработка сталь 35
Сталь конструкционная углеродистая качественная. Используется в отраслевой промышленности. Это детали невысокой прочности, подвергающиеся невысокому уровню напряжения: оси, цилиндры, коленчатые валы, шатуны, шпиндели, звездочки, тяги, ободы, траверсы, валы, бандажи, диски и другие детали.
Термообработка стали 20Х13
Сталь коррозионно-стойкая жаропрочная. Используется в энергетическом машиностроении и печестроении; турбинные лопатки, болты, гайки, арматура крекинг-установок с длительным сроком службы при температурах до 500 град; сталь мартенситного класса Сталь марки 20Х13 и другие стали мартенситного класса: жаропрочные хромистые стали мартенситного класса применяют в различных энергетических установках, они работают при температуре до 600° С. Из них изготовляют роторы, диски и лопатки турбин, в последнее время их используют для кольцевых деталей больших толщин. Существует большое количество марок сталей данного класса. Общим для всех является пониженное содержание хрома, наличие молибдена, ванадия и вольфрама. Они эффективно упрочняются обычными методами термообработки, которая основана на у – a-превращении и предусматривает получение в структуре мартенсита с последующим улучшением в зависимости от требований технических условий. (заменители: 12Х13, 14Х17Н2)
Пресс-служба группы компаний ВоКа
17 сентября 2016г
metizmsk.ru
температура, режимы, технология, твердость стали после закалки
Для придания стали определенных эксплуатационных качеств на протяжении многих десятилетий проводится термообработка. Сегодня, как и несколько столетий назад, закалка стали предусматривает нагрев металла и его последующее охлаждение в определенной среде. Температура нагрева стали под закалку должна быть выбрана в соответствии с составом металла и механическими свойствами, которые нужно получить. Допущенные ошибки при выборе режимов закалки приведут к повышению хрупкости структуры или мягкости поверхностного слоя. Именно поэтому рассмотрим способы закалки стали, особенности применяемых технологий, а также многие другие моменты.
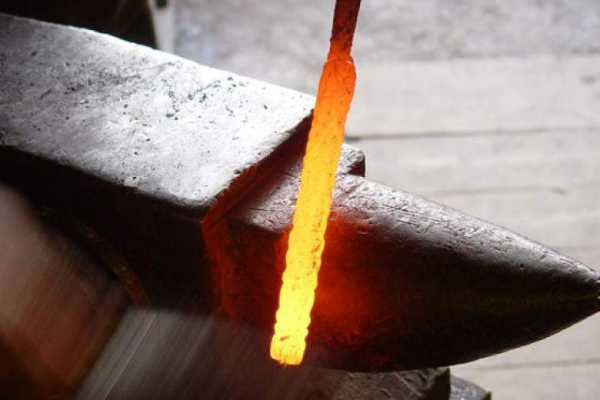
Какой бывает закалка метала?
Для чего нужна закалка стали знали еще древние кузнецы. Правильно выбранная температура закалки стали позволяет изменять основные эксплуатационные характеристики материала, так как происходит преобразование структуры.
Закалка – термообработка стали, которая сегодня проводится для улучшения механических качеств металла. Процесс основан на перестроении атомной решетки за счет воздействия высокой температуры с последующим охлаждением.
Технология закалки стали позволяет придать недорогим сортам металла более высокие эксплуатационные качества. За счет этого снижается стоимость изготавливаемых изделий, повышается прибыльность налаженного производства.
Основные цели, которые преследуются при проведении закалки:
- Повышение твердости поверхностного слоя.
- Увеличение показателя прочности.
- Уменьшение пластичности до требуемого значения, что существенно повышает сопротивление на изгиб.
- Уменьшение веса изделий при сохранении прочности и твердости
Существуют самые различные методы закалки стали с последующим отпуском, которые существенно отличаются друг от друга. Наиболее важными режимами нагрева можно назвать:
- Температуру нагрева.
- Время, требующееся для нагрева.
- Время выдержки металла при заданной температуре.
- Скорость охлаждения.
Изменение свойств стали при закалке может проходить в зависимости от всех вышеприведенных показателей, но наиболее значимым называют температуру нагрева. От нее зависит то, как будет происходить перестроение атомной решетки. К примеру, время выдержки при закалке стали выбирается в соответствии с тем, какой прочностью и твердостью должно обладать зубчатое колесо для обеспечения длительной эксплуатации в условиях повышенного износа.

