Устройство резака газового – устройство, настройка, портативный, своими руками
alexxlab | 29.06.2019 | 0 | Вопросы и ответы
условия эксплуатации ножей, инжекторные устройства
Газовая резка металла предусматривает использование высоких температур для его нагревания, стимулируя процесс плавления или возгорания. Обширный диапазон применения газового резака позволяет использовать его для работы в ручном режиме. Устройство газового резака применяется для создания из металлических листов сложных конструктивных форм.
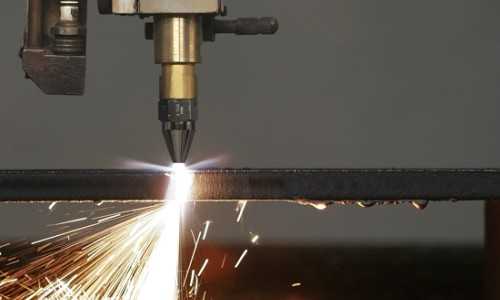
Устройство газового резака используется для создания сложных конструктивных форм из металлических листов.
Зачем нужен газовый резак?
Благодаря достоинствам газовая резка металла используется очень часто. Она проводится без применения сложного оборудования, не требует большого количества источников энергии, простая в исполнении. Наиболее часто она применяется в сельском хозяйстве, при проведении ремонтных работ в промышленности.
Резак используют при работе с изделиями из алюминия, чугуна, латуни, бронзы. В процессе эксплуатации применяют 2 вида газа — кислород и пропан. Резка пропаном используется для стальных листов с содержанием углерода выше 0,8%.
Использование смеси пропана и кислорода для работы газового ножа
Схема газового резака.
В процессе разрезания металла формируется газовое облако с высокой температурой. Наблюдается окисление продуктов сгорания за счет влияния кислорода.
Для работы с применением пропана используют несколько видов горелок:
- индукторные;
- модели с камерами;
- камерно-вихревые.
При кислородной резке металла применяют горючие жидкости, образующие температуру смеси до 1800°C. Чистота кислорода для работы составляет 98,5-99,5%.
В процессе осуществления мероприятий под водой используют резак с бензиново-кислородным горением, а легированные стали разрезают кислородно-флюсовой резкой.
Газовый нож для ручной резки с применением ацетилена разъединяет металл толщиной 60 мм, образуя шов шириной от 2,0 до 4,5 м.
Подготовленный материал обрабатывается при помощи смеси, находящейся в корпусе ножа, предназначенного для разрезания вручную. Устройства для разъединения материалов подразделяют на следующие виды:
Схема кислородного резака.
- по характеру используемой смеси;
- по функциональным признакам.
Инжекторные ножи изготавливают по ГОСТ 5191-796. Они имеют несколько мощностей, зависящих от толщины металла.
Конструкция газового ножа обязана удовлетворять такому требованию, как наличие ствола, состоящего из специальных запорных вентилей, способных подогревать пламя. Обязательно присутствие крепления из двух ниппелей и гаек согласно ГОСТ 9356-75.
К газовому ножу прилагается наконечник с трубкой и сменные мундштуки. Дозирующее устройство оснащено удлинительной трубкой. Работа газового ножа осуществляется с применением газов, имеющих величину сгорания 16,9 МДж/м³.
Следует использовать для работы детали ножей, изготовленные из латуни. Для создания ствола резака используют алюминиевые материалы, не влияющие на работу газового ножа.
Для изготовления мундштуков используют бронзу марки БрХ1. Особое внимание уделяют созданию деталей смесительной емкости. Они изготавливаются из сплавов, содержащих медь не более 70%. Общая длина газового ножа составляет 700 мм.
Устройство ручного газового ножа
Основная задача устройства для резки состоит в подаче режущей струи в центральное отверстие мундштука. Нож имеет ствол, соединенный резинотканными рукавами с ниппелем, а через него с правой резьбой для подачи кислорода. Соединение через штуцер с левой резьбой обеспечивает подачу ацетилена и других газов.
Устройство ручного газового ножа.
Небольшое количество кислорода попадает в инжектор, а затем в емкость перед смесительной камерой. В ней горючий газ смешивается с кислородом из-за создания разреженного пространства.
Смесь транспортируется в промежуток между гильзой и соплом, а часть кислорода поступает в центральный канал. С помощью вентилей происходит регулировка интенсивности подогревающего пламени.
Основное устройство состоит из инжектора и смесительной емкости. От ее функционирования зависит работа газового ножа. Сбой в работе происходит при изменении размеров зазора между концом инжектора и самой камерой.
Ствол содержит маркировку вида ножа, на смесителе обозначают вид используемого топлива.
Схема инжекторного газового резака.
Ножи средней мощности пригодны для разъединения листов металла толщиной до 200 мм. Устройства, обладающие большей мощностью, работают на смеси сжиженного или природного газа. Комплектующие ножи к аналогичным модификациям горелок отличаются между собой наличием соединительных деталей. Ножи включают в свой состав корпус, несколько мундштуков, рычаг пуска, вентили. Используется рабочее давление газа не ниже 0,8-1,2 Мпа при общем его расходе-74 м³/г. Масса ножа составляет 2 кг.
Резка металлов осуществляется не только с применением газового ножа, но и с использованием плазменных аппаратов. Современный плазморез вместо рабочего газа использует сжатый воздух. Универсальность аппарата позволяет производить не только резку, но и создание дуги между электродами.
Условия эксплуатации газовых ножей
Работа с устройством для разъединения материалов требует от газорезчика собранности и внимания. Прежде всего, мастеру нужно проверить нож, найти видимые повреждения. Он проверяет соединение между рукавами и резаком. Рукав продувают с помощью газа. Осматривают механизм взаимодействия рукава и штуцера.
До подключения левого рукава устанавливают наличие давления в ноже. Используя данные инструкции, крепят два мундштука. При слабом подсосе требуется прочистить инжектор.
Устанавливают герметичность в соединениях ножа. Одновременно подтягивают крепления сальника до упора или полностью заменяют кольца уплотнителя смесительной камеры. Контролируют уровень жидкости в водяном затворе.
После проведения процедуры проверки необходимо отрегулировать пламя в газовом ноже. До начала процесса устанавливают запас ацетилена. При возникшей необходимости ликвидации пламени закрывают вентиль емкости с ацетиленом, а затем — кислородный кран.
Ручной газовый резак имеет эргономичный дизайн, удобен при обслуживании, пригоден для использования горючих газов.
moyasvarka.ru
2.1. Резак. Устройство резака
Рис. 10. Инжекторный резак (8)
Резаки служат для смешивания горючего газа с кислородом, образования подогревающего пламени и подачи к разрезаемому металлу струи режущего кислорода. Рассмотрим устройство резака.
Устройство резака
Рис. 11. Устройство инжекторного резака (11)
Как и сварочные горелки, резаки имеют инжекторное устройство, обеспечивающее нормальную работу при любом давлении горючего газа. Инжекторный резак отличается от инжекторной горелки тем, что имеет отдельный канал для подачи режущего кислорода и специальную головку, которая представляет собой два сменных мундштука – внутренний и наружный.
Ацетиленокислородный инжекторный резак состоит из двух основных частей – ствола и наконечника. Ствол состоит из рукоятки с ниппелями для присоединения кислородного и ацетиленового рукавов, корпуса с регулировочными кислородным и ацетиленовым вентилями, инжектора, смесительной камеры, смесительной трубки, дюзы, трубки режущего кислорода с вентилем для режущего кислорода. Ствол прикрепляется к корпусу резака накидной гайкой.
Кислород из баллона поступает в резак через ниппель и в корпусе разветвляется по двум каналам. Часть газа, проходя через кислородный вентиль, направляется в инжектор. Выходя из инжектора с большой скоростью, струя кислорода создает разрежение и подсасывает ацетилен, образующий с кислородом в смесительной трубке горючую смесь, которая проходя через зазор между наружным и внутренним мундштуками, сгорает, образуя подогревающее пламя.
Другая часть кислорода через вентиль режущего кислорода поступает в трубку режущего кислорода и выходя через центральный канал внутреннего мундштука, образует струю режущего кислорода.