Цвета закалки стали
При рассмотрении того, какие стали подвергаются закалке стоит учитывать, что температура нагрева зависит от уровня содержания углерода и различных примесей. Единицы закалки стали представлены максимальной температурой, а также временем выдержки.
При рассмотрении данного процесса изменения основных эксплуатационных свойств следует учитывать нижеприведенные моменты:
- Закалка направлена на повышение твердости. Однако с увеличением твердости металл становится и более хрупким.
- На поверхности может образовываться слой окалины, так как потеря углерода и других примесей у поверхностных слоев больше, чем в середине. Толщина данного слоя учитывается при расчета припуска, максимальных размеров будущих деталей.
Выполняется закалка углеродистой стали с учетом того, с какой скоростью будет проходить охлаждение. При несоблюдении разработанных технологий может возникнуть ситуация, когда перестроенная атомная решетка перейдет в промежуточное состояние. Это существенно ухудшит основные качества материала. К примеру, охлаждение со слишком большой скоростью становится причиной образования трещин и различных дефектов, которые не позволяют использовать заготовку в дальнейшем.
Процесс закалки сталей предусматривает применение камерных печей, которые могут нагревать среду до температуры 800 градусов Цельсия и поддерживать ее на протяжении длительного периода. Это позволяет продлить время закалки стали и повысить качество получаемых заготовок. Некоторые стали под закалку пригодны только при условии нагрева среды до температуры 1300 градусов Цельсия, для чего проводится установка иных печей.
Отдельная технология разрабатывается для случая, когда заготовка имеет тонкие стены и грани. Представлена она поэтапным нагревом.
Полную закалку используют обычно для сталей и деталей, которые не подвержены растрескиванию или короблению.
Зачастую технология поэтапного нагрева предусматривает достижение температуры 500 градусов Цельсия на первом этапе, после чего выдерживается определенный промежуток времени для обеспечения равномерности нагрева и проводится повышение температуры до критического значения. Холодная закалка стали не приводит к перестроению всей атомной сетки, что определяет только несущественное увеличение эксплуатационных характеристик.
Как ранее было отмечено, есть различные виды закалки стали, но всегда нужно обеспечить равномерность нагрева. В ином случае перестроение атомной решетки будет проходить так, что могут появиться серьезные дефекты.
Методы предотвращения образования окалины и критического снижения концентрации углерода
Назначение закалки стали проводится с учетом того, какими качествами должна обладать деталь. Процесс перестроения атомной сетки связан с большими рисками появления различных дефектов, что учитывается на этапе разработки технологического процесса.
Даже наиболее распространенные методы, к примеру, закалка стали в воде, характерно появления окалины или существенного повышения хрупкости структуры при снижении концентрации углерода. В некоторых случаях закалка стали проводится уже после финишной обработки, что не позволяет устранить даже мелкие дефекты. Именно поэтому были разработаны технологии, которые снижают вероятность появления окалины или трещин. Примером можно назвать технологию, когда закалка стали проходит в среде защитного газа. Однако сложные способы закалки стали существенно повышают стоимость проведения процедуры, так как газовая среда достигается при установке печей с высокой степенью герметичности.
Более простая технология, при которой проводится закалка углеродистой стали, предусматривает применение чугунной стружки или отработанного карбюризатора. В данном случае сталь под закалку помещают в емкость, заполненную рассматриваемыми материалами, после чего только проводится нагрев. Температура закалки несущественно корректируется с учетом созданной оболочки из стружки. Технология предусматривает обмазывание емкости снаружи глиной для того, чтобы избежать попадание кислорода, из-за чего начинается процесс окислений.

Температура нагрева стали при термообработке
Как ранее было отмечено, термообработка предусматривает и охлаждение сталей, для чего может использоваться не только водяная, но, к примеру, и соляная ванная. При использовании кислот в качестве охлаждающей жидкости одним из требований является периодическое раскисление сталей. Данный процесс позволяет исключить вероятность снижения показателя концентрации углерода в поверхностном слое. Чтобы провести процесс раскисления используется борная кислота или древесный уголь. Также не стоит забывать о том, что процесс раскисления сталей приводит к появлению пламя на заготовки во время ее опускания в ванную. Поэтому при закалке, закалкой сталей с применением соляных ванн следует соблюдать разработанную технику безопасности.