Рис. 12. Инжекторный резак в разрезе и инжектор (13)
www.e-ope.ee
Ацетиленовый резак: устройство, принцип работы, особенности
Одним из самых востребованных металлообрабатывающих приборов является газовый резак, который позволяет раскраивать изделия из железа и стали в соответствии с утвержденным проектом. Действие таких устройств основано на нагревании материала до высоких температур, его сгорании в кислородной струе и удалении той же струей продуктов горения из зоны реза.
На крупных производственных объектах особой популярностью пользуется ацетиленовый резак, который способен разрезать стальные листы и изделия металлопроката толщиной 300 миллиметров и более. Одновременно с этим увеличивается производительность предприятия, улучшается качество обработки изделий и ускоряется производственный процесс.
Устройство ацетиленовых резаков
Любой газокислородный резак состоит их трех основных частей – газовых баллонов, ствола и наконечника. Ствол представляет собой рукоятку с ниппелями, которые служат для присоединения газовых рукавов с кислородом и ацетиленом. На корпусе также имеется три клапана, с помощью которых регулируют подачу режущего и подогревающего кислорода, а также рабочего газа (ацетилена).
Одним из основных элементов, входящих в ацетиленовый резак, является инжектор – ускоритель заряженных частиц. Сразу к нему присоединена камера смешения, в которой образуется горючая смесь из ацетилена и химически чистого кислорода. Камера смешения плавно переходит в трубку подачи подогревающего кислорода.
Перед самым инжектором на стволе имеется ответвление – трубка режущего кислорода. На ней расположен вентиль, регулирующий подачу химически чистого кислорода. Торцы трубок подачи подогревающей смеси и режущего кислорода присоединены к наконечнику. Он состоит из внутреннего и наружного мундштуков, которые помещены в специальную головку резака.
Принцип действия ацетиленового резака
Как и любой другой газокислородный нож, ацетиленовый резак обрабатывает металлические изделия одновременным воздействием высокой температурой и направленной кислородной струей. После присоединения газовых рукавов к ниппелям кислород направляется в двух направлениях. Одна часть газа, через специальное ответвление, попадает в трубку режущего кислорода, а другая – в инжектор.
Выходя из инжектора, кислород развивает высокую скорость и создает зону разряжения в смесительной камере. Из-за разницы давления в камеру начинает «подсасываться» ацетилен, который равномерно смешивается с О2. Полученная смесь газов на высокой скорости движется дальше и вырывается через зазор между внутренним и внешним мундштуками, одновременно воспламеняясь.
Так образуется подогревающее пламя, которое доводит материал до аморфного (полужидкого/полутвердого) состояния. Через установленный на ацетиленовый резак наконечник вырывается также струя режущего кислорода, которая своей высокой скоростью «сдувает» расплавленный металл.
Особенности ацетиленового резака
Все особенности ацетиленового резака обусловлены рабочим газом – ацетиленом. В отличие от других видов топлива он способен разогреваться до температуры порядка 3100 градусов по Цельсию. Именно благодаря этому обеспечивается:
- Наивысшая производительность – при помощи ацетиленового газокислородного ножа можно разрезать материал толщиной более 300 мм.
- Низкая доля окислительных процессов – структурные связи в молекулах мгновенно разрушаются без образования соединений с кислородом.
- Высокое качество резки.
На рынке в широком ассортименте представлен резак ацетиленовый «Маяк». Модели отличаются главным образом либо конструкцией ствола, либо его заменяемой частью – мундштуком, от которого зависит интенсивность, а также размер газовой струи.
Универсальные резаки
В некоторых случаях использовать резак газовый ацетиленовый экономически нецелесообразно. При этом иметь два резака, работающих на разных типах топлива, неразумно. Поэтому на крупных производственных объектах особой популярностью пользуются универсальные газокислородные ножи. Их главная особенность заключается в способности работать от разных видов топлива.Подавляющее большинство универсальных агрегатов используется для ручной резки нелегированных изделий или сталей с низким процентом углерода в их составе. Наибольшее распространение получил пропановый/ацетиленовый резак. Первый тип газа используется для обработки материалов толщиной до 200 мм, а второй – свыше 300 мм.
fb.ru
Резаки для ручной резки газовой (кислородной), промышленные устройства
Предназначение резаков состоит в разрезании металла путем его нагрева и рассечения струей газа. Так можно разрезать металлические изделия практически любой формы за короткое время. Все резаки для ручной резки
Данная смесь призвана обеспечить соответствующий нагрев поверхности металла по определенной линии. После нагрева на место будущего реза подается кислород, который окисляет и вытесняет своим напором расплавленный металл. Образуется достаточно ровный рез. Работа проводится быстро и эффективно. По своему предназначению различают устройства для ручной, механизированной резки, а также аппараты специального назначения. Мы рассмотрим подробно бытовые и промышленные резаки для ручной резки.
Какими бывают резаки для ручной резки металла?
Существует множество модификаций данных устройств.
Они квалифицируются по множеству признаков, которые мы сейчас постараемся перечислить:
- По виду реза. Резаки для ручной газовой резки подразделяются на следующие типы: поверхностные, разделительные и кислородно-флюсовые.
- По принципу своего действия. Различают инжекторные и безинжекторные устройства.
- По конструкции мундштуков (наконечников). Бывают многосопловые и щелевые.
- По виду используемого горючего. Существуют аппараты для жидкого топлива, для газов-заменителей, а также для ацетилена.
- По уровню давления кислорода. Низкое или высокое давление.
Устройство газового резака
Резаки для ручной кислородной резки, независимо от квалификации, имеют схожее устройство, ведь все они работают по схожему принципу.
Резак состоит из корпуса, на котором расположены регулирующие подачу газов клапаны, газовых трубок, рукоятки и головки для навинчивания мундштука. К корпусу крепится смесительная камера с инжектором. Поступающий в трубки кислород идет в двух направлениях. Часть его, предназначенная для подогрева, подается в главный канал инжектора. Кислород в смесительной камере создает разрежение, из-за чего происходит подсос ацетилена. Смесь направляется к мундштуку и выходит через него в виде подогревающего пламени.
Вторая часть кислорода проходит в головку, откуда уже выходит через канал мундштука с образованием режущей кислородной струи.
Виды мундштуков для резаков
Многосопловые мундштуки
Такие мундштуки имеют несколько каналов (сопел), имеющих диаметр от 0,7 до 1 мм. Сопла расположены вокруг канала, по которому проходит кислород. Могут быть цельными или составными. Различные газы поступают по различным соплам, смешиваясь и сгорая на выходе. Такие мундштуки используют с газами-заменителями, которые обладают невысокими скоростями горения.
Есть и недостаток — сопла при частом использовании забиваются шлаками. Это может вызывать обратное направление пламени или хлопки.
Щелевые мундштуки
Состоят из двух отдельных мундштуков, входящих друг в друга. Между ними находится кольцевой зазор, по которому проходит смесь кислорода с ацетиленом. Воспламененная смесь выбрасывается через головку и служит для нагрева металла. По каналу внутреннего мундштука идет поток кислорода, которым осуществляется непосредственная резка.
steelguide.ru
Газовая резка металла – виды, технология, оборудование
В связи с тем, что операция не отличается сложностью и отсутствуют жесткие требования к местам осуществления работ газовая резка приобрела широкую популярность при проведении многих работ. Далее разберем технологию газовой резки металла, ее особенности, применяемые устройства и принципы его работы.
Резка металла газом отличается простотой, так как не нуждается в использовании дополнительных источников энергии и сложного оборудования. Подобный способ обработки популярен среди многих специалистов во всех отраслях промышленности. Почти все оборудование для резания отличается мобильностью и простотой транспортировки.
Разновидности газовой резки
Газопламенная резка металла может классифицироваться по нескольким признакам, исходя из типа применяемого газа и ряда иных нюансов. Каждый метод лучшим образом решает определенные задачи. К примеру, при возможном подключении к электрической сети, возможно применение кислородно-электрической дуговой резки, при обработке низкоуглеродистой стали целесообразно применять газовоздушную смесь на основе пропана. К числу самых распространенных относятся:
- Пропановая – самый популярный способ работы. Существует ряд определенных ограничений. Техника применима для титанового сплава, низкоуглеродистых и низколегированных сталей. При наличии углерода, легирующего компонента более 1% следует использовать иные методы. Резка и сварка данным способом может предполагать применение иных газовых смесей с метаном, ацетиленом и иных.