Рассматривая данные методы термической обработки с последующим охлаждением следует отметить, что они существенно повышают себестоимость заготовки. Однако сегодня охлаждение в воде или закалка при заполнении камеры кислородом не позволяют повысить показатели свойств стали без появления дефектов.
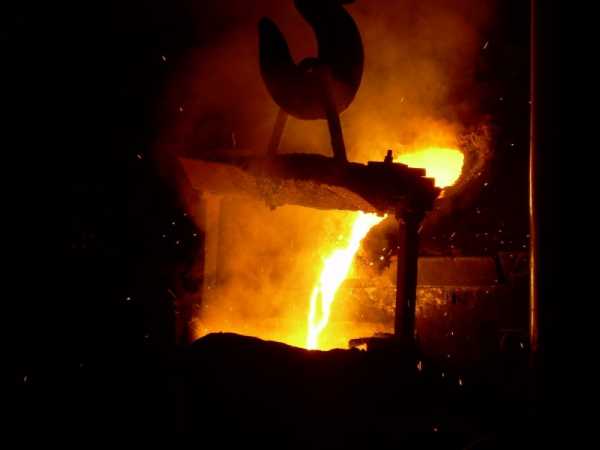
Закалка стали — технологический процесс
Процедура охлаждения
Рассматривая все виды закалки стали стоит учитывать, что не только температура нагрева оказывает сильное воздействие на структуру, но и время выдержки, а также процедура охлаждения. На протяжении многих лет для охлаждения сталей использовали обычную воду, в составе которой нет большого количества примесей. Стоит учитывать, что примеси в воде не позволяют провести полную закалку с соблюдением скорости охлаждения. Оптимальной температурой воды, используемой для охлаждения закалённой детали, считают показатель 30 градусов Цельсия. Однако стоит учитывать, что жидкость подвергается нагреву при опускании раскаленных заготовок. Холодная проточная вода не может использоваться при охлаждении.
Обычно используют воду при охлаждении для получения не ответственных деталей. Это связано с тем, что изменение атомной сетки в данном случае обычно приводят к короблению и появлению трещин. Закаливание с последующим охлаждением в воде проводят в нижеприведенных случаях:
- При цементировании металла.
- При поверхностной закалке.
- При простой форме заготовки.
Детали после финишной обработки подобным образом не охлаждаются.
Для придания нужной твердости заготовкам сложной формы используют охлаждающую жидкость, состоящую из каустической соды, нагреваемой до температуры 60 градусов Цельсия. Стоит учитывать, что закаленное железо при использовании данной охлаждающей жидкости приобретает более светлый оттенок. Специалисты уделяют внимание важности соблюдения техники безопасности, так как могут выделяться токсичные вещества при нагреве рассматриваемых веществ.

Процесс закалки стали
Тонкостенные детали также подвергаются термической обработке. Закалочное воздействие с последующим неправильным охлаждением приведет к тому, что концентрация углерода снизиться до критических значений. Выходом из сложившейся ситуации становится использование минеральных масел в качестве охлаждающей среды. Используют их по причине того, что масло способствует равномерному охлаждению. Однако попадание воды в состав масла становится причиной появления трещин. Поэтому заготовки должны подвергаться охлаждению при использовании масла с соблюдением мер безопасности.
Рассматривая назначение минеральных масел в качестве охлаждающей жидкости следует учитывать и некоторые недостатки этого метода:
- Соблюдая режимы нагрева можно создать ситуацию, когда раскаленная заготовка контактирует с маслом, что приводит к выделению вредных веществ.
- В определенном интервале воздействия высокой температуры масло может загореться.
- Подобный метод охлаждения позволяет выдержать требуемую твердость, измеряемую в определенных единицах, а также избежать появления трещин в структуре, но на поверхности остается налет, удаление которого также создает весьма большое количество проблем.
- Само масло со временем теряет свои свойства, а его стоимость довольно велика.
Какие именно жидкости используют для охлаждения стали?
Вышеприведенная информация определяет то, что жидкость и режим охлаждения выбираются в зависимости от формы, размеров заготовки, а также того, насколько качественной должна быть поверхность после закалки. Комбинированным методом охлаждения называется процесс применения нескольких охлаждающих жидкостей. Примером можно назвать закалку детали сложной формы, когда сначала охлаждение проходит в воде, а потом масляной ванне. В этом случае учитывается то, до какой температуры на каком этапе охлаждается металл.