- Воздушно-дуговая. Достаточно эффективный способ раскраивания деталей из металла. На изделие воздействует электрическая дуга, а остаточные элементы удаляются воздушными струями. Кислородная электрическая резка предусматривает подачу газовой смеси вдоль электрода. К минусам метода можно отнести довольно неглубокий рез, но его ширина может быть практически неограниченной.
- Кислородно-флюсовая. Отличается тем, что к рабочей зоне подается дополнительные компоненты – флюсы. Зачастую это порошкообразный материал. Благодаря им формируется лучшая податливость металла в процессе резки. Технология хороша при резании сплавов, у которых образовывается твердоплавкий окисел: чугун, легированная сталь, алюминий, медь и ее сплавы.
- Копьевая. Кислородно-копьевая резка применяется при разделении значительных объемов стали. Главной особенностью является существенное увеличение скорости выполнения работы. Подобная технология газовой резки металла формирует энергоемкую струю, снижающей расход копьев из стали. Повышенная скорость работы достигается также за счет полного и быстрого сгорания металла.
Применяемое оборудование
Резка металла газовым резаком сопровождается применением ряда дополнительных и основных компонентов. В целом оборудование состоит из:
- Редуктор – необходим для понижения давления до требуемых значений. Имеет 2 манометра для контроля данных на входе и выходе.
- Газовый и кислородный баллон.
- Соединительные шланги. Длина шланга не должна быть больше 30 метров.
Редуктор необходим для осуществления регулировки давления и поддержания его в автоматическом режиме в заданных значениях. Может состоять из 1 или 2 камер. В случае наличия двух камер, то у устройства повышается надежность.
Стальные баллоны имеют объем от 0,4 до 55 дм3. Имеют запорный вентиль, который может быть различной конфигурации, исходя из типа применяемого газа.
Технология газовой резки
Газовая резка металла кислородом предполагает нагрев детали примерно до 1100 °С. После этого к рабочей зоне подается кислородная струя, соприкасающаяся с прогретой поверхностью и в последствии загорающаяся. Горящий поток с легкостью режет металлическую деталь. При этом требуется постоянный и стабильный поток газовой смеси.
Металл должен иметь меньшую температуру горения, чем температура плавления. Иначе расплавленную, не сгоревшую массу будет затруднительно убрать с поверхности.
Исходя из этого, газокислородная резка металла проводится благодаря сгоранию газовой смеси. Основным элементом оборудования выступает газовый резак, обеспечивающий регулирование и формирование газовоздушной смеси. Данный инструмент производит воспламенение и перемещение струи в рабочей зоне.
Газоплазменная резка металлов – это одна из операций термической обработки. Основным преимуществом является то, что позволяет раскраивать материал любых толщин, сохраняя высокий КПД. Другим достоинством будет полная автономность и независимость от стороннего источника питания.
Технология может применяться для резания различных материалов. Исключением будет латунь, нержавеющая сталь, медь и алюминий.
Сколько расходуется газа
Объем расходуемого газа будет зависеть от способов осуществления работы. К примеру, во время воздушно дуговой резки будет вырабатываться больше газа, чем в случае с кислородно-флюсовой. В основной мере расход станет зависеть от:
- Опытности сварщика. Без должного опыта традиционно расходуется большее количество газа.
- Целостности и технических параметров применяемого оборудования.
- Типа и толщины обрабатываемых деталей.
- Ширины и глубины резки.
Условия для выполнения работы
Для успешного проведения работы необходимо достижение более высокой температуры плавления, чем температура воспламенения. Отлично соответствуют этому требованию низкоуглеродистые сплавы, которые расплавляются на 1500°С, а воспламениться способны на 1300 °С. Сталь со средним и высоким содержанием углерода будут резаться газом хуже, т.к. высокий процент содержания углерода способствует понижению температуры плавления и увеличению градуса воспламенения.
Следующим требованием является наличие не очень высокой теплопроводности. В противном случае активно отделяется нагретый шлак и операция становится неустойчивой, что может способствовать прекращению резки. Оптимальная теплопроводность наблюдается у стали и железа. Газовая резка металла пропаном других металлов в основном невозможна.
Также необходимо соблюдение следующих условий для резания:
- Кислородная (газовая) струя сжигает определенный объем металла. При этом необходимо постоянное выделение такого количества теплоты, которого будет достаточно для непрерывного проведения операции. Только 30% тепловой энергии образует пламя резака, оставшиеся 70% образовываются в процессе сгорания металлов.
- Высокий уровень жидкотекучести образовывающегося шлака. Это требуется для простой выдувки шлака из рабочей зоны.
Достоинства и недостатки технологии
Резание металла при помощи газа имеет ряд преимуществ:
- Отличное решение при необходимости резки изделий большой толщины или криволинейных резов по шаблонам. Возможность выполнения глухих отверстий глубиной до 5 см.
- Масса газового резака не велика, он удобен и мобилен. Отсутствует громоздкость, большой вес и повышенный шум, присущий электро и бензоинструменту.
- Технология позволяет увеличить скорость работы до 2 раз в сравнении с бензиновым инструментом.
- Газовая заправка баллона обходится дешевле и его хватает на большие объемы работы, чем в случае заправки бензином.
- Газовый резак позволяет создавать узкую и чистую кромку на срезе.
К числу минусов можно отнести возможность взрыва газовоздушных смесей, нагреву значительных площадей изделий, ограниченный круг доступных к обработке металлов, которые рассматривались выше.
Деформация металла
Из-за термического воздействия на заготовку процесс деформации будет вполне естественным и его избежать сложно. При нагреве возможно изменение формы. В итоге можно получить вывернутую и вогнутую вырезанную деталь.
Деформационным процессам способствуют:
- Проведение неравномерного прогрева;
- Быстрое перемещение горелки;
- Высокая скорость охлаждения по окончанию работы.
В процессе работы нужно по максимальной возможности исключать влияние этих факторов. Иначе потребуется исправление поведенной заготовки. Существует ряд методов, позволяющих устранить или исключить дефекты:
- Отпуск или обжиг;
- Исправление листовых изделий на вальцах;
- Надежное закрепление до начала работы;
- Соблюдение верной последовательности действий в соответствии с толщиной и типом металла.
Без должного опыта выполнения данной операции начинать рекомендуется с малых деталей, а не сразу с массивных изделий.
Возможность обратного удара во время резки
Раскраивая металл газовым оборудованием необходимо учитывать то, что возможен эффект обратного удара. Он предполагает начало горение газового потока в обратном направлении, что предполагает значительное повышение скорости этого процесса. Сбой может спровоцировать поломку оборудования и даже его взрыв. Устраняется опасность путем установки дополнительного клапана.
oxmetall.ru
Газовый резак своими руками – пошаговая инструкция
Для того чтобы изготовить газовый резак своими руками, достаточно желания, некоторого количества свободного времени и нескольких самых простых составных частей. Российские умельцы давно придумали несколько вариантов конструкций, которые могут быть собраны любым желающим. По своим характеристикам таким изделия, конечно же, уступят изготовленным в заводских условиях. Тем не менее, они окажутся полезными при необходимости выполнить незначительные объемы по резке металла.
Достоинства газовых резаков
Газовые резаки или автогены пользуются популярностью из-за простоты и удобства работы с ними. При некоторой кустарности изготовления, газовый резак, выполненный своими руками, обладает вполне сносной производительностью и мощностью. Самостоятельное изготовление изделия позволяет сэкономить значительное количество средств, и вполне окупиться при необходимости выполнения небольших объемов работ с металлом.
В результате становится понятным, почему российские изобретатели не остались в стороне, не придумав какого-нибудь простейшего способа как сделать резак по металлу.