Если вы нашли ошибку, пожалуйста, выделите фрагмент текста и нажмите Ctrl+Enter.
stankiexpert.ru
Металловедение и программирование – Разработка технологического процесса изготовления медицинского скальпеля
1. Выбор материала
Скальпели предназначены для рассечения мягких биологических тканей при хирургических вмешательствах.
В зависимости от назначения инструмент изготавливается:
– скальпель многоразовый;
– скальпель одноразовый стерильный;
– съемное лезвие для скальпеля;
– съемное лезвие для скальпеля одноразовое стерильное;
Для изготовления скальпелей и съемных лезвий применяется сталь нержавеющая марок 40Х13 ГОСТ 5582, 95Х18 ГОСТ 5949.
Выбранная для изготовления скальпеля сталь должна быть коррозиостойкой и позволять не только производить первоначальную острую заточку, но и длительно сохранять ее при пользовании.
Рассмотрим технологию изготовления скальпелей из стали 40Х13.
Химический состав и механические свойства данной стали приведены в таблицах 1 и 2.
Таблица 1 Химический состав стали 40Х13
C |
Cr |
Fe |
Mn |
P |
S |
Si |
0,36-0,45 |
12-14,0 |
Осн. |
≤0,8 |
≤0,030 |
≤0,025 |
≤0,8 |
Таблица 2 Нормированные механические свойства при 20 °С
ГОСТ |
Вид продукции |
Режим термической обработки |
Сталь |
σв, Н/мм² |
δ5, % |
HRC |
НВ |
не менее |
|||||||
ГОСТ 5582-75 |
Лист тонкий |
Отжиг или отпуск при 740-800 °С |
40Х13 |
550 |
15 |
– |
– |
ГОСТ 5949-75 |
Сорт Ø, ¤ до 200 мм Калиброванная сталь |
Отжиг или отпуск |
40Х13 |
– |
– |
– |
229-143 |
Закалка: с 950-1050°С; отпуск при 200-300°С, охлаждение на воздухе или в масле |
40Х13 |
– |
– |
50 |
– |
Содержание хрома в количестве 12-14% обеспечивает необходимую коррозиостойкость стали. Благодаря высокому содержанию углерода стали имеют мартенситную структуру с наличием карбидов и остаточного аустенита, что обеспечивает необходимую твердость и износостойкость. Мартенситные стали обладают хорошей коррозионной стойкостью в атмосферных условиях, в слабоагрессивных средах (в слабых растворах солей, кислот) и имеют высокие механические свойства.
2. Термообработка
Эти стали применяют после закалки и отпуска на заданную твердость. Благодаря малой критической скорости закалки стали 40X13 закаливаются на мартенсит при охлаждении на воздухе (рис. 1). Закалку изделий из этих сталей проводят от температур 950—1020°С, так как только выше этих температур происходит полное растворение в аустените карбидов Сr23С6. После закалки стали отпускают на требуемую твердость. Так, после закалки сталь 40Х13 имеет твердость HRC 56-58, после отпуска при 200—300 °С HRC 50, а после отпуска при 600 °С HRC 32-34. В интервале 480-520 °С наблюдается существенное снижение пластичности и ударной вязкости сталей из-за развития отпускной хрупкости.
Рис. 1 Диаграмма изотермического распада переохлажденного аустенита стали 40Х13. 1 – закалка в масле, 2 – охлаждение на воздухе, 3- охлаждение в печи
После закалки стали имеют высокую коррозионную стойкость. Отпуск при 200—400 °С проводят для снятия внутренних напряжений; он не оказывает влияния на коррозионную стойкость. При отпуске выше 500 °С происходит распад мартенсита на феррито-карбидную смесь и выделение карбидов типа Ме23С6, структура стали становится гетерогенной, ферритная матрица обедняется хромом, коррозионная стойкость резко снижается. Отпуск при более высоких температурах повышает коррозионную стойкость.
Термообратка скальпеля из стали 40Х13 проводится путем закалки при температуре 950—1020°С с охлаждением на воздухе и низкого отпуска при 200 °С, что дает возможность сохранить Мартенситную структуру.
Литература:
– ГОСТ 30208-94 (ИСО 7153-1-88)/ГОСТ Р 50328.1-92 (ИСО 7153-1-88) Инструменты хирургические. Металлические материалы. Часть 1. Нержавеющая сталь.
– Специальные стали. Учебник для вузов. Гольдштейи М. И., Грачев С. В., Векслер Ю. Г. М.: Металлургия, 1985. 408 с.
artmetals.ucoz.org