Необходимые материалы и инструменты
Для работ по изготовлению небольшого газового резака необходимо предварительно укомплектоваться:
- двумя капельницами достаточно большого размера;
- иглой, при помощи которой накачивают обычные мячи для игры в футбол;
- обыкновенной бутылкой из пластика объемом 1,5-2 л. или, в качестве альтернативного варианта, компрессором для аквариума;
- баллоном, которым заправляют обычные зажигалки, наполненным пропан-бутаном;
- проволокой из меди;
- автомобильным соском для камеры;
- набором инструментов, содержащим паяльник, термо-клей, нож обычный или канцелярский, надфиль, точильный брусок или камень и т.д.
Изготовление
Процесс изготовления происходит в несколько последовательно выполняемых этапов:
- Изготавливается подающая газ игла, исполняющая роль наконечника газового резака. На игле, применяющейся чтобы накачивать мячи, на расстоянии около 2 см от конца делается маленький надрез при помощи надфиля.
- Изготавливается подающая воздух (кислород) игла. Для этого необходимо взять иглу из капельницы, спилить острый наконечник точилом, изогнуть под 45 градусов на том же расстоянии (около 2 см). После этого изогнутая игла вставляется в отверстие, которое заранее было проделано в большой.
- При необходимости торчащие концы получившейся конструкции из двух игл выравниваются надфилем или точильным камнем.
- Для герметизации стыка и фиксации соединения игл друг к другу необходимо обмотать его проволокой из меди, заранее приготовленной и зачищенной от окиси. После этого обмотка покрывается флюсом, используемым для пайки, и тщательно, но аккуратно пропаивается оловом.
- К задним окончаниям игл присоединяются трубочки капельниц. При этом зажимы с них не снимаются, так как они будут использоваться для регулирования размера пламени.
- Изготавливается емкость для кислорода (или обычного воздуха, находящегося под давлением). Для этого в дне приготовленной бутылки из пластика вырезается отверстие под сосок из автомобильной камеры, который туда и устанавливается с использованием клея и специальной гайки. Такая конструкция позволит накачать в бутылку обыкновенным автонасосом сжатый воздух. В качестве альтернативного и более удобного варианта может быть использован компрессор для аквариума или даже электрический автонасос.
- В крышке ПВХ бутылки изготавливается отверстие для установки в нем капельницы, которая предварительно разрезается до так называемой «юбки». Место соединения крышки и капельницы также должно быть тщательно загерметизировано с использованием термо-клея.
- Получившаяся конструкция соединяется при помощи трубки капельницы с отверстием маленькой иглы. Таким образом, часть резака, по которой должен будет проходить сжатый воздух, практически выполнена.
- Изготавливается вторая магистраль, предназначенная для прохождения газа из баллона, который используется для заправки зажигалок. В пластмассовой крышке баллончика необходимо изготовить отверстие, диаметр которого должен совпадать с трубкой капельницы. Затем трубка вставляется в полученное отверстие. На ее конец устанавливается специальная насадка, которая обычно поставляется вместе с баллоном. Соединение должно быть максимально плотным, герметичным и прочным. После этого трубка с установленной насадкой фиксируется в пластиковой крышке таким образом, чтобы в закрытом положении она оказывала давление на сосок баллона.
Свой собственный газовый резак по металлу готов.
Работа с изготовленным резаком
Перед началом работы на изготовленном собственноручно мини-резаке, необходимо накачать бутылку из пластика воздухом (при использовании компрессора или автомобильного электронасоса — включить их). Затем следует аккуратно закрыть крышку баллончика для зажигалок.
После выполнение всех перечисленных процедур необходимо открыть ограничительные зажимы, расположенные на трубках капельниц. После этого из каждой из игл должен начать выходить, соответственно, воздух и газ. Для начала работы резаком достаточно поднести огонек зажигалки или спичку к кончику резака.
Появившееся пламя необходимо отрегулировать вращением зажимов до ровного голубого цвета. Резак, режущий металл, готов к использованию. Производительности и мощности вполне хватит, чтобы с легкостью резать листовой металл до 1-2 мм толщиной. При этом температура пламени может доходить до 1,5 тысяч градусов.
Другим часто встречающимся вариантом газового резака, выполненного собственными силами, является водородный автоген, использующий в работе электролизный принцип. Его изготовление несколько сложнее и требует более значительных затрат средств и времени.
Заключение
Изготовление газового резака своими руками возможно и достаточно просто реализуемо. В результате можно получить эффективно работающее изделие, обладающее достаточно высокой производительностью и мощностью. При этом затраты времени и средств, необходимых для этого, относительно невелики. Способами и технологиями изготовления подобного оборудования, известными читателям, можно поделиться в комментариях к статье.
wikimetall.ru
Газорезка и необходимые знания при выборе газорезательного инструмента
В данной статье мы поговорим о газовых резаках. Для чего нужен газовый резак? Как ни странно, но он нужен для резки металла. Для этого сначала нужно нагреть метал до температуры плавления, а затем подать туда струю кислорода для того, чтобы металл начал гореть, и таким образом, осуществляется резка.
Для этого чаще всего используют два типа горючего газа:
- Пропан
- Ацетилен
Обычно на газорезке, предназначенной для резки с пропаном в наименовании имеется буква “П” в ацетиленовой версии используется буква “А”.
Газорезки могут делиться по толщине реза:
Резаки с пометкой “Р1” способны резать металл до 100 миллиметров.
С пометкой “Р3” способны резать металл до 300 миллиметров.
Сейчас, к сожалению, не все производители соблюдают это требование. К примеру, на рынке могут встретиться резаки, помеченные индексом “Р3”, и потребители думают, что они могут осилить металл до 300 миллиметров, но это оказывается не так.
Также резаки делятся между собой по принципу смешения газа:
Инжекторный резак. Они имеют 2 трубки. Горючий и подогревающий кислород движется на выход по одной трубке, а режущий кислород по другой.
Есть ещё и резаки с тремя трубками. Они называются “С внутрисопловым смешиванием газа”. Все 3 вида газа идут по отдельной трубке и смешиваются на выходе в отдельной установке, под названием “Сопля”. Поэтому этот вид газорезки называется внутрисопловое смешивание.
По типу подачи режущего кислорода резаки делятся на вентильные и рычажные:
Вентильные резаки имеют специальный вентиль, с помощью которого газорезчик может увеличивать и уменьшать подачу кислорода.
Рычажный. Исходя из названия, можно понять, что он имеет специальный рычаг, по нажатию на который происходит подача режущего кислорода.
Как выбрать газовый резак для газорезки?
Здесь пойдёт речь о том, как правильно выбрать резак? Р1 или Р3? Как выбрать резак по внешнему виду?
Прежде всего, нужно отметить, что невозможно сделать выбор глядя на какую-то рекламу или картинку. Для того, чтобы правильно выбрать резак его нужно как минимум взять в руки.
Для начала нужно определиться с тем, для каких целей вы хотите приобрести резак? Если вам нужен резак чтобы резать металл до 100 миллиметров, то нужно приобретать резак с пометкой Р1. Если же нужно резать металл до 300 миллиметров, соответственно это будет приспособление с пометкой Р3. Далее, нужно обратить внимание на внешний вид резака и из чего изготовлен наружный мундштук резака. Для хорошей и безопасной работы с устройством нужно приобретать резак с мундштуком, изготовленным из хромистой бронзы или из материала не уступающим ей по своим физико-механическим свойствам. Например, это может быть медь.
Также необходимо обратить внимание на то, из чего изготовлена внутренняя часть мундштука. Для безопасного и долгосрочного использования газорезки — внутренний мундштук должен изготавливаться из хромистой бронзы или меди. Различить их можно по цвету.
Из чего должен быть изготовлен резак?
Изготовление резаков допускается из латуни, она имеет жёлтый цвет. Из меди, она будет иметь цвет меди. Или из нержавеющей стали, серого цвета. Приобретать резаки, изготовленные из других материалов – не рекомендуется.
Для долгосрочной работы рекомендуется приобретать разобранный резак. Он должен иметь разъёмные соединения на тот случай, если, допустим, из строя вышел наконечник, износилась головка или прогорела трубка. Такие газорезки можно легко разобрать и без особого труда и усилий заменить испорченную делать.
Желаем сделать вам удачный выбор, руководствоваться данной статьёй и следить за безопасностью своей жизни и жизни своего помощника – резака.
weldering.